Discover the Best Electrical Prongs: A Complete Sourcing Guide (2025)
Introduction: Navigating the Global Market for electrical prongs
In today’s interconnected world, sourcing the right electrical prongs can pose significant challenges for international B2B buyers. With numerous plug types, voltage requirements, and safety standards varying across regions—especially in diverse markets like Africa, South America, the Middle East, and Europe—understanding the nuances of electrical connectivity is crucial. This guide serves as a comprehensive resource for navigating the global market for electrical prongs, covering essential topics such as types of plugs and sockets, their applications in various industries, effective supplier vetting processes, and cost considerations.
By providing detailed insights into the different electrical prong configurations, this guide empowers businesses to make informed purchasing decisions that align with their operational needs. Whether you are based in Nigeria, the UK, or any other region, understanding local regulations and compatibility issues can significantly reduce risks and enhance the efficiency of your electrical installations.
Additionally, we will explore the importance of supplier relationships and how to assess the quality and reliability of manufacturers in a global marketplace. With actionable strategies and expert tips, this guide is designed to equip international B2B buyers with the knowledge they need to navigate the complexities of electrical prongs confidently, ensuring compliance and maximizing operational success.
Understanding electrical prongs Types and Variations
Type Name | Key Distinguishing Features | Primary B2B Applications | Brief Pros & Cons for Buyers |
---|---|---|---|
Type C | Two round pins, ungrounded, rated at 2.5A, 10A, and 16A | Common in appliances and consumer electronics across Europe, Africa, and South America | Pros: Widely used, compatible with many devices. Cons: Not grounded, which may pose safety risks. |
Type G | Three rectangular pins, grounded, rated at 13A | Predominantly used in the UK and Middle East for heavy-duty appliances | Pros: High safety standard due to grounding. Cons: Bulkier design may limit compatibility with some devices. |
Type E | Two round pins with a hole for grounding, rated at 16A | Used in France, Belgium, and Poland for various electrical devices | Pros: Compatible with Type F plugs, versatile. Cons: Limited to specific regions, requiring adapters for international use. |
Type N | Three pins, grounded, rated at 10A, 16A, and 20A | Primarily used in Brazil and South Africa for industrial and commercial settings | Pros: High amperage capacity for industrial applications. Cons: Less common globally, may require special sourcing. |
Type I | Two or three pins, rated at 10A and 15A, grounded options available | Common in Australia, New Zealand, and parts of China for general use | Pros: Versatile with grounded options. Cons: Compatibility issues with non-grounded devices. |
What are the characteristics of Type C electrical prongs?
Type C plugs feature two round pins and are primarily ungrounded, making them a common choice for smaller appliances and consumer electronics. They are rated for 2.5A, 10A, and 16A, allowing for versatility in usage. For B2B buyers, the widespread acceptance of Type C plugs in Europe, Africa, and South America makes them a reliable option for sourcing electrical devices. However, their lack of grounding can pose safety risks, so businesses should assess their application environments carefully.
Why is Type G suitable for heavy-duty applications?
Type G plugs are distinguished by their three rectangular pins and grounding feature, rated at 13A. This design is predominantly used in the UK and parts of the Middle East, making it ideal for heavy-duty appliances such as ovens and large machinery. The grounding pin enhances safety, reducing the risk of electrical faults. B2B buyers should consider Type G when sourcing equipment that requires a reliable and safe connection, although the bulkier design may limit compatibility with some devices.
How does Type E differ from other plug types?
Type E plugs are characterized by their two round pins and an additional hole for grounding, rated at 16A. They are commonly found in France, Belgium, and Poland, making them suitable for various electrical devices. The compatibility with Type F plugs enhances their versatility, allowing for broader application. For B2B buyers, the primary consideration should be the need for regional compliance and sourcing challenges, as Type E plugs may require adapters for international use.
What are the advantages of Type N for industrial applications?
Type N plugs, with their three pins and grounding, are rated at 10A, 16A, and 20A, making them suitable for industrial and commercial settings, particularly in Brazil and South Africa. The higher amperage capacity allows for robust applications, catering to equipment that demands significant power. B2B buyers should consider the specific requirements of their operations, as sourcing Type N plugs may be more challenging due to their limited global presence.
Why choose Type I plugs for versatility?
Type I plugs can feature either two or three pins and are rated for 10A and 15A, with grounded options available. They are commonly used in Australia, New Zealand, and parts of China, making them versatile for various applications. For B2B buyers, the availability of grounded options enhances safety, although compatibility issues may arise with non-grounded devices. Businesses should evaluate their equipment needs and regional standards when considering Type I plugs.
Key Industrial Applications of electrical prongs
Industry/Sector | Specific Application of Electrical Prongs | Value/Benefit for the Business | Key Sourcing Considerations for this Application |
---|---|---|---|
Manufacturing | Machinery and Equipment Connection | Ensures reliable power supply, reducing downtime | Compliance with international standards (e.g., NEMA, IEC) and voltage ratings suitable for local infrastructure. |
Construction | Temporary Power Supply | Facilitates quick setup and teardown on job sites | Durability and weather resistance are crucial, especially in outdoor environments. |
Telecommunications | Network Equipment Powering | Maintains continuous operation of critical systems | Look for prongs that support high amperage and have surge protection features. |
Energy | Renewable Energy Systems | Enhances efficiency in energy transfer | Compatibility with local grid systems and adherence to safety regulations are essential. |
Hospitality | Appliances and Equipment | Improves guest experience through reliable power supply | Consider the variety of plug types used in different regions and the need for adapters. |
How Are Electrical Prongs Used in Manufacturing?
In the manufacturing sector, electrical prongs are critical for connecting machinery and equipment to power sources. They ensure a reliable power supply, which is vital for maintaining continuous operations and minimizing downtime. Buyers need to focus on sourcing prongs that comply with international standards, such as NEMA or IEC, and that are rated for the specific voltage and amperage used in their local infrastructure. This is particularly important for buyers in regions like Nigeria and Brazil, where power supply conditions may vary.
What Role Do Electrical Prongs Play in Construction?
Electrical prongs are extensively used in the construction industry for setting up temporary power supplies at job sites. They facilitate quick connections for tools and equipment, enabling efficient project execution. For international buyers, sourcing durable and weather-resistant prongs is essential, as many construction sites are exposed to harsh environmental conditions. Additionally, understanding local electrical standards can help prevent compatibility issues that could delay projects.
How Are Electrical Prongs Essential in Telecommunications?
In telecommunications, electrical prongs are employed to power network equipment, ensuring uninterrupted service delivery. This is crucial for maintaining the operation of servers and communication devices, especially in data centers. When sourcing prongs for this application, buyers should prioritize options that support high amperage and include surge protection features to safeguard sensitive equipment from electrical fluctuations. This is especially relevant for buyers in Europe, where stringent electrical regulations often apply.
How Do Electrical Prongs Benefit Renewable Energy Systems?
Electrical prongs find significant application in renewable energy systems, such as solar panels and wind turbines. They facilitate efficient energy transfer from these systems to the local grid. Buyers must ensure that the prongs they source are compatible with local grid systems and comply with safety regulations. This is particularly important in regions like Africa and South America, where the adoption of renewable technologies is rapidly increasing and local standards may differ significantly.
Why Are Electrical Prongs Important in the Hospitality Sector?
In the hospitality industry, electrical prongs are used for connecting various appliances and equipment, enhancing the guest experience through reliable power supply. Hotels and restaurants often require a variety of plug types due to international clientele, making it essential to source adaptable solutions. Buyers should consider the different plug types prevalent in their regions, such as Type G in the UK or Type C in many European and African countries, to ensure compatibility and avoid inconvenience for guests.
3 Common User Pain Points for ‘electrical prongs’ & Their Solutions
Scenario 1: Navigating Different Plug Types in International Markets
The Problem: B2B buyers often face challenges when trying to source electrical prongs that are compatible with various socket types across different regions. For instance, a company in Nigeria seeking to import equipment from Europe may find that the electrical prongs used in their machinery do not match the local socket types. This mismatch can lead to costly delays, equipment malfunctions, and increased operational risks.
The Solution: To effectively navigate this issue, it is crucial for buyers to conduct thorough research on the specific electrical standards of the countries they are importing from and to. This includes understanding the various plug types (like Type C in Europe and Type G in the UK) and their compatibility with existing infrastructure. Buyers should consider investing in universal adapters or sourcing products designed with interchangeable prongs. Additionally, collaborating with suppliers who have expertise in international standards can facilitate smoother transactions and ensure compliance with local regulations. Using a checklist to verify plug compatibility before making any purchase can also prevent future headaches.
Scenario 2: Overcoming Voltage and Amperage Confusion
The Problem: Voltage and amperage discrepancies often plague international B2B buyers. For example, a South American company purchasing machinery designed for 220V operations may inadvertently acquire equipment rated for 110V due to a lack of clarity in product specifications. This can lead to equipment failure or even safety hazards, resulting in significant financial losses and reputational damage.
The Solution: To mitigate this risk, B2B buyers should establish a robust verification process for voltage and amperage requirements before finalizing purchases. This includes cross-referencing equipment specifications with local electrical standards and consulting with manufacturers to confirm compatibility. Buyers should also consider sourcing equipment that features dual voltage capabilities, allowing for operation across various electrical systems. Engaging with experienced electrical engineers or consultants can further ensure that installations comply with local standards, thereby enhancing safety and operational efficiency.
Scenario 3: Ensuring Quality and Compliance in Electrical Prongs
The Problem: The proliferation of substandard electrical prongs in the market poses a significant challenge for B2B buyers. In regions like the Middle East, where safety standards are stringent, using inferior quality prongs can lead to electrical failures, safety hazards, and potential legal ramifications. Buyers may struggle to differentiate between reliable and unreliable suppliers, leading to poor purchasing decisions.
The Solution: To ensure the quality and compliance of electrical prongs, buyers should prioritize working with reputable suppliers who can provide certifications and test reports for their products. It’s essential to request samples for testing before placing large orders, ensuring that the prongs meet local standards and regulations. Additionally, buyers should stay informed about the latest industry standards and certifications relevant to their region, such as IEC or UL listings. Establishing long-term partnerships with suppliers who demonstrate a commitment to quality and safety can further enhance reliability in sourcing. Regular audits of supplier practices and product quality checks can also help mitigate risks associated with substandard products.
Strategic Material Selection Guide for electrical prongs
When selecting materials for electrical prongs, it is essential to consider the properties and performance characteristics that will meet the demands of various applications. Below is an analysis of four common materials used in the manufacturing of electrical prongs, focusing on their key properties, advantages and disadvantages, and considerations for international B2B buyers.
What are the Key Properties of Brass for Electrical Prongs?
Brass is a popular choice for electrical prongs due to its excellent conductivity and resistance to corrosion. Typically composed of copper and zinc, brass can withstand temperatures up to 200°C (392°F) and offers good mechanical strength.
Pros and Cons of Brass:
– Pros: Brass is relatively inexpensive, easy to machine, and provides a good balance of strength and conductivity. Its corrosion resistance makes it suitable for various environments.
– Cons: While brass is durable, it can tarnish over time, which may affect its aesthetic appeal. It may also not perform well in highly acidic or alkaline environments.
Impact on Application:
Brass prongs are widely compatible with electrical systems and are often used in residential and commercial applications. However, buyers must ensure that brass meets the specific electrical and mechanical requirements of their applications.
Considerations for International Buyers:
Brass components should comply with international standards such as ASTM B16 for brass fittings. Buyers from regions like Africa and South America should ensure that the brass used is of high quality to avoid issues related to corrosion.
How Does Stainless Steel Perform as a Material for Electrical Prongs?
Stainless steel is known for its superior corrosion resistance and strength, making it ideal for harsh environments. With a temperature rating of up to 300°C (572°F), stainless steel prongs can withstand high thermal stress.
Pros and Cons of Stainless Steel:
– Pros: Its durability and resistance to rust make stainless steel an excellent choice for outdoor applications or in humid environments. It also maintains its appearance over time.
– Cons: Stainless steel is generally more expensive than brass and can be more challenging to machine, which may increase manufacturing costs.
Impact on Application:
Stainless steel is often used in industrial applications where durability is critical. Its compatibility with various media makes it suitable for diverse environments, including marine and chemical applications.
Considerations for International Buyers:
B2B buyers should look for compliance with standards such as ASTM A240 for stainless steel. In regions like Europe and the Middle East, buyers should also consider the specific grades of stainless steel that best suit their application needs.
What are the Advantages of Using Plastic for Electrical Prongs?
Plastic prongs, often made from thermoplastics, provide a lightweight and cost-effective alternative to metal. They can handle temperatures up to 100°C (212°F) and are generally resistant to chemicals and moisture.
Pros and Cons of Plastic:
– Pros: Plastic is lightweight, inexpensive, and can be molded into complex shapes, allowing for versatile designs. It is also non-corrosive and electrically insulating.
– Cons: Plastic has lower mechanical strength compared to metals and may not withstand high temperatures or heavy loads.
Impact on Application:
Plastic prongs are commonly used in low-voltage applications and consumer electronics. They are not suitable for high-current applications due to their lower thermal and mechanical properties.
Considerations for International Buyers:
Buyers should ensure that the plastic materials used comply with relevant standards such as UL 94 for flammability. In regions like Africa and South America, the availability of high-quality plastics can vary, so sourcing from reputable suppliers is crucial.
Why is Copper a Preferred Material for Electrical Prongs?
Copper is renowned for its exceptional electrical conductivity, making it the preferred choice for electrical prongs. It can handle temperatures up to 300°C (572°F) and has excellent thermal properties.
Pros and Cons of Copper:
– Pros: Copper’s high conductivity ensures efficient energy transfer, making it ideal for high-performance applications. It is also relatively easy to work with and can be recycled.
– Cons: Copper is prone to corrosion and oxidation, which can lead to performance degradation over time. It is also more expensive than brass and plastic.
Impact on Application:
Copper prongs are commonly found in high-power applications, such as industrial machinery and electrical installations. Their superior conductivity makes them suitable for applications requiring minimal energy loss.
Considerations for International Buyers:
B2B buyers must ensure that copper components meet standards such as ASTM B170 for copper wire. In Europe, compliance with RoHS regulations regarding hazardous substances is also essential.
Summary Table of Material Selection for Electrical Prongs
Material | Typical Use Case for Electrical Prongs | Key Advantage | Key Disadvantage/Limitation | Relative Cost (Low/Med/High) |
---|---|---|---|---|
Brass | Residential and commercial applications | Good conductivity and corrosion resistance | Tarnishes over time | Low |
Stainless Steel | Industrial applications | Superior corrosion resistance | Higher cost and manufacturing complexity | High |
Plastic | Low-voltage consumer electronics | Lightweight and cost-effective | Lower mechanical strength | Low |
Copper | High-power industrial applications | Exceptional electrical conductivity | Prone to corrosion | Medium |
This guide aims to equip international B2B buyers with the necessary insights to make informed decisions regarding the selection of materials for electrical prongs, ensuring compliance with relevant standards and suitability for specific applications.
In-depth Look: Manufacturing Processes and Quality Assurance for electrical prongs
The manufacturing of electrical prongs involves a detailed process designed to ensure high quality and compliance with international standards. For B2B buyers, especially from regions like Africa, South America, the Middle East, and Europe, understanding these processes can be crucial when selecting suppliers and ensuring product reliability.
What Are the Main Stages in the Manufacturing Process of Electrical Prongs?
Material Preparation
The first stage in manufacturing electrical prongs is material preparation. High-quality conductive materials, typically copper or aluminum, are sourced based on required specifications. These materials undergo a thorough inspection to ensure they meet industry standards regarding conductivity, durability, and corrosion resistance. B2B buyers should prioritize suppliers who provide certification of material quality to avoid issues later in the supply chain.
Forming Techniques
Once materials are prepared, the next step is forming. Techniques such as stamping, die-casting, and extrusion are commonly used. Stamping involves cutting shapes from metal sheets, while die-casting allows for intricate designs to be formed in molds. Extrusion is used for creating long shapes with uniform cross-sections. The choice of technique can impact the prong’s performance and compatibility with various socket types, making it essential for buyers to understand the manufacturing techniques employed by their suppliers.
Assembly Processes
After forming, the components are assembled. This stage may involve soldering, welding, or mechanical fastening, depending on the design of the prong. Automated assembly lines are often utilized to enhance efficiency and precision. It’s vital for B2B buyers to inquire about the assembly methods used, as they can influence the final product’s robustness and reliability.
Finishing Touches
The final stage of manufacturing electrical prongs is finishing. This can include processes like plating, coating, and polishing to enhance appearance and protect against corrosion. For instance, nickel or tin plating is commonly applied to improve conductivity and resistance to tarnishing. Buyers should check whether suppliers use environmentally friendly finishing processes, as this can impact compliance with international regulations.
How Is Quality Assurance Implemented in Electrical Prong Manufacturing?
What International Standards Should B2B Buyers Be Aware Of?
Quality assurance in the manufacturing of electrical prongs is governed by several international standards. ISO 9001 is the most recognized standard for quality management systems, ensuring that manufacturers have effective processes in place. Additionally, certifications such as CE mark in Europe and UL certification in the United States signify that products meet safety and performance standards. B2B buyers should look for suppliers who hold these certifications, as they reflect a commitment to quality and safety.
What Are the Key Quality Control Checkpoints?
Quality control (QC) is typically divided into three main checkpoints:
-
Incoming Quality Control (IQC): This involves the inspection of raw materials upon arrival at the manufacturing facility. Ensuring that materials meet specified standards is crucial, as defects at this stage can lead to significant quality issues down the line.
-
In-Process Quality Control (IPQC): Throughout the manufacturing process, various inspections are conducted to ensure that each stage is executed correctly. This includes monitoring dimensions, assembly integrity, and adherence to safety standards.
-
Final Quality Control (FQC): Before the products are shipped, a thorough final inspection is performed. This includes testing for electrical conductivity, mechanical strength, and compliance with applicable standards. Random sampling methods may be used to validate product quality.
What Common Testing Methods Are Used for Electrical Prongs?
Electrical prongs undergo several testing methods to ensure they meet performance and safety criteria. Common tests include:
- Electrical Testing: Measures conductivity and insulation resistance to ensure safe operation.
- Mechanical Testing: Evaluates the durability and strength of prongs under various conditions, including stress tests.
- Environmental Testing: Assesses how products perform under different environmental conditions, such as extreme temperatures or humidity.
B2B buyers should ask suppliers for detailed reports on these tests to verify product compliance.
How Can B2B Buyers Verify Supplier Quality Control Processes?
What Steps Should Be Taken to Ensure Supplier Compliance?
To ensure that suppliers adhere to quality control processes, buyers should consider the following steps:
-
Audits: Conduct regular audits of suppliers’ manufacturing facilities. This allows buyers to evaluate the processes and technologies used, and assess compliance with international standards.
-
Quality Reports: Request detailed quality assurance reports from suppliers. These should include records of inspections, test results, and any corrective actions taken for defects.
-
Third-Party Inspections: Engage third-party inspection agencies to verify quality claims. This adds an extra layer of assurance and can help build trust in the supplier relationship.
What Are the Quality Control Nuances for International B2B Buyers?
For international buyers, particularly from Africa, South America, the Middle East, and Europe, it’s crucial to understand regional compliance requirements. Different regions may have specific regulations regarding electrical safety and environmental impact. Familiarizing oneself with these regulations can help avoid compliance issues that could lead to product recalls or market entry barriers.
Additionally, language barriers and cultural differences can impact communication with suppliers. Establishing clear expectations regarding quality standards and processes from the outset can mitigate misunderstandings.
By understanding the manufacturing processes and quality assurance measures for electrical prongs, B2B buyers can make informed decisions, ensuring they partner with suppliers who prioritize quality and compliance. This knowledge not only enhances supply chain reliability but also supports the overall success of their business operations.
Practical Sourcing Guide: A Step-by-Step Checklist for ‘electrical prongs’
In today’s global marketplace, sourcing electrical prongs effectively can significantly impact your business operations. Whether you’re based in Africa, South America, the Middle East, or Europe, understanding the nuances of procurement can lead to better decision-making and increased efficiency. This practical sourcing guide outlines a step-by-step checklist to streamline your purchasing process for electrical prongs.
Step 1: Define Your Technical Specifications
Before initiating any procurement process, it’s essential to have a clear understanding of your technical requirements. This includes determining the type of electrical prongs needed, such as NEMA configurations or international plug types (e.g., Type C, Type G). Defining specifications will help you avoid compatibility issues down the line and ensure that the prongs meet your operational needs.
Step 2: Research Compliance Standards
Understanding the compliance requirements in your region is crucial. Different countries have specific standards regarding electrical products, including safety regulations and certification marks. Familiarize yourself with these standards to ensure that the electrical prongs you procure are compliant, reducing the risk of legal issues or product recalls.
Step 3: Evaluate Potential Suppliers
Before committing to a supplier, conduct thorough evaluations. Request company profiles, product samples, and references from other businesses in your industry. Look for suppliers that have a proven track record of reliability and quality. It’s also beneficial to assess their production capacity to ensure they can meet your demand.
- Check Reviews and Ratings: Online reviews and ratings can provide insight into a supplier’s reliability and customer service.
- Request Certifications: Ensure that suppliers have the necessary certifications, such as ISO 9001 or CE marks, which indicate adherence to quality standards.
Step 4: Verify Supplier Certifications
Supplier certifications are key indicators of quality and compliance. Verify that the suppliers you are considering hold relevant certifications for electrical components, which may vary by region. This step is important to ensure that the electrical prongs you purchase are safe and reliable for use in your applications.
Step 5: Assess Pricing and Payment Terms
Pricing can vary significantly among suppliers, so it’s essential to obtain multiple quotes. However, don’t just focus on the lowest price; consider the total cost of ownership, including shipping, duties, and potential tariffs. Additionally, review payment terms and conditions to ensure they align with your cash flow needs.
- Negotiate Terms: Explore options for discounts on bulk orders or favorable payment terms to enhance your purchasing strategy.
- Consider Currency Risks: If sourcing internationally, be aware of currency fluctuations that could affect overall costs.
Step 6: Request Samples for Testing
Before placing a large order, request samples of the electrical prongs. Testing these samples will help you evaluate their quality and compatibility with your existing systems. This step can prevent costly mistakes and ensure that you are making an informed decision.
Step 7: Establish a Communication Plan
Effective communication is vital throughout the sourcing process. Establish clear lines of communication with your supplier to address any concerns or questions that may arise. Regular updates can help ensure that timelines are met and that both parties are aligned on expectations.
By following this checklist, international B2B buyers can streamline their sourcing process for electrical prongs, ensuring that they make informed decisions that align with their business needs.
Comprehensive Cost and Pricing Analysis for electrical prongs Sourcing
Understanding the cost structure and pricing dynamics for sourcing electrical prongs is critical for international B2B buyers. This analysis delves into the key cost components, price influencers, and provides actionable buyer tips to navigate the complexities of purchasing electrical prongs, particularly for businesses in Africa, South America, the Middle East, and Europe.
What Are the Key Cost Components in Electrical Prongs Sourcing?
When sourcing electrical prongs, several cost components come into play:
-
Materials: The choice of materials significantly impacts the overall cost. High-quality materials such as copper and durable plastics tend to increase initial expenses but can enhance longevity and performance.
-
Labor: Labor costs vary based on the region of manufacturing. Countries with lower labor costs may offer cheaper pricing, but this can sometimes come at the expense of quality.
-
Manufacturing Overhead: This includes indirect costs associated with production, such as utilities, rent, and administrative expenses. Efficient manufacturing processes can help minimize these overheads.
-
Tooling: Initial tooling costs can be substantial, particularly for custom designs. This cost is often amortized over larger production runs, making it essential to consider volume when assessing tooling expenses.
-
Quality Control (QC): Implementing stringent QC measures ensures that products meet safety and performance standards, which can add to costs but is vital for maintaining brand reputation.
-
Logistics: Shipping and handling costs are particularly important for international buyers. Factors such as distance, shipping methods, and freight rates can significantly influence total costs.
-
Margin: Suppliers will add a margin to cover their costs and profit. Understanding the typical margin range in the industry can help buyers gauge fair pricing.
How Do Price Influencers Affect Electrical Prongs Costs?
Several factors influence the pricing of electrical prongs:
-
Volume/MOQ (Minimum Order Quantity): Bulk purchases often lead to reduced per-unit costs. Buyers should negotiate MOQs to achieve more favorable pricing.
-
Specifications and Customization: Customized prongs tailored to specific requirements usually cost more than standard options. Buyers should evaluate the necessity of customization against their budget.
-
Materials and Quality Certifications: Higher quality materials and certifications (like UL or CE) may increase costs but provide assurances of safety and reliability, which can be crucial in certain markets.
-
Supplier Factors: The reputation and reliability of suppliers can affect pricing. Established suppliers might charge a premium due to their proven track record, but they often offer better support and assurance of quality.
-
Incoterms: Understanding Incoterms is essential for international transactions as they define the responsibilities of buyers and sellers regarding shipping, insurance, and duties, impacting the total landed cost.
What Are the Best Practices for International B2B Buyers?
To maximize value when sourcing electrical prongs, buyers should consider the following tips:
-
Negotiate Effectively: Building a good relationship with suppliers can lead to better pricing and terms. Always approach negotiations with a clear understanding of your budget and requirements.
-
Focus on Cost-Efficiency: Consider the Total Cost of Ownership (TCO), which includes not just the purchase price but also logistics, installation, and maintenance costs over the product’s lifespan.
-
Understand Pricing Nuances: Different regions may have varying pricing structures due to local regulations, tariffs, and market demand. Buyers from Africa, South America, the Middle East, and Europe should conduct thorough market research to understand these nuances.
-
Request Detailed Quotes: Always ask for itemized quotes that break down costs. This transparency allows for better comparison and understanding of where expenses lie.
-
Be Aware of Indicative Prices: Prices for electrical prongs can fluctuate based on market conditions, raw material costs, and supply chain factors. Therefore, always treat quoted prices as indicative and verify them before finalizing orders.
By understanding these cost structures and pricing dynamics, international B2B buyers can make informed decisions that enhance their purchasing strategies for electrical prongs, ensuring quality products while optimizing their expenditure.
Alternatives Analysis: Comparing electrical prongs With Other Solutions
Exploring Viable Alternatives to Electrical Prongs
When considering electrical connections for commercial and industrial applications, electrical prongs are often the standard choice. However, there are several alternatives that can provide similar functionalities with varying benefits. This analysis will compare electrical prongs against two viable alternatives: wireless charging technology and smart plug systems. Understanding these options can help B2B buyers make informed decisions that align with their specific operational needs.
Comparison Aspect | Electrical Prongs | Wireless Charging Technology | Smart Plug Systems |
---|---|---|---|
Performance | Reliable for direct power delivery; suitable for high amperage | Limited by range; efficiency may vary based on alignment | Offers smart features like energy monitoring; performance can depend on network reliability |
Cost | Generally low cost per unit; installation costs vary | Higher initial investment; installation can be complex | Moderate cost with potential savings from energy efficiency |
Ease of Implementation | Straightforward installation; requires basic electrical knowledge | More complex; may require specialized equipment | User-friendly; often plug-and-play with existing outlets |
Maintenance | Low maintenance; durable with proper use | Minimal, but requires compatible devices; potential for obsolescence | Regular updates may be needed; smart features may require troubleshooting |
Best Use Case | Industrial settings requiring high power loads | Consumer electronics and mobile devices | Residential and commercial spaces looking for automation |
What Are the Pros and Cons of Wireless Charging Technology?
Wireless charging technology offers a modern approach to power delivery, particularly in consumer electronics. Pros include the convenience of not needing physical connectors, reducing wear and tear on devices. This technology is especially useful for mobile devices and electric vehicles. However, cons include a limited range and reduced efficiency if devices are not perfectly aligned on the charging pad. Additionally, the initial setup can be costly and may not be suitable for high-power applications, making it less ideal for industrial settings.
What Are the Advantages and Disadvantages of Smart Plug Systems?
Smart plug systems have gained traction in both residential and commercial environments. The advantages of smart plugs include their ability to monitor energy usage, schedule devices, and integrate with home automation systems. This makes them an excellent choice for businesses looking to enhance energy efficiency. However, disadvantages include dependence on stable internet connectivity and potential security vulnerabilities associated with IoT devices. Furthermore, while they offer automation benefits, their performance can be less reliable than traditional electrical prongs in high-demand scenarios.
Conclusion: How Can B2B Buyers Choose the Right Solution?
Choosing the right electrical connection solution involves evaluating specific operational needs, budget constraints, and the intended application. For buyers focused on high power requirements and reliability, traditional electrical prongs remain a strong choice. Conversely, those looking to enhance operational efficiency and embrace automation may find wireless charging or smart plug systems to be more suitable, provided they can accommodate the associated costs and complexities. Ultimately, understanding the unique advantages and limitations of each option will enable B2B buyers to select a solution that aligns with their strategic goals and enhances their operational capabilities.
Essential Technical Properties and Trade Terminology for electrical prongs
What Are the Essential Technical Properties of Electrical Prongs?
When sourcing electrical prongs for international markets, understanding the technical properties is crucial for ensuring compatibility, safety, and performance. Here are some key specifications to consider:
1. Material Grade
Electrical prongs are typically made from various materials, including brass, copper, and plastics. The material grade affects conductivity, durability, and resistance to corrosion. For B2B buyers, selecting the right material is essential to ensure that the prongs can withstand environmental conditions and usage demands, especially in regions with high humidity or extreme temperatures.
2. Current Rating (Amperage)
The current rating, measured in amps (A), indicates the maximum amount of electrical current a prong can handle safely. Common ratings include 15A, 20A, and 30A. It is critical for buyers to match the current rating with their specific electrical systems to prevent overheating or failure, which can lead to safety hazards.
3. Voltage Rating
Voltage rating specifies the maximum voltage that the prong can handle, typically expressed in volts (V). For instance, common ratings are 125V, 250V, or higher for industrial applications. Understanding voltage ratings helps buyers ensure that their devices operate efficiently and safely within their designated voltage ranges, particularly when dealing with international standards that vary by region.
4. NEMA Configuration
The National Electrical Manufacturers Association (NEMA) provides specific configurations for electrical plugs and connectors. Each configuration has distinct pin arrangements and ratings, such as NEMA 5-15 for standard household plugs. B2B buyers should be familiar with NEMA configurations to ensure compatibility with their electrical systems, especially when importing products from different countries.
5. Grounding Type
Grounding types determine whether a prong has a grounding pin, which is essential for safety. Grounded plugs typically have three pins, while ungrounded plugs have two. Buyers must consider the grounding requirements of their electrical installations, particularly in regions prone to electrical surges or faults.
What Are Common Trade Terms Related to Electrical Prongs?
Understanding industry jargon is essential for effective communication and negotiation in the B2B marketplace. Here are some commonly used terms in the electrical prong trade:
1. OEM (Original Equipment Manufacturer)
An OEM is a company that produces parts or equipment that may be marketed by another manufacturer. For B2B buyers, partnering with OEMs can provide access to specialized products tailored to specific needs, enhancing product offerings and competitiveness in local markets.
2. MOQ (Minimum Order Quantity)
MOQ refers to the smallest quantity of a product that a supplier is willing to sell. It is crucial for buyers to understand MOQs to avoid overcommitting resources, especially when entering new markets or testing new products. Negotiating favorable MOQs can lead to more flexible purchasing options.
3. RFQ (Request for Quotation)
An RFQ is a document sent to suppliers requesting pricing and terms for specific products. For international buyers, submitting a detailed RFQ can facilitate better responses from suppliers, ensuring that all necessary specifications are included, thus reducing the risk of misunderstandings.
4. Incoterms (International Commercial Terms)
Incoterms are a set of predefined commercial terms used in international trade to clarify the responsibilities of buyers and sellers. Understanding these terms helps B2B buyers navigate shipping, insurance, and delivery obligations, reducing risks associated with international transactions.
5. Certification Standards
Certification standards, such as UL (Underwriters Laboratories) or CE (Conformité Européenne), indicate compliance with safety regulations. Buyers should prioritize sourcing products that meet relevant certification standards to ensure quality and safety, particularly in regulated markets.
By grasping these technical properties and trade terms, international B2B buyers can make informed decisions when purchasing electrical prongs, ensuring compatibility and reliability across various applications.
Navigating Market Dynamics and Sourcing Trends in the electrical prongs Sector
What Are the Current Market Dynamics in the Electrical Prongs Sector?
The electrical prongs market is witnessing significant growth, driven by the increasing demand for electrical connectivity across various sectors, including construction, manufacturing, and consumer electronics. Global initiatives towards renewable energy and smart home technology are reshaping sourcing strategies, leading to a surge in the adoption of energy-efficient and multifunctional electrical plugs. International B2B buyers, particularly from Africa, South America, the Middle East, and Europe, should pay attention to the shift towards smart plugs that offer connectivity features, such as Wi-Fi and Bluetooth capabilities, which cater to the growing smart home market.
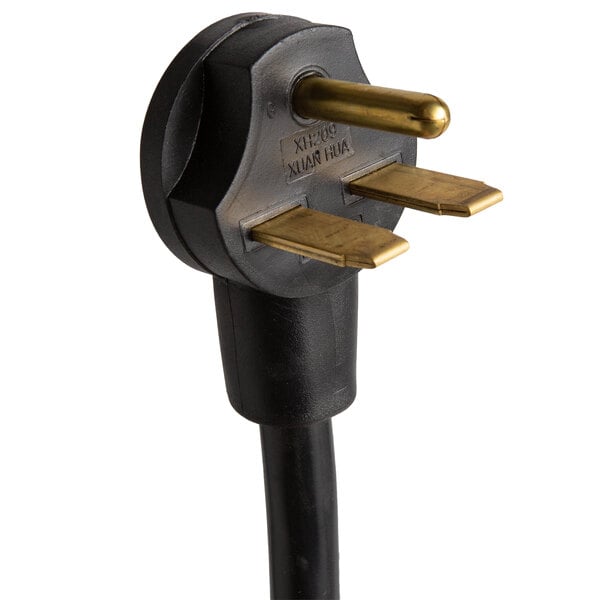
A stock image related to electrical prongs.
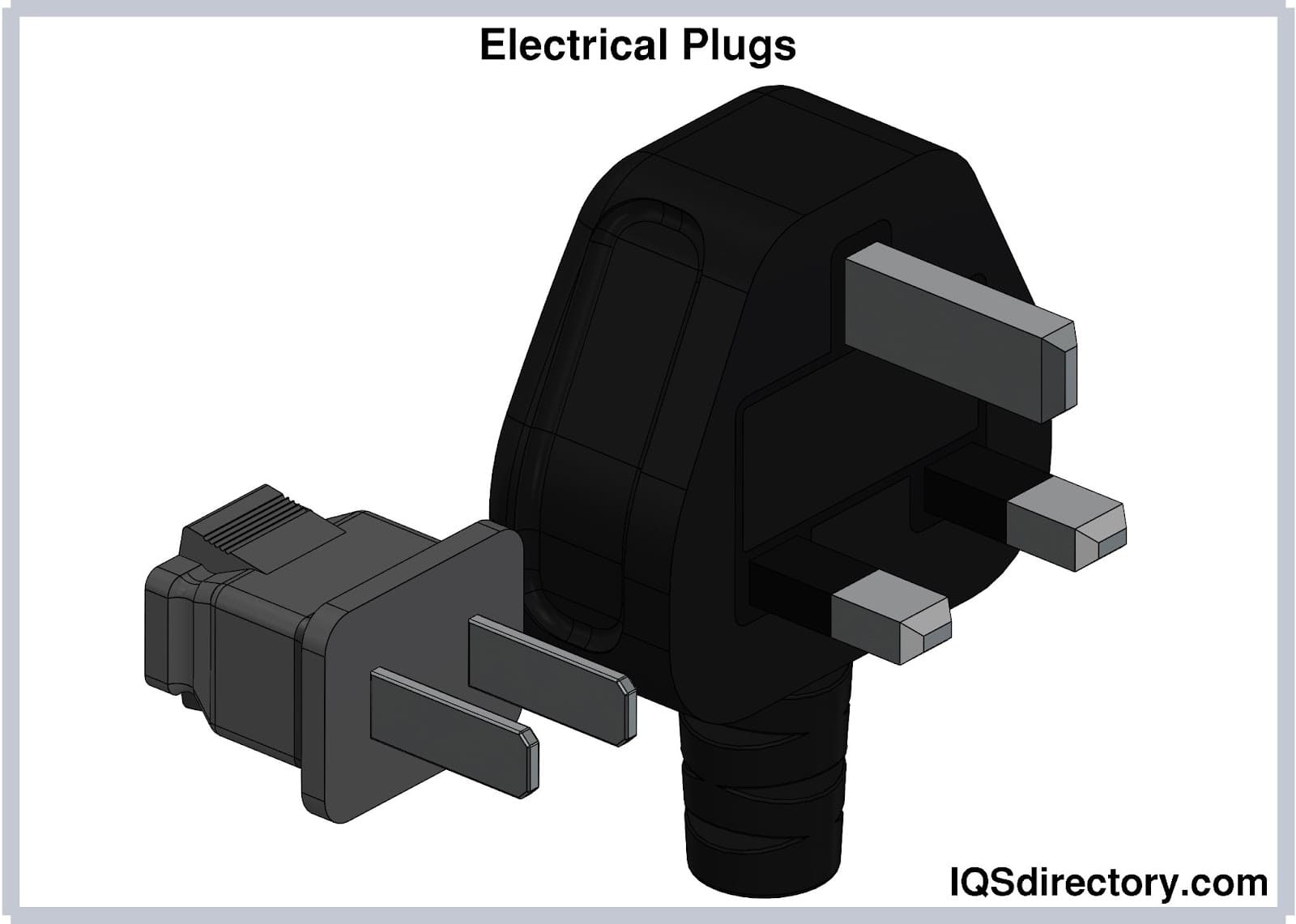
A stock image related to electrical prongs.
Furthermore, the rise of e-commerce platforms has revolutionized sourcing practices, enabling buyers to access a wider range of products and suppliers globally. This shift is particularly beneficial for businesses in regions like Nigeria and Brazil, where local suppliers may not always meet quality standards. Strategic partnerships with manufacturers that offer customizable solutions can also enhance product offerings, allowing companies to differentiate themselves in competitive markets.
The electrical prongs sector is also influenced by regulatory changes, particularly concerning safety and environmental standards. Compliance with international standards such as IEC 60884-1 ensures that products are not only safe but also compatible with various global plug types, thus facilitating easier market entry for international buyers.
How Can B2B Buyers Ensure Sustainability and Ethical Sourcing in Electrical Prongs?
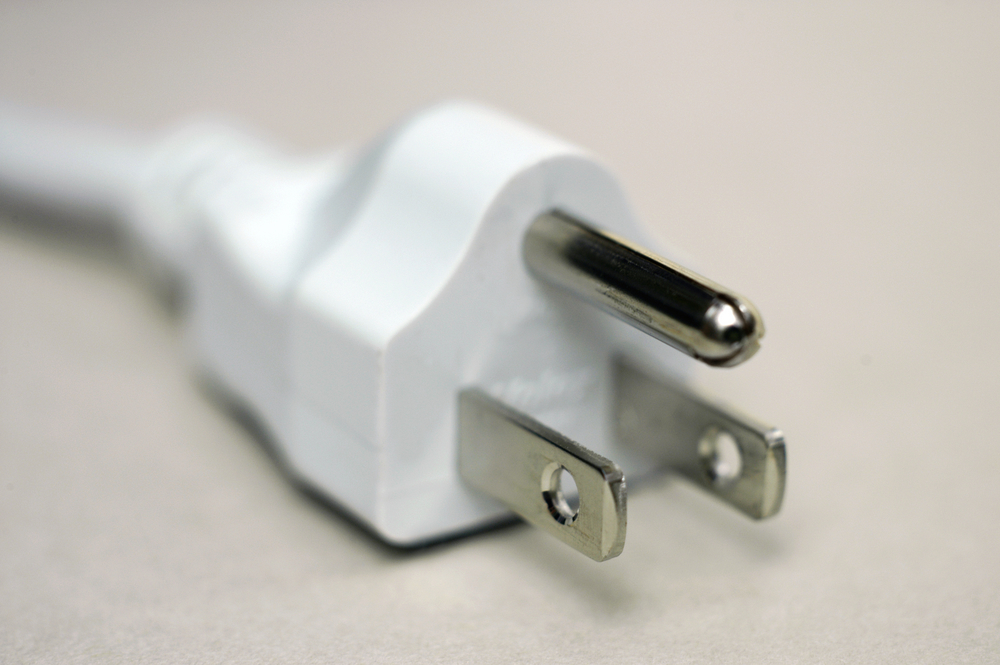
A stock image related to electrical prongs.
Sustainability and ethical sourcing are becoming paramount for international B2B buyers in the electrical prongs sector. The environmental impact of manufacturing processes and the materials used in electrical prongs can be significant, making it essential for companies to consider their supply chains carefully. Buyers should seek suppliers who prioritize eco-friendly materials and sustainable production methods, such as using recyclable or biodegradable components.
Certifications such as the Forest Stewardship Council (FSC) and ISO 14001 can serve as reliable indicators of a supplier’s commitment to sustainability. Moreover, sourcing from manufacturers that utilize energy-efficient practices in their production can help companies reduce their carbon footprint.
Ethical sourcing also involves ensuring fair labor practices and transparency within the supply chain. Engaging with suppliers who have clear policies regarding labor rights and environmental responsibility fosters trust and enhances brand reputation. Buyers should conduct thorough due diligence to verify that their suppliers adhere to ethical standards, particularly when sourcing from regions with varying regulatory frameworks.
What Is the Evolution of Electrical Prongs and Its Relevance for B2B Buyers?
The evolution of electrical prongs can be traced back to the late 19th century when the first standardized plug designs emerged to ensure compatibility and safety in electrical systems. The introduction of different plug types worldwide, such as Type C in Europe and Type G in the UK, was essential in addressing the diverse electrical needs of various regions. This historical context is particularly relevant for B2B buyers as it underscores the importance of understanding local regulations and standards when sourcing electrical prongs.
Today, the focus has shifted towards innovation in design and functionality, with manufacturers developing plugs that not only meet safety standards but also incorporate advanced features like surge protection and smart technology. Understanding this evolution allows buyers to make informed decisions when selecting products that align with current market trends and consumer expectations. By staying attuned to these developments, businesses can enhance their offerings and maintain a competitive edge in the electrical prongs market.
Frequently Asked Questions (FAQs) for B2B Buyers of electrical prongs
-
How do I choose the right electrical prong for my region?
Choosing the right electrical prong requires understanding the specific plug types and voltage requirements in your region. For instance, Africa predominantly uses Type C and Type M plugs, while Type G is common in the UK. It’s crucial to verify the voltage and amperage ratings as well, ensuring compatibility with local electrical standards. Always consult a reliable electrical standards guide or local regulations before making a purchase. -
What is the best type of electrical prong for industrial applications?
For industrial applications, consider using heavy-duty electrical prongs such as NEMA configurations (e.g., NEMA L5-30 or L6-30) that can handle higher amperages and voltages. These types are designed for robust environments and provide reliable connections for machinery and equipment. Assess your specific power needs, including voltage and amperage, to determine the best fit. -
How can I ensure the quality of electrical prongs when sourcing internationally?
To ensure quality when sourcing electrical prongs internationally, vet suppliers thoroughly. Check for certifications such as ISO, CE, or UL, which indicate compliance with international safety standards. Request samples before bulk orders to evaluate the product quality firsthand. Additionally, consider using third-party inspection services to assess manufacturing processes and product standards. -
What are the common minimum order quantities (MOQs) for electrical prongs?
Minimum order quantities (MOQs) can vary significantly based on the supplier and the type of electrical prong. Generally, MOQs range from 100 to 1,000 units for standard products. However, some suppliers may offer lower MOQs for customized or specialized prongs. It’s advisable to discuss your specific needs with suppliers to negotiate favorable terms, especially if you’re testing a new market. -
What payment terms should I negotiate with suppliers of electrical prongs?
When negotiating payment terms, aim for conditions that provide both security and flexibility. Common terms include a 30% upfront deposit with the remaining balance due before shipment. For larger orders, consider negotiating for longer payment periods or letter of credit options to mitigate risk. Always ensure that payment methods are secure and protect your financial interests. -
How do I handle logistics and shipping for international orders of electrical prongs?
Logistics for international orders require careful planning to ensure timely delivery and compliance with customs regulations. Work with a reliable freight forwarder experienced in handling electrical components. Be aware of shipping costs, potential tariffs, and necessary documentation. It’s also wise to choose insurance options for high-value shipments to protect against loss or damage during transit. -
Can electrical prongs be customized for specific applications?
Yes, many suppliers offer customization options for electrical prongs to meet specific application requirements. Customization can include variations in plug types, materials, or amperage ratings. When seeking customization, clearly communicate your needs and specifications to the supplier. Be prepared for potential minimum order quantities and lead times that may vary based on the complexity of the customizations. -
What are the safety standards for electrical prongs in international markets?
Safety standards for electrical prongs differ by region and application. For example, the European Union mandates compliance with the Low Voltage Directive (LVD) and other specific standards, while the U.S. adheres to National Electrical Code (NEC) regulations. Always ensure that products are certified by recognized bodies relevant to your target market. Conducting due diligence on standards will help mitigate risks associated with electrical safety in your operations.
Important Disclaimer & Terms of Use
⚠️ Important Disclaimer
The information provided in this guide, including content regarding manufacturers, technical specifications, and market analysis, is for informational and educational purposes only. It does not constitute professional procurement advice, financial advice, or legal advice.
While we have made every effort to ensure the accuracy and timeliness of the information, we are not responsible for any errors, omissions, or outdated information. Market conditions, company details, and technical standards are subject to change.
B2B buyers must conduct their own independent and thorough due diligence before making any purchasing decisions. This includes contacting suppliers directly, verifying certifications, requesting samples, and seeking professional consultation. The risk of relying on any information in this guide is borne solely by the reader.
Strategic Sourcing Conclusion and Outlook for electrical prongs
What Are the Key Takeaways for B2B Buyers in Electrical Prongs?
In today’s global marketplace, strategic sourcing of electrical prongs is vital for international B2B buyers, particularly those operating in regions like Africa, South America, the Middle East, and Europe. Understanding the diverse plug and socket types is crucial, as it directly impacts compatibility and safety in electrical installations. Buyers should prioritize sourcing from reputable manufacturers that comply with international standards to ensure product reliability and durability.
How Can Strategic Sourcing Enhance Your Business Operations?
Investing time in strategic sourcing not only reduces costs but also enhances supply chain efficiency. By leveraging local suppliers in target markets, businesses can minimize lead times and improve responsiveness to market demands. This approach fosters stronger relationships with suppliers, which can lead to better pricing, exclusive deals, and innovative product offerings.
What Does the Future Hold for Electrical Prongs?
As the world increasingly shifts towards renewable energy and smart technology, the demand for advanced electrical prongs will rise. Buyers should stay informed about emerging trends and innovations to adapt their sourcing strategies accordingly. By doing so, businesses can position themselves ahead of competitors and capitalize on new market opportunities.
In conclusion, international B2B buyers are encouraged to prioritize strategic sourcing of electrical prongs as a means to enhance operational efficiency and drive growth. Embrace the evolving landscape of electrical components and invest in partnerships that will secure your place in the future of electrical solutions.