Enhance Air Quality: The Ultimate Air Scrubber Guide (2025)
Introduction: Navigating the Global Market for air scrubber
As international B2B buyers increasingly prioritize indoor air quality, sourcing effective air scrubbers has emerged as a critical challenge. Poor indoor air can significantly impact health, productivity, and overall business operations. This comprehensive guide aims to equip you with the essential knowledge to navigate the global market for air scrubbers, ensuring you make informed purchasing decisions. We will explore various types of air scrubbers, their specific applications across different industries, and factors to consider when vetting suppliers. Additionally, we will provide insights into cost considerations and the latest advancements in air purification technologies.
With a focus on the unique needs of buyers from Africa, South America, the Middle East, and Europe—particularly in countries like Germany and France—this guide empowers you to understand the diverse market landscape. By examining the benefits of air scrubbers, such as their ability to reduce allergens, eliminate odors, and mitigate airborne pathogens, you can confidently select products that align with your organizational goals. Whether you’re a facility manager in a commercial building or a procurement officer for a government institution, this guide will serve as your roadmap to achieving superior indoor air quality and enhancing your operational efficiency.
Understanding air scrubber Types and Variations
Type Name | Key Distinguishing Features | Primary B2B Applications | Brief Pros & Cons for Buyers |
---|---|---|---|
In-Duct Air Scrubbers | Installed in HVAC systems; continuous air purification | Commercial buildings, hospitals | Pros: Seamless integration, continuous operation. Cons: Higher installation costs, requires HVAC access. |
Portable Air Scrubbers | Mobile units; ideal for spot treatment | Construction sites, disaster recovery | Pros: Flexibility, easy to move. Cons: Limited coverage area, may require multiple units for large spaces. |
Negative Air Machines | Creates negative air pressure to contain contaminants | Abatement projects, restoration work | Pros: Effective in controlling airborne pollutants. Cons: Noise level can be high, requires proper setup. |
UV-C Air Scrubbers | Utilizes ultraviolet light to kill pathogens | Laboratories, healthcare facilities | Pros: High efficacy against viruses and bacteria. Cons: Limited effectiveness on larger particulate matter. |
Chemical Scrubbers | Employs chemical reactions to remove specific gases | Industrial applications, wastewater treatment | Pros: Effective for specific contaminants. Cons: Can be costly and complex to maintain. |
What are In-Duct Air Scrubbers and Their Benefits for B2B Buyers?
In-duct air scrubbers are integrated directly into the HVAC systems of commercial buildings. They continuously purify air by using advanced technologies like ActivePure, which neutralizes pathogens and contaminants. Ideal for hospitals and large office spaces, these systems ensure a consistent air quality standard, vital for health and productivity. B2B buyers should consider installation costs and the need for HVAC access but can benefit from long-term savings on air quality management.
Why Choose Portable Air Scrubbers for Temporary Needs?
Portable air scrubbers are versatile units that can be easily relocated to address specific air quality issues, making them perfect for construction sites or disaster recovery efforts. Their mobility allows businesses to target areas with contamination or poor air quality quickly. However, buyers should be aware that while they offer flexibility, their limited coverage may necessitate multiple units, which can increase costs.
How Do Negative Air Machines Control Contaminants?
Negative air machines create a controlled environment by generating negative pressure, preventing contaminants from escaping into other areas. They are particularly useful in abatement projects, such as mold remediation or during renovations. While they effectively manage airborne pollutants, buyers must consider the noise levels and the complexity of setup, ensuring they have the necessary expertise for installation.
What Makes UV-C Air Scrubbers Effective in Healthcare Settings?
UV-C air scrubbers utilize ultraviolet light to inactivate viruses and bacteria in the air, making them highly effective for environments like laboratories and healthcare facilities. These units are essential for maintaining stringent hygiene standards. However, B2B buyers should note that while they excel at targeting pathogens, they may not be as effective against larger particulate matter, necessitating a combined approach with other filtration methods.
When to Consider Chemical Scrubbers in Industrial Applications?
Chemical scrubbers are specialized systems that use chemical reactions to remove specific gases and pollutants from the air, making them suitable for industrial applications, such as wastewater treatment facilities. While they can effectively address targeted contaminants, buyers should evaluate the complexity and costs associated with maintenance and operation, which can be significant compared to other air purification technologies.
Key Industrial Applications of air scrubber
Industry/Sector | Specific Application of Air Scrubber | Value/Benefit for the Business | Key Sourcing Considerations for this Application |
---|---|---|---|
Healthcare | Infection control in hospitals and clinics | Reduces airborne pathogens, improving patient and staff safety | Compliance with health regulations; efficiency and capacity |
Food Processing | Odor and contaminant control in food production facilities | Ensures product safety and quality, enhances worker comfort | FDA compliance; robust filtration systems; energy efficiency |
Construction | Dust and particle management on job sites | Protects workers’ health, minimizes cleanup costs | Portability; durability; adaptability to various environments |
Hospitality | Indoor air quality improvement in hotels | Enhances guest experience, increases customer satisfaction | Aesthetic design; quiet operation; maintenance support |
Educational Institutions | Air purification in schools and universities | Reduces allergens and pollutants, promoting better learning | Scalability; integration with existing HVAC systems; cost-effectiveness |
How Are Air Scrubbers Used in Healthcare Facilities?
In healthcare settings, air scrubbers play a critical role in infection control by reducing airborne pathogens. Hospitals and clinics often face challenges with airborne diseases, which can compromise patient safety. Air scrubbers equipped with advanced filtration technology actively neutralize bacteria and viruses, including strains like MRSA and COVID-19. For international buyers, especially in regions with high disease prevalence, sourcing air scrubbers that meet stringent health regulations and offer high efficiency is essential.
What Role Do Air Scrubbers Play in Food Processing?
In the food processing industry, air scrubbers are utilized to maintain a contaminant-free environment. These systems effectively eliminate odors and airborne particles that can affect food quality and safety. By ensuring clean air, businesses can comply with food safety standards and enhance worker comfort. Buyers in this sector must consider FDA compliance and the effectiveness of filtration systems, as well as the energy efficiency of the units to minimize operational costs.
How Do Air Scrubbers Benefit Construction Sites?
Construction sites are notorious for dust and particulate matter, which can pose health risks to workers. Air scrubbers are employed to manage dust levels, providing cleaner air and reducing the need for extensive cleanup after projects. This application not only protects worker health but also contributes to compliance with occupational safety regulations. Buyers should prioritize portable and durable models that can adapt to various environments and withstand the rigors of construction.
Why Are Air Scrubbers Important in Hospitality?
In the hospitality industry, air scrubbers significantly enhance indoor air quality, which is crucial for guest satisfaction. By actively removing allergens and pollutants, hotels can offer a more pleasant environment, improving overall guest experiences. International buyers should look for systems that are aesthetically pleasing and operate quietly to maintain a welcoming atmosphere. Maintenance support and energy efficiency are also key considerations to ensure long-term operational viability.
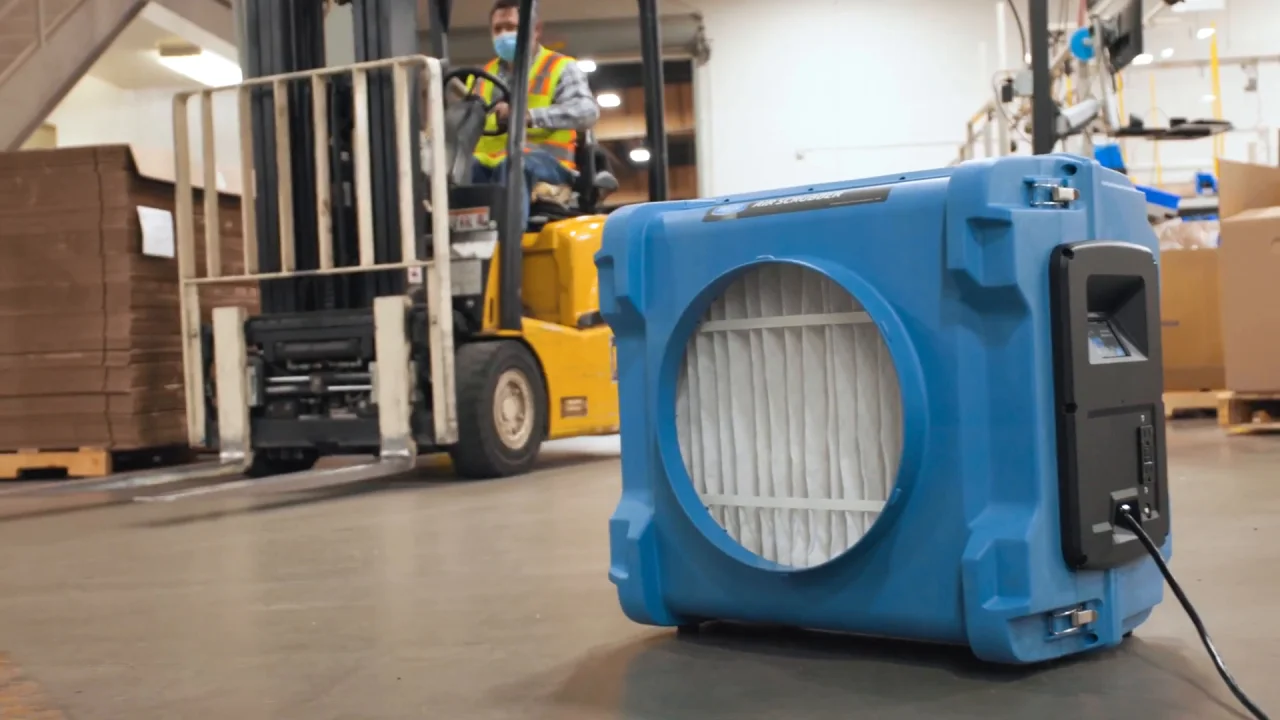
A stock image related to air scrubber.
How Do Educational Institutions Benefit from Air Scrubbers?
Educational institutions utilize air scrubbers to create a healthier learning environment by reducing allergens and airborne pollutants. This is particularly important in schools where children may be more susceptible to respiratory issues. Clean air contributes to improved focus and academic performance. Buyers in this sector should seek scalable solutions that can integrate with existing HVAC systems while also being cost-effective to accommodate budget constraints.
3 Common User Pain Points for ‘air scrubber’ & Their Solutions
Scenario 1: Difficulty in Ensuring Indoor Air Quality Compliance
The Problem:
B2B buyers in sectors such as healthcare, education, and food services often face stringent regulations regarding indoor air quality. These regulations require maintaining specific air purity standards to safeguard health and prevent contamination. Buyers may struggle with sourcing effective air scrubbers that not only meet compliance standards but also fit the unique requirements of their facilities. In addition, they may find it challenging to evaluate the effectiveness of various air scrubbers, leading to potential non-compliance and health risks for employees and clients.
The Solution:
To ensure compliance, it’s crucial to select air scrubbers that are certified and validated against industry standards. Buyers should look for air scrubbers that have been tested for specific contaminants relevant to their industry, such as bacteria, allergens, and volatile organic compounds (VOCs). A good starting point is to consult with manufacturers who provide comprehensive data on their products’ performance in real-world settings.
Additionally, buyers can engage third-party testing facilities to assess air quality before and after the installation of air scrubbers. This will not only provide peace of mind but also serve as documentation for compliance audits. Regular maintenance and filter replacement are also vital to ensure optimal performance and compliance. Establish a schedule based on the manufacturer’s recommendations and any environmental factors that may affect air quality.
Scenario 2: High Operational Costs of Air Scrubbing Systems
The Problem:
Many businesses are concerned about the operational costs associated with running air scrubbers, especially in large facilities where energy consumption can be significant. Buyers may face the dilemma of balancing effective air purification with budget constraints. High energy bills can lead to reluctance in adopting advanced air purification technologies, even if they promise better indoor air quality.
The Solution:
To mitigate operational costs, buyers should prioritize energy-efficient air scrubbers that offer variable speed controls and programmable settings. Look for models with high Energy Star ratings or other energy efficiency certifications. These systems often have smart features that allow for real-time monitoring and adjustment based on occupancy levels and air quality readings, reducing unnecessary energy consumption.
Additionally, consider incorporating air scrubbers into a broader energy management strategy. Implementing predictive maintenance schedules can also help reduce costs by identifying potential inefficiencies before they lead to costly repairs or increased energy use. It’s beneficial to conduct a cost-benefit analysis, weighing the long-term savings from improved air quality against initial investment and operational costs.
Scenario 3: Lack of Knowledge About Installation and Maintenance
The Problem:
B2B buyers often face challenges related to the installation and maintenance of air scrubbers, particularly if they lack technical expertise. Misunderstanding how to properly install or maintain the equipment can lead to suboptimal performance, higher operating costs, and even health risks due to inadequate air purification. This can be especially problematic for international buyers who may encounter different installation standards and practices in their regions.
The Solution:
To address these concerns, buyers should seek air scrubbers that come with comprehensive installation and maintenance manuals, ideally supported by video tutorials or online resources. Engaging a qualified HVAC technician or a certified installer familiar with the specific model can ensure proper setup and compliance with local regulations.
Furthermore, consider establishing a partnership with the manufacturer for ongoing support and training. Some companies offer training programs for their products that educate staff on effective usage and maintenance practices. Regular training can empower facility management teams to handle routine checks and maintenance effectively, ensuring that air scrubbers operate at peak performance.
By taking these actionable steps, international B2B buyers can navigate common challenges associated with air scrubbers, ensuring they make informed decisions that enhance indoor air quality while remaining compliant and cost-effective.
Strategic Material Selection Guide for air scrubber
What Materials Are Commonly Used in Air Scrubbers?
When selecting materials for air scrubbers, it is essential to consider their properties, performance, and suitability for specific applications. Below, we analyze four common materials used in the construction of air scrubbers, focusing on their key properties, advantages, disadvantages, and specific considerations for international B2B buyers.
What Are the Key Properties of Aluminum in Air Scrubbers?
Aluminum is frequently used in air scrubber construction due to its lightweight nature and excellent corrosion resistance. It typically has a temperature rating up to 150°C (302°F) and can withstand moderate pressure levels. Its inherent resistance to oxidation makes it ideal for environments where moisture is present.
Pros and Cons:
– Pros: Lightweight, corrosion-resistant, and easy to fabricate, aluminum is cost-effective for large-scale production.
– Cons: While durable, it is less robust than other metals like stainless steel, which may limit its use in high-stress applications.
Impact on Application:
Aluminum is compatible with various filtration media, making it versatile for different air quality applications. However, its lower strength may not be suitable for extremely demanding environments.
Considerations for International Buyers:
Buyers in Europe and the Middle East should ensure compliance with relevant standards such as EN 573 for aluminum alloys, while those in Africa and South America should consider local regulations regarding material sourcing and environmental impact.
How Does Stainless Steel Enhance Air Scrubber Performance?
Stainless steel is renowned for its strength and durability, with a temperature rating often exceeding 300°C (572°F). Its excellent corrosion resistance, particularly in harsh environments, makes it a preferred choice for industrial applications.
Pros and Cons:
– Pros: High durability and strength, excellent resistance to corrosion, and longevity in demanding conditions.
– Cons: Higher manufacturing costs and complexity due to the need for specialized welding techniques.
Impact on Application:
Stainless steel is ideal for air scrubbers that require high-performance filtration systems, especially in industries like pharmaceuticals and food processing where hygiene is critical.
Considerations for International Buyers:
Compliance with standards such as ASTM A240 for stainless steel is crucial. Buyers from Germany and France should also consider certifications like ISO 9001 for quality assurance.
What Role Does Plastic Play in Air Scrubber Design?
Plastics, particularly high-density polyethylene (HDPE) and polyvinyl chloride (PVC), are increasingly being used in air scrubbers due to their lightweight and cost-effective nature. They typically perform well at temperatures up to 60°C (140°F).
Pros and Cons:
– Pros: Cost-effective, lightweight, and resistant to chemical corrosion.
– Cons: Limited temperature and pressure ratings compared to metals, which may restrict their use in high-performance applications.
Impact on Application:
Plastics are suitable for residential air scrubbers and less demanding commercial applications, where the risk of extreme conditions is low.
Considerations for International Buyers:
Buyers should ensure compliance with standards such as ASTM D638 for plastics. In regions like South America, where environmental regulations are evolving, sourcing recyclable materials can enhance sustainability.
How Do Fiberglass Materials Contribute to Air Scrubber Efficiency?
Fiberglass is used in air scrubbers for its excellent filtration properties and thermal insulation. It is capable of withstanding temperatures up to 200°C (392°F) and provides good chemical resistance.
Pros and Cons:
– Pros: Lightweight, good thermal insulation, and effective in filtering fine particles.
– Cons: Can be more expensive than traditional materials and may require specialized handling during installation.
Impact on Application:
Fiberglass is particularly effective in environments that require high levels of air purification, such as laboratories and clean rooms.
Considerations for International Buyers:
Compliance with standards such as ASTM D578 for fiberglass is essential. Buyers in Africa and the Middle East should also consider the availability of local suppliers to reduce lead times.
Summary Table of Material Selection for Air Scrubbers
Material | Typical Use Case for Air Scrubber | Key Advantage | Key Disadvantage/Limitation | Relative Cost (Low/Med/High) |
---|---|---|---|---|
Aluminum | Residential and light commercial air scrubbers | Lightweight and corrosion-resistant | Less robust than other metals | Medium |
Stainless Steel | Industrial air scrubbers in demanding environments | High durability and strength | Higher manufacturing costs | High |
Plastic | Residential and low-demand commercial applications | Cost-effective and lightweight | Limited temperature and pressure ratings | Low |
Fiberglass | High-performance air scrubbers in labs | Excellent filtration properties | More expensive and requires specialized handling | Medium |
This guide provides B2B buyers with essential insights into material selection for air scrubbers, ensuring informed decisions that align with their operational needs and regulatory requirements.
In-depth Look: Manufacturing Processes and Quality Assurance for air scrubber
What Are the Main Stages of Manufacturing Air Scrubbers?
The manufacturing process of air scrubbers involves several key stages designed to ensure high-quality output and compliance with international standards. Understanding these stages is crucial for B2B buyers seeking reliable suppliers.
Material Preparation: What Materials Are Used in Air Scrubber Manufacturing?
Material preparation is the foundational step in the manufacturing of air scrubbers. Common materials include:
- Metal Components: Steel or aluminum is often used for the housing to ensure durability.
- Filtration Media: HEPA filters, activated carbon, and other specialized materials are selected for their efficacy in removing specific contaminants.
- Electronic Components: Sensors and control systems are crucial for the operation of advanced air scrubbers.
Each material must undergo rigorous quality checks before moving to the next stage. Suppliers should provide certificates of compliance for these materials to ensure they meet safety and performance standards.
Forming: How Are Air Scrubber Components Fabricated?
The forming stage involves various techniques to create the individual components of the air scrubber:
- Metal Fabrication: Techniques such as laser cutting, welding, and bending are used to create the outer casing and internal structures. Precision in this stage is critical, as any inaccuracies can affect performance and durability.
- Molding: For plastic components, injection molding is often used, ensuring that parts fit together seamlessly.
- Filter Production: The production of filtration media involves processes like pleating for HEPA filters, which increases the surface area for better filtration efficiency.
Buyers should inquire about the manufacturing capabilities and technologies employed by their suppliers to ensure they utilize modern and efficient techniques.
Assembly: What Does the Assembly Process Look Like for Air Scrubbers?
Once the components are fabricated, the assembly stage begins. This process typically includes:
- Component Integration: Each part, from the housing to the filtration system, is brought together in a clean environment to avoid contamination.
- Electrical Assembly: Wiring and connecting electronic components, including motors and sensors, are done in accordance with strict electrical standards.
- Quality Checks: As components are assembled, initial quality checks (IPQC) are performed to ensure that each unit functions as intended.
For B2B buyers, understanding the assembly process helps in assessing the complexity and reliability of the final product.
Finishing: How Are Air Scrubbers Prepared for Market?
The finishing stage involves several steps aimed at ensuring the product is ready for distribution:
- Surface Treatment: This may include powder coating or painting to enhance durability and aesthetics.
- Final Quality Control: A final inspection (FQC) is conducted to verify that the air scrubber meets all specifications and performance criteria before packaging.
Buyers should ask suppliers about their finishing processes, as these can significantly impact the longevity and performance of the air scrubber.
What Quality Assurance Standards Should B2B Buyers Consider?
Quality assurance (QA) is essential for ensuring that air scrubbers meet international safety and performance standards. Buyers should familiarize themselves with the following standards:
International Standards: Which Certifications Are Relevant?
-
ISO 9001: This is a widely recognized standard that outlines quality management principles. Compliance indicates that a manufacturer consistently provides products that meet customer and regulatory requirements.
-
CE Marking: In Europe, CE marking is crucial for products sold within the European Economic Area. It signifies that the product meets health, safety, and environmental protection standards.
-
API Standards: For air scrubbers used in industrial applications, American Petroleum Institute (API) standards may apply, particularly regarding safety and reliability.
Understanding these certifications can help buyers choose suppliers that adhere to high-quality manufacturing practices.
What Are the Key Quality Control Checkpoints in Air Scrubber Manufacturing?
To maintain high standards throughout the manufacturing process, several quality control checkpoints are implemented:
-
Incoming Quality Control (IQC): Before materials are used, they undergo rigorous testing to ensure they meet specified standards. This includes checking for defects in raw materials and components.
-
In-Process Quality Control (IPQC): During the manufacturing process, various checks are conducted to monitor the assembly and fabrication stages. This ensures that any issues are identified and addressed promptly.
-
Final Quality Control (FQC): After assembly, the final product is tested for performance, efficiency, and safety. This is the last line of defense to ensure only high-quality products reach the market.
How Can B2B Buyers Verify Supplier Quality Control?
When sourcing air scrubbers, buyers can take several steps to verify the quality control practices of potential suppliers:
-
Supplier Audits: Conducting audits can provide insights into a supplier’s manufacturing processes and quality management systems. Buyers should consider onsite visits to assess the facility firsthand.
-
Requesting Quality Reports: Suppliers should be willing to provide detailed quality reports that outline their testing methodologies, results, and adherence to relevant standards.
-
Third-Party Inspections: Engaging third-party inspection agencies can add an additional layer of assurance. These agencies can conduct independent evaluations of the products and processes.
What Are the Quality Control Nuances for International B2B Buyers?
International buyers, particularly from regions such as Africa, South America, the Middle East, and Europe, should be aware of certain nuances in quality control:
-
Regulatory Compliance: Different regions may have specific regulatory requirements. Understanding local regulations is crucial for ensuring compliance and avoiding potential fines or product recalls.
-
Logistical Considerations: The transportation of air scrubbers can introduce risks. Buyers should verify that suppliers have robust quality control measures in place for handling and shipping products.
-
Cultural Differences: Communication styles and business practices can vary significantly across regions. Building strong relationships with suppliers can help facilitate better understanding and adherence to quality expectations.
By being informed and proactive, international B2B buyers can navigate the complexities of sourcing air scrubbers, ensuring they receive high-quality products that meet their specific needs.
Practical Sourcing Guide: A Step-by-Step Checklist for ‘air scrubber’
In the evolving landscape of indoor air quality management, sourcing an effective air scrubber is essential for businesses aiming to provide a safe and healthy environment. This step-by-step checklist will guide B2B buyers, particularly from Africa, South America, the Middle East, and Europe, in procuring the right air scrubber for their specific needs.
Step 1: Define Your Technical Specifications
Understanding your requirements is the first step in sourcing an air scrubber. Consider the size of the area you need to purify, the types of contaminants you are targeting, and any specific features that may be necessary, such as portability or integration with existing HVAC systems. This clarity will help you identify products that meet your operational needs.
- Contaminants: Identify if you need to eliminate allergens, mold, bacteria, or odors.
- Area Size: Measure the square footage to ensure the air scrubber can handle the volume of air required.
Step 2: Research Available Technologies
Different air scrubbers use various technologies, such as HEPA filters, UV light, or ActivePure technology. Familiarizing yourself with these technologies will help you understand their effectiveness against specific pollutants. Look for products that provide detailed explanations of their filtration methods and how they work.
- HEPA Filters: Effective for trapping small particles.
- ActivePure Technology: Proven to reduce pathogens and improve air quality actively.
Step 3: Evaluate Potential Suppliers
Before committing, it’s crucial to vet suppliers thoroughly. Request company profiles, case studies, and references from buyers in a similar industry or region. Investigate their reputation in the market and any certifications that demonstrate compliance with international standards.
- Certifications: Look for ISO certifications or other relevant quality assurances.
- Case Studies: Ask for examples of successful implementations in similar environments.
Step 4: Assess Product Performance and Reviews
Examine product performance metrics and customer reviews to gauge the efficacy of the air scrubbers you are considering. Look for independent testing results or certifications that validate the manufacturer’s claims.
- Testing Results: Seek third-party lab results that demonstrate effectiveness against specific contaminants.
- Customer Feedback: Analyze reviews to understand user experiences and reliability.
Step 5: Consider After-Sales Support and Warranty
A robust after-sales support system can significantly enhance your purchasing decision. Ensure the supplier offers comprehensive training, installation support, and a clear warranty policy. This support is crucial for maintaining the air scrubber’s efficiency over time.
- Warranty Terms: Check the length and coverage of the warranty.
- Technical Support: Confirm the availability of customer service for troubleshooting and maintenance.
Step 6: Request Quotes and Compare Pricing
Once you have shortlisted potential air scrubbers, request quotes from multiple suppliers. Compare the pricing, but also consider what is included in the cost, such as installation, maintenance, and additional filters.
- Total Cost of Ownership: Factor in ongoing costs for maintenance and replacement filters.
- Negotiation: Use quotes to negotiate better terms or discounts.
Step 7: Make an Informed Decision
After thorough research and evaluation, choose the air scrubber that best fits your requirements and budget. Ensure that your final choice aligns with your organizational goals regarding health, safety, and environmental standards.
- Documentation: Keep all agreements and product specifications documented for future reference.
- Feedback Loop: Establish a process for evaluating the air scrubber’s performance post-installation to ensure it meets your expectations.
By following this practical sourcing guide, international B2B buyers can navigate the complexities of procuring an air scrubber, ultimately ensuring a healthier indoor environment for their operations.
Comprehensive Cost and Pricing Analysis for air scrubber Sourcing
What Are the Key Cost Components in Air Scrubber Sourcing?
When sourcing air scrubbers, international B2B buyers must consider multiple cost components that contribute to the overall pricing structure. The primary elements include:
-
Materials: High-quality components, such as HEPA filters, UV light systems, and specialized catalysts, significantly influence costs. The choice of materials directly affects durability and efficiency.
-
Labor: Labor costs encompass both manufacturing and assembly. Regions with higher labor costs will naturally see a rise in the final price. Understanding the labor market in the supplier’s location can provide insights into potential pricing variations.
-
Manufacturing Overhead: This includes expenses related to factory operations, such as utilities, rent, and equipment maintenance. Manufacturers with efficient overhead management can offer more competitive pricing.
-
Tooling: The cost of machinery and tools necessary for production can vary widely. For customized air scrubber designs, tooling costs may increase, impacting the overall pricing.
-
Quality Control (QC): Effective QC processes ensure product reliability, but they also add to the cost. Buyers should inquire about the QC measures in place and how they contribute to pricing.
-
Logistics: Shipping costs can vary based on distance, weight, and shipping method. For international buyers, understanding Incoterms can help clarify who bears these costs and when they apply.
-
Margin: Supplier profit margins can vary based on market conditions, competition, and product demand. Buyers should be aware of typical margins in the air scrubber market to gauge fair pricing.
How Do Price Influencers Affect Air Scrubber Costs?
Several factors can influence the pricing of air scrubbers, particularly for international buyers:
-
Volume/MOQ: Suppliers often have minimum order quantities (MOQs). Purchasing in bulk can lead to significant discounts, making it essential to assess the volume requirements before negotiating.
-
Specifications and Customization: Customized air scrubbers tailored to specific needs or specifications will generally cost more than standard models. Buyers should weigh the necessity of custom features against the associated costs.
-
Materials: The choice of materials not only affects performance but also price. Premium materials may enhance durability and efficiency but will come at a higher cost.
-
Quality and Certifications: Products that meet international quality standards and certifications (like ISO or CE) may have higher upfront costs but can lead to lower Total Cost of Ownership (TCO) through enhanced reliability and energy efficiency.
-
Supplier Factors: The reputation and reliability of suppliers can influence pricing. Established suppliers may charge a premium for their products, but their reliability can justify the higher cost.
-
Incoterms: Understanding the implications of Incoterms is crucial for international transactions. They dictate the responsibilities of buyers and sellers regarding shipping, insurance, and tariffs, which can impact overall costs.
What Are the Best Buyer Tips for Cost Efficiency in Air Scrubber Procurement?
To maximize cost efficiency when sourcing air scrubbers, buyers should consider the following tips:
-
Negotiate Wisely: Effective negotiation can yield better pricing. Be prepared to discuss volume discounts and payment terms.
-
Evaluate Total Cost of Ownership (TCO): Consider not just the initial purchase price but also long-term costs such as maintenance, energy consumption, and potential replacement parts.
-
Research Market Prices: Understanding the average market price for air scrubbers in different regions can help in negotiations. This knowledge can empower buyers to make informed decisions.
-
Assess Supplier Reliability: Look for suppliers with proven track records and positive reviews. A reliable supplier can minimize costs associated with product returns and warranty claims.
-
Understand Pricing Nuances: Be aware of the specific pricing dynamics in target markets, such as Africa, South America, the Middle East, and Europe. Regional factors, including import tariffs and local demand, can significantly influence costs.
Disclaimer on Indicative Prices
Prices for air scrubbers can vary widely based on specifications, supplier, and market conditions. Buyers are encouraged to conduct thorough market research and obtain multiple quotes to ensure they are making informed purchasing decisions.
Alternatives Analysis: Comparing air scrubber With Other Solutions
Understanding Alternatives to Air Scrubbers for Air Quality Improvement
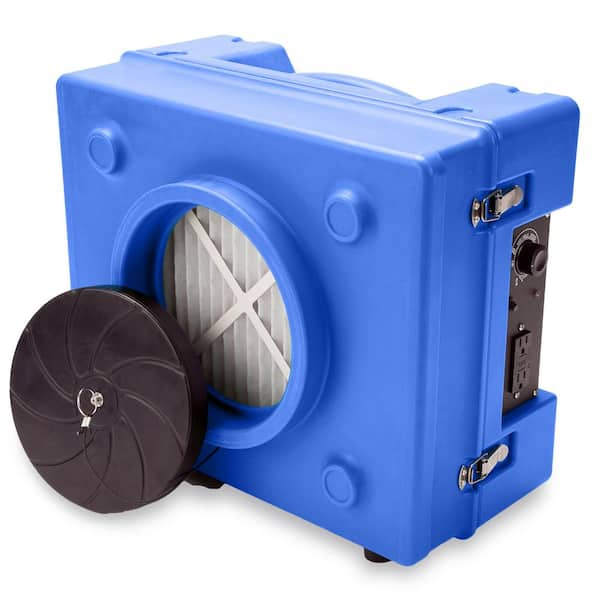
A stock image related to air scrubber.
In the pursuit of cleaner indoor air, B2B buyers are often confronted with various solutions, each with unique benefits and drawbacks. This section explores the effectiveness of air scrubbers in comparison to other air purification technologies, including HEPA filters and UV-C air purifiers. By analyzing these alternatives, international buyers, especially from Africa, South America, the Middle East, and Europe, can make informed decisions that best suit their operational needs.
Comparison Table of Air Scrubber and Alternatives
Comparison Aspect | Air Scrubber | HEPA Filter | UV-C Air Purifier |
---|---|---|---|
Performance | Actively reduces airborne pollutants and pathogens; proven effectiveness against viruses | Highly effective at trapping particles but does not actively eliminate them | Destroys microorganisms using UV light; effective against bacteria and viruses |
Cost | Moderate to high initial investment; ongoing maintenance costs | Generally low initial cost; replacement filters needed regularly | Moderate initial investment; low maintenance costs |
Ease of Implementation | Requires professional installation in HVAC systems | Easy to install; can be DIY | Requires installation; may need electrical work |
Maintenance | Moderate; requires regular cleaning and occasional part replacement | High; filters need to be replaced every 6-12 months | Low; UV bulbs need replacement every 1-2 years |
Best Use Case | Ideal for large facilities needing consistent air quality control | Suitable for smaller spaces or specific rooms | Best for environments with high levels of pathogens, such as hospitals |
What Are the Pros and Cons of HEPA Filters?
HEPA (High-Efficiency Particulate Air) filters are widely recognized for their ability to trap particles as small as 0.3 microns, including dust, pollen, and pet dander. Their primary advantage lies in their low initial cost and ease of installation, making them a popular choice for both residential and commercial settings. However, HEPA filters do not actively eliminate pollutants; instead, they merely trap them, which means that without regular maintenance and replacement, they can become less effective over time. This approach may not address airborne pathogens or odors, making it less suitable for environments that require stringent air quality standards.
How Do UV-C Air Purifiers Work and What Are Their Benefits?
UV-C air purifiers utilize ultraviolet light to destroy bacteria, viruses, and mold spores, making them a potent option for environments with high pathogen levels, such as hospitals or labs. They are relatively low-maintenance, requiring minimal upkeep beyond replacing the UV bulbs every couple of years. However, the effectiveness of UV-C purifiers can be limited by factors such as air flow and exposure time, meaning they are often best used in conjunction with other filtration systems. Furthermore, the initial installation may require electrical work, which could pose challenges for some businesses.
Conclusion: How Can B2B Buyers Choose the Right Air Quality Solution?
When selecting an air purification system, B2B buyers should consider their specific needs, including the size of the facility, the types of contaminants present, and the importance of ongoing maintenance. Air scrubbers offer a proactive solution that actively eliminates pollutants and pathogens, making them ideal for large commercial spaces that require consistent air quality control. Conversely, HEPA filters and UV-C purifiers can serve as effective alternatives, particularly in smaller settings or specialized environments. By evaluating the performance, cost, and ease of implementation of each option, buyers can make a well-informed choice that aligns with their operational goals and budget constraints.
Essential Technical Properties and Trade Terminology for air scrubber
What are the Essential Technical Properties of Air Scrubbers?
When considering air scrubbers for B2B applications, understanding their critical technical specifications is vital. Here are key properties that buyers should evaluate:
1. Filtration Efficiency (HEPA Rating)
The High-Efficiency Particulate Air (HEPA) filter is crucial in determining how effectively an air scrubber can capture airborne particles. A HEPA filter must trap at least 99.97% of particles that are 0.3 microns in size. This specification is important for industries that require stringent air quality standards, such as healthcare and food processing. High filtration efficiency leads to better indoor air quality, reducing health risks and improving employee productivity.
2. Airflow Rate (CFM)
The airflow rate, measured in cubic feet per minute (CFM), indicates how much air the scrubber can process in a given time. A higher CFM rating is essential for larger spaces or environments with high contamination levels. For B2B buyers, understanding the airflow requirements based on the size of their facilities ensures that the air scrubber can adequately meet air quality needs without straining the HVAC system.
3. Noise Level (Decibels)
Noise level is often overlooked but is critical in selecting an air scrubber, especially for office environments. Noise is measured in decibels (dB), and lower dB ratings are preferable to avoid disruption. Buyers should consider the operational noise levels in relation to their work environment to maintain productivity and comfort.
4. Energy Efficiency (Wattage)
Energy consumption is a key consideration for B2B buyers, particularly in regions where electricity costs are high. Air scrubbers with lower wattage ratings can help reduce operating costs. Look for units with energy-efficient certifications, as these can also contribute to sustainability goals, which are increasingly important in today’s business environment.
5. Durability and Material Grade
The materials used in constructing air scrubbers affect their lifespan and maintenance needs. Common materials include galvanized steel or high-grade plastics that resist corrosion and wear. Buyers should assess the durability based on their specific operational conditions, especially in industries prone to harsh environments, such as manufacturing or chemical processing.
What are the Key Trade Terms Associated with Air Scrubbers?
Familiarity with industry terminology is essential for effective communication and negotiation. Here are some common trade terms relevant to air scrubbers:
1. OEM (Original Equipment Manufacturer)
An OEM refers to a company that produces parts or equipment that may be marketed by another manufacturer. Understanding OEM relationships can help buyers identify reliable suppliers and ensure they receive quality components that meet their specifications.
2. MOQ (Minimum Order Quantity)
MOQ is the smallest quantity of a product that a supplier is willing to sell. This term is crucial for B2B buyers to understand their purchasing limits and negotiate better pricing. Knowing the MOQ helps in budgeting and managing inventory effectively.
3. RFQ (Request for Quotation)
An RFQ is a document used to solicit price quotes from suppliers for specific products or services. It is a formal way to initiate the procurement process and allows buyers to compare prices and terms from different vendors, ensuring they secure the best deal.
4. Incoterms (International Commercial Terms)
Incoterms are a set of predefined commercial terms published by the International Chamber of Commerce (ICC) that define the responsibilities of sellers and buyers in international transactions. Familiarity with Incoterms helps buyers understand shipping responsibilities, insurance, and risk management, which is particularly important for international B2B transactions.
5. Lead Time
Lead time refers to the amount of time it takes from placing an order to receiving the product. Understanding lead times is essential for planning and managing supply chain operations. Buyers should consider lead times when scheduling installations or maintenance to avoid operational disruptions.
By grasping these technical properties and trade terminologies, international B2B buyers can make informed purchasing decisions regarding air scrubbers, ensuring they meet their specific air quality needs while navigating the complexities of global trade.
Navigating Market Dynamics and Sourcing Trends in the air scrubber Sector
What Are the Key Market Dynamics Influencing the Air Scrubber Sector?
The air scrubber market is currently experiencing robust growth driven by increasing awareness of indoor air quality (IAQ) and its impact on health, particularly in commercial and industrial sectors. As global regulatory frameworks tighten regarding environmental standards and health safety, B2B buyers are compelled to seek effective solutions to mitigate airborne pollutants. Markets in Africa, South America, the Middle East, and Europe (notably Germany and France) are witnessing heightened demand for advanced air purification technologies, propelled by urbanization and a growing middle class.
Emerging technologies such as ActivePure® and advanced photohydrolysis are revolutionizing air purification, enabling air scrubbers to actively neutralize pathogens and allergens rather than merely filtering them. Additionally, the COVID-19 pandemic has shifted the focus toward solutions that can effectively eliminate viruses, thereby increasing the attractiveness of air scrubbers in sectors like healthcare, hospitality, and education. International B2B buyers must stay informed about these technological advancements and consider sourcing from manufacturers that offer comprehensive and validated solutions to meet their specific needs.
How Can Sustainability and Ethical Sourcing Impact the Air Scrubber Industry?
Sustainability is becoming a cornerstone of procurement strategies for international B2B buyers, particularly in regions emphasizing environmental responsibility. The air scrubber sector is no exception; companies are increasingly expected to demonstrate their commitment to reducing environmental impact. This includes sourcing materials that are recyclable or biodegradable, as well as adopting manufacturing processes that minimize waste and energy consumption.
Buyers should prioritize suppliers that have obtained ‘green’ certifications, such as Energy Star or LEED, which indicate compliance with stringent environmental standards. Additionally, ethical supply chains that ensure fair labor practices and responsible sourcing can enhance a company’s reputation and marketability. By opting for sustainable products, businesses can not only contribute to a healthier planet but also position themselves competitively in a marketplace that increasingly values corporate social responsibility.
How Has the Air Scrubber Market Evolved Over Time?
The evolution of air scrubber technology can be traced back to its roots in the 1990s when NASA collaborated with researchers to develop air purification solutions for space environments. Since then, advancements in material science and engineering have led to the creation of more effective air scrubbers that utilize advanced filtration methods and active purification technologies. Initially limited to residential applications, the use of air scrubbers has expanded significantly into commercial, industrial, and institutional markets.
Today, air scrubbers are equipped with sophisticated features such as real-time air quality monitoring and multi-stage filtration systems, making them essential tools for improving indoor air quality. As the market continues to evolve, international B2B buyers must remain adaptable and informed about these trends to leverage the best solutions for their air quality challenges.
Frequently Asked Questions (FAQs) for B2B Buyers of air scrubber
-
How do I solve indoor air quality problems in commercial spaces?
To address indoor air quality issues in commercial environments, consider installing air scrubbers that actively purify air and eliminate pollutants. Unlike traditional filters, air scrubbers use advanced technologies to neutralize allergens, mold spores, and viruses. Evaluate your space’s specific needs, such as size and contamination levels, to select the right model. Additionally, regular maintenance and monitoring of air quality can further enhance the effectiveness of these systems. -
What is the best air scrubber for large facilities?
For large facilities, look for air scrubbers with high airflow capacity and multi-stage filtration systems. Models that cover areas of over 1,500 square feet and utilize HEPA filters are ideal, as they effectively capture a wide range of contaminants. Brands like XPOWER and ActivePure offer robust options tailored for commercial applications. Always assess the specific contaminants present in your facility to choose a model that best meets your needs. -
What are the key factors to consider when sourcing air scrubbers internationally?
When sourcing air scrubbers from international suppliers, focus on product quality, compliance with local regulations, and supplier reliability. Investigate certifications such as ISO and CE to ensure adherence to safety standards. Additionally, consider the supplier’s experience with international shipping and their ability to provide after-sales support. Engaging in thorough due diligence, including checking references and previous customer reviews, can safeguard your investment. -
How can I customize air scrubbers to meet specific operational needs?
Many manufacturers offer customization options for air scrubbers, allowing you to tailor features like filtration types, airflow rates, and sizes based on your operational requirements. Discuss your specific needs with potential suppliers to explore available options. Additionally, inquire about the possibility of integrating smart technology for real-time monitoring and control, which can enhance the efficiency of your air purification system. -
What is the minimum order quantity (MOQ) for air scrubbers?
Minimum order quantities for air scrubbers can vary widely based on the manufacturer and the complexity of the product. Typically, MOQs can range from 10 to 50 units for commercial-grade models. It’s important to communicate your purchasing needs with suppliers upfront to negotiate favorable terms. Consider placing a pilot order to evaluate product performance before committing to larger quantities. -
What payment terms should I expect when buying air scrubbers internationally?
Payment terms for international purchases of air scrubbers can vary significantly. Common options include upfront payment, 30-60 days net terms, or a combination of deposit and balance upon delivery. Ensure to clarify payment methods accepted, such as bank transfers or letters of credit, to facilitate smooth transactions. Additionally, consider discussing potential discounts for early payments or bulk orders to optimize your procurement costs.
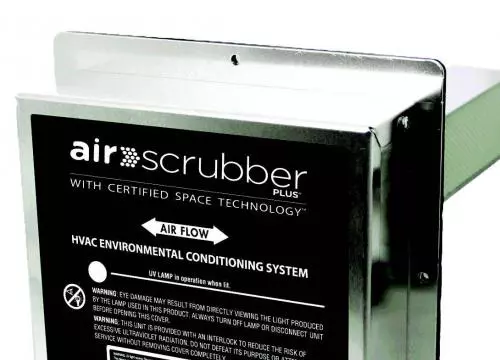
A stock image related to air scrubber.
-
How can I ensure quality assurance when purchasing air scrubbers?
To ensure quality assurance, request detailed product specifications, certifications, and test results from suppliers. Many reputable manufacturers provide third-party lab results that validate their products’ effectiveness against common contaminants. Establish a clear quality inspection process upon receiving products, including functionality tests and adherence to specifications. Consider forming partnerships with suppliers who offer warranties or guarantees for added peace of mind. -
What logistics considerations should I keep in mind when importing air scrubbers?
When importing air scrubbers, logistics considerations include shipping methods, customs regulations, and delivery timelines. Opt for reliable freight forwarders who are familiar with the import/export process in your region. Ensure all necessary documentation, such as invoices and certificates of origin, are prepared to facilitate smooth customs clearance. Additionally, account for potential duties and taxes in your budget to avoid unexpected costs upon arrival.
Important Disclaimer & Terms of Use
⚠️ Important Disclaimer
The information provided in this guide, including content regarding manufacturers, technical specifications, and market analysis, is for informational and educational purposes only. It does not constitute professional procurement advice, financial advice, or legal advice.
While we have made every effort to ensure the accuracy and timeliness of the information, we are not responsible for any errors, omissions, or outdated information. Market conditions, company details, and technical standards are subject to change.
B2B buyers must conduct their own independent and thorough due diligence before making any purchasing decisions. This includes contacting suppliers directly, verifying certifications, requesting samples, and seeking professional consultation. The risk of relying on any information in this guide is borne solely by the reader.
Strategic Sourcing Conclusion and Outlook for air scrubber
In the evolving landscape of indoor air quality management, air scrubbers present a compelling solution for businesses across various sectors. By strategically sourcing advanced air purification systems, B2B buyers can significantly enhance the health and safety of their facilities. This technology not only addresses the pressing issues of airborne contaminants, allergens, and odors but also showcases the ability to mitigate risks associated with airborne pathogens, including viruses like COVID-19.
What Are the Key Benefits of Strategic Sourcing for Air Scrubbers?
Investing in air scrubbers through strategic sourcing ensures that companies can access cutting-edge technologies that offer superior air quality control. Buyers from Africa, South America, the Middle East, and Europe should prioritize partnerships with reputable manufacturers that provide comprehensive support and customization options. This approach allows for tailored solutions that meet specific regional regulations and health standards.
How Can International Buyers Leverage Air Scrubber Technology?
As organizations increasingly recognize the importance of indoor air quality, the demand for air scrubbers is expected to grow. International B2B buyers are encouraged to explore partnerships with suppliers that offer robust warranties and maintenance programs, ensuring long-term value and performance. By taking proactive steps now, companies can position themselves as leaders in workplace health and safety.
In conclusion, the strategic sourcing of air scrubbers is not merely a trend but a necessary evolution in operational standards. Embrace this opportunity to improve indoor environments and protect the wellbeing of your workforce, and take action today to secure a healthier future for your business.