Improve Efficiency: The Complete Spur Gear Guide (2025)
Introduction: Navigating the Global Market for spur gear
In the competitive landscape of industrial manufacturing, sourcing high-quality spur gears can present a significant challenge for B2B buyers. Whether you’re operating in Africa, South America, the Middle East, or Europe, understanding the intricacies of spur gear procurement is essential for optimizing operational efficiency. This guide delves into the diverse types of spur gears, their applications across various industries, and best practices for supplier vetting.
By exploring factors such as material selection, manufacturing processes, and cost considerations, we aim to empower international buyers with the knowledge necessary for informed purchasing decisions. You will discover how to assess potential suppliers effectively, ensuring that they meet your specific requirements for quality and reliability. Additionally, the guide will cover the importance of understanding gear specifications, including pressure angles and tooth profiles, which are crucial for achieving optimal performance in your machinery.
Whether you are a seasoned procurement professional or new to the gear sourcing process, this comprehensive resource will equip you with actionable insights to navigate the global market for spur gears. By addressing common challenges and providing clarity on key aspects of the buying process, we strive to enhance your purchasing strategy and strengthen your supply chain.
Understanding spur gear Types and Variations
Type Name | Key Distinguishing Features | Primary B2B Applications | Brief Pros & Cons for Buyers |
---|---|---|---|
Standard Spur Gears | Simple design, parallel teeth, high precision, low axial thrust | Machinery, automotive, conveyor systems | Pros: Cost-effective, easy to manufacture. Cons: Noisy operation, limited load capacity. |
Ground Spur Gears | Induction hardened, high accuracy, ground tooth finish | Robotics, aerospace, high-performance gearboxes | Pros: High strength and wear resistance. Cons: Higher cost due to manufacturing complexity. |
Profile Shifted Spur Gears | Adjusted tooth profile for strength and center distance flexibility | Custom machinery, precision instruments | Pros: Enhanced strength, customizable. Cons: May require specific tooling for production. |
Plastic Spur Gears | Made from lightweight materials, corrosion-resistant | Consumer products, low-load applications | Pros: Lightweight, cost-effective. Cons: Limited load capacity, lower durability compared to metal. |
High-Load Spur Gears | Designed for heavy loads, thicker teeth, robust materials | Industrial machinery, heavy-duty applications | Pros: High load capacity, durability. Cons: Heavier and more expensive than standard gears. |
What are Standard Spur Gears and When Should You Use Them?
Standard spur gears feature a straightforward design with teeth that are parallel to the axis of rotation. They are widely used in various applications, including machinery, automotive systems, and conveyor belts. Their ease of manufacture makes them a cost-effective choice for many B2B buyers. However, they can produce noise during operation, which may be a concern in noise-sensitive environments.
Why Choose Ground Spur Gears for High-Precision Applications?
Ground spur gears are known for their high accuracy and strength, thanks to their induction-hardened surfaces and ground tooth finish. These gears are ideal for applications that require precision, such as robotics, aerospace, and high-performance gearboxes. While they offer significant advantages in terms of performance, they come at a higher price point, making them suitable for buyers who prioritize quality over cost.
How Do Profile Shifted Spur Gears Enhance Performance?
Profile shifted spur gears feature an adjusted tooth profile that allows for minor changes in center distance and enhances tooth strength. They are particularly useful in custom machinery and precision instruments where adjustments are necessary. While they provide customization options, buyers should be aware that they may require specific tooling for production, which can increase lead times and costs.
What are the Advantages of Using Plastic Spur Gears?
Plastic spur gears are lightweight and corrosion-resistant, making them suitable for consumer products and low-load applications. They are an excellent choice for companies looking to reduce weight and cost in their designs. However, buyers should consider the limited load capacity and durability compared to metal gears, particularly in high-stress environments.
When to Invest in High-Load Spur Gears for Heavy-Duty Applications?
High-load spur gears are designed to handle significant loads and feature thicker teeth and robust materials. They are commonly used in industrial machinery and heavy-duty applications where durability is critical. While they provide excellent load capacity, they are heavier and more expensive than standard gears, which may affect the overall design and cost of projects for B2B buyers.
Key Industrial Applications of spur gear
Industry/Sector | Specific Application of Spur Gear | Value/Benefit for the Business | Key Sourcing Considerations for this Application |
---|---|---|---|
Automotive | Transmission systems | Efficient power transfer, enhancing vehicle performance | Material durability, precision manufacturing, and compatibility with existing systems |
Industrial Machinery | Conveyor systems | Streamlined operations, reduced downtime | Load capacity, size specifications, and environmental resistance |
Renewable Energy | Wind turbine gearboxes | Improved energy conversion efficiency | Corrosion resistance, weight considerations, and high torque handling |
Agriculture | Tractors and harvesting equipment | Enhanced reliability and performance in tough conditions | Customization options, material selection, and maintenance ease |
Robotics | Automated assembly lines | Increased automation efficiency and precision | Precision engineering, backlash specifications, and ease of integration |
How Are Spur Gears Used in the Automotive Industry?
In the automotive sector, spur gears are integral to transmission systems, enabling efficient power transfer from the engine to the wheels. They help optimize vehicle performance by ensuring smooth gear shifts and enhancing fuel efficiency. International B2B buyers, particularly in regions like Europe and the Middle East, should prioritize sourcing gears made from durable materials to withstand high stress and wear. Precision manufacturing is crucial to ensure compatibility with various transmission designs, thus minimizing operational issues.
What Role Do Spur Gears Play in Industrial Machinery?
Spur gears are widely used in conveyor systems within industrial machinery, facilitating the movement of materials across production lines. Their design allows for a direct transfer of motion, which is essential for maintaining a consistent workflow. For buyers in Africa and South America, sourcing gears that can handle heavy loads and resist environmental factors such as dust and moisture is vital. Additionally, the ability to customize gear sizes and configurations can significantly enhance operational efficiency.
How Are Spur Gears Beneficial in Renewable Energy Applications?
In the renewable energy sector, particularly in wind turbine gearboxes, spur gears play a critical role in converting wind energy into electrical energy. Their robust design allows for high torque handling, which is essential for the efficient operation of turbines. Buyers from Europe, where renewable energy initiatives are prominent, should consider sourcing gears that offer corrosion resistance and high efficiency to ensure longevity and performance in various weather conditions.
Why Are Spur Gears Important in Agriculture?
Spur gears are commonly found in agricultural machinery, such as tractors and harvesting equipment, where they help transmit power to various components. Their reliability in harsh environments ensures that agricultural operations can proceed without unexpected downtime. B2B buyers in regions like Africa, where agriculture is a significant industry, should focus on sourcing gears that offer high durability and ease of maintenance, as these factors contribute to reduced operational costs and increased productivity.
How Do Spur Gears Enhance Robotics Automation?
In robotics, spur gears are essential for automated assembly lines, providing precise motion control for robotic arms and other components. Their ability to maintain accuracy during operation increases overall efficiency in manufacturing processes. For international buyers, especially from South America and Europe, sourcing gears with specific backlash tolerances and integration capabilities is crucial for ensuring seamless operation within robotic systems. This attention to detail can lead to enhanced automation performance and reduced error rates.
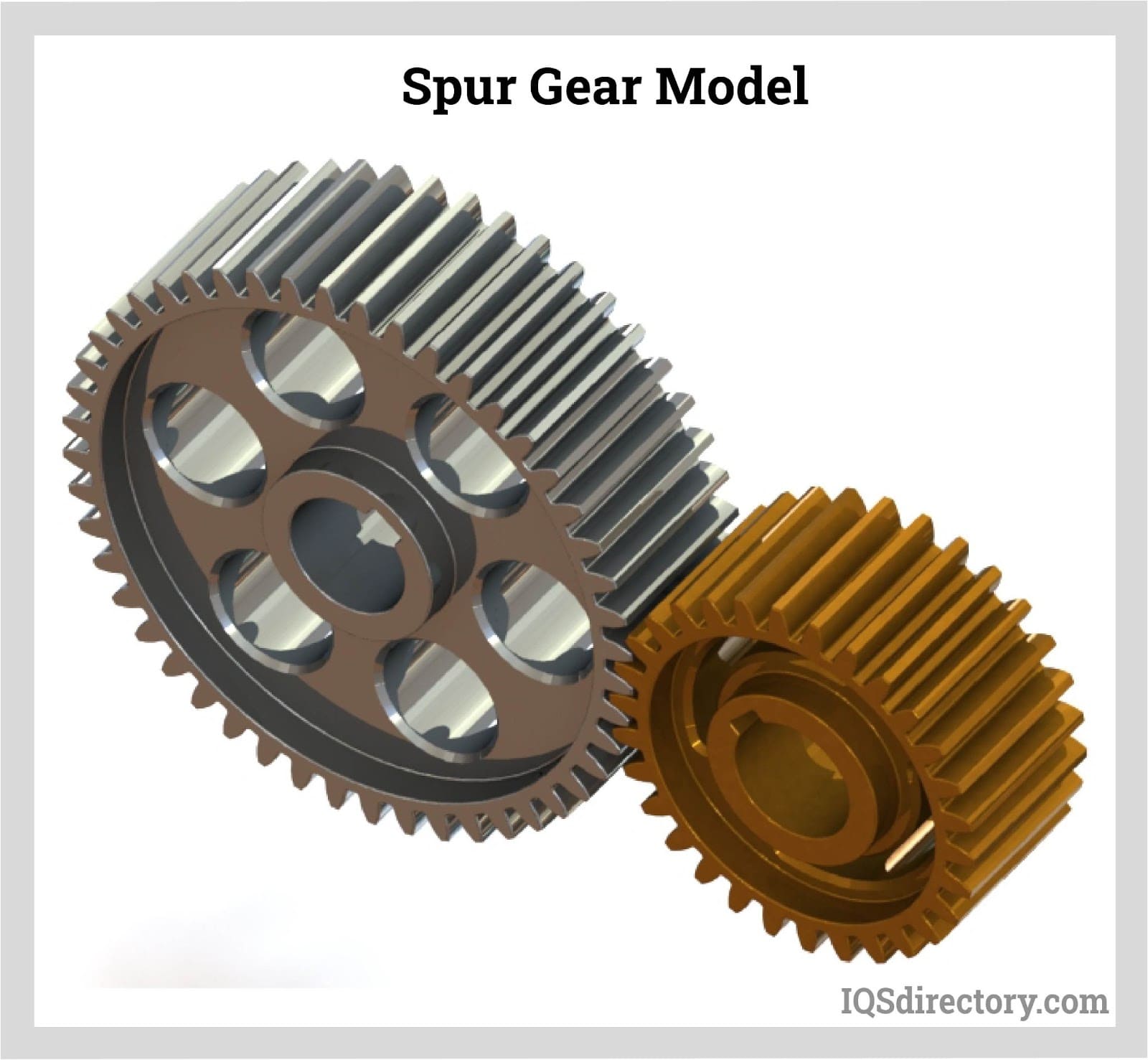
A stock image related to spur gear.
3 Common User Pain Points for ‘spur gear’ & Their Solutions
Scenario 1: Difficulty in Selecting the Right Material for Spur Gears
The Problem: One of the most common challenges faced by B2B buyers is choosing the appropriate material for spur gears that can withstand specific operational conditions. For instance, a manufacturer in the UAE may require spur gears that are resistant to high temperatures and corrosive environments, yet may not have the expertise to discern which material—be it steel, brass, or plastic—will provide the necessary durability and performance. This lack of clarity can lead to premature gear failure, increased downtime, and ultimately, higher costs.
The Solution: To address this issue, it is crucial for buyers to conduct a thorough analysis of the operating environment and the specific requirements of their application. Begin by evaluating factors such as load capacity, environmental conditions (like humidity or exposure to chemicals), and desired lifespan. For example, if high corrosion resistance is needed, stainless steel or brass may be appropriate choices, while polyacetal could be considered for lower-load applications where weight reduction is key. Furthermore, partnering with reputable suppliers who can provide material specifications and performance data will aid in making informed decisions. Buyers should also consider custom solutions that may involve the combination of materials to meet specific application requirements.
Scenario 2: Managing Noise and Vibration Issues in Gear Operation
The Problem: Noise and vibration can significantly impact the efficiency and longevity of machinery employing spur gears. A manufacturing plant in South America might find that their gear systems generate excessive noise during operation, which not only affects the working environment but can also lead to mechanical wear and tear. This scenario often arises from improper gear alignment, excessive backlash, or the use of gears with unsuitable tooth profiles.
The Solution: To mitigate noise and vibration, it is essential to focus on precise gear alignment and appropriate backlash settings. Buyers should ensure that the installation process adheres to manufacturer guidelines, using alignment tools to minimize misalignment. Additionally, selecting spur gears with an involute tooth profile can help reduce noise levels, as this design allows for smoother engagement between teeth. It’s also advisable to consider gears with lower tooth counts for applications requiring higher speed, as they typically generate less noise. Regular maintenance checks can identify issues early, preventing excessive wear and promoting a quieter operational environment.
Scenario 3: Challenges in Sourcing Custom Spur Gears
The Problem: Global B2B buyers often face hurdles when sourcing custom spur gears tailored to specific project requirements. For instance, a company in Europe might require gears with unique dimensions and specifications that are not readily available in standard inventories. This situation can lead to production delays, increased costs, and frustration due to the lack of suitable off-the-shelf options.
The Solution: To overcome sourcing challenges, it is beneficial to establish relationships with suppliers who specialize in custom gear manufacturing. Buyers should clearly communicate their specifications, including dimensions, materials, and performance requirements, to facilitate accurate quotations. Utilizing CAD software to create detailed drawings can enhance clarity and minimize misunderstandings. Additionally, it’s wise to engage suppliers early in the design process, as they can offer valuable insights on manufacturability and may suggest alternative materials or designs that could reduce costs and lead times. Finally, leveraging online platforms that connect buyers with multiple suppliers can provide competitive options and expedite the sourcing process.
Strategic Material Selection Guide for spur gear
What Are the Key Properties of Common Materials Used for Spur Gears?
When selecting materials for spur gears, it is essential to consider their properties, as they significantly influence performance, durability, and application suitability. Here, we analyze four commonly used materials: Carbon Steel, Stainless Steel, Polyacetal, and Brass.
How Does Carbon Steel Perform as a Spur Gear Material?
Key Properties: Carbon steel, particularly grades like C45 and SCM440, offers excellent tensile strength and hardness. It can withstand high loads and has good wear resistance, making it suitable for high-torque applications. However, it is susceptible to corrosion if not properly treated.
Pros & Cons: The primary advantage of carbon steel is its high strength-to-weight ratio, which contributes to durability. It is also relatively cost-effective compared to other materials. On the downside, carbon steel requires surface treatments like hardening or coating to enhance corrosion resistance, which can complicate manufacturing processes.
Impact on Application: Carbon steel is ideal for applications in machinery where high load-bearing capacity is required, such as in automotive or industrial equipment. However, it may not be suitable for environments with high humidity or corrosive substances unless treated.
Considerations for International Buyers: Buyers from regions like Europe and the Middle East should ensure compliance with standards such as DIN or ASTM, particularly regarding hardness and tensile strength specifications.
What Advantages Does Stainless Steel Offer for Spur Gears?
Key Properties: Stainless steel, such as 1.4305, is known for its excellent corrosion resistance and durability. It maintains strength at elevated temperatures and can withstand harsh environments.
Pros & Cons: The key advantage of stainless steel is its resistance to rust and corrosion, making it suitable for applications in food processing, pharmaceuticals, or marine environments. However, it is generally more expensive than carbon steel and can be more challenging to machine.
Impact on Application: Stainless steel spur gears are ideal for applications where hygiene and corrosion resistance are critical. They are commonly used in food processing equipment and medical devices.
Considerations for International Buyers: Compliance with international standards like ISO and ASTM is crucial for buyers in Europe and South America. Additionally, understanding the specific grades and their properties can aid in selecting the right material for the application.
Why Choose Polyacetal for Spur Gears?
Key Properties: Polyacetal (POM) is a thermoplastic with excellent dimensional stability and low friction properties. It is lightweight and resistant to moisture, making it suitable for various applications.
Pros & Cons: The main advantage of polyacetal is its low friction coefficient, which reduces wear and tear. It is also resistant to many chemicals. However, it may not handle high loads as effectively as metals, limiting its use in heavy-duty applications.
Impact on Application: Polyacetal is ideal for applications requiring lightweight and low-friction components, such as in automotive and consumer electronics. However, it may not be suitable for high-temperature environments.
Considerations for International Buyers: Buyers should be aware of the material’s compliance with food safety standards if used in food-related applications, especially in Europe and the Middle East.
What Role Does Brass Play in Spur Gear Applications?
Key Properties: Brass, particularly Ms58, offers good machinability and corrosion resistance. It has decent strength and is often used in applications requiring electrical conductivity.
Pros & Cons: The advantage of brass is its excellent machinability and aesthetic appeal, making it suitable for decorative applications. However, it is generally weaker than steel and may not be suitable for high-torque applications.
Impact on Application: Brass spur gears are commonly used in low-load applications, such as in clocks and small machinery. They are also preferred in applications requiring electrical conductivity.
Considerations for International Buyers: Buyers should ensure that the brass used complies with relevant standards, such as ASTM B16 for copper alloys, particularly in regions like the Middle East and Europe.
Summary Table of Spur Gear Materials
Material | Typical Use Case for spur gear | Key Advantage | Key Disadvantage/Limitation | Relative Cost (Low/Med/High) |
---|---|---|---|---|
Carbon Steel | High-torque machinery | High strength-to-weight ratio | Susceptible to corrosion without treatment | Medium |
Stainless Steel | Food processing, medical devices | Excellent corrosion resistance | More expensive and harder to machine | High |
Polyacetal | Automotive, consumer electronics | Low friction and lightweight | Limited load-bearing capacity | Medium |
Brass | Clocks, low-load machinery | Good machinability and corrosion resistance | Weaker than steel, not suitable for high-torque | Medium |
In-depth Look: Manufacturing Processes and Quality Assurance for spur gear
What Are the Typical Manufacturing Processes for Spur Gears?
Manufacturing spur gears involves several critical stages, each designed to ensure precision and quality. Understanding these processes can help B2B buyers make informed decisions when selecting suppliers.
How Is Material Prepared for Spur Gear Manufacturing?
The first step in spur gear manufacturing is material preparation. Common materials include various grades of steel (e.g., C45, 16MnCr5), plastics (like acetal and polyketone), and brass. Each material is chosen based on the desired mechanical properties, such as strength, wear resistance, and cost-effectiveness.
- Material Selection: Buyers should consider the application of the spur gear and environmental factors when selecting materials. For example, stainless steel is ideal for corrosive environments, while carbon steels are suitable for general applications.
- Material Inspection: Prior to processing, materials undergo inspection to ensure they meet specified grades and tolerances. This may include checking for impurities, dimensions, and mechanical properties.
What Forming Techniques Are Commonly Used in Spur Gear Production?
Once the material is prepared, the next stage is forming, which shapes the raw material into gear blanks.
- Machining: This involves cutting the gear teeth into the blanks using processes such as hobbing, shaping, or broaching. Hobbing is the most common method due to its efficiency and ability to produce high-precision teeth.
- Casting and Forging: For larger production runs, casting or forging may be utilized. These methods can create complex shapes and reduce material waste.
- Heat Treatment: After forming, gears often undergo heat treatment processes like carburizing or induction hardening to enhance hardness and wear resistance. This step is critical for ensuring longevity and performance.
How Are Spur Gears Assembled and Finished?
The assembly and finishing stages refine the spur gears for operational readiness.
- Assembly: While spur gears are typically sold individually, they may be assembled into gearboxes or other machinery components. During assembly, precise alignment is crucial to minimize backlash and ensure smooth operation.
- Finishing: This stage involves processes such as grinding or polishing to achieve the final dimensions and surface finish. Ground gears offer superior accuracy and reduced noise during operation. Buyers should inquire about the finishing techniques used to ensure they meet application requirements.
What Quality Assurance Practices Are Essential for Spur Gears?
Quality assurance (QA) is critical in ensuring that spur gears meet international and industry-specific standards. Understanding these practices helps buyers assess supplier reliability.
Which International Standards Should Spur Gear Manufacturers Adhere To?
International standards such as ISO 9001 provide a framework for quality management systems that ensure consistent product quality. Additionally, industry-specific certifications, such as CE marking for European markets or API standards for oil and gas applications, are essential for compliance.
- ISO 9001: This standard focuses on meeting customer requirements and enhancing satisfaction through effective quality management systems.
- CE Marking: Required for products sold in the European Economic Area, it indicates conformity with health, safety, and environmental protection standards.
What Are the Key Quality Control Checkpoints in Spur Gear Manufacturing?
Quality control (QC) checkpoints are integral to maintaining product integrity throughout the manufacturing process. B2B buyers should be familiar with the following checkpoints:
- Incoming Quality Control (IQC): This involves inspecting raw materials upon receipt to ensure they meet specified standards before production begins.
- In-Process Quality Control (IPQC): Throughout the manufacturing stages, periodic checks are performed to identify any deviations from specifications and implement corrective actions promptly.
- Final Quality Control (FQC): Before shipment, gears undergo rigorous testing and inspection to verify that they meet all required specifications and standards.
What Common Testing Methods Are Employed for Spur Gear Quality Assurance?
Several testing methods are used to ensure the performance and reliability of spur gears:
- Dimensional Inspection: Verifies that the gear dimensions adhere to specified tolerances using tools like calipers and micrometers.
- Hardness Testing: Measures the hardness of the gear material, ensuring it meets requirements for wear resistance.
- Load Testing: Assesses the gear’s ability to handle specified loads without failure, simulating real-world operating conditions.
How Can B2B Buyers Verify Supplier Quality Control?
For international B2B buyers, particularly those from regions like Africa, South America, the Middle East, and Europe, verifying a supplier’s quality control processes is crucial.
What Steps Can Buyers Take to Ensure Supplier Compliance with Quality Standards?
- Supplier Audits: Conducting regular audits of potential suppliers can help ensure they adhere to quality standards and practices. This includes reviewing their manufacturing processes, quality management systems, and compliance with international standards.
- Requesting Quality Reports: Buyers should request documentation of quality assurance practices, including inspection reports, certifications, and test results. This transparency helps establish trust and accountability.
- Third-Party Inspections: Engaging third-party inspection services can provide an unbiased evaluation of the supplier’s products and processes, offering additional assurance of quality.
What Nuances Should International Buyers Consider Regarding Quality Control?
B2B buyers must be aware of regional differences in manufacturing practices and standards. For instance, suppliers in Europe may be more accustomed to stringent regulations compared to those in some African or South American countries. Buyers should also consider:
- Cultural Differences: Understanding cultural nuances can facilitate better communication and collaboration with suppliers.
- Regulatory Compliance: Familiarity with local regulations and compliance requirements can help buyers avoid potential legal issues and ensure smooth transactions.
By comprehensively understanding the manufacturing processes and quality assurance practices for spur gears, international B2B buyers can make informed decisions that align with their operational needs and standards.
Practical Sourcing Guide: A Step-by-Step Checklist for ‘spur gear’
Introduction
Sourcing spur gears effectively is vital for international B2B buyers, particularly those operating in Africa, South America, the Middle East, and Europe. This checklist serves as a practical guide to help you navigate the complexities of procuring spur gears, ensuring you make informed decisions that meet your operational needs and compliance standards.
Step 1: Define Your Technical Specifications
Before initiating the procurement process, clearly outline the technical specifications required for your spur gears. This includes parameters such as gear material (e.g., steel, plastic), dimensions (module, teeth count), and operational requirements (e.g., load capacity, torque). Precise specifications will streamline the sourcing process and help in communicating effectively with suppliers.
- Material Requirements: Consider factors like durability and environmental conditions that the gears will face.
- Performance Metrics: Identify the maximum torque and speed to ensure compatibility with your machinery.
Step 2: Research and Identify Potential Suppliers
Conduct thorough research to identify reputable suppliers who specialize in spur gears. Utilize industry-specific directories, trade shows, and online marketplaces to compile a list of potential partners.
- Supplier Background: Look for suppliers with a proven track record in your specific industry.
- Local vs. International Suppliers: Consider suppliers from your region to reduce shipping costs and lead times.
Step 3: Evaluate Supplier Certifications and Compliance
It’s crucial to verify that your potential suppliers adhere to industry standards and certifications relevant to spur gears. This ensures the quality and reliability of the products you will receive.
- ISO Certifications: Look for ISO 9001 or similar certifications that indicate a commitment to quality management.
- Regulatory Compliance: Ensure that the gears comply with local regulations in your operating regions, such as CE marking in Europe.
Step 4: Request Samples and Test Performance
Before making a bulk purchase, request samples of the spur gears to evaluate their performance and quality. Testing the samples can save you from costly mistakes.
- Performance Testing: Assess the gears for noise levels, durability under load, and fit with your existing machinery.
- Quality Assurance: Use samples to verify that the manufacturing process meets your specifications.
Step 5: Negotiate Pricing and Terms
Once you have identified a suitable supplier, engage in negotiations to discuss pricing, payment terms, and delivery schedules.
- Volume Discounts: Inquire about discounts for bulk purchases or long-term contracts.
- Payment Options: Understand the payment terms, including upfront costs, milestones, and final payments.
Step 6: Finalize Contracts and Ensure Clear Communication
After negotiations, finalize contracts that clearly outline all terms, including specifications, delivery timelines, and penalties for non-compliance. Clear communication is essential to avoid misunderstandings.
- Contract Clauses: Include clauses for warranties, returns, and maintenance support.
- Regular Updates: Establish a communication plan for updates during the manufacturing and delivery phases.
Step 7: Monitor Delivery and Quality Assurance
Upon receiving the spur gears, conduct a thorough inspection to ensure they meet the agreed specifications and quality standards.
- Quality Control Checks: Implement quality assurance processes to verify the accuracy of dimensions and material quality.
- Feedback Loop: Maintain a feedback mechanism with the supplier for continuous improvement in future orders.
Following this comprehensive checklist will enhance your sourcing strategy for spur gears, ensuring a successful procurement process that meets your operational demands and quality standards.
Comprehensive Cost and Pricing Analysis for spur gear Sourcing
What Are the Key Cost Components in Spur Gear Manufacturing?
When sourcing spur gears, understanding the cost structure is crucial for international B2B buyers. The primary cost components include:
-
Materials: The choice of materials significantly impacts pricing. Common materials such as steel (e.g., C45, 16MnCr5) and plastics (e.g., POM, PA 12) vary in cost. High-grade materials typically enhance durability and performance but come at a higher price.
-
Labor: Labor costs can vary by region, with countries in Europe often having higher labor costs compared to those in Africa or South America. Skilled labor is essential for precision manufacturing, particularly for gears requiring intricate designs.
-
Manufacturing Overhead: This includes costs associated with factory maintenance, utilities, and indirect labor. The overhead rate can vary significantly based on the manufacturing facility’s location and efficiency.
-
Tooling: Initial tooling costs are crucial for custom or high-precision gears. Advanced machinery and tooling setups can lead to higher upfront costs but may reduce per-unit costs for large orders.
-
Quality Control (QC): Rigorous QC processes ensure that gears meet specified tolerances and performance standards. The costs associated with testing and certification can add to the overall price, especially for gears used in critical applications.
-
Logistics: Transportation and shipping costs are influenced by the distance from the supplier to the buyer, the mode of transport, and any tariffs or import duties. Buyers should consider Incoterms, as they dictate who bears the shipping costs and risks.
-
Margin: Suppliers typically add a profit margin to cover their expenses and risks. This margin can vary widely based on market conditions and competition.
What Factors Influence Spur Gear Pricing for International Buyers?
Several factors can influence the pricing of spur gears, especially for international B2B transactions:
-
Volume/MOQ (Minimum Order Quantity): Larger orders often attract volume discounts, reducing the per-unit cost. Buyers should negotiate MOQs that align with their needs while leveraging bulk pricing.
-
Specifications and Customization: Custom gears tailored to specific applications may incur additional costs. Standardized products are generally more cost-effective. Buyers should clearly define their requirements to avoid unexpected expenses.
-
Material Quality and Certifications: Higher quality materials and certifications (like ISO standards) can increase costs but are essential for applications where reliability is critical. Buyers should weigh the benefits of certification against the associated costs.
-
Supplier Factors: The supplier’s reputation, production capacity, and geographic location can all influence pricing. Suppliers with a strong track record may charge a premium, reflecting their reliability and quality assurance.
-
Incoterms: Understanding the chosen Incoterms (e.g., FOB, CIF) is vital for budgeting. These terms define the responsibilities of buyers and sellers in terms of shipping costs and risks.
How Can International B2B Buyers Optimize Their Spur Gear Sourcing Costs?
To maximize cost-efficiency in sourcing spur gears, buyers should consider the following strategies:
-
Negotiate Terms: Engage in discussions with suppliers to negotiate better terms, including pricing, payment terms, and shipping costs. Building a long-term relationship can lead to more favorable conditions.
-
Evaluate Total Cost of Ownership (TCO): Assess the TCO, which includes initial purchase price, maintenance, and operational costs. Investing in higher-quality gears may lead to lower maintenance costs and improved performance over time.
-
Be Aware of Pricing Nuances: Understand that prices can fluctuate based on global market trends, exchange rates, and geopolitical factors. Staying informed about market conditions can aid in timing purchases more strategically.
-
Conduct Supplier Audits: Regular audits of suppliers can ensure compliance with quality standards and help identify areas for cost reduction. This practice can also foster transparency and trust between buyers and suppliers.
Disclaimer on Pricing
Prices for spur gears can vary widely based on the factors discussed above. It is essential for buyers to obtain detailed quotes from multiple suppliers and consider all associated costs to make informed purchasing decisions. Always request updated pricing and terms to reflect current market conditions.
Alternatives Analysis: Comparing spur gear With Other Solutions
Understanding Alternative Solutions to Spur Gears
When considering mechanical systems, spur gears are often a go-to choice for transmitting motion between parallel shafts. However, alternative solutions exist that may better suit specific applications or requirements. This section will compare spur gears with helical gears and worm gears, highlighting their performance, cost, ease of implementation, maintenance, and best use cases. Understanding these alternatives can help international B2B buyers make informed decisions tailored to their operational needs.
Comparison Table of Spur Gears and Alternatives
Comparison Aspect | Spur Gear | Helical Gear | Worm Gear |
---|---|---|---|
Performance | High efficiency, low backlash | Higher load capacity, quieter | High torque at low speeds |
Cost | Generally lower | Higher due to complex design | Moderate, depending on gear ratio |
Ease of Implementation | Simple design, easy to install | More complex, requires precision | Requires precise alignment |
Maintenance | Low maintenance needs | Moderate, requires lubrication | Higher due to wear on worm gear |
Best Use Case | General machinery, conveyors | Automotive, high-speed applications | Heavy-duty applications, reducers |
In-Depth Analysis of Alternative Solutions
What Are the Advantages and Disadvantages of Helical Gears?
Helical gears feature teeth that are cut at an angle to the axis of rotation, resulting in smoother engagement between gears. This design allows for higher load capacities and quieter operation compared to spur gears. However, they are generally more expensive due to their complex manufacturing processes and require precise installation to avoid misalignment. Helical gears are often used in automotive applications and machinery that demands high-speed operation, making them ideal for sectors where performance and noise levels are critical.
When Should You Consider Worm Gears?
Worm gears consist of a worm (screw) that meshes with a gear (wheel), providing high torque and significant reduction ratios in a compact design. They excel in applications requiring high torque at low speeds, such as in conveyor systems and heavy machinery. However, they can be more challenging to maintain due to wear on the worm and require regular lubrication to function efficiently. The cost can also vary based on the gear ratio, making it essential for buyers to evaluate their specific application needs against the potential long-term maintenance costs.
How to Choose the Right Solution for Your Needs
When selecting between spur gears, helical gears, and worm gears, B2B buyers should consider their specific application requirements. If the focus is on cost-effectiveness and simplicity, spur gears may be the best choice. For applications requiring higher efficiency and quieter operation, helical gears could be more appropriate. Conversely, if the application demands high torque and compact design, worm gears might be the ideal solution.
Ultimately, understanding the unique advantages and limitations of each gear type will empower international buyers from regions like Africa, South America, the Middle East, and Europe to make informed decisions that enhance their operational efficiency and align with their budgetary constraints.
Essential Technical Properties and Trade Terminology for spur gear
What Are the Key Technical Properties of Spur Gears?
When considering the procurement of spur gears, understanding their technical properties is vital for making informed decisions. Here are some essential specifications that international B2B buyers should consider:
1. Material Grade: How Does It Affect Durability and Performance?
Spur gears are commonly made from various materials, including steel, plastic, and brass. The choice of material significantly impacts the gear’s durability, wear resistance, and overall performance. For example, C45 steel is often used for its strength and toughness, while POM (Acetal Homopolymer) is preferred for applications requiring low friction. Selecting the right material can enhance the gear’s lifespan and reduce maintenance costs.
2. Module: Why Is It Crucial for Gear Compatibility?
The module indicates the size of the gear teeth and is a critical factor in ensuring compatibility between meshing gears. It is defined as the ratio of the pitch diameter to the number of teeth. A consistent module across gear sets is essential to prevent failures and ensure smooth operation. For international buyers, understanding module specifications helps in selecting gears that will seamlessly integrate into existing machinery.
3. Pressure Angle: How Does It Impact Load Capacity?
The pressure angle refers to the angle at which the teeth of the gears engage. Common values are 20 degrees and 14.5 degrees. A higher pressure angle can increase load capacity but may also lead to increased noise. Buyers should consider the operational environment—higher angles may be suitable for heavy-duty applications, while lower angles can be advantageous for quieter operation.
4. Tolerance: What Role Does Precision Play?
Tolerance specifies the allowable deviation in dimensions, which is crucial for ensuring proper fit and functionality. For spur gears, tighter tolerances generally indicate higher precision, which can be essential in high-speed or high-load applications. Understanding tolerance levels is particularly important for B2B buyers looking to maintain quality standards in their products.
5. Backlash: Why Is It Important for Gear Performance?
Backlash is the slight play between meshing gears that allows for smooth operation and lubrication. While some backlash is necessary, excessive play can lead to increased wear and noise. Buyers should evaluate the acceptable backlash levels for their applications to ensure optimal gear performance and longevity.
What Are Common Trade Terminology and Their Importance in B2B Transactions?
Familiarity with industry jargon can facilitate better communication and negotiation. Here are some common terms relevant to spur gear procurement:
1. OEM (Original Equipment Manufacturer): What Does It Mean for Buyers?
An OEM is a company that produces parts or equipment that may be marketed by another manufacturer. Understanding this term helps buyers identify reliable suppliers who can provide components that meet specific quality standards and specifications.
2. MOQ (Minimum Order Quantity): How Does It Affect Your Purchasing Strategy?
MOQ refers to the minimum number of units a supplier is willing to sell. This term is crucial for budgeting and inventory management, particularly for international buyers who may face shipping costs that make small orders impractical.
3. RFQ (Request for Quotation): How to Use It Effectively?
An RFQ is a document sent to suppliers to request pricing and terms for specific products. When submitting an RFQ for spur gears, it’s essential to include detailed specifications and quantities to receive accurate quotes. This process can streamline procurement and help in comparing different suppliers.
4. Incoterms: How Do They Impact International Shipping?
Incoterms are international commercial terms that define the responsibilities of buyers and sellers in international transactions. Understanding these terms helps buyers clarify who is responsible for shipping, insurance, and duties, thereby preventing misunderstandings and disputes.
5. Lead Time: Why Is It Critical for Planning?
Lead time refers to the time taken from placing an order to receiving the products. Knowing the lead time for spur gears is essential for production planning and inventory management, especially in industries where downtime can be costly.
By grasping these technical properties and trade terminologies, international B2B buyers can make informed decisions, ensuring that their investments in spur gears align with their operational needs and budgetary constraints.
Navigating Market Dynamics and Sourcing Trends in the spur gear Sector
What Are the Current Market Trends Influencing Spur Gear Sourcing?
The spur gear market is witnessing dynamic shifts driven by several global factors. Increased automation across industries—particularly in manufacturing, automotive, and renewable energy—is a significant contributor to the growing demand for high-precision gear systems. For international B2B buyers, especially those from regions like Africa, South America, the Middle East, and Europe, understanding these trends is crucial for strategic sourcing.
Technological advancements such as 3D printing and CNC machining are enabling manufacturers to produce gears with intricate designs and superior specifications, enhancing customization options for buyers. Additionally, the rise of Industry 4.0 has led to the integration of IoT technologies in manufacturing processes, allowing real-time monitoring and optimization of gear performance. This trend is particularly relevant for buyers looking to invest in reliable, efficient gear systems that can be seamlessly integrated into smart machinery.
Moreover, the market is experiencing a shift towards localized sourcing to mitigate supply chain disruptions. Buyers are increasingly seeking suppliers closer to their operational bases, which helps reduce lead times and transportation costs. This trend is especially prominent in Europe and the Middle East, where economic conditions are fostering regional partnerships. Understanding these market dynamics will enable buyers to make informed decisions and leverage emerging opportunities in spur gear procurement.
How Can Sustainability and Ethical Sourcing Impact Spur Gear Procurement?
Sustainability and ethical sourcing have become paramount in the spur gear sector. As environmental regulations tighten globally, buyers are increasingly pressured to ensure that their supply chains are environmentally friendly. The production of spur gears can have significant environmental impacts, particularly concerning energy consumption and waste generation. Therefore, sourcing from manufacturers who prioritize eco-friendly practices is essential.
Buyers should look for suppliers who offer ‘green’ certifications and use sustainable materials in their products. For instance, spur gears made from recycled metals or bio-based polymers can significantly reduce the carbon footprint associated with manufacturing processes. Additionally, companies that adopt energy-efficient technologies and waste reduction strategies contribute positively to sustainable development goals, making them more attractive partners for B2B buyers.
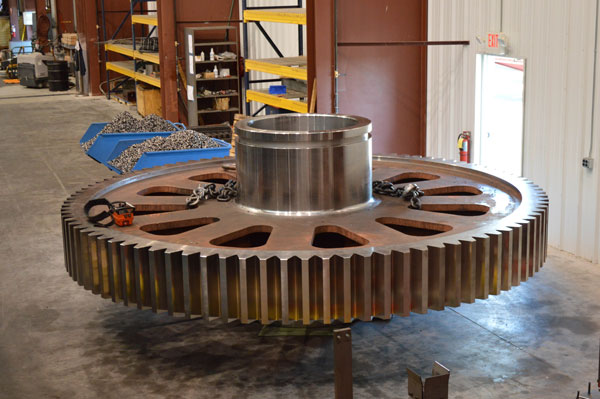
A stock image related to spur gear.
Ethical sourcing extends beyond environmental concerns; it also encompasses labor practices and supply chain transparency. Buyers are increasingly favoring suppliers who demonstrate a commitment to fair labor practices and social responsibility. By prioritizing ethical sourcing, businesses not only enhance their brand reputation but also build long-lasting partnerships with suppliers that share similar values.
How Has the Spur Gear Industry Evolved Over Time?
The evolution of the spur gear industry is rooted in advancements in mechanical engineering and manufacturing technologies. Historically, spur gears have been utilized since the early days of machinery, serving as a fundamental component in mechanical systems due to their simple design and efficiency in transmitting power.
With the Industrial Revolution, the demand for more robust and reliable gears surged, leading to innovations in materials and manufacturing processes. The introduction of precision engineering in the mid-20th century allowed for the production of high-accuracy spur gears, which became essential in various applications, from automotive to aerospace.
Today, the sector continues to evolve with digital technologies and automation, reflecting a trend towards greater customization and efficiency. Modern spur gears are designed using sophisticated computer-aided design (CAD) tools, enabling manufacturers to produce gears that meet specific client requirements while optimizing performance and durability. This evolution is crucial for B2B buyers aiming to stay competitive in an ever-changing global market.
Frequently Asked Questions (FAQs) for B2B Buyers of spur gear
-
How do I choose the right spur gear for my application?
Selecting the appropriate spur gear involves assessing key factors such as load requirements, material, and size specifications. Consider the maximum torque your application will demand, as well as the environmental conditions where the gear will operate (e.g., temperature, exposure to chemicals). It is also essential to look at the gear’s tooth profile and backlash specifications to ensure smooth operation. When in doubt, consult with manufacturers for their recommendations based on your specific needs. -
What materials are commonly used for spur gears and what are their advantages?
Spur gears are typically made from materials such as steel, stainless steel, brass, and various plastics like polyacetal and POM. Steel, particularly alloyed types, offers high strength and durability, making it suitable for heavy-duty applications. Stainless steel is preferred in corrosive environments, while plastics are lightweight and resistant to wear, ideal for applications requiring lower noise levels. Selecting the right material can significantly impact the gear’s performance and longevity. -
What is the minimum order quantity (MOQ) for spur gears when sourcing from international suppliers?
Minimum order quantities can vary widely among suppliers, typically ranging from 50 to several hundred units. It’s important to clarify MOQ with potential suppliers before proceeding, as this can affect your budgeting and inventory management. Some manufacturers may offer flexibility on MOQs for established relationships or larger contracts, so it’s beneficial to negotiate based on your needs. -
How can I verify the quality of spur gears from international suppliers?
To ensure quality, request detailed specifications and certifications from suppliers, such as ISO 9001 for quality management systems. Ask for samples before placing large orders and conduct a quality inspection either through a third-party service or in-house if feasible. Additionally, consider suppliers with a proven track record and positive customer reviews to mitigate risks associated with subpar products. -
What payment terms should I expect when sourcing spur gears internationally?
Payment terms can vary significantly depending on the supplier and the country of origin. Common terms include upfront payments, net 30/60 days, or letters of credit for larger orders. Be sure to discuss and agree upon terms that protect both parties; for instance, consider partial payments upfront with the balance due upon delivery. Understanding the currency fluctuations and payment processing fees is also crucial when dealing with international transactions. -
What are the typical lead times for spur gear production and delivery?
Lead times for spur gear production can range from 2 to 12 weeks, depending on factors like the complexity of the gear, material availability, and the supplier’s production capacity. For customized gears, expect longer lead times due to design and manufacturing adjustments. Always confirm lead times upfront to plan your project timelines effectively and consider discussing expedited options if urgent. -
How do I manage logistics and shipping when sourcing spur gears internationally?
Managing logistics involves selecting reliable freight forwarders and understanding the shipping terms (Incoterms) agreed upon with your supplier. Consider the total landed cost, which includes shipping, customs duties, and insurance. To streamline the process, ensure all documentation is in order, including commercial invoices and packing lists. Regular communication with your supplier and logistics provider can help mitigate delays and unexpected costs. -
What customization options are available for spur gears?
Many manufacturers offer customization options, including modifications in size, tooth design, and material selection to meet specific application requirements. Custom spur gears can be designed for unique load specifications or environmental conditions. When discussing customization, provide detailed specifications and application information to the supplier to ensure they can meet your needs effectively.
Important Disclaimer & Terms of Use
⚠️ Important Disclaimer
The information provided in this guide, including content regarding manufacturers, technical specifications, and market analysis, is for informational and educational purposes only. It does not constitute professional procurement advice, financial advice, or legal advice.
While we have made every effort to ensure the accuracy and timeliness of the information, we are not responsible for any errors, omissions, or outdated information. Market conditions, company details, and technical standards are subject to change.
B2B buyers must conduct their own independent and thorough due diligence before making any purchasing decisions. This includes contacting suppliers directly, verifying certifications, requesting samples, and seeking professional consultation. The risk of relying on any information in this guide is borne solely by the reader.
Strategic Sourcing Conclusion and Outlook for spur gear
What Are the Key Takeaways for B2B Buyers in Spur Gear Sourcing?
In conclusion, strategic sourcing of spur gears is essential for optimizing performance and cost efficiency across various applications. By understanding the specifications—such as material choices, tooth profiles, and dimensional standards—international B2B buyers can make informed decisions that align with their operational needs. Prioritizing suppliers that offer customization and high-quality manufacturing processes can significantly enhance reliability and longevity in gear performance, particularly in demanding environments common in sectors across Africa, South America, the Middle East, and Europe.
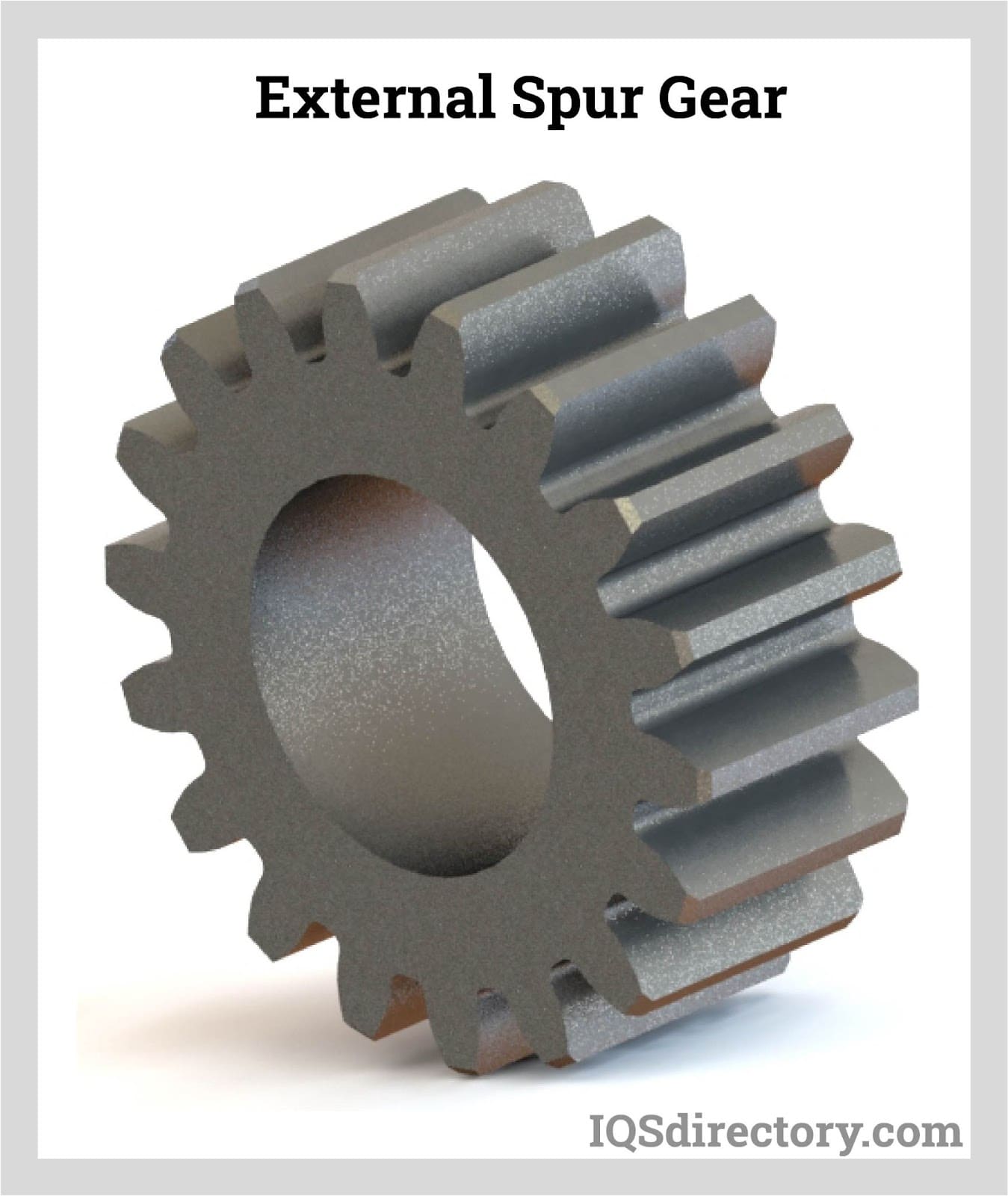
A stock image related to spur gear.
How Can Buyers Prepare for Future Trends in Spur Gear Sourcing?
As the demand for precision and efficiency grows, staying ahead of technological advancements will be crucial. Emerging trends, including the integration of smart technologies and improved manufacturing techniques, present opportunities for buyers to leverage cutting-edge spur gear solutions. By actively engaging with suppliers who prioritize innovation, businesses can better position themselves in a competitive landscape.
What Should B2B Buyers Do Next?
To maximize value, B2B buyers should begin evaluating their current spur gear suppliers and exploring options that emphasize quality, customization, and technological advancement. Collaborating with manufacturers that align with these criteria will not only improve operational efficiency but also foster long-term partnerships essential for future growth. Now is the time to take action and secure a competitive edge in your industry.