Discover Top Benefits of Choosing a Plastic Fabrication Company (2025)
Introduction: Navigating the Global Market for plastic fabrication company
Navigating the global market for a plastic fabrication company can be a daunting challenge for international B2B buyers, particularly those operating in diverse regions like Africa, South America, the Middle East, and Europe. The complexity of sourcing high-quality plastic products that meet specific industry standards and regulations can hinder operational efficiency. This guide serves as a comprehensive resource, addressing key aspects such as the various types of plastic fabrication processes, their applications across multiple industries, and critical supplier vetting criteria to ensure quality and reliability.
In addition, we delve into the cost considerations associated with plastic fabrication, empowering buyers to make informed financial decisions. By understanding the nuances of plastic materials and fabrication methods—including injection molding, extrusion, and CNC machining—international buyers will be better equipped to identify the right suppliers that align with their operational needs.
This guide not only provides actionable insights but also equips B2B buyers with the knowledge to navigate potential challenges and capitalize on opportunities in the plastic fabrication market. Whether you are based in South Africa, Nigeria, or elsewhere, our goal is to enhance your purchasing process, ensuring that you choose suppliers who can deliver innovative and customized plastic solutions tailored to your business requirements.
Understanding plastic fabrication company Types and Variations
Type Name | Key Distinguishing Features | Primary B2B Applications | Brief Pros & Cons for Buyers |
---|---|---|---|
Custom Plastic Fabrication | Tailored solutions, unique designs, specific requirements | Aerospace, automotive, medical devices | Pros: Highly specialized, meets specific needs. Cons: Longer lead times, potentially higher costs. |
Plastic Extrusion Companies | Continuous production, high-volume output, standard shapes | Packaging, construction, consumer goods | Pros: Cost-effective for large orders. Cons: Limited design flexibility compared to custom fabrication. |
Injection Molding Manufacturers | Mass production, precise replication, complex geometries | Electronics, toys, household products | Pros: High efficiency, low per-unit cost. Cons: High initial setup costs, not suitable for small runs. |
CNC Machining Plastic Fabricators | Precision cutting, complex shapes, multiple materials | Industrial machinery, automotive parts, custom components | Pros: High accuracy, versatile materials. Cons: Slower production rates, higher costs for small batches. |
Thermoforming Specialists | Heat-based shaping, large sheets, low tooling costs | Food packaging, medical trays, automotive parts | Pros: Lower tooling costs, quick setup. Cons: Limited to shallow shapes, not ideal for intricate designs. |
What Are the Characteristics of Custom Plastic Fabrication Companies?
Custom plastic fabrication companies focus on creating tailored solutions to meet specific client needs. These companies are adept at working with various materials and techniques, including CNC machining and die cutting. B2B buyers should consider their unique specifications, as these companies can produce items like specialized medical devices or aerospace components. However, buyers should be aware of potentially longer lead times and higher costs associated with custom solutions.
How Do Plastic Extrusion Companies Operate?
Plastic extrusion companies utilize a continuous manufacturing process to produce standardized shapes and components. This method is ideal for high-volume production, making it a popular choice for industries such as packaging and construction. Buyers looking for cost-effective solutions for large orders will find extrusion beneficial. However, the trade-off is limited design flexibility, as the process is best suited for simpler shapes.
What Are the Benefits of Injection Molding Manufacturers?
Injection molding manufacturers specialize in mass-producing plastic products with high precision. This method is particularly effective for creating complex geometries, making it suitable for various applications, including electronics and consumer goods. While injection molding can significantly reduce per-unit costs for large production runs, buyers must consider the high initial setup costs and the process’s unsuitability for small-scale orders.
What Role Does CNC Machining Play in Plastic Fabrication?
CNC machining plastic fabricators provide precise cutting and shaping of plastic materials, allowing for complex designs and high accuracy. This method is commonly used in industries such as automotive and machinery. B2B buyers should appreciate the versatility of CNC machining, as it can accommodate various materials. However, the production rate may be slower than other methods, and costs can be higher for smaller batches.
Why Choose Thermoforming Specialists for Your Projects?
Thermoforming specialists focus on shaping plastic sheets using heat, making this method ideal for creating shallow and large components like trays and packaging. The lower tooling costs and quick setup time make thermoforming an attractive option for B2B buyers needing speed and efficiency in production. However, it is essential to note that this technique is not well-suited for intricate designs, limiting its applications in certain industries.
Key Industrial Applications of plastic fabrication company
Industry/Sector | Specific Application of plastic fabrication company | Value/Benefit for the Business | Key Sourcing Considerations for this Application |
---|---|---|---|
Automotive | Custom plastic components for vehicle interiors | Reduces weight, improves fuel efficiency, enhances aesthetics | Quality of materials, compliance with safety standards, ability to handle custom designs |
Healthcare | Medical device housings and components | Ensures durability, biocompatibility, and regulatory compliance | Certifications (ISO, FDA), material properties, design flexibility |
Food & Beverage | Food-grade plastic containers and packaging | Extends shelf life, ensures safety and hygiene | Compliance with food safety regulations, material sourcing, custom sizes and shapes |
Construction | Plastic piping and fittings | Increases durability, reduces corrosion and maintenance costs | Material specifications, compatibility with existing systems, local availability |
Electronics | Enclosures and parts for electronic devices | Provides insulation, protects components from damage | Electrical properties, thermal resistance, precision fabrication capabilities |
How Are Custom Plastic Components Used in the Automotive Industry?
In the automotive sector, plastic fabrication companies produce custom components such as dashboards, door panels, and interior trims. These components are vital for reducing vehicle weight, which leads to improved fuel efficiency. Buyers from regions like Africa and South America should prioritize suppliers that can provide materials compliant with international safety standards, as well as those who can manage custom designs to meet specific aesthetic or functional requirements.
What Role Do Plastic Fabrication Companies Play in Healthcare?
In healthcare, plastic fabrication is crucial for manufacturing medical device housings and components, ensuring they meet stringent durability and biocompatibility standards. For international buyers, particularly in the Middle East and Europe, it’s essential to partner with manufacturers who hold relevant certifications (such as ISO and FDA) and can demonstrate flexibility in design to accommodate a range of medical applications. The reliability of these products is paramount for patient safety and regulatory compliance.
How Are Plastic Containers Enhancing the Food & Beverage Sector?
Plastic fabrication companies provide food-grade containers and packaging solutions that significantly extend product shelf life while ensuring safety and hygiene. For B2B buyers in regions like Africa, it’s critical to source materials that comply with local and international food safety regulations. Additionally, the ability to customize sizes and shapes can cater to specific product needs, enhancing the overall supply chain efficiency in the food and beverage industry.
What Are the Benefits of Plastic Piping in Construction?
In the construction industry, plastic piping and fittings are increasingly preferred due to their durability and resistance to corrosion. This not only reduces long-term maintenance costs but also ensures a longer lifespan for infrastructure projects. Buyers in Europe and South America should consider sourcing from companies that provide precise material specifications and compatibility with existing systems, as these factors can significantly impact project timelines and costs.
How Do Plastic Enclosures Benefit the Electronics Industry?
Plastic fabrication companies are essential in creating enclosures and parts for electronic devices, providing necessary insulation and protection from environmental factors. For international buyers, especially in Africa and the Middle East, understanding the electrical properties and thermal resistance of materials is vital. Selecting suppliers with precision fabrication capabilities ensures that the components meet the specific demands of advanced electronic applications, ultimately enhancing product reliability and performance.
3 Common User Pain Points for ‘plastic fabrication company’ & Their Solutions
Scenario 1: Difficulty in Meeting Custom Specifications
The Problem:
B2B buyers often face challenges when they require custom plastic components that meet specific dimensions, tolerances, or material specifications. For instance, a manufacturing company in South Africa may need a unique plastic part for a new product line but finds that standard off-the-shelf solutions do not fit their requirements. This can lead to delays in production, increased costs, and frustration as they navigate the complexities of custom orders.
The Solution:
To overcome this challenge, buyers should thoroughly communicate their specifications with potential plastic fabrication companies. It’s essential to provide detailed drawings, material requirements, and any applicable industry standards. Utilizing advanced digital tools like CAD software can help visualize the requirements clearly, ensuring that all parties have a mutual understanding before production begins. Furthermore, establishing a close working relationship with the fabricator can facilitate quick adjustments and iterations, reducing lead times and improving overall satisfaction. Requesting prototypes or samples before full production can also be an effective way to verify that the specifications are met.
Scenario 2: Uncertainty About Material Selection
The Problem:
Another common issue for international B2B buyers is the uncertainty surrounding which plastic material is most suitable for their applications. For example, a company in Brazil may be unsure whether to use polypropylene or polyethylene for a specific component that requires durability and resistance to chemicals. This lack of clarity can result in choosing the wrong material, leading to product failure and financial losses.
The Solution:
To navigate this dilemma, buyers should engage with plastic fabrication companies that have expertise in material science. It’s beneficial to ask for consultations where fabricators can provide insights into the properties of various plastics and their suitability for specific applications. Buyers should prepare a list of the functional requirements of their products, including temperature resistance, chemical exposure, and mechanical stresses, to guide the discussion. Additionally, referencing industry standards and case studies from similar applications can help in making an informed decision. Testing different materials in controlled environments before full-scale production can also provide valuable data to ascertain the best choice.
Scenario 3: Challenges with Quality Control and Consistency
The Problem:
Quality control is a significant concern for B2B buyers in the plastic fabrication industry, especially when dealing with overseas suppliers. A buyer in the Middle East might experience variability in product quality, leading to inconsistencies in the final products and potential reputational damage. This can stem from differing manufacturing processes, quality assurance protocols, or raw material sourcing.
The Solution:
To address quality control challenges, buyers should prioritize partnering with plastic fabrication companies that are ISO certified or have robust quality management systems in place. It is crucial to establish clear quality expectations from the outset, including acceptable tolerances, testing methods, and documentation requirements. Implementing a quality assurance process that includes regular audits and inspections can help maintain standards throughout the production process. Additionally, utilizing technology such as real-time monitoring systems can provide transparency and allow buyers to track the production stages, ensuring that any deviations from quality standards are promptly addressed. Engaging in open communication and feedback loops with the fabricator can also foster a culture of continuous improvement, enhancing product consistency over time.
Strategic Material Selection Guide for plastic fabrication company
What Are the Key Properties of Common Materials Used in Plastic Fabrication?
When selecting materials for plastic fabrication, it is crucial to understand their properties and how they align with your project requirements. Here, we analyze four common materials: Polyethylene (PE), Polypropylene (PP), Polyvinyl Chloride (PVC), and Acrylonitrile Butadiene Styrene (ABS). Each of these materials has unique characteristics that can significantly influence the performance and suitability of the final product.
Polyethylene (PE): Versatile and Cost-Effective
Key Properties: Polyethylene is known for its excellent chemical resistance, low moisture absorption, and good impact strength. It can withstand temperatures ranging from -50°C to 80°C, making it suitable for various applications.
Pros & Cons: PE is lightweight and relatively inexpensive, which makes it a popular choice for many industries. However, its lower temperature resistance and susceptibility to UV degradation limit its use in outdoor applications.
Impact on Application: PE is compatible with a wide range of chemicals, making it ideal for containers and packaging. However, it may not be suitable for high-pressure applications due to its lower strength compared to other materials.
Considerations for International Buyers: Buyers from regions like Africa and South America should ensure compliance with local regulations regarding food safety and chemical resistance. Common standards such as ASTM D1248 are essential for ensuring quality and safety.
Polypropylene (PP): Strong and Lightweight
Key Properties: Polypropylene offers higher temperature resistance than PE, with a range of -20°C to 100°C. It is also known for its excellent fatigue resistance and chemical stability.
Pros & Cons: The lightweight nature of PP makes it an attractive option for various applications, including automotive and consumer goods. However, its higher cost and complexity in manufacturing processes can be a drawback for some projects.
Impact on Application: PP is particularly well-suited for applications requiring durability, such as automotive parts and medical devices. Its resistance to many chemicals allows for use in harsh environments.
Considerations for International Buyers: Buyers should be aware of specific regional standards, such as DIN 16961 in Europe, which governs the use of PP in food contact applications. Understanding local regulations is crucial for compliance and market entry.
Polyvinyl Chloride (PVC): Durable and Versatile
Key Properties: PVC is known for its excellent durability, chemical resistance, and ability to withstand temperatures from -15°C to 60°C. It is also inherently flame retardant.
Pros & Cons: The durability of PVC makes it ideal for construction and plumbing applications. However, it can be more expensive than other materials and may require additional additives for specific applications.
Impact on Application: PVC is widely used in construction for pipes, siding, and window frames due to its strength and longevity. However, its rigidity can limit its use in applications requiring flexibility.
Considerations for International Buyers: Buyers in the Middle East and Europe should consider compliance with standards such as EN 1401 for drainage pipes. Understanding the environmental regulations surrounding PVC use is also vital.
Acrylonitrile Butadiene Styrene (ABS): Tough and Impact-Resistant
Key Properties: ABS is known for its high impact resistance and toughness, with a temperature range of -20°C to 80°C. It also has good chemical resistance and is easy to machine.
Pros & Cons: ABS is widely used in consumer products, automotive components, and electronic housings due to its strength and durability. However, it can be more expensive than alternatives like PE and PP.
Impact on Application: The high impact resistance of ABS makes it suitable for applications where durability is critical, such as in automotive and consumer electronics. However, it may not be the best choice for high-temperature applications.
Considerations for International Buyers: Compliance with international standards such as ISO 527 for mechanical properties is essential for ensuring product quality. Understanding local market preferences can also influence material choice.
Summary Table of Material Selection for Plastic Fabrication
Material | Typical Use Case for plastic fabrication company | Key Advantage | Key Disadvantage/Limitation | Relative Cost (Low/Med/High) |
---|---|---|---|---|
Polyethylene (PE) | Packaging, containers | Excellent chemical resistance | Lower temperature resistance | Low |
Polypropylene (PP) | Automotive parts, medical devices | High fatigue resistance | Higher manufacturing complexity | Medium |
Polyvinyl Chloride (PVC) | Construction, plumbing | Durable and flame retardant | More expensive than alternatives | Medium |
Acrylonitrile Butadiene Styrene (ABS) | Consumer products, electronics | High impact resistance | Higher cost compared to PE and PP | High |
This guide provides a comprehensive overview of material selection for plastic fabrication, helping international B2B buyers make informed decisions that align with their specific needs and regional regulations.
In-depth Look: Manufacturing Processes and Quality Assurance for plastic fabrication company
What Are the Main Stages of Manufacturing Processes in Plastic Fabrication?
The manufacturing process for plastic fabrication consists of several critical stages: material preparation, forming, assembly, and finishing. Understanding these stages can help international B2B buyers ensure they are sourcing high-quality products.
Material Preparation
Material preparation is the first step in the manufacturing process. It involves selecting appropriate raw materials, which can range from thermoplastics like polyethylene and polypropylene to thermosetting plastics such as epoxy. Key considerations include the material’s mechanical properties, chemical resistance, and thermal stability. Suppliers should provide detailed specifications and certifications for the materials used, ensuring compliance with industry standards.
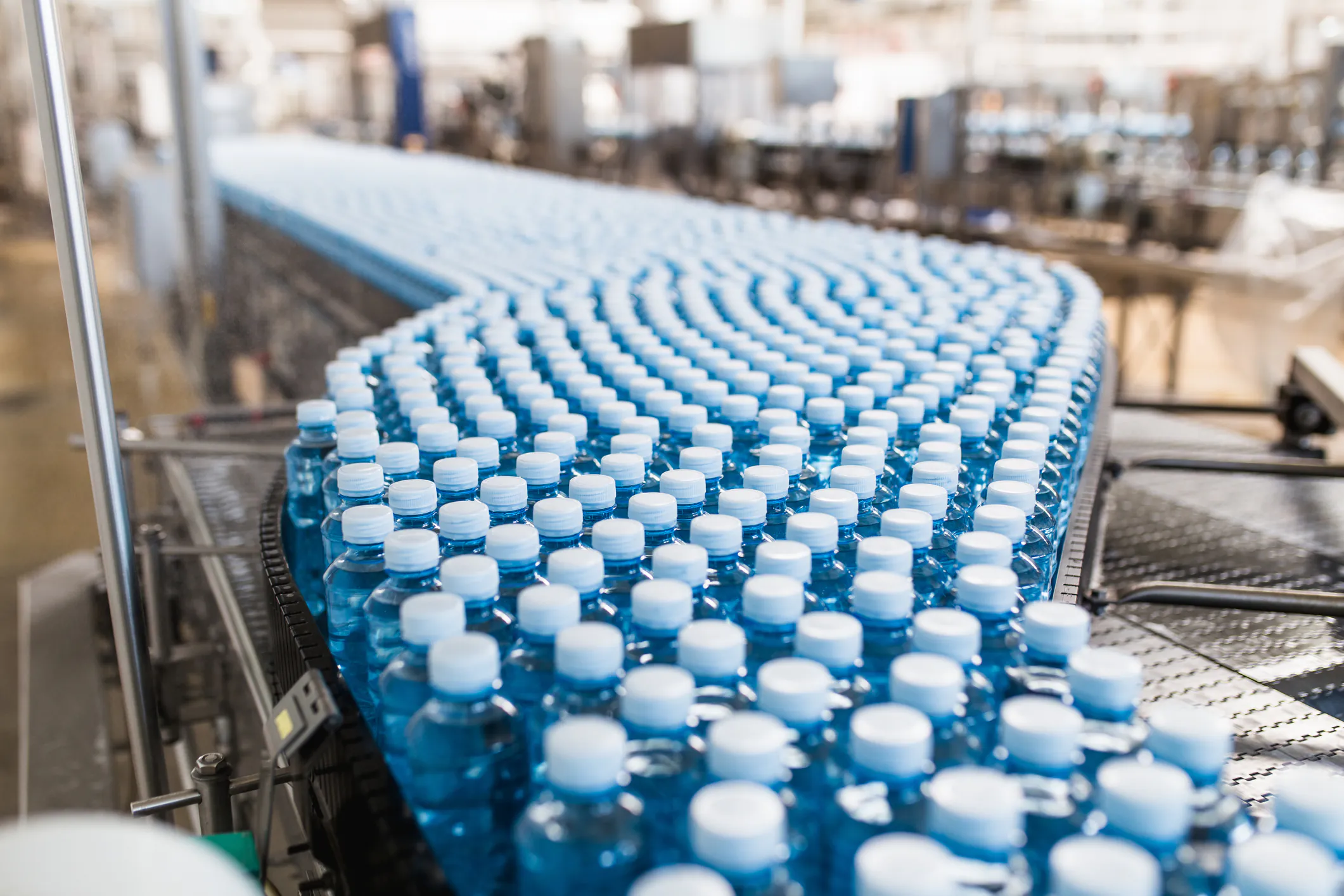
A stock image related to plastic fabrication company.
What Forming Techniques Are Commonly Used in Plastic Fabrication?
The forming stage encompasses various techniques tailored to produce specific shapes and sizes. The most common methods include:
- Injection Molding: This process involves injecting molten plastic into a mold cavity. It is highly efficient for mass production and can produce complex shapes with high precision.
- Blow Molding: Used primarily for hollow products, this method forms a plastic tube that is inflated to fit the mold. It’s ideal for items like bottles and containers.
- Thermoforming: In this technique, plastic sheets are heated and formed over a mold. It is suitable for creating large parts like trays and packaging.
- Extrusion: This continuous process involves forcing melted plastic through a die to create long shapes, such as pipes and sheets.
Each of these techniques has its advantages and specific applications, and buyers should inquire about the capabilities of their potential suppliers.
How Is Assembly Conducted in Plastic Fabrication?
The assembly process combines various components produced during the forming stage. This may involve techniques such as welding, adhesive bonding, or mechanical fastening. Buyers should ensure that the assembly methods align with their product requirements, as these can significantly affect the final product’s durability and performance. Additionally, suppliers should provide information on the tools and technologies employed in the assembly process, as these can impact efficiency and quality.
What Finishing Processes Are Employed to Enhance Plastic Products?
Finishing processes are critical for improving the aesthetic and functional qualities of plastic products. Common finishing techniques include:
- Surface Treatment: Techniques such as sanding, polishing, or coating can enhance the appearance and durability of the product.
- Painting and Printing: Custom branding and labeling can be applied to meet specific client needs.
- Quality Inspection: Before final delivery, products undergo rigorous inspections to ensure they meet specified tolerances and quality standards.
International buyers should confirm that the supplier employs finishing processes that comply with relevant standards, as this can affect product performance in various environments.
What International Standards Govern Quality Assurance in Plastic Fabrication?
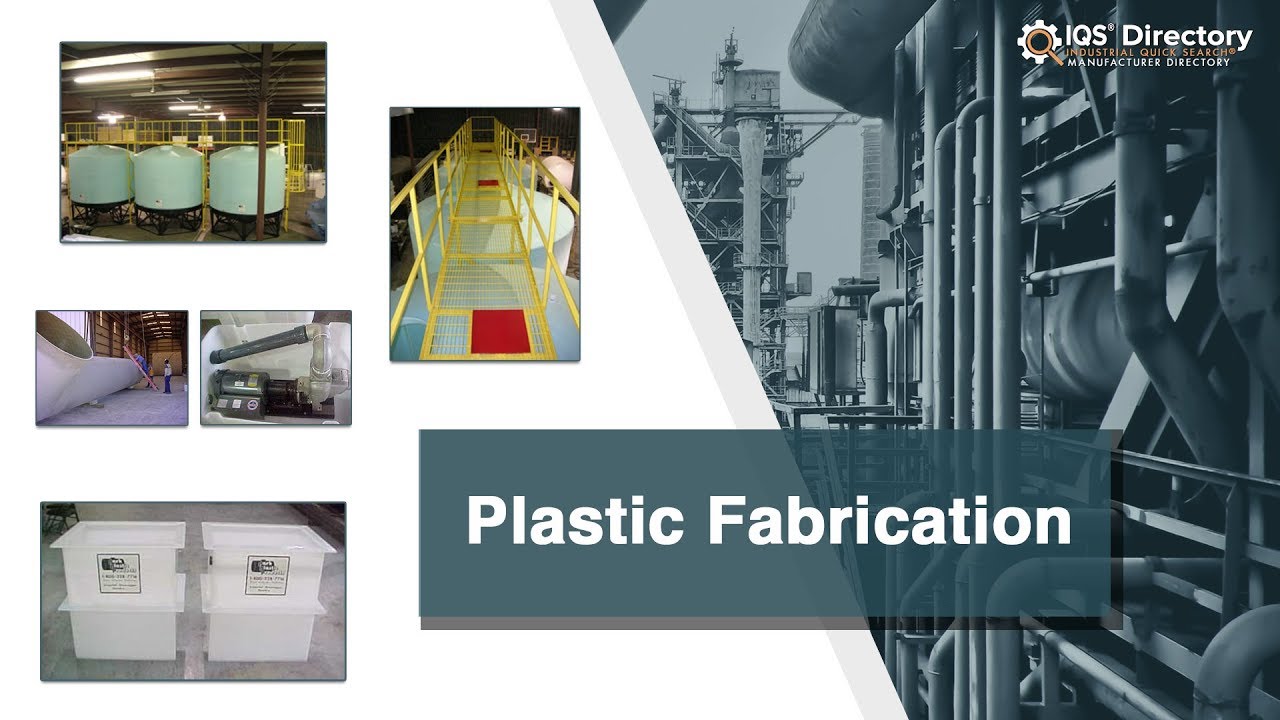
A stock image related to plastic fabrication company.
Quality assurance (QA) is paramount in the plastic fabrication industry. Buyers should look for suppliers that adhere to international standards such as ISO 9001, which outlines requirements for a quality management system (QMS). Compliance with ISO 9001 ensures that the supplier consistently meets customer and regulatory requirements.
What Industry-Specific Certifications Should B2B Buyers Consider?
In addition to ISO standards, industry-specific certifications may be crucial. For example:
- CE Marking: Indicates conformity with European health, safety, and environmental protection standards.
- API Certification: Relevant for suppliers serving the oil and gas industry, ensuring products meet specific performance criteria.
Understanding these certifications allows buyers to assess the credibility of suppliers and the quality of the products they manufacture.
What Are the Key QC Checkpoints in Plastic Fabrication?
Effective quality control (QC) involves several checkpoints throughout the manufacturing process:
- Incoming Quality Control (IQC): This initial stage involves inspecting raw materials to ensure they meet the specified standards before they enter the production process.
- In-Process Quality Control (IPQC): Continuous monitoring during the manufacturing process helps identify defects early on, allowing for timely corrections.
- Final Quality Control (FQC): This final inspection ensures that the finished product meets all specifications and quality standards before shipment.
B2B buyers should inquire about the specific QC measures their suppliers implement, as these can significantly affect product reliability and performance.
How Can B2B Buyers Verify Supplier Quality Control Practices?
To ensure that a supplier’s QC practices align with their quality expectations, buyers can take several steps:
- Request Audits and Reports: Buyers should ask for recent audit reports that detail the supplier’s compliance with quality standards and any corrective actions taken.
- Engage Third-Party Inspectors: Utilizing independent inspection services can provide an unbiased assessment of the supplier’s quality processes and product quality.
- Evaluate Supplier Certifications: Review certifications and accreditations to verify that the supplier meets industry standards.
What Nuances Should International Buyers Be Aware of Regarding QC and Certifications?
International B2B buyers, especially from regions like Africa, South America, the Middle East, and Europe, should be aware of potential discrepancies in quality standards and certifications. Different regions may have varying regulatory requirements, which could affect product quality and compliance. It is advisable for buyers to:
- Understand Local Regulations: Familiarize themselves with the specific regulations and standards that apply in their region to ensure compliance.
- Communicate Clearly: Establish clear communication with suppliers regarding quality expectations and standards from the outset.
- Build Relationships: Developing strong relationships with suppliers can facilitate better understanding and adherence to quality requirements.
By focusing on these aspects, international buyers can make informed decisions and ensure they partner with reliable plastic fabrication companies that prioritize quality assurance throughout their manufacturing processes.
Practical Sourcing Guide: A Step-by-Step Checklist for ‘plastic fabrication company’
In today’s competitive global market, sourcing a reliable plastic fabrication company is essential for businesses looking to manufacture high-quality plastic products. This guide provides a practical checklist for international B2B buyers, particularly those from Africa, South America, the Middle East, and Europe, to streamline the procurement process and ensure they partner with the right suppliers.
Step 1: Define Your Technical Specifications
Before reaching out to potential suppliers, clearly outline your technical requirements. This includes the type of plastic materials needed, the fabrication processes you require (e.g., injection molding, CNC machining), and any specific dimensions or tolerances.
– Why It Matters: A well-defined specification helps suppliers assess their capability to meet your needs and reduces misunderstandings later in the project.
Step 2: Research Supplier Capabilities
Conduct thorough research on potential plastic fabrication companies. Look for their production capabilities, technology used, and the range of services offered.
– What to Look For: Suppliers should have experience in your specific industry and the ability to handle custom projects. Review their portfolios for previous work that aligns with your requirements.
Step 3: Evaluate Potential Suppliers
Before committing, it’s crucial to vet suppliers thoroughly. Request company profiles, case studies, and references from buyers in a similar industry or region.
– Key Considerations: Assess their quality control processes and certifications, such as ISO 9001, which indicate a commitment to maintaining high standards.
Step 4: Check for Compliance and Certifications
Verify that the suppliers comply with relevant industry regulations and hold necessary certifications. This is particularly important for sectors like automotive, medical, and food packaging.
– Why This Step is Critical: Compliance ensures that the products meet safety and quality standards, which is essential to avoid costly recalls or legal issues.
Step 5: Request Samples and Prototypes
Once you’ve narrowed down your list of suppliers, request samples or prototypes of their work. This will give you a tangible sense of their craftsmanship and attention to detail.
– What to Evaluate: Assess the quality, finish, and dimensional accuracy of the samples. This step can significantly influence your final decision.
Step 6: Negotiate Terms and Conditions
Discuss pricing, lead times, payment terms, and delivery schedules with the shortlisted suppliers. Ensure all terms are documented to avoid disputes later.
– Important Points: Understand the total cost of ownership, including shipping and customs duties, especially when sourcing from international suppliers.
Step 7: Establish Communication Protocols
Set clear communication channels and protocols with your chosen supplier. This includes defining points of contact, regular updates, and feedback mechanisms.
– Why It’s Important: Effective communication fosters a strong partnership and ensures that any issues are addressed promptly, leading to smoother project execution.
By following this checklist, B2B buyers can make informed decisions when sourcing plastic fabrication companies, ultimately leading to successful partnerships and high-quality product outcomes.
Comprehensive Cost and Pricing Analysis for plastic fabrication company Sourcing
What Are the Key Cost Components in Plastic Fabrication?
When sourcing from plastic fabrication companies, understanding the cost structure is essential for making informed purchasing decisions. The primary cost components include:
-
Materials: The choice of plastic resin significantly impacts costs. Common materials include polyethylene, polypropylene, PVC, and specialized plastics like nylon and Teflon. Prices fluctuate based on market conditions, material availability, and regional sourcing.
-
Labor: Labor costs vary depending on the complexity of the project and the skill level required. Regions with lower labor costs may offer competitive pricing, but it’s crucial to assess the quality of workmanship to avoid compromising on product standards.
-
Manufacturing Overhead: This encompasses costs related to facility maintenance, utilities, and equipment depreciation. Efficient manufacturing processes can minimize overhead costs, leading to better pricing for buyers.
-
Tooling: Custom molds and tools represent a significant upfront investment. The cost is typically amortized over production runs, so larger orders can lead to lower per-unit tooling costs.
-
Quality Control (QC): Ensuring product quality incurs costs related to inspection, testing, and compliance with industry standards. Buyers should consider these costs as part of the total investment, especially when sourcing high-specification components.
-
Logistics: Shipping and handling costs can vary widely based on distance, shipping method, and packaging. International buyers should factor in import duties and customs clearance fees to avoid unexpected expenses.
-
Margin: Finally, suppliers will add a profit margin to cover their costs and ensure business viability. Understanding typical margins in the industry can help buyers negotiate better pricing.
How Do Price Influencers Affect Plastic Fabrication Costs?
Several factors influence pricing in the plastic fabrication sector:
-
Volume and Minimum Order Quantity (MOQ): Larger orders often lead to reduced per-unit costs. Understanding the supplier’s MOQ can help buyers plan their orders more effectively.
-
Specifications and Customization: Customized products typically incur higher costs due to additional design and tooling requirements. Buyers should balance the need for customization with budget constraints.
-
Material Selection: High-performance or specialty materials will naturally drive up costs. When sourcing, consider whether the material is essential for the application or if alternatives exist that could reduce expenses.
-
Quality and Certifications: Products that require specific certifications (like ISO or ASTM) may have higher costs due to the additional testing and compliance processes involved. Buyers in regulated industries must factor in these costs when evaluating suppliers.
-
Supplier Factors: Reputation, experience, and location of the supplier can significantly impact pricing. Suppliers with a proven track record may charge a premium, but the assurance of quality and reliability could justify the cost.
-
Incoterms: The agreed-upon Incoterms dictate who bears responsibility for shipping and insurance costs. Understanding these terms is crucial for calculating the total landed cost of products.
What Are Essential Buyer Tips for Sourcing Plastic Fabrication?
For international B2B buyers, particularly from Africa, South America, the Middle East, and Europe, here are actionable tips:
-
Negotiate Wisely: Leverage your understanding of cost components and market conditions to negotiate better terms. Suppliers may be more flexible on pricing for larger orders or long-term contracts.
-
Focus on Cost-Efficiency: Consider not just the purchase price but the total cost of ownership (TCO), which includes maintenance, operational costs, and potential waste. Investing in higher-quality products may yield savings in the long run.
-
Understand Pricing Nuances: Be aware of seasonal fluctuations in material costs and how geopolitical factors might impact pricing. Staying informed can help you time your purchases strategically.
-
Build Relationships: Establishing strong partnerships with suppliers can lead to better pricing, priority service, and insights into new products or technologies.
Disclaimer on Indicative Prices
Prices in the plastic fabrication industry can vary significantly based on multiple factors, including market conditions, location, and specific project requirements. Always seek detailed quotes from suppliers to ensure accurate pricing information tailored to your needs.
Alternatives Analysis: Comparing plastic fabrication company With Other Solutions
Exploring Alternatives to Plastic Fabrication Companies
In the competitive landscape of manufacturing, particularly for international B2B buyers in regions such as Africa, South America, the Middle East, and Europe, exploring alternatives to traditional plastic fabrication methods is crucial. While plastic fabrication companies offer specialized services for custom plastic products, other methods may provide cost-effective, efficient, or innovative solutions depending on specific project requirements. This analysis will compare plastic fabrication companies with two viable alternatives: additive manufacturing (3D printing) and metal fabrication.
Comparison Aspect | Plastic Fabrication Company | Additive Manufacturing (3D Printing) | Metal Fabrication |
---|---|---|---|
Performance | High precision for complex shapes; suitable for large production runs. | Excellent for prototyping and small batches; complex geometries possible. | Strong and durable; ideal for heavy-duty applications. |
Cost | Moderate initial costs, but can lower with larger orders. | Generally lower for small runs; material costs can be high. | Higher initial investment; cost-effective for large volumes. |
Ease of Implementation | Requires detailed specifications and longer lead times. | Quick setup and rapid production; designs can be easily modified. | Longer setup time due to tooling and machining processes. |
Maintenance | Routine maintenance required; longevity depends on material choice. | Minimal maintenance; technology rapidly evolving. | High maintenance; tools and machinery require regular upkeep. |
Best Use Case | Mass production of custom parts; industries like automotive and aerospace. | Rapid prototyping, custom one-off parts; useful in medical and consumer products. | Structural components, machinery parts; ideal for industries like construction and manufacturing. |
In-Depth Look at Each Alternative
How Does Additive Manufacturing (3D Printing) Compare?
Additive manufacturing, commonly known as 3D printing, has emerged as a transformative technology in product development and manufacturing. This method allows for the creation of intricate designs without the need for extensive tooling. The primary advantages include reduced material waste and the ability to quickly iterate designs based on real-time feedback. However, while the initial costs can be lower for small production runs, the price per unit may escalate significantly for larger quantities due to material costs. This method is particularly beneficial for industries needing rapid prototyping, such as medical devices or consumer electronics.
What About Metal Fabrication?
Metal fabrication involves the construction of metal structures through cutting, bending, and assembling processes. This method is renowned for producing robust and durable components, making it ideal for heavy-duty applications in sectors like construction and automotive. While the initial setup costs are higher due to specialized machinery and tools, metal fabrication can be very cost-effective for large-scale production runs. The main drawbacks include longer lead times and more complex maintenance requirements. Therefore, businesses should consider this option when strength and durability are paramount.
How Should B2B Buyers Choose the Right Solution?
When selecting between plastic fabrication companies and alternative methods like additive manufacturing or metal fabrication, B2B buyers must assess their specific needs. Factors such as production volume, material properties, design complexity, and budget constraints play a crucial role in decision-making. For projects requiring high precision and customization, plastic fabrication may be optimal. Conversely, for rapid prototyping or when dealing with metal components, exploring additive manufacturing or metal fabrication may yield better results. Ultimately, understanding the strengths and weaknesses of each method will empower buyers to make informed choices that align with their operational goals.
Essential Technical Properties and Trade Terminology for plastic fabrication company
What Are the Key Technical Properties in Plastic Fabrication?
Understanding the essential technical properties of plastic materials is crucial for B2B buyers in ensuring that the products they source meet their specific requirements. Here are some critical specifications to consider:
1. Material Grade
Material grade refers to the classification of plastic materials based on their properties and intended uses. Common grades include ABS, PVC, polycarbonate, and nylon. Selecting the right material grade is vital as it impacts durability, chemical resistance, and overall performance. For example, ABS is favored for its toughness and impact resistance, making it suitable for automotive and consumer goods applications.
2. Tolerance
Tolerance is the allowable variation in dimensions of a fabricated part. It is crucial for ensuring that components fit together correctly in assemblies. Tight tolerances are often required in industries such as aerospace and medical devices, where precision is paramount. Understanding tolerance specifications helps in negotiating with suppliers to ensure that the final products meet your exact needs.
3. Thermal Properties
Thermal properties, including heat deflection temperature and thermal conductivity, determine how a plastic material behaves under temperature changes. For instance, materials with high heat deflection temperatures are essential for applications that involve exposure to heat, such as automotive parts. B2B buyers must assess these properties to avoid material failure in high-temperature environments.
4. Chemical Resistance
Chemical resistance indicates how well a plastic can withstand exposure to various chemicals, including acids, bases, and solvents. This property is critical for industries like chemical processing and pharmaceuticals, where materials may come into contact with aggressive substances. Buyers should inquire about the chemical resistance of materials to ensure long-term reliability.
5. Impact Strength
Impact strength measures a material’s ability to resist sudden force or shock. This property is especially important in applications where durability is crucial, such as in packaging or automotive components. Buyers should prioritize materials with high impact strength to minimize the risk of product failure during transport or use.
What Are Common Trade Terms in Plastic Fabrication?
Familiarity with industry jargon is essential for effective communication and negotiation in the plastic fabrication sector. Here are several key terms to know:
1. OEM (Original Equipment Manufacturer)
OEM refers to companies that produce parts and equipment that may be marketed by another manufacturer. In the context of plastic fabrication, understanding OEM relationships is vital for buyers looking to source custom parts that fit within their larger product offerings.
2. MOQ (Minimum Order Quantity)
MOQ is the smallest quantity of a product that a supplier is willing to sell. Knowing the MOQ is important for budget-conscious buyers, as it can significantly affect purchasing decisions. Suppliers may have different MOQs depending on the type of plastic or fabrication process involved.
3. RFQ (Request for Quote)
An RFQ is a document that solicits price quotes from suppliers for specific products or services. For B2B buyers, submitting a well-defined RFQ can lead to competitive pricing and faster responses from potential suppliers, ensuring a smoother procurement process.
4. Incoterms (International Commercial Terms)
Incoterms are a set of international rules that define the responsibilities of buyers and sellers in global trade. Understanding these terms helps buyers clarify shipping responsibilities, costs, and risks associated with their orders, which is crucial for planning and budgeting in cross-border transactions.
5. CNC Machining (Computer Numerical Control)
CNC machining is a manufacturing process that uses computer-controlled tools to create precise parts from plastic materials. This technology is essential for producing high-tolerance components and is widely used in the plastic fabrication industry. Recognizing the capabilities and limitations of CNC machining can help buyers select the right suppliers for their needs.
By grasping these technical properties and trade terminologies, international B2B buyers can make more informed decisions, ultimately leading to more successful partnerships in the plastic fabrication industry.
Navigating Market Dynamics and Sourcing Trends in the plastic fabrication company Sector
What Are the Key Market Dynamics Affecting the Plastic Fabrication Sector?
The plastic fabrication sector is undergoing significant transformation driven by various global forces. Increasing demand for lightweight and durable materials across industries, from automotive to consumer goods, is propelling the growth of plastic fabrication. As international B2B buyers, particularly from Africa, South America, the Middle East, and Europe, consider sourcing from global suppliers, understanding these market dynamics is crucial.
Emerging technologies such as automation, 3D printing, and advanced computer-aided design (CAD) are revolutionizing the production processes. These innovations enable faster prototyping, reduced lead times, and customization at scale, providing a competitive edge to companies that embrace them. Furthermore, the rise of e-commerce platforms facilitates easier connection between buyers and suppliers, enhancing transparency and efficiency in the sourcing process.
Another trend is the shift towards regional sourcing, spurred by geopolitical factors and the need for supply chain resilience. Buyers are increasingly seeking local suppliers to mitigate risks associated with long-distance shipping and fluctuating tariffs. This trend is particularly relevant for buyers in regions like Africa and South America, where local manufacturing capabilities are expanding.
How Is Sustainability Impacting Sourcing Decisions in the Plastic Fabrication Industry?
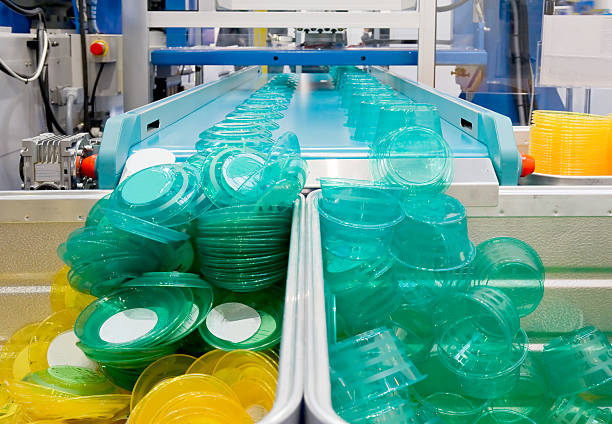
A stock image related to plastic fabrication company.
Sustainability has emerged as a fundamental consideration in the plastic fabrication industry, influencing sourcing decisions for B2B buyers. The environmental impact of plastic production and disposal is prompting companies to adopt more sustainable practices. Buyers are increasingly prioritizing suppliers who demonstrate a commitment to reducing their carbon footprint and utilizing eco-friendly materials.
Ethical sourcing is also gaining traction, with businesses looking to ensure that their supply chains are responsible and transparent. This includes choosing suppliers who comply with ethical labor practices and environmental regulations. Certifications such as ISO 14001 (Environmental Management) and the use of recycled or biodegradable materials can serve as indicators of a supplier’s commitment to sustainability.
For international buyers, understanding the sustainability practices of potential suppliers can provide a competitive advantage. Companies that align with sustainable practices are not only better positioned to meet regulatory requirements but also resonate with environmentally conscious consumers, enhancing brand loyalty and market appeal.
What Is the Evolution of the Plastic Fabrication Industry?
The plastic fabrication industry has a rich history that reflects the evolution of materials and manufacturing techniques. Initially, the use of plastics dates back to the early 20th century, with the introduction of Bakelite, the first synthetic plastic. Over the decades, advancements in polymer science have led to the development of a wide array of plastic materials, each with unique properties suitable for various applications.
The 1960s and 1970s saw the introduction of more sophisticated fabrication techniques, such as injection molding and blow molding, which allowed for mass production of plastic products. In recent years, the focus has shifted towards customization and sustainability, driven by technological advancements and changing consumer preferences.
Today, the plastic fabrication sector is characterized by a blend of traditional methods and cutting-edge technologies, enabling manufacturers to meet the diverse needs of industries worldwide. For international B2B buyers, understanding this evolution is essential for making informed sourcing decisions and identifying innovative suppliers capable of delivering high-quality plastic solutions.
Frequently Asked Questions (FAQs) for B2B Buyers of plastic fabrication company
-
How can I identify a reliable plastic fabrication company for my business needs?
To find a trustworthy plastic fabrication company, start by assessing their industry experience and client testimonials. Look for companies that have successfully handled projects similar to yours. Request samples of previous work to evaluate quality. Certifications such as ISO 9001 can indicate a commitment to quality management. Additionally, consider suppliers that offer transparent communication and responsive customer service, as these traits are vital for a smooth collaboration. -
What factors should I consider when evaluating plastic fabrication suppliers?
When assessing plastic fabrication suppliers, consider their production capabilities, material expertise, and technology used in fabrication. Check their ability to handle your specific requirements, such as custom designs and volume production. Evaluate their pricing structure, payment terms, and lead times. It’s also wise to inquire about their quality assurance processes and any certifications that demonstrate compliance with industry standards. -
What customization options are available for plastic fabrication projects?
Plastic fabrication companies typically offer a range of customization options, including material selection, size, shape, and finish. Many suppliers can work with various plastics, such as acrylic, polycarbonate, and nylon, to meet specific functional and aesthetic needs. Discuss your project requirements in detail with the supplier to explore options such as CNC machining, injection molding, and thermoforming, ensuring the final product aligns with your specifications. -
What is the minimum order quantity (MOQ) for plastic fabrication?
The MOQ for plastic fabrication varies by supplier and the complexity of the project. Some companies may have low MOQs for standard products, while custom projects might require higher minimums due to setup costs. Always confirm the MOQ with potential suppliers to avoid unexpected costs. If your order falls below the MOQ, inquire if the company offers prototyping or small batch production services. -
What payment terms can I expect when working with international plastic fabrication suppliers?
Payment terms can vary significantly among suppliers, especially in international transactions. Common arrangements include upfront payments, partial payments upon order confirmation, and balances due upon delivery. It’s crucial to clarify payment methods (e.g., bank transfers, credit cards) and discuss any associated fees or currency exchange issues. Establishing clear payment terms in your contract can help prevent misunderstandings later on. -
How do I ensure quality assurance in my plastic fabrication projects?
To ensure quality assurance, request documentation of the supplier’s quality control processes. Many reputable fabricators will have standard operating procedures in place, including material inspections, in-process checks, and final product testing. Ask about certifications, such as ISO 9001 or industry-specific standards, which indicate compliance with quality management systems. Additionally, consider conducting regular audits or requesting samples for verification before full-scale production. -
What logistics considerations should I keep in mind when sourcing plastic fabrication from abroad?
When sourcing plastic fabrication internationally, consider shipping methods, costs, and delivery times. Evaluate whether the supplier offers support with customs clearance and documentation, which can simplify the import process. Understand the potential for tariffs or duties that may apply to your order, and factor these into your overall budget. Additionally, establish a clear communication plan for tracking orders and addressing any logistical challenges that may arise. -
How can I manage communication effectively with my plastic fabrication supplier?
Effective communication with your plastic fabrication supplier is essential for project success. Establish clear points of contact and preferred communication channels, whether via email, phone, or project management tools. Be explicit about your project requirements, timelines, and feedback loops. Regular updates and check-ins can help address issues promptly. Consider time zone differences when scheduling meetings to ensure all parties are aligned and informed throughout the process.
Important Disclaimer & Terms of Use
⚠️ Important Disclaimer
The information provided in this guide, including content regarding manufacturers, technical specifications, and market analysis, is for informational and educational purposes only. It does not constitute professional procurement advice, financial advice, or legal advice.
While we have made every effort to ensure the accuracy and timeliness of the information, we are not responsible for any errors, omissions, or outdated information. Market conditions, company details, and technical standards are subject to change.
B2B buyers must conduct their own independent and thorough due diligence before making any purchasing decisions. This includes contacting suppliers directly, verifying certifications, requesting samples, and seeking professional consultation. The risk of relying on any information in this guide is borne solely by the reader.
Strategic Sourcing Conclusion and Outlook for plastic fabrication company
What Are the Key Takeaways for B2B Buyers in Plastic Fabrication?
In the dynamic landscape of plastic fabrication, strategic sourcing emerges as a critical component for international B2B buyers, particularly in regions like Africa, South America, the Middle East, and Europe. By understanding the diverse capabilities of plastic fabricators—from custom machining and extrusion to innovative design solutions—buyers can streamline their procurement processes and enhance operational efficiency. Establishing partnerships with reputable suppliers not only ensures access to high-quality materials but also fosters innovation through collaborative development.
How Can Strategic Sourcing Enhance Your Supply Chain?
Investing in strategic sourcing allows businesses to mitigate risks associated with supply chain disruptions, especially in volatile markets. It enables buyers to evaluate suppliers based on their technical expertise, production capabilities, and responsiveness to client needs. By prioritizing suppliers that align with your strategic goals, you can secure a competitive advantage in your industry.
What’s Next for International B2B Buyers?
As the global market continues to evolve, staying informed about emerging trends in plastic fabrication will be crucial. Engage with suppliers, attend industry conferences, and leverage digital platforms to connect with innovative fabricators. This proactive approach will empower you to make informed decisions that drive growth and sustainability in your operations. Don’t hesitate to explore new partnerships that can elevate your business to new heights in the plastic fabrication sector.