Discover the Benefits of Friction Hinges: A Complete Guide (2025)
Introduction: Navigating the Global Market for friction hinge
Navigating the complex landscape of sourcing friction hinges can be a daunting challenge for B2B buyers, particularly those from diverse regions such as Africa, South America, the Middle East, and Europe. With an increasing demand for precise movement control in various applications—from industrial machinery to consumer electronics—understanding the nuances of friction hinges is essential. This guide delves into a comprehensive exploration of friction hinges, encompassing types, applications, supplier vetting, cost considerations, and key performance metrics.
International buyers will benefit from insights into how to evaluate suppliers effectively, ensuring compliance with regional standards and regulations. By understanding the differences between adjustable and non-adjustable friction hinges, as well as the torque specifications relevant to specific applications, buyers can make informed choices that enhance their product offerings and operational efficiency.
Additionally, this guide highlights critical factors such as material selection, design considerations, and the importance of sustainability—particularly relevant for buyers in emerging markets where eco-friendly practices are increasingly prioritized. With actionable strategies and expert recommendations, this resource empowers B2B buyers to navigate the global market confidently, ensuring that their procurement processes are efficient, cost-effective, and aligned with their operational needs.
By leveraging this guide, international B2B buyers can take the guesswork out of sourcing friction hinges, ensuring they select the best options tailored to their unique business requirements.
Understanding friction hinge Types and Variations
Type Name | Key Distinguishing Features | Primary B2B Applications | Brief Pros & Cons for Buyers |
---|---|---|---|
Adjustable Friction Hinge | Allows customization of friction levels for varied resistance. | Electronics, furniture, automotive | Pros: Versatile, customizable. Cons: More complex installation. |
Constant Torque Hinge | Maintains consistent resistance throughout the range of motion. | Display cases, access panels | Pros: Reliable, consistent performance. Cons: Limited adjustability. |
Positioning Hinge | Locks in set positions, often with defined detents. | Doors, lids, machinery covers | Pros: Secure positioning, easy to use. Cons: Limited movement flexibility. |
Counterbalance Hinge | Balances weight for easier operation, often used in heavy doors. | Industrial applications, heavy equipment | Pros: Reduces strain, supports heavy loads. Cons: May require more space. |
Plastic Friction Hinge | Lightweight, often made from thermoplastics, adjustable friction. | Lightweight applications, portable devices | Pros: Lightweight, corrosion-resistant. Cons: May not support heavy loads. |
What Are the Characteristics of Adjustable Friction Hinges?
Adjustable friction hinges are designed for versatility, allowing users to modify the friction level to suit different applications. This feature is particularly beneficial in settings where varying resistance is needed, such as in electronics or automotive components. Buyers should consider the ease of adjustment and the specific torque range required for their applications, as well as installation complexity.
How Do Constant Torque Hinges Function in B2B Applications?
Constant torque hinges provide uniform resistance, making them ideal for applications where a consistent hold is necessary, such as display cases and access panels. Their reliability in maintaining set positions without additional adjustment is a significant advantage. Buyers should evaluate the torque specifications to ensure compatibility with their specific needs and the operational environment.
Why Choose Positioning Hinges for Your Business Needs?
Positioning hinges are equipped with detents that allow them to lock into predefined positions, making them suitable for doors, lids, and machinery covers. This locking mechanism enhances usability and security, particularly in industrial settings. When purchasing, consider the angles available for locking and the weight capacity to ensure they meet application demands.
What Advantages Do Counterbalance Hinges Offer in Heavy-Duty Applications?
Counterbalance hinges are engineered to assist in the operation of heavy doors or panels by balancing the weight, thus reducing the force required to open or close them. This makes them particularly valuable in industrial applications where heavy equipment is involved. Buyers should assess the load capacity and installation space to determine the suitability of these hinges for their specific use cases.
How Do Plastic Friction Hinges Stand Out in Lightweight Applications?
Plastic friction hinges are made from lightweight materials such as thermoplastics, offering an excellent solution for applications where weight is a concern. They are often adjustable and corrosion-resistant, making them ideal for portable devices. Buyers should consider the load limits and environmental factors, such as exposure to chemicals or extreme temperatures, when selecting these hinges for their projects.
Key Industrial Applications of friction hinge
Industry/Sector | Specific Application of Friction Hinge | Value/Benefit for the Business | Key Sourcing Considerations for this Application |
---|---|---|---|
Electronics | Laptop and Tablet Screens | Provides adjustable screen angles, enhancing user experience and functionality. | Look for torque specifications that match the device’s weight and usage. |
Automotive | Car Hoods and Trunks | Ensures easy access while securely holding open, improving safety and convenience. | Consider environmental durability and resistance to corrosion. |
Medical Equipment | Hospital Beds and Medical Cabinets | Allows for smooth adjustments and secure positioning, enhancing patient comfort and care. | Ensure compliance with health regulations and material safety standards. |
Furniture | Adjustable Office Desks | Facilitates ergonomic adjustments for user comfort, promoting productivity. | Focus on aesthetics and durability in high-usage environments. |
Industrial Machinery | Access Panels in Machinery | Provides secure access for maintenance while holding panels in position, increasing efficiency. | Check for load capacity and resistance to wear in harsh environments. |
How Are Friction Hinges Used in Electronics?
In the electronics industry, friction hinges are commonly utilized in laptops and tablets, allowing screens to remain at various angles. This adjustability enhances user experience by providing comfort and functionality during use. International buyers should consider the torque specifications required for their devices, ensuring that the hinges can support the weight and frequent adjustments without wear. Sourcing hinges that meet these specifications is crucial for maintaining product integrity and user satisfaction.
What Role Do Friction Hinges Play in the Automotive Sector?
Friction hinges are vital in automotive applications, particularly for car hoods and trunks. They enable these components to stay open securely, facilitating easy access for maintenance and repairs. This functionality not only enhances user convenience but also contributes to safety by preventing accidental closures. Buyers in this sector must prioritize sourcing hinges that offer durability and corrosion resistance, as automotive parts are often exposed to harsh environmental conditions.
How Are Friction Hinges Beneficial for Medical Equipment?
In the medical field, friction hinges are employed in hospital beds and medical cabinets, allowing for smooth adjustments and secure positioning of equipment. This is essential for patient comfort and ease of access for healthcare providers. Buyers should ensure that the hinges comply with health regulations and are made from materials that are safe and durable, as they will be subject to frequent use and cleaning.
What Advantages Do Friction Hinges Provide in Furniture Design?
Friction hinges are increasingly used in adjustable office desks, allowing users to modify their workstations for ergonomic comfort. This adaptability promotes productivity and well-being in the workplace. When sourcing these hinges, buyers should consider both aesthetic appeal and durability, especially in high-usage environments where wear and tear are common.
How Do Friction Hinges Improve Efficiency in Industrial Machinery?
In industrial settings, friction hinges are essential for access panels in machinery. They provide secure access for maintenance while ensuring that the panels remain in position, enhancing operational efficiency. Buyers should focus on the load capacity and resistance to wear, particularly in environments that may expose the hinges to heavy use and harsh conditions. Ensuring that sourced hinges meet these requirements can significantly improve machinery uptime and maintenance workflows.
3 Common User Pain Points for ‘friction hinge’ & Their Solutions
Scenario 1: Challenges with Torque Adjustment in Friction Hinges
The Problem: B2B buyers often face difficulties when the torque settings of friction hinges do not align with their specific application requirements. For instance, a manufacturer in Nigeria may need a friction hinge for a lid that needs to stay open at various angles but finds that the hinge either provides too much resistance or insufficient support. This misalignment can lead to safety hazards, equipment damage, or operational inefficiencies, resulting in increased costs and potential downtime.
The Solution: To effectively source and specify the right friction hinge, it is crucial to understand the torque requirements specific to the application. Buyers should consult with manufacturers or suppliers to discuss the exact load and angle specifications. It is advisable to opt for adjustable friction hinges that allow for precise torque adjustments during installation. Additionally, utilizing torque measurement tools during setup can help achieve the desired performance. Suppliers like Sugatsune offer friction hinges with varying torque settings, enabling buyers to select a model that best suits their needs. Regular maintenance checks can further ensure that the torque remains consistent over time.
Scenario 2: Durability Concerns in Harsh Environments
The Problem: Many international B2B buyers, particularly in regions like South America or the Middle East, often encounter issues with the durability of friction hinges in harsh environments. For example, a company manufacturing outdoor equipment may find that standard hinges corrode or fail under high temperatures or humidity, leading to product failure and customer dissatisfaction.
The Solution: To overcome durability challenges, it is essential to select friction hinges made from materials that are resistant to environmental factors. Buyers should look for hinges made from stainless steel or specialized plastics that are designed for outdoor use. Additionally, it is beneficial to check for certifications such as RoHS compliance and other relevant standards that indicate a product’s suitability for specific conditions. Collaborating with suppliers who provide extensive technical data and can recommend products based on environmental challenges can also be invaluable. Implementing regular inspections and maintenance can help extend the lifespan of the hinges in such conditions.
Scenario 3: Complexity in Installation and Integration
The Problem: B2B buyers often struggle with the complexity involved in the installation and integration of friction hinges into existing systems. For instance, a European furniture manufacturer might face issues when trying to incorporate friction hinges into a new line of products, resulting in delays and increased labor costs due to misalignment or improper mounting.
The Solution: To simplify the installation process, buyers should prioritize friction hinges that come with comprehensive installation guides and CAD files. Engaging with suppliers that offer technical support can also facilitate a smoother integration process. It is important to accurately measure the installation area and select hinges that fit the specific design parameters. Using hinges with pre-drilled holes or adjustable mounting options can also streamline the installation. Additionally, conducting a trial run with a small batch before full-scale production can help identify potential issues early on, thus saving time and resources. Providing training for installation staff can further enhance efficiency and reduce errors during the integration process.
Strategic Material Selection Guide for friction hinge
What Are the Common Materials Used for Friction Hinges?
Friction hinges are essential components in various applications, providing controlled movement and position retention for doors, lids, and panels. Selecting the right material for these hinges is crucial for ensuring optimal performance and longevity. Here, we analyze four common materials used in friction hinge manufacturing, focusing on their properties, advantages, disadvantages, and considerations for international B2B buyers.
How Does Aluminum Benefit Friction Hinges?
Aluminum is a popular choice for friction hinges due to its lightweight nature and excellent corrosion resistance. It typically exhibits a temperature rating of up to 150°C and can withstand moderate pressure, making it suitable for various environments.
Pros: The primary advantages of aluminum include its low weight, which helps reduce the overall weight of the product, and its resistance to rust and corrosion. This makes aluminum friction hinges ideal for outdoor applications or humid environments.
Cons: However, aluminum can be less durable than other metals, particularly under high-stress conditions. It may also be more expensive than plastic options, depending on the alloy used.
Impact on Application: Aluminum hinges are compatible with a wide range of media, including water and mild chemicals. However, they may not perform well in highly corrosive environments, such as those found in certain industrial applications.
Considerations for International Buyers: Buyers in regions like Africa and South America should ensure compliance with local standards such as ASTM or DIN, particularly regarding corrosion resistance and mechanical properties.
What Role Does Stainless Steel Play in Friction Hinges?
Stainless steel is renowned for its strength and durability, making it an excellent choice for friction hinges that require high performance in demanding applications. It typically offers a temperature rating of up to 300°C and is highly resistant to corrosion and wear.
Pros: The key advantages of stainless steel include its robust mechanical properties and resistance to rust, making it suitable for both indoor and outdoor use. Additionally, it can withstand harsh environmental conditions, including exposure to chemicals.
Cons: The primary drawback is its higher cost compared to aluminum and plastic options. Moreover, stainless steel hinges may be heavier, which could be a consideration in lightweight applications.
Impact on Application: Stainless steel is compatible with a variety of media, including oils and solvents, making it versatile for industrial settings.
Considerations for International Buyers: Buyers should check for compliance with international standards such as JIS and ASTM, especially in regions with stringent quality regulations like Europe and the Middle East.
How Do Plastic Materials Affect Friction Hinge Performance?
Plastic materials, particularly fiberglass-reinforced thermoplastics, are increasingly being used in friction hinges due to their lightweight and cost-effective nature. These materials typically have a temperature rating of up to 80°C and moderate pressure resistance.
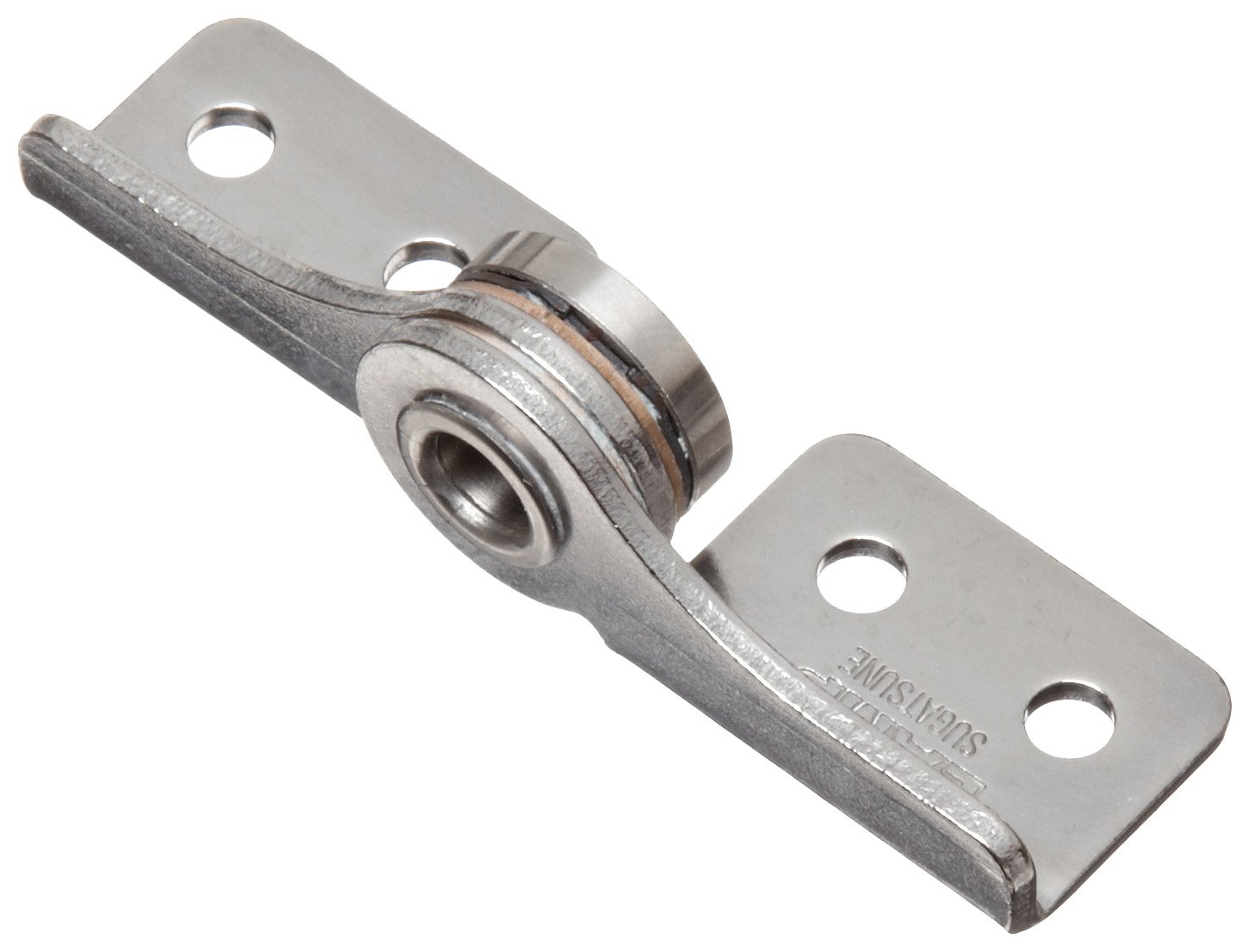
A stock image related to friction hinge.
Pros: The advantages of plastic hinges include their low cost and resistance to corrosion and chemicals. They are also lightweight, which can be beneficial in applications where weight is a concern.
Cons: However, plastic hinges may not offer the same level of durability as metal options, particularly under high-stress conditions. They can also be less stable at elevated temperatures.
Impact on Application: Plastic hinges are suitable for applications involving mild chemicals and moisture but may not be appropriate for high-temperature environments.
Considerations for International Buyers: Buyers should ensure that the plastic materials used comply with safety and environmental regulations relevant to their region, particularly in Europe where RoHS compliance is critical.
What Are the Advantages of Using Composite Materials for Friction Hinges?
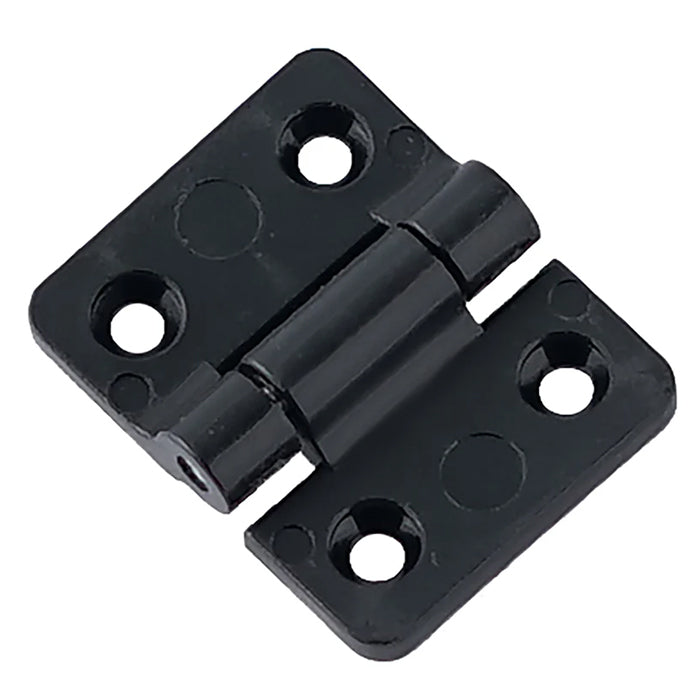
A stock image related to friction hinge.
Composite materials, which combine different materials to enhance performance, are becoming popular in friction hinge applications. They can offer a balance of strength, weight, and corrosion resistance, with temperature ratings varying widely based on the specific composite used.
Pros: The main advantages of composite materials include their high strength-to-weight ratio and resistance to environmental factors. They can be tailored to meet specific application requirements, making them versatile.
Cons: On the downside, composite materials can be more expensive and may involve complex manufacturing processes, which can increase production time.
Impact on Application: Composites are suitable for a wide range of media and environmental conditions, making them ideal for specialized applications.
Considerations for International Buyers: Buyers should verify that composite materials meet relevant industry standards and certifications, particularly in regions with strict quality control measures.
Summary of Material Selection for Friction Hinges
Material | Typical Use Case for Friction Hinge | Key Advantage | Key Disadvantage/Limitation | Relative Cost (Low/Med/High) |
---|---|---|---|---|
Aluminum | Lightweight applications | Excellent corrosion resistance | Less durable under high stress | Medium |
Stainless Steel | Industrial and outdoor applications | High strength and durability | Higher cost and weight | High |
Plastic | Cost-sensitive applications | Lightweight and cost-effective | Lower durability under stress | Low |
Composite | Specialized applications | Tailored performance and strength | Higher cost and complexity | Medium to High |
This strategic material selection guide serves as a valuable resource for international B2B buyers seeking to make informed decisions regarding friction hinge materials, ensuring compatibility and performance tailored to their specific applications.
In-depth Look: Manufacturing Processes and Quality Assurance for friction hinge
Friction hinges are critical components in various applications, providing positional control and stability for doors, lids, and panels. Understanding the manufacturing processes and quality assurance measures involved in producing these hinges is essential for international B2B buyers, especially those operating in regions such as Africa, South America, the Middle East, and Europe. This section delves into the typical manufacturing stages, quality control standards, and best practices for verifying supplier quality.
What Are the Main Stages of Manufacturing Friction Hinges?
Manufacturing friction hinges involves several key stages, each crucial for ensuring the final product meets the required specifications. The primary stages include material preparation, forming, assembly, and finishing.
1. Material Preparation: What Materials Are Used for Friction Hinges?
The first step in the manufacturing process involves selecting and preparing the appropriate materials. Friction hinges are typically made from a combination of metals, such as stainless steel or aluminum, and high-performance plastics. These materials are chosen for their durability, corrosion resistance, and ability to withstand the mechanical stresses that friction hinges endure.
During material preparation, raw materials are cut to size and may undergo treatments to enhance their properties, such as annealing or coating. For instance, coatings can improve wear resistance and aesthetics, making them suitable for various applications from electronics to heavy machinery.
2. Forming: How Are Friction Hinges Shaped?
The forming process involves shaping the prepared materials into the desired hinge components. This can be achieved through various techniques, including:
- Stamping: This method uses a die to cut and shape metal sheets into hinge parts. It is efficient for high-volume production and ensures uniformity.
- Machining: For precision components, CNC (Computer Numerical Control) machining is often employed. This technique allows for intricate designs and tight tolerances.
- Injection Molding: For plastic components, injection molding is used to create complex shapes and ensure consistency across batches.
Each method must be selected based on the specific design requirements and production volume.
3. Assembly: How Are Friction Hinges Assembled?
Once the individual components are formed, they are assembled into complete friction hinges. This stage typically involves:
- Joining Techniques: Components may be joined through welding, riveting, or using specialized adhesives, depending on the material and design.
- Torque Adjustment: During assembly, the friction mechanism is adjusted to achieve the desired torque specifications. This is crucial for ensuring that the hinge can hold a position securely while still allowing for smooth movement.
4. Finishing: What Finishing Processes Are Common?
The finishing stage enhances the aesthetic and functional properties of the friction hinges. Common finishing processes include:
- Coating: Applying a protective layer, such as powder coating or plating, to prevent corrosion and improve appearance.
- Polishing: This step is often employed for stainless steel components to achieve a smooth, shiny surface.
Finishing processes not only add to the durability of the hinges but also ensure they meet industry standards for appearance and functionality.
What Are the Quality Control Standards for Friction Hinges?
Quality assurance in the manufacturing of friction hinges is vital for ensuring reliability and performance. Various international standards and industry-specific certifications guide these processes.
1. Relevant International Standards: Which Standards Should Buyers Be Aware Of?
ISO 9001 is the most recognized quality management standard globally, applicable across industries, including hinge manufacturing. Compliance with ISO 9001 ensures that manufacturers have robust quality management systems in place, focusing on continuous improvement and customer satisfaction.
In addition to ISO standards, industry-specific certifications like CE marking (for products sold in the European Economic Area) and API (American Petroleum Institute) standards for products used in the oil and gas industry are crucial. These certifications indicate that the products meet stringent safety and performance criteria.
2. What Are the Quality Control Checkpoints in the Manufacturing Process?
Quality control checkpoints are integrated throughout the manufacturing process to identify and rectify defects early. Key checkpoints include:
- Incoming Quality Control (IQC): Inspects raw materials upon arrival to ensure they meet specified standards.
- In-Process Quality Control (IPQC): Monitors production processes and procedures to maintain quality during manufacturing.
- Final Quality Control (FQC): Conducts thorough inspections and tests on finished products to verify they meet all specifications before shipping.
How Can B2B Buyers Verify Supplier Quality?
For international B2B buyers, especially in regions like Africa, South America, the Middle East, and Europe, verifying supplier quality is crucial for mitigating risks associated with product failures.
1. What Methods Can Be Used for Supplier Audits?
Conducting supplier audits is an effective way to assess compliance with quality standards. Buyers can perform:
- On-site Audits: Visiting the manufacturing facility to evaluate processes, equipment, and overall operational practices.
- Documentation Reviews: Examining quality assurance documentation, including inspection reports, certifications, and compliance records.
2. How Can Third-Party Inspections Enhance Quality Assurance?
Engaging third-party inspection services can provide an unbiased evaluation of the supplier’s quality control processes. This can include:
- Product Testing: Independent testing of friction hinges for performance, durability, and compliance with relevant standards.
- Factory Audits: Third-party organizations can conduct comprehensive audits to verify adherence to quality management systems and manufacturing practices.
What Nuances Should International Buyers Consider in Quality Control?
International buyers must be aware of specific nuances in quality control that may vary by region. For instance, understanding local regulations, cultural differences in manufacturing practices, and varying standards of quality can impact supplier selection and product reliability.
Additionally, building strong relationships with suppliers through clear communication regarding quality expectations can lead to improved outcomes. Establishing a feedback loop where performance metrics are shared can foster continuous improvement and innovation in product development.
In conclusion, understanding the manufacturing processes and quality assurance measures for friction hinges is essential for international B2B buyers. By focusing on material preparation, forming, assembly, and finishing, alongside robust quality control mechanisms, buyers can ensure they select reliable suppliers that meet their specific needs.
Practical Sourcing Guide: A Step-by-Step Checklist for ‘friction hinge’
This practical sourcing guide aims to assist international B2B buyers in navigating the procurement of friction hinges effectively. By following this step-by-step checklist, you can ensure that you make informed decisions that meet your specific operational needs.
Step 1: Define Your Technical Specifications
Before you start sourcing friction hinges, it’s essential to outline your technical requirements. Consider the specific application of the hinge, such as load capacity, opening angle, and whether you need adjustable torque.
– Torque Requirements: Determine the amount of resistance needed for your application to ensure stability.
– Material Considerations: Decide on the material (e.g., stainless steel, plastic) based on environmental factors like corrosion resistance.
Step 2: Research Market Trends and Innovations
Stay updated on the latest trends and innovations in the friction hinge market. This knowledge can help you identify products that enhance functionality and durability.
– Product Innovations: Look for features such as concealed designs or eco-friendly materials.
– Industry Applications: Understand how different industries are utilizing friction hinges to improve efficiency.
Step 3: Evaluate Potential Suppliers
Before committing, it’s crucial to vet suppliers thoroughly. Request company profiles, case studies, and references from buyers in a similar industry or region.
– Supplier Experience: Check for industry experience and expertise in manufacturing friction hinges.
– Quality Assurance: Verify if the supplier adheres to international quality standards (e.g., ISO certifications).
Step 4: Request Samples for Testing
Always request samples of the friction hinges you are considering. Testing samples allows you to evaluate their performance and suitability for your specific application.
– Performance Testing: Assess the hinge’s torque and opening angles under operational conditions.
– Material Durability: Examine the sample for signs of wear or degradation, especially in harsh environments.
Step 5: Negotiate Pricing and Terms
Once you’ve identified potential suppliers, engage in negotiations regarding pricing, lead times, and payment terms. This step is crucial for maximizing value while ensuring timely delivery.
– Bulk Pricing: Inquire about discounts for larger orders or long-term contracts.
– Payment Flexibility: Discuss payment terms that align with your cash flow needs.
Step 6: Verify Compliance with Regulations
Ensure that the friction hinges you are sourcing comply with relevant regulations and standards in your region. This is particularly important for buyers in industries with stringent safety requirements.
– Regulatory Standards: Check if the hinges are RoHS compliant or meet other local regulations.
– Documentation: Request necessary certifications and test reports from suppliers.
Step 7: Establish a Clear Communication Channel
Effective communication with your supplier is essential throughout the sourcing process. Establishing clear lines of communication can help resolve issues quickly and ensure a smooth procurement experience.
– Point of Contact: Designate a specific person for communication to streamline discussions.
– Feedback Mechanism: Set up a process for providing feedback on product performance and supplier service.
By following this checklist, international B2B buyers can strategically approach the sourcing of friction hinges, ensuring they select the right products for their operational needs while fostering strong supplier relationships.
Comprehensive Cost and Pricing Analysis for friction hinge Sourcing
What are the Key Cost Components in Friction Hinge Manufacturing?
Understanding the cost structure of friction hinge sourcing is essential for international B2B buyers. The primary cost components include:
-
Materials: The choice of materials significantly impacts pricing. Common materials include stainless steel, plastic, and fiberglass-reinforced thermoplastic. Higher-quality materials may increase costs but can lead to improved durability and functionality.
-
Labor: Labor costs vary by region and production scale. In countries with lower labor costs, such as parts of Africa and South America, sourcing from local manufacturers can reduce overall expenses.
-
Manufacturing Overhead: This includes indirect costs like factory utilities, equipment maintenance, and administrative expenses. Efficient production processes can help minimize overhead costs.
-
Tooling: The initial setup for tooling can be a significant one-time expense. Custom designs may require more specialized tooling, which can increase costs.
-
Quality Control (QC): Implementing stringent QC measures can add to the cost but is crucial for ensuring product reliability, especially for high-stakes applications.
-
Logistics: Transportation and handling costs can vary greatly depending on the shipping methods and distances involved. International shipping can introduce additional complexities and costs.
-
Margin: Suppliers typically factor in their profit margin, which can vary based on market conditions and competition.
How Do Price Influencers Affect Friction Hinge Costs?
Several factors can influence the pricing of friction hinges:
-
Volume/MOQ (Minimum Order Quantity): Purchasing in bulk can lead to significant discounts. Suppliers are often willing to negotiate prices based on order size, making it advantageous for buyers to consolidate their orders.
-
Specifications and Customization: Tailored designs or specific features (like adjustable torque) can increase costs. Buyers should weigh the benefits of customization against their budget constraints.
-
Materials: The choice of material not only impacts the cost but also the performance characteristics of the hinge. For instance, corrosion-resistant materials may cost more but can offer better longevity in harsh environments.
-
Quality and Certifications: Products that meet international quality standards (like ISO or RoHS compliance) may come at a premium but can provide peace of mind regarding safety and performance.
-
Supplier Factors: The reputation and reliability of the supplier can affect pricing. Established suppliers may charge more due to their quality assurance processes, while newer suppliers might offer lower prices to gain market entry.
-
Incoterms: Understanding the shipping terms (like FOB, CIF, etc.) is critical as they dictate the responsibilities of buyers and sellers regarding shipping costs and risk.
What Tips Can Help Buyers Negotiate Better Prices for Friction Hinges?
Negotiating effectively can lead to more favorable pricing for friction hinges:
-
Research and Compare: Conduct thorough market research to understand average pricing and available suppliers. Use this information to negotiate better terms.
-
Total Cost of Ownership (TCO): Consider the long-term costs associated with the hinges, including maintenance and replacement. Sometimes a higher upfront cost can lead to lower TCO.
-
Be Flexible with Specifications: If possible, be open to slight modifications in specifications that could lead to cost savings without significantly impacting functionality.
-
Build Relationships with Suppliers: Establishing strong relationships can lead to better deals and priority treatment in terms of pricing and availability.
-
Timing of Orders: Aligning purchases with off-peak times for suppliers can sometimes yield discounts, as manufacturers may be more willing to negotiate during slower periods.
Conclusion: Why is it Important to Understand Pricing Nuances in International Markets?
Understanding the cost structure and pricing nuances is vital for international B2B buyers, especially in diverse regions like Africa, South America, the Middle East, and Europe. Prices can vary significantly based on local market conditions, supplier capabilities, and logistical considerations. By being informed about these factors, buyers can make strategic sourcing decisions that align with their budget and operational needs.
Disclaimer: The prices mentioned here are indicative and can vary based on supplier, order volume, and market conditions. Always seek quotes from multiple suppliers to ensure the best pricing.
Alternatives Analysis: Comparing friction hinge With Other Solutions
Exploring Alternatives to Friction Hinges
When considering the right hinge solution for your business needs, it’s essential to evaluate various alternatives to friction hinges. Each option comes with distinct advantages and disadvantages that can impact the functionality, durability, and cost-effectiveness of your application. Below, we provide a detailed comparison of friction hinges against two viable alternatives: Torque Hinges and Piano Hinges.
Comparison Table
Comparison Aspect | Friction Hinge | Torque Hinge | Piano Hinge |
---|---|---|---|
Performance | Offers adjustable resistance; ideal for holding positions | Provides consistent resistance; great for controlled motion | Allows for continuous support; good for heavy doors |
Cost | Moderate to high cost; varies by customization | Generally moderate; depending on specifications | Low to moderate; economical for long lengths |
Ease of Implementation | Requires precise alignment; moderate complexity | Similar alignment needs; generally straightforward | Easy to install; can be cut to length |
Maintenance | Low maintenance; durable materials | Low maintenance; long-lasting | Low maintenance; depends on material quality |
Best Use Case | Ideal for applications needing varied positioning (e.g., laptop screens) | Suitable for doors and lids requiring stable angles (e.g., electronics) | Best for heavy-duty applications (e.g., piano lids, cabinets) |
Detailed Breakdown of Alternatives
What Are Torque Hinges and Their Advantages?
Torque hinges, also referred to as friction hinges, utilize a similar principle but typically offer a more consistent resistance throughout their range of motion. They are particularly effective in applications where a stable angle is required for extended periods. This makes them suitable for electronics and machinery where reliable positioning is crucial. However, while they provide excellent hold, torque hinges may lack the fine-tuned adjustability found in some friction hinges, which can limit their versatility in certain applications.
Why Choose Piano Hinges?
Piano hinges, also known as continuous hinges, provide a robust solution for heavy doors and panels. They run the entire length of the door or lid, distributing weight evenly and offering excellent support. This makes them ideal for large applications such as cabinets, gates, and piano lids. While they are generally more affordable and easier to install, they do not provide the same level of position control as friction or torque hinges. This means they may not be suitable for applications where precise positioning is critical.
Conclusion: How to Choose the Right Hinge Solution
When selecting the best hinge solution for your needs, consider the specific application, required performance, and budget constraints. Friction hinges offer the advantage of adjustable positioning, making them ideal for applications where variable angles are necessary. Torque hinges provide consistent resistance and are well-suited for stable installations, while piano hinges offer a cost-effective solution for heavy-duty needs. By carefully assessing your requirements, you can make an informed decision that balances functionality, cost, and ease of implementation, ensuring optimal performance for your projects across diverse markets in Africa, South America, the Middle East, and Europe.
Essential Technical Properties and Trade Terminology for friction hinge
What Are the Key Technical Properties of Friction Hinges?
When selecting friction hinges for your B2B applications, understanding their technical properties is essential for ensuring optimal performance. Here are some critical specifications to consider:
1. Material Grade
Friction hinges are typically made from various materials, including stainless steel, plastic, and aluminum. The choice of material affects durability, resistance to corrosion, and overall strength. For example, stainless steel offers excellent strength and resistance to environmental factors, making it ideal for outdoor applications. Buyers should evaluate the material based on their specific environmental conditions and application requirements.
2. Torque Rating
Torque rating measures the amount of rotational force a hinge can withstand while maintaining a desired position. It is expressed in units such as gf/cm or kgf/cm. Higher torque ratings allow for heavier doors or lids to be held open at a specific angle. Understanding torque requirements is crucial for ensuring the hinge can support the weight of the application, especially in industries like automotive and electronics.
3. Load Capacity
Load capacity refers to the maximum weight a friction hinge can support without compromising its functionality. This property is essential for applications where the hinge will bear significant weight over time. Buyers must assess their specific load requirements to prevent hinge failure, which could lead to operational inefficiencies or safety hazards.
4. Adjustability
Some friction hinges feature adjustable friction settings, allowing users to modify the resistance to movement. This is particularly important in applications requiring different levels of resistance at various times. An adjustable hinge provides flexibility and can accommodate changing operational needs, making it a valuable feature for manufacturers seeking efficiency.
5. Mounting Method
The mounting method determines how the hinge is installed, impacting its functionality and ease of use. Common mounting methods include front mount, concealed mount, and countersunk options. Selecting the appropriate mounting method is crucial for ensuring a secure and stable installation that meets design requirements and aesthetic preferences.
What Are Common Trade Terms Related to Friction Hinges?
Navigating the B2B market for friction hinges involves understanding industry-specific terminology. Here are some key terms to familiarize yourself with:
1. OEM (Original Equipment Manufacturer)
An OEM is a company that produces parts or equipment that may be marketed by another manufacturer. In the context of friction hinges, an OEM may design and produce custom hinges for specific applications, allowing buyers to receive tailored solutions that meet their unique specifications.
2. MOQ (Minimum Order Quantity)
MOQ refers to the smallest number of units a supplier is willing to sell. Understanding the MOQ is vital for B2B buyers, as it can impact inventory management and overall costs. Buyers should negotiate MOQs that align with their purchasing needs to avoid excess inventory or stock shortages.
3. RFQ (Request for Quotation)
An RFQ is a document sent to suppliers requesting pricing information for specific products or services. In the friction hinge market, an RFQ allows buyers to compare prices, terms, and conditions from multiple suppliers, facilitating informed purchasing decisions.
4. Incoterms (International Commercial Terms)
Incoterms are standardized international shipping terms that define the responsibilities of buyers and sellers in a transaction. Familiarity with Incoterms is crucial for international B2B buyers, as it clarifies issues like shipping costs, risk transfer, and delivery responsibilities, ensuring smoother transactions across borders.
5. Lead Time
Lead time is the amount of time between placing an order and receiving the product. Understanding lead times is essential for project planning and inventory management. Buyers should communicate with suppliers to establish realistic lead times that align with their operational timelines.
By grasping these technical properties and trade terminologies, B2B buyers can make informed decisions when sourcing friction hinges, ultimately leading to improved efficiency and reduced operational risks.
Navigating Market Dynamics and Sourcing Trends in the friction hinge Sector
What Are the Current Market Dynamics and Key Trends in the Friction Hinge Sector?
The friction hinge market is experiencing a robust growth trajectory, driven by increased demand across various sectors such as electronics, automotive, and furniture. As businesses globally look for solutions that enhance functionality while maintaining aesthetic appeal, friction hinges have gained prominence. Notably, the surge in smart home technology and the need for user-friendly appliances have catalyzed the adoption of adjustable friction hinges, allowing for customizable resistance and positioning.
International B2B buyers from regions such as Africa, South America, the Middle East, and Europe should pay attention to emerging trends such as automation and IoT integration. Manufacturers are increasingly developing friction hinges that incorporate smart technology, enabling remote control and monitoring capabilities. This evolution not only enhances user experience but also opens new avenues for product applications in security and convenience.
Moreover, the sourcing landscape is evolving, with buyers now prioritizing manufacturers that offer transparency in their supply chains. The rise of digital marketplaces has facilitated easier access to global suppliers, enabling buyers to compare products and prices across borders. This shift is particularly beneficial for buyers in Africa and South America, where traditional sourcing channels may be less accessible.
How Is Sustainability Influencing Sourcing in the Friction Hinge Sector?
Sustainability has become a pivotal consideration for B2B buyers in the friction hinge sector. As environmental concerns grow, companies are increasingly expected to adopt ethical sourcing practices. This includes utilizing materials that minimize ecological impact, such as recycled metals and biodegradable plastics. Buyers should actively seek suppliers who provide certifications that demonstrate their commitment to sustainability, such as ISO 14001 for environmental management and RoHS compliance for hazardous substances.
The importance of ethical supply chains cannot be overstated; consumers are becoming more discerning, favoring brands that prioritize sustainability. For international buyers, particularly in regions with stringent environmental regulations, selecting suppliers who align with these values can mitigate risks and enhance brand reputation. Furthermore, integrating ‘green’ materials into product design not only supports environmental goals but can also yield cost savings through energy-efficient manufacturing processes.
How Have Friction Hinges Evolved Over Time?
The evolution of friction hinges can be traced back to their initial use in basic mechanical applications, where they simply served as pivot points. Over the years, innovations in materials and engineering have transformed them into sophisticated components capable of precise motion control. Today, friction hinges are integral to modern appliances, offering features like adjustable torque settings and enhanced durability.
The introduction of advanced materials, such as fiberglass-reinforced thermoplastics, has further broadened their application scope, making them suitable for diverse environments, from industrial machinery to consumer electronics. This evolution not only reflects technological advancements but also highlights the increasing demand for reliable and efficient solutions in the B2B marketplace.
As friction hinges continue to adapt to industry needs, buyers are encouraged to stay informed about the latest advancements and trends. Understanding these dynamics will enable B2B buyers to make informed sourcing decisions that align with their operational goals and sustainability commitments.
Frequently Asked Questions (FAQs) for B2B Buyers of friction hinge
-
How do I choose the right friction hinge for my application?
Choosing the right friction hinge involves evaluating several factors, including the weight and size of the door or lid, the desired angle of operation, and the environmental conditions. Assess the torque specifications, which determine how much resistance the hinge can provide. Consider whether you need an adjustable or fixed torque hinge based on your application. Additionally, ensure that the materials are suitable for your specific environment, such as corrosion resistance for outdoor use or compliance with industry standards. -
What are the advantages of using friction hinges in my products?
Friction hinges offer several benefits, including precise control of movement, the ability to hold doors or lids at specific angles, and reduced risk of slamming shut. This feature enhances user experience, particularly in applications like electronics or automotive where ease of access is crucial. Furthermore, they can be customized for specific torque requirements, making them versatile for various industries. Using friction hinges can also improve product longevity by reducing wear and tear on traditional hinge mechanisms. -
What should I consider when sourcing friction hinges from international suppliers?
When sourcing friction hinges internationally, consider factors such as supplier reputation, product quality, compliance with international standards, and delivery timelines. Conduct thorough due diligence by checking references and certifications. It’s also crucial to understand the supplier’s manufacturing capabilities and whether they can meet your specific requirements. Additionally, inquire about their quality assurance processes to ensure consistent product quality and reliability. -
What are the common minimum order quantities (MOQs) for friction hinges?
Minimum order quantities (MOQs) for friction hinges can vary significantly between suppliers, typically ranging from 100 to 1,000 units. Some manufacturers may offer lower MOQs for standard products, while custom designs often require larger orders. It’s advisable to discuss MOQs upfront with potential suppliers to understand their flexibility and whether they can accommodate smaller orders, especially for new product trials or smaller-scale projects. -
How can I customize friction hinges to fit my specific needs?
Customization of friction hinges can involve adjustments to dimensions, torque settings, and materials. Many suppliers offer design services where you can specify the required torque range, size, and finish. It’s essential to communicate your application requirements clearly to the manufacturer. Additionally, consider requesting prototypes to test functionality before committing to a larger order, ensuring that the customized hinges perform as expected in your applications. -
What payment terms should I expect when purchasing friction hinges internationally?
Payment terms for international purchases of friction hinges typically vary by supplier. Common terms include upfront payment, 30% deposit with the balance due before shipment, or net 30/60 days after delivery. It’s crucial to clarify payment methods accepted, such as wire transfers, letters of credit, or online payment platforms. Establishing clear terms early in negotiations can help avoid misunderstandings and ensure smooth transactions. -
How do I ensure quality assurance when sourcing friction hinges?
Ensuring quality assurance when sourcing friction hinges involves several strategies. First, request detailed product specifications and certifications from suppliers. Conduct factory audits if possible, or consider third-party inspections. Implement a quality control process that includes testing samples upon receipt to verify that they meet your standards. Establishing a clear communication channel with your supplier regarding quality expectations can also help prevent issues down the line. -
What logistics considerations should I keep in mind when importing friction hinges?
When importing friction hinges, consider logistics aspects such as shipping methods, customs duties, and delivery timelines. Evaluate whether you need air freight for faster delivery or sea freight for cost-effectiveness. Understand the customs regulations in your country to avoid delays and additional fees. Working with a reliable freight forwarder can help streamline the shipping process, ensuring that your products arrive safely and on time. Additionally, factor in lead times and order processing times when planning your inventory management.
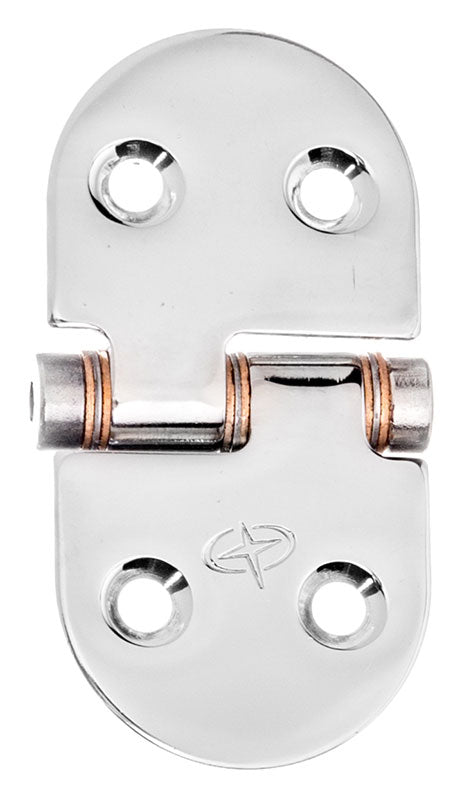
A stock image related to friction hinge.
Important Disclaimer & Terms of Use
⚠️ Important Disclaimer
The information provided in this guide, including content regarding manufacturers, technical specifications, and market analysis, is for informational and educational purposes only. It does not constitute professional procurement advice, financial advice, or legal advice.
While we have made every effort to ensure the accuracy and timeliness of the information, we are not responsible for any errors, omissions, or outdated information. Market conditions, company details, and technical standards are subject to change.
B2B buyers must conduct their own independent and thorough due diligence before making any purchasing decisions. This includes contacting suppliers directly, verifying certifications, requesting samples, and seeking professional consultation. The risk of relying on any information in this guide is borne solely by the reader.
Strategic Sourcing Conclusion and Outlook for friction hinge
What Are the Key Takeaways for B2B Buyers of Friction Hinges?
As we conclude our exploration of friction hinges, it is essential to recognize the critical role they play in various applications across industries. For international B2B buyers, particularly in Africa, South America, the Middle East, and Europe, understanding the nuances of friction hinge sourcing can lead to significant operational efficiencies. Prioritize suppliers who offer a range of torque options and adjustable features to meet your specific needs, ensuring that the hinges can provide optimal performance in your unique environments.
Why Is Strategic Sourcing Important for Friction Hinges?
Strategic sourcing not only enhances your procurement processes but also builds long-term relationships with reliable manufacturers. By evaluating suppliers based on their product quality, compliance with industry standards, and capacity for customization, you can secure the best solutions for your business. Moreover, engaging with suppliers who understand local market dynamics can provide a competitive edge.
How Can You Prepare for Future Trends in Friction Hinge Technology?
Looking ahead, the demand for innovative and sustainable solutions in hinge technology will continue to rise. By staying informed about advancements in materials and design, B2B buyers can adapt to changing market conditions and consumer preferences. Leverage this knowledge to make informed purchasing decisions that align with your long-term strategic goals.
In conclusion, as you navigate the complexities of sourcing friction hinges, focus on building partnerships that foster innovation and quality. This proactive approach will not only enhance your operational capabilities but also position your business for sustained growth in an ever-evolving market landscape.