Master Ceramic Machining: The Complete Guide for 2025
Introduction: Navigating the Global Market for ceramic machining
Ceramic machining is a vital process for international B2B buyers seeking to source high-quality components across various industries, including aerospace, medical devices, and electronics. However, navigating the complexities of this specialized market can pose significant challenges, particularly when it comes to ensuring quality, precision, and cost-effectiveness. In this guide, we delve into the intricacies of ceramic machining, exploring different types of materials, machining techniques, and their specific applications. We also provide actionable insights on supplier vetting, pricing structures, and quality control measures.
For buyers from Africa, South America, the Middle East, and Europe—regions characterized by diverse manufacturing needs—understanding the ceramic machining landscape is crucial for making informed purchasing decisions. By outlining best practices and industry standards, this guide empowers you to effectively evaluate potential suppliers and select the right machining processes tailored to your project requirements.
In the following sections, we will address common challenges faced in the ceramic machining industry and present innovative solutions that can streamline your procurement process. Whether you are looking for advanced technical ceramics or seeking suppliers capable of high-tolerance machining, our comprehensive guide equips you with the knowledge necessary to enhance your sourcing strategies and drive successful outcomes in the global market.
Understanding ceramic machining Types and Variations
Type Name | Key Distinguishing Features | Primary B2B Applications | Brief Pros & Cons for Buyers |
---|---|---|---|
CNC Milling | High precision, versatile for complex shapes | Aerospace, automotive, electronics | Pros: Excellent surface finish, tight tolerances. Cons: Can be costly for low-volume runs. |
Grinding | Utilizes abrasive particles for surface finishing | Medical devices, precision instruments | Pros: Achieves fine surface quality. Cons: Tool wear can be high, requiring frequent replacements. |
Turning | Rotational machining for cylindrical parts | Oil & gas, manufacturing components | Pros: Efficient for bulk production. Cons: Limited to specific geometries. |
Electrical Discharge Machining (EDM) | Non-contact method using electrical discharges | Aerospace, tooling, mold making | Pros: Can machine complex shapes. Cons: Slower process compared to traditional methods. |
Laser Machining | Uses focused laser beams for precision cutting | Electronics, telecommunications | Pros: High accuracy and minimal thermal impact. Cons: Equipment can be expensive and requires specialized training. |
What Are the Key Characteristics of CNC Milling in Ceramic Machining?
CNC milling is distinguished by its ability to create intricate shapes and features with high precision. This method is particularly suitable for complex geometries, making it ideal for industries like aerospace and electronics, where precision is paramount. When considering CNC milling, buyers should assess the machine’s capability to handle the specific ceramic material and the associated costs for setup and operation, especially for low-volume production runs.
How Does Grinding Benefit B2B Buyers in Ceramic Machining?
Grinding is a prevalent technique for achieving fine surface finishes on ceramic parts. It employs abrasive wheels or belts, making it effective for both large-scale material removal and achieving tight tolerances. This method is particularly useful in sectors such as medical device manufacturing and precision instruments. Buyers should consider the trade-off between the high-quality finish it provides and the potential for increased tool wear, which can impact long-term operational costs.
Why Is Turning a Viable Option for Ceramic Machining?
Turning is a machining process where a ceramic workpiece is rotated against a cutting tool, making it effective for producing cylindrical components like tubes and shafts. It is widely used in industries such as oil and gas and general manufacturing. Buyers should evaluate the specific geometries they require, as turning is limited to cylindrical forms, and consider the durability of specialized cutting tools needed for ceramic materials.
What Advantages Does Electrical Discharge Machining (EDM) Offer?
EDM is a non-contact machining process that utilizes electrical discharges to remove material, allowing for the creation of complex shapes that are difficult to achieve with traditional methods. This technique is particularly advantageous in aerospace and mold-making applications. Buyers should note that while EDM offers precision and versatility, it typically operates at a slower pace compared to conventional machining methods, which may affect production timelines.
How Does Laser Machining Enhance Ceramic Machining Processes?
Laser machining employs concentrated laser beams to cut through ceramic materials with high accuracy, making it suitable for applications in electronics and telecommunications. This method is characterized by minimal thermal impact on the surrounding material, preserving the integrity of delicate components. However, buyers should be aware that the initial investment in laser equipment can be significant, and specialized training may be necessary to operate the machinery effectively.
Key Industrial Applications of ceramic machining
Industry/Sector | Specific Application of Ceramic Machining | Value/Benefit for the Business | Key Sourcing Considerations for this Application |
---|---|---|---|
Aerospace | Engine components and turbine blades | Enhanced performance and durability under extreme conditions | Certification of materials, precision tolerances, and heat resistance |
Electronics | Ceramic substrates for electronic circuits | Improved thermal management and electrical insulation | Supplier reliability, compliance with international standards, and customization capabilities |
Medical Devices | Surgical instruments and implants | Biocompatibility and resistance to wear and corrosion | Quality assurance processes, certifications, and material traceability |
Automotive | Brake components and sensors | Increased safety and performance in high-stress environments | Compliance with automotive standards, durability testing, and cost-effectiveness |
Energy & Utilities | Insulators for power transmission | Enhanced reliability and reduced maintenance costs | Supplier experience in high-voltage applications, material quality, and lead times |
How is Ceramic Machining Used in Aerospace Applications?
In the aerospace sector, ceramic machining is critical for producing engine components and turbine blades that can withstand extreme temperatures and pressures. The high hardness and durability of ceramic materials reduce wear and extend the lifespan of these components, which is essential for safety and performance. International buyers must ensure that suppliers can meet stringent certification requirements and precision tolerances, particularly for high-performance applications that demand exceptional reliability.
What are the Applications of Ceramic Machining in Electronics?
Ceramic machining plays a vital role in the electronics industry, particularly in the manufacturing of ceramic substrates for electronic circuits. These substrates provide superior thermal management and electrical insulation, which are essential for the reliability of electronic devices. B2B buyers should consider suppliers that demonstrate compliance with international standards, as well as those who offer customization capabilities to meet specific design requirements.
How Does Ceramic Machining Benefit Medical Device Manufacturing?
In the medical field, ceramic machining is employed to create surgical instruments and implants that require high levels of biocompatibility and wear resistance. The unique properties of ceramics make them ideal for applications that demand durability and hygiene. International buyers need to prioritize suppliers with robust quality assurance processes and relevant certifications, as well as those who can provide material traceability to ensure safety in medical applications.
What Role Does Ceramic Machining Play in Automotive Components?
Ceramic machining is increasingly utilized in the automotive industry for manufacturing brake components and sensors. The use of ceramics in these applications leads to improved safety and performance, particularly in high-stress environments. Buyers from international markets must look for suppliers who comply with automotive industry standards, conduct thorough durability testing, and offer cost-effective solutions without compromising on quality.
How is Ceramic Machining Applied in Energy and Utility Sectors?
In the energy and utilities sectors, ceramic machining is essential for producing insulators used in power transmission systems. These insulators enhance reliability and reduce maintenance costs by providing excellent electrical insulation and resistance to environmental factors. When sourcing, international buyers should focus on suppliers with extensive experience in high-voltage applications, as well as those who can guarantee material quality and timely delivery.
3 Common User Pain Points for ‘ceramic machining’ & Their Solutions
Scenario 1: Difficulty in Achieving Precision and Tolerances in Ceramic Machining
The Problem: One of the most significant challenges faced by B2B buyers in ceramic machining is achieving the desired precision and tolerances. Ceramic materials, known for their exceptional hardness and brittleness, can complicate the machining process. Buyers often find that their components do not meet the specified tolerances, leading to increased costs and delays in production. The fragility of ceramics can also result in chipping or cracking during machining, further complicating the production of intricate parts.
The Solution: To overcome these precision challenges, it is essential to invest in advanced machining technologies and tooling. Consider sourcing cutting tools with diamond coatings or using ceramic-based materials that provide superior hardness and wear resistance. When specifying machining parameters, focus on optimizing cutting speeds, feed rates, and depths of cut to minimize tool wear and maximize surface quality. Implementing a rigorous quality control process, such as using Coordinate Measuring Machines (CMM), will ensure that all components are manufactured to exact specifications. Additionally, consider post-machining processes like thermal stress relieving to enhance the durability and performance of the final product.
Scenario 2: Excessive Tool Wear and Short Tool Life
The Problem: B2B buyers often experience excessive tool wear when machining ceramics, leading to increased operational costs and reduced productivity. The high hardness of ceramic materials not only wears down cutting tools quickly but also affects the overall efficiency of the machining process. This scenario can result in frequent tool replacements, which can be both time-consuming and costly, ultimately impacting delivery schedules and customer satisfaction.
The Solution: To address tool wear issues, prioritize the selection of high-performance tooling designed specifically for ceramic machining. Tools with advanced materials, such as polycrystalline diamond (PCD) or cubic boron nitride (CBN), are engineered to withstand the rigors of machining hard materials. Additionally, utilizing coolant or lubricants during the machining process can significantly reduce friction and heat buildup, extending tool life. Regularly monitoring tool condition and performance through scheduled maintenance checks will also help identify when tools need replacement, minimizing downtime and ensuring consistent production quality.
Scenario 3: Challenges in Surface Finish Quality and Microcracking
The Problem: Achieving the desired surface finish in ceramic components is often a daunting task for B2B buyers. The brittleness of ceramics makes them susceptible to microcracks and surface roughness during machining, which can compromise the integrity of the final product. Buyers may find that after machining, the components require extensive finishing processes, leading to additional costs and delays in the supply chain.
The Solution: To enhance surface finish quality and reduce the likelihood of microcracking, it’s crucial to implement a multi-step machining approach. Start with rough machining to remove bulk material, followed by finer machining processes such as grinding or lapping to achieve the desired surface finish. Choosing the right abrasives and grinding parameters is essential; for instance, using finer grit sizes can help improve surface quality without introducing significant stress. Additionally, consider integrating a post-machining polishing process that can alleviate residual stresses and enhance the final surface finish. Regular training for machinists on handling ceramics can also be beneficial, ensuring they understand the nuances of working with these materials to minimize defects.
Strategic Material Selection Guide for ceramic machining
What Are the Key Properties of Alumina Ceramics for B2B Buyers?
Alumina ceramics, primarily composed of aluminum oxide (Al2O3), are renowned for their exceptional hardness and wear resistance. They can withstand high temperatures, typically rated up to 1600°C, making them suitable for applications in harsh environments. Additionally, alumina exhibits excellent chemical resistance to acids and alkalis, which is crucial for industries like chemical processing and pharmaceuticals.
Pros & Cons: Alumina ceramics are durable and cost-effective, often considered a standard in ceramic machining. However, their brittleness can lead to cracking under mechanical stress, and the manufacturing process can be complex, requiring specialized equipment for shaping and finishing.
Impact on Application: Given their high dielectric strength, alumina ceramics are ideal for electrical insulators and substrates in electronic devices. Their compatibility with various media, including aggressive chemicals, enhances their utility in diverse applications.
Considerations for International Buyers: Compliance with standards such as ASTM and DIN is critical when sourcing alumina ceramics. Buyers from regions like Africa and the Middle East should ensure that suppliers can meet these standards, as they can impact product reliability and safety.
How Does Zirconia Ceramic Compare in Terms of Performance?
Zirconia ceramics, or zirconium dioxide (ZrO2), are characterized by their superior toughness and strength compared to other ceramics. They can operate effectively at temperatures exceeding 2000°C and exhibit excellent resistance to wear and corrosion.
Pros & Cons: The primary advantage of zirconia is its ability to withstand high mechanical stress without fracturing, making it suitable for demanding applications like turbine blades and dental implants. However, the high cost of zirconia ceramics and the complexity of their manufacturing processes can be significant drawbacks for B2B buyers.
Impact on Application: Zirconia’s low thermal conductivity makes it an excellent choice for thermal barrier coatings. Its compatibility with various aggressive media also makes it suitable for chemical processing applications.
Considerations for International Buyers: Buyers should be aware of the differences in quality and specifications across regions. Compliance with international standards is essential, especially for applications in the medical and aerospace sectors, where the margin for error is minimal.
What Are the Advantages of Silicon Nitride in Ceramic Machining?
Silicon nitride (Si3N4) is a high-performance ceramic known for its exceptional strength and thermal stability. It operates effectively at temperatures up to 1400°C and has excellent resistance to thermal shock and oxidation.
Pros & Cons: Silicon nitride’s high fracture toughness and low density make it suitable for lightweight applications, such as in automotive and aerospace components. However, its higher manufacturing costs and the need for advanced machining techniques can be limiting factors for some buyers.
Impact on Application: Its excellent wear resistance and low thermal expansion make silicon nitride ideal for bearings, cutting tools, and high-temperature applications.
Considerations for International Buyers: Buyers from Europe and South America should prioritize suppliers who can demonstrate compliance with ISO standards, as these can significantly impact product quality and performance.
How Do Glass Ceramics Fit into the Ceramic Machining Landscape?
Glass ceramics are a unique class of materials that combine the properties of glass and ceramics. They offer excellent thermal stability and can withstand temperatures up to 1200°C.
Pros & Cons: Glass ceramics are highly resistant to thermal shock and have good mechanical strength, making them suitable for applications like cooktops and dental prosthetics. However, they can be more challenging to machine due to their brittleness, and their cost can be higher than traditional ceramics.
Impact on Application: These materials are particularly effective in applications requiring low thermal expansion and high strength, such as in the aerospace and electronics sectors.
Considerations for International Buyers: When sourcing glass ceramics, buyers should be aware of the specific standards applicable in their regions, as compliance can vary significantly.
Summary Table of Material Analysis
Material | Typical Use Case for Ceramic Machining | Key Advantage | Key Disadvantage/Limitation | Relative Cost (Low/Med/High) |
---|---|---|---|---|
Alumina Ceramics | Electrical insulators | High hardness and chemical resistance | Brittle, prone to cracking | Medium |
Zirconia Ceramics | Turbine blades, dental implants | Superior toughness and strength | High cost, complex manufacturing | High |
Silicon Nitride | Bearings, cutting tools | Excellent thermal stability and fracture toughness | Higher manufacturing costs | High |
Glass Ceramics | Cooktops, dental prosthetics | Good thermal shock resistance | More challenging to machine, higher cost | Medium to High |
This strategic material selection guide provides international B2B buyers with essential insights into the properties, advantages, and limitations of various ceramics used in machining. Understanding these factors can significantly enhance decision-making processes and optimize product performance across diverse applications.
In-depth Look: Manufacturing Processes and Quality Assurance for ceramic machining
What Are the Key Stages in the Ceramic Machining Manufacturing Process?
Ceramic machining is a sophisticated process that involves several critical stages to ensure the production of high-quality ceramic components. The main stages include material preparation, forming, assembly, and finishing. Understanding these stages is essential for B2B buyers seeking reliable suppliers.
How is Material Prepared for Ceramic Machining?
Material preparation begins with selecting the appropriate ceramic materials, which may include alumina, zirconia, or silicon carbide, depending on the application. Once the material is chosen, it undergoes various processes such as crushing, milling, and sieving to achieve the desired particle size and consistency. This step is crucial as it directly affects the final product’s properties, including strength and durability.
After the material is processed, it is often mixed with additives to enhance its machinability and performance. The mixture is then dried to remove excess moisture, ensuring that it is ready for the forming stage.
What Techniques Are Used in Forming Ceramic Components?
The forming stage involves shaping the prepared ceramic material into the desired dimensions. Common techniques include:
- Pressing: This method uses high pressure to compact the ceramic powder into molds. It is suitable for producing complex shapes with high density.
- Injection Molding: This technique allows for the creation of intricate parts by injecting a ceramic slurry into molds. It is ideal for mass production due to its efficiency.
- Isostatic Pressing: This method applies equal pressure from all directions, resulting in uniform density and improved mechanical properties.
Each technique has its advantages and is chosen based on the component’s design requirements and production volume.
How is Assembly Handled in Ceramic Machining?
The assembly stage is relevant for complex products that require multiple ceramic components to be joined together. Techniques such as brazing and adhesive bonding are commonly employed, depending on the thermal and mechanical properties required. Proper alignment and fit are critical to ensure the integrity of the final product, particularly in applications such as aerospace or medical devices.
What Finishing Processes Are Essential for Quality Ceramic Products?
Finishing processes are crucial in ceramic machining as they enhance the product’s surface quality and dimensional accuracy. Key finishing techniques include:
- Grinding: Utilized to achieve tight tolerances and a smooth surface finish. This process is particularly challenging due to the hardness of ceramics.
- Polishing: This technique further refines the surface, reducing roughness and improving aesthetic appeal.
- Lapping: A precision finishing process that uses abrasive slurry to achieve extremely tight tolerances and surface finishes.
These finishing processes are vital for ensuring that the ceramic components meet the stringent requirements of various industries.
How is Quality Assurance Implemented in Ceramic Machining?
Quality assurance (QA) in ceramic machining involves rigorous standards and checkpoints to ensure that the final products meet international and industry-specific guidelines.
What International Standards Should B2B Buyers Look for?
International standards such as ISO 9001 are crucial for ensuring consistent quality management systems among suppliers. Additionally, industry-specific certifications like CE (Conformité Européenne) for European markets and API (American Petroleum Institute) standards for oil and gas applications are significant. B2B buyers should verify that their suppliers hold these certifications to ensure compliance with safety and performance criteria.
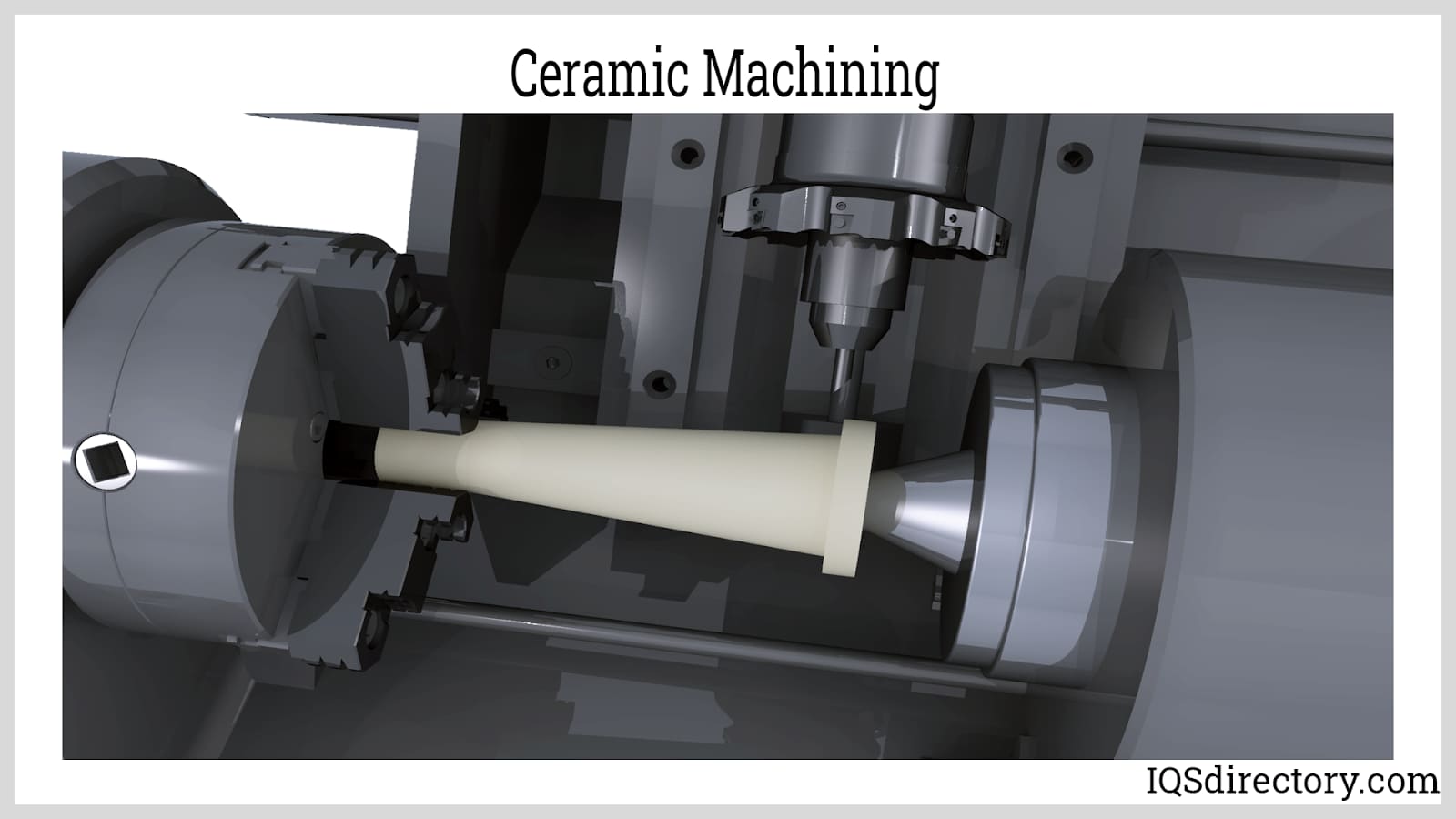
A stock image related to ceramic machining.
What Are the Key Quality Control Checkpoints in Ceramic Machining?
Quality control (QC) checkpoints are implemented at various stages of the manufacturing process:
- Incoming Quality Control (IQC): This stage involves inspecting raw materials to ensure they meet specified requirements before processing begins.
- In-Process Quality Control (IPQC): During manufacturing, periodic checks are performed to monitor critical parameters such as dimensions, surface finish, and tolerances.
- Final Quality Control (FQC): After finishing, the final products undergo comprehensive testing to verify that they meet all specifications.
These checkpoints are essential for maintaining high-quality standards throughout the production process.
What Common Testing Methods Are Used in Quality Assurance?
Testing methods in ceramic machining may include:
- Dimensional Inspection: Using coordinate measuring machines (CMM) to verify that the parts meet specified dimensions.
- Surface Roughness Testing: Assessing the surface finish to ensure it meets the required standards.
- Mechanical Testing: Evaluating properties such as hardness, strength, and fracture toughness to confirm the material’s suitability for its intended application.
Understanding these testing methods helps B2B buyers gauge the effectiveness of their suppliers’ quality assurance processes.
How Can B2B Buyers Verify Supplier Quality Control?
B2B buyers can take several steps to verify the quality control processes of their suppliers:
- Conduct Audits: Regular audits can provide insights into the supplier’s production practices and adherence to quality standards.
- Request Quality Reports: Suppliers should provide detailed quality reports that outline their testing results and compliance with standards.
- Engage Third-Party Inspectors: Utilizing independent inspectors can offer an unbiased evaluation of the supplier’s quality control measures.
These strategies are particularly important for buyers from Africa, South America, the Middle East, and Europe, where supply chain complexities may necessitate additional verification.
What Are the Quality Control Nuances for International B2B Buyers?
International B2B buyers must be aware of the nuances related to quality control when dealing with suppliers from different regions. Understanding local regulations, cultural differences in business practices, and language barriers can significantly impact quality assurance processes. Buyers should establish clear communication channels and expectations regarding quality standards to mitigate these challenges.
Additionally, being informed about potential delays in the supply chain and how they may affect product quality is essential. For instance, sourcing materials from regions with varying quality standards can influence the overall quality of the finished product.
By recognizing these factors, B2B buyers can make more informed decisions when selecting suppliers for ceramic machining projects, ensuring they receive high-quality components that meet their specifications and industry requirements.
Practical Sourcing Guide: A Step-by-Step Checklist for ‘ceramic machining’
This guide provides a practical checklist for international B2B buyers seeking to procure ceramic machining services. By following these steps, you can ensure that you select the right suppliers and achieve high-quality results tailored to your specific requirements.
Step 1: Define Your Technical Specifications
Clearly outline the specific properties and dimensions of the ceramic components you need. This includes material type (e.g., alumina, zirconia), required tolerances, and surface finish quality. A well-defined specification helps potential suppliers understand your needs and enables accurate quotations.
Step 2: Research Potential Suppliers
Conduct thorough research to identify suppliers with a proven track record in ceramic machining. Look for companies that specialize in the type of ceramics you require and have experience in your industry. Utilize online directories, industry forums, and trade shows to gather information on various suppliers.
Step 3: Evaluate Supplier Capabilities
Before committing, assess the capabilities of your shortlisted suppliers. Request details on their machining technologies, equipment, and expertise in handling ceramics. Key factors to consider include:
– Precision Equipment: Ensure they use state-of-the-art CNC machines and tools designed for high-tolerance machining.
– Quality Control Processes: Inquire about their quality assurance measures, such as the use of CMM (Coordinate Measuring Machines) for dimensional accuracy.
Step 4: Verify Certifications and Compliance
Check if the suppliers have relevant certifications, such as ISO 9001 or industry-specific standards. These certifications indicate that the supplier adheres to quality management practices and can produce components that meet international standards. Additionally, ensure compliance with environmental regulations, particularly if your project has sustainability goals.
Step 5: Request Samples and Prototypes
Before finalizing your supplier, request samples or prototypes of their work. This step allows you to evaluate the quality of their machining and the properties of the ceramic materials they use. Look for:
– Surface Finish: Inspect the surface quality for any microcracks or imperfections.
– Dimensional Accuracy: Ensure that the samples meet your specified tolerances.
Step 6: Discuss Lead Times and Production Capacity
Engage in a conversation about lead times and the supplier’s production capacity. Understanding their timelines helps you plan your project effectively and avoid delays. Ask about their ability to scale production if your demand increases, as well as their contingency plans for unforeseen circumstances.
Step 7: Establish Communication and Support Channels
Effective communication is crucial for a successful partnership. Ensure that the supplier has a dedicated team for customer support and technical inquiries. Discuss their preferred communication methods and response times, and establish a clear point of contact for any project-related queries.
By following this checklist, B2B buyers can make informed decisions when sourcing ceramic machining services. This structured approach not only minimizes risks but also enhances the chances of obtaining high-quality ceramic components tailored to your specific needs.
Comprehensive Cost and Pricing Analysis for ceramic machining Sourcing
What Are the Key Cost Components in Ceramic Machining?
When sourcing ceramic machining services, understanding the cost structure is crucial for international B2B buyers. The primary components influencing the overall cost include:
-
Materials: The type of ceramics used (e.g., alumina, zirconia) significantly affects pricing. High-performance materials often come with a premium due to their specialized properties.
-
Labor: Skilled labor is essential for machining ceramics due to their unique properties and challenges. Labor costs can vary based on the region, expertise level, and complexity of the machining processes involved.
-
Manufacturing Overhead: This encompasses costs related to machinery maintenance, utilities, and facilities. Advanced technologies like CNC machining require higher overhead due to the need for regular updates and skilled technicians.
-
Tooling: The costs of cutting tools, especially those with diamond coatings or specialized ceramics, can be substantial. Tooling expenses also depend on the complexity and precision required for the parts being produced.
-
Quality Control (QC): Ensuring that the ceramic components meet strict tolerances and specifications adds to the cost. Implementing rigorous QC processes may involve additional testing and certification.
-
Logistics: Shipping costs can vary significantly based on the distance, mode of transport, and Incoterms. These factors are especially pertinent for international buyers, as they impact the final landed cost.
-
Margin: Supplier margins can vary based on their market positioning and the perceived value of their services. Understanding these margins can help in negotiations.
How Do Price Influencers Impact Ceramic Machining Costs?
Several factors can influence the pricing of ceramic machining services:
-
Volume/MOQ: Bulk orders often lead to lower per-unit costs due to economies of scale. Establishing a minimum order quantity (MOQ) with suppliers can also provide leverage in negotiations.
-
Specifications and Customization: Customized parts with specific tolerances or finishes will typically cost more. The more complex the design, the higher the machining costs.
-
Materials Used: Different ceramics have varying costs. For instance, zirconia is generally more expensive than alumina due to its superior properties.
-
Quality Certifications: Suppliers that offer certified products, such as ISO 9001, may charge a premium for assurance of quality and reliability.
-
Supplier Factors: The supplier’s reputation, experience, and geographic location can all affect pricing. Suppliers in regions with higher labor costs may have higher prices.
-
Incoterms: Understanding the terms of shipping and delivery can help buyers negotiate better pricing. For instance, FOB (Free on Board) arrangements may result in lower costs compared to CIF (Cost, Insurance, and Freight).
What Are the Best Buyer Tips for Cost-Efficiency in Ceramic Machining?
-
Negotiate Effectively: Always engage in discussions about pricing, especially if ordering in bulk. Highlighting your potential for repeat business can encourage suppliers to offer better rates.
-
Consider Total Cost of Ownership (TCO): When evaluating suppliers, factor in not just the initial costs but also long-term costs associated with quality, delivery times, and potential rework.
-
Explore Multiple Suppliers: Don’t settle for the first quote. Comparing multiple suppliers can provide insights into market rates and help identify the most cost-effective solutions.
-
Understand Pricing Nuances: Be aware of regional pricing differences. For instance, suppliers in Europe may have different cost structures compared to those in Africa or South America due to labor and material availability.
-
Request Detailed Quotes: Ensure that suppliers provide a breakdown of costs. This transparency allows you to identify areas where you might negotiate better terms or find alternative solutions.
-
Leverage Technology: Utilize software tools for project management and supply chain management to enhance efficiency and reduce costs related to logistics and communication.
Disclaimer on Indicative Prices
It’s important to note that the prices for ceramic machining services can vary widely based on the factors discussed above. Therefore, the figures provided in this analysis are indicative and should be confirmed through direct consultation with suppliers for accurate and up-to-date pricing information.
Alternatives Analysis: Comparing ceramic machining With Other Solutions
Understanding Alternative Solutions to Ceramic Machining
When considering manufacturing processes, it’s essential for B2B buyers to evaluate alternatives to ceramic machining. This analysis helps identify solutions that may offer similar benefits while aligning with budget constraints, production requirements, and long-term goals. Below, we compare ceramic machining against two viable alternatives: CNC Machining of Metals and Plastic Injection Molding.
Comparison Table of Ceramic Machining and Alternatives
Comparison Aspect | Ceramic Machining | CNC Machining of Metals | Plastic Injection Molding |
---|---|---|---|
Performance | High precision, suitable for complex geometries; excellent wear resistance | High precision, good for complex shapes; material-dependent | High volume production; consistent quality |
Cost | Higher initial tooling costs; suitable for low to medium volume | Moderate to high, depending on material and tooling | Low per-unit cost at high volumes; initial setup can be high |
Ease of Implementation | Requires specialized equipment and skilled operators | Readily available technology; operator training necessary | Requires significant initial investment for molds |
Maintenance | High maintenance due to tooling wear; careful handling required | Moderate maintenance; tooling requires periodic replacement | Low maintenance once molds are established |
Best Use Case | High-performance applications in aerospace, electronics, and medical devices | Aerospace, automotive, and custom parts | High-volume consumer products, packaging, and components |
Detailed Breakdown of Alternatives
CNC Machining of Metals
CNC machining of metals is a widely adopted manufacturing process that utilizes computer-controlled machines to create parts from metal stock. This method excels in producing components with high precision and tolerances, making it suitable for industries like aerospace and automotive. The main advantage is its flexibility in material choice, allowing for the production of complex shapes. However, the cost of tooling can be significant, especially for high-grade materials, and the process may not achieve the same wear resistance as ceramic machining.
Plastic Injection Molding
Plastic injection molding is a manufacturing process that involves injecting molten plastic into a mold to create parts. This method is highly efficient for producing large quantities of identical components, making it ideal for consumer goods and packaging. The key advantages include low per-unit costs at high volumes and rapid production rates. However, the initial investment for mold design and manufacturing can be substantial. Moreover, this method is not suitable for high-temperature applications or where superior material properties are required, such as in aerospace or high-performance electrical components.
How to Choose the Right Solution for Your Needs
When selecting the appropriate machining solution, B2B buyers should consider several factors, including the specific requirements of their projects, budget constraints, and production volume. Ceramic machining is ideal for high-performance applications where durability and precision are paramount. In contrast, CNC machining of metals may be more suitable for general manufacturing needs that do not demand the specialized properties of ceramics. Finally, plastic injection molding offers an excellent option for high-volume production, particularly in consumer goods, but may not meet the stringent requirements of more demanding applications. By carefully evaluating these alternatives, buyers can make informed decisions that align with their operational goals and market demands.
Essential Technical Properties and Trade Terminology for ceramic machining
What Are the Key Technical Properties of Ceramic Machining?
When considering ceramic machining, understanding specific technical properties is crucial for B2B buyers. Here are some essential specifications that can significantly impact purchasing decisions and manufacturing processes:
1. Material Grade
Material grade refers to the classification of ceramic materials based on their composition and performance characteristics. Common grades include alumina, zirconia, and silicon carbide. The choice of material grade affects the mechanical strength, thermal stability, and wear resistance of the final product, making it essential for applications in industries such as aerospace and medical devices.
2. Tolerance Levels
Tolerance levels denote the allowable deviation from specified dimensions in ceramic components. In ceramic machining, tolerances can range from ±0.01 mm to ±0.05 mm, depending on the machining method and material type. Precise tolerances are vital for ensuring that components fit correctly in assemblies, especially in high-precision applications like electronics or turbine engines.
3. Surface Finish
Surface finish refers to the texture and smoothness of a machined ceramic part. It is often quantified using roughness measurements (e.g., Ra values). A finer surface finish can enhance the performance of components, especially in applications where friction or wear is a concern. Buyers should consider the required surface finish to ensure compatibility with their operational needs.
4. Hardness and Brittleness
Ceramic materials are characterized by their high hardness, which provides excellent wear resistance but also increases brittleness. This property can lead to challenges during machining, as brittle materials are prone to cracking or chipping. Understanding the hardness and brittleness of the ceramic being machined helps buyers select appropriate machining techniques and tools, thus minimizing waste and maximizing yield.
5. Thermal Conductivity
Thermal conductivity indicates how well a material can conduct heat. Ceramics typically have low thermal conductivity, which can complicate machining processes by causing excessive heat buildup. Buyers must consider thermal properties when selecting machining parameters and cooling techniques to enhance tool life and achieve desired finishes.
What Are Common Trade Terms in Ceramic Machining?
Navigating the ceramic machining landscape requires familiarity with specific industry terminology. Here are some common trade terms that B2B buyers should know:
1. OEM (Original Equipment Manufacturer)
OEM refers to a company that produces parts or equipment that may be marketed by another manufacturer. In ceramic machining, understanding OEM relationships is essential for ensuring that parts meet specific design and quality standards required by end-users.
2. MOQ (Minimum Order Quantity)
MOQ is the smallest quantity of a product that a supplier is willing to sell. For ceramic components, MOQs can vary significantly based on the material, machining complexity, and supplier capabilities. Buyers should be aware of MOQs to align their purchasing strategies with production needs and budget constraints.
3. RFQ (Request for Quotation)
An RFQ is a formal request to suppliers for price estimates on specific products or services. In the context of ceramic machining, issuing an RFQ helps buyers gather competitive pricing and terms, allowing for informed decision-making when selecting suppliers.
4. Incoterms (International Commercial Terms)
Incoterms are a set of standardized trade terms that define the responsibilities of buyers and sellers in international transactions. Understanding Incoterms is crucial for B2B buyers engaged in cross-border procurement of ceramic components, as they clarify shipping responsibilities, risk management, and cost allocation.
5. CMM (Coordinate Measuring Machine)
A CMM is a device used to measure the physical geometrical characteristics of an object. In ceramic machining, CMMs are essential for ensuring that parts meet specified tolerances and quality standards. Buyers should consider suppliers that utilize CMM technology to guarantee precision and quality in their components.
By familiarizing themselves with these technical properties and trade terminologies, international B2B buyers can make better-informed decisions, optimize their sourcing strategies, and enhance the efficiency of their manufacturing processes.
Navigating Market Dynamics and Sourcing Trends in the ceramic machining Sector
What Are the Key Trends and Market Dynamics in the Ceramic Machining Sector?
The ceramic machining sector is witnessing significant growth driven by the increasing demand for high-performance materials across various industries. Key markets include electronics, aerospace, automotive, and medical devices, where ceramic components are favored for their unique properties such as high hardness, thermal resistance, and electrical insulation. For international B2B buyers, particularly from Africa, South America, the Middle East, and Europe, understanding these dynamics is crucial for effective sourcing strategies.
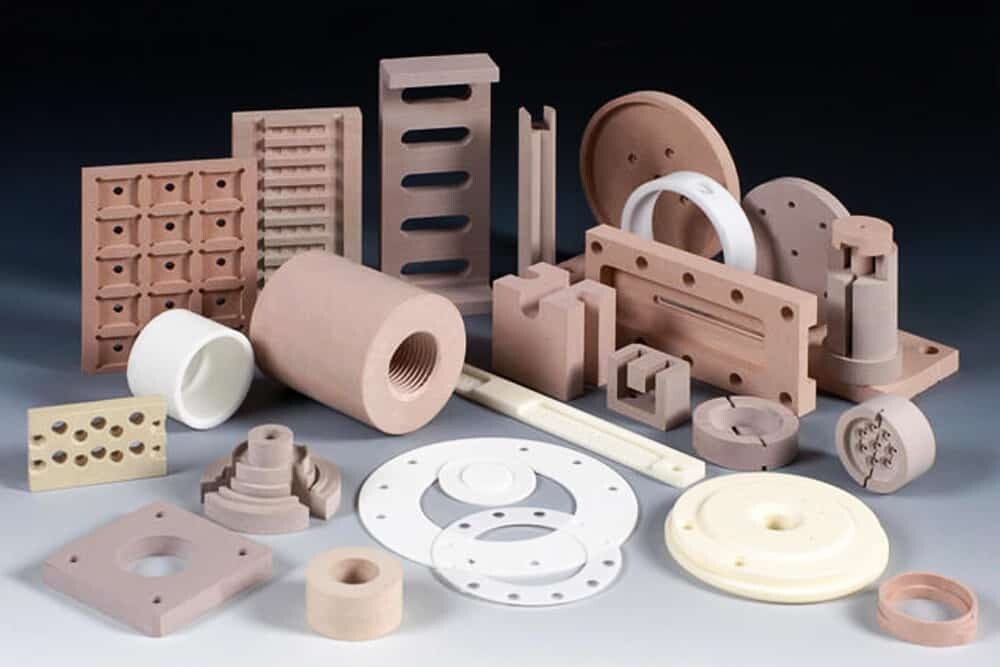
A stock image related to ceramic machining.
Emerging technologies are reshaping sourcing trends in this sector. The rise of advanced CNC machining techniques, such as laser machining and ultrasonic machining, allows for higher precision and efficiency, reducing production costs and waste. Additionally, the integration of Industry 4.0 technologies, such as IoT and AI in machining processes, enhances real-time monitoring and predictive maintenance, improving operational efficiency. Buyers should pay attention to suppliers who are adopting these innovations, as they can provide a competitive edge in production capabilities.
Market dynamics are also influenced by shifts in global supply chains. The increasing focus on localized sourcing due to geopolitical uncertainties and the pandemic has led many companies to reassess their supply chains. B2B buyers should consider suppliers that offer flexible and responsive supply chain solutions, ensuring timely delivery and quality assurance. Countries like Turkey are becoming prominent hubs for ceramic machining due to their strategic location and growing manufacturing capabilities, presenting new opportunities for international buyers.
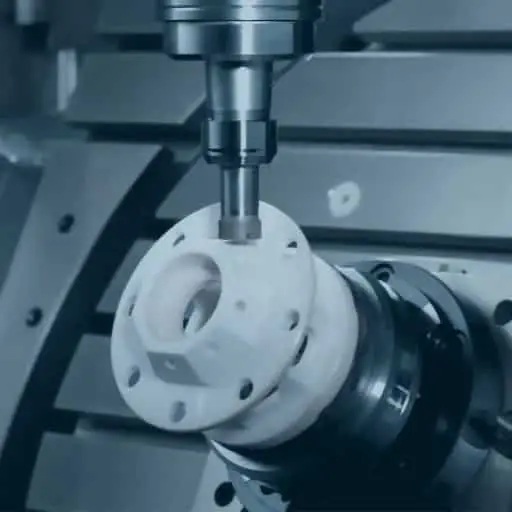
A stock image related to ceramic machining.
How Is Sustainability and Ethical Sourcing Impacting Ceramic Machining?
Sustainability is becoming a critical concern in the ceramic machining industry. The environmental impact of traditional machining processes, such as high energy consumption and waste generation, necessitates a shift toward greener practices. B2B buyers should prioritize suppliers that implement sustainable manufacturing processes, utilize energy-efficient machinery, and engage in waste reduction initiatives.
Ethical sourcing is equally important, particularly for international buyers who are increasingly conscious of the social and environmental implications of their supply chains. Ensuring that suppliers adhere to ethical labor practices and environmental regulations can enhance a company’s brand reputation and customer trust. Certifications such as ISO 14001 for environmental management and ISO 45001 for occupational health and safety are indicators of a supplier’s commitment to sustainability.
Moreover, the use of ‘green’ materials in ceramic machining is on the rise. Suppliers offering eco-friendly ceramic materials, such as recycled ceramics or biodegradable alternatives, can attract buyers looking to reduce their carbon footprint. By choosing partners with a strong commitment to sustainability and ethical sourcing, B2B buyers can contribute to a more responsible supply chain while meeting their operational needs.
What Is the Historical Context of Ceramic Machining for B2B Buyers?
Ceramic machining has evolved significantly over the past few decades. Initially, ceramics were primarily used in traditional applications due to their brittleness and difficulty in machining. However, advancements in technology have transformed ceramics into high-performance materials suitable for various industrial applications.
The introduction of precision machining techniques in the late 20th century allowed manufacturers to overcome challenges associated with ceramic brittleness and hardness. Innovations such as diamond grinding and advanced CNC machining have expanded the possibilities for ceramic applications, leading to increased use in critical sectors like aerospace and medical devices.
Today, the ceramic machining sector stands at the intersection of traditional craftsmanship and cutting-edge technology, presenting vast opportunities for international B2B buyers. Understanding this historical context helps buyers appreciate the advancements that have shaped the industry and informs their sourcing decisions in a rapidly changing market.
Frequently Asked Questions (FAQs) for B2B Buyers of ceramic machining
-
How do I solve challenges related to machining ceramics?
Machining ceramics presents challenges such as brittleness, high hardness, and low thermal conductivity. To mitigate these issues, it’s essential to use advanced cutting tools with diamond coatings and optimize cutting parameters, including speed and feed rate. Employing coolant or lubricants can help reduce heat buildup, while vibration damping techniques enhance stability during machining. Additionally, consider post-machining treatments like thermal stress relieving and surface polishing to improve dimensional accuracy and surface finish, ensuring the integrity of your components. -
What is the best ceramic material for high-temperature applications?
For high-temperature applications, zirconia ceramics are often the best choice due to their exceptional strength, toughness, and thermal stability. They maintain their mechanical properties at elevated temperatures, making them ideal for aerospace, automotive, and industrial applications. Alumina ceramics are also suitable for high-temperature uses, offering good wear resistance and thermal insulation. When selecting materials, consider the specific operating conditions and thermal requirements to ensure optimal performance. -
How can I ensure quality control when sourcing ceramic machining services?
To ensure quality control in ceramic machining, establish clear specifications for tolerances and surface finishes. Request detailed documentation, including material certifications and machining reports. Work with suppliers who utilize advanced quality assurance processes, such as CNC Coordinate Measuring Machines (CMM) for precise measurement and traceability. Regular communication and audits can further help maintain quality standards and address any issues promptly during production. -
What are the typical minimum order quantities (MOQs) for ceramic machining?
Minimum order quantities (MOQs) for ceramic machining can vary significantly depending on the supplier and the complexity of the components. Generally, MOQs may range from 50 to several hundred pieces, especially for custom parts. When negotiating with suppliers, discuss your specific needs and explore options for lower MOQs, particularly for prototype or small-batch orders. Establishing a strong relationship with your supplier may also help reduce MOQ requirements. -
What payment terms should I expect when sourcing ceramic machining services internationally?
Payment terms for international ceramic machining services can vary by supplier, but common practices include a deposit of 30-50% upfront, with the balance due upon completion or delivery. Other options may include Letter of Credit (LC) arrangements or payment upon receipt of goods. Always clarify payment terms before finalizing agreements to ensure both parties are aligned. Be aware of currency fluctuations and consider negotiating terms that mitigate foreign exchange risks. -
How can I vet suppliers for ceramic machining effectively?
Vetting suppliers for ceramic machining involves assessing their experience, capabilities, and reputation in the industry. Start by reviewing their portfolio and case studies to gauge their expertise in your specific application. Request references from previous clients to understand their reliability and customer service. Additionally, visiting the supplier’s facility or conducting virtual audits can provide insights into their production processes and quality control measures. -
What logistics considerations should I keep in mind when importing ceramic components?
When importing ceramic components, consider factors such as shipping methods, customs regulations, and lead times. Choose a reliable logistics partner familiar with handling fragile materials to minimize the risk of damage during transit. Be aware of import duties and taxes that may apply, and ensure all necessary documentation, such as certificates of origin and compliance, is in order. Planning for potential delays in customs clearance can also help streamline the import process. -
What customization options are available for ceramic machining?
Customization options for ceramic machining are extensive and can include variations in material composition, dimensions, and surface finishes. Many suppliers offer tailored machining processes to meet specific performance requirements, such as enhanced wear resistance or improved thermal properties. Discuss your project needs with potential suppliers to explore available customization options and ensure that the final product aligns with your operational goals and technical specifications.
Important Disclaimer & Terms of Use
⚠️ Important Disclaimer
The information provided in this guide, including content regarding manufacturers, technical specifications, and market analysis, is for informational and educational purposes only. It does not constitute professional procurement advice, financial advice, or legal advice.
While we have made every effort to ensure the accuracy and timeliness of the information, we are not responsible for any errors, omissions, or outdated information. Market conditions, company details, and technical standards are subject to change.
B2B buyers must conduct their own independent and thorough due diligence before making any purchasing decisions. This includes contacting suppliers directly, verifying certifications, requesting samples, and seeking professional consultation. The risk of relying on any information in this guide is borne solely by the reader.
Strategic Sourcing Conclusion and Outlook for ceramic machining
Why Is Strategic Sourcing Essential for B2B Buyers in Ceramic Machining?
In conclusion, the world of ceramic machining presents significant opportunities for international B2B buyers, especially those from Africa, South America, the Middle East, and Europe. Understanding the unique properties and challenges of ceramic materials is crucial in making informed purchasing decisions. Strategic sourcing enables buyers to leverage supplier capabilities, optimize costs, and enhance product quality.
By focusing on high-tolerance machining and advanced techniques, businesses can ensure they procure superior ceramic components tailored to their specific applications. As industries increasingly rely on ceramics for their durability and performance, investing in reliable suppliers and innovative machining technologies will be key to maintaining a competitive edge.
What Are the Next Steps for International B2B Buyers?
Looking ahead, buyers should prioritize building strong relationships with reputable ceramic machining suppliers. Engaging in collaborative projects can foster innovation and lead to tailored solutions that meet evolving market demands. Additionally, continuous education about advancements in ceramic machining technologies will empower buyers to make strategic decisions that drive operational efficiency.
Take action today—explore partnerships that align with your business objectives and harness the potential of ceramic machining to elevate your product offerings.