Discover the Best Types of Power Cords for Your Business (2025)
Introduction: Navigating the Global Market for types of power cords
In today’s interconnected world, sourcing the right types of power cords presents a significant challenge for international B2B buyers. With the diverse array of standards and specifications across various regions—including Africa, South America, the Middle East, and Europe—understanding the nuances of power cord compatibility is essential. This guide offers a comprehensive overview of power cord types, their applications, and the critical factors to consider when selecting suppliers.
From the IEC 60320 standard prevalent in many countries to the specific plug types like NEMA in North America and CEE 7/7 in Europe, navigating these options can be daunting. Buyers will gain insights into the advantages and limitations of different cord types, enabling them to make informed decisions that align with their operational needs.
Moreover, this guide addresses supplier vetting processes, cost considerations, and safety standards to ensure that buyers are equipped to choose reliable and compliant power cords. By empowering international B2B buyers with actionable insights, this resource aims to streamline the purchasing process, ultimately enhancing operational efficiency and reducing the risk of compatibility issues. Whether you are based in Egypt or Spain, understanding the global market for power cords is crucial for successful procurement strategies.
Understanding types of power cords Types and Variations
Type Name | Key Distinguishing Features | Primary B2B Applications | Brief Pros & Cons for Buyers |
---|---|---|---|
IEC 60320 | International standard for appliance connectors; includes types C13, C14, C15, C19 | Data centers, IT equipment, and industrial appliances | Pros: Universal compatibility; Cons: May require adapters in certain regions. |
NEMA Connectors | Standardized plugs and sockets primarily in North America; NEMA 5-15 is most common | Electronics, appliances, and industrial machinery in North America | Pros: Widely available; Cons: Limited to North American use. |
CEE 7/7 | Commonly used in Europe; accommodates multiple plug types (Type E, Type F) | Commercial and residential electrical appliances in Europe | Pros: Versatile; Cons: May not be compatible outside Europe. |
AS/NZS 3112 | Australian and New Zealand standard; Type I connector design | Electrical appliances and machinery in Australia and New Zealand | Pros: Reliable for local use; Cons: Not suitable for international devices. |
JIS C 8303 | Japanese standard with Type A and B connectors; specific to Japan | Consumer electronics and household appliances in Japan | Pros: Optimized for local devices; Cons: Limited international compatibility. |
What Are the Key Characteristics of IEC 60320 Power Cords?
IEC 60320 power cords are designed to connect appliances to a mains power supply, featuring a variety of connector types, such as C13 and C19. These connectors are prevalent in data centers and IT environments, making them essential for businesses that rely on standardized equipment. When purchasing IEC 60320 cords, B2B buyers should consider compatibility with existing infrastructure and the potential need for adapters when operating in regions with different plug standards.
How Do NEMA Connectors Serve North American Markets?
NEMA connectors, particularly the NEMA 5-15, dominate the North American market. These plugs are designed for general-purpose use, providing a reliable connection for a wide range of appliances and industrial equipment. For businesses operating in or exporting to North America, understanding NEMA standards is crucial. Buyers should evaluate the power requirements of their equipment to ensure they select the appropriate NEMA configuration.
Why Are CEE 7/7 Power Cords Important for European Buyers?
The CEE 7/7 standard is the go-to choice for many European countries, supporting various plug types. This flexibility is advantageous for businesses that operate in multiple European markets. When sourcing CEE 7/7 power cords, B2B buyers should assess their specific regional needs and ensure that the cords can accommodate varying voltage and current requirements across different countries.
What Should Buyers Know About AS/NZS 3112 Power Cords?
The AS/NZS 3112 standard governs power cords in Australia and New Zealand, featuring the Type I connector. These cords are tailored for local electrical systems and are critical for businesses operating in these regions. When purchasing AS/NZS 3112 cords, buyers should confirm compliance with local regulations and consider the durability of the cords for industrial applications.
How Do JIS C 8303 Power Cords Benefit Japanese Businesses?
JIS C 8303 power cords, including Types A and B, are specifically designed for the Japanese market. They are integral to consumer electronics and household appliances. B2B buyers in Japan should focus on sourcing cords that meet JIS standards to ensure compatibility and safety. Additionally, understanding the specific voltage and current ratings is vital for optimal performance in local applications.
Key Industrial Applications of types of power cords
Industry/Sector | Specific Application of Types of Power Cords | Value/Benefit for the Business | Key Sourcing Considerations for this Application |
---|---|---|---|
Data Centers | Connecting servers and networking equipment | Ensures reliable power supply for critical operations | Compliance with IEC standards, voltage ratings, and length |
Healthcare Facilities | Powering medical devices and equipment | Enhances patient safety and operational efficiency | Hospital-grade certifications, durability, and flexibility |
Manufacturing | Supply power to machinery and industrial equipment | Improves productivity and reduces downtime | Compatibility with local standards and environmental ratings |
Telecommunications | Powering communication devices and infrastructure | Supports uninterrupted service and connectivity | Consideration of cable lengths and environmental conditions |
Retail and Commercial | Connecting point-of-sale systems and digital displays | Facilitates smooth transactions and customer engagement | Aesthetic design and compliance with local electrical codes |
How Are Types of Power Cords Used in Data Centers?
In data centers, various types of power cords, particularly IEC 60320 connectors such as C13 and C19, are crucial for connecting servers, storage devices, and networking equipment. These power cords ensure a stable and reliable power supply, which is vital for maintaining uptime and operational efficiency. International B2B buyers should prioritize sourcing cords that comply with IEC standards to ensure compatibility with local power systems. Additionally, considering the length and gauge of the cords can help prevent overheating and ensure optimal performance.
What Are the Key Applications of Power Cords in Healthcare Facilities?
Healthcare facilities rely heavily on specialized power cords to connect medical devices such as imaging machines, patient monitors, and surgical equipment. These power cords must meet stringent safety standards, including hospital-grade certifications, to mitigate risks and enhance patient safety. Buyers in this sector should consider sourcing cords that offer durability and flexibility, allowing for easy maneuverability in crowded environments. Furthermore, ensuring that the cords are compliant with local regulations is critical for operational efficiency.
How Do Power Cords Benefit Manufacturing Operations?
In manufacturing, power cords are essential for supplying electricity to machinery, robotics, and assembly lines. Reliable power connections directly impact productivity and minimize downtime, making it essential for manufacturers to choose high-quality power cords that can withstand the rigors of industrial environments. International buyers should focus on sourcing cords that are compatible with local electrical standards and rated for the specific voltage and current requirements of their equipment. Environmental ratings are also important to ensure longevity and performance in challenging conditions.
Why Are Power Cords Important in Telecommunications?
Telecommunications infrastructure, including routers, switches, and cellular towers, relies on specific types of power cords for uninterrupted service. Power cords must be sourced with consideration for cable lengths and environmental durability to withstand outdoor conditions. For B2B buyers in this sector, ensuring that power cords meet local and international standards is crucial for maintaining service reliability and quality. Additionally, investing in surge protection features can safeguard equipment against power fluctuations.
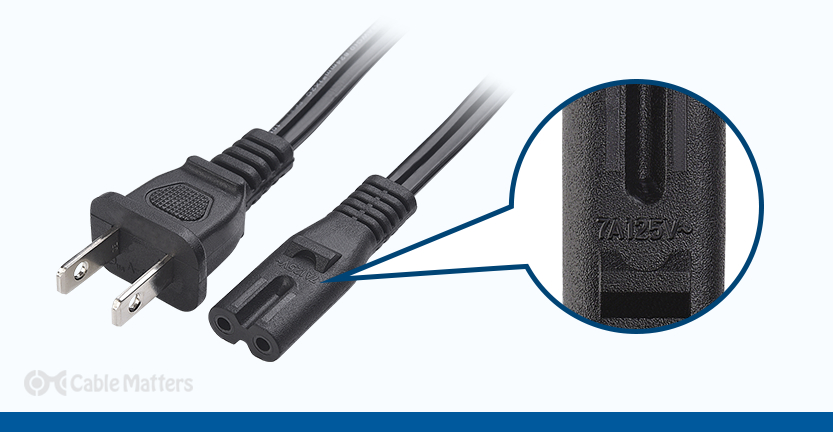
A stock image related to types of power cords.
What Role Do Power Cords Play in Retail and Commercial Settings?
In retail environments, power cords are vital for connecting point-of-sale systems, digital displays, and other electronic devices. The aesthetic design of these power cords can enhance the customer experience while ensuring functionality. B2B buyers should prioritize sourcing cords that comply with local electrical codes and standards to avoid potential liabilities. Additionally, ensuring that power cords are durable and flexible can facilitate quick setup and adjustments in dynamic retail settings, ultimately improving operational efficiency.
3 Common User Pain Points for ‘types of power cords’ & Their Solutions
Scenario 1: Navigating Different Power Plug Standards Across Regions
The Problem: International B2B buyers often face confusion due to the multitude of power plug standards and types in different regions. For instance, a company in Egypt may import equipment designed for European CEE 7/7 plugs, only to find that their local sockets are incompatible. This can lead to costly delays in equipment deployment, disrupt operations, and result in additional expenses for adapters or replacement cords that meet local standards.
The Solution: To effectively navigate this issue, B2B buyers should conduct thorough research on the power cord and plug standards applicable to their target markets. Utilizing resources like the IEC 60320 standard can provide a foundational understanding of connector types. Buyers should also create a detailed compatibility chart that outlines the power cord standards for each region they operate in. When sourcing equipment, ensure that the power cords are either compliant with IEC standards or include regional adapters. Establishing relationships with reliable suppliers who understand local regulations can also streamline the procurement process, ensuring that equipment arrives ready for use without the need for additional modifications.
Scenario 2: Managing Power Cord Quality and Safety Standards
The Problem: Another common challenge for B2B buyers is ensuring the quality and safety of power cords. In regions like South America and the Middle East, where regulations may vary significantly, buyers often encounter substandard power cords that can lead to equipment damage or even safety hazards. Poor-quality cords can cause overheating, electrical failures, and pose fire risks, endangering both personnel and property.
The Solution: Buyers should prioritize sourcing power cords from reputable manufacturers who comply with international safety standards such as UL (Underwriters Laboratories) or CE (Conformité Européenne). It’s essential to request certifications and test reports for the cords being procured. Implementing a quality assurance process, including random inspections of received products, can help identify any potential issues before they affect operations. Additionally, investing in power cords specifically designed for the intended load and environmental conditions (e.g., temperature, humidity) can further mitigate risks. Engaging in continuous training on safety standards for staff involved in procurement and handling can also elevate safety practices within the organization.
Scenario 3: Addressing Compatibility Issues with Existing Infrastructure
The Problem: Compatibility issues often arise when integrating new equipment with existing power infrastructure. For example, a European company expanding its operations to Africa may find that their existing data centers utilize different power cord types, such as NEMA or CEE connectors. This discrepancy can lead to operational inefficiencies and increased costs due to the need for new power cords or adapters.
The Solution: To overcome compatibility challenges, B2B buyers should conduct a comprehensive audit of their current power infrastructure. This includes identifying the types of power cords and connectors already in use and documenting their specifications. When purchasing new equipment, buyers should ensure that the power cords included are compatible with existing systems. In cases where compatibility cannot be ensured, consider investing in universal power cords or adapters that can accommodate multiple standards. Additionally, maintaining an inventory of commonly used power cords can facilitate quick replacements and reduce downtime. Engaging with a consultant or power management specialist can also provide insights into optimizing power infrastructure for seamless integration of new technologies.
Strategic Material Selection Guide for types of power cords
When selecting power cords for international applications, understanding the materials used in their construction is crucial. Different materials offer unique properties that can affect performance, durability, and compliance with international standards. Below, we analyze four common materials used in power cords, providing insights tailored for B2B buyers from Africa, South America, the Middle East, and Europe.
What Are the Key Properties of PVC in Power Cords?
Polyvinyl Chloride (PVC) is one of the most widely used materials for power cord insulation. It has excellent electrical insulation properties, which makes it suitable for a variety of applications. PVC can withstand temperatures ranging from -15°C to 70°C, making it versatile for different environments. Additionally, it offers good resistance to chemicals and abrasion.
Pros and Cons of PVC:
PVC is cost-effective and easy to manufacture, which contributes to lower overall production costs. However, it has limitations in terms of flexibility at lower temperatures and can become brittle over time. This brittleness may lead to cracking or failure in extreme conditions.
Impact on Application:
PVC is compatible with a wide range of media, including both AC and DC power. It is often used in household and light commercial applications. However, B2B buyers must consider regional standards, as PVC may not meet the stringent requirements in some European countries.
How Does Rubber Compare as a Material for Power Cords?
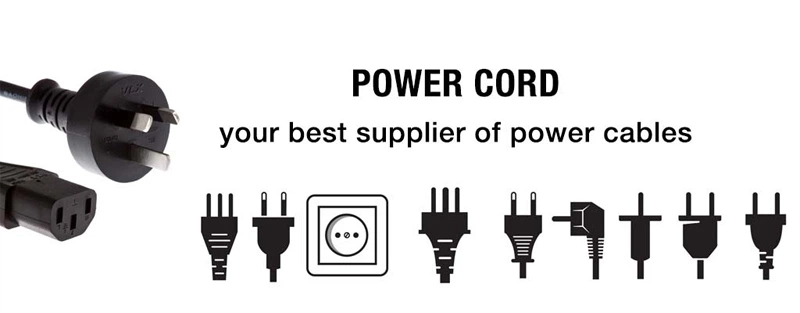
A stock image related to types of power cords.
Rubber, particularly thermoplastic elastomers (TPE), is another common material for power cords. It offers excellent flexibility and can withstand a broader temperature range, typically from -40°C to 90°C. Rubber is also highly resistant to abrasion and tearing, making it ideal for heavy-duty applications.
Pros and Cons of Rubber:
The primary advantage of rubber is its durability and flexibility, which allows for easy handling in various environments. However, rubber can be more expensive than PVC and may require more complex manufacturing processes, which can increase costs.
Impact on Application:
Rubber power cords are particularly suitable for industrial settings or outdoor applications where flexibility and durability are paramount. Buyers in regions with harsh climates, such as parts of Africa and the Middle East, may prefer rubber cords for their resilience.
What Are the Benefits of Silicone in Power Cord Manufacturing?
Silicone is gaining popularity as a high-performance material for power cords, especially in applications requiring extreme temperature resistance (from -60°C to 200°C). It is also highly resistant to UV light, ozone, and various chemicals, making it suitable for outdoor use.
Pros and Cons of Silicone:
Silicone’s key advantage is its ability to maintain performance across a wide range of temperatures and environmental conditions. However, it is generally more expensive than PVC and rubber, which may deter some budget-conscious buyers.
Impact on Application:
Silicone is ideal for applications in the automotive and aerospace industries, where performance under extreme conditions is critical. B2B buyers should ensure compliance with international standards, such as ASTM and DIN, when sourcing silicone-based power cords.
Why is Polyurethane a Preferred Material for Certain Power Cords?
Polyurethane (PU) is another advanced material used in power cord construction. It offers excellent abrasion resistance and flexibility, even in low temperatures. PU can also withstand a wide temperature range, typically from -40°C to 80°C.
Pros and Cons of Polyurethane:
The main advantage of PU is its superior flexibility and durability compared to PVC and rubber. However, it can be more costly and may require specialized manufacturing techniques, which can complicate the supply chain.
Impact on Application:
Polyurethane is often used in applications requiring high flexibility, such as robotics and portable electronics. Buyers from regions with high humidity or temperature fluctuations, such as South America, should consider PU for its resilience.
Summary Table of Power Cord Materials
Material | Typical Use Case for types of power cords | Key Advantage | Key Disadvantage/Limitation | Relative Cost (Low/Med/High) |
---|---|---|---|---|
PVC | Household and light commercial applications | Cost-effective and easy to manufacture | Limited flexibility at low temps | Low |
Rubber | Industrial and outdoor applications | Excellent flexibility and durability | Higher cost and manufacturing complexity | Medium |
Silicone | Automotive and aerospace applications | Extreme temperature resistance | More expensive than other materials | High |
Polyurethane | Robotics and portable electronics | Superior flexibility and durability | Higher cost and specialized manufacturing | Medium to High |
This strategic material selection guide provides actionable insights for B2B buyers looking to navigate the complexities of power cord materials. Understanding these properties and their implications can lead to better purchasing decisions that align with regional standards and application requirements.
In-depth Look: Manufacturing Processes and Quality Assurance for types of power cords
What Are the Key Stages in the Manufacturing Process of Power Cords?
The manufacturing process for power cords involves several critical stages that ensure the final product meets the required standards for safety and performance. These stages include material preparation, forming, assembly, and finishing.
Material Preparation: Sourcing and Quality Control
The manufacturing process begins with the selection of high-quality materials. Typically, manufacturers source copper for the conductors, PVC or rubber for insulation, and various metals for connectors. The sourcing of these materials is crucial as they must comply with international standards, such as the IEC 60320 for connectors, to ensure safety and reliability.
During this stage, suppliers are often evaluated based on their ability to provide materials that meet specified standards. B2B buyers should inquire about material certifications and request documentation that verifies compliance with international standards. This step is essential for ensuring that the raw materials used in power cords do not pose any safety risks.
How Is the Forming Stage Conducted for Power Cords?
The forming stage involves shaping the conductors and insulation into the desired configurations. This typically includes processes like:
- Wire Drawing: Copper is drawn into thin wires, which are then used as conductors. The gauge of the wire is critical, as it affects the cord’s current-carrying capacity.
- Insulation Extrusion: Insulation materials are extruded over the copper conductors, ensuring they are properly covered to prevent electrical hazards.
- Connector Molding: The plastic or metal connectors are molded into their final shapes, ready for assembly.
Manufacturers may employ advanced techniques such as automated machinery and robotics to enhance precision and efficiency in these processes. For B2B buyers, understanding the technology used in forming can provide insights into the quality and reliability of the power cords.
What Happens During the Assembly of Power Cords?
In the assembly stage, various components of the power cord are combined. This includes the attachment of the insulated wires to the molded connectors. Key techniques employed during assembly may include:
- Soldering: This method is often used to ensure a secure connection between wires and connectors.
- Crimping: A mechanical process that connects a connector to a wire without soldering, often used in high-volume production.
Quality assurance during assembly is paramount. Manufacturers typically conduct visual inspections and functional tests at this stage to ensure that all connections are secure and that the assembly meets specifications.
What Finishing Techniques Are Used in Power Cord Manufacturing?
The finishing stage involves several critical processes that enhance the durability and usability of power cords. This includes:
- Strain Relief Application: This technique involves adding features to prevent excessive stress on the wire connections, significantly reducing the risk of failure.
- Labeling: Proper labeling is essential for compliance with safety standards and to provide users with necessary information regarding the product’s specifications.
- Final Inspection and Testing: Each power cord undergoes a final inspection, which may include testing for electrical continuity and insulation integrity.
B2B buyers should ensure that their suppliers implement thorough finishing processes, as these can significantly impact the longevity and reliability of the power cords.
How Is Quality Assurance Implemented in Power Cord Manufacturing?
Quality assurance (QA) is an integral part of power cord manufacturing. Manufacturers typically adhere to international standards, such as ISO 9001, which outlines requirements for quality management systems.
What International Standards Should B2B Buyers Be Aware Of?
International standards relevant to power cords include:
- ISO 9001: A standard that ensures consistent quality in manufacturing processes.
- CE Marking: Required for products sold in the European Economic Area, indicating conformity with health, safety, and environmental protection standards.
- UL Certification: Ensures that power cords meet safety standards set by Underwriters Laboratories, particularly important for markets in North America.
For B2B buyers, understanding these certifications is crucial when sourcing power cords, as they indicate compliance with safety and performance standards.
What Are the Key Quality Control Checkpoints in Power Cord Manufacturing?
Quality control (QC) is typically structured around several checkpoints throughout the manufacturing process:
- Incoming Quality Control (IQC): This involves inspecting raw materials and components before they enter the production line to ensure they meet specified standards.
- In-Process Quality Control (IPQC): Conducted during the manufacturing process to identify and rectify issues immediately, reducing waste and ensuring product consistency.
- Final Quality Control (FQC): A comprehensive inspection conducted on finished products to ensure they meet all specifications and standards before shipping.
B2B buyers should inquire about the QC processes employed by suppliers and request access to QC reports that outline testing results and compliance with relevant standards.
How Can B2B Buyers Verify Supplier Quality Control?
B2B buyers can take several steps to verify the quality control measures of their suppliers:
- Supplier Audits: Conducting on-site audits can provide insight into the manufacturing processes and QC practices of potential suppliers.
- Requesting Documentation: Buyers should ask for certificates of compliance, test reports, and quality management system documentation.
- Third-Party Inspections: Engaging third-party inspection services can provide an unbiased evaluation of the supplier’s quality control practices.
What Are the QC and Certification Nuances for International Buyers?
International B2B buyers, particularly from regions like Africa, South America, the Middle East, and Europe, must navigate various certification requirements. These can vary significantly based on local regulations and standards. For example:
- In Africa, buyers should be aware of local regulations that may not align with international standards, necessitating additional compliance checks.
- In Europe, the CE marking is crucial, while in South America, buyers may encounter different certification processes, such as the INMETRO certification in Brazil.
Understanding these nuances can help buyers make informed decisions and avoid compliance issues when sourcing power cords for their markets.
In summary, power cord manufacturing involves intricate processes and strict quality assurance measures that B2B buyers must consider when sourcing products. By focusing on supplier standards and QC practices, buyers can ensure they procure reliable and compliant power cords that meet their operational needs.
Practical Sourcing Guide: A Step-by-Step Checklist for ‘types of power cords’
Introduction
Navigating the procurement of power cords can be a complex endeavor, especially for international B2B buyers who need to ensure compatibility with local standards and regulations. This step-by-step checklist is designed to guide you through the essential considerations and actions needed to source the right types of power cords for your business operations in diverse markets, including Africa, South America, the Middle East, and Europe.
Step 1: Define Your Technical Specifications
Understanding your technical requirements is crucial. Identify the type of power supply, voltage, and current ratings necessary for your equipment. This will help you narrow down the types of power cords needed, such as C13 or NEMA 5-15P, depending on your region and equipment compatibility.
- Voltage and Current Ratings: Ensure the power cord can handle the required voltage (e.g., 110V vs. 220V) and current (e.g., 15A).
- Connector Types: Familiarize yourself with IEC 60320 standards and local plug types relevant to your target market.
Step 2: Research Local Standards and Regulations
Different regions have specific standards for electrical appliances and power cords. Understanding these regulations is vital to avoid compliance issues.
- IEC Standards: Most countries adhere to IEC 60320 for connectors; however, local plug standards may vary.
- Country-Specific Requirements: For example, in Europe, CEE 7/7 is common, while in South America, NBR 14136 may be applicable.
Step 3: Evaluate Potential Suppliers
Before making a commitment, conduct a thorough evaluation of potential suppliers. This step ensures that you are partnering with reliable manufacturers who meet your quality standards.
- Company Profiles: Request detailed company information, including their manufacturing capabilities and experience in your industry.
- References and Case Studies: Look for testimonials from other businesses in your region to gauge reliability and service quality.
Step 4: Assess Quality Assurance Practices
Quality assurance is critical when sourcing power cords, as substandard products can lead to equipment failures and safety hazards.
- Certification and Compliance: Verify that the suppliers adhere to international safety standards such as UL, CE, or RoHS.
- Testing Protocols: Inquire about their testing methods for durability and performance under various conditions.
Step 5: Negotiate Pricing and Terms
Once you have identified potential suppliers, the next step is to negotiate pricing and contract terms. This is crucial for ensuring that you receive the best value without compromising on quality.
- Volume Discounts: Discuss pricing tiers based on order quantities to maximize savings.
- Payment Terms: Clarify payment methods and timelines to align with your cash flow requirements.
Step 6: Request Samples for Testing
Before placing a large order, request samples of the power cords. Testing samples can help you assess their compatibility and performance under your specific conditions.
- Compatibility Testing: Ensure that the samples work seamlessly with your equipment.
- Durability and Safety Checks: Conduct tests to evaluate the cords’ resistance to wear and tear and their safety features.
Step 7: Finalize Logistics and Shipping Arrangements
Finally, consider the logistics of shipping and delivery. Ensuring timely and safe delivery is essential for maintaining your operational schedule.
- Shipping Options: Evaluate different shipping methods based on cost and delivery times.
- Customs and Duties: Be aware of any import regulations or duties that may apply in your country to avoid unexpected costs.
By following these steps, international B2B buyers can effectively source the right types of power cords that meet their technical needs while ensuring compliance with local standards and regulations.
Comprehensive Cost and Pricing Analysis for types of power cords Sourcing
What Are the Key Cost Components in Power Cord Manufacturing?
When sourcing power cords, international B2B buyers should be aware of the various cost components that impact the final pricing. The primary elements include:
-
Materials: The type of materials used significantly affects costs. Common materials include copper for conductors, PVC or rubber for insulation, and various plastics for connectors. The choice of materials can vary based on regional availability and quality standards.
-
Labor: Labor costs can fluctuate based on the manufacturing location. Countries with lower labor costs may offer competitive pricing, but this can affect quality and compliance with international standards.
-
Manufacturing Overhead: This includes the costs of facilities, equipment, and utilities. Efficient manufacturing processes can help minimize overhead, thus reducing overall costs.
-
Tooling: The initial setup for manufacturing, including molds for connectors and fixtures for assembly, is a significant upfront cost. Custom tooling for specialized power cords can further increase this expense.
-
Quality Control (QC): Ensuring that power cords meet safety and performance standards is crucial. Costs associated with QC processes can vary based on the level of certification required, such as IEC, NEMA, or other local standards.
-
Logistics: Shipping and handling costs are critical, especially for international buyers. Factors like distance, shipping method, and customs duties can add to the overall cost.
-
Margin: Manufacturers and suppliers typically include a profit margin, which can vary significantly based on competition, brand reputation, and the complexity of the product.
How Do Price Influencers Affect Power Cord Sourcing?
Several factors influence the pricing of power cords, particularly for international B2B buyers:
-
Volume/MOQ: The minimum order quantity (MOQ) can greatly affect pricing. Larger orders typically attract bulk discounts, making it essential for buyers to consolidate their needs.
-
Specifications and Customization: Custom specifications, such as length, gauge, and connector types, can increase costs. Buyers should evaluate whether standard products meet their needs to avoid unnecessary expenses.
-
Materials: The quality and type of materials directly impact the price. For instance, using higher-grade copper or specialized insulation materials will increase costs but may provide better performance and durability.
-
Quality and Certifications: Products that meet international safety standards (e.g., UL, CE) may command higher prices. Buyers should consider the long-term benefits of investing in certified products.
-
Supplier Factors: The supplier’s reputation, reliability, and service levels can influence pricing. Established suppliers may charge more but offer better support and quality assurance.
-
Incoterms: Understanding shipping terms is vital for cost management. Incoterms define responsibilities for shipping, insurance, and tariffs, affecting the total landed cost of power cords.
What Are Effective Buyer Tips for Cost-Efficiency in Power Cord Sourcing?
To optimize sourcing costs, B2B buyers should consider the following strategies:
-
Negotiate Wisely: Engage suppliers in discussions about pricing based on volume, long-term contracts, or bundled services. Establishing a strong relationship can lead to better terms and pricing.
-
Evaluate Total Cost of Ownership (TCO): Consider not just the purchase price but also the costs associated with installation, maintenance, and potential replacements over time. Higher-quality power cords may have a higher initial cost but lower TCO due to durability.
-
Understand Pricing Nuances for International Sourcing: Buyers from regions like Africa, South America, the Middle East, and Europe should be aware of regional pricing differences. Currency fluctuations, local tariffs, and shipping costs can significantly affect the final price.
-
Be Informed About Market Trends: Keeping abreast of market conditions, such as material shortages or changes in demand, can provide leverage in negotiations and purchasing decisions.
In conclusion, understanding the intricate cost structure and pricing dynamics of power cords is essential for international B2B buyers. By focusing on these factors, buyers can make informed decisions that align with their operational needs and budget constraints.
Alternatives Analysis: Comparing types of power cords With Other Solutions
In the landscape of electrical connectivity, power cords serve a fundamental role in linking devices to power sources. However, with advancing technology and varying application needs, it is essential to explore alternatives that can fulfill similar functions. This analysis compares traditional types of power cords with two viable alternative solutions: Power over Ethernet (PoE) and wireless power transfer technologies.
Comparison Aspect | Types Of Power Cords | Power over Ethernet (PoE) | Wireless Power Transfer |
---|---|---|---|
Performance | Reliable for high voltage and current requirements, suitable for a wide range of devices. | Delivers both power and data over a single cable, effective for low to medium power devices. | Ideal for low-power applications, offers convenience without physical connections. |
Cost | Generally low-cost, varies by type and length. | Moderate initial investment for PoE switches and compatible devices. | High setup costs, especially for infrastructure adaptation. |
Ease of Implementation | Simple to implement with standard electrical outlets. | Requires compatible infrastructure and may need network upgrades. | Easy for end-user devices but requires compatible receivers and transmitters. |
Maintenance | Minimal maintenance, replaceable if damaged. | Maintenance of network hardware needed; potential for network downtimes. | Requires careful handling of devices to avoid damage; limited range can be a concern. |
Best Use Case | Best for high-demand devices like servers and industrial equipment. | Best for smart devices, IP cameras, and VoIP phones in networked environments. | Best for consumer electronics and devices in proximity, such as smartphones and wearables. |
What Are the Advantages and Disadvantages of Power over Ethernet (PoE)?
Power over Ethernet (PoE) technology provides a compelling alternative by allowing electrical power and data to be transmitted over standard Ethernet cables. This solution is particularly advantageous in smart environments, where devices like IP cameras and VoIP phones benefit from both power and data connectivity without the need for additional wiring.
However, while PoE offers reduced cable clutter and simplified installations, it has limitations in terms of distance and power capacity. Typically, PoE can deliver up to 15.4W per port, which may not be sufficient for high-power devices. Additionally, organizations may need to invest in PoE-enabled switches, which can increase initial costs.
How Does Wireless Power Transfer Compare to Power Cords?
Wireless power transfer, utilizing magnetic resonance or inductive coupling, presents a modern approach to powering devices without physical connectors. This technology is increasingly popular for consumer electronics, allowing devices to be charged simply by being placed on a charging pad.
The primary advantage of wireless power is convenience; it eliminates the hassle of plugging and unplugging devices. However, its limitations include lower power transfer efficiency and range, along with potential heat generation. Furthermore, not all devices are compatible with wireless charging, which may necessitate a combination of power solutions for businesses.
How Should B2B Buyers Choose the Right Power Solution?
When evaluating power solutions, B2B buyers should consider their specific operational needs, budget constraints, and the types of devices in use. For environments that require robust power delivery to heavy-duty equipment, traditional power cords remain the most reliable option. Conversely, for smart offices or environments where cabling can be cumbersome, PoE may provide an effective solution. Lastly, for consumer-facing applications where user convenience is paramount, wireless power transfer could enhance the user experience.
Ultimately, the decision should align with the operational demands of the business, future scalability, and potential infrastructure investments to ensure seamless connectivity and efficiency.
Essential Technical Properties and Trade Terminology for types of power cords
What Are the Essential Technical Properties of Power Cords?
Understanding the technical properties of power cords is crucial for B2B buyers, especially when sourcing products for diverse markets across Africa, South America, the Middle East, and Europe. Here are some essential specifications to consider:
-
Material Grade
– Power cords are typically made from copper or aluminum. Copper is preferred for its superior conductivity and durability, making it ideal for high-performance applications. Aluminum is lighter and more cost-effective but may not provide the same conductivity. Buyers should evaluate the material based on the specific electrical requirements and environmental conditions. -
Current Rating (Amperage)
– The current rating indicates the maximum amount of electric current a power cord can safely carry. Common ratings include 10A, 15A, and 20A. Selecting a cord with an appropriate current rating is critical to prevent overheating and potential fire hazards. B2B buyers should ensure that the selected power cords meet the amperage requirements of the devices they intend to power. -
Voltage Rating
– This specification indicates the maximum voltage that the power cord can handle. Standard voltage ratings include 250V for European markets and 125V for North American markets. Ensuring compatibility with local voltage standards is essential to avoid equipment damage and ensure safety. -
Temperature Rating
– Power cords are rated for specific temperature ranges, typically from -20°C to 60°C. This rating indicates the environmental conditions under which the cord can operate safely. Buyers should consider the ambient temperature of the installation site to select cords that can withstand local conditions. -
Insulation Type
– The insulation material used in power cords affects flexibility, durability, and resistance to environmental factors like moisture and chemicals. Common types include PVC, rubber, and silicone. Choosing the right insulation type can extend the lifespan of the power cord and ensure safe operation in various environments. -
Cable Length
– The length of the power cord can significantly impact installation and usability. Buyers should consider their specific layout and equipment needs when selecting cable lengths. Longer cords may introduce voltage drop issues, so it’s essential to balance convenience with electrical performance.
What Are the Key Trade Terminology and Acronyms Related to Power Cords?
Familiarity with industry jargon can streamline the purchasing process. Here are some common terms that B2B buyers should know:
-
OEM (Original Equipment Manufacturer)
– An OEM is a company that produces parts or equipment that may be marketed by another manufacturer. In the power cord industry, knowing whether a supplier is an OEM can help buyers gauge the quality and reliability of the products. -
MOQ (Minimum Order Quantity)
– MOQ refers to the smallest quantity of a product that a supplier is willing to sell. Understanding MOQ is essential for budgeting and inventory management, especially for international buyers who may have different purchasing capabilities. -
RFQ (Request for Quotation)
– An RFQ is a document issued when an organization wants to procure goods or services. It outlines the specifications and quantities required, allowing suppliers to provide competitive pricing. Using RFQs can help buyers obtain the best deals and ensure they are sourcing the correct products. -
Incoterms (International Commercial Terms)
– Incoterms are a set of international rules that define the responsibilities of buyers and sellers in international transactions. Understanding these terms is vital for managing shipping costs, risks, and delivery timelines, especially for buyers importing power cords from other countries. -
CE Marking
– The CE marking indicates that a product meets European safety standards. For B2B buyers in Europe, ensuring that power cords have CE marking is crucial for compliance with regulations and to ensure product safety. -
UL Certification
– UL certification indicates that a product has been tested for safety and performance. For power cords, UL certification is particularly important in North America, as it assures buyers of the product’s reliability and compliance with safety standards.
By understanding these technical properties and trade terms, international B2B buyers can make informed decisions when sourcing power cords tailored to their specific needs.
Navigating Market Dynamics and Sourcing Trends in the types of power cords Sector
What Are the Current Market Dynamics Affecting Power Cords?
The global market for power cords is being significantly shaped by technological advancements, regulatory changes, and evolving consumer preferences. Key drivers include the increasing adoption of renewable energy sources and the rise of smart devices that demand versatile power solutions. For international B2B buyers, particularly from Africa, South America, the Middle East, and Europe, understanding these dynamics is crucial for effective sourcing strategies.
Emerging trends show a shift towards standardized products, such as those adhering to the IEC 60320 standard, which facilitates compatibility across different regions. The demand for high-quality, durable power cords is on the rise, driven by the need for reliable performance in critical applications like data centers and industrial settings. Additionally, as businesses increasingly rely on e-commerce for procurement, suppliers are enhancing their online presence and logistics capabilities to meet the growing demand for quick and efficient delivery.
Another important trend is the focus on customization. B2B buyers are looking for suppliers that can provide tailored solutions, such as specific lengths, connector types, and cable configurations, to meet unique operational requirements. This trend emphasizes the importance of supplier flexibility and responsiveness in the competitive market landscape.
How Can Sustainability Influence Power Cord Sourcing Decisions?
Sustainability has become a pivotal consideration for B2B buyers in the power cord sector. The environmental impact of manufacturing processes and materials used in power cords has prompted companies to seek more sustainable options. Ethical sourcing practices are increasingly prioritized, with buyers looking for suppliers who demonstrate a commitment to reducing carbon footprints and using recyclable materials.
Buyers should consider the availability of ‘green’ certifications, such as RoHS (Restriction of Hazardous Substances) and Energy Star, which indicate compliance with environmental regulations and standards. These certifications not only enhance the credibility of suppliers but also align with the growing demand for eco-friendly products among consumers and businesses alike.
Furthermore, the shift towards circular economy principles is influencing sourcing strategies. Buyers are now considering suppliers who offer take-back programs or recycling options for old power cords, which can minimize waste and promote resource efficiency. By prioritizing sustainability, B2B buyers can not only enhance their brand image but also contribute to a more sustainable future.
What Is the Historical Context of Power Cord Development?
The evolution of power cords has been driven by technological advancements and changing safety standards. Initially, power cords were simple, unshielded cables designed for basic electrical connections. However, as electrical systems became more complex, the need for standardized connectors and enhanced safety features emerged.
In the mid-20th century, the introduction of international standards such as IEC 60320 revolutionized the industry by promoting compatibility and safety across various applications. This standardization facilitated global trade and allowed manufacturers to produce a diverse range of power cord types suitable for different regions, including Europe, North America, and Asia.
Today, the industry continues to innovate, focusing on durability, efficiency, and sustainability, ensuring that power cords meet the demands of modern technology while adhering to environmental standards. Understanding this historical context helps B2B buyers appreciate the advancements in quality and safety that influence their sourcing decisions today.
Frequently Asked Questions (FAQs) for B2B Buyers of types of power cords
-
How do I choose the right power cord for my equipment?
Selecting the appropriate power cord involves understanding the voltage and current requirements of your equipment, as well as the plug type compatible with your local electrical infrastructure. Research the IEC 60320 standards, which specify various connector types like C13, C15, and C19. Additionally, consider the length of the cord needed for your setup and whether you require features such as surge protection or hospital-grade specifications for sensitive equipment. -
What is the best power cord type for international usage?
For international usage, it’s advisable to opt for power cords that conform to the IEC 60320 standard, as they are widely recognized and compatible with various plug types across countries. The C13 to C14 and C19 to C20 configurations are particularly versatile for IT and data center applications. If you’re operating across multiple regions, consider universal power cords or adapters that accommodate different plug types. -
How can I verify the quality of power cords before purchasing?
To ensure quality, always source power cords from reputable manufacturers who provide certifications such as UL, CE, or RoHS compliance. Request samples for testing, and check for features like strain relief and heat resistance. Additionally, verify the manufacturer’s warranty and return policies, which can be indicators of product reliability. Reviews and testimonials from other B2B buyers can also provide valuable insights into product performance. -
What are the common payment terms for bulk power cord orders?
Payment terms can vary significantly based on the supplier and the region. Common arrangements include net 30 or net 60 terms, which allow you to pay within 30 or 60 days after receiving the goods. Some suppliers may require a deposit upfront, especially for custom orders. Always negotiate clear terms before finalizing your purchase, and consider using escrow services for large transactions to safeguard your investment.
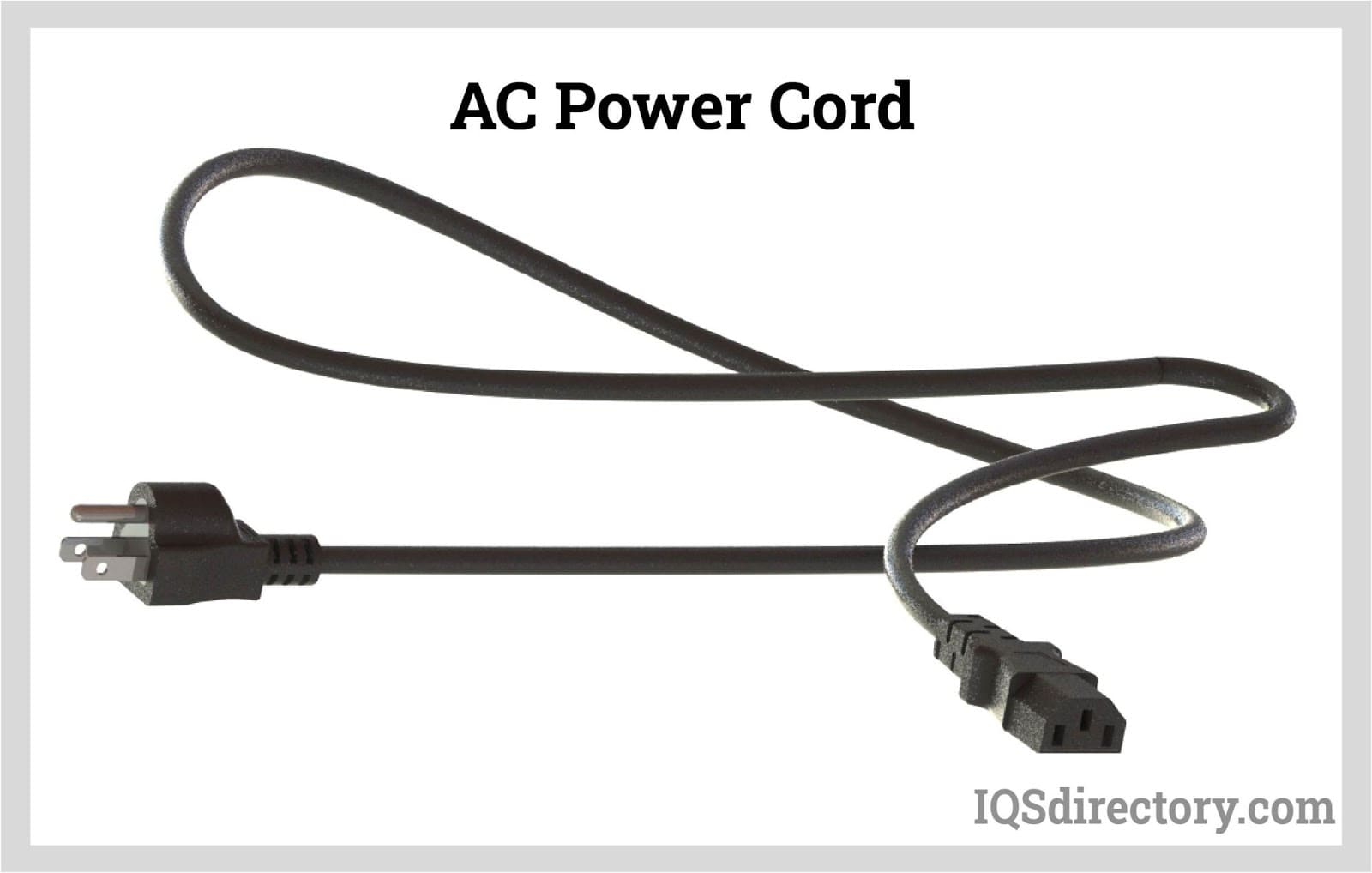
A stock image related to types of power cords.
-
What is the minimum order quantity (MOQ) for power cords?
Minimum order quantities (MOQs) for power cords can vary based on the supplier and the type of cord. Generally, MOQs may range from 100 to 1,000 units. For custom power cords, MOQs may be higher due to setup costs. It’s beneficial to discuss your specific needs with suppliers to see if they can accommodate lower MOQs, especially if you’re just starting or testing a new market. -
How do I handle logistics and shipping for international power cord orders?
When managing logistics for international orders, consider partnering with freight forwarders experienced in handling electrical components. Ensure that the supplier provides all necessary documentation, such as customs declarations and compliance certificates. Familiarize yourself with the import regulations of your country to avoid delays. Additionally, consider shipping options like air freight for speed or sea freight for cost savings, depending on your urgency and budget. -
What customization options are available for power cords?
Many manufacturers offer customization options for power cords, including specific lengths, colors, and connector types. You can also request modifications such as added strain relief or specific shielding for enhanced durability. When discussing customization, provide detailed specifications and intended applications to ensure the final product meets your requirements. Be aware that custom orders may have longer lead times and higher MOQs. -
How can I ensure compliance with international electrical standards?
To ensure compliance with international standards, familiarize yourself with the relevant regulations in your target markets, such as IEC standards for connectors and local electrical codes. Work with suppliers who provide certifications for their products, and consult with local authorities or third-party testing labs if necessary. Keeping abreast of changes in regulations will help you maintain compliance and avoid potential legal issues in your operations.
Important Disclaimer & Terms of Use
⚠️ Important Disclaimer
The information provided in this guide, including content regarding manufacturers, technical specifications, and market analysis, is for informational and educational purposes only. It does not constitute professional procurement advice, financial advice, or legal advice.
While we have made every effort to ensure the accuracy and timeliness of the information, we are not responsible for any errors, omissions, or outdated information. Market conditions, company details, and technical standards are subject to change.
B2B buyers must conduct their own independent and thorough due diligence before making any purchasing decisions. This includes contacting suppliers directly, verifying certifications, requesting samples, and seeking professional consultation. The risk of relying on any information in this guide is borne solely by the reader.
Strategic Sourcing Conclusion and Outlook for types of power cords
As international B2B buyers navigate the diverse landscape of power cords, understanding the varying standards and specifications across regions is paramount. Key takeaways highlight the importance of aligning product selection with local standards, such as the IEC 60320 and regional plug types like NEMA or CEE. Strategic sourcing not only ensures compliance with local regulations but also optimizes operational efficiency by minimizing compatibility issues and enhancing supply chain reliability.
How Can Strategic Sourcing Enhance Your Power Cord Procurement?
Investing in strategic sourcing allows businesses to identify quality suppliers who can provide the right power cords tailored to specific needs, whether it’s for data centers, hospitals, or commercial use. This approach empowers buyers to leverage competitive pricing and superior service levels, ultimately leading to reduced costs and increased value.
What Is the Future Outlook for Power Cord Types?
Looking ahead, the demand for versatile and high-performance power cords will continue to rise, especially with the expansion of technology in sectors like renewable energy and smart devices. Buyers from Africa, South America, the Middle East, and Europe should proactively engage with suppliers who understand their unique market requirements. By prioritizing strategic sourcing, businesses can not only enhance their operational capabilities but also drive innovation and sustainability in their electrical infrastructure.