Discover the Key Parts of an Electric Motor (2025)
Introduction: Navigating the Global Market for parts of an electric motor
Electric motors are essential components across a multitude of industries, yet sourcing the right parts of an electric motor can pose significant challenges for B2B buyers globally. Whether you are in Africa, South America, the Middle East, or Europe, understanding the intricacies of motor components—such as stators, rotors, bearings, and lead wires—can make a substantial difference in your procurement strategy. This comprehensive guide delves into the various types of electric motor components, their applications, and the latest technological advancements, enabling you to make informed purchasing decisions.
By exploring detailed insights into supplier vetting, cost considerations, and performance metrics, this guide equips international buyers with the knowledge needed to navigate the global market effectively. Each section is tailored to address the unique challenges faced by businesses in diverse regions, ensuring that you can identify reliable suppliers and optimize your supply chain. Moreover, we highlight key factors that influence motor efficiency and reliability, providing actionable advice that can enhance your operational performance and reduce long-term costs.
As you navigate through this guide, you’ll gain a deeper understanding of how to select the right electric motor parts that align with your business needs, ultimately empowering you to enhance productivity and drive innovation in your operations.
Understanding parts of an electric motor Types and Variations
Type Name | Key Distinguishing Features | Primary B2B Applications | Brief Pros & Cons for Buyers |
---|---|---|---|
Squirrel-Cage Rotor | Simple construction, robust design, high efficiency | HVAC systems, industrial machinery, pumps | Pros: Low maintenance, cost-effective. Cons: Limited speed control. |
Permanent Magnet Stator | Utilizes permanent magnets for high efficiency and compact size | Electric vehicles, robotics, consumer electronics | Pros: High torque density, energy-efficient. Cons: Higher initial cost. |
Inductor Stator | Uses electromagnetic induction, typically larger and heavier | Heavy machinery, large fans, compressors | Pros: Good performance under variable loads. Cons: Requires more space. |
Brushless DC Motor Components | No brushes, high efficiency, and low heat generation | Robotics, electric bicycles, medical devices | Pros: Extended lifespan, quiet operation. Cons: More complex control systems. |
Laminated Core Stator | Made of thin sheets to reduce energy losses | Electric generators, transformers | Pros: Improved efficiency, reduced noise. Cons: More expensive due to manufacturing process. |
What Are the Key Characteristics of a Squirrel-Cage Rotor?
The squirrel-cage rotor is recognized for its simple yet robust construction, which typically involves aluminum or copper bars connected at both ends by rings. This design allows for high efficiency and minimal maintenance, making it suitable for applications in HVAC systems, industrial machinery, and pumps. B2B buyers should consider the rotor’s cost-effectiveness and reliability, though they should note its limitations in speed control.
How Does a Permanent Magnet Stator Enhance Motor Performance?
Permanent magnet stators utilize strong magnets to create a magnetic field, resulting in compact and highly efficient designs. These stators are prevalent in electric vehicles, robotics, and consumer electronics, where space and energy efficiency are critical. While they offer high torque density and efficiency, the initial investment can be higher compared to traditional options, which buyers must weigh against long-term energy savings.
Why Choose an Inductor Stator for Heavy Machinery?
Inductor stators rely on electromagnetic induction to operate, making them ideal for heavy machinery and applications where variable loads are common. They are generally larger and heavier but provide excellent performance under varying operational conditions. Buyers should consider the need for more space and potential additional costs in exchange for their robust performance capabilities.
What Advantages Do Brushless DC Motor Components Offer?
Brushless DC motor components are designed without brushes, leading to high efficiency and reduced heat generation. These motors are often used in robotics, electric bicycles, and medical devices. The extended lifespan and quieter operation are significant advantages for B2B buyers; however, the complexity of control systems may require specialized knowledge or additional investment.
How Do Laminated Core Stators Improve Efficiency?
Laminated core stators consist of thin metal sheets stacked together to minimize energy losses due to eddy currents. This construction is particularly beneficial in electric generators and transformers, where efficiency is paramount. While these stators improve performance and reduce noise, the manufacturing process can increase costs, making it essential for buyers to evaluate their budget against the expected operational benefits.
Key Industrial Applications of parts of an electric motor
Industry/Sector | Specific Application of parts of an electric motor | Value/Benefit for the Business | Key Sourcing Considerations for this Application |
---|---|---|---|
Manufacturing | Conveyor Systems | Increased efficiency in material handling | Quality of rotor and stator materials to ensure durability and performance under load. |
Renewable Energy | Wind Turbines | Sustainable energy production with reduced costs | Sourcing high-quality permanent magnets and efficient stator designs for optimal energy conversion. |
Automotive | Electric Vehicles (EVs) | Enhanced performance and reduced carbon footprint | Compatibility with battery systems and lightweight materials for improved efficiency. |
HVAC Systems | Electric Fans and Compressors | Improved energy efficiency and reduced operational costs | Reliability of motor components under varying thermal conditions. |
Mining | Electric Drilling Machines | Enhanced operational efficiency and reduced downtime | Robustness of motor parts to withstand harsh environments and heavy loads. |
How Are Parts of an Electric Motor Utilized in Manufacturing?
In the manufacturing sector, electric motors are integral to conveyor systems that facilitate the movement of materials. The rotor and stator work together to provide the necessary torque for the conveyor belts, enhancing overall efficiency. International buyers must consider the quality of materials used in these components to ensure they can withstand continuous operation and heavy loads. Additionally, sourcing from suppliers with a strong reputation for reliability can mitigate risks associated with downtime.
What Role Do Electric Motor Parts Play in Renewable Energy?
In the renewable energy industry, particularly in wind turbines, the parts of electric motors—especially the stator and rotor—are crucial for converting kinetic energy into electrical energy. High-performance components reduce energy losses and improve the overall efficiency of energy production. Buyers in this sector should focus on sourcing high-quality permanent magnets and advanced stator designs that optimize energy conversion while also considering local regulations and sustainability practices.
How Are Electric Motors Applied in the Automotive Industry?
Electric vehicles (EVs) rely heavily on electric motors, where the rotor and stator are designed to deliver high torque and efficiency. These components are essential for the vehicle’s performance and contribute to a lower carbon footprint. B2B buyers should prioritize sourcing lightweight materials and ensuring compatibility with existing battery systems to enhance vehicle efficiency. Understanding regional automotive regulations and standards is also critical for international buyers.
Why Are Electric Motor Parts Important for HVAC Systems?
In HVAC systems, electric motors drive fans and compressors, playing a vital role in regulating indoor climates. The efficiency of these systems directly impacts energy consumption and operational costs. Buyers need to ensure that the motor components can perform reliably under varying thermal conditions and have a long lifespan. Sourcing from manufacturers who specialize in HVAC applications can provide added value through tailored solutions.
How Do Electric Motors Benefit the Mining Industry?
Electric drilling machines in the mining sector heavily depend on robust electric motors for efficient operation. The rotor and stator must be designed to handle extreme conditions, including dust, moisture, and heavy loads. International buyers should focus on sourcing durable motor components that can withstand these harsh environments, as well as ensuring that suppliers have a proven track record in the mining industry. This will help mitigate potential downtime and maintenance costs.
3 Common User Pain Points for ‘parts of an electric motor’ & Their Solutions
Scenario 1: Challenges with Stator Winding Insulation Failures
The Problem: One of the most common issues faced by B2B buyers of electric motor parts is the failure of stator winding insulation. This failure often results in costly downtime and maintenance. Buyers from diverse regions, especially in Africa and the Middle East, where operational conditions can be harsh, may find that insulation degrades due to thermal stress or electrical stress from transient voltages. Such failures not only impede the efficiency of the motor but can also lead to catastrophic motor failures, affecting production timelines and operational budgets.
The Solution: To mitigate stator winding insulation failures, buyers should focus on sourcing high-quality insulation materials that can withstand the specific operational environments of their motors. Consider investing in advanced insulation systems, such as those made from high-performance polymers or glass fiber composites, which offer superior thermal and electrical resistance. Additionally, implementing regular maintenance checks to monitor insulation integrity can prevent unexpected failures. Engaging with suppliers who provide detailed specifications and performance data on their insulation products will ensure that you make informed decisions that align with your operational requirements.
Scenario 2: Inadequate Rotor Performance Due to Poor Design
The Problem: B2B buyers often encounter issues with rotor performance that stem from inadequate design and material choices. This challenge is particularly relevant for buyers in South America and Europe, where the demand for high-efficiency motors is on the rise. A poorly designed rotor can lead to reduced torque output, inefficient power consumption, and increased wear and tear. This not only impacts the motor’s performance but also escalates operational costs and diminishes overall productivity.
The Solution: To address rotor performance issues, buyers should prioritize the selection of rotors that are designed with optimal magnetic properties and mechanical strength. This can be achieved by collaborating with manufacturers who specialize in high-precision rotor designs tailored to specific applications. Additionally, consider using rotors made from laminated silicon steel, which minimizes eddy current losses and enhances efficiency. Conducting thorough testing and validation of rotor performance under various operational conditions will also help in identifying potential inefficiencies before they become problematic.
Scenario 3: Sourcing Quality Bearings for Optimal Motor Functionality
The Problem: Another significant pain point for international B2B buyers is sourcing quality bearings that support the rotor effectively. Bearings are crucial for minimizing friction and ensuring smooth operation; however, buyers often struggle with selecting the right type, especially when faced with various options available in the market. This issue is particularly pronounced in regions like Africa and the Middle East, where environmental factors can influence bearing performance, leading to premature failures and increased maintenance costs.
The Solution: Buyers should adopt a strategic approach to sourcing bearings by focusing on those that are specifically designed for electric motor applications. Look for suppliers that offer bearings with enhanced sealing capabilities and corrosion resistance to withstand challenging environments. Implementing a predictive maintenance program that includes regular bearing inspections can also extend their lifespan and prevent unexpected failures. Furthermore, collaborating with suppliers who provide technical support and guidance on the optimal selection of bearing types will ensure that you make decisions that enhance motor reliability and efficiency.
Strategic Material Selection Guide for parts of an electric motor
What Are the Key Materials Used in Electric Motor Components?
When selecting materials for electric motor components, international B2B buyers must consider a variety of factors that influence performance, durability, and cost. Here, we analyze four common materials used in electric motors: copper, silicon steel, aluminum, and permanent magnets. Each material has unique properties that can significantly impact the motor’s efficiency and application suitability.
How Does Copper Influence Electric Motor Performance?
Copper is predominantly used for windings in electric motors due to its excellent electrical conductivity and thermal properties. It can handle high temperatures and provides low resistance, which is crucial for efficient energy transfer. However, copper is relatively expensive compared to other materials, which can increase the overall cost of the motor.
Pros: Copper’s high conductivity allows for smaller wire gauges, reducing weight and space requirements in motor designs. It also exhibits good corrosion resistance, enhancing the motor’s longevity.
Cons: The high cost of copper can be a limiting factor for budget-sensitive projects. Additionally, its weight may be a concern in applications where minimizing mass is critical.
Impact on Application: Copper is compatible with a variety of media and environments, making it suitable for diverse applications, from industrial machinery to electric vehicles.
Considerations for International Buyers: Compliance with international standards such as ASTM B170 (for copper wire) is essential. Buyers should also be aware of local sourcing options to mitigate costs.
What Role Does Silicon Steel Play in Motor Efficiency?
Silicon steel is commonly used for the cores of stators and rotors due to its magnetic properties. The addition of silicon improves the material’s electrical resistivity, reducing eddy current losses and enhancing overall efficiency.
Pros: Silicon steel allows for thinner laminations, which can significantly reduce weight and improve the magnetic circuit’s efficiency. This material can achieve high saturation levels, making it ideal for high-performance motors.
Cons: While effective, silicon steel can be more challenging to manufacture into precise shapes, potentially increasing production costs and complexity.
Impact on Application: This material is particularly effective in applications requiring high magnetic efficiency, such as transformers and high-speed motors.
Considerations for International Buyers: Buyers should consider the compliance with standards like DIN EN 10106 for electrical steel sheets. Availability may vary by region, impacting lead times.
How Does Aluminum Compare as a Motor Material?
Aluminum is often used as an alternative to copper for winding and as a structural material for motor housings. It is lighter and less expensive, making it attractive for cost-sensitive applications.
Pros: The lightweight nature of aluminum allows for easier handling and reduced overall weight of the motor. It also has good corrosion resistance, making it suitable for outdoor and humid environments.
Cons: Aluminum has lower conductivity compared to copper, which may necessitate larger wire gauges to achieve similar performance levels, potentially offsetting some weight savings.
Impact on Application: Aluminum is well-suited for applications where weight is a critical factor, such as in aerospace and automotive industries.
Considerations for International Buyers: Compliance with ASTM B800 (for aluminum wire) is important. Buyers should also evaluate local aluminum supply chains to ensure availability.
What Are the Advantages of Using Permanent Magnets in Motors?
Permanent magnets are essential for certain types of motors, such as brushless DC motors, where they provide a constant magnetic field. They are typically made from iron-based alloys or oxides.
Pros: Permanent magnets offer high energy density, enabling compact motor designs with excellent torque characteristics. They also eliminate the need for external power sources to create magnetic fields.
Cons: The cost of high-performance permanent magnets can be significant, particularly for rare-earth magnets. Additionally, they may have limitations in high-temperature applications.
Impact on Application: Permanent magnets are ideal for applications requiring high efficiency and compact size, such as consumer electronics and electric vehicles.
Considerations for International Buyers: Buyers should be aware of compliance with standards like ISO 9001 for quality management systems. Sourcing from regions with stable supply chains is crucial, especially for rare-earth materials.
Summary Table of Material Selection for Electric Motors
Material | Typical Use Case for parts of an electric motor | Key Advantage | Key Disadvantage/Limitation | Relative Cost (Low/Med/High) |
---|---|---|---|---|
Copper | Windings | Excellent electrical conductivity | High cost | High |
Silicon Steel | Stator and rotor cores | High efficiency and reduced eddy losses | Manufacturing complexity | Medium |
Aluminum | Windings and housing | Lightweight and cost-effective | Lower conductivity than copper | Medium |
Permanent Magnets | Brushless DC motors | High energy density and compact design | High cost and temperature limitations | High |
This strategic material selection guide provides essential insights for international B2B buyers looking to optimize their electric motor components for performance, cost, and compliance. Understanding these materials will facilitate informed purchasing decisions that align with specific application requirements.
In-depth Look: Manufacturing Processes and Quality Assurance for parts of an electric motor
What Are the Main Stages of Manufacturing Electric Motor Parts?
The manufacturing process for electric motor parts is intricate and requires precision at every stage. Understanding these processes can help international B2B buyers, particularly from Africa, South America, the Middle East, and Europe, make informed purchasing decisions.
1. Material Preparation: What Materials Are Used for Electric Motor Components?
The first step in manufacturing electric motor parts involves selecting the right materials. Common materials include:
- Copper and Aluminum: Used for windings and conductors due to their excellent conductivity.
- Silicon Steel: Essential for stator and rotor cores, providing the necessary magnetic properties.
- Insulating Materials: Rubber, enamel, and high-molecular compounds are used to prevent electrical short circuits.
Proper material selection is crucial for ensuring the performance and longevity of motor components. Buyers should inquire about the sources and specifications of these materials to ensure compliance with international standards.
2. Forming: How Are Electric Motor Parts Shaped?
Forming is a critical stage where raw materials are shaped into specific components. Key techniques include:
- Stamping and Die-Cutting: Used to create precise shapes for stator and rotor laminations. This process ensures minimal waste and high accuracy.
- Winding: Involves wrapping wire around the stator and rotor cores. Automated winding machines are often employed for consistency and efficiency.
- Casting and Machining: For components like end plates and brackets, casting methods (such as sand casting or die casting) are utilized, followed by machining for precision finishing.
Understanding the forming techniques can help buyers assess the manufacturing capabilities of suppliers and the potential quality of the components.
3. Assembly: What Are the Key Steps in Assembling Electric Motor Parts?
The assembly process combines all manufactured components into a functional electric motor. Key steps include:
- Component Integration: Stators, rotors, bearings, and other parts are meticulously assembled. This often involves the use of jigs and fixtures to maintain alignment and precision.
- Connection of Electrical Components: Lead wires are connected to the winding and other circuitry, ensuring proper electrical flow.
- Final Assembly: The motor is then enclosed in its housing, ensuring all parts are securely fixed.
Effective assembly techniques are essential for achieving high-performance motors. Buyers should inquire about the assembly processes and whether they utilize skilled labor or automation to ensure quality.
4. Finishing: How Is Quality Enhanced in the Final Stages of Production?
Finishing processes enhance the appearance and performance of electric motor parts. This stage may include:
- Surface Treatment: Processes such as anodizing or powder coating are applied to prevent corrosion and improve durability.
- Balancing and Testing: Rotors are balanced to minimize vibrations during operation, which is crucial for motor longevity.
Buyers should consider the finishing techniques employed by suppliers as they can significantly affect the performance and life expectancy of the motor.
What Quality Assurance Practices Are Essential for Electric Motor Parts?
Quality assurance (QA) is vital in ensuring that electric motor parts meet international standards and customer expectations. Understanding these practices can help B2B buyers in selecting reliable suppliers.
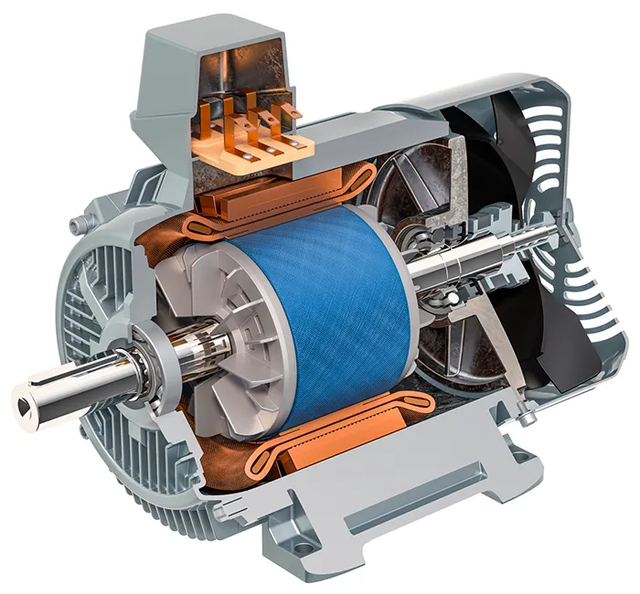
A stock image related to parts of an electric motor.
1. What Are the Relevant International Standards for Quality Assurance?
International standards, such as ISO 9001, ensure that manufacturers maintain consistent quality in their processes. Additionally, specific industry standards may apply, including:
- CE Marking: Indicates compliance with European health, safety, and environmental protection standards.
- API Standards: Relevant for motors used in the oil and gas sector.
Familiarizing oneself with these standards can help buyers ensure that the components they purchase are safe and reliable.
2. What Are the Key Quality Control Checkpoints?
Quality control (QC) checkpoints are critical in the manufacturing process. The following are common checkpoints:
- Incoming Quality Control (IQC): Involves inspecting raw materials upon arrival to verify compliance with specifications.
- In-Process Quality Control (IPQC): Continuous monitoring during the manufacturing process to catch defects early.
- Final Quality Control (FQC): A thorough inspection of the finished product to ensure it meets all specifications before shipment.
Buyers should ask suppliers about their QC processes and how they ensure quality at each stage.
3. What Common Testing Methods Are Used for Electric Motor Parts?
Testing is an integral part of quality assurance. Common testing methods include:
- Electrical Testing: Ensures that components function as intended and meet electrical specifications.
- Mechanical Testing: Assesses the durability and performance of parts under stress.
- Thermal Testing: Evaluates the performance of components under various temperature conditions.
Buyers should inquire about the specific tests conducted on the products they are purchasing to ensure reliability.
How Can B2B Buyers Verify Supplier Quality Control?
Verifying a supplier’s quality control processes is essential for international B2B buyers. Here are some effective methods:
1. What Should Buyers Look for in Supplier Audits?
Conducting supplier audits can help buyers gain insight into manufacturing practices. Key areas to assess include:
- Compliance with Standards: Ensure that the supplier adheres to relevant international standards.
- Documentation: Review quality control documentation, including inspection reports and testing results.
2. How Can Buyers Utilize Quality Reports and Third-Party Inspections?
Requesting quality reports from suppliers can provide transparency regarding their QC processes. Additionally, third-party inspections can offer an unbiased evaluation of the supplier’s capabilities. Buyers should look for certifications from reputable organizations to validate the supplier’s quality claims.
3. What Are the QC and Certification Nuances for International Buyers?
International buyers may face unique challenges regarding quality control and certification. It’s essential to understand:
- Regional Standards: Different regions may have specific standards and certifications that need to be met.
- Import Regulations: Familiarize yourself with import regulations in your country to ensure compliance with local laws.
By taking these factors into account, B2B buyers can effectively navigate the complexities of sourcing electric motor parts while ensuring high quality and compliance with international standards.
Practical Sourcing Guide: A Step-by-Step Checklist for ‘parts of an electric motor’
In the competitive landscape of international B2B procurement, sourcing parts for electric motors is a critical task that requires careful planning and execution. This guide provides a step-by-step checklist tailored for buyers from Africa, South America, the Middle East, and Europe, ensuring that you make informed decisions and secure quality components for your electric motor needs.
Step 1: Define Your Technical Specifications
Clearly outline the requirements for the electric motor parts you need. This includes specifications for the rotor, stator, bearings, and other components. Understanding the technical parameters, such as voltage, current, and efficiency levels, is vital for ensuring compatibility with your existing systems and achieving optimal performance.
- Consider application-specific needs: Different applications may require unique motor designs, such as AC versus DC motors or specific rotor types like squirrel-cage or permanent magnet rotors.
- Document performance standards: Ensure that the specifications align with industry standards to avoid compliance issues later.
Step 2: Research Potential Suppliers
Conduct thorough research to identify suppliers with a proven track record. Utilize industry directories, trade shows, and online platforms to compile a list of potential vendors.
- Look for specialization: Focus on suppliers who specialize in electric motor components, as they are more likely to provide high-quality products.
- Check geographical advantages: Consider suppliers located in your region to reduce shipping costs and lead times.
Step 3: Evaluate Supplier Certifications and Compliance
Verify that potential suppliers hold relevant certifications and comply with international standards. This step is crucial for ensuring the quality and reliability of the parts you source.
- Key certifications to look for: ISO 9001 for quality management, CE marking for European compliance, and other industry-specific certifications.
- Request documentation: Ask for certification documents and ensure they are up-to-date and valid.
Step 4: Analyze Pricing and Payment Terms
Compare pricing structures and payment options among different suppliers. This not only helps you find competitive rates but also ensures that you understand the total cost of ownership.
- Consider bulk discounts: Inquire about pricing for larger orders, which could lead to significant savings.
- Evaluate payment flexibility: Look for suppliers who offer favorable payment terms, such as extended payment periods or financing options.
Step 5: Request Samples and Test Quality
Before making a large order, request samples to assess the quality of the components. This step allows you to validate that the parts meet your specifications and performance expectations.
- Conduct performance tests: Evaluate samples under actual operating conditions to ensure reliability.
- Assess material quality: Pay attention to the materials used in construction, such as the type of wire for windings or the quality of the core material.
Step 6: Establish Communication and Support Channels
Ensure that the supplier has robust communication and support mechanisms in place. Clear communication is essential for addressing issues that may arise during the procurement process.
- Determine response times: Assess how quickly suppliers respond to inquiries and support requests.
- Inquire about after-sales support: Understand the warranty terms and support services offered post-purchase.
Step 7: Finalize Contracts and Agreements
Once you have selected a supplier, finalize contracts that outline all terms and conditions. This includes pricing, delivery schedules, and quality assurances.
- Include clear terms: Ensure that all aspects of the agreement, including dispute resolution processes, are clearly defined.
- Review legal implications: Consider consulting with a legal expert to ensure compliance with international trade regulations.
By following this comprehensive checklist, international B2B buyers can effectively source parts for electric motors, ensuring quality, compliance, and cost-effectiveness in their procurement processes.
Comprehensive Cost and Pricing Analysis for parts of an electric motor Sourcing
What Are the Key Cost Components for Electric Motor Parts?
When sourcing parts for electric motors, understanding the cost structure is crucial for international B2B buyers. The primary cost components include materials, labor, manufacturing overhead, tooling, quality control (QC), logistics, and profit margins.
-
Materials: The choice of materials significantly impacts costs. Common materials include copper for windings, silicon steel for cores, and various insulating materials. Prices can fluctuate based on global market conditions and availability, particularly for metals like copper and aluminum.
-
Labor: Labor costs vary by region and can affect the overall pricing of motor parts. Countries with lower labor costs may offer competitive pricing but could compromise on quality. Conversely, regions with higher labor costs often guarantee better craftsmanship and advanced manufacturing techniques.
-
Manufacturing Overhead: This encompasses costs associated with the operation of machinery, utilities, and facility maintenance. Efficient production processes can lower these costs, which can be advantageous for suppliers in regions with high operational expenses.
-
Tooling: Initial tooling costs for creating custom parts can be substantial. For standard parts, tooling expenses are typically amortized over larger production runs, reducing the per-unit cost. Buyers should consider the tooling costs when evaluating suppliers.
-
Quality Control: Ensuring that parts meet international standards often requires rigorous QC processes. These costs can add up, especially for specialized or high-performance motor components. Certifications such as ISO can also influence pricing.
-
Logistics: Shipping and handling costs can vary significantly based on the origin of the parts and the destination. Incoterms can greatly affect who bears these costs. For international buyers, understanding these terms is essential to avoid unexpected expenses.
-
Margin: Suppliers typically add a profit margin to cover their risks and operational costs. Margins can vary based on the supplier’s market position, product uniqueness, and competitive landscape.
How Do Price Influencers Affect Electric Motor Parts Sourcing?
Several factors influence the pricing of electric motor components that international buyers should consider:
-
Volume and Minimum Order Quantity (MOQ): Suppliers often provide discounts for larger orders. Understanding the MOQ can help buyers negotiate better pricing.
-
Specifications and Customization: Customized components may incur higher costs due to specialized manufacturing processes. Buyers should clarify specifications early in negotiations to avoid unexpected costs.
-
Material Quality and Certifications: Higher quality materials and certifications often lead to increased costs but can enhance the performance and reliability of motor parts. Buyers should weigh the benefits of investing in quality against budget constraints.
-
Supplier Factors: The reputation and reliability of suppliers can affect pricing. Established suppliers may charge more due to their proven track record, while new entrants might offer lower prices to gain market share.
-
Incoterms: Understanding Incoterms is vital for international transactions. These terms dictate shipping responsibilities and costs, impacting the total landed cost of parts.
What Buyer Tips Can Enhance Cost-Efficiency in Sourcing Electric Motor Parts?
To optimize sourcing strategies, buyers from Africa, South America, the Middle East, and Europe should consider the following:
-
Negotiation: Engage in proactive negotiations with suppliers. Understanding their cost structure can provide leverage when discussing pricing and terms.
-
Total Cost of Ownership (TCO): Evaluate the TCO, not just the initial purchase price. Consider factors such as maintenance, energy efficiency, and lifespan when assessing the value of components.
-
Pricing Nuances: Be aware of regional pricing differences and how local economic conditions can influence costs. Buyers should conduct market research to identify competitive pricing.
-
Long-Term Relationships: Building long-term relationships with suppliers can lead to better pricing, improved quality, and priority service.
-
Stay Informed: Keep abreast of market trends, material costs, and technological advancements. This knowledge can help buyers make informed decisions and negotiate effectively.
Disclaimer on Indicative Prices
Prices for electric motor parts can vary widely based on the aforementioned factors. Buyers should conduct thorough due diligence and consult multiple suppliers to obtain accurate and competitive pricing tailored to their specific needs.
Alternatives Analysis: Comparing parts of an electric motor With Other Solutions
Understanding Alternatives to Electric Motor Parts
In the realm of industrial applications, the components of electric motors—primarily the stator and rotor—are crucial for converting electrical energy into mechanical motion. However, various alternative technologies exist that can achieve similar outcomes, offering B2B buyers different pathways to meet their operational needs. This section will compare the key components of electric motors with alternative solutions such as hydraulic systems and pneumatic systems.
Comparison Table of Electric Motor Parts and Alternatives
Comparison Aspect | Parts of an Electric Motor | Hydraulic Systems | Pneumatic Systems |
---|---|---|---|
Performance | High efficiency (up to 95%) | Very high torque output | Fast response time |
Cost | Moderate initial investment | Higher due to fluid management | Lower initial cost |
Ease of Implementation | Requires electrical setup | Complex installation | Easier to set up |
Maintenance | Regular checks on windings | Requires fluid monitoring | Minimal maintenance |
Best Use Case | Precision machinery, robotics | Heavy machinery, construction | Assembly lines, tools |
Exploring Hydraulic Systems as an Alternative
Hydraulic systems utilize pressurized fluid to create motion, achieving high torque outputs, making them ideal for heavy machinery applications. The significant advantage of hydraulics is their ability to handle heavy loads efficiently. However, they come with higher costs associated with fluid management and system complexity. Maintenance can also be more demanding due to the need for fluid monitoring and potential leaks. In scenarios where high torque and load-bearing capacity are paramount, hydraulic systems can be an excellent choice.
Evaluating Pneumatic Systems as a Viable Solution
Pneumatic systems operate using compressed air to generate movement. These systems are known for their rapid response times and simplicity in design, making them suitable for assembly lines and tools that require quick actuation. Pneumatics typically have a lower initial cost compared to hydraulic systems and can be easier to implement. However, they may not provide the same level of force as electric motors or hydraulics, limiting their use in heavy-duty applications. Their maintenance requirements are minimal, which can lead to lower operational costs over time.
Conclusion: How to Choose the Right Solution for Your Needs
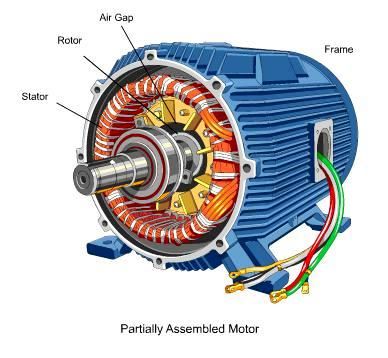
A stock image related to parts of an electric motor.
When considering alternatives to electric motor parts, B2B buyers should assess their specific operational needs, including performance requirements, budget constraints, and maintenance capabilities. Electric motors offer high efficiency and precision, making them suitable for applications where these factors are critical. Conversely, hydraulic systems excel in heavy-load scenarios, while pneumatic systems provide quick, cost-effective solutions for lighter applications. By evaluating these aspects, international buyers can make informed decisions that align with their business objectives and enhance their operational efficiency.
Essential Technical Properties and Trade Terminology for parts of an electric motor
What Are the Key Technical Properties of Electric Motor Parts?
Understanding the technical properties of electric motor components is essential for B2B buyers to ensure optimal performance, efficiency, and reliability in their applications. Here are some critical specifications to consider:
What Material Grades Are Commonly Used in Electric Motors?
-
Copper and Aluminum Wire
– Definition: Conductors made from copper or aluminum used for winding in motors.
– Importance: Copper is preferred for its superior conductivity, while aluminum is lighter and often more cost-effective. The choice of material directly affects efficiency, operational costs, and thermal performance. -
Silicon Steel for Cores
– Definition: A type of steel alloy that contains silicon, used for the magnetic cores of stators and rotors.
– Importance: Silicon steel enhances magnetic permeability and reduces energy losses due to hysteresis and eddy currents. This property is crucial for improving motor efficiency and extending service life. -
Insulation Class Ratings
– Definition: A classification system indicating the maximum temperature an insulating material can withstand.
– Importance: Selecting the right insulation class (e.g., Class B, F, or H) ensures that the motor can operate in specific environmental conditions without overheating, thus enhancing reliability and safety. -
Tolerance Levels
– Definition: The permissible limits of variation in a physical dimension or measured value.
– Importance: Tight tolerances are critical in manufacturing motor components to ensure proper fit and function, which can lead to reduced wear and increased efficiency in operation. -
Magnetic Flux Density
– Definition: The measure of the strength of the magnetic field within the motor.
– Importance: Higher magnetic flux density can improve torque and efficiency. Buyers should assess this property to ensure the motor meets their performance requirements.
Which Trade Terms Are Essential for B2B Buyers in the Electric Motor Industry?
Familiarity with industry jargon can streamline communication and negotiations in the B2B marketplace. Here are some essential terms:
What Does OEM Mean in the Electric Motor Industry?
- Original Equipment Manufacturer (OEM):
- Definition: A company that produces parts or equipment that may be marketed by another manufacturer.
- Importance: Understanding OEM relationships helps buyers identify quality standards and ensures they are sourcing components that meet their specifications.
What Is MOQ and Why Is It Important?
- Minimum Order Quantity (MOQ):
- Definition: The smallest quantity of a product that a supplier is willing to sell.
- Importance: Knowing the MOQ helps buyers plan their purchases effectively to avoid excess inventory or stockouts, particularly in international transactions.
How Does RFQ Impact Procurement?
- Request for Quotation (RFQ):
- Definition: A document sent to suppliers to request pricing and terms for specific products.
- Importance: An RFQ allows buyers to compare offers from different suppliers, ensuring they secure the best price and terms for their electric motor components.
What Are Incoterms and Their Significance?
- International Commercial Terms (Incoterms):
- Definition: A set of rules that define the responsibilities of buyers and sellers in international trade.
- Importance: Understanding Incoterms helps buyers clarify shipping responsibilities, risk management, and costs, facilitating smoother international transactions.
Why Is Understanding Lead Time Critical?
- Lead Time:
- Definition: The total time taken from placing an order to the receipt of goods.
- Importance: Recognizing lead times is vital for planning production schedules and ensuring timely delivery of components, especially in global supply chains.
By grasping these technical properties and trade terms, international B2B buyers can make informed decisions, optimize procurement processes, and enhance operational efficiency.
Navigating Market Dynamics and Sourcing Trends in the parts of an electric motor Sector
What Are the Current Market Dynamics and Key Trends in the Electric Motor Parts Sector?
The electric motor parts market is experiencing significant growth, driven by increased demand for energy-efficient solutions across various industries, including automotive, aerospace, and manufacturing. As global economies focus on reducing carbon emissions, electric motors are becoming pivotal in transitioning to sustainable energy systems. International B2B buyers, particularly from regions such as Africa, South America, the Middle East, and Europe, are witnessing an uptick in demand for high-performance motor components, such as stators and rotors. The rise of electric vehicles (EVs) has particularly influenced sourcing trends, with a shift towards components that enable higher efficiency and lower energy consumption.
Emerging technologies, such as IoT and AI, are transforming how manufacturers optimize motor performance and reliability. Smart motors equipped with sensors provide real-time data, enhancing predictive maintenance and reducing downtime. Additionally, there is a growing trend towards collaborative partnerships and direct sourcing from manufacturers to streamline supply chains and reduce costs. B2B buyers are increasingly prioritizing suppliers that can demonstrate not only quality but also innovation in design and materials.
How Is Sustainability Influencing Sourcing Decisions in the Electric Motor Parts Market?
Sustainability has become a critical factor for international B2B buyers when selecting suppliers in the electric motor parts sector. The environmental impact of manufacturing processes and the materials used in motor components is under scrutiny, pushing companies to adopt ethical sourcing practices. Buyers are increasingly seeking suppliers who can provide transparency in their supply chains, ensuring that materials are sourced responsibly and sustainably.
Certifications such as ISO 14001 for environmental management and adherence to REACH regulations for chemical safety are becoming essential for suppliers to demonstrate their commitment to sustainability. Moreover, the use of green materials, such as recycled metals and eco-friendly insulating materials, is gaining traction. By prioritizing suppliers with sustainable practices, buyers can not only enhance their brand reputation but also contribute to global efforts in reducing carbon footprints and promoting circular economies in the manufacturing sector.
What Historical Developments Have Shaped the Electric Motor Parts Market?
The evolution of electric motors dates back to the early 19th century, with significant advancements occurring throughout the 20th century. Initially, electric motors were predominantly used in industrial applications, but the advent of consumer electronics and electric vehicles has expanded their market reach. The introduction of more efficient materials and manufacturing processes has enabled the production of compact, high-performance motors suitable for various applications.
The shift towards electrification in transportation and renewable energy sources has further propelled the demand for advanced motor components. As a result, international B2B buyers are now presented with a diverse array of sourcing options that leverage modern technology and materials science, ensuring optimal performance and sustainability in electric motor parts.
Frequently Asked Questions (FAQs) for B2B Buyers of parts of an electric motor
-
How do I solve compatibility issues when sourcing electric motor parts?
When sourcing electric motor parts, ensure compatibility by closely reviewing the specifications of your existing motors. Identify key parameters such as voltage, current ratings, and physical dimensions of components like rotors and stators. Engaging with suppliers who can provide detailed technical documentation can also mitigate compatibility issues. Furthermore, consider requesting samples or prototypes to verify that the parts fit and function as intended before committing to larger orders. -
What is the best type of stator for high-efficiency electric motors?
The best type of stator for high-efficiency electric motors is one designed with laminated cores and advanced insulating materials, optimizing electromagnetic capabilities. Stators that employ distributed windings also tend to offer better efficiency due to lower losses. For applications requiring compact size and lightweight, printed circuit board (PCB) stators may be suitable, particularly in low-power devices. Always evaluate your specific application needs and consult with manufacturers to select the most effective stator type. -
What are the key considerations when vetting suppliers for electric motor parts?
Key considerations include the supplier’s industry reputation, compliance with international standards (like ISO), and experience in manufacturing electric motor components. Requesting certifications and quality assurance processes can provide insights into their operational standards. It’s also beneficial to check references from other clients and assess their ability to meet delivery timelines and customization requests. Conducting factory visits or audits, if feasible, can further ensure that the supplier aligns with your quality expectations. -
How can I customize electric motor parts to meet specific requirements?
Customization of electric motor parts can be achieved by working closely with your supplier to discuss your specific requirements, such as size, material, and performance specifications. Many manufacturers offer design services that can help tailor components to fit unique applications. Be prepared to provide detailed drawings or prototypes and discuss potential impacts on lead times and costs, as custom orders may require longer production periods and higher minimum order quantities (MOQs).
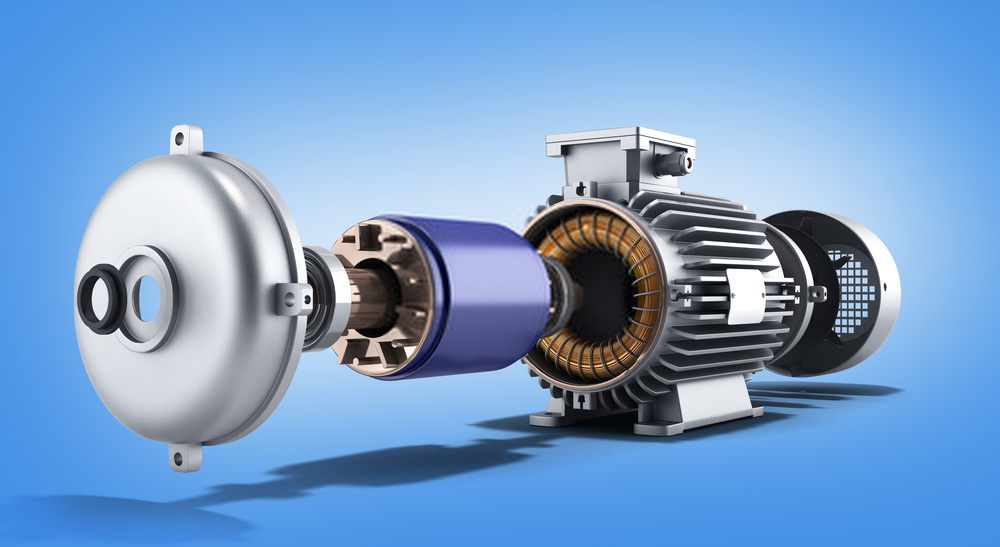
A stock image related to parts of an electric motor.
-
What are the typical minimum order quantities (MOQs) for electric motor parts?
MOQs for electric motor parts can vary significantly based on the supplier and the complexity of the components. Generally, standard components may have lower MOQs, while customized parts can require higher quantities. It’s crucial to communicate your needs with potential suppliers to understand their MOQ policies. Some suppliers might offer flexibility in MOQs for initial orders or prototypes, which can be beneficial for businesses looking to test new products without committing to large volumes. -
What payment terms should I negotiate with suppliers of electric motor parts?
When negotiating payment terms with suppliers, aim for conditions that balance risk and cash flow. Common terms include a deposit upfront with the balance due upon delivery or net 30-60 days after receiving the goods. Consider discussing payment methods, including letters of credit or escrow services, especially for larger orders or when dealing with new suppliers. Clear communication about payment schedules can help build trust and ensure a smooth transaction process. -
How do I ensure quality assurance (QA) for electric motor parts sourced internationally?
To ensure quality assurance for internationally sourced electric motor parts, establish clear specifications and quality standards before placing orders. Request detailed quality control processes from suppliers, including inspection protocols and testing certifications. Third-party quality audits can also provide independent verification of product quality. Additionally, consider implementing a return policy for defective parts, which can serve as an added layer of assurance in your procurement process. -
What logistics considerations should I keep in mind when importing electric motor parts?
Logistics considerations include understanding shipping regulations, customs duties, and import tariffs in your country. Work with suppliers to determine the most efficient shipping methods, taking into account factors like cost, speed, and reliability. It’s also important to coordinate logistics with your production timelines to avoid delays. Consider partnering with a freight forwarder who specializes in your industry, as they can provide valuable insights and streamline the shipping process for international orders.
Important Disclaimer & Terms of Use
⚠️ Important Disclaimer
The information provided in this guide, including content regarding manufacturers, technical specifications, and market analysis, is for informational and educational purposes only. It does not constitute professional procurement advice, financial advice, or legal advice.
While we have made every effort to ensure the accuracy and timeliness of the information, we are not responsible for any errors, omissions, or outdated information. Market conditions, company details, and technical standards are subject to change.
B2B buyers must conduct their own independent and thorough due diligence before making any purchasing decisions. This includes contacting suppliers directly, verifying certifications, requesting samples, and seeking professional consultation. The risk of relying on any information in this guide is borne solely by the reader.
Strategic Sourcing Conclusion and Outlook for parts of an electric motor
How Can Strategic Sourcing Enhance Your Electric Motor Component Procurement?
In conclusion, strategic sourcing plays a pivotal role in the procurement of electric motor components, such as rotors, stators, bearings, and winding materials. By understanding the distinct characteristics and functions of these components, international B2B buyers can make informed decisions that optimize performance and reduce costs. Leveraging advanced materials and manufacturing techniques not only enhances the efficiency of electric motors but also aligns with sustainability goals, which is increasingly important in markets across Africa, South America, the Middle East, and Europe.
What Should International Buyers Focus on for Future Procurement?
As the demand for electric motors continues to grow, focusing on high-quality suppliers that adhere to international standards can significantly impact your operational efficiency. Buyers should prioritize partnerships with manufacturers that offer innovative solutions, such as enhanced insulation materials and optimized rotor designs, to ensure long-term reliability and performance.
Why Act Now?
With the electric motor market evolving rapidly, now is the time to reassess your sourcing strategies. By investing in quality components and fostering strong supplier relationships, you position your business for success in an increasingly competitive landscape. Embrace the future of electric motor technology—strategize your sourcing today for a more sustainable and efficient tomorrow.