Improve Efficiency: The Complete Ball Check Valve Guide (2025)
Introduction: Navigating the Global Market for ball check valve
In today’s rapidly evolving industrial landscape, sourcing reliable ball check valves presents a significant challenge for international B2B buyers. These essential components play a critical role in preventing backflow in various applications, from wastewater management to HVAC systems. Understanding the nuances of ball check valves—such as their construction, functionality, and appropriate usage—is vital for making informed purchasing decisions. This comprehensive guide will explore the different types of ball check valves, their diverse applications, and key factors for supplier vetting.
International buyers, particularly from Africa, South America, the Middle East, and Europe, will benefit from actionable insights into the cost considerations and performance metrics of these valves. The guide will also address common concerns such as maintenance requirements and potential noise issues, ensuring that buyers can select the right products for their specific needs. By providing a detailed analysis of market trends and supplier options, this guide empowers businesses to navigate the global market effectively, mitigating risks associated with subpar products and service providers.
With the right knowledge and strategies, B2B buyers can enhance operational efficiency and reliability within their systems. As we delve deeper into the world of ball check valves, you will gain the expertise needed to make strategic purchasing decisions that align with your business objectives.
Understanding ball check valve Types and Variations
Type Name | Key Distinguishing Features | Primary B2B Applications | Brief Pros & Cons for Buyers |
---|---|---|---|
Standard Ball Check Valve | Freely floating ball, seals against a machined seat | Water treatment, irrigation | Pros: Simple design, minimal maintenance. Cons: Limited pressure range. |
Floating Ball Check Valve | Designed for vacuum applications, ball remains buoyant | Wastewater treatment, chemical processing | Pros: Effective for low-pressure scenarios. Cons: Requires careful installation. |
True Union Ball Check Valve | Removable housing for easy maintenance and inspection | Industrial piping, HVAC systems | Pros: Simplifies repair and replacement. Cons: Higher initial cost. |
Corrosion-Resistant Ball Check Valve | Constructed with materials that withstand harsh environments | Oil and gas, mining | Pros: Extended lifespan in corrosive applications. Cons: Heavier and potentially more expensive. |
Compact Ball Check Valve | Smaller footprint, ideal for space-constrained applications | Residential plumbing, small machinery | Pros: Space-efficient design. Cons: Limited flow capacity. |
What Are the Characteristics of a Standard Ball Check Valve?
The standard ball check valve features a ball that floats freely within the valve body, sealing against a machined seat when backflow occurs. This design allows for efficient flow in one direction and is ideal for applications such as water treatment and irrigation. When purchasing, consider the valve’s pressure rating and material compatibility with the fluid being transported, as these factors can influence performance and longevity.
How Does a Floating Ball Check Valve Work?
Floating ball check valves are specifically designed for low-pressure applications, where the ball remains buoyant and can effectively prevent backflow. Commonly used in wastewater treatment and chemical processing, these valves are advantageous in systems where vacuum conditions may arise. Buyers should assess the installation requirements and ensure that the valve’s materials are suitable for the specific media being handled.
What Are the Benefits of a True Union Ball Check Valve?
True union ball check valves feature a removable housing, making them ideal for installations requiring regular maintenance or inspection. This design is prevalent in industrial piping and HVAC systems, where ease of access is crucial. While they may come with a higher upfront cost, the long-term savings from reduced maintenance downtime make them a wise investment for many B2B applications.
Why Choose a Corrosion-Resistant Ball Check Valve?
Corrosion-resistant ball check valves are constructed from specialized materials to withstand harsh environments, making them suitable for industries such as oil and gas or mining. These valves offer an extended lifespan and reliable performance in corrosive media. Buyers should consider the specific environmental conditions and the potential impact of corrosion on valve longevity when making purchasing decisions.
What Makes a Compact Ball Check Valve Ideal for Small Spaces?
Compact ball check valves are designed for applications where space is at a premium, such as residential plumbing or small machinery. Their smaller footprint allows for flexible installation options. However, buyers should be aware of the limited flow capacity associated with these valves and ensure that they meet the system’s flow requirements before purchasing.
Key Industrial Applications of ball check valve
Industry/Sector | Specific Application of Ball Check Valve | Value/Benefit for the Business | Key Sourcing Considerations for this Application |
---|---|---|---|
Water & Wastewater | Submersible wastewater lift stations | Prevents backflow, ensuring efficient wastewater management | Material compatibility, pressure ratings, and maintenance ease |
Oil & Gas | Oil and gas pipelines | Ensures one-way flow, preventing contamination and leaks | Corrosion resistance, pressure ratings, and certification standards |
HVAC Systems | Chilled water systems | Maintains system integrity and efficiency by preventing backflow | Temperature ratings, compatibility with refrigerants, and size |
Agriculture | Irrigation systems | Protects water quality and promotes efficient water use | Material durability, flow rates, and maintenance requirements |
Food & Beverage | Processing and bottling lines | Ensures product safety by preventing contamination during processing | Compliance with food safety standards, material suitability, and ease of cleaning |
How are Ball Check Valves Used in Water & Wastewater Management?
In submersible wastewater lift stations, ball check valves are crucial for maintaining effective flow control. They prevent backflow, which can lead to contamination of clean water sources. For international buyers, especially in regions like Africa and South America, sourcing valves that can withstand varying pressures and are resistant to corrosion is essential. Additionally, ease of maintenance is a key consideration, as it impacts operational efficiency and costs.
What Role Do Ball Check Valves Play in Oil & Gas Pipelines?
Ball check valves are extensively used in oil and gas pipelines to ensure a one-way flow of fluids, preventing contamination and potential leaks. This is critical for maintaining product integrity and environmental safety. Buyers from the Middle East and Europe should prioritize valves made from corrosion-resistant materials and ensure they meet relevant industry standards to withstand harsh operational conditions.
How Do Ball Check Valves Benefit HVAC Systems?
In HVAC systems, ball check valves are utilized within chilled water systems to prevent backflow, ensuring system efficiency and integrity. They help maintain consistent pressure and temperature, which is vital for energy efficiency. Buyers in Europe and other regions should consider the compatibility of the valve materials with various refrigerants and the temperature ratings to ensure optimal performance.
In What Ways Do Ball Check Valves Enhance Agricultural Irrigation?
In agricultural irrigation systems, ball check valves protect water quality by preventing backflow, which can introduce contaminants into the water supply. This is particularly important in regions like South America and Africa, where water scarcity is a concern. Buyers should focus on the durability of materials to withstand various environmental conditions and the specific flow rates required for their irrigation systems.
Why are Ball Check Valves Important in Food & Beverage Processing?
In the food and beverage industry, ball check valves are used in processing and bottling lines to ensure product safety by preventing contamination. Compliance with food safety standards is paramount for international buyers, particularly in Europe. Sourcing considerations should include the suitability of materials for food contact, ease of cleaning, and overall maintenance requirements to ensure hygiene and efficiency in production.
3 Common User Pain Points for ‘ball check valve’ & Their Solutions
Scenario 1: Inconsistent Performance in High-Pressure Applications
The Problem: Many B2B buyers experience challenges when using ball check valves in high-pressure systems, especially in industries such as water treatment and oil and gas. The primary issue arises when the valve fails to open under high pressure due to insufficient cracking pressure, leading to flow interruptions and potential system failures. This can result in costly downtime and operational inefficiencies, creating frustration for engineers and procurement teams who rely on consistent performance.
The Solution: To mitigate this issue, it’s crucial for buyers to understand the specific cracking pressure requirements of their applications. When sourcing ball check valves, look for those with adjustable or customizable cracking pressure settings. Additionally, choose a valve made from materials that can withstand high pressures, such as stainless steel or specialized alloys. When installing the valve, ensure that it is oriented correctly and that there is no debris obstructing the seat. Regular maintenance checks should also be scheduled to identify any wear or damage that could affect performance.
Scenario 2: Backflow Contamination in Critical Systems
The Problem: In industries like pharmaceuticals, food processing, and wastewater management, backflow can lead to contamination of sensitive systems. B2B buyers often find that standard ball check valves may not provide adequate protection against backflow, especially when the pressure differentials fluctuate. This contamination risk not only poses safety hazards but can also result in regulatory non-compliance and significant financial penalties.
The Solution: To address backflow issues effectively, buyers should consider investing in ball check valves that include advanced sealing technologies or dual ball designs that enhance backflow prevention. It’s also advisable to conduct a thorough risk assessment of the system to determine the potential for backflow scenarios. Regular testing and validation of the valve’s performance under varying conditions should be part of a robust maintenance program. Collaborating with suppliers who specialize in backflow prevention can also yield tailored solutions that meet specific industry standards and regulations.
Scenario 3: Noise and Vibration Issues in Pumping Stations
The Problem: Noise and vibration generated by ball check valves can be a significant concern for B2B buyers operating pumping stations, particularly in urban or residential areas. This problem often arises due to water hammer effects or inadequate valve sizing, resulting in disruptive sounds that can lead to complaints from nearby residents or regulatory scrutiny.
The Solution: To reduce noise and vibration, buyers should ensure proper sizing and selection of ball check valves based on the specific flow rates and system pressures. Implementing a soft-closing mechanism or selecting valves designed to mitigate water hammer can significantly alleviate these issues. Additionally, consider using dampening materials or vibration isolation mounts during installation. Regularly monitoring the system for pressure fluctuations and addressing them promptly can prevent excessive noise and prolong the life of the valves, ensuring a quieter and more efficient operation.
Alternatives Analysis: Comparing ball check valve With Other Solutions
Understanding Alternatives to Ball Check Valves
In the quest for effective fluid control solutions, B2B buyers often explore various valve technologies. While ball check valves are renowned for their reliability and simplicity, understanding alternative solutions can help in making an informed decision that aligns with specific operational requirements. Below, we compare ball check valves with two viable alternatives: Swing Check Valves and Diaphragm Check Valves.
Comparison Table
Comparison Aspect | Ball Check Valve | Swing Check Valve | Diaphragm Check Valve |
---|---|---|---|
Performance | Excellent for preventing backflow; self-cleaning feature | Good for larger pipe sizes; more susceptible to backflow in low flow conditions | Effective in low-pressure applications; prevents backflow effectively |
Cost | Generally moderate cost | Typically lower initial cost | Higher initial cost due to complexity |
Ease of Implementation | Simple installation; minimal space required | Requires more space; installation can be complex | Installation may require specific fittings and expertise |
Maintenance | Virtually maintenance-free | May require regular inspection; parts may wear out | Requires periodic replacement of diaphragm, but generally low maintenance |
Best Use Case | Submersible pumps, wastewater applications | Water supply systems, large pipelines | Chemical processing, food and beverage applications |
Detailed Breakdown of Alternatives
Swing Check Valves
Swing check valves utilize a hinged disc that swings open when fluid flows in the correct direction and closes when flow reverses. This design is particularly effective in larger pipelines where flow dynamics can be more significant.
Pros:
– Cost-effective for large installations.
– Simple design with fewer parts, leading to lower manufacturing costs.
Cons:
– Not suitable for low flow conditions, as the disc may not close properly, leading to potential backflow.
– Requires more installation space compared to ball check valves, which may be a limitation in compact setups.
Diaphragm Check Valves
Diaphragm check valves use a flexible diaphragm that opens and closes to regulate flow. These valves are particularly useful in applications where backflow prevention is critical, such as in chemical processing or food and beverage industries.
Pros:
– Highly effective in low-pressure applications, providing excellent sealing capabilities.
– Suitable for a variety of fluid types, including corrosive substances.
Cons:
– Higher initial costs due to the complexity of the design.
– Requires periodic replacement of the diaphragm, which may increase long-term maintenance costs.
Conclusion: How to Choose the Right Solution for Your Needs
When selecting a valve solution, international B2B buyers should consider their specific operational requirements, including the type of fluid, pressure conditions, and installation constraints. Ball check valves offer reliability and low maintenance, making them ideal for wastewater applications. However, if budget constraints are significant, swing check valves may provide a more economical alternative for larger systems. For specialized applications involving sensitive fluids, diaphragm check valves offer superior sealing but come with higher upfront costs. By carefully evaluating these factors, buyers can choose the most suitable valve solution that meets their unique needs.
Strategic Material Selection Guide for ball check valve
What Are the Key Materials Used in Ball Check Valves?
When selecting a ball check valve, the choice of material is crucial for ensuring optimal performance and longevity. Here, we analyze four common materials used in manufacturing ball check valves: brass, stainless steel, PVC, and bronze. Each material has unique properties that influence its suitability for specific applications.
How Does Brass Impact Ball Check Valve Performance?
Brass is a popular choice for ball check valves due to its excellent machinability and corrosion resistance. It typically withstands temperatures up to 200°C (392°F) and pressures around 20 bar (290 psi).
Pros: Brass is durable and cost-effective, making it suitable for a wide range of applications, including water supply and HVAC systems. Its good thermal conductivity also helps in maintaining temperature stability.
Cons: However, brass can corrode in highly acidic or alkaline environments, which limits its use in certain applications. Additionally, the presence of lead in some brass alloys raises health concerns, particularly in drinking water applications.
Impact on Application: Brass ball check valves are ideal for non-corrosive fluids and are commonly used in plumbing and irrigation systems. Buyers should ensure compliance with local regulations regarding lead content, especially in regions like Europe and North America.
What Advantages Does Stainless Steel Offer for Ball Check Valves?
Stainless steel is renowned for its exceptional strength and corrosion resistance, making it suitable for harsh environments. It can handle temperatures up to 300°C (572°F) and pressures exceeding 40 bar (580 psi).
Pros: Its durability and resistance to rust and corrosion make stainless steel an excellent choice for applications involving aggressive chemicals or high-pressure systems.
Cons: The main drawback is the higher cost associated with stainless steel compared to other materials. Additionally, its weight can be a consideration in applications where lightweight components are preferred.
Impact on Application: Stainless steel ball check valves are often used in the oil and gas industry, as well as in food processing, where hygiene is paramount. International buyers should consider certifications such as ASTM and ISO standards for quality assurance.
Why Choose PVC for Ball Check Valves?
PVC (Polyvinyl Chloride) is a lightweight and cost-effective plastic material commonly used in ball check valves, particularly for non-pressurized applications. It can withstand temperatures up to 60°C (140°F) and pressures around 10 bar (145 psi).
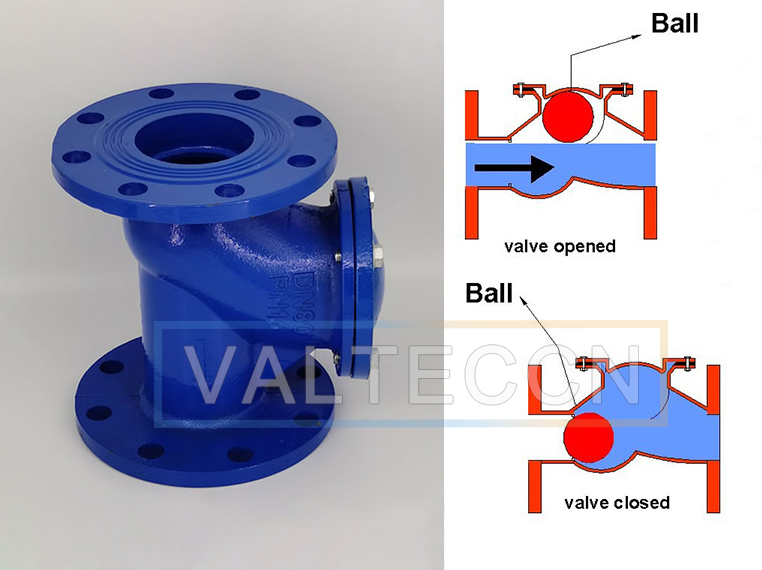
A stock image related to ball check valve.
Pros: PVC is resistant to many chemicals, making it suitable for agricultural and irrigation applications. Its lightweight nature simplifies installation and reduces shipping costs.
Cons: However, PVC has limitations in high-temperature and high-pressure applications. It can also become brittle over time when exposed to UV light.
Impact on Application: PVC ball check valves are ideal for water treatment plants and irrigation systems. Buyers in regions like Africa and South America should ensure compliance with local environmental regulations regarding plastic materials.
What Role Does Bronze Play in Ball Check Valve Applications?
Bronze is another robust material used for ball check valves, particularly in marine and industrial applications. It typically supports temperatures up to 250°C (482°F) and pressures around 30 bar (435 psi).
Pros: Bronze offers excellent corrosion resistance, especially in seawater and other harsh environments. It is also highly durable and can withstand significant wear and tear.
Cons: The primary downside is its cost, which is generally higher than brass and PVC. Additionally, bronze can be heavy, which may not be suitable for all applications.
Impact on Application: Bronze ball check valves are commonly used in marine applications and industrial processes that involve corrosive fluids. International buyers should consider standards such as ASTM B584 for bronze materials.
Summary Table of Material Properties
Material | Typical Use Case for ball check valve | Key Advantage | Key Disadvantage/Limitation | Relative Cost (Low/Med/High) |
---|---|---|---|---|
Brass | Plumbing, HVAC | Cost-effective, good machinability | Corrosion in acidic environments | Medium |
Stainless Steel | Oil & gas, food processing | High strength, corrosion resistant | Higher cost, heavier | High |
PVC | Water treatment, irrigation | Lightweight, chemical resistant | Low temperature tolerance, UV sensitivity | Low |
Bronze | Marine applications, industrial | Excellent corrosion resistance | Higher cost, heavy | Medium to High |
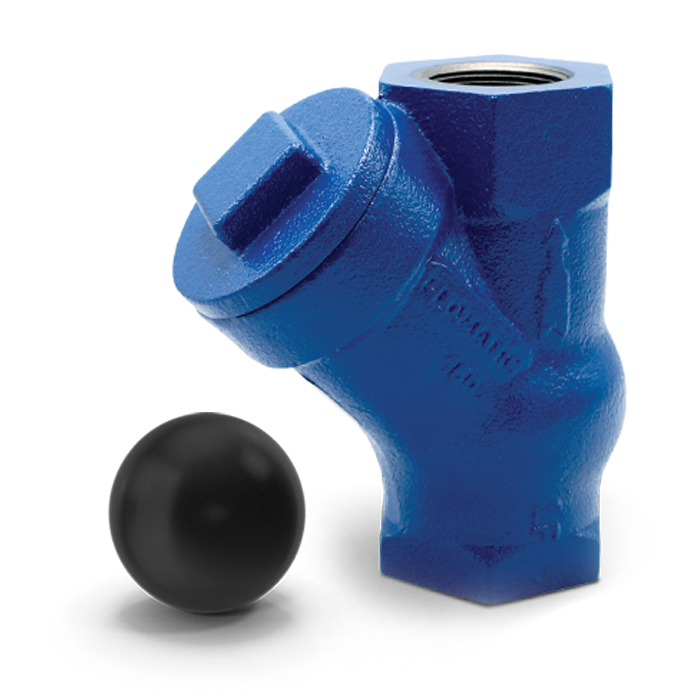
A stock image related to ball check valve.
This strategic material selection guide equips international B2B buyers with the necessary insights to make informed decisions when sourcing ball check valves, taking into account the specific requirements of their applications and compliance with local standards.
In-depth Look: Manufacturing Processes and Quality Assurance for ball check valve
What are the Key Stages in the Manufacturing Process of Ball Check Valves?
The manufacturing process of ball check valves involves several critical stages that ensure the final product meets the required performance and quality standards. These stages typically include material preparation, forming, assembly, and finishing.
Material Preparation: What Materials Are Used and How Are They Processed?
The first step in manufacturing ball check valves is material preparation. Common materials include metals like stainless steel, brass, and bronze, as well as thermoplastics for specific applications. Each material is selected based on its properties, such as corrosion resistance and durability, which are essential for the valve’s function.
Once the materials are selected, they undergo processes such as cutting, machining, and heat treatment. Machining involves precision cutting to create the valve’s components, including the ball, seat, and housing. Heat treatment may be applied to enhance hardness and strength, particularly for metal components. This step is crucial as it directly impacts the valve’s longevity and reliability in various applications.
How Are Ball Check Valves Formed?
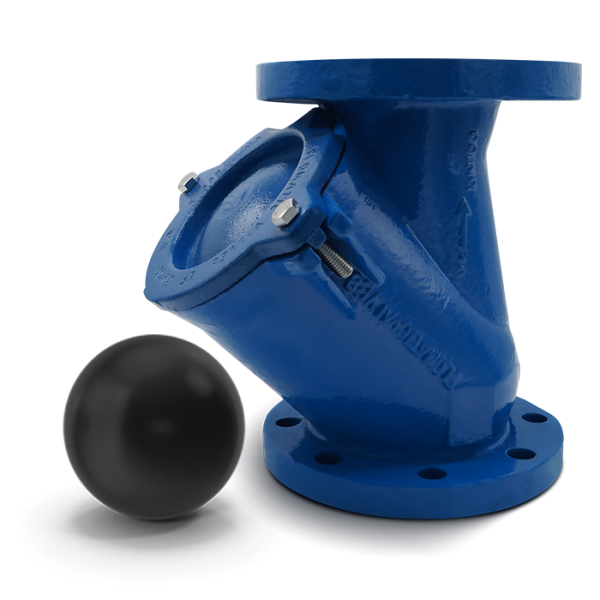
A stock image related to ball check valve.
Following material preparation, the next stage is forming. This typically involves the use of advanced machining techniques such as CNC (Computer Numerical Control) milling and turning. These techniques allow for precise shaping of the valve components, ensuring a tight fit and optimal sealing capability.
For thermoplastic valves, injection molding is a common forming technique. This process allows for high-volume production and consistent quality, which is vital for meeting the demands of B2B buyers. The forming stage is critical, as any imperfections can lead to leaks or valve failure in operational conditions.
What Are the Assembly and Finishing Processes for Ball Check Valves?
How Are Ball Check Valves Assembled?
The assembly stage involves bringing together all the formed components. This includes inserting the ball into the valve body and securing the seat. Proper alignment is essential to ensure the ball can move freely and create an effective seal when needed.
During assembly, manufacturers may also apply lubricants to facilitate the movement of the ball and reduce wear during operation. Automated assembly systems are often employed to enhance efficiency and consistency, particularly in high-volume production settings.
What Finishing Techniques Are Used to Ensure Quality?
Once assembled, the ball check valves undergo finishing processes that may include surface treatment, coating, and quality inspections. Surface treatments such as anodizing or plating are applied to enhance corrosion resistance, especially for valves intended for harsh environments.
Finishing processes also often include polishing to ensure smooth surfaces, which helps in reducing friction and wear. This is particularly important for valves that operate under high flow rates or pressure conditions.
What Quality Assurance Measures Are Implemented for Ball Check Valves?
Which International Standards Apply to Ball Check Valve Manufacturing?
Quality assurance (QA) is a fundamental aspect of ball check valve manufacturing. Manufacturers typically adhere to international standards such as ISO 9001, which outlines requirements for a quality management system. Compliance with this standard helps ensure that products consistently meet customer and regulatory requirements.
In addition to ISO standards, industry-specific certifications like CE marking (for European markets) and API (American Petroleum Institute) standards are also crucial. These certifications validate that the valves meet strict safety and performance criteria, making them suitable for various applications across industries.
What Are the Key Quality Control Checkpoints?
Quality control (QC) checkpoints are integral to the manufacturing process. Common QC checkpoints include:
-
Incoming Quality Control (IQC): This involves inspecting raw materials upon receipt to ensure they meet specified requirements before production begins.
-
In-Process Quality Control (IPQC): Throughout the manufacturing process, inspections are conducted at various stages to identify any defects or deviations from specifications.
-
Final Quality Control (FQC): Once the valves are fully assembled, a comprehensive inspection is performed to ensure that all components function correctly and meet quality standards.
What Testing Methods Are Commonly Used for Ball Check Valves?
Testing methods are crucial for verifying the functionality and reliability of ball check valves. Common tests include:
-
Hydrostatic Testing: This test assesses the valve’s ability to withstand pressure without leaking. It simulates the operational conditions the valve will face in the field.
-
Functional Testing: This ensures the valve operates correctly under different pressure conditions and effectively prevents backflow.
-
Leak Testing: This involves checking the valve for any leaks at specified pressure levels, ensuring that it seals properly.
How Can B2B Buyers Verify Supplier Quality Control?
For international B2B buyers, particularly those from Africa, South America, the Middle East, and Europe, verifying supplier quality control is essential to ensure product reliability. Here are some strategies:
-
Supplier Audits: Conducting audits of potential suppliers can provide insights into their manufacturing processes, quality control measures, and adherence to international standards.
-
Requesting Quality Reports: Buyers should ask suppliers for detailed quality reports that outline testing methods, results, and compliance with relevant standards.
-
Third-Party Inspections: Engaging third-party inspection agencies can provide an unbiased assessment of the supplier’s quality control processes and product reliability. This is particularly important for buyers in regions with specific regulatory requirements.
What Are the Quality Control and Certification Nuances for International Buyers?
International buyers must be aware of the nuances in quality control and certification requirements that vary by region. For instance, European buyers may prioritize CE certification, while buyers in the Middle East may look for compliance with local standards. Understanding these nuances can help buyers make informed decisions and ensure that the ball check valves they purchase meet their specific operational requirements.
In conclusion, understanding the manufacturing processes and quality assurance practices for ball check valves is vital for B2B buyers. By focusing on material selection, manufacturing techniques, and rigorous quality control, buyers can ensure they procure reliable and high-performance valves suited to their applications.
Practical Sourcing Guide: A Step-by-Step Checklist for ‘ball check valve’
In today’s global marketplace, procuring a ball check valve requires a systematic approach to ensure that you select the right product for your specific application. This checklist is designed to guide international B2B buyers, particularly from Africa, South America, the Middle East, and Europe, through the essential steps of sourcing a ball check valve effectively.
Step 1: Define Your Technical Specifications
Understanding the precise requirements of your application is crucial. Define the flow rate, pressure ratings, and temperature ranges necessary for your system. Consider the material compatibility as well, as different environments may require specific materials like stainless steel or PVC to prevent corrosion and ensure longevity.
Step 2: Research Different Types of Ball Check Valves
Not all ball check valves are created equal. Familiarize yourself with the various designs, such as floating and sinking ball types, and their respective applications. For instance, floating ball valves are often preferred for anti-flooding applications, while sinking balls are more common in wastewater systems. Knowing the differences will help narrow your options.
Step 3: Evaluate Potential Suppliers
Before making a purchase, it’s essential to vet potential suppliers thoroughly. Request detailed company profiles, case studies, and references from buyers in similar industries or regions. Ensure that suppliers have a track record of reliability and quality, as this will impact the performance of your ball check valve in the long term.
Step 4: Verify Supplier Certifications
Check for relevant certifications that indicate compliance with industry standards, such as ISO 9001 or API certification. Certifications ensure that the products meet specific safety and quality benchmarks, which is especially important in sectors like oil and gas or water treatment where reliability is non-negotiable.
Step 5: Request Samples or Product Demonstrations
Whenever possible, request samples of the ball check valves or arrange for product demonstrations. This allows you to evaluate the quality, functionality, and suitability of the valves for your specific needs. Observing the valve in action can also highlight any potential issues that may not be evident in specifications alone.
Step 6: Understand Pricing Structures and Terms
Engage suppliers in discussions about pricing, payment terms, and potential discounts for bulk purchases. Understanding the total cost of ownership, including shipping and customs fees, will help you make an informed decision. Be cautious of prices that seem too low, as they may indicate compromised quality.
Step 7: Plan for After-Sales Support and Maintenance
Inquire about the after-sales support offered by suppliers, including warranty terms, maintenance guidelines, and availability of replacement parts. A supplier that provides comprehensive support can save you time and resources in the long run, ensuring the longevity and efficiency of your ball check valves.
By following this step-by-step checklist, you will be well-equipped to make informed decisions when sourcing ball check valves, ultimately enhancing the reliability and efficiency of your operations.
Comprehensive Cost and Pricing Analysis for ball check valve Sourcing
What Are the Key Cost Components for Sourcing Ball Check Valves?
When sourcing ball check valves, understanding the cost structure is critical for effective budgeting and negotiation. The main cost components include:
-
Materials: The choice of materials significantly impacts costs. Common materials include brass, stainless steel, and various thermoplastics. Higher-grade materials may be necessary for corrosive environments, leading to increased costs.
-
Labor: Manufacturing labor costs can vary widely based on the production location. Countries with lower labor costs may offer savings, but quality and manufacturing practices should be carefully evaluated.
-
Manufacturing Overhead: This includes costs associated with the factory’s operation, such as utilities, equipment depreciation, and facility maintenance. A higher overhead might indicate a more established supplier with better quality assurance processes.
-
Tooling: Custom tooling for specialized valves can add significant costs. If you require unique specifications or custom designs, this investment should be factored into your total cost analysis.
-
Quality Control (QC): Implementing stringent quality control measures is essential for ensuring product reliability. Suppliers with robust QC processes may charge more, but the long-term benefits often outweigh these costs.
-
Logistics: Transportation and handling can significantly affect the final price, especially for international shipments. Factors such as distance, shipping method, and any tariffs or duties should be carefully considered.
-
Margin: Supplier margins can vary based on market conditions, competition, and the supplier’s positioning. Understanding the supplier’s pricing strategy can provide insights into potential negotiation points.
How Do Price Influencers Affect Ball Check Valve Costs?
Several factors influence the pricing of ball check valves, particularly for international buyers:
-
Volume and Minimum Order Quantity (MOQ): Purchasing in bulk can lead to significant discounts. Suppliers often have MOQs that can affect pricing, so understanding these thresholds is essential for cost savings.
-
Specifications and Customization: Customized valves typically come at a premium. Buyers should assess whether off-the-shelf solutions meet their needs to avoid unnecessary costs.
-
Materials: As mentioned earlier, the choice of materials directly impacts price. For instance, a valve made from stainless steel will generally be more expensive than one made from PVC.
-
Quality and Certifications: Valves with specific quality certifications (e.g., ISO, API) may command higher prices. However, these certifications often ensure reliability and compliance with safety standards.
-
Supplier Factors: The reputation, reliability, and financial stability of suppliers can influence pricing. Established suppliers may offer better support and warranties, justifying higher costs.
-
Incoterms: Understanding Incoterms (International Commercial Terms) is crucial for international transactions. They dictate the responsibilities of buyers and sellers concerning shipping, insurance, and tariffs, affecting overall costs.
What Are the Best Negotiation Tips for International B2B Buyers?
Effective negotiation strategies can lead to better pricing and terms:
-
Research and Benchmarking: Conduct thorough market research to understand typical pricing for ball check valves. Use this information as leverage during negotiations.
-
Build Relationships: Developing a strong relationship with suppliers can lead to better deals and more favorable terms. Trust can often result in flexibility during negotiations.
-
Discuss Total Cost of Ownership (TCO): Focus on the TCO rather than just the upfront price. Consider long-term factors such as maintenance, reliability, and potential downtime costs.
-
Explore Payment Terms: Negotiate favorable payment terms, such as extended payment periods or discounts for early payment, to improve cash flow.
-
Be Open to Alternatives: If a supplier cannot meet your price, consider alternative solutions, such as adjusting specifications or exploring different suppliers.
What Should International Buyers Consider Regarding Pricing Nuances?
International buyers must navigate unique challenges in pricing:
-
Currency Fluctuations: Be aware of the impact of currency exchange rates on pricing. Fluctuations can significantly affect the total cost.
-
Shipping and Customs: Factor in shipping costs and potential customs duties when calculating the final price. Understanding these elements can prevent unexpected expenses.
-
Cultural Differences: Cultural nuances can affect negotiation styles and expectations. Be prepared to adapt your approach based on the supplier’s background.
Disclaimer for Indicative Prices
Prices for ball check valves can vary widely based on the aforementioned factors. It is essential to request quotes from multiple suppliers and consider all cost components to get an accurate picture of total expenses.
Essential Technical Properties and Trade Terminology for ball check valve
What Are the Key Technical Properties of Ball Check Valves?
Understanding the essential technical specifications of ball check valves is critical for international B2B buyers, particularly when selecting valves for specific applications. Here are some important properties to consider:
1. Material Grade
Ball check valves are typically constructed from materials such as brass, bronze, stainless steel, PVC, or thermoplastics. The choice of material affects corrosion resistance, durability, and suitability for various media (e.g., water, chemicals). For example, stainless steel is often preferred in corrosive environments, while PVC is lightweight and cost-effective for non-pressurized systems. Selecting the right material ensures longevity and minimizes maintenance costs.
2. Cracking Pressure
Cracking pressure is the minimum pressure required to open the valve and allow flow. This specification is crucial for determining whether the valve can operate effectively in your specific application, especially in systems where fluid pressure may vary significantly. Understanding the cracking pressure helps buyers ensure that the valve will function as intended without backflow issues.
3. Valve Size and Tolerance
The size of the valve, typically measured in inches or millimeters, directly impacts its flow capacity and compatibility with existing piping systems. Tolerance refers to the allowable deviation from specified dimensions, which can affect the valve’s fit and performance. Accurate sizing and tolerance specifications are essential for seamless installation and operational efficiency.
4. Flow Rate
The flow rate indicates the volume of fluid that can pass through the valve per unit time, often expressed in liters per minute (L/min) or gallons per minute (GPM). This property is critical for ensuring that the valve meets the demands of your application, whether it’s for irrigation, HVAC systems, or wastewater management. Selecting a valve with the appropriate flow rate prevents bottlenecks and maintains system efficiency.
5. Pressure Rating
The pressure rating denotes the maximum pressure the valve can withstand without failure. This specification is vital for applications where high pressure is a concern, such as in industrial settings. A valve that cannot handle the required pressure may lead to leaks or catastrophic failures, resulting in costly downtime and repairs.
What Trade Terminology Should B2B Buyers Know?
Familiarity with industry jargon can significantly enhance the procurement process for ball check valves. Here are some common terms that buyers should understand:
1. OEM (Original Equipment Manufacturer)
An OEM is a company that produces parts or equipment that may be marketed by another manufacturer. Understanding OEM relationships can help buyers identify reputable suppliers and ensure they are purchasing high-quality, reliable products that meet industry standards.
2. MOQ (Minimum Order Quantity)
MOQ refers to the smallest quantity of a product that a supplier is willing to sell. Knowing the MOQ is essential for budget planning and ensuring that you can meet your operational needs without overcommitting resources.
3. RFQ (Request for Quotation)
An RFQ is a document that a buyer sends to suppliers to solicit price quotes for specific products. Crafting a detailed RFQ can lead to better pricing and terms, making it an important tool for international buyers negotiating with multiple suppliers.
4. Incoterms
Incoterms (International Commercial Terms) define the responsibilities of buyers and sellers regarding shipping, insurance, and tariffs. Familiarity with these terms is crucial for international transactions, as they dictate the cost and risk associated with transporting goods across borders.
5. Lead Time
Lead time is the period between placing an order and receiving the goods. For B2B buyers, understanding lead times is vital for inventory management and ensuring that projects remain on schedule, particularly in sectors where delays can result in significant financial losses.
By grasping these technical properties and trade terminologies, international B2B buyers can make informed decisions when sourcing ball check valves, ensuring optimal performance and compliance with their specific operational requirements.
Navigating Market Dynamics and Sourcing Trends in the ball check valve Sector
What Are the Current Market Dynamics and Key Trends in the Ball Check Valve Sector?
The ball check valve market is experiencing significant growth driven by increasing demand across various sectors such as water treatment, oil and gas, and manufacturing. Key market drivers include the rising need for efficient fluid control systems and stringent regulations regarding backflow prevention to protect water supplies. In regions like Africa and South America, expanding infrastructure projects are propelling the demand for reliable check valves. Conversely, in Europe and the Middle East, the emphasis on upgrading existing systems for improved efficiency is leading to the adoption of advanced ball check valve technologies.
Emerging trends in B2B sourcing for ball check valves include digitalization and automation in supply chain management. Buyers are increasingly utilizing online platforms to procure valves, allowing for better price comparison and supplier evaluation. Additionally, the introduction of IoT-enabled valves is gaining traction, providing real-time monitoring and maintenance alerts, thus enhancing operational efficiency. International B2B buyers should focus on suppliers that offer customized solutions to meet specific application needs, especially in regions where environmental conditions may impact valve performance.
How Does Sustainability and Ethical Sourcing Impact the Ball Check Valve Market?
Sustainability is becoming a crucial factor in the sourcing of ball check valves. Buyers are increasingly concerned about the environmental impact of their purchases and are seeking suppliers that prioritize sustainable practices. This includes the use of eco-friendly materials and processes, which not only reduce the carbon footprint but also comply with global environmental standards.
Ethical sourcing is equally important, as businesses strive to build transparent and responsible supply chains. Certifications such as ISO 14001 for environmental management and the use of recycled materials in valve production are indicators of a supplier’s commitment to sustainability. International buyers, particularly those in Europe and the Middle East, are more likely to favor manufacturers that can demonstrate their dedication to reducing environmental impact and ensuring ethical labor practices.
What Is the Evolution of Ball Check Valves in the B2B Context?
The evolution of ball check valves has been marked by significant advancements in materials and design. Initially designed for basic applications, modern ball check valves are now engineered with high-performance materials that enhance durability and resistance to corrosive environments. Innovations such as self-cleaning mechanisms and the integration of smart technology have transformed their functionality, making them indispensable in industries that require reliable fluid management.
The shift towards automation in valve operation is also noteworthy. As industries increasingly adopt IoT solutions, ball check valves are being equipped with sensors that provide critical data for predictive maintenance and operational efficiency. This evolution not only improves the performance of fluid systems but also aligns with the growing demand for smart manufacturing solutions, ultimately benefiting international B2B buyers looking for advanced and reliable products.
Frequently Asked Questions (FAQs) for B2B Buyers of ball check valve
-
How do I choose the right ball check valve for my application?
Choosing the right ball check valve involves understanding the specific requirements of your application. Consider factors such as fluid type, pressure, temperature, and flow rates. Ensure the valve material is compatible with the fluid to prevent corrosion or degradation. Evaluate the cracking pressure needed to open the valve; this is crucial for proper functioning. Consulting with suppliers who can provide technical specifications and advice based on your application can greatly enhance your selection process. -
What are the common applications of ball check valves in different industries?
Ball check valves are widely used in various industries due to their reliability in preventing backflow. Common applications include wastewater treatment, HVAC systems, irrigation, and pumping stations. They are essential in processes where backflow could cause contamination or system failure. Understanding the specific industry standards and requirements can help you select the appropriate ball check valve tailored to your application. -
What customization options are available for ball check valves?
Customization options for ball check valves include material selection, size, and pressure ratings. Manufacturers often provide options for different ball materials, such as Buna-N or corrosion-resistant phenolic, depending on the fluid being handled. Additionally, you may request specific dimensions or features like true union designs for easier maintenance. Always discuss your specific needs with potential suppliers to ensure you receive a valve that meets your exact specifications. -
What is the minimum order quantity (MOQ) for ball check valves?
Minimum order quantities (MOQ) for ball check valves can vary significantly among suppliers. Some manufacturers may have a low MOQ for standard products, while custom or specialized valves may require larger orders. It’s advisable to confirm the MOQ during your initial discussions with suppliers, especially if you are a smaller business or testing a new application. This will help you manage costs and ensure you have enough inventory for your needs. -
What payment terms should I expect when sourcing ball check valves internationally?
Payment terms for international sourcing of ball check valves typically vary by supplier and the nature of the transaction. Common terms include payment upfront, net 30, or letter of credit, depending on the trust established between the buyer and seller. It’s essential to discuss and agree upon these terms before finalizing your order to avoid any misunderstandings. Always ensure that the payment method is secure and offers protection against fraud. -
How can I ensure the quality of ball check valves when sourcing from international suppliers?
To ensure the quality of ball check valves, request certifications and compliance documents from suppliers that demonstrate adherence to international standards, such as ISO or API. Conducting due diligence through supplier audits or third-party inspections can also provide peace of mind. Additionally, reviewing customer feedback and case studies can help gauge a supplier’s reputation in delivering quality products consistently. -
What logistics considerations should I keep in mind when importing ball check valves?
When importing ball check valves, consider logistics factors such as shipping methods, lead times, and customs regulations. Choose a reliable freight forwarder familiar with international shipping to navigate potential challenges. Be aware of any import duties and taxes that may apply to your shipment. Properly planning your logistics will help ensure timely delivery and mitigate any unforeseen delays. -
What are the common challenges faced when sourcing ball check valves internationally?
Common challenges in sourcing ball check valves internationally include language barriers, cultural differences, and varying quality standards. Additionally, navigating customs regulations and ensuring compliance can pose hurdles. To mitigate these issues, establish clear communication with suppliers, conduct thorough research on their practices, and seek recommendations from other businesses in your industry. This proactive approach will help you build strong relationships and facilitate smoother transactions.
Important Disclaimer & Terms of Use
⚠️ Important Disclaimer
The information provided in this guide, including content regarding manufacturers, technical specifications, and market analysis, is for informational and educational purposes only. It does not constitute professional procurement advice, financial advice, or legal advice.
While we have made every effort to ensure the accuracy and timeliness of the information, we are not responsible for any errors, omissions, or outdated information. Market conditions, company details, and technical standards are subject to change.
B2B buyers must conduct their own independent and thorough due diligence before making any purchasing decisions. This includes contacting suppliers directly, verifying certifications, requesting samples, and seeking professional consultation. The risk of relying on any information in this guide is borne solely by the reader.
Strategic Sourcing Conclusion and Outlook for ball check valve
How Can Strategic Sourcing Enhance Your Ball Check Valve Procurement?
In conclusion, effective strategic sourcing is essential for international B2B buyers seeking ball check valves. Understanding the technical specifications, such as materials and design variations, is crucial for selecting the right valve that meets your operational needs. Key takeaways include recognizing the importance of quality assurance, supplier reliability, and cost efficiency. For instance, choosing ball check valves made from corrosion-resistant materials can significantly enhance longevity and reduce maintenance costs, particularly in harsh environments.
What Should International Buyers Consider Moving Forward?
As you navigate the procurement landscape, prioritize suppliers who offer comprehensive support and a wide range of product options tailored to your industry requirements. Engage with manufacturers who understand regional challenges and can provide localized solutions. The global market for ball check valves continues to evolve, driven by technological advancements and increasing demand across sectors.
How Can You Stay Ahead in the Ball Check Valve Market?
Investing time in strategic sourcing now will position your business for success in the future. Leverage relationships with suppliers and stay informed about industry trends to optimize your procurement strategies. By doing so, you can ensure a reliable supply chain and enhance operational efficiency. Take the next step in your sourcing journey today—explore diverse offerings and connect with trusted suppliers to secure the best solutions for your business needs.