Discover the Best Wire Connector: The Ultimate Sourcing Guide (2025)
Introduction: Navigating the Global Market for wire connector
In an increasingly interconnected world, sourcing the right wire connectors can pose a significant challenge for international B2B buyers, particularly in regions like Africa, South America, the Middle East, and Europe. The complexity arises from the diverse range of types, specifications, and applications that wire connectors offer, making it crucial to understand not only what products are available but also how to evaluate suppliers effectively. This comprehensive guide delves into the various types of wire connectors, their applications across industries, and essential considerations for supplier vetting.
By exploring the nuances of wire connectors—including specifications like gauge, insulation types, and pricing models—this guide equips B2B buyers with the knowledge they need to make informed purchasing decisions. Understanding the cost implications and the quality of materials used in wire connectors is vital, especially for businesses in developing regions where budget constraints may be more pronounced. Moreover, the guide will highlight best practices for identifying reliable suppliers and the importance of compliance with international standards, ensuring that your sourcing decisions lead to long-term value.
Whether you’re looking to enhance the performance of electrical systems or seeking durable solutions for industrial applications, this guide provides actionable insights tailored to the unique needs of international buyers. Embrace the opportunity to optimize your sourcing strategy and secure the best wire connectors for your business.
Understanding wire connector Types and Variations
Type Name | Key Distinguishing Features | Primary B2B Applications | Brief Pros & Cons for Buyers |
---|---|---|---|
Fork Terminals | Open-ended design for easy attachment, insulated | Automotive, Industrial Equipment | Pros: Easy to install, reusable. Cons: Limited to specific applications. |
Ring Terminals | Circular design for secure connections, insulated | Electrical Panels, Machinery | Pros: Strong connection, prevents accidental disconnection. Cons: Requires mounting. |
Butt Connectors | Straight connection for joining wires, insulated | Electrical Wiring, Telecommunications | Pros: Simple installation, good for splicing. Cons: May require additional tools. |
Quick Connect Terminals | Snap-on design for rapid connections, insulated | Consumer Electronics, Automotive | Pros: Fast installation, reusable. Cons: May not suit high-current applications. |
Waterproof Connectors | Sealed design to prevent moisture ingress | Outdoor Equipment, Marine Applications | Pros: Durable, protects against environmental factors. Cons: Higher cost. |
What are Fork Terminals and Their Applications?
Fork terminals feature an open-ended design that allows for easy attachment to screws or studs, making them ideal for applications where frequent disconnection is necessary. Commonly used in automotive and industrial equipment, these connectors offer a reliable electrical connection while being reusable. When purchasing fork terminals, buyers should consider the gauge of wire and the environment in which they will be used, as exposure to moisture may affect performance.
Why Choose Ring Terminals for Your B2B Needs?
Ring terminals provide a circular design that ensures a secure connection when mounted on a stud or screw. They are particularly useful in electrical panels and machinery where a robust connection is essential. The insulated design minimizes the risk of short circuits. Buyers should evaluate the mounting requirements and ensure compatibility with their equipment. While offering a strong connection, ring terminals can be more challenging to install than other types.
How Do Butt Connectors Benefit Electrical Wiring?
Butt connectors are designed for straightforward wire splicing, making them a staple in electrical wiring and telecommunications. Their insulated structure provides a secure connection, reducing the risk of shorts. When considering butt connectors, buyers should assess the gauge of wire being joined and whether additional crimping tools will be necessary for installation. They are favored for their simplicity but may require careful handling to ensure a proper splice.
What Advantages Do Quick Connect Terminals Offer?
Quick connect terminals feature a snap-on design that allows for rapid connections, making them perfect for consumer electronics and automotive applications. Their ease of use can significantly speed up assembly processes. However, buyers should be cautious about their suitability for high-current applications, as the connection may not be as robust as that of other terminal types. Evaluating the specific needs of the project is essential for optimal performance.
Why are Waterproof Connectors Essential for Certain Applications?
Waterproof connectors are designed with sealed mechanisms that prevent moisture ingress, making them crucial for outdoor equipment and marine applications. Their durability ensures reliable performance in harsh environments. While these connectors provide excellent protection against the elements, they tend to be more expensive than standard connectors. Buyers should weigh the costs against the potential risks of using non-waterproof options in challenging conditions.
Key Industrial Applications of wire connector
Industry/Sector | Specific Application of Wire Connector | Value/Benefit for the Business | Key Sourcing Considerations for this Application |
---|---|---|---|
Automotive | Electrical wiring harness assembly | Ensures reliable connections for safety and performance | Compliance with automotive standards and certifications |
Renewable Energy | Solar panel installations | Facilitates efficient energy transfer and durability | Resistance to environmental factors and long-term reliability |
Industrial Automation | Machine control systems | Enhances operational efficiency and reduces downtime | Compatibility with various wire sizes and types |
Telecommunications | Network infrastructure setup | Supports high-speed data transmission | Quality assurance and performance testing |
Construction | Electrical installations in commercial buildings | Provides safe and efficient power distribution | Compliance with local electrical codes and standards |
How is Wire Connector Used in the Automotive Industry?
In the automotive sector, wire connectors are critical for assembling electrical wiring harnesses that power various components, from engines to infotainment systems. These connectors ensure secure and reliable connections, which are vital for vehicle safety and performance. For international buyers, especially from regions like Africa and South America, sourcing connectors that meet specific automotive standards and certifications is essential to ensure compliance and reliability in harsh driving conditions.
What Role Do Wire Connectors Play in Renewable Energy?
In renewable energy applications, particularly solar panel installations, wire connectors facilitate efficient energy transfer between solar cells and inverters. These connectors must withstand environmental challenges such as UV exposure and moisture to maintain their integrity and functionality over time. Buyers in regions like the Middle East, where solar energy is rapidly expanding, should prioritize sourcing connectors that offer high resistance to environmental factors and ensure long-term reliability.
How are Wire Connectors Essential for Industrial Automation?
Wire connectors are integral to industrial automation systems, enabling seamless connections within machine control systems. They help enhance operational efficiency by ensuring that electrical signals are transmitted without interruption, thus reducing downtime. For businesses in Europe and the Middle East, sourcing connectors that are compatible with various wire sizes and types is crucial for maintaining the flexibility and scalability of their automation solutions.
Why are Wire Connectors Important for Telecommunications?
In the telecommunications industry, wire connectors are essential for setting up network infrastructure, ensuring high-speed data transmission between devices. They help maintain signal integrity and reduce latency, which is critical in today’s fast-paced digital environment. For international buyers, particularly from Europe, ensuring that connectors meet stringent quality assurance and performance testing standards is vital for operational success and customer satisfaction.
How Do Wire Connectors Contribute to Construction Projects?
In the construction industry, wire connectors are used extensively in electrical installations within commercial buildings. They enable safe and efficient power distribution throughout the structure, ensuring compliance with local electrical codes and standards. Buyers from Africa and South America should focus on sourcing connectors that not only meet these codes but also offer durability and reliability in diverse climatic conditions, enhancing the safety and longevity of their electrical systems.
3 Common User Pain Points for ‘wire connector’ & Their Solutions
Scenario 1: Difficulty in Selecting the Right Type of Wire Connector
The Problem: B2B buyers often face overwhelming choices when it comes to selecting wire connectors. The vast array of types—such as butt connectors, ring terminals, and splicing connectors—can lead to confusion about which option is best suited for a specific application. This indecision is exacerbated by the need to consider factors such as wire gauge, insulation type, and environmental conditions. For instance, a buyer in Brazil might need connectors that can withstand high humidity, while a buyer in Europe might prioritize connectors that are compliant with stringent electrical standards.
The Solution: To navigate this complexity, buyers should start by clearly defining their project requirements. Create a checklist that includes wire gauge, insulation type, environmental exposure, and any regulatory standards that must be met. Engaging with reputable suppliers who offer technical support can also be beneficial. For example, suppliers like Remington Industries provide detailed specifications and usage guidelines for their products, helping buyers make informed decisions. Utilizing product comparison tools on supplier websites can further streamline the selection process, allowing buyers to compare features and prices effectively.
Scenario 2: Poor Quality and Reliability of Connectors
The Problem: Reliability is crucial for B2B buyers, particularly when dealing with electrical systems in demanding environments. A common pain point is receiving subpar wire connectors that fail under load or environmental stress, leading to costly downtime and potential safety hazards. For instance, in the UAE’s harsh desert climate, connectors that are not rated for extreme temperatures can degrade rapidly, resulting in failure.
The Solution: To ensure quality and reliability, buyers should prioritize sourcing connectors from established manufacturers with a proven track record. Conducting due diligence, such as reviewing customer testimonials and certifications, can provide insights into the reliability of products. Additionally, consider investing in connectors with robust insulation and protective features, such as waterproofing or corrosion resistance. Suppliers often provide testing data and certifications that verify their products meet industry standards, which can be a strong indicator of quality. Building long-term relationships with trusted suppliers can also facilitate access to high-quality components and prompt support in case of issues.
Scenario 3: Installation Challenges Leading to Increased Labor Costs
The Problem: Installation of wire connectors can sometimes be a daunting task, particularly for companies with limited technical expertise. Inadequate installation can lead to poor connections, short circuits, or even fire hazards, resulting in increased labor costs and project delays. This is especially concerning for international buyers who may not have access to skilled labor or training resources.
The Solution: To mitigate installation challenges, companies should invest in comprehensive training for their technicians. Many manufacturers offer training resources, including videos and installation guides, which can be invaluable for ensuring proper techniques are followed. Additionally, utilizing connectors that feature user-friendly designs—such as quick-connect terminals or those with built-in guides—can simplify the installation process. Collaborating with suppliers that provide hands-on training sessions or workshops can also enhance the skills of the workforce. Lastly, consider employing connectors that allow for tool-free installation, reducing the chance of human error and speeding up the overall process.
Strategic Material Selection Guide for wire connector
When selecting wire connectors, the choice of material is crucial for ensuring optimal performance and longevity in various applications. Here, we analyze four common materials used in wire connectors, focusing on their properties, advantages, disadvantages, and considerations for international B2B buyers, particularly from regions like Africa, South America, the Middle East, and Europe.
What Are the Key Properties of Copper in Wire Connectors?
Copper is one of the most widely used materials for wire connectors due to its excellent conductivity and mechanical properties. It typically has a temperature rating of up to 200°C and offers good corrosion resistance, especially when tin-plated.
Pros: Copper connectors provide low electrical resistance, ensuring efficient power transmission. They are also relatively easy to manufacture and can be formed into various shapes, making them versatile for different applications.
Cons: The primary disadvantage of copper is its susceptibility to corrosion, particularly in humid or saline environments. Additionally, copper can be more expensive than some alternatives, impacting overall project costs.
Impact on Application: Copper connectors are ideal for high-performance applications, such as in electrical panels and automotive wiring, where conductivity is paramount.
Considerations for International Buyers: Buyers should ensure that copper connectors comply with international standards such as ASTM B187 and consider local regulations regarding the use of copper in electrical applications.
How Do Aluminum Connectors Compare for Durability and Cost?
Aluminum is another popular material for wire connectors, particularly in applications requiring lightweight solutions. Aluminum connectors typically have a lower temperature rating, around 100°C, and can be prone to oxidation.
Pros: Aluminum is lighter and generally less expensive than copper, making it an attractive option for large-scale projects. It also has good corrosion resistance when properly coated.
Cons: The main drawback is that aluminum has higher electrical resistance than copper, which can lead to overheating in high-load applications. Additionally, the manufacturing process can be more complex, requiring special techniques to ensure reliable connections.
Impact on Application: Aluminum connectors are commonly used in overhead power lines and large electrical installations where weight is a significant factor.
Considerations for International Buyers: Compliance with standards such as ASTM B800 is essential, and buyers should be aware of the specific requirements for aluminum connectors in their regions, particularly in terms of installation practices to prevent connection failures.
What Are the Advantages of PVC Insulated Connectors?
PVC (Polyvinyl Chloride) insulation is frequently used in wire connectors to provide electrical insulation and protection against environmental factors. PVC connectors can typically withstand temperatures up to 85°C.
Pros: The primary advantage of PVC insulation is its excellent electrical insulation properties and resistance to moisture, chemicals, and abrasion. PVC connectors are also cost-effective and widely available.
Cons: However, PVC can become brittle over time, especially when exposed to UV light or extreme temperatures, which may limit their lifespan in outdoor applications.
Impact on Application: PVC insulated connectors are suitable for general-purpose applications, including household wiring and automotive uses, where environmental exposure is moderate.
Considerations for International Buyers: Buyers should check for compliance with standards like IEC 60227, especially in regions with stringent electrical safety regulations.
How Do Nylon Connectors Enhance Performance in Harsh Environments?
Nylon is often used for connectors that require additional mechanical strength and durability. Nylon connectors can generally withstand temperatures of up to 120°C and offer good chemical resistance.
Pros: The primary benefit of nylon is its robustness and resistance to wear and tear, making it suitable for harsh environments. Nylon connectors also provide excellent insulation and can be used in both indoor and outdoor applications.
Cons: The cost of nylon connectors can be higher than PVC options, and they may not be as readily available in all markets.
Impact on Application: Nylon connectors are ideal for applications in industrial settings or outdoor environments where exposure to chemicals and extreme temperatures is common.
Considerations for International Buyers: Buyers should ensure that nylon connectors meet relevant standards such as UL 94 for flammability and consider local sourcing options to minimize lead times.
Summary Table of Material Selection for Wire Connectors
Material | Typical Use Case for Wire Connector | Key Advantage | Key Disadvantage/Limitation | Relative Cost (Low/Med/High) |
---|---|---|---|---|
Copper | Electrical panels, automotive wiring | Excellent conductivity | Susceptible to corrosion | Medium |
Aluminum | Overhead power lines, large installations | Lightweight, cost-effective | Higher electrical resistance | Low |
PVC Insulated | Household wiring, automotive | Good insulation, moisture resistance | Can become brittle over time | Low |
Nylon | Industrial settings, outdoor applications | Robust, chemical resistant | Higher cost, less availability | High |
This strategic material selection guide offers valuable insights for international B2B buyers, helping them make informed decisions based on performance, cost, and compliance with regional standards.
In-depth Look: Manufacturing Processes and Quality Assurance for wire connector
What Are the Main Stages of Manufacturing Wire Connectors?
The manufacturing of wire connectors involves a series of well-defined stages that ensure high-quality products are produced consistently. Understanding these stages is crucial for international B2B buyers looking to source reliable wire connectors.
1. Material Preparation
The first step in the manufacturing process is the preparation of raw materials. Wire connectors are typically made from metals like copper or brass, often plated with tin or nickel to enhance conductivity and prevent corrosion. In this stage, suppliers ensure that the raw materials meet specific quality standards, which may include checking for impurities and verifying the metal’s gauge.
2. Forming
Once the materials are prepared, they undergo forming processes. This can include stamping, which shapes the metal into the desired connector form. High-speed presses are often employed to ensure precision and efficiency. Other forming techniques may involve extrusion or forging, depending on the connector type. At this stage, manufacturers focus on achieving tight tolerances to ensure proper fit and functionality.
3. Assembly
The assembly stage involves putting together various components of the wire connectors. This could include inserting insulation, assembling terminals, and attaching contact points. Automated assembly lines are commonly used to enhance speed and reduce human error. It’s crucial at this stage to ensure that all components fit together correctly, as improper assembly can lead to connectivity issues in the final product.
4. Finishing
The finishing stage includes processes such as plating, coating, or applying insulation to the connectors. This not only enhances the connectors’ aesthetics but also provides additional protection against environmental factors. The finishing process must comply with industry standards to ensure durability and reliability, which is particularly important for connectors used in harsh conditions.
How Is Quality Assurance Implemented in Wire Connector Manufacturing?
Quality assurance is a critical aspect of the manufacturing process for wire connectors, ensuring that products meet both industry standards and customer expectations. For international buyers, understanding the quality assurance protocols can be a decisive factor in supplier selection.
What International Standards Should B2B Buyers Consider?
Several international standards govern the manufacturing and quality assurance of wire connectors:
-
ISO 9001: This standard focuses on quality management systems and is widely recognized globally. Manufacturers with ISO 9001 certification demonstrate their commitment to quality and continuous improvement.
-
CE Marking: In Europe, the CE mark indicates compliance with health, safety, and environmental protection standards for products sold within the European Economic Area.
-
API Standards: For connectors used in the oil and gas sector, API standards ensure safety and reliability under extreme conditions.
Understanding these certifications can help B2B buyers assess the credibility of potential suppliers.
What Are the Key Quality Control Checkpoints?
Quality control (QC) in wire connector manufacturing typically involves several checkpoints throughout the production process:
-
Incoming Quality Control (IQC): This involves inspecting raw materials upon arrival to ensure they meet specified standards before production begins.
-
In-Process Quality Control (IPQC): During manufacturing, regular checks are conducted to monitor processes and detect any deviations from quality standards. This can include monitoring machine settings and conducting visual inspections.
-
Final Quality Control (FQC): Once production is complete, finished products undergo rigorous testing to ensure they meet all specifications. This may involve electrical testing, tensile strength tests, and environmental simulations.
What Testing Methods Are Commonly Used for Wire Connectors?
B2B buyers should be aware of various testing methods used to ensure the reliability of wire connectors:
-
Electrical Testing: This checks the conductivity and resistance of the connectors, ensuring they perform as expected under load.
-
Mechanical Testing: Tests such as tensile strength and pull-out tests assess the physical integrity of the connectors.
-
Environmental Testing: Connectors are subjected to conditions such as temperature extremes, humidity, and exposure to chemicals to ensure they can withstand real-world applications.
How Can International Buyers Verify Supplier Quality Control?
For B2B buyers, particularly in regions like Africa, South America, the Middle East, and Europe, verifying the quality control measures of suppliers is essential. Here are some strategies:
Conducting Audits
Regular audits of suppliers can provide insight into their manufacturing processes and quality control systems. Buyers should request documentation of past audits and any corrective actions taken to address identified issues.
Requesting Quality Reports
Buyers should ask for detailed quality reports that outline testing results and compliance with international standards. These reports can serve as a valuable resource for assessing supplier reliability.
Utilizing Third-Party Inspections
Engaging third-party inspection services can provide an unbiased assessment of a supplier’s quality control measures. These inspections can be conducted at various stages of production, offering reassurance to buyers about the quality of the connectors being produced.
What Are the Quality Control Nuances for B2B Buyers in Different Regions?
When sourcing wire connectors from international suppliers, B2B buyers should be aware of regional quality control nuances. For instance:
-
Africa: Buyers should consider the local regulatory landscape, which may vary significantly between countries. Ensuring that suppliers comply with both local and international standards is vital.
-
South America: The importance of certifications like ANATEL (National Telecommunications Agency) for connectors used in telecommunications should be noted.
-
Middle East: Specific certifications may be required for connectors used in sectors such as oil and gas, which can differ from those in other regions.
-
Europe: In addition to CE marking, European buyers should ensure suppliers adhere to RoHS (Restriction of Hazardous Substances) regulations, which limit the use of specific hazardous materials.
By understanding these factors, B2B buyers can make informed decisions when selecting suppliers for wire connectors, ensuring they meet both quality and compliance requirements.
Practical Sourcing Guide: A Step-by-Step Checklist for ‘wire connector’
In the competitive landscape of B2B procurement, sourcing wire connectors effectively can make a significant difference in your project’s success. This practical sourcing guide provides a structured checklist to help international buyers—especially from Africa, South America, the Middle East, and Europe—navigate the complexities of acquiring quality wire connectors.
Step 1: Define Your Technical Specifications
Clearly outlining your technical requirements is the first step in sourcing wire connectors. This includes determining the appropriate wire gauge, connector type (e.g., butt connectors, ring terminals, quick connect terminals), and material specifications (such as tin-plated copper or brass). Knowing these details upfront helps you communicate effectively with suppliers and ensures compatibility with your existing systems.
Step 2: Research Potential Suppliers
Conduct thorough research to identify potential suppliers that specialize in wire connectors. Look for companies with a strong online presence, positive reviews, and a track record of reliability. Pay attention to suppliers that cater specifically to your region, as they may have better understanding of local standards and regulations.
- Actionable Tip: Utilize platforms like LinkedIn or industry-specific trade directories to find reputable suppliers.
Step 3: Evaluate Supplier Certifications
It’s crucial to verify that your chosen suppliers hold relevant certifications, such as ISO 9001 for quality management or UL certification for safety standards. These certifications indicate that the supplier adheres to industry best practices and can provide reliable products.
- Actionable Tip: Request copies of certification documents and check their validity through official channels.
Step 4: Request Product Samples
Before making a bulk purchase, request samples of the wire connectors to assess their quality. This step allows you to examine the product firsthand and evaluate factors like durability, insulation quality, and ease of use.
- Actionable Tip: Test the samples in real-world applications to ensure they meet your specific requirements.
Step 5: Compare Pricing and Terms
Once you have shortlisted potential suppliers, compare their pricing structures and terms of sale. Look beyond just the unit price; consider factors like shipping costs, payment terms, and bulk order discounts.
- Actionable Tip: Use a spreadsheet to track and compare these variables across different suppliers to make an informed decision.
Step 6: Assess After-Sales Support
Evaluate the level of after-sales support offered by suppliers. Reliable customer service can be invaluable, especially if you encounter issues with the products or need assistance with installation.
- Actionable Tip: Inquire about warranty policies, return procedures, and technical support availability.
Step 7: Establish Long-Term Relationships
Finally, consider the potential for building long-term relationships with your chosen suppliers. A trusted partnership can lead to better pricing, priority service, and collaboration on future projects.
- Actionable Tip: Maintain open communication with suppliers and provide feedback on their products and services to foster a positive relationship.
By following this checklist, international B2B buyers can navigate the procurement process for wire connectors more effectively, ensuring they secure high-quality products that meet their project requirements.
Comprehensive Cost and Pricing Analysis for wire connector Sourcing
What Are the Key Cost Components in Wire Connector Manufacturing?
When sourcing wire connectors, understanding the cost structure is essential for B2B buyers. The primary cost components include:
-
Materials: The choice of materials significantly impacts the overall price. Common materials used include PVC, tin-plated copper, and brass. Premium materials often result in higher durability and performance, but they also increase the cost.
-
Labor: Labor costs can vary widely depending on the region of production. In countries with lower labor costs, like some in Africa and South America, prices may be more competitive. However, regions with higher labor costs, such as parts of Europe, may lead to increased manufacturing expenses.
-
Manufacturing Overhead: This encompasses all indirect costs associated with production, such as utilities, rent, and administrative expenses. Efficient production processes can help minimize these costs.
-
Tooling: Initial tooling costs for custom designs can be significant. Buyers should consider whether they need standard or custom connectors, as custom tooling may add to upfront costs.
-
Quality Control (QC): Investments in quality control are vital to ensure product reliability. Higher QC standards often mean higher costs but can lead to lower total ownership costs due to decreased failure rates.
-
Logistics: Shipping costs can vary based on distance, shipping method, and volume. International buyers should factor in customs duties and potential delays in logistics.
-
Margin: Suppliers will include a profit margin in their pricing. Understanding the typical margins in your industry can help in negotiations.
How Do Price Influencers Affect Wire Connector Costs?
Several factors can influence the pricing of wire connectors:
-
Volume and Minimum Order Quantity (MOQ): Larger orders typically result in lower per-unit costs. Buyers should negotiate MOQs to align with their needs while maximizing cost-efficiency.
-
Specifications and Customization: Customized connectors that meet specific industry standards or unique applications will generally cost more than standard options. Clearly defining your requirements can lead to better pricing.
-
Material Quality and Certifications: Wire connectors that meet specific certifications (like UL or CE) may have higher prices due to the additional testing and compliance requirements. However, these certifications can enhance safety and performance, which may justify the cost.
-
Supplier Factors: The reputation and reliability of the supplier can impact pricing. Established suppliers may charge a premium but often provide better quality assurance and customer service.
-
Incoterms: The chosen Incoterms can affect pricing by determining who bears the cost and risk of shipping. Understanding terms like FOB (Free on Board) or CIF (Cost, Insurance, and Freight) is crucial for budgeting.
What Are the Best Practices for Negotiating Wire Connector Prices?
International B2B buyers can employ several strategies to optimize their sourcing of wire connectors:
-
Negotiate Based on Total Cost of Ownership (TCO): Rather than focusing solely on the purchase price, consider the TCO, which includes installation, maintenance, and potential failure costs. A higher initial price may lead to lower long-term costs if the product is more durable.
-
Understand Pricing Nuances for International Buyers: Currency fluctuations and international tariffs can affect pricing. Buyers from Africa, South America, the Middle East, and Europe should account for these factors in their budgets.
-
Leverage Supplier Relationships: Building strong relationships with suppliers can lead to better pricing and terms. Regular communication and feedback can enhance collaboration and lead to more favorable deals.
-
Stay Informed About Market Trends: Keeping abreast of industry trends and competitor pricing can give buyers leverage in negotiations. Market research can inform strategic purchasing decisions.
Conclusion
Understanding the comprehensive cost structure and pricing factors associated with wire connector sourcing is essential for international B2B buyers. By analyzing cost components, recognizing price influencers, and employing effective negotiation strategies, buyers can make informed decisions that align with their operational needs and budgetary constraints. Always remember to verify prices, as they can fluctuate based on market conditions and supplier practices.
Alternatives Analysis: Comparing wire connector With Other Solutions
Introduction: Why Consider Alternatives to Wire Connectors?
In the B2B landscape, especially for international buyers from regions like Africa, South America, the Middle East, and Europe, evaluating alternatives to wire connectors is crucial for making informed purchasing decisions. While wire connectors serve as essential components for establishing electrical connections, several alternative solutions exist that may offer enhanced performance, cost savings, or ease of implementation depending on the specific application. Understanding these alternatives allows buyers to optimize their projects and achieve greater efficiency.
Comparison Table of Wire Connector and Alternatives
Comparison Aspect | Wire Connector | WAGO Lever Nuts | Crimp Connectors |
---|---|---|---|
Performance | Reliable for moderate loads | Excellent for varying conductor sizes | Highly effective for solid connections |
Cost | $10 – $20 per pack (average) | $15 – $25 per pack (average) | $5 – $15 per pack (average) |
Ease of Implementation | Requires basic tools to install | Tool-free installation | Requires crimping tool |
Maintenance | Low maintenance | Minimal maintenance | Requires inspection for integrity |
Best Use Case | General electrical connections | Splicing wires in tight spaces | Permanent connections in automotive or industrial settings |
Detailed Breakdown of Alternatives
What Are WAGO Lever Nuts and Their Benefits?
WAGO Lever Nuts are a popular alternative that provides tool-free installation, making them an attractive option for those who prioritize speed and ease of use. They can accommodate multiple wire sizes and types, which enhances their versatility in various applications. However, they may come at a higher price point compared to traditional wire connectors, which could be a consideration for budget-conscious buyers. Additionally, their compact design makes them suitable for use in tight spaces, but they may not be as robust for heavy-duty applications.
How Do Crimp Connectors Compare in Terms of Reliability?
Crimp connectors are another viable alternative that offers a permanent solution for electrical connections. They provide excellent electrical conductivity and are typically more cost-effective than wire connectors. However, the installation process requires specific crimping tools, which may not be readily available to all users. Moreover, crimp connectors necessitate careful inspection to ensure the integrity of the connection, as improper crimping can lead to failures. This makes them more suitable for applications where long-term reliability is paramount, such as in automotive or industrial settings.
Conclusion: Choosing the Right Solution for Your Needs
When selecting between wire connectors and their alternatives, international B2B buyers must consider various factors, including performance, cost, ease of implementation, and the specific use case of the application. For projects requiring quick and versatile installations, WAGO Lever Nuts may be the best choice. Conversely, for those seeking a reliable, long-lasting connection, crimp connectors could provide the necessary durability. Ultimately, understanding the unique requirements of your project and the environments in which these connections will operate is key to making the right decision.
Essential Technical Properties and Trade Terminology for wire connector
What Are the Essential Technical Properties of Wire Connectors?
Understanding the technical properties of wire connectors is crucial for international B2B buyers, particularly in regions like Africa, South America, the Middle East, and Europe. Here are some of the most important specifications to consider:
What Materials Are Commonly Used in Wire Connectors?
Wire connectors are typically made from materials like copper, brass, or aluminum. Copper is favored for its excellent electrical conductivity, making it ideal for high-performance applications. Brass is often used in quick-connect terminals due to its corrosion resistance and durability. Aluminum connectors are lightweight and cost-effective but may have lower conductivity than copper.
How Does Wire Gauge Affect Connector Performance?
Wire gauge is a critical factor that indicates the thickness of the wire being used. Measured in AWG (American Wire Gauge), it influences both the current-carrying capacity and the mechanical strength of the connection. For instance, connectors designed for 10-22 AWG are versatile and can accommodate various applications, but buyers should ensure compatibility with their specific wire gauge to prevent overheating or failure.
What Is the Importance of Insulation in Wire Connectors?
Insulation materials such as PVC or nylon are crucial for preventing short circuits and ensuring safety. PVC is commonly used due to its cost-effectiveness and good electrical properties, while nylon offers higher resistance to heat and chemicals. Buyers should evaluate the environmental conditions their products will face to choose the appropriate insulation type.
How Do Connector Tolerances Impact Quality?
Tolerance refers to the allowable variation in dimensions and performance of wire connectors. High-quality connectors typically have tighter tolerances, ensuring better fit and performance. This is particularly important in high-stakes applications, such as in automotive or industrial settings, where connector failure can lead to significant operational disruptions.
What Is the Role of Temperature Ratings in Wire Connectors?
Each wire connector has a specified temperature rating, indicating the maximum operating temperature it can withstand without degrading. Connectors with higher temperature ratings are essential for applications in extreme environments, such as in the oil and gas industry. Buyers should always check these ratings to ensure reliability and safety in their specific applications.
What Are the Common Trade Terms Related to Wire Connectors?
Navigating the procurement process involves familiarizing oneself with industry jargon. Here are some common terms that B2B buyers should know:
What Is an OEM (Original Equipment Manufacturer)?
An OEM is a company that produces parts or equipment that may be marketed by another manufacturer. Understanding OEM relationships is vital for buyers looking for quality assurance and compatibility in wire connectors, especially when sourcing from different suppliers.
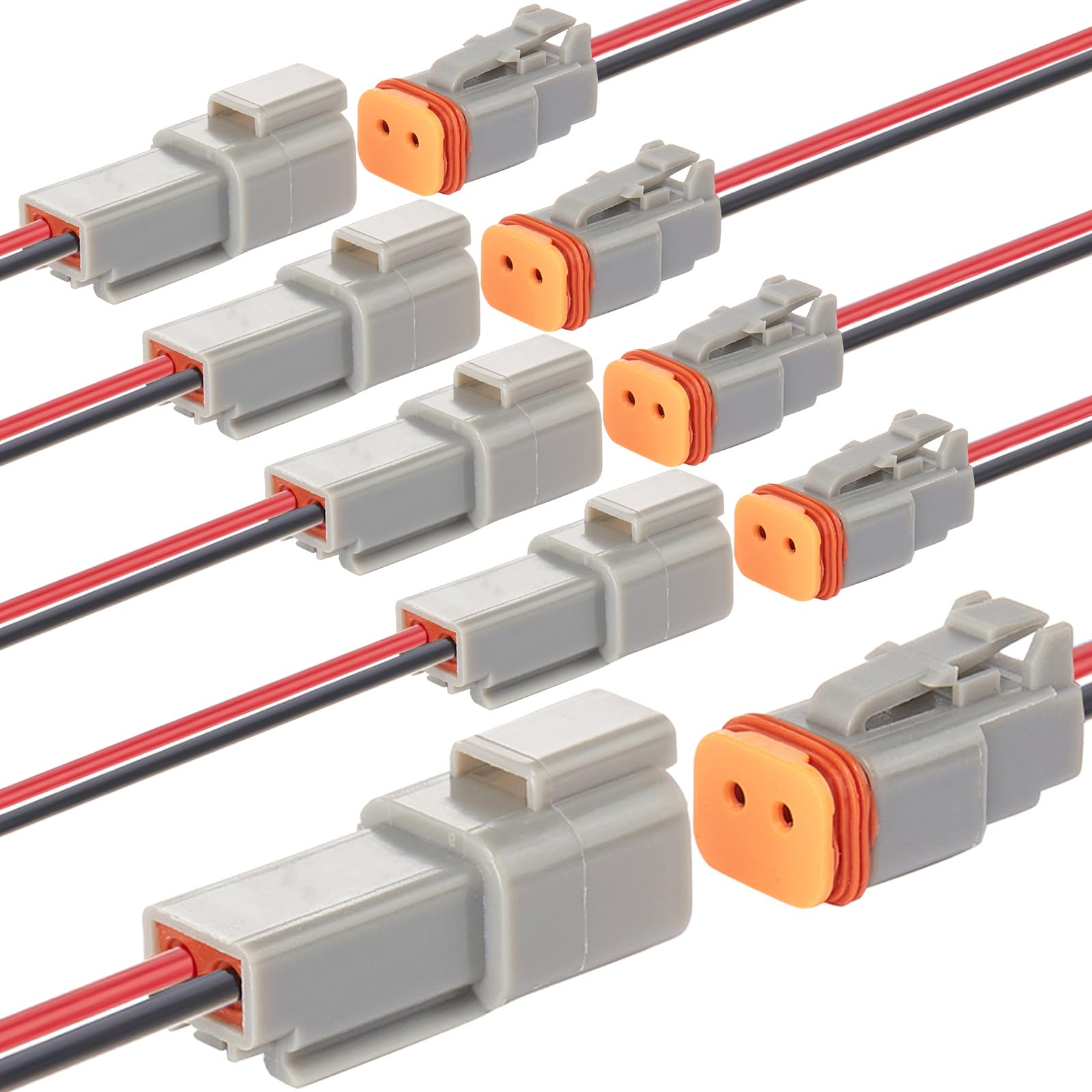
A stock image related to wire connector.
What Does MOQ (Minimum Order Quantity) Mean?
MOQ refers to the smallest quantity of a product that a supplier is willing to sell. For wire connectors, MOQs can significantly affect your purchasing strategy, particularly for smaller businesses or startups. Knowing the MOQ helps buyers budget effectively and manage inventory levels.
How Important Is an RFQ (Request for Quotation)?
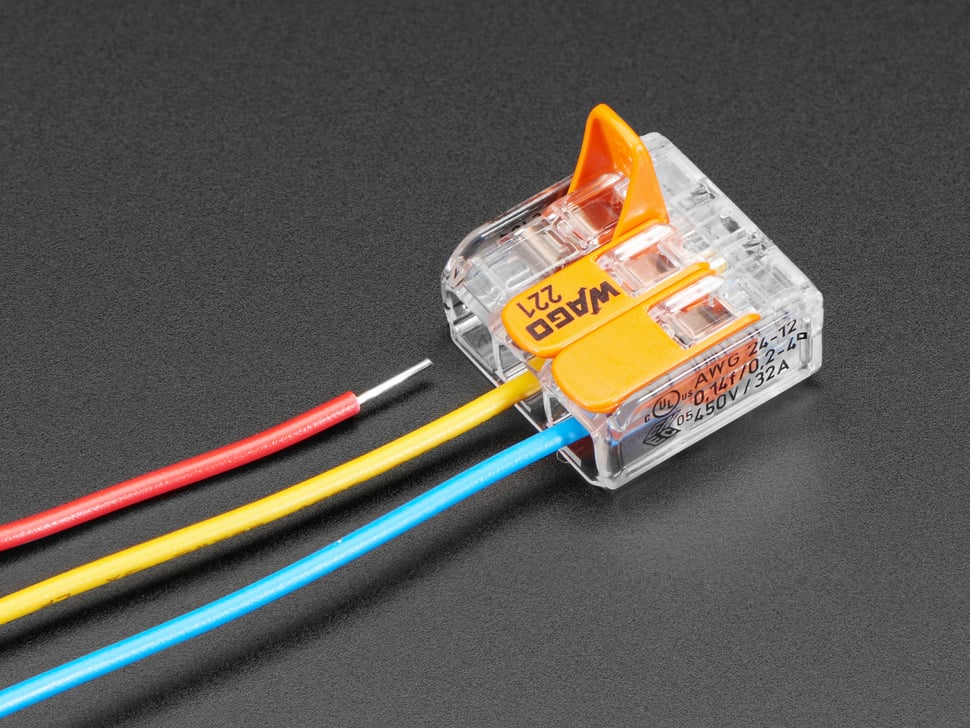
A stock image related to wire connector.
An RFQ is a document that solicits price bids from suppliers for specific products or services. Issuing an RFQ for wire connectors enables buyers to compare prices, quality, and terms from various suppliers, facilitating informed decision-making.
What Are Incoterms and Why Are They Important?
Incoterms (International Commercial Terms) are a set of predefined rules that define the responsibilities of buyers and sellers in international transactions. Understanding these terms is crucial for B2B buyers to clarify shipping, insurance, and tariffs related to wire connectors, thus avoiding potential disputes.
By grasping these technical properties and trade terminologies, international B2B buyers can make informed decisions, ensuring they select the right wire connectors for their specific applications.
Navigating Market Dynamics and Sourcing Trends in the wire connector Sector
What are the Current Market Dynamics and Sourcing Trends in the Wire Connector Sector?
The wire connector market is witnessing significant growth driven by the increasing demand for electrical connectivity solutions across various industries, including automotive, telecommunications, and renewable energy. As international B2B buyers, particularly from Africa, South America, the Middle East, and Europe, navigate these dynamics, understanding the emerging trends can provide a competitive edge.
One of the most notable trends is the rise of smart technologies and automation, which require sophisticated connectivity solutions. Innovations such as IoT devices are pushing manufacturers to develop more efficient, reliable, and compact wire connectors. Additionally, the demand for customized solutions tailored to specific applications is on the rise, compelling suppliers to adopt flexible manufacturing processes.
Another key market driver is the global push towards renewable energy sources, including solar and wind power. This transition necessitates high-quality wire connectors that can withstand extreme environmental conditions. B2B buyers should consider sourcing connectors that are specifically designed for outdoor and industrial applications, ensuring durability and performance.
Moreover, geopolitical factors and supply chain disruptions, exacerbated by the pandemic, have prompted buyers to diversify their sourcing strategies. Establishing relationships with multiple suppliers and considering local manufacturers can mitigate risks associated with supply chain vulnerabilities. Buyers should also leverage digital platforms for sourcing, which offer insights into supplier capabilities and product availability.
How Can Sustainability and Ethical Sourcing Impact Your B2B Buying Decisions?
Sustainability is becoming a paramount concern in the wire connector sector, with increasing pressure on manufacturers to minimize their environmental impact. B2B buyers must prioritize sourcing from suppliers who adhere to sustainable practices. This includes using eco-friendly materials, such as recyclable plastics and metals, and implementing energy-efficient manufacturing processes.
The importance of ethical supply chains cannot be overstated, particularly for buyers in regions such as Africa and South America, where sourcing from local suppliers can stimulate economic growth. Ensuring that suppliers comply with labor laws and provide fair working conditions is essential. Buyers should seek certifications like ISO 14001, which indicates a commitment to environmental management, and look for products that carry ‘green’ labels or certifications.
Furthermore, as consumers increasingly demand sustainability, aligning with eco-conscious suppliers can enhance a company’s reputation and marketability. Buyers should consider the long-term benefits of investing in sustainable products, which often lead to cost savings through reduced waste and improved efficiency.
What is the Evolution of Wire Connectors and Its Relevance to Today’s B2B Landscape?
The evolution of wire connectors has been marked by significant technological advancements. Initially, wire connectors were simple devices designed to join two or more wires. Over the decades, innovations such as crimping techniques, insulation materials, and waterproofing solutions have transformed the industry.
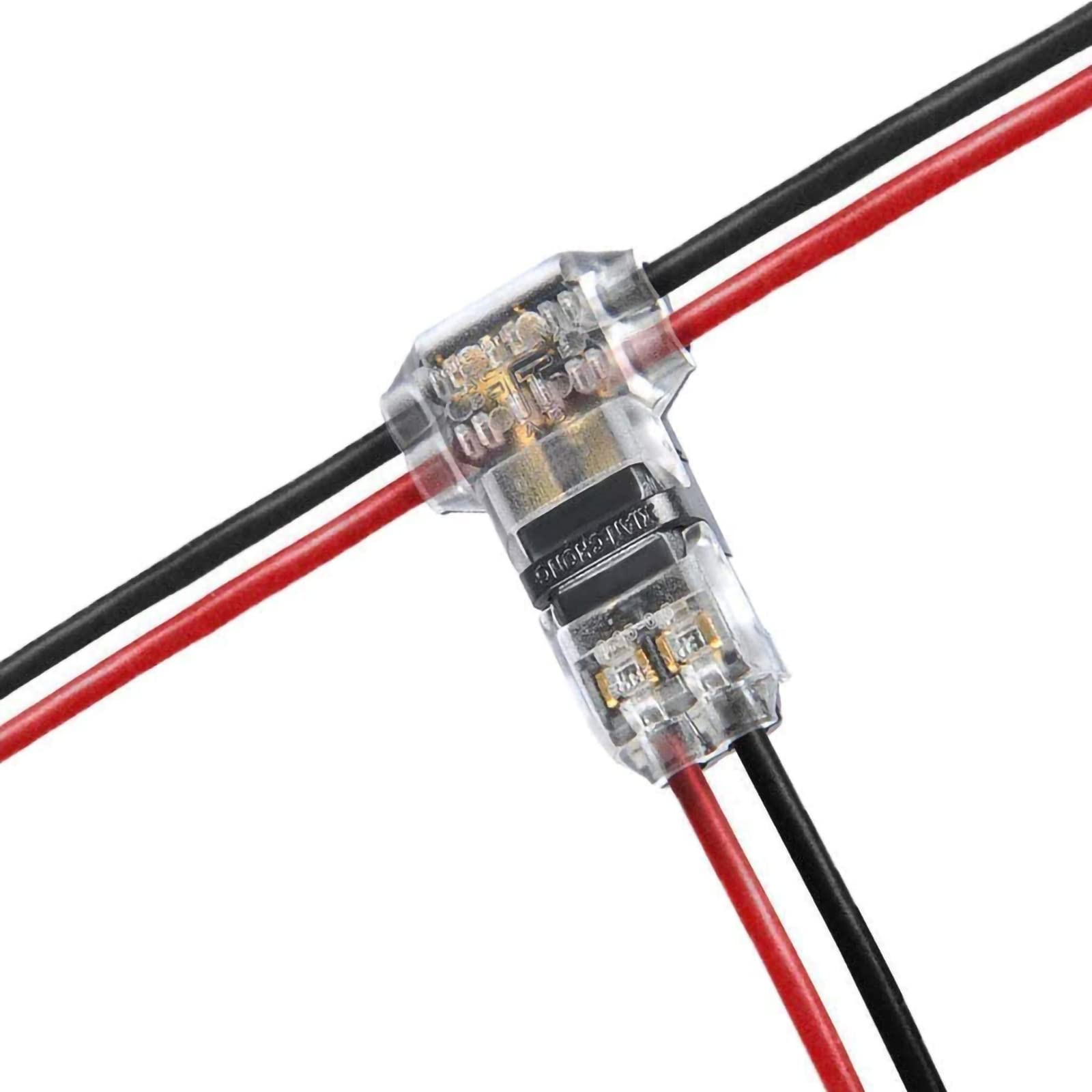
A stock image related to wire connector.
Today’s connectors are not only more reliable but also incorporate features that enhance safety and ease of use, such as quick-connect systems and modular designs. For B2B buyers, understanding this evolution is crucial, as it highlights the importance of choosing advanced connectors that meet the specific demands of modern applications.
As the industry continues to evolve, staying informed about the latest technologies and trends will enable buyers to make informed purchasing decisions that align with their operational needs and sustainability goals.
Frequently Asked Questions (FAQs) for B2B Buyers of wire connector
-
How do I choose the right wire connector for my application?
Selecting the appropriate wire connector hinges on several factors including wire gauge, insulation type, and intended application. For example, if your project involves high-temperature environments, consider connectors made from materials like nylon or heat-resistant PVC. Additionally, assess whether you need insulated or non-insulated connectors based on safety and operational requirements. Always consult technical specifications provided by manufacturers to ensure compatibility with your specific electrical systems. -
What are the most reliable types of wire connectors for industrial use?
For industrial applications, butt connectors, ring terminals, and quick connect terminals are highly regarded for their reliability and ease of use. Butt connectors provide a strong, secure join for wires, while ring terminals are excellent for making secure connections to studs or screws. Quick connect terminals allow for fast disconnection, ideal for equipment that requires frequent maintenance. When sourcing, prioritize connectors made from high-quality materials such as tin-plated copper or brass to enhance conductivity and durability. -
What should I consider when sourcing wire connectors internationally?
When sourcing wire connectors from international suppliers, consider factors like compliance with local regulations, quality assurance certifications, and the supplier’s reputation. Verify that the connectors meet international standards such as IEC or UL certifications, ensuring safety and reliability. Additionally, assess the supplier’s ability to provide customization options and their experience in handling exports to your region, which can significantly affect logistics and delivery times. -
How can I vet suppliers for wire connectors in Africa, South America, the Middle East, and Europe?
Vetting suppliers involves a thorough evaluation of their business practices, product quality, and customer service. Start by checking their certifications, customer reviews, and industry reputation. Request samples to assess product quality firsthand and inquire about their manufacturing processes. Establishing communication with other B2B buyers in your region who have experience with the supplier can also provide valuable insights into their reliability and performance. -
What are the minimum order quantities (MOQs) for wire connectors?
Minimum order quantities for wire connectors can vary significantly depending on the supplier and the type of connector. Typically, MOQs range from as low as 100 pieces for standard connectors to several thousand for custom or specialized types. Always discuss MOQs with your supplier early in negotiations to understand the implications for your inventory and cash flow, especially if you are a smaller business. -
What payment terms should I expect when purchasing wire connectors internationally?
Payment terms for international purchases can vary widely, but common options include upfront payment, partial payment upon order confirmation, and payment upon delivery. Some suppliers may offer credit terms, especially for established relationships. It’s essential to negotiate terms that align with your cash flow and risk management strategies. Utilizing secure payment methods like letters of credit or escrow services can further protect your transaction. -
How do I ensure quality assurance for wire connectors?
To ensure quality assurance, request certifications and test reports from suppliers that validate their products meet specified standards. Implementing a quality control process that includes receiving inspections and testing samples from each batch can help mitigate risks. Additionally, consider engaging third-party inspection services for larger orders, especially when sourcing from regions with varying manufacturing standards. -
What logistics considerations should I keep in mind when importing wire connectors?
When importing wire connectors, logistics considerations include shipping methods, customs clearance, and lead times. Evaluate whether air freight or sea freight is more cost-effective based on your urgency and budget. Ensure that the supplier provides all necessary documentation, such as invoices and packing lists, to facilitate smooth customs processing. Additionally, account for potential delays due to customs inspections or regulatory compliance in your planning.
Important Disclaimer & Terms of Use
⚠️ Important Disclaimer
The information provided in this guide, including content regarding manufacturers, technical specifications, and market analysis, is for informational and educational purposes only. It does not constitute professional procurement advice, financial advice, or legal advice.
While we have made every effort to ensure the accuracy and timeliness of the information, we are not responsible for any errors, omissions, or outdated information. Market conditions, company details, and technical standards are subject to change.
B2B buyers must conduct their own independent and thorough due diligence before making any purchasing decisions. This includes contacting suppliers directly, verifying certifications, requesting samples, and seeking professional consultation. The risk of relying on any information in this guide is borne solely by the reader.
Strategic Sourcing Conclusion and Outlook for wire connector
What Are the Key Takeaways for B2B Buyers in Wire Connector Sourcing?
In summary, strategic sourcing of wire connectors is essential for international B2B buyers aiming to enhance operational efficiency and reduce costs. Understanding product specifications, such as wire gauge and insulation type, enables buyers to select the most suitable connectors for their applications. Additionally, leveraging supplier relationships and negotiating bulk purchase agreements can lead to significant savings, especially in regions like Africa, South America, and the Middle East, where price sensitivity is higher.
How Can International Buyers Navigate the Wire Connector Market?
As you look towards the future, consider the growing demand for advanced wire connector solutions driven by technological advancements and increasing automation across industries. Buyers should stay informed about market trends, such as the shift toward environmentally friendly materials and the adoption of smart technologies, to ensure they remain competitive.
What Steps Should Buyers Take Next?
Engage with reputable suppliers, conduct thorough market research, and assess the total cost of ownership for wire connectors. By prioritizing these strategies, international B2B buyers can secure high-quality products that meet their specific needs while optimizing their supply chain. Embrace these insights to position your business for success in an evolving market landscape.