Discover Different Lock Types: The Ultimate Sourcing Guide (2025)
Introduction: Navigating the Global Market for different lock types
In today’s global marketplace, sourcing the right types of locks for various applications can be a daunting task for international B2B buyers, especially when considering security, compliance, and cost. With a myriad of options available—from mortice deadlocks and padlocks to advanced electronic locking systems—understanding which lock type best suits your needs is crucial. This comprehensive guide will explore the myriad types of locks, their specific applications, and essential factors for supplier vetting, all while keeping regional considerations in mind for buyers from Africa, South America, the Middle East, and Europe, including the UK and South Africa.
As a B2B buyer, making informed purchasing decisions hinges on not only recognizing the different lock types but also understanding their security features, installation requirements, and associated costs. This guide will empower you with actionable insights, ensuring you can confidently navigate the complexities of the global lock market. By examining factors such as durability, technology trends, and compliance with international standards, you will be better equipped to select locks that enhance your security infrastructure. Whether you’re securing commercial premises, residential properties, or sensitive environments, this guide is designed to be your go-to resource for understanding the nuances of different lock types and ensuring your procurement process aligns with your organizational goals.
Understanding different lock types Types and Variations
Type Name | Key Distinguishing Features | Primary B2B Applications | Brief Pros & Cons for Buyers |
---|---|---|---|
5 Lever Mortice Deadlock | Fitted within the door, requires a key to operate from both sides | Commercial buildings, warehouses | Pros: High security, BS3621 compliant options available. Cons: More expensive than basic locks, installation may require skilled labor. |
Euro Cylinder Lock | Commonly used in uPVC doors, removable cylinder for easy rekeying | Residential complexes, office buildings | Pros: Versatile, easy to replace or rekey. Cons: Vulnerable to cylinder snapping if not reinforced. |
Deadbolts | Variants include single, double, and thumbturn; installed on external doors | Retail stores, office entrances | Pros: Strong resistance to forced entry. Cons: Single cylinder can be vulnerable if access to the interior is available. |
Padlocks | Portable, available as combination or keyed; can be shrouded for extra security | Temporary storage, outdoor equipment | Pros: Highly portable, versatile for various applications. Cons: Combination locks can be easier to bypass. |
Key Operated Multipoint Locking | Engages multiple locking points along the door frame, typically operated by a single key | High-security facilities, residential doors | Pros: Offers superior security by distributing locking points. Cons: More complex installation and higher cost. |
What Are the Characteristics of a 5 Lever Mortice Deadlock?
The 5 lever mortice deadlock is a robust locking solution commonly installed in wooden doors. It operates using a key from both the inside and outside, ensuring high security. For B2B buyers, especially in commercial settings, choosing a BS3621 compliant model guarantees that the lock has been rigorously tested against common burglary techniques. When purchasing, consider the lock’s material and whether it fits the specific door type, as well as the cost of installation.
How Does a Euro Cylinder Lock Work and Where Is It Used?
The Euro cylinder lock is a versatile option, particularly suited for uPVC doors. Its design allows for easy rekeying, which is beneficial for businesses that may need to change access frequently. Commonly found in residential complexes and office buildings, these locks provide a balance between security and convenience. When selecting a Euro cylinder lock, buyers should assess the security features, such as anti-snap protection, to prevent unauthorized access.
What Are the Advantages of Using Deadbolts in Commercial Settings?
Deadbolts are essential for securing external doors in commercial properties. They come in various types, including single and double cylinder options, offering flexibility depending on the security needs. For instance, a double cylinder deadbolt adds an extra layer of security but may pose risks in emergency situations. B2B buyers should evaluate the specific security needs of their premises and consider the ease of use for employees when choosing deadbolts.
Why Are Padlocks a Good Choice for Temporary Security Solutions?
Padlocks are renowned for their portability and ease of use, making them ideal for temporary security applications such as securing outdoor equipment or storage units. Available in combination and keyed varieties, they provide flexibility in securing items. However, the security level can vary significantly, so B2B buyers should opt for high-quality padlocks with features like shrouded shackles to enhance resistance against cutting tools.
What Makes Key Operated Multipoint Locking Systems Ideal for High-Security Facilities?
Key operated multipoint locking systems engage multiple locking points along the door frame, providing enhanced security for high-risk environments such as banks or secure offices. This type of lock is operated by a single key, simplifying access while maximizing security. When considering this option, B2B buyers should focus on the lock’s installation requirements and ongoing maintenance to ensure long-term effectiveness in safeguarding their assets.
Key Industrial Applications of different lock types
Industry/Sector | Specific Application of Different Lock Types | Value/Benefit for the Business | Key Sourcing Considerations for this Application |
---|---|---|---|
Manufacturing | Secure access control for production facilities | Protects intellectual property and equipment from theft | Look for high-security locks with key control systems |
Logistics and Warehousing | Padlocks for container and warehouse security | Prevents unauthorized access to goods and reduces theft risk | Consider weather-resistant materials for outdoor use |
Hospitality | Key card systems for hotel room access | Enhances guest convenience and security | Ensure compatibility with existing systems and easy integration |
Healthcare | Mortice locks for secure access to patient records and medicines | Protects sensitive information and ensures compliance with regulations | Choose locks that meet health and safety standards |
Retail | Electronic locks for inventory storage areas | Improves inventory management and reduces shrinkage | Evaluate electronic options for scalability and remote access control |
How is Different Lock Types Used in Manufacturing?
In the manufacturing industry, different lock types, particularly high-security mortice locks, are essential for securing production facilities. These locks help protect valuable intellectual property and machinery from theft. International B2B buyers should prioritize locks with robust key control systems, which restrict unauthorized key duplication and enhance overall security. Additionally, locks should be durable enough to withstand industrial environments, ensuring long-term reliability.
What are the Specific Applications of Locks in Logistics and Warehousing?
In logistics and warehousing, padlocks serve as a primary security measure for containers and storage units. Their portability allows for flexible security solutions across various locations. The use of weather-resistant padlocks is particularly important in regions with harsh climates, ensuring that security measures remain effective. B2B buyers in this sector should look for padlocks with shrouded shackles to resist bolt cutter attacks, thereby reducing the risk of theft.
How are Lock Types Utilized in the Hospitality Industry?
The hospitality sector frequently employs electronic key card systems to manage access to guest rooms. This technology enhances guest convenience by allowing easy access without physical keys, while also improving security through the ability to deactivate lost cards. Buyers should ensure that the chosen system can integrate seamlessly with existing hotel management software and is user-friendly for both staff and guests. Additionally, the durability of the electronic locks is crucial for high-traffic environments.
Why are Mortice Locks Important in Healthcare?
In healthcare settings, mortice locks are vital for securing access to sensitive areas, such as patient records and medication storage. These locks help maintain compliance with strict regulations regarding patient privacy and safety. Buyers in this sector should select mortice locks that meet health and safety standards, ensuring they are reliable and secure. Additionally, ease of access for authorized personnel is crucial, necessitating locks that can be opened quickly in emergencies.
How Do Electronic Locks Benefit the Retail Industry?
In retail, electronic locks provide a sophisticated solution for securing inventory storage areas, significantly reducing shrinkage and improving inventory management. These locks allow for controlled access, enabling retailers to monitor who enters storage areas and when. When sourcing electronic locks, businesses should consider options that offer scalability and remote access capabilities, allowing for centralized management of multiple locations. This flexibility can lead to enhanced security and operational efficiency across retail operations.
3 Common User Pain Points for ‘different lock types’ & Their Solutions
Scenario 1: Navigating Security Standards for Lock Types
The Problem:
Many international B2B buyers face significant challenges when selecting locks that meet specific security standards. For example, businesses operating in Europe may require locks that conform to the European Norm (EN) standards, while buyers in the UK often look for locks that are Kitemarked to British Standard BS3621. This inconsistency can lead to confusion and the risk of procuring locks that do not provide adequate security, potentially exposing the business to theft or loss.
The Solution:
To mitigate this issue, it is crucial for buyers to conduct thorough research on the local security standards applicable to their region. Engaging with reputable suppliers who specialize in the local market can provide insights into the most suitable lock types that meet regulatory requirements. For instance, consider investing in a five-lever mortice deadlock that is BS3621 approved for UK markets, as this ensures the lock has been tested against common burglary techniques. Additionally, utilizing comprehensive checklists that outline the necessary certifications and security features can streamline the procurement process and enhance security compliance.
Scenario 2: Selecting the Right Lock Type for Diverse Applications
The Problem:
B2B buyers often struggle with selecting appropriate lock types for various applications within their facilities. For example, a company might require different locks for external entry points, internal office doors, and storage areas. The challenge lies in balancing security needs with budget constraints, as some lock types may be more expensive due to their enhanced security features.
The Solution:
A practical approach is to categorize locks based on their application and security requirements. For external doors, investing in high-security deadbolts or multi-point locking systems can provide robust protection. For internal office doors, simpler knob locks may suffice, allowing for cost savings without compromising security. Conducting a risk assessment to identify high-risk areas within the facility can help prioritize lock types that warrant a higher investment. Furthermore, consider bulk purchasing options with suppliers to negotiate better pricing for locks that meet the diverse needs of the organization.
Scenario 3: Managing Key Control and Access Issues
The Problem:
Managing key control is a common pain point for B2B buyers, especially in larger organizations with multiple access points. Issues such as lost keys, unauthorized duplication, and the need for frequent rekeying can lead to security vulnerabilities and operational inefficiencies. This is particularly concerning in industries like hospitality or warehousing, where access control is critical.
The Solution:
Implementing a master key system can significantly enhance key management while providing flexibility and security. This system allows for different levels of access based on user roles, enabling staff to enter specific areas while restricting access to sensitive zones. For instance, consider using rekeyable padlocks for storage areas to facilitate easy key changes without replacing the entire lock. Additionally, employing electronic access control systems, such as keycards or biometric scanners, can further streamline access management while providing detailed records of entry. Investing in a centralized key management system can also help track key distribution and usage, thereby reducing the risk of unauthorized access.
Strategic Material Selection Guide for different lock types
When selecting locks for various applications, the choice of material plays a crucial role in determining the lock’s performance, durability, and overall effectiveness. Below, we analyze four common materials used in lock manufacturing, focusing on their properties, advantages and disadvantages, and considerations for international B2B buyers.
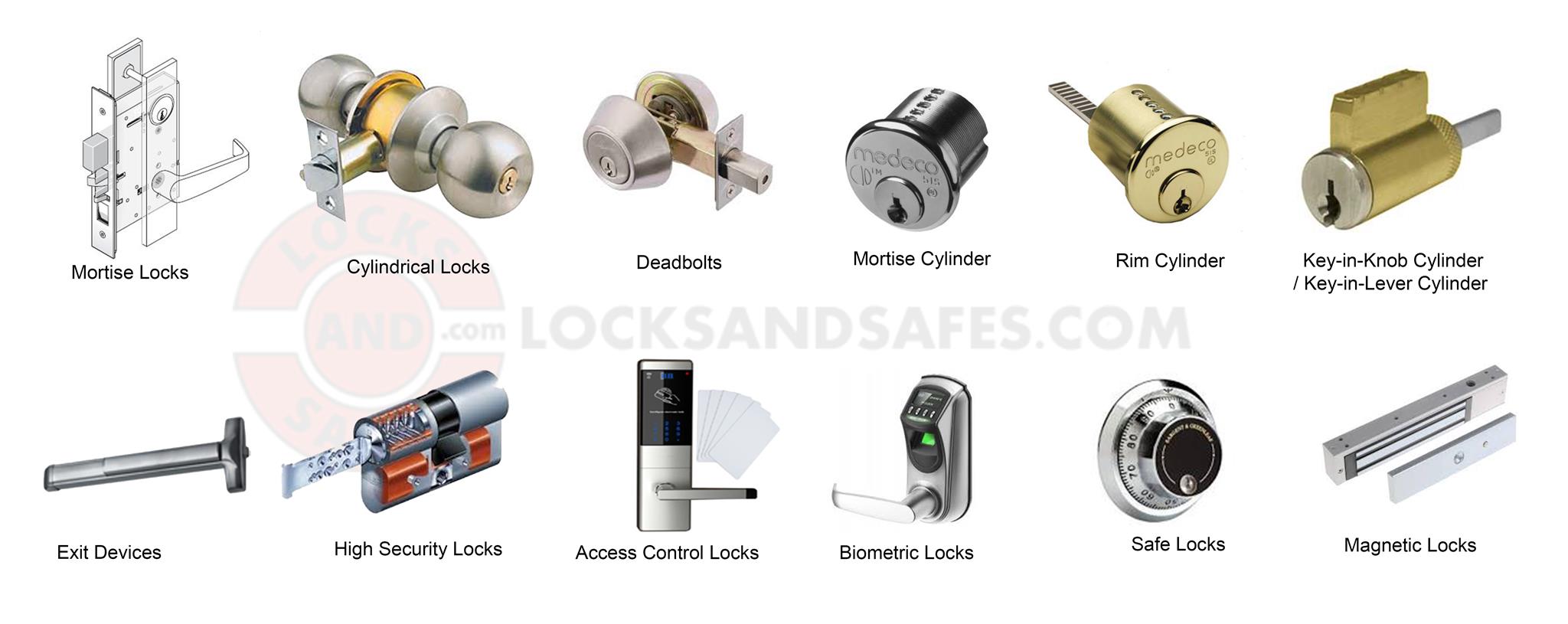
A stock image related to different lock types.
What Are the Key Properties of Steel in Lock Manufacturing?
Steel is one of the most commonly used materials for locks due to its strength and durability. It typically offers high tensile strength and resistance to impact, making it suitable for high-security applications. Steel locks can withstand significant pressure and are often treated for corrosion resistance, which is essential in humid or coastal environments.
Pros: Steel locks are highly durable, resistant to physical attacks, and can be manufactured at a relatively low cost. They are suitable for various applications, including residential and commercial settings.
Cons: While steel is robust, it can be susceptible to rust and corrosion if not properly treated, especially in regions with high moisture levels. Additionally, the manufacturing process can be complex, affecting production timelines.
Impact on Application: Steel locks are ideal for external doors and high-security areas but may not be suitable for environments with extreme corrosion risks unless treated appropriately.
How Does Brass Compare as a Material for Locks?
Brass is another popular material for lock manufacturing, known for its aesthetic appeal and resistance to corrosion. It is a copper-zinc alloy that provides good mechanical properties and is often used in residential locks and decorative applications.
Pros: Brass locks are resistant to corrosion and tarnishing, making them suitable for various climates. They also offer a pleasing appearance, which is beneficial for decorative applications.
Cons: While brass is durable, it is softer than steel, making it less resistant to physical attacks. Consequently, it may not be the best choice for high-security applications.
Impact on Application: Brass locks are commonly used in residential settings and interior doors but should be avoided in high-risk areas where security is paramount.
What Benefits Does Zinc Die-Casting Offer for Lock Production?
Zinc die-casting is a manufacturing process that produces complex shapes with high precision. Zinc alloy locks are lightweight and can be molded into intricate designs, making them popular for various consumer products.
Pros: Zinc locks are cost-effective and can be produced in large quantities with consistent quality. They also offer good corrosion resistance, making them suitable for various environments.
Cons: Although zinc is lightweight, it is not as strong as steel, which may limit its use in high-security applications. Additionally, zinc locks may not perform well under extreme temperature variations.
Impact on Application: Zinc die-cast locks are suitable for low to medium-security applications, such as interior doors or cabinets, but should be avoided in high-security environments.
Why Is Stainless Steel a Preferred Material for High-Security Locks?
Stainless steel combines the strength of steel with enhanced corrosion resistance, making it an excellent choice for high-security applications. It is often used in environments where exposure to moisture and chemicals is a concern.
Pros: Stainless steel locks are highly durable, resistant to corrosion, and can withstand harsh environmental conditions. They are ideal for both residential and commercial applications requiring high security.
Cons: The primary drawback is the higher cost of stainless steel compared to other materials. Additionally, the manufacturing process can be more complex, leading to longer lead times.
Impact on Application: Stainless steel locks are ideal for external doors, commercial properties, and areas prone to corrosion, ensuring both security and longevity.
Summary Table of Material Selection for Lock Types
Material | Typical Use Case for different lock types | Key Advantage | Key Disadvantage/Limitation | Relative Cost (Low/Med/High) |
---|---|---|---|---|
Steel | High-security external doors | High strength and durability | Susceptible to rust without treatment | Medium |
Brass | Residential and decorative locks | Corrosion-resistant and aesthetic | Softer, less secure than steel | Medium |
Zinc Die-Casting | Interior doors and cabinets | Cost-effective and lightweight | Not suitable for high-security areas | Low |
Stainless Steel | High-security commercial and external doors | Excellent corrosion resistance | Higher cost and complex manufacturing | High |
This strategic material selection guide provides international B2B buyers with insights into the properties and considerations of various materials used in lock manufacturing, helping them make informed decisions tailored to their specific needs and regional conditions.
In-depth Look: Manufacturing Processes and Quality Assurance for different lock types
What Are the Main Stages in the Manufacturing Process of Locks?
The manufacturing process for locks typically involves several critical stages, each requiring specialized techniques and attention to detail. Understanding these stages can help B2B buyers assess the quality and reliability of their suppliers.
-
Material Preparation
The first step in lock manufacturing is selecting high-quality raw materials. Common materials include steel, brass, zinc alloys, and plastics. Each material’s properties affect the lock’s durability and security. For instance, stainless steel is often preferred for its corrosion resistance, while brass is known for its aesthetic appeal and resistance to wear. Suppliers should provide certifications for material quality, ensuring compliance with international standards such as ASTM or ISO 9001. -
Forming
Once materials are prepared, they undergo various forming processes. Techniques such as forging, casting, and machining are commonly employed. Forging involves shaping heated metal into the desired form, which enhances strength. Casting allows for more intricate designs but may introduce weaknesses if not executed correctly. Machining, often used for precision parts, ensures tight tolerances critical for lock functionality. B2B buyers should inquire about the specific forming techniques employed and their implications for the final product’s security. -
Assembly
After forming, individual components are assembled. This stage often includes the installation of internal mechanisms such as pins, tumblers, and springs. Automated assembly lines are increasingly common, improving efficiency and consistency. However, manual assembly may still be necessary for more complex lock designs. Quality assurance during assembly is crucial, as improper installation can lead to malfunction or security vulnerabilities. Buyers should verify that the assembly process follows stringent quality control measures. -
Finishing
The final manufacturing stage involves surface treatments and coatings. Processes such as anodizing, plating, or powder coating enhance the lock’s aesthetic appeal and provide additional protection against wear and corrosion. For instance, chrome plating can improve corrosion resistance while offering a polished look. Buyers should consider the environmental impact of these finishing processes and seek suppliers who adhere to eco-friendly practices.
What Quality Assurance Standards Should B2B Buyers Consider?
Quality assurance (QA) is vital in the lock manufacturing industry, ensuring that products meet safety and performance standards. International standards like ISO 9001 provide frameworks for consistent quality management systems. In addition to ISO certifications, industry-specific standards should also be considered, such as:
- CE Marking: Required for products sold in the European Economic Area, indicating compliance with health, safety, and environmental protection standards.
- API Standards: Particularly relevant for locks used in industrial applications, ensuring that products meet specific performance criteria.
B2B buyers should ensure that their suppliers can provide evidence of compliance with these standards, as it reflects a commitment to quality.
What Are the Key Quality Control Checkpoints in Lock Manufacturing?
Implementing a robust quality control system involves several checkpoints throughout the manufacturing process:
-
Incoming Quality Control (IQC)
This initial checkpoint involves inspecting raw materials upon arrival. Suppliers should conduct tests to verify that materials meet specified standards, including tensile strength and corrosion resistance. Documentation of these tests should be readily available for buyer review. -
In-Process Quality Control (IPQC)
During the manufacturing process, IPQC ensures that every stage meets quality requirements. This includes monitoring forming techniques, assembly accuracy, and adherence to design specifications. Regular audits and process checks can help identify potential defects early, reducing waste and ensuring product reliability. -
Final Quality Control (FQC)
The final inspection occurs before products are packaged and shipped. FQC includes testing locks for functionality, durability, and security. Common testing methods involve cycle testing (to simulate repeated use), resistance to manipulation (such as lock picking), and environmental testing (to assess performance under extreme conditions). Buyers should request detailed reports of FQC results to verify the product’s quality.
How Can B2B Buyers Verify Supplier Quality Control Processes?
B2B buyers should adopt a proactive approach to supplier verification to ensure that quality control processes align with their standards. Here are effective strategies:
-
Supplier Audits: Conducting regular audits of suppliers can provide insights into their manufacturing practices, quality control measures, and compliance with international standards. Audits should cover all aspects of the manufacturing process, from material sourcing to final assembly.
-
Requesting Quality Reports: Suppliers should provide comprehensive quality assurance documentation, including IQC, IPQC, and FQC reports. These documents should detail inspection results, testing methodologies, and any corrective actions taken for identified issues.
-
Third-Party Inspections: Engaging independent third-party inspection services can offer an unbiased assessment of a supplier’s quality control processes. These inspections can be particularly beneficial for buyers in regions with varying regulatory standards, such as Africa and South America.
What Are the Quality Control Nuances for International B2B Buyers?
When sourcing locks from international suppliers, B2B buyers must navigate several nuances that may affect quality assurance:
-
Regional Standards Compliance: Different regions may have varying quality standards and regulatory requirements. For example, locks sold in Europe must meet CE marking requirements, while those in the United States may need to comply with ANSI standards. Understanding these differences is crucial for ensuring product compliance.
-
Cultural and Language Barriers: Communication challenges can arise when dealing with suppliers from different countries. Buyers should ensure that quality specifications are clearly defined and understood by all parties to avoid misunderstandings that could impact quality.
-
Supply Chain Transparency: Buyers should seek suppliers who maintain transparency in their supply chain, allowing for traceability of materials and processes. This transparency helps buyers assess potential risks and ensure compliance with their quality standards.
In conclusion, understanding the manufacturing processes and quality assurance measures for different lock types is essential for B2B buyers. By focusing on material preparation, forming, assembly, and finishing, along with adhering to international quality standards and implementing rigorous quality control measures, buyers can ensure they are sourcing reliable and secure locking solutions.
Practical Sourcing Guide: A Step-by-Step Checklist for ‘different lock types’
In the ever-evolving landscape of security, selecting the right lock type is paramount for businesses looking to protect their assets. This guide provides a comprehensive checklist for international B2B buyers, particularly from Africa, South America, the Middle East, and Europe. By following these steps, you can ensure that your procurement process is efficient, informed, and aligned with best practices.
Step 1: Define Your Security Needs
Understanding your specific security requirements is the first step in the procurement process. Identify the areas you need to secure—such as external doors, internal access points, or sensitive storage areas. Different lock types offer varying levels of security; for example, deadbolts provide higher security than knob locks.
- Consider the threat level: Assess the potential risks your business faces, including burglary or unauthorized access.
- Evaluate environmental factors: Determine whether locks will be exposed to harsh weather conditions, which may affect your choice of materials.
Step 2: Research Different Lock Types
Familiarize yourself with the various types of locks available in the market. Understanding the differences between padlocks, deadbolts, mortice locks, and electronic locks will enable you to make informed decisions.
- Compare features and benefits: For instance, mortice locks are embedded within the door for added security, while padlocks offer portability.
- Review industry standards: Look for locks that comply with local regulations and international standards, such as BS3621 in the UK.
Step 3: Evaluate Potential Suppliers
Before making a purchase, thoroughly vet potential suppliers. This step is critical to ensure you are sourcing quality products that meet your specifications.
- Request company profiles: Ask for information about their manufacturing processes, quality control measures, and certifications.
- Seek references: Contact previous clients or industry peers who have purchased similar products to gauge supplier reliability.
Step 4: Verify Product Certifications
Ensure that the locks you are considering are certified for quality and security. Certifications can be an indicator of a lock’s performance against common burglary techniques.
- Look for recognized standards: Check for certifications such as CE marking in Europe or ANSI/BHMA ratings in the USA.
- Assess warranty and guarantees: Quality suppliers often provide warranties that reflect their confidence in product durability.
Step 5: Request Samples and Conduct Testing
Before finalizing your order, request samples of the locks you are considering. Testing the locks in real-world scenarios can reveal their effectiveness and ease of use.
- Evaluate lock performance: Check for ease of installation, functionality, and durability.
- Gather feedback from staff: Involve your team in the testing process to ensure the locks meet operational needs and usability.
Step 6: Negotiate Terms and Pricing
Once you have selected a supplier and tested the products, it’s time to discuss pricing and contractual terms. Effective negotiation can lead to better pricing and favorable terms for your business.
- Consider bulk purchase discounts: Many suppliers offer reduced rates for larger orders, which can significantly lower your overall costs.
- Clarify delivery timelines and support: Ensure that your supplier can meet your delivery requirements and provide ongoing support.
Step 7: Plan for Installation and Maintenance
Finally, consider how the locks will be installed and maintained over time. A good lock is only effective if it is properly installed and regularly serviced.
- Hire professional installers: Ensure that experienced professionals handle the installation to avoid common pitfalls.
- Establish a maintenance schedule: Regular checks and servicing can prolong the lifespan of your locks and ensure they function optimally.
By following this practical checklist, international B2B buyers can navigate the complexities of sourcing different lock types effectively, ensuring robust security solutions tailored to their specific needs.
Comprehensive Cost and Pricing Analysis for different lock types Sourcing
What Are the Key Cost Components in Lock Manufacturing?
When sourcing different types of locks, understanding the cost structure is essential for B2B buyers. The primary cost components include:
-
Materials: This encompasses the raw materials used, such as steel, brass, or zinc alloys. The quality of materials significantly affects the lock’s durability and security features.
-
Labor: Labor costs vary based on the region of manufacturing. Skilled labor might be required for high-security locks, impacting overall pricing.
-
Manufacturing Overhead: This includes indirect costs associated with production, such as utilities, equipment maintenance, and facility costs. Efficient production methods can help minimize these overheads.
-
Tooling: The initial investment in tools and machinery for lock production can be substantial. Custom designs may require specialized tools, increasing costs.
-
Quality Control (QC): Ensuring that locks meet safety standards and performance specifications necessitates rigorous quality control measures, which can add to the total cost.
-
Logistics: The transportation of locks from manufacturing sites to buyers impacts pricing. Factors such as shipping distance, mode of transport, and tariffs can vary significantly based on the region.
-
Margin: Suppliers will include a profit margin in their pricing, which can differ based on market dynamics and competition.
How Do Price Influencers Affect Lock Pricing?
Several factors influence the pricing of locks in the international B2B market:
-
Volume/MOQ (Minimum Order Quantity): Purchasing in bulk often leads to lower per-unit costs. Negotiating MOQs can yield better pricing for larger orders.
-
Specifications and Customization: Custom locks tailored to specific requirements typically incur higher costs. Standardized products often offer more competitive pricing.
-
Material Quality and Certifications: High-quality materials and certifications (e.g., ISO, ANSI, or BS3621 for mortice locks) can drive prices up, but they also ensure better security and longevity.
-
Supplier Factors: The reputation, reliability, and geographical location of suppliers can affect pricing. Established suppliers may charge more due to their credibility.
-
Incoterms: Understanding Incoterms is crucial for international transactions. They define responsibilities for shipping, insurance, and tariffs, which can significantly impact total costs.
What Are the Best Negotiation Strategies for B2B Buyers?
For international buyers, particularly those from Africa, South America, the Middle East, and Europe, effective negotiation strategies can lead to cost savings:
-
Understand Total Cost of Ownership (TCO): TCO includes not just the purchase price but also installation, maintenance, and potential replacement costs. A higher initial investment in quality locks may result in lower long-term expenses.
-
Leverage Supplier Relationships: Building strong relationships with suppliers can lead to better pricing and terms over time. Regular communication can also facilitate negotiations for discounts.
-
Request Multiple Quotes: Obtaining quotes from several suppliers allows for comparison and can provide leverage in negotiations. Highlighting competitive offers can encourage better pricing.
-
Be Aware of Regional Market Trends: Understanding local market conditions can help in negotiating effectively. For instance, buyers in Europe may face different pricing dynamics compared to those in Africa or South America.
What Pricing Nuances Should International Buyers Consider?
International B2B buyers must be aware of specific pricing nuances:
-
Currency Fluctuations: Prices may vary significantly based on currency exchange rates. Buyers should consider hedging strategies to mitigate risks associated with currency volatility.
-
Import Duties and Tariffs: These can add substantial costs to imported locks. Understanding the applicable duties can help in budgeting and pricing negotiations.
-
Shipping and Handling Fees: International shipping can be costly. Opting for consolidated shipments can reduce expenses.
-
Cultural Considerations: Different regions may have varying expectations regarding negotiation styles and pricing transparency. Understanding cultural nuances can aid in smoother negotiations.
Disclaimer on Indicative Prices
Prices for locks can vary widely based on factors like design complexity, materials used, and market conditions. For example, while a 5-lever mortice deadlock may start at approximately £26 in the UK, similar locks in Africa or South America may have different pricing structures due to local manufacturing costs and market demand. Always consult multiple suppliers to obtain accurate pricing tailored to specific needs.
Alternatives Analysis: Comparing different lock types With Other Solutions
Introduction: Understanding Alternatives to Traditional Lock Types
In the evolving landscape of security solutions, businesses must evaluate not only traditional lock types but also alternative technologies that provide comparable or superior protection. This analysis focuses on comparing various lock types with modern security solutions, helping international B2B buyers from regions like Africa, South America, the Middle East, and Europe make informed decisions tailored to their specific needs.
Comparison of Different Lock Types Against Alternative Solutions
Comparison Aspect | Different Lock Types | Smart Lock Technology | Biometric Security Systems |
---|---|---|---|
Performance | Varies by type; generally reliable | High, with remote access | Extremely high; unique to each user |
Cost | Moderate; £26-£150+ per unit | Higher initial investment | High due to technology costs |
Ease of Implementation | Moderate; requires installation | Generally easy; requires Wi-Fi | Complex; may need professional installation |
Maintenance | Low; occasional servicing | Moderate; requires updates | Moderate; sensor checks needed |
Best Use Case | Standard security for doors | Residential/commercial entry points | High-security areas requiring strict access control |
In-Depth Analysis of Alternatives
What Are the Advantages of Smart Lock Technology?
Smart lock technology offers significant advantages over traditional locks, particularly in terms of convenience and remote accessibility. Users can control access through smartphones or keypads, allowing for easy entry without physical keys. However, smart locks come with a higher initial cost and dependency on power and internet connectivity. They may also be vulnerable to hacking, necessitating robust cybersecurity measures.
Why Consider Biometric Security Systems?
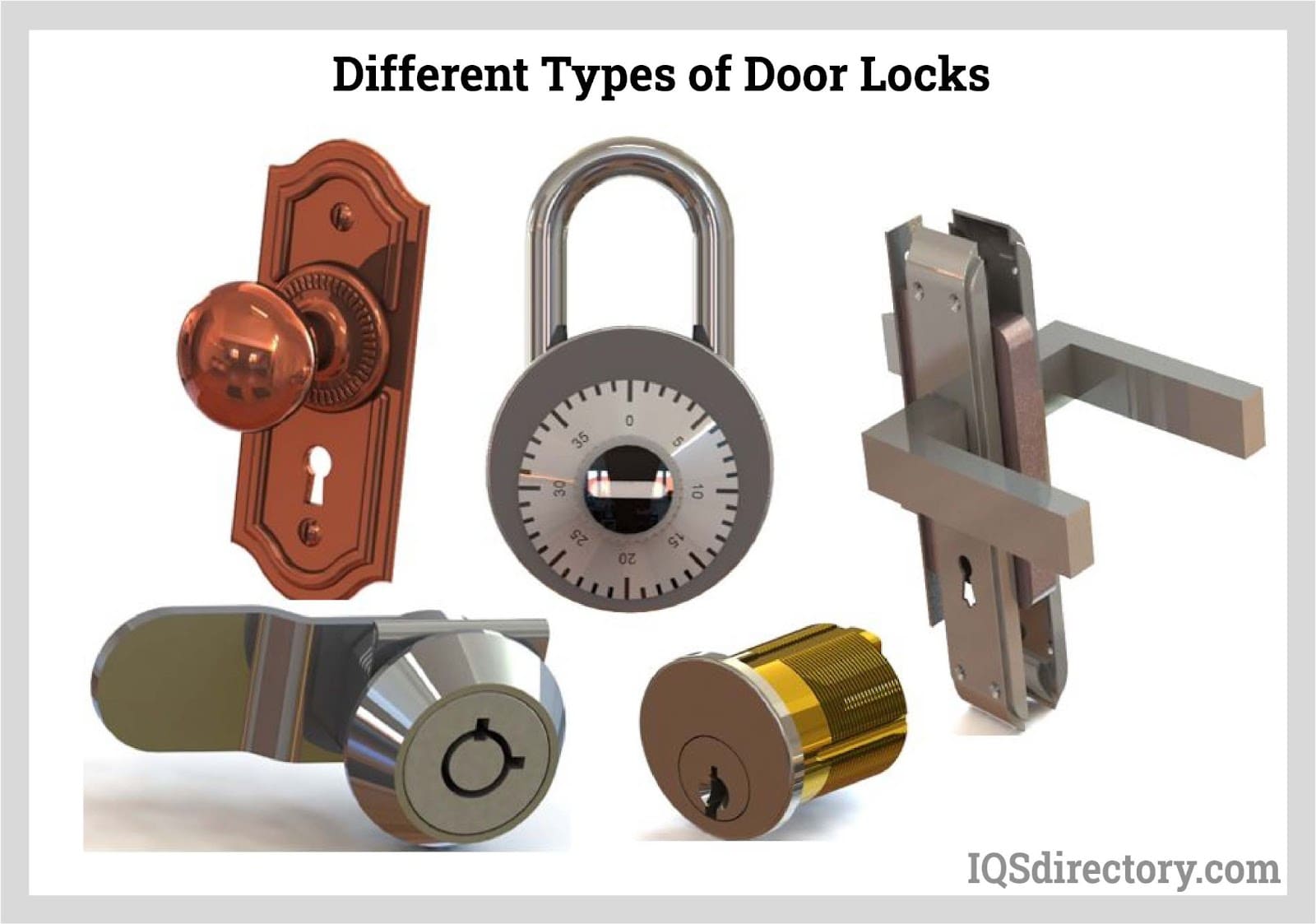
A stock image related to different lock types.
Biometric security systems, which use fingerprint, facial recognition, or iris scans, provide unparalleled security by ensuring that only authorized users can gain access. This technology is ideal for high-security environments, such as data centers or financial institutions. While the performance is exceptional, the installation process can be complex and costly, making it a significant investment. Additionally, maintenance is necessary to ensure sensors function correctly, which could lead to increased operational costs.
Conclusion: How to Choose the Right Security Solution
When selecting the right security solution, B2B buyers must assess their unique requirements, including the level of security needed, budget constraints, and the ease of implementation. Traditional lock types may still be suitable for many businesses, especially where cost and simplicity are priorities. However, for those seeking advanced security features and convenience, smart locks or biometric systems may offer compelling benefits. By carefully evaluating these options against their specific operational needs, businesses can enhance their security posture effectively.
Essential Technical Properties and Trade Terminology for different lock types
What Are the Key Technical Properties of Different Lock Types?
Understanding the technical properties of various lock types is essential for B2B buyers looking to ensure security and reliability. Here are some critical specifications to consider:
-
Material Grade
The material used in lock manufacturing significantly impacts durability and security. Common materials include brass, stainless steel, and zinc alloys. For example, stainless steel locks are more resistant to corrosion, making them ideal for outdoor applications in humid climates like those found in parts of Africa and South America. Choosing the right material grade can enhance the lifespan of locks, reducing replacement costs over time. -
Security Rating
Many locks come with security ratings that indicate their resistance to forced entry and tampering. These ratings are often determined by standardized tests, such as those conducted by organizations like the British Standards Institute (BSI). Locks with higher ratings (e.g., BS3621) typically provide better security. Understanding these ratings helps buyers select locks that meet specific security needs, especially in high-risk areas. -
Tolerance Levels
Tolerance refers to the permissible limits of variation in a lock’s dimensions and operation. High-tolerance locks ensure precise fit and function, reducing the risk of jamming or malfunction. This is particularly important for locks used in commercial applications where reliability is critical. Buyers should verify the tolerance specifications to avoid issues during installation and operation. -
Latch and Bolt Types
Different locks utilize various mechanisms, such as deadbolts, spring latches, or electronic bolts. Each type has distinct advantages and disadvantages regarding security and convenience. For instance, deadbolts provide superior security but can be less convenient than electronic locks that offer keyless entry. Understanding the operational mechanisms helps buyers choose locks that align with their security protocols and user needs. -
Finish and Coating
The finish of a lock can affect both aesthetics and functionality. Locks may be coated with finishes such as nickel, chrome, or powder coating to enhance appearance and protect against wear. Buyers should consider the environmental conditions where the locks will be installed; for example, powder-coated locks may be better suited for outdoor use in coastal regions due to their corrosion resistance.
What Are Common Trade Terms Related to Lock Types?
Familiarity with industry terminology is vital for effective communication between buyers and suppliers. Here are some common trade terms relevant to lock purchasing:
-
OEM (Original Equipment Manufacturer)
OEM refers to companies that produce parts or equipment that may be marketed by another manufacturer. Understanding OEM relationships can help buyers identify reputable lock suppliers and ensure product quality. -
MOQ (Minimum Order Quantity)
MOQ is the smallest number of units a supplier is willing to sell. This term is crucial for B2B buyers, as it affects inventory management and cash flow. Knowing the MOQ helps buyers negotiate better terms and avoid overstocking or understocking issues. -
RFQ (Request for Quotation)
An RFQ is a document used to solicit price quotations from suppliers for specific products or services. This process allows buyers to compare costs and terms from multiple suppliers, ensuring they make informed purchasing decisions. -
Incoterms (International Commercial Terms)
Incoterms define the responsibilities of buyers and sellers in international transactions, particularly regarding shipping and delivery. Familiarity with these terms can help buyers mitigate risks associated with logistics, particularly in regions with complex trade regulations.
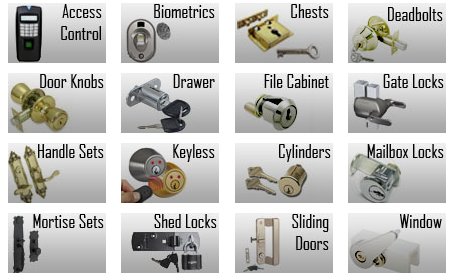
A stock image related to different lock types.
-
Lead Time
Lead time refers to the time taken from placing an order to receiving the goods. Understanding lead times is essential for effective project planning, especially for buyers in sectors where timely delivery is critical. -
Certification Standards
Certification standards, such as ISO or ANSI, provide guidelines on the quality and safety of locks. Buyers should look for locks that comply with relevant certification standards to ensure they meet industry expectations and regulatory requirements.
By grasping these technical properties and trade terms, international B2B buyers can make informed decisions when selecting locks, ultimately enhancing their security solutions.
Navigating Market Dynamics and Sourcing Trends in the different lock types Sector
What Are the Global Drivers Influencing the Lock Types Market?
The lock types market is influenced by several global drivers, including urbanization, increasing security concerns, and technological advancements. As cities expand, the need for effective security solutions for residential and commercial properties grows. This trend is particularly evident in developing regions like Africa and South America, where crime rates can be higher, prompting businesses and consumers to invest in robust locking mechanisms. Moreover, the rise of smart technologies has led to the emergence of smart locks, which are gaining traction in Europe and the Middle East due to their convenience and enhanced security features.
Current and emerging B2B tech trends include the integration of IoT (Internet of Things) into locking solutions. Smart locks, capable of remote access and monitoring, are appealing to businesses looking to streamline operations and enhance security. Additionally, blockchain technology is being explored for secure transaction processing in lock manufacturing and distribution, ensuring transparency and trust in supply chains.
International B2B buyers should also consider the growing importance of regional certifications and standards, such as the BS3621 in the UK, which ensures that locks meet certain security requirements. Understanding these market dynamics allows buyers to make informed sourcing decisions tailored to their regional needs.
How Is Sustainability and Ethical Sourcing Reshaping the Lock Types Market?
Sustainability and ethical sourcing are increasingly significant in the lock types sector. The environmental impact of manufacturing processes, including resource depletion and waste generation, is prompting manufacturers to adopt greener practices. B2B buyers are becoming more discerning, often prioritizing suppliers that demonstrate a commitment to sustainability.
The importance of ethical supply chains cannot be overstated. Buyers from Africa, South America, and the Middle East are particularly focused on sourcing from companies that ensure fair labor practices and responsible sourcing of materials. Certifications such as ISO 14001, which focuses on effective environmental management systems, are becoming essential for suppliers seeking to appeal to conscientious buyers.
Moreover, the use of ‘green’ materials, such as recycled metals and eco-friendly coatings, is gaining traction. Buyers should look for products that are certified to meet environmental standards, as this not only enhances brand reputation but also aligns with the growing consumer demand for sustainable products. By prioritizing sustainability, B2B buyers can contribute to reducing the industry’s overall environmental footprint while ensuring compliance with evolving regulations.
What Is the Brief Evolution of Lock Types and Their Significance in B2B?
The evolution of lock types can be traced back to ancient civilizations, where simple mechanical devices were used to secure valuables. Over the centuries, advancements in metallurgy and engineering led to the development of more sophisticated locking mechanisms. The 19th century saw the introduction of pin-tumbler locks, which remain popular today due to their effectiveness and reliability.
In recent years, the focus has shifted towards digital and smart locks, driven by the need for enhanced security and convenience in an increasingly connected world. These modern locks not only provide traditional security but also integrate features such as keyless entry and remote monitoring, making them invaluable for businesses looking to enhance their operational efficiency.
As the lock industry continues to innovate, B2B buyers must stay informed about the latest developments and trends. Understanding the historical context of lock types enables buyers to appreciate the advancements made and how they can leverage these innovations to meet their security needs effectively.
Frequently Asked Questions (FAQs) for B2B Buyers of different lock types
-
How do I choose the right lock type for my business needs?
Choosing the right lock type involves assessing your security requirements and the environment in which the lock will be installed. For high-security needs, consider deadbolts or mortice locks that conform to industry standards. For portable security, padlocks may be ideal. Evaluate factors such as door material, usage frequency, and potential vulnerabilities. Consult with suppliers to understand the features of various lock types, and ensure they align with your risk management strategy. -
What is the best lock type for outdoor commercial applications?
For outdoor commercial applications, deadbolts and padlocks are generally the best options. Deadbolts provide strong security against forced entry, especially when installed on solid doors. Look for deadbolts that are weather-resistant and have a high ANSI grade rating. Padlocks are also effective for securing gates or storage units; opt for shrouded padlocks to resist cutting. Always ensure that the chosen locks are suited for the specific environmental conditions of your location. -
How can I ensure the locks I purchase are of high quality?
To ensure high-quality locks, look for products that meet recognized industry standards, such as ANSI or BS3621 certifications. Research reputable manufacturers with a proven track record in the lock industry. Request product samples for testing and evaluate their durability and functionality. Additionally, consider reading customer reviews and seeking recommendations from other B2B buyers in your region to gauge reliability. -
What are the minimum order quantities (MOQ) for different lock types?
Minimum order quantities (MOQ) can vary significantly based on the manufacturer and the type of lock. Typically, MOQs range from 50 to 500 units for bulk orders. When negotiating with suppliers, inquire about MOQs for specific lock types and whether they offer flexibility for smaller orders or trial purchases. Understanding MOQs is crucial for budgeting and inventory management, especially for new product lines. -
What payment terms should I expect when sourcing locks internationally?
Payment terms can vary based on the supplier’s policies and the buyer’s relationship with them. Common terms include 30% upfront payment with the balance due upon delivery, or net 30 to net 60 days after invoice. Some suppliers may offer payment through letters of credit for larger transactions, providing added security. Always clarify payment terms upfront to avoid misunderstandings and ensure smooth transactions. -
How do I vet suppliers for purchasing different lock types?
Vetting suppliers involves assessing their reputation, product quality, and reliability. Start by checking their credentials, certifications, and industry experience. Request references from previous clients and conduct background checks. Evaluate their customer service and responsiveness by reaching out with inquiries. Additionally, consider visiting their manufacturing facilities if possible, to observe production processes and quality control measures in place. -
What customization options are available for locks?
Many manufacturers offer customization options, including lock finishes, keying systems, and branding. Common customizations include the ability to have locks keyed alike or to specific key codes for enhanced security. Some suppliers may also provide options for specific sizes or features tailored to your business needs. Discuss your requirements with potential suppliers to explore available customization options and associated costs. -
What logistics considerations should I keep in mind when importing locks?
When importing locks, consider logistics aspects such as shipping methods, customs regulations, and delivery timelines. Choose reliable freight forwarders familiar with international trade laws, particularly in your region. Ensure that all necessary documentation, including import permits and customs declarations, is prepared in advance to avoid delays. Additionally, factor in potential tariffs and duties that may affect your overall cost.
Important Disclaimer & Terms of Use
⚠️ Important Disclaimer
The information provided in this guide, including content regarding manufacturers, technical specifications, and market analysis, is for informational and educational purposes only. It does not constitute professional procurement advice, financial advice, or legal advice.
While we have made every effort to ensure the accuracy and timeliness of the information, we are not responsible for any errors, omissions, or outdated information. Market conditions, company details, and technical standards are subject to change.
B2B buyers must conduct their own independent and thorough due diligence before making any purchasing decisions. This includes contacting suppliers directly, verifying certifications, requesting samples, and seeking professional consultation. The risk of relying on any information in this guide is borne solely by the reader.
Strategic Sourcing Conclusion and Outlook for different lock types
In conclusion, understanding the diverse types of locks available in the market is crucial for international B2B buyers seeking to enhance security. From the robust 5 Lever Mortice Deadlocks, which are preferred for their reliability and security standards, to the versatile deadbolts and portable padlocks, each lock type serves specific needs and environments. Buyers should prioritize sourcing locks that not only meet local security standards but also address the unique security challenges faced in their regions, particularly in Africa, South America, the Middle East, and Europe.
Why is Strategic Sourcing Important for Lock Purchases?
Strategic sourcing enables businesses to evaluate suppliers based on quality, compliance, and cost-effectiveness, ensuring that the locks they purchase provide maximum security without exceeding budget constraints. Engaging with reputable manufacturers and suppliers can yield better pricing, reliable delivery, and superior customer support.
How Can International Buyers Prepare for Future Security Needs?
Looking ahead, the demand for advanced locking mechanisms will continue to grow as businesses prioritize security in an increasingly volatile world. International buyers are encouraged to stay informed about emerging technologies and trends in lock security, such as smart locks and biometric systems. By proactively sourcing innovative solutions, businesses can secure their assets and maintain a competitive edge.
Take the next step in your strategic sourcing journey by evaluating your current lock systems and exploring options that align with your security needs and budget.