Discover the Best Type A Plug: Your Essential Guide (2025)
Introduction: Navigating the Global Market for type a plug
In the ever-evolving landscape of global commerce, sourcing the right electrical components, such as the Type A plug, presents a unique set of challenges for international B2B buyers. The Type A plug, widely recognized for its two flat parallel prongs and prevalent use in North America and parts of Central America, serves as a critical interface for countless electrical devices. However, with varying standards across regions—including Africa, South America, the Middle East, and Europe—it is essential to navigate the complexities of compatibility, regulations, and safety standards.
This comprehensive guide aims to equip B2B buyers with the knowledge necessary to make informed purchasing decisions regarding Type A plugs. From an in-depth examination of plug types and their applications to effective strategies for vetting suppliers and understanding cost implications, this resource addresses the key concerns that businesses face when sourcing electrical components. We delve into the nuances of market demand, helping buyers identify reliable suppliers who meet their specific needs while ensuring compliance with local regulations.
Whether you are looking to expand your product offerings or ensure the safety and efficiency of your operations, this guide empowers B2B buyers to make strategic decisions that enhance their competitive edge in the market. By understanding the global landscape of Type A plugs, you can confidently navigate the intricacies of international trade and secure the best solutions for your business.
Understanding type a plug Types and Variations
Type Name | Key Distinguishing Features | Primary B2B Applications | Brief Pros & Cons for Buyers |
---|---|---|---|
Type A (NEMA 1-15) | Ungrounded, two flat parallel prongs, polarized design | Consumer electronics, light appliances | Pros: Common in North America; Cons: Lack of grounding increases risk of electrical shock. |
Type B (NEMA 5-15) | Grounded, two flat prongs plus a round grounding pin | Heavy-duty appliances, industrial equipment | Pros: Provides grounding for safety; Cons: Less common in some regions, may require adapters. |
Type A (Japanese Version) | Similar to Type A but with equal-width prongs | Small electronics, portable devices | Pros: Compatibility with US sockets; Cons: Limited to 100V supply, not suitable for higher voltage devices. |
Type A with Locking Mechanism | Features holes in prongs for locking | Vending machines, industrial equipment | Pros: Prevents accidental disconnection; Cons: May require specialized sockets. |
Type A (Modified for International Use) | Adapted design for global compatibility | Travel adapters, consumer electronics | Pros: Versatile for global use; Cons: May compromise on safety standards. |
What Are the Key Features of Type A (NEMA 1-15) Plugs?
Type A plugs, commonly referred to as NEMA 1-15, are ungrounded connectors featuring two flat parallel prongs. Their polarized design, where one prong is wider than the other, ensures proper orientation when connecting to outlets. These plugs are widely used in North America and are suitable for consumer electronics and light appliances. However, the absence of grounding increases the risk of electrical shock, making them less ideal for high-power devices or environments where safety is critical.
How Do Type B (NEMA 5-15) Plugs Enhance Safety?
Type B plugs are characterized by their three-prong design, which includes a grounding pin. This feature is essential for heavy-duty applications and industrial equipment, providing an additional layer of safety against electrical faults. While they are commonly used in North America, their compatibility varies in other regions, which may necessitate the use of adapters. Buyers should consider the grounding feature as a significant advantage, particularly in environments where electrical safety is paramount.
What Distinguishes the Japanese Version of Type A Plugs?
The Japanese variant of Type A plugs resembles its North American counterpart but features two equally sized prongs. This design allows for compatibility with Type A sockets in the U.S., making it convenient for small electronics and portable devices. However, it operates at a lower voltage of 100V, which may not be suitable for devices requiring higher voltage. B2B buyers should ensure that their equipment matches the voltage specifications when purchasing these plugs.
In What Scenarios Are Type A Plugs with Locking Mechanisms Used?
Type A plugs equipped with locking mechanisms are designed for applications such as vending machines and industrial equipment, where accidental disconnection can lead to operational disruptions. These plugs feature holes in the prongs that allow for secure locking into sockets. While they offer enhanced reliability, buyers must ensure they have compatible sockets, as these specialized designs may not be universally available.
How Do Modified Type A Plugs Cater to International Buyers?
Modified Type A plugs are designed for international compatibility, often used in travel adapters and consumer electronics. These plugs may compromise on safety standards to accommodate various voltage systems and socket types worldwide. B2B buyers should be cautious when purchasing these plugs, as they may not meet local safety regulations, potentially leading to operational hazards in their specific markets.
Key Industrial Applications of type a plug
Industry/Sector | Specific Application of type a plug | Value/Benefit for the Business | Key Sourcing Considerations for this Application |
---|---|---|---|
Consumer Electronics | Powering small appliances and gadgets | Reliable power supply for daily operations | Voltage compatibility and safety certifications |
Hospitality | Charging stations in hotels | Enhanced guest experience with convenience | Durability and compliance with local regulations |
Retail | Point of Sale (POS) systems | Streamlined transactions and customer service | Plug design to fit existing infrastructure |
Construction and Engineering | Temporary power supply for tools and equipment | Increased efficiency on job sites | Load capacity and weather resistance |
Education | Classroom technology integration | Facilitates learning with modern devices | Compatibility with diverse electrical systems |
How is the Type A Plug Used in Consumer Electronics?
In the consumer electronics industry, the type A plug is commonly used to power small appliances such as laptops, chargers, and other electronic devices. This plug’s design, featuring two flat parallel pins, allows for a secure connection to the power source, ensuring that devices operate reliably. For international B2B buyers, it is critical to ensure that the voltage ratings match their equipment specifications, particularly in regions like Africa and South America where voltage standards may vary. Additionally, safety certifications must be verified to mitigate risks of electrical hazards.
What is the Role of Type A Plugs in the Hospitality Sector?
In the hospitality sector, type A plugs are integral to charging stations found in hotels and resorts. These stations provide guests with convenient access to power for their devices, enhancing their overall experience. For businesses, investing in high-quality type A plugs can lead to improved guest satisfaction and loyalty. B2B buyers from Europe and the Middle East should consider sourcing plugs that comply with local electrical standards to avoid potential compliance issues and ensure safe usage.
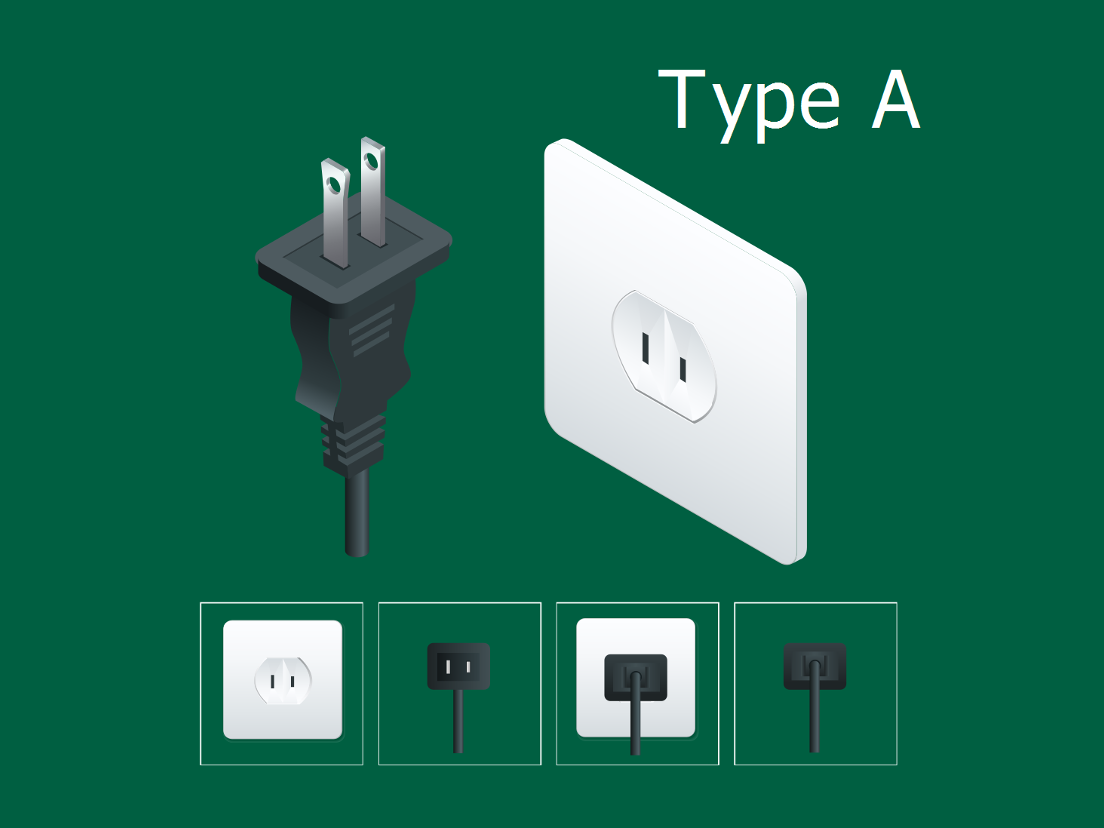
A stock image related to type a plug.
How Do Retailers Benefit from Type A Plugs in Point of Sale Systems?
Retail environments utilize type A plugs to connect Point of Sale (POS) systems, which are vital for processing transactions efficiently. The reliability of these plugs ensures that retail operations run smoothly, thus enhancing customer service. For international buyers, it is important to select type A plugs that are compatible with existing infrastructure and offer durability for frequent use. Additionally, understanding the local power supply conditions can help in sourcing the most suitable products.
Why is the Type A Plug Important for Construction and Engineering?
In construction and engineering, type A plugs are often used for temporary power supply to tools and equipment. This application is crucial for maintaining productivity on job sites, where reliable power is essential for various operations. B2B buyers must consider the load capacity of type A plugs and their weather resistance, especially in regions with extreme weather conditions. Ensuring that the plugs are robust enough to withstand the rigors of construction will prevent downtime and enhance operational efficiency.
How is the Type A Plug Used in Educational Institutions?
Educational institutions leverage type A plugs for integrating modern classroom technology, such as projectors and interactive boards. This allows for a dynamic learning environment that engages students effectively. For B2B buyers in the education sector, compatibility with diverse electrical systems is a key consideration, as schools often have varying infrastructure setups. Additionally, sourcing plugs that meet safety standards is essential to provide a secure learning environment for students and faculty alike.
3 Common User Pain Points for ‘type a plug’ & Their Solutions
Scenario 1: Incompatibility with Local Electrical Standards
The Problem:
International B2B buyers often face compatibility issues when sourcing Type A plugs, especially when importing electrical equipment to regions like Africa or South America. For instance, a company in South Africa might import machinery designed for North American markets, only to discover that the Type A plug does not fit local sockets. This not only leads to delays in installation but also increases costs due to the need for adapters or replacements, causing frustration and impacting project timelines.
The Solution:
To mitigate these compatibility issues, it is crucial for B2B buyers to conduct thorough research on local electrical standards before procurement. Buyers should specify the electrical requirements, including plug types, voltage, and frequency, in their sourcing documentation. Additionally, partnering with suppliers who offer localized solutions—such as equipment with interchangeable plugs or adapters tailored for the target market—can streamline the process. It’s beneficial to consult with electrical engineers familiar with local standards to ensure compliance and avoid costly mistakes.
Scenario 2: Safety Concerns with Ungrounded Plugs
The Problem:
Many Type A plugs are ungrounded, raising safety concerns for B2B buyers, particularly in industrial settings where electrical equipment is heavily used. For example, if a company in the UAE imports devices with Type A plugs for use in a manufacturing facility, there is a significant risk of electric shock if an appliance malfunctions. This not only endangers employees but can also result in liability issues and increased insurance costs.
The Solution:
To address safety concerns, B2B buyers should prioritize sourcing equipment that incorporates Type B plugs or devices with grounding features. When purchasing equipment, buyers should explicitly request grounded alternatives and ensure that their suppliers comply with international safety standards. Implementing regular safety audits and training for employees on the risks associated with ungrounded plugs can further enhance workplace safety. Investing in surge protectors and circuit breakers can also provide an additional layer of protection against electrical faults.
Scenario 3: Limited Availability of Replacement Parts
The Problem:
Another challenge faced by B2B buyers is the limited availability of replacement parts for Type A plugs in regions outside North America. For instance, a company in Spain may find it difficult to source replacement plugs for imported equipment, leading to prolonged downtimes and operational inefficiencies. This scarcity can disrupt business continuity and create a reliance on international shipping, which can be costly and time-consuming.
The Solution:
To overcome this issue, B2B buyers should establish relationships with local distributors who specialize in electrical components. It is advisable to conduct a market analysis to identify suppliers that stock compatible replacement parts for Type A plugs. Additionally, buyers can negotiate agreements with manufacturers to ensure a steady supply of necessary components. Implementing a robust inventory management system can also help track usage and anticipate replacement needs, minimizing downtime and ensuring that operations run smoothly. Regular communication with suppliers about anticipated demand can facilitate timely restocking of critical components.
Strategic Material Selection Guide for type a plug
What Are the Common Materials Used for Type A Plugs?
When selecting materials for Type A plugs, international B2B buyers must consider various factors, including electrical performance, durability, and compliance with regional standards. Here, we analyze four common materials used in the production of Type A plugs: thermoplastics, thermosetting plastics, copper alloys, and nickel plating. Each material has unique properties that can significantly impact the performance and suitability of the plug for specific applications.
How Do Thermoplastics Perform in Type A Plugs?
Thermoplastics, such as polyvinyl chloride (PVC) and acrylonitrile butadiene styrene (ABS), are widely used in the manufacturing of Type A plugs due to their excellent electrical insulation properties and ease of processing. These materials can withstand temperatures up to 85°C and are resistant to various chemicals and moisture, making them suitable for indoor applications.
Pros: Thermoplastics are relatively low-cost and easy to mold, allowing for efficient mass production. They also provide good mechanical strength and flexibility, which helps in protecting the internal components of the plug.
Cons: While thermoplastics offer decent durability, they may not perform well under extreme temperatures or prolonged exposure to UV light, leading to degradation over time.
Impact on Application: Thermoplastics are ideal for general-purpose plugs used in residential and light commercial settings. However, they may not be suitable for heavy-duty applications where high temperatures or harsh environments are expected.
Considerations for International Buyers: Buyers from regions such as Africa and South America should ensure that the selected thermoplastic complies with local electrical standards, such as IEC or UL certifications.
What Role Do Thermosetting Plastics Play in Type A Plug Manufacturing?
Thermosetting plastics, like phenolic resin, are known for their high thermal resistance and mechanical strength. They can withstand temperatures up to 150°C, making them suitable for applications where heat generation is a concern.
Pros: These materials are highly durable and resistant to deformation under stress, providing long-lasting performance in demanding environments.
Cons: Thermosetting plastics are more expensive and complex to manufacture compared to thermoplastics, which can increase the overall cost of the Type A plug.
Impact on Application: Thermosetting plastics are ideal for plugs used in industrial settings or applications where high thermal loads are present.
Considerations for International Buyers: Buyers in Europe, particularly in countries like Spain, should verify that thermosetting materials meet EU safety and environmental regulations, such as RoHS compliance.
How Do Copper Alloys Enhance Electrical Conductivity in Type A Plugs?
Copper alloys, such as brass, are commonly used for the prongs of Type A plugs due to their excellent electrical conductivity and resistance to corrosion. Brass can handle high current loads, making it suitable for plugs rated at 15 A.
Pros: Copper alloys provide superior conductivity, which minimizes energy loss and enhances the efficiency of the electrical connection.
Cons: While copper is durable, it can corrode over time if not properly coated or treated, leading to reduced performance.
Impact on Application: Copper alloys are particularly beneficial in applications requiring reliable and efficient electrical connections, such as in commercial or industrial settings.
Considerations for International Buyers: Buyers from the Middle East should ensure that copper components meet local standards for electrical safety and corrosion resistance.
Why Is Nickel Plating Important for Type A Plugs?
Nickel plating is often applied to copper prongs to enhance corrosion resistance and improve the overall durability of Type A plugs. This coating can withstand a range of environmental conditions, making it suitable for various applications.
Pros: Nickel plating provides excellent protection against oxidation and wear, extending the lifespan of the plug.
Cons: The plating process can add to manufacturing costs and may require additional quality control measures to ensure uniformity.
Impact on Application: Nickel-plated plugs are ideal for outdoor or humid environments where corrosion is a concern.
Considerations for International Buyers: Buyers in humid regions, such as parts of Africa, should prioritize nickel-plated plugs to ensure longevity and reliability.
Summary Table of Material Selection for Type A Plugs
Material | Typical Use Case for Type A Plug | Key Advantage | Key Disadvantage/Limitation | Relative Cost (Low/Med/High) |
---|---|---|---|---|
Thermoplastics | General-purpose residential plugs | Low cost and easy to mold | Limited temperature resistance | Low |
Thermosetting Plastics | Industrial applications with high thermal loads | High durability and thermal resistance | Higher manufacturing complexity | High |
Copper Alloys | Commercial and industrial plugs | Superior electrical conductivity | Susceptible to corrosion | Medium |
Nickel Plating | Outdoor and humid environment applications | Excellent corrosion resistance | Increases manufacturing costs | Medium |
This strategic material selection guide provides B2B buyers with essential insights into the materials used in Type A plugs, helping them make informed decisions tailored to their specific regional needs and application requirements.
In-depth Look: Manufacturing Processes and Quality Assurance for type a plug
What Are the Main Stages of Manufacturing a Type A Plug?
The manufacturing process of a Type A plug involves several critical stages, each designed to ensure the final product meets safety and performance standards. Here’s a breakdown of the key stages:
-
Material Preparation
– The primary materials used for Type A plugs include thermoplastic for the outer casing and copper or brass for the prongs. The quality of these materials is vital; therefore, suppliers should provide certifications to confirm their compliance with international standards.
– Material inspections are conducted to verify that the components meet specifications before they proceed to the next stage. -
Forming
– The forming process includes stamping the metal prongs from sheets of copper or brass. This is typically done using high-precision stamping machines to ensure uniformity and accuracy in dimensions.
– Injection molding is utilized to create the plastic casing, which is formed around the prongs. This process ensures that the plug is both durable and insulated. -
Assembly
– After the prongs and casing are formed, they are assembled together. This stage may involve mechanical fastening or ultrasonic welding, depending on the design requirements.
– Proper alignment during assembly is crucial to ensure that the prongs fit correctly into outlets and that the plug operates safely. -
Finishing
– The final finishing touches may include plating the prongs with nickel or tin to enhance conductivity and prevent corrosion. This step is essential for ensuring the longevity and reliability of the plug.
– Finally, quality checks are performed to ensure that the plugs are free from defects and meet all aesthetic standards.
How Is Quality Assurance Implemented in Type A Plug Manufacturing?
Quality assurance (QA) is an integral part of the manufacturing process, ensuring that each Type A plug is safe and reliable. The following outlines the relevant international standards and the quality control checkpoints involved:
-
What Are the Relevant International Standards for Type A Plugs?
– Compliance with ISO 9001 is critical, as this standard outlines the requirements for a quality management system that can help organizations ensure they meet customer and regulatory requirements.
– In addition to ISO 9001, specific standards such as CE marking in Europe and UL certification in the United States indicate that the product meets safety requirements.
– B2B buyers should be aware of the local regulations in their respective regions, as these may affect importability and marketability. -
What Are the Key Quality Control Checkpoints?
– Incoming Quality Control (IQC): This checkpoint involves inspecting materials and components as they arrive at the manufacturing facility. Ensuring that all incoming materials meet specified requirements is crucial for maintaining quality throughout the production process.
– In-Process Quality Control (IPQC): Continuous monitoring occurs during the manufacturing process. This includes regular checks on machine settings, dimensions, and assembly accuracy to prevent defects.
– Final Quality Control (FQC): At this stage, finished products are thoroughly tested for electrical safety, mechanical integrity, and overall performance. This may involve stress testing and electrical load testing to ensure compliance with safety standards.
What Testing Methods Are Commonly Used for Type A Plugs?
To ensure that Type A plugs meet safety and performance standards, manufacturers employ various testing methods:
-
Electrical Testing
– Electrical continuity tests verify that the current can flow through the plug without interruption. This ensures that there are no short circuits or open circuits.
– Insulation resistance testing checks that the insulation material can withstand high voltages without allowing current to pass through it, preventing potential shock hazards. -
Mechanical Testing
– Mechanical stress tests assess the durability of the plug under various physical conditions, such as pulling and twisting forces.
– Thermal cycling tests evaluate how the plug performs under extreme temperature changes, ensuring it retains functionality without warping or melting. -
Environmental Testing
– Plugs may also undergo environmental testing to simulate exposure to moisture, dust, and other environmental factors. This helps ensure that they remain functional and safe in various conditions.
How Can B2B Buyers Verify Supplier Quality Control Practices?
For international B2B buyers, particularly those from Africa, South America, the Middle East, and Europe, verifying a supplier’s quality control practices is essential. Here are some actionable insights:
-
Conduct Supplier Audits
– Performing on-site audits allows buyers to assess the manufacturing processes and quality control measures firsthand. This provides assurance that the supplier adheres to international standards and maintains high production quality. -
Request Quality Assurance Reports
– Buyers should request detailed quality assurance reports that outline the results of various testing methods and inspections. These reports should include data on defect rates, compliance with standards, and any corrective actions taken. -
Utilize Third-Party Inspection Services
– Engaging third-party inspection services can provide an unbiased evaluation of the manufacturing processes. These services can conduct random checks and tests on the products before they are shipped, ensuring that only compliant items reach the buyer. -
Understand Certification Nuances for International Trade
– B2B buyers must be aware of the certification requirements specific to their regions. For instance, European buyers should ensure that products are CE marked, while those in the Middle East may need to check for local compliance certifications.
Conclusion
The manufacturing processes and quality assurance protocols for Type A plugs are designed to ensure safety, reliability, and compliance with international standards. For B2B buyers, particularly those in diverse markets like Africa, South America, the Middle East, and Europe, understanding these processes is crucial. By implementing rigorous supplier verification methods, buyers can secure high-quality products that meet their operational needs.
Practical Sourcing Guide: A Step-by-Step Checklist for ‘type a plug’
In the global marketplace, sourcing Type A plugs can present unique challenges and opportunities for B2B buyers, particularly those operating in diverse regions such as Africa, South America, the Middle East, and Europe. This checklist serves as a practical guide to help you navigate the procurement process effectively.
Step 1: Define Your Technical Specifications
Start by outlining the specific technical requirements for the Type A plug you need. Consider factors such as voltage, current rating (typically 15 A for Type A), and any specific safety standards applicable in your region.
– Voltage Compatibility: Ensure that the plug can operate efficiently within the local voltage range (typically 120V in North America).
– Safety Compliance: Identify relevant safety certifications (e.g., UL, CE) that the plugs must meet to ensure reliability and safety.
Step 2: Research Potential Suppliers
Conduct thorough research to identify reputable suppliers who specialize in electrical components. Look for companies with a strong track record in your region or industry.
– Industry Experience: Focus on suppliers who have experience with Type A plugs and understand the specific needs of your market.
– Supplier Reviews: Check customer reviews and testimonials to gauge reliability and product quality.
Step 3: Evaluate Supplier Certifications
Before committing to a supplier, verify that they hold the necessary certifications and quality assurances for their products. This is crucial for ensuring compliance and safety.
– ISO Certifications: Look for ISO 9001 or similar quality management certifications, which indicate a commitment to quality.
– Product Testing: Inquire about testing procedures and standards the products have undergone to ensure they meet safety and performance benchmarks.
Step 4: Request Samples for Testing
Once you have shortlisted potential suppliers, request samples of the Type A plugs for testing. This is a critical step to assess the quality and compatibility of the plugs with your equipment.
– Quality Assessment: Evaluate the plugs for durability, conductivity, and overall build quality.
– Compatibility Checks: Ensure that the plugs fit into your existing sockets and meet the required specifications.
Step 5: Negotiate Pricing and Terms
With samples tested and suppliers evaluated, initiate negotiations on pricing, payment terms, and delivery schedules. This step is essential for securing the best deal.
– Bulk Purchase Discounts: Discuss potential discounts for bulk orders, which can significantly reduce costs.
– Payment Flexibility: Look for suppliers who offer flexible payment terms, such as net 30 or net 60, to improve cash flow.
Step 6: Confirm Logistics and Shipping Arrangements
Before finalizing the order, confirm logistics and shipping arrangements to ensure timely delivery. This is particularly important for international transactions.
– Shipping Options: Evaluate shipping methods and choose the one that balances cost and delivery speed.
– Customs and Duties: Be aware of any customs regulations and duties that may apply when importing Type A plugs into your country.
Step 7: Establish a Long-Term Relationship
After successful procurement, aim to build a long-term relationship with your supplier. This can facilitate smoother transactions and better support in future sourcing needs.
– Regular Communication: Maintain open lines of communication to discuss future orders or any issues that may arise.
– Feedback Loop: Provide feedback on product performance to help the supplier improve their offerings and service.
By following this comprehensive checklist, B2B buyers can effectively source Type A plugs that meet their technical requirements while ensuring compliance, quality, and favorable terms.
Comprehensive Cost and Pricing Analysis for type a plug Sourcing
What Are the Key Cost Components in Sourcing Type A Plugs?
When sourcing Type A plugs, understanding the cost structure is crucial for international B2B buyers. The primary cost components include:
-
Materials: The cost of raw materials like copper for the prongs, plastic for the housing, and any additional components such as insulation or certification labels. The prices of these materials can fluctuate based on global supply chains and demand.
-
Labor: Labor costs encompass wages for workers involved in manufacturing and assembly. The location of production can significantly affect these costs; for instance, labor is typically cheaper in Southeast Asia compared to Europe.
-
Manufacturing Overhead: This includes costs related to factory maintenance, utilities, and indirect labor. Efficient manufacturing processes can help minimize overhead costs.
-
Tooling: Initial tooling costs for molds and equipment can be significant, especially for customized plugs. These costs are typically amortized over the production run.
-
Quality Control (QC): Ensuring that plugs meet safety and quality standards involves additional costs. Regular inspections and certifications can drive up costs but are essential for compliance, especially in markets like Europe and the Middle East.
-
Logistics: Shipping and handling costs should not be overlooked. These costs vary depending on the distance from the supplier to the buyer, shipping method, and any tariffs or duties applicable in the importing country.
-
Margin: Suppliers typically add a profit margin to their costs, which can vary based on market conditions and competition. Understanding the margin can help buyers negotiate better prices.
How Do Price Influencers Affect Type A Plug Sourcing?
Several factors influence the pricing of Type A plugs, and buyers should consider these when sourcing:
-
Volume/MOQ: The Minimum Order Quantity (MOQ) can significantly affect pricing. Bulk orders often qualify for discounts, so it’s beneficial for buyers to consolidate their needs.
-
Specifications and Customization: Customized plugs may incur additional costs due to unique specifications, such as different pin sizes or materials. Standardized products typically have lower prices due to economies of scale.
-
Materials and Quality Certifications: Higher-quality materials and certifications (like CE or UL) can increase costs. However, investing in quality can reduce the risk of failures and enhance safety.
-
Supplier Factors: The reputation and reliability of suppliers can impact pricing. Established suppliers may charge more due to their track record, while newer or less reliable suppliers might offer lower prices but with higher risks.
-
Incoterms: The choice of Incoterms (e.g., FOB, CIF) will influence the total landed cost of the plugs. Buyers should understand their responsibilities in terms of shipping and insurance to avoid unexpected expenses.
What Are the Best Practices for Negotiating Type A Plug Prices?
Negotiating effectively can lead to better pricing and terms for Type A plugs:
-
Research and Benchmarking: Understand market prices by researching various suppliers and comparing offers. This knowledge empowers buyers during negotiations.
-
Establish Long-term Relationships: Building a strong relationship with suppliers can lead to better pricing over time, as suppliers may offer loyalty discounts or more favorable terms to repeat customers.
-
Focus on Total Cost of Ownership (TCO): Consider not just the purchase price but the TCO, which includes maintenance, operational efficiency, and potential downtime costs. A higher initial price may lead to lower long-term costs if the product is of better quality.
-
Leverage Volume: If possible, consolidate orders across multiple product lines to increase order volume. This strategy may provide leverage for better pricing.
-
Be Aware of Pricing Nuances: Understand that international buyers may face fluctuating exchange rates, tariffs, and shipping costs that can affect the final price. Consider these factors in negotiations.
Conclusion
Sourcing Type A plugs requires a comprehensive understanding of the cost structure, pricing influencers, and effective negotiation strategies. By being informed and strategic, international B2B buyers from Africa, South America, the Middle East, and Europe can secure favorable terms and ensure quality compliance in their purchases. Always remember that prices may vary based on market conditions, and it’s advisable to seek multiple quotes for an informed decision.
Alternatives Analysis: Comparing type a plug With Other Solutions
Exploring Alternatives to Type A Plugs
In the realm of electrical connectivity, Type A plugs are commonly used in various regions, especially in North and Central America. However, as global trade expands and businesses operate across borders, understanding alternative solutions is crucial for international B2B buyers. This section delves into viable alternatives to Type A plugs, comparing them based on performance, cost, ease of implementation, maintenance, and best use cases.
Comparison Table
Comparison Aspect | Type A Plug | Type C Plug | Type B Plug |
---|---|---|---|
Performance | Suitable for 120V, 15A | Handles 230V, 16A | Suitable for 120V, 15A |
Cost | Low cost, widely available | Moderate cost, less common | Moderate cost, common in North America |
Ease of Implementation | Simple installation, no grounding | Requires compatible sockets | Requires grounding for safety |
Maintenance | Low maintenance | Low maintenance | Moderate, grounding checks needed |
Best Use Case | Lightweight devices, low power | Appliances requiring higher voltage | General use in North America |
What are the Advantages and Disadvantages of Using Type C Plugs?
Type C plugs, also known as the Europlug, are a popular alternative in many regions, especially in Europe and parts of Africa and Asia. One of the significant advantages of the Type C plug is its ability to handle higher voltage applications (up to 230V and 16A), making it suitable for a broader range of devices, including heavier appliances. However, its lack of grounding can pose safety risks when used with devices that require grounding. Additionally, Type C plugs may require compatible sockets, which could incur additional installation costs in regions that predominantly use Type A plugs.
How Does the Type B Plug Compare to Type A?
The Type B plug is a grounded option primarily used in North America. Its design includes a grounding pin, which enhances safety by preventing electric shock. This makes it ideal for devices that draw significant power or operate in environments where electrical faults could occur. However, Type B plugs may incur higher costs in regions where they are not standard, as the infrastructure may need upgrading to accommodate them. While Type B plugs are slightly more complex to install due to the grounding requirements, their safety benefits make them a strong contender for B2B applications where reliability is crucial.
Conclusion: Which Plug Solution is Right for Your Business?
When selecting the right plug solution for your business needs, consider the specific requirements of your devices and the regional standards where your operations are based. If your products are lightweight and low-power, the Type A plug may suffice. However, for businesses dealing with higher voltage appliances or requiring enhanced safety measures, exploring Type C or Type B plugs could be advantageous. Conducting a thorough needs assessment, including cost implications and installation requirements, will ensure that you make an informed decision that aligns with your operational goals.
Essential Technical Properties and Trade Terminology for type a plug
What Are the Essential Technical Properties of Type A Plugs?
Understanding the technical properties of Type A plugs is crucial for B2B buyers who are sourcing electrical components. Here are key specifications that should be considered:
1. Material Grade
Type A plugs are typically made from durable materials such as polycarbonate or thermoplastic. These materials provide high impact resistance and thermal stability, essential for maintaining performance in various environments. For B2B buyers, selecting plugs made from high-quality materials ensures safety and longevity, reducing the risk of product failure and subsequent liability.
2. Current Rating
The Type A plug is rated for a maximum current of 15 A. This specification indicates how much electrical load the plug can safely handle without overheating. Buyers should ensure that the plugs sourced for their applications match the current requirements of the devices they intend to power, as exceeding this limit can lead to overheating and potential hazards.
3. Pin Dimensions and Tolerances
Type A plugs feature two flat blades that measure 15.9 – 18.3 mm in length and 1.5 mm in thickness, with a width difference between the neutral and hot blades. Tolerances are critical for ensuring compatibility with sockets. Buyers should verify that the plugs they procure meet these dimensional specifications to avoid issues with connectivity or safety.
4. Polarization
Type A plugs are often polarized, meaning one blade is wider than the other. This design prevents incorrect insertion into sockets, ensuring that the electrical device operates safely. For B2B buyers, understanding the importance of polarization can help in selecting the right plug for devices that require a specific orientation to function correctly.
5. Temperature Rating
The typical operating temperature range for Type A plugs is -10°C to 60°C. This specification is vital for applications in varying climates, ensuring that the plugs will function effectively without degradation. Buyers should consider the environmental conditions where the plugs will be used to avoid failures.
6. Insulation Type
While Type A plugs are not insulated (the pin shanks lack a covering), it’s important for buyers to understand the risks associated with this design. In environments with high moisture or dust, uninsulated plugs can pose safety risks. Buyers should assess the application environment before making purchasing decisions.
What Are Common Trade Terminologies Related to Type A Plugs?
Familiarity with industry jargon can help B2B buyers navigate sourcing more effectively. Here are some essential terms:
1. OEM (Original Equipment Manufacturer)
OEM refers to companies that manufacture products that are sold under another company’s brand. For B2B buyers, understanding OEM relationships can facilitate sourcing strategies and ensure that the components meet specific quality standards.
2. MOQ (Minimum Order Quantity)
MOQ is the minimum quantity of products a supplier is willing to sell. Knowing the MOQ is essential for buyers to assess the feasibility of their orders, especially when sourcing Type A plugs in bulk.
3. RFQ (Request for Quotation)
An RFQ is a document sent to suppliers asking for pricing and terms for specific products. B2B buyers should prepare detailed RFQs to ensure they receive accurate quotes for Type A plugs that meet their specifications.
4. Incoterms (International Commercial Terms)
Incoterms define the responsibilities of buyers and sellers in international transactions, including shipping and insurance. Understanding Incoterms is crucial for B2B buyers to manage logistics and ensure that they are aware of their responsibilities when importing Type A plugs.
5. Certification Standards
Certification standards such as UL (Underwriters Laboratories) or CE (Conformité Européenne) signify that a product meets specific safety and performance criteria. Buyers should prioritize sourcing Type A plugs that comply with relevant certification standards to ensure safety and reliability.
6. Lead Time
Lead time refers to the time it takes from placing an order until it is delivered. Understanding lead time is important for B2B buyers to effectively plan their inventory and avoid delays in production.
By grasping these technical properties and trade terminologies, international B2B buyers can make informed decisions when sourcing Type A plugs, ensuring safety, compliance, and efficiency in their operations.
Navigating Market Dynamics and Sourcing Trends in the type a plug Sector
What Are the Current Market Dynamics and Sourcing Trends for Type A Plugs?
The Type A plug market is influenced by several global drivers, including the rise of digitalization and increasing demand for electronic devices. As international B2B buyers from Africa, South America, the Middle East, and Europe seek reliable power solutions, understanding these dynamics becomes essential. In particular, the growth of e-commerce and the globalization of supply chains have led to an uptick in the sourcing of electrical components, including Type A plugs.
Emerging trends in B2B technology, such as smart manufacturing and automation, are also reshaping how companies procure these products. Manufacturers are increasingly investing in automation technologies to improve efficiency and reduce costs, resulting in competitive pricing for international buyers. Additionally, the push for universal compatibility is driving innovations in plug design, with the aim of creating multi-standard solutions that can cater to diverse markets.
For international buyers, navigating the complexities of sourcing Type A plugs involves assessing suppliers based on their compliance with international standards and certifications. This is particularly crucial for buyers in regions like Europe and the Middle East, where regulatory frameworks are stringent. Understanding local electrical standards and the specific demands of various markets can help businesses mitigate risks associated with product compatibility and safety.
How Can Sustainability and Ethical Sourcing Impact the Type A Plug Sector?
The environmental impact of electrical components, including Type A plugs, is becoming a focal point for B2B buyers. The production and disposal of electrical plugs can generate significant waste and pollution, making it imperative for companies to prioritize sustainability in their sourcing decisions. By opting for suppliers that adhere to environmentally friendly practices, buyers can minimize their carbon footprint and contribute to broader sustainability goals.
Ethical supply chains are also gaining traction. Buyers are increasingly scrutinizing their suppliers’ labor practices and sourcing materials. This trend is particularly relevant in regions like Africa and South America, where labor conditions may vary widely. Businesses that prioritize ethical sourcing not only enhance their brand reputation but also build stronger relationships with consumers who are becoming more conscious of their purchasing decisions.
To further support these initiatives, buyers should look for ‘green’ certifications and materials in their sourcing process. Certifications such as RoHS (Restriction of Hazardous Substances) and WEEE (Waste Electrical and Electronic Equipment) indicate that the products meet specific environmental standards. By choosing Type A plugs that comply with these regulations, international buyers can align their purchasing strategies with global sustainability goals.
What Is the Historical Context Behind Type A Plugs for B2B Buyers?
The Type A plug, first introduced in the early 1900s, has evolved significantly over the decades. Originally designed for use in North America, it has become a standard in various countries, including Japan and parts of Central America. Understanding the historical context of Type A plugs provides valuable insights into their design and functionality.
As B2B buyers navigate sourcing decisions, acknowledging the evolution of this plug type can inform their choices regarding compatibility and safety. The Type A plug’s ungrounded design, while convenient, poses certain risks, particularly in environments with high electrical demands. Knowledge of these historical nuances can guide buyers in selecting products that meet modern safety standards while considering the specific needs of their target markets.
In summary, the Type A plug sector is marked by dynamic market trends, a growing emphasis on sustainability, and a rich historical context. For international B2B buyers, leveraging this information can enhance their sourcing strategies, ensuring they make informed decisions that align with both their operational needs and ethical commitments.
Frequently Asked Questions (FAQs) for B2B Buyers of type a plug
-
How do I solve compatibility issues when sourcing type A plugs for different regions?
To address compatibility issues with type A plugs, first, research the specific electrical standards of the target market, such as voltage and frequency. Verify if the equipment will be used in countries with type A outlets (like the US, Canada, and Japan) and check for any local regulations regarding plug specifications. Consider sourcing plugs that comply with international standards to ensure versatility. Additionally, establish relationships with manufacturers who can provide customized solutions for different markets to avoid compatibility problems. -
What is the best approach for vetting suppliers of type A plugs?
When vetting suppliers, start by checking their certifications and compliance with international safety standards, such as IEC or UL. Request samples to evaluate the quality and functionality of their type A plugs. Additionally, assess their production capacity, lead times, and customer reviews. Engage in direct communication to understand their quality assurance processes and after-sales support. This thorough vetting process will help ensure you partner with reliable suppliers who can meet your business needs. -
What customization options are available for type A plugs?
Many manufacturers offer customization options for type A plugs, including variations in color, length of wires, and additional safety features like built-in surge protectors. You can also request specific branding or labeling on the plugs to align with your company’s identity. To explore these options, communicate your requirements clearly with potential suppliers and inquire about their capabilities. Be sure to consider the implications of customization on pricing and lead times. -
What are the minimum order quantities (MOQs) for type A plugs from international suppliers?
Minimum order quantities for type A plugs can vary significantly between suppliers, typically ranging from 500 to 10,000 units. Factors influencing MOQs include the supplier’s production capacity, your customization requirements, and the material costs. When negotiating, consider discussing flexible MOQs, especially if you are testing a new market or product line. Building a strong relationship with your supplier may also lead to more favorable terms in future orders. -
What payment terms should I expect when sourcing type A plugs internationally?
Payment terms can vary widely, but common practices include 30% upfront payment and 70% upon delivery, or payment via letters of credit. It is essential to discuss and agree on payment terms that protect both parties. Additionally, consider using secure payment methods that offer buyer protection. For larger orders, negotiating better terms can be beneficial, so be prepared to present your business’s credibility and purchasing history to your supplier. -
How do I ensure quality assurance (QA) for type A plugs sourced from overseas?
To ensure quality assurance for type A plugs, establish clear quality standards and specifications before placing an order. Request pre-shipment inspections or third-party quality audits to verify compliance with these standards. Additionally, consider implementing a trial order to assess the quality of the products before committing to larger quantities. Building a strong relationship with your supplier will also facilitate open communication regarding any quality concerns that may arise. -
What logistics considerations should I keep in mind when importing type A plugs?
When importing type A plugs, consider shipping methods, customs regulations, and potential tariffs. Evaluate options such as air freight for speed or sea freight for cost-effectiveness. Ensure you have a reliable logistics partner who understands the import/export process and can handle documentation efficiently. Additionally, be aware of lead times and plan for any delays, especially during peak shipping seasons or due to regulatory changes in your target market. -
How can I stay informed about changes in regulations for type A plugs in my target markets?
Staying informed about regulatory changes for type A plugs involves subscribing to industry publications, joining relevant trade associations, and following government websites that outline electrical safety standards. Networking with industry peers and participating in forums can also provide valuable insights into emerging trends and regulations. Additionally, consider working with local consultants who specialize in compliance issues to navigate any complexities related to your specific markets.
Important Disclaimer & Terms of Use
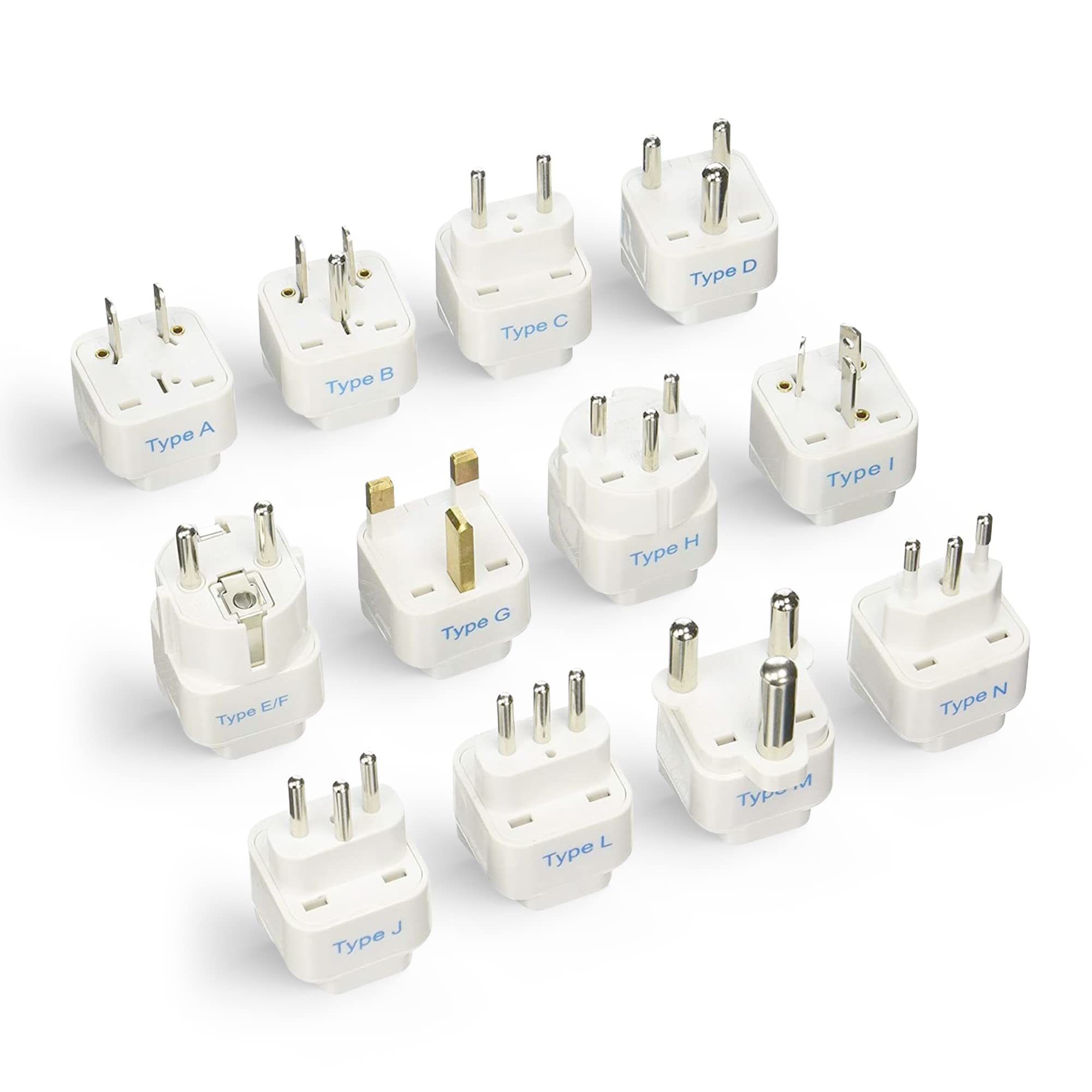
A stock image related to type a plug.
⚠️ Important Disclaimer
The information provided in this guide, including content regarding manufacturers, technical specifications, and market analysis, is for informational and educational purposes only. It does not constitute professional procurement advice, financial advice, or legal advice.
While we have made every effort to ensure the accuracy and timeliness of the information, we are not responsible for any errors, omissions, or outdated information. Market conditions, company details, and technical standards are subject to change.
B2B buyers must conduct their own independent and thorough due diligence before making any purchasing decisions. This includes contacting suppliers directly, verifying certifications, requesting samples, and seeking professional consultation. The risk of relying on any information in this guide is borne solely by the reader.
Strategic Sourcing Conclusion and Outlook for type a plug
What Are the Key Takeaways for B2B Buyers of Type A Plugs?
In navigating the complexities of sourcing Type A plugs, international B2B buyers must prioritize a strategic approach. Understanding the specific regulations and safety standards in regions like Africa, South America, the Middle East, and Europe is crucial. The Type A plug, predominantly used in North America and parts of Japan, lacks grounding features, which can pose safety risks if not properly managed. Ensuring compliance with local electrical standards and leveraging suppliers that adhere to rigorous quality checks will mitigate these risks.
How Does Strategic Sourcing Enhance Your Supply Chain?
Strategic sourcing is not merely about cost reduction; it involves building long-term partnerships with reliable manufacturers. By investing in quality suppliers, businesses can enhance their product offerings, improve safety, and ensure compliance with international standards. This is particularly pertinent for buyers in emerging markets, where the demand for reliable electrical components is on the rise.
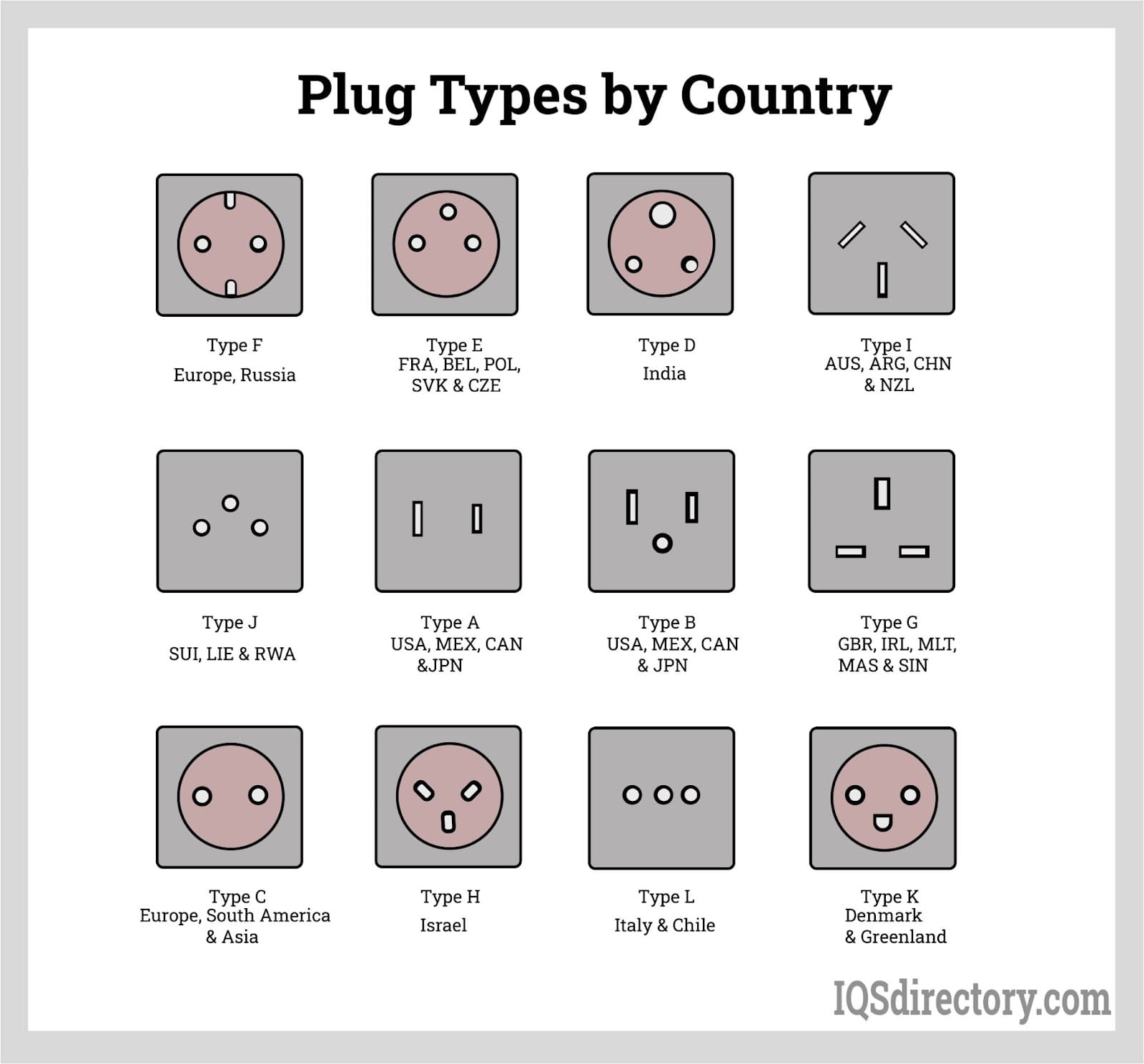
A stock image related to type a plug.
What Does the Future Hold for Type A Plug Buyers?
Looking ahead, the demand for Type A plugs is expected to grow as global connectivity increases and electronic devices proliferate. For buyers in regions like Spain and the UAE, tapping into diverse sourcing networks will be vital. Embrace innovation and flexibility in your sourcing strategy to stay competitive. As the landscape evolves, proactive engagement with suppliers will pave the way for success in the international marketplace.