Discover the 5 Essential Types of Check Valves (2025)
Introduction: Navigating the Global Market for types of check valves
In the complex world of fluid control systems, selecting the right types of check valves is crucial for ensuring efficient and reliable operations. B2B buyers, especially those in Africa, South America, the Middle East, and Europe, face the challenge of sourcing check valves that not only meet technical specifications but also align with budgetary constraints and operational requirements. This comprehensive guide addresses these challenges by providing in-depth insights into various check valve types, including spring, ball, and swing check valves, along with their specific applications in industries ranging from wastewater management to chemical processing.
By exploring the intricacies of each valve type, this guide equips international B2B buyers with the knowledge needed to make informed purchasing decisions. It covers critical factors such as supplier vetting processes, total cost of ownership, and the importance of understanding fluid dynamics to mitigate risks like backflow and pressure surges. Additionally, the guide emphasizes the significance of selecting check valves tailored to unique operational contexts, ensuring that buyers can optimize their systems for performance and longevity.
Navigating the global market for check valves can be daunting, but this resource empowers you to enhance your procurement strategy and secure quality products that drive operational success. Whether you are operating in the bustling markets of South Africa or the industrial hubs of Europe, the insights provided here will help you make confident, informed decisions that align with your business goals.
Understanding types of check valves Types and Variations
Type Name | Key Distinguishing Features | Primary B2B Applications | Brief Pros & Cons for Buyers |
---|---|---|---|
Swing Check Valve | Relies on gravity and flow for operation; offers a full bore | Water and wastewater systems | Pros: Simple design, low maintenance; Cons: Can be less effective in high-pressure systems. |
Ball Check Valve | Compact design with a rotating ball for flow control | Wastewater management, industrial applications | Pros: Cost-effective, self-cleaning; Cons: No open/close indicator. |
Lift Check Valve | Guided disc design, suitable for high-pressure environments | High-rise buildings, industrial plants | Pros: Reliable in vertical installations; Cons: More complex and expensive. |
Nozzle Check Valve | Spring-assisted closure for quick response | Pumped systems, where water hammer is a concern | Pros: Fast acting, minimizes backflow; Cons: Higher head loss compared to others. |
Piston Check Valve | Precision control with a piston mechanism | Oil and gas, chemical processing | Pros: Excellent for high-pressure applications; Cons: Requires careful installation and maintenance. |
What Are the Key Characteristics of Swing Check Valves?
Swing check valves are designed to allow fluid flow in one direction while preventing backflow. Their operation depends on gravity and the flow of the fluid, making them a cost-effective choice for many water and wastewater applications. These valves feature a disc that swings open with flow and closes when flow stops or reverses. For B2B buyers, the simplicity of the design translates into lower maintenance costs, but they may not perform well in high-pressure systems where more robust options are needed.
How Do Ball Check Valves Benefit B2B Applications?
Ball check valves utilize a spherical ball that moves to allow or obstruct flow. Their compact design and lack of external parts make them both affordable and reliable, especially in wastewater management systems. The smooth bore design prevents solid deposits, making them ideal for applications where cleanliness is vital. However, the absence of an open/close indicator may pose challenges in monitoring operations, which is a consideration for buyers looking for operational transparency.
Why Choose Lift Check Valves for High-Pressure Environments?
Lift check valves are particularly effective in high-pressure situations, characterized by their guided disc design. They can be installed in horizontal, vertical, or angled positions, making them versatile for various industrial applications, including water treatment facilities and high-rise buildings. While they offer reliable performance, their complexity and higher costs may be a deterrent for some buyers, who must weigh the benefits against the investment required.
What Makes Nozzle Check Valves Suitable for Pumped Systems?
Nozzle check valves are engineered for quick response, utilizing a spring to assist in closing the valve when flow stops. This design minimizes the risk of water hammer, making them ideal for pumped systems where sudden flow changes occur. While they offer rapid action and effective backflow prevention, they may incur higher head loss compared to swing check valves, which could impact overall system efficiency. B2B buyers should consider these factors in relation to their specific operational needs.
How Do Piston Check Valves Provide Precision Control?
Piston check valves, also known as plug check valves, are engineered for precision control in fluid management systems. They are particularly suitable for high-pressure applications found in industries such as oil and gas and chemical processing. While they offer exceptional reliability, buyers must consider the complexity and installation requirements, as these valves often necessitate more meticulous maintenance to ensure optimal performance.
Key Industrial Applications of types of check valves
Industry/Sector | Specific Application of types of check valves | Value/Benefit for the Business | Key Sourcing Considerations for this Application |
---|---|---|---|
Water Treatment | Swing check valves in water distribution systems | Prevents backflow, ensuring clean water supply | Material compatibility, pressure rating, and certifications |
Oil & Gas | Ball check valves in pipeline systems | Reliable operation under high pressure and flow rates | Resistance to corrosion, temperature tolerance, and maintenance needs |
Food and Beverage | Lift check valves in processing equipment | Ensures hygienic flow and prevents contamination | Compliance with food safety standards, ease of cleaning, and valve material |
HVAC Systems | Nozzle check valves in heating systems | Protects pumps from water hammer and pressure surges | Flow characteristics, installation space, and valve sizing |
Mining | Piston check valves in slurry transport | Prevents backflow and protects equipment from damage | Abrasion resistance, valve size, and maintenance requirements |
How Are Check Valves Used in Water Treatment Facilities?
In water treatment facilities, swing check valves are integral to maintaining the integrity of water distribution systems. They prevent backflow, which can contaminate clean water supplies. For international buyers, especially in regions like Africa and South America where water quality is paramount, sourcing valves that meet local regulations and standards is crucial. Considerations should include material compatibility with treated water, pressure ratings, and certifications to ensure reliability and compliance.

A stock image related to types of check valves.
What Role Do Check Valves Play in the Oil & Gas Industry?
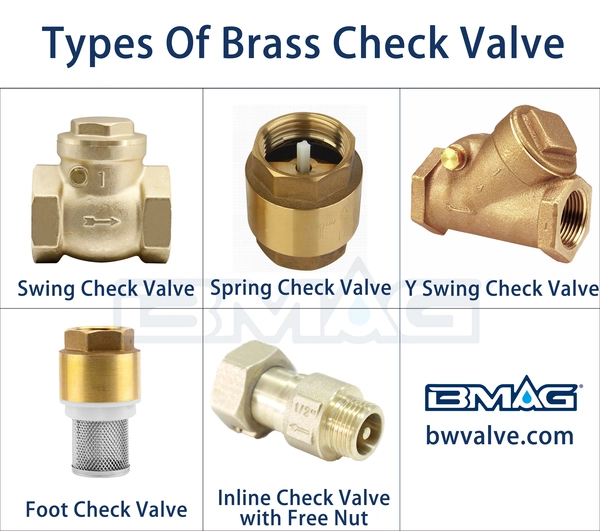
A stock image related to types of check valves.
Ball check valves are commonly used in oil and gas pipeline systems due to their robust design and ability to handle high pressures and flow rates. They ensure that fluids flow in one direction, preventing backflow that could damage equipment or lead to leaks. For buyers from the Middle East and Europe, factors such as corrosion resistance, temperature tolerance, and maintenance requirements are essential when selecting these valves to ensure long-term operational efficiency.
Why Are Lift Check Valves Important in Food and Beverage Processing?
In the food and beverage industry, lift check valves are crucial for ensuring hygienic flow within processing equipment. They help to prevent contamination by allowing only unidirectional flow, thus safeguarding product integrity. Buyers must prioritize compliance with food safety standards and consider ease of cleaning and the valve material to ensure they meet health regulations, particularly in European markets where such standards are stringent.
How Do Nozzle Check Valves Protect HVAC Systems?
Nozzle check valves are used in HVAC systems to prevent water hammer, which can occur when pumps suddenly stop or start. By allowing controlled flow and minimizing pressure surges, these valves protect pumps and associated equipment from damage. For international buyers, especially in regions with varying climates like Europe and the Middle East, sourcing valves with appropriate flow characteristics and installation requirements is vital to ensure system reliability.
What Benefits Do Piston Check Valves Offer in Mining Applications?
In mining, piston check valves are employed in slurry transport systems to prevent backflow and protect equipment from damage caused by reverse flow. Their robust design is essential in harsh environments where abrasion resistance is necessary. Buyers should consider the valve size, maintenance requirements, and the specific operational conditions of their mining site, particularly in South American markets where mineral extraction is prevalent.
3 Common User Pain Points for ‘types of check valves’ & Their Solutions
Scenario 1: Inadequate Performance Leading to System Failures
The Problem: Many B2B buyers encounter issues with check valves that do not perform as expected, leading to system failures. For instance, a manufacturing plant in South Africa may install a swing check valve to prevent backflow in its water supply system. However, if the valve is not suited for the specific pressure and flow conditions of the system, it may fail to close properly during reverse flow. This can result in costly downtime, damage to equipment, and potential safety hazards, all of which significantly impact operational efficiency and profitability.
The Solution: To mitigate this issue, B2B buyers should perform a thorough assessment of the operating conditions before selecting a check valve. This includes evaluating the system’s pressure, flow rate, and potential surge scenarios. It’s crucial to choose a valve that is rated for higher pressures and has features like a non-slam design, which can help prevent the rapid closure that causes water hammer. Buyers should also consult with manufacturers who can provide detailed specifications and performance data for each valve type. This informed approach ensures that the selected valve aligns with the operational requirements, enhancing reliability and minimizing the risk of system failures.
Scenario 2: High Maintenance Costs Due to Poor Valve Selection
The Problem: A common pain point for international B2B buyers is the unexpected high maintenance costs associated with check valves. For example, a water treatment facility in Brazil may opt for a low-cost ball check valve, assuming it would suffice for their operations. However, the valve’s construction may lead to frequent clogging, necessitating regular maintenance and replacement. This not only incurs additional costs but also affects the facility’s ability to maintain optimal flow rates, thereby compromising service delivery.
The Solution: Buyers can alleviate maintenance costs by investing in high-quality check valves designed for their specific applications. It is essential to consider the fluid characteristics, such as viscosity and particulate content, when selecting a valve. For wastewater applications, for instance, a self-cleaning ball check valve or a diaphragm valve may be more effective due to their design features that minimize clogging. Additionally, engaging with suppliers who offer warranties and maintenance packages can provide long-term savings. Establishing a maintenance schedule and training staff on proper valve care can also contribute to reduced costs and prolonged valve lifespan.
Scenario 3: Inability to Monitor Valve Performance Effectively
The Problem: B2B buyers often struggle with the inability to monitor the performance of check valves, which can lead to undetected issues in fluid systems. For instance, a chemical processing plant in France may install various types of check valves without any monitoring systems in place. This lack of oversight can result in unnoticed leaks or backflow incidents, ultimately causing chemical contamination and regulatory compliance issues.
The Solution: To address this challenge, buyers should consider check valves equipped with open/close indicators or integrate monitoring systems that provide real-time feedback on valve performance. For example, swing check valves can be fitted with visual indicators or smart sensors that alert operators to any abnormalities in valve operation. Additionally, implementing a digital monitoring solution can enhance visibility into the system’s health, allowing for proactive maintenance and timely interventions. Investing in these technologies not only improves operational safety but also helps maintain compliance with industry regulations, thereby protecting the company’s reputation and bottom line.
Strategic Material Selection Guide for types of check valves
What Are the Key Properties of Common Materials Used in Check Valves?
When selecting check valves for specific applications, the choice of material is crucial. The material not only affects the valve’s performance but also its longevity and suitability for various media. Here, we analyze four common materials used in check valve manufacturing: stainless steel, brass, PVC, and cast iron.
How Does Stainless Steel Perform in Check Valve Applications?
Key Properties: Stainless steel is known for its excellent corrosion resistance and ability to withstand high temperatures and pressures. It typically has a temperature rating of up to 400°F (204°C) and can handle pressures exceeding 2000 psi, depending on the specific grade.
Pros & Cons: The durability of stainless steel makes it ideal for high-stress environments, but it comes at a higher cost compared to other materials. Manufacturing complexity can also be a factor, as stainless steel requires specialized machining processes.
Impact on Application: Stainless steel check valves are suitable for a wide range of media, including aggressive chemicals and high-temperature fluids. They are commonly used in industries such as oil and gas, food and beverage, and pharmaceuticals.
Considerations for International Buyers: Buyers in regions like Europe and the Middle East should ensure compliance with standards such as ASTM A312 for seamless pipes and fittings. In Africa and South America, local regulations may also dictate the necessity for certain certifications.
What Advantages Does Brass Offer for Check Valves?
Key Properties: Brass is a copper-zinc alloy that provides good corrosion resistance and is suitable for moderate temperature and pressure applications, typically rated up to 250°F (121°C) and 150 psi.
Pros & Cons: Brass check valves are relatively inexpensive and easy to manufacture, making them a popular choice for residential and light commercial applications. However, they may not perform well in highly corrosive environments or at extreme temperatures.
Impact on Application: Brass is often used in water supply systems, HVAC applications, and low-pressure gas systems. Its compatibility with potable water makes it a preferred choice in plumbing.
Considerations for International Buyers: Compliance with standards like NSF/ANSI 61 for drinking water system components is vital, especially in Europe and North America. Buyers in regions like South America should be aware of local material regulations.
Why Choose PVC for Check Valves?
Key Properties: PVC (Polyvinyl Chloride) is a lightweight plastic that offers excellent chemical resistance and is typically rated for temperatures up to 140°F (60°C) and pressures around 150 psi.
Pros & Cons: The low cost and ease of installation make PVC check valves an attractive option for many applications. However, they are not suitable for high-temperature or high-pressure environments, limiting their use.
Impact on Application: PVC check valves are commonly used in irrigation, drainage, and wastewater applications due to their resistance to corrosive chemicals.
Considerations for International Buyers: Buyers should ensure that PVC materials meet standards such as ASTM D1784. In regions like Africa, where PVC is widely used, understanding local market preferences can also influence purchasing decisions.
What Role Does Cast Iron Play in Check Valve Design?
Key Properties: Cast iron is known for its strength and durability, with temperature ratings typically up to 300°F (149°C) and pressure ratings around 250 psi.
Pros & Cons: Cast iron check valves are robust and suitable for heavy-duty applications, but they are heavier and more expensive to transport. They also require more maintenance due to susceptibility to corrosion if not properly coated.
Impact on Application: These valves are commonly used in municipal water systems, sewage treatment plants, and industrial applications where durability is essential.
Considerations for International Buyers: Compliance with standards such as ASTM A126 for cast iron valves is crucial, especially in Europe and North America. Buyers in the Middle East should also consider the impact of environmental factors, such as humidity, on material selection.
Summary Table of Material Selection for Check Valves
Material | Typical Use Case for types of check valves | Key Advantage | Key Disadvantage/Limitation | Relative Cost (Low/Med/High) |
---|---|---|---|---|
Stainless Steel | Oil and gas, pharmaceuticals | Excellent corrosion resistance | Higher cost, manufacturing complexity | High |
Brass | Water supply, HVAC | Cost-effective, easy to manufacture | Limited in corrosive environments | Medium |
PVC | Irrigation, drainage, wastewater | Lightweight, low cost | Not suitable for high temperatures | Low |
Cast Iron | Municipal water systems, industrial | Durable and robust | Heavy, requires maintenance | Medium |
This strategic material selection guide serves as a comprehensive resource for international B2B buyers, helping them make informed decisions when selecting check valves for their specific applications. Understanding the properties, advantages, and limitations of each material is crucial for ensuring long-term operational efficiency and compliance with local standards.
In-depth Look: Manufacturing Processes and Quality Assurance for types of check valves
What Are the Main Stages of Check Valve Manufacturing Processes?
The manufacturing of check valves involves several critical stages that ensure the final product meets industry standards and performance expectations. Understanding these stages can help B2B buyers from Africa, South America, the Middle East, and Europe make informed decisions when sourcing check valves.
Material Preparation: How Are Raw Materials Selected and Processed?
The first step in the manufacturing process is the selection and preparation of raw materials. Common materials used for check valves include stainless steel, brass, and various plastics, depending on the application requirements.
-
Material Selection: The choice of material is crucial, as it affects durability, corrosion resistance, and overall performance. For instance, stainless steel is often preferred for its strength and resistance to harsh environments, while PVC is selected for cost-effective applications.
-
Material Processing: Once selected, materials undergo processes such as cutting, machining, and heat treatment. Machining involves shaping the material to precise dimensions, which is essential for ensuring a proper fit and function within the valve assembly.
Which Techniques Are Employed in Forming Check Valves?
After material preparation, the next stage is forming the components of the check valve. Various techniques are utilized depending on the type of valve being produced.
-
Casting: This technique is commonly used for metal check valves. Molten metal is poured into molds to create the valve body. Casting allows for complex shapes and is often used for larger valves.
-
Molding: For plastic check valves, injection molding is typically used. This process involves injecting molten plastic into a mold, allowing for high-volume production with consistent quality.
-
Machining: In cases where precision is paramount, components may be further refined through CNC machining. This ensures that all parts meet exact specifications, which is critical for maintaining performance standards.
What Steps Are Involved in the Assembly of Check Valves?
The assembly of check valves is a meticulous process that combines various components into a fully functional unit.
-
Component Assembly: This involves fitting together parts such as the valve body, disc, and seals. Careful alignment is crucial to prevent leaks and ensure proper operation.
-
Sealing and Testing: After assembly, seals are installed to prevent fluid leakage. This stage often includes pressure testing to ensure that the valve can withstand operational stresses.
How Are Finishing Processes Applied in Check Valve Manufacturing?
Finishing processes enhance the appearance and functionality of check valves. These processes can include:
-
Surface Treatment: Techniques such as coating, polishing, or anodizing improve corrosion resistance and aesthetic appeal. For instance, a nickel plating can be applied to enhance durability in corrosive environments.
-
Quality Inspection: After finishing, valves undergo rigorous inspection to ensure they meet quality standards. This includes checking dimensions, surface finish, and overall appearance.
What Are the Key Quality Assurance Standards for Check Valves?
Quality assurance is vital in the manufacturing of check valves to ensure reliability and safety in various applications. International and industry-specific standards play a significant role.
-
ISO 9001: This is the most recognized quality management standard, focusing on consistent quality and customer satisfaction. Manufacturers certified under ISO 9001 demonstrate their commitment to maintaining quality throughout their processes.
-
CE Marking: In Europe, CE marking indicates compliance with health, safety, and environmental protection standards. This is particularly important for B2B buyers in Europe who require assurance of product safety.
-
API Standards: The American Petroleum Institute (API) provides standards relevant for check valves used in oil and gas applications. Compliance with API standards is crucial for valves operating in demanding environments.
What Quality Control Checkpoints Are Essential in the Manufacturing Process?
Quality control checkpoints are integrated throughout the manufacturing process to ensure that each valve meets specifications. These checkpoints include:
-
Incoming Quality Control (IQC): This involves inspecting raw materials upon receipt to ensure they meet required standards. Non-compliance at this stage can lead to defects in the final product.
-
In-Process Quality Control (IPQC): During production, regular checks are conducted to monitor processes and ensure adherence to quality standards. This helps identify issues early in the manufacturing process.
-
Final Quality Control (FQC): Once the valves are fully assembled, they undergo final inspections, including functional tests and pressure tests, to confirm they operate correctly and meet performance standards.
How Can B2B Buyers Verify Supplier Quality Control?
For international B2B buyers, especially from diverse regions, verifying a supplier’s quality control processes is crucial for mitigating risk.
-
Supplier Audits: Conducting audits of potential suppliers allows buyers to assess their manufacturing processes, quality control measures, and compliance with industry standards. This can be done through on-site visits or third-party audit services.
-
Quality Reports: Requesting quality assurance reports from suppliers can provide insights into their quality management practices and any certifications they hold. This documentation can help in evaluating the supplier’s reliability.
-
Third-Party Inspections: Engaging third-party inspection services can offer an unbiased assessment of a supplier’s quality control processes. This is particularly useful for buyers unfamiliar with local manufacturing standards.
What Are the QC and Certification Nuances for International Buyers?
International B2B buyers must navigate various quality control and certification nuances, especially when sourcing from different regions.
-
Understanding Regional Standards: Different regions may have varying quality standards and certifications. For instance, while ISO 9001 is globally recognized, specific industries may require additional certifications, such as API for oil and gas.
-
Cultural and Regulatory Differences: Buyers should be aware of cultural differences that may affect communication and negotiation regarding quality expectations. Additionally, understanding local regulations can prevent compliance issues.
-
Building Relationships: Establishing strong relationships with suppliers can facilitate better communication regarding quality control. Regular dialogue can help ensure that both parties understand quality expectations and any changes in standards.
By understanding the manufacturing processes and quality assurance practices for check valves, B2B buyers can make informed decisions, ensuring they select reliable suppliers that meet their operational needs.
Practical Sourcing Guide: A Step-by-Step Checklist for ‘types of check valves’
Introduction
Navigating the procurement process for check valves can be complex, especially for international B2B buyers from diverse regions such as Africa, South America, the Middle East, and Europe. This guide serves as a practical checklist to help you make informed decisions when sourcing different types of check valves. By following these steps, you can ensure optimal performance, reliability, and cost-effectiveness in your fluid control systems.
Step 1: Define Your Technical Specifications
Clearly outline the technical requirements for the check valves you need. Consider factors such as the type of fluid being transported, temperature, pressure, and flow characteristics.
– Fluid Compatibility: Ensure the materials of the valve can withstand the specific chemicals or solids in your application.
– Pressure Ratings: Choose valves that can handle the maximum pressure expected in your system to prevent failures.
Step 2: Identify the Appropriate Check Valve Type
Different applications require different types of check valves, such as swing, ball, or lift check valves.
– Application Suitability: Understand which type fits best based on your system dynamics and fluid flow requirements. For instance, ball check valves are ideal for wastewater applications due to their self-cleaning design.
– Maintenance Requirements: Assess the maintenance needs of each valve type to ensure they align with your operational capabilities.
Step 3: Evaluate Supplier Certifications
Before selecting a supplier, verify their certifications and industry standards compliance.
– Quality Assurance: Look for ISO certifications or other relevant quality assurance marks that demonstrate adherence to international standards.
– Local Regulations: Ensure that the supplier meets any specific local regulations applicable to your region, particularly in the Middle East or Europe.
Step 4: Request Samples for Testing
Always request product samples before placing large orders. This allows for a firsthand evaluation of the valve’s performance in your specific application.
– Functional Testing: Test the valve under real conditions to assess flow characteristics and check for any potential leaks or failures.
– Material Inspection: Evaluate the materials used in the sample to ensure they meet your specifications for durability and compatibility.
Step 5: Review Total Cost of Ownership (TCO)
Consider the total cost of ownership, not just the initial purchase price of the check valves.
– Long-term Costs: Factor in maintenance, energy consumption, and potential downtime costs due to valve failures.
– Lifecycle Analysis: Assess how the valve’s design may impact its lifespan and performance over time, especially in high-demand applications.
Step 6: Check References and Case Studies
Before finalizing a supplier, check their references and request case studies from clients in similar industries or regions.
– Performance Track Record: Understanding how a supplier’s products have performed in real-world applications can provide insights into reliability and customer satisfaction.
– Feedback from Local Buyers: Engaging with buyers from your region can offer valuable information about the supplier’s responsiveness and support services.
Step 7: Negotiate Terms and Conditions
Once you’ve identified a suitable supplier, negotiate the terms of the purchase, including price, delivery timelines, and warranty conditions.
– Contract Clarity: Ensure that all terms are clearly outlined in the contract to prevent misunderstandings later on.
– After-Sales Support: Discuss available after-sales support options, as effective service can significantly impact the long-term performance of your check valves.
By following this structured checklist, you can streamline your procurement process for check valves, ensuring that you select the most suitable products and suppliers for your specific needs.
Comprehensive Cost and Pricing Analysis for types of check valves Sourcing
What Are the Key Cost Components in Check Valve Manufacturing?
Understanding the cost structure behind check valves is essential for international B2B buyers looking to optimize their sourcing strategy. The primary cost components include:
-
Materials: The choice of materials significantly impacts the overall cost. Common materials for check valves include stainless steel, brass, PVC, and various alloys. Each material comes with its own price point and performance characteristics, which can affect the valve’s durability and suitability for specific applications.
-
Labor: Labor costs vary depending on the manufacturing location. Regions with lower labor costs, such as parts of Africa and South America, may offer competitive pricing. However, this could come at the expense of quality control and precision.
-
Manufacturing Overhead: This encompasses indirect costs related to production, such as utilities, rent, and administrative expenses. Efficient manufacturing processes can help reduce overhead, but buyers must assess how these savings affect product quality.
-
Tooling: The initial investment in tooling can be significant, especially for custom check valves. Buyers should consider the tooling costs as part of the total investment, particularly if they require specialized designs.
-
Quality Control (QC): Investing in rigorous QC processes ensures that the valves meet the required specifications and certifications. This is crucial for buyers in regulated industries, as non-compliance can lead to costly failures.
-
Logistics: Shipping and handling costs can vary greatly based on the origin and destination of the products. Buyers should account for potential tariffs and customs fees, especially when sourcing from different continents.
-
Margin: Supplier margins can vary based on the manufacturer’s reputation, product quality, and market demand. Understanding the typical margin in your region can help in negotiating better pricing.
How Do Price Influencers Affect Check Valve Sourcing?
Several factors influence the pricing of check valves, and understanding these can help buyers make informed purchasing decisions:
-
Volume/MOQ: Minimum Order Quantities (MOQs) and bulk purchase discounts can significantly impact pricing. Higher volumes generally lead to lower per-unit costs, making it worthwhile to consolidate orders when possible.
-
Specifications and Customization: Custom designs or specific material requirements can lead to increased costs. Buyers should clearly define their needs to avoid unnecessary expenses associated with customization.
-
Material Choices: The selection of materials not only affects the initial purchase price but also the longevity and maintenance costs of the valve. For instance, investing in higher-quality materials may result in lower long-term operational costs.
-
Quality and Certifications: Valves that meet international standards or specific industry certifications often come at a premium. Buyers should weigh the benefits of certified products against their budget constraints.
-
Supplier Factors: The reputation and reliability of suppliers can influence pricing. Established suppliers may charge more but often provide better support and quality assurance.
-
Incoterms: Understanding Incoterms is crucial for international buyers. Terms like FOB (Free on Board) or CIF (Cost, Insurance, and Freight) can affect the total landed cost of the product.
What Are the Best Negotiation and Cost-Efficiency Tips for International B2B Buyers?
To ensure a favorable procurement process, buyers should consider the following strategies:
-
Conduct Market Research: Understanding market trends and pricing benchmarks can empower buyers during negotiations. This knowledge can help in assessing fair pricing and in identifying potential suppliers who offer the best value.
-
Emphasize Total Cost of Ownership (TCO): TCO includes not just the purchase price but also installation, maintenance, and operational costs. Highlighting the long-term benefits of quality valves can justify a higher initial price.
-
Negotiate Terms and Conditions: Buyers should negotiate payment terms, delivery schedules, and warranties. Flexible payment options can improve cash flow, while favorable warranty terms can mitigate risks associated with product failures.
-
Assess Supplier Capabilities: Evaluating a supplier’s production capabilities and quality management systems can lead to better sourcing decisions. Building strong relationships with reliable suppliers can result in improved pricing and service in the long run.
-
Stay Informed on Regional Factors: Buyers from Africa, South America, the Middle East, and Europe should stay abreast of local market conditions, including currency fluctuations and trade regulations, as these can impact pricing and availability.
Conclusion
While sourcing check valves, understanding the cost structure and pricing influencers is vital for international buyers. By leveraging effective negotiation strategies and focusing on total cost of ownership, buyers can optimize their procurement process, ensuring both quality and cost-efficiency in their valve sourcing endeavors.
Alternatives Analysis: Comparing types of check valves With Other Solutions
Introduction to Alternatives in Fluid Control Solutions
When it comes to ensuring unidirectional flow in fluid systems, check valves are essential components. However, various alternatives exist that can serve similar purposes. For international B2B buyers, particularly from regions like Africa, South America, the Middle East, and Europe, understanding the differences among these options is crucial for making informed purchasing decisions. This section compares types of check valves with two viable alternatives: ball valves and diaphragm valves, focusing on performance, cost, ease of implementation, maintenance, and best use cases.
Comparison Aspect | Types Of Check Valves | Ball Valves | Diaphragm Valves |
---|---|---|---|
Performance | Prevents backflow effectively; varies by type (e.g., swing, ball) | Provides a reliable shut-off; not specifically for backflow | Excellent for throttling and flow control; suitable for slurries |
Cost | Moderate initial cost; varies by design | Generally low-cost; durable | Higher initial cost; maintenance can be costly |
Ease of Implementation | Easy installation, depending on type | Simple installation; compact size | Requires careful installation to ensure proper sealing |
Maintenance | Low maintenance; depends on type | Minimal maintenance; long lifespan | Requires periodic checks; diaphragm wear can be an issue |
Best Use Case | Water and wastewater systems, industrial applications | General fluid handling, shut-off applications | Chemical processing, food and beverage, and other sensitive applications |
Detailed Breakdown of Alternatives
What are the Advantages and Disadvantages of Ball Valves?
Ball valves are widely recognized for their simplicity and effectiveness in controlling flow. They feature a spherical closure element that provides a tight seal when closed, making them ideal for shut-off applications. The primary advantages of ball valves include their low cost and minimal maintenance requirements. However, they are not designed to prevent backflow, which limits their use in applications where fluid reversal is a concern. For B2B buyers in industries that require quick shut-off without backflow prevention, ball valves can be a suitable choice.
How Do Diaphragm Valves Perform Compared to Check Valves?
Diaphragm valves utilize a flexible diaphragm to control flow, making them excellent for applications that require precise throttling and isolation. These valves excel in handling slurries and corrosive fluids, providing a reliable seal that prevents contamination. While diaphragm valves offer superior performance in specific applications, they come with a higher initial cost and may require more frequent maintenance due to diaphragm wear. Buyers focused on chemical processing or food production may find diaphragm valves advantageous, despite the increased costs.
Conclusion: How to Choose the Right Solution for Your Needs
Selecting the right fluid control solution hinges on understanding the specific requirements of your application. For B2B buyers, it is essential to evaluate factors such as performance needs, budget constraints, ease of implementation, and long-term maintenance considerations. While types of check valves provide reliable backflow prevention, alternatives like ball and diaphragm valves offer distinct advantages for different scenarios. Conducting a thorough analysis of each option will empower buyers to make informed decisions that align with their operational goals and industry standards.
Essential Technical Properties and Trade Terminology for types of check valves
What Are the Key Technical Properties of Check Valves for B2B Buyers?
Understanding the essential technical properties of check valves is crucial for international B2B buyers, particularly those operating in diverse markets such as Africa, South America, the Middle East, and Europe. Here are the critical specifications to consider:
1. Material Grade: What Should You Look For?
The material grade of a check valve determines its durability, corrosion resistance, and suitability for different fluid types. Common materials include stainless steel, brass, and PVC. For example, stainless steel is ideal for high-pressure applications and corrosive environments, making it a preferred choice in the oil and gas sector. Selecting the appropriate material ensures longevity and reduces maintenance costs, which is vital for operational efficiency.
2. Pressure Rating: How Does It Impact Performance?
The pressure rating indicates the maximum pressure a valve can withstand without failing. This specification is essential for applications involving high-pressure fluids, such as in industrial plants or water treatment facilities. Ensuring that the check valve’s pressure rating meets or exceeds system requirements prevents catastrophic failures and costly downtimes, making it a critical factor in the purchasing decision.
3. Size and Flow Capacity: Why Are They Important?
Size and flow capacity, often measured in diameter and Cv (flow coefficient), affect how efficiently a check valve can operate within a system. The right size ensures minimal head loss and optimal flow rates, preventing bottlenecks in fluid transport systems. Buyers should assess the specific requirements of their applications to select valves that align with their flow characteristics, ensuring seamless operation.
4. Tolerance and Fit: What Should You Consider?
Tolerance refers to the allowable deviation in dimensions and performance characteristics of the valve components. Accurate tolerances are critical for ensuring that check valves fit properly within piping systems and operate effectively. Poorly fitted valves can lead to leaks, inefficiencies, and increased maintenance costs. For B2B buyers, understanding tolerance specifications helps in achieving the right fit for their applications.
5. Temperature Range: How Does It Affect Material Selection?
The operating temperature range dictates the materials used in the valve’s construction. High-temperature applications may require specialized materials that can withstand thermal expansion and prevent degradation. Buyers must consider the maximum and minimum temperatures their systems will experience to select valves that maintain integrity and performance under varying conditions.
What Are Common Trade Terms Related to Check Valves?
Familiarity with industry terminology is essential for effective communication and negotiation in B2B transactions. Here are some commonly used terms:
1. OEM (Original Equipment Manufacturer): What Does It Mean?
OEM refers to companies that manufacture products that are sold under another brand name. In the context of check valves, buyers may seek OEMs for customized solutions that meet specific operational requirements. Understanding OEM relationships can lead to better pricing and tailored products.
2. MOQ (Minimum Order Quantity): How Does It Affect Purchases?
MOQ is the minimum number of units a supplier is willing to sell in a single order. Knowing the MOQ is vital for budgeting and inventory management, especially for international buyers who need to assess shipping and storage costs.
3. RFQ (Request for Quotation): Why Is It Important?
An RFQ is a formal process in which buyers request pricing and terms from suppliers. Submitting an RFQ allows B2B buyers to compare offers, negotiate terms, and ensure they are getting the best value for their investment in check valves.
4. Incoterms (International Commercial Terms): What Should You Know?
Incoterms are standardized trade terms that define the responsibilities of buyers and sellers in international transactions. Understanding these terms is crucial for B2B buyers to clarify shipping, insurance, and tariff responsibilities, thus avoiding potential disputes during the procurement process.
5. Lead Time: How Does It Impact Supply Chain Management?
Lead time refers to the time taken from placing an order to receiving the product. For check valves, understanding lead times is crucial for project planning and inventory management, especially in industries with tight deadlines.
By grasping these technical properties and trade terms, international B2B buyers can make informed decisions when sourcing check valves, ensuring optimal performance and cost-efficiency in their operations.
Navigating Market Dynamics and Sourcing Trends in the types of check valves Sector
What Are the Current Market Dynamics and Key Trends in the Check Valves Sector?
The check valves market is experiencing robust growth, driven by the increasing demand for fluid control in various industries, including water treatment, oil and gas, and manufacturing. According to market reports, the global check valve market is projected to witness a compound annual growth rate (CAGR) of over 5% through the next decade. This growth is significantly influenced by the rising need for infrastructure development in emerging markets across Africa and South America, coupled with advancements in B2B technology that facilitate better sourcing and supply chain management.
Emerging trends include the adoption of automation and smart technology in valve systems, which allow for enhanced monitoring and control of fluid dynamics. For B2B buyers, this represents an opportunity to invest in check valves that not only meet operational needs but also integrate seamlessly with existing digital systems. Additionally, manufacturers are increasingly focusing on producing lightweight, corrosion-resistant materials that enhance the longevity and efficiency of check valves, catering to the specific requirements of international markets, particularly in regions with challenging environmental conditions like the Middle East.
As B2B buyers navigate this evolving landscape, understanding local market dynamics, compliance standards, and technological advancements will be crucial. For instance, European buyers may prioritize eco-friendly certifications and compliance with stringent environmental regulations, while those in Africa might focus on cost-effective solutions that withstand harsh operational conditions.
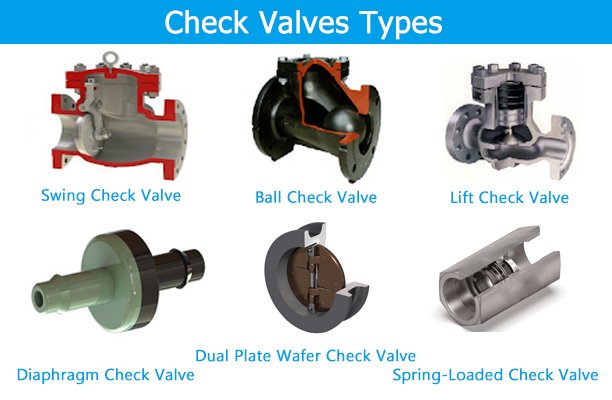
A stock image related to types of check valves.
How Does Sustainability and Ethical Sourcing Impact the Check Valves Market?
Sustainability is becoming a central tenet in the sourcing of check valves, driven by both regulatory pressures and consumer demand for environmentally friendly products. The environmental impact of manufacturing processes, particularly in terms of resource consumption and waste generation, is under scrutiny. International B2B buyers are increasingly seeking suppliers who adhere to sustainable practices, ensuring that their sourcing decisions contribute positively to the environment.
Ethical supply chains are also gaining importance, particularly in regions like Europe, where consumers are highly conscious of the origins of their products. Buyers are encouraged to assess suppliers based on their sustainability credentials, including certifications like ISO 14001, which signifies effective environmental management systems. Furthermore, the choice of materials, such as recycled metals or biodegradable plastics in the production of check valves, is becoming a focal point for environmentally conscious buyers.
By prioritizing suppliers who demonstrate a commitment to sustainability, B2B buyers can not only reduce their environmental footprint but also enhance their brand reputation in a market that values corporate responsibility. This strategic approach can lead to long-term partnerships with manufacturers who are aligned with these values, ultimately benefiting both parties.
What Is the Evolution of Check Valves and Its Importance for B2B Buyers?
The evolution of check valves dates back to ancient water control systems, but significant advancements have been made over the centuries. From the early mechanical designs to modern automated systems, check valves have transformed to meet the demands of increasingly complex fluid control applications. The introduction of materials like PVC and advanced alloys has improved durability and functionality, making check valves suitable for a wider range of applications.
For B2B buyers, understanding this evolution is crucial as it informs purchasing decisions. Knowing the historical context can help buyers appreciate the advancements in technology and materials, allowing them to select products that not only fulfill current requirements but also anticipate future industry trends. As the market continues to innovate, being informed about the historical development of check valves enables buyers to make strategic decisions that align with both operational needs and sustainability goals.
In summary, navigating the check valves market requires a keen understanding of current dynamics, sustainability considerations, and the historical context of these essential components. By leveraging these insights, international B2B buyers can optimize their sourcing strategies and contribute to more efficient and responsible fluid control systems.
Frequently Asked Questions (FAQs) for B2B Buyers of types of check valves
-
How do I solve issues related to backflow in my piping system?
To address backflow issues effectively, selecting the right type of check valve is crucial. Swing check valves are commonly used in applications with low pressure and flow rates, while ball check valves are ideal for wastewater applications due to their self-cleaning properties. Additionally, consider integrating non-slam designs to minimize pressure surges. Regular maintenance and inspections will also help identify potential backflow risks before they escalate into costly problems. -
What is the best check valve for high-pressure applications?
For high-pressure environments, lift check valves are often the best choice. They feature a guided disc that lifts with the flow, ensuring efficient passage and preventing backflow when the flow ceases. Their robust design makes them suitable for industrial settings, water treatment facilities, and high-rise buildings. When selecting a lift check valve, ensure it meets the specific pressure and flow requirements of your system to ensure optimal performance. -
How can I vet suppliers for check valves in international markets?
When sourcing check valves from international suppliers, conduct thorough due diligence. Verify the supplier’s certifications and compliance with industry standards, such as ISO and API. Request samples and check their quality assurance processes. Additionally, seek references or reviews from other B2B buyers in your region. Engaging with local industry associations can also provide insights into reliable suppliers and help you navigate potential trade challenges. -
What customization options are available for check valves?
Customization options for check valves can vary widely among manufacturers. Common modifications include size, material, and design features tailored to specific applications. For instance, you may require valves made from corrosion-resistant materials for harsh environments. Discuss your needs with suppliers early in the procurement process to explore the available options and ensure that the customized solutions meet your operational requirements. -
What are the minimum order quantities (MOQs) for check valves?
Minimum order quantities for check valves can differ significantly based on the supplier and the type of valve. Some manufacturers may have MOQs as low as 10 pieces, while others may require orders of 100 or more. It’s essential to clarify these terms upfront to align your procurement strategy with your budget and project timelines. Consider negotiating MOQs, especially if you are a new buyer or if you are looking to establish a long-term partnership. -
What payment terms should I expect when sourcing check valves internationally?
Payment terms for international transactions can vary, but common practices include advance payments, letters of credit, or payment upon delivery. Some suppliers may offer net terms (e.g., net 30 or net 60 days) for established relationships. Always discuss and negotiate payment terms upfront to avoid any misunderstandings. It’s advisable to use secure payment methods that provide buyer protection, especially when dealing with new suppliers. -
How can I ensure quality assurance (QA) for check valves sourced internationally?
To ensure quality assurance for internationally sourced check valves, request detailed specifications and certifications from the supplier. Many manufacturers conduct rigorous testing, including pressure tests and material inspections, prior to shipment. Consider hiring a third-party inspection service to verify the quality before the goods leave the supplier’s facility. Establishing clear QA protocols and communication channels can help mitigate risks and ensure that the products meet your standards. -
What logistics considerations should I keep in mind when importing check valves?
When importing check valves, logistics play a critical role in ensuring timely delivery. Consider factors such as shipping methods, customs clearance, and potential tariffs. Work with a reputable freight forwarder who understands the import regulations of your region. Additionally, plan for lead times and communicate with your supplier about production schedules to align delivery with your operational needs. Effective logistics management can significantly reduce delays and unexpected costs.
Important Disclaimer & Terms of Use
⚠️ Important Disclaimer
The information provided in this guide, including content regarding manufacturers, technical specifications, and market analysis, is for informational and educational purposes only. It does not constitute professional procurement advice, financial advice, or legal advice.
While we have made every effort to ensure the accuracy and timeliness of the information, we are not responsible for any errors, omissions, or outdated information. Market conditions, company details, and technical standards are subject to change.
B2B buyers must conduct their own independent and thorough due diligence before making any purchasing decisions. This includes contacting suppliers directly, verifying certifications, requesting samples, and seeking professional consultation. The risk of relying on any information in this guide is borne solely by the reader.
Strategic Sourcing Conclusion and Outlook for types of check valves
As the global demand for efficient and reliable fluid control systems continues to rise, understanding the diverse types of check valves and their applications is crucial for international B2B buyers. The selection of the right check valve—be it spring, swing, or ball check—should be guided by an analysis of specific operational conditions, fluid dynamics, and potential risks associated with backflow.
Strategic sourcing in this context not only enhances operational efficiency but also mitigates long-term costs associated with maintenance and equipment protection. Buyers must assess factors such as fluid compatibility, flow characteristics, and total cost of ownership to make informed decisions that align with their operational goals.
Looking ahead, the market for check valves is set to evolve with advancements in technology and increased focus on sustainability. By prioritizing strategic sourcing and leveraging partnerships with reputable manufacturers, B2B buyers from Africa, South America, the Middle East, and Europe can secure high-quality check valves that meet their unique requirements.
Engage with trusted suppliers today to explore innovative solutions that will enhance your fluid control systems and contribute to your business’s success in a competitive landscape.