Enhance Efficiency: The Ultimate Guide to Belt Conveyor Systems (2025)
Introduction: Navigating the Global Market for belt conveyor systems
In today’s fast-paced global market, sourcing efficient belt conveyor systems is essential for businesses aiming to enhance their operational productivity. With the increasing complexity of supply chains, international B2B buyers face the challenge of selecting the right conveyor solutions that not only meet their material handling needs but also fit within budgetary constraints. This comprehensive guide addresses these challenges head-on, providing detailed insights into various types of belt conveyor systems, their applications across different industries, and the critical factors to consider when vetting suppliers.
Throughout this guide, we will explore the diverse range of belt conveyor options available, including slider bed, roller bed, and incline systems, among others. Buyers will gain clarity on the unique benefits and limitations of each type, enabling them to make informed decisions tailored to their specific operational requirements. Additionally, we delve into the cost structures associated with these systems and the importance of considering factors such as customization, delivery timelines, and service support.
This resource is particularly valuable for B2B buyers from Africa, South America, the Middle East, and Europe, including key markets like Spain and Germany. By providing actionable insights and practical strategies, this guide empowers international buyers to navigate the complexities of sourcing belt conveyor systems effectively, ultimately driving efficiency and growth in their operations.
Understanding belt conveyor systems Types and Variations
Type Name | Key Distinguishing Features | Primary B2B Applications | Brief Pros & Cons for Buyers |
---|---|---|---|
Slider Bed Belt Conveyor | Flat surface, continuous belt, simple construction | Manufacturing, packaging, distribution | Pros: Economical, easy to install. Cons: Limited to transport applications, cannot accumulate products. |
Roller Bed Belt Conveyor | Utilizes rollers beneath the belt for reduced friction | Heavy item handling, warehousing | Pros: Better for heavy loads, allows accumulation. Cons: More complex installation and maintenance. |
Incline Belt Conveyor | Designed for transporting materials at an angle | Bulk material handling, recycling | Pros: Efficient for vertical transport. Cons: Requires careful load management to prevent slippage. |
Troughed Belt Conveyor | Sides raised to form a trough for bulk materials | Mining, agriculture, bulk material handling | Pros: Ideal for loose materials, prevents spillage. Cons: Higher initial cost and space requirements. |
Cleanroom Belt Conveyor | Designed for sterile environments, compliant with ISO standards | Pharmaceuticals, electronics manufacturing | Pros: Ensures cleanliness, protects sensitive products. Cons: Higher cost and maintenance requirements. |
What are the Characteristics of Slider Bed Belt Conveyors?
Slider bed belt conveyors feature a flat surface and a continuous loop belt that runs over a solid bed. This design makes them an economical choice for transporting lightweight to moderately heavy items in manufacturing and distribution settings. When considering a slider bed conveyor, buyers should evaluate the specific material types being handled and the need for incline or decline functionality, as this model is best suited for horizontal transport.
How Do Roller Bed Belt Conveyors Enhance Material Handling?
Roller bed belt conveyors incorporate rollers beneath the belt, reducing friction and allowing for heavier loads to be transported more efficiently. This type is particularly advantageous in warehousing and heavy item handling applications, where accumulation of products is necessary. Buyers should consider the complexity of installation and maintenance, as well as the potential need for additional supports for heavier loads.
Why Choose Incline Belt Conveyors for Vertical Transport?
Incline belt conveyors are engineered to move products between different elevations, making them ideal for bulk material handling or recycling operations. Their design allows for efficient vertical transport, but buyers must ensure that products are secure to prevent slippage during transit. It’s important to assess the angle of incline and the weight of materials being transported to avoid operational issues.
What Advantages Do Troughed Belt Conveyors Offer for Bulk Materials?
Troughed belt conveyors are characterized by their raised sides, forming a trough that effectively contains bulk materials such as grains or aggregates. This design minimizes the risk of spillage and is commonly used in mining and agricultural applications. Buyers should be aware of the higher initial investment and space requirements, as well as the need for regular maintenance to ensure optimal performance.
How Do Cleanroom Belt Conveyors Meet Industry Standards?
Cleanroom belt conveyors are specifically designed for environments that require strict cleanliness standards, such as pharmaceuticals and electronics manufacturing. These conveyors are built to comply with ISO standards, ensuring that sensitive products are protected from contamination. While they offer significant benefits for maintaining product integrity, buyers should consider the higher costs and ongoing maintenance required to uphold cleanliness standards.
Key Industrial Applications of belt conveyor systems
Industry/Sector | Specific Application of Belt Conveyor Systems | Value/Benefit for the Business | Key Sourcing Considerations for this Application |
---|---|---|---|
Manufacturing | Assembly Line Automation | Increases throughput and minimizes manual labor costs. | Assess load capacity and belt material compatibility. |
Food Processing | Bulk Ingredient Handling | Ensures hygienic transport of food products. | Look for FDA-compliant materials and easy cleanability. |
Packaging | Automated Sorting and Packaging | Enhances speed and accuracy in packaging operations. | Consider modular designs for flexibility in layout changes. |
Mining | Material Transport for Bulk Materials | Reduces manual handling and increases efficiency. | Evaluate durability and resistance to harsh environments. |
Warehousing | Order Fulfillment and Distribution | Streamlines operations and improves order accuracy. | Check for integration with existing warehouse management systems. |
How is Belt Conveyor Systems Used in Manufacturing?
In the manufacturing sector, belt conveyor systems are integral to assembly line automation. These systems facilitate the continuous movement of products and components, which significantly increases throughput while reducing the need for manual labor. For international buyers, especially in regions like Europe and Africa, it’s crucial to evaluate the load capacity and material compatibility of the conveyor systems to ensure they meet specific production requirements. Additionally, understanding local regulations regarding workplace safety and equipment standards is essential.
What Role Do Belt Conveyor Systems Play in Food Processing?
In food processing, belt conveyor systems are commonly used for bulk ingredient handling. They ensure the hygienic transport of various food products, from raw materials to packaged goods. For B2B buyers in South America and the Middle East, it’s vital to source conveyors made from FDA-compliant materials that allow for easy cleaning and maintenance. This not only ensures compliance with health regulations but also minimizes the risk of contamination in food production processes.
How are Belt Conveyor Systems Applied in Packaging?
Packaging industries leverage belt conveyor systems for automated sorting and packaging processes. These conveyors enhance speed and accuracy, reducing labor costs and improving overall efficiency. For buyers in Europe, particularly in countries like Germany and Spain, considering modular designs is beneficial as they allow for quick reconfiguration in response to changing packaging needs. Buyers should also focus on the adaptability of the conveyor to various product sizes and weights to optimize their operations.
How Do Belt Conveyor Systems Benefit the Mining Sector?
In mining, belt conveyor systems are essential for the transport of bulk materials such as coal, minerals, and aggregates. They significantly reduce manual handling, which can be labor-intensive and hazardous, while also increasing operational efficiency. International buyers from regions like Africa, where mining is a critical industry, should evaluate the durability and resistance of conveyor systems to harsh environments, including extreme temperatures and abrasive materials, to ensure long-term performance.
What Advantages Do Belt Conveyor Systems Offer in Warehousing?
In warehousing, belt conveyor systems are utilized for order fulfillment and distribution tasks. They streamline operations by facilitating the efficient movement of goods from storage to shipping areas, thus improving order accuracy and reducing processing times. B2B buyers, particularly in South America, should consider sourcing conveyors that can integrate seamlessly with existing warehouse management systems. This integration can enhance inventory tracking and optimize overall supply chain management.
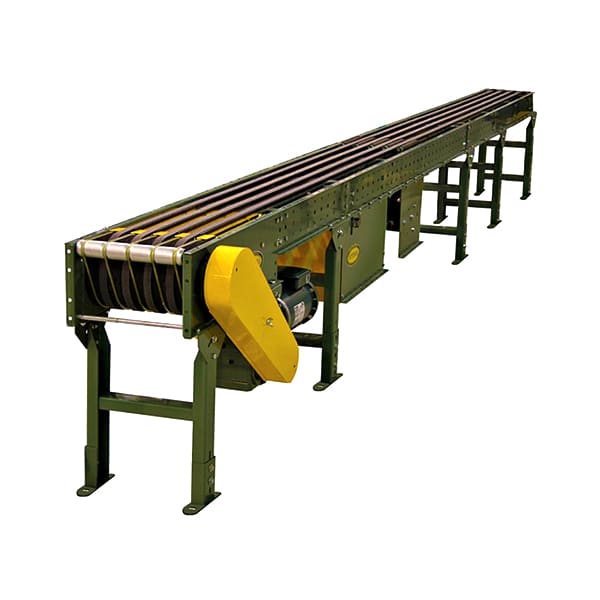
A stock image related to belt conveyor systems.
3 Common User Pain Points for ‘belt conveyor systems’ & Their Solutions
Scenario 1: Inefficient Material Handling Processes
The Problem: Many B2B buyers in industries such as manufacturing and logistics face challenges with inefficient material handling processes. For instance, a company in South America might be relying on manual labor to transport goods, leading to increased labor costs, slower production times, and a higher risk of product damage. This inefficiency not only affects their bottom line but also hampers their ability to meet customer demands in a timely manner.
The Solution: Investing in a belt conveyor system can significantly streamline material handling processes. To address this pain point, buyers should first evaluate their specific needs, including the types of products being transported and the layout of their facilities. Choosing a modular conveyor system, such as the TB30 from Montech, allows for easy customization and scalability. Buyers should work closely with suppliers to select the right configurations that optimize workflow, ensuring the conveyor can handle various product sizes and weights. Additionally, integrating sensors and automation technology can enhance operational efficiency, allowing the conveyor to adjust to different speeds and load requirements.
Scenario 2: Limited Space and Layout Constraints
The Problem: In densely packed facilities, such as warehouses in Europe, space constraints can pose a significant challenge when implementing new systems. B2B buyers often struggle with how to fit new equipment like belt conveyors into existing layouts without disrupting operations. This can lead to costly redesigns or the need to relocate entire sections of a facility.
The Solution: To overcome space limitations, buyers should consider modular and compact belt conveyor systems that can be tailored to fit specific areas of their facility. For example, the TB40 conveyor from Montech features a compact design with a 24 V brushless DC motor, making it suitable for tight spaces while still handling substantial loads. Buyers should conduct a thorough assessment of their layout and engage with suppliers to develop a customized plan that maximizes efficiency without sacrificing space. Utilizing tools such as CAD software for planning can help visualize how the conveyor will fit into the existing workflow, ensuring a smooth integration process.
Scenario 3: High Maintenance Costs and Downtime
The Problem: Frequent breakdowns and maintenance issues with existing conveyor systems can lead to significant downtime and increased operational costs. This is particularly problematic for industries that rely on continuous production, such as those in the Middle East and Africa. B2B buyers often find that older conveyor systems require more frequent repairs, resulting in unexpected expenses and disruptions in service.
The Solution: To mitigate maintenance costs, buyers should invest in modern, high-quality belt conveyor systems designed for durability and ease of maintenance. Selecting conveyors with robust materials and construction, such as heavy-duty belts made for challenging environments, can reduce the frequency of repairs. Additionally, establishing a routine maintenance schedule can preemptively address potential issues before they escalate. Buyers should also seek suppliers who offer comprehensive support and warranties, ensuring that any problems that do arise can be resolved quickly and efficiently. By focusing on quality and support, buyers can significantly reduce maintenance-related downtime, leading to improved productivity and cost-effectiveness in their operations.
Strategic Material Selection Guide for belt conveyor systems
What Are the Key Materials for Belt Conveyor Systems?
When selecting materials for belt conveyor systems, it is essential to consider various factors that influence performance, durability, and suitability for specific applications. Below, we analyze four common materials used in belt conveyors, focusing on their properties, advantages, disadvantages, and specific considerations for international B2B buyers.
How Does Rubber Perform in Belt Conveyor Systems?
Key Properties: Rubber belts are known for their excellent flexibility and grip. They can withstand a range of temperatures, typically from -30°C to 80°C, and exhibit good resistance to wear and abrasion.
Pros & Cons: Rubber is durable and provides a high coefficient of friction, making it ideal for transporting heavy or slippery items. However, it can be more expensive than other materials and may degrade when exposed to certain chemicals or extreme temperatures.
Impact on Application: Rubber belts are particularly effective in environments where high friction is necessary, such as in construction or mining applications. However, they may not be suitable for applications involving corrosive materials.
Considerations for International Buyers: Buyers from regions like Europe and the Middle East should ensure compliance with local standards such as DIN or ASTM for rubber materials. Additionally, understanding the specific chemical exposure in their applications is crucial for selecting the right rubber type.
What Advantages Do PVC Belts Offer?
Key Properties: Polyvinyl Chloride (PVC) belts are lightweight, flexible, and resistant to moisture. They typically operate effectively in temperatures ranging from -10°C to 60°C.
Pros & Cons: PVC belts are cost-effective and easy to clean, making them suitable for food processing and packaging industries. However, they may lack the durability of rubber belts in heavy-duty applications and can be prone to tearing under excessive load.
Impact on Application: PVC is often used in applications involving light to moderate weight products, such as in food and beverage industries. Their smooth surface is beneficial for transporting delicate items.
Considerations for International Buyers: Buyers should verify compliance with food safety standards, especially in Europe, where regulations like EU 1935/2004 apply. Understanding the local market preferences for belt materials can also aid in selection.
Why Choose Polyurethane for Belt Conveyors?
Key Properties: Polyurethane belts are known for their high abrasion resistance and can handle temperatures up to 100°C. They also offer excellent chemical resistance.
Pros & Cons: The durability of polyurethane makes it suitable for heavy-duty applications, and it can handle a wide variety of products. However, it tends to be more expensive than rubber or PVC and may require specialized manufacturing processes.
Impact on Application: Polyurethane belts are ideal for industries dealing with sharp or abrasive materials, such as recycling or metal processing. They can also handle high temperatures, making them suitable for hot material transport.
Considerations for International Buyers: Buyers should consider the specific chemical and temperature requirements of their applications. Compliance with international standards such as ISO can also be a deciding factor.
What Role Does Fabric Play in Conveyor Belt Systems?
Key Properties: Fabric belts, often made from polyester or nylon, are lightweight and flexible. They can handle a variety of temperatures but generally have lower heat resistance compared to rubber or polyurethane.
Pros & Cons: Fabric belts are cost-effective and suitable for light to medium loads. However, they may wear out faster than other materials and can be less effective in high-friction applications.
Impact on Application: These belts are commonly used in packaging and light manufacturing applications where flexibility and cost are more critical than durability.
Considerations for International Buyers: Buyers should assess the load requirements and environmental conditions of their operations. Understanding local manufacturing capabilities can also influence the choice of fabric belts.
Summary Table of Material Selection for Belt Conveyor Systems
Material | Typical Use Case for belt conveyor systems | Key Advantage | Key Disadvantage/Limitation | Relative Cost (Low/Med/High) |
---|---|---|---|---|
Rubber | Heavy-duty applications in construction | High durability and grip | Expensive, sensitive to chemicals | High |
PVC | Food processing and packaging | Cost-effective and easy to clean | Less durable under heavy loads | Medium |
Polyurethane | Recycling and metal processing | Excellent abrasion and chemical resistance | Higher cost and specialized manufacturing | High |
Fabric | Light manufacturing and packaging | Cost-effective and flexible | Wears out faster, lower heat resistance | Low |
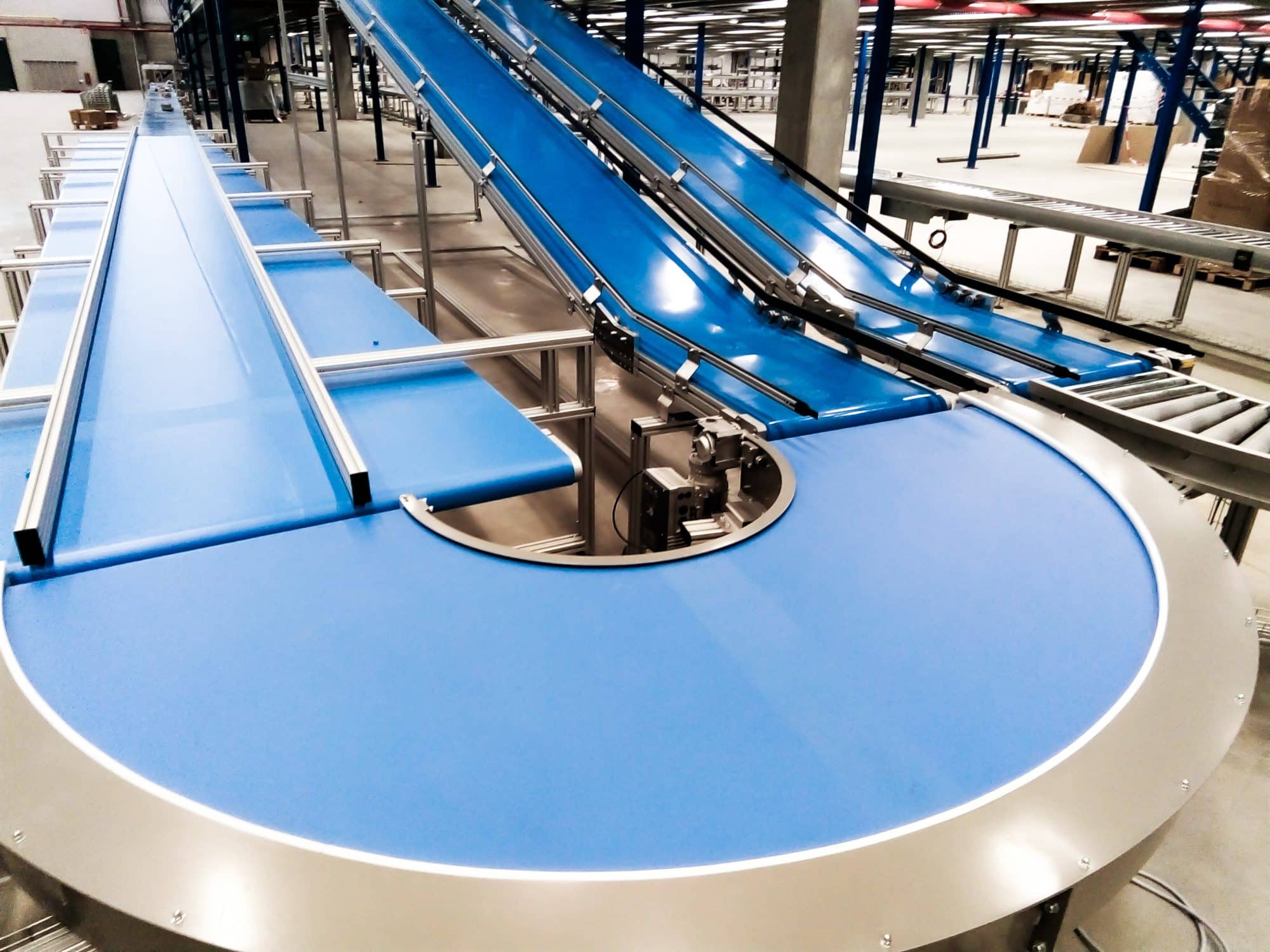
A stock image related to belt conveyor systems.
This strategic material selection guide aims to provide international B2B buyers with actionable insights to make informed decisions when sourcing belt conveyor systems. Understanding the properties and applications of each material will help in selecting the most suitable option for specific operational needs.
In-depth Look: Manufacturing Processes and Quality Assurance for belt conveyor systems
What Are the Main Stages in Manufacturing Belt Conveyor Systems?
The manufacturing of belt conveyor systems involves several key stages that ensure the final product is both functional and reliable. Understanding these stages is crucial for international B2B buyers, especially when evaluating suppliers.
1. Material Preparation
The first step in the manufacturing process is the selection and preparation of materials. Common materials used for belt conveyors include various types of rubber, fabric, and metal components. The choice of materials depends on the specific application requirements, such as load capacity, environmental conditions, and the type of products being transported.
B2B buyers should look for suppliers who source high-quality materials that meet international standards. This can often be verified through material certification documents, which ensure that materials are suitable for the intended use.
2. Forming Processes: How Are Components Shaped?
Once materials are prepared, the next stage is forming the components. This typically involves several techniques:
- Cutting: Materials are cut to size using precision cutting tools. CNC (Computer Numerical Control) machines are often employed to ensure accuracy.
- Molding: For rubber belts, molding processes are used to create the desired shapes. This includes processes like compression molding or injection molding, which are critical for producing belts with specific properties.
- Welding and Joining: Metal components are often welded or joined using mechanical fasteners. This ensures that the frame of the conveyor system is sturdy and can support the load.
Buyers should inquire about the specific forming techniques used by suppliers, as these can impact the durability and performance of the conveyor systems.
3. Assembly: What Are the Key Steps?
After forming, components are assembled into the final conveyor system. This stage typically includes:
- Frame Assembly: The frame is constructed to support the belt and other components. It is essential that this structure is robust to handle operational stresses.
- Belt Installation: The belt is installed and adjusted to ensure proper tension and alignment. This is crucial for the smooth operation of the conveyor.
- Integration of Additional Features: Depending on the application, features such as sensors, motors, and control systems may be integrated during this stage.
B2B buyers should assess the assembly processes of potential suppliers, as well-assembled systems tend to have longer lifespans and require less maintenance.
4. Finishing: How Is Quality Enhanced?
The finishing stage involves applying protective coatings, painting, or other treatments to enhance durability and aesthetics. This may include:
- Surface Treatments: Coatings may be applied to resist corrosion or wear, depending on the environment where the conveyor will operate.
- Final Inspection: Before leaving the manufacturing facility, each conveyor system undergoes a final inspection to ensure it meets design specifications and quality standards.
Buyers should request information about finishing processes and any guarantees related to durability and performance.
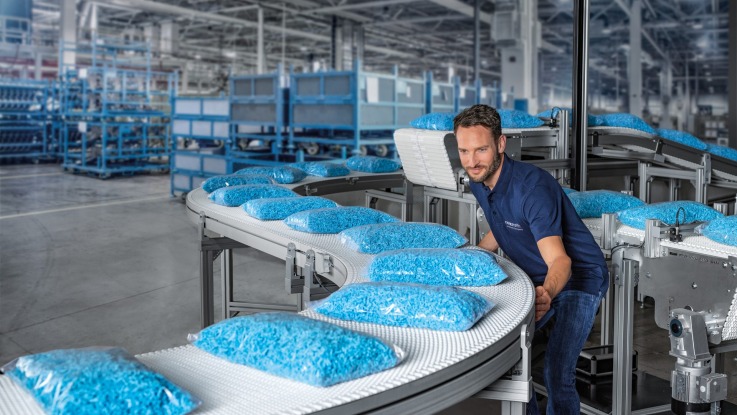
A stock image related to belt conveyor systems.
What Quality Assurance Measures Are Essential for Belt Conveyor Systems?
Quality assurance is crucial in ensuring that belt conveyor systems operate effectively and safely. International B2B buyers should be familiar with the following quality assurance measures.
Relevant International Standards: What Should Buyers Know?
Manufacturers of belt conveyor systems often adhere to international standards such as:
- ISO 9001: This standard outlines the requirements for a quality management system (QMS). Compliance with ISO 9001 indicates that a manufacturer has effective processes in place for managing quality.
- CE Marking: Required for products sold in the European Economic Area (EEA), CE marking signifies that a product meets EU safety, health, and environmental protection requirements.
- API Standards: For conveyors used in specific industries like oil and gas, adherence to API (American Petroleum Institute) standards is essential.
Buyers should verify that their suppliers are compliant with relevant standards, as this ensures a level of quality and safety.
What Are the Quality Control Checkpoints?
Quality control (QC) is integrated into various stages of the manufacturing process. The common QC checkpoints include:
- Incoming Quality Control (IQC): This involves inspecting materials upon arrival to ensure they meet specified standards.
- In-Process Quality Control (IPQC): Regular checks during the manufacturing process help catch any defects early.
- Final Quality Control (FQC): Before shipment, each conveyor system undergoes a final inspection to confirm it meets all specifications.
B2B buyers should inquire about the QC measures implemented by potential suppliers and request documentation of past inspections.
Common Testing Methods: How Are Products Evaluated?
Testing methods are crucial for verifying the performance and safety of belt conveyor systems. Common methods include:
- Load Testing: Ensures that the conveyor can handle the specified weight without failure.
- Operational Testing: Verifies that all components, including motors and sensors, function correctly.
- Environmental Testing: Assesses how well the conveyor performs under various environmental conditions (e.g., temperature, humidity).
Buyers should ask suppliers for testing certifications and results, as these documents provide assurance of quality and reliability.
How Can B2B Buyers Verify Supplier Quality Control?
When sourcing belt conveyor systems, B2B buyers from Africa, South America, the Middle East, and Europe should consider several strategies to verify supplier quality control.
What Audit Processes Are Available?
Conducting audits of potential suppliers can provide insights into their manufacturing and quality assurance processes. Buyers can perform:
- On-Site Audits: Visiting the manufacturing facility allows buyers to observe processes firsthand and assess the quality of materials and workmanship.
- Supplier Audits: These can be conducted by third-party companies specializing in supplier evaluation, which adds an extra layer of credibility.
How Can Buyers Access Quality Reports and Certifications?
Buyers should request quality assurance reports and certifications from suppliers. Key documents to consider include:
- Quality Management System Certification: Proof of compliance with ISO 9001 or other relevant standards.
- Material Certifications: Documentation verifying the quality and safety of materials used in production.
What Are the Nuances of QC/Certifications for International Buyers?
International buyers should be aware of specific nuances in quality control and certification processes:
- Regulatory Compliance: Different regions may have unique regulatory requirements that must be met for products to be imported or used.
- Cultural Considerations: Understanding the business practices and expectations in different regions can enhance communication and negotiations with suppliers.
By being informed about these aspects of manufacturing processes and quality assurance, international B2B buyers can make educated decisions when sourcing belt conveyor systems, ensuring they receive products that meet their operational needs and quality expectations.
Practical Sourcing Guide: A Step-by-Step Checklist for ‘belt conveyor systems’
This guide aims to provide international B2B buyers with a structured approach to sourcing belt conveyor systems effectively. By following this checklist, you can ensure that your procurement process is efficient, cost-effective, and tailored to your specific operational needs.
Step 1: Define Your Technical Specifications
Before engaging with suppliers, it’s essential to clarify your technical requirements. Identify the dimensions, load capacity, and type of materials you plan to transport. Consider factors such as:
– Belt Width and Length: Ensure the conveyor will fit your workspace and transport your products efficiently.
– Material Type: Select the appropriate belt material (e.g., rubber, fabric) based on the nature of your products and their handling conditions.
Step 2: Assess Your Operational Needs
Understanding your operational workflow is crucial for selecting the right conveyor system. Evaluate how the conveyor will integrate into your existing processes, focusing on:
– Product Flow: Determine if you need continuous or indexed movement.
– Incline Requirements: Assess if the conveyor needs to transport materials at an incline and what angle is appropriate for your products.
Step 3: Evaluate Potential Suppliers
Conducting thorough research on potential suppliers is vital. Look for companies with a proven track record in your industry. Key considerations include:
– Company Reputation: Seek reviews, case studies, and testimonials from other buyers.
– Certifications: Verify if the supplier holds relevant industry certifications, ensuring compliance with safety and quality standards.
Step 4: Request Customized Proposals
Once you’ve shortlisted potential suppliers, request detailed proposals tailored to your specifications. A good proposal should include:
– Technical Drawings: Visual representations of the proposed system to ensure it meets your needs.
– Cost Breakdown: A comprehensive breakdown of costs, including installation and maintenance.
Step 5: Analyze Delivery and Installation Options
Delivery timelines and installation support can significantly affect your operations. Confirm:
– Lead Times: Understand how long it will take for the conveyor system to be delivered.
– Installation Services: Check if the supplier offers installation services and training for your team.
Step 6: Consider After-Sales Support and Maintenance
After-sales support is crucial for the long-term success of your conveyor system. Inquire about:
– Warranty Terms: Ensure that the warranty covers parts and labor for a reasonable period.
– Maintenance Services: Look for suppliers that offer ongoing maintenance and readily available spare parts.
Step 7: Negotiate Terms and Finalize the Agreement
Once you have selected a supplier, it’s time to negotiate terms. Discuss:
– Payment Terms: Ensure the payment structure aligns with your budget.
– Contractual Obligations: Clearly outline delivery schedules, warranty conditions, and liability clauses in the contract to prevent any future disputes.
By following these steps, you can streamline your sourcing process for belt conveyor systems, ensuring you select a solution that enhances efficiency and productivity in your operations.
Comprehensive Cost and Pricing Analysis for belt conveyor systems Sourcing
What Are the Key Cost Components for Belt Conveyor Systems?
When sourcing belt conveyor systems, understanding the cost structure is crucial for international B2B buyers. The primary cost components include:
-
Materials: The choice of materials directly impacts the cost. Common materials for belts include fabric, rubber, and specialized composites for heavy-duty applications. The selection should align with the operational demands, such as load capacity and environmental conditions.
-
Labor: Labor costs involve both direct manufacturing labor and skilled technicians for installation. Depending on the complexity of the system, labor costs can vary significantly.
-
Manufacturing Overhead: This encompasses utilities, facility costs, and depreciation of machinery used in production. Overhead costs can fluctuate based on geographical location and production scale.
-
Tooling: Custom tooling may be required for specialized conveyor designs. This is often a fixed cost but can be amortized over larger orders, making it more economical per unit when volume is increased.
-
Quality Control (QC): Investing in QC processes ensures that the conveyor systems meet safety and performance standards. This can add to the upfront cost but may reduce long-term maintenance expenses.
-
Logistics: Shipping costs, including freight and insurance, vary widely based on the supplier’s location and the buyer’s destination. Factors like customs duties and tariffs should also be considered.
-
Margin: Suppliers typically add a profit margin to their costs. This can be influenced by market competition, brand reputation, and the perceived value of the product.
How Do Price Influencers Affect Belt Conveyor Systems?
Several factors can influence the pricing of belt conveyor systems:
-
Volume/MOQ (Minimum Order Quantity): Higher order volumes often lead to better pricing due to economies of scale. Buyers should negotiate for bulk discounts or tiered pricing based on projected needs.
-
Specifications and Customization: Custom configurations and specifications typically incur additional costs. Understanding the specific requirements beforehand can help streamline the design process and minimize unexpected expenses.
-
Materials Quality and Certifications: Premium materials and certifications (e.g., ISO standards) can raise prices. However, they often lead to enhanced durability and performance, which can reduce overall maintenance costs.
-
Supplier Factors: The reputation, reliability, and customer service quality of the supplier can impact pricing. Established suppliers may charge a premium for their experience and reliability.
-
Incoterms: The choice of Incoterms affects the total landed cost. Buyers should clearly understand responsibilities for shipping, insurance, and customs clearance to avoid unexpected costs.
What Are the Best Negotiation Tips for International B2B Buyers?
Negotiating effectively can lead to significant cost savings. Here are some strategies tailored for international B2B buyers, particularly from Africa, South America, the Middle East, and Europe:
-
Understand Total Cost of Ownership (TCO): Evaluate not just the upfront cost but the total cost over the product’s lifecycle, including installation, maintenance, and operational expenses. This approach can justify a higher initial investment for superior quality.
-
Leverage Local Market Knowledge: Buyers in different regions may benefit from local market insights, including common pricing practices and supplier capabilities. This knowledge can be a powerful tool during negotiations.
-
Flexibility in Specifications: Being open to alternative materials or designs can lead to cost reductions. Suppliers may have existing solutions that meet your needs at a lower price point.
-
Build Relationships: Developing long-term relationships with suppliers can lead to better pricing, priority service, and access to new products. Frequent communication and feedback can foster trust and collaboration.
-
Be Aware of Pricing Nuances: Different regions may have varying pricing structures due to economic conditions, import tariffs, and currency fluctuations. Staying informed about these factors can enhance negotiation outcomes.
Disclaimer on Pricing
Prices for belt conveyor systems can vary significantly based on the aforementioned factors. It’s essential for buyers to obtain multiple quotes and perform thorough due diligence to ensure competitive pricing and value for their investment.
Alternatives Analysis: Comparing belt conveyor systems With Other Solutions
Understanding the Need for Alternatives in Material Handling Solutions
In the realm of industrial automation and material handling, selecting the right system is crucial for enhancing efficiency and productivity. While belt conveyor systems are a popular choice due to their versatility and simplicity, it is essential for B2B buyers to evaluate alternative solutions that may better meet their specific operational needs. This analysis will compare belt conveyor systems against roller conveyor systems and automated guided vehicles (AGVs), providing valuable insights for international buyers, particularly in Africa, South America, the Middle East, and Europe.
Comparison Table of Material Handling Solutions
Comparison Aspect | Belt Conveyor Systems | Roller Conveyor Systems | Automated Guided Vehicles (AGVs) |
---|---|---|---|
Performance | High for continuous transport | Excellent for heavy or bulky loads | Flexible routing, real-time adjustments |
Cost | Moderate initial investment | Lower initial cost | Higher upfront costs, but scalable |
Ease of Implementation | Simple installation | Easy setup with minimal training | Complex setup, requires programming |
Maintenance | Low to moderate maintenance | Generally low maintenance | Higher maintenance due to technology |
Best Use Case | Transporting packaged goods | Handling pallets and heavy items | Multi-directional transport in dynamic environments |
Detailed Breakdown of Alternatives
What Are the Pros and Cons of Roller Conveyor Systems?
Roller conveyor systems are a robust alternative to belt conveyors, particularly effective for transporting heavy and bulky items. They excel in environments where the material being moved has a flat, rigid bottom surface. The primary advantage of roller conveyors is their ability to handle substantial loads with minimal effort, making them ideal for warehouses and distribution centers. However, they require more floor space and are less effective for items that are not stable or cannot roll, potentially limiting their application in diverse industries.
How Do Automated Guided Vehicles (AGVs) Compare?
Automated Guided Vehicles (AGVs) represent a more advanced solution in material handling, providing flexibility in transporting goods across large facilities. These vehicles can navigate autonomously, allowing for dynamic routing and real-time adjustments based on operational needs. While AGVs offer significant advantages in terms of automation and adaptability, they come with higher initial costs and require a more complex setup, including software integration and training for staff. Additionally, ongoing maintenance can be more demanding compared to simpler systems like belt or roller conveyors.
How Can B2B Buyers Choose the Right Solution?
Selecting the right material handling solution depends on various factors, including the types of products being transported, the layout of the facility, and budget constraints. B2B buyers should conduct a thorough analysis of their operational requirements and consider the advantages and disadvantages of each system. For instance, if the primary need is for transporting lightweight or packaged goods over long distances, a belt conveyor may be the most cost-effective choice. Conversely, for operations that involve heavy loads or require flexible routing, roller conveyors or AGVs may provide superior performance. Ultimately, the decision should align with the company’s long-term operational goals and the specific demands of their industry.
Essential Technical Properties and Trade Terminology for belt conveyor systems
What Are the Key Technical Properties of Belt Conveyor Systems?
When considering the purchase of belt conveyor systems, understanding their technical properties is crucial for making informed decisions. Here are some essential specifications to evaluate:
1. Material Grade
The material grade of the conveyor belt, typically made from fabric or rubber, is a key factor influencing durability and performance. High-grade materials provide better resistance to wear and tear, chemicals, and temperature variations, which is particularly important for operations in industries such as manufacturing and distribution. Buyers should assess their specific needs based on the products being transported and environmental conditions.
2. Belt Width and Length
Belt width and length directly impact the system’s capacity and suitability for different applications. Standard widths range from 6 inches to 72 inches, while lengths can extend from 5 to 102 feet. For international buyers, especially those in Africa and South America, it’s essential to select dimensions that align with their operational space and the size of the items being transported to optimize workflow efficiency.
3. Load Capacity
The load capacity of a belt conveyor system refers to the maximum weight it can handle effectively. Systems can support loads ranging from as little as 5 lbs to over 1,280 lbs. Buyers must consider the weight and shape of the items to ensure they select a conveyor that can safely and efficiently transport their products.
4. Drive Mechanism
The drive mechanism, often a single motor, determines the system’s efficiency and reliability. Options such as variable frequency drives (VFD) allow for speed adjustments, which can be critical for operations requiring different handling speeds. Understanding the drive system helps buyers choose a conveyor that meets their production requirements without compromising on performance.
5. Incline Capability
Many belt conveyors are designed to handle inclines, with a typical maximum angle of 25 degrees. This feature is particularly beneficial in operations where space is limited, allowing for vertical transport of goods. Buyers should evaluate whether incline capabilities are necessary for their operations to maximize space efficiency.
What Are Common Trade Terms Related to Belt Conveyor Systems?
Familiarity with industry terminology can greatly enhance communication and negotiation. Here are key terms to know:
1. OEM (Original Equipment Manufacturer)
OEM refers to companies that produce components that are used in another company’s end product. Understanding OEM relationships can help buyers identify reliable sources for conveyor systems and parts, ensuring they receive quality components that meet their specifications.
2. MOQ (Minimum Order Quantity)
MOQ indicates the smallest number of units that a supplier is willing to sell. For B2B buyers, especially in regions like the Middle East and Europe, knowing the MOQ helps in budgeting and inventory planning, ensuring that they meet supplier requirements without overcommitting.
3. RFQ (Request for Quotation)
An RFQ is a document that a buyer sends to suppliers to request pricing for specific products or services. This is a critical step in the procurement process, allowing buyers to compare costs and negotiate terms effectively.
4. Incoterms (International Commercial Terms)
Incoterms are a set of predefined commercial terms used in international trade that clarify the responsibilities of buyers and sellers regarding shipping, insurance, and tariffs. For international buyers, understanding Incoterms is essential for reducing risks and ensuring smooth transactions.
5. Lead Time
Lead time refers to the duration between placing an order and receiving the goods. This is particularly important for B2B buyers who need to plan their operations around delivery schedules. Knowing lead times helps in managing inventory and production schedules effectively.
By understanding these technical properties and trade terms, international B2B buyers can make more informed decisions when investing in belt conveyor systems, ensuring they select the right equipment to meet their operational needs.
Navigating Market Dynamics and Sourcing Trends in the belt conveyor systems Sector
What Are the Key Market Dynamics and Sourcing Trends in the Belt Conveyor Systems Sector?
The global belt conveyor systems market is witnessing significant growth driven by the increasing demand for automation in various industries, including manufacturing, packaging, and logistics. This trend is particularly pronounced in regions such as Africa, South America, the Middle East, and Europe (notably Spain and Germany), where businesses are prioritizing efficiency and productivity to remain competitive. The adoption of Industry 4.0 technologies, such as IoT and AI, is revolutionizing the way conveyor systems are designed and operated. These technologies enable real-time monitoring and predictive maintenance, ensuring minimal downtime and optimizing operational efficiency.
Emerging trends include the customization of conveyor systems to meet specific operational needs, such as varying load capacities and product dimensions. International B2B buyers are increasingly interested in modular and versatile systems that can adapt to changing production requirements. Additionally, the rise of e-commerce has heightened the demand for advanced material handling solutions, making it crucial for buyers to consider suppliers that offer not only standard products but also innovative configurations tailored to their unique processes. Furthermore, the shift towards sustainable practices is influencing sourcing decisions, with buyers seeking suppliers committed to environmentally friendly practices.
How Does Sustainability and Ethical Sourcing Impact the Belt Conveyor Systems Sector?
Sustainability has become a pivotal consideration for international B2B buyers in the belt conveyor systems sector. The environmental impact of manufacturing processes and materials used in conveyor systems is under scrutiny, prompting companies to seek suppliers that prioritize eco-friendly practices. This includes the use of recyclable materials, energy-efficient motors, and sustainable production methods. For instance, buyers are increasingly looking for belt conveyor systems made with materials that have a lower carbon footprint and can be recycled at the end of their lifecycle.
The importance of ethical supply chains cannot be overstated. Buyers are now more aware of the sourcing practices of their suppliers, seeking those who adhere to fair labor practices and transparency in their operations. Certifications such as ISO 14001 (Environmental Management) and other ‘green’ certifications are becoming essential criteria in the supplier selection process. By choosing suppliers with recognized sustainability credentials, B2B buyers can enhance their corporate social responsibility initiatives and appeal to environmentally conscious customers.
What Is the Evolution of Belt Conveyor Systems and Its Relevance to Modern B2B Buyers?
The evolution of belt conveyor systems dates back to the late 18th century when they were first used in coal mines. Over the years, advancements in technology have transformed these systems into highly efficient and versatile material handling solutions. The introduction of electric motors, variable frequency drives, and automated controls has enabled conveyor systems to handle a wider range of products and applications.
In the modern B2B landscape, understanding this evolution is crucial for buyers as it informs their purchasing decisions. Knowledge of historical advancements helps buyers appreciate the capabilities of current systems and the potential for future innovations. As industries continue to evolve, those who stay informed about the history and technological advancements in belt conveyor systems can make better investment choices, ensuring they select systems that not only meet their current needs but also adapt to future demands.
Frequently Asked Questions (FAQs) for B2B Buyers of belt conveyor systems
-
How do I choose the right belt conveyor system for my needs?
Choosing the right belt conveyor system involves assessing your specific operational requirements. Consider factors such as the type of materials being transported, weight capacity, and the layout of your facility. Evaluate the different types of belt materials and configurations available, such as slider bed or roller bed conveyors, to ensure compatibility with your products. Additionally, consult with suppliers who can provide customized solutions tailored to your operational needs. Conducting a thorough cost-benefit analysis can help you make an informed decision. -
What is the best type of belt conveyor for heavy loads?
For transporting heavy loads, heavy-duty belt conveyors are ideal. These systems are specifically designed to handle substantial weights, often ranging from 500 to 1,280 lbs, depending on the model. Look for options with robust frame construction, suitable belt materials, and the ability to adjust for incline or decline if needed. Selecting a conveyor with a variable frequency drive can also provide better control over speed and acceleration, enhancing efficiency in your operations. -
What customization options are available for belt conveyor systems?
Many manufacturers offer extensive customization options for belt conveyor systems, allowing you to tailor the system to your specific requirements. Customizations can include belt width, length, material type, and additional features like side rails, inclines, or curves. Some suppliers also provide modular designs that can be easily reconfigured as your operational needs evolve. When sourcing, inquire about the manufacturer’s flexibility in design and their ability to accommodate special requests. -
What are the minimum order quantities (MOQs) for belt conveyor systems?
Minimum order quantities for belt conveyor systems can vary significantly by supplier and region. Generally, manufacturers may have MOQs ranging from one unit for custom systems to larger quantities for standard models. For international buyers, it’s advisable to discuss MOQs during initial communications with suppliers, as some may be willing to negotiate terms based on your needs or offer sample units for evaluation. -
What payment terms should I expect when purchasing belt conveyor systems?
Payment terms can differ based on the supplier and the nature of the transaction. Common arrangements include a deposit upon order confirmation, followed by the balance due before shipping. For larger orders, some suppliers might offer extended payment terms or financing options. It’s important to clarify these terms upfront and ensure they align with your cash flow needs. Additionally, consider using secure payment methods to mitigate risks in international transactions. -
How do I ensure quality assurance for belt conveyor systems?
To ensure quality assurance, work with reputable manufacturers who adhere to international quality standards. Request documentation of certifications, such as ISO 9001, and inquire about their quality control processes. Consider conducting factory visits or audits if possible, especially for large investments. Additionally, seek customer testimonials or references to assess the reliability and performance of the conveyor systems before making a purchase. -
What logistics considerations should I keep in mind when sourcing belt conveyors internationally?
When sourcing belt conveyors internationally, logistics play a crucial role in the overall success of your project. Consider shipping methods, potential tariffs, and customs regulations in both the supplier’s and your own country. Ensure that the supplier can provide detailed shipping information and support with documentation to facilitate smooth customs clearance. Additionally, factor in delivery times and plan for potential delays in your project timeline to avoid disruptions in your operations. -
How can I vet suppliers for belt conveyor systems?
Vetting suppliers is essential for a successful procurement process. Start by researching potential suppliers online and checking their industry reputation through reviews and case studies. Request references from previous clients and inquire about their experiences. Evaluate the supplier’s production capabilities, lead times, and after-sales support. Attending industry trade shows can also provide opportunities to meet suppliers in person and assess their offerings firsthand. Always ensure that the supplier aligns with your quality and service expectations before proceeding with an order.
Important Disclaimer & Terms of Use
⚠️ Important Disclaimer
The information provided in this guide, including content regarding manufacturers, technical specifications, and market analysis, is for informational and educational purposes only. It does not constitute professional procurement advice, financial advice, or legal advice.
While we have made every effort to ensure the accuracy and timeliness of the information, we are not responsible for any errors, omissions, or outdated information. Market conditions, company details, and technical standards are subject to change.
B2B buyers must conduct their own independent and thorough due diligence before making any purchasing decisions. This includes contacting suppliers directly, verifying certifications, requesting samples, and seeking professional consultation. The risk of relying on any information in this guide is borne solely by the reader.
Strategic Sourcing Conclusion and Outlook for belt conveyor systems
What Are the Key Takeaways for International B2B Buyers of Belt Conveyor Systems?
In the competitive landscape of material handling, belt conveyor systems stand out for their versatility and efficiency. For international B2B buyers, particularly from Africa, South America, the Middle East, and Europe, understanding the various types of belt conveyors—such as slider bed, incline, and troughed systems—can significantly enhance operational efficiency. Strategic sourcing is paramount; it allows companies to select the right system tailored to their specific needs while optimizing costs.
How Can Strategic Sourcing Enhance Your Operations?
Investing in high-quality belt conveyor systems not only improves productivity but also streamlines logistics and reduces labor costs. Buyers should focus on suppliers that offer modular and customizable solutions, enabling easy adjustments as operational demands evolve. Additionally, seeking partners who provide robust support and quick delivery can mitigate downtime and enhance overall efficiency.
What Does the Future Hold for Belt Conveyor Systems?
As industries increasingly adopt automation, the demand for advanced belt conveyor systems is set to rise. Buyers are encouraged to stay informed about technological advancements and emerging trends in material handling solutions. Now is the time to evaluate your current systems and consider strategic investments in belt conveyors to future-proof your operations. Engage with suppliers to explore innovative solutions that can elevate your business to new heights in efficiency and productivity.