Eliminate Static: The Ultimate Guide to Static Eliminators (2025)
Introduction: Navigating the Global Market for static eliminator
Navigating the complexities of sourcing static eliminators can be a daunting challenge for international B2B buyers, especially in regions such as Africa, South America, the Middle East, and Europe. As industries increasingly rely on precision manufacturing and electronics, the need for effective static control solutions becomes paramount. Static eliminators play a crucial role in mitigating static electricity, which can lead to product defects, equipment damage, and safety hazards. This guide aims to simplify the sourcing process by providing a comprehensive overview of various types of static eliminators, including their applications, features, and benefits.
In the following sections, readers will find actionable insights on how to vet suppliers, evaluate costs, and understand the latest technological advancements in static elimination. From understanding the differences between ionizers and other types of static eliminators to exploring maintenance-free options, this guide empowers B2B buyers to make informed purchasing decisions. With a focus on practical solutions tailored to the unique challenges faced by businesses in diverse markets, this resource will enhance your procurement strategy and contribute to operational efficiency. Whether you are based in Nigeria, Brazil, or any other region, navigating the global market for static eliminators has never been easier.
Understanding static eliminator Types and Variations
Type Name | Key Distinguishing Features | Primary B2B Applications | Brief Pros & Cons for Buyers |
---|---|---|---|
Bar Type Ionizer | Long, narrow design for static elimination over a wide area | Packaging, textiles, electronics | Pros: Covers large areas; Cons: Requires installation space. |
Point Type Ionizer | Focused ion generation for targeted static elimination | Precision manufacturing, assembly lines | Pros: High efficiency; Cons: Limited coverage area. |
Fan Type Ionizer | Integrated fan for enhanced air circulation without external supply | Cleanrooms, electronic manufacturing | Pros: No need for air supply; Cons: May require more maintenance. |
Air Gun Type Ionizer | Portable design for localized static control | Fieldwork, maintenance, repairs | Pros: Versatile and mobile; Cons: Limited static elimination range. |
Blower Type Ionizer | High airflow capabilities for large area static elimination | Automotive, printing, and textiles | Pros: Effective for large spaces; Cons: Can be noisy. |
What are the Key Characteristics of Bar Type Ionizers?
Bar type ionizers are designed to eliminate static electricity over expansive surfaces, making them ideal for applications in packaging, textiles, and electronics. Their elongated structure allows for a more uniform distribution of ions, effectively neutralizing static charges across large areas. Buyers should consider the installation space and environmental factors, as these units typically require a fixed position.
How Do Point Type Ionizers Work and Where Are They Best Used?
Point type ionizers concentrate ion generation at specific points, making them perfect for precision manufacturing and assembly lines where static control is critical. Their targeted approach ensures high efficiency in static elimination, although they cover a limited area. B2B buyers should evaluate the specific points in their processes that require static control to maximize the effectiveness of these devices.
What Advantages Do Fan Type Ionizers Offer for Cleanroom Applications?
Fan type ionizers combine ion generation with built-in fans, facilitating effective static control in environments like cleanrooms and electronic manufacturing. These devices do not require an external air supply, which simplifies installation. However, they may demand more frequent maintenance compared to other types due to the moving parts involved. Buyers should assess their maintenance capabilities and operational needs when considering this option.
Why Choose Air Gun Type Ionizers for Portability?
Air gun type ionizers are designed for portability, allowing users to control static electricity in various locations, particularly in fieldwork or maintenance situations. Their flexibility makes them suitable for a range of applications, but they have a limited static elimination range compared to fixed installations. Businesses should evaluate the frequency and nature of their static control needs to determine if this mobile solution fits their requirements.
How Do Blower Type Ionizers Operate in Large Spaces?
Blower type ionizers are effective for large areas, utilizing high airflow capabilities to distribute ions widely. They are commonly used in industries such as automotive, printing, and textiles. While they offer excellent coverage, the noise produced during operation can be a consideration for some environments. B2B buyers should weigh the benefits of extensive coverage against the potential for increased sound levels in their operational settings.
Key Industrial Applications of static eliminator
Industry/Sector | Specific Application of Static Eliminator | Value/Benefit for the Business | Key Sourcing Considerations for this Application |
---|---|---|---|
Electronics Manufacturing | Preventing static damage to sensitive electronic components | Reduces defects and rework costs, ensuring product reliability | Ensure compatibility with various component types and sizes. |
Packaging and Printing | Eliminating static in packaging processes | Enhances product quality by preventing dust and contaminants | Look for models that can integrate with existing production lines. |
Textile and Garment Production | Static control during fabric handling and processing | Improves efficiency and reduces waste from static cling | Consider energy efficiency and maintenance requirements. |
Pharmaceuticals and Food Industry | Maintaining cleanliness in sterile environments | Ensures compliance with health regulations and product safety | Evaluate certifications for hygiene and compatibility with clean rooms. |
Automotive Manufacturing | Static elimination during paint and coating applications | Enhances finish quality and reduces rework | Choose systems that can operate in high-temperature environments. |
How is Static Eliminator Used in Electronics Manufacturing?
In electronics manufacturing, static eliminators are crucial for preventing electrostatic discharge (ESD) that can damage sensitive components. These devices neutralize static charges on components and work surfaces, thereby reducing defects caused by static electricity. For international B2B buyers, it’s essential to consider the compatibility of static eliminators with various electronic components and the specific ESD protection levels required by different products.
What Role Does Static Eliminator Play in Packaging and Printing?
In the packaging and printing sectors, static eliminators are used to eliminate static charges during the packaging process. This application is vital as static can attract dust and debris, compromising product quality. Buyers should seek static eliminators that can seamlessly integrate with existing production lines and that are capable of handling various packaging materials, especially in fast-paced environments.
Why is Static Control Important in Textile and Garment Production?
Static electricity can cause significant issues in textile and garment production, leading to static cling that affects fabric handling and processing. Static eliminators are employed to mitigate these problems, improving efficiency and reducing waste. B2B buyers in this sector should focus on energy-efficient models that minimize maintenance needs while still providing effective static control.
How Does Static Eliminator Ensure Compliance in Pharmaceuticals and Food Industries?
In the pharmaceuticals and food industries, maintaining a static-free environment is crucial for compliance with health regulations. Static eliminators help maintain cleanliness in sterile environments by preventing dust accumulation on surfaces and equipment. Buyers should evaluate the certifications of static eliminators for hygiene and their compatibility with cleanroom standards to ensure product safety.
What Benefits Do Static Eliminators Offer in Automotive Manufacturing?
In automotive manufacturing, static eliminators are essential during paint and coating applications to prevent defects caused by static charges. They enhance finish quality by ensuring a uniform application of coatings without interference from static cling. Buyers should consider systems that can operate effectively in high-temperature environments, as this is often required in automotive production processes.
3 Common User Pain Points for ‘static eliminator’ & Their Solutions
Scenario 1: Ineffective Static Elimination in High-Volume Production Environments
The Problem: In high-volume manufacturing environments, such as electronics or pharmaceuticals, static electricity can cause significant disruptions. B2B buyers often encounter issues where static charges lead to product defects, equipment malfunctions, or safety hazards. This not only affects product quality but also results in costly downtime and rework. Buyers may feel frustrated as conventional static eliminators fail to provide adequate coverage or speed, leading to a constant battle against static buildup.
The Solution: To effectively combat static in these dynamic settings, it’s essential to select a static eliminator that offers high-speed performance and broad coverage. Consider investing in systems like the High-Accuracy High-Speed Sensing Ionizer, which provides rapid static elimination (within 0.1 seconds) and requires minimal maintenance. When sourcing, look for devices that offer maintenance-free operation and can automatically adjust to variations in static levels. Implementing a comprehensive static control strategy that includes regular monitoring and using multiple static eliminators in key areas can greatly enhance effectiveness, ensuring consistent product quality and operational efficiency.
Scenario 2: High Maintenance Costs and Downtime
The Problem: Many businesses face escalating maintenance costs associated with traditional static eliminators that require frequent cleaning and part replacements. B2B buyers may find themselves spending substantial time and resources on maintenance, which detracts from their core operations. This is particularly challenging for companies in regions with limited access to technical support and replacement parts, leading to longer downtimes and reduced productivity.
The Solution: Transitioning to modern static eliminators designed for low maintenance can alleviate this burden. For example, the SJ-Q series from KEYENCE features electrode probes that do not need replacement for up to ten years and require cleaning only once a year. When evaluating static eliminators, prioritize those with advanced features such as self-diagnosis functions and automatic cleaning capabilities. Additionally, consider establishing a partnership with a reliable supplier who can provide ongoing support and quick access to parts, thereby reducing downtime and total cost of ownership.
Scenario 3: Limited Flexibility in Diverse Operational Settings
The Problem: B2B buyers often operate in diverse environments with varying static control needs, from cleanrooms to outdoor settings. Traditional static eliminators may lack the versatility to adapt to these different situations, leading to ineffective static control. Buyers may struggle to find a single solution that meets all their operational requirements, resulting in inconsistent performance and additional costs for multiple devices.
The Solution: It is crucial to choose a static eliminator that offers flexibility and adaptability to various environments. Products like the Air-Free High-Speed Sensing Ionizer provide effective static elimination without the need for air, making them suitable for sensitive areas where airflow might disrupt operations. When specifying your requirements, consider the specific environmental conditions and operational needs. Look for static eliminators that come with customizable settings or interchangeable components, allowing for tailored solutions across different applications. This not only enhances static control but also streamlines procurement and reduces overall equipment complexity, ensuring a more efficient operational workflow.
Strategic Material Selection Guide for static eliminator
What Are the Key Materials Used in Static Eliminators?
When selecting materials for static eliminators, it is crucial to consider their properties, advantages, and limitations. Here, we analyze four common materials used in the manufacturing of static eliminators, focusing on their performance characteristics and implications for international B2B buyers.
How Does Conductive Plastic Perform in Static Eliminators?
Key Properties: Conductive plastics are often engineered to provide a balance between electrical conductivity and mechanical strength. They can withstand moderate temperatures and pressures, typically rated up to 100°C, depending on the formulation.
Pros & Cons: The primary advantage of conductive plastics is their lightweight nature, which reduces shipping costs and installation complexity. They are also resistant to corrosion, making them suitable for various environments. However, they may not be as durable as metals and can be more expensive to produce, impacting overall costs.
Impact on Application: Conductive plastics are particularly effective in applications where weight is a concern, such as in portable static eliminators. Their compatibility with various media makes them versatile, but they may not perform well in extreme conditions.
Considerations for International Buyers: Buyers from regions like Africa and South America should ensure that the selected conductive plastic complies with local standards, such as ASTM or ISO. Understanding the specific environmental conditions in which the static eliminator will operate is essential for material selection.
What Role Does Stainless Steel Play in Static Eliminators?
Key Properties: Stainless steel is known for its excellent corrosion resistance and high strength. It can handle high temperatures (up to 800°C) and pressures, making it suitable for demanding applications.
Pros & Cons: The durability of stainless steel is a significant advantage, as it can last for many years without significant wear. However, it is heavier than other materials, which can increase shipping costs. Additionally, the manufacturing process can be complex and costly.
Impact on Application: Stainless steel is ideal for static eliminators used in harsh environments, such as manufacturing plants and chemical processing facilities. Its robustness ensures reliable performance, even in challenging conditions.
Considerations for International Buyers: Buyers in the Middle East and Europe should verify that the stainless steel used meets relevant standards, such as DIN or EN, to ensure quality and compliance with local regulations.
How Do Aluminum Alloys Enhance Static Eliminators?
Key Properties: Aluminum alloys are lightweight yet strong, with good corrosion resistance and thermal conductivity. They typically perform well at temperatures up to 200°C.
Pros & Cons: The lightweight nature of aluminum alloys makes them easy to handle and install, reducing labor costs. However, they may not be as strong as stainless steel and can be susceptible to wear over time, particularly in abrasive environments.
Impact on Application: Aluminum alloys are often used in static eliminators designed for less demanding applications, where weight savings are critical. They are suitable for environments with moderate exposure to corrosive substances.
Considerations for International Buyers: Buyers in regions like Europe and Africa should consider local availability and cost of aluminum alloys. Compliance with standards such as JIS or ASTM is also essential to ensure product reliability.
Why Are Ceramics Important in Static Eliminators?
Key Properties: Ceramics offer excellent electrical insulation and can withstand high temperatures (up to 1500°C) and pressures. They are also chemically inert, making them ideal for various applications.
Pros & Cons: The primary advantage of ceramics is their exceptional durability and resistance to wear and tear. However, they can be brittle and prone to cracking under impact, which may limit their use in certain applications.
Impact on Application: Ceramics are often used in static eliminators that require high performance in extreme conditions. Their chemical resistance makes them suitable for environments with aggressive substances.
Considerations for International Buyers: Buyers should evaluate the specific ceramic materials used in static eliminators for compliance with local standards. Understanding the fragility of ceramics is also crucial when considering shipping and handling.
Summary Table of Material Selection for Static Eliminators
Material | Typical Use Case for Static Eliminator | Key Advantage | Key Disadvantage/Limitation | Relative Cost (Low/Med/High) |
---|---|---|---|---|
Conductive Plastic | Portable static eliminators | Lightweight and corrosion-resistant | Less durable than metals | Medium |
Stainless Steel | Harsh industrial environments | High durability and strength | Heavy and costly to manufacture | High |
Aluminum Alloys | Moderate exposure environments | Lightweight and easy to handle | Less strong and wear-prone | Medium |
Ceramics | Extreme conditions | Excellent durability and insulation | Brittle and prone to cracking | High |
This comprehensive analysis provides international B2B buyers with actionable insights into material selection for static eliminators, ensuring informed purchasing decisions tailored to specific applications and regional considerations.
In-depth Look: Manufacturing Processes and Quality Assurance for static eliminator
What Are the Typical Manufacturing Processes for Static Eliminators?
The manufacturing of static eliminators involves several critical stages, each essential for ensuring the performance and reliability of the final product. Below are the main stages of the manufacturing process:
How Is Material Prepared for Static Eliminators?
Material preparation is the first step in the manufacturing process. This involves sourcing high-quality raw materials, such as conductive plastics, metal components, and ionizing elements. Suppliers should provide documentation verifying the material properties, including electrical conductivity and durability. For international buyers, especially those from Africa and South America, it is crucial to ensure that materials comply with local regulations and international standards to avoid future complications.
What Forming Techniques Are Used in Static Eliminator Manufacturing?
Once materials are prepared, the next step is forming. Various techniques can be employed, including injection molding for plastic components and metal stamping or machining for metal parts. The choice of technique often depends on the design specifications and the volume of production. For example, injection molding is highly efficient for large quantities, while machining may be used for custom or low-volume components.
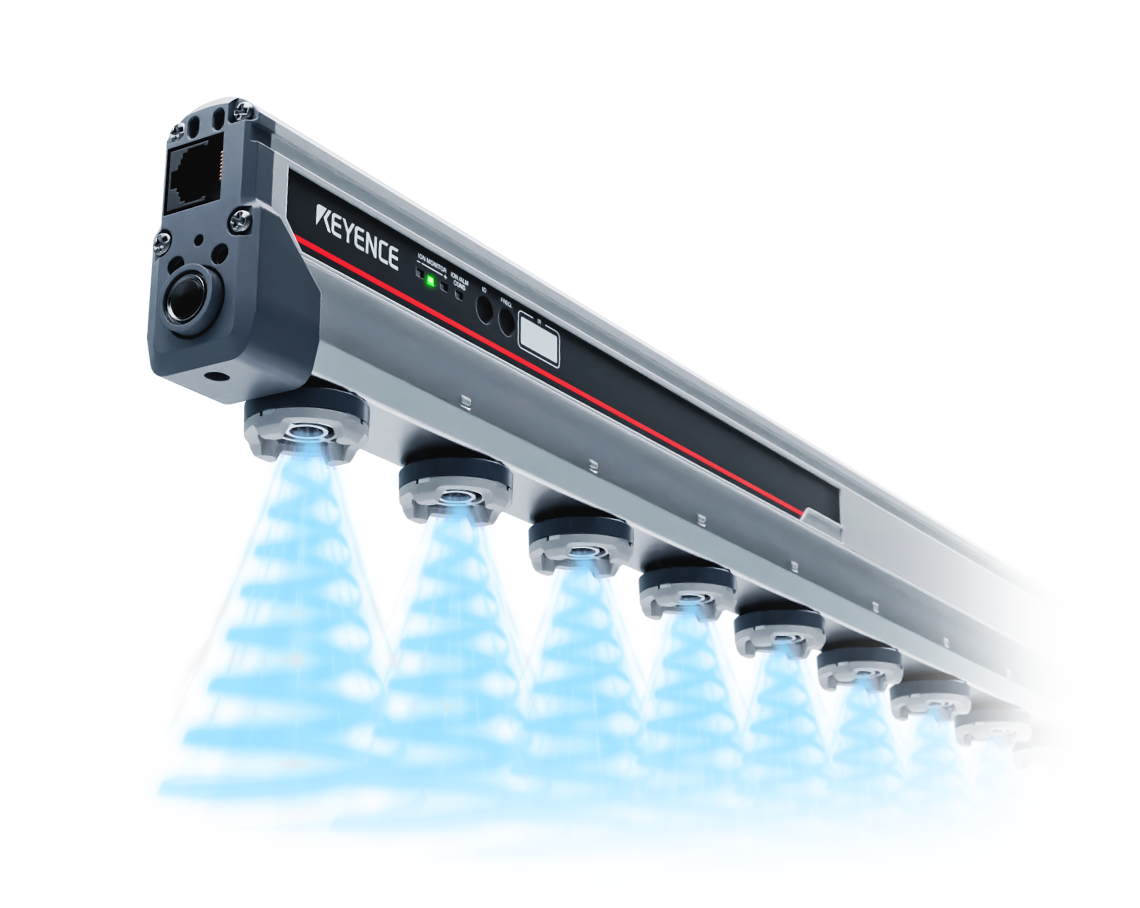
A stock image related to static eliminator.
In advanced manufacturing environments, techniques such as 3D printing may also be utilized for prototyping or producing complex parts that require high precision. This flexibility allows manufacturers to innovate and adapt to changing market needs.
How Is Assembly Conducted for Static Eliminators?
The assembly stage involves putting together the various components to create a functional static eliminator. This process can be manual or automated, depending on the complexity of the product and the scale of production. Automated assembly lines may use robotics for tasks such as part placement and soldering, while manual assembly might be necessary for more intricate components that require fine-tuning.
Quality assurance begins during assembly, with operators trained to detect defects early. Components are often assembled in a cleanroom environment to minimize contamination, which is particularly important for devices that rely on precise ionization.
What Finishing Processes Are Essential for Static Eliminators?
Finishing processes enhance the performance and aesthetic appeal of static eliminators. This may involve surface treatments, such as coating or polishing, to improve durability and electrical performance. For instance, coatings can prevent corrosion in metal parts, ensuring longevity in various operational environments.
Additionally, labeling and packaging are crucial for B2B buyers. Proper labeling ensures compliance with local regulations, while packaging must protect the product during transport, especially for international shipments.
What Quality Assurance Measures Are Implemented in Static Eliminator Manufacturing?
Quality assurance (QA) is critical in the production of static eliminators, ensuring that products meet both internal and external standards.
Which International Standards Are Relevant for Static Eliminators?
Manufacturers typically adhere to international standards like ISO 9001, which outlines the requirements for a quality management system. Compliance with ISO standards assures buyers that the manufacturer maintains high-quality production processes.
In addition to ISO certifications, specific industry standards may apply, such as CE marking in Europe, which indicates conformity with health and safety standards. Buyers in the Middle East and Africa should also look for compliance with regional standards, which can vary significantly.
What Are the Key Quality Control Checkpoints in the Manufacturing Process?
Quality control (QC) checkpoints are established throughout the manufacturing process to ensure product integrity. Common checkpoints include:
-
Incoming Quality Control (IQC): This step verifies the quality of raw materials before they enter the production line. Materials that do not meet specifications are rejected.
-
In-Process Quality Control (IPQC): During manufacturing, periodic inspections are conducted to ensure that each stage meets the required standards. This may involve visual inspections, dimensional checks, and functional tests.
-
Final Quality Control (FQC): After assembly, the finished product undergoes rigorous testing to confirm that it functions correctly and meets performance specifications. This might include electrical testing for ionizers to ensure effective static elimination.
What Common Testing Methods Are Used for Static Eliminators?
Several testing methods are employed to validate the performance of static eliminators. These include:
-
Electrical Testing: Measuring the ion balance and elimination speed to ensure compliance with product specifications.
-
Durability Testing: Simulating operational conditions to test the longevity of components under stress.
-
Environmental Testing: Assessing performance in various environmental conditions, such as temperature and humidity variations, which is especially relevant for buyers in diverse climates like those found in Africa and South America.
How Can B2B Buyers Verify Supplier Quality Control?
For international B2B buyers, particularly those from Europe, the Middle East, and Africa, verifying supplier quality control is essential to mitigate risks.
What Auditing Practices Should Buyers Employ?
Buyers can conduct supplier audits to assess compliance with quality standards. This may include reviewing documentation, inspecting production facilities, and observing manufacturing processes firsthand. Regular audits help ensure that suppliers maintain consistent quality over time.
How Important Are Quality Control Reports?
Requesting quality control reports from suppliers is another effective way to verify their QC processes. These reports should detail the results of IQC, IPQC, and FQC, including any corrective actions taken for defects.
What Role Does Third-Party Inspection Play in Quality Assurance?
Engaging third-party inspection services can provide an additional layer of assurance. These independent entities can conduct audits and tests, providing unbiased assessments of supplier capabilities and product quality. This is particularly valuable for buyers who may not have the resources to conduct in-depth inspections themselves.
Conclusion
Understanding the manufacturing processes and quality assurance measures for static eliminators is crucial for international B2B buyers. By familiarizing themselves with these aspects, buyers can make informed decisions, ensuring they partner with reliable manufacturers that meet their quality and performance expectations. This knowledge is especially valuable for companies operating in diverse markets across Africa, South America, the Middle East, and Europe.
Practical Sourcing Guide: A Step-by-Step Checklist for ‘static eliminator’
This practical sourcing guide provides international B2B buyers with a structured checklist to effectively procure static eliminators, ensuring they meet their specific operational needs. As static electricity can cause various production issues, selecting the right static eliminator is crucial for maintaining product quality and operational efficiency.
Step 1: Define Your Technical Specifications
Establishing clear technical specifications is the first step in sourcing a static eliminator. Consider the specific environment where the device will be used, such as clean rooms, production lines, or laboratory settings. Key parameters to define include:
– Elimination Speed: How quickly the device can neutralize static charges.
– Ion Balance: The desired voltage balance to avoid creating additional static charges.
Step 2: Identify Your Application Needs
Understanding the particular applications for which the static eliminator will be used is essential. Different types of static eliminators are designed for specific tasks, such as:
– Point-Type Ionizers: Ideal for localized static elimination in small areas.
– Fan-Type Units: Suitable for larger spaces where air circulation is needed.
Step 3: Evaluate Potential Suppliers
Before making a purchase, conduct thorough evaluations of potential suppliers. Look for suppliers with a strong reputation in the industry by reviewing:
– Company Profiles: Assess their history and experience with static elimination technologies.
– Customer References: Seek testimonials or case studies from businesses in similar sectors or regions.
Step 4: Request Product Demonstrations
Requesting product demonstrations can provide valuable insights into the effectiveness and ease of use of the static eliminators you’re considering. A live demonstration will allow you to:
– Assess Performance: Observe how quickly and effectively the device neutralizes static charges.
– Evaluate Usability: Determine if the device is user-friendly and fits well within your operational workflow.
Step 5: Verify Compliance and Certifications
Ensure that the static eliminators you are considering comply with relevant safety and industry standards. Certifications can indicate quality and reliability, so look for:
– ISO Certifications: These demonstrate adherence to international quality management standards.
– Local Compliance: Verify compliance with regulations specific to your country or region, especially in industries like pharmaceuticals or electronics.
Step 6: Consider Maintenance Requirements
Maintenance can significantly affect the total cost of ownership for static eliminators. Inquire about:
– Maintenance Frequency: Understand how often the device needs maintenance or parts replacement.
– Maintenance Costs: Evaluate potential costs associated with upkeep to ensure they align with your budget.
Step 7: Analyze Total Cost of Ownership
Finally, conduct a comprehensive analysis of the total cost of ownership (TCO) for the static eliminators you are considering. This should include:
– Initial Purchase Price: The upfront cost of the device.
– Operating Costs: Energy consumption, maintenance costs, and potential downtime due to equipment failure.
By following this checklist, B2B buyers can make informed decisions when sourcing static eliminators, ensuring they select the right equipment to enhance their operational efficiency and product quality.
Comprehensive Cost and Pricing Analysis for static eliminator Sourcing
What Are the Key Cost Components in Static Eliminator Sourcing?
When evaluating the cost structure of static eliminators, several components contribute to the final pricing. Understanding these elements is crucial for international B2B buyers seeking cost-effective solutions.
-
Materials: The choice of materials significantly influences the cost. High-quality conductive materials and advanced technologies, such as those used in high-speed sensing ionizers, can lead to higher initial costs but often result in lower total ownership costs due to reduced maintenance and longer lifespans.
-
Labor: Labor costs vary by region, impacting overall pricing. In regions like Africa and South America, labor costs may be lower, but this can affect the quality of craftsmanship. Buyers should assess the skill levels of the workforce to ensure that quality is not compromised for cost savings.
-
Manufacturing Overhead: This includes expenses related to factory operations, utilities, and equipment maintenance. Suppliers in regions with higher operational costs may charge more, influencing the final price.
-
Tooling: Custom tooling for specialized static eliminators can significantly affect pricing. While initial tooling costs can be high, they may be amortized over larger orders, making bulk purchases more economical.
-
Quality Control (QC): Rigorous QC processes ensure product reliability, particularly for high-performance models. Suppliers with stringent QC measures may charge more, but this often translates to fewer defects and reduced warranty claims.
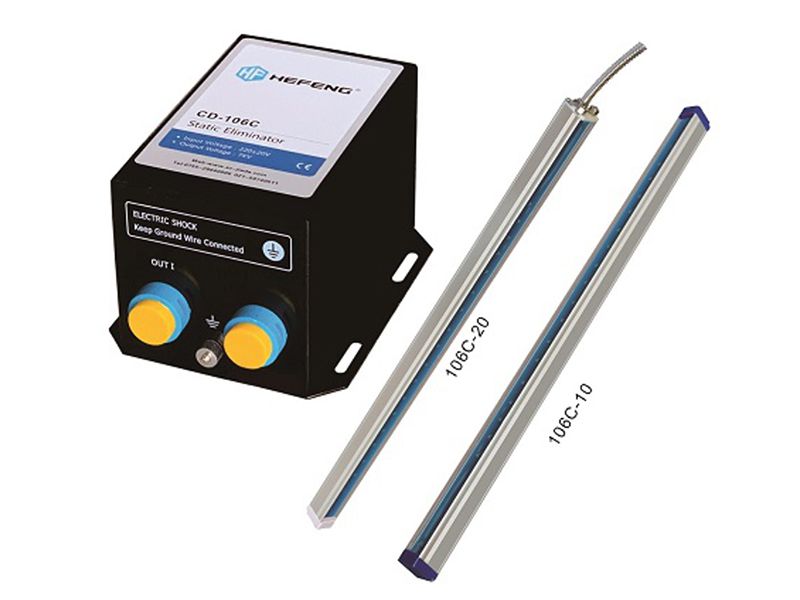
A stock image related to static eliminator.
-
Logistics: Transportation and shipping costs can vary widely based on location and Incoterms. Buyers from Europe or the Middle East sourcing from Asia may face higher logistics costs, impacting the total price.
-
Margin: Supplier profit margins can differ based on market competition and product uniqueness. Understanding these margins can help buyers negotiate better prices, especially when purchasing in volume.
How Do Price Influencers Impact Static Eliminator Costs?
Several factors can influence the pricing of static eliminators, which are essential for buyers to consider when sourcing.
-
Volume/MOQ (Minimum Order Quantity): Purchasing in larger quantities often leads to reduced unit prices. Buyers should negotiate MOQs that align with their operational needs while maximizing cost savings.
-
Specifications and Customization: Custom-built solutions tailored to specific applications can significantly increase costs. Buyers must evaluate whether the added functionality justifies the higher price.
-
Materials and Quality Certifications: Products made from premium materials or those certified to international standards (ISO, CE, etc.) may come at a premium. Buyers should weigh the benefits of these certifications against budget constraints.
-
Supplier Factors: The reputation, reliability, and location of suppliers can influence prices. Established suppliers may charge more due to their proven track record, while lesser-known companies may offer lower prices but higher risks.
-
Incoterms: Understanding the implications of different Incoterms can help buyers manage costs effectively. For example, choosing Ex Works (EXW) might save upfront costs but could lead to higher logistics expenses.
What Are the Best Buyer Tips for Sourcing Static Eliminators?
To navigate the complexities of sourcing static eliminators successfully, consider the following actionable tips:
-
Negotiate Effectively: Leverage your purchasing power, especially if buying in bulk. Suppliers are often willing to negotiate on price, especially for large orders.
-
Focus on Cost-Efficiency: Evaluate the Total Cost of Ownership (TCO), which includes initial costs, maintenance, and operational expenses over the product’s lifespan. Sometimes, a higher upfront investment can lead to lower overall costs.
-
Understand Pricing Nuances: International buyers should be aware of currency fluctuations and their impact on pricing. Building flexibility into contracts can mitigate risks associated with price changes.
-
Seek Local Suppliers: Whenever possible, consider sourcing from local suppliers to reduce shipping costs and lead times, especially for urgent projects.
-
Conduct Thorough Research: Before making a decision, research multiple suppliers and gather quotes. This will provide a clearer picture of market prices and help in identifying the best value.
Disclaimer for Indicative Prices
Prices for static eliminators can vary widely based on the factors discussed above. Buyers should request detailed quotes from multiple suppliers and conduct thorough due diligence to ensure they are making informed purchasing decisions.
Alternatives Analysis: Comparing static eliminator With Other Solutions
When considering solutions for static electricity control, it’s essential to evaluate alternatives to traditional static eliminators. Various technologies exist that can effectively mitigate static charges, each with its own strengths and weaknesses. This analysis aims to provide international B2B buyers, especially from regions like Africa, South America, the Middle East, and Europe, with a clearer understanding of their options.
Comparison Table of Static Eliminators and Alternatives
Comparison Aspect | Static Eliminator | Ionizing Blower | Chemical Antistatic Agents |
---|---|---|---|
Performance | High efficacy in static charge removal; fast response time | Effective over large areas; slower than static eliminators | Reduces static charge over time; variable effectiveness based on application |
Cost | Moderate initial investment; low maintenance costs | Higher upfront and operational costs | Low-cost solutions; may require frequent reapplication |
Ease of Implementation | Requires electrical setup; usually straightforward | Installation may be complex; requires air supply | Simple application; minimal setup required |
Maintenance | Low; some models maintenance-free | Moderate; filter and fan maintenance required | Low; depends on application frequency |
Best Use Case | Precision applications in manufacturing | Large-scale industrial environments | Textile and packaging industries |
What Are the Advantages and Disadvantages of Ionizing Blowers?
Ionizing blowers are an excellent alternative for controlling static electricity, particularly in large industrial settings. They work by blowing ionized air across surfaces, effectively neutralizing static charges over a broad area.
Pros:
– Ideal for large environments, ensuring uniform static control.
– Can be integrated into existing production lines with relative ease.
Cons:
– They typically consume more energy than static eliminators, leading to higher operational costs.
– Maintenance can be more involved due to the need to clean or replace filters regularly.
How Do Chemical Antistatic Agents Compare to Static Eliminators?
Chemical antistatic agents are often used in industries like textiles and packaging to minimize static electricity. These agents can be applied directly to surfaces to reduce static buildup.
Pros:
– Generally lower cost and easier to apply than electronic solutions.
– Effective for specific applications, particularly in non-manufacturing settings.
Cons:
– Their effectiveness may diminish over time, requiring frequent reapplication.
– They may not provide immediate results, making them less suitable for high-speed manufacturing processes.
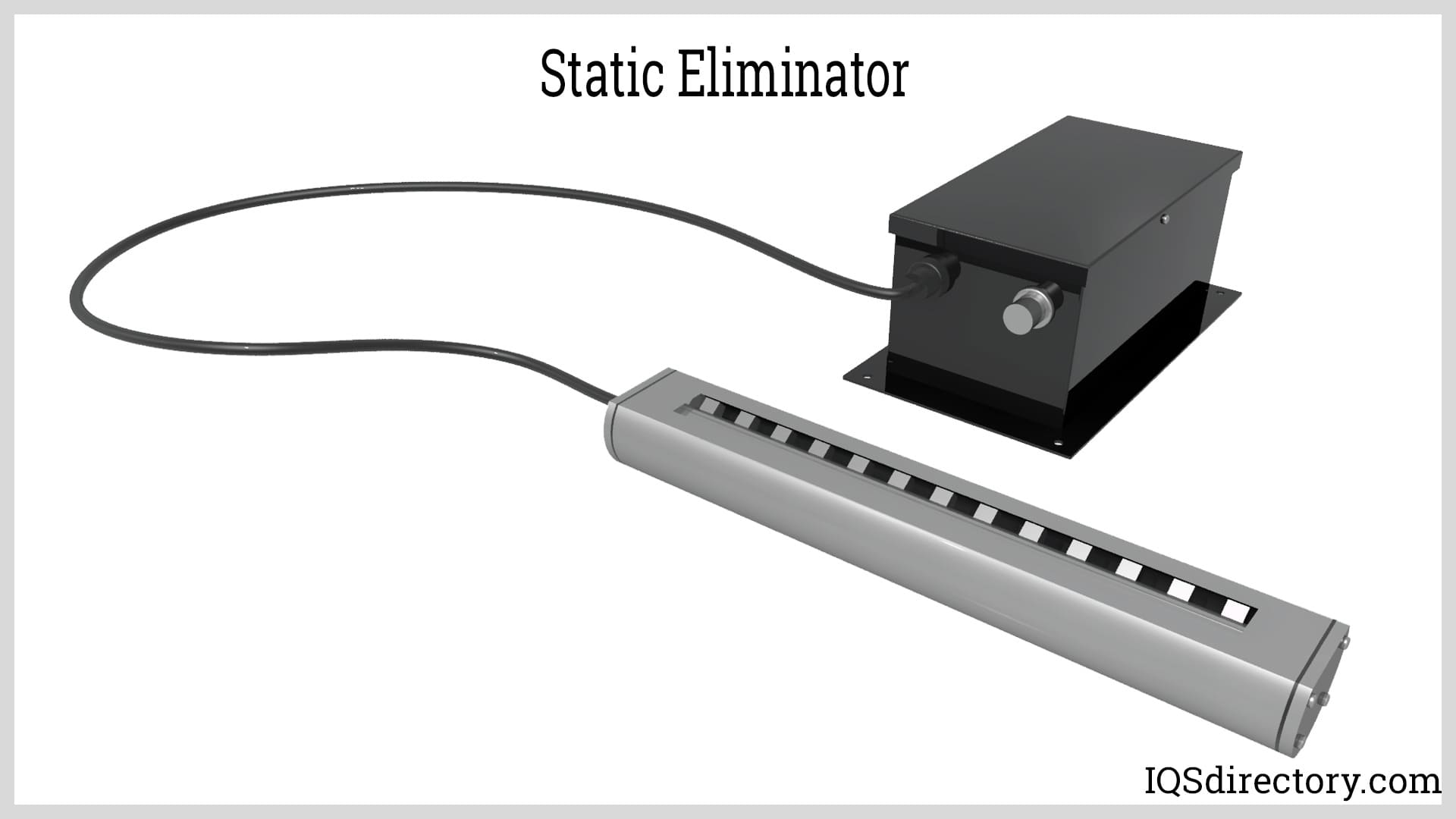
A stock image related to static eliminator.
Conclusion: How Can B2B Buyers Choose the Right Static Control Solution?
Choosing the right static control solution requires a thorough understanding of your specific operational needs and environment. For precision applications where immediate static elimination is critical, static eliminators are often the best choice. However, for larger environments where static charge can be more pervasive, ionizing blowers may offer better coverage. Alternatively, if cost-effectiveness and ease of use are priorities, especially in sectors like textiles, chemical antistatic agents could be a suitable solution. By assessing performance, cost, maintenance, and specific use cases, B2B buyers can make informed decisions that align with their operational goals.
Essential Technical Properties and Trade Terminology for static eliminator
What Are the Key Technical Properties of Static Eliminators?
When selecting a static eliminator, understanding its technical properties is crucial for ensuring optimal performance in various applications. Here are some essential specifications to consider:
1. Ion Balance
Ion balance measures the equilibrium of positive and negative ions produced by the static eliminator. An ideal ion balance is typically within ±5V. This specification is vital for B2B buyers as a stable ion balance reduces the risk of recharging and ensures efficient static elimination, thereby enhancing product quality and reducing defects during manufacturing processes.
2. Static Elimination Speed
This property indicates how quickly the device can neutralize static charges, often measured in seconds (e.g., 0.1 seconds for high-performance models). A faster static elimination speed minimizes downtime in production lines, which is crucial for maintaining productivity and operational efficiency.
3. Maintenance Requirements
Static eliminators can have varying maintenance needs, from frequent cleaning of electrode probes to maintenance-free designs. For businesses, selecting a model with lower maintenance requirements translates to reduced labor costs and less operational disruption, making it a more economical choice over time.
4. Operating Distance
The effective range from which a static eliminator can operate is essential, especially in large industrial settings. Specifications often define this distance in meters or feet. Understanding this property helps buyers determine whether a static eliminator can cover the required area without needing multiple units, optimizing resource allocation.
5. Power Consumption
Efficiency in power usage is increasingly important due to rising energy costs. Static eliminators that utilize advanced technologies, such as supersonic structures, can significantly reduce air consumption and energy costs. B2B buyers should evaluate power consumption to ensure operational cost-effectiveness.
6. Material Grade
The materials used in static eliminators affect durability and performance. Common materials include stainless steel and high-grade plastics. Selecting devices made from superior materials can enhance longevity and reduce the frequency of replacements, providing better ROI for businesses.
What Common Trade Terminology Should B2B Buyers Know?
Understanding industry-specific jargon is crucial for effective communication and negotiation in B2B transactions. Here are some common terms related to static eliminators:
1. OEM (Original Equipment Manufacturer)
This term refers to companies that produce parts or equipment that may be marketed by another manufacturer. In the context of static eliminators, buyers may source devices from OEMs that specialize in high-quality equipment tailored to specific industrial needs.
2. MOQ (Minimum Order Quantity)
MOQ indicates the smallest quantity a supplier is willing to sell. Knowing the MOQ is essential for B2B buyers to gauge inventory requirements and manage budget constraints effectively.
3. RFQ (Request for Quotation)
An RFQ is a document sent to suppliers requesting pricing and terms for specific goods or services. In the context of static eliminators, submitting an RFQ allows buyers to compare options and negotiate better deals based on detailed specifications.
4. Incoterms (International Commercial Terms)
These are a series of predefined commercial terms published by the International Chamber of Commerce (ICC) that clarify the responsibilities of buyers and sellers in international transactions. Familiarity with Incoterms is crucial for B2B buyers to understand shipping, risk, and insurance responsibilities when procuring static eliminators from different countries.
5. Lead Time
Lead time is the time taken between placing an order and receiving the product. For static eliminators, understanding lead times can help businesses plan their production schedules and maintain operational continuity.
6. Warranty Period
This term refers to the duration for which the manufacturer guarantees the performance of the static eliminator. A longer warranty period can indicate higher product quality and reliability, providing peace of mind for buyers investing in these devices.
By comprehensively understanding these technical properties and trade terms, international B2B buyers can make informed decisions when sourcing static eliminators, ultimately enhancing their operational efficiency and product quality.
Navigating Market Dynamics and Sourcing Trends in the static eliminator Sector
What are the Current Market Dynamics and Key Trends in the Static Eliminator Sector?
The global static eliminator market is experiencing robust growth, driven by increasing industrial automation and the rising need for quality control in manufacturing processes. The demand for static eliminators is particularly pronounced in sectors such as electronics, packaging, and pharmaceuticals, where static electricity can compromise product integrity. Emerging technologies like high-speed sensing ionizers and energy-efficient models are reshaping sourcing strategies. Buyers from Africa, South America, the Middle East, and Europe should focus on suppliers that offer advanced features, such as maintenance-free operations and minimal energy consumption, which can lead to significant cost savings over time.
Regional market dynamics reveal distinct preferences and sourcing trends. For instance, European buyers are increasingly prioritizing energy-efficient and sustainable solutions due to stringent environmental regulations. In contrast, buyers from Africa and South America may seek cost-effective options that do not compromise performance, as they often operate in price-sensitive markets. Furthermore, the Middle Eastern market is showing interest in compact and versatile solutions that cater to diverse industrial applications. Understanding these regional nuances is crucial for international B2B buyers looking to optimize their sourcing strategies.
How Can International Buyers Ensure Sustainability and Ethical Sourcing in Static Eliminator Purchases?
Sustainability is becoming a central theme in B2B purchasing decisions, particularly in the static eliminator sector. Buyers should consider the environmental impact of their sourcing decisions, focusing on manufacturers that prioritize eco-friendly materials and processes. The adoption of ‘green’ certifications, such as ISO 14001 for environmental management, can help buyers identify suppliers committed to reducing their ecological footprint.
Moreover, ethical sourcing practices are gaining traction as businesses become more aware of the social implications of their supply chains. This includes ensuring fair labor practices and the responsible extraction of raw materials. Buyers should engage with suppliers that transparently disclose their sourcing practices and provide evidence of compliance with ethical standards. By prioritizing sustainability and ethical sourcing, international B2B buyers can enhance their brand reputation and appeal to increasingly eco-conscious consumers.
What is the Evolution and History of Static Eliminators Relevant to B2B Buyers?
The evolution of static eliminators traces back to the mid-20th century, with early models utilizing radioactive materials like polonium-210 to ionize air and neutralize static charges. These devices were primarily used in specialized applications, such as cleaning film and lenses. However, concerns over safety and environmental impact led to the development of non-radioactive alternatives.
By the 1980s, advancements in technology led to the introduction of electronic static eliminators, which offered improved efficiency and safety. Today, the market is characterized by a diverse range of products, including ionizers that operate without air and those designed for specific applications. This historical context is essential for B2B buyers, as it highlights the progression towards safer, more effective solutions that meet the evolving demands of various industries. Understanding this evolution can help buyers make informed decisions and select products that align with modern industrial needs.
Frequently Asked Questions (FAQs) for B2B Buyers of static eliminator
-
How do I solve static electricity issues in my manufacturing facility?
To effectively solve static electricity problems, start by assessing your facility’s specific needs. Identify areas with high static build-up and choose the appropriate static eliminator type—options include ionizers, blowers, or handheld devices. Ensure the selected equipment matches your operational environment, such as cleanrooms or production lines. Regular maintenance and monitoring of equipment performance are crucial to sustaining effective static control. Consulting with a specialist can provide tailored solutions that minimize downtime and enhance product quality. -
What is the best static eliminator for sensitive electronic components?
For sensitive electronic components, a high-speed ionizer with low air consumption is ideal. Devices like the SJ-E series from KEYENCE offer rapid static elimination while minimizing particle adherence, making them suitable for electronics manufacturing. Look for features such as maintenance-free operation and self-diagnosis to ensure reliability. Additionally, consider ionizers that operate without air if your environment requires a dust-free atmosphere, ensuring optimal performance without compromising product integrity. -
How can I ensure the quality and reliability of static eliminators from suppliers?
To ensure quality and reliability, thoroughly vet suppliers by reviewing their certifications, quality assurance processes, and customer testimonials. Request samples or case studies to evaluate product performance in environments similar to yours. Additionally, inquire about their warranty policies and after-sales support to address any operational challenges. Engaging in direct communication with the supplier can also provide insights into their commitment to quality and responsiveness to customer needs. -
What customization options are available for static eliminators?
Many manufacturers offer customization options for static eliminators to meet specific industrial requirements. Customizations may include size, voltage specifications, or additional features like automatic cleaning systems. Discuss your needs with potential suppliers, providing details about your operating conditions and any unique challenges. This will help ensure that the static eliminator you choose is tailored to optimize performance and integrate seamlessly into your existing processes. -
What are the minimum order quantities (MOQ) for static eliminators?
Minimum order quantities (MOQ) can vary significantly among suppliers, often depending on the type of product and its manufacturing complexity. For bulk purchases, MOQs may be lower, while customized units typically require larger orders. When sourcing static eliminators, ask potential suppliers about their MOQs and explore options for smaller trial orders to assess performance before committing to larger quantities. This approach mitigates risk and helps ensure the product meets your expectations. -
What payment terms should I expect when purchasing static eliminators internationally?
Payment terms for international purchases of static eliminators can vary, typically ranging from upfront payment to net 30 or net 60 days after delivery. Discuss payment methods such as wire transfers, letters of credit, or online payment systems to find a solution that works for both parties. Ensure that all payment terms are clearly outlined in the purchase agreement to avoid misunderstandings. Additionally, consider currency fluctuations and their potential impact on costs when negotiating terms. -
How can I manage logistics and shipping for static eliminators?
Effective logistics management for shipping static eliminators involves selecting reliable freight forwarders experienced in handling industrial equipment. Assess shipping options, including air freight for urgent needs and sea freight for cost-effectiveness. Ensure that your supplier provides proper packaging to protect equipment during transit. Additionally, familiarize yourself with customs regulations in your country to avoid delays, and consider using insurance to mitigate risks associated with international shipping. -
What are the common maintenance practices for static eliminators?
Regular maintenance practices for static eliminators include routine cleaning of electrode probes, checking for wear and tear, and ensuring proper functioning of all components. Some advanced models offer maintenance-free operation with self-cleaning features. Schedule periodic inspections to assess performance and replace parts as needed. Maintaining a log of service history can help track equipment performance over time, ensuring that static eliminators operate efficiently and effectively throughout their lifespan.
Important Disclaimer & Terms of Use
⚠️ Important Disclaimer
The information provided in this guide, including content regarding manufacturers, technical specifications, and market analysis, is for informational and educational purposes only. It does not constitute professional procurement advice, financial advice, or legal advice.
While we have made every effort to ensure the accuracy and timeliness of the information, we are not responsible for any errors, omissions, or outdated information. Market conditions, company details, and technical standards are subject to change.
B2B buyers must conduct their own independent and thorough due diligence before making any purchasing decisions. This includes contacting suppliers directly, verifying certifications, requesting samples, and seeking professional consultation. The risk of relying on any information in this guide is borne solely by the reader.
Strategic Sourcing Conclusion and Outlook for static eliminator
As the global demand for static eliminators continues to rise, strategic sourcing remains pivotal for international B2B buyers aiming to enhance operational efficiency and reduce costs. By selecting high-performance models—such as the maintenance-free options and energy-efficient designs highlighted in this guide—businesses can significantly lower their total cost of ownership while ensuring optimal static control across various applications.
What are the key considerations for sourcing static eliminators in diverse markets? Understanding regional requirements, compliance standards, and technological advancements is crucial. Buyers from Africa, South America, the Middle East, and Europe should prioritize suppliers that offer comprehensive support, including training and maintenance, to maximize the lifespan and efficacy of their static eliminators.
Looking ahead, the integration of advanced technologies such as supersonic structures and automated maintenance systems will reshape the landscape of static elimination solutions. International buyers are encouraged to stay informed on innovations and market trends, ensuring they make informed sourcing decisions that align with their sustainability goals and operational needs. Embrace the future of static control—partner with trusted suppliers and leverage cutting-edge technology to secure your competitive advantage in the global marketplace.