Improve Efficiency: The Complete Shaft Coupler Guide (2025)
Introduction: Navigating the Global Market for shaft coupler
In the ever-evolving landscape of global manufacturing, sourcing the right shaft coupler can pose significant challenges for international B2B buyers. Understanding the intricacies of different types of couplings, their applications, and how to effectively evaluate suppliers is essential for businesses aiming to enhance their operational efficiency. This comprehensive guide serves as a valuable resource for buyers from Africa, South America, the Middle East, and Europe—including key markets like Saudi Arabia and Egypt—by addressing critical factors that influence purchasing decisions in the shaft coupler market.
Throughout this guide, we will explore various types of shaft couplers, including rigid, flexible, and chain couplings, each tailored to specific operational needs. We will delve into their applications across diverse industries, from automotive to industrial machinery, providing insights that empower buyers to make informed choices. Additionally, we will discuss essential criteria for vetting suppliers, including quality assurance, compliance with international standards, and cost considerations.
By equipping you with actionable insights and a thorough understanding of the shaft coupler market, this guide aims to streamline your procurement process, reduce downtime, and enhance your overall operational performance. Whether you are a seasoned buyer or new to the market, the information contained herein will be instrumental in navigating the complexities of sourcing shaft couplers effectively.
Understanding shaft coupler Types and Variations
Type Name | Key Distinguishing Features | Primary B2B Applications | Brief Pros & Cons for Buyers |
---|---|---|---|
Rigid Shaft Couplings | No flexibility; designed for precise alignment | CNC machinery, automotive, robotics | Pros: High torque transmission, durable. Cons: Cannot accommodate misalignment. |
Flexible Jaw Couplings | Allows for angular misalignment; features interlocking jaws | Conveyor systems, pumps, compressors | Pros: Accommodates misalignment, easy installation. Cons: Limited torque capacity. |
Chain Couplings | Uses roller chains for torque transmission; moderate misalignment | Agricultural machinery, industrial drives | Pros: Handles angular misalignment, high torque. Cons: Requires lubrication, bulkier. |
Metal Disc Couplings | Flexible discs provide torsional rigidity; low backlash | High-speed applications, servo motors | Pros: High precision, minimal wear. Cons: More expensive, complex installation. |
Oldham Couplings | Features a central disc allowing for radial misalignment | Printing presses, textile machinery | Pros: Compensates for radial misalignment. Cons: Limited torque capacity. |
What Are Rigid Shaft Couplings and When Should They Be Used?
Rigid shaft couplings are designed to connect two shafts without any allowance for misalignment. These couplings are typically made from durable materials such as aluminum or stainless steel and are used in applications requiring precise alignment, such as CNC machinery and robotics. When purchasing, consider the torque requirements and the need for alignment, as these couplings are not suitable for applications where shaft misalignment might occur.
How Do Flexible Jaw Couplings Enhance Performance?
Flexible jaw couplings consist of two hubs with interlocking jaws and a flexible element that allows for some angular misalignment. They are commonly used in conveyor systems and pumps where flexibility is essential. Buyers should assess the operational environment and the extent of misalignment expected, as these couplings can improve system performance but have limitations in torque capacity.
What Are the Advantages of Chain Couplings?
Chain couplings utilize roller chains to connect shafts, making them suitable for applications that require high torque transmission and moderate angular misalignment, such as agricultural machinery and industrial drives. While they offer robust performance, buyers must consider the need for regular lubrication and the additional space they may require in machinery setups.
Why Choose Metal Disc Couplings for Precision?
Metal disc couplings are engineered for high-speed applications and provide exceptional torsional rigidity while allowing for some misalignment. Their design minimizes backlash, making them ideal for servo motors and other precision-driven machinery. However, they tend to be more expensive and may require a more complex installation process, so buyers should evaluate their application needs and budget accordingly.
What Makes Oldham Couplings Unique?
Oldham couplings feature a central disc that allows for radial misalignment, making them suitable for applications like printing presses and textile machinery. They are advantageous in scenarios where space is limited. However, their torque capacity is lower than other coupling types, which is a crucial consideration for buyers when selecting the appropriate coupling for their machinery needs.
Key Industrial Applications of shaft coupler
Industry/Sector | Specific Application of Shaft Coupler | Value/Benefit for the Business | Key Sourcing Considerations for this Application |
---|---|---|---|
Manufacturing | Connecting motors to conveyor systems | Enhances operational efficiency and reduces downtime | Consider torque capacity, misalignment tolerance, and material durability. |
Agriculture | Power transmission in agricultural machinery | Increases reliability and performance of equipment | Look for couplers that can withstand harsh environments and provide flexibility. |
Mining | Joining shafts in drilling equipment | Improves safety and operational reliability | Ensure couplers meet industry standards for strength and durability. |
Automotive | Engine and transmission connections | Optimizes power transfer and minimizes vibration | Evaluate compatibility with existing systems and ease of installation. |
Energy | Coupling turbines to generators | Enhances energy efficiency and reduces maintenance costs | Assess thermal and mechanical stress ratings for high-performance applications. |
How is Shaft Coupler Used in Manufacturing?
In the manufacturing sector, shaft couplers are primarily used to connect electric motors to conveyor systems. This application is critical as it ensures the smooth transmission of power, enabling continuous operation of machinery. By utilizing couplers that accommodate angular misalignments, manufacturers can minimize wear and tear on components, thereby reducing maintenance costs and downtime. B2B buyers in this sector should prioritize sourcing couplers with high torque ratings and robust materials to withstand heavy industrial use.
What is the Role of Shaft Coupler in Agriculture?
Shaft couplers play a vital role in agricultural machinery, such as tractors and harvesters, by connecting power sources to various implements. This application ensures that machinery operates reliably under demanding conditions, such as rough terrains and variable loads. For international buyers, especially in regions like Africa and South America, it is essential to select couplers that are resistant to corrosion and can handle the unique stresses of agricultural operations. Flexibility in design is also key, as it allows for adjustments to different equipment types.
How is Shaft Coupler Utilized in Mining?
In the mining industry, shaft couplers are essential for joining shafts in drilling and excavation equipment. These couplers must provide high strength and reliability to handle the extreme conditions often found in mining operations. They help to improve safety by reducing the risk of equipment failure, which can lead to costly downtime and hazards for workers. Buyers should focus on couplers that comply with industry standards for durability and performance, particularly in harsh environments.
What is the Importance of Shaft Coupler in Automotive Applications?
In the automotive industry, shaft couplers are used to connect engines to transmissions, facilitating efficient power transfer. This application is crucial for optimizing vehicle performance and minimizing vibrations that can lead to mechanical failures. For B2B buyers, particularly those sourcing components in Europe and the Middle East, it is important to ensure compatibility with existing automotive systems and consider the ease of installation. High-quality couplers that can withstand high temperatures and mechanical stress are essential for long-lasting performance.
How Does Shaft Coupler Enhance Energy Production?
Shaft couplers are integral in the energy sector, particularly in coupling turbines to generators. This application is designed to enhance energy efficiency and reduce maintenance costs by ensuring reliable power transmission. For international buyers in regions with developing energy infrastructure, selecting couplers that can handle high thermal and mechanical stresses is vital. Buyers should also consider the lifecycle cost of couplers, including maintenance and replacement, to ensure long-term operational efficiency.
3 Common User Pain Points for ‘shaft coupler’ & Their Solutions
Scenario 1: Misalignment Issues Leading to Equipment Failure
The Problem: Many B2B buyers, especially in industries such as manufacturing and agriculture, face challenges with shaft misalignment. This misalignment can result from improper installation or wear over time, leading to excessive vibration, noise, and eventual equipment failure. For instance, a manufacturing plant in Egypt may find that their conveyor system is experiencing increased downtime, causing significant disruptions in productivity and potential losses in revenue.
The Solution: To combat misalignment issues, buyers should consider sourcing flexible shaft couplings, which can accommodate a degree of angular, parallel, and axial misalignment. When selecting a coupler, it’s essential to evaluate the specific application requirements, including torque, speed, and alignment tolerances. Buyers should work closely with suppliers to ensure that the chosen coupler is rated for the maximum expected load and can handle the specific misalignment conditions of their equipment. Additionally, conducting regular maintenance and alignment checks can help prevent misalignment issues before they escalate, ensuring continuous operation and reducing the risk of costly breakdowns.
Scenario 2: Inadequate Coupling Selection Leading to Downtime
The Problem: Another common pain point for B2B buyers is selecting the wrong type of shaft coupler for their specific application, which can lead to operational inefficiencies and increased downtime. For example, a company in Brazil might choose a rigid coupling for an application requiring flexibility, resulting in stress on the shafts and potential failure. This not only affects the equipment but also leads to delays in production schedules, affecting overall business performance.
The Solution: To avoid this scenario, it is crucial for buyers to thoroughly understand the operational conditions and requirements of their applications before purchasing a shaft coupler. Engaging with manufacturers or distributors to gain insights into the various types of couplers available—such as rigid, flexible, or universal couplings—can provide clarity on the best fit. Furthermore, buyers should consider the environment in which the coupler will operate, including factors like temperature, moisture, and exposure to chemicals, as these can impact the material selection. Utilizing a decision matrix to compare the specifications and performance characteristics of different couplers can also facilitate informed purchasing decisions, leading to better performance and reduced downtime.
Scenario 3: Increased Maintenance Costs Due to Poor Coupler Performance
The Problem: Frequent maintenance and replacement of shaft couplers can significantly drive up operational costs for businesses. In regions like the Middle East, where extreme temperatures can affect the performance of mechanical components, poorly selected or maintained couplings can lead to increased wear and tear. A typical scenario might involve a company in Saudi Arabia facing high maintenance costs due to premature failure of couplings that are not designed to withstand local conditions.
The Solution: To mitigate maintenance costs, buyers should invest in high-quality shaft couplers that are specifically engineered for their operating environment. This includes selecting couplings made from durable materials that can resist heat and corrosion. It’s advisable to conduct a thorough assessment of the environmental factors before making a purchase. Additionally, implementing a predictive maintenance program that utilizes sensors and monitoring systems can provide real-time data on the performance of couplings. This proactive approach allows businesses to schedule maintenance activities before failures occur, ultimately saving costs and enhancing the lifespan of their equipment. Working with suppliers who offer warranties and support can also provide peace of mind and reduce long-term expenses associated with maintenance.
Strategic Material Selection Guide for shaft coupler
When selecting materials for shaft couplers, international B2B buyers must consider various factors that influence product performance, durability, and compliance with regional standards. Here, we analyze four common materials used in shaft couplers: aluminum, stainless steel, plastic, and cast iron. Each material has unique properties and implications for specific applications, particularly relevant to buyers from Africa, South America, the Middle East, and Europe.
What Are the Key Properties of Aluminum for Shaft Couplers?
Aluminum is a lightweight material known for its excellent strength-to-weight ratio. It typically has a temperature rating of up to 150°C and offers good corrosion resistance, making it suitable for various environments. Aluminum couplers can handle moderate loads and are often used in applications where weight reduction is critical, such as in aerospace and automotive industries.
Pros and Cons of Aluminum Couplers
The primary advantage of aluminum is its low weight, which can enhance performance in dynamic applications. However, its lower durability compared to steel can be a limitation in high-torque applications. Additionally, while aluminum is relatively cost-effective, the manufacturing processes may involve complexities, especially for intricate designs.
Impact on Application
Aluminum couplers are compatible with numerous media but may not be suitable for high-pressure applications. Buyers should ensure that the specific aluminum alloy used meets the requirements for their intended application.
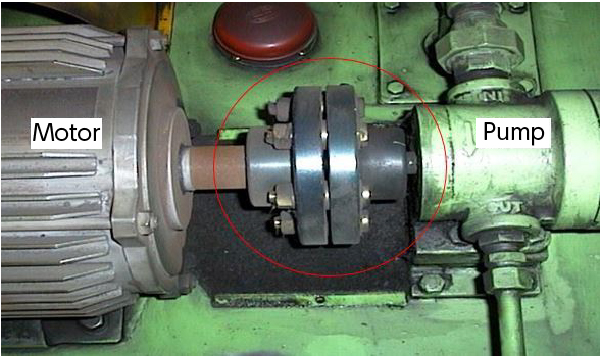
A stock image related to shaft coupler.
How Does Stainless Steel Compare for Shaft Couplers?
Stainless steel is renowned for its high corrosion resistance and durability, making it ideal for harsh environments, such as those found in chemical processing or marine applications. It can withstand temperatures up to 300°C and offers excellent mechanical strength.
Pros and Cons of Stainless Steel Couplers
The key advantage of stainless steel is its longevity and ability to maintain performance under extreme conditions. However, it is more expensive than aluminum and can be heavier, which may not be suitable for all applications. Manufacturing stainless steel couplers can also be more complex due to the material’s hardness.
Impact on Application
Stainless steel couplers are highly versatile and can handle a wide range of media, including corrosive substances. Buyers from regions with stringent environmental regulations should consider stainless steel for compliance with standards such as ASTM and DIN.
What Role Does Plastic Play in Shaft Coupler Applications?
Plastic couplers, typically made from materials like nylon or PVC, offer excellent resistance to corrosion and chemicals. They can operate effectively at temperatures up to 80°C and are lightweight, making them suitable for low-load applications.
Pros and Cons of Plastic Couplers
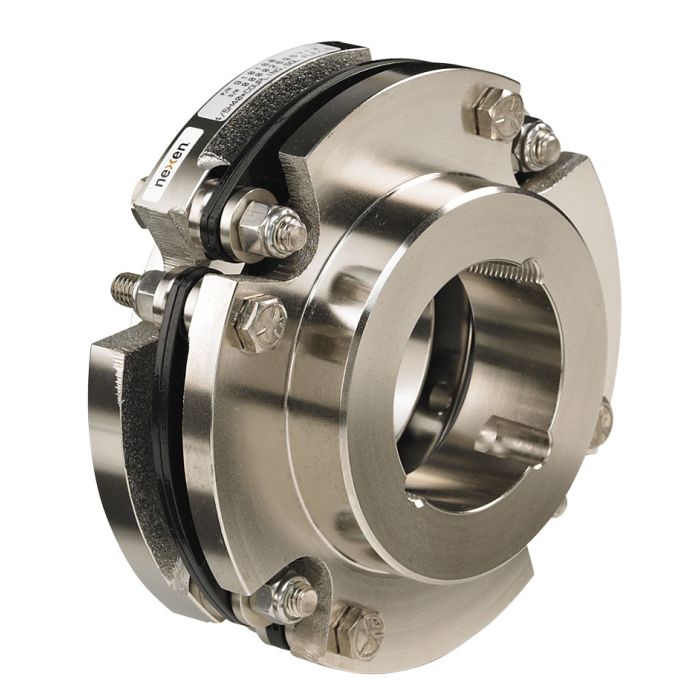
A stock image related to shaft coupler.
The primary advantage of plastic is its cost-effectiveness and ease of manufacturing, allowing for complex shapes. However, plastic couplers have lower strength and are not suitable for high-torque applications. Their limited temperature and pressure ratings can also restrict their use.
Impact on Application
Plastic couplers are ideal for applications involving non-corrosive media and environments where weight is a concern. Buyers should evaluate the specific type of plastic to ensure compatibility with the intended application.
Why Choose Cast Iron for Shaft Couplers?
Cast iron is a traditional material known for its strength and ability to absorb vibrations. It can handle high loads and is often used in heavy machinery applications. Cast iron couplers can withstand temperatures up to 200°C.
Pros and Cons of Cast Iron Couplers
The main advantage of cast iron is its durability and ability to withstand high torque. However, it is relatively heavy and can be prone to corrosion if not treated properly. The manufacturing process can also be more labor-intensive, leading to higher costs.
Impact on Application
Cast iron couplers are suitable for heavy industrial applications, particularly in environments where vibration dampening is essential. Buyers should ensure that the couplers meet relevant standards and specifications for their specific applications.
Summary Table of Material Selection for Shaft Couplers
Material | Typical Use Case for Shaft Coupler | Key Advantage | Key Disadvantage/Limitation | Relative Cost (Low/Med/High) |
---|---|---|---|---|
Aluminum | Aerospace, automotive | Lightweight and good corrosion resistance | Lower durability in high-torque applications | Medium |
Stainless Steel | Chemical processing, marine | High corrosion resistance and durability | Higher cost and weight | High |
Plastic | Low-load applications | Cost-effective and easy to manufacture | Low strength and limited temperature ratings | Low |
Cast Iron | Heavy machinery | Excellent durability and vibration absorption | Heavy and prone to corrosion | Medium |
In conclusion, selecting the right material for shaft couplers involves a careful consideration of performance requirements, application environments, and regional compliance standards. International B2B buyers should assess these factors to ensure optimal performance and longevity of their couplings.
In-depth Look: Manufacturing Processes and Quality Assurance for shaft coupler
What Are the Key Stages in Manufacturing Shaft Couplers?
The manufacturing of shaft couplers involves several critical stages that ensure the final product meets the necessary performance and quality standards. Understanding these processes can help international B2B buyers evaluate potential suppliers effectively.
1. Material Preparation
The initial step in manufacturing shaft couplers is the selection and preparation of raw materials. Common materials include aluminum, stainless steel, and various alloys, chosen for their strength, corrosion resistance, and machinability. The raw materials undergo rigorous inspections to ensure they meet predefined specifications, which is vital for ensuring the durability and performance of the couplers.
2. Forming Techniques
Once the materials are prepared, the next stage is forming. Various techniques are employed depending on the type of coupler being produced:
- Machining: This is the most common method, where raw materials are cut, shaped, and drilled using CNC machines. Precision machining is crucial for achieving the tight tolerances required for proper coupling functionality.
- Casting: For larger couplers, casting techniques may be employed. The molten metal is poured into molds, allowing for complex shapes that would be difficult to achieve through machining alone.
- Forging: This method improves the mechanical properties of the material by reshaping it under high pressure and temperature, resulting in enhanced strength.
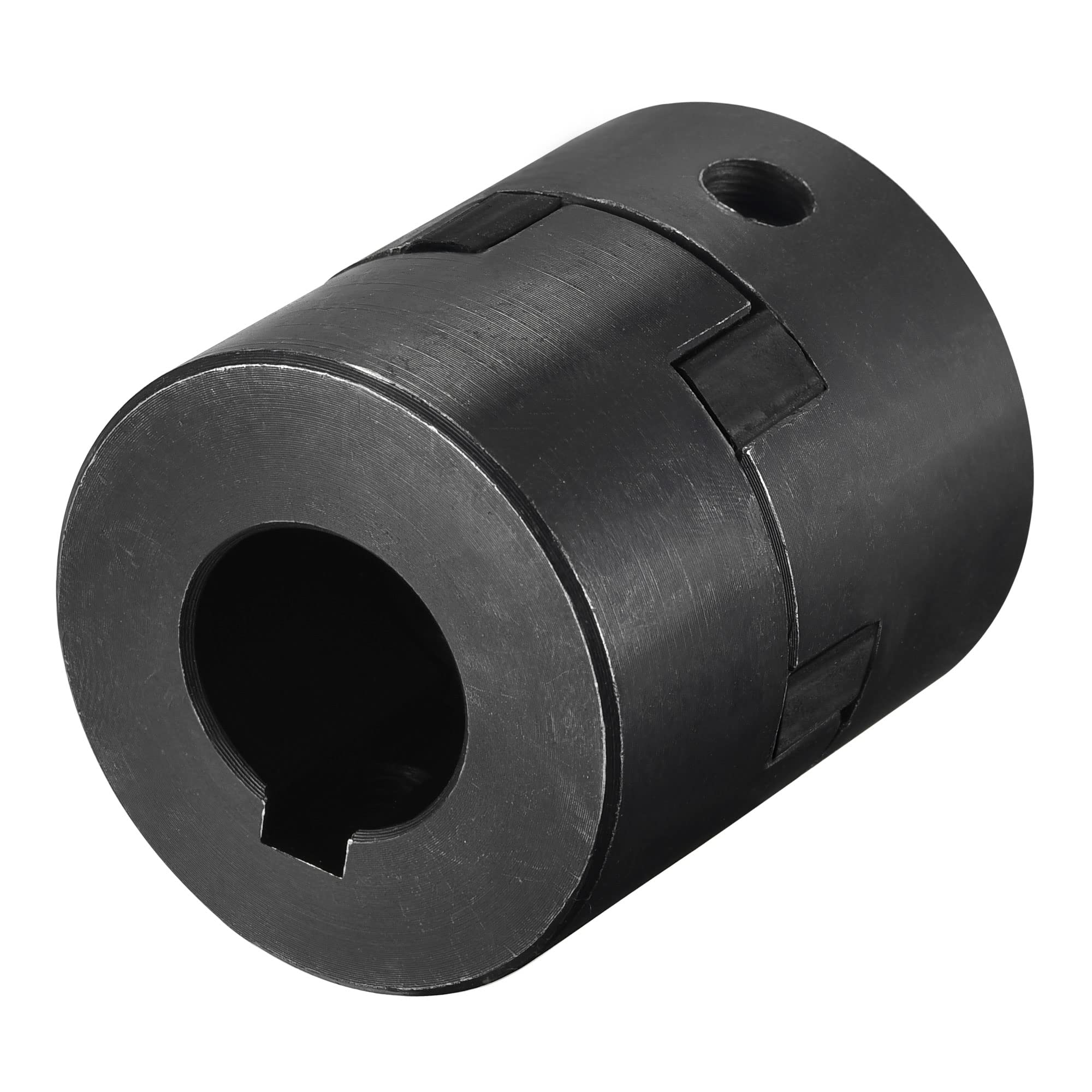
A stock image related to shaft coupler.
3. Assembly
After forming, components are assembled. This may include fitting various parts, such as hubs and sleeves, together. Depending on the design, assembly may involve welding, bolting, or using adhesive bonding. Ensuring proper alignment and fitting during assembly is critical to prevent issues such as vibration or premature wear during operation.
4. Finishing Processes
Finishing processes enhance the performance and aesthetic appeal of the shaft couplers. These may include:
- Surface Treatment: Techniques like anodizing, plating, or powder coating are used to improve corrosion resistance and surface hardness.
- Balancing: Dynamic balancing is performed to ensure that the coupler operates smoothly at high speeds, reducing wear and extending service life.
How Is Quality Assurance Implemented in Shaft Coupler Manufacturing?
Quality assurance is integral to the manufacturing process of shaft couplers. It ensures that products meet international standards and customer expectations. Here are the key elements of quality assurance in this context:
Relevant International Standards for Quality Assurance
International standards such as ISO 9001 play a significant role in ensuring quality in manufacturing processes. ISO 9001 focuses on quality management systems (QMS) that help organizations improve efficiency and customer satisfaction. Additionally, industry-specific certifications, such as CE marking for products sold in Europe and API standards for oil and gas applications, are essential for compliance and marketability.
What Are the Key Quality Control Checkpoints?
Quality control (QC) in shaft coupler manufacturing typically includes several checkpoints throughout the production process:
- Incoming Quality Control (IQC): This involves inspecting raw materials upon arrival to verify they meet specifications. Suppliers should provide material certifications to confirm quality.
- In-Process Quality Control (IPQC): During production, regular inspections are conducted to monitor the manufacturing process, ensuring that any deviations from standards are identified and corrected promptly.
- Final Quality Control (FQC): After production, the finished couplers undergo rigorous testing, including dimensional checks, mechanical property assessments, and functional tests to ensure they meet performance criteria.
What Testing Methods Are Commonly Used for Shaft Couplers?
Several testing methods are employed to validate the quality and performance of shaft couplers:
- Tensile Testing: This measures the strength of materials and ensures they can withstand operational loads.
- Torque Testing: This assesses the coupler’s ability to transmit torque without failure, which is critical for applications involving high rotational speeds.
- Vibration Testing: This identifies any potential issues related to misalignment or imbalance, which can lead to premature wear or failure.
How Can B2B Buyers Verify Supplier Quality Control Processes?
For international B2B buyers, particularly those from Africa, South America, the Middle East, and Europe, verifying a supplier’s quality control processes is essential. Here are practical steps to ensure supplier compliance with quality standards:
Conduct Supplier Audits
Regular supplier audits can provide insights into the manufacturing processes and quality control measures in place. This includes reviewing documentation related to quality management systems and certifications.
Request Quality Reports
Buyers should request quality assurance reports and test results for specific products. This documentation should detail the outcomes of various testing methods and compliance with relevant standards.
Engage Third-Party Inspectors
Utilizing third-party inspection services can provide an unbiased assessment of a supplier’s quality control processes. These inspectors can verify that the manufacturing practices adhere to international standards and industry best practices.
What Are the Quality Control Nuances for International B2B Buyers?
International buyers need to be aware of specific nuances in quality control that can vary by region:
- Compliance with Local Regulations: Different countries may have unique regulations regarding product safety and quality. Understanding these requirements is crucial for avoiding compliance issues.
- Cultural Differences in Quality Standards: Quality expectations can differ based on regional practices. Buyers should communicate their requirements clearly to ensure mutual understanding.
In conclusion, understanding the manufacturing processes and quality assurance mechanisms for shaft couplers is vital for B2B buyers. By focusing on supplier audits, quality certifications, and testing methods, international buyers can make informed decisions and ensure they procure reliable, high-quality products.
Practical Sourcing Guide: A Step-by-Step Checklist for ‘shaft coupler’
The procurement of shaft couplers is a critical process for B2B buyers in various industries, particularly in regions like Africa, South America, the Middle East, and Europe. This guide provides a step-by-step checklist to ensure that buyers make informed decisions when sourcing shaft couplers, optimizing performance while minimizing risks.
Step 1: Define Your Technical Specifications
Before reaching out to suppliers, it is essential to clearly outline your technical requirements. Consider factors such as the type of shaft coupling needed (e.g., rigid, flexible, or chain couplings), the size and material specifications, and the operational environment.
- Torque Requirements: Determine the torque load the coupler will need to handle.
- Alignment Tolerances: Identify acceptable levels of misalignment to ensure compatibility with your machinery.
Step 2: Research and Identify Potential Suppliers
Invest time in researching reputable suppliers who specialize in shaft couplers. Look for companies that have a proven track record in your industry and offer a variety of products.
- Supplier Reputation: Check online reviews, industry forums, and trade publications for feedback on potential suppliers.
- Geographic Location: Consider suppliers based in regions with established manufacturing standards, such as Europe or North America.
Step 3: Evaluate Supplier Certifications and Compliance
Before making a purchase, verify that potential suppliers have the necessary certifications. Compliance with international standards (like ISO, CE, or RoHS) ensures that the products meet quality and safety regulations.
- Quality Assurance: Request documentation that demonstrates adherence to quality management systems.
- Material Certifications: Ensure that the materials used in the couplers are certified for the specific applications you require.
Step 4: Request Detailed Product Specifications
Engage with suppliers to obtain detailed specifications for the couplers you are considering. This information is crucial for determining if the product meets your needs.
- Technical Data Sheets: Ask for datasheets that provide information on load capacities, dimensions, and materials.
- Performance Metrics: Inquire about performance tests and certifications that demonstrate the durability and reliability of the couplers.
Step 5: Assess Pricing and Payment Terms
Once you have identified suitable suppliers, compare pricing structures and payment terms. Keep in mind that the cheapest option may not always provide the best value.
- Bulk Discounts: Ask about pricing for larger orders, which can lead to significant savings.
- Payment Flexibility: Evaluate payment options that align with your cash flow requirements, such as net terms or installment plans.
Step 6: Conduct a Supplier Visit or Virtual Inspection
If possible, arrange a visit to the supplier’s facility or a virtual inspection. This step allows you to assess their manufacturing capabilities and quality control processes firsthand.
- Factory Tour: Observe the production processes, equipment, and quality assurance measures in place.
- Meet the Team: Engage with the engineers or product managers to discuss technical aspects and support.
Step 7: Finalize the Order and Establish Clear Communication
Once you have selected a supplier, finalize your order with clear communication regarding delivery timelines, installation support, and after-sales service.
- Contractual Agreements: Ensure that all terms are documented, including warranties and service commitments.
- Ongoing Communication: Maintain an open line of communication to address any potential issues during the order fulfillment process.
By following this checklist, B2B buyers can effectively navigate the sourcing process for shaft couplers, ensuring that they select the right products for their operational needs while fostering strong supplier relationships.
Comprehensive Cost and Pricing Analysis for shaft coupler Sourcing
What Are the Key Cost Components in Shaft Coupler Manufacturing?
Understanding the cost structure of shaft couplers is essential for international B2B buyers seeking to optimize their procurement strategy. The primary cost components involved in the manufacturing of shaft couplers include:
-
Materials: The choice of materials significantly influences the cost. Common materials include aluminum, stainless steel, and specialized alloys. High-quality materials often come at a premium but can enhance durability and performance.
-
Labor: Labor costs vary by region and depend on the complexity of the manufacturing process. Skilled labor is often required for precision engineering, which can increase costs.
-
Manufacturing Overhead: This encompasses costs related to factory maintenance, utilities, and administrative expenses. Efficient manufacturing processes can help mitigate these costs.
-
Tooling: Initial tooling costs for custom designs can be substantial. However, these costs are typically amortized over larger production runs, making them less impactful on unit costs for high-volume orders.
-
Quality Control (QC): Ensuring compliance with industry standards and certifications adds to the cost but is critical for maintaining product reliability and customer satisfaction.
-
Logistics: Transportation and warehousing costs can vary widely depending on the supplier’s location and the terms of shipment. International shipping can incur additional fees, which should be factored into the total cost.
-
Margin: Suppliers typically apply a markup to cover costs and generate profit. Understanding the supplier’s margin can help buyers negotiate better pricing.
How Do Price Influencers Affect Shaft Coupler Costs?
Several factors influence the pricing of shaft couplers, particularly for international buyers:
-
Volume/MOQ: Bulk orders often qualify for lower per-unit pricing. Establishing a minimum order quantity (MOQ) can lead to significant cost savings.
-
Specifications and Customization: Customized couplers tailored to specific applications may incur additional costs. Buyers should assess whether the added functionality justifies the increased expense.
-
Materials: The choice between standard and premium materials directly impacts pricing. Buyers should evaluate whether the performance benefits of higher-grade materials align with their operational needs.
-
Quality and Certifications: Products that meet international quality standards, such as ISO or CE certifications, typically command higher prices. Buyers should weigh the benefits of certified products against their budgets.
-
Supplier Factors: The supplier’s reputation, location, and production capabilities can affect pricing. Established suppliers may charge more due to their reliability and quality assurance processes.
-
Incoterms: Understanding Incoterms (International Commercial Terms) is crucial for managing logistics costs. Terms like FOB (Free On Board) or CIF (Cost, Insurance, and Freight) can significantly affect the total landed cost of products.
What Are Essential Buyer Tips for Cost-Efficiency?
For international B2B buyers, particularly from regions such as Africa, South America, the Middle East, and Europe, the following tips can enhance cost-efficiency in shaft coupler sourcing:
-
Negotiate Effectively: Leverage your purchasing power by negotiating terms with suppliers. Discuss volume discounts, payment terms, and delivery schedules to find mutually beneficial arrangements.
-
Consider Total Cost of Ownership (TCO): Evaluate the TCO, which includes purchase price, maintenance, and operational costs. Choosing a slightly more expensive coupler that offers better durability can result in lower overall costs.
-
Research Multiple Suppliers: Conduct thorough research and obtain quotes from various suppliers. This not only provides a better understanding of market rates but also gives leverage during negotiations.
-
Stay Informed About Market Trends: Keep an eye on fluctuations in material costs and supply chain dynamics. Being informed can help anticipate price changes and adjust procurement strategies accordingly.
-
Understand Pricing Nuances: Recognize that pricing can vary significantly based on geographic location, market demand, and currency fluctuations. Buyers should account for these factors when making sourcing decisions.
Disclaimer
The prices mentioned in this analysis are indicative and subject to change based on market conditions and individual supplier agreements. Buyers are encouraged to conduct their own due diligence and obtain specific quotes from suppliers.
Alternatives Analysis: Comparing shaft coupler With Other Solutions
The selection of the right coupling technology is crucial for ensuring efficient power transmission in various industrial applications. While shaft couplers are widely utilized, there are viable alternatives that may better suit specific needs. This section compares shaft couplers with two notable alternatives: Flexible Jaw Couplings and Universal Joints. Understanding the strengths and weaknesses of each option will empower international B2B buyers, especially from regions like Africa, South America, the Middle East, and Europe, to make informed decisions.
Comparison Table
Comparison Aspect | Shaft Coupler | Flexible Jaw Couplings | Universal Joints |
---|---|---|---|
Performance | High torque transmission | Good with angular misalignment | Excellent for variable angles |
Cost | Moderate to high depending on type | Generally lower cost | Higher initial investment |
Ease of Implementation | Straightforward installation | Simple installation | More complex due to alignment needs |
Maintenance | Low maintenance | Moderate maintenance | Regular maintenance required |
Best Use Case | Fixed applications with minimal misalignment | Applications with slight misalignment | Applications requiring large angular movements |
What are the Advantages and Disadvantages of Flexible Jaw Couplings?
Flexible jaw couplings are designed to accommodate angular misalignment between shafts while providing good torque transmission. They are typically made from durable materials that can withstand wear and tear, making them a reliable choice for many applications.
Pros:
– Cost-effective solution for moderate misalignment.
– Easy to install and replace, reducing downtime.
– Suitable for applications with vibration damping requirements.
Cons:
– Limited capacity for high torque applications compared to shaft couplers.
– Performance may degrade over time due to wear of the flexible elements.
How Do Universal Joints Compare to Shaft Couplers?
Universal joints are ideal for applications requiring significant angular movement between shafts. They are commonly used in automotive and heavy machinery applications where shafts are not aligned perfectly.
Pros:
– Can handle a wide range of angles and misalignment.
– Highly versatile across different machinery types.
Cons:
– Higher initial investment and installation complexity.
– Requires regular maintenance to ensure optimal performance and longevity.
Conclusion: How Should B2B Buyers Choose the Right Coupling Solution?
When selecting a coupling solution, B2B buyers should consider their specific application requirements, including the degree of misalignment, torque needs, and budget constraints. Shaft couplers may be the best choice for applications with minimal misalignment and high torque demands. Conversely, if the application involves slight misalignment or vibration, flexible jaw couplings may provide a cost-effective and efficient solution. For scenarios involving significant angular movement, universal joints offer unmatched flexibility, albeit at a higher cost and maintenance level. By carefully evaluating these factors, buyers can select the most suitable coupling technology to optimize their machinery’s performance and reliability.
Essential Technical Properties and Trade Terminology for shaft coupler
What Are the Key Technical Properties of Shaft Couplers?
When selecting a shaft coupler for your application, understanding its technical properties is crucial. Here are some essential specifications to consider:
1. Material Grade
The material used in the construction of shaft couplers significantly impacts their performance and durability. Common materials include aluminum for lightweight applications, stainless steel for corrosion resistance, and carbon steel for high strength. Selecting the right material can enhance the lifespan of the coupler, especially in harsh environments typical in industries across Africa, South America, and the Middle East.
2. Torque Capacity
This specification indicates the maximum torque that a coupler can transmit without failure. It is critical for ensuring that the coupler can handle the operational demands of your machinery. Buyers should assess the torque requirements of their applications to avoid premature wear or failure, which can lead to costly downtime.
3. Misalignment Tolerance
Shaft couplers must accommodate misalignment between connected shafts. Misalignment can occur due to thermal expansion or installation errors. Understanding the maximum angular, parallel, and axial misalignment that a coupler can handle helps in selecting a coupler that maintains operational efficiency and minimizes stress on machinery.
4. Bore Size and Type
The bore size and type (e.g., keyed, splined, or straight) determine how well the coupler fits onto the shafts. Accurate bore specifications are essential for ensuring a secure fit and optimal torque transmission. Decisions regarding bore size should be based on the shaft diameter and the application’s specific requirements.
5. Compliance Standards
Ensuring that the coupler meets industry compliance standards, such as RoHS or REACH, is vital for global trade, especially for buyers in Europe and regions with stringent regulations. Compliance indicates that the coupler has been manufactured without hazardous substances and meets safety and environmental guidelines.
What Are Common Trade Terms Used in Shaft Coupler Transactions?
Understanding industry terminology can enhance communication and negotiation in B2B transactions. Here are some essential trade terms related to shaft couplers:
1. OEM (Original Equipment Manufacturer)
An OEM is a company that produces parts or equipment that may be marketed by another manufacturer. In the context of shaft couplers, buyers often seek OEMs to ensure they receive quality products that meet specific application standards.
2. MOQ (Minimum Order Quantity)
This term refers to the smallest quantity of a product that a supplier is willing to sell. Knowing the MOQ is essential for buyers to manage their inventory and budget effectively, especially when importing shaft couplers from international suppliers.
3. RFQ (Request for Quote)
An RFQ is a document that potential buyers send to suppliers to request pricing and availability for specific products, such as shaft couplers. It is a critical step in the procurement process, enabling buyers to compare options and make informed purchasing decisions.
4. Incoterms (International Commercial Terms)
Incoterms are a set of predefined commercial terms published by the International Chamber of Commerce that clarify the responsibilities of buyers and sellers in international transactions. Understanding these terms helps in negotiating shipping costs and responsibilities, which is vital for B2B buyers dealing with international suppliers.
5. Lead Time
Lead time refers to the time it takes from placing an order to receiving the product. It is crucial for planning and inventory management, particularly in industries where downtime can be costly. Buyers should always inquire about lead times when negotiating contracts for shaft couplers.
By familiarizing yourself with these technical properties and trade terms, you can make more informed decisions when sourcing shaft couplers, ultimately enhancing the efficiency and reliability of your operations.
Navigating Market Dynamics and Sourcing Trends in the shaft coupler Sector
What Are the Current Market Dynamics and Key Trends in the Shaft Coupler Sector?
The shaft coupler market is experiencing significant transformation driven by technological advancements and evolving industrial requirements. As industries across Africa, South America, the Middle East, and Europe continue to expand, demand for efficient power transmission solutions is on the rise. Key market drivers include the increasing need for automation, growth in manufacturing sectors, and the expansion of renewable energy projects. Emerging technologies such as IoT and Industry 4.0 are also influencing sourcing trends, allowing for smarter, data-driven decision-making in coupling applications.
International B2B buyers should pay close attention to the trend towards customization in shaft couplers. Manufacturers are increasingly offering bespoke solutions tailored to specific application needs, enhancing performance and reducing downtime. Furthermore, the shift towards digital platforms for sourcing parts is reshaping the procurement landscape, making it easier for buyers to access a wider range of products and suppliers. For example, online marketplaces are becoming critical channels for sourcing shaft couplers, enabling buyers to compare prices and specifications efficiently.
Additionally, the growing emphasis on reducing operational costs is prompting businesses to seek high-performance couplers that offer longevity and reduced maintenance needs. As a result, the demand for high-quality materials and innovative designs is expected to rise, compelling suppliers to invest in research and development to stay competitive. B2B buyers are thus encouraged to evaluate suppliers not only on price but also on product quality, reliability, and support services to ensure optimal value.
How Is Sustainability Shaping Sourcing Practices in the Shaft Coupler Market?
Sustainability has emerged as a key consideration for international B2B buyers in the shaft coupler sector. The environmental impact of manufacturing processes and the growing awareness of climate change are driving companies to adopt more sustainable practices. Ethical sourcing is becoming increasingly important, with businesses prioritizing suppliers that demonstrate a commitment to reducing their carbon footprint and utilizing eco-friendly materials.
Buyers should seek out manufacturers that offer ‘green’ certifications or use sustainable materials in their products. For instance, the use of recycled metals or biodegradable packaging can significantly reduce environmental impact. Additionally, companies that implement energy-efficient manufacturing processes not only contribute to sustainability but also often achieve cost savings that can be passed on to buyers.
Moreover, the demand for transparency in supply chains is growing, with businesses seeking assurances that their suppliers adhere to ethical labor practices and environmental regulations. By prioritizing sustainability and ethical sourcing, B2B buyers can enhance their corporate social responsibility (CSR) profiles, which can be a decisive factor in gaining customer trust and loyalty.
What Is the Evolution of the Shaft Coupler Sector and Its Relevance to B2B Buyers?
The shaft coupler sector has evolved significantly since its inception, adapting to the changing needs of various industries. Originally, couplers were simple mechanical devices designed to connect two shafts for transmitting power. Over the years, advancements in materials science and engineering have led to the development of specialized couplers capable of handling complex tasks, such as compensating for misalignment and absorbing shock loads.
This evolution is particularly relevant for B2B buyers today, as modern couplers are designed with enhanced performance characteristics, such as improved torque capacity and reduced wear. The shift towards high-tech solutions in manufacturing has also made it imperative for buyers to stay informed about the latest innovations in coupler technology. Understanding the historical context of shaft couplers can aid buyers in making informed decisions about which products will best meet their operational needs and provide long-term value.
In summary, the shaft coupler market is characterized by dynamic trends influenced by technological advancements, sustainability, and evolving buyer expectations. By staying abreast of these developments, international B2B buyers can make strategic sourcing decisions that align with their operational goals and ethical standards.
Frequently Asked Questions (FAQs) for B2B Buyers of shaft coupler
-
How do I choose the right shaft coupler for my application?
Selecting the correct shaft coupler involves considering several factors such as the type of machinery, torque requirements, shaft alignment, and environmental conditions. Assess the operational load and misalignment types—angular, parallel, or axial. For example, flexible couplers are suitable for applications with significant misalignment, while rigid couplers work best for precise alignment. Additionally, consider the material of the coupler for durability in your specific environment, such as stainless steel for corrosive conditions. Consult technical specifications and possibly engage with suppliers for tailored advice. -
What are the advantages of using flexible shaft couplers?
Flexible shaft couplers offer several benefits, including the ability to accommodate misalignment between shafts, which is critical for preventing wear and tear on machinery. They can absorb shock loads and vibrations, enhancing the longevity of connected components. Additionally, flexible couplers typically have lower inertia, which can lead to improved responsiveness in dynamic applications. This makes them ideal for industries such as manufacturing and automotive, where precise motion control is essential. -
What is the minimum order quantity (MOQ) for shaft couplers?
The MOQ for shaft couplers can vary significantly based on the supplier and the type of coupler required. Many manufacturers set an MOQ to ensure cost-effectiveness in production and shipping. For international B2B buyers, it’s crucial to discuss MOQ during the initial negotiation phase. Some suppliers might offer flexibility on MOQs for new customers or large orders, while others may have strict limits based on their production capabilities. Always clarify these details to avoid potential disruptions in your supply chain. -
How do I verify the quality of shaft couplers from suppliers?
To ensure the quality of shaft couplers, request certifications such as ISO or other industry-specific standards from potential suppliers. Conducting factory audits or requesting samples can also provide insights into manufacturing processes and product quality. Additionally, reviewing past customer testimonials and performance data can help gauge reliability. If possible, engage in a trial order to evaluate the couplers under actual operating conditions before committing to a larger purchase. -
What payment terms should I expect when sourcing shaft couplers internationally?
Payment terms can vary widely among suppliers and regions. Common practices include payment in advance, 30% deposit with the balance due upon shipment, or net 30/60 days after delivery. For international transactions, consider using secure payment methods such as letters of credit or escrow services to protect your investment. Always negotiate payment terms upfront and ensure they align with your cash flow needs and risk management strategies. -
How can I ensure timely delivery of shaft couplers?
To guarantee timely delivery, establish clear communication with your supplier regarding lead times and shipping methods. It’s advisable to factor in potential delays due to customs clearance, especially for international shipments. Utilize tracking systems to monitor the shipment’s progress and maintain flexibility in your production schedule. Consider working with suppliers who have a robust logistics network and can provide real-time updates on shipping status. -
What customization options are available for shaft couplers?
Many manufacturers offer customization options to meet specific application needs. This can include adjustments in dimensions, material selection, and design features tailored to unique operational conditions. Discuss your requirements with potential suppliers, providing detailed specifications of your application. Custom couplers may involve longer lead times and higher costs, so weigh these factors against the benefits of a tailored solution. -
How do I handle international trade regulations when sourcing shaft couplers?
When sourcing shaft couplers from abroad, familiarize yourself with the trade regulations of both the exporting and importing countries. This includes understanding tariffs, import duties, and compliance with safety standards. Engage with a logistics partner who specializes in international trade to navigate customs processes effectively. Additionally, ensure that all necessary documentation, such as certificates of origin and compliance, are in order to avoid delays and penalties.
Important Disclaimer & Terms of Use
⚠️ Important Disclaimer
The information provided in this guide, including content regarding manufacturers, technical specifications, and market analysis, is for informational and educational purposes only. It does not constitute professional procurement advice, financial advice, or legal advice.
While we have made every effort to ensure the accuracy and timeliness of the information, we are not responsible for any errors, omissions, or outdated information. Market conditions, company details, and technical standards are subject to change.
B2B buyers must conduct their own independent and thorough due diligence before making any purchasing decisions. This includes contacting suppliers directly, verifying certifications, requesting samples, and seeking professional consultation. The risk of relying on any information in this guide is borne solely by the reader.
Strategic Sourcing Conclusion and Outlook for shaft coupler
As the demand for efficient and reliable power transmission solutions continues to rise, the role of strategic sourcing in acquiring high-quality shaft couplers becomes increasingly critical. Buyers from Africa, South America, the Middle East, and Europe must prioritize partnerships with reputable manufacturers who can provide robust and innovative coupling solutions tailored to specific operational needs. By leveraging insights from the market, international B2B buyers can navigate the complexities of sourcing, ensuring that they select couplers that not only meet performance criteria but also align with their long-term business objectives.
Understanding the diverse types of shaft couplers—such as rigid, flexible, and torque-limiting options—enables buyers to make informed decisions that enhance machinery efficiency and reduce maintenance costs. Furthermore, maintaining open lines of communication with suppliers can facilitate better negotiations and support during the implementation phase.
Looking ahead, the evolution of technology in coupling design will likely introduce even more advanced solutions. B2B buyers are encouraged to stay abreast of these developments and consider integrating cutting-edge couplers into their operations. By doing so, they can position themselves competitively in the global marketplace, ensuring sustained growth and operational excellence.