Discover Cost Savings with AGV Forklift Solutions (2025)
Introduction: Navigating the Global Market for agv forklift
In today’s fast-paced global market, sourcing an Automated Guided Vehicle (AGV) forklift can be a daunting challenge for international B2B buyers. As operations become increasingly complex, companies in Africa, South America, the Middle East, and Europe are turning to AGV forklifts to streamline logistics and enhance productivity. This guide provides a comprehensive overview of the various types of AGV forklifts available, their applications across diverse industries, and the critical factors to consider when selecting a supplier.
Navigating the AGV forklift market requires a strategic approach to supplier vetting, understanding cost structures, and assessing technological capabilities. Whether you are looking to reduce labor costs, minimize product damage, or enhance operational efficiency, this guide will empower you to make informed purchasing decisions. We will delve into the benefits of integrating AGV forklifts into your logistics framework, explore the latest advancements in automation technology, and provide actionable insights tailored to the unique needs of businesses in your region.
By equipping you with the knowledge to navigate this evolving landscape, we aim to help you leverage AGV forklifts effectively, ensuring that your investment translates into tangible returns and sustainable operational improvements.
Understanding agv forklift Types and Variations
Type Name | Key Distinguishing Features | Primary B2B Applications | Brief Pros & Cons for Buyers |
---|---|---|---|
Counterbalance AGV | Equipped with counterbalance weights for stability; can lift and transport heavy loads. | Warehousing, manufacturing, heavy-duty applications. | Pros: High load capacity; versatile. Cons: Larger footprint; may require more space. |
Reach Truck AGV | Features extendable forks to handle loads in narrow aisles; optimized for vertical lifting. | High-density storage, retail environments. | Pros: Maximizes vertical space; efficient in tight spaces. Cons: Limited to specific aisle widths. |
Tugger AGV | Designed to pull multiple trailers or carts; often used in assembly lines and distribution. | Automotive, manufacturing, distribution centers. | Pros: Increases material transport efficiency; reduces manual labor. Cons: Requires careful planning of routes. |
Pallet Jack AGV | Low-profile design for moving pallets; typically operates in conjunction with other AGVs. | General warehousing, retail stock management. | Pros: Cost-effective; easy to integrate. Cons: Limited lifting capability; not suited for heavy loads. |
Mini Load AGV | Compact design for transporting small items; often used with automated storage systems. | E-commerce, small parts manufacturing. | Pros: Space-efficient; ideal for small item handling. Cons: Limited load capacity; not suitable for larger items. |
What Are the Characteristics and Suitability of Counterbalance AGVs?
Counterbalance AGVs are designed with stability in mind, utilizing counterweights to balance heavy loads effectively. They excel in environments where heavy lifting is required, such as manufacturing plants and large warehouses. When considering a counterbalance AGV, B2B buyers should evaluate their load requirements and floor space, as these vehicles can have a larger footprint compared to other types. Additionally, their versatility in handling various load types makes them a reliable choice for diverse applications.
How Do Reach Truck AGVs Optimize Warehouse Space?
Reach truck AGVs are characterized by their extendable forks, which allow operators to lift loads to great heights, making them ideal for high-density storage environments. These AGVs are particularly suitable for retail operations and warehouses where vertical space is maximized. B2B buyers should consider aisle width and height restrictions when selecting a reach truck AGV, as their efficiency is contingent upon the operational layout. Their ability to navigate narrow aisles while maximizing storage capacity makes them a preferred option for many businesses.
Why Are Tugger AGVs Beneficial in Manufacturing and Distribution?
Tugger AGVs are specifically designed for moving multiple trailers or carts, making them indispensable in assembly lines and distribution centers. They enhance operational efficiency by automating the transport of materials across different areas of a facility. When purchasing a tugger AGV, B2B buyers should assess their material flow processes to ensure optimal route planning and integration with existing systems. The ability to reduce manual labor and streamline logistics processes is a significant advantage for companies looking to enhance productivity.
What Makes Pallet Jack AGVs a Cost-Effective Solution?
Pallet jack AGVs are low-profile vehicles designed primarily for moving pallets and are often used in conjunction with other automated systems. Their cost-effectiveness and ease of integration make them an attractive choice for businesses looking to automate their warehouse operations without significant investment. B2B buyers should consider the weight and size of the pallets being handled, as well as the overall layout of the warehouse. While they may not lift as much as other AGVs, their functionality in general warehousing applications is valuable.
How Do Mini Load AGVs Facilitate Small Item Handling?
Mini load AGVs are compact vehicles designed for transporting small items, often within automated storage systems. They are ideal for industries such as e-commerce and small parts manufacturing, where space is at a premium. B2B buyers should focus on the load capacity and dimensions of the items being handled when considering mini load AGVs, as their effectiveness is dependent on the nature of the inventory. Their space-efficient design and ability to operate in tight areas make them a practical solution for businesses managing smaller products.
Key Industrial Applications of agv forklift
Industry/Sector | Specific Application of AGV Forklift | Value/Benefit for the Business | Key Sourcing Considerations for this Application |
---|---|---|---|
Manufacturing | Automated assembly line material transport | Increases efficiency and reduces labor costs | Compatibility with existing systems, load capacity |
Warehousing and Distribution | Inventory management and order fulfillment | Enhances accuracy and speed of order processing | Navigation technology, software integration capabilities |
Retail | Stock replenishment and goods movement | Improves stock availability and reduces downtime | Flexibility in design, ease of operation |
Food and Beverage | Transporting raw materials and finished products | Ensures compliance with hygiene standards and efficiency | Temperature control features, safety certifications |
Pharmaceuticals | Handling sensitive materials and products | Minimizes risk of contamination and improves traceability | Regulatory compliance, specialized handling capabilities |
How is AGV Forklift Used in Manufacturing?
In the manufacturing sector, AGV forklifts are employed for automating the transport of materials along assembly lines. This application addresses the challenge of labor shortages and the need for increased production rates. By utilizing AGVs, manufacturers can streamline operations, reduce human error, and enhance workplace safety. International buyers should consider the compatibility of AGVs with existing production equipment and their load capacity to meet specific operational needs.
What Role Does AGV Forklift Play in Warehousing and Distribution?
AGV forklifts are pivotal in warehousing and distribution for inventory management and order fulfillment processes. They facilitate the automated movement of goods from storage to picking areas, significantly enhancing the accuracy and speed of order processing. This application is particularly advantageous for businesses aiming to meet high customer expectations in fast-paced environments. Buyers should evaluate navigation technologies and software integration capabilities to ensure seamless operation within their existing systems.
How Can AGV Forklift Improve Retail Operations?
In retail environments, AGV forklifts assist in stock replenishment and the movement of goods to sales floors. This application helps retailers maintain optimal stock levels, thereby improving product availability and reducing downtime. For international buyers, sourcing AGVs that offer flexibility in design and ease of operation is crucial, as retail environments can vary significantly in layout and operational demands.
What Are the Benefits of AGV Forklift in the Food and Beverage Industry?
AGV forklifts are utilized in the food and beverage industry to transport raw materials and finished products while adhering to strict hygiene standards. This application not only boosts operational efficiency but also ensures compliance with health regulations. Buyers in this sector should prioritize AGVs with temperature control features and safety certifications to protect sensitive products and maintain quality throughout the supply chain.
How Do AGV Forklifts Support the Pharmaceutical Sector?
In the pharmaceutical industry, AGV forklifts handle sensitive materials and products, minimizing the risk of contamination and enhancing traceability. This application is vital for maintaining compliance with stringent regulatory requirements. International buyers should focus on sourcing AGVs that meet regulatory standards and possess specialized handling capabilities to ensure the safe transport of pharmaceutical products.
3 Common User Pain Points for ‘agv forklift’ & Their Solutions
Scenario 1: Inconsistent Operational Efficiency Due to Manual Handling
The Problem:
Many B2B buyers in industries such as manufacturing and warehousing face significant challenges with operational efficiency when relying on manual material handling. In environments where high throughput and accuracy are critical, the presence of human error can lead to delays, misplacements, and increased operational costs. For instance, in a South African warehouse, workers may spend excessive time transporting goods, resulting in bottlenecks that disrupt the supply chain and affect customer satisfaction.
The Solution:
To combat these inefficiencies, investing in Automated Guided Vehicles (AGVs) can streamline operations. Buyers should begin by assessing their specific workflow requirements and identifying repetitive tasks that could benefit from automation. When sourcing AGVs, look for models that offer flexibility in navigation—such as those using advanced laser or magnetic technologies, which can adapt to changing layouts. Collaborating with a reliable supplier who provides comprehensive support, including installation and training, will ensure a smooth transition. Additionally, integrating AGVs with existing warehouse management systems can enhance tracking and coordination, ultimately improving throughput and reducing operational costs.
Scenario 2: High Initial Investment and ROI Concerns
The Problem:
International buyers, especially in emerging markets like South America, often grapple with the high initial costs associated with implementing AGV technology. The perception of AGVs as a luxury rather than a necessity can hinder investment, especially when stakeholders question the potential return on investment (ROI). This concern is particularly acute in industries with tight margins, where every dollar counts, making buyers hesitant to adopt what they may view as an expensive solution.
The Solution:
To alleviate these concerns, buyers should conduct a thorough cost-benefit analysis that incorporates not just the upfront costs but also long-term savings and productivity gains. Engaging with AGV manufacturers to understand the total cost of ownership (TCO) is vital. Look for AGVs that offer energy-efficient technologies, reducing operational costs over time. Additionally, buyers can explore financing options or leasing agreements that spread out the initial investment. Case studies from similar industries can also provide compelling evidence of ROI, showcasing how other companies have successfully implemented AGVs to enhance productivity while lowering labor costs.
Scenario 3: Safety and Compliance Challenges in Warehouse Operations
The Problem:
Safety remains a paramount concern for B2B buyers operating in warehouses and distribution centers, particularly in regions such as the Middle East, where regulatory compliance is strict. The integration of AGVs introduces new safety protocols and training requirements. Buyers may worry about the potential for accidents during the transition phase, especially when human workers and AGVs share the same space.
The Solution:
To address safety concerns, buyers should prioritize selecting AGVs equipped with advanced safety features such as obstacle detection and emergency stop mechanisms. Before implementation, it’s essential to conduct a thorough risk assessment of the workspace. Buyers should involve their workforce in training sessions focused on AGV operation and safety protocols to foster an environment of collaboration rather than competition between human workers and machines. Additionally, implementing a phased rollout of AGVs can help mitigate risks, allowing teams to adjust to the technology gradually while ensuring compliance with local safety regulations. Regular maintenance and software updates for AGVs will also enhance operational safety and reliability, ultimately creating a safer workplace for all employees.
Strategic Material Selection Guide for agv forklift
When selecting materials for Automated Guided Vehicle (AGV) forklifts, international B2B buyers must consider properties that affect performance, durability, and cost-effectiveness. Here, we analyze four common materials used in AGV forklifts: steel, aluminum, plastic composites, and rubber. Each material presents unique properties, advantages, and considerations that can influence purchasing decisions.
What Are the Key Properties of Steel in AGV Forklifts?
Steel is a widely used material in the construction of AGV forklifts due to its high strength and durability. It typically has excellent temperature and pressure ratings, making it suitable for heavy-duty applications. Steel’s corrosion resistance can be enhanced through galvanization or powder coating, which is crucial for operations in humid or corrosive environments.
Pros and Cons of Steel:
– Pros: High durability, excellent load-bearing capacity, and good resistance to wear and tear.
– Cons: Heavier than other materials, which can reduce energy efficiency; potential for rust if not treated properly.
Impact on Application:
Steel is ideal for environments where heavy loads are common, such as warehouses or manufacturing facilities. However, its weight may limit agility in smaller spaces.
Considerations for International Buyers:
Buyers must ensure compliance with international standards such as ASTM and DIN for material quality. In regions like South Africa and Saudi Arabia, understanding local regulations on material sourcing and environmental impact is essential.
How Does Aluminum Benefit AGV Forklifts?
Aluminum is another popular choice for AGV forklifts, known for its lightweight nature and resistance to corrosion. This material is particularly advantageous in applications requiring frequent movement and agility.
Pros and Cons of Aluminum:
– Pros: Lightweight, good corrosion resistance, and ease of fabrication.
– Cons: Lower strength compared to steel, which may limit load capacity.
Impact on Application:
Aluminum is suitable for AGVs operating in environments where speed and maneuverability are prioritized, such as retail or smaller warehouses.
Considerations for International Buyers:
Buyers should consider the cost of aluminum, which can be higher than steel. Compliance with international standards related to aluminum alloys is crucial, particularly in Europe, where strict regulations may apply.
What Role Do Plastic Composites Play in AGV Forklifts?
Plastic composites are increasingly being used in AGV forklifts due to their versatility and resistance to various chemicals. These materials can be engineered to provide specific properties, such as impact resistance and lightweight characteristics.
Pros and Cons of Plastic Composites:
– Pros: Lightweight, resistant to corrosion and chemicals, and customizable properties.
– Cons: Generally less durable than metals and may have a higher initial cost.
Impact on Application:
Plastic composites are ideal for environments where exposure to corrosive substances is a concern, such as in food processing or chemical handling.
Considerations for International Buyers:
Buyers should verify compliance with food safety standards (if applicable) and consider the recyclability of plastic composites, which is increasingly important in Europe and other regions focused on sustainability.
Why Is Rubber Important for AGV Forklifts?
Rubber is primarily used in the tires and wheels of AGV forklifts. Its properties provide excellent traction and shock absorption, essential for smooth operation on various surfaces.
Pros and Cons of Rubber:
– Pros: Good traction, shock-absorbing qualities, and resistance to wear.
– Cons: Limited lifespan compared to metal components and can degrade under extreme conditions.
Impact on Application:
Rubber is critical for AGVs operating on uneven or hard surfaces, where stability and control are necessary.
Considerations for International Buyers:
Buyers should consider local climate conditions that may affect rubber durability, as well as compliance with safety standards related to materials used in warehouse environments.
Summary Table of Material Selection for AGV Forklifts
Material | Typical Use Case for AGV Forklift | Key Advantage | Key Disadvantage/Limitation | Relative Cost (Low/Med/High) |
---|---|---|---|---|
Steel | Heavy-duty applications in warehouses | High durability and load capacity | Heavier, potential for rust | Medium |
Aluminum | Agile operations in retail environments | Lightweight and corrosion-resistant | Lower strength than steel | High |
Plastic Composites | Environments with corrosive substances | Customizable and resistant to chemicals | Less durable than metals | Medium |
Rubber | AGV tires and wheels for traction | Good shock absorption and traction | Limited lifespan under extreme conditions | Low |
This strategic material selection guide provides international B2B buyers with actionable insights to make informed decisions when investing in AGV forklifts, ensuring they choose the right materials for their specific operational needs.
In-depth Look: Manufacturing Processes and Quality Assurance for agv forklift
What Are the Typical Manufacturing Processes for AGV Forklifts?
The manufacturing of Automated Guided Vehicle (AGV) forklifts involves several critical stages that ensure the final product meets performance and safety standards. Understanding these processes is essential for international B2B buyers to evaluate potential suppliers effectively.
How Are Materials Prepared for AGV Forklift Production?
The first stage of the manufacturing process is material preparation. This phase involves sourcing high-quality raw materials, such as steel and electronic components, which are crucial for the structural integrity and operational efficiency of AGVs. Suppliers often use advanced software systems to track inventory and ensure that materials meet specific quality standards.
Once materials are sourced, they undergo initial inspections to verify their quality and compliance with international standards. These inspections can include testing for tensile strength, corrosion resistance, and dimensional accuracy. This stage is crucial, as any defects in materials can lead to issues in the final product.
What Forming Techniques Are Utilized in AGV Forklift Manufacturing?
After material preparation, the next step is forming. This process typically involves several techniques, including:
- Cutting: High-precision laser cutting machines are employed to shape metal sheets into the required components for the AGV structure.
- Welding: Robotic welding systems are often used to assemble these parts, ensuring strong, consistent joints that can withstand operational stresses.
- Molding: For non-metal parts, such as plastic components or rubber wheels, injection molding is commonly used.
These forming techniques are vital in creating the framework and components that will support the AGV’s functionality.
How Is the Assembly Process for AGV Forklifts Conducted?
The assembly stage is where all the individual components come together to create the AGV forklift. This phase typically follows a systematic approach:
- Sub-Assembly: Smaller groups of components are assembled first, such as electronic systems, drive units, and chassis.
- Main Assembly: The sub-assemblies are then integrated into the main structure. This includes installing navigation systems, batteries, and safety features.
- System Integration: The final assembly involves connecting all electronic and mechanical systems, ensuring they work seamlessly together.
During assembly, manufacturers adhere to standardized procedures to guarantee consistency and quality. Each assembly line is often equipped with specialized tools and equipment that enhance precision and efficiency.
What Finishing Processes Are Essential for AGV Forklifts?
Finishing processes play a crucial role in enhancing the durability and aesthetic appeal of AGV forklifts. These processes may include:
- Surface Treatment: Techniques such as powder coating or galvanization are applied to protect against corrosion and wear. This is particularly important for AGVs that operate in harsh environments.
- Quality Testing: After finishing, each AGV undergoes rigorous testing to ensure it meets safety and performance criteria. This can include weight capacity tests, speed tests, and operational simulations.
The finishing stage is critical as it not only impacts the AGV’s longevity but also its overall performance in various operational scenarios.
What Are the Quality Assurance Standards for AGV Forklifts?
Quality assurance (QA) is integral to the manufacturing process of AGV forklifts. Buyers should be aware of the international standards and industry-specific certifications that ensure product reliability.
Which International Standards Are Relevant for AGV Forklifts?
AGV manufacturers often adhere to several international quality standards, including:
- ISO 9001: This standard focuses on quality management systems and is widely recognized globally. It ensures that manufacturers have a systematic approach to managing quality throughout their operations.
- CE Marking: For products sold in Europe, CE marking indicates compliance with health, safety, and environmental protection standards. It is crucial for B2B buyers in Europe to verify that AGVs bear this mark.
- API Standards: In certain industries, particularly oil and gas, adherence to American Petroleum Institute (API) standards may be required.
These certifications not only provide assurance of product quality but also enhance the credibility of the manufacturer in the eyes of international buyers.
What Are the Key Quality Control Checkpoints in AGV Manufacturing?
Quality control (QC) checkpoints are established throughout the manufacturing process to ensure that AGVs meet specified standards. Key checkpoints include:
- Incoming Quality Control (IQC): Raw materials are inspected upon arrival to verify compliance with required specifications.
- In-Process Quality Control (IPQC): Ongoing inspections during production help identify and rectify issues early in the manufacturing process.
- Final Quality Control (FQC): Before shipment, each AGV undergoes a comprehensive final inspection, which may include functionality tests and safety checks.
Implementing these checkpoints helps mitigate risks and ensures that only high-quality products reach the market.
How Can B2B Buyers Verify Supplier Quality Control?
International B2B buyers must take proactive steps to verify the quality control processes of potential suppliers. Here are some actionable strategies:
What Are the Best Practices for Conducting Supplier Audits?
Conducting supplier audits is an effective way to assess a manufacturer’s adherence to quality standards. Buyers should consider:
- On-Site Audits: Visiting the manufacturing facility allows buyers to observe processes, check quality control measures, and evaluate equipment and technology used.
- Document Reviews: Requesting documentation, such as quality management system certifications and inspection reports, provides insights into the supplier’s commitment to quality.
How Can Buyers Utilize Third-Party Inspections?
Engaging third-party inspection services can provide an unbiased evaluation of a supplier’s quality control practices. These services can conduct detailed inspections at various stages of production and provide comprehensive reports that highlight any areas of concern.
What Are the Quality Certification Nuances for International Buyers?
Buyers from different regions, such as Africa, South America, the Middle East, and Europe, may encounter unique challenges regarding quality certifications. For instance:
- Regional Certifications: Understanding local regulations and certifications is crucial. For example, buyers in South Africa may require SANS certification for specific equipment.
- Documentation Variability: Different regions may have varying documentation requirements for customs and compliance. Buyers should ensure that suppliers provide all necessary paperwork for smooth importation.
By being informed about these nuances, B2B buyers can make more strategic purchasing decisions and ensure that their AGV forklifts meet both operational needs and regulatory requirements.
Practical Sourcing Guide: A Step-by-Step Checklist for ‘agv forklift’
In the fast-evolving world of logistics and material handling, sourcing an Automated Guided Vehicle (AGV) forklift requires a strategic approach. This checklist provides international B2B buyers—particularly from Africa, South America, the Middle East, and Europe—with actionable insights to streamline the procurement process.
Step 1: Define Your Technical Specifications
Understanding your operational needs is crucial before initiating the sourcing process. Consider the following:
– Load Capacity: What weight will the AGV need to handle? Ensure the specifications align with your warehouse requirements.
– Operating Environment: Will the AGV operate indoors, outdoors, or in both settings? This influences the type of AGV suitable for your operations.
Step 2: Research Different AGV Technologies
Not all AGVs are created equal. Familiarize yourself with the various types, such as:
– Navigation Systems: Different AGVs utilize various navigation technologies, such as magnetic or laser-guided systems. Choose one that fits your warehouse layout and operational complexity.
– Functionality: Assess whether you need an AGV for pallet transport, unit load handling, or specialized applications like hazardous materials.
Step 3: Evaluate Potential Suppliers
Before making a commitment, thoroughly vet potential suppliers. This step is essential for ensuring reliability and quality:
– Company Reputation: Look for suppliers with positive reviews and case studies in your industry. Request references from other businesses in similar regions.
– Technical Support: Assess the level of after-sales support and maintenance services offered. Reliable technical assistance is crucial for minimizing downtime.
Step 4: Check Compliance and Certifications
Safety and compliance should be top priorities when selecting an AGV forklift. Verify:
– Industry Standards: Ensure that the AGV meets international safety standards relevant to your industry.
– Supplier Certifications: Look for certifications such as ISO or CE, which indicate adherence to quality and safety norms.
Step 5: Request Product Demonstrations
Seeing an AGV in action can provide invaluable insights into its performance and suitability for your operations. During demonstrations:
– Performance Assessment: Evaluate the AGV’s efficiency in handling your specific tasks. Consider speed, maneuverability, and error rates.
– User Experience: Get feedback from your operators on ease of use and comfort. A user-friendly interface can significantly impact productivity.
Step 6: Analyze Total Cost of Ownership (TCO)
Understanding the full financial impact of an AGV is essential for budgeting. Consider:
– Initial Purchase Price vs. Long-Term Savings: While an AGV may have a higher upfront cost, its ability to streamline operations can lead to significant cost savings over time.
– Maintenance and Operating Costs: Factor in maintenance schedules, energy consumption, and potential training costs for staff.
Step 7: Finalize Your Purchase Agreement
Once you have selected a supplier and product, it’s time to negotiate and finalize the agreement. Pay attention to:
– Terms and Conditions: Review warranty coverage, service agreements, and delivery timelines.
– Flexibility in Payment Options: Inquire about financing plans or leasing options, which can ease the initial financial burden.
By following this step-by-step checklist, B2B buyers can effectively navigate the complexities of sourcing AGV forklifts, ensuring they make informed decisions that enhance operational efficiency.
Comprehensive Cost and Pricing Analysis for agv forklift Sourcing
What Are the Key Cost Components for Sourcing AGV Forklifts?
When evaluating the cost structure for Automated Guided Vehicle (AGV) forklifts, several components come into play. Understanding these elements will help international B2B buyers make informed decisions.
-
Materials: The cost of raw materials, such as steel and electronic components, significantly impacts the overall pricing of AGV forklifts. Advanced technologies, like sensors and AI systems, add to the material costs, especially if opting for high-quality, durable components designed for demanding environments.
-
Labor: Labor costs encompass both direct manufacturing labor and the expertise required for assembly and quality control. Given the complexity of AGVs, skilled labor is essential, which can increase the production cost.
-
Manufacturing Overhead: This includes indirect costs such as utilities, rent, and depreciation of equipment used in the manufacturing process. Overhead costs can vary significantly based on the location of the manufacturing facility, influencing pricing for international buyers.
-
Tooling: The investment in specialized tooling for AGV production can be substantial. Customization options often require unique tooling, which can drive up initial costs but may lead to better alignment with specific operational needs.
-
Quality Control (QC): Robust QC measures are crucial for ensuring that AGVs meet safety and operational standards. The cost associated with thorough testing and certification processes can be significant but is necessary for reliable performance.
-
Logistics: Shipping costs, including packaging, transportation, and import duties, can substantially affect the final price. Buyers should consider these logistics costs, especially when sourcing from manufacturers in different regions.
-
Margin: Suppliers typically add a profit margin to cover their costs and risks. This margin can vary based on competition, market demand, and the perceived value of the AGV technology.
How Do Price Influencers Impact AGV Forklift Costs?
Several factors can influence the pricing of AGV forklifts, particularly for international buyers from regions like Africa, South America, the Middle East, and Europe.
-
Volume/MOQ: Purchasing in bulk can lead to significant discounts. Suppliers often offer better pricing for larger orders, which can be advantageous for companies planning to integrate multiple AGVs into their operations.
-
Specifications and Customization: Custom-built AGVs tailored to specific operational needs can lead to higher costs. Buyers should clearly define their requirements to avoid unnecessary expenses while ensuring the AGV performs optimally in their environment.
-
Materials and Quality Certifications: Higher-quality materials and certifications (e.g., ISO, CE) typically increase costs. However, these investments can lead to lower Total Cost of Ownership (TCO) through reduced maintenance and longer operational lifespans.
-
Supplier Factors: The reputation and reliability of the supplier can influence pricing. Established brands may charge a premium, but their products often come with better support and warranty options.
-
Incoterms: The terms of shipping (Incoterms) can significantly impact final costs. Understanding the responsibilities of the buyer and seller can help manage logistics costs effectively.
What Are Essential Tips for Negotiating AGV Forklift Prices?
-
Understand Total Cost of Ownership (TCO): Evaluate not only the initial purchase price but also long-term costs, including maintenance, energy consumption, and potential downtime. A higher upfront cost may be justified by lower operating expenses.
-
Leverage Negotiation: Engage suppliers in discussions about pricing, especially if you have competitive quotes. Highlighting your purchasing power or interest in long-term partnerships can lead to better deals.
-
Consider Financing Options: Many suppliers offer financing plans that can ease the initial financial burden. Investigating these options can make AGVs more accessible, particularly for businesses in emerging markets.
-
Research Local Incentives: Some regions may offer incentives for automation investments. Understanding local policies can help reduce costs or enhance financing possibilities.
-
Be Aware of Pricing Nuances: International buyers should consider currency fluctuations and import tariffs, which can affect the final cost. Negotiating fixed prices or considering local suppliers may mitigate these risks.
By carefully analyzing these cost components and price influencers, international B2B buyers can make informed decisions that align with their operational needs and budget constraints.
Alternatives Analysis: Comparing agv forklift With Other Solutions
When considering the implementation of automated material handling solutions, it is crucial for B2B buyers to evaluate various alternatives to AGV forklifts. Each solution has distinct advantages and limitations that can significantly impact operational efficiency, cost-effectiveness, and adaptability to specific business needs.
Comparison Table of AGV Forklift Against Alternative Solutions
Comparison Aspect | AGV Forklift | Automated Guided Carts (AGCs) | Manual Forklifts |
---|---|---|---|
Performance | High efficiency in repetitive tasks; can navigate complex environments autonomously. | Moderate efficiency; best for straightforward paths and low-volume transport. | High flexibility but dependent on operator skill; inconsistent performance. |
Cost | Higher initial investment; potential long-term savings through reduced labor costs. | Generally lower cost than AGVs; less automation leads to higher labor costs long-term. | Lower upfront costs; ongoing labor costs can accumulate significantly. |
Ease of Implementation | Requires significant initial setup and integration with existing systems. | Easier to implement; can be integrated into existing workflows with minimal disruption. | Simple to implement; requires training for operators. |
Maintenance | Requires specialized maintenance; may involve higher costs and downtime. | Lower maintenance needs; simpler technology leads to fewer issues. | Routine maintenance is straightforward but can lead to unexpected repairs. |
Best Use Case | Ideal for high-volume warehouses with repetitive tasks and complex layouts. | Best for low to moderate volume environments with simple transport needs. | Suitable for diverse applications but not optimal for high-volume tasks. |
In-Depth Look at Alternative Solutions
What Are Automated Guided Carts (AGCs) and How Do They Compare?
Automated Guided Carts (AGCs) are designed for transporting goods across predefined paths within a facility. They typically utilize magnetic strips or simple navigation systems, making them easier to implement than AGV forklifts. While AGCs have a lower initial cost, their reliance on human operators for complex tasks can result in higher long-term operational costs. AGCs are best suited for environments with predictable workflows and lower transport volumes, where flexibility is not as critical.
How Do Manual Forklifts Stack Up Against AGV Forklifts?
Manual forklifts are operated by trained personnel and are highly flexible, allowing for a wide range of applications, from unloading trucks to moving materials within a warehouse. They have lower upfront costs compared to AGV forklifts and do not require complex integration. However, manual forklifts rely heavily on operator skill, which can lead to inconsistent performance and higher labor costs over time. They are best suited for smaller operations or those with diverse material handling needs, but may not be efficient for high-volume tasks.
How Can B2B Buyers Choose the Right Material Handling Solution?
Choosing the right material handling solution requires a thorough assessment of your specific operational needs, including volume, complexity, and budget. AGV forklifts are ideal for high-volume operations that require precision and efficiency, while AGCs may be a better fit for facilities with simpler logistics. Manual forklifts offer flexibility but come with ongoing labor costs that can add up. By evaluating the distinct characteristics of each option, B2B buyers can make informed decisions that align with their operational goals and budget constraints, ultimately enhancing productivity and profitability.
Essential Technical Properties and Trade Terminology for agv forklift
What Are the Essential Technical Properties of AGV Forklifts?
Understanding the technical specifications of Automated Guided Vehicle (AGV) forklifts is crucial for B2B buyers looking to optimize their material handling processes. Below are key properties that significantly influence the performance and suitability of AGVs for various applications.
1. Load Capacity: How Much Can an AGV Forklift Handle?
Load capacity refers to the maximum weight an AGV forklift can safely lift and transport. This specification is critical as it directly affects operational efficiency and safety. For instance, an AGV with a higher load capacity can handle bulkier items, which is essential in sectors like manufacturing and warehousing. Buyers should assess their material handling needs to select an AGV that meets or exceeds their load requirements.
2. Battery Life and Charging Time: How Long Can an AGV Operate?
Battery life indicates how long an AGV can operate before needing a recharge. This property is vital for minimizing downtime and maintaining workflow efficiency. Many AGVs utilize lithium-ion batteries, which offer faster charging times and longer operational periods. Understanding battery specifications helps buyers plan their operations and avoid interruptions due to charging needs.
3. Navigation Technology: How Does an AGV Find Its Way?
AGV forklifts employ various navigation technologies, including laser guidance, magnetic tape, and vision-based systems. The choice of navigation affects the AGV’s adaptability to different environments. For example, laser-guided AGVs can navigate complex warehouse layouts, making them ideal for dynamic operations. Buyers should consider their facility’s layout and the complexity of tasks when selecting AGVs based on navigation technology.
4. Dimensions and Maneuverability: Can It Fit in My Warehouse?
The physical dimensions of an AGV, including its width, height, and turning radius, determine its ability to maneuver in tight spaces. A compact AGV is advantageous in warehouses with narrow aisles, while larger models may be suited for open areas. Buyers must evaluate their facility’s space constraints to ensure that the chosen AGV can operate efficiently within those limitations.
5. Safety Features: What Protects Workers and Equipment?
Safety features are critical in preventing accidents and protecting both operators and goods. Common safety specifications include emergency stop buttons, obstacle detection sensors, and speed control. These features enhance operational safety, particularly in environments with high foot traffic. Buyers should prioritize AGVs with robust safety mechanisms to reduce liability and ensure a safe working environment.
What Are Common Trade Terms Related to AGV Forklifts?
Familiarity with industry terminology is essential for effective communication and decision-making in B2B transactions. Below are several key terms that buyers should understand when engaging with AGV suppliers.
1. OEM (Original Equipment Manufacturer): Who Makes My AGV?
An OEM is a company that manufactures products that are sold under another company’s brand. In the AGV market, working with an OEM can ensure that the AGVs meet specific quality standards and performance requirements. Buyers should consider the reputation of the OEM to ensure reliability and service support.
2. MOQ (Minimum Order Quantity): What Is the Smallest Order I Can Place?
MOQ refers to the smallest number of units a supplier is willing to sell in a single order. Understanding MOQ is crucial for budget planning and inventory management. Buyers should negotiate MOQs based on their operational needs to avoid excess inventory costs.
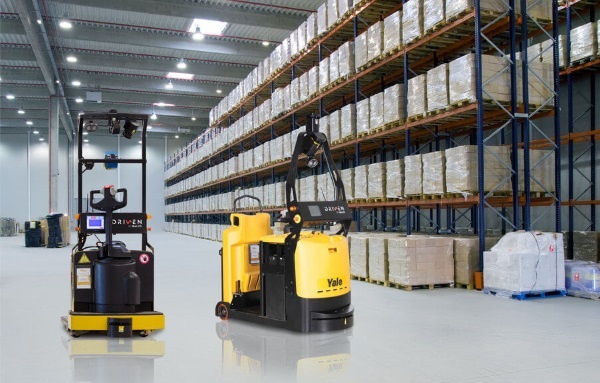
A stock image related to agv forklift.
3. RFQ (Request for Quotation): How Do I Get Pricing?
An RFQ is a formal document that buyers send to suppliers to request pricing and terms for specific products. Crafting a detailed RFQ can help buyers receive accurate quotes and compare offers effectively. Including technical specifications and required quantities in an RFQ is essential for obtaining relevant responses.
4. Incoterms (International Commercial Terms): What Are My Shipping Responsibilities?
Incoterms are a set of predefined commercial terms that outline the responsibilities of buyers and sellers in international transactions. They clarify who is responsible for shipping costs, insurance, and risk during transit. Understanding these terms can help buyers negotiate better shipping arrangements and avoid unexpected costs.
5. TCO (Total Cost of Ownership): What Will My AGV Truly Cost?
TCO encompasses all costs associated with owning and operating an AGV over its lifetime, including purchase price, maintenance, and operational costs. Evaluating TCO helps buyers make informed decisions by comparing the long-term value of different AGV options rather than focusing solely on initial purchase price.
By understanding these essential technical properties and trade terms, B2B buyers can make informed decisions when selecting AGV forklifts that best meet their operational needs.
Navigating Market Dynamics and Sourcing Trends in the agv forklift Sector
What Are the Key Trends Driving the AGV Forklift Market?
The Automated Guided Vehicle (AGV) forklift market is experiencing significant growth, driven by various global factors. The increasing demand for automation in warehouses and manufacturing facilities is a primary driver. Companies are seeking solutions that enhance operational efficiency, reduce labor costs, and minimize errors in material handling. In regions such as Africa, South America, the Middle East, and Europe, businesses are adopting AGVs to cope with labor shortages and rising operational costs.
Emerging technologies, such as advanced sensors and AI-driven navigation systems, are enhancing the capabilities of AGVs, making them more adaptable to diverse environments. For instance, AGVs now incorporate machine learning algorithms that allow them to optimize routes and adapt to changing warehouse layouts dynamically. This flexibility is particularly beneficial for international B2B buyers looking to streamline their supply chains and improve turnaround times.
Additionally, the rise of e-commerce is pushing companies to seek efficient inventory management solutions. AGVs can significantly speed up the transportation of goods within warehouses, providing a competitive edge in fulfilling customer orders promptly. As global supply chains continue to evolve, international buyers must stay informed about these trends to make strategic purchasing decisions that align with their operational goals.
How Can Sustainability and Ethical Sourcing Impact AGV Forklift Purchases?
Sustainability is becoming a vital consideration in the procurement of AGV forklifts. International buyers are increasingly focused on the environmental impact of their operations, seeking solutions that not only enhance efficiency but also reduce carbon footprints. AGVs are often designed with energy-efficient technologies, such as lithium-ion batteries, which contribute to lower emissions and reduced energy consumption compared to traditional forklifts.
Moreover, ethical sourcing is gaining traction among B2B buyers. Companies are prioritizing suppliers that adhere to sustainable practices and have transparent supply chains. Certifications such as ISO 14001 (Environmental Management) and ISO 50001 (Energy Management) are indicators of a manufacturer’s commitment to sustainability. Buyers from regions like Europe and the Middle East are particularly attentive to these certifications, as they align with stringent regulatory standards and consumer expectations.
Investing in AGVs from manufacturers with a strong sustainability ethos not only enhances a company’s operational efficiency but also bolsters its reputation in the market. By aligning purchasing decisions with ethical sourcing standards, companies can contribute to a more sustainable future while meeting their operational needs.
What Is the Historical Context of AGV Forklifts for B2B Buyers?
The evolution of Automated Guided Vehicles (AGVs) dates back to the mid-20th century when they were initially developed for simple material transport tasks within manufacturing plants. Early models relied heavily on fixed guidance systems, such as rails or magnetic strips. However, with advancements in technology, AGVs have transitioned to more sophisticated navigation systems, including laser guidance and vision-based navigation, allowing for greater flexibility and efficiency in warehouse operations.
The introduction of AGV forklifts has transformed the material handling landscape, especially in sectors with high demand for automation. As industries continue to embrace digital transformation, AGVs are becoming integral components of modern supply chains. For B2B buyers, understanding this evolution provides valuable insights into the potential for future innovations and the importance of selecting AGVs that can adapt to evolving operational requirements. By investing in the latest AGV technologies, companies can position themselves at the forefront of industry advancements, ensuring sustained competitiveness in a rapidly changing market.
Frequently Asked Questions (FAQs) for B2B Buyers of agv forklift
-
How do I choose the right AGV forklift for my warehouse operations?
Selecting the appropriate AGV forklift involves evaluating your specific operational needs, such as load capacity, navigation technology, and the type of goods being handled. Consider the layout of your warehouse and the workflows to determine whether you require a counterbalance AGV, reach truck AGV, or another type. It’s also beneficial to consult with suppliers who can provide tailored solutions based on your operational goals, ensuring enhanced efficiency and productivity. -
What are the key features to look for in an AGV forklift?
When sourcing an AGV forklift, prioritize features such as navigation technology (laser, magnetic, or vision-based), load capacity, battery life, and safety mechanisms. Advanced AGVs may also offer flexibility in navigating dynamic environments and integrating with existing warehouse management systems. Additionally, consider the after-sales support and service options provided by the supplier to ensure ongoing operational efficiency. -
What is the typical lead time for AGV forklift delivery?
Lead times for AGV forklifts can vary significantly based on the manufacturer’s location, the complexity of the order, and customization requirements. Typically, you can expect a lead time ranging from 6 to 12 weeks. To mitigate delays, it’s advisable to plan your procurement well in advance and maintain clear communication with the supplier regarding production schedules and shipping logistics. -
How can I ensure the quality of AGV forklifts when purchasing internationally?
To ensure quality, conduct thorough due diligence on potential suppliers. Request certifications such as ISO standards, and inquire about their quality assurance processes. Additionally, consider visiting the manufacturing facility or using third-party inspection services. Reading reviews and case studies from other international buyers can also provide insights into a supplier’s reliability and product quality. -
What customization options are available for AGV forklifts?
Many manufacturers offer customization options to meet specific operational needs. Customizations can include modifications to the AGV’s size, load capacity, navigation systems, or software interfaces. When discussing your requirements with suppliers, ensure they provide clear details on the customization process, associated costs, and timelines to ensure the final product aligns with your operational goals. -
What are the minimum order quantities (MOQ) for AGV forklifts?
Minimum order quantities can vary by supplier and the specific models being ordered. Some manufacturers may have flexible MOQs, while others may require bulk orders to justify production costs. It’s advisable to discuss your purchasing needs with potential suppliers to negotiate terms that align with your budget and operational scale, particularly if you are a smaller business or just starting with automation. -
What payment terms should I expect when sourcing AGV forklifts?
Payment terms for AGV forklifts often range from upfront payments to payment upon delivery or a combination of both. Many suppliers may require a deposit (20-50%) upon order confirmation, with the balance due before shipment. It’s essential to clarify payment terms during negotiations to ensure alignment with your financial planning and cash flow management. -
What logistics considerations should I keep in mind when importing AGV forklifts?
When importing AGV forklifts, consider factors such as shipping methods, customs regulations, and potential tariffs. Choose a reliable logistics partner who understands international shipping and can assist with documentation and compliance. Additionally, plan for potential delays by allowing buffer time in your project timelines and ensuring your receiving facilities are prepared for the equipment’s arrival.
Important Disclaimer & Terms of Use
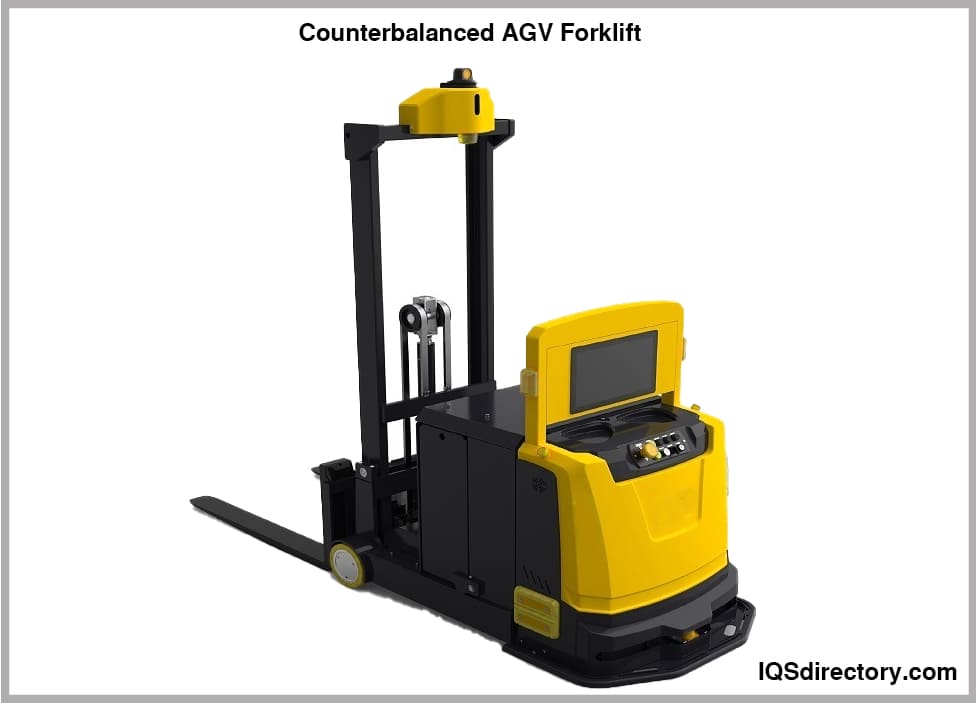
A stock image related to agv forklift.
⚠️ Important Disclaimer
The information provided in this guide, including content regarding manufacturers, technical specifications, and market analysis, is for informational and educational purposes only. It does not constitute professional procurement advice, financial advice, or legal advice.
While we have made every effort to ensure the accuracy and timeliness of the information, we are not responsible for any errors, omissions, or outdated information. Market conditions, company details, and technical standards are subject to change.
B2B buyers must conduct their own independent and thorough due diligence before making any purchasing decisions. This includes contacting suppliers directly, verifying certifications, requesting samples, and seeking professional consultation. The risk of relying on any information in this guide is borne solely by the reader.
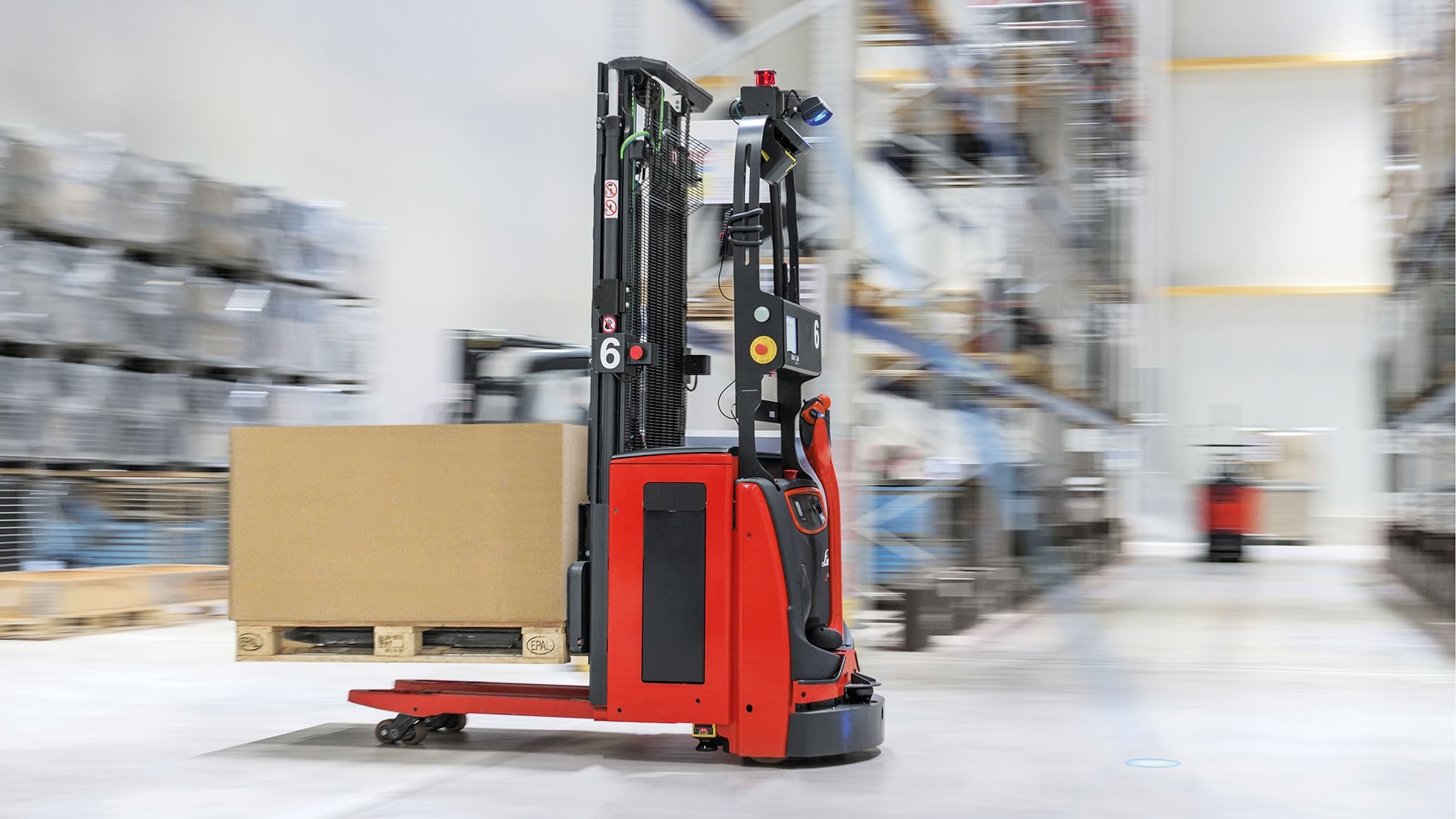
A stock image related to agv forklift.
Strategic Sourcing Conclusion and Outlook for agv forklift
As the demand for efficiency and cost-effectiveness in material handling increases, investing in Automated Guided Vehicles (AGVs) like forklifts is becoming a strategic priority for businesses worldwide. For international B2B buyers, particularly from regions like Africa, South America, the Middle East, and Europe, understanding the benefits of AGVs—such as improved labor efficiency, reduced damage costs, and enhanced operational flexibility—is essential.
How Can Strategic Sourcing Enhance AGV Procurement?
Strategic sourcing plays a pivotal role in ensuring that businesses select the right AGV solutions tailored to their specific operational needs. By evaluating suppliers based on performance, technology, and customer support, buyers can secure equipment that not only meets current demands but also scales with future growth. Leveraging partnerships with reliable manufacturers can facilitate access to the latest innovations, ensuring businesses remain competitive in an increasingly automated landscape.
What Does the Future Hold for AGV Forklifts?
Looking ahead, the evolution of AGV technology, including advancements in navigation and artificial intelligence, promises to further streamline operations. For B2B buyers, this is an opportune moment to embrace automation. By making informed sourcing decisions today, companies can position themselves at the forefront of their industries, ultimately driving profitability and operational excellence. Engage with trusted suppliers, assess your unique needs, and take the first steps towards a more automated future.