Master Air Solenoid Sourcing: The Complete Buyer’s Guide (2025)
Introduction: Navigating the Global Market for air solenoid
In today’s rapidly evolving industrial landscape, sourcing reliable air solenoid valves can be a daunting challenge for international B2B buyers, particularly those operating in diverse markets such as Africa, South America, the Middle East, and Europe. With a plethora of options available, it is crucial to understand the specific needs of your application—be it for pneumatic systems, fluid control, or automation. This guide aims to demystify the complexities of the air solenoid market by exploring various types, applications, and essential considerations when selecting the right product for your business needs.
Throughout this comprehensive resource, you will gain insights into the different categories of air solenoids, their operational mechanisms, and the industries that commonly utilize them. Additionally, we will cover vital aspects such as supplier vetting processes, cost analysis, and best practices for optimizing your procurement strategy. By equipping yourself with this knowledge, you will be empowered to make informed purchasing decisions that align with your operational goals and budget constraints.
Whether you are a manufacturer in the UAE, a distributor in South America, or a project manager in Europe, this guide serves as your roadmap to navigating the global market for air solenoids, ensuring you select the most suitable solutions for your unique requirements.
Understanding air solenoid Types and Variations
Type Name | Key Distinguishing Features | Primary B2B Applications | Brief Pros & Cons for Buyers |
---|---|---|---|
On/Off Solenoid Valves | Simple design, directly controls flow with an electrical signal. | Water, air, and gas control in manufacturing. | Pros: Easy installation, reliable operation. Cons: Limited to binary operation. |
Diverting Solenoid Valves | Directs flow between multiple paths; can handle multiple media. | Chemical processing, water treatment. | Pros: Versatile in applications, space-saving design. Cons: More complex installation. |
Compact Solenoid Valves | Smaller size, ideal for tight spaces; maintains high performance. | Robotics, automotive assembly lines. | Pros: Ideal for limited space, efficient. Cons: May have lower flow rates. |
High-Pressure Solenoid Valves | Designed to withstand higher pressure levels; robust construction. | Oil & gas, hydraulic systems. | Pros: Durable under extreme conditions. Cons: Higher cost, requires careful selection. |
Miniature Solenoid Valves | Extremely small size, suitable for miniature applications. | Medical devices, laboratory equipment. | Pros: Perfect for compact systems. Cons: Limited media handling capacity. |
What Are On/Off Solenoid Valves and Their Applications?
On/Off solenoid valves are characterized by their straightforward design, allowing them to effectively start or stop the flow of fluids through a system. They are commonly used in various manufacturing processes involving water, air, and gas control. When purchasing, buyers should consider the voltage requirements and flow capacity to ensure compatibility with existing systems. Their reliability makes them a preferred choice, although they only offer binary control without flow regulation.
How Do Diverting Solenoid Valves Work?
Diverting solenoid valves are engineered to redirect fluid flow between multiple paths, making them invaluable in applications such as chemical processing and water treatment. These valves can handle various media, including gases and liquids, and are particularly useful when space is limited. Buyers should evaluate the specific flow requirements and compatibility with their systems, as the complexity of installation may require additional expertise compared to simpler valve types.
What Are the Advantages of Compact Solenoid Valves?
Compact solenoid valves are designed for applications where space is a constraint. Their smaller size does not compromise performance, making them suitable for use in robotics and automotive assembly lines. When considering a purchase, businesses should assess the flow rates and pressure limits, as compact valves may not handle as much flow compared to their larger counterparts. Their efficiency and adaptability make them a popular choice in modern manufacturing environments.
Why Choose High-Pressure Solenoid Valves?
High-pressure solenoid valves are built to endure extreme pressure conditions, making them essential in industries like oil & gas and hydraulic systems. They offer durability and reliability under challenging conditions, which is critical for maintaining operational integrity. Buyers need to pay careful attention to the pressure ratings and materials used in the valve construction to ensure they meet the specific demands of their applications. While they tend to have a higher upfront cost, their long-term reliability can justify the investment.
What Are the Key Features of Miniature Solenoid Valves?
Miniature solenoid valves are designed for applications where space is at a premium, such as in medical devices and laboratory equipment. Their compact size allows for integration into tight spaces without sacrificing performance. When purchasing, it’s important for buyers to consider the media compatibility and flow capacity, as these valves typically have limitations in handling larger volumes. Despite their constraints, their ability to fit into small systems makes them indispensable in specialized applications.
Key Industrial Applications of air solenoid
Industry/Sector | Specific Application of air solenoid | Value/Benefit for the Business | Key Sourcing Considerations for this Application |
---|---|---|---|
Manufacturing | Automated assembly lines | Increased efficiency and reduced labor costs | Compatibility with existing systems and voltage ratings |
Agriculture | Irrigation control systems | Enhanced water management and crop yield | Durability in harsh environments and corrosion resistance |
Oil & Gas | Pipeline flow control | Improved safety and reduced leakage | Compliance with industry standards and pressure ratings |
Food and Beverage | Packaging and bottling processes | Consistent quality and reduced waste | Hygiene standards and material certifications |
Automotive | Pneumatic systems in vehicle assembly | Streamlined operations and reduced cycle times | Size and weight constraints, as well as voltage specifications |
How is Air Solenoid Used in Manufacturing Automation?
In the manufacturing sector, air solenoids are crucial for automating assembly lines. They control the flow of air to actuate various tools and machinery, enabling tasks such as clamping, lifting, and positioning of parts. This automation significantly increases operational efficiency and reduces labor costs, making it an attractive investment for businesses. International buyers should consider voltage compatibility and integration with existing systems to ensure seamless operations.
What Role Do Air Solenoids Play in Agricultural Irrigation Systems?
Air solenoids are widely used in agricultural irrigation control systems, allowing for precise management of water flow. They help automate the opening and closing of valves based on moisture levels, ensuring optimal irrigation and improving crop yields. For buyers in regions like Africa and South America, sourcing solenoids that can withstand harsh environmental conditions and are resistant to corrosion is essential for long-term reliability.
How Are Air Solenoids Utilized in Oil and Gas Pipeline Management?
In the oil and gas industry, air solenoids are pivotal for managing pipeline flow and pressure. They allow operators to remotely control valves, enhancing safety by minimizing the risk of leaks and spills. Buyers must consider compliance with industry safety standards and the solenoid’s ability to handle high-pressure environments when sourcing these components.
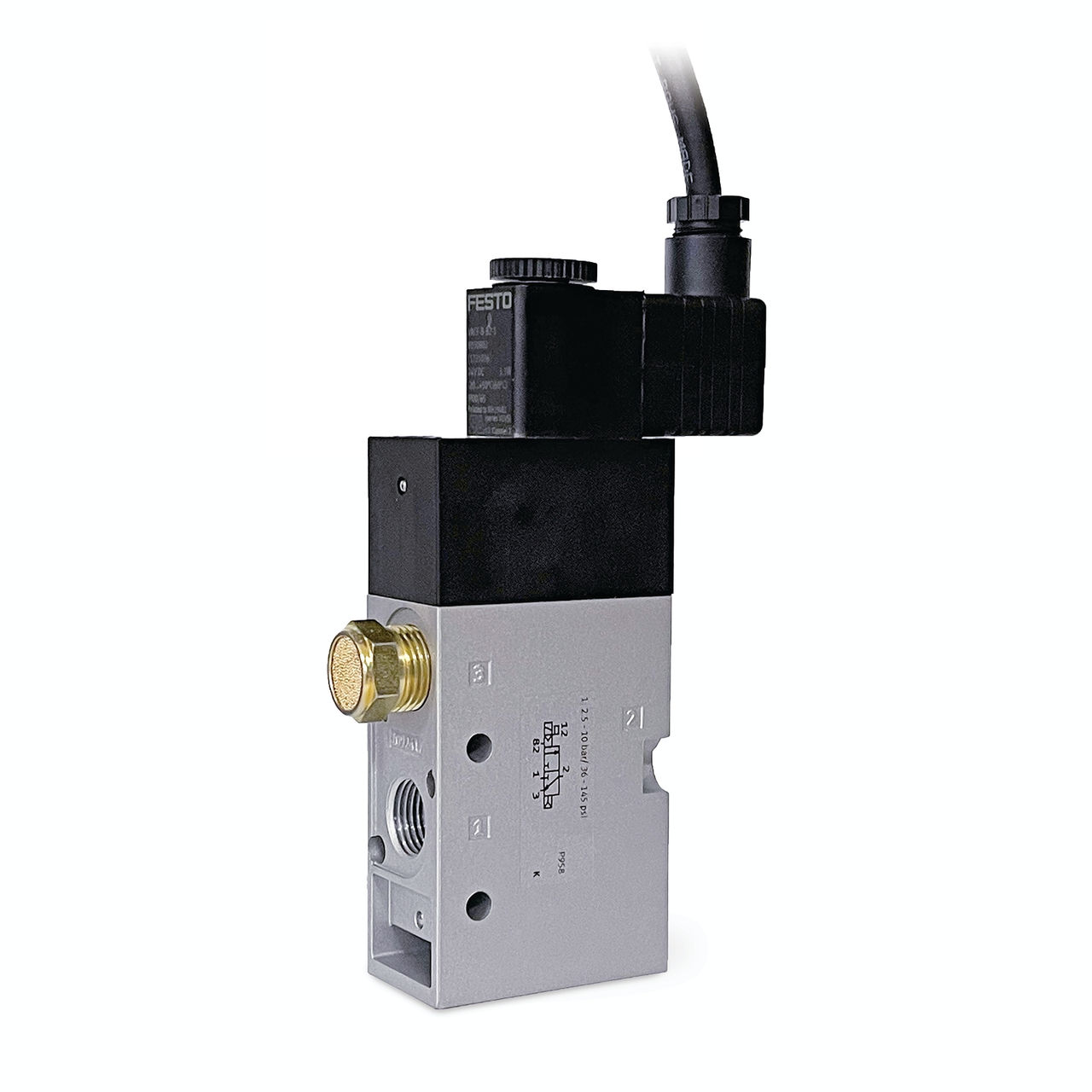
A stock image related to air solenoid.
Why Are Air Solenoids Important in Food and Beverage Packaging?
In the food and beverage sector, air solenoids are integral to packaging and bottling processes. They ensure precise control over the filling and sealing operations, which helps maintain product quality and reduces waste. Buyers need to prioritize hygiene standards and material certifications to ensure that the components meet health regulations, particularly in Europe and the Middle East.
How Do Air Solenoids Enhance Automotive Assembly Lines?
In the automotive industry, air solenoids are essential for pneumatic systems used in vehicle assembly. They facilitate quick and efficient operations, such as extending and retracting cylinders that perform critical assembly tasks. Buyers should focus on size, weight constraints, and voltage specifications to ensure that the solenoids fit within the design of their assembly systems, especially in competitive markets like Europe and the UAE.
3 Common User Pain Points for ‘air solenoid’ & Their Solutions
Scenario 1: Inconsistent Performance of Air Solenoids in Harsh Environments
The Problem: Many B2B buyers in industrial sectors, particularly in regions like Africa and the Middle East, face challenges with air solenoids that fail to perform consistently in harsh environmental conditions. Factors such as extreme temperatures, humidity, and exposure to corrosive substances can lead to premature wear and malfunction of solenoid valves. This inconsistency not only disrupts operations but can also result in costly downtime and repairs.
The Solution: To ensure reliable performance, it is crucial to select air solenoids that are specifically designed for harsh environments. Buyers should prioritize solenoids made from durable materials such as stainless steel or brass with corrosion-resistant coatings. Furthermore, implementing regular maintenance schedules that include cleaning and inspection can extend the lifespan of solenoids. Investing in high-quality solenoids from reputable manufacturers who provide detailed specifications on environmental ratings can significantly mitigate risks associated with performance variability.
Scenario 2: Difficulty in Sourcing the Right Size and Type of Air Solenoid
The Problem: B2B buyers often struggle to find the appropriate size and type of air solenoid that fits their specific application needs. With a wide variety of models, including different voltage requirements, connection types, and flow rates, the process can be overwhelming. This confusion can lead to incorrect purchases, increased operational costs, and delays in project timelines.
The Solution: Buyers should start by conducting a thorough assessment of their system requirements, including the exact specifications for pipe size, voltage, and flow rate. Utilizing online resources and product catalogs from trusted suppliers can aid in understanding the available options. Additionally, engaging with technical support teams from manufacturers can provide insights into selecting the right product. Developing a standardized specification sheet that outlines the critical parameters can streamline the sourcing process, ensuring the right solenoid is selected on the first attempt.
Scenario 3: High Energy Consumption of Air Solenoids
The Problem: In regions like South America and Europe, where energy costs are a significant concern, B2B buyers may find that the air solenoids they currently use consume more power than necessary. This inefficiency can lead to increased operational costs and negatively impact sustainability goals.
The Solution: To address energy consumption issues, buyers should consider investing in energy-efficient solenoid valves. These models are designed to operate effectively with lower power requirements and often include features like integrated flow control. Additionally, conducting an energy audit can help identify specific areas where solenoid operation can be optimized. Implementing smart control systems that can adjust solenoid operation based on real-time demand can also contribute to energy savings. By prioritizing energy efficiency in purchasing decisions, companies can reduce costs and enhance their sustainability efforts.
By addressing these common pain points with targeted solutions, B2B buyers can enhance their operational efficiency, reduce costs, and ensure the longevity of their air solenoid systems.
Strategic Material Selection Guide for air solenoid
What Are the Key Materials Used in Air Solenoids?
When selecting air solenoids for various applications, the choice of material plays a crucial role in performance, durability, and overall cost-effectiveness. Below, we analyze four common materials used in air solenoids: brass, stainless steel, plastic, and aluminum. Each material has unique properties and considerations that international B2B buyers should be aware of, particularly in regions like Africa, South America, the Middle East, and Europe.
How Does Brass Perform in Air Solenoid Applications?
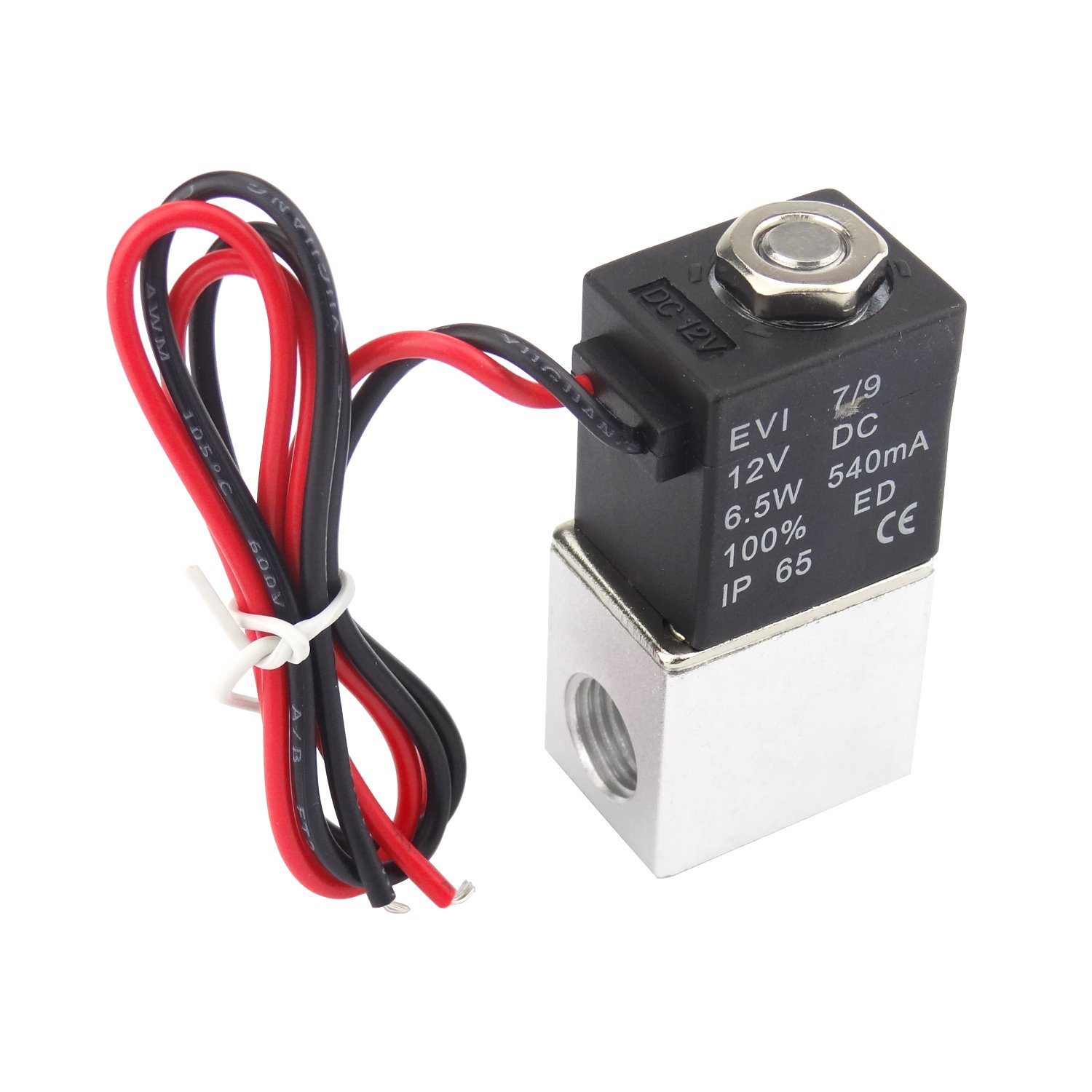
A stock image related to air solenoid.
Brass is a popular choice for air solenoids due to its excellent machinability and corrosion resistance. It typically has a temperature rating of up to 200°C and can handle moderate pressures.
Pros: Brass solenoids are durable and provide good sealing properties, making them suitable for various applications. They are also relatively cost-effective compared to other materials.
Cons: However, brass can be susceptible to dezincification in aggressive environments, which can compromise its integrity over time. Additionally, it may not be ideal for applications involving corrosive media.
Impact on Application: Brass is compatible with air, water, and some oils, making it versatile. However, it is essential for buyers to ensure that the specific media used does not lead to corrosion.
Considerations for International Buyers: Compliance with standards such as ASTM B16 and DIN 50930-6 is crucial. Buyers in regions like the UAE and Europe often prefer brass for its balance of cost and performance.
What Advantages Does Stainless Steel Offer for Air Solenoids?
Stainless steel is known for its superior corrosion resistance and strength, making it suitable for harsh environments. It can withstand temperatures up to 300°C and high-pressure applications.
Pros: The durability and resistance to oxidation and corrosion make stainless steel ideal for applications involving aggressive fluids or gases.
Cons: The primary drawback is its higher cost compared to brass and plastic. Manufacturing stainless steel components can also be more complex, leading to longer lead times.
Impact on Application: Stainless steel solenoids are compatible with a wide range of media, including corrosive chemicals, making them suitable for industrial applications.
Considerations for International Buyers: Buyers should ensure compliance with standards like ASTM A276 and ISO 9001. In regions like South America and the Middle East, stainless steel is often preferred for its longevity.
How Do Plastic Air Solenoids Compare?
Plastic solenoids are lightweight and resistant to corrosion, making them an attractive option for specific applications. They typically have lower temperature and pressure ratings, generally around 60°C and 10 bar.
Pros: The lightweight nature of plastic solenoids makes installation easier, and they are often less expensive than metal options.
Cons: However, their lower durability can be a concern in high-stress environments. They may also be unsuitable for high-temperature applications.
Impact on Application: Plastic solenoids are best suited for non-corrosive gases and fluids, limiting their application range.
Considerations for International Buyers: Buyers should check for compliance with standards such as ASTM D638 and ISO 527. In regions like Africa, plastic solenoids can be a cost-effective solution for less demanding applications.
What Role Does Aluminum Play in Air Solenoid Design?
Aluminum is lightweight and has good thermal conductivity, making it a viable option for air solenoids. It can handle temperatures up to 150°C and moderate pressures.
Pros: Aluminum solenoids are easy to manufacture and provide a good balance between weight and strength.
Cons: However, they are less corrosion-resistant than stainless steel, which can limit their use in certain applications.
Impact on Application: Aluminum solenoids are suitable for air and non-corrosive fluids but may not be ideal for harsh environments.
Considerations for International Buyers: Compliance with standards like ASTM B221 and DIN 17615 is essential. In Europe, aluminum solenoids are often chosen for applications where weight savings are critical.
Summary Table of Material Selection for Air Solenoids
Material | Typical Use Case for air solenoid | Key Advantage | Key Disadvantage/Limitation | Relative Cost (Low/Med/High) |
---|---|---|---|---|
Brass | General industrial applications | Good machinability and cost-effective | Susceptible to dezincification | Medium |
Stainless Steel | Harsh environments with corrosive media | Superior corrosion resistance | Higher cost and manufacturing complexity | High |
Plastic | Lightweight, non-corrosive applications | Lightweight and easy to install | Lower durability and temperature limits | Low |
Aluminum | Air and non-corrosive fluids | Good balance of weight and strength | Less corrosion resistance | Medium |
This strategic material selection guide aims to equip international B2B buyers with the insights needed to make informed decisions when sourcing air solenoids, ensuring compatibility with their specific applications while adhering to regional standards.
In-depth Look: Manufacturing Processes and Quality Assurance for air solenoid
What Are the Main Stages of Manufacturing Air Solenoids?
The manufacturing process of air solenoids involves several key stages, each critical for ensuring the final product meets the required specifications and quality standards. Understanding these stages helps international B2B buyers identify reliable suppliers.
Material Preparation: What Materials Are Commonly Used?
The first stage in the manufacturing of air solenoids is material preparation. Common materials include stainless steel, brass, and various plastics, chosen for their durability, resistance to corrosion, and ability to withstand high pressures. Suppliers often source these materials from certified vendors to ensure quality. Buyers should inquire about the origin of materials and whether they meet international standards for safety and performance.
Forming: How Are Components Shaped?
The forming stage involves shaping raw materials into specific components using techniques like machining, stamping, and injection molding. Machining is often used for precision parts, while stamping is suitable for creating metal parts rapidly. Injection molding is common for plastic components. During this stage, buyers should confirm that the supplier employs CNC (Computer Numerical Control) machines for accuracy and repeatability.
Assembly: What Techniques Are Used for Assembly?
Assembly is the next crucial stage, where individual components are put together to form the complete air solenoid. This may involve manual assembly or automated processes, depending on the scale of production. Techniques like soldering, crimping, and using adhesives are commonly employed. It is vital for buyers to ensure that suppliers have skilled labor and modern assembly lines to minimize defects and ensure efficiency.
Finishing: What Is Involved in the Final Touches?
The finishing stage includes processes such as surface treatment, painting, and quality checks to enhance the solenoid’s appearance and protect it from environmental factors. Treatments may include anodizing or powder coating, which improve corrosion resistance. Buyers should ask suppliers about their finishing techniques and whether they comply with environmental regulations, particularly if they are sourcing from regions with strict compliance requirements.
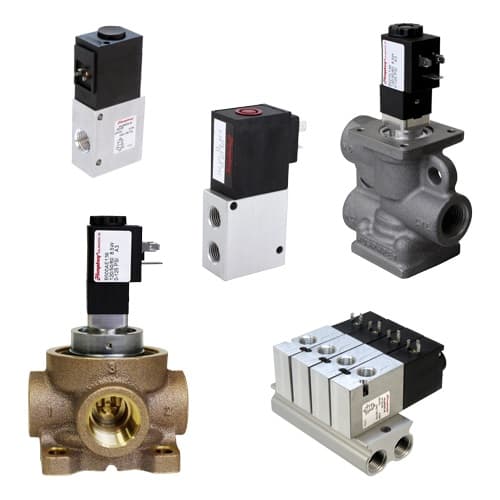
A stock image related to air solenoid.
What Quality Control Measures Are Essential for Air Solenoids?
Quality assurance is integral to the manufacturing of air solenoids, ensuring that products meet both international standards and customer expectations. Understanding the QC processes can help B2B buyers make informed decisions.
What International Standards Should Buyers Look For?
International standards such as ISO 9001, which focuses on quality management systems, are critical for manufacturers of air solenoids. Compliance with these standards indicates that a supplier has established processes for continuous improvement and customer satisfaction. Additionally, industry-specific certifications like CE (Conformité Européenne) for European markets and API (American Petroleum Institute) for oil and gas applications should be verified.
What Are the Key Quality Control Checkpoints?
Quality control typically involves several checkpoints throughout the manufacturing process:
- Incoming Quality Control (IQC): This initial inspection checks raw materials against specified criteria before production begins.
- In-Process Quality Control (IPQC): Ongoing checks during the manufacturing process ensure that components meet design specifications and tolerances.
- Final Quality Control (FQC): This final inspection verifies that the finished air solenoid functions correctly and meets all quality standards.
B2B buyers should confirm that suppliers have robust QC protocols in place at each of these stages.
How Are Air Solenoids Tested for Quality Assurance?
Testing methods play a crucial role in quality assurance for air solenoids. Buyers should understand the common testing procedures to assess supplier reliability.
What Common Testing Methods Are Used?
Typical testing methods include:
- Functional Testing: Ensures that the solenoid operates correctly under expected conditions.
- Leak Testing: Verifies that the solenoid does not leak under pressure, using methods such as pressure decay or helium leak detection.
- Durability Testing: Simulates long-term usage to assess the solenoid’s lifespan and reliability.
Buyers should request documentation of testing results and certifications from suppliers to ensure compliance with relevant standards.
How Can B2B Buyers Verify Supplier Quality Control?
To ensure a reliable supply chain, B2B buyers must take proactive steps to verify the quality control processes of potential suppliers.
What Steps Should Buyers Take for Supplier Verification?
- Conduct Audits: Periodic audits of the supplier’s manufacturing facilities can reveal insights into their QC processes and adherence to standards.
- Request Quality Reports: Suppliers should provide detailed reports on quality control processes, including any certifications or testing results.
- Engage Third-Party Inspectors: Utilizing third-party inspectors can provide an impartial assessment of the supplier’s quality assurance practices.
By implementing these steps, buyers can mitigate risks associated with product quality and compliance.
What Are the Unique QC Considerations for International Buyers?
International B2B buyers, particularly those from Africa, South America, the Middle East, and Europe, face specific challenges when sourcing air solenoids.
How Do Regional Standards Affect Quality Control?
Different regions have varying standards and regulations that can impact the quality of air solenoids. For example, European buyers may prioritize CE certification, while Middle Eastern buyers may focus on compliance with local regulations. Buyers should familiarize themselves with the specific standards applicable to their region and ensure that suppliers are compliant.
What Cultural and Logistical Factors Should Be Considered?
Cultural differences and logistical challenges can also affect the quality assurance process. Buyers should maintain open communication with suppliers to address any potential misunderstandings regarding quality expectations. Additionally, understanding the logistics involved in shipping and handling can help mitigate risks associated with product integrity during transit.
Conclusion: Why Is Understanding Manufacturing and Quality Control Crucial for B2B Buyers?
A comprehensive understanding of manufacturing processes and quality assurance for air solenoids is essential for B2B buyers. By focusing on material preparation, forming, assembly, finishing, and rigorous quality control measures, buyers can make informed decisions that align with their operational needs. This not only ensures product reliability but also fosters long-term supplier relationships, ultimately contributing to a successful procurement strategy.
Practical Sourcing Guide: A Step-by-Step Checklist for ‘air solenoid’
To effectively procure air solenoids for your business needs, following a structured approach can streamline the process and ensure you make informed decisions. This guide outlines essential steps that international B2B buyers should take when sourcing air solenoids, particularly those operating in Africa, South America, the Middle East, and Europe.
Step 1: Define Your Technical Specifications
Clearly outline the technical requirements for the air solenoid you need. This includes specifications such as voltage (12V, 24V, or 110V), size (e.g., 1/4″, 1/2″), and material (brass, stainless steel). Understanding these parameters will help you communicate effectively with suppliers and ensure the solenoid fits your operational needs.
Step 2: Research Potential Suppliers
Conduct thorough research to identify reliable suppliers. Look for manufacturers and distributors with proven track records in your industry. Utilize online platforms, trade shows, and industry publications to gather information. Consider factors such as:
- Geographic location: Proximity can affect shipping costs and delivery times.
- Industry reputation: Check reviews and testimonials from other businesses.
Step 3: Evaluate Supplier Certifications and Standards
It’s essential to verify that suppliers adhere to relevant quality standards and certifications, such as ISO 9001. This ensures that the air solenoids meet international quality and safety standards, reducing the risk of equipment failure. Ask for documentation and review their compliance history.
Step 4: Request Samples for Testing
Before making a bulk purchase, request samples of the air solenoids. Testing samples in your own operational environment allows you to evaluate performance, reliability, and compatibility with your existing systems. Pay attention to:
- Response time: How quickly does the solenoid actuate?
- Durability: Does it withstand the operating conditions (e.g., pressure, temperature)?
Step 5: Compare Pricing and Terms
Gather quotes from multiple suppliers to compare pricing structures. Be sure to consider total cost, including shipping and any potential tariffs or import duties. Additionally, review payment terms and warranties offered by suppliers. This will help you find the best overall value.
Step 6: Negotiate Contract Terms
Once you’ve selected a supplier, negotiate the contract terms to ensure clarity on delivery schedules, payment plans, and after-sales support. Establishing a solid agreement protects both parties and can lead to better service and pricing in future transactions.
Step 7: Plan for Long-term Supply Chain Management
Consider the long-term implications of your supplier relationship. Establish communication channels for ongoing support and feedback. Regularly assess supplier performance to ensure they continue to meet your needs, especially as your business scales or changes.
By following this checklist, B2B buyers can approach the procurement of air solenoids with confidence, ensuring they select the right products and suppliers for their operational needs.
Comprehensive Cost and Pricing Analysis for air solenoid Sourcing
Analyzing the cost and pricing structure for air solenoids is crucial for international B2B buyers, especially those from regions like Africa, South America, the Middle East, and Europe. Understanding the various components of costs, price influencers, and effective negotiation strategies can help buyers make informed purchasing decisions.
What Are the Key Cost Components in Air Solenoid Pricing?
-
Materials: The choice of materials significantly impacts the cost of air solenoids. Common materials include brass, stainless steel, and plastic. Each material has a different cost profile, with stainless steel typically being more expensive due to its durability and resistance to corrosion. For instance, a stainless steel solenoid valve can cost upwards of $40, while plastic alternatives may start around $18.
-
Labor: Labor costs vary based on the manufacturing location. Countries with lower labor costs can produce air solenoids more economically. However, it is essential to consider the skill level of the workforce, as higher expertise often correlates with better quality.
-
Manufacturing Overhead: This includes costs related to utilities, equipment maintenance, and factory space. Efficient manufacturing processes can reduce overhead, allowing suppliers to offer more competitive pricing.
-
Tooling: Custom tooling for specific solenoid designs or specifications can add to the initial costs. However, amortizing these costs over larger production runs can lead to lower per-unit prices.
-
Quality Control (QC): Ensuring the reliability and safety of air solenoids involves thorough quality control processes. Suppliers who implement rigorous QC measures may charge higher prices, but this can lead to significant savings in the long run by reducing failure rates.
-
Logistics: Shipping costs depend on distance, shipping method, and the volume of the order. International buyers should factor in these costs, especially when sourcing from different continents.
-
Margin: Supplier profit margins can vary widely based on brand reputation, market demand, and competition. Established brands may command higher prices due to perceived quality.
What Influences the Pricing of Air Solenoids?
-
Volume and Minimum Order Quantity (MOQ): Suppliers often offer discounts for larger orders. Understanding the MOQ can help buyers negotiate better pricing structures.
-
Specifications and Customization: Custom specifications can lead to higher costs due to the need for specialized tooling or materials. Buyers should be clear about their requirements to avoid unnecessary expenses.
-
Quality and Certifications: Products that meet international quality standards or come with certifications (e.g., ISO) might have a premium price. However, such investments can enhance reliability and reduce the Total Cost of Ownership (TCO).
-
Supplier Factors: The supplier’s reputation, experience, and location can influence pricing. Engaging with reputable suppliers may incur higher costs but can also guarantee better service and product reliability.
-
Incoterms: The agreed terms for shipping and delivery (e.g., FOB, CIF) can affect the final cost. Buyers should carefully evaluate these terms to ensure they understand all associated costs.
How Can International Buyers Effectively Negotiate Air Solenoid Prices?
-
Research and Benchmarking: Buyers should conduct thorough market research to understand price ranges for different types of air solenoids. Knowing competitor pricing can strengthen negotiation positions.
-
Leverage Volume Discounts: Consider consolidating orders to meet MOQs and negotiate bulk pricing. This approach can significantly reduce per-unit costs.
-
Focus on Total Cost of Ownership (TCO): When evaluating suppliers, consider not just the purchase price but also factors such as maintenance costs, lifespan, and failure rates. A higher initial investment may lead to lower overall costs.
-
Build Relationships: Establishing strong relationships with suppliers can lead to better pricing, improved service, and more favorable payment terms.
-
Be Aware of Pricing Nuances: Understand the regional market dynamics, such as currency fluctuations and economic conditions, which can affect pricing. Buyers from Africa, South America, the Middle East, and Europe should be particularly mindful of these factors when sourcing air solenoids.
Conclusion
In conclusion, a comprehensive understanding of the cost structure, pricing influencers, and effective negotiation strategies can empower international B2B buyers in their sourcing of air solenoids. By focusing on these aspects, buyers can achieve cost-efficiency and ensure that their investments yield the best possible returns.
Alternatives Analysis: Comparing air solenoid With Other Solutions
Understanding Alternatives to Air Solenoids
In the industrial landscape, selecting the right component for fluid and gas control can significantly impact efficiency, cost, and operational effectiveness. While air solenoids are popular for their reliability and automation capabilities, several alternative solutions may offer distinct advantages depending on specific use cases. This analysis compares air solenoids with two viable alternatives: electric ball valves and pneumatic actuators.
Comparison Table of Air Solenoid and Alternatives
Comparison Aspect | Air Solenoid | Electric Ball Valve | Pneumatic Actuator |
---|---|---|---|
Performance | High responsiveness and automation | Excellent for on/off control | Good for linear motion and force |
Cost | Moderate initial investment | Typically higher than solenoids | Variable; depends on size and type |
Ease of Implementation | Simple installation with standard fittings | Requires more complex installation | Installation can be cumbersome |
Maintenance | Low maintenance; reliable over time | Moderate; depends on usage | Higher; seals and air supply need regular checks |
Best Use Case | Quick on/off control for fluid handling | Applications needing precise flow control | Heavy-duty applications requiring high force |
Pros and Cons of Electric Ball Valves
Electric ball valves are often used in applications requiring precise flow control. They provide a tight seal and can handle high pressures, making them suitable for various liquids and gases. One of the primary advantages of electric ball valves is their durability and long lifespan, which can result in lower replacement costs over time. However, they typically come at a higher initial cost than air solenoids and may require more complex electrical installations, which can lead to increased setup times. Furthermore, their performance can be affected by the fluid type and temperature, which must be considered when selecting for specific applications.
Pros and Cons of Pneumatic Actuators
Pneumatic actuators are known for their ability to provide significant force and rapid operation, making them ideal for heavy-duty applications such as material handling and automation systems. They are highly efficient, especially in environments where air pressure is readily available. However, pneumatic actuators require a consistent air supply and regular maintenance to ensure optimal performance, as issues with seals and pressure can lead to operational failures. Additionally, their installation can be more cumbersome compared to air solenoids, potentially increasing labor costs during setup.
Conclusion: Choosing the Right Solution for Your Needs
When deciding between air solenoids and their alternatives, B2B buyers should carefully evaluate their specific operational requirements, budget constraints, and maintenance capabilities. Air solenoids may be best suited for applications requiring quick and reliable on/off control with minimal maintenance. In contrast, electric ball valves could be more advantageous for scenarios where precise flow regulation is critical, despite their higher costs. Pneumatic actuators may serve best in heavy-duty applications, provided that the buyer can accommodate the necessary air supply and maintenance needs. Ultimately, the choice will depend on aligning the product features with the buyer’s operational goals and environmental conditions.
Essential Technical Properties and Trade Terminology for air solenoid
What Are the Key Technical Properties of Air Solenoids?
When selecting air solenoids for industrial applications, understanding their technical properties is crucial. Below are some essential specifications that international B2B buyers should consider:
1. Material Grade
The material used in solenoids significantly influences their durability and performance. Common materials include stainless steel, brass, and plastic. Stainless steel is preferred for corrosive environments, while brass offers good conductivity and resistance to wear. Understanding the material grade helps in assessing the solenoid’s lifespan and suitability for specific applications.
2. Voltage Rating
Air solenoids operate at various voltage levels, including 12V, 24V, and 110V. Choosing the correct voltage is vital for compatibility with existing systems. A mismatch can lead to inefficient operation or equipment failure. Buyers should verify the voltage requirements of their systems before making a purchase.
3. Pressure Rating
The pressure rating indicates the maximum pressure the solenoid can handle. This specification is crucial for applications involving gases and liquids under pressure. Selecting a solenoid with an appropriate pressure rating ensures safe and efficient operation, preventing leaks or failures that could disrupt production.
4. Flow Rate
The flow rate, usually expressed in liters per minute (L/min), measures how much fluid can pass through the solenoid in a given time. Higher flow rates are essential for applications requiring rapid actuation. Buyers should evaluate their system’s flow requirements to ensure optimal performance.
5. Response Time
Response time refers to how quickly a solenoid can open or close upon receiving an electrical signal. In fast-paced industrial environments, a quick response time can enhance productivity and system efficiency. Buyers should prioritize solenoids with shorter response times for applications demanding high-speed operations.
6. Operating Temperature Range
The operating temperature range defines the environments in which a solenoid can function effectively. Extreme temperatures can affect performance and longevity. Buyers should assess the environmental conditions of their application to select solenoids that can withstand the required temperature range.
What Are Common Trade Terms Related to Air Solenoids?
Understanding industry jargon can facilitate smoother transactions and negotiations in the B2B space. Here are some key terms that buyers should be familiar with:
1. OEM (Original Equipment Manufacturer)
OEM refers to companies that manufacture products that are marketed by another company. In the context of air solenoids, buyers may seek OEMs for custom solutions tailored to specific applications, ensuring compatibility and quality.
2. MOQ (Minimum Order Quantity)
MOQ is the minimum number of units that a supplier is willing to sell. Understanding MOQ is crucial for budgeting and inventory management. Buyers should inquire about MOQs when assessing suppliers to avoid over-committing to unnecessary stock.
3. RFQ (Request for Quotation)
An RFQ is a document that buyers send to suppliers to request pricing and terms for specific products. Submitting an RFQ can help buyers gather competitive quotes and make informed purchasing decisions. It’s a critical step in the procurement process.
4. Incoterms (International Commercial Terms)
Incoterms are standardized trade terms that define the responsibilities of buyers and sellers in international transactions. Familiarity with Incoterms helps buyers understand shipping costs, risks, and responsibilities associated with their purchases.
5. Lead Time
Lead time is the time it takes from placing an order to receiving the product. Understanding lead times is essential for planning and inventory management. Buyers should communicate their timelines clearly with suppliers to ensure timely delivery.
6. Warranty and Support Terms
Warranty refers to the manufacturer’s promise regarding the performance and durability of the product. Understanding warranty terms can help buyers assess the long-term value of their investment and the level of support they can expect post-purchase.
By grasping these essential technical properties and trade terms, international B2B buyers can make more informed decisions regarding air solenoids, ensuring they choose the right products for their specific needs.
Navigating Market Dynamics and Sourcing Trends in the air solenoid Sector
What Are the Current Market Dynamics and Key Trends in the Air Solenoid Sector?
The air solenoid market is currently experiencing significant growth driven by several global factors. The increasing demand for automation in various industries, including manufacturing, automotive, and food processing, has led to a surge in the adoption of air solenoids. These devices are essential for efficient fluid control systems, which are vital for optimizing production processes. Additionally, the rise of smart technologies and the Internet of Things (IoT) is pushing manufacturers to innovate, resulting in advanced solenoid designs that offer improved performance and energy efficiency.
Emerging B2B tech trends also play a crucial role in shaping the market. For instance, the integration of IoT capabilities in solenoid valves is enabling remote monitoring and control, thus enhancing operational efficiency and reducing downtime. Moreover, the demand for compact and lightweight designs is increasing, driven by the need for space-saving solutions in industrial applications. International buyers, particularly from regions such as Africa and the Middle East, are increasingly focusing on suppliers that offer customizable solutions to meet specific operational requirements.
In terms of market dynamics, the competition among manufacturers is intensifying, leading to price fluctuations and variations in product quality. B2B buyers should be vigilant in evaluating suppliers based on their product offerings, quality certifications, and service support to ensure they make informed purchasing decisions.
How Can Sustainability and Ethical Sourcing Impact the Air Solenoid Supply Chain?
Sustainability and ethical sourcing have become critical considerations for international B2B buyers in the air solenoid sector. The environmental impact of manufacturing processes, including resource consumption and waste generation, is under scrutiny. Buyers are increasingly seeking suppliers who prioritize sustainable practices, such as using recycled materials and implementing energy-efficient production methods.
Ethical supply chains are essential for fostering trust and reliability in business relationships. Buyers should look for suppliers who adhere to international standards and certifications, such as ISO 14001 for environmental management and ISO 45001 for occupational health and safety. Additionally, the use of ‘green’ materials, such as low-impact plastics and recyclable metals, is gaining traction. This shift not only benefits the environment but can also enhance brand reputation and customer loyalty.
As sustainability becomes a key differentiator in the marketplace, B2B buyers should prioritize partnerships with suppliers committed to ethical sourcing and environmental stewardship. This strategic approach can lead to long-term cost savings, improved product quality, and compliance with global regulations.
How Has the Air Solenoid Sector Evolved Over Time?
The evolution of the air solenoid sector has been marked by technological advancements and increasing application diversity. Initially, solenoids were primarily mechanical devices used for simple on/off control. However, the introduction of electronic control systems has transformed their functionality, allowing for precise control over fluid dynamics and enabling integration with automated systems.
Over the years, manufacturers have focused on enhancing the durability and efficiency of solenoid valves. Innovations such as the development of corrosion-resistant materials and compact designs have broadened their application across various industries, including aerospace, pharmaceuticals, and energy. This evolution reflects the growing importance of automation and control in modern manufacturing processes, making air solenoids indispensable tools in today’s industrial landscape.
As B2B buyers navigate this evolving market, understanding these historical trends can provide valuable insights into future developments and help in making strategic purchasing decisions.
Frequently Asked Questions (FAQs) for B2B Buyers of air solenoid
-
How do I select the right air solenoid for my application?
Selecting the appropriate air solenoid valve depends on several factors, including the type of fluid, pressure requirements, and operating voltage. Evaluate your system’s specifications, such as flow rate and connection type, to determine compatibility. Additionally, consider environmental factors, like temperature and exposure to corrosive substances, which may necessitate materials like stainless steel or brass. Consult with suppliers to ensure the chosen solenoid meets your operational needs, and inquire about customization options if standard models do not fit your requirements. -
What is the best voltage for air solenoids in industrial applications?
The best voltage for air solenoids typically depends on the specific application and local power supply availability. Common voltages include 12V, 24V, and 110V. For mobile or low-power applications, 12V and 24V options are often preferred due to their efficiency and ease of integration. Conversely, 110V solenoids may be better suited for stationary equipment connected to standard electrical outlets. It’s crucial to align the voltage with your operational requirements and ensure compatibility with your control systems. -
What are the key factors to consider when vetting air solenoid suppliers?
When vetting suppliers for air solenoids, consider their industry experience, product certifications, and client references. Look for manufacturers with a proven track record in your specific sector, as they will better understand your needs. Evaluate their quality assurance processes, including testing and compliance with international standards. Additionally, assess their responsiveness and customer support, as effective communication can significantly impact your supply chain efficiency. -
How can I ensure quality assurance for my air solenoid purchases?
To ensure quality assurance, request detailed documentation on the manufacturing processes and quality control measures from your supplier. This may include certifications like ISO 9001 or specific industry standards relevant to your application. Consider arranging for third-party inspections or audits if purchasing in bulk, especially from overseas suppliers. Additionally, establish a clear return policy and warranty conditions to safeguard your investment against defects. -
What are the typical minimum order quantities (MOQs) for air solenoids?
Minimum order quantities for air solenoids can vary widely based on the supplier and the specific product line. Generally, MOQs can range from as low as 10 units for standard items to several hundred for custom or specialized valves. When negotiating with suppliers, discuss your anticipated usage to explore options for lower MOQs or trial orders. This approach can help you mitigate financial risk while evaluating the supplier’s product quality and reliability. -
What payment terms should I expect when sourcing air solenoids internationally?
Payment terms for international purchases of air solenoids typically include options such as upfront payment, net 30/60/90 days, or letters of credit. Many suppliers may require a deposit before production, especially for customized products. It’s essential to clarify the payment structure during negotiations and consider using secure payment methods to protect your transaction. Additionally, factor in currency exchange rates and potential import duties when budgeting for your purchase. -
What logistics considerations should I keep in mind when importing air solenoids?
When importing air solenoids, consider factors such as shipping methods, delivery timelines, and customs regulations. Choose a reliable freight forwarder familiar with your destination country’s import laws to ensure compliance and avoid delays. It’s also crucial to calculate total landed costs, including shipping fees, tariffs, and taxes. Ensure that your supplier provides accurate shipping documentation to facilitate a smooth customs clearance process. -
Can I customize air solenoids to fit my specific requirements?
Yes, many suppliers offer customization options for air solenoids, allowing you to tailor specifications such as size, voltage, connection types, and material choices. Discuss your unique requirements with potential suppliers to understand their capabilities and any associated costs. Customization can enhance compatibility with your systems and improve performance, but be mindful of longer lead times and potential MOQs. Always request prototypes or samples to evaluate the customized product before committing to larger orders.
Important Disclaimer & Terms of Use
⚠️ Important Disclaimer
The information provided in this guide, including content regarding manufacturers, technical specifications, and market analysis, is for informational and educational purposes only. It does not constitute professional procurement advice, financial advice, or legal advice.
While we have made every effort to ensure the accuracy and timeliness of the information, we are not responsible for any errors, omissions, or outdated information. Market conditions, company details, and technical standards are subject to change.
B2B buyers must conduct their own independent and thorough due diligence before making any purchasing decisions. This includes contacting suppliers directly, verifying certifications, requesting samples, and seeking professional consultation. The risk of relying on any information in this guide is borne solely by the reader.
Strategic Sourcing Conclusion and Outlook for air solenoid
What are the Key Takeaways for B2B Buyers in Air Solenoid Sourcing?
As international B2B buyers navigate the procurement landscape for air solenoids, strategic sourcing emerges as a critical factor in ensuring operational efficiency and cost-effectiveness. Emphasizing the importance of understanding product specifications, such as voltage requirements and material compatibility, can significantly impact performance and longevity. By prioritizing suppliers that offer a diverse range of options—ranging from compact designs suitable for tight spaces to high-pressure variants—businesses can tailor their choices to meet specific operational needs.
How Can Strategic Sourcing Enhance Supply Chain Resilience?
In the rapidly evolving global marketplace, establishing strong relationships with reliable suppliers is paramount. By investing time in evaluating vendor capabilities and ensuring they adhere to quality standards, buyers can mitigate risks associated with supply chain disruptions. Furthermore, considering regional suppliers from Africa, South America, the Middle East, and Europe can provide logistical advantages and foster local economic growth.
What Does the Future Hold for Air Solenoid Procurement?
Looking ahead, the demand for innovative and efficient air solenoid solutions is set to rise, driven by advancements in automation and fluid control technologies. Buyers are encouraged to stay informed about emerging trends and innovations in the sector to make proactive sourcing decisions. Engaging with industry experts and participating in trade events can provide valuable insights and networking opportunities. Now is the time to leverage strategic sourcing to enhance operational capabilities and ensure a competitive edge in the marketplace.