Discover Force Sensing: The Complete Buyer’s Guide (2025)
Introduction: Navigating the Global Market for force sensing
In an increasingly interconnected world, sourcing reliable force sensing technologies can pose significant challenges for international B2B buyers, particularly those operating in diverse markets like Africa, South America, the Middle East, and Europe. With applications ranging from healthcare and automotive to consumer electronics and industrial automation, understanding the nuances of force sensing is crucial for making informed purchasing decisions. This guide aims to demystify the complexities of force sensing by covering various types of sensors, including strain gauge, piezoresistive, capacitive, and piezoelectric technologies, as well as their specific applications across industries.
Navigating the global market for force sensing also requires a keen understanding of supplier vetting processes, cost considerations, and integration challenges. By providing actionable insights into these areas, this guide empowers B2B buyers to identify suitable suppliers, assess product quality, and negotiate favorable terms. Whether you are a procurement officer in Italy looking for advanced medical sensors or a logistics manager in Brazil seeking robust industrial solutions, this comprehensive resource will enhance your sourcing strategy and drive better outcomes for your organization.
Ultimately, the goal is to equip you with the knowledge and tools necessary to leverage force sensing technologies effectively, ensuring that your investments yield maximum return and operational efficiency.
Understanding force sensing Types and Variations
Type Name | Key Distinguishing Features | Primary B2B Applications | Brief Pros & Cons for Buyers |
---|---|---|---|
Strain Gauge Sensors | Utilize thin wires or foils to measure strain; high accuracy | Load cells, pressure measurement | Pros: High precision, widely used. Cons: Sensitive to temperature changes. |
Piezoresistive Sensors | Change resistance based on applied force; compact design | Medical devices, robotics | Pros: High sensitivity, suitable for small applications. Cons: Limited range. |
Capacitive Sensors | Measure changes in capacitance; ideal for small force detection | Touchscreens, proximity sensors | Pros: Low power consumption, excellent for delicate applications. Cons: Affected by environmental factors. |
Piezoelectric Sensors | Generate voltage with mechanical stress; fast response time | Vibration monitoring, impact detection | Pros: High-speed response, good for dynamic force measurement. Cons: Limited to dynamic applications. |
Optical Force Sensors | Use light changes to measure force; non-contact measurement | Biomechanics, material testing | Pros: Non-invasive, high accuracy. Cons: Higher cost, sensitive to light interference. |
What are Strain Gauge Sensors and Their B2B Suitability?
Strain gauge sensors are renowned for their precision in measuring mechanical strain. These sensors are typically used in load cells and pressure measurement devices, making them essential for industries like manufacturing and construction. For B2B buyers, understanding the temperature sensitivity of strain gauges is crucial, as fluctuations can affect accuracy. Companies seeking reliable, high-precision measurements will find strain gauges to be a dependable choice, but they must account for environmental conditions during installation.
How Do Piezoresistive Sensors Work in B2B Applications?
Piezoresistive sensors utilize materials like silicon that alter their resistance in response to applied force. This makes them particularly suitable for applications in medical devices and robotics, where compact size and high sensitivity are essential. B2B purchasers should consider the calibration process and the specific force range required for their applications, as these sensors may have limitations in terms of maximum load capacity. Their ability to provide accurate readings in small-scale applications makes them a valuable asset in precision-driven industries.
Why Choose Capacitive Sensors for Your Business Needs?
Capacitive sensors are designed to detect changes in capacitance caused by applied force, making them ideal for touchscreens and proximity sensors. They are particularly advantageous in low-power applications, which is beneficial for businesses focused on energy efficiency. However, B2B buyers should be aware that environmental factors, such as humidity and dust, can affect sensor performance. Understanding the operational environment is key when selecting capacitive sensors for applications that require consistent and reliable performance.
What Advantages Do Piezoelectric Sensors Offer for Dynamic Measurements?
Piezoelectric sensors are unique in that they generate a voltage when subjected to mechanical stress, making them suitable for applications involving vibration monitoring and impact detection. Their fast response time is a significant advantage in dynamic environments, such as automotive testing or robotics. However, they are best suited for dynamic rather than static force measurements, which B2B buyers should keep in mind when evaluating their application needs. Companies looking for sensors that can handle rapid changes in force will benefit from piezoelectric technology.
How Do Optical Force Sensors Stand Out in the Market?
Optical force sensors measure force by detecting changes in light properties, offering a non-contact measurement solution. This technology is particularly useful in biomechanics and material testing, where precision and non-invasiveness are critical. For B2B buyers, the higher initial cost and sensitivity to light interference are important considerations. However, the accuracy and flexibility of optical sensors make them an attractive option for companies looking to invest in advanced measurement technologies that require minimal physical interaction.
Key Industrial Applications of force sensing
Industry/Sector | Specific Application of Force Sensing | Value/Benefit for the Business | Key Sourcing Considerations for this Application |
---|---|---|---|
Automotive | Load Testing in Vehicle Manufacturing | Enhances safety and performance through precise load analysis. | Calibration requirements, environmental durability. |
Healthcare | Patient Monitoring Systems | Improves patient outcomes through accurate force measurements during rehabilitation. | Compliance with medical standards, biocompatibility. |
Robotics | Gripping and Manipulation Systems | Increases efficiency and precision in automated processes. | Sensor integration compatibility, response time. |
Consumer Electronics | Touchscreen Interfaces | Enhances user experience by providing responsive touch feedback. | Size constraints, sensitivity, and cost-effectiveness. |
Aerospace | Structural Integrity Testing | Ensures safety and reliability of aircraft components. | Certification standards, weight limitations. |
How is Force Sensing Used in Automotive Load Testing?
In the automotive sector, force sensing is pivotal for load testing during vehicle manufacturing. These sensors help engineers measure the load exerted on different vehicle components, ensuring they can withstand operational stresses. By providing precise data on structural integrity, force sensors enhance safety and performance. For international buyers, sourcing requires an understanding of calibration processes and the environmental durability of sensors, especially in regions with varying climates.
What Role Does Force Sensing Play in Healthcare Monitoring Systems?
Force sensing is increasingly utilized in healthcare, particularly in patient monitoring systems, where it measures forces exerted during physical rehabilitation exercises. This technology allows for real-time feedback on a patient’s performance, leading to improved recovery outcomes. Buyers in the healthcare sector must consider compliance with medical device standards and ensure the biocompatibility of materials used in force sensors, especially in regions like Europe where regulations are stringent.
How is Force Sensing Transforming Robotics?
In robotics, force sensing is integral to gripping and manipulation systems, allowing robots to adapt their grip based on the object’s weight and texture. This capability increases efficiency and precision in automated processes, such as assembly lines or packaging. For B2B buyers, the key sourcing considerations include ensuring compatibility with existing robotic systems and evaluating the sensors’ response times to maintain operational efficiency.
Why is Force Sensing Critical in Consumer Electronics Touchscreens?
Force sensing technology enhances consumer electronics, particularly in touchscreen interfaces. By measuring the force applied to a screen, these sensors provide a more responsive user experience, allowing for features like pressure-sensitive controls. Buyers must consider factors such as size constraints and the sensitivity of sensors, as well as their cost-effectiveness, particularly in competitive markets in South America and Europe.
What Importance Does Force Sensing Have in Aerospace Structural Testing?
In the aerospace industry, force sensing is crucial for structural integrity testing of aircraft components. Sensors help detect stress points and ensure that materials can endure the forces experienced during flight. This application is vital for maintaining safety and reliability standards. Buyers need to be aware of certification standards and weight limitations when sourcing force sensors, particularly for applications in regions with rigorous aerospace regulations.
3 Common User Pain Points for ‘force sensing’ & Their Solutions
Scenario 1: Navigating Calibration Challenges for Force Sensors
The Problem: A common challenge for B2B buyers in the force sensing market is the calibration of force sensors. Many buyers, particularly in sectors like manufacturing and robotics, encounter difficulties when integrating these sensors into their existing systems. Without proper calibration, the sensors may provide inaccurate readings, leading to flawed data that can affect product quality and operational efficiency. This scenario is particularly frustrating for buyers in regions like Africa and South America, where access to technical support may be limited.
The Solution: To address calibration issues, buyers should prioritize selecting force sensors that come with detailed calibration protocols and support. Before purchasing, inquire about the calibration process and whether the manufacturer provides calibration services or training. Additionally, consider investing in sensors that offer adjustable sensitivity settings, which can be fine-tuned based on specific application needs. For example, utilizing a sensor with a built-in calibration feature can streamline the process, allowing for quick adjustments in the field. Implementing routine calibration checks as part of your maintenance schedule will also ensure consistent performance over time, minimizing operational disruptions.
Scenario 2: Ensuring Compatibility with Existing Systems
The Problem: Many B2B buyers face compatibility issues when integrating force sensors into their existing machinery or software systems. This is especially pertinent for businesses in the Middle East and Europe, where diverse technologies are used across different industries. Incompatibility can lead to increased costs due to required modifications, delays in production, or even the need to replace existing equipment, which can significantly impact the bottom line.
The Solution: To mitigate compatibility issues, conduct thorough research on the specifications of the force sensors before making a purchase. Engage with suppliers to discuss your existing systems and ensure that the sensors you are considering can seamlessly integrate with your current technology stack. Look for sensors that support standard communication protocols such as I2C, SPI, or RS-232, which can facilitate easier integration. Additionally, consider working with suppliers who provide comprehensive technical support and integration services. This partnership can help identify potential issues early and ensure that the integration process is smooth, saving both time and resources.
Scenario 3: Addressing Sensitivity and Accuracy Concerns
The Problem: In applications such as healthcare and automotive, sensitivity and accuracy of force sensors are critical. Buyers often report that their sensors do not meet the required sensitivity levels for specific applications, leading to inaccurate data collection and decision-making. This is particularly challenging in Europe, where regulatory standards demand high precision in measurements for safety and efficacy.
The Solution: To overcome sensitivity and accuracy challenges, it is essential to select force sensors that are designed specifically for the intended application. Buyers should look for sensors that are tested and certified for their specific industry standards. Additionally, engaging in a dialogue with manufacturers about your application requirements can provide insights into the best sensor technology to meet those needs. For instance, piezoresistive sensors may be ideal for high-sensitivity applications, while strain gauge sensors might be better suited for general-purpose measurements. Always request performance data and case studies to ensure that the chosen sensor has a proven track record in similar applications, providing confidence in its accuracy and reliability.
Strategic Material Selection Guide for force sensing
What Are the Key Materials for Force Sensing Applications?
When selecting materials for force sensing applications, it’s essential to consider the specific requirements of the application, including environmental conditions, mechanical properties, and regulatory compliance. Here, we analyze four common materials used in force sensing technology, focusing on their properties, advantages, disadvantages, and implications for international B2B buyers.
How Do Strain Gauges Perform in Force Sensing?
Key Properties: Strain gauges are typically made from metallic foil or wire, offering high sensitivity and a wide range of operating temperatures, usually between -50°C to 200°C. They can withstand significant mechanical stress, making them suitable for various applications.
Pros & Cons: Strain gauges are known for their accuracy and reliability, particularly in load cells. However, they can be sensitive to environmental factors, such as humidity and temperature fluctuations, which may require additional protective coatings. Manufacturing complexity can be moderate, as precise installation is crucial for optimal performance.
Impact on Application: Strain gauges are compatible with various media, including liquids and gases, but their performance may degrade in corrosive environments unless properly protected.
Considerations for International Buyers: Compliance with standards such as ASTM E251 and ISO 376 is critical. Buyers from regions like Africa and South America should ensure that their suppliers can meet local regulations regarding material safety and performance.
What Are the Advantages of Piezoresistive Materials?
Key Properties: Piezoresistive materials, often silicon-based, exhibit a significant change in electrical resistance when subjected to mechanical stress. They operate effectively within a temperature range of -40°C to 125°C and can handle moderate pressures.
Pros & Cons: The primary advantage of piezoresistive sensors is their high sensitivity, making them ideal for applications requiring precise measurements. However, they can be more expensive than other materials and may have limited durability in extreme conditions.
Impact on Application: These materials are particularly suited for applications in the medical and automotive sectors, where precise force measurements are critical. Compatibility with various media is generally good, but caution is advised in highly corrosive environments.
Considerations for International Buyers: Buyers should ensure that piezoresistive sensors comply with international standards such as JIS B 7500 and DIN 1319, particularly in Europe and the Middle East, where regulatory compliance is stringent.
Why Choose Capacitive Materials for Force Sensing?
Key Properties: Capacitive sensors utilize conductive plates to measure changes in capacitance due to applied force. They typically operate effectively within a temperature range of -20°C to 85°C and are less sensitive to environmental conditions compared to other types.
Pros & Cons: Capacitive sensors are generally robust and can be manufactured at a lower cost. However, they may require careful calibration and can be less effective in high-pressure applications.
Impact on Application: These sensors are widely used in consumer electronics, such as touchscreens, but may not be suitable for applications involving heavy loads or extreme environmental conditions.
Considerations for International Buyers: Compliance with standards like IEC 61000-6-3 is essential for capacitive sensors. Buyers should also consider the availability of local suppliers, particularly in regions with emerging markets such as Africa and South America.
How Do Piezoelectric Materials Contribute to Force Sensing?
Key Properties: Piezoelectric materials generate an electrical charge in response to applied mechanical stress. They can operate over a wide temperature range, typically -40°C to 120°C, and are particularly effective for dynamic force measurements.
Pros & Cons: The main advantage of piezoelectric sensors is their ability to measure rapid changes in force, making them suitable for applications in automotive and aerospace industries. However, they are less effective for static measurements and can be sensitive to temperature changes.
Impact on Application: Piezoelectric sensors are ideal for impact detection and vibration monitoring, but their performance may be compromised in static load applications.
Considerations for International Buyers: Buyers should ensure compliance with relevant standards such as ASTM E2623 and ISO 16063, especially in Europe, where quality assurance is critical.
Summary Table of Material Selection for Force Sensing
Material | Typical Use Case for Force Sensing | Key Advantage | Key Disadvantage/Limitation | Relative Cost (Low/Med/High) |
---|---|---|---|---|
Strain Gauge | Load cells, pressure sensors | High accuracy and reliability | Sensitive to environmental factors | Medium |
Piezoresistive | Medical devices, automotive sensors | High sensitivity | More expensive, limited durability | High |
Capacitive | Touchscreens, consumer electronics | Robust and cost-effective | Requires careful calibration | Low |
Piezoelectric | Impact detection, vibration monitoring | Excellent for dynamic measurements | Poor for static measurements | Medium |
This strategic material selection guide provides B2B buyers with actionable insights into the various materials used in force sensing applications, helping them make informed decisions tailored to their specific needs and regional compliance requirements.
In-depth Look: Manufacturing Processes and Quality Assurance for force sensing
What are the Main Stages of the Manufacturing Process for Force Sensing Devices?
The manufacturing process for force sensing devices involves several key stages: material preparation, forming, assembly, and finishing. Each stage plays a critical role in ensuring the performance and reliability of the final product.
Material Preparation: What Materials are Used in Force Sensors?
The first step in manufacturing force sensors is selecting the appropriate materials. Common materials include semi-conductive inks for force sensing resistors, metals for strain gauges, and specialized polymers for capacitive sensors. The chosen materials must exhibit specific properties such as sensitivity, durability, and environmental resistance.
During material preparation, manufacturers often conduct a thorough evaluation of raw materials, ensuring they meet the necessary specifications and industry standards. This can involve chemical analysis, mechanical testing, and supplier audits to guarantee material quality.
How is the Forming Process Conducted in Force Sensor Manufacturing?
The forming process varies depending on the type of force sensor being produced. For instance, in the case of strain gauge sensors, thin wires or foils are bonded to a substrate, and the assembly is subjected to various mechanical processes such as etching and lamination to create the desired sensor structure.
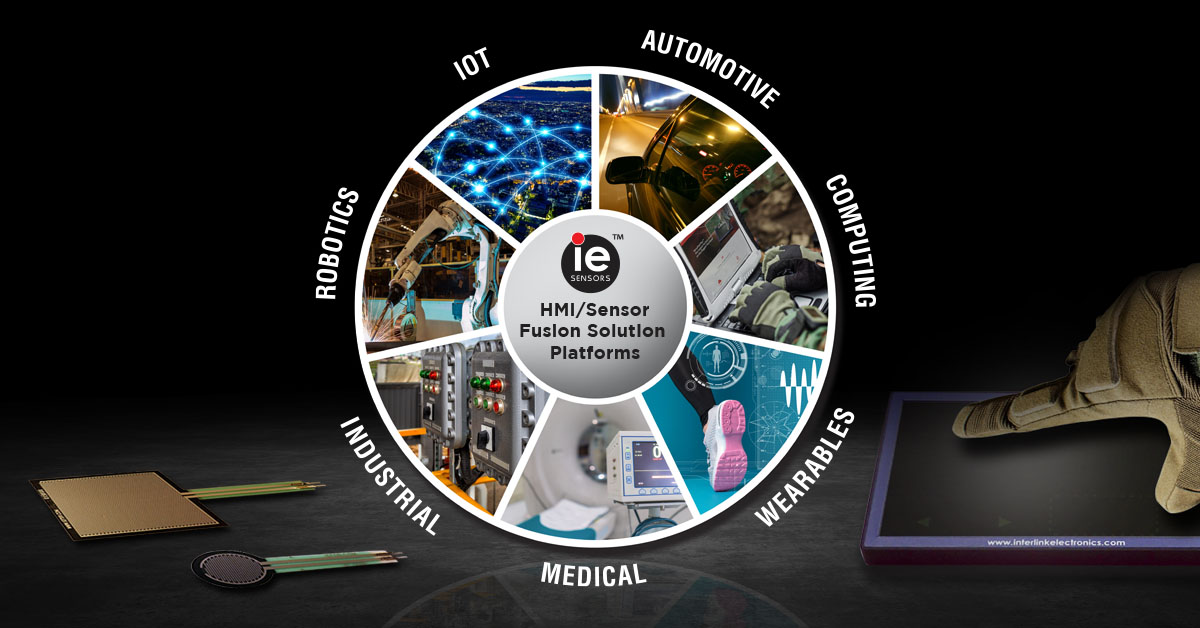
A stock image related to force sensing.
For piezoresistive sensors, a semi-conductive material is typically deposited onto flexible substrates using techniques like screen printing or inkjet printing. This stage is crucial for defining the sensor’s sensitivity and response characteristics. Manufacturers also utilize advanced techniques such as laser cutting or CNC machining to achieve precise dimensions and shapes.
What Does the Assembly Stage Involve for Force Sensors?
The assembly stage is where the various components of the sensor are integrated. This may include attaching electronic components, encapsulating the sensor in protective housing, and ensuring proper alignment of sensing elements.
Quality checks are critical during this stage, as even minor misalignments can lead to significant performance issues. Automated assembly processes are common, but manual assembly may still be employed for more complex sensors.
How is the Finishing Process Implemented in Force Sensor Production?
Finishing involves surface treatments, calibration, and packaging. This stage ensures that the sensors meet aesthetic and functional requirements. Calibration is particularly important, as it aligns the sensor’s output with known force measurements.
Manufacturers may use specialized calibration rigs to apply known forces while recording the sensor’s output, ensuring accurate performance. Finally, the sensors are packaged for shipment, which includes protective measures to prevent damage during transit.
What Quality Assurance Standards Should International B2B Buyers Consider?
Quality assurance in force sensor manufacturing is paramount. Buyers should look for adherence to international standards like ISO 9001, which outlines requirements for a quality management system. Compliance with such standards indicates a commitment to quality and continuous improvement.
What Industry-Specific Certifications are Important for Force Sensors?
In addition to ISO standards, certain industry-specific certifications may be relevant, depending on the application. For example, CE marking is essential for products sold in the European market, signifying compliance with safety and environmental standards. Similarly, API certification may be necessary for sensors used in the oil and gas industry.
Buyers should inquire about these certifications during the supplier selection process, as they provide reassurance regarding the product’s quality and reliability.
What Quality Control Checkpoints are Crucial in the Manufacturing Process?
Quality control (QC) checkpoints are integral to ensuring the final product meets quality standards. Typical checkpoints include:
-
Incoming Quality Control (IQC): This involves inspecting raw materials before they enter the production process. Ensuring that materials meet specifications helps prevent defects later in manufacturing.
-
In-Process Quality Control (IPQC): Throughout the manufacturing process, samples may be tested at various stages to identify any deviations from quality standards. This can include dimensional checks, functional tests, and visual inspections.
-
Final Quality Control (FQC): After assembly, each sensor should undergo final testing to verify its performance against specifications. This includes calibration and functional testing under simulated operational conditions.
What Common Testing Methods are Used in Force Sensor Quality Assurance?
Several testing methods are employed to ensure the quality and reliability of force sensors:
-
Calibration Testing: This involves applying known forces to the sensor and measuring its output to establish a correlation.
-
Environmental Testing: Sensors may be subjected to extreme temperature, humidity, or pressure conditions to evaluate their performance in real-world scenarios.
-
Durability Testing: This includes mechanical stress tests to assess the sensor’s lifespan and reliability under repeated use.
How Can B2B Buyers Verify Supplier Quality Control Processes?
For international B2B buyers, verifying a supplier’s quality control processes is critical. Here are several methods to ensure supplier reliability:
-
Conduct Supplier Audits: Regular audits can help assess compliance with quality standards and identify areas for improvement. Buyers should consider both on-site visits and remote audits.
-
Request Quality Reports: Suppliers should provide documentation of their quality control processes, including test results and certification compliance.
-
Engage Third-Party Inspection Services: Utilizing independent third-party inspectors can provide an objective evaluation of the supplier’s quality practices and product performance.
What are the Quality Control Nuances for International B2B Buyers?
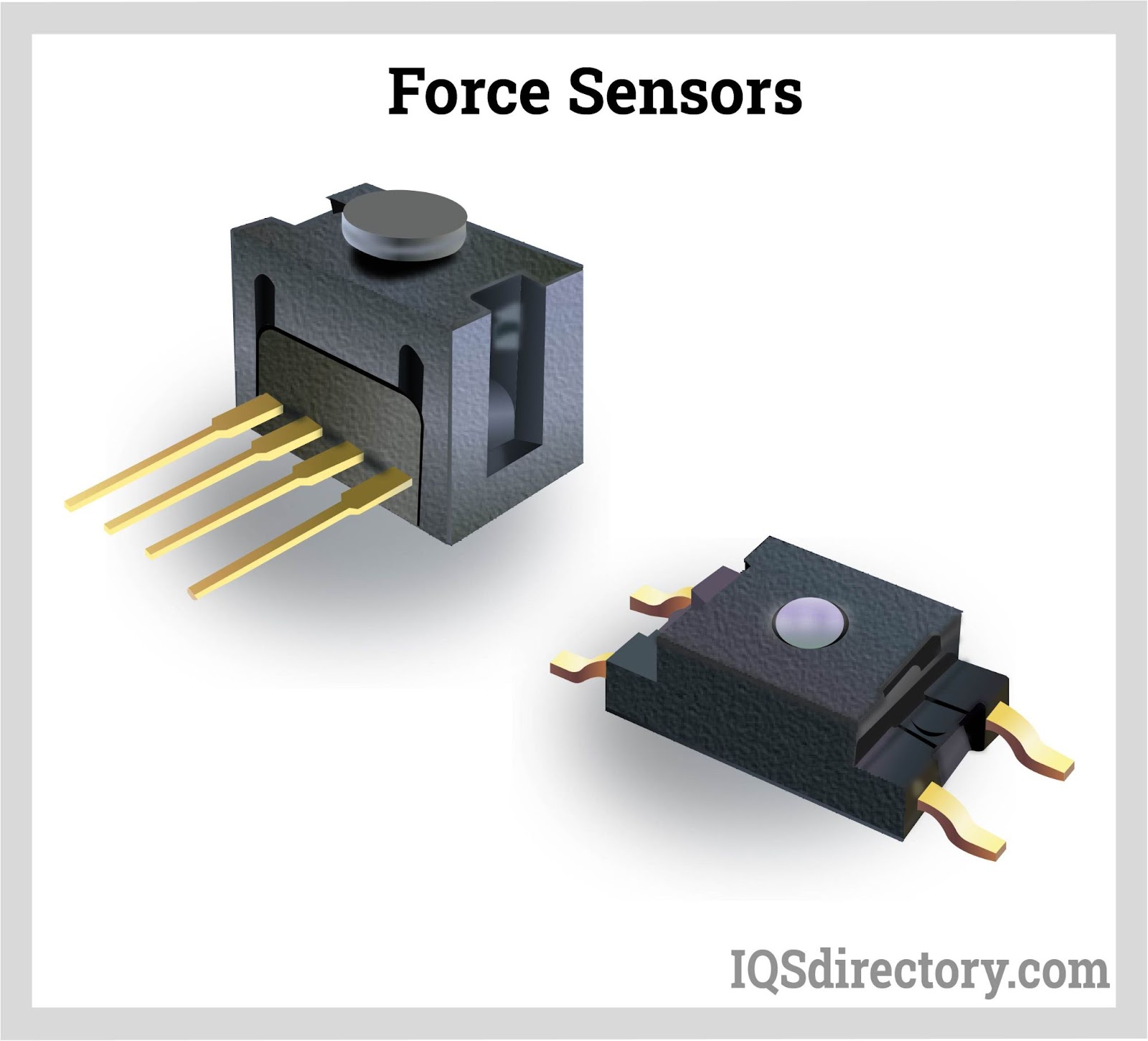
A stock image related to force sensing.
International B2B buyers must navigate various quality control nuances, particularly when sourcing from different regions. For example, buyers from Africa may encounter suppliers with varying levels of adherence to international standards.
In South America and the Middle East, regulatory compliance can differ significantly from European standards. As such, it’s essential for buyers to familiarize themselves with local regulations and certification requirements. Establishing clear communication with suppliers about quality expectations and conducting regular follow-ups can help mitigate potential issues.
By understanding the manufacturing processes and quality assurance practices for force sensing devices, international B2B buyers can make informed purchasing decisions, ensuring they select reliable suppliers that meet their specific needs.
Practical Sourcing Guide: A Step-by-Step Checklist for ‘force sensing’
In today’s competitive landscape, sourcing high-quality force sensing technologies is crucial for businesses aiming to enhance their products or services. This guide outlines a practical checklist for international B2B buyers, particularly those from Africa, South America, the Middle East, and Europe, to navigate the procurement process effectively.
Step 1: Define Your Technical Specifications
Clearly articulating your technical requirements is the first and most important step in sourcing force sensors. Consider the type of force measurement you need—whether it’s for delicate applications like touchscreens or robust environments such as industrial machinery. Specify parameters like sensitivity, measurement range, and form factor to ensure the sensors meet your exact needs.
- Consider the application: Different technologies (strain gauges, piezoresistive, capacitive) serve distinct purposes.
- Identify environmental factors: Temperature, humidity, and potential exposure to chemicals can affect sensor performance.
Step 2: Research Supplier Capabilities
Thoroughly investigate potential suppliers to ensure they have the expertise and resources to meet your needs. Look for manufacturers with a proven track record in the specific type of force sensing technology you require.
- Review their product range: A supplier offering various technologies can provide solutions for different applications.
- Check for innovation: Suppliers that invest in R&D often have more advanced products and better support.
Step 3: Evaluate Potential Suppliers
Before making a commitment, it’s essential to vet suppliers thoroughly. Request company profiles, case studies, and references from buyers in similar industries or regions.
- Ask for testimonials: Positive feedback from existing customers can provide insight into reliability and product performance.
- Investigate their support capabilities: Ensure they offer training, technical support, and a clear return policy.
Step 4: Verify Compliance and Certifications
Ensure that the suppliers comply with international quality standards and certifications relevant to your industry. This is particularly important for sectors such as medical devices, automotive, and aerospace, where precision and reliability are critical.
- Look for ISO certifications: These indicate adherence to quality management principles.
- Check for industry-specific certifications: Depending on your region, specific certifications may be required.
Step 5: Request Samples for Testing
Before finalizing your order, request samples to evaluate their performance in real-world applications. Testing samples allows you to assess sensitivity, response time, and durability under your specific conditions.
- Conduct thorough testing: Evaluate the sensor in conditions that mimic actual usage.
- Document findings: Keep detailed records of performance metrics for future reference.
Step 6: Negotiate Terms and Pricing
Once you’ve identified a suitable supplier, engage in negotiations regarding pricing, delivery timelines, and payment terms. Understanding the full cost of ownership, including maintenance and potential upgrades, is vital for budgeting.
- Consider bulk purchase discounts: Larger orders often qualify for reduced rates.
- Clarify delivery schedules: Timely delivery is crucial to maintain your project timelines.
Step 7: Establish a Long-Term Relationship
After the initial purchase, focus on building a strong relationship with your supplier. Open communication can lead to better service, support, and potential discounts on future orders.
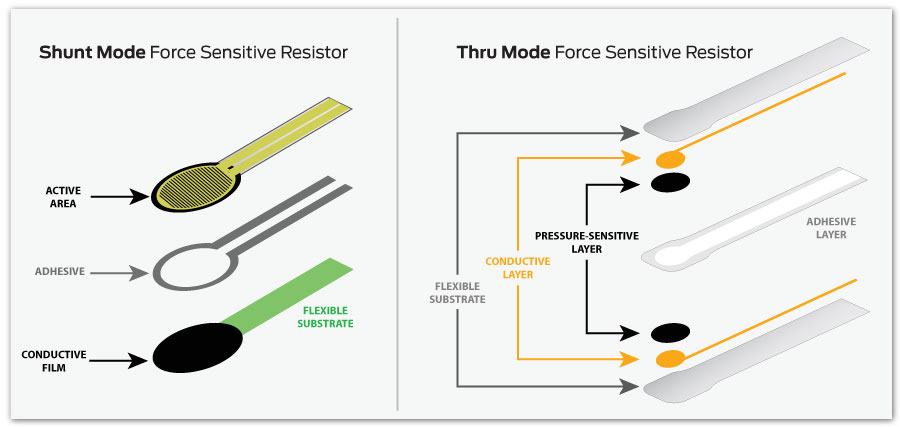
A stock image related to force sensing.
- Schedule regular check-ins: Discuss any issues and explore new product offerings.
- Provide feedback: Constructive feedback can help suppliers improve their products and services.
By following these steps, B2B buyers can ensure they select the right force sensing technologies that align with their operational needs, paving the way for enhanced product performance and customer satisfaction.
Comprehensive Cost and Pricing Analysis for force sensing Sourcing
What Are the Key Cost Components in Force Sensing Sourcing?
When analyzing the cost structure of force sensing technologies, several key components must be considered:
-
Materials: The primary materials used in force sensors include piezoresistive elements, strain gauges, and various substrates. The quality and type of materials directly impact the sensor’s performance and durability. For instance, advanced materials like silicon can increase costs but provide better sensitivity and reliability.
-
Labor: Labor costs encompass the wages of skilled workers involved in the design, assembly, and testing of force sensors. Countries with lower labor costs may offer competitive pricing, but this could affect the overall quality and reliability of the product.
-
Manufacturing Overhead: This includes costs related to utilities, rent, and administrative expenses. Efficient manufacturing processes can help minimize these overheads, allowing suppliers to offer more competitive prices.
-
Tooling: Initial setup for manufacturing force sensors often requires significant investment in specialized tooling and equipment. This one-time cost can be amortized over large production runs, reducing the per-unit cost.
-
Quality Control (QC): High-quality force sensors require rigorous testing and quality assurance processes. The costs associated with QC can vary significantly based on the complexity of the sensors and the certifications required for different markets.
-
Logistics: Transportation and shipping costs are critical, especially for international buyers. Factors such as distance, shipping method, and customs duties can significantly influence the final cost.
-
Margin: Supplier margins can vary based on market competition and demand. Understanding the typical margins in the industry can help buyers negotiate better prices.
How Do Volume and Specifications Influence Force Sensor Pricing?
The pricing of force sensors is heavily influenced by several factors:
-
Volume/MOQ (Minimum Order Quantity): Larger orders typically result in lower per-unit prices due to economies of scale. B2B buyers should consider negotiating for bulk purchasing agreements to maximize savings.
-
Specifications and Customization: Customized sensors designed for specific applications may incur additional costs. Buyers should clearly define their requirements to avoid unexpected expenses during the design phase.
-
Materials Quality and Certifications: Higher-quality materials and certifications (e.g., ISO, CE) can lead to increased prices but ensure reliability and compliance with industry standards. Buyers in highly regulated markets should prioritize these factors.
-
Supplier Factors: The reputation and reliability of suppliers can also impact pricing. Established suppliers with a proven track record may charge a premium, but their products may offer better long-term value.
-
Incoterms: Understanding shipping terms (Incoterms) is crucial for international transactions. Different terms can affect the total landed cost, including shipping fees, insurance, and duties.
What Are Effective Negotiation Strategies for International B2B Buyers?
International buyers, particularly from Africa, South America, the Middle East, and Europe, can adopt several strategies to optimize their sourcing costs:
-
Leverage Total Cost of Ownership (TCO): Rather than focusing solely on the purchase price, consider the TCO, which includes maintenance, operational costs, and potential downtime. This approach can help identify the most cost-effective options.
-
Negotiate Terms: Engage suppliers in discussions about payment terms, delivery schedules, and warranty periods. Flexible terms can provide additional financial relief and better align with your cash flow needs.
-
Market Research: Conduct thorough research on market prices and trends. Understanding the typical pricing landscape for force sensors can empower buyers during negotiations.
-
Build Long-term Relationships: Establishing strong relationships with suppliers can lead to better pricing and preferential treatment in future transactions. Regular communication and feedback can enhance these partnerships.
What Should International Buyers Keep in Mind About Pricing Nuances?
Pricing nuances can significantly affect international transactions. Buyers should be aware of currency fluctuations, local tariffs, and the economic conditions of both their own and the supplier’s country. Additionally, staying informed about changes in regulations can help avoid unexpected costs related to compliance.
Disclaimer on Indicative Prices
It is essential to note that prices for force sensors can vary widely based on the factors discussed above. Buyers should seek quotes from multiple suppliers and consider all cost components to make informed purchasing decisions.
Alternatives Analysis: Comparing force sensing With Other Solutions
Understanding Alternative Solutions to Force Sensing Technology
In the dynamic landscape of industrial applications, selecting the right measurement technology is crucial for optimizing performance and achieving business objectives. While force sensing technology is widely recognized for its effectiveness in measuring mechanical forces, several alternative solutions also exist. This section explores how force sensing compares to other viable technologies, providing B2B buyers with actionable insights tailored to their specific needs.
Comparison Table of Force Sensing and Alternatives
Comparison Aspect | Force Sensing | Strain Gauge Technology | Capacitive Sensors |
---|---|---|---|
Performance | High accuracy, real-time data | Very accurate, but can drift over time | Moderate accuracy; best for small forces |
Cost | Moderate to high | Generally low | Moderate |
Ease of Implementation | Requires calibration; moderate complexity | Simple installation; easy to calibrate | Straightforward; minimal setup |
Maintenance | Low; infrequent recalibration | Moderate; requires regular checks | Low; generally maintenance-free |
Best Use Case | Robotics, automotive, aerospace | Weighing systems, structural health | Touchscreens, proximity sensing |
What are the Pros and Cons of Strain Gauge Technology?
Strain gauge technology excels in applications requiring high accuracy in force measurement, making it a popular choice in load cells and pressure sensors. The primary advantage is its low cost and simplicity of implementation, which is attractive for businesses looking to minimize upfront expenses. However, the technology can experience drift over time, necessitating regular recalibration to maintain accuracy. This can increase long-term costs and operational complexity, particularly in high-demand environments.
How Do Capacitive Sensors Compare in Performance and Application?
Capacitive sensors are another alternative that utilizes changes in capacitance to measure force. They are especially effective for detecting small forces, making them ideal for applications like touchscreens and proximity sensors. Their setup is generally straightforward and requires minimal maintenance, which can be a significant advantage for companies looking to streamline operations. However, capacitive sensors may not provide the same level of accuracy as force sensing technologies, particularly in high-force applications, limiting their use in more demanding environments.
Conclusion: How to Choose the Right Solution for Your Needs
Selecting the right technology for force measurement depends on various factors, including the specific application, budget constraints, and desired performance characteristics. For B2B buyers, understanding the strengths and limitations of force sensing, strain gauges, and capacitive sensors is essential. Buyers should evaluate their operational requirements, such as accuracy, ease of implementation, and maintenance needs, to make an informed decision. Ultimately, the right choice will align with both immediate project goals and long-term operational efficiency, ensuring that businesses can effectively meet their measurement demands.
Essential Technical Properties and Trade Terminology for force sensing
What Are the Key Technical Properties of Force Sensing Devices?
Understanding the technical properties of force sensing devices is crucial for B2B buyers, especially when selecting the right sensor for specific applications. Here are some essential specifications to consider:
1. Material Grade
The material used in force sensors significantly affects their performance, durability, and application suitability. Common materials include silicon for piezoresistive sensors and stainless steel for strain gauge sensors. Selecting the right material grade ensures optimal performance in varying environmental conditions, such as temperature and humidity, which is essential for industries like automotive or medical devices.
2. Sensitivity
Sensitivity refers to the sensor’s ability to detect small changes in force. It is typically measured in mV/V (millivolts per volt) or N (Newtons) and is critical for applications requiring precise measurements, such as robotics or delicate touch applications. High sensitivity is particularly important for B2B buyers in sectors like consumer electronics or healthcare, where accuracy is paramount.
3. Tolerance
Tolerance indicates the allowable deviation from a specified measurement, expressed as a percentage. For instance, a tolerance of ±1% means the sensor can deviate from its stated measurement by 1%. Understanding tolerance is crucial for ensuring that the sensor meets the required performance standards, especially in regulated industries like pharmaceuticals or aerospace.
4. Operating Temperature Range
Every force sensor has a specified temperature range within which it operates effectively. This range affects the sensor’s accuracy and reliability. For international buyers, particularly in regions with extreme climates, selecting a sensor with an appropriate operating temperature range is vital for maintaining performance and longevity.
5. Response Time
Response time measures how quickly a sensor can react to an applied force. This is particularly important in dynamic applications where forces change rapidly, such as in robotics or automotive testing. A faster response time can enhance system performance and efficiency, making it a key consideration for B2B buyers focused on automation and real-time data processing.
What Are Common Trade Terms in the Force Sensing Industry?
Familiarity with industry terminology can streamline communication and enhance negotiation processes for B2B buyers. Here are some common terms used in the force sensing market:
1. OEM (Original Equipment Manufacturer)
An OEM is a company that produces parts or equipment that may be marketed by another manufacturer. Understanding OEM relationships is essential for buyers looking to integrate force sensing technology into their products, as it can affect pricing, lead times, and product support.
2. MOQ (Minimum Order Quantity)
MOQ refers to the minimum quantity of a product that a supplier is willing to sell. This term is crucial for buyers to understand, especially when budgeting for projects or inventory. Knowing the MOQ helps in planning and can influence supplier selection, particularly for small to medium-sized enterprises.
3. RFQ (Request for Quotation)
An RFQ is a formal document sent to suppliers requesting pricing information for specific products or services. It is an essential step in the procurement process, allowing buyers to compare costs and terms from multiple vendors. Including detailed specifications in an RFQ can lead to more accurate and competitive quotes.
4. Incoterms (International Commercial Terms)
Incoterms are internationally recognized rules that define the responsibilities of buyers and sellers in international transactions. They clarify who pays for shipping, insurance, and tariffs, which is vital for B2B buyers importing force sensing technology from different countries. Understanding these terms can prevent misunderstandings and additional costs.
5. Calibration
Calibration is the process of adjusting a sensor to ensure accurate measurements. This is particularly important for force sensors, as inaccuracies can lead to significant operational issues. B2B buyers should inquire about calibration services and requirements when selecting force sensing devices to ensure they meet the necessary standards for their applications.
By understanding these technical properties and industry terms, international B2B buyers can make informed decisions that align with their operational requirements and market dynamics.
Navigating Market Dynamics and Sourcing Trends in the force sensing Sector
What Are the Key Trends Driving the Force Sensing Market?
The force sensing market is witnessing significant growth, driven by technological advancements and increasing demand across various industries. One of the primary global drivers is the rise of automation and smart technologies, particularly in sectors like manufacturing, automotive, and healthcare. These industries are increasingly incorporating force sensors into their systems for enhanced precision and efficiency. Additionally, the proliferation of IoT devices is creating a surge in demand for compact and cost-effective force sensing solutions, making them indispensable for real-time data collection and analysis.
International B2B buyers, especially from Africa, South America, the Middle East, and Europe, should pay attention to emerging trends such as the integration of artificial intelligence and machine learning with force sensing technologies. This convergence allows for advanced predictive analytics and monitoring capabilities, which can significantly enhance operational efficiency. Another notable trend is the shift towards customizable and application-specific force sensors, catering to unique industry needs, particularly in specialized fields like biomechanics and robotics.
Furthermore, the demand for wireless and flexible sensor technologies is on the rise, allowing for easier integration into existing systems. Buyers should also consider the geographical dynamics of sourcing, as emerging markets in Africa and South America are becoming increasingly important hubs for manufacturing and innovation in force sensing technologies.
How Can Sustainability and Ethical Sourcing Impact the Force Sensing Sector?
Sustainability and ethical sourcing have emerged as critical considerations for B2B buyers in the force sensing market. The environmental impact of manufacturing processes and material sourcing is under scrutiny, prompting companies to adopt greener practices. Force sensing manufacturers are increasingly focusing on reducing waste and energy consumption during production. This not only addresses environmental concerns but also aligns with consumer preferences for sustainable products.
Moreover, ethical supply chains are essential for maintaining brand reputation and ensuring compliance with international standards. Buyers should seek suppliers that prioritize ethical sourcing of materials, such as recycled or sustainably sourced components. Certifications such as ISO 14001 (Environmental Management) and RoHS (Restriction of Hazardous Substances) can serve as indicators of a supplier’s commitment to sustainability.
The use of ‘green’ materials in the production of force sensors is gaining traction, with many manufacturers exploring biodegradable options and non-toxic materials. This shift not only benefits the environment but can also enhance product appeal in markets increasingly focused on sustainability. For B2B buyers, selecting suppliers that adhere to these practices can lead to improved market positioning and customer loyalty.
What Is the Historical Context of Force Sensing Technologies?
The history of force sensing technologies dates back several decades, with the earliest applications emerging in industrial settings. Initially, these sensors utilized basic strain gauge technology, which provided limited functionality and accuracy. Over time, advancements in materials science and electronics paved the way for more sophisticated methods such as piezoresistive and capacitive sensing.
The evolution of force sensors has paralleled the growth of smart technologies and automation, leading to their integration in consumer electronics, automotive systems, and healthcare devices. Today, force sensors are not only more accurate and sensitive but also versatile, accommodating a wide range of applications from robotics to medical diagnostics. Understanding this evolution is crucial for B2B buyers, as it highlights the importance of innovation and adaptability in selecting suppliers that can meet the demands of modern applications.
Frequently Asked Questions (FAQs) for B2B Buyers of force sensing
-
How do I solve the issue of inaccurate force measurements with sensors?
To resolve inaccuracies in force measurements, begin by calibrating your force sensors according to the manufacturer’s guidelines. Calibration involves applying known weights and recording the sensor’s output to establish a reliable correlation. Ensure that the sensor is installed correctly and that environmental factors, such as temperature and humidity, are controlled, as these can affect readings. Regular maintenance and testing should also be conducted to detect any drift in measurements over time. -
What is the best force sensing technology for delicate applications?
For applications requiring high sensitivity and precision, piezoresistive and capacitive force sensors are often the best choices. Piezoresistive sensors are particularly effective in miniature designs, making them ideal for delicate tasks like medical devices and robotics. Capacitive sensors, on the other hand, excel in touch applications, such as smartphones and tablets, where small force variations need to be accurately detected. Evaluating the specific requirements of your application will help determine the most suitable technology. -
How can I ensure the quality of force sensing products from suppliers?
To ensure product quality, conduct thorough supplier vetting by reviewing their certifications, such as ISO 9001, which indicates adherence to quality management standards. Request samples to evaluate the performance and reliability of the sensors in your specific application. Additionally, seek testimonials or case studies from other clients and inquire about their quality assurance processes. Establishing a good communication channel for ongoing support is also essential for addressing potential quality issues. -
What are the typical minimum order quantities (MOQs) for force sensing devices?
Minimum order quantities for force sensing devices can vary significantly based on the manufacturer and the complexity of the sensors. Generally, MOQs can range from 50 to several thousand units, depending on the type of sensor and customization requirements. For specialized or custom sensors, manufacturers may have higher MOQs. It is advisable to discuss your specific needs with suppliers to negotiate favorable terms that align with your business model. -
What payment terms should I expect when sourcing force sensing products internationally?
Payment terms for international transactions can differ based on the supplier’s policies and your relationship with them. Common options include advance payment, letter of credit, or payment upon delivery. Many suppliers may require a partial upfront payment, especially for large orders. It’s essential to clarify these terms before finalizing the contract and ensure that they are documented to avoid misunderstandings. -
How can I customize force sensors to fit my specific application needs?
Customization options for force sensors often include size, sensitivity, and output signal type. When approaching suppliers, clearly outline your specifications, including the intended application, force range, and environmental conditions. Some manufacturers offer custom designs, while others may have standardized models that can be slightly modified. Engaging in early discussions with the supplier can lead to optimal solutions tailored to your requirements. -
What logistics considerations should I keep in mind when importing force sensing devices?
When importing force sensing devices, consider shipping times, customs duties, and import regulations in your country. Collaborate with logistics providers who have experience in handling electronic components to ensure proper packaging and handling. Additionally, understand the delivery timelines and whether the supplier offers support for shipping logistics, which can help streamline the process and minimize delays. -
How do I select the right supplier for force sensing devices in my region?
Selecting the right supplier involves researching potential candidates through online platforms, industry trade shows, and recommendations from peers. Evaluate their reputation, customer service, and technical support capabilities. Consider suppliers with local presence or distribution channels in your region to facilitate easier communication and logistics. Additionally, inquire about their experience with international clients to ensure they understand the specific needs of your market.
Important Disclaimer & Terms of Use
⚠️ Important Disclaimer
The information provided in this guide, including content regarding manufacturers, technical specifications, and market analysis, is for informational and educational purposes only. It does not constitute professional procurement advice, financial advice, or legal advice.
While we have made every effort to ensure the accuracy and timeliness of the information, we are not responsible for any errors, omissions, or outdated information. Market conditions, company details, and technical standards are subject to change.
B2B buyers must conduct their own independent and thorough due diligence before making any purchasing decisions. This includes contacting suppliers directly, verifying certifications, requesting samples, and seeking professional consultation. The risk of relying on any information in this guide is borne solely by the reader.
Strategic Sourcing Conclusion and Outlook for force sensing
In the dynamic landscape of force sensing technology, strategic sourcing emerges as a critical element for international B2B buyers. Understanding the various types of force sensors—such as piezoresistive, capacitive, and strain gauge technologies—enables businesses to make informed decisions that enhance product performance and operational efficiency. For buyers in Africa, South America, the Middle East, and Europe, leveraging local suppliers and manufacturers can not only reduce costs but also foster innovative partnerships that drive growth.
Why Is Strategic Sourcing Essential for Force Sensing Solutions?
By investing in strategic sourcing, companies can align their procurement processes with their operational goals, ensuring they acquire high-quality sensors that meet specific application needs. This approach mitigates risks associated with supply chain disruptions, particularly in regions with fluctuating market conditions.
What Does the Future Hold for Force Sensing Technology?
As demand for smart and automated systems increases globally, the future of force sensing technology looks promising. Buyers should remain proactive in exploring emerging trends such as integration with IoT devices and advancements in sensor miniaturization.
In conclusion, international B2B buyers should prioritize strategic sourcing as a pathway to enhance their competitive edge. Embrace the evolving landscape of force sensing technology and make informed decisions that will position your business for success in the coming years.