Master Blow Casting: The Ultimate Cost-Saving Guide (2025)
Introduction: Navigating the Global Market for blow casting
Navigating the global market for blow casting presents a unique set of challenges for B2B buyers, particularly those in emerging markets across Africa, South America, the Middle East, and Europe. As businesses seek reliable suppliers for blow casting products—ranging from packaging solutions to automotive components—understanding the nuances of sourcing and supplier evaluation becomes critical. This guide delves into the multifaceted world of blow casting, offering insights into various types of blow casting processes, their applications across different industries, and essential criteria for vetting suppliers.
With a focus on empowering international B2B buyers, this comprehensive resource aims to equip decision-makers with the knowledge needed to make informed purchasing choices. We will explore the cost implications of different blow casting methods, highlight the importance of quality assurance, and provide actionable strategies for negotiating with suppliers. Additionally, buyers will gain insights into market trends and regional considerations that may impact their sourcing strategies.
By understanding the intricacies of blow casting, businesses can enhance their procurement strategies, ensure product quality, and ultimately drive growth in competitive markets. Whether you are a small business in Africa looking to expand your supplier base or a large corporation in Europe seeking innovative blow casting solutions, this guide will serve as your roadmap to successful sourcing and partnership in the global marketplace.
Understanding blow casting Types and Variations
Type Name | Key Distinguishing Features | Primary B2B Applications | Brief Pros & Cons for Buyers |
---|---|---|---|
Extrusion Blow Molding | Utilizes continuous extrusion of plastic to form a parison, which is then blown into a mold. | Bottles, containers, and hollow parts. | Pros: Cost-effective for large volumes. Cons: Limited to simple shapes. |
Injection Blow Molding | Combines injection molding and blow molding for precise shape and finish. | Specialty bottles, jars, and complex parts. | Pros: High precision and detail. Cons: Higher initial setup costs. |
Stretch Blow Molding | Involves stretching the parison before blowing, enhancing strength and clarity. | PET bottles for beverages and cosmetics. | Pros: Improved mechanical properties. Cons: More complex process requiring specialized equipment. |
Reheat Stretch Blow Molding | Uses preforms that are reheated before being blown into shape, ensuring uniform wall thickness. | High-volume production of PET bottles. | Pros: Excellent for high clarity and strength. Cons: Energy-intensive process. |
Multi-layer Blow Molding | Incorporates multiple layers for enhanced barrier properties and functionality. | Packaging for food, pharmaceuticals, and chemicals. | Pros: Customizable properties. Cons: Complex manufacturing process. |
What Are the Characteristics and Suitability of Extrusion Blow Molding?
Extrusion blow molding (EBM) is characterized by its continuous process where a thermoplastic is extruded to create a parison, which is then inflated into a mold. This method is particularly suitable for producing large quantities of hollow plastic items, such as bottles and containers, at a relatively low cost. For B2B buyers, the key consideration is the trade-off between the simplicity of design and the production volume; while EBM is efficient for straightforward shapes, it may not be ideal for intricate designs.
How Does Injection Blow Molding Stand Out for Precision?
Injection blow molding (IBM) uniquely combines injection molding with blow molding, allowing for high precision in the manufacturing of complex shapes. This method is best suited for specialty products, such as small bottles with intricate designs or tight tolerances. B2B buyers should consider IBM when seeking high-quality finishes and detailed shapes, despite the higher initial setup costs that may be involved.
Why Choose Stretch Blow Molding for Beverage Bottles?
Stretch blow molding (SBM) is distinguished by its technique of stretching the parison before blowing, which enhances the strength and clarity of the final product. This method is particularly relevant for producing PET bottles used in the beverage and cosmetics industries. Buyers should recognize that while SBM offers improved mechanical properties, it requires specialized machinery and a more complex process, which can lead to higher operational costs.
What Are the Benefits of Reheat Stretch Blow Molding?
Reheat stretch blow molding (RSBM) involves reheating preforms before blowing them into shape, resulting in uniform wall thickness and enhanced strength. This technique is particularly advantageous for high-volume production of PET bottles. For B2B buyers, the primary consideration is the energy consumption associated with the reheating process, which may impact overall production costs, but the benefits of clarity and strength can justify the investment.
How Does Multi-layer Blow Molding Enhance Product Functionality?
Multi-layer blow molding is a sophisticated technique that allows for the creation of containers with multiple layers, providing enhanced barrier properties and functionality. This method is especially useful for packaging sensitive products in the food, pharmaceutical, and chemical industries. B2B buyers should evaluate the customization options that multi-layer molding offers, but also be aware of the complexity and potential costs associated with the manufacturing process.
Key Industrial Applications of blow casting
Industry/Sector | Specific Application of Blow Casting | Value/Benefit for the Business | Key Sourcing Considerations for this Application |
---|---|---|---|
Automotive | Production of fuel tanks and reservoirs | Lightweight and durable components that enhance fuel efficiency | Compatibility with existing manufacturing processes and regulations |
Consumer Goods | Manufacturing of bottles and containers | Cost-effective production of high-volume packaging solutions | Material quality and recyclability standards |
Industrial Equipment | Creation of complex machinery parts | Ability to create intricate designs with reduced weight | Precision in design specifications and lead times |
Medical Devices | Production of medical containers | Ensured sterility and safety in medical applications | Compliance with health regulations and material safety |
Electronics | Housing for electronic components | Enhanced protection and lightweight design | Electrical insulation properties and heat resistance |
How is Blow Casting Used in the Automotive Industry?
In the automotive sector, blow casting is primarily utilized to produce lightweight fuel tanks and reservoirs. The process allows manufacturers to create components that not only meet stringent safety standards but also enhance fuel efficiency due to their reduced weight. International buyers, particularly from Africa and South America, should consider sourcing materials that comply with local regulations and are compatible with existing manufacturing processes to ensure seamless integration.
What are the Applications of Blow Casting in Consumer Goods?
Blow casting is extensively used in the consumer goods industry for manufacturing bottles and containers. This method enables the production of high-volume packaging solutions that are both cost-effective and versatile. For B2B buyers in Europe, especially in countries like France, it’s crucial to focus on the recyclability of materials, as sustainable packaging is becoming increasingly important in consumer preferences.
How Does Blow Casting Benefit Industrial Equipment Manufacturing?
In the realm of industrial equipment, blow casting is leveraged to create complex machinery parts that require intricate designs and reduced weight. This application not only improves performance but also reduces material costs. Buyers in the Middle East should prioritize precision in design specifications to ensure the final product meets their operational needs and can withstand demanding environments.
Why is Blow Casting Important for Medical Devices?
The medical device industry utilizes blow casting for the production of sterile medical containers. This application guarantees safety and compliance with health regulations, which are critical in healthcare settings. International buyers need to focus on sourcing materials that meet stringent safety and quality standards, ensuring that products are reliable and effective in their intended use.
How is Blow Casting Used in Electronics Manufacturing?
In the electronics sector, blow casting is employed to create housings for electronic components. This application offers enhanced protection and lightweight design, which are vital for the durability and functionality of electronic devices. Buyers from South America and Europe should ensure that the materials sourced provide adequate electrical insulation and heat resistance to meet the technical demands of their products.
3 Common User Pain Points for ‘blow casting’ & Their Solutions
Scenario 1: Inconsistent Quality of Blow Casted Products
The Problem: One of the most pressing challenges faced by B2B buyers in the blow casting industry is the inconsistency in product quality. This inconsistency can arise from several factors, including variations in raw materials, equipment malfunctions, or inadequate process controls. Buyers from regions like Africa and South America may find that the lack of standardized processes leads to defects, which can affect their supply chains and ultimately lead to financial losses and damaged reputations.
The Solution: To address quality inconsistencies, it is essential to implement a rigorous quality assurance (QA) program. Buyers should prioritize suppliers that adhere to international quality standards, such as ISO 9001. When sourcing blow casting products, request detailed documentation of the supplier’s QA processes, including material specifications, production controls, and testing methods. Additionally, consider establishing a partnership with suppliers who invest in advanced technologies such as automated quality monitoring systems. Regular audits and inspections can also help ensure compliance with quality standards, thereby reducing the risk of defects and enhancing overall product reliability.
Scenario 2: High Production Costs in Blow Casting Operations
The Problem: Many B2B buyers experience challenges with high production costs associated with blow casting operations. This issue can stem from inefficient production processes, wastage of materials, or rising energy costs, particularly in regions where resources are limited. In competitive markets, such as those in Europe and the Middle East, high production costs can significantly erode profit margins and hinder competitiveness.
The Solution: To mitigate production costs, buyers should focus on optimizing the blow casting process. Conduct a thorough review of the production workflow to identify areas where efficiencies can be gained, such as reducing cycle times or minimizing scrap rates. Investing in energy-efficient machinery can lead to substantial long-term savings. Additionally, collaborating with suppliers who offer innovative materials that reduce waste or enhance the production process can be beneficial. Implementing lean manufacturing principles can also streamline operations, further reducing costs while maintaining quality standards.
Scenario 3: Limited Access to Advanced Blow Casting Technologies
The Problem: Buyers, particularly in developing regions such as parts of Africa and South America, often face challenges in accessing advanced blow casting technologies. Limited availability of cutting-edge machinery and techniques can lead to outdated production methods, reducing competitiveness in global markets. This technological gap can hinder innovation and the ability to meet evolving customer demands.
The Solution: To overcome this barrier, B2B buyers should actively seek partnerships with technology providers or manufacturers who specialize in advanced blow casting technologies. Participating in industry trade shows and conferences can help buyers network with suppliers and gain insights into the latest innovations. Additionally, consider forming collaborative agreements with educational institutions or research organizations that focus on materials science and manufacturing technologies. This approach can facilitate knowledge transfer and provide access to new technologies. Investing in training programs for employees to enhance their skills in using advanced equipment can also significantly improve production capabilities and product offerings.
Strategic Material Selection Guide for blow casting
What are the Common Materials Used in Blow Casting?
Blow casting is a versatile manufacturing process used to create hollow plastic parts. The selection of the right material is crucial for ensuring the performance, durability, and cost-effectiveness of the final product. Below, we analyze four common materials used in blow casting, focusing on their properties, advantages, disadvantages, and considerations for international B2B buyers.
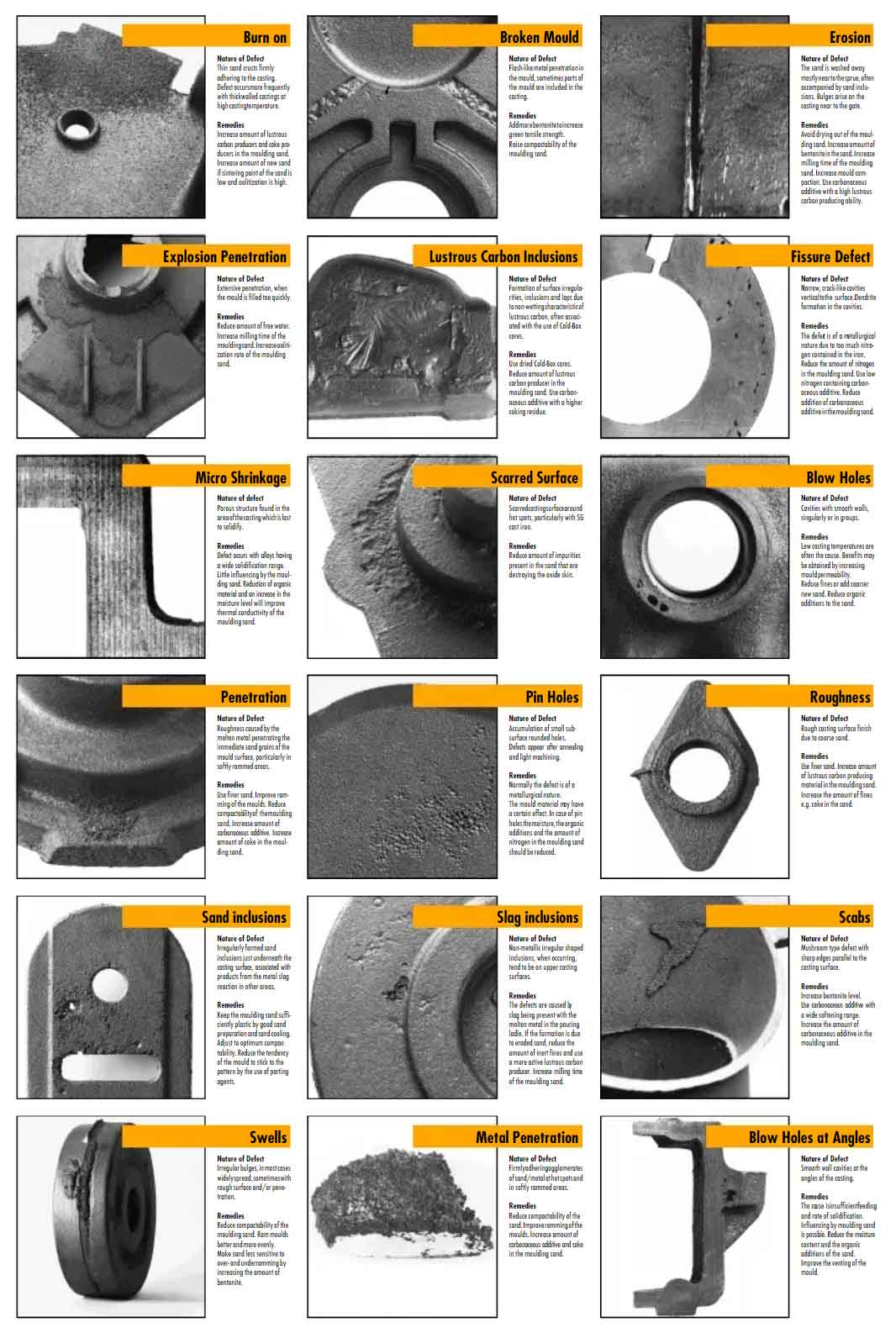
A stock image related to blow casting.
How Does Polyethylene (PE) Perform in Blow Casting?
Polyethylene (PE) is one of the most widely used materials in blow casting due to its excellent balance of properties. It exhibits a high resistance to impact and moisture, making it suitable for various applications, including containers and toys.
Key Properties: PE has a temperature rating of up to 80°C and is resistant to many chemicals, though it can be affected by strong oxidizing agents.
Pros & Cons: Its durability and low cost make it a popular choice. However, it has limited temperature resistance compared to other materials, which may restrict its use in high-heat applications.
Impact on Application: PE is compatible with food-grade applications, making it ideal for packaging. However, it may not be suitable for applications requiring high-temperature resistance.
Considerations for International Buyers: Compliance with food safety standards (like FDA in the U.S. or EU regulations) is crucial. Buyers should also be aware of local preferences for recycled materials, especially in Europe.
What Advantages Does Polypropylene (PP) Offer?
Polypropylene (PP) is another common material used in blow casting, known for its versatility and lightweight nature.
Key Properties: PP has a temperature rating of up to 100°C and exhibits excellent chemical resistance, particularly to acids and bases.
Pros & Cons: Its low density and good fatigue resistance make it suitable for various applications. However, it can be more expensive than PE and may require more complex manufacturing processes.
Impact on Application: PP is ideal for automotive components and industrial containers due to its strength and chemical resistance.
Considerations for International Buyers: Buyers should consider compliance with automotive industry standards, such as ISO/TS 16949, especially in regions like Europe and South America.
Why Choose Polyvinyl Chloride (PVC) for Blow Casting?
Polyvinyl Chloride (PVC) is a widely used thermoplastic in blow casting, known for its rigidity and strength.
Key Properties: PVC can withstand temperatures up to 60°C and offers excellent resistance to environmental degradation.
Pros & Cons: Its durability and low cost make it an attractive option. However, PVC can be less flexible and may require additives to improve its processing characteristics.
Impact on Application: PVC is commonly used in construction materials and piping systems due to its strength and durability.
Considerations for International Buyers: Buyers should be aware of regulations regarding the use of PVC, especially in Europe, where there are stringent environmental regulations.
How Does Acrylonitrile Butadiene Styrene (ABS) Compare?
Acrylonitrile Butadiene Styrene (ABS) is a high-performance thermoplastic known for its toughness and impact resistance.
Key Properties: ABS has a temperature rating of up to 80°C and offers good chemical resistance.
Pros & Cons: Its excellent impact resistance and aesthetic qualities make it suitable for consumer products. However, it is generally more expensive than PE and PP.
Impact on Application: ABS is often used in applications requiring high strength and a good surface finish, such as automotive interiors and electronic housings.
Considerations for International Buyers: Compliance with standards such as ASTM D3965 for automotive applications is essential, particularly for buyers in Europe and the Middle East.
Summary Table of Material Selection for Blow Casting
Material | Typical Use Case for blow casting | Key Advantage | Key Disadvantage/Limitation | Relative Cost (Low/Med/High) |
---|---|---|---|---|
Polyethylene (PE) | Food packaging, toys | High impact resistance | Limited temperature resistance | Low |
Polypropylene (PP) | Automotive components, industrial containers | Excellent chemical resistance | Higher cost and complexity | Medium |
Polyvinyl Chloride (PVC) | Construction materials, piping | Strong and durable | Less flexible, requires additives | Low |
Acrylonitrile Butadiene Styrene (ABS) | Consumer products, automotive interiors | High toughness and aesthetic appeal | Generally more expensive | High |
This strategic material selection guide provides valuable insights for international B2B buyers looking to optimize their blow casting processes, ensuring compliance and suitability for diverse applications across different regions.
In-depth Look: Manufacturing Processes and Quality Assurance for blow casting
What Are the Main Stages in the Blow Casting Manufacturing Process?
Blow casting is a widely used manufacturing process for producing hollow plastic parts. It combines the principles of extrusion and blowing to create items ranging from bottles to complex industrial components. Understanding the stages involved in this process is crucial for B2B buyers seeking to ensure quality and efficiency in production.
1. Material Preparation
The blow casting process begins with the selection and preparation of raw materials, typically thermoplastic polymers such as polyethylene (PE), polypropylene (PP), or polyvinyl chloride (PVC). These materials are usually supplied in pellet form and must be dried to remove moisture, which can adversely affect the final product’s quality.
Actionable Insight: When sourcing materials, B2B buyers should confirm that suppliers utilize high-quality, moisture-free pellets and understand their material processing capabilities. Requesting material safety data sheets (MSDS) can provide critical information on the properties of the materials being used.
2. Forming
The forming stage involves heating the raw material until it reaches a molten state. The molten polymer is then extruded into a parison, a hollow tube-like structure. The parison is clamped into a mold, and air is injected into it, causing it to expand and take the shape of the mold.
Key Techniques:
– Single-Stage Blow Molding: This method combines the extrusion and blowing processes into one machine, making it efficient for high-volume production.
– Two-Stage Blow Molding: This involves separate steps for forming the parison and blowing it into the mold, offering greater flexibility and control over the final product’s thickness.
Actionable Insight: Buyers should inquire about the specific blow molding techniques employed by suppliers, as this can significantly impact production costs and lead times.
3. Assembly
In many cases, blow-molded parts are not standalone products. They may require additional components to be assembled, such as caps, fittings, or labels. The assembly process can involve manual labor or automated systems, depending on the complexity and volume of the products.
Actionable Insight: Buyers should assess the supplier’s assembly capabilities and technologies to ensure they can meet specific project requirements efficiently.
4. Finishing
The final stage in the blow casting process is finishing, which may include trimming excess material, surface treatment, and printing or labeling. This step is crucial for enhancing the aesthetics and functionality of the final product.
Actionable Insight: Request samples of finished products to evaluate the quality of the finishing processes. Understanding the post-production capabilities of suppliers can provide insight into their overall quality assurance practices.
How Is Quality Assurance Implemented in Blow Casting?
Quality assurance (QA) is vital in the blow casting process to ensure that products meet industry standards and customer expectations. B2B buyers must be familiar with the quality control checkpoints and international standards that suppliers adhere to.
Relevant International Standards for Blow Casting
-
ISO 9001: This is the most recognized quality management system standard globally. It emphasizes a process approach to enhance customer satisfaction by meeting customer requirements.
-
CE Marking: This certification indicates that products meet European safety, health, and environmental protection standards. It is essential for B2B buyers in Europe to ensure compliance with CE marking for blow-molded products.
-
API Standards: For industries like oil and gas, American Petroleum Institute (API) standards may apply, ensuring that products meet specific performance and safety requirements.
Actionable Insight: Buyers should request documentation demonstrating compliance with these standards, such as certificates of conformity, to ensure that the supplier’s processes align with recognized quality benchmarks.
What Are the Key Quality Control Checkpoints in Blow Casting?
Quality control checkpoints are critical in the manufacturing process to identify and address issues early. B2B buyers should be aware of the following key checkpoints:
-
Incoming Quality Control (IQC): This involves inspecting raw materials upon delivery to ensure they meet specified requirements before production begins.
-
In-Process Quality Control (IPQC): During production, periodic checks are conducted to monitor parameters such as temperature, pressure, and material flow. This helps in identifying deviations from set standards.
-
Final Quality Control (FQC): After production, the finished products undergo rigorous testing to verify that they meet design specifications and quality standards. This may include dimensional checks, visual inspections, and functional testing.
Actionable Insight: Buyers should establish clear communication with suppliers regarding their quality control processes. Requesting quality control reports can provide transparency and build trust.
How Can B2B Buyers Verify Supplier Quality Control Practices?
To ensure that suppliers maintain robust quality control practices, B2B buyers can take several proactive steps:
-
Conduct Audits: Periodic audits of suppliers’ facilities can provide firsthand insights into their manufacturing and quality assurance processes. Buyers should consider both scheduled and surprise audits.
-
Request Quality Assurance Reports: Suppliers should provide documentation of their quality control processes, including inspection reports and compliance certificates. This information is crucial for verifying adherence to quality standards.
-
Engage Third-Party Inspectors: Hiring independent inspectors can provide an objective assessment of a supplier’s quality control measures and production processes.
Actionable Insight: Develop a checklist for supplier audits that includes specific quality control criteria relevant to blow casting. This will help streamline the evaluation process and ensure all critical areas are covered.
What Are the Nuances in Quality Control for International B2B Buyers?
International B2B buyers, particularly from diverse regions such as Africa, South America, the Middle East, and Europe, must navigate various nuances in quality control:
-
Cultural Differences: Understanding the cultural context of suppliers can enhance communication and collaboration in quality assurance efforts.
-
Regulatory Compliance: Different regions may have specific regulations regarding product safety and quality. Buyers must ensure that suppliers comply with both local and international standards.
-
Logistics and Supply Chain Considerations: Variability in shipping times and customs regulations can affect product delivery and quality. Buyers should maintain open lines of communication with suppliers regarding logistics to mitigate risks.
Actionable Insight: Engage in regular dialogue with suppliers to understand their quality control challenges and establish a cooperative approach to addressing them. This can foster a stronger partnership and improve overall product quality.
By comprehensively understanding the manufacturing processes and quality assurance practices involved in blow casting, B2B buyers can make informed decisions when selecting suppliers. This proactive approach will not only enhance product quality but also ensure compliance with international standards, ultimately leading to successful business outcomes.
Practical Sourcing Guide: A Step-by-Step Checklist for ‘blow casting’
In the competitive landscape of international B2B sourcing, understanding the intricacies of blow casting is essential for making informed procurement decisions. This guide serves as a practical checklist for buyers looking to source blow casting services or products effectively, ensuring that they meet quality standards and align with their business needs.
Step 1: Define Your Technical Specifications
Establishing clear technical specifications is the foundation of a successful sourcing process. Detail the dimensions, material types, and any specific properties your blow cast products must possess. This clarity helps suppliers understand your requirements and allows for accurate quotes and timelines.
- Material Requirements: Specify if you need plastics, resins, or other materials.
- Production Tolerances: Define acceptable variances in size and weight.
Step 2: Research and Identify Potential Suppliers
Conduct thorough market research to identify suppliers who specialize in blow casting. Utilize online platforms, trade shows, and industry networks to compile a list of potential partners. This step is crucial as it sets the stage for all future interactions.
- Industry Directories: Leverage resources like ThomasNet or Alibaba for supplier listings.
- Networking Events: Attend industry conferences to meet suppliers in person.
Step 3: Evaluate Supplier Capabilities
Before committing, it’s crucial to vet suppliers thoroughly. Assess their production capabilities, technology used, and workforce expertise to ensure they can meet your specific needs. Request detailed company profiles, case studies, and references from buyers in similar industries or regions.
- Production Capacity: Inquire about their maximum output and lead times.
- Quality Assurance Processes: Understand their quality control measures and certifications.
Step 4: Request Samples and Prototypes
Once you have shortlisted suppliers, request samples or prototypes of their blow cast products. This hands-on evaluation allows you to assess the quality and suitability of their offerings for your applications.
- Testing Procedures: Discuss how the samples will be tested for durability and compliance with your specifications.
- Feedback Loop: Provide feedback to suppliers to gauge their responsiveness and willingness to make adjustments.
Step 5: Verify Supplier Certifications and Compliance
Ensure that potential suppliers adhere to relevant industry standards and certifications, such as ISO 9001 or specific safety regulations. This verification is essential for mitigating risks associated with quality and compliance issues.
- Documentation Review: Request copies of certifications and compliance documents.
- Third-Party Audits: Consider suppliers that have undergone third-party audits for added assurance.
Step 6: Negotiate Terms and Conditions
Engage in negotiations to finalize pricing, payment terms, and delivery schedules. Clear agreements help avoid misunderstandings later in the process and establish a solid foundation for your business relationship.
- Payment Terms: Clarify upfront costs, payment schedules, and methods of payment.
- Delivery Timelines: Confirm realistic timelines for production and shipping.
Step 7: Establish Communication Protocols
Effective communication is key to a successful sourcing relationship. Set up regular check-ins and establish points of contact to streamline the flow of information throughout the production process.
- Reporting Structures: Define who will be responsible for updates and issue resolution.
- Feedback Mechanisms: Create a system for providing ongoing feedback to ensure alignment with your expectations.
By following this structured checklist, international B2B buyers can make informed decisions when sourcing blow casting services and products, ultimately leading to more successful partnerships and outcomes.
Comprehensive Cost and Pricing Analysis for blow casting Sourcing
What Are the Key Cost Components in Blow Casting Sourcing?
When sourcing blow casting products, understanding the cost structure is crucial for international B2B buyers. The primary cost components include:
-
Materials: The type of raw materials—such as plastics, resins, and additives—significantly impacts the overall cost. High-quality materials can enhance product durability but may also increase initial costs.
-
Labor: Labor costs vary depending on the geographical location of the manufacturing facility. Regions with lower labor costs can provide competitive pricing, but it’s essential to consider the skill level and training of the workforce, which can influence product quality.
-
Manufacturing Overhead: This includes costs associated with running the production facility, such as utilities, maintenance, and administrative expenses. Efficient manufacturing processes can help minimize overhead, affecting the final pricing.
-
Tooling: Blow casting often requires specialized molds and equipment. The tooling costs can be substantial, particularly for customized products. Buyers should consider whether the tooling costs are included in the quoted price or if they will be billed separately.
-
Quality Control (QC): Implementing rigorous quality control measures is essential to ensure product reliability. However, these processes add to the overall cost. Buyers should inquire about the QC standards in place and how they affect pricing.
-
Logistics: Transportation costs can fluctuate based on the distance between the manufacturing site and the buyer’s location, as well as the chosen shipping method. Understanding logistics costs is vital for calculating the total cost of ownership.
-
Margin: Suppliers typically add a margin to cover their costs and ensure profitability. This margin can vary based on market conditions, competition, and the specific supplier’s business model.
How Do Price Influencers Affect Blow Casting Costs?
Several factors influence the pricing of blow casting products, making it imperative for buyers to be aware of these variables:
-
Volume/MOQ (Minimum Order Quantity): Larger orders often lead to lower per-unit costs due to economies of scale. Buyers should assess their needs and consider bulk purchasing to negotiate better pricing.
-
Specifications and Customization: Customized products tailored to specific requirements can significantly increase costs. Buyers should weigh the benefits of customization against the potential price increase.
-
Materials: The choice of materials not only affects the quality but also the cost. Premium materials will drive up the price, so it’s important to evaluate whether the added benefits justify the expense.
-
Quality and Certifications: Products that meet international quality standards or have specific certifications (like ISO) may come at a premium. Buyers should consider the importance of these certifications in their purchasing decision.
-
Supplier Factors: The reputation and reliability of the supplier can influence pricing. Established suppliers may charge more due to their proven track record, while emerging suppliers might offer competitive rates to gain market share.
-
Incoterms: The chosen Incoterms can affect overall costs. For instance, choosing FOB (Free On Board) means the buyer assumes responsibility for shipping costs once the product is loaded onto the transport vessel, while DDP (Delivered Duty Paid) means the supplier covers all shipping and duty costs.
What Tips Can Help International B2B Buyers Negotiate Better Pricing?
For buyers from Africa, South America, the Middle East, and Europe, effective negotiation and understanding pricing nuances can lead to significant savings:
-
Negotiate Terms: Engaging in open discussions about pricing can yield better terms. Don’t hesitate to ask for discounts based on order size or loyalty.
-
Focus on Cost-Efficiency: Consider the Total Cost of Ownership (TCO), which includes purchase price, shipping, maintenance, and disposal costs. Sometimes, a higher initial investment can lead to lower long-term costs.
-
Understand Pricing Nuances: Be aware of local market conditions, currency fluctuations, and geopolitical factors that might affect pricing. This knowledge can empower buyers during negotiations.
-
Build Relationships: Establishing strong relationships with suppliers can lead to better pricing and terms over time. Trust and reliability often lead to preferential treatment in future negotiations.
Disclaimer on Indicative Prices
It’s important to note that prices in the blow casting industry can vary widely based on the aforementioned factors. The estimates provided in this analysis are indicative and should be used as a guideline rather than a definitive pricing structure. Always obtain detailed quotations from multiple suppliers to ensure a comprehensive understanding of the market.
Alternatives Analysis: Comparing blow casting With Other Solutions
Blow casting is a widely-used manufacturing process for producing hollow plastic parts. However, international B2B buyers often seek alternatives that may better fit their specific needs based on performance, cost, and application. Below, we compare blow casting with two viable alternatives: injection molding and rotational molding.
Comparison Table of Blow Casting and Alternatives
Comparison Aspect | Blow Casting | Injection Molding | Rotational Molding |
---|---|---|---|
Performance | High precision for large hollow objects; suitable for low to medium volumes | High precision and excellent surface finish; ideal for high volumes | Good for large, complex shapes; lower precision compared to others |
Cost | Moderate initial setup cost; economical for low to medium production | High initial setup cost; cost-effective for high production volumes | Low initial setup cost; cost-effective for medium to high production volumes |
Ease of Implementation | Requires specialized equipment and skilled labor | Complex machinery; requires technical expertise | Simpler machinery; easier for operators |
Maintenance | Moderate maintenance required; depends on equipment quality | High maintenance; involves regular servicing of molds | Low maintenance; less wear and tear on equipment |
Best Use Case | Ideal for large, hollow products like tanks and bottles | Best for high-volume, precise parts like automotive components | Suitable for large, lightweight parts such as playground equipment |
What Are the Pros and Cons of Injection Molding?
Injection molding is a prevalent method for producing high-quality plastic parts. Its primary advantages include exceptional precision, the ability to produce complex geometries, and a smooth surface finish. This method is especially beneficial for high-volume production, as it minimizes per-unit costs. However, the initial setup costs can be significantly higher due to the need for specialized molds and machinery. Additionally, the process can be less flexible when adapting to design changes after production has begun.
How Does Rotational Molding Compare to Blow Casting?
Rotational molding is another alternative that offers unique advantages. It is particularly effective for producing large, hollow objects with uniform wall thickness. The initial setup costs are lower than those for blow casting and injection molding, making it an attractive option for startups or small businesses. However, the process is generally slower, and it may not achieve the same level of precision or surface finish as injection molding. Rotational molding is ideal for products like kayaks, storage tanks, and playground equipment, where large size and durability are more critical than intricate details.
How Should B2B Buyers Choose the Right Solution?
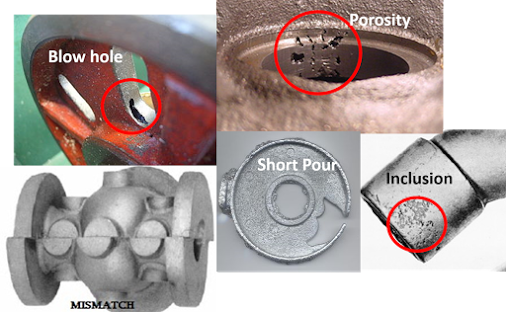
A stock image related to blow casting.
When selecting the appropriate manufacturing solution, B2B buyers must consider several factors, including production volume, cost constraints, and the specific characteristics of the end product. Blow casting is well-suited for large hollow items where precision is not the highest priority. In contrast, injection molding excels in high-volume production scenarios requiring tight tolerances. Rotational molding presents a balanced option for those needing larger items without the complexity of high precision. Ultimately, the decision should align with the buyer’s operational capabilities, budget, and product requirements, ensuring the chosen method enhances productivity and meets market demands.
Essential Technical Properties and Trade Terminology for blow casting
What Are the Essential Technical Properties of Blow Casting?
Understanding the technical properties of blow casting is critical for B2B buyers looking to optimize their procurement strategies. Here are some key specifications that influence the quality and performance of blow-molded products:
-
Material Grade
– Definition: The specific type of plastic used in the blow casting process, such as polyethylene (PE), polypropylene (PP), or polyvinyl chloride (PVC).
– Importance: Different material grades offer varying properties, including flexibility, durability, and resistance to chemicals. Selecting the right material can impact product longevity and suitability for specific applications. -
Tolerance
– Definition: The permissible limit of variation in a physical dimension of a product, typically expressed in millimeters or inches.
– Importance: Tight tolerances are crucial in applications requiring precise fit and function. Understanding tolerance levels helps buyers ensure that the products meet their operational requirements and can reduce costs associated with rework or product failure. -
Wall Thickness
– Definition: The thickness of the material used in the blow-molded product, often varying in different sections of the product.
– Importance: Wall thickness affects strength, weight, and material consumption. Buyers must consider wall thickness to balance durability and cost-effectiveness while ensuring compliance with industry standards. -
Finish Quality
– Definition: The surface texture and aesthetic quality of the blow-molded product, which can range from matte to glossy finishes.
– Importance: A high-quality finish is essential for consumer-facing products, as it can influence marketability and customer satisfaction. Buyers should specify finish requirements based on their target market and branding strategy. -
Impact Resistance
– Definition: The ability of a material to withstand sudden force or shock without breaking.
– Importance: Impact resistance is crucial for products subjected to rough handling or extreme conditions. Buyers in industries like packaging or automotive must prioritize materials that offer superior impact resistance to reduce liability and improve safety.
Which Trade Terminology Should B2B Buyers Understand in Blow Casting?
Familiarity with industry-specific jargon is essential for effective communication and negotiation in the blow casting sector. Here are some commonly used terms:
-
OEM (Original Equipment Manufacturer)
– Definition: A company that produces parts or equipment that may be marketed by another manufacturer.
– Usage: Understanding OEM relationships can help buyers navigate supply chains and ensure they are sourcing quality products that meet their specifications. -
MOQ (Minimum Order Quantity)
– Definition: The smallest quantity of a product that a supplier is willing to sell.
– Usage: Knowing the MOQ can help buyers plan their inventory and manage cash flow effectively. It is especially important for startups or businesses with limited budgets. -
RFQ (Request for Quotation)
– Definition: A document sent to suppliers requesting a detailed quote for specific products or services.
– Usage: Issuing an RFQ allows buyers to compare prices and terms from multiple suppliers, fostering competitive pricing and better negotiation outcomes. -
Incoterms (International Commercial Terms)
– Definition: A set of international rules that define the responsibilities of sellers and buyers for the delivery of goods under sales contracts.
– Usage: Understanding Incoterms is crucial for international transactions, as they clarify shipping responsibilities, risk management, and cost allocation. -
Lead Time
– Definition: The time taken from placing an order until the product is delivered.
– Usage: Buyers should consider lead times when planning production schedules and inventory management. Shorter lead times can enhance responsiveness to market demand.
By grasping these technical properties and trade terms, B2B buyers can make informed decisions that enhance their sourcing strategies and align with their operational goals.
Navigating Market Dynamics and Sourcing Trends in the blow casting Sector
What Are the Current Market Dynamics and Key Trends in Blow Casting?
The blow casting sector is experiencing significant transformation driven by various global trends. The increasing demand for lightweight and durable materials across industries such as automotive, consumer goods, and packaging is propelling the blow casting market. Notably, regions like Africa, South America, the Middle East, and Europe are witnessing a surge in investment in manufacturing capabilities and technological advancements. This growth is largely attributed to the rising adoption of automation and Industry 4.0 technologies, which enhance production efficiency and reduce costs.
Emerging technologies, such as 3D printing and advanced robotics, are redefining sourcing strategies, enabling manufacturers to offer customized solutions while minimizing waste. Moreover, international B2B buyers are increasingly focusing on supplier diversification to mitigate risks associated with global supply chain disruptions. In this context, understanding local market dynamics becomes crucial; for instance, buyers from Africa may prioritize suppliers who can navigate regulatory environments effectively, while European buyers might demand compliance with stringent environmental standards.
Furthermore, the ongoing push for digital transformation is reshaping how businesses approach procurement and supplier relationships. E-procurement platforms and digital marketplaces are gaining traction, offering buyers streamlined access to global suppliers, transparent pricing, and real-time inventory management. As these trends evolve, B2B buyers must remain vigilant and adaptable to leverage emerging opportunities in the blow casting market.
How Can Sustainability and Ethical Sourcing Impact Blow Casting?
Sustainability is becoming a pivotal factor in the decision-making process for B2B buyers in the blow casting sector. The environmental impact of manufacturing processes is under increased scrutiny, prompting companies to adopt greener practices. This includes the use of recycled materials, energy-efficient technologies, and waste reduction strategies. Buyers are encouraged to seek suppliers who are committed to sustainability, as this not only aligns with global environmental goals but also enhances brand reputation.
Ethical sourcing practices are equally essential, particularly in regions where labor practices may vary significantly. Buyers must ensure that their suppliers adhere to ethical labor standards and provide safe working conditions. Certifications such as ISO 14001 for environmental management and Fair Trade certifications can serve as indicators of a supplier’s commitment to sustainability and ethical practices.
Moreover, incorporating sustainable materials and processes into the blow casting supply chain can yield long-term cost savings. For instance, the use of biodegradable plastics and eco-friendly additives can reduce waste disposal costs and enhance product appeal in environmentally conscious markets. By prioritizing sustainability and ethical sourcing, B2B buyers can not only fulfill regulatory requirements but also foster customer loyalty and drive competitive advantage.
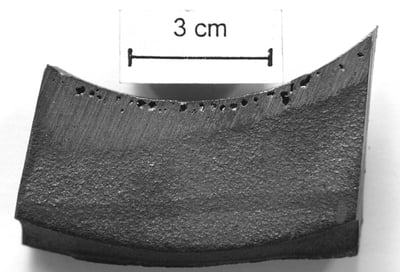
A stock image related to blow casting.
What Is the Evolution of Blow Casting and Its Relevance for B2B Buyers?
The blow casting process has evolved significantly since its inception, transitioning from manual techniques to highly automated systems. Initially utilized for producing simple containers, the technology has advanced to accommodate complex shapes and larger volumes. This evolution has been driven by the increasing demand for high-quality, cost-effective solutions in various industries.
Historically, blow casting was primarily limited to thermoplastics; however, recent innovations have expanded its applications to include thermosetting plastics and composite materials. This diversification allows B2B buyers to access a broader range of products, meeting the specific needs of their industries.
Understanding the historical context of blow casting can provide valuable insights into current market dynamics and future trends. As manufacturers continue to invest in research and development, international B2B buyers stand to benefit from enhanced product offerings, improved sustainability practices, and more robust supply chain solutions. The evolution of blow casting not only highlights the adaptability of the industry but also underscores the importance of strategic sourcing in a rapidly changing global market.
Frequently Asked Questions (FAQs) for B2B Buyers of blow casting
-
How do I solve quality assurance issues when sourcing blow casting products?
To mitigate quality assurance concerns, establish a comprehensive quality control (QC) plan with your supplier. This should include pre-production samples, in-process inspections, and final product evaluations. Request certifications such as ISO 9001 to ensure compliance with international quality standards. Additionally, consider employing third-party inspection services for added assurance, especially if you’re sourcing from regions with different manufacturing standards. Regular communication with your supplier about quality expectations can also help in addressing potential issues early. -
What is the best way to vet suppliers for blow casting?
The best approach to vet suppliers is to conduct thorough research, starting with their online presence, including reviews and testimonials. Request references from previous clients, particularly those in similar industries or regions. Evaluate their manufacturing capabilities by visiting their facilities or utilizing virtual tours. Check for necessary certifications, such as ISO or industry-specific standards, to ensure compliance. Additionally, consider their experience in international trade and familiarity with your target market regulations to ensure smoother transactions. -
What customization options are available for blow casting products?
Customization options for blow casting products often include variations in size, shape, color, and material type. Many suppliers offer design services, allowing you to develop prototypes based on your specifications. Discuss your requirements early in the negotiation process to ensure that the supplier can accommodate your needs. It is also beneficial to use CAD software for precise designs, enabling you to visualize the final product. Be aware that customization may impact lead times and minimum order quantities (MOQs). -
What are the typical minimum order quantities (MOQs) for blow casting?
Minimum order quantities for blow casting can vary significantly based on the supplier and the complexity of the product. Generally, MOQs can range from a few hundred to several thousand units. Suppliers may set higher MOQs for customized products due to the increased setup costs. It’s advisable to discuss MOQs during initial negotiations and explore options for smaller orders or trial runs, particularly if you are testing a new product line or entering a new market. -
What payment terms should I negotiate when sourcing blow casting?
Payment terms are crucial in establishing a secure transaction framework. Common terms include a deposit (typically 30-50%) upfront, with the balance paid upon completion or prior to shipment. Consider negotiating payment via letter of credit (LC) for larger orders, as it provides additional security for both parties. Explore the option of staggered payments based on production milestones to further reduce risk. Always ensure that the payment terms are documented clearly in the contract to avoid misunderstandings. -
How can I ensure timely logistics for blow casting shipments?
To ensure timely logistics, collaborate closely with your supplier on shipping schedules and choose reliable freight forwarders experienced in international shipping. Discuss lead times early in the process and factor in potential delays due to customs clearance or local regulations. Utilizing technology, such as shipment tracking systems, can provide real-time updates. It’s also wise to have contingency plans for logistics disruptions, especially if you are sourcing from regions prone to political or economic instability. -
What are the key considerations for international trade compliance in blow casting?
When engaging in international trade, ensure compliance with both exporting and importing regulations. Familiarize yourself with tariffs, trade agreements, and customs documentation required for your specific products. Utilize resources such as trade compliance consultants or legal advisors to navigate complex regulations in target markets. Ensure that your supplier is also compliant with international safety standards, as this can impact your ability to sell in certain regions. -
What are the advantages of sourcing blow casting from emerging markets?
Sourcing blow casting from emerging markets can offer significant cost advantages due to lower labor and production costs. These regions often have rapidly developing manufacturing capabilities and increasing technological advancements. Additionally, establishing relationships with suppliers in emerging markets can provide access to unique materials and innovative designs. However, it’s essential to conduct thorough due diligence to mitigate risks associated with quality, lead times, and logistics.
Important Disclaimer & Terms of Use
⚠️ Important Disclaimer
The information provided in this guide, including content regarding manufacturers, technical specifications, and market analysis, is for informational and educational purposes only. It does not constitute professional procurement advice, financial advice, or legal advice.
While we have made every effort to ensure the accuracy and timeliness of the information, we are not responsible for any errors, omissions, or outdated information. Market conditions, company details, and technical standards are subject to change.
B2B buyers must conduct their own independent and thorough due diligence before making any purchasing decisions. This includes contacting suppliers directly, verifying certifications, requesting samples, and seeking professional consultation. The risk of relying on any information in this guide is borne solely by the reader.
Strategic Sourcing Conclusion and Outlook for blow casting
What Are the Key Takeaways for B2B Buyers in Blow Casting?
In conclusion, effective strategic sourcing is paramount for international B2B buyers engaged in the blow casting industry. By prioritizing quality suppliers, understanding market dynamics, and leveraging technological advancements, businesses can significantly enhance their operational efficiency and product quality. Buyers should focus on building strong relationships with manufacturers, particularly in regions like Africa, South America, the Middle East, and Europe, where local expertise can provide competitive advantages.
How Can International Buyers Benefit from Strategic Sourcing?
The value of strategic sourcing extends beyond mere cost savings; it fosters innovation, flexibility, and sustainability within supply chains. As global markets evolve, buyers must remain agile and responsive to shifting demands. Engaging with suppliers who prioritize sustainable practices can also enhance brand reputation and meet increasing consumer expectations for eco-friendly products.
What Should Buyers Consider Moving Forward?
Looking ahead, international B2B buyers are encouraged to adopt a proactive approach to sourcing in the blow casting sector. By investing in data analytics and market research, they can better anticipate trends and consumer needs. As the industry continues to grow, embracing collaboration and transparency with suppliers will be essential for driving long-term success. Now is the time to strengthen your sourcing strategy and position your business for future opportunities.