Discover the Best Types of Mixers for Your Business Needs (2025)
Introduction: Navigating the Global Market for types of mixers
In today’s competitive global landscape, sourcing the right types of mixers can be a daunting challenge for international B2B buyers. With diverse applications ranging from food processing to pharmaceuticals, selecting the appropriate mixing equipment is crucial for ensuring product quality and operational efficiency. This comprehensive guide delves into the various types of mixers available on the market, including agitators, emulsifiers, and high shear mixers, while also addressing their specific applications and benefits.
As buyers from regions such as Africa, South America, the Middle East, and Europe seek to enhance their production processes, understanding the nuances of each mixer type becomes vital. This guide not only provides detailed insights into the features and functionalities of different mixers but also offers practical advice on supplier vetting, cost considerations, and maintenance requirements.
By empowering B2B buyers with the knowledge needed to make informed purchasing decisions, this guide aims to streamline the sourcing process, enabling businesses to achieve optimal mixing solutions tailored to their unique operational needs. Whether you are in Nigeria seeking efficient solutions for food processing or in Europe looking to enhance your pharmaceutical manufacturing, understanding the global market for types of mixers is your first step towards success.
Understanding types of mixers Types and Variations
Type Name | Key Distinguishing Features | Primary B2B Applications | Brief Pros & Cons for Buyers |
---|---|---|---|
Agitators | Rotating impeller, suitable for liquid-liquid and liquid-gas mixing | Food and beverage, pharmaceuticals, chemicals | Pros: Effective for blending miscible liquids; versatile. Cons: Not suitable for high-viscosity products. |
High Shear Mixers | Rotor-stator design, extreme shear forces for emulsification | Cosmetics, pharmaceuticals, food processing | Pros: Excellent for creating uniform emulsions. Cons: Higher initial cost; requires skilled operation. |
Ribbon Blenders | Ribbon-like paddles for bulk powder blending | Food production, chemicals, pharmaceuticals | Pros: Efficient for bulk solids; good mixing uniformity. Cons: Maintenance can be complex; higher energy consumption. |
Homogenizers | High pressure and shear to create uniform mixtures | Dairy, beverage, pharmaceuticals | Pros: Produces consistent product quality; suitable for various phases. Cons: Expensive; can require specialized parts. |
Emulsifiers | Combines immiscible liquids using high shear and vacuum | Cosmetics, food, pharmaceuticals | Pros: Effective for difficult mixtures; high-quality emulsification. Cons: Requires careful calibration; higher operational costs. |
What Are Agitators and Their Key Applications?
Agitators are mixing devices that utilize a rotating impeller to blend liquids, making them ideal for applications in food and beverage, pharmaceuticals, and chemical processes. They can efficiently mix miscible liquids and facilitate gas-liquid interactions. When considering an agitator, buyers should evaluate the viscosity of the materials being mixed, as these devices are not suitable for highly viscous products. Additionally, the choice between axial and radial flow designs can impact mixing efficiency.
How Do High Shear Mixers Improve Product Quality?
High shear mixers utilize rotor-stator designs to create intense shear forces, enabling the emulsification and homogenization of mixtures. These mixers are particularly valuable in the cosmetics, pharmaceuticals, and food processing industries, where product consistency is crucial. Buyers should consider the initial investment and the need for skilled personnel to operate these machines effectively. The ability to produce high-quality emulsions can lead to improved product performance and customer satisfaction.
Why Choose Ribbon Blenders for Bulk Mixing?
Ribbon blenders are designed with long, intersecting paddles that efficiently mix bulk powders and solids. They are commonly used in food production, chemicals, and pharmaceuticals due to their ability to achieve homogeneity with minimal energy. However, buyers should be aware that while they are effective, ribbon blenders may require complex maintenance and can consume more energy compared to other mixing solutions. Understanding the specific mixing needs and operational costs is essential for making an informed purchase.
What Role Do Homogenizers Play in Industrial Mixing?
Homogenizers apply high pressure and shear to create uniform mixtures, making them vital in dairy, beverage, and pharmaceutical industries. These machines excel at blending liquids of different phases, ensuring consistent product quality. Buyers should consider the investment costs and the need for specialized parts, as homogenizers can be expensive. Their ability to deliver high-quality results makes them a worthwhile investment for companies prioritizing product consistency.
How Are Emulsifiers Essential in Mixing Immiscible Liquids?
Emulsifiers are specialized devices that effectively combine immiscible liquids, such as oil and water, using high shear and vacuum techniques. They are widely used in cosmetics, food production, and pharmaceuticals, where product stability is critical. When purchasing emulsifiers, buyers should factor in the calibration requirements and the potentially higher operational costs. The quality of emulsification directly impacts the final product, making these mixers a valuable asset in any production line.
Key Industrial Applications of types of mixers
Industry/Sector | Specific Application of Types of Mixers | Value/Benefit for the Business | Key Sourcing Considerations for this Application |
---|---|---|---|
Food and Beverage | Homogenization of dairy products and emulsification of sauces | Improved product consistency and extended shelf life | Compliance with food safety standards and certifications |
Pharmaceuticals | Mixing active ingredients in drug formulations | Enhanced bioavailability and product efficacy | Precision in mixing ratios and compatibility of materials |
Chemicals | Blending of adhesives and sealants | Increased adhesion properties and reduced production time | Resistance to chemical corrosion and durability |
Cosmetics and Personal Care | Emulsification of creams and lotions | Superior texture and skin feel, leading to customer satisfaction | Ability to handle high viscosity ingredients and ease of cleaning |
Construction Materials | Mixing of concrete and mortar | Improved structural integrity and faster curing times | Equipment size and power requirements for large batches |
How Are Mixers Used in the Food and Beverage Industry?
In the food and beverage sector, mixers play a crucial role in the homogenization of dairy products and the emulsification of sauces. For instance, high shear mixers are employed to create a uniform blend of milk and cream, ensuring that the fat molecules are evenly distributed. This not only enhances the taste and mouthfeel but also extends the product’s shelf life. International buyers must consider compliance with food safety standards, as well as the mixer’s capacity to handle varying viscosities, particularly in regions with diverse ingredient qualities.
What Are the Applications of Mixers in Pharmaceuticals?
In the pharmaceutical industry, mixers are essential for combining active ingredients in drug formulations. Homogenizers and agitators are commonly used to achieve a uniform mixture, which is vital for the bioavailability and efficacy of medications. Buyers in this sector need to focus on precision in mixing ratios and the compatibility of materials, ensuring that the mixers meet stringent regulatory requirements. Additionally, equipment that minimizes contamination risks during the mixing process is a critical consideration for sourcing.
How Are Mixers Utilized in the Chemicals Sector?
The chemicals industry frequently employs mixers for blending adhesives and sealants. Ribbon blenders and paddle mixers are effective in achieving a homogenous mixture, which enhances the adhesion properties of the final product. This results in faster production times and improved performance in applications such as construction and automotive manufacturing. When sourcing mixers for chemical applications, buyers should prioritize equipment that offers resistance to corrosion and is designed for easy maintenance, especially in regions with varying environmental conditions.
What Role Do Mixers Play in Cosmetics and Personal Care?
In the cosmetics and personal care industry, mixers are vital for emulsifying creams and lotions. Emulsifiers are used to blend oil and water-based ingredients, creating a smooth and stable product that enhances customer satisfaction. For international buyers, particularly in emerging markets, it is essential to ensure that the mixers can handle high viscosity ingredients while being easy to clean to maintain hygiene standards. Additionally, sourcing equipment that complies with cosmetic regulations is critical for market entry and acceptance.
How Are Mixers Important in Construction Materials?
Mixers are indispensable in the construction materials industry for mixing concrete and mortar. The right type of mixer ensures a consistent blend, which is crucial for the structural integrity of buildings and infrastructure. High-capacity mixers that can handle large batches are often required, along with considerations for power requirements to ensure efficiency. Buyers must evaluate equipment based on its performance in different environmental conditions, particularly in regions with extreme weather patterns, to ensure reliability and effectiveness.
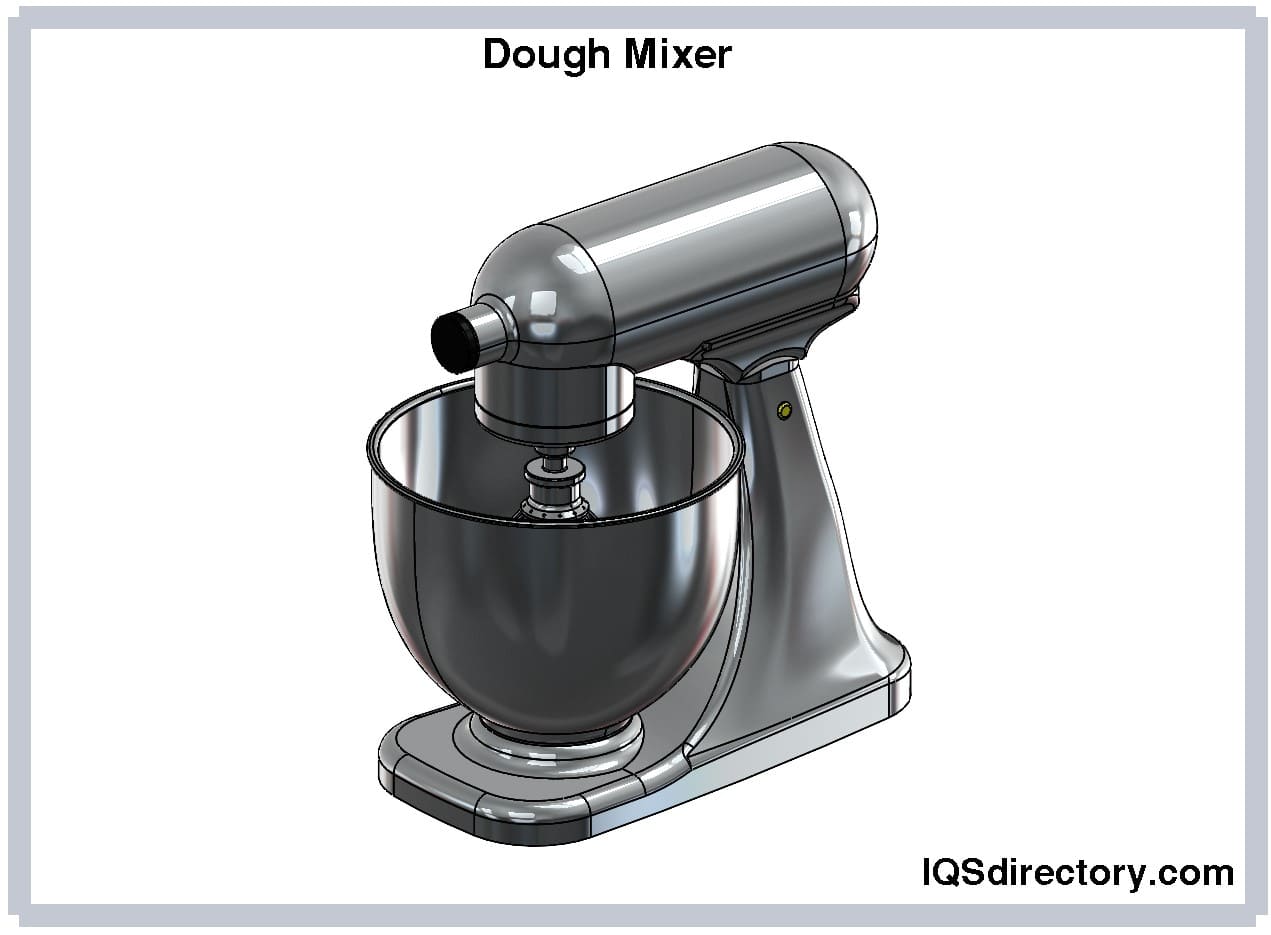
A stock image related to types of mixers.
3 Common User Pain Points for ‘types of mixers’ & Their Solutions
Scenario 1: Overcoming Inconsistent Product Quality in Emulsions
The Problem: In industries such as cosmetics or food production, maintaining consistent quality in emulsions is crucial. B2B buyers often face challenges when their mixers fail to produce stable emulsions, leading to variations in texture and appearance. This inconsistency not only affects product quality but also impacts brand reputation and customer satisfaction. For example, a manufacturer in Nigeria producing lotion may find that their emulsifier cannot adequately mix oil and water, resulting in separation and a product that does not meet market standards.
The Solution: To address this issue, buyers should invest in high-shear emulsifiers designed specifically for mixing immiscible liquids. When sourcing equipment, look for mixers that feature adjustable shear rates and a variety of rotor-stator configurations to accommodate different viscosities. Additionally, consider investing in training for operators to ensure they understand the equipment’s capabilities and how to optimize settings for different formulations. Regular maintenance and calibration of the mixing equipment will also help maintain performance and consistency, thus ensuring that every batch meets the desired quality standards.
Scenario 2: Managing Production Downtime Due to Mixer Failures
The Problem: Production downtime can be a significant pain point for manufacturers using mixers, especially in the food and beverage sector in regions like South America. When a mixer unexpectedly fails, it can halt the entire production line, leading to delays, increased costs, and missed delivery deadlines. A beverage manufacturer in Brazil might experience a breakdown in their tank mixer, causing a backlog in orders and a loss of customer trust.
The Solution: To mitigate the risk of unexpected failures, B2B buyers should prioritize investing in high-quality, durable mixers from reputable manufacturers. Implementing a preventive maintenance schedule is critical; this includes regular inspections and timely replacement of wear parts. Additionally, investing in smart technology that provides real-time monitoring and diagnostics can help predict potential failures before they occur. Establishing a relationship with a local service provider for quick repairs and support can also minimize downtime and ensure that production lines remain efficient and responsive to market demands.
Scenario 3: Struggling with High Operational Costs Due to Inefficient Mixing Processes
The Problem: Many B2B buyers, particularly in the Middle East, face high operational costs stemming from inefficient mixing processes. For instance, a chemical manufacturer may find that their current paddle mixer consumes excessive energy and requires longer mixing times, leading to inflated production costs and reduced profitability. As energy prices continue to rise, this inefficiency can have a profound impact on the bottom line.
The Solution: To combat high operational costs, buyers should assess the efficiency of their current mixing equipment. Switching to a more energy-efficient mixer, such as a ribbon blender or a high-shear mixer, can significantly reduce both energy consumption and mixing times. When evaluating new equipment, consider the total cost of ownership, including energy usage, maintenance costs, and output efficiency. Utilizing simulation software to model different mixing processes can also provide insights into optimizing operational parameters. Training staff on best practices for efficient mixing can further reduce waste and improve overall productivity, ultimately enhancing profitability.
Strategic Material Selection Guide for types of mixers
What Are the Key Materials Used in Mixers and Their Properties?
When selecting mixers for industrial applications, the choice of materials is critical. The materials not only impact the performance and durability of the mixers but also influence compliance with regional standards. Below, we analyze four common materials used in the manufacturing of mixers: stainless steel, carbon steel, plastic, and ceramic.
How Does Stainless Steel Enhance Mixer Performance?
Key Properties: Stainless steel is renowned for its excellent corrosion resistance, high-temperature tolerance, and durability. It can withstand pressures significantly above atmospheric levels, making it suitable for high-pressure applications.
Pros & Cons: The primary advantage of stainless steel is its longevity and resistance to rust and chemical degradation, which is crucial in industries like food and pharmaceuticals. However, it comes with a higher upfront cost and can be more complex to manufacture due to the need for specialized welding techniques.
Impact on Application: Stainless steel is compatible with a wide range of media, including corrosive substances, making it ideal for applications requiring hygiene and purity, such as food processing and pharmaceuticals.
Considerations for International Buyers: Buyers in regions like Africa and South America should ensure that the stainless steel used complies with international standards such as ASTM A240. Additionally, understanding local sourcing options can help mitigate costs.
Why Choose Carbon Steel for Industrial Mixers?
Key Properties: Carbon steel offers good strength and toughness, along with moderate corrosion resistance. It is typically rated for lower temperatures and pressures compared to stainless steel.
Pros & Cons: Carbon steel is more affordable than stainless steel, making it an attractive option for budget-conscious projects. However, it is prone to rust and corrosion, which limits its application in wet or corrosive environments.
Impact on Application: This material is suitable for dry mixing applications or where the media is not corrosive. It may be less suitable for food applications due to hygiene concerns.
Considerations for International Buyers: Buyers should be aware of the need for protective coatings or treatments to enhance the lifespan of carbon steel mixers, especially in humid climates prevalent in parts of Africa and South America.
How Do Plastics Compare in Mixer Applications?
Key Properties: Plastics, such as polyethylene and polypropylene, are lightweight, cost-effective, and resistant to a variety of chemicals. They have lower temperature and pressure ratings compared to metals.
Pros & Cons: The main advantage of plastic mixers is their affordability and ease of handling. However, they may not be suitable for high-temperature applications and can wear out faster than metal options.
Impact on Application: Plastics are ideal for mixing non-corrosive liquids and powders, making them suitable for agricultural and certain food processing applications.
Considerations for International Buyers: Buyers should check for compliance with food safety standards, especially in regions like Europe where regulations are stringent. Understanding local recycling regulations can also influence material choice.
What Are the Benefits of Using Ceramic in Mixers?
Key Properties: Ceramics are known for their hardness, wear resistance, and ability to withstand high temperatures. They are also chemically inert, making them suitable for aggressive media.
Pros & Cons: The key advantage of ceramics is their durability in harsh environments. However, they can be brittle and may not withstand impact, which can be a limitation in certain applications.
Impact on Application: Ceramics are particularly effective in applications involving abrasive materials, such as in the mining or pharmaceutical industries.
Considerations for International Buyers: Buyers should ensure that ceramic components meet relevant international standards, particularly in regions with strict quality controls like Europe.
Summary Table of Mixer Materials
Material | Typical Use Case for types of mixers | Key Advantage | Key Disadvantage/Limitation | Relative Cost (Low/Med/High) |
---|---|---|---|---|
Stainless Steel | Food processing, pharmaceuticals | High durability and corrosion resistance | Higher cost and complex manufacturing | High |
Carbon Steel | Dry mixing applications | Cost-effective | Prone to rust and corrosion | Medium |
Plastic | Agricultural and non-corrosive liquids | Lightweight and affordable | Limited temperature and pressure tolerance | Low |
Ceramic | Abrasive materials in mining/pharma | High wear resistance | Brittle and impact-sensitive | Medium |
This strategic material selection guide provides B2B buyers with essential insights into the materials used in mixers, helping them make informed decisions tailored to their specific operational needs and regional compliance requirements.
In-depth Look: Manufacturing Processes and Quality Assurance for types of mixers
What Are the Main Stages in the Manufacturing Process of Mixers?
The manufacturing process of mixers involves several critical stages that ensure the final product meets quality standards and functions effectively in industrial applications. Understanding these stages can help B2B buyers make informed decisions when selecting suppliers.
Material Preparation: What Materials Are Used for Mixers?
The first step in the manufacturing process is material preparation, where raw materials are selected based on the type of mixer being produced. Common materials include stainless steel, which is favored for its durability and resistance to corrosion, especially in food and pharmaceutical applications. Other materials like high-density polyethylene (HDPE) are used for specific applications requiring lightweight and chemical-resistant properties.
During this stage, raw materials undergo quality checks to ensure they meet specifications. Buyers should inquire about the supplier’s sourcing practices and whether they comply with international standards for material quality.
Forming: How Are Mixer Components Shaped?
Once materials are prepared, they undergo forming, which involves shaping the components of the mixer. This can be achieved through various techniques such as machining, welding, and molding. For example, stainless steel parts may be cut and welded to form the body of the mixer, while plastic components might be injection molded.
Advanced technologies like CNC machining are often employed for precision and consistency. B2B buyers should assess whether suppliers utilize state-of-the-art machinery and skilled labor, as these factors can significantly impact the quality of the final product.
Assembly: What Is the Assembly Process for Mixers?
The assembly stage involves bringing together all the formed components into a cohesive unit. This includes installing motors, gearboxes, and other mechanical parts. For complex mixers, such as high shear mixers, precise assembly is crucial to ensure optimal performance.
During assembly, manufacturers often conduct in-process quality checks (IPQC) to identify any defects early in the production process. Buyers should verify that suppliers have a robust assembly process in place, including clear documentation of assembly procedures.
Finishing: How Is the Final Product Prepared for Delivery?
Finishing involves surface treatments, painting, or coating to enhance the durability and appearance of the mixer. This stage may also include cleaning and polishing to ensure that the mixer is ready for use, particularly in industries where hygiene is paramount, such as food processing.
Quality control checks are conducted during this stage as well, focusing on the aesthetic and functional aspects of the mixer. Buyers should inquire about the finishing techniques employed by suppliers, as these can influence the longevity and performance of the mixers.
What Quality Assurance Practices Should B2B Buyers Look For?
Quality assurance (QA) is critical in the manufacturing of mixers, ensuring that the end product meets both international and industry-specific standards. For B2B buyers, understanding these QA practices can help mitigate risks associated with purchasing equipment.
Which International Standards Are Relevant for Mixer Manufacturing?
International standards such as ISO 9001 play a vital role in ensuring quality management systems are in place. ISO 9001 certifies that manufacturers have documented processes for quality control, which can lead to improved customer satisfaction and reduced operational risks.
In addition to ISO standards, industry-specific certifications like CE marking for European markets, or API (American Petroleum Institute) standards for the oil and gas industry, should also be considered. These certifications indicate that the mixers have been tested and comply with safety and performance requirements.
What Are the Key Quality Control Checkpoints in Mixer Manufacturing?
Quality control in mixer manufacturing involves several key checkpoints, including:
- Incoming Quality Control (IQC): This involves inspecting raw materials upon arrival to ensure they meet specified standards.
- In-Process Quality Control (IPQC): Conducted during the manufacturing process to catch defects early, minimizing waste and rework.
- Final Quality Control (FQC): A comprehensive inspection of the finished product to ensure it meets all specifications before shipping.
B2B buyers should ask suppliers about their QC checkpoints and how they document results at each stage.
How Can Buyers Verify Supplier Quality Control Practices?
Verifying a supplier’s quality control practices is essential for international B2B buyers. Here are actionable steps to ensure the reliability of a supplier’s QC processes:
What Are Effective Methods for Supplier Audits and Inspections?
Conducting supplier audits can provide firsthand insight into their manufacturing processes and quality assurance practices. Buyers should look for opportunities to perform on-site inspections, which can help assess the supplier’s adherence to standards and their operational capabilities.
Third-party inspections can also be beneficial, especially when dealing with suppliers in regions where buyers may have limited access. Engage with reputable inspection agencies to verify compliance with international standards and ensure that the equipment meets the specified requirements.
How Can Buyers Utilize Reports and Certifications?
Buyers should request comprehensive reports from suppliers that detail their quality control processes, including test results and certifications. Understanding the nuances of these documents, such as the scope of certifications and any deviations from standards, can help buyers make informed decisions.
Additionally, maintaining a database of suppliers and their certifications can aid in evaluating potential partners based on quality performance over time. This proactive approach can enhance supply chain reliability and mitigate risks associated with equipment failures.
What Are the Quality Control Nuances for International Buyers?
For international B2B buyers, particularly those from Africa, South America, the Middle East, and Europe, there are unique quality control nuances to consider.
How Do Regional Regulations Impact Quality Assurance?
Different regions may have specific regulations that affect the manufacturing and quality assurance processes of mixers. Buyers should familiarize themselves with local standards, such as those set by the South African Bureau of Standards (SABS) or the Brazilian National Institute of Metrology, Quality and Technology (INMETRO).
Understanding these regulations can help buyers ensure that the mixers they purchase will be compliant with local laws, thereby avoiding potential legal issues or fines.
What Should Buyers Know About Cultural and Communication Differences?
Cultural differences can influence manufacturing practices and quality perceptions. Buyers should establish clear communication channels with suppliers to discuss quality expectations and any specific requirements unique to their markets.
Utilizing local representatives or consultants familiar with the regional landscape can also facilitate better understanding and strengthen supplier relationships, ultimately leading to improved quality assurance outcomes.
By focusing on these manufacturing processes and quality assurance practices, B2B buyers can enhance their procurement strategies and ensure they invest in reliable, high-quality mixers tailored to their specific industry needs.
Practical Sourcing Guide: A Step-by-Step Checklist for ‘types of mixers’
Introduction
Sourcing the right type of mixer is critical for businesses looking to enhance their production processes, particularly in industries such as food and beverage, pharmaceuticals, and chemicals. This practical checklist will guide international B2B buyers through the essential steps to ensure they select mixers that meet their operational needs while optimizing efficiency and cost-effectiveness.
Step 1: Define Your Mixing Requirements
Start by clearly outlining your specific mixing needs. Consider the types of materials you will be mixing—liquids, solids, or a combination—and their respective viscosities. Understanding your requirements will help you determine the appropriate mixer type, such as high shear mixers for emulsification or agitators for liquid blending.
Step 2: Research Mixer Types and Applications
Familiarize yourself with the various types of mixers available in the market. Each type, such as drum mixers, homogenizers, and emulsifiers, has distinct applications and capabilities. Researching these options will enable you to select a mixer that aligns with your production goals and industry standards.
Step 3: Evaluate Potential Suppliers
Before making a purchase, thoroughly vet potential suppliers. Request detailed company profiles, product catalogs, and references from other businesses in your industry or region. This step is crucial to ensure that the supplier has a solid reputation and provides reliable products that meet your quality standards.
- Look for certifications: Verify if suppliers have relevant industry certifications, which can indicate adherence to quality and safety standards.
- Check for experience: Consider suppliers with proven experience in your specific industry to ensure they understand your unique challenges and requirements.
Step 4: Assess Technical Specifications
Once you’ve narrowed down potential mixers, evaluate their technical specifications. Pay attention to factors such as power requirements, mixing capacity, and speed settings. These specifications will impact your production efficiency and overall operational costs.
- Consider energy efficiency: Opt for mixers that offer energy-efficient features to reduce operational costs over time.
- Ensure compatibility: Confirm that the mixer can handle the materials you intend to process without compromising performance.
Step 5: Request Demonstrations or Trials
If possible, request a demonstration or trial of the mixer. This hands-on experience will help you gauge its performance, usability, and suitability for your production environment. It also provides an opportunity to ask questions and clarify any concerns regarding the equipment.
Step 6: Review After-Sales Support and Warranty Options
Inquire about the after-sales support that suppliers offer, including maintenance services and availability of spare parts. A solid support plan can minimize downtime and ensure your mixer operates efficiently over its lifespan.
- Warranty coverage: Evaluate the warranty terms to understand what is covered and for how long, as this can significantly impact your total cost of ownership.
Step 7: Compare Pricing and Total Cost of Ownership
Finally, compare pricing among different suppliers while considering the total cost of ownership. This includes initial purchase price, operating costs, and potential maintenance expenses. A lower upfront cost may not always equate to savings in the long run if the equipment requires frequent repairs or uses excessive energy.
By following this checklist, B2B buyers can make informed decisions when sourcing mixers, ensuring they choose equipment that meets their operational needs while maximizing efficiency and value.
Comprehensive Cost and Pricing Analysis for types of mixers Sourcing
What Are the Key Cost Components in Sourcing Different Types of Mixers?
When sourcing mixers, understanding the cost structure is essential for international B2B buyers. The primary cost components include:
-
Materials: The choice of materials significantly impacts the price. For example, stainless steel mixers, which are preferred for their durability and hygiene, typically cost more than those made from plastic. The quality of materials used in construction directly correlates with the mixer’s lifespan and performance.
-
Labor: Labor costs vary by region and can influence the overall pricing. In countries with higher wage standards, such as those in Europe, labor costs will be a significant factor. Conversely, regions with lower labor costs may offer competitive pricing, but this can sometimes come at the expense of quality.
-
Manufacturing Overhead: This includes costs associated with running the manufacturing facility, such as utilities and equipment maintenance. A well-optimized facility can reduce overhead, leading to more competitive pricing for buyers.
-
Tooling: Custom tooling for specialized mixers can add to the cost. Buyers should consider whether off-the-shelf solutions meet their needs or if they require custom designs, which can significantly increase initial costs.
-
Quality Control (QC): The rigor of quality control processes influences both the cost and reliability of the mixers. Suppliers that implement stringent QC measures may charge higher prices, but this often results in better long-term performance and fewer operational disruptions.
-
Logistics: Shipping costs and delivery times vary significantly across regions. Buyers from Africa and South America may face higher logistics costs due to limited local suppliers or longer shipping distances from manufacturing hubs.
-
Margin: Supplier margins can vary widely based on market demand and competition. Understanding the average margins in the industry can help buyers negotiate better deals.
How Do Price Influencers Affect Mixer Sourcing?
Several factors influence pricing when sourcing mixers:
-
Volume/MOQ (Minimum Order Quantity): Ordering in bulk can lead to significant savings. Suppliers often provide discounts for larger orders, making it crucial for buyers to assess their needs against potential cost savings.
-
Specifications and Customization: Customized mixers that meet specific operational requirements typically command higher prices. Buyers should weigh the benefits of customization against their budget constraints.
-
Materials: The choice of materials not only affects the initial cost but also influences the total cost of ownership (TCO). For instance, mixers made with corrosion-resistant materials may have higher upfront costs but offer lower maintenance expenses over time.
-
Quality and Certifications: Mixers that meet international quality standards and certifications may come at a premium. However, investing in certified equipment can enhance operational reliability and reduce the risk of compliance issues.
-
Supplier Factors: The reputation and reliability of the supplier can impact pricing. Established suppliers with proven track records may charge more, but they often provide better support and warranty options.
-
Incoterms: Understanding the terms of sale (Incoterms) is crucial for international buyers. These terms define responsibilities regarding shipping, insurance, and tariffs, all of which can affect the final cost.
What Are Effective Buyer Tips for Negotiating Mixer Prices?
For international B2B buyers, particularly from Africa, South America, the Middle East, and Europe, effective negotiation strategies can lead to significant savings:
-
Leverage Total Cost of Ownership (TCO): Focus on the long-term costs associated with the mixer, including maintenance, energy consumption, and potential downtime. This approach can justify a higher initial investment if it leads to lower overall costs.
-
Research and Compare Suppliers: Always compare multiple suppliers to understand market prices. This data can be leveraged during negotiations to secure better terms.
-
Build Relationships: Establishing strong relationships with suppliers can lead to better pricing, especially for repeat orders. Suppliers are often more willing to negotiate with partners they trust.
-
Be Clear on Requirements: Clearly define your needs and specifications before engaging suppliers. This clarity can lead to more accurate quotes and reduce the likelihood of unexpected costs.
-
Consider Local Suppliers: For buyers in emerging markets, sourcing from local manufacturers may reduce logistics costs and lead to faster delivery times, even if the initial price is slightly higher.
Disclaimer on Indicative Prices
Prices for mixers can vary widely based on multiple factors, including specifications, supplier location, and market conditions. It is advisable for buyers to request quotes from multiple suppliers and consider all cost components before making a purchasing decision.
Alternatives Analysis: Comparing types of mixers With Other Solutions
Understanding Alternatives to Traditional Mixers
When evaluating the best mixing solutions for industrial applications, it’s essential to consider alternatives to traditional types of mixers. While mixers are versatile and widely used, there are other technologies and methods that can achieve similar results in blending, emulsifying, and homogenizing materials. This analysis aims to provide B2B buyers with insights into how various mixing solutions compare to traditional mixers in terms of performance, cost, ease of implementation, maintenance, and best use cases.
Comparison Aspect | Types Of Mixers | Alternative 1: Agitators | Alternative 2: Homogenizers |
---|---|---|---|
Performance | High efficiency in blending various materials; suitable for both liquid and solid mixtures. | Effective for liquid-liquid and liquid-gas mixing; less effective for very viscous substances. | Excels in achieving uniform mixtures, especially for emulsions and high-viscosity products. |
Cost | Moderate to high initial investment, depending on the type and capacity. | Generally lower cost; requires less complex technology. | Higher cost due to advanced technology and capabilities. |
Ease of Implementation | Requires careful setup and calibration; training may be needed for operators. | Relatively straightforward to install and operate; minimal training required. | More complex to set up; may require specialized training for operators. |
Maintenance | Regular maintenance needed to ensure optimal performance; some parts may require replacement. | Lower maintenance demands; simpler components lead to less wear and tear. | Higher maintenance requirements due to complex mechanics and potential wear on parts. |
Best Use Case | Ideal for diverse industries including food, pharmaceuticals, and chemicals. | Best suited for applications involving mixing miscible liquids or gas into liquids. | Perfect for products requiring emulsification and consistency, such as creams and sauces. |
Pros and Cons of Alternatives to Traditional Mixers
What Are the Advantages and Disadvantages of Using Agitators?
Agitators are a popular alternative for mixing liquids, particularly in industries like food and beverage processing. Their primary advantage lies in their simplicity and lower cost compared to traditional mixers. They can efficiently blend miscible liquids and even introduce gases into liquids. However, agitators struggle with high-viscosity materials and may not achieve the same level of homogeneity that mixers can provide. This makes them less suitable for applications requiring precise emulsification or uniformity.
How Do Homogenizers Compare to Traditional Mixers?
Homogenizers are another viable alternative, particularly for creating emulsions and achieving a consistent product texture. They apply high pressure and shear forces to break down particles, making them ideal for applications in the dairy, cosmetic, and pharmaceutical industries. While they deliver superior performance in terms of product consistency, they come at a higher cost and require more complex maintenance. Additionally, their setup can be more involved, necessitating specialized knowledge for effective operation.
How Should B2B Buyers Choose the Right Mixing Solution?
When selecting the appropriate mixing solution, B2B buyers should assess their specific operational needs and constraints. Factors such as the nature of the materials being mixed, desired consistency, production volume, and budget play crucial roles in the decision-making process. For instance, if the primary requirement is to mix liquids efficiently, agitators may suffice. Conversely, if the goal is to achieve a high-quality emulsion or consistent product, investing in a homogenizer or a specific type of mixer might be more advantageous. Ultimately, understanding the strengths and limitations of each option will empower buyers to make informed decisions that align with their production goals and operational efficiency.
Essential Technical Properties and Trade Terminology for types of mixers
What Are the Essential Technical Properties of Mixers for International B2B Buyers?
Understanding the technical properties of mixers is crucial for B2B buyers, especially in regions like Africa, South America, the Middle East, and Europe. Here are some critical specifications that impact the efficiency, durability, and suitability of mixers for various applications:
-
Material Grade
The material used in the construction of mixers, such as stainless steel or food-grade plastics, significantly affects durability and compliance with industry standards. For instance, stainless steel is preferred in food and pharmaceutical applications due to its resistance to corrosion and ease of cleaning. B2B buyers should prioritize mixers made from high-grade materials to ensure longevity and safety. -
Power Rating (Horsepower)
The power rating indicates the mixer’s capacity to handle different viscosities and volumes. Higher horsepower ratings enable the mixer to process thicker substances or larger batches efficiently. Buyers must assess their production needs to select a mixer with an appropriate power rating, ensuring optimal performance and return on investment. -
Mixing Capacity (Batch Size)
This specification refers to the maximum volume that a mixer can handle in one operation. Understanding the mixing capacity is vital for B2B buyers to ensure that the equipment meets their production demands. Inadequate capacity can lead to inefficiencies and increased operational costs, while oversized mixers can lead to unnecessary expenses. -
Speed Range (RPM)
The revolutions per minute (RPM) of a mixer affects the mixing action and efficiency. Different materials require different mixing speeds; for example, high shear mixers operate at higher RPMs to achieve emulsification. Buyers should evaluate the speed range to ensure that the mixer can accommodate their specific application requirements. -
Tolerance Levels
Tolerance refers to the allowable deviation from specified dimensions in mixer components. High tolerance levels are crucial in applications where precision is paramount, such as in pharmaceuticals and food processing. B2B buyers should inquire about tolerance specifications to ensure that the mixer will produce consistent and accurate results. -
Temperature Control Capabilities
Some mixing processes require precise temperature management to ensure quality. Mixers with built-in temperature control can heat or cool mixtures as needed, which is vital in applications like emulsification or chemical reactions. Buyers must consider whether temperature control is necessary for their processes.
Which Trade Terms Are Important for B2B Buyers of Mixers?
Familiarity with industry jargon is essential for effective communication and negotiation in B2B transactions. Here are some common trade terms relevant to the purchasing of mixers:
-
OEM (Original Equipment Manufacturer)
This term refers to companies that produce components or equipment that may be marketed by another company under its brand name. B2B buyers should verify whether they are purchasing from an OEM to ensure quality and authenticity. -
MOQ (Minimum Order Quantity)
MOQ indicates the smallest quantity of a product that a supplier is willing to sell. Understanding MOQ is crucial for buyers to manage inventory costs effectively and ensure that their orders align with their production schedules. -
RFQ (Request for Quotation)
An RFQ is a document sent to suppliers requesting pricing and terms for specific products. This process is essential for buyers to obtain competitive pricing and detailed information about the mixers they are considering. -
Incoterms (International Commercial Terms)
These are standardized trade terms used in international sales contracts that define the responsibilities of buyers and sellers regarding shipping, insurance, and tariffs. Familiarity with Incoterms is crucial for B2B buyers to understand their obligations and manage logistics effectively. -
Lead Time
Lead time refers to the period between placing an order and receiving it. Understanding lead times is essential for buyers to plan their production schedules and inventory management efficiently. -
Warranty and After-Sales Support
Warranty terms specify the duration and coverage of repairs and replacements for the mixer. After-sales support is crucial for maintenance and troubleshooting. B2B buyers should inquire about these aspects to ensure they receive comprehensive support for their investment.
By understanding these essential technical properties and trade terminologies, international B2B buyers can make informed decisions that align with their operational needs and strategic goals.
Navigating Market Dynamics and Sourcing Trends in the types of mixers Sector
What Are the Current Market Dynamics and Key Trends in the Types of Mixers Sector?
The global market for industrial mixers is witnessing robust growth, driven by various factors including increased demand for processed foods, pharmaceuticals, and chemicals. As of 2023, the market is expected to expand significantly in regions like Africa, South America, the Middle East, and Europe. International B2B buyers are increasingly looking for efficient mixing solutions that can handle diverse materials, from viscous liquids to powders.
Technological advancements are shaping the sourcing trends in this sector. Automation and the integration of smart technology are becoming essential, allowing for better control and monitoring of mixing processes. For instance, high shear mixers and homogenizers equipped with IoT capabilities enable real-time data analysis, enhancing operational efficiency and product quality. Additionally, the rise of e-commerce platforms is facilitating easier access to various types of mixers, enabling buyers to compare features, prices, and supplier credentials from different regions.
Emerging markets, particularly in Africa and South America, are focusing on local manufacturing capabilities to reduce dependency on imports. This shift not only fosters regional economic growth but also encourages the development of customized mixing solutions tailored to local industry needs. Moreover, as companies increasingly prioritize sustainability, there is a growing demand for mixers made from eco-friendly materials, aligning with global trends towards greener manufacturing practices.
How Is Sustainability and Ethical Sourcing Impacting the Types of Mixers Industry?
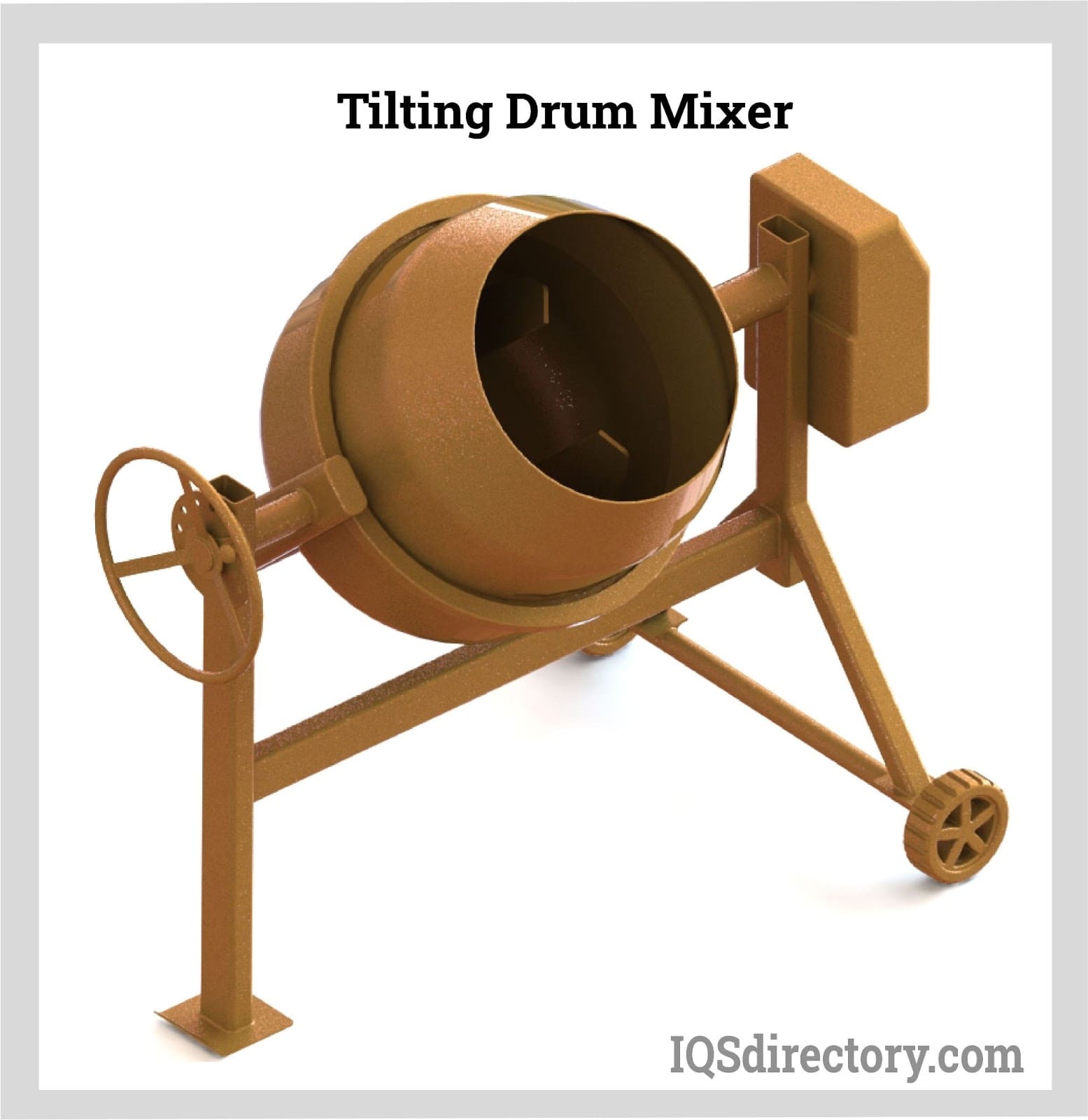
A stock image related to types of mixers.
Sustainability has become a critical focus for international B2B buyers in the types of mixers sector. The environmental impact of manufacturing processes, including energy consumption and waste generation, is under scrutiny. Buyers are increasingly prioritizing suppliers who adopt sustainable practices, such as utilizing energy-efficient machinery and reducing water usage in production.
Ethical sourcing is equally important, as businesses seek to ensure that their supply chains are free from exploitative practices. This includes verifying that raw materials for mixers, such as stainless steel and plastics, are sourced responsibly. Certifications like ISO 14001 for environmental management and Fair Trade certification are becoming key indicators for buyers assessing supplier integrity.
Furthermore, the use of ‘green’ materials in manufacturing mixers is gaining traction. For example, mixers made from recycled materials or biodegradable components not only appeal to environmentally conscious buyers but can also enhance brand reputation. As regulations around environmental compliance tighten, buyers must consider the sustainability credentials of their suppliers to mitigate risks and align with consumer expectations.
How Have Types of Mixers Evolved Over Time?
The evolution of mixers can be traced back to early manual methods of blending substances, which gradually transitioned to mechanical solutions with the advent of the Industrial Revolution. The introduction of powered mixers revolutionized the industry, enabling large-scale production and consistent quality. Over the decades, technological advancements have led to the development of specialized mixers, including high shear mixers and emulsifiers, catering to specific industrial needs.
Today, the focus is on efficiency, precision, and sustainability, with innovations such as smart mixers that incorporate automation and data analytics. This evolution reflects a broader trend towards optimizing manufacturing processes to meet the demands of a competitive global market. B2B buyers are now faced with a plethora of options, allowing them to select mixers that not only meet their technical requirements but also align with their sustainability goals.
Frequently Asked Questions (FAQs) for B2B Buyers of types of mixers
-
How do I choose the right type of mixer for my application?
Choosing the right mixer hinges on several factors including the materials you need to process, the desired consistency of the final product, and the scale of production. For instance, high shear mixers are ideal for emulsifying and dispersing liquids, while ribbon blenders excel in bulk powder mixing. Assess the viscosity of your materials, production volume, and whether you require batch or continuous mixing. Engaging with suppliers who understand your industry can also provide valuable insights and recommendations tailored to your specific needs. -
What is the best mixer for emulsifying liquids?
For emulsifying liquids, a high shear mixer or an emulsifier is often the best choice. High shear mixers utilize rotor-stator mechanisms to create intense shear forces, breaking down droplets and achieving a homogeneous blend. Emulsifiers are particularly effective for mixing immiscible liquids, such as oil and water, often used in cosmetic and food industries. Evaluate your specific emulsification needs, including batch size and processing time, to determine the most suitable equipment. -
What should I consider when vetting suppliers for mixers?
When vetting suppliers, prioritize their industry experience, product range, and customer reviews. Check for certifications and compliance with international standards, especially if you are sourcing from regions with different regulatory requirements. Request references and case studies to understand their capabilities and reliability. Additionally, inquire about after-sales support, warranty terms, and their ability to provide customized solutions for your unique mixing challenges. -
What are the typical minimum order quantities (MOQs) for industrial mixers?
Minimum order quantities (MOQs) can vary significantly based on the supplier and the type of mixer. Generally, MOQs may range from a single unit for standard models to several units for custom-built mixers. Discuss your production needs with the supplier to negotiate favorable terms. Understanding your budget and timelines will help you make informed decisions and potentially secure better pricing or terms for bulk orders. -
What payment terms should I expect when purchasing mixers internationally?
Payment terms for international purchases typically vary by supplier and may include options like advance payment, letters of credit, or payment upon delivery. Common practices involve a deposit upfront, followed by the balance upon shipping or delivery. It’s essential to clarify payment methods, currency, and any applicable taxes or duties. Ensure you have a clear agreement to protect your interests, especially when dealing with overseas suppliers.
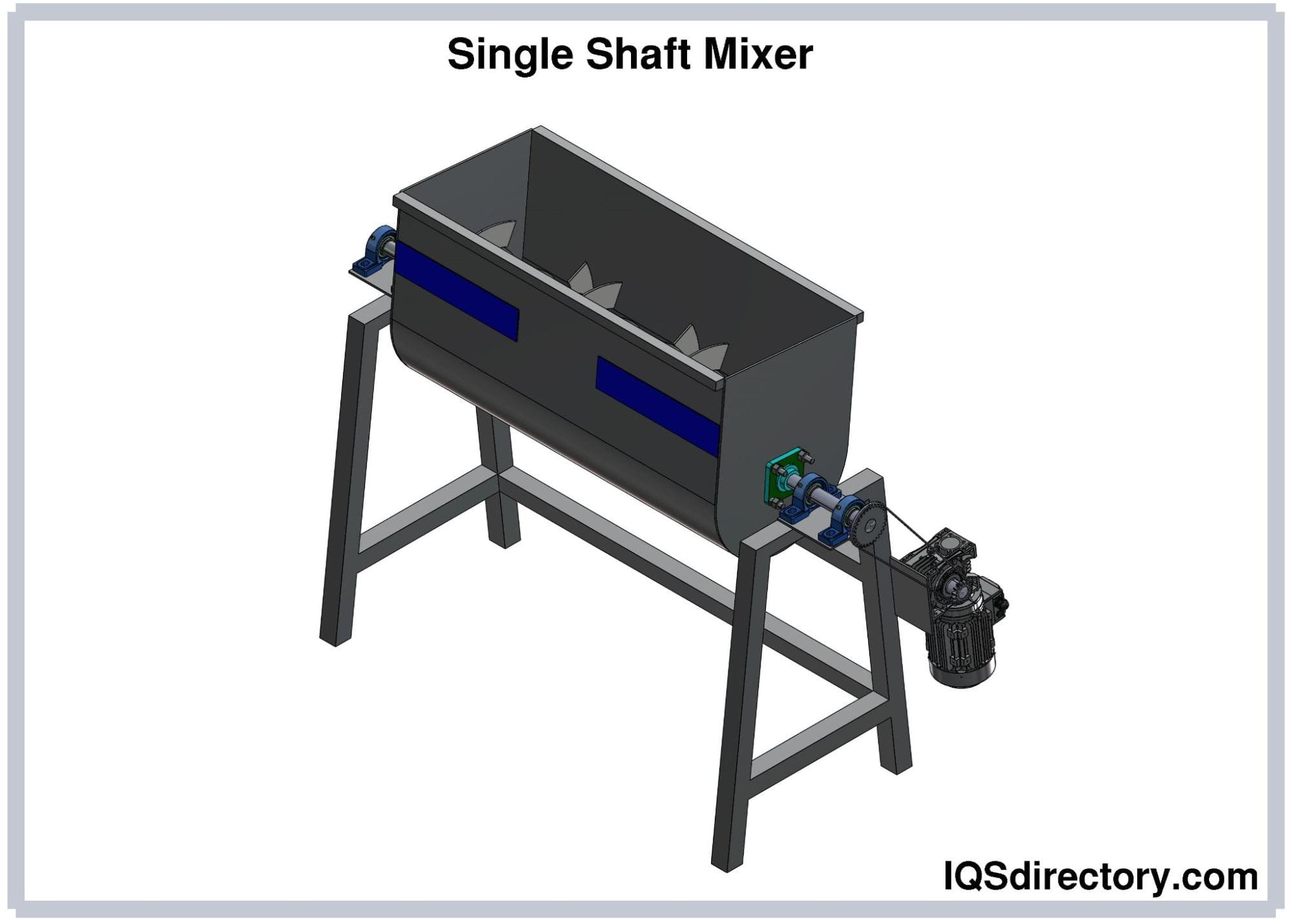
A stock image related to types of mixers.
-
How can I ensure quality assurance (QA) for the mixers I purchase?
To ensure quality assurance, request detailed product specifications, test certificates, and compliance with relevant industry standards. Many reputable suppliers will offer a QA process, which includes pre-shipment inspections and testing of mixers before delivery. Establish clear quality benchmarks and testing protocols that the equipment must meet. Additionally, consider a warranty or service agreement that covers maintenance and repairs to safeguard your investment. -
What logistics considerations should I be aware of when importing mixers?
Logistics considerations include shipping methods, customs clearance, and delivery timelines. Choose a reliable freight forwarder familiar with importing machinery to navigate potential challenges such as tariffs and documentation requirements. Factor in lead times for production and shipping, especially if sourcing from different continents. Ensure that the supplier provides necessary shipping documents, such as invoices and packing lists, to facilitate a smooth import process. -
How do I assess the total cost of ownership (TCO) for a mixer?
Assessing the total cost of ownership (TCO) involves evaluating not just the initial purchase price but also maintenance costs, energy consumption, and potential downtime during operation. Consider the efficiency of the mixer and its capacity to meet your production demands without frequent breakdowns. Additionally, factor in the cost of spare parts and any necessary training for operators. A thorough TCO analysis can help you make a more informed investment decision that aligns with your long-term operational goals.
Important Disclaimer & Terms of Use
⚠️ Important Disclaimer
The information provided in this guide, including content regarding manufacturers, technical specifications, and market analysis, is for informational and educational purposes only. It does not constitute professional procurement advice, financial advice, or legal advice.
While we have made every effort to ensure the accuracy and timeliness of the information, we are not responsible for any errors, omissions, or outdated information. Market conditions, company details, and technical standards are subject to change.
B2B buyers must conduct their own independent and thorough due diligence before making any purchasing decisions. This includes contacting suppliers directly, verifying certifications, requesting samples, and seeking professional consultation. The risk of relying on any information in this guide is borne solely by the reader.
Strategic Sourcing Conclusion and Outlook for types of mixers
In summary, understanding the diverse types of mixers and their applications is crucial for international B2B buyers seeking to optimize their production processes. Whether you are in the food, pharmaceutical, or chemical industry, selecting the right mixer—be it agitators, emulsifiers, or industrial blenders—can significantly enhance efficiency, product quality, and cost-effectiveness.
Strategic sourcing plays a pivotal role in this decision-making process. By leveraging supplier relationships, conducting thorough market research, and evaluating technological advancements, buyers can secure mixers that not only meet current operational needs but also future-proof their investments against evolving industry standards.
As we look ahead, the demand for innovative mixing solutions will continue to rise, particularly across emerging markets in Africa, South America, the Middle East, and Europe. It is essential for buyers to stay informed about the latest trends and technologies in mixer design and functionality. By doing so, businesses can position themselves advantageously in a competitive landscape.
Take action now: evaluate your mixing requirements and explore strategic partnerships with reputable suppliers to ensure your operations remain at the forefront of efficiency and quality.