Discover the Complete NEMA Plug Chart for Global Sourcing (2025)
Introduction: Navigating the Global Market for nema plug chart
In an increasingly interconnected world, navigating the complexities of sourcing reliable electrical components, such as NEMA plugs, can pose significant challenges for international B2B buyers. Understanding the intricacies of the NEMA plug chart is essential for ensuring compatibility and safety in electrical applications. This guide provides a comprehensive overview of NEMA configurations, including both non-locking and locking plugs, their voltage and current specifications, and common applications across various industries.
For B2B buyers from Africa, South America, the Middle East, and Europe—such as Italy and South Africa—this resource is invaluable. It not only demystifies the technical jargon but also offers actionable insights on supplier vetting, cost considerations, and the implications of different configurations on your operations. By equipping yourself with knowledge about NEMA standards, you can make informed purchasing decisions that align with your business needs and regulatory requirements.
Whether you are sourcing components for residential use, industrial applications, or specialized machinery, this guide empowers you to confidently navigate the global market for NEMA plugs. By understanding the diverse options available and their specific applications, you can ensure seamless integration into your projects, ultimately enhancing efficiency and safety in your electrical systems.
Understanding nema plug chart Types and Variations
Type Name | Key Distinguishing Features | Primary B2B Applications | Brief Pros & Cons for Buyers |
---|---|---|---|
Non-Locking Plugs | Easy plug-in design; typically used in homes. | Residential appliances, light commercial settings. | Pros: Simple to use, widely available. Cons: Moderate safety; risk of accidental disconnection. |
Locking Plugs | Twist-and-lock mechanism for secure connections. | Industrial settings, outdoor equipment, generators. | Pros: High safety, prevents accidental disconnection. Cons: Higher cost, more complex installation. |
Straight Blade Configurations | Flat blade design, varying amperage and voltage. | General electrical connections, light machinery. | Pros: Versatile, compatible with many devices. Cons: Limited to lower voltage applications. |
Twist-Lock Configurations | Curved blades that lock into place; high durability. | Heavy machinery, high-vibration environments. | Pros: Excellent for high-load applications. Cons: Bulkier and may require specialized knowledge for installation. |
3-Phase Configurations | Multiple poles for complex power systems. | Large industrial machines, commercial power supply. | Pros: Efficient for high-power needs. Cons: Requires careful planning and installation expertise. |
What Are the Key Characteristics of Non-Locking Plugs?
Non-locking plugs are characterized by their straightforward plug-in design, making them suitable for residential and light commercial applications. They typically support voltage levels of 125V and current ratings of 15A to 20A. B2B buyers should consider their widespread availability and ease of use, which are beneficial for standard household appliances. However, the moderate safety level may not be ideal for environments where accidental disconnection is a concern.
How Do Locking Plugs Enhance Safety?
Locking plugs employ a twist-and-lock mechanism that secures the connection, making them ideal for industrial applications and outdoor environments where vibrations are common. These plugs generally support higher voltage and current ratings, such as 250V and 30A. For B2B buyers, the enhanced safety feature is crucial in preventing accidental disconnections, particularly in high-stakes settings. However, the increased cost and complexity of installation may require additional training or resources.
What Are the Advantages of Straight Blade Configurations?
Straight blade configurations are designed for versatility, accommodating various voltage and amperage requirements. Commonly used in general electrical connections, they are particularly suited for light machinery. B2B buyers benefit from their compatibility with many devices, making them a go-to choice for various applications. Nonetheless, their limitation to lower voltage levels may restrict their use in more demanding industrial scenarios.
Why Choose Twist-Lock Configurations for Heavy Machinery?
Twist-lock configurations feature curved blades that lock securely into place, providing exceptional durability and reliability in high-load applications. These connectors are particularly useful in environments prone to vibration, such as construction sites or factories. B2B buyers should weigh the benefits of high performance against the potential downsides, including the bulkier design and the need for specialized installation knowledge.
What Makes 3-Phase Configurations Essential for Industrial Use?
3-phase configurations are tailored for complex power systems, allowing for the efficient distribution of electricity to large industrial machines. They typically feature multiple poles and can handle high power requirements, making them indispensable in commercial power supply settings. While their efficiency is a significant advantage for B2B buyers, careful planning and installation expertise are necessary to ensure optimal functionality and safety in the workplace.
Key Industrial Applications of nema plug chart
Industry/Sector | Specific Application of NEMA Plug Chart | Value/Benefit for the Business | Key Sourcing Considerations for this Application |
---|---|---|---|
Manufacturing | Power supply for machinery and tools | Ensures compatibility and safety in high-load environments | Voltage and amperage ratings, locking vs. non-locking options, durability under vibration |
Construction | Electrical setups for construction sites | Provides secure connections for temporary power sources | Weather resistance, portability, compliance with local regulations |
Agriculture | Powering irrigation systems and agricultural machinery | Enhances operational efficiency and reduces downtime | Compatibility with local voltage standards, ruggedness, ease of installation |
Automotive | Charging stations for electric vehicles | Supports renewable energy initiatives and reduces emissions | Compliance with international charging standards, safety features |
Telecommunications | Powering communication towers and data centers | Ensures uninterrupted service and equipment reliability | Scalability options, environmental conditions, ease of maintenance |
How is the NEMA Plug Chart Used in Manufacturing?
In the manufacturing sector, the NEMA plug chart is essential for ensuring that machinery and tools are powered safely and efficiently. By utilizing the correct NEMA configurations, businesses can avoid electrical incompatibilities that may lead to equipment failures or safety hazards. International buyers, particularly from regions like Africa and South America, must consider voltage ratings and amperage capacities to match local electrical standards. Additionally, selecting locking configurations can mitigate risks associated with vibrations in industrial settings.
What Role Does the NEMA Plug Chart Play in Construction?
Construction sites often require temporary electrical setups for various tools and equipment. The NEMA plug chart facilitates the selection of connectors that provide secure and reliable power connections. This is crucial for ensuring worker safety and operational efficiency. For buyers in regions such as the Middle East and Europe, it’s vital to source plugs that are weather-resistant and compliant with local electrical codes. The ability to quickly deploy and dismantle electrical setups also adds value to construction projects.
How is the NEMA Plug Chart Beneficial for Agriculture?
In agriculture, the NEMA plug chart aids in powering irrigation systems and heavy machinery. Correctly matching plugs and receptacles ensures that these systems operate efficiently, reducing the risk of downtime during critical growing periods. Buyers from Africa, where agricultural efficiency is paramount, should focus on rugged, durable configurations that can withstand harsh environmental conditions. Additionally, understanding local voltage requirements is crucial for seamless integration into existing power systems.
How Does the NEMA Plug Chart Assist in the Automotive Sector?
The automotive industry increasingly relies on electric vehicle charging stations, where the NEMA plug chart plays a pivotal role. It helps ensure that the correct charging configurations are used, supporting initiatives for cleaner energy. For B2B buyers in Europe, familiarizing themselves with international charging standards is essential for compliance and interoperability. Sourcing plugs with safety features can further enhance the reliability of charging stations, making them a crucial investment for automotive businesses.
What is the Importance of the NEMA Plug Chart in Telecommunications?
In the telecommunications sector, the NEMA plug chart is vital for powering communication towers and data centers. A reliable power supply is critical to maintaining uninterrupted service and operational reliability. For international buyers, particularly in regions with varying electrical standards, it’s important to source plugs that can accommodate different voltage levels while ensuring ease of maintenance. The ability to scale power solutions effectively is also a key consideration for businesses looking to expand their telecommunications infrastructure.
3 Common User Pain Points for ‘nema plug chart’ & Their Solutions
Scenario 1: Difficulty in Selecting the Right NEMA Configuration for Equipment
The Problem: B2B buyers often face confusion when selecting the appropriate NEMA configuration for their equipment. For instance, a manufacturing company in South Africa may require a specific NEMA plug for machinery that operates at 250V and 30A. Without a clear understanding of the various configurations, such as NEMA 6-30 or L6-30, buyers risk purchasing incompatible connectors, leading to delays in operations and potential safety hazards.
The Solution: To effectively navigate this issue, buyers should start by familiarizing themselves with the NEMA plug chart and understanding the significance of each configuration. It is essential to gather detailed specifications of the machinery, including voltage and amperage requirements. By cross-referencing these specifications with the NEMA chart, buyers can determine the correct configuration. Additionally, engaging with suppliers who provide comprehensive product catalogs and technical support can help clarify any uncertainties. Regular training sessions for the procurement team on electrical standards and NEMA configurations can also enhance decision-making processes.
Scenario 2: Incompatibility with Local Electrical Standards
The Problem: International buyers, particularly from Europe or the Middle East, may encounter challenges when their equipment does not align with local electrical standards. For example, a company in Italy importing machinery from the United States may find that the NEMA plugs are incompatible with their existing outlets, which could be based on different voltage ratings and plug designs. This incompatibility can lead to increased costs due to the need for adapters or additional wiring, not to mention the risk of equipment malfunction.
The Solution: To mitigate this problem, buyers should conduct thorough market research before making purchases. This includes understanding local electrical codes and standards. When consulting the NEMA plug chart, buyers should look for configurations that are compatible with their local standards. Moreover, working with a local electrical engineer can provide insights into necessary modifications or adapters. Establishing relationships with suppliers who understand both the NEMA standards and local requirements can streamline the purchasing process and ensure compatibility.
Scenario 3: Misunderstanding Amperage Ratings Leading to Overloading Risks
The Problem: A common issue faced by B2B buyers is the misunderstanding of amperage ratings associated with NEMA configurations. For instance, a construction firm in South America may purchase a NEMA 5-15 plug rated for 15A but mistakenly use it to power a high-wattage tool that requires 30A. This oversight not only risks damaging the equipment but also poses significant safety hazards, including fire risks and equipment failure.
The Solution: To avoid such dangerous scenarios, it is crucial for buyers to be well-versed in the amperage ratings outlined in the NEMA plug chart. Each configuration clearly states its amperage limits; therefore, buyers must ensure that the equipment’s power requirements match or fall below the plug’s rating. Implementing a systematic review process before equipment procurement can help verify compatibility. Additionally, companies should invest in training for their technical teams on the implications of amperage ratings and the importance of adhering to specifications. Utilizing color-coded or labeled plugs and receptacles can also aid in preventing misuse and ensuring safe operation.
Strategic Material Selection Guide for nema plug chart
When selecting materials for NEMA plugs and receptacles, international B2B buyers must consider various factors that impact product performance, durability, and compliance with regional standards. Below, we analyze four common materials used in the manufacturing of NEMA plugs and their implications for different applications.
What Are the Key Properties of Thermoplastic Materials in NEMA Plugs?
Thermoplastic materials, such as Nylon and Polycarbonate, are widely used in NEMA plugs due to their excellent electrical insulation properties and resistance to impact. These materials can withstand temperatures ranging from -40°C to 85°C, making them suitable for various environmental conditions. Additionally, they exhibit good chemical resistance, which is essential for applications involving exposure to oils or solvents.
Pros & Cons:
– Pros: Lightweight, cost-effective, and easy to mold into complex shapes. They also provide good electrical insulation.
– Cons: Lower temperature resistance compared to thermosetting plastics, which may limit their use in high-temperature environments.
Impact on Application:
Thermoplastics are ideal for residential and light commercial applications, where the risk of extreme temperatures and heavy mechanical stress is minimal.
Considerations for International Buyers:
Buyers from regions like Africa and South America should ensure that the thermoplastic materials comply with local standards, such as IEC 60309 for industrial plugs.
How Do Metal Materials Enhance the Performance of NEMA Plugs?
Metal materials, particularly brass and stainless steel, are often used for the contacts and pins in NEMA plugs. These metals provide excellent conductivity and mechanical strength, which are crucial for high-load applications. Brass can handle temperatures up to 150°C, while stainless steel offers superior corrosion resistance, making it suitable for harsh environments.
Pros & Cons:
– Pros: High durability, excellent conductivity, and resistance to wear and corrosion.
– Cons: Heavier than plastic counterparts and may require additional surface treatments to prevent corrosion.
Impact on Application:
Metal components are essential in industrial settings where plugs are frequently connected and disconnected, such as in manufacturing or construction sites.
Considerations for International Buyers:
Buyers in Europe and the Middle East should verify that metal components meet ASTM or DIN standards for electrical connectors to ensure safety and reliability.
What Role Do Thermosetting Plastics Play in NEMA Plug Manufacturing?
Thermosetting plastics, such as Bakelite and epoxy resins, are used in applications requiring high thermal stability and mechanical strength. These materials can withstand temperatures exceeding 150°C and are resistant to deformation under stress.
Pros & Cons:
– Pros: Exceptional heat resistance and structural integrity, making them suitable for heavy-duty applications.
– Cons: More expensive and complex to manufacture compared to thermoplastics.
Impact on Application:
Thermosetting plastics are often used in locking NEMA configurations, where a secure connection is critical, such as in outdoor or industrial applications.
Considerations for International Buyers:
Buyers should consider the availability of thermosetting plastics in their regions and ensure compliance with safety standards relevant to high-temperature applications.
How Do Composite Materials Improve NEMA Plug Performance?
Composite materials, which combine plastic and metal properties, are increasingly being used in NEMA plugs. These materials offer a balance of strength, weight, and electrical insulation. They can withstand a wide temperature range and provide enhanced impact resistance.
Pros & Cons:
– Pros: Lightweight, strong, and resistant to various environmental factors.
– Cons: More expensive than traditional materials and can be more challenging to recycle.
Impact on Application:
Composites are particularly beneficial in applications where weight and durability are critical, such as in portable generators or outdoor equipment.
Considerations for International Buyers:
International buyers should assess the environmental regulations regarding composite materials in their regions, especially in Europe, where recycling standards are stringent.
Summary Table of Material Selection for NEMA Plugs
Material | Typical Use Case for NEMA Plug Chart | Key Advantage | Key Disadvantage/Limitation | Relative Cost (Low/Med/High) |
---|---|---|---|---|
Thermoplastic | Residential and light commercial | Lightweight and cost-effective | Lower temperature resistance | Low |
Metal (Brass/Stainless Steel) | Industrial applications | High durability and conductivity | Heavier and may require corrosion treatment | Medium |
Thermosetting Plastic | Heavy-duty and outdoor applications | Exceptional heat resistance | More expensive and complex to manufacture | High |
Composite | Portable generators and outdoor use | Strong and lightweight | More expensive and recycling challenges | Medium |
This analysis should guide international B2B buyers in making informed decisions regarding material selection for NEMA plugs, ensuring compliance with local standards and suitability for their specific applications.
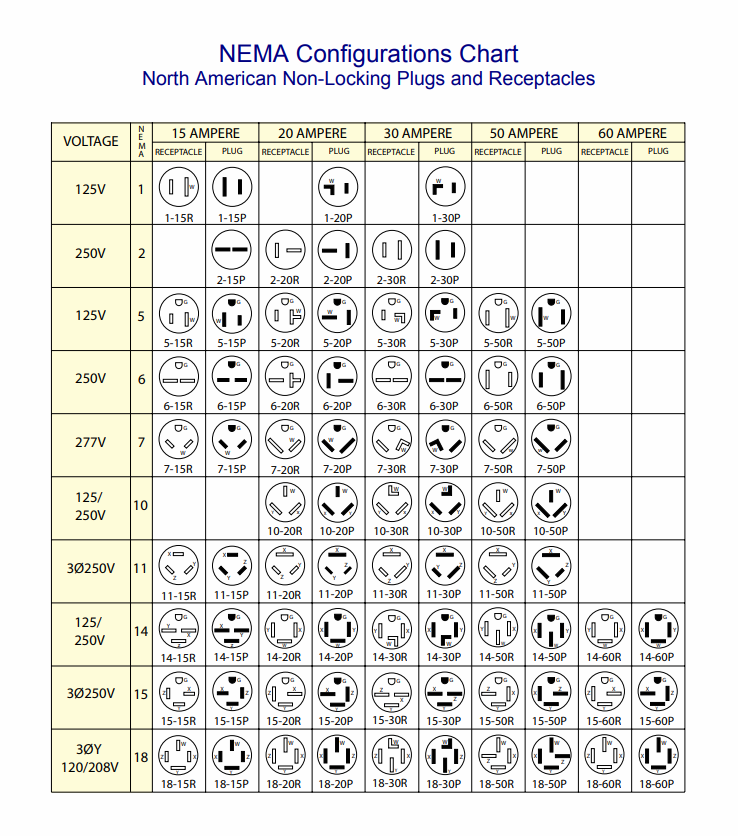
A stock image related to nema plug chart.
In-depth Look: Manufacturing Processes and Quality Assurance for nema plug chart
What Are the Main Stages in the Manufacturing Process of NEMA Plugs?
The manufacturing of NEMA plugs involves several critical stages that ensure the final product meets industry standards and customer expectations. The key stages include material preparation, forming, assembly, and finishing.
Material Preparation
The first step in the manufacturing process is the selection and preparation of materials. Common materials used in NEMA plugs include thermoplastics for the housing, copper or brass for the blades, and various alloys for the pins. Quality assurance starts here, as the materials must meet specific standards for conductivity, durability, and thermal resistance. Suppliers should provide certification for raw materials, ensuring they comply with international standards.
Forming Techniques
Once materials are prepared, the next stage involves forming the components. This typically includes:
- Injection Molding: Used for creating the thermoplastic housing of the plugs. Precision in this step is crucial to ensure that the final product fits perfectly with the receptacles.
- Stamping and Machining: These techniques are used to create the metal parts such as blades and pins. High-speed stamping machines can produce large volumes quickly while maintaining accuracy.
Manufacturers often use Computer Numerical Control (CNC) machines for machining to achieve high precision in dimensions, which is vital for electrical connectivity and safety.
Assembly Process
After forming, the components are assembled. This process may involve:
- Manual Assembly: Skilled workers assemble the plugs, ensuring that each part fits correctly and that the electrical connections are secure.
- Automated Assembly: In larger facilities, automated systems may be used to enhance speed and consistency.
Quality checks during assembly, such as visual inspections and electrical continuity tests, help catch any defects early in the process.
Finishing Techniques
The final stage involves finishing processes that enhance the plugs’ durability and appearance. This may include:
- Surface Treatment: Processes like plating or coating can prevent corrosion and enhance electrical performance.
- Final Inspections: Each finished product undergoes rigorous testing to ensure it meets the required specifications.
How is Quality Assurance Implemented in NEMA Plug Manufacturing?
Quality assurance (QA) in the manufacturing of NEMA plugs is a structured process that ensures products are consistently produced to meet specified requirements.
What International Standards Are Relevant for NEMA Plugs?
International standards play a crucial role in the manufacturing of NEMA plugs. Compliance with standards such as ISO 9001 ensures that manufacturers have a quality management system in place. This standard emphasizes continuous improvement and customer satisfaction, which are essential for B2B transactions.
Additionally, certifications such as CE marking for the European market and UL certification for North America indicate that the products meet safety and performance standards. These certifications can be critical for international buyers, particularly in regions like Africa, South America, and the Middle East, where regulatory compliance is necessary for market entry.
What Are the Key Quality Control Checkpoints?
Quality control (QC) is integrated into various stages of the manufacturing process. Key checkpoints include:
- Incoming Quality Control (IQC): This involves inspecting raw materials upon arrival to ensure they meet the required specifications before production begins.
- In-Process Quality Control (IPQC): Ongoing inspections during the production process help identify defects early. Techniques such as statistical process control (SPC) may be used to monitor production metrics.
- Final Quality Control (FQC): Once the plugs are assembled, they undergo comprehensive testing. This may include electrical tests for continuity and insulation resistance, as well as mechanical tests for durability.
What Testing Methods Are Commonly Used for NEMA Plugs?
Various testing methods are employed to verify the performance and safety of NEMA plugs:
- Electrical Testing: This includes checking for continuity, insulation resistance, and load testing to ensure the plugs can handle specified voltages and currents without overheating.
- Mechanical Testing: Tests for mechanical strength, including pull tests and vibration tests, are conducted to ensure that the plugs can withstand physical stresses during use.
- Environmental Testing: Products may be subjected to extreme temperatures, humidity, and exposure to chemicals to assess their durability in different conditions.
How Can B2B Buyers Verify Supplier Quality Control?
B2B buyers, particularly those from diverse regions, should take several steps to verify the quality control processes of their suppliers:
-
Supplier Audits: Conducting on-site audits can provide insight into a manufacturer’s quality management systems and production processes. This can help buyers assess compliance with international standards.
-
Requesting Documentation: Buyers should ask suppliers for quality assurance documentation, including test reports, certifications, and compliance with relevant standards. This transparency is crucial for building trust.
-
Third-Party Inspections: Engaging third-party inspection services can provide an unbiased assessment of product quality. These services can conduct random checks at various stages of production to ensure compliance with specifications.
-
Understanding Certification Nuances: International buyers should be aware of the specific certifications that apply in their regions. For example, while CE marking may be crucial for the European market, UL certification may be more relevant for North American buyers.
Conclusion: Why Quality Assurance Matters for NEMA Plugs in International Trade
For international B2B buyers, understanding the manufacturing processes and quality assurance measures associated with NEMA plugs is vital. High-quality plugs not only ensure safety and reliability but also enhance customer satisfaction and compliance with regulatory standards. By focusing on manufacturers with robust quality assurance processes, buyers can mitigate risks and ensure that their electrical connections are secure and effective.
Practical Sourcing Guide: A Step-by-Step Checklist for ‘nema plug chart’
In today’s global marketplace, sourcing the right electrical components, such as NEMA plugs, is crucial for ensuring compatibility and safety in electrical systems. This guide provides a step-by-step checklist to assist international B2B buyers, particularly from Africa, South America, the Middle East, and Europe, in effectively procuring NEMA plug charts tailored to their operational needs.
Step 1: Define Your Technical Specifications
Understanding your technical requirements is the first step in sourcing NEMA plugs. Identify the voltage and amperage needs for your applications, as well as whether you require locking or non-locking configurations. This clarity will help you narrow down your options and ensure you purchase components that meet your operational standards.
Step 2: Research NEMA Configurations Relevant to Your Industry
Different industries utilize various NEMA configurations. For example, residential applications often use NEMA 5-15, while industrial settings may require configurations like L14-30. Familiarize yourself with the specific configurations that align with your equipment and operational environment to avoid compatibility issues.
Step 3: Evaluate Potential Suppliers
Before committing to a supplier, it’s crucial to conduct thorough evaluations. Look for suppliers with a proven track record in your industry and region. Request company profiles, case studies, and references from previous buyers to gauge their reliability and product quality.
- Check for Industry Certifications: Ensure that the supplier adheres to relevant industry standards and certifications, which can indicate a commitment to quality and safety.
- Assess Product Range: Evaluate whether the supplier offers a comprehensive selection of NEMA configurations to meet all your needs.
Step 4: Request Samples for Testing
Before making a bulk order, request samples of the NEMA plugs you intend to purchase. Testing the samples allows you to verify compatibility with your existing systems and assess the quality of the materials used. This step is essential to ensure that the products will perform reliably in your applications.
Step 5: Understand Pricing and Payment Terms
Pricing can vary significantly between suppliers, so it’s important to compare costs while considering the total value offered. Inquire about payment terms, discounts for bulk purchases, and any additional fees that may apply. Understanding the financial aspects will help you budget appropriately and avoid unexpected costs.
Step 6: Confirm Shipping and Delivery Options
Discuss shipping logistics with your chosen supplier. Ensure that they can deliver to your location and confirm the lead times for your orders. Knowing the shipping details upfront can help you plan your inventory and avoid disruptions in your operations.
Step 7: Establish a Communication Protocol
Effective communication is key to a successful supplier relationship. Establish clear lines of communication for order updates, quality concerns, and support. This will ensure that both parties are aligned throughout the procurement process and can address any issues that may arise promptly.
By following this practical sourcing guide, B2B buyers can confidently navigate the procurement of NEMA plug charts, ensuring they select the right products for their specific applications and operational requirements.
Comprehensive Cost and Pricing Analysis for nema plug chart Sourcing
What Are the Key Cost Components in NEMA Plug Chart Sourcing?
When sourcing NEMA plugs and receptacles, understanding the cost structure is crucial for B2B buyers. The primary cost components typically include:
-
Materials: Raw materials such as copper for blades, thermoplastics for housings, and rubber for insulation significantly impact the overall cost. Quality materials not only enhance durability but also influence safety standards.
-
Labor: The manufacturing process requires skilled labor, which varies by region. Labor costs can be higher in Europe compared to South America or Africa, affecting the final pricing.
-
Manufacturing Overhead: This includes expenses related to factory operations, utilities, and administrative costs. Efficient manufacturing processes can help reduce overheads and ultimately lower prices.
-
Tooling: Custom molds and tools for specific configurations can be a significant upfront investment. This is especially relevant for customized NEMA configurations, where tooling costs can be amortized over larger production runs.
-
Quality Control (QC): Ensuring compliance with international standards, such as UL and IEC certifications, necessitates rigorous QC processes. These additional checks contribute to the overall cost but are essential for maintaining product integrity.
-
Logistics: Transportation and warehousing costs also play a critical role. Factors like shipping methods (air vs. sea), distance, and tariffs can affect the final price, especially for international buyers.
-
Margin: Suppliers typically build a profit margin into their pricing. Understanding the average margins in the industry can help buyers negotiate better deals.
How Do Price Influencers Affect NEMA Plug Sourcing?
Several factors can influence the pricing of NEMA plugs and receptacles:
-
Volume and Minimum Order Quantity (MOQ): Larger orders often lead to significant discounts. Negotiating MOQ terms can help in reducing per-unit costs.
-
Specifications and Customization: Custom configurations or additional features (like weatherproofing or specific amperage ratings) can increase costs. Buyers should evaluate whether these enhancements justify the price increase.
-
Material Quality and Certifications: High-quality materials and certifications come at a premium but are essential for safety and compliance. Buyers must balance cost with the necessity for certified products, particularly in regulated markets.
-
Supplier Factors: The reputation and reliability of suppliers can influence price. Established suppliers with a track record of quality may charge more, but they also reduce risks associated with product failures.
-
Incoterms: The terms of shipping and delivery affect final costs. Buyers should choose Incoterms that align with their logistics capabilities and budget constraints.
What Are Effective Buyer Tips for NEMA Plug Sourcing?
For international B2B buyers, particularly in Africa, South America, the Middle East, and Europe, here are several actionable tips:
-
Negotiate Wisely: Always negotiate prices and terms. Understanding your supplier’s cost structure can provide leverage in discussions.
-
Assess Total Cost of Ownership (TCO): Consider not just the purchase price but also the costs associated with installation, maintenance, and potential failures. A cheaper product might lead to higher TCO if it fails to meet quality standards.
-
Stay Informed About Pricing Nuances: Currency fluctuations, local economic conditions, and international trade policies can affect pricing. Being aware of these factors can help buyers make informed decisions.
-
Build Long-term Relationships: Establishing long-term partnerships with suppliers can lead to better pricing and terms over time. Suppliers may offer loyalty discounts or prioritize orders for repeat customers.
Conclusion: Understanding NEMA Plug Pricing Dynamics
While the pricing of NEMA plugs and receptacles can vary widely, a thorough understanding of the cost components and influencing factors allows buyers to make informed decisions. By focusing on strategic sourcing practices and maintaining strong supplier relationships, B2B buyers can optimize their procurement processes and achieve cost efficiencies.
Alternatives Analysis: Comparing nema plug chart With Other Solutions
Understanding Alternatives for NEMA Plug Charts
When it comes to electrical connectivity solutions, the NEMA plug chart offers a standardized way to identify configurations and ensure compatibility among various devices. However, international B2B buyers should also consider alternative solutions that may better suit their specific operational needs and environments. This section will compare the NEMA plug chart against two viable alternatives: IEC (International Electrotechnical Commission) connectors and CEE (International Commission on the Rules for the Approval of Electrical Equipment) connectors.
Comparison Table of NEMA Plug Chart and Alternatives
Comparison Aspect | NEMA Plug Chart | IEC Connectors | CEE Connectors |
---|---|---|---|
Performance | Reliable for North America | High performance in global markets | Robust for industrial applications |
Cost | Moderate cost | Varies, generally higher | Higher upfront investment |
Ease of Implementation | Simple installation | Requires specific training | May need additional tools |
Maintenance | Low maintenance | Moderate maintenance needs | Low maintenance |
Best Use Case | Residential and light commercial | Global applications, versatile | Heavy-duty industrial settings |
What Are the Advantages and Disadvantages of IEC Connectors?
IEC connectors are widely recognized for their global applicability and high performance. They are standardized across many countries, making them a preferred choice for international businesses. The ability to use IEC connectors can facilitate easier international trade and equipment compatibility. However, the initial costs may be higher due to their advanced design and material quality. Additionally, the installation process may require specialized training to ensure proper usage and safety, which can be a barrier for some organizations.
How Do CEE Connectors Compare in Industrial Applications?
CEE connectors are specifically designed for high-load industrial environments. They feature a robust construction that can withstand harsh conditions, making them ideal for outdoor and heavy-duty applications. The unique locking mechanism provides additional safety, ensuring a secure connection even in high-vibration settings. However, the upfront investment can be significant, and the implementation might require specialized tools or adapters, which could complicate the installation process for smaller operations.
Conclusion: How to Choose the Right Electrical Connection Solution
When selecting an electrical connection solution, B2B buyers should consider their specific needs, including the operational environment, compatibility requirements, and cost constraints. The NEMA plug chart is an excellent choice for applications within North America, particularly for residential and light commercial uses. Conversely, IEC connectors are suitable for businesses operating on a global scale, while CEE connectors are better for heavy-duty industrial applications. By assessing these factors, buyers can make informed decisions that align with their operational goals and enhance overall efficiency.
Essential Technical Properties and Trade Terminology for nema plug chart
What Are the Key Technical Properties of NEMA Plugs?
Understanding the technical properties of NEMA plugs is crucial for B2B buyers, as these specifications directly influence the performance and safety of electrical systems. Here are some essential properties to consider:
1. Voltage Rating: What Voltage Levels Do NEMA Plugs Support?
NEMA plugs are designed to operate at various voltage levels, typically ranging from 125V to 600V. This rating indicates the maximum voltage that the plug can safely handle. For example, NEMA 5-15 is rated for 125V, while NEMA L6-30 is rated for 250V. Choosing the correct voltage rating is critical to ensure compatibility with your electrical systems and to prevent potential overloads that could lead to failures or hazards.
2. Current Rating: How Does Amperage Impact Electrical Connections?
The current rating, measured in amperes (A), specifies the maximum current a plug can safely conduct. Common ratings include 15A, 20A, 30A, and 50A. Higher amperage ratings are essential for industrial applications where equipment demands more power. Selecting plugs with appropriate current ratings ensures that your devices operate efficiently without risking overheating or electrical fires.
3. Number of Poles and Wires: Why Is Configuration Important?
NEMA plugs are categorized by the number of poles and wires, which determines how they connect to power sources. For instance, a 3-pole, 4-wire configuration (like NEMA L14-30) allows for both single-phase and three-phase systems, providing flexibility in applications. Understanding these configurations is vital for ensuring that plugs are suitable for specific equipment and operational requirements.
4. Material and Construction: What Materials Are Used in NEMA Plugs?
NEMA plugs are typically constructed from durable materials like thermoplastic or nylon, which offer resistance to heat and impact. The quality of materials affects the longevity and reliability of the plugs, making it essential to source from reputable manufacturers. Buyers should prioritize plugs that meet relevant safety standards, ensuring they are suitable for their intended environments, whether residential, commercial, or industrial.
What Trade Terminology Should B2B Buyers Know About NEMA Plugs?
Familiarizing yourself with industry terminology can streamline the purchasing process and improve communication with suppliers. Here are some common terms relevant to NEMA plugs:
1. OEM (Original Equipment Manufacturer): What Does It Mean for Buyers?
An OEM refers to a company that produces parts or equipment that may be marketed by another manufacturer. In the context of NEMA plugs, working with OEMs ensures that you receive high-quality components that meet specific design and performance standards. This relationship is crucial for maintaining equipment reliability and safety.
2. MOQ (Minimum Order Quantity): How Does This Affect Your Purchases?
MOQ is the smallest quantity of a product that a supplier is willing to sell. Understanding the MOQ is essential for budgeting and inventory management, especially for businesses that may not require large volumes of NEMA plugs. Negotiating MOQs can help you optimize your purchasing strategy, ensuring you have enough stock without overcommitting resources.
3. RFQ (Request for Quotation): Why Is This Important?
An RFQ is a document sent to suppliers requesting pricing information for specific products, such as NEMA plugs. This process helps buyers compare costs and terms from multiple suppliers, ensuring they get the best deal. Providing detailed specifications in your RFQ can lead to more accurate quotes and better procurement outcomes.
4. Incoterms: How Do They Influence International Trade?
Incoterms (International Commercial Terms) define the responsibilities of buyers and sellers in international transactions. Understanding these terms is essential for B2B buyers engaged in global sourcing of NEMA plugs, as they dictate who is responsible for shipping, insurance, and tariffs. Familiarity with Incoterms can significantly reduce the risk of misunderstandings during the import/export process.
By grasping these technical properties and trade terms, international B2B buyers can make informed decisions regarding NEMA plugs, ensuring they choose the right products for their specific electrical needs.
Navigating Market Dynamics and Sourcing Trends in the nema plug chart Sector
What Are the Current Market Dynamics and Key Trends Affecting NEMA Plug Chart Sourcing?
The global market for NEMA plugs and receptacles is experiencing significant growth, driven by increasing energy consumption and the need for safe electrical connections across various sectors. International B2B buyers, particularly from Africa, South America, the Middle East, and Europe, are witnessing a surge in demand for both non-locking and locking configurations due to their application in residential, commercial, and industrial sectors.
Emerging trends include the integration of smart technology in electrical systems, which necessitates advanced NEMA configurations capable of supporting higher voltage and current ratings. Additionally, the rise of renewable energy sources, such as solar and wind, is creating a need for specialized NEMA plugs that can handle varying electrical loads efficiently. Buyers should also consider regional compliance with electrical safety standards, as various markets may have specific requirements that impact sourcing decisions.
The ongoing shift towards automation in manufacturing processes is influencing the design and production of NEMA plugs, with a focus on enhancing connectivity and reducing downtime. This trend towards automation is particularly relevant for industries in South America and Africa, where investment in infrastructure is critical. Understanding these market dynamics will help buyers make informed sourcing decisions that align with their operational needs and regional compliance.
How Can B2B Buyers Ensure Sustainability and Ethical Sourcing in the NEMA Plug Sector?
Sustainability is becoming a core consideration for B2B buyers in the NEMA plug sector. The environmental impact of electrical components, from production to disposal, has prompted many organizations to prioritize ethical sourcing practices. Buyers should look for suppliers that adhere to recognized environmental standards and certifications, such as ISO 14001, which demonstrates a commitment to reducing ecological footprints.
Moreover, the use of sustainable materials in NEMA plug manufacturing is gaining traction. Buyers should consider suppliers that utilize recycled or eco-friendly materials, which can help minimize waste and reduce overall environmental impact. By prioritizing suppliers with ‘green’ certifications, businesses can enhance their corporate social responsibility profiles and appeal to environmentally conscious customers.
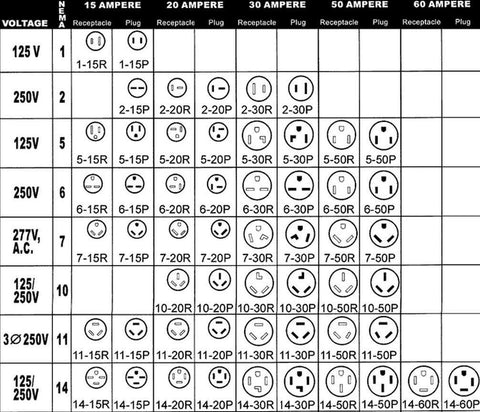
A stock image related to nema plug chart.
In addition, ethical supply chains are crucial for ensuring fair labor practices and transparency in sourcing. Buyers should conduct due diligence on potential suppliers to verify their labor practices and ensure compliance with international labor standards. This commitment not only fosters a positive brand image but also contributes to a more sustainable and responsible industry.
What Is the Historical Context of NEMA Plugs and Their Evolution?
The National Electrical Manufacturers Association (NEMA) was established in 1926, initially to standardize electrical components in the United States. The introduction of NEMA plug configurations provided a reliable and uniform means for connecting electrical devices, significantly enhancing safety and compatibility. Over the decades, as electrical systems became more complex and diverse, the NEMA plug chart evolved to include various configurations that cater to different voltage and current requirements.
Today, NEMA plugs are recognized not only in North America but also globally, as international markets increasingly adopt these standards for their electrical systems. The evolution of NEMA configurations has been driven by advancements in technology and the growing demand for safer, more efficient electrical connections in both residential and industrial applications. Understanding this historical context allows B2B buyers to appreciate the importance of selecting the right NEMA configuration for their specific needs.
Frequently Asked Questions (FAQs) for B2B Buyers of nema plug chart
-
How do I choose the right NEMA plug configuration for my equipment?
Choosing the right NEMA plug configuration requires understanding the voltage and amperage requirements of your equipment. Identify the power needs of your devices, typically specified in the user manual or on the equipment label. Consult the NEMA plug chart to match the voltage (e.g., 125V or 250V) and current (e.g., 15A, 20A, or higher) ratings. Ensure compatibility with existing receptacles and consider the application environment; for instance, industrial settings may require locking configurations for safety against vibrations. -
What is the best way to verify the quality of NEMA plugs from suppliers?
To verify the quality of NEMA plugs, request certifications such as UL (Underwriters Laboratories) or CSA (Canadian Standards Association) marks, which indicate compliance with safety standards. Conduct supplier audits to assess manufacturing practices and quality control processes. Reviewing customer testimonials and seeking references can provide insights into the supplier’s reliability. Additionally, consider ordering samples for testing before committing to a larger purchase. -
What are the typical minimum order quantities (MOQs) for NEMA plugs?
Minimum order quantities (MOQs) for NEMA plugs can vary significantly among suppliers. Many manufacturers set MOQs ranging from 100 to 1,000 units, depending on the configuration and customization required. When sourcing internationally, it’s essential to discuss MOQs upfront to avoid unexpected commitments. Some suppliers may offer flexibility for bulk orders, while others may accommodate smaller orders at a higher price per unit, especially for custom configurations. -
How can I ensure the NEMA plugs meet my specific customization needs?
To ensure NEMA plugs meet your customization needs, clearly communicate your requirements to the supplier, including specifications like voltage, amperage, color, and branding. Request design samples or prototypes to evaluate before mass production. It’s beneficial to work with suppliers experienced in custom manufacturing to avoid pitfalls. Additionally, discuss lead times and costs associated with custom orders to align expectations with your project timeline and budget.
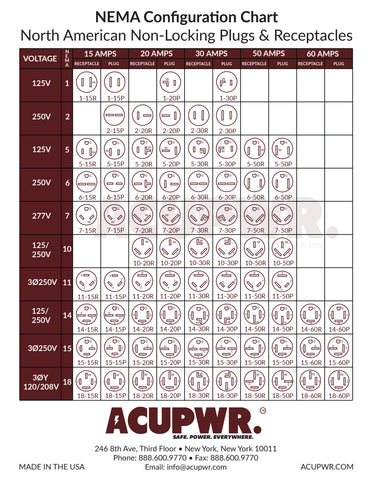
A stock image related to nema plug chart.
-
What payment terms should I consider when sourcing NEMA plugs internationally?
When sourcing NEMA plugs internationally, consider payment terms that provide security for both parties. Common arrangements include a deposit (e.g., 30-50%) before production and the balance upon delivery or inspection. Letter of credit (L/C) can also be a secure option, particularly for large orders. Always ensure that payment terms are clearly outlined in the contract to avoid disputes. Assess the supplier’s payment flexibility and reputation to establish trust. -
What logistics considerations are crucial when importing NEMA plugs?
Logistics considerations when importing NEMA plugs include selecting reliable shipping partners, understanding customs regulations, and planning for potential delays. Ensure compliance with import/export laws specific to electrical components in your region. Choose between air freight for speed or sea freight for cost-effectiveness based on your timeline. Additionally, factor in insurance coverage for high-value shipments and review the supplier’s experience with international shipping to mitigate risks. -
How do I assess the reliability of a supplier for NEMA plugs?
Assessing the reliability of a supplier for NEMA plugs involves researching their industry reputation, years in business, and customer reviews. Request references from existing clients, particularly those in your region or industry. Conduct a factory visit or virtual audit to evaluate production capabilities and quality control measures. Verify certifications and compliance with international standards to ensure the products meet safety and performance requirements. -
What are the common applications for different NEMA plug configurations?
Different NEMA plug configurations serve various applications. For instance, NEMA 5-15 is commonly used for standard household appliances, while NEMA 6-20 is suited for high-demand equipment like air conditioners. Locking configurations like NEMA L14-30 are ideal for generators and industrial equipment where secure connections are critical. Understanding these applications helps in selecting the right plug type for specific operational needs, ensuring both safety and functionality.
Important Disclaimer & Terms of Use
⚠️ Important Disclaimer
The information provided in this guide, including content regarding manufacturers, technical specifications, and market analysis, is for informational and educational purposes only. It does not constitute professional procurement advice, financial advice, or legal advice.
While we have made every effort to ensure the accuracy and timeliness of the information, we are not responsible for any errors, omissions, or outdated information. Market conditions, company details, and technical standards are subject to change.
B2B buyers must conduct their own independent and thorough due diligence before making any purchasing decisions. This includes contacting suppliers directly, verifying certifications, requesting samples, and seeking professional consultation. The risk of relying on any information in this guide is borne solely by the reader.
Strategic Sourcing Conclusion and Outlook for nema plug chart
What Are the Key Takeaways for B2B Buyers from the NEMA Plug Chart?
In summary, the NEMA plug chart serves as an essential resource for international B2B buyers seeking to make informed decisions regarding electrical connections. Understanding the distinctions between non-locking and locking configurations, along with their voltage and amperage ratings, is critical for selecting the right components for various applications. The strategic sourcing of NEMA plugs and receptacles not only ensures compatibility with existing systems but also enhances safety and operational efficiency in both industrial and commercial environments.
How Can Strategic Sourcing Improve Your Procurement Process?
Investing in strategic sourcing practices allows buyers from Africa, South America, the Middle East, and Europe to streamline their procurement processes. By collaborating with trusted suppliers and leveraging NEMA configuration knowledge, businesses can minimize risks associated with electrical compatibility and ensure the longevity of their equipment.
What’s Next for International B2B Buyers?
Looking ahead, the demand for reliable electrical components will continue to grow as industries expand and innovate. International buyers are encouraged to stay abreast of advancements in NEMA standards and configurations to ensure they are equipped with the best solutions for their operational needs. Take action now by evaluating your current sourcing strategies and exploring partnerships that align with your business goals to enhance performance and safety in your electrical applications.