Enhance Efficiency: The Ultimate Water Jet Sourcing Guide (2025)
Introduction: Navigating the Global Market for water jet
Navigating the global market for water jet technology can be a daunting challenge for B2B buyers, particularly those from diverse regions such as Africa, South America, the Middle East, and Europe, including countries like Italy and Colombia. With the ability to cut virtually any material with precision, water jet systems have become indispensable tools across various industries. However, finding the right water jet solution that aligns with specific business needs, budget constraints, and operational capabilities requires careful consideration and informed decision-making.
This comprehensive guide addresses essential aspects of sourcing water jet technology, including the different types of water jet systems available, their applications across industries, and strategies for effective supplier vetting. Additionally, we will delve into cost considerations, maintenance requirements, and the latest innovations in water jet technology, ensuring that buyers are well-equipped to make educated purchasing decisions.
By providing actionable insights and practical advice tailored to the unique challenges faced by international B2B buyers, this guide empowers businesses to leverage water jet technology effectively. Whether you are looking to enhance production capabilities, reduce operational costs, or improve product quality, understanding the nuances of the water jet market is crucial for success. Join us as we explore the pathways to making informed investments in water jet technology that can propel your business forward in today’s competitive landscape.
Understanding water jet Types and Variations
Type Name | Key Distinguishing Features | Primary B2B Applications | Brief Pros & Cons for Buyers |
---|---|---|---|
Abrasive Waterjet | Uses an abrasive material mixed with water for cutting | Metal fabrication, aerospace, automotive | Pros: Versatile for hard materials; high precision. Cons: Higher operating costs due to abrasives. |
Pure Waterjet | Utilizes high-pressure water without abrasives | Food processing, soft materials, glass cutting | Pros: Clean cuts; no heat-affected zone. Cons: Limited to softer materials. |
Robotic Waterjet | Integrates robotic arms for complex cutting tasks | Aerospace, automotive, custom fabrication | Pros: High flexibility; can automate complex cuts. Cons: Requires significant investment and programming expertise. |
Desktop Waterjet | Compact, entry-level models for small shops | Prototyping, education, small-scale production | Pros: Affordable; easy to use. Cons: Limited cutting thickness and material types. |
Multi-Axis Waterjet | Capable of cutting at various angles and depths | Architectural designs, artistic applications | Pros: Exceptional design capabilities; intricate cuts. Cons: More complex setup and operation. |
What Are the Characteristics of Abrasive Waterjets?
Abrasive waterjets are characterized by their ability to cut through a wide range of materials, including metals and composites, by mixing water with abrasive particles like garnet. This type is highly suitable for industries such as aerospace and automotive, where precision is paramount. When considering an abrasive waterjet, buyers should evaluate the cost of abrasives and maintenance, as these can significantly impact operating expenses.
How Do Pure Waterjets Differ in Application?
Pure waterjets utilize only high-pressure water to perform cuts, making them ideal for soft materials such as food products, rubber, and certain plastics. The absence of abrasives means cleaner cuts with no secondary processing required. However, buyers should note that this type is limited in its ability to cut hard materials, which may restrict its application in more demanding industries.
Why Choose Robotic Waterjets for Complex Cutting Tasks?
Robotic waterjets incorporate robotic arms, allowing for intricate and complex cutting tasks that traditional systems may struggle with. They are particularly beneficial in sectors like aerospace and automotive, where custom fabrication is essential. While they offer high flexibility and automation, buyers should be prepared for a higher upfront investment and the need for skilled operators to program and maintain the systems.
What Are the Benefits of Desktop Waterjets for Small Businesses?
Desktop waterjets are compact and designed for smaller operations, making them accessible for startups, educational institutions, and prototyping. They are affordable and user-friendly, suitable for cutting materials like foam, rubber, and thin metals. However, buyers should be aware of their limitations in cutting thickness and material diversity, which may restrict scalability for larger projects.
How Do Multi-Axis Waterjets Enhance Design Capabilities?
Multi-axis waterjets are advanced systems capable of cutting at various angles and depths, making them ideal for artistic applications and architectural designs. Their ability to produce intricate shapes and detailed cuts is unmatched, providing significant advantages for creative industries. However, the complexity of setup and operation can pose challenges for buyers, necessitating thorough training and expertise to maximize their potential.
Key Industrial Applications of water jet
Industry/Sector | Specific Application of Water Jet | Value/Benefit for the Business | Key Sourcing Considerations for this Application |
---|---|---|---|
Aerospace | Precision Cutting of Aircraft Components | Reduces weight while maintaining structural integrity | Look for high precision systems with advanced software |
Automotive | Custom Parts Manufacturing | Enables rapid prototyping and reduced lead times | Seek versatility to handle various materials and thicknesses |
Construction & Stone | Stone Cutting and Fabrication | Enhances design flexibility and reduces waste | Ensure compatibility with both natural and engineered stone |
Food Processing | Food Product Shaping and Cutting | Maintains hygiene and reduces contamination risks | Consider systems that comply with food safety standards |
Arts & Crafts | Artistic Designs in Glass and Other Materials | Allows intricate designs with minimal material loss | Evaluate ease of use and support for creative applications |
How is Water Jet Technology Used in Aerospace Applications?
In the aerospace industry, water jet technology is utilized for precision cutting of aircraft components, including complex shapes in metals and composites. This method is essential as it reduces weight while maintaining structural integrity, crucial for performance and safety. International buyers should prioritize high-precision systems equipped with advanced software to handle the unique requirements of aerospace manufacturing, ensuring compliance with stringent industry standards.
What Role Does Water Jet Play in Automotive Manufacturing?
Water jet cutting is increasingly popular in automotive manufacturing for custom parts production and rapid prototyping. It allows manufacturers to quickly iterate designs and produce parts without the need for extensive tooling, significantly reducing lead times. B2B buyers, particularly in regions like South America and Europe, should seek versatile water jet systems capable of handling various materials and thicknesses to meet diverse automotive application needs.
How is Water Jet Technology Transforming Construction and Stone Fabrication?
In the construction sector, particularly for stone fabrication, water jet technology offers the ability to cut natural and engineered stone with high precision. This enhances design flexibility and minimizes waste, which is particularly beneficial in projects where material costs are significant. Buyers should ensure that the water jet systems they source are compatible with both types of stone and can handle various cutting styles, such as intricate patterns or straight cuts.
How is Water Jet Used in Food Processing?
Water jet technology is applied in the food processing industry for shaping and cutting food products, such as pastries and meats. This method maintains hygiene standards and reduces contamination risks, as it is a cold cutting process. International buyers in this sector must consider systems that comply with food safety regulations and offer easy cleaning features to maintain operational efficiency.
What are the Benefits of Water Jet Technology in Arts and Crafts?
In the arts and crafts sector, water jet cutting allows for the creation of intricate designs in materials like glass, metal, and wood. This technology enables artisans to achieve detailed cuts with minimal material loss, which is essential for artistic applications. When sourcing water jet systems, buyers should evaluate ease of use and the machine’s ability to support various creative applications, ensuring that it meets the unique needs of artists and designers.
3 Common User Pain Points for ‘water jet’ & Their Solutions
Scenario 1: High Operating Costs Due to Inefficient Waterjet Systems
The Problem: Many international B2B buyers, especially in emerging markets like Africa and South America, face the challenge of high operating costs associated with outdated or inefficient waterjet systems. These systems often consume excessive energy and require frequent maintenance, leading to increased downtime and reduced productivity. Buyers may also struggle with the high costs of replacement parts, which can strain budgets, especially for small to medium-sized enterprises.
The Solution: To mitigate these high operating costs, buyers should consider investing in modern, energy-efficient waterjet systems that are designed for lower maintenance and operation costs. Researching manufacturers that offer integrated systems, such as pumps and cutting heads, can help ensure compatibility and reduce energy consumption. Additionally, opting for systems with advanced features, such as automated maintenance alerts and energy-saving modes, can help businesses maintain optimal performance while minimizing costs. Buyers should also evaluate the total cost of ownership (TCO) of potential waterjet systems, factoring in energy consumption, maintenance, and potential downtime, to make informed purchasing decisions.
Scenario 2: Difficulty in Cutting Complex Materials and Shapes
The Problem: B2B buyers in industries like aerospace and automotive often encounter challenges when it comes to cutting complex materials or intricate shapes with traditional cutting technologies. Waterjet technology is favored for its versatility, but many buyers may struggle with setting up and programming the machines to achieve the desired precision and quality. This can lead to increased waste, rework, and delays in project timelines.
The Solution: To address this issue, buyers should prioritize sourcing waterjet systems that come equipped with user-friendly software designed for complex cutting tasks. Look for systems that support advanced CAD/CAM integration, allowing operators to easily import designs and generate cutting paths. Training programs offered by manufacturers can also be invaluable, equipping staff with the necessary skills to maximize the machine’s capabilities. Furthermore, engaging with experienced application engineers from the manufacturer can provide tailored advice on specific materials and cutting techniques, ensuring optimal results and reducing waste.
Scenario 3: Limited Knowledge on Material Compatibility and Cutting Parameters
The Problem: Many B2B buyers, particularly those new to waterjet technology, often find themselves overwhelmed by the variety of materials that can be cut and the specific parameters required for each. This lack of understanding can lead to improper settings, resulting in subpar cut quality or even damage to the waterjet machine. Buyers from diverse regions, such as the Middle East and Europe, may also face unique challenges based on the availability of materials and local industry standards.
The Solution: To overcome this knowledge gap, buyers should seek out comprehensive resource materials and support from waterjet manufacturers. This includes detailed material compatibility charts, recommended cutting parameters, and case studies highlighting successful applications across various industries. Buyers can also benefit from joining industry forums and attending workshops or trade shows, where they can interact with experts and peers to share experiences and insights. Establishing a relationship with a trusted supplier who offers ongoing support and training can further enhance understanding and ensure that buyers can leverage their waterjet systems to their full potential.
Strategic Material Selection Guide for water jet
When selecting materials for water jet cutting, it is crucial to understand the properties, advantages, and limitations of each material. This knowledge will help international B2B buyers make informed decisions that align with their operational needs and compliance requirements. Below, we analyze four common materials used in water jet applications: metals, composites, glass, and stone.
What Are the Key Properties of Metals in Water Jet Cutting?
Metals, including aluminum, stainless steel, and carbon steel, are popular choices for water jet cutting due to their versatility and strength. Key properties relevant to their performance include high-temperature resistance, varying levels of corrosion resistance, and the ability to withstand high-pressure water streams.
Pros: Metals are durable and can be cut into intricate shapes with precision. They are widely used in industries such as automotive and aerospace, where strength and reliability are paramount.
Cons: Metals can be more expensive than other materials, and their cutting may require additional post-processing to achieve desired finishes. Additionally, thicker metals may require more powerful water jet systems, increasing operational costs.
Impact on Application: Metals are compatible with various media, including abrasive garnet, making them suitable for high-precision applications.
Considerations for International Buyers: Compliance with standards such as ASTM and DIN is essential, particularly in Europe and the Middle East. Buyers should also consider local availability and pricing fluctuations due to market conditions.
How Do Composites Perform in Water Jet Cutting?
Composites, such as carbon fiber and fiberglass, are increasingly used in industries like aerospace and automotive due to their lightweight and high-strength characteristics. They exhibit excellent resistance to corrosion and temperature variations.
Pros: Composites allow for complex shapes and designs while maintaining structural integrity. They are also lighter than metals, which can reduce transportation costs.
Cons: Cutting composites can produce dust and debris, requiring additional safety measures. Moreover, they may have a higher initial cost compared to traditional materials.
Impact on Application: Composites are particularly suitable for applications requiring a combination of strength and reduced weight, such as in aerospace components.
Considerations for International Buyers: Buyers should ensure compliance with industry-specific standards and certifications, particularly in Europe and the Middle East, where regulations can be stringent.
What Are the Benefits and Limitations of Glass in Water Jet Cutting?
Glass is a unique material that can be cut with water jets to create intricate designs for architectural and artistic applications. Its key properties include brittleness and varying levels of thermal resistance.
Pros: Water jet cutting minimizes the risk of thermal stress and cracking, which is common with traditional cutting methods. This allows for clean edges and detailed designs.
Cons: The brittleness of glass can lead to breakage during handling and cutting, necessitating careful operational procedures. Additionally, glass can be more expensive than other materials.
Impact on Application: Glass is ideal for decorative elements and architectural features, where aesthetics are critical.
Considerations for International Buyers: Compliance with safety standards is vital, especially in regions with strict regulations regarding glass products. Buyers should also be aware of local suppliers and their capabilities.
How Does Stone Compare in Water Jet Cutting Applications?
Stone, including natural and engineered varieties, is commonly used in construction and landscaping. Its properties include high density and durability, making it suitable for various applications.
Pros: Water jet cutting allows for precise shapes and intricate designs in stone, reducing the need for further finishing. It is also effective in cutting thick materials without generating heat.
Cons: The weight of stone can increase shipping and handling costs. Additionally, specific water jet systems may be required to handle the density of stone materials.
Impact on Application: Stone is widely used in countertops, flooring, and architectural features, where durability and aesthetics are essential.
Considerations for International Buyers: Buyers should consider local sourcing options to minimize costs and ensure compliance with regional standards for construction materials.
Summary Table of Material Selection for Water Jet Cutting
Material | Typical Use Case for Water Jet | Key Advantage | Key Disadvantage/Limitation | Relative Cost (Low/Med/High) |
---|---|---|---|---|
Metals | Automotive, aerospace parts | High durability and strength | Higher cost, potential need for post-processing | Medium |
Composites | Aerospace components, automotive | Lightweight, complex shapes | Produces dust, higher initial cost | High |
Glass | Architectural features, art | Minimizes thermal stress | Brittle, careful handling needed | High |
Stone | Countertops, flooring | Precise cuts, durability | Heavy, may require specialized systems | Medium |
This strategic material selection guide provides valuable insights for international B2B buyers, helping them navigate the complexities of water jet cutting applications and make informed decisions tailored to their specific needs and compliance requirements.
In-depth Look: Manufacturing Processes and Quality Assurance for water jet
What Are the Main Stages of Waterjet Manufacturing Processes?
Manufacturing waterjet systems involves several critical stages, each designed to ensure that the final product meets the high standards required by various industries. Understanding these stages is essential for international B2B buyers looking for quality and reliability in their waterjet equipment.
1. Material Preparation: How Is the Right Material Chosen and Processed?
The first stage in the manufacturing process is material preparation. High-quality materials such as stainless steel, aluminum, and composite materials are selected based on the specific waterjet system design. This selection is crucial as it directly impacts the durability and performance of the waterjet.
Once materials are chosen, they undergo cutting and machining processes to create components like pump casings, cutting heads, and tables. Advanced CNC machines are often utilized during this stage to ensure precision and consistency in material dimensions. Proper material handling is also critical to prevent contamination and ensure the integrity of the materials used.
2. Forming: What Techniques Are Used to Shape Waterjet Components?
The forming stage involves shaping the prepared materials into the desired components of the waterjet system. Common techniques include:
- CNC Machining: This technique allows for high precision in cutting and shaping parts such as the cutting head and pump components.
- Welding: Components may be welded together to create a robust structure. This requires skilled labor and adherence to strict welding standards to ensure strength and durability.
- Casting: In some cases, casting techniques are used for complex shapes that cannot be easily machined.
The choice of technique will depend on the specific design requirements and the type of material being used.
3. Assembly: How Are Waterjet Systems Assembled for Optimal Performance?
Once the components are formed, they are assembled to create the complete waterjet system. This stage involves:
- Integration of Components: Each part, from the pump to the cutting head, must be integrated seamlessly. This requires careful alignment and fitting to ensure that the system operates effectively.
- System Testing: Before final assembly is complete, initial testing is conducted to verify that all components work together. This may include pressure tests and functionality tests for the cutting head.
Proper assembly is critical, as any misalignment can lead to inefficiencies and increased wear on the machine.
4. Finishing: What Processes Ensure Quality and Aesthetic Appeal?
The finishing stage includes surface treatment and painting, which not only enhance the aesthetic appeal of the waterjet systems but also protect them from corrosion and wear. Techniques such as anodizing, powder coating, or painting are commonly used.
Additionally, quality control checks are conducted during this stage to ensure that the system meets all design specifications and quality standards.
What Quality Assurance Measures Are Essential for Waterjet Manufacturing?
Quality assurance (QA) is crucial in the manufacturing of waterjet systems, ensuring that products meet both international standards and customer expectations. Here are key aspects to consider:
Relevant International Standards: Which Certifications Should Buyers Look For?
Internationally recognized standards such as ISO 9001 play a significant role in quality assurance for waterjet manufacturers. ISO 9001 focuses on maintaining quality management systems and ensuring consistent quality in production processes.
Other relevant certifications may include:
- CE Marking: Indicates compliance with European safety, health, and environmental protection standards.
- API Certification: Particularly important for waterjet systems used in oil and gas industries, ensuring that products meet specific industry standards.
Buyers should verify that suppliers hold these certifications to ensure that products meet required safety and performance benchmarks.
What Are the Key Quality Control Checkpoints in Waterjet Manufacturing?
Quality control in waterjet manufacturing typically includes several checkpoints:
-
Incoming Quality Control (IQC): This initial checkpoint involves inspecting raw materials and components as they arrive at the manufacturing facility. This step ensures that all incoming materials meet specified requirements before they are used in production.
-
In-Process Quality Control (IPQC): During the manufacturing process, periodic checks are conducted to ensure that each stage of production adheres to quality standards. This may include measuring tolerances and inspecting welds.
-
Final Quality Control (FQC): Once assembly is complete, the entire waterjet system undergoes thorough testing and inspection. This includes performance tests to verify that the system operates within specified parameters.
How Can B2B Buyers Verify Supplier Quality Control?
To ensure that suppliers adhere to stringent quality assurance measures, B2B buyers can take several steps:
-
Conduct Audits: Regular audits of suppliers can help buyers assess the quality management systems in place. This may involve visiting manufacturing facilities and reviewing quality control processes.
-
Request Quality Reports: Suppliers should provide documentation detailing their quality assurance practices, including testing results and compliance with international standards.
-
Engage Third-Party Inspectors: Utilizing independent third-party inspection services can provide an unbiased assessment of the supplier’s quality control processes and product quality.
What Nuances Should International B2B Buyers Consider Regarding Quality Control?
International B2B buyers, particularly from regions like Africa, South America, the Middle East, and Europe, should be aware of several nuances in quality control:
-
Cultural Differences: Different regions may have varying approaches to quality assurance. Understanding these cultural contexts can help buyers better navigate supplier relationships.
-
Regulatory Compliance: Buyers must ensure that suppliers comply with both local and international regulations, which can vary significantly across regions.
-
Language Barriers: Communication can sometimes hinder the quality assurance process. Buyers should ensure that they and their suppliers share a common understanding of quality expectations and standards.
By focusing on these manufacturing processes and quality assurance measures, international B2B buyers can make informed decisions when selecting waterjet suppliers, ensuring they receive high-quality systems that meet their operational needs.
Practical Sourcing Guide: A Step-by-Step Checklist for ‘water jet’
To successfully procure a water jet cutting system, it’s essential to follow a structured approach. This checklist will guide you through the critical steps necessary to make an informed purchasing decision, ensuring that you choose the right equipment for your business needs.
Step 1: Define Your Technical Specifications
Before exploring suppliers, clearly outline your technical requirements. Consider factors such as the types of materials you will be cutting (e.g., metals, glass, stone), the maximum thickness, and the precision needed. This clarity will help you narrow down your options and find a water jet that meets your specific applications.
- Material Types: Identify the primary materials you will be processing.
- Thickness Requirements: Specify the maximum thickness for each material type.
Step 2: Set a Budget and Total Cost of Ownership
Determine your budget, factoring in not just the initial purchase price but also ongoing operational costs, maintenance, and potential upgrades. Understanding the total cost of ownership (TCO) will help you evaluate the long-term value of different options.
- Initial Costs: Look at the price of the water jet machine itself.
- Operational Costs: Include consumables, energy consumption, and maintenance.
Step 3: Research Potential Suppliers
Conduct thorough research to identify reputable suppliers with a track record in the water jet industry. Look for companies that have been in business for several years and have a strong presence in your region.
- Supplier Reviews: Check customer testimonials and case studies.
- Industry Experience: Prioritize suppliers familiar with your specific industry applications.
Step 4: Request Detailed Proposals and Demonstrations
Once you have a shortlist of suppliers, request detailed proposals that include specifications, pricing, and warranty information. If possible, arrange for live demonstrations to see the equipment in action and assess its performance.
- Proposal Clarity: Ensure the proposal outlines all costs and specifications.
- Demonstration: Observe the machine’s capabilities with materials similar to your own.
Step 5: Verify Supplier Certifications and Support
Confirm that the supplier meets relevant industry standards and certifications. Additionally, evaluate the level of after-sales support they provide, including training, maintenance, and troubleshooting services.
- Certifications: Look for ISO certifications or other industry-specific standards.
- Support Services: Inquire about training programs and technical support availability.
Step 6: Analyze Warranty and Maintenance Options
Examine the warranty terms offered by the supplier and what they cover. A robust warranty indicates confidence in the product and can protect your investment.
- Warranty Duration: Assess the length and coverage of the warranty.
- Maintenance Plans: Consider options for preventive maintenance and emergency repairs.
Step 7: Finalize the Purchase and Plan for Installation
Once you’ve selected a supplier and negotiated terms, finalize the purchase. Plan for installation, including any site preparation or utility requirements, to ensure a smooth setup process.
- Installation Requirements: Verify what is needed for installation, such as space and power supply.
- Timeline: Establish a timeline for delivery and installation to minimize downtime.
By following these steps, you will be well-equipped to make an informed decision when sourcing a water jet cutting system, ultimately enhancing your operational efficiency and productivity.
Comprehensive Cost and Pricing Analysis for water jet Sourcing
What Are the Key Cost Components in Water Jet Sourcing?
When sourcing water jet systems, understanding the detailed cost structure is essential for B2B buyers. The primary cost components include:
-
Materials: The quality and type of materials used in manufacturing water jet systems significantly impact costs. High-grade stainless steel or specialized alloys for cutting heads can elevate prices.
-
Labor: Skilled labor is necessary for both manufacturing and maintenance of water jet systems. Costs vary by region; for instance, labor in Europe may be higher compared to South America or Africa.
-
Manufacturing Overhead: This includes expenses related to facility operations, equipment maintenance, and utilities. Efficient production techniques can help reduce overhead costs.
-
Tooling: Specialized tools and dies required for producing water jet components can be a significant investment. Custom tooling may be necessary for specific applications, further affecting costs.
-
Quality Control (QC): Rigorous testing and quality assurance processes are vital to ensure system reliability. Implementing comprehensive QC can increase upfront costs but may save on long-term maintenance.
-
Logistics: Transporting water jet systems involves considerable logistics costs, especially for international shipping. These costs can fluctuate based on distance, shipping method, and customs duties.
-
Margin: Suppliers typically add a margin to cover their costs and ensure profitability. This can vary widely based on the supplier’s business model and market competition.
How Do Price Influencers Affect Water Jet Costs?
Several factors influence the pricing of water jet systems, which buyers should consider:
-
Volume/MOQ: Purchasing in larger volumes can lead to significant discounts. Establishing long-term relationships with suppliers may also yield favorable pricing.
-
Specifications and Customization: Customized solutions tailored to specific industry needs often incur higher costs. Buyers must balance their requirements with budget constraints.
-
Materials: The choice of materials not only affects the initial purchase price but also influences operational efficiency and durability. Premium materials may lead to higher upfront costs but lower maintenance over time.
-
Quality and Certifications: Suppliers that adhere to international quality standards and certifications may charge more, reflecting their commitment to reliability and performance.
-
Supplier Factors: The reputation and experience of the supplier can impact pricing. Established suppliers may offer higher prices due to their proven track record, while emerging suppliers might have more competitive rates.
-
Incoterms: Understanding the chosen Incoterms is crucial, as they define the responsibilities of buyers and sellers in terms of shipping costs, insurance, and risk. This can significantly affect the total landed cost of the equipment.
What Are Effective Buyer Tips for Water Jet Sourcing?
To maximize value when sourcing water jet systems, B2B buyers should consider the following strategies:
-
Negotiate Wisely: Effective negotiation can lead to reduced prices and better terms. Buyers should be prepared to discuss volume discounts, payment terms, and additional services.
-
Focus on Cost-Efficiency: Evaluate the total cost of ownership (TCO) rather than just the purchase price. This includes maintenance, operational costs, and potential downtime.
-
Understand Pricing Nuances for International Buyers: Buyers from Africa, South America, the Middle East, and Europe must be aware of regional pricing variations and market dynamics. Exchange rates, local tariffs, and import duties can all impact costs.
-
Request Multiple Quotes: Obtaining quotes from various suppliers can help buyers gauge market prices and negotiate better deals.
-
Evaluate Supplier Support: Assessing the level of support offered by suppliers, including training and after-sales service, can influence long-term satisfaction and productivity.
Disclaimer for Indicative Prices
The prices mentioned in this analysis are indicative and subject to change based on market conditions, supplier pricing strategies, and specific buyer requirements. B2B buyers are encouraged to conduct thorough market research and consult with suppliers to obtain accurate and current pricing information.
Alternatives Analysis: Comparing water jet With Other Solutions
When considering cutting technologies, it’s essential to evaluate various alternatives to water jet systems. The right choice depends on specific business needs, material types, and operational capabilities. Below, we will compare water jet cutting technology against two viable alternatives: laser cutting and plasma cutting.
Comparison Aspect | Water Jet | Laser Cutting | Plasma Cutting |
---|---|---|---|
Performance | Excellent for a wide range of materials, including metals, glass, and ceramics; no heat-affected zones. | Fast and precise for thin materials, best with metals; limited for reflective materials. | High-speed cutting for metals; less precision on intricate designs. |
Cost | Higher initial investment; ongoing costs for abrasive materials and maintenance. | Moderate initial cost; lower operational costs; focuses on specific materials. | Generally lower initial cost; higher consumable costs for electrodes and gases. |
Ease of Implementation | Requires skilled operation; setup can be complex but is user-friendly with modern interfaces. | Straightforward setup; requires alignment and calibration but easy to operate. | Relatively easy to set up; can be operated with basic training. |
Maintenance | Regular maintenance needed for pumps and nozzles; robust but requires skilled technicians. | Low maintenance; mostly requires lens and mirror cleaning and occasional part replacements. | Requires regular maintenance on consumables; performance can degrade over time. |
Best Use Case | Ideal for cutting intricate shapes in various materials, especially where precision and edge quality are paramount. | Best suited for high-speed cutting of thin metals and applications where speed is more critical than thickness. | Excellent for heavy-duty applications where speed is essential, such as construction and heavy fabrication. |
What Are the Advantages and Disadvantages of Laser Cutting?
Laser cutting is renowned for its speed and precision, particularly with thin materials such as sheet metal. It operates using a focused beam of light to melt or vaporize the material, allowing for clean cuts with minimal kerf. However, its limitations include challenges with reflective materials (like copper and brass) and thicker materials, which may require more power than a standard laser can provide. Overall, while laser cutting is efficient, it may not be the best choice for diverse material types and thicker sections.
How Does Plasma Cutting Compare?
Plasma cutting utilizes high-velocity ionized gas to cut through electrically conductive materials. It is particularly effective for thick metals and can achieve high cutting speeds, making it suitable for heavy industrial applications. However, plasma cutting can produce rough edges and is less precise than water jet or laser cutting, making it less ideal for intricate designs. Additionally, it can create heat-affected zones, which may necessitate further finishing processes.
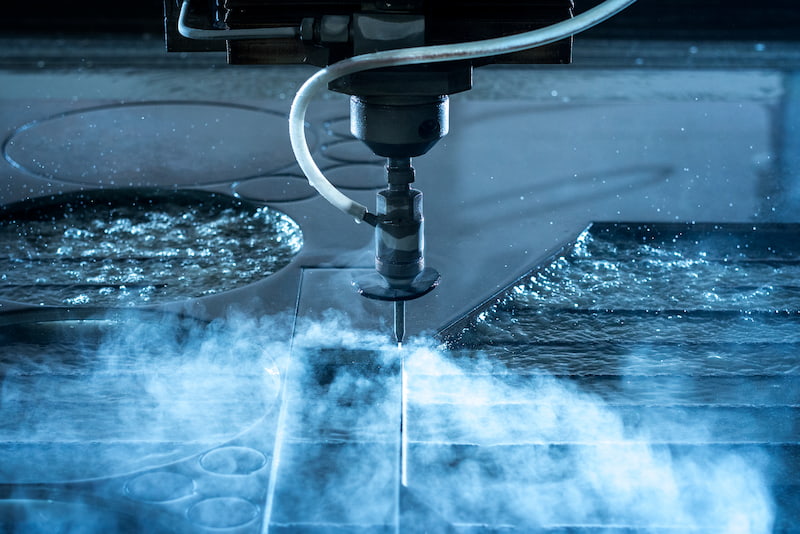
A stock image related to water jet.
Conclusion: How to Choose the Right Cutting Technology for Your Business?
In selecting the appropriate cutting technology, international B2B buyers must assess their specific operational needs, including the types of materials they work with, the required precision, and budget constraints. Water jet cutting excels in versatility and edge quality, making it suitable for a wide range of industries, from aerospace to construction. In contrast, laser and plasma cutting may offer advantages in speed and cost-effectiveness for specific applications. Careful consideration of these factors will enable buyers to make informed decisions that align with their production goals and operational capabilities.
Essential Technical Properties and Trade Terminology for water jet
What Are the Essential Technical Properties of Water Jet Systems?
Water jet cutting technology offers a range of specifications crucial for B2B buyers to understand. Here are some key technical properties:
What Is Material Grade and Why Is It Important?
Material grade refers to the classification of materials based on their physical and chemical properties. In water jet cutting, this determines how well a material can withstand the cutting process. For instance, metals like stainless steel or aluminum come with various grades that affect their machinability and durability. B2B buyers should select water jet systems compatible with their specific material grades to ensure efficiency and quality in their cutting processes.
How Does Tolerance Affect Cutting Precision?
Tolerance is the permissible limit or limits of variation in a physical dimension. In the context of water jet cutting, tighter tolerances mean more precise cuts, which are crucial for industries requiring high accuracy, such as aerospace and automotive. Understanding the tolerance levels your water jet can achieve helps in selecting the right equipment for your operational needs, minimizing material waste and rework.
What Is Cutting Thickness and Its Significance?
Cutting thickness defines the maximum depth of material that a water jet can effectively cut. Different water jet systems have varying capabilities; for example, some can cut through materials up to 1 inch thick while others can manage even thicker materials. Knowing the cutting thickness is vital for B2B buyers, as it influences the choice of equipment based on the specific projects or materials they plan to handle.
Why Is Pump Pressure a Key Specification?
Pump pressure, measured in PSI (pounds per square inch), is a critical specification that affects the cutting speed and efficiency of a water jet system. Higher pump pressures enable the cutting of denser and thicker materials but also require more robust machinery. Understanding pump pressure allows B2B buyers to select the right equipment tailored to their cutting demands, ensuring optimal performance.
What Are Common Trade Terminology Terms in Water Jet Technology?
Understanding industry-specific terminology is essential for effective communication and decision-making in B2B transactions. Here are some common terms:
What Does OEM Mean in the Context of Water Jet Systems?
OEM stands for Original Equipment Manufacturer. In water jet technology, it refers to companies that produce components or systems that are then sold by another company under its brand. For buyers, working with OEMs ensures they receive high-quality parts that are specifically designed for their water jet systems, which can lead to better performance and reliability.
How Does MOQ Affect Purchasing Decisions?
MOQ, or Minimum Order Quantity, is the smallest number of units that a supplier is willing to sell. This term is especially important for B2B buyers in Africa, South America, the Middle East, and Europe, as it can impact cash flow and inventory management. Understanding MOQ helps buyers negotiate better terms and avoid overcommitting to stock that may not be immediately needed.
What Is an RFQ and Why Is It Essential?
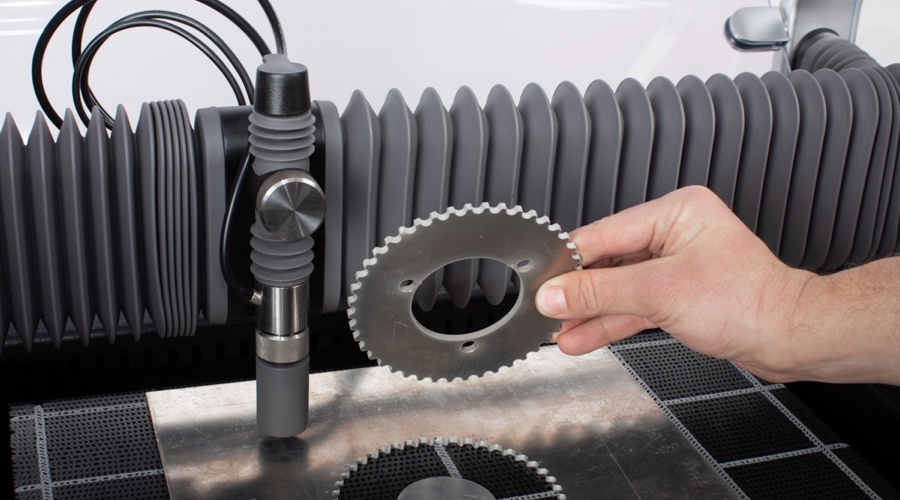
A stock image related to water jet.
RFQ stands for Request for Quotation. This document is used by buyers to solicit price proposals from suppliers for specific products or services. An RFQ is essential for B2B buyers to ensure they receive competitive pricing and to understand the total cost of ownership, including shipping and any applicable taxes or duties.
How Do Incoterms Influence International Trade?
Incoterms, short for International Commercial Terms, define the responsibilities of buyers and sellers in international transactions. They clarify who is responsible for shipping, insurance, and tariffs, which can significantly affect the overall cost and logistics of purchasing water jet systems. Understanding Incoterms is crucial for B2B buyers to avoid misunderstandings and ensure smooth cross-border transactions.
By grasping these essential technical properties and trade terminology, international B2B buyers can make informed decisions when investing in water jet technology, ultimately enhancing their operational efficiency and market competitiveness.
Navigating Market Dynamics and Sourcing Trends in the water jet Sector
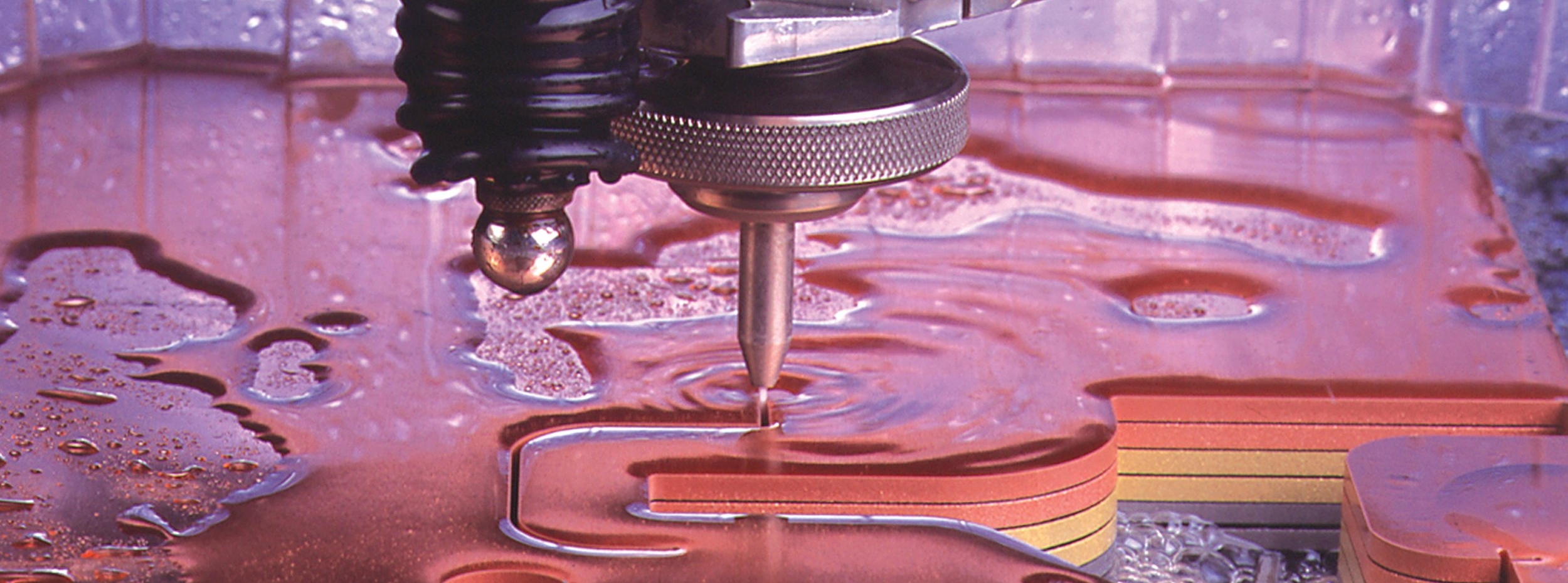
A stock image related to water jet.
What Are the Current Market Dynamics and Key Trends in the Water Jet Sector?
The global water jet cutting market is witnessing significant growth, driven by the demand for precision cutting across various industries, including aerospace, automotive, and manufacturing. Key drivers include the increasing adoption of automation and Industry 4.0 technologies, which allow for enhanced operational efficiency and reduced waste. Moreover, water jet systems can cut a wide variety of materials, from metals to glass, making them versatile tools for international buyers looking to diversify their production capabilities.
In Africa and South America, there is a growing interest in localized manufacturing solutions, spurred by government initiatives to bolster domestic industries. This trend is complemented by the rise of small to medium-sized enterprises (SMEs) that require cost-effective and flexible cutting solutions. In contrast, the Middle East and European markets are focusing on advanced water jet technologies that offer improved edge quality and faster processing times. B2B buyers should consider these regional dynamics when sourcing water jet systems, ensuring they select machines that align with their specific operational needs and market demands.
Emerging technologies such as hybrid cutting systems, which combine water jet and laser cutting methods, are gaining traction. These innovations promise to enhance cutting speed and precision, catering to the demands of high-end industries. Additionally, the integration of IoT (Internet of Things) in water jet machines is becoming commonplace, allowing for real-time monitoring and predictive maintenance, further improving productivity.
How Can B2B Buyers Ensure Sustainability and Ethical Sourcing in Water Jet Technologies?
Sustainability is becoming a critical consideration for B2B buyers in the water jet sector. The environmental impact of water jet cutting is relatively low compared to traditional cutting methods, as it generates minimal waste and does not produce harmful fumes. However, buyers should still prioritize suppliers that implement sustainable practices in their operations. This includes using recyclable materials, reducing water consumption, and minimizing energy usage during the cutting process.
Ethical sourcing is also paramount. B2B buyers should look for suppliers that demonstrate transparency in their supply chains and adhere to fair labor practices. Certifications such as ISO 14001 for environmental management and ISO 9001 for quality management are essential indicators of a supplier’s commitment to sustainability and ethical operations. Additionally, sourcing from local suppliers can further reduce the carbon footprint associated with transportation.
Moreover, the demand for ‘green’ materials in water jet applications is on the rise. Buyers should explore options for cutting materials that are recyclable or made from sustainable resources. By aligning their sourcing strategies with sustainability goals, B2B buyers can not only reduce their environmental impact but also enhance their brand reputation in an increasingly eco-conscious market.
What Is the Brief Evolution and History of Water Jet Technology?
Water jet cutting technology has evolved significantly since its inception in the 1960s. Initially developed for the aerospace industry, it has expanded into various sectors due to its versatility and precision. The introduction of abrasive materials in the 1970s allowed water jets to cut through tougher materials, further broadening their applications.
In the 1980s and 1990s, advancements in computer numerical control (CNC) technology enabled more complex cutting patterns and higher precision, making water jets a preferred choice for manufacturers. The 21st century has seen the integration of digital technologies, such as CAD/CAM systems and IoT, revolutionizing the operational capabilities of water jet machines.
As the technology continues to advance, international B2B buyers can leverage these developments to enhance their production efficiency and product quality, ensuring they remain competitive in a fast-evolving global market. Understanding the historical context of water jet technology helps buyers appreciate the innovation trajectory and anticipate future trends that may impact their sourcing decisions.
Frequently Asked Questions (FAQs) for B2B Buyers of water jet
-
How do I choose the right water jet cutting machine for my business needs?
Choosing the right water jet cutting machine involves assessing your specific cutting requirements, including material types, thicknesses, and production volume. Consider the versatility of the machine, as some models can cut various materials like metals, glass, and composites. Evaluate the technology behind the pump and cutting head, as higher pressures can result in more efficient cuts. Additionally, look for user-friendly software and integration capabilities with existing systems. Consulting with manufacturers and requesting demonstrations can provide valuable insights tailored to your operational needs. -
What is the best water jet cutting technology for precision applications?
For precision applications, consider a water jet cutting system that offers advanced features such as high-pressure pumps and precision cutting heads. Systems equipped with abrasive water jet technology provide excellent edge quality and can handle intricate designs with minimal kerf loss. Brands with a strong reputation in the industry, like Flow or WAZER, often have proven solutions tailored for precision cutting. Always verify technical specifications and user reviews to ensure the technology aligns with your accuracy requirements. -
How can I effectively vet water jet suppliers for international trade?
Vetting water jet suppliers involves several steps. Begin by researching their market reputation and customer reviews, focusing on their experience in international trade. Request references from previous clients and assess their responsiveness to inquiries. Verify their certifications and compliance with international quality standards. It’s beneficial to arrange a factory visit or video tour to inspect their production capabilities and quality control processes. Lastly, consider their after-sales support and warranty policies, as reliable service is crucial for long-term partnerships. -
What customization options are typically available for water jet systems?
Most water jet manufacturers offer customization options to fit specific operational needs. Customizations can include adjustments in cutting head design, software configurations, and integrated automation features. You may also request modifications for specialized materials or specific thicknesses. Discussing your unique requirements with potential suppliers will help identify the best solutions. Additionally, inquire about the availability of training programs to ensure your team can maximize the customized features effectively. -
What are the typical minimum order quantities (MOQs) for water jet systems?
Minimum order quantities for water jet systems can vary significantly based on the manufacturer and the type of equipment. Some suppliers may not have an MOQ for individual machines, while others might set a minimum for bulk orders or additional components. It’s crucial to communicate directly with suppliers about your needs and any budget constraints. When sourcing internationally, also consider logistics and shipping costs, which can impact overall project feasibility. -
What payment terms should I expect when purchasing water jet equipment internationally?
Payment terms for international water jet purchases often vary by supplier and region. Common terms include upfront deposits (usually 20-50%), with the balance due upon delivery or installation. Some suppliers may offer financing options or payment plans to ease cash flow concerns. Be sure to clarify terms related to currency, taxes, and potential tariffs that may apply to your purchase. Understanding these details will help you budget effectively and avoid surprises during the transaction process. -
How do I ensure quality assurance (QA) for my water jet equipment?
To ensure quality assurance for your water jet equipment, request detailed documentation from the supplier, including quality control processes and testing protocols. Look for suppliers with ISO certifications or similar industry standards that emphasize product quality. During the procurement process, ask about their warranty policies and the availability of maintenance services. Additionally, consider conducting pre-shipment inspections to verify that the equipment meets your specifications before it leaves the supplier’s facility. -
What logistical considerations should I keep in mind when importing water jet machines?
When importing water jet machines, consider logistics such as shipping methods, customs clearance processes, and local regulations in your destination country. It’s essential to work with a freight forwarder familiar with heavy machinery to navigate import duties and taxes effectively. Prepare for potential delays by factoring in lead times for manufacturing and shipping. Also, ensure that you have the necessary infrastructure for installation, including power supply and workspace requirements, to avoid complications upon arrival.
Important Disclaimer & Terms of Use
⚠️ Important Disclaimer
The information provided in this guide, including content regarding manufacturers, technical specifications, and market analysis, is for informational and educational purposes only. It does not constitute professional procurement advice, financial advice, or legal advice.
While we have made every effort to ensure the accuracy and timeliness of the information, we are not responsible for any errors, omissions, or outdated information. Market conditions, company details, and technical standards are subject to change.
B2B buyers must conduct their own independent and thorough due diligence before making any purchasing decisions. This includes contacting suppliers directly, verifying certifications, requesting samples, and seeking professional consultation. The risk of relying on any information in this guide is borne solely by the reader.
Strategic Sourcing Conclusion and Outlook for water jet
How Can Strategic Sourcing Enhance Your Waterjet Operations?
In today’s competitive landscape, strategic sourcing of waterjet technology can significantly elevate operational efficiency and product quality. By investing in high-quality systems, such as those offered by Flow, WAZER, and Laguna Tools, businesses can achieve precision cutting across a diverse range of materials, from metals to composites. This flexibility not only reduces the need for secondary processes but also minimizes waste, translating to cost savings and enhanced productivity.
What Should International Buyers Consider When Sourcing Waterjet Systems?
International buyers, particularly from Africa, South America, the Middle East, and Europe, should prioritize partnerships with manufacturers that offer comprehensive support, including installation, training, and ongoing maintenance. Understanding the specific cutting needs of your industry—whether it be aerospace, automotive, or fabrication—will guide you in selecting the right waterjet configuration. Additionally, leveraging localized suppliers can streamline logistics and reduce lead times, providing a competitive edge.
What Lies Ahead for Waterjet Technology?
As waterjet technology continues to evolve, the future looks promising. Innovations in automation and software integration are set to enhance cutting capabilities and operational ease. By staying informed about these advancements and strategically sourcing the right equipment, businesses can position themselves to capitalize on emerging opportunities. Now is the time to explore the potential of waterjet cutting in your operations and embrace the benefits of precision manufacturing.