Explore Types of Gears: The Complete Buyer’s Guide (2025)
Introduction: Navigating the Global Market for types of gears
In today’s rapidly evolving industrial landscape, sourcing the right types of gears can be a daunting task for international B2B buyers. Whether you are in Africa, South America, the Middle East, or Europe, understanding the diverse range of gear types—such as spur, helical, bevel, and worm gears—is essential for optimizing machinery performance and ensuring seamless operations. This comprehensive guide is designed to demystify the complexities surrounding gear selection, providing insights into their various applications, manufacturing standards, and the critical factors influencing purchasing decisions.
The guide delves deep into the characteristics and functionalities of each gear type, enabling buyers to make informed choices that align with their specific operational needs. Additionally, it offers practical advice on supplier vetting processes, cost considerations, and the importance of precision standards such as ISO and AGMA. By equipping B2B buyers with actionable insights, this resource aims to facilitate smarter procurement strategies that not only enhance productivity but also foster long-term partnerships with reliable suppliers.
As you navigate the global market for gears, this guide will serve as your go-to reference, empowering you to tackle the challenges of gear sourcing with confidence and clarity. Whether you’re seeking to improve efficiency in manufacturing or enhance the performance of your machinery, understanding the intricacies of gear types is the first step towards achieving your business objectives.
Understanding types of gears Types and Variations
Type Name | Key Distinguishing Features | Primary B2B Applications | Brief Pros & Cons for Buyers |
---|---|---|---|
Spur Gears | Straight teeth, parallel shafts, high accuracy | Manufacturing, automotive, conveyor systems | Pros: Simple design, cost-effective; Cons: Limited load capacity. |
Helical Gears | Winding teeth, higher load capacity, quieter operation | Robotics, aerospace, high-speed machinery | Pros: Smooth operation, better efficiency; Cons: Requires thrust bearings. |
Bevel Gears | Cone-shaped, used for intersecting shafts | Automotive differentials, machine tools | Pros: Versatile for angle changes; Cons: Complex design can increase costs. |
Worm Gears | Screw-like design, high torque, non-intersecting shafts | Lifts, conveyors, and heavy machinery | Pros: High torque transmission; Cons: Low efficiency due to sliding contact. |
Planetary Gears | Central sun gear with orbiting planet gears | Automotive transmissions, robotics | Pros: Compact design, high efficiency; Cons: Complex assembly and maintenance. |
What Are the Characteristics and Suitability of Spur Gears for B2B Buyers?
Spur gears are the most common type of gear, featuring straight teeth that are parallel to the axis of rotation. They are known for their simplicity and high accuracy in motion transfer, making them ideal for applications in manufacturing, automotive, and conveyor systems. When purchasing spur gears, buyers should consider the required load capacity, as these gears may not handle heavy loads as efficiently as others. Their cost-effectiveness and ease of production make them a go-to choice for many businesses.
How Do Helical Gears Enhance Performance in Various Applications?
Helical gears feature teeth that are cut at an angle, allowing for smoother engagement and reducing noise during operation. This design enables them to transmit higher loads and is particularly suited for high-speed applications in industries like robotics and aerospace. B2B buyers should evaluate the thrust forces generated by helical gears, which necessitate additional thrust bearings. While they offer improved performance, the complexity of their design can lead to higher manufacturing costs.
In What Scenarios Are Bevel Gears Most Effective?
Bevel gears are characterized by their cone-shaped design, allowing them to transmit power between shafts that intersect at various angles. They are commonly used in automotive differentials and machine tools. For B2B buyers, the versatility of bevel gears is appealing, but they should be mindful of the potential for increased costs due to their complex manufacturing processes. Evaluating the specific angle requirements and load capacities is crucial for ensuring optimal performance.
What Advantages Do Worm Gears Offer Despite Their Limitations?
Worm gears consist of a screw-like worm and a gear wheel, providing high torque and enabling motion between non-intersecting shafts. They are often utilized in lifts, conveyors, and heavy machinery. While worm gears excel in torque transmission, B2B buyers should be aware of their lower efficiency due to the sliding contact between the worm and the wheel. Proper lubrication is essential for maintaining performance and extending the lifespan of these gears.
Why Are Planetary Gears Preferred in High-Performance Mechanisms?
Planetary gears consist of a central sun gear with multiple planet gears orbiting around it. This configuration allows for a compact design and high efficiency, making them ideal for applications in automotive transmissions and robotics. B2B buyers should consider the complexity of planetary gear systems, as they can require intricate assembly and maintenance. However, their ability to handle high loads and provide variable gear ratios makes them a valuable choice for demanding applications.
Key Industrial Applications of types of gears
Industry/Sector | Specific Application of types of gears | Value/Benefit for the Business | Key Sourcing Considerations for this Application |
---|---|---|---|
Manufacturing | Gear Drives in Conveyor Systems | Enhanced efficiency in material handling processes | Durability, load capacity, and compatibility with existing systems |
Automotive | Transmission Systems in Vehicles | Improved fuel efficiency and performance | Precision engineering, weight reduction, and compliance with industry standards |
Oil & Gas | Pumping Systems and Drill Rigs | Reliable operation under extreme conditions | Resistance to corrosion, high torque capacity, and maintenance requirements |
Renewable Energy | Gearboxes in Wind Turbines | Increased energy conversion efficiency | Reliability, performance in variable conditions, and availability of spare parts |
Robotics | Motion Control in Robotic Arms | Enhanced precision and repeatability in operations | Customization options, weight, and material considerations |
How are types of gears used in manufacturing, and what problems do they solve?
In the manufacturing sector, types of gears are crucial in gear drives for conveyor systems. These systems facilitate the efficient movement of materials, significantly reducing manual handling and increasing throughput. By employing durable and high-capacity gears, manufacturers can prevent breakdowns and ensure continuous operation. International buyers should focus on sourcing gears that meet rigorous durability standards and are compatible with their existing machinery to avoid costly retrofits.
What role do gears play in automotive transmission systems?
In the automotive industry, gears are essential components of transmission systems, where they facilitate the transfer of power from the engine to the wheels. High-quality helical and bevel gears are commonly used to enhance fuel efficiency and overall vehicle performance. For B2B buyers, sourcing precision-engineered gears that meet industry standards is vital, as they contribute to the vehicle’s longevity and reliability. Additionally, considerations for weight reduction can lead to better fuel economy.
How are gears utilized in oil and gas applications?
In the oil and gas sector, types of gears are extensively utilized in pumping systems and drill rigs. These applications require gears that can operate reliably under extreme environmental conditions, including high temperatures and corrosive substances. By sourcing gears with high torque capacity and resistance to corrosion, companies can ensure the long-term functionality of their equipment. International buyers must also consider maintenance requirements and the availability of replacement parts to minimize downtime.
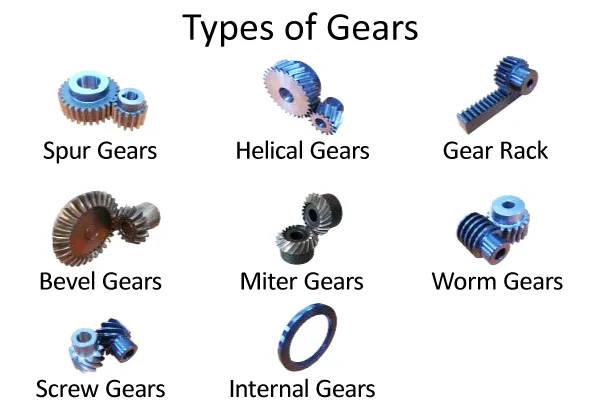
A stock image related to types of gears.
What benefits do gears provide in renewable energy systems?
Gears are integral to the operation of gearboxes in wind turbines, where they convert rotational energy from the blades into electrical energy. Efficient gear systems significantly enhance energy conversion rates, making them essential for maximizing output in renewable energy applications. Buyers in this sector should prioritize sourcing reliable and efficient gear systems that can perform well under variable environmental conditions, ensuring consistent energy production.
How do gears contribute to robotics?
In robotics, types of gears play a vital role in motion control for robotic arms. The precision and repeatability offered by high-quality gears enable robots to perform intricate tasks with accuracy. For B2B buyers, selecting gears that can be customized to fit specific applications is crucial, as is considering factors such as weight and material to optimize performance. Ensuring that sourced gears meet industry standards will enhance the operational efficiency of robotic systems.
3 Common User Pain Points for ‘types of gears’ & Their Solutions
Scenario 1: Misalignment in Gear Selection Leading to Operational Inefficiencies
The Problem: Many B2B buyers, particularly in manufacturing sectors across Africa and South America, face significant challenges when selecting the appropriate type of gear for their machinery. Misalignment in gear selection can lead to operational inefficiencies, increased wear and tear, and ultimately, costly downtimes. Buyers often struggle with understanding the nuances between different gear types, such as spur, helical, and bevel gears, and how these differences can impact their specific applications.
The Solution: To overcome this challenge, buyers should invest time in understanding the specific requirements of their machinery and the applications they are designed for. Start by conducting a thorough analysis of your operational needs, including torque requirements, speed, and load conditions. Utilize comprehensive gear catalogs and consult with reputable gear manufacturers who can provide insights into the most suitable gear types for your applications. Consider leveraging online gear selection tools that allow you to input your specific parameters to receive tailored recommendations. This proactive approach not only minimizes the risk of selecting the wrong gear type but also enhances operational efficiency and longevity of machinery.
Scenario 2: Inadequate Understanding of Gear Specifications and Standards
The Problem: International B2B buyers often encounter confusion regarding gear specifications and standards, such as ISO, AGMA, and DIN ratings. This lack of understanding can lead to purchasing gears that do not meet quality or performance expectations, resulting in mechanical failures or suboptimal performance. For instance, a buyer in the Middle East may purchase a set of gears without fully comprehending the implications of precision grades, which can directly affect the functionality of their systems.
The Solution: To address this pain point, buyers should prioritize educating themselves on the relevant specifications and standards that govern gear manufacturing and performance. It is advisable to request detailed technical documentation and material specifications from suppliers before making a purchase. Additionally, engaging with industry experts or consultants who specialize in gear technology can provide invaluable insights. Buyers should also consider establishing long-term relationships with suppliers who demonstrate a commitment to quality and compliance with international standards. This knowledge and these relationships will empower buyers to make informed decisions, ensuring that the gears they procure align with their operational needs and quality expectations.
Scenario 3: Difficulty in Sourcing Custom Gears for Specialized Applications
The Problem: In specialized industries, such as automotive or aerospace, B2B buyers often face challenges in sourcing custom gears that meet unique specifications. For instance, a company in Europe may require gears that are tailored to fit specific machinery designs, but standard stock options do not suffice. This can lead to delays in production schedules and increased costs if custom solutions are not readily available.
The Solution: To effectively address this sourcing challenge, buyers should adopt a proactive approach by collaborating with manufacturers that offer custom gear solutions. Begin by clearly defining your gear specifications, including dimensions, material requirements, and performance criteria. Reach out to manufacturers that specialize in custom gear fabrication and request prototypes or samples to evaluate compatibility with your applications. Establishing a clear communication line with the manufacturer about your needs and timelines will facilitate a smoother production process. Additionally, consider leveraging local suppliers who may have a better understanding of regional requirements and quicker turnaround times. By focusing on customization and building strong supplier relationships, buyers can ensure they have the right gears for their specialized applications without incurring unnecessary delays or costs.
Strategic Material Selection Guide for types of gears
What Are the Key Properties of Common Gear Materials?
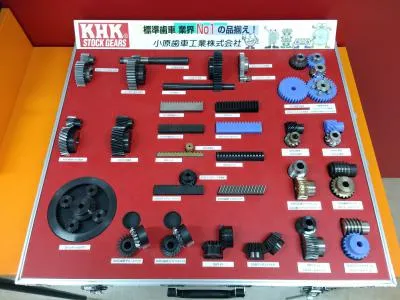
A stock image related to types of gears.
When selecting materials for gears, it is essential to consider their properties, which directly influence performance, durability, and application suitability. Here, we analyze four common materials used in gear manufacturing: steel, aluminum, plastic, and bronze.
How Does Steel Compare as a Gear Material?
Key Properties: Steel is renowned for its high strength and hardness, making it suitable for high-load applications. It typically has a temperature rating of up to 300°C and excellent wear resistance. Corrosion resistance can be enhanced through coatings or alloying.
Pros & Cons: Steel gears are highly durable and can withstand high torque and pressure, making them ideal for heavy machinery. However, they are relatively heavy and can be costly to manufacture, especially when precision machining is required. The complexity of processing steel can also lead to longer lead times.
Impact on Application: Steel gears are commonly used in automotive, aerospace, and industrial applications where high strength and durability are paramount. They are compatible with various media, including oils and lubricants, which are essential for maintaining performance.
Considerations for International Buyers: Buyers from regions such as Africa and South America should consider local availability and compliance with international standards such as ASTM and DIN. In the Middle East, where high temperatures are common, selecting heat-treated steel may be beneficial.
What Advantages Does Aluminum Offer for Gear Manufacturing?
Key Properties: Aluminum is lightweight, with good corrosion resistance and a temperature rating of around 150°C. It has a lower density than steel, which can be advantageous in applications where weight is a critical factor.
Pros & Cons: The primary advantage of aluminum gears is their weight, making them suitable for applications where reducing mass is essential, such as in aerospace and automotive industries. However, they are less durable than steel and can wear out more quickly under high loads, which may limit their use in heavy-duty applications.
Impact on Application: Aluminum gears are often used in lightweight machinery and equipment, particularly where high-speed operation is required. Their compatibility with various lubricants makes them versatile for different applications.
Considerations for International Buyers: Buyers in Europe and Australia may prefer aluminum gears due to their lightweight properties, especially in transportation applications. Compliance with local standards and regulations regarding aluminum alloys should also be considered.
Why Choose Plastic for Gear Applications?
Key Properties: Plastic gears are made from engineering plastics like nylon or acetal, offering good chemical resistance and a temperature rating of up to 100°C. They are lightweight and can be molded into complex shapes.
Pros & Cons: The main advantage of plastic gears is their low weight and noise-dampening properties, making them suitable for consumer products and applications requiring quiet operation. However, they have lower load-bearing capacities and may not withstand high temperatures or heavy loads.
Impact on Application: Plastic gears are ideal for applications in the consumer electronics and automotive industries, where noise reduction and weight savings are crucial. They are also resistant to corrosion, making them suitable for humid or chemically aggressive environments.
Considerations for International Buyers: Buyers in South America and the Middle East should evaluate the specific plastic types available in their regions, as well as compliance with international standards like ISO for engineering plastics.
What Role Does Bronze Play in Gear Manufacturing?
Key Properties: Bronze is a copper alloy known for its excellent wear resistance and ability to withstand high temperatures (up to 300°C). It offers good corrosion resistance, particularly in marine environments.
Pros & Cons: Bronze gears are highly durable and can operate in harsh conditions, making them suitable for applications in marine and heavy machinery. However, they are more expensive than steel and aluminum, which can be a drawback for cost-sensitive projects.
Impact on Application: Bronze gears are often used in applications requiring high strength and resistance to wear, such as in pumps and marine equipment. Their compatibility with various lubricants enhances their performance in demanding environments.
Considerations for International Buyers: International buyers, particularly in Europe and the Middle East, should consider the higher costs associated with bronze gears. Compliance with standards such as ASTM for bronze alloys is also crucial.
Summary Table of Gear Materials
Material | Typical Use Case for types of gears | Key Advantage | Key Disadvantage/Limitation | Relative Cost (Low/Med/High) |
---|---|---|---|---|
Steel | Heavy machinery, automotive | High strength and durability | Heavy and costly to manufacture | High |
Aluminum | Aerospace, automotive | Lightweight and corrosion-resistant | Less durable under high loads | Medium |
Plastic | Consumer electronics, automotive | Low weight and noise-dampening | Lower load-bearing capacity | Low |
Bronze | Marine equipment, pumps | Excellent wear resistance | Higher cost than other materials | High |
This strategic material selection guide provides international B2B buyers with insights to make informed decisions based on material properties, application suitability, and compliance with regional standards.
In-depth Look: Manufacturing Processes and Quality Assurance for types of gears
What Are the Main Stages in Manufacturing Gears?
Manufacturing gears involves several critical stages that ensure high-quality production and performance. Understanding these processes is essential for B2B buyers looking to make informed purchasing decisions.
Material Preparation for Gear Manufacturing
The initial stage in gear manufacturing is material preparation. Common materials used for gears include steel, aluminum, brass, and engineering plastics. The choice of material affects the gear’s performance, durability, and cost.
- Material Selection: Buyers should prioritize materials that suit their application, considering factors like strength, wear resistance, and environmental conditions.
- Material Processing: Raw materials may undergo processes such as annealing or hardening to enhance their mechanical properties before they are shaped.
What Key Techniques Are Used for Gear Forming?
Once materials are prepared, they undergo forming processes to achieve the desired shape and specifications.
-
Machining: This is the most common method for creating precision gears. Techniques include:
– Hobbing: A machining process that cuts the gear teeth using a rotating hob.
– Shaping: Involves the use of a shaping machine to produce gear teeth through linear motion.
– Broaching: A method that uses a toothed tool to remove material and create gear profiles. -
Casting: For larger gears, casting techniques such as sand casting or die casting are used. This method is cost-effective for mass production but may require additional finishing.
-
Forging: This process enhances the material’s strength by shaping it under high pressure and temperature, making it suitable for high-load applications.
-
Additive Manufacturing: Increasingly, 3D printing is being utilized for creating complex gear designs that traditional methods cannot easily achieve.
How Is Gear Assembly Done?
After forming, gears may need to be assembled with other components, such as shafts or housings. This stage may involve:
- Fitting: Ensuring that parts fit together correctly to avoid misalignment, which can lead to premature wear.
- Lubrication: Applying grease or oil to reduce friction and enhance performance.
- Testing Assembly: Conducting initial tests to ensure that the gear operates smoothly within its intended assembly.
What Finishing Processes Are Important for Gears?
Finishing processes enhance the surface quality and overall performance of gears.
- Grinding: This process refines the gear teeth, ensuring precise dimensions and a smooth finish, which is crucial for high-speed applications.
- Heat Treatment: Techniques like carburizing or quenching improve hardness and wear resistance, increasing the gear’s lifespan.
- Coating: Applying protective coatings can prevent corrosion and reduce friction.
What Are the Quality Assurance Standards for Gear Manufacturing?
Quality assurance is critical in ensuring that gears meet international standards and customer specifications. Buyers should be aware of the following standards and practices.
Which International Standards Should B2B Buyers Consider?
- ISO 9001: This standard focuses on quality management systems, ensuring that manufacturers consistently meet customer and regulatory requirements.
- CE Marking: For gears sold in the European market, CE marking indicates compliance with EU safety and environmental requirements.
- API Standards: Particularly relevant for gears used in the oil and gas industry, API standards ensure that equipment meets rigorous safety and reliability requirements.
What Are the QC Checkpoints in Gear Manufacturing?
Quality control checkpoints are essential to maintain high standards throughout the manufacturing process.
- Incoming Quality Control (IQC): This involves inspecting raw materials upon arrival to ensure they meet specified standards.
- In-Process Quality Control (IPQC): Regular checks during the manufacturing process help identify defects early and maintain quality.
- Final Quality Control (FQC): A thorough inspection of finished gears ensures they meet all specifications and performance criteria.
How Can B2B Buyers Verify Supplier Quality Control?
B2B buyers should implement strategies to verify and validate the quality control processes of their suppliers.
- Supplier Audits: Conducting on-site audits allows buyers to assess the manufacturer’s quality control systems and processes directly.
- Quality Reports: Requesting detailed QC reports and certificates can provide insights into the manufacturing processes and any testing conducted.
- Third-Party Inspections: Engaging third-party inspection services can offer an unbiased evaluation of the manufacturer’s quality assurance practices.
What Are the Common Testing Methods Used in Gear Quality Control?
Testing methods are crucial in confirming that gears will perform reliably in their applications.
- Dimensional Inspection: Using tools like calipers and micrometers, manufacturers ensure that gears meet precise dimensional specifications.
- Load Testing: This method assesses how gears perform under various load conditions, identifying any potential failure points.
- Noise and Vibration Testing: Gears should operate smoothly and quietly; testing helps detect any anomalies that could indicate future issues.
What Are the QC and Certification Nuances for International Buyers?
Understanding the nuances of quality control and certification is vital for international B2B buyers, particularly in regions like Africa, South America, the Middle East, and Europe.
- Regulatory Compliance: Buyers must ensure that the gears comply with local regulations, which may differ from international standards.
- Cultural Considerations: Different regions may have varying expectations regarding quality and certification, impacting purchasing decisions.
- Documentation: Buyers should require comprehensive documentation, including material certifications and test reports, to facilitate smooth importation and compliance with local laws.
Conclusion
For international B2B buyers, particularly those in Africa, South America, the Middle East, and Europe, understanding the manufacturing processes and quality assurance measures for gears is crucial for making informed purchasing decisions. By focusing on material selection, manufacturing techniques, quality standards, and verification methods, buyers can ensure that they source high-quality gears that meet their operational needs.
Practical Sourcing Guide: A Step-by-Step Checklist for ‘types of gears’
To assist international B2B buyers in successfully procuring various types of gears, this practical sourcing guide outlines essential steps to follow. Understanding the intricacies of gear selection and supplier evaluation can significantly impact the efficiency and effectiveness of mechanical designs. This checklist serves as a comprehensive resource for buyers, particularly from Africa, South America, the Middle East, and Europe.
Step 1: Define Your Technical Specifications
Clearly outline the specific technical requirements for the gears you need. Consider factors such as gear type (spur, helical, bevel, etc.), dimensions (module, number of teeth, etc.), and performance standards (ISO, AGMA). This clarity will guide your sourcing process and ensure that you select gears that meet your operational needs.
- Gear Type: Identify the type of gear that aligns with your machinery.
- Performance Standards: Ensure compliance with relevant industry standards to avoid future operational issues.
Step 2: Research Potential Suppliers
Conduct thorough research on potential suppliers who specialize in the types of gears you require. Look for manufacturers that have a solid reputation and a track record of delivering quality products. Utilize online directories, industry forums, and trade shows to gather information about suppliers.
- Market Presence: Evaluate how long the supplier has been in business and their market reach.
- Product Range: Ensure they offer the specific gear types you need.
Step 3: Evaluate Supplier Certifications
Before finalizing any procurement, verify the certifications of your potential suppliers. Look for ISO certifications or other relevant industry standards that demonstrate their commitment to quality and safety. This step is crucial for mitigating risks associated with subpar products.
- Quality Assurance: Ensure the supplier has a quality management system in place.
- Compliance: Check for compliance with local and international regulations.
Step 4: Request Samples and Prototypes
Before making a bulk purchase, request samples or prototypes of the gears. This allows you to assess the quality, fit, and performance of the products in your specific applications. Testing these samples can save you from costly mistakes later on.
- Performance Testing: Evaluate the samples under operational conditions.
- Fit and Compatibility: Ensure the gears mesh well with your existing machinery.
Step 5: Analyze Pricing and Terms
Collect detailed quotes from multiple suppliers and analyze their pricing structures. Look beyond just the initial cost; consider factors such as shipping fees, payment terms, and warranty policies. Understanding the total cost of ownership will help you make an informed decision.
- Total Cost of Ownership: Factor in maintenance, shipping, and potential downtime costs.
- Negotiation: Be prepared to negotiate terms that align with your budget and needs.
Step 6: Check References and Customer Feedback
Always ask for references and seek feedback from previous customers of the suppliers you are considering. This can provide insights into the reliability of the supplier, their customer service, and the overall satisfaction of their clients.
- Industry Relevance: Focus on references from companies in your industry.
- Long-term Relationships: Assess how the supplier has handled long-term relationships and support.
Step 7: Finalize Your Supplier and Place Your Order
Once you have completed the evaluation process and feel confident in your choice, finalize the supplier agreement. Ensure that all terms are clearly outlined in the contract, including delivery timelines, payment schedules, and quality assurance measures.
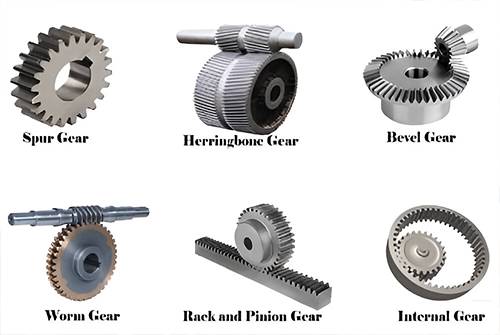
A stock image related to types of gears.
- Contract Clarity: Ensure all aspects of the agreement are understood and documented.
- Follow-up: Establish a follow-up process for tracking order status and addressing any issues that may arise.
By following these steps, B2B buyers can navigate the complexities of sourcing gears effectively, ensuring they choose the right products and suppliers for their mechanical applications.
Comprehensive Cost and Pricing Analysis for types of gears Sourcing
What Are the Key Cost Components in Gear Sourcing?
When sourcing gears, international B2B buyers must understand the various cost components that influence pricing. The main components include:
-
Materials: The choice of materials greatly affects the cost. Common materials include carbon steel, stainless steel, and engineering plastics. Specialty materials or high-performance alloys can further increase costs.
-
Labor: Labor costs vary by region and manufacturing complexity. Skilled labor for precision machining and assembly may demand higher wages, influencing overall pricing.
-
Manufacturing Overhead: This includes costs related to facility maintenance, utilities, and equipment depreciation. Efficient manufacturing processes can help reduce overhead costs.
-
Tooling: Initial tooling costs can be significant, especially for custom or high-volume orders. This includes the creation of molds, dies, and specialized machinery.
-
Quality Control (QC): Implementing stringent QC measures is essential for ensuring product reliability. Costs associated with testing and certification can add to the overall price.
-
Logistics: Shipping and handling costs, including customs duties and taxes, can significantly impact pricing, especially for international transactions.
-
Margin: Supplier profit margins also play a role in pricing. Margins can vary based on the supplier’s market positioning and the competitive landscape.
How Do Price Influencers Affect Gear Pricing?
Several factors can influence the final price of gears, particularly for international buyers:
-
Volume and Minimum Order Quantity (MOQ): Larger orders often attract discounts. Understanding MOQ is crucial for cost-effective purchasing.
-
Specifications and Customization: Custom gears tailored to specific applications generally come at a premium. Buyers should assess whether standard products can meet their needs to avoid unnecessary costs.
-
Materials and Quality Certifications: Higher quality materials and certifications (ISO, AGMA) can increase costs but may provide better durability and performance, justifying the investment.
-
Supplier Factors: The reputation, reliability, and location of suppliers can influence pricing. Established suppliers may charge more due to their perceived quality and service.
-
Incoterms: Understanding Incoterms is vital for international transactions. Terms like FOB (Free on Board) or CIF (Cost, Insurance, and Freight) determine who is responsible for shipping costs and risks, affecting the total landed cost.
What Are the Best Buyer Tips for Cost-Efficiency in Gear Sourcing?
To maximize cost-efficiency when sourcing gears, international B2B buyers should consider the following strategies:
-
Negotiate Terms: Leverage volume purchases to negotiate better terms and prices. Building a long-term relationship with suppliers can also lead to favorable pricing.
-
Evaluate Total Cost of Ownership (TCO): Consider not only the upfront cost but also the long-term costs associated with maintenance, downtime, and potential failures. Investing in higher-quality gears may reduce TCO over time.
-
Understand Pricing Nuances for International Purchases: Be aware of currency fluctuations, tariffs, and trade agreements that can impact costs when sourcing from different regions.
-
Request Detailed Quotations: Ensure suppliers provide transparent breakdowns of costs, including materials, labor, and logistics. This clarity can help in comparing offers and making informed decisions.
-
Stay Informed on Market Trends: Keep an eye on market conditions and material costs, as these can fluctuate based on demand, availability, and geopolitical factors.
Disclaimer on Indicative Prices
Pricing for gears can vary widely based on the factors mentioned above. It is essential for buyers to conduct thorough market research and obtain multiple quotes to ensure they receive competitive pricing tailored to their specific requirements.
Alternatives Analysis: Comparing types of gears With Other Solutions
Introduction to Alternatives for Gear Solutions
In the realm of mechanical engineering and design, gears play a pivotal role in transmitting power and controlling motion. However, there are alternative solutions that can achieve similar objectives, offering unique benefits and considerations. This section explores these alternatives, providing B2B buyers with insights to make informed decisions based on their specific operational needs.
Comparison Table of Gear Types and Alternatives
Comparison Aspect | Types of Gears | Alternative 1: Belt Drives | Alternative 2: Chain Drives |
---|---|---|---|
Performance | High efficiency, excellent load capacity, and precise motion control. | Good for moderate loads; can slip under heavy loads. | Very efficient for high loads, less precise than gears. |
Cost | Higher initial investment; requires specialized materials. | Generally lower cost; minimal maintenance. | Moderate cost; may require more frequent maintenance. |
Ease of Implementation | Complex assembly requiring precise alignment. | Simple installation and adjustment. | Requires precise alignment but generally straightforward. |
Maintenance | Regular lubrication needed; potential for wear. | Minimal maintenance; occasional belt replacement. | Requires regular lubrication; may stretch over time. |
Best Use Case | High precision applications like robotics and automotive. | Ideal for moderate-speed applications like conveyors. | Best for heavy-duty applications like motorcycles and industrial machinery. |
Detailed Breakdown of Alternatives
What Are the Benefits and Drawbacks of Belt Drives?
Belt drives utilize flexible belts to transmit power between shafts. They are often preferred for applications where noise reduction and ease of installation are priorities. While they are cost-effective and require less maintenance than gears, they may not perform well under heavy loads, as belts can slip, leading to inefficiencies. For B2B buyers in sectors such as material handling or manufacturing, belt drives can be an attractive alternative for moderate-speed applications where precision is less critical.
How Do Chain Drives Compare to Gear Solutions?
Chain drives employ a series of interconnected links to transfer power, making them suitable for high-load applications. They offer a balance between efficiency and durability, often used in heavy machinery, bicycles, and motorcycles. However, chain drives require regular lubrication and can stretch over time, necessitating maintenance. For buyers in industries like automotive or heavy equipment, chain drives can provide robust performance where high torque is essential, albeit with less precision than gears.
Conclusion: Choosing the Right Solution for Your Needs
Selecting the appropriate power transmission solution hinges on understanding the specific requirements of your application. Gears excel in high-precision environments, while belt and chain drives offer viable alternatives for cost-sensitive or less demanding applications. B2B buyers should assess factors such as performance needs, budget constraints, and maintenance capabilities to determine the most effective solution for their operations. By carefully weighing these alternatives, businesses can optimize their mechanical systems for efficiency and reliability.
Essential Technical Properties and Trade Terminology for types of gears
What Are the Essential Technical Properties of Gears?
Understanding the technical properties of gears is crucial for B2B buyers, particularly those involved in machinery manufacturing or mechanical engineering. Here are some critical specifications to consider:
1. Material Grade
The material used in gear manufacturing significantly affects its performance and durability. Common materials include steel, cast iron, and engineering plastics. Steel gears, for instance, are preferred for their strength and ability to withstand high loads, while plastic gears may be chosen for their lightweight and corrosion resistance. Selecting the appropriate material grade can enhance the longevity and reliability of the gears in various applications.
2. Tolerance
Tolerance refers to the allowable variation in the dimensions of gear teeth. High precision in manufacturing ensures that gears mesh correctly, which is vital for reducing noise and wear. Tight tolerances are essential in applications requiring high-speed operations or heavy loads. For international buyers, understanding the tolerance standards (like ISO or AGMA) is crucial for ensuring compatibility and performance in their specific applications.
3. Module
The module is a metric measurement that indicates the size of the gear teeth. It is defined as the ratio of the pitch diameter to the number of teeth. A suitable module choice ensures efficient power transmission and minimizes wear. Buyers should assess the module when selecting gears for specific applications to match the existing machinery or design requirements.
4. Face Width
Face width is the width of the gear tooth, which influences the gear’s load-bearing capacity. A wider face can distribute the load more evenly, enhancing performance and durability. Understanding the face width is essential for buyers looking to optimize gear performance in applications involving high torque or load.
5. Helix Angle
The helix angle is a critical factor for helical gears, influencing how the gears engage and transmit power. A higher helix angle can improve load distribution and reduce noise but may also increase axial thrust. Buyers should consider the helix angle when selecting gears for applications requiring smooth operation and high efficiency.
What Are Common Trade Terms Used in Gear Procurement?
Familiarizing oneself with industry terminology can streamline the procurement process and enhance communication between buyers and suppliers. Here are some essential terms:
1. OEM (Original Equipment Manufacturer)
An OEM refers to a company that produces parts or equipment that may be marketed by another manufacturer. In the gear industry, working with OEMs ensures that the gears meet specific standards and compatibility requirements for end products.
2. MOQ (Minimum Order Quantity)
MOQ is the smallest quantity of a product that a supplier is willing to sell. Understanding the MOQ is vital for buyers, especially when evaluating suppliers’ capabilities and planning inventory levels.
3. RFQ (Request for Quotation)
An RFQ is a document issued by buyers to solicit price quotes from suppliers for specific products. Including detailed specifications in an RFQ ensures that suppliers provide accurate pricing and lead times, facilitating informed decision-making.
4. Incoterms (International Commercial Terms)
Incoterms are a set of international rules that define the responsibilities of buyers and sellers in the shipping process. Understanding these terms helps buyers manage logistics and shipping costs effectively, ensuring clarity in delivery obligations.
5. Lead Time
Lead time refers to the period between placing an order and receiving the goods. For international buyers, understanding lead times is crucial for inventory management and production scheduling, especially when dealing with cross-border logistics.
By grasping these essential technical properties and trade terminologies, international B2B buyers can make informed decisions when sourcing gears, ultimately enhancing their operational efficiency and product quality.
Navigating Market Dynamics and Sourcing Trends in the types of gears Sector
What Are the Current Market Trends Impacting the Types of Gears Sector?
The global market for gears is undergoing significant transformation driven by technological advancements, increasing automation, and the demand for energy-efficient solutions. Key trends include the integration of Industry 4.0 technologies, such as IoT and AI, which enable predictive maintenance and enhance operational efficiency. For international B2B buyers from Africa, South America, the Middle East, and Europe, understanding these trends is crucial for making informed sourcing decisions.
Emerging markets are witnessing a surge in demand for high-precision gears, particularly in sectors like automotive, aerospace, and manufacturing. The shift towards electric vehicles (EVs) is also influencing gear design, with a growing emphasis on lightweight materials and compact gear systems. Moreover, the increasing focus on sustainability is prompting manufacturers to innovate by utilizing advanced materials and production methods that reduce environmental impact.
Market dynamics are further shaped by geopolitical factors and trade policies, especially for buyers in regions like the Middle East and Europe, where supply chain stability can be affected by international relations. To navigate these complexities, B2B buyers should prioritize suppliers that demonstrate flexibility and resilience in their supply chains while also keeping abreast of regional regulations and standards.
How Is Sustainability Influencing Sourcing Decisions in the Types of Gears Sector?
Sustainability is becoming a cornerstone of sourcing strategies in the gears sector, driven by both regulatory pressures and consumer demand for environmentally responsible products. The environmental impact of gear production is significant, particularly in terms of energy consumption and waste generation. As a result, B2B buyers are increasingly prioritizing suppliers that adhere to sustainable practices and offer ‘green’ certifications.
Ethical sourcing is essential in ensuring that the materials used in gear production are obtained responsibly. This includes sourcing metals and plastics from suppliers that follow environmentally friendly extraction and manufacturing processes. Additionally, buyers should seek out manufacturers that utilize recycled materials or bio-based alternatives in their gear production.
The adoption of sustainability certifications, such as ISO 14001 (Environmental Management) and ISO 50001 (Energy Management), can serve as indicators of a supplier’s commitment to reducing environmental impact. By choosing suppliers with these certifications, B2B buyers can enhance their own sustainability profiles while contributing to the broader goal of reducing the carbon footprint associated with industrial operations.
How Has the Types of Gears Sector Evolved Over Time?
The evolution of the gears sector can be traced back to the Industrial Revolution, when gears were first mechanized to facilitate the efficient transfer of power in machinery. Initially, gears were made from wood and later transitioned to metals, significantly enhancing durability and performance. The 20th century saw advancements in gear design and manufacturing techniques, leading to the creation of specialized gear types such as helical, bevel, and worm gears, each serving distinct applications.
In recent decades, the focus has shifted towards precision engineering and the integration of computer-aided design (CAD) technologies, allowing for more complex gear geometries and improved performance metrics. As industries evolve, the types of gears continue to adapt, particularly in response to the demands of automation and renewable energy technologies.
This historical context is essential for B2B buyers as it highlights the importance of innovation and adaptability in selecting gear suppliers. Understanding the evolution of gears can inform purchasing decisions and encourage partnerships with manufacturers who prioritize research and development to stay ahead in a competitive marketplace.
Frequently Asked Questions (FAQs) for B2B Buyers of types of gears
-
1. How do I select the right type of gear for my application?
Selecting the appropriate gear type depends on various factors, including the application requirements, load capacity, speed, and space constraints. Begin by identifying the torque and speed needed for your machinery. For high-load applications, consider helical or bevel gears for their strength and efficiency. If space is limited, worm gears might be suitable. Always evaluate the environment where the gears will operate, as factors like temperature and humidity can affect material choice. Additionally, consult with suppliers for their technical expertise to ensure optimal gear selection. -
2. What are the key specifications to consider when sourcing gears?
When sourcing gears, focus on specifications such as material, size (module, number of teeth), precision grade (ISO, AGMA, DIN), and operational efficiency. Determine the required torque capacity and load conditions to ensure the gears meet your performance needs. Don’t overlook the necessity for heat treatment or grinding based on your application. Additionally, consider the gear’s design—whether spur, helical, or bevel—as this will affect performance and compatibility with existing systems. Request detailed technical documentation from suppliers to assess compliance with your requirements. -
3. How can I ensure the quality of gears from international suppliers?
To ensure quality from international suppliers, start by verifying their certifications (e.g., ISO 9001) and production processes. Request samples for testing before placing larger orders. It’s also beneficial to check reviews and testimonials from other customers, particularly those in your industry. Establish clear quality assurance standards in your contracts, including tolerances and performance criteria. Regular communication and site visits can help maintain oversight and foster a better understanding of the supplier’s capabilities. -
4. What are the minimum order quantities (MOQs) for gears, and how do they vary by supplier?
Minimum order quantities (MOQs) for gears can vary widely depending on the supplier and the type of gear. Generally, standard gears may have lower MOQs, while customized or specialized gears will often require larger orders due to setup costs. Discuss your needs directly with suppliers to negotiate MOQs that align with your production requirements. Some suppliers may offer flexibility for first orders or trial runs, especially if you’re exploring a long-term partnership. -
5. What payment terms should I expect when sourcing gears internationally?
Payment terms for international gear sourcing typically vary by supplier and region. Common arrangements include advance payment, net 30/60/90 days, or a letter of credit for larger orders. Be prepared to negotiate terms based on your purchasing volume and relationship with the supplier. Ensure that payment terms are clearly outlined in your contracts to avoid misunderstandings. Additionally, consider the currency fluctuations and transaction fees associated with international payments. -
6. How do I handle logistics and shipping for gears sourced from overseas?
Handling logistics for international gear procurement involves selecting reliable freight forwarders and understanding shipping regulations. Determine the most cost-effective shipping method (air, sea, or land) based on your timeline and budget. Ensure that your supplier is familiar with the necessary export documentation, such as bills of lading and customs declarations. Additionally, consider insurance for valuable shipments. Establish clear communication channels with your logistics provider to track shipments and address any potential issues promptly. -
7. Can gears be customized to meet specific application needs?
Yes, many suppliers offer customization options for gears to meet specific application requirements. Customization may include alterations in size, tooth design, material selection, and surface treatment. When discussing your needs with suppliers, provide detailed specifications and application context to facilitate the design process. Keep in mind that customized gears may involve longer lead times and higher costs, so it’s essential to balance customization needs with your budget and timelines. -
8. What are the common applications for different types of gears in industry?
Different types of gears serve various applications across industries. Spur gears are commonly used in simple mechanical devices for speed reduction. Helical gears are prevalent in high-speed applications due to their smooth operation. Bevel gears are ideal for changing the direction of power transmission in machinery. Worm gears are often utilized in applications requiring high torque at low speeds, such as conveyor systems. Understanding the application of each gear type will help you make informed purchasing decisions that enhance operational efficiency.
Important Disclaimer & Terms of Use
⚠️ Important Disclaimer
The information provided in this guide, including content regarding manufacturers, technical specifications, and market analysis, is for informational and educational purposes only. It does not constitute professional procurement advice, financial advice, or legal advice.
While we have made every effort to ensure the accuracy and timeliness of the information, we are not responsible for any errors, omissions, or outdated information. Market conditions, company details, and technical standards are subject to change.
B2B buyers must conduct their own independent and thorough due diligence before making any purchasing decisions. This includes contacting suppliers directly, verifying certifications, requesting samples, and seeking professional consultation. The risk of relying on any information in this guide is borne solely by the reader.
Strategic Sourcing Conclusion and Outlook for types of gears
As international B2B buyers navigate the complex landscape of gear types, it is essential to understand the strategic importance of sourcing the right components for specific applications. Different gears, including spur, helical, bevel, and worm gears, offer unique advantages in terms of efficiency, load capacity, and operational noise. Recognizing these differences enables businesses to optimize their mechanical designs, ensuring reliable performance and longevity.
Strategic sourcing is not just about finding the lowest price; it encompasses selecting suppliers who provide high-quality products that meet international standards. Buyers from regions such as Africa, South America, the Middle East, and Europe should prioritize suppliers that demonstrate a commitment to innovation, quality assurance, and sustainability. This approach not only enhances operational efficiency but also fosters long-term partnerships that can adapt to evolving technological demands.
Looking ahead, the global demand for precision-engineered gears will continue to rise as industries expand and modernize. Buyers are encouraged to leverage this opportunity by engaging with suppliers who offer advanced solutions tailored to their specific needs. By prioritizing strategic sourcing practices, companies can position themselves for success in an increasingly competitive marketplace.