Discover Cost-Saving Tips for Baler Machinery (2025)
Introduction: Navigating the Global Market for baler machinery
Baler machinery plays a crucial role in waste management and recycling, offering solutions to one of the most pressing challenges faced by businesses today—efficiently compressing and handling various types of waste. As international B2B buyers from regions such as Africa, South America, the Middle East, and Europe seek to optimize their operations, understanding the diverse types of balers available, including vertical and horizontal balers, becomes essential. This comprehensive guide delves into the intricate world of baler machinery, addressing key elements such as types, applications, supplier vetting, and cost considerations.
By exploring the different applications of balers, from cardboard and plastic to textiles and metals, buyers will gain insights into which equipment best meets their specific needs. Additionally, the guide emphasizes the importance of supplier credibility, helping buyers navigate the global marketplace to find reliable manufacturers who offer quality products and support. With actionable insights and expert recommendations, this resource empowers B2B buyers to make informed purchasing decisions, ensuring they select the right baler machinery tailored to their operational requirements.
In an era where sustainability is paramount, investing in the right baler not only enhances waste management efficiency but also contributes to environmental stewardship. This guide serves as a vital tool for international buyers aiming to leverage baler technology to reduce costs, improve operational efficiency, and achieve their sustainability goals.
Understanding baler machinery Types and Variations
Type Name | Key Distinguishing Features | Primary B2B Applications | Brief Pros & Cons for Buyers |
---|---|---|---|
Cardboard Balers | Hydraulic press for compressing cardboard into bales; often vertical or horizontal. | Recycling cardboard, packaging industries | Pros: Efficient for large volumes; reduces storage space. Cons: Requires space for operation; may need manual labor for loading. |
Automatic Balers | Fully automated systems that handle large volumes; high pressure capabilities. | Large-scale recycling, manufacturing | Pros: High throughput; minimal labor required. Cons: Higher initial investment; complex maintenance. |
Manual Balers | Smaller, often vertical designs; operated by hand for lower volumes. | Small businesses, local recycling | Pros: Lower cost; easy to use. Cons: Limited capacity; labor-intensive. |
Industrial Shredders | Designed to shred various materials before baling; heavy-duty construction. | Waste management, recycling facilities | Pros: Versatile; prepares materials for more efficient baling. Cons: Higher operational costs; requires more space. |
Tire Shredders | Specialized for shredding tires into manageable pieces for recycling. | Tire recycling, automotive industries | Pros: Reduces tire volume significantly; essential for eco-friendly disposal. Cons: Requires specific maintenance; high energy consumption. |
What Are the Key Characteristics of Cardboard Balers?
Cardboard balers are essential for businesses that handle significant amounts of cardboard waste. They utilize hydraulic pressure to compress cardboard into manageable bales, which can then be easily transported or stored. When considering a cardboard baler, buyers should evaluate their volume of waste, available space, and whether they need a manual or automatic model. The efficiency of these machines in reducing waste volume can lead to substantial savings in transportation and storage costs.
How Do Automatic Balers Enhance Efficiency in B2B Operations?
Automatic balers are ideal for large-scale operations, capable of handling high volumes of materials with minimal human intervention. These machines are equipped with advanced technology that automates the baling process, allowing for a faster throughput. B2B buyers should consider their production scale, as the initial investment is higher compared to manual balers. However, the long-term savings on labor and increased efficiency often justify the cost, making them a smart choice for large manufacturers and recycling centers.
Why Choose Manual Balers for Small Businesses?
Manual balers are a practical choice for small businesses or those with lower waste volumes. These machines are typically more affordable and easier to operate, requiring less space than their automatic counterparts. Buyers should assess their waste management needs, as manual balers can be labor-intensive, necessitating staff to load materials. Despite their limitations in capacity, they provide an economical solution for businesses looking to manage waste without significant upfront costs.
What Role Do Industrial Shredders Play in Waste Management?
Industrial shredders are crucial for preparing materials for baling, particularly when dealing with diverse waste streams. They efficiently reduce the size of various materials, making the baling process more effective. Buyers should consider the type of materials they need to shred and the volume they handle, as these factors influence the choice of shredder. While they offer versatility, the operational costs and space requirements may be higher, necessitating careful planning.
How Are Tire Shredders Specialized for Recycling Needs?
Tire shredders are specialized machines designed to process tires, breaking them down into smaller pieces suitable for recycling. This equipment is essential for businesses in the automotive industry, where tire disposal is a significant concern. Buyers should look into the energy consumption and maintenance requirements of tire shredders, as they can be high. However, the environmental benefits and compliance with waste management regulations make them a valuable investment for companies focused on sustainability.
Key Industrial Applications of baler machinery
Industry/Sector | Specific Application of baler machinery | Value/Benefit for the Business | Key Sourcing Considerations for this Application |
---|---|---|---|
Recycling and Waste Management | Cardboard Baling | Reduces waste volume, lowers transportation costs, and improves recycling efficiency. | Ensure baler capacity matches waste volume; consider space constraints. |
Textile Industry | Textile Baling | Streamlines waste handling, increases storage efficiency, and improves recycling rates. | Focus on the type of textiles; assess the need for manual vs. automatic balers. |
Agriculture | Straw and Hay Baling | Enhances storage efficiency, reduces spoilage, and simplifies transportation. | Evaluate the type of material and required bale size; consider local climate conditions. |
Manufacturing | Plastic Baling | Facilitates recycling processes, reduces landfill costs, and promotes sustainability. | Identify the specific type of plastic; ensure the baler’s specifications meet output needs. |
Automotive Industry | Tire Baling | Minimizes storage space, prepares tires for recycling, and supports environmental compliance. | Assess the baler’s capability to handle various tire sizes and types; consider the need for specialized equipment. |
How is Baler Machinery Used in Recycling and Waste Management?
In the recycling and waste management sector, baler machinery is primarily used for compressing cardboard, plastics, and other recyclables into manageable bales. This process not only reduces waste volume but also optimizes transportation logistics, leading to significant cost savings. International B2B buyers should consider the baler’s capacity to handle their specific waste volume and the available space for installation, especially in regions like Africa and South America where infrastructure may vary.
What Role Does Baler Machinery Play in the Textile Industry?
In the textile industry, baler machinery is utilized to compact used clothing and textile scraps into bales for recycling or resale. This application addresses the challenges of waste management by streamlining operations and improving storage efficiency. Buyers from the Middle East and Europe should focus on the type of textiles being baled and whether a manual or automatic baler is most suitable for their operational needs.
How is Baler Machinery Beneficial in Agriculture?
Agricultural operations use baler machinery to compress straw and hay, making it easier to store and transport these materials. This application not only enhances storage efficiency but also minimizes spoilage, which is crucial in regions with varying climates. Buyers in Africa and South America should evaluate the type of material being baled and the required bale size to ensure compatibility with their storage facilities.
Why is Baler Machinery Important for the Manufacturing Sector?
In manufacturing, baler machinery is essential for compacting plastic waste, which can significantly reduce landfill costs and promote sustainability. This application is increasingly vital as businesses face pressure to adopt eco-friendly practices. Buyers should identify the specific type of plastic they will be processing and ensure that the baler’s specifications align with their output requirements, particularly in Europe where regulatory standards may be stricter.
How Does Baler Machinery Support the Automotive Industry?
The automotive industry employs baler machinery to compress scrap tires, preparing them for recycling or proper disposal. This application reduces the amount of space required for tire storage and aids in meeting environmental compliance standards. Buyers should assess the baler’s capability to handle different tire sizes and types, ensuring that they choose a solution that meets their operational demands and sustainability goals.
3 Common User Pain Points for ‘baler machinery’ & Their Solutions
Scenario 1: Inadequate Baling Capacity for Growing Operations
The Problem:
As businesses scale, many B2B buyers discover that their existing baler machinery cannot keep up with increasing volumes of waste material. This often leads to bottlenecks in the recycling process, resulting in higher labor costs and increased waste disposal fees. For instance, a packaging company may find that its vertical baler can only handle a fraction of the cardboard waste generated during peak production periods, causing delays and inefficiencies. Such scenarios can lead to operational disruptions and reduced profitability.
The Solution:
To address this issue, buyers should assess their current and future baling needs carefully. Start by evaluating your production output and waste generation rates to determine the required baling capacity. When sourcing new balers, consider automatic horizontal balers that offer higher throughput and can process larger volumes of material continuously. These machines typically have a higher compression force and are designed for bulk processing, making them ideal for businesses anticipating growth. Additionally, consult with manufacturers to discuss customized options that can meet specific capacity requirements and integrate seamlessly into existing workflows.
Scenario 2: High Maintenance Costs and Downtime
The Problem:
Frequent breakdowns and high maintenance costs can plague B2B buyers of baler machinery. In industries like manufacturing and retail, where waste management is critical to operational efficiency, unexpected machine failures can lead to significant downtime. For example, a retailer using a baler for cardboard may experience delays in waste removal, leading to cluttered spaces and potential safety hazards. This not only affects productivity but can also increase operational costs, as repairs and downtime accumulate.
The Solution:
Investing in high-quality, durable baler machinery with robust warranty and service agreements can mitigate maintenance issues. Buyers should prioritize manufacturers known for reliability and excellent after-sales service. Additionally, implementing a regular maintenance schedule can help prevent unexpected breakdowns. This includes routine inspections, timely lubrication, and replacing worn parts before they fail. Consider investing in training for your staff on how to operate the machinery properly, as improper use is a common cause of breakdowns. Many manufacturers offer training sessions that can empower employees and ensure the baler operates at peak efficiency.
Scenario 3: Difficulty in Material Specification and Machine Selection
The Problem:
Many B2B buyers face challenges when selecting the right baler for their specific material types, leading to poor performance and inefficiencies. For instance, a company might purchase a baler intended for cardboard but later find it inadequate for handling plastic or mixed materials. This mismatch can result in suboptimal bale quality and increased operational costs as the machine struggles to perform effectively.
The Solution:
To avoid such pitfalls, buyers should engage in thorough research and consultation before making a purchase. Clearly define the types of materials to be baled and their specific characteristics, such as density and moisture content. Utilize tools and resources provided by manufacturers, such as an applications table, to match your material types with suitable baler models. Don’t hesitate to reach out to manufacturers for expert guidance—many offer tailored advice based on your unique requirements. Finally, consider the future versatility of the baler; selecting a machine that can handle multiple material types can provide greater flexibility as your business evolves.
Strategic Material Selection Guide for baler machinery
What Are the Key Materials Used in Baler Machinery?
When selecting baler machinery, the choice of materials is crucial for ensuring optimal performance, durability, and cost-effectiveness. Below, we analyze four common materials used in baler machinery—steel, aluminum, rubber, and plastics—focusing on their properties, advantages, disadvantages, and specific considerations for international B2B buyers.
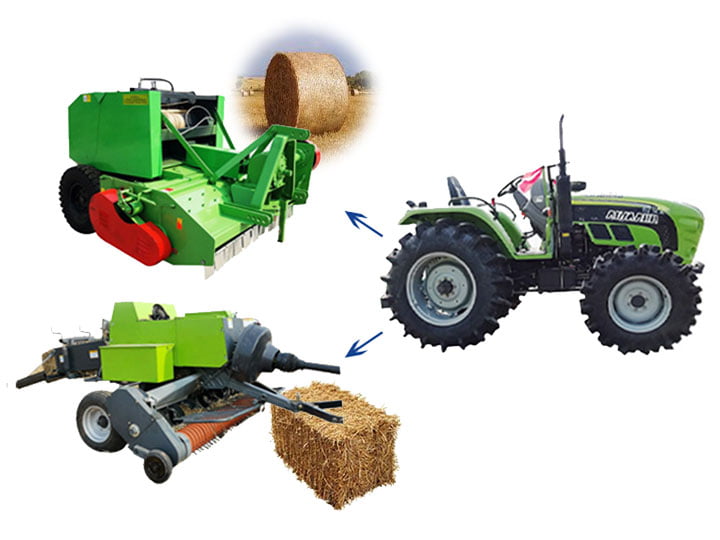
A stock image related to baler machinery.
How Does Steel Impact Baler Machinery Performance?
Key Properties: Steel is known for its high tensile strength and durability. It can withstand high pressures and temperatures, making it suitable for heavy-duty applications. Additionally, steel exhibits excellent corrosion resistance when treated with appropriate coatings.
Pros & Cons: The primary advantage of steel is its strength and longevity, which translates to lower maintenance costs over time. However, steel can be heavier and more expensive than alternative materials, potentially increasing shipping costs for international buyers. Manufacturing complexity can also be a factor, as steel components often require specialized machining.
Impact on Application: Steel is ideal for balers that handle heavy materials such as metals, cardboard, and plastics. Its robustness ensures that the machinery can operate under rigorous conditions without compromising performance.
Considerations for International Buyers: Buyers from regions like Africa and the Middle East should consider local steel standards and certifications, such as ASTM or EN standards, to ensure compliance. Additionally, understanding local supply chains for steel components can help mitigate costs.
What Role Does Aluminum Play in Baler Machinery?
Key Properties: Aluminum is lightweight yet strong, offering good corrosion resistance, especially when anodized. It has a lower melting point than steel, making it easier to work with in manufacturing.
Pros & Cons: The main advantage of aluminum is its weight, which can reduce transportation costs and facilitate easier installation. However, aluminum is generally less durable than steel, making it less suitable for extremely heavy loads. Its higher cost compared to steel can also be a drawback for budget-conscious buyers.
Impact on Application: Aluminum balers are often used in environments where weight is a concern, such as mobile balers or in facilities with limited space. They are particularly effective for baling lighter materials like cardboard and plastics.
Considerations for International Buyers: Buyers in Europe should be aware of the EU’s regulations regarding aluminum recycling and sustainability. Compliance with local environmental standards can enhance the marketability of the baler machinery.
How Do Rubber Components Enhance Baler Machinery?
Key Properties: Rubber is flexible and resilient, capable of absorbing shock and reducing vibrations. It is resistant to wear and tear, making it suitable for applications that involve frequent movement.
Pros & Cons: The flexibility of rubber allows for better sealing and cushioning in baler machinery, which can enhance performance and reduce noise. However, rubber components may degrade over time, especially when exposed to extreme temperatures or chemicals, leading to increased replacement costs.
Impact on Application: Rubber is commonly used in seals, gaskets, and rollers within balers. Its shock-absorbing properties make it ideal for handling delicate materials that require gentle processing.
Considerations for International Buyers: Buyers from South America and Africa should ensure that the rubber used meets local standards for durability and environmental impact. Understanding the local climate can also inform the selection of rubber grades that withstand specific conditions.
What Types of Plastics Are Used in Baler Machinery?
Key Properties: Plastics are lightweight and resistant to corrosion, making them suitable for various applications. They can be molded into complex shapes, allowing for versatile designs.
Pros & Cons: The main advantage of plastics is their cost-effectiveness and ease of manufacturing. However, they may not be as durable as metals, particularly under high-pressure conditions. Some plastics can also be sensitive to UV light and temperature variations.
Impact on Application: Plastics are often used in balers for components such as hoppers and covers, where weight reduction is beneficial. They are effective for baling materials like plastic films and lightweight cardboard.
Considerations for International Buyers: Buyers in the Middle East should consider the types of plastics used and their compliance with local recycling regulations. Understanding the end-of-life disposal options for plastic components is also essential for sustainability.
Summary Table of Material Selection for Baler Machinery
Material | Typical Use Case for baler machinery | Key Advantage | Key Disadvantage/Limitation | Relative Cost (Low/Med/High) |
---|---|---|---|---|
Steel | Heavy-duty baling of metals, cardboard, and plastics | High strength and durability | Heavier and more expensive | High |
Aluminum | Mobile balers for cardboard and plastics | Lightweight and corrosion-resistant | Less durable than steel | Medium |
Rubber | Seals, gaskets, and rollers | Flexible and shock-absorbing | Can degrade under extreme conditions | Low |
Plastics | Hoppers and covers for lightweight materials | Cost-effective and versatile | Less durable under high pressure | Low |
This comprehensive analysis provides B2B buyers with actionable insights into material selection for baler machinery, enabling informed decisions tailored to their specific operational needs and regional considerations.
In-depth Look: Manufacturing Processes and Quality Assurance for baler machinery
What Are the Main Stages of the Manufacturing Process for Baler Machinery?
The manufacturing process of baler machinery involves several critical stages, each designed to ensure that the final product meets the rigorous demands of efficiency and durability. Understanding these stages can help international B2B buyers make informed decisions when evaluating suppliers.
Material Preparation: How Are Raw Materials Selected and Processed?
The first step in the manufacturing of baler machinery is material preparation. Manufacturers typically use high-grade steel and other robust materials that can withstand the intense pressures involved in baling operations. The selection of materials often adheres to international standards to ensure strength and longevity.
- Cutting and Shaping: The raw materials are cut into specified dimensions using precision cutting tools. Techniques such as laser cutting and plasma cutting may be employed to achieve high accuracy.
- Surface Treatment: To enhance durability, materials undergo surface treatments such as galvanizing or powder coating. These processes protect against corrosion and wear, which are crucial for machines operating in harsh environments.
Which Key Techniques Are Used in the Forming and Assembly of Baler Machinery?
Once the materials are prepared, the next stage involves forming and assembly.
Forming Techniques: What Methods Are Commonly Used?
Various techniques are employed in forming the components of balers:
- Welding: This technique is pivotal in joining metal parts. Robotic welding systems are increasingly used for consistency and precision.
- Stamping: High-pressure stamping is often utilized to create complex shapes from metal sheets, allowing for lightweight yet strong components.
Assembly Process: How Are Components Brought Together?
The assembly process involves several steps to ensure that each component fits and functions correctly:
- Initial Assembly: Components such as hydraulic systems, frames, and control panels are initially assembled in a controlled environment.
- System Integration: The integration of hydraulic systems is a critical part of assembly. This includes testing the hydraulic lines for leaks and ensuring that all electronic components are wired correctly.
What Are the Finishing Techniques Applied to Baler Machinery?
Finishing touches are essential to enhance both aesthetics and functionality.
- Final Assembly: After all components are integrated, the baler undergoes a final assembly phase where additional parts, such as safety guards and controls, are installed.
- Quality Coating: A final coating may be applied to improve the machine’s resistance to environmental factors.
What International Standards Guide Quality Assurance for Baler Machinery?
Quality assurance is a vital aspect of the manufacturing process. International standards play a significant role in ensuring that baler machinery meets safety and performance criteria.
ISO 9001: What Does This Standard Entail?
ISO 9001 is an internationally recognized standard for quality management systems. Compliance with ISO 9001 ensures that manufacturers consistently provide products that meet customer and regulatory requirements.
- Documentation and Procedures: Manufacturers must maintain comprehensive documentation and adhere to established procedures, which can help B2B buyers assess a supplier’s commitment to quality.
What Industry-Specific Standards Are Relevant for Baler Machinery?
In addition to ISO standards, specific industry certifications can further assure buyers of a product’s quality:
- CE Marking: Required in Europe, CE marking indicates compliance with health, safety, and environmental protection standards.
- API Certification: For balers used in oil and gas applications, API certification may be necessary, ensuring that equipment meets industry-specific safety and performance standards.
What Are the Key Quality Control Checkpoints in Baler Machinery Manufacturing?
Effective quality control (QC) involves multiple checkpoints throughout the manufacturing process to ensure that every aspect of the baler meets quality standards.
Incoming Quality Control (IQC): How Are Raw Materials Inspected?
IQC is the first line of defense against defects. Raw materials are inspected upon arrival for compliance with specifications. This includes:
- Material Testing: Tests may include tensile strength assessments and chemical composition analysis.
- Supplier Audits: Regular audits of suppliers can ensure that they adhere to required standards, providing peace of mind to buyers.
In-Process Quality Control (IPQC): What Monitoring Techniques Are Employed?
During the manufacturing process, IPQC is crucial for identifying defects early.
- Visual Inspections: Operators conduct visual inspections at various stages of assembly to ensure components fit correctly.
- Functional Testing: Systems such as hydraulic presses are tested under load conditions to ensure they perform as expected.
Final Quality Control (FQC): What Tests Are Conducted Before Shipment?
Before balers are shipped to buyers, final quality control checks are conducted.
- Performance Testing: The completed baler undergoes a series of tests to ensure it meets specified operational parameters, such as compression force and cycle time.
- Safety Checks: All safety features are verified to ensure compliance with regulatory requirements.
How Can B2B Buyers Verify Supplier Quality Control Processes?
For international B2B buyers, verifying a supplier’s quality control processes is essential for mitigating risks.
What Auditing Practices Should Be Considered?
- Third-Party Inspections: Engaging third-party inspection services can provide an unbiased assessment of a supplier’s manufacturing processes.
- Quality Reports: Requesting detailed QC reports from suppliers can help assess their adherence to quality standards and identify any potential issues.
What Nuances Should International Buyers Be Aware of Regarding QC?
When sourcing baler machinery from different regions, buyers should be aware of specific nuances that may affect quality assurance:
- Cultural Differences: Understanding the cultural approach to quality can influence expectations and communication with suppliers.
- Regulatory Compliance: Familiarity with local regulations in the supplier’s country can help buyers ensure that they are compliant with both local and international standards.
By grasping the intricacies of the manufacturing processes and quality assurance measures, international B2B buyers can make informed decisions and ensure they procure reliable, high-quality baler machinery suitable for their operational needs.
Practical Sourcing Guide: A Step-by-Step Checklist for ‘baler machinery’
Introduction
This practical sourcing guide provides a step-by-step checklist for B2B buyers seeking to procure baler machinery. Understanding the complexities of baler machines and the market can significantly impact your operational efficiency and cost-effectiveness. This guide aims to streamline your sourcing process, ensuring you make informed decisions tailored to your specific needs.
Step 1: Define Your Technical Specifications
Before you begin sourcing baler machinery, it’s essential to clearly outline your technical requirements. Consider the type of materials you will be baling, such as cardboard, plastics, or textiles. Each material type may require different baling techniques and machine capabilities.
- Material Type: Identify whether you need a manual or automatic baler based on the volume and type of waste.
- Bale Size: Determine the dimensions and weight of the bales required for your storage and transportation needs.
Step 2: Assess Your Space and Installation Requirements
Understanding your facility’s layout is crucial to ensure the selected baler fits seamlessly into your operations. Measure the available space and consider ceiling height, especially if the baler has a high hopper.
- Space Planning: Ensure there is sufficient clearance for operation and maintenance.
- Access Points: Verify that the machine can be easily transported and installed without obstructing workflows.
Step 3: Evaluate Potential Suppliers
Selecting the right supplier is paramount. Conduct thorough research on potential manufacturers and their reputations in the market.
- Company Background: Look for companies with a proven track record in the baler industry, especially those with experience in your region.
- Customer Reviews: Seek testimonials and case studies from previous clients to gauge satisfaction and reliability.
Step 4: Request Detailed Quotations
Once you’ve narrowed down your list of suppliers, request detailed quotations that outline costs, specifications, and service agreements.
- Cost Breakdown: Ensure the quote includes all potential costs, such as delivery, installation, and after-sales support.
- Warranty and Support: Understand the warranty terms and the level of technical support provided post-purchase.
Step 5: Verify Compliance and Certifications
It’s vital to confirm that the baler machinery complies with industry standards and regulations applicable in your region.
- Safety Standards: Check for certifications such as CE marking in Europe or ISO standards that ensure quality and safety.
- Environmental Compliance: Ensure that the machine meets local environmental regulations, especially if it involves waste management.
Step 6: Plan for After-Sales Service and Maintenance
Consider the after-sales service offered by the supplier, as this can impact the longevity and performance of your baler machinery.
- Service Agreements: Look for suppliers who provide comprehensive service contracts covering maintenance and repair.
- Availability of Parts: Ensure that spare parts are readily available to minimize downtime in case of repairs.
Step 7: Finalize the Purchase and Arrange for Training
After selecting a supplier and finalizing the contract, arrange for operator training to ensure efficient use of the baler machinery.
- Training Programs: Many suppliers offer training sessions to familiarize your staff with the equipment.
- Operational Guidelines: Request detailed manuals and operational guidelines to enhance safety and productivity.
By following this checklist, you can navigate the procurement process of baler machinery more effectively, ensuring you select the right equipment for your operational needs.
Comprehensive Cost and Pricing Analysis for baler machinery Sourcing
What Are the Key Cost Components in Baler Machinery Sourcing?
When sourcing baler machinery, understanding the cost structure is crucial for international B2B buyers. The primary components of the cost include:
-
Materials: The choice of materials significantly impacts the overall cost. High-quality steel, hydraulic components, and electronic parts will increase upfront costs but may offer durability and lower maintenance expenses over time.
-
Labor: Labor costs vary by region and the complexity of the manufacturing process. Countries with lower labor costs can provide competitive pricing but may compromise on quality.
-
Manufacturing Overhead: This includes utilities, rent, and administrative expenses associated with production. Efficient manufacturers will have lower overhead, which can reflect in pricing.
-
Tooling: Custom tooling for specific baler designs can be a significant one-time expense. This cost is often amortized over the production run but should be considered in the pricing discussion.
-
Quality Control (QC): Investing in rigorous QC processes can increase costs but ensures that the balers meet international standards, which is especially important for buyers in markets with stringent regulations.
-
Logistics: Shipping costs can vary widely based on the distance, mode of transport, and Incoterms. Understanding these factors is essential for budgeting accurately.
-
Margin: Manufacturers typically add a margin to cover their costs and ensure profitability. Buyers should be aware that this margin can vary between suppliers.
What Influences the Pricing of Baler Machinery?
Several factors influence the pricing of baler machinery, including:
-
Volume and Minimum Order Quantity (MOQ): Higher order volumes often lead to reduced unit costs. Buyers should negotiate MOQs to optimize pricing, especially when sourcing from manufacturers in different regions.
-
Specifications and Customization: Customized balers designed for specific materials or processes can increase costs. Buyers should weigh the need for customization against potential cost savings from standard models.
-
Material Quality and Certifications: Balers made from premium materials and those with relevant certifications (e.g., ISO) may command higher prices. However, they can lead to lower Total Cost of Ownership (TCO) due to enhanced durability and performance.
-
Supplier Factors: The reputation and experience of the supplier can influence pricing. Established manufacturers may charge more due to their proven track record and reliability.
-
Incoterms: The choice of Incoterms affects the total landed cost. Buyers should carefully consider terms like FOB (Free On Board) versus CIF (Cost, Insurance, and Freight) to understand their responsibilities and costs.
How Can International Buyers Negotiate for Better Pricing?
Negotiation is a critical skill for international B2B buyers. Here are some actionable tips:
-
Research Market Rates: Understanding average market prices can provide leverage during negotiations. Buyers should gather quotes from multiple suppliers for comparison.
-
Leverage Long-Term Relationships: Building strong relationships with suppliers can lead to better pricing and terms. Loyalty often translates into favorable negotiations.
-
Consider Total Cost of Ownership (TCO): Instead of focusing solely on upfront costs, buyers should evaluate TCO, which includes maintenance, operational efficiency, and potential resale value.
-
Be Aware of Currency Fluctuations: For buyers in Africa, South America, the Middle East, and Europe, currency fluctuations can impact pricing. Locking in prices or negotiating in stable currencies can mitigate risks.
What Are the Pricing Nuances for B2B Buyers in Different Regions?
International buyers should be aware of regional pricing nuances. For instance, buyers in Africa may encounter higher shipping costs due to limited infrastructure. In contrast, European buyers might benefit from proximity to manufacturers, reducing logistics expenses.
Additionally, understanding local regulations and import duties is essential for accurate cost estimation. Buyers should also be prepared for potential tariffs, especially when sourcing from countries with trade restrictions.
Conclusion
While sourcing baler machinery, it is essential to consider various cost components, pricing influencers, and negotiation strategies. By understanding these elements, international B2B buyers can make informed decisions that align with their operational needs and budget constraints. Always keep in mind that indicative prices may vary based on specific requirements and market conditions, so thorough research and strategic negotiation are vital.
Alternatives Analysis: Comparing baler machinery With Other Solutions
Introduction to Alternative Waste Management Solutions
In the realm of waste management and recycling, baler machinery is a popular choice for compacting materials into manageable bales. However, several alternative solutions exist that can also effectively handle waste reduction and recycling processes. Understanding these alternatives allows international B2B buyers, particularly those from Africa, South America, the Middle East, and Europe, to make informed decisions tailored to their specific operational needs.
Comparison Table of Baler Machinery vs. Alternative Solutions
Comparison Aspect | Baler Machinery | Trash Compactors | Industrial Shredders |
---|---|---|---|
Performance | High-density bales for storage | Reduces volume significantly | Shreds materials into smaller pieces |
Cost | Moderate initial investment | Lower cost, but may require more energy | High initial cost and maintenance |
Ease of Implementation | Requires space and setup | Generally easier to integrate | May require specialized installation |
Maintenance | Regular maintenance needed | Low maintenance | High maintenance due to wear and tear |
Best Use Case | Recycling cardboard, plastics, textiles | General waste reduction | Preparing materials for recycling or disposal |
What are the Pros and Cons of Trash Compactors?
Trash compactors serve as a viable alternative to balers, particularly for general waste management. They utilize hydraulic or mechanical force to compress various types of waste into dense blocks, which can be easier to handle and transport.
Pros:
– Cost-Effective: Generally, trash compactors have a lower initial cost compared to balers, making them accessible for businesses with budget constraints.
– Space Efficiency: They require less space than balers, making them suitable for facilities with limited room.
Cons:
– Limited Material Types: Trash compactors are not as effective for specialized materials such as cardboard or textiles, which benefit more from baling.
– Energy Consumption: They may consume more energy due to continuous operation, which can lead to higher operational costs over time.
How Do Industrial Shredders Compare as an Alternative?
Industrial shredders are designed to reduce materials into smaller sizes, making them another alternative worth considering. They can handle a wide range of materials, including plastics, metals, and paper.
Pros:
– Versatility: Shredders can process various materials, making them adaptable to different recycling needs.
– Preparation for Recycling: By shredding materials, they facilitate further processing, such as granulation for plastics or metal recycling.
Cons:
– Higher Cost: The initial investment and ongoing maintenance can be significant, especially for heavy-duty models.
– Operational Complexity: Shredders may require more technical expertise for operation and maintenance compared to balers or compactors.
Conclusion: How Can B2B Buyers Choose the Right Solution?
When selecting the right waste management solution, B2B buyers should evaluate their specific needs, including the types of materials they handle, available space, budget constraints, and operational capabilities. Balers are ideal for businesses focusing on recycling specific materials like cardboard and textiles, while trash compactors may be better suited for general waste reduction. Industrial shredders offer versatility for various materials but come with higher costs and maintenance demands. By weighing these factors, buyers can make informed decisions that align with their waste management strategies and contribute to sustainable practices.
Essential Technical Properties and Trade Terminology for baler machinery
What Are the Essential Technical Properties of Baler Machinery?
When selecting baler machinery, understanding its technical properties is crucial for ensuring optimal performance and suitability for specific applications. Here are some key specifications that international B2B buyers should consider:
1. Pressure Force
Pressure force is the amount of hydraulic pressure applied by the baler to compress materials into bales. It is typically measured in tons and can range from 20 tons to over 120 tons in heavy-duty models. Selecting the right pressure force is essential because it determines the machine’s capability to handle different materials effectively. For instance, baling cardboard may require less force than baling metal scraps.
2. Bale Size and Weight
Bale size refers to the dimensions of the compressed material, while weight indicates how much the bale weighs. Common bale sizes for cardboard and plastics are often standardized to facilitate transport and storage. Understanding the required bale size and weight is vital for logistics and processing; oversized bales may not fit in containers or storage areas, leading to increased costs and inefficiencies.
3. Cycle Time
Cycle time is the duration it takes for a baler to complete a full baling cycle, including loading, compressing, and ejection of the bale. Faster cycle times improve productivity, particularly in high-volume operations. Buyers should evaluate their processing needs to select a baler that meets their operational speed requirements without compromising on quality.
4. Material Compatibility
Different balers are designed to handle specific types of materials such as cardboard, plastics, or metals. Compatibility with the material type is crucial for achieving maximum efficiency and output. For example, a baler designed for plastic may not perform well with textiles. Buyers must clearly define the types of materials they will be processing to choose the appropriate machine.
5. Power Source
Baler machines can be powered by electricity, diesel, or hydraulics. The choice of power source can affect operational costs, maintenance needs, and overall machine performance. For instance, electric balers are often more energy-efficient and suitable for indoor environments, while diesel-powered machines may be preferred for remote locations. Understanding the power requirements is essential for aligning with operational capabilities and infrastructure.
What Are Common Trade Terms in Baler Machinery?
Familiarity with industry-specific terminology can facilitate smoother negotiations and transactions. Here are some essential trade terms relevant to baler machinery:
1. OEM (Original Equipment Manufacturer)
OEM refers to companies that produce parts or equipment that may be marketed by another manufacturer. For baler machinery, working with OEMs ensures that buyers receive high-quality, standardized components that meet industry specifications. This is particularly important for parts replacement and service.
2. MOQ (Minimum Order Quantity)
MOQ is the smallest quantity of a product that a supplier is willing to sell. Understanding MOQ is essential for budgeting and inventory management. Buyers should negotiate MOQs with suppliers to ensure they can meet their operational needs without overcommitting financially.
3. RFQ (Request for Quotation)
An RFQ is a document that buyers send to suppliers to request pricing and terms for specific products or services. An effective RFQ should clearly outline the technical specifications and quantities needed for baler machinery. This process helps buyers compare offers and make informed purchasing decisions.
4. Incoterms (International Commercial Terms)
Incoterms are a set of predefined international trade terms that clarify the responsibilities of buyers and sellers in shipping goods. Understanding Incoterms is vital for international transactions, as they dictate who is responsible for costs such as shipping, insurance, and tariffs. This knowledge helps prevent misunderstandings and disputes in cross-border trade.
5. After-sales Service
This term refers to the support provided by a manufacturer after a sale is completed. For baler machinery, after-sales service can include installation, maintenance, and repairs. Ensuring that a supplier offers reliable after-sales service is crucial for minimizing downtime and maintaining operational efficiency.
By understanding these technical properties and trade terminology, B2B buyers can make more informed decisions when investing in baler machinery, ensuring they select the right equipment for their specific needs.
Navigating Market Dynamics and Sourcing Trends in the baler machinery Sector
What Are the Current Market Dynamics and Key Trends in the Baler Machinery Sector?
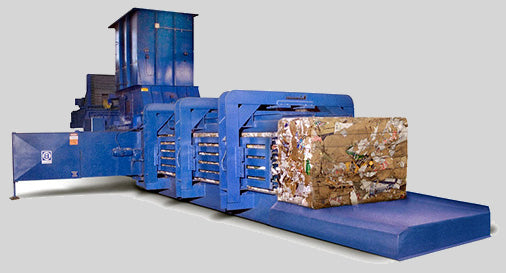
A stock image related to baler machinery.
The global baler machinery market is experiencing notable growth driven by the increasing need for efficient waste management and recycling solutions. Key trends include the adoption of automation and smart technology, which enhance operational efficiency and reduce labor costs. International B2B buyers are particularly interested in fully automatic balers that can handle high volumes of materials, such as cardboard, plastics, and metals, while maintaining consistent output quality.
In regions like Africa and South America, where waste management infrastructure is still developing, there is a rising demand for cost-effective and robust baling solutions. Buyers in the Middle East are focusing on advanced machinery that aligns with their sustainability goals and regulatory requirements. European buyers, particularly in the UK and Germany, are seeking machines that not only comply with stringent environmental standards but also offer innovative features such as energy efficiency and ease of maintenance.
Moreover, the growing emphasis on circular economy practices is pushing businesses to invest in balers that facilitate recycling and waste reduction, thus creating new revenue streams. The integration of Internet of Things (IoT) technologies into balers allows for real-time monitoring and predictive maintenance, which are becoming increasingly important for buyers looking to optimize their operations.
How Important Is Sustainability and Ethical Sourcing in the Baler Machinery Market?
Sustainability has become a crucial factor for B2B buyers in the baler machinery sector. The environmental impact of machinery production and operation is under scrutiny, prompting buyers to seek manufacturers that prioritize eco-friendly practices. This includes the use of sustainable materials in production and energy-efficient designs that minimize carbon footprints.
Ethical sourcing is equally important, as buyers want assurance that their equipment is produced in compliance with labor and environmental standards. Certifications such as ISO 14001 (Environmental Management) and ISO 9001 (Quality Management) are indicators of a manufacturer’s commitment to sustainability and ethical practices.
Additionally, the demand for “green” balers that use recycled or recyclable materials is on the rise. Buyers are increasingly looking for machinery that contributes to their overall sustainability goals, such as reducing waste generation and improving recycling rates. By aligning with suppliers that uphold high ethical and environmental standards, companies can enhance their corporate social responsibility (CSR) profiles and appeal to environmentally-conscious consumers.
What Is the Brief Evolution of Baler Machinery and Its Significance for B2B Buyers?
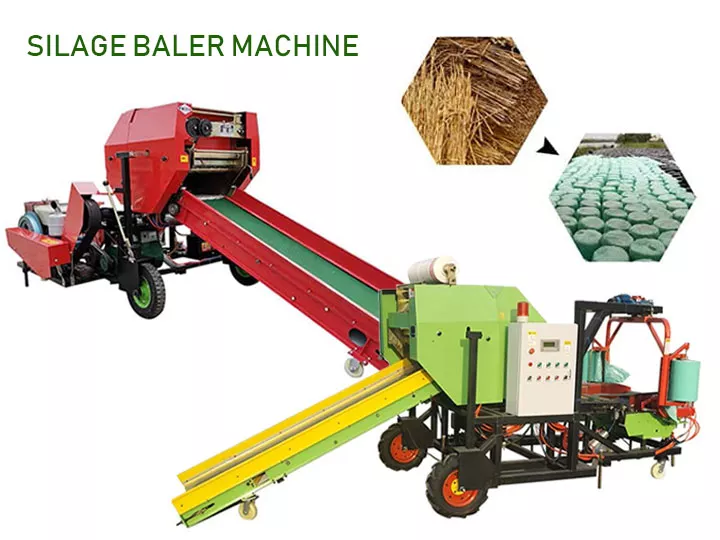
A stock image related to baler machinery.
The evolution of baler machinery dates back to the mid-19th century when hay presses were first developed to streamline agricultural processes. These early machines laid the groundwork for modern balers, which have since diversified into various types designed for specific materials, including cardboard, plastics, and metals.
As waste management practices evolved, so did baler technology, incorporating advancements such as hydraulic presses, automation, and sophisticated control systems. This evolution is significant for B2B buyers, as it reflects the industry’s responsiveness to changing market demands and environmental regulations. Understanding this history allows buyers to appreciate the technological advancements that improve efficiency and sustainability in waste management solutions today.
In summary, the baler machinery sector is shaped by evolving market dynamics, a strong emphasis on sustainability, and a rich history of technological innovation. International B2B buyers must stay informed about these trends to make strategic sourcing decisions that align with their operational goals and sustainability initiatives.
Frequently Asked Questions (FAQs) for B2B Buyers of baler machinery
-
How do I choose the right baler machine for my business needs?
Selecting the right baler machine begins with understanding your material type, such as cardboard, plastics, or metals. Assess the volume of material you handle daily and the desired bale size, which will affect your storage and transportation strategies. Additionally, consider the space available in your facility, including ceiling height for taller machines. Consulting with manufacturers can provide tailored recommendations based on your specific requirements, ensuring you invest in a machine that maximizes efficiency and productivity. -
What are the key features to look for in a baler machine?
When evaluating baler machines, prioritize features like pressure capacity, bale size options, and automation level. Hydraulic efficiency is crucial for compacting materials effectively. Look for machines with robust construction and high-quality components for durability. Safety features such as emergency stops and protective guards are also essential. Additionally, consider the machine’s ease of maintenance, availability of spare parts, and manufacturer support to ensure long-term operational efficiency. -
What are the typical payment terms when purchasing baler machinery internationally?
Payment terms can vary significantly between suppliers, especially in international transactions. Common arrangements include a percentage upfront (usually 30-50%) with the balance due upon delivery or after installation. Letters of credit and escrow services can provide additional security for both parties. It’s advisable to clarify payment methods, currency, and any potential import duties or taxes that could affect the total cost when negotiating with suppliers. -
How can I vet a baler machinery supplier effectively?
To vet a baler machinery supplier, start by researching their industry reputation through customer reviews and testimonials. Request references from previous clients and assess the supplier’s experience with your specific material types. Verify their certifications, quality assurance processes, and compliance with international standards. Engaging with suppliers in trade shows or industry events can also provide insight into their offerings and reliability. Finally, consider visiting their manufacturing facility if possible to evaluate their production capabilities firsthand. -
What is the minimum order quantity (MOQ) for baler machines?
Minimum order quantities for baler machines can vary widely depending on the manufacturer and the type of machinery required. While some manufacturers may offer single units, others might set a MOQ to ensure production efficiency and cost-effectiveness. It’s essential to discuss your specific needs with potential suppliers to understand their MOQ policies and explore options for customization or bulk orders that may lower your overall costs. -
How do I ensure quality assurance for imported baler machines?
To ensure quality assurance for imported baler machines, request detailed product specifications and certifications from the manufacturer. Conduct pre-shipment inspections, if possible, to verify that the machine meets your standards. Additionally, consider working with third-party quality control firms that can conduct inspections on your behalf. Establish clear warranty terms and after-sales support agreements to address any issues that may arise post-purchase. -
What logistics considerations should I keep in mind when importing baler machinery?
When importing baler machinery, it’s crucial to consider shipping methods, delivery timelines, and customs clearance processes. Engage a logistics provider experienced in handling heavy machinery to navigate international shipping regulations effectively. Prepare all necessary documentation, including bills of lading, commercial invoices, and import permits, to ensure smooth customs processing. Additionally, account for potential delays and costs associated with transportation and storage upon arrival. -
What are the common applications for baler machines in different industries?
Baler machines are widely used across various industries, including recycling, agriculture, and manufacturing. Common applications include compacting cardboard, plastics, and textiles for recycling, as well as processing agricultural waste like straw and hay. In manufacturing, balers help manage waste materials efficiently, reducing disposal costs. Understanding your specific industry needs will help you select a baler that optimally fits your operational requirements and contributes to sustainability efforts.
Important Disclaimer & Terms of Use
⚠️ Important Disclaimer
The information provided in this guide, including content regarding manufacturers, technical specifications, and market analysis, is for informational and educational purposes only. It does not constitute professional procurement advice, financial advice, or legal advice.
While we have made every effort to ensure the accuracy and timeliness of the information, we are not responsible for any errors, omissions, or outdated information. Market conditions, company details, and technical standards are subject to change.
B2B buyers must conduct their own independent and thorough due diligence before making any purchasing decisions. This includes contacting suppliers directly, verifying certifications, requesting samples, and seeking professional consultation. The risk of relying on any information in this guide is borne solely by the reader.
Strategic Sourcing Conclusion and Outlook for baler machinery
What Are the Key Takeaways for International B2B Buyers of Baler Machinery?
In the competitive landscape of baler machinery, strategic sourcing remains crucial for international B2B buyers, particularly from Africa, South America, the Middle East, and Europe. Understanding the diverse types of balers—such as vertical, horizontal, and automatic models—enables buyers to select machinery that aligns with their specific waste management needs. Buyers must consider factors such as material type, bale size, output capacity, and available space to optimize their investment.
How Can Strategic Sourcing Enhance Waste Management Efforts?
Investing in high-quality balers not only improves operational efficiency but also significantly reduces waste disposal costs. The integration of advanced technologies in baling equipment enhances productivity and sustainability, ultimately contributing to a company’s bottom line. Moreover, sourcing from reputable manufacturers ensures long-term reliability and support, which are essential for maintaining operational continuity.
What’s Next for B2B Buyers in the Baler Machinery Market?
As the global focus on sustainability intensifies, the demand for efficient waste management solutions will continue to rise. Buyers are encouraged to leverage digital platforms to explore a wide range of options and connect with experienced suppliers. By prioritizing strategic sourcing, businesses can position themselves for success in an evolving marketplace. Embrace the opportunity to enhance your waste management strategy today—invest in baler machinery that meets your operational needs and supports your sustainability goals.