Improve Strength & Efficiency: The Ultimate Bolt Shank Guide (2025)
Introduction: Navigating the Global Market for bolt shank
Navigating the complex landscape of sourcing bolt shanks can pose significant challenges for international B2B buyers, particularly those operating in diverse regions like Africa, South America, the Middle East, and Europe. As companies strive to enhance the integrity and durability of their bolted joints, understanding the various types of bolt shanks, their applications, and the nuances of supplier vetting becomes essential. This guide delves into the intricacies of bolt shank design, including waisted, tapered, and unthreaded options, and highlights their specific advantages in enhancing joint performance and reducing maintenance costs.
International buyers will benefit from insights into the cost implications of different bolt shank types, as well as strategies for identifying reliable suppliers. By addressing critical considerations such as material selection, manufacturing tolerances, and application suitability, this comprehensive guide empowers businesses to make informed purchasing decisions. Whether you are a manufacturer in Brazil seeking to optimize production efficiency or a construction firm in Poland looking for reliable fastening solutions, understanding the global market for bolt shanks is pivotal. Equip yourself with the knowledge necessary to enhance your sourcing strategy and ensure your projects meet the highest standards of quality and performance.
Understanding bolt shank Types and Variations
Type Name | Key Distinguishing Features | Primary B2B Applications | Brief Pros & Cons for Buyers |
---|---|---|---|
Unthreaded Shank | Smooth, threadless section for stability | Heavy machinery, structural | Pros: Reduces risk of loosening; Cons: Limited to specific applications. |
Waisted Shank | Tapered design to reduce stress concentration | High-stress environments | Pros: Enhances fatigue resistance; Cons: May require specialized fittings. |
Oval Shank | Oval shape for enhanced grip and fit | Electrical and mechanical joints | Pros: Improved alignment; Cons: May not fit standard fasteners. |
Tapered Shank | Conical shape for interference fit | Aerospace, automotive | Pros: Self-locking and centering; Cons: Higher manufacturing costs. |
Threaded Shank | Fully threaded for maximum grip | General construction | Pros: Versatile and widely used; Cons: More prone to loosening under vibration. |
What Are the Characteristics of Unthreaded Shank Bolts?
Unthreaded shank bolts feature a smooth section that provides stability in bolted joints. This design minimizes the chance of loosening due to vibrations, making them ideal for heavy machinery and structural applications. When purchasing, consider the load requirements and environmental factors, as these bolts are typically suited for static loads rather than dynamic applications.
How Do Waisted Shank Bolts Enhance Performance?
Waisted shank bolts have a tapered design that reduces stress concentration, making them suitable for high-stress environments. Their design allows for better fatigue resistance, especially in applications subject to cyclic loading. Buyers should evaluate the compatibility of waisted shank bolts with existing fittings and the specific performance requirements of their projects.
What Are the Benefits of Using Oval Shank Bolts?
Oval shank bolts are characterized by their unique shape, which helps improve alignment and grip within the joint. These bolts are particularly beneficial in electrical and mechanical applications where precise fit and reduced movement are crucial. When sourcing oval shank bolts, consider the need for specialized tools for installation and the availability of compatible components.
Why Choose Tapered Shank Bolts for Your Applications?
Tapered shank bolts feature a conical design that allows for an interference fit, providing a self-locking and self-centering mechanism. This type is commonly used in aerospace and automotive industries due to its ability to withstand high loads and maintain integrity under stress. Buyers should be aware of the higher manufacturing costs and ensure that their applications can accommodate this specialized design.
What Are the Key Considerations for Threaded Shank Bolts?
Threaded shank bolts are fully threaded to maximize grip in a joint, making them versatile and widely used in general construction. While they offer ease of installation and adjustment, they are more susceptible to loosening under vibration. B2B buyers should assess the specific requirements of their projects, including load conditions and potential vibration exposure, to determine if threaded shank bolts are the right choice.
Key Industrial Applications of bolt shank
Industry/Sector | Specific Application of bolt shank | Value/Benefit for the Business | Key Sourcing Considerations for this Application |
---|---|---|---|
Construction | Structural steel connections | Enhances load-bearing capacity, ensuring safety and durability | Material certifications, compliance with local standards, delivery timelines |
Automotive | Engine assembly and chassis fastening | Provides reliability in high-stress applications, reducing maintenance costs | Tolerance specifications, corrosion resistance, and compatibility with other components |
Oil & Gas | Pipeline and rig assembly | Ensures integrity under high pressure and temperature, reducing leak risks | Source from certified manufacturers, consider material grade and environmental conditions |
Aerospace | Aircraft fuselage and wing assembly | Critical for safety and performance, minimizing weight while maximizing strength | Aerospace-grade materials, adherence to strict industry regulations, and traceability |
Heavy Machinery | Equipment assembly and maintenance | Increases lifespan and reduces downtime through improved joint performance | Customization options, availability of various shank designs, and bulk purchasing agreements |
How is Bolt Shank Used in Construction Applications?
In the construction industry, bolt shanks are crucial for structural steel connections. The threadless portion of the bolt allows for a larger shear area, which enhances the load-bearing capacity of the joint. This is particularly important in high-rise buildings and bridges where safety is paramount. Buyers should focus on sourcing bolts that meet local construction standards and have the necessary certifications to ensure compliance and safety in their projects.
What Role Does Bolt Shank Play in Automotive Manufacturing?
Automotive manufacturers rely on bolt shanks for engine assembly and chassis fastening. The design of the bolt shank facilitates a secure fit that withstands the vibrations and stresses encountered during vehicle operation. For international buyers, it is essential to ensure that sourced bolts meet specific tolerance levels and corrosion resistance standards, as these factors significantly affect the longevity and reliability of automotive components.
How are Bolt Shanks Applied in the Oil & Gas Sector?
In the oil and gas industry, bolt shanks are integral to the assembly of pipelines and rigs. They provide a strong connection capable of withstanding high pressures and extreme temperatures, thus minimizing the risk of leaks. Buyers should prioritize sourcing from certified manufacturers who can provide high-grade materials that meet the harsh environmental conditions typical in this sector, ensuring both safety and operational efficiency.
Why is Bolt Shank Critical in Aerospace Applications?
The aerospace sector uses bolt shanks in the assembly of aircraft fuselages and wings, where every component must meet rigorous safety standards. The absence of threads on the shank allows for a more uniform distribution of stress, which is vital for maintaining structural integrity. Buyers in this field must ensure that all sourced bolts are aerospace-grade and comply with strict industry regulations, including traceability and material certifications.
How Do Heavy Machinery Applications Benefit from Bolt Shank Design?
In heavy machinery, bolt shanks are essential for equipment assembly and maintenance. They provide enhanced performance under cyclic loading conditions, thereby increasing the lifespan of machinery. For buyers, it is important to consider customization options for bolt shank designs to fit specific machinery requirements, as well as to negotiate bulk purchasing agreements to optimize costs while ensuring quality.
3 Common User Pain Points for ‘bolt shank’ & Their Solutions
Scenario 1: Challenges with Shear Load Performance in Bolt Shanks
The Problem: In many industrial applications, particularly in sectors like construction and manufacturing, bolts are subjected to significant shear loads. B2B buyers often face the issue of bolt failure due to insufficient shear capacity, leading to costly downtime and repairs. In regions like Africa and South America, where the demand for robust infrastructure is high, the consequences of using inadequate bolt shanks can be dire, affecting safety and operational efficiency.
The Solution: To enhance shear performance, buyers should prioritize sourcing bolt shanks designed with larger surface areas and minimal stress concentration points. When specifying bolts, it’s crucial to ensure that the shear plane is aligned with the shank rather than the threaded part. This alignment can significantly increase the bolt’s performance under shear loading. Additionally, consider using waisted shank bolts, which reduce the diameter and subsequently lower fatigue stress, thus extending the life of the joint. Collaborate with suppliers who can provide detailed specifications and material certifications to ensure the chosen bolts meet the necessary performance standards for your specific application.
Scenario 2: Difficulty in Selecting the Right Bolt Shank for High-Performance Applications
The Problem: B2B buyers often struggle with selecting the appropriate bolt shank type for high-performance applications, especially in sectors like aerospace and automotive. The lack of clear guidelines on the different shank designs—such as tapered or oval shanks—can lead to incorrect purchases, resulting in performance issues and increased costs. This is particularly critical in Europe, where regulatory compliance and safety standards are stringent.
The Solution: To navigate this challenge, buyers should invest time in understanding the specific requirements of their applications. For high-performance environments, consider using tapered shank bolts, which offer an interference fit that enhances joint integrity. Additionally, consult technical data sheets from manufacturers to compare various shank designs. Implementing a standardized evaluation process for bolt selection, based on load requirements, environmental conditions, and joint configurations, can streamline procurement and ensure the reliability of bolted connections. Engaging with experienced suppliers who offer technical support and guidance can also mitigate the risks associated with improper bolt selection.
Scenario 3: Managing Vibration-Induced Loosening of Bolt Shanks
The Problem: One of the recurring issues B2B buyers encounter is the loosening of bolts due to vibrations in machinery or structural components. This problem is particularly prevalent in the Middle East, where heavy machinery is often subjected to extreme operational conditions. The consequences of loose bolts can include equipment failure, increased maintenance costs, and safety hazards.
The Solution: To combat vibration-induced loosening, it’s essential to select bolt shanks that are specifically designed to minimize radial movement. Bolts with a smooth shank are beneficial as they provide greater resistance against loosening compared to fully threaded bolts. Additionally, consider incorporating locking mechanisms such as lock washers or thread-locking adhesives to secure the bolts in place. Regular maintenance checks to assess bolt tension and integrity can also help prevent issues before they escalate. Establish a robust maintenance protocol that includes periodic inspections and re-tightening schedules, particularly in high-vibration environments, to enhance the longevity and reliability of bolted joints.
Strategic Material Selection Guide for bolt shank
What are the Common Materials for Bolt Shank and Their Properties?
When selecting materials for bolt shanks, international B2B buyers must consider various factors that influence performance, cost, and suitability for specific applications. Below is an analysis of four common materials used for bolt shanks, focusing on their key properties, advantages, disadvantages, and implications for global buyers.
How Does Carbon Steel Perform as a Bolt Shank Material?
Key Properties: Carbon steel is known for its high tensile strength and hardness, making it suitable for applications requiring durability. It typically has a temperature rating of up to 300°C (572°F) and can withstand moderate pressure.
Pros & Cons: The primary advantage of carbon steel is its cost-effectiveness and strength. However, it is susceptible to corrosion, which may necessitate additional coatings or treatments, increasing overall manufacturing complexity.
Impact on Application: Carbon steel is ideal for structural applications in construction and heavy machinery. However, it may not be suitable for environments exposed to saltwater or harsh chemicals.
Considerations for International Buyers: Buyers from regions like Africa and South America should ensure compliance with local standards (e.g., ASTM A307). In Europe, adherence to DIN standards is essential, especially in industrial applications.
What are the Benefits of Stainless Steel for Bolt Shank Applications?
Key Properties: Stainless steel offers excellent corrosion resistance and can handle high temperatures (up to 800°C or 1472°F). It is also known for its aesthetic appeal and strength.
Pros & Cons: The main advantage is its durability and resistance to rust, making it suitable for outdoor and marine applications. However, stainless steel is generally more expensive than carbon steel and may require specialized machining.
Impact on Application: This material is ideal for applications in the food processing, pharmaceutical, and marine industries due to its hygienic properties.
Considerations for International Buyers: Compliance with standards such as ASTM A193 and JIS B117 is critical. Buyers in the Middle East and Europe often prefer stainless steel for its longevity and reliability.
Why Choose Alloy Steel for Bolt Shank Manufacturing?
Key Properties: Alloy steel, which includes elements like chromium and nickel, enhances strength and toughness, with temperature ratings often exceeding 400°C (752°F).
Pros & Cons: The advantages of alloy steel include improved fatigue resistance and the ability to withstand higher loads. However, it is typically more expensive and may require more complex manufacturing processes.
Impact on Application: Alloy steel is commonly used in high-stress applications such as automotive and aerospace industries, where performance is critical.
Considerations for International Buyers: Buyers should ensure compliance with relevant standards like ASTM A490 and DIN 933. Regions like Europe may have specific regulations regarding alloy compositions.
What Role Does Titanium Play in Bolt Shank Applications?
Key Properties: Titanium is lightweight yet exceptionally strong, with a temperature rating that can exceed 600°C (1112°F). It also boasts excellent corrosion resistance, particularly in aggressive environments.
Pros & Cons: The primary advantage of titanium is its strength-to-weight ratio, making it ideal for aerospace and high-performance applications. However, it is one of the most expensive materials and can be challenging to machine.
Impact on Application: Titanium is perfect for applications where weight is a concern, such as in the aerospace and automotive sectors.
Considerations for International Buyers: Compliance with ASTM B348 and similar standards is crucial. Buyers in Europe and the Middle East often prioritize titanium for its superior performance in demanding environments.
Summary Table of Bolt Shank Materials
Material | Typical Use Case for bolt shank | Key Advantage | Key Disadvantage/Limitation | Relative Cost (Low/Med/High) |
---|---|---|---|---|
Carbon Steel | Heavy machinery, construction | Cost-effective and strong | Susceptible to corrosion | Low |
Stainless Steel | Food processing, marine applications | Excellent corrosion resistance | Higher cost and machining needs | Med |
Alloy Steel | Automotive, aerospace | High strength and fatigue resistance | More expensive and complex to manufacture | High |
Titanium | Aerospace, high-performance applications | Lightweight and strong | Very high cost and difficult to machine | High |
This strategic material selection guide provides international B2B buyers with essential insights into the various materials available for bolt shanks, enabling informed decisions that align with their specific applications and regional compliance requirements.
In-depth Look: Manufacturing Processes and Quality Assurance for bolt shank
What Are the Key Manufacturing Processes for Bolt Shanks?
The manufacturing of bolt shanks involves several critical processes that ensure the final product meets the stringent requirements of various industries. Understanding these processes can help B2B buyers make informed decisions when sourcing bolt shanks for their projects.
How is Material Prepared for Bolt Shank Manufacturing?
The first stage in manufacturing bolt shanks is material preparation. Typically, high-strength steel or alloy materials are selected based on the specific application. The material is subjected to heat treatment to enhance its mechanical properties, such as tensile strength and hardness. Additionally, the material may be tested for chemical composition to ensure it meets industry standards.
What Forming Techniques Are Used in Bolt Shank Production?
Once the material is prepared, the forming process begins. This can be accomplished through various techniques, including:
- Cold Heading: This method involves shaping the material at room temperature, which preserves its grain structure and enhances strength. Cold heading is particularly effective for producing high volumes of bolt shanks with consistent quality.
- Hot Forging: For larger bolt shanks or those requiring complex shapes, hot forging is employed. The material is heated to a specific temperature, making it malleable and easier to shape.
- Machining: After forming, machining may be used to achieve precise dimensions and surface finishes. CNC (Computer Numerical Control) machines are commonly utilized for this purpose, ensuring high accuracy and repeatability.
What Are the Finishing Processes for Bolt Shanks?
Finishing processes are crucial for enhancing the durability and performance of bolt shanks. Common finishing techniques include:
- Surface Treatment: Processes like galvanization, plating, or powder coating are applied to improve corrosion resistance and enhance aesthetics.
- Heat Treatment: Additional heat treatment may be performed post-forming to further improve mechanical properties, especially for high-performance applications.
- Inspection and Quality Control: After finishing, bolt shanks undergo rigorous quality control checks to ensure they meet specified tolerances and performance standards.
How is Quality Assurance Implemented in Bolt Shank Manufacturing?
Quality assurance (QA) is a vital component of the bolt shank manufacturing process. B2B buyers must be aware of the QA measures in place to guarantee product reliability and compliance with industry standards.
What International Standards Guide Bolt Shank Quality Assurance?
Manufacturers often adhere to international standards such as ISO 9001, which outlines the criteria for a quality management system. Additionally, industry-specific standards may apply, including:
- CE Marking: Required for products sold in the European Economic Area, ensuring compliance with safety and environmental regulations.
- API Standards: For bolt shanks used in the oil and gas industry, adherence to American Petroleum Institute (API) standards is crucial.
These standards not only help in maintaining quality but also facilitate international trade by ensuring products meet globally recognized specifications.
What Are the Key Quality Control Checkpoints in Bolt Shank Production?
Quality control checkpoints throughout the manufacturing process ensure that any defects are identified and rectified early. Common checkpoints include:
- Incoming Quality Control (IQC): This involves testing raw materials upon arrival to ensure they meet specifications.
- In-Process Quality Control (IPQC): Continuous monitoring during the manufacturing process helps identify deviations from quality standards.
- Final Quality Control (FQC): A thorough inspection of the finished bolt shanks is performed to ensure they meet all specified requirements before shipment.
How Can B2B Buyers Verify Supplier Quality Control?
For international B2B buyers, verifying supplier quality control is essential to ensure the reliability of bolt shanks. Here are several methods to consider:
What Auditing Practices Should Buyers Implement?
Conducting regular audits of suppliers is a proactive approach to verify their manufacturing processes and quality control measures. Buyers should:
- Request Access to Quality Management Documentation: Review the supplier’s quality management system documentation, including certifications and audit reports.
- Conduct On-site Audits: If feasible, visiting the supplier’s facility can provide insights into their manufacturing capabilities and quality control processes.
What Testing Methods Are Commonly Used for Bolt Shanks?
Understanding the testing methods employed by suppliers can give buyers confidence in the product’s performance. Common testing methods include:
- Tensile Testing: To measure the strength and ductility of the bolt shank.
- Fatigue Testing: To assess the performance under cyclic loading conditions, which is critical for applications subject to repeated stresses.
- Non-Destructive Testing (NDT): Techniques such as ultrasonic testing or magnetic particle inspection can identify internal defects without damaging the product.
What Are the Specific QC and Certification Nuances for International Buyers?
When sourcing bolt shanks internationally, particularly from regions like Africa, South America, the Middle East, and Europe, buyers should be aware of specific QC and certification nuances:
- Regional Standards Compliance: Ensure that products comply with local regulations and standards that may differ from international norms.
- Documentation Requirements: Verify that suppliers provide all necessary documentation, including certificates of compliance, test reports, and material traceability records.
- Cultural Considerations: Understanding cultural differences in business practices and communication can facilitate smoother transactions and foster better relationships with suppliers.
By comprehensively understanding the manufacturing processes and quality assurance protocols for bolt shanks, B2B buyers can make informed decisions that enhance the performance and longevity of their applications.
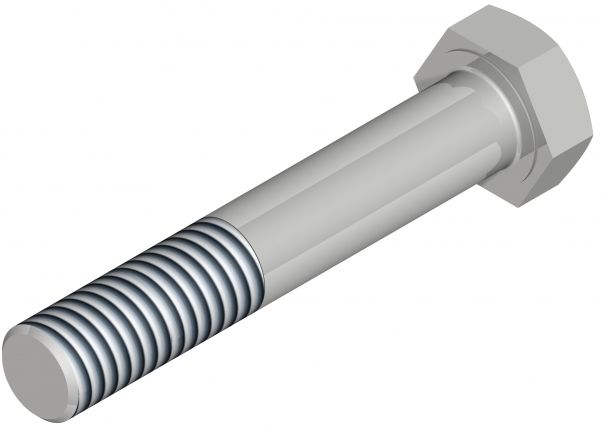
A stock image related to bolt shank.
Practical Sourcing Guide: A Step-by-Step Checklist for ‘bolt shank’
In the competitive landscape of B2B procurement, sourcing high-quality bolt shanks is critical for ensuring the integrity and longevity of your assemblies. This guide provides actionable steps for international buyers, especially those from Africa, South America, the Middle East, and Europe, to navigate the sourcing process effectively.
Step 1: Define Your Technical Specifications
Establishing precise technical specifications is the foundation of successful sourcing. Consider the type of bolt shank required—unthreaded, tapered, or oval—and its dimensions, material, and load capacity. This clarity not only streamlines communication with suppliers but also ensures that the product meets your engineering requirements.
- Material Considerations: Determine if you need carbon steel, stainless steel, or specialized alloys based on your application.
- Performance Criteria: Assess the shear strength and fatigue resistance needed for your specific application.
Step 2: Conduct Market Research for Suppliers
Understanding the market landscape is essential to identify potential suppliers. Research manufacturers that specialize in bolt shanks and evaluate their reputation through industry reviews and client testimonials.
- Regional Considerations: Focus on suppliers within your geographical region to minimize shipping costs and lead times.
- Certifications: Look for suppliers with ISO certifications or other industry-specific standards that demonstrate quality control.
Step 3: Evaluate Potential Suppliers
Before committing, it’s crucial to vet suppliers thoroughly. Request company profiles, case studies, and references from buyers in a similar industry or region. This step mitigates risks associated with supplier reliability and product quality.
- Supplier Track Record: Examine their history of fulfilling orders on time and their responsiveness to customer inquiries.
- Quality Assurance Processes: Inquire about the testing and quality assurance measures they implement to ensure product integrity.
Step 4: Request Samples for Testing
Obtaining samples is vital to assess the quality of the bolt shanks firsthand. Testing samples allows you to verify their performance against your specifications before making a bulk order.
- Testing Parameters: Evaluate shear strength, tensile strength, and fatigue resistance through controlled tests.
- Compatibility Check: Ensure the samples fit seamlessly with your existing components.
Step 5: Negotiate Pricing and Terms
Once you’ve identified a suitable supplier, engage in negotiations to secure favorable pricing and payment terms. This step is crucial for maximizing your budget while maintaining quality.
- Volume Discounts: Discuss bulk order discounts, especially if you plan to purchase regularly.
- Payment Flexibility: Explore options for payment terms that align with your cash flow requirements.
Step 6: Finalize Logistics and Delivery Schedule
Plan the logistics of your order to avoid delays in production. Coordinate with the supplier to establish a clear delivery schedule that aligns with your project timelines.
- Shipping Methods: Consider the best shipping options based on cost and delivery speed.
- Customs Regulations: Ensure compliance with customs regulations in your country to avoid unexpected delays.
Step 7: Review and Assess Post-Purchase
After receiving your bolt shanks, conduct a thorough review to assess the quality and performance of the product in your application.
- Feedback Loop: Provide feedback to the supplier based on your experience to foster a long-term relationship.
- Continual Assessment: Regularly evaluate the performance of the bolt shanks in your applications to identify any need for adjustments in future orders.
By following this structured approach, international B2B buyers can enhance their sourcing strategy for bolt shanks, ensuring they secure high-quality products that meet their operational needs.
Comprehensive Cost and Pricing Analysis for bolt shank Sourcing
What Are the Key Cost Components in Bolt Shank Sourcing?
When sourcing bolt shanks, understanding the cost structure is essential for effective budgeting and negotiation. The primary cost components include:
-
Materials: The type of steel or alloy used significantly influences the cost. High-strength materials, such as carbon steel or stainless steel, will typically command higher prices due to their enhanced performance characteristics.
-
Labor: Manufacturing bolt shanks involves skilled labor, particularly in precision machining processes. Labor costs can vary based on the geographic location of the supplier, with regions such as Europe generally having higher labor costs compared to some areas in Africa or South America.
-
Manufacturing Overhead: This encompasses costs related to utilities, equipment maintenance, and factory management. A facility’s operational efficiency can directly impact overhead costs, influencing the final price of bolt shanks.
-
Tooling: Specialized tooling is often required for producing specific bolt shank designs. The investment in tooling can be substantial, particularly for custom or high-precision shanks, and these costs are typically amortized over the production run.
-
Quality Control (QC): Rigorous QC processes ensure that the bolt shanks meet industry standards. This includes testing for tensile strength and fatigue resistance, which adds to the overall cost but is crucial for ensuring product reliability.
-
Logistics: Transportation costs can vary significantly based on the distance from the manufacturer to the buyer, chosen shipping methods, and customs duties. For international buyers, understanding the implications of logistics on overall pricing is vital.
-
Margin: Suppliers will typically add a profit margin to cover their costs and ensure profitability. This margin can fluctuate based on market demand and competition.
How Do Pricing Influencers Affect Bolt Shank Costs?
Several factors influence the pricing of bolt shanks:
-
Volume/MOQ: Bulk purchases often lead to lower unit prices due to economies of scale. Buyers should negotiate Minimum Order Quantities (MOQs) that align with their needs without incurring excess inventory costs.
-
Specifications and Customization: Custom-designed bolt shanks will inherently be more expensive than standard options. Clearly defining specifications upfront can prevent unexpected costs later.
-
Materials: As mentioned, the choice of materials affects pricing. Specialty alloys or coatings for corrosion resistance may increase costs but can enhance longevity and performance.
-
Quality and Certifications: Products that meet specific quality standards or certifications (e.g., ISO, ASTM) may come with a premium. However, investing in certified products can reduce Total Cost of Ownership (TCO) by minimizing failures and replacements.
-
Supplier Factors: Supplier reputation, reliability, and service levels can impact pricing. Established suppliers may charge more but offer better quality assurance and faster delivery.
-
Incoterms: Understanding shipping terms (e.g., FOB, CIF) is essential for calculating total costs. Incoterms dictate who is responsible for shipping costs and risks, which can affect overall pricing.
What Negotiation Strategies Can Optimize Bolt Shank Sourcing Costs?
For international B2B buyers, particularly those in Africa, South America, the Middle East, and Europe, effective negotiation is crucial:
-
Research Market Prices: Understanding the prevailing market rates for bolt shanks will empower buyers during negotiations. Leverage online platforms and industry reports to gather data.
-
Build Relationships: Establishing long-term relationships with suppliers can lead to better pricing and service. Suppliers are often more willing to negotiate with reliable, repeat customers.
-
Discuss Payment Terms: Flexible payment terms can reduce immediate financial burdens. Options such as extended payment plans can be beneficial.
-
Consider Total Cost of Ownership: While initial pricing is important, consider the long-term costs associated with bolt shanks, such as maintenance, replacement, and downtime. Investing in higher-quality products may yield savings over time.
-
Explore Alternate Suppliers: Diversifying suppliers can create competitive pressure, leading to better pricing. However, ensure that quality and service levels are not compromised.
Conclusion
Sourcing bolt shanks involves navigating a complex landscape of costs and pricing influencers. By understanding the underlying cost components, leveraging effective negotiation strategies, and considering the Total Cost of Ownership, international B2B buyers can make informed purchasing decisions that align with their operational needs and budget constraints. Always remember that prices can fluctuate based on market conditions, so it’s advisable to regularly review and compare supplier offerings.
Alternatives Analysis: Comparing bolt shank With Other Solutions
When evaluating fastening solutions, it’s essential for B2B buyers to consider various alternatives to bolt shanks. Each solution has its unique advantages and drawbacks, making it important to choose the right option based on specific requirements. Below, we compare bolt shanks with two viable alternatives: tapered shank bolts and unthreaded fasteners.
Comparison Aspect | Bolt Shank | Tapered Shank Bolts | Unthreaded Fasteners |
---|---|---|---|
Performance | High shear and tensile strength; effective in reducing fatigue stress. | Excellent for interference fit; self-locking mechanism enhances joint stability. | Provides a smooth surface for load distribution; minimizes radial movement. |
Cost | Generally low manufacturing costs, especially for mass production. | Higher initial cost due to specialized manufacturing processes. | Cost-effective due to simplified design and fewer parts required. |
Ease of Implementation | Standardized dimensions simplify procurement and installation. | Requires precise fitting; installation may need special tools. | Simple installation; often requires no additional tools. |
Maintenance | Requires regular checks for loosening; may need replacement in high-stress applications. | Low maintenance; high durability reduces the need for frequent replacements. | Minimal maintenance; excellent longevity reduces operational downtime. |
Best Use Case | Ideal for high-performance applications requiring robust joint integrity. | Best suited for applications with high vibration or dynamic loads, such as in automotive and aerospace. | Effective in static applications where load distribution is critical, like in structural assemblies. |
What Are the Advantages and Disadvantages of Tapered Shank Bolts?
Tapered shank bolts offer an interference fit that enhances joint stability through a self-locking mechanism. This feature is particularly advantageous in applications subjected to vibrations, as it reduces the risk of loosening over time. However, the installation of tapered shank bolts can be more complicated, requiring precise measurements and potentially specialized tools. Their higher initial cost may also be a consideration for budget-conscious buyers.
How Do Unthreaded Fasteners Compare?
Unthreaded fasteners provide a unique solution by minimizing radial movement between the joined components. This design allows for effective load distribution, which is particularly beneficial in static applications like structural assemblies. The simplicity of unthreaded fasteners translates into easier installation and lower costs, making them an appealing option for many projects. However, they may not provide the same level of tensile strength or resistance to dynamic loads as bolt shanks or tapered shank bolts.
How to Choose the Right Fastening Solution for Your Needs?
When selecting the appropriate fastening solution, B2B buyers should consider the specific requirements of their applications, including load conditions, environmental factors, and budget constraints. Bolt shanks excel in high-performance scenarios where robustness is crucial, while tapered shank bolts are ideal for dynamic environments with significant vibration. On the other hand, unthreaded fasteners are best suited for static applications where simplicity and cost-effectiveness are priorities. By assessing these factors, buyers can make informed decisions that align with their operational needs.
Essential Technical Properties and Trade Terminology for bolt shank
What Are the Key Technical Properties of a Bolt Shank?
Understanding the technical specifications of bolt shanks is crucial for international B2B buyers, particularly those involved in manufacturing, construction, and engineering. Here are some essential properties that buyers should consider:
1. Material Grade: Why Does It Matter?
The material grade of a bolt shank directly impacts its strength, durability, and resistance to corrosion. Common materials include carbon steel, stainless steel, and alloy steel. For instance, stainless steel bolts are ideal for environments with high humidity or corrosive elements. Selecting the right material grade can enhance the longevity of the joint and reduce maintenance costs, which is particularly important in regions with challenging weather conditions, such as the Middle East and parts of Africa.
2. Tolerance: How Does It Affect Fit and Function?
Tolerance refers to the permissible limit of variation in dimensions. For bolt shanks, this is critical for ensuring a snug fit within the assembly. A precise tolerance reduces the risk of joint failure due to movement or vibration, which is especially important in applications like automotive manufacturing or heavy machinery. Understanding tolerance specifications can help buyers select the right bolt for their specific needs and avoid costly assembly errors.
3. Shank Length: What Should Buyers Consider?
The length of the shank influences how well the bolt engages with the materials it is fastening. Longer shanks may be required in applications with thicker materials, while shorter shanks can reduce weight and costs in less demanding situations. Buyers should consider the application requirements to ensure that the bolt provides adequate engagement without compromising strength.
4. Shank Diameter: Why Is It Critical?
The diameter of the shank is essential for load-bearing capacity. A larger diameter shank can withstand greater loads and shear forces, making it suitable for heavy-duty applications. Conversely, a smaller diameter may be more appropriate for lighter assemblies. Buyers must balance between the required strength and the overall weight of the assembly, especially in industries like aerospace and automotive.
5. Surface Finish: What Are the Options?
The surface finish of a bolt shank can affect its resistance to wear and corrosion. Options include zinc plating, black oxide, and passivation for stainless steel. A proper surface finish not only enhances aesthetics but also plays a significant role in the performance of the joint. Buyers should consider the environmental conditions the bolt will face when selecting the appropriate surface treatment.
What Are Common Trade Terms Related to Bolt Shanks?
Familiarity with trade terminology is vital for effective communication and negotiation in the B2B marketplace. Here are some essential terms that buyers should know:
1. OEM (Original Equipment Manufacturer): What Does It Mean?
OEM refers to companies that produce parts that are used in another company’s end product. Understanding OEM specifications can help buyers ensure that they are sourcing components that meet industry standards and compatibility requirements.
2. MOQ (Minimum Order Quantity): How Does It Impact Purchasing?
MOQ is the smallest number of units a supplier is willing to sell. Knowing the MOQ can help buyers plan their inventory and manage costs effectively, especially when ordering for large projects or mass production.
3. RFQ (Request for Quotation): Why Is It Important?
An RFQ is a document sent to suppliers requesting pricing and terms for specific quantities of products. Submitting an RFQ allows buyers to compare different suppliers and negotiate better terms, making it a critical step in the procurement process.
4. Incoterms: What Are They and Why Do They Matter?
Incoterms are international commercial terms that define the responsibilities of buyers and sellers in shipping and delivery. Understanding these terms is essential for buyers to know who bears the costs and risks at different stages of transportation, which can vary significantly across regions like Africa, South America, the Middle East, and Europe.
5. Lead Time: How Does It Affect Project Planning?
Lead time refers to the time taken from placing an order to receiving the products. Knowing the lead time is crucial for project scheduling, particularly in industries where delays can lead to significant costs.
By understanding these technical properties and trade terms, international B2B buyers can make informed decisions, ensuring they select the right bolt shank for their applications while optimizing procurement processes.
Navigating Market Dynamics and Sourcing Trends in the bolt shank Sector
What are the Key Market Dynamics and Trends in the Bolt Shank Sector for International B2B Buyers?
The bolt shank sector is witnessing significant transformations driven by globalization, technological advancements, and evolving customer demands. One of the primary global drivers is the increasing emphasis on high-performance materials and designs that enhance durability and efficiency. In regions like Africa, South America, the Middle East, and Europe, industries such as construction, automotive, and energy are increasingly demanding innovative fastening solutions that can withstand extreme conditions. This trend has propelled the development of specialized bolt shank designs, including waisted and tapered shank bolts, which provide superior performance under shear and tension loads.
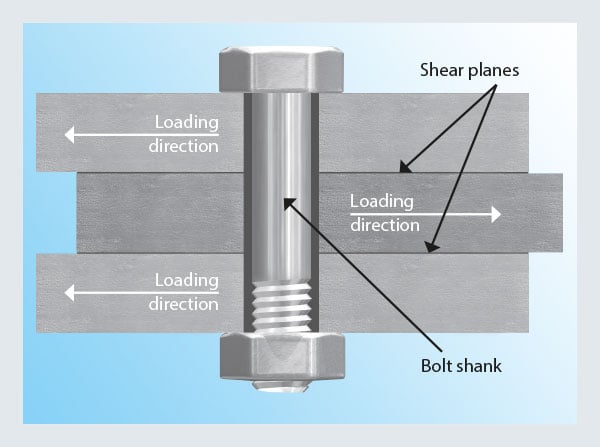
A stock image related to bolt shank.
Emerging B2B technologies, such as digital supply chain management and predictive analytics, are also reshaping sourcing strategies in the bolt shank market. These technologies allow buyers to better forecast demand and optimize inventory levels, reducing lead times and costs. Furthermore, the rise of e-commerce platforms tailored for industrial buyers is facilitating easier access to a wider range of suppliers and products, enabling buyers from diverse regions like Brazil and Poland to source competitively.
Moreover, there is a growing trend towards customization in bolt shank products, as buyers seek tailored solutions that meet specific application requirements. This trend emphasizes the importance of establishing strong relationships with suppliers who can provide flexible manufacturing capabilities and rapid prototyping services.
How Can B2B Buyers Prioritize Sustainability and Ethical Sourcing in the Bolt Shank Market?
Sustainability has become a critical focus for international B2B buyers, especially those from environmentally conscious regions like Europe. The environmental impact of manufacturing processes and material sourcing is under scrutiny, prompting buyers to prioritize suppliers who demonstrate a commitment to sustainable practices. In the bolt shank sector, this includes sourcing materials that are recycled or derived from renewable resources, as well as ensuring that production processes minimize waste and energy consumption.
Buyers should also consider the importance of ethical supply chains. This involves verifying that suppliers adhere to fair labor practices and environmental regulations throughout their manufacturing operations. Certifications such as ISO 14001 for environmental management and ISO 45001 for occupational health and safety can serve as indicators of a supplier’s commitment to ethical practices. By partnering with suppliers who hold such certifications, B2B buyers can enhance their brand reputation and ensure compliance with increasingly stringent regulations.
Additionally, the use of ‘green’ materials in bolt shank production can lead to reduced environmental footprints. For example, choosing fasteners made from low-carbon steel or recycled alloys not only supports sustainability goals but can also appeal to eco-conscious customers.
What is the Historical Context of Bolt Shank Development Relevant to Today’s B2B Buyers?
The evolution of bolt shank technology has been pivotal in shaping modern fastening solutions. Historically, the introduction of unthreaded shank designs allowed for improved performance under shear loads, significantly enhancing the reliability of bolted joints. Early applications primarily focused on structural integrity, but as industries advanced, the need for specialized designs emerged.
In recent decades, the development of high-strength materials and innovative manufacturing techniques, such as cold forging and heat treatment, has further refined bolt shank performance. This historical context is essential for B2B buyers as it underscores the importance of selecting advanced bolt shank solutions that not only meet current operational demands but also anticipate future challenges in their respective industries.
By understanding the historical advancements in bolt shank technology, buyers can make informed decisions that align with both current market trends and future industry needs, ensuring they remain competitive in an ever-evolving landscape.
Frequently Asked Questions (FAQs) for B2B Buyers of bolt shank
-
How do I select the right bolt shank for my application?
Choosing the right bolt shank involves assessing the load requirements and environmental conditions of your application. Consider factors such as the type of load (tension or shear), the materials being joined, and the presence of any vibrations. A larger shank diameter may provide better shear capacity, while a reduced shank can enhance elasticity. Additionally, consult with suppliers about specific performance metrics and material grades to ensure optimal compatibility with your project needs. -
What are the advantages of using unthreaded shank bolts?
Unthreaded shank bolts offer several benefits, including improved shear strength and reduced stress concentration. By eliminating threads in the shank area, these bolts can better withstand lateral forces and vibrations, making them ideal for high-stress applications. Furthermore, they can simplify manufacturing processes, as they often require less machining time, which can lead to cost savings in large production runs. -
How can I ensure the quality of bolt shanks from international suppliers?
To ensure quality, it’s crucial to vet suppliers thoroughly. Request certifications such as ISO 9001 or other relevant quality management system certifications. Conduct factory audits if possible, and ask for samples to evaluate the quality of materials and workmanship. Additionally, consider using third-party inspection services for large orders, especially if sourcing from regions with varying manufacturing standards. -
What are typical minimum order quantities (MOQs) for bolt shanks?
Minimum order quantities for bolt shanks can vary significantly based on the supplier and the type of bolt required. Generally, MOQs range from 100 to 1,000 units for standard sizes. For customized or specialized bolts, MOQs may be higher due to increased manufacturing complexity. It’s advisable to discuss your specific needs with suppliers to negotiate terms that align with your purchasing strategy. -
What payment terms should I expect when sourcing bolt shanks internationally?
Payment terms can vary by supplier and region, but common practices include advance payment, letter of credit, or payment upon delivery. For new suppliers, it is typical to negotiate a partial upfront payment (30-50%) with the balance due upon shipment or delivery. Always clarify terms in your purchase agreement and consider using escrow services for high-value transactions to mitigate risk. -
How do I handle logistics and shipping for bolt shanks sourced from overseas?
When sourcing bolt shanks internationally, coordinate closely with your supplier on shipping options. Consider factors like shipping time, costs, and customs clearance procedures. It’s advisable to work with a logistics provider experienced in international trade to ensure compliance with import regulations and to manage any potential delays. Additionally, factor in insurance for high-value shipments to protect your investment during transit. -
Can I customize bolt shanks for specific applications?
Yes, many suppliers offer customization options for bolt shanks, including alterations in length, diameter, and material specifications. When seeking customization, provide detailed specifications and discuss your requirements with the supplier. Be prepared for potential lead times that may exceed standard production schedules, as custom orders typically require additional engineering and manufacturing processes. -
What certifications should I look for when sourcing bolt shanks?
When sourcing bolt shanks, look for certifications that demonstrate compliance with industry standards. Common certifications include ISO 9001 for quality management, ASTM for material specifications, and CE marking for compliance with European safety standards. These certifications can indicate that the products meet necessary performance criteria and manufacturing practices, ensuring reliability and safety in your applications.
Important Disclaimer & Terms of Use
⚠️ Important Disclaimer
The information provided in this guide, including content regarding manufacturers, technical specifications, and market analysis, is for informational and educational purposes only. It does not constitute professional procurement advice, financial advice, or legal advice.
While we have made every effort to ensure the accuracy and timeliness of the information, we are not responsible for any errors, omissions, or outdated information. Market conditions, company details, and technical standards are subject to change.
B2B buyers must conduct their own independent and thorough due diligence before making any purchasing decisions. This includes contacting suppliers directly, verifying certifications, requesting samples, and seeking professional consultation. The risk of relying on any information in this guide is borne solely by the reader.
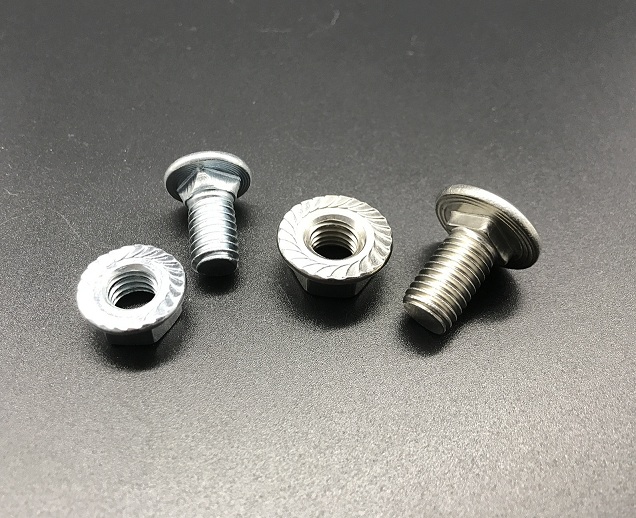
A stock image related to bolt shank.
Strategic Sourcing Conclusion and Outlook for bolt shank
In conclusion, strategic sourcing for bolt shank solutions can significantly enhance the performance, longevity, and cost-effectiveness of bolted joints. Understanding the technical specifications, such as the benefits of unthreaded shanks for shear load performance and the importance of elastic resilience in tension applications, is essential for international B2B buyers. By optimizing the design and material choices, companies can reduce maintenance costs and improve operational efficiency.
For buyers in regions like Africa, South America, the Middle East, and Europe, leveraging local suppliers who understand the specific market demands can lead to better sourcing decisions. Additionally, considering innovations such as waisted shank designs can provide competitive advantages by extending the lifespan of fasteners in demanding applications.
As you move forward, it is crucial to engage with suppliers who can offer customized solutions tailored to your unique operational needs. Explore partnerships that prioritize quality and innovation in bolt shank manufacturing to ensure your projects are both successful and sustainable. By embracing strategic sourcing, you position your business for future growth and resilience in an evolving market landscape.