Discover the Best Air Fliter: A Complete Buying Guide (2025)
Introduction: Navigating the Global Market for air fliter
Navigating the global market for air filters can be a daunting task for B2B buyers, particularly when sourcing high-quality products that meet specific operational needs and regulatory standards. With increasing awareness of indoor air quality and its impact on health, businesses across Africa, South America, the Middle East, and Europe are seeking reliable air filtration solutions. This comprehensive guide offers valuable insights into various types of air filters, their applications, and the nuances of supplier vetting to ensure that you make informed purchasing decisions.
The guide delves into the essential aspects of air filters, including the different types available—such as HEPA, activated carbon, and electrostatic filters—and their respective MERV ratings to help you assess filtration efficiency. It also outlines key factors influencing cost, such as material quality and customization options, which can significantly affect your procurement strategy. Furthermore, we address the importance of choosing reputable suppliers, offering tips on how to evaluate their credentials, reliability, and customer service.
By equipping international B2B buyers with actionable insights and a thorough understanding of the air filter market, this guide empowers you to navigate challenges effectively and optimize your purchasing decisions. Whether you are based in Egypt, Kenya, or elsewhere, the information provided will enhance your ability to secure the best air filtration solutions tailored to your business needs.
Understanding air fliter Types and Variations
Type Name | Key Distinguishing Features | Primary B2B Applications | Brief Pros & Cons for Buyers |
---|---|---|---|
HEPA Filters | High Efficiency Particulate Air (HEPA) filters capture 99.97% of particles down to 0.3 microns. | Hospitals, laboratories, and clean rooms. | Pros: Excellent air quality, reduces allergens. Cons: Higher cost, requires regular replacement. |
Electrostatic Filters | Uses static electricity to attract and trap particles. | Industrial settings, HVAC systems. | Pros: Effective for smaller particles, reusable. Cons: May require cleaning and maintenance. |
Activated Carbon Filters | Contains carbon that absorbs odors and gases. | Restaurants, chemical plants, and offices. | Pros: Effective for odor removal, improves air quality. Cons: Limited particle filtration capability. |
Pleated Filters | Increased surface area for better airflow and filtration efficiency. | Commercial buildings, schools, and offices. | Pros: Longer lifespan, better airflow. Cons: May be more expensive upfront. |
HEPA-Type Filters | Similar to HEPA but may not meet strict standards. | General use in homes and small offices. | Pros: Cost-effective, decent filtration. Cons: Less effective than true HEPA filters. |
What Are HEPA Filters and When Should They Be Used?
HEPA filters are known for their exceptional ability to trap fine particles, making them essential in environments where air quality is critical, such as hospitals and laboratories. For B2B buyers, investing in HEPA filters ensures compliance with health regulations and enhances the safety of sensitive operations. However, their higher cost and the need for regular replacements can be a consideration, especially for businesses with budget constraints.
How Do Electrostatic Filters Work and What Are Their Benefits?
Electrostatic filters utilize static electricity to attract and capture airborne particles. This feature makes them particularly effective in industrial settings and HVAC systems, where they can significantly improve air quality. B2B buyers should consider the maintenance aspect, as these filters require regular cleaning to maintain their efficiency. Their reusable nature can be a cost-saving advantage in the long run.
What Are Activated Carbon Filters and Where Are They Most Effective?
Activated carbon filters are designed to absorb odors and harmful gases, making them ideal for environments such as restaurants and chemical plants. For B2B buyers, the choice of activated carbon filters can greatly improve the comfort of employees and customers. However, it’s important to note that while they excel at odor removal, they may not filter out particulate matter as effectively as other types.
Why Choose Pleated Filters for Commercial Applications?
Pleated filters are designed with an increased surface area, allowing for better airflow and filtration efficiency. They are commonly used in commercial buildings, schools, and offices, where maintaining air quality is crucial. For B2B buyers, the longer lifespan of pleated filters can lead to lower maintenance costs over time, although they may require a higher initial investment.
What Are HEPA-Type Filters and Their Typical Use Cases?
HEPA-type filters provide a cost-effective alternative to true HEPA filters, capturing a decent amount of particles without meeting the strict standards of HEPA certification. They are suitable for general use in homes and small offices, making them attractive for B2B buyers looking for budget-friendly options. However, businesses should weigh their effectiveness against the specific air quality needs of their environments.
Key Industrial Applications of air fliter
Industry/Sector | Specific Application of Air Filter | Value/Benefit for the Business | Key Sourcing Considerations for this Application |
---|---|---|---|
Manufacturing | HVAC Systems for Dust Control | Reduces equipment wear and improves air quality | MERV rating, filter size, and compatibility with existing systems |
Food Processing | Air Filtration in Clean Rooms | Ensures compliance with health regulations | Certifications, filter material, and effectiveness against contaminants |
Pharmaceuticals | Air Quality Management in Production Areas | Protects sensitive processes and products | ISO certifications, filter lifespan, and particle size efficiency |
Automotive | Paint Booth Filtration Systems | Enhances finish quality and reduces contaminants | Filter type, airflow requirements, and maintenance frequency |
Healthcare Facilities | Air Filtration in Patient Care Areas | Improves patient safety and comfort | HEPA certification, filter change frequency, and installation support |
How is Air Filter Technology Utilized in Manufacturing?
In the manufacturing sector, air filters play a crucial role in HVAC systems to control dust and particulate matter. This is particularly important in environments where machinery is sensitive to dirt and debris. By maintaining clean air, businesses can reduce equipment wear and tear, ultimately leading to lower maintenance costs and increased operational efficiency. International buyers must consider the Minimum Efficiency Reporting Value (MERV) ratings to ensure that filters meet the specific dust control needs of their facilities.
What is the Role of Air Filters in Food Processing?
Air filtration in food processing facilities is vital for maintaining a clean and safe environment. Filters are used in clean rooms to prevent contamination that could compromise product integrity. Compliance with health regulations is a key driver for this application, as air quality directly impacts food safety. Buyers should focus on certifications that validate the effectiveness of filters against various contaminants, ensuring they select products that meet stringent industry standards.
Why are Air Filters Important in Pharmaceuticals?
In pharmaceutical manufacturing, air quality management is critical due to the sensitivity of production processes. Air filters help to protect products from airborne contaminants that could affect their efficacy. This sector often requires filters with ISO certifications and specific particle size efficiencies to ensure compliance with regulatory standards. B2B buyers must prioritize sourcing filters that offer long lifespans and reliable performance in controlling air quality.
How are Air Filters Used in Automotive Paint Booths?
Automotive paint booths utilize specialized air filters to enhance finish quality by trapping airborne particles that could mar paint jobs. A clean air environment is essential for achieving high-quality finishes, and effective filtration can reduce the need for rework. Buyers should consider the type of filters used, airflow requirements, and the frequency of maintenance to ensure optimal performance in their paint booths.
What Benefits Do Air Filters Provide in Healthcare Facilities?
In healthcare settings, air filtration systems are crucial for patient care areas to improve air quality and reduce the risk of airborne infections. High-efficiency particulate air (HEPA) filters are commonly used to ensure a safe environment for patients. When sourcing filters, healthcare facilities must focus on certification standards, recommended filter change frequencies, and installation support to maintain compliance and safeguard patient health.
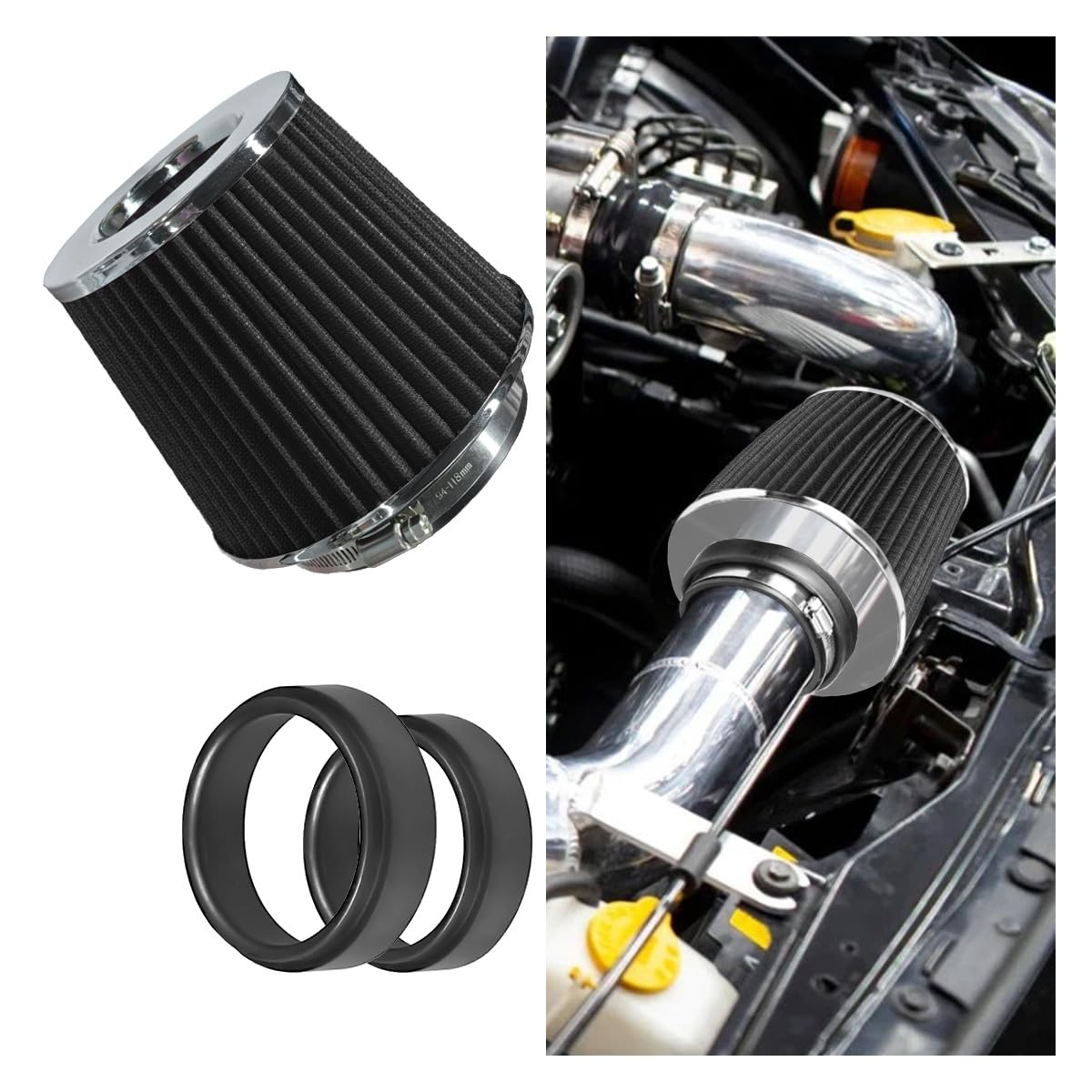
A stock image related to air fliter.
3 Common User Pain Points for ‘air fliter’ & Their Solutions
Scenario 1: Sizing Issues Leading to Inefficient Air Filtration
The Problem: Many B2B buyers, especially in industries such as manufacturing or healthcare, face significant challenges in sourcing the correct size of air filters for their HVAC systems. Incorrect sizing can lead to inadequate filtration, increased energy consumption, and ultimately higher operational costs. For instance, a buyer in an industrial facility may purchase filters that are too small or too large for their systems, causing air bypass and decreased indoor air quality. This not only impacts the health of employees but can also lead to compliance issues with health and safety regulations.
The Solution: To mitigate sizing issues, B2B buyers should conduct a thorough inventory of their HVAC systems before making a purchase. This includes measuring the dimensions of existing filters and consulting the system’s specifications to determine the required filter size. Investing in a filter finder tool offered by many suppliers can simplify this process. Additionally, buyers should consider ordering custom-sized filters if standard sizes are not available. Establishing a relationship with a reliable supplier that offers a wide range of sizes and custom options can ensure that the right filters are always on hand, improving operational efficiency and compliance with health standards.
Scenario 2: Inconsistent Quality of Air Filters
The Problem: Another common pain point for B2B buyers is the inconsistency in the quality of air filters, which can vary significantly between manufacturers. For instance, a buyer sourcing filters for a hospital may find that some brands do not effectively trap allergens or pathogens, putting patients at risk. This inconsistency can lead to frustration, as companies must often deal with frequent replacements or even potential health hazards due to poor air quality.
The Solution: To address quality concerns, buyers should prioritize sourcing air filters from reputable manufacturers that provide detailed product specifications, including MERV ratings and testing certifications. Engaging in supplier audits and seeking recommendations from industry peers can also help in identifying reliable vendors. Buyers should consider trialing a few brands before committing to larger orders. Additionally, establishing a regular review process to assess the performance of filters can help in maintaining air quality standards and ensuring that only the best products are used in their facilities.
Scenario 3: Lack of Knowledge on Filter Maintenance and Replacement
The Problem: Many B2B buyers struggle with understanding the maintenance schedules for air filters, leading to either premature replacements or excessive delays in changing filters. For example, a facility manager may overlook the need for regular replacements, resulting in clogged filters that reduce airflow and efficiency. This not only increases energy costs but can also damage HVAC systems over time, leading to costly repairs or replacements.
The Solution: To prevent maintenance issues, B2B buyers should implement a proactive maintenance schedule based on the specific needs of their environment. This includes setting reminders for filter replacements based on usage and environmental conditions. Suppliers can assist by offering filter subscription services that automate the ordering process when replacements are due. Additionally, educating staff about the importance of air filter maintenance and incorporating it into regular facility management training can ensure that everyone is aware of the best practices for maintaining air quality. By establishing a clear maintenance protocol, buyers can enhance the longevity of their HVAC systems and improve overall operational efficiency.
Strategic Material Selection Guide for air fliter
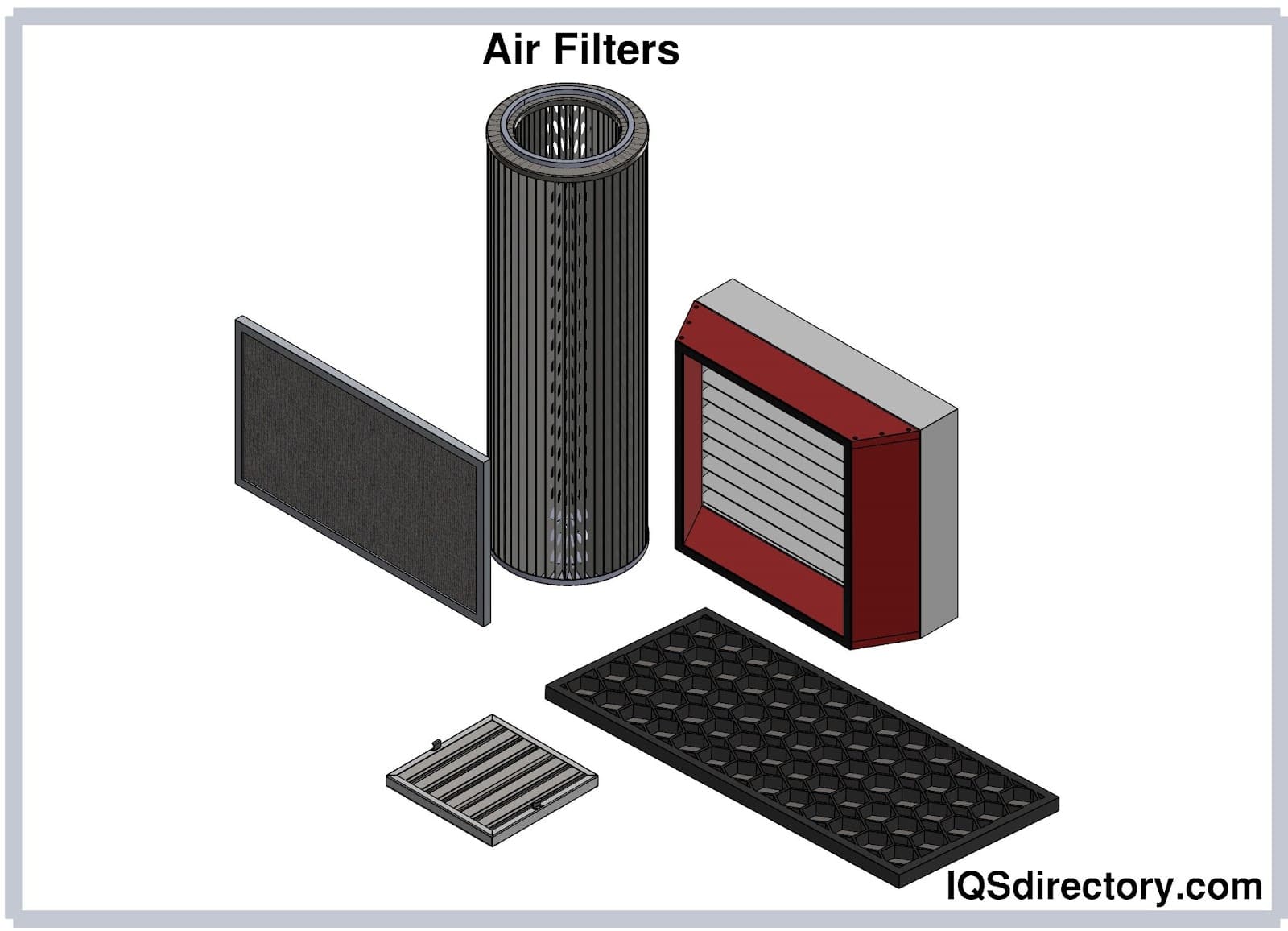
A stock image related to air fliter.
When selecting materials for air filters, international B2B buyers must consider various properties and implications that affect performance, cost, and compliance. Below is an analysis of four common materials used in air filter manufacturing, focusing on their key properties, advantages, disadvantages, and specific considerations for buyers from regions such as Africa, South America, the Middle East, and Europe.
What Are the Key Properties of Fiberglass in Air Filters?
Fiberglass is a widely used material in air filters due to its excellent filtration capabilities. It can withstand high temperatures and is resistant to moisture, making it suitable for various environments. The typical temperature rating for fiberglass filters is around 250°F (121°C).
Pros: Fiberglass filters are generally low-cost, lightweight, and easy to manufacture. They provide good air flow and can capture larger particles effectively.
Cons: However, they may not be as durable as other materials, with a shorter lifespan and lower efficiency in capturing smaller particles compared to pleated or HEPA filters.
Impact on Application: Fiberglass filters are ideal for commercial HVAC systems but may not meet stringent air quality standards required in sensitive environments, such as hospitals or laboratories.
Considerations for International Buyers: Compliance with local standards, such as ASTM or DIN, is crucial. Buyers in regions with high humidity, like parts of Africa and South America, should consider the moisture resistance of fiberglass filters.
How Does Polyester Compare as an Air Filter Material?
Polyester is another common material used in air filters, known for its versatility and efficiency. It can handle temperatures up to 300°F (149°C) and is resistant to chemicals and moisture.
Pros: Polyester filters are durable, have a longer lifespan than fiberglass, and can effectively capture allergens and fine particles. They are also available in various thicknesses and sizes, making them customizable for specific applications.
Cons: The manufacturing process can be more complex, leading to higher costs. Additionally, polyester filters may require more frequent replacement in high-dust environments.
Impact on Application: Polyester filters are suitable for both residential and commercial applications, especially where air quality is a priority.
Considerations for International Buyers: Buyers should ensure that polyester filters meet local air quality standards and consider the cost implications of importing these materials.
What Are the Advantages of HEPA Filters in Air Filtration?
High-Efficiency Particulate Air (HEPA) filters are known for their superior filtration capabilities, capturing 99.97% of particles that are 0.3 microns or larger. They can operate effectively at temperatures up to 200°F (93°C).
Pros: HEPA filters provide the highest level of air quality and are essential in environments that require stringent air cleanliness, such as hospitals and laboratories.
Cons: The main drawbacks are their higher cost and the need for more robust HVAC systems to accommodate the lower airflow rates.
Impact on Application: HEPA filters are ideal for applications where air purity is critical, but they may not be necessary for all environments.
Considerations for International Buyers: Compliance with international standards, such as EN 1822, is essential. Buyers should also be aware of the increased operational costs associated with HEPA filters.
How Do Electrostatic Filters Function in Air Filtration?
Electrostatic filters use static electricity to attract and trap particles, making them highly effective at capturing dust, pollen, and other allergens. They can handle temperatures up to 180°F (82°C).
Pros: These filters are washable and reusable, leading to lower long-term costs. They also provide good airflow and can capture smaller particles compared to traditional filters.
Cons: However, they may require regular cleaning to maintain efficiency, and their initial cost can be higher than traditional filters.
Impact on Application: Electrostatic filters are suitable for residential and light commercial applications, where ease of maintenance is a priority.
Considerations for International Buyers: Buyers should ensure that these filters comply with local regulations and consider the availability of cleaning facilities in their regions.
Summary Table of Air Filter Materials
Material | Typical Use Case for air filter | Key Advantage | Key Disadvantage/Limitation | Relative Cost (Low/Med/High) |
---|---|---|---|---|
Fiberglass | Commercial HVAC systems | Low-cost and lightweight | Shorter lifespan and lower efficiency | Low |
Polyester | Residential and commercial | Durable and customizable | Higher manufacturing complexity | Medium |
HEPA | Hospitals and laboratories | Superior air quality | Higher cost and lower airflow | High |
Electrostatic | Residential and light commercial | Washable and reusable | Requires regular cleaning | Medium |
This guide provides B2B buyers with essential insights into material selection for air filters, ensuring informed purchasing decisions that align with regional standards and operational needs.
In-depth Look: Manufacturing Processes and Quality Assurance for air fliter
What Are the Key Stages in Air Filter Manufacturing Processes?
The manufacturing of air filters is a detailed process that involves several critical stages, each contributing to the overall effectiveness and quality of the final product. Understanding these stages can help B2B buyers assess the capabilities of potential suppliers.
Material Preparation: What Raw Materials Are Used?
The first stage involves selecting high-quality raw materials tailored for specific filter applications. Common materials include:
- Fiberglass: Used for its lightweight and effective filtration capabilities.
- Polyester: Known for durability and moisture resistance.
- Activated Carbon: Utilized for odor control and chemical absorption.
Once selected, these materials undergo a pre-treatment process, including cutting and shaping into required dimensions, ensuring they are suitable for further processing.
How Are Air Filters Formed and Assembled?
The forming stage typically employs advanced techniques such as:
- Pleating: This method increases the surface area of the filter material, enhancing its filtration efficiency. Pleated filters can trap more particles compared to flat filters.
- Heat Bonding: For synthetic materials, heat bonding helps to fuse fibers together, ensuring structural integrity and performance.
Following the forming process, filters are assembled. This involves:
- Framing: Filters are placed within a sturdy frame made from metal or plastic to provide support.
- Sealing: Edges are sealed using adhesives or gaskets to prevent unfiltered air from bypassing the filter.
What Finishing Techniques Ensure Quality?
Finishing processes include additional treatments that enhance performance, such as:
- Coating: Some filters receive a coating that improves dust capture and airflow.
- Labeling: Proper labeling is essential for compliance and helps end-users understand the product specifications and installation instructions.
How Is Quality Assurance Implemented in Air Filter Production?
Quality assurance (QA) is integral to air filter manufacturing, ensuring products meet specific performance and safety standards. For international B2B buyers, understanding these QA protocols can facilitate better supplier evaluations.
What International Standards Should Buyers Look For?
Many air filter manufacturers adhere to recognized international standards, such as:
- ISO 9001: This standard focuses on quality management systems and is applicable across various industries, ensuring a consistent quality approach.
- CE Marking: Essential for products sold in Europe, indicating conformity with health, safety, and environmental protection standards.
What Are the Key Quality Control Checkpoints?
Quality control (QC) occurs at multiple checkpoints throughout the manufacturing process:
- Incoming Quality Control (IQC): Before production begins, raw materials are inspected to ensure they meet specified criteria.
- In-Process Quality Control (IPQC): During manufacturing, operators regularly check parameters such as airflow resistance and filtration efficiency.
-
Final Quality Control (FQC): The finished product undergoes rigorous testing, including:
-
MERV Testing: Assessing the Minimum Efficiency Reporting Value to determine filter efficiency.
- Airflow Tests: Ensuring the filter allows adequate airflow while maintaining filtration effectiveness.
How Can B2B Buyers Verify Supplier Quality Control?
For international B2B buyers, especially those in Africa, South America, the Middle East, and Europe, verifying a supplier’s quality control processes is crucial. Here are actionable steps:
What Documentation Should Be Requested?
- Quality Assurance Reports: Suppliers should provide documentation detailing their QA processes and results of any certifications.
- Testing Certificates: Request certificates from accredited laboratories demonstrating compliance with relevant standards.
How Can Audits and Inspections Be Conducted?
- Supplier Audits: Conduct on-site audits to evaluate the manufacturing processes, QC protocols, and overall facility standards.
- Third-Party Inspections: Engaging third-party inspection services can provide an unbiased evaluation of the supplier’s quality practices.
What Testing Methods Are Commonly Used in Air Filter Quality Assurance?
Understanding the testing methods employed by manufacturers can provide insights into their commitment to quality. Common testing methodologies include:
- Efficiency Testing: Measures the filter’s ability to capture particles of varying sizes, often using particle counters.
- Durability Testing: Simulates real-world conditions to assess how filters hold up under stress, including high airflow and humidity levels.
- Environmental Testing: Evaluates how filters perform in different environmental conditions, which is particularly relevant for buyers in diverse climates.
What Unique Quality Control Considerations Exist for International Buyers?
For B2B buyers from regions like Africa and South America, unique considerations may arise:
- Local Regulations: Ensure that suppliers are compliant with local regulations and standards, which may differ from international norms.
- Cultural and Logistical Factors: Consider the supplier’s ability to meet delivery timelines, especially in regions with logistical challenges.
Conclusion: How to Choose a Reliable Air Filter Supplier?
Choosing the right air filter supplier requires a comprehensive understanding of their manufacturing processes and quality assurance protocols. By focusing on key areas such as material selection, manufacturing techniques, quality control measures, and compliance with international standards, B2B buyers can make informed decisions that align with their operational needs and expectations. Always ensure that potential suppliers demonstrate a commitment to quality and transparency, as this will ultimately impact your business’s performance and reliability in air filtration solutions.
Practical Sourcing Guide: A Step-by-Step Checklist for ‘air fliter’
To assist international B2B buyers in sourcing air filters effectively, this guide provides a systematic checklist that outlines essential steps for a successful procurement process. By following this step-by-step approach, buyers can ensure they select the right products and suppliers for their specific needs.
Step 1: Define Your Technical Specifications
Understanding your specific requirements for air filters is the first critical step in the sourcing process. Determine the type of air filters needed based on the application—whether for residential, commercial, or industrial use. Key specifications to consider include:
– Filter Size: Ensure you know the dimensions of the filters required.
– MERV Rating: Identify the Minimum Efficiency Reporting Value (MERV) needed for your environment, which affects air quality and filtration efficiency.
Step 2: Research Potential Suppliers
Take the time to explore various suppliers, focusing on those that cater specifically to your region, such as Africa, South America, the Middle East, and Europe. Look for suppliers with a strong reputation and experience in the air filtration market. Important aspects to consider include:
– Product Range: Ensure the supplier offers a variety of filters that meet your specifications.
– Local Availability: Check if they can deliver to your location efficiently.
Step 3: Evaluate Supplier Certifications
Before making any commitments, it’s essential to verify that potential suppliers hold necessary certifications. Certifications can indicate compliance with industry standards and quality assurance. Look for:
– ISO Certifications: These demonstrate adherence to international quality management standards.
– MERV Ratings: Ensure the filters meet the required MERV ratings as certified by relevant authorities.
Step 4: Request Samples and Product Specifications
To assess the quality of the air filters, request samples from shortlisted suppliers. This allows you to evaluate the product firsthand before placing a bulk order. Key actions include:
– Inspect Samples: Check for build quality, material used, and filter efficiency.
– Review Specifications: Ensure the product specifications align with your defined needs.
Step 5: Compare Pricing and Terms
Once you have gathered all necessary information, it’s time to compare pricing from different suppliers. However, do not focus solely on price; consider the overall value offered. Important factors to assess include:
– Bulk Discounts: Inquire about pricing for large orders.
– Payment Terms: Understand the payment options and any potential financing available.
Step 6: Finalize the Purchase Agreement
Once you have selected a supplier, it’s crucial to finalize the purchase agreement. This document should outline all terms and conditions, including delivery timelines, warranty information, and return policies. Ensure to:
– Negotiate Terms: Don’t hesitate to negotiate for better conditions or additional benefits.
– Clarify Delivery Logistics: Confirm the delivery method and timeline to avoid any unexpected delays.
Step 7: Establish a Long-term Relationship
After successful procurement, consider establishing a long-term relationship with your chosen supplier. This can lead to better pricing, priority service, and customized solutions over time. Key steps include:
– Regular Communication: Maintain open lines of communication for future needs.
– Performance Reviews: Periodically review the supplier’s performance to ensure they continue to meet your expectations.
By following these steps, international B2B buyers can streamline their air filter sourcing process, ensuring they select high-quality products and reliable suppliers tailored to their specific requirements.
Comprehensive Cost and Pricing Analysis for air fliter Sourcing
What Are the Key Cost Components in Air Filter Manufacturing?
Understanding the cost structure of air filter manufacturing is crucial for international B2B buyers. The main cost components include:
-
Materials: The type of media used (e.g., synthetic fibers, activated carbon) significantly impacts the price. High-efficiency filters, such as HEPA or MERV-rated filters, typically use more expensive materials.
-
Labor: Labor costs can vary significantly based on geographic location. In regions with higher labor costs, such as Europe, manufacturers may need to adjust their pricing strategies.
-
Manufacturing Overhead: This includes utilities, rent, and equipment maintenance. Manufacturers often pass on these costs to buyers, so understanding the production environment can provide insight into pricing.
-
Tooling: Custom filters require specialized equipment, increasing initial costs. Buyers should consider these costs when requesting bespoke solutions.
-
Quality Control (QC): Rigorous quality testing ensures compliance with international standards, impacting overall costs. Filters meeting higher certification standards (like ISO or ASHRAE) will usually be priced higher.
-
Logistics: Transportation costs fluctuate based on distance and mode of transport. Import duties and tariffs can further complicate pricing for international buyers.
-
Margin: Finally, suppliers typically add a margin to cover their expenses and profit. This margin can vary based on market competition and demand.
How Do Price Influencers Affect Air Filter Costs?
Several factors influence the pricing of air filters, making it vital for buyers to understand these nuances:
-
Volume and Minimum Order Quantity (MOQ): Larger orders generally result in lower per-unit costs due to economies of scale. Buyers should negotiate MOQs to optimize pricing.
-
Specifications and Customization: Customized filters tailored to specific applications will usually incur higher costs. Buyers should clearly communicate their needs to get accurate quotes.
-
Material Quality and Certifications: Filters with higher MERV ratings or specialized materials (e.g., antimicrobial properties) will command higher prices. Certifications also play a role; filters with recognized endorsements can attract a premium.
-
Supplier Factors: The reputation and reliability of the supplier can influence pricing. Established suppliers may charge more due to their proven quality and service.
-
Incoterms: Understanding shipping terms is crucial, as they dictate who bears the cost of shipping and insurance. Terms like FOB (Free on Board) or CIF (Cost, Insurance, and Freight) can significantly affect the total landed cost of the filters.
What Tips Can International Buyers Use to Optimize Air Filter Procurement?
For B2B buyers from Africa, South America, the Middle East, and Europe, optimizing procurement can lead to significant savings:
-
Negotiation Strategies: Engage suppliers in discussions about volume discounts or long-term contracts. Establishing a strong relationship can lead to better pricing and terms.
-
Focus on Total Cost of Ownership (TCO): Evaluate not just the purchase price, but also installation, maintenance, and replacement costs. A cheaper filter may lead to higher long-term expenses due to frequent replacements or inefficiencies.
-
Understand Pricing Nuances: Be aware that pricing may vary significantly between regions. Factors like local demand, import tariffs, and currency fluctuations can affect costs.
-
Leverage Technology: Use online platforms to compare prices and specifications across multiple suppliers. This can aid in making informed decisions and finding the best deals.
-
Plan for Logistics: Consider the total logistics cost, including shipping time and reliability. Delays can impact operations, so it’s essential to factor these into your overall cost assessment.
Disclaimer on Indicative Prices
Prices for air filters can fluctuate based on market conditions, supplier negotiations, and specific order requirements. It is advisable for buyers to conduct thorough market research and request detailed quotes to ensure they are getting competitive rates.
Alternatives Analysis: Comparing air fliter With Other Solutions
Understanding Alternatives to Air Filters
When it comes to improving indoor air quality, air filters are a popular choice among businesses. However, there are several alternatives that may provide similar or even enhanced benefits depending on specific needs and contexts. This analysis aims to compare air filters with two viable alternatives: air purifiers and UV air sanitizers.
Comparison Table
Comparison Aspect | Air Filter | Air Purifier | UV Air Sanitizer |
---|---|---|---|
Performance | Effective in trapping dust, pollen, and allergens based on MERV ratings | Removes airborne particles, odors, and some gases; effectiveness varies by model | Kills bacteria and viruses using UV-C light; effective against pathogens |
Cost | Generally low-cost; varies with MERV rating and size | Higher initial investment; ongoing filter replacement costs | Moderate to high initial costs; no consumables but may require maintenance |
Ease of Implementation | Simple installation in existing HVAC systems or standalone units | Requires space and power; often portable and easy to set up | Installation may require professional help depending on the system |
Maintenance | Regular filter changes necessary (every 1-3 months) | Filter changes required; some models have washable filters | Requires periodic bulb replacement; minimal maintenance otherwise |
Best Use Case | Ideal for general dust and allergen control in commercial buildings | Best for environments needing odor control and allergen reduction | Effective in healthcare settings or areas with high pathogen exposure |
Detailed Breakdown of Alternatives
What Are the Benefits and Drawbacks of Air Purifiers?
Air purifiers are designed to remove a wide range of contaminants from indoor air. They utilize various technologies, including HEPA filters and activated carbon, to trap particles and neutralize odors. The primary advantage of air purifiers is their ability to address specific air quality issues, such as pet dander or smoke. However, they often come with higher initial costs and require regular maintenance, including filter replacements. Additionally, their effectiveness can vary significantly between models, necessitating careful selection based on specific air quality needs.
How Do UV Air Sanitizers Work, and What Are Their Pros and Cons?
UV air sanitizers leverage ultraviolet light to kill airborne pathogens, including bacteria and viruses. This makes them particularly advantageous in settings like hospitals and clinics where infection control is critical. The main benefit of UV sanitizers is their ability to continuously disinfect air without the need for consumables, reducing long-term operational costs. However, they typically have a higher upfront cost and may require professional installation, which can be a barrier for some businesses. Furthermore, UV systems are not effective against particulate matter like dust and pollen, limiting their use to specific air quality challenges.
Conclusion: How Should B2B Buyers Choose the Right Solution?
In selecting the right air quality solution, B2B buyers should consider their specific needs, budget constraints, and the environment in which the product will be used. Air filters are generally the most cost-effective option for general dust and allergen control, while air purifiers offer versatility for addressing specific contaminants. For high-risk environments, UV air sanitizers provide an added layer of protection against pathogens. Understanding these alternatives and their unique advantages will empower buyers to make informed decisions tailored to their operational requirements.
Essential Technical Properties and Trade Terminology for air fliter
What Are the Essential Technical Properties of Air Filters?
When sourcing air filters for industrial or commercial applications, understanding their technical properties is crucial. Here are some of the key specifications to consider:
1. Material Grade
Air filters can be made from various materials, including fiberglass, polyester, and pleated paper. The material grade impacts the filter’s efficiency, durability, and cost. For instance, polyester filters typically offer better filtration and longer lifespan compared to fiberglass. Selecting the appropriate material ensures that the filter meets the specific air quality standards required in different regions, such as those mandated in Europe or the Middle East.
2. MERV Rating
The Minimum Efficiency Reporting Value (MERV) is a critical metric that measures the efficiency of air filters. It ranges from 1 to 20, with higher ratings indicating better filtration capabilities. Filters with a MERV rating of 8-13 are suitable for commercial applications, while those rated 14-20 are ideal for environments requiring superior air quality, like hospitals. Understanding MERV ratings helps buyers choose filters that align with their air quality requirements.
3. Filter Size
Air filters come in various sizes, typically measured in inches. Common dimensions include 20 x 20 x 1 inches and 16 x 25 x 1 inches. Sourcing the correct size is vital to ensure proper fit and function within HVAC systems. Custom sizes may also be available, which is particularly beneficial for unique installations.
4. Airflow Resistance
This property refers to the amount of resistance a filter poses to airflow, often quantified in inches of water gauge (in. wg). High airflow resistance can lead to reduced efficiency in HVAC systems and increased energy costs. Thus, understanding the balance between filtration efficiency and airflow resistance is essential for optimizing system performance.
5. Lifespan and Replacement Cycle
The lifespan of an air filter can vary based on its type, usage, and environmental conditions. Most filters are designed to last between one to six months. Buyers should assess the expected lifespan and replacement cycle to manage maintenance schedules effectively and ensure continuous air quality.
What Are Common Trade Terms in the Air Filter Industry?
Familiarity with industry jargon is important for successful procurement and negotiation. Here are some common terms:
1. OEM (Original Equipment Manufacturer)
OEM refers to companies that produce products that are marketed under another company’s brand. Understanding OEM relationships can help buyers ensure compatibility and quality assurance in the filters they purchase.
2. MOQ (Minimum Order Quantity)
MOQ is the smallest quantity of a product that a supplier is willing to sell. This term is significant for international buyers as it influences inventory management and cost-effectiveness. Knowing the MOQ can help in planning orders that align with budget constraints.
3. RFQ (Request for Quotation)
An RFQ is a document used to invite suppliers to bid on specific products or services. For air filter procurement, issuing an RFQ can help buyers compare pricing, specifications, and lead times from multiple suppliers, ensuring they get the best deal.
4. Incoterms
Incoterms, short for International Commercial Terms, are a set of predefined commercial terms related to international trade. They define the responsibilities of buyers and sellers regarding shipping, insurance, and tariffs. Familiarity with Incoterms is essential for international buyers, as they influence the total cost and risk associated with air filter procurement.
5. Lead Time
Lead time refers to the amount of time it takes from placing an order until the product is delivered. Understanding lead times is crucial for inventory planning and ensuring that air filters are available when needed, especially in regions with variable supply chains.
By grasping these technical properties and trade terminologies, international B2B buyers can make informed decisions when sourcing air filters, ultimately ensuring optimal performance and compliance with local air quality standards.
Navigating Market Dynamics and Sourcing Trends in the air fliter Sector
What Are the Key Market Dynamics and Sourcing Trends in the Air Filter Sector?
The global air filter market is experiencing significant growth, driven by increasing awareness of air quality and rising health concerns. International B2B buyers, particularly from Africa, South America, the Middle East, and Europe, are increasingly prioritizing efficient air filtration solutions in various sectors, including HVAC, automotive, and industrial manufacturing. Emerging technologies, such as smart filters equipped with IoT capabilities, are reshaping sourcing strategies, enabling buyers to track filter performance in real-time and optimize replacement schedules.
Additionally, the demand for customizable air filters is on the rise. Buyers are seeking solutions that cater to specific environmental conditions, such as high dust levels in Africa or industrial pollutants in South America. Understanding regional air quality challenges is essential for suppliers to tailor their offerings. The market is also seeing a shift toward online procurement platforms, allowing international buyers to access a wider range of products and suppliers quickly.
How Is Sustainability Influencing Air Filter Sourcing Decisions?
Sustainability has become a critical factor in the sourcing of air filters. As businesses globally strive for greener operations, the demand for eco-friendly air filters made from recyclable materials is rising. Suppliers who can demonstrate their commitment to sustainable practices—such as using low-VOC adhesives and filters that reduce energy consumption—are increasingly favored by B2B buyers.
Moreover, ethical sourcing is vital, particularly in regions where environmental regulations are stringent. Buyers are now more discerning about their suppliers’ practices, seeking certifications such as ISO 14001 for environmental management systems and ENERGY STAR ratings for energy-efficient products. By prioritizing suppliers with these credentials, companies can enhance their sustainability profiles while ensuring compliance with local regulations.
What Is the Evolution of Air Filter Technology?
The air filter industry has evolved significantly over the past few decades. Initially focused on basic filtration, advancements have led to the development of high-efficiency particulate air (HEPA) filters and electrostatic filters, which offer superior filtration capabilities. The introduction of smart technology has further transformed the landscape, with filters now capable of monitoring air quality and providing data analytics for improved indoor air management.
As international B2B buyers navigate this evolving market, understanding the historical context of air filter technology can inform their purchasing decisions. The transition from traditional to innovative filtration solutions highlights the importance of selecting suppliers who stay ahead of technological trends and can meet the diverse needs of various industries across different regions.
By focusing on these key market dynamics, sustainability considerations, and the evolution of technology, international B2B buyers can make informed decisions that align with their operational goals and environmental responsibilities.
Frequently Asked Questions (FAQs) for B2B Buyers of air fliter
-
How do I solve the problem of finding the right air filter for my business needs?
Finding the right air filter requires understanding your specific air quality requirements, including the types of contaminants you need to filter out. Start by determining the MERV (Minimum Efficiency Reporting Value) rating suitable for your application—higher ratings indicate better filtration. Additionally, consider the size and compatibility with your HVAC system. Consulting with suppliers who offer custom solutions can also streamline the process, ensuring you acquire filters tailored to your operational needs. -
What is the best air filter for industrial applications?
For industrial applications, look for air filters with a high MERV rating, ideally between 13 to 16, as they effectively capture airborne particles, allergens, and dust. Filters designed for heavy-duty use, such as HEPA filters, are also beneficial for environments where air quality is critical. Suppliers offering customizable options can help you choose filters that meet specific requirements like size, filtration capabilities, and durability, ensuring optimal performance in demanding settings. -
How can I verify the credibility of an air filter supplier?
To verify a supplier’s credibility, research their reputation in the industry by checking reviews and testimonials from previous clients. Request certifications that demonstrate compliance with international quality standards such as ISO or ASHRAE. Additionally, assess their experience in international trade, especially with regions relevant to your business, like Africa or South America. Engaging in direct communication can also provide insights into their customer service and responsiveness. -
What are the minimum order quantities (MOQ) for air filters?
Minimum order quantities for air filters can vary significantly based on the supplier and the specific products. Typically, suppliers may set MOQs ranging from 50 to 500 units. It’s important to discuss this upfront to ensure the MOQ aligns with your business needs. Consider negotiating terms if you require fewer units, especially if you are testing a new product or entering a new market. -
What payment terms should I expect when sourcing air filters internationally?
Payment terms when sourcing air filters can differ based on the supplier’s policies and the nature of your business relationship. Common terms include advance payment, letter of credit, or net 30/60 days after delivery. It’s crucial to clarify these terms in the contract and ensure they accommodate your financial processes. Additionally, consider the impact of currency exchange rates and transaction fees when dealing with international suppliers. -
How do I ensure quality assurance for air filters from international suppliers?
Ensuring quality assurance involves several steps, including demanding product certifications and conducting factory audits if possible. Request samples before placing bulk orders to evaluate the product’s performance. Establishing a clear quality control checklist that the supplier must adhere to can also mitigate risks. Regular communication and feedback during the procurement process will help maintain standards and address any issues promptly. -
What logistics considerations should I keep in mind when importing air filters?
When importing air filters, consider shipping costs, delivery times, and customs regulations in your country. Collaborate with logistics providers who have experience in handling HVAC products to ensure smooth transit. Understanding the incoterms (like FOB or CIF) will help clarify responsibilities regarding shipping and insurance. Additionally, factor in potential delays due to customs clearance, especially in regions with complex regulations. -
Can I customize air filters for specific applications?
Yes, many suppliers offer customization options for air filters. This can include adjustments in size, filtration material, and MERV ratings to meet specific air quality needs. Customization is particularly beneficial for businesses in unique industries, such as pharmaceuticals or food processing, where air purity is paramount. Discuss your requirements with potential suppliers to explore available options and ensure that the filters are designed to meet your operational standards.
Important Disclaimer & Terms of Use
⚠️ Important Disclaimer
The information provided in this guide, including content regarding manufacturers, technical specifications, and market analysis, is for informational and educational purposes only. It does not constitute professional procurement advice, financial advice, or legal advice.
While we have made every effort to ensure the accuracy and timeliness of the information, we are not responsible for any errors, omissions, or outdated information. Market conditions, company details, and technical standards are subject to change.
B2B buyers must conduct their own independent and thorough due diligence before making any purchasing decisions. This includes contacting suppliers directly, verifying certifications, requesting samples, and seeking professional consultation. The risk of relying on any information in this guide is borne solely by the reader.
Strategic Sourcing Conclusion and Outlook for air fliter
What Are the Key Takeaways for Strategic Sourcing of Air Filters?
In conclusion, strategic sourcing of air filters is essential for international B2B buyers seeking quality, efficiency, and sustainability. By understanding the diverse range of products available, including custom sizes and various MERV ratings, buyers can select filters that meet specific operational needs while ensuring compliance with local standards. Leveraging bulk purchasing and establishing long-term relationships with reputable suppliers can lead to significant cost savings and improved supply chain reliability.
How Can B2B Buyers Prepare for Future Trends in Air Filtration?
As the demand for cleaner air grows, driven by health concerns and environmental regulations, the air filter market will continue to evolve. Buyers from regions such as Africa, South America, the Middle East, and Europe must stay informed about technological advancements and eco-friendly options to remain competitive. Investing in smart filtration solutions and maintaining regular communication with suppliers will be crucial in adapting to these changes.
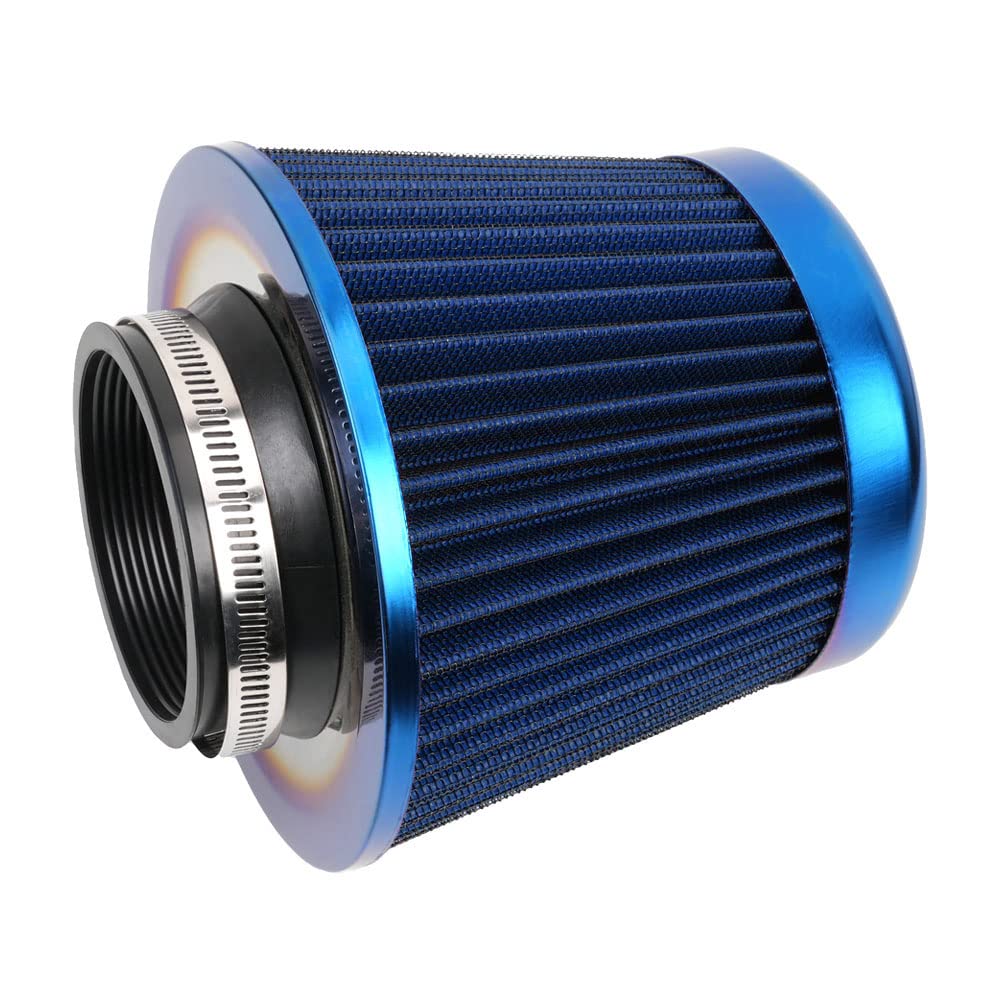
A stock image related to air fliter.
What Steps Should Buyers Take Next?
For B2B buyers, the next step is to evaluate current air filtration strategies and identify areas for improvement. Engage with suppliers to explore innovative solutions that enhance air quality and operational efficiency. By prioritizing strategic sourcing, businesses not only protect their workforce but also position themselves favorably in a rapidly changing market landscape.