Master CNC Efficiency: The Complete M Codes List Guide (2025)
Introduction: Navigating the Global Market for cnc programming m codes list
Navigating the global market for CNC programming M codes can be a daunting task for international B2B buyers, especially those from regions like Africa, South America, the Middle East, and Europe. With the intricacies involved in sourcing the right CNC machinery and understanding the specific M codes that control various machine functions, many buyers face the challenge of ensuring compatibility and functionality for their unique production needs. This guide serves as a comprehensive resource, detailing the different types of M codes, their applications across various CNC machines, and best practices for supplier vetting and cost considerations.
International buyers will find actionable insights tailored to their specific markets, whether they are looking to optimize manufacturing processes in Egypt or expand operations in Brazil. By providing a clear understanding of M codes, including their significance in programming and machine operation, this guide empowers decision-makers to make informed purchasing choices. Additionally, we explore supplier relationships, emphasizing the importance of selecting manufacturers that not only meet technical specifications but also align with regional compliance and support standards.
This resource aims to demystify the complexities of CNC programming M codes, enabling buyers to effectively leverage technology for enhanced operational efficiency and productivity. Ultimately, our goal is to equip B2B buyers with the knowledge and tools needed to navigate the global CNC market confidently.
Understanding cnc programming m codes list Types and Variations
Type Name | Key Distinguishing Features | Primary B2B Applications | Brief Pros & Cons for Buyers |
---|---|---|---|
Basic M-Codes | Standard codes like M00 (Stop), M02 (End of Program) | General machining operations | Pros: Easy to understand; Cons: Limited functionality |
Manufacturer-Specific M-Codes | Unique codes tailored to specific CNC machines | Specialized applications | Pros: Enhanced capabilities; Cons: May require specific training |
Advanced M-Codes | Includes codes for automation and advanced features | High-volume production | Pros: Increased efficiency; Cons: Complexity in programming |
Safety and Maintenance M-Codes | Codes dedicated to safety features and maintenance actions | Industrial safety and maintenance | Pros: Improved safety; Cons: May require additional monitoring |
User-Defined M-Codes | Custom codes created for specific business needs | Tailored machining solutions | Pros: Flexibility; Cons: Requires programming knowledge |
What are Basic M-Codes and Their Applications?
Basic M-Codes form the foundation of CNC programming. They include essential commands such as M00 (Program Stop) and M02 (End of Program). These codes are universally recognized across various CNC machines and are vital for general machining operations. For B2B buyers, understanding these codes is essential for basic CNC operations, offering a straightforward approach to programming. However, while they are easy to learn, their limited functionality may restrict advanced operations.
How Do Manufacturer-Specific M-Codes Enhance Functionality?
Manufacturer-specific M-Codes are tailored to the capabilities of individual CNC machines, providing unique commands that enhance operational efficiency. These codes, such as those from Haas or Fanuc, allow for specialized applications like tool changes or coolant management. B2B buyers should consider the specific M-Codes of the machines they are investing in, as understanding these codes can significantly improve productivity. However, the need for specific training can be a barrier to some organizations.
What are Advanced M-Codes and Their Benefits for High-Volume Production?
Advanced M-Codes incorporate commands designed for automation and complex machining tasks, such as M60 (Automatic Pallet Change) or M67 (High Pressure Coolant On). These codes are particularly beneficial in high-volume production environments where efficiency and speed are paramount. For B2B buyers, investing in machines that utilize advanced M-Codes can lead to significant time savings and operational efficiency. However, the complexity of programming these codes can present a learning curve for operators.
Why are Safety and Maintenance M-Codes Critical in Industrial Settings?
Safety and maintenance M-Codes focus on ensuring the safe operation of CNC machines and facilitating regular maintenance tasks. Codes like M09 (Coolant Off) or M38 (Door Open) are crucial in preventing accidents and ensuring machine longevity. For B2B buyers, prioritizing machines that integrate these codes can enhance workplace safety and reduce downtime. However, implementing these features may require additional monitoring and training to ensure compliance.
How Can User-Defined M-Codes Provide Tailored Solutions?
User-defined M-Codes allow organizations to create custom commands that address specific operational needs. This flexibility enables B2B buyers to optimize their CNC programming for unique machining processes or workflows. While the ability to define these codes offers significant advantages, it also necessitates a higher level of programming knowledge and expertise. Therefore, businesses must weigh the benefits of customization against the potential need for specialized training.
Key Industrial Applications of cnc programming m codes list
Industry/Sector | Specific Application of CNC Programming M Codes List | Value/Benefit for the Business | Key Sourcing Considerations for this Application |
---|---|---|---|
Aerospace | Precision component manufacturing | High accuracy and consistency in complex parts | Ensure compatibility with aerospace standards and certifications. |
Automotive | Tooling and machining of engine components | Reduced production time and enhanced part quality | Look for suppliers with robust quality control measures. |
Medical Devices | Fabrication of surgical instruments | Compliance with strict regulatory requirements | Verify supplier’s adherence to ISO 13485 and similar standards. |
Electronics | PCB manufacturing and assembly | Improved efficiency and reduced waste | Assess the supplier’s technology and automation capabilities. |
Metal Fabrication | Custom metal part production | Flexibility in design and rapid prototyping | Evaluate the supplier’s machine capabilities and M-Code familiarity. |
How is CNC Programming M Codes List Used in Aerospace Manufacturing?
In the aerospace industry, CNC programming M codes are essential for the precision manufacturing of complex components such as turbine blades and landing gear parts. These M codes control various machine functions, ensuring that each component meets stringent safety and performance standards. International B2B buyers must ensure that the CNC machines they source are compatible with aerospace-specific M codes and can maintain the required tolerances and finishes.
What Role Do CNC M Codes Play in Automotive Tooling?
The automotive sector relies heavily on CNC programming M codes for tooling and machining engine components. These codes help automate processes like spindle control and tool changes, significantly reducing production time while enhancing the quality of parts produced. Buyers in South America and Africa should focus on sourcing machines that can handle high-volume production and have a proven track record of reliability in automotive applications.
How are M Codes Utilized in Medical Device Manufacturing?
In the medical device industry, CNC programming M codes are critical for fabricating surgical instruments and implants. The use of these codes ensures that products comply with strict regulatory requirements, such as those set by the FDA or ISO. Buyers from the Middle East and Europe should prioritize suppliers who can demonstrate compliance with industry standards and have the capability to produce high-precision components.
Why are M Codes Important in Electronics Manufacturing?
CNC programming M codes are vital in the electronics sector, particularly for the manufacturing and assembly of printed circuit boards (PCBs). These codes streamline processes, enhance efficiency, and minimize waste, leading to cost savings. B2B buyers should evaluate the technological capabilities of their suppliers, ensuring they can integrate advanced M code functionalities to optimize production lines.
How Do M Codes Enhance Flexibility in Metal Fabrication?
In metal fabrication, CNC programming M codes facilitate the production of custom metal parts through automated machining processes. This flexibility allows businesses to quickly adapt to changing design specifications and market demands. International buyers, especially from diverse regions like Europe and Africa, should consider the supplier’s familiarity with various M codes and their ability to handle complex fabrications efficiently.
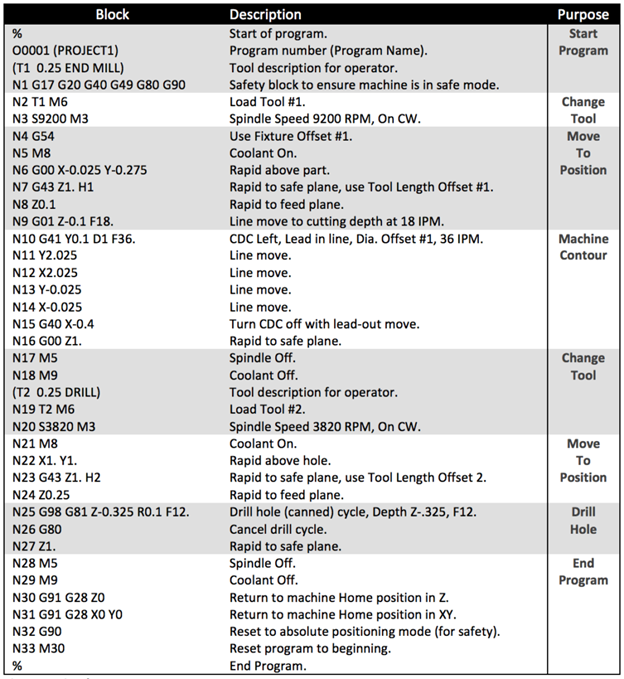
A stock image related to cnc programming m codes list.
3 Common User Pain Points for ‘cnc programming m codes list’ & Their Solutions
Scenario 1: Difficulty in Understanding Manufacturer-Specific M-Codes
The Problem: International B2B buyers often face the challenge of navigating the vast array of M-codes, which can differ significantly across manufacturers. For example, a buyer in Egypt may source CNC machines from different suppliers, each providing unique M-code functionalities. This inconsistency can lead to operational inefficiencies, such as incorrect programming and increased machine downtime, ultimately impacting productivity and profitability.
The Solution: To mitigate this challenge, buyers should invest time in creating a comprehensive M-code reference document that includes the specifications from each manufacturer they work with. This document should not only list the M-codes but also detail their functions and any specific machine requirements. Additionally, buyers should engage in training sessions with machine suppliers to ensure a clear understanding of the M-codes relevant to their specific equipment. This proactive approach will empower users to program CNC machines accurately, thus enhancing operational efficiency.
Scenario 2: Overcoming Lack of Standardized M-Code Documentation
The Problem: Many companies, particularly in emerging markets in South America and Africa, struggle with a lack of standardized documentation for M-codes. This inconsistency can lead to confusion among operators, resulting in incorrect setups and programming errors that could damage machinery or waste materials. For instance, a company might use a generic M-code list that does not align with their CNC machine’s requirements, leading to costly mistakes.
The Solution: Buyers should prioritize obtaining manufacturer-specific manuals that include detailed M-code listings and usage instructions. When purchasing CNC machines, insist on receiving complete documentation and seek out suppliers who provide comprehensive user manuals. Moreover, creating an internal knowledge base that consolidates all M-code information can further enhance understanding and accessibility for all operators. Regular training workshops can also be beneficial, allowing teams to stay updated on any changes or enhancements in M-code functionalities.
Scenario 3: Inefficient Problem-Solving Due to Lack of M-Code Knowledge
The Problem: CNC operators often encounter issues during production runs, such as machine errors or tool changes, but lack the knowledge of which M-code to employ to rectify the situation. For example, a buyer in Saudi Arabia may have operators who are unfamiliar with the M-codes for coolant control, leading to overheating and tool wear. This lack of knowledge can result in extended downtime and increased maintenance costs.
The Solution: To address this issue, businesses should invest in comprehensive training programs that focus on M-code applications and troubleshooting. Collaborating with CNC machine manufacturers for tailored training sessions can ensure that operators understand the critical M-codes relevant to their machines. Additionally, creating a quick-reference guide that operators can keep near their workstations can facilitate faster problem-solving during production. Encouraging a culture of continuous learning and knowledge sharing will empower teams to become more proficient in managing CNC machines, ultimately leading to smoother operations and reduced costs.
Strategic Material Selection Guide for cnc programming m codes list
What Are the Key Properties of Common Materials for CNC Programming M Codes?
When selecting materials for CNC programming, especially in the context of M codes, it is essential to consider their properties that directly affect machining performance. Here, we analyze four common materials: Aluminum, Steel, Titanium, and Plastic. Each material has unique characteristics that influence their suitability for various applications in CNC machining.
How Does Aluminum Perform in CNC Machining?
Aluminum is a lightweight material known for its excellent machinability and corrosion resistance. It has a temperature rating of around 660°C, making it suitable for high-speed machining operations. The primary advantage of aluminum is its low density, which allows for faster processing speeds and reduced wear on tools. However, its softness can lead to deformation under heavy loads, making it less suitable for high-stress applications.
For international B2B buyers, particularly in regions like Africa and South America, aluminum’s widespread availability and compliance with standards such as ASTM B211 make it a popular choice. However, buyers should consider the cost implications of sourcing high-grade aluminum, as prices can fluctuate based on global demand.
What Are the Advantages and Disadvantages of Using Steel in CNC Applications?
Steel is a robust material with high tensile strength and excellent durability, making it ideal for heavy-duty applications. It typically has a temperature rating of up to 1500°C, allowing it to withstand extreme conditions. The main advantage of steel is its versatility; it can be alloyed to enhance specific properties, such as corrosion resistance or hardness. However, steel’s density can lead to increased machining time and tool wear.
For buyers in the Middle East and Europe, compliance with DIN standards is crucial when selecting steel grades. The cost of steel can vary significantly based on the alloying elements used, so it’s essential for buyers to assess their specific requirements to avoid overspending.
Why Consider Titanium for High-Performance CNC Machining?
Titanium is renowned for its high strength-to-weight ratio and exceptional corrosion resistance, making it suitable for aerospace and medical applications. It can withstand temperatures exceeding 1600°C, which is advantageous for high-performance environments. The primary disadvantage of titanium is its high cost and the complexity of machining, which often requires specialized tools and techniques.
International buyers, especially from Europe and the Middle East, should be aware of compliance with ASTM and ISO standards for titanium products. The investment in titanium can be justified by its long-term performance benefits, particularly in demanding applications.
How Do Plastics Compare in CNC Machining?
Plastics, such as acrylic and polycarbonate, offer excellent machinability and are lightweight, making them suitable for a variety of applications, including prototypes and low-stress components. They typically have lower temperature ratings (around 100-150°C), which limits their use in high-temperature environments. The primary advantage of plastics is their cost-effectiveness and ease of machining, while the main disadvantage is their lower durability compared to metals.
For B2B buyers in Africa and South America, the availability of various plastic materials that comply with JIS standards can be a significant advantage. However, buyers should consider the environmental impact and recycling options when selecting plastics for their projects.
Summary Table of Material Selection for CNC Programming M Codes
Material | Typical Use Case for cnc programming m codes list | Key Advantage | Key Disadvantage/Limitation | Relative Cost (Low/Med/High) |
---|---|---|---|---|
Aluminum | Lightweight components, automotive parts | Excellent machinability and corrosion resistance | Softer than steel, can deform under load | Medium |
Steel | Structural components, heavy machinery | High strength and durability | Increased wear on tools, heavier | Medium to High |
Titanium | Aerospace parts, medical implants | High strength-to-weight ratio | High cost and complex machining | High |
Plastic | Prototypes, low-stress components | Cost-effective and easy to machine | Lower durability, limited temperature resistance | Low to Medium |
This table provides a concise overview of the materials discussed, allowing international B2B buyers to make informed decisions based on their specific needs and applications in CNC programming.
In-depth Look: Manufacturing Processes and Quality Assurance for cnc programming m codes list
What Are the Main Stages of Manufacturing Processes for CNC Programming M Codes?
The manufacturing process for CNC programming M codes is critical in ensuring that machines operate effectively and efficiently. Here are the key stages involved:
Material Preparation: How Do You Ensure Quality Raw Materials?
The first step in the manufacturing process is material preparation, which involves selecting and sourcing high-quality raw materials that meet industry standards. This may include metals, plastics, or composites, depending on the application. For B2B buyers, it is essential to verify that suppliers provide materials that comply with international standards such as ISO 9001 or ASTM specifications. This ensures that the materials have the necessary mechanical properties and chemical compositions.
Forming: What Techniques Are Used in CNC Machining?
Once the materials are prepared, the next stage is forming. CNC machining involves various techniques, including milling, turning, and drilling, which are controlled through G- and M-codes. Each technique is selected based on the desired shape and specifications of the final product. For B2B buyers, understanding the specific M codes used for tool changes, spindle operations, and coolant management is crucial, as these will directly affect the quality and precision of the finished part.
Assembly: How Is the Assembly Process Managed?
After forming, the components may require assembly, especially in complex systems where multiple parts come together to create a final product. This stage often involves precise alignment and fastening techniques. Buyers should inquire about the assembly methods employed by suppliers, including the use of jigs and fixtures, to ensure that the final product meets the specified tolerances and quality standards.
Finishing: What Finishing Processes Are Commonly Used?
The finishing stage is where products are polished, coated, or otherwise treated to enhance their appearance and durability. Techniques such as anodizing, painting, and surface grinding may be employed. B2B buyers should ensure that suppliers have robust finishing processes in place that comply with relevant quality standards and customer requirements, as this can significantly impact the product’s performance and lifespan.
How is Quality Assurance Implemented in CNC Manufacturing?
Quality assurance (QA) is a critical component of the manufacturing process, ensuring that products meet specified standards and customer expectations. Here are the key elements of QA in CNC manufacturing:
What International Standards Should B2B Buyers Look For?
B2B buyers should be aware of relevant international standards that govern quality assurance in manufacturing. ISO 9001 is a widely recognized standard that outlines the requirements for a quality management system (QMS). Compliance with this standard ensures that suppliers have established processes for continuous improvement and customer satisfaction. Additionally, industry-specific certifications, such as CE marking for products sold in Europe or API standards for oil and gas equipment, may also be relevant depending on the application.
What Are the Key Quality Control Checkpoints?
Quality control (QC) checkpoints are integral to the QA process and typically include Incoming Quality Control (IQC), In-Process Quality Control (IPQC), and Final Quality Control (FQC).
-
IQC: This involves inspecting raw materials upon arrival to ensure they meet specified standards. Buyers should ask suppliers about their IQC processes and the criteria used for material acceptance.
-
IPQC: This stage monitors the manufacturing process to detect any deviations in real-time. Techniques such as statistical process control (SPC) can be beneficial here. B2B buyers can request documentation of IPQC measures taken during production.
-
FQC: The final inspection ensures that the completed products meet all specifications before shipment. This may involve dimensional checks, visual inspections, and functional testing.
What Common Testing Methods Are Used?
Common testing methods include dimensional inspections using calipers and gauges, non-destructive testing (NDT) for structural integrity, and functional tests to verify operational performance. B2B buyers should understand these testing methods and ensure that their suppliers have the necessary equipment and protocols in place.
How Can B2B Buyers Verify Supplier Quality Control?
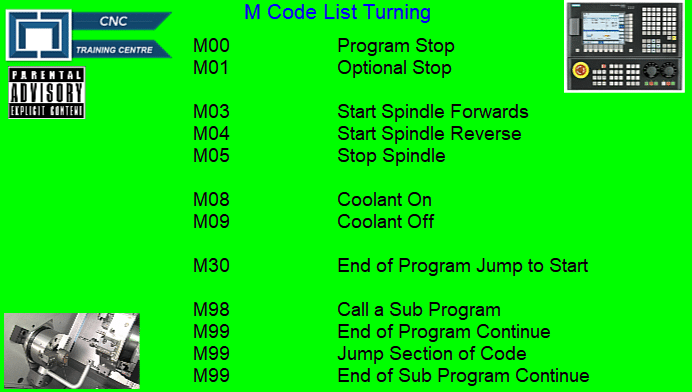
A stock image related to cnc programming m codes list.
Verifying a supplier’s quality control measures is essential for B2B buyers to ensure reliability and consistency in the products they purchase. Here are some actionable steps:
What Are the Best Practices for Conducting Supplier Audits?
Conducting supplier audits is an effective way to assess a supplier’s quality control processes. Buyers should consider establishing a regular audit schedule and develop a checklist that covers all critical areas, including material sourcing, manufacturing processes, and quality management systems. This can also involve reviewing documentation such as quality assurance plans, inspection reports, and certifications.
How Can Reports and Documentation Enhance Transparency?
Requesting detailed reports and documentation from suppliers can enhance transparency and provide insight into their quality assurance processes. Key documents to request include:
- Quality Management System Documentation: This outlines the supplier’s processes for maintaining quality standards.
- Inspection Reports: These documents provide evidence of inspections and tests conducted at various stages of production.
- Certificates of Compliance: These verify that the products meet specific industry standards.
Should B2B Buyers Consider Third-Party Inspections?
Engaging third-party inspection services can provide an additional layer of assurance regarding product quality. Third-party inspectors can conduct unbiased evaluations of the manufacturing processes and final products, ensuring that they comply with international standards. This is particularly important for B2B buyers from diverse regions, as it helps mitigate risks associated with varying quality standards.
What Are the Quality Control Nuances for International B2B Buyers?
International B2B buyers, particularly from Africa, South America, the Middle East, and Europe, should be aware of specific nuances in quality control that may affect their purchasing decisions.
How Do Regional Regulations Impact Quality Assurance?
Different regions may have varying regulatory requirements that affect product quality and compliance. For example, products exported to Europe must meet CE marking requirements, while those intended for the Middle East may need to comply with Gulf Standards (GSO). Buyers should familiarize themselves with the specific regulations applicable to their target markets and ensure their suppliers are compliant.
What Challenges Do B2B Buyers Face in Quality Assurance?
B2B buyers may face challenges such as language barriers, differing quality standards, and varying levels of supplier transparency. It is crucial for buyers to establish clear communication channels and expectations with suppliers to overcome these challenges. Additionally, leveraging technology such as digital quality management systems can facilitate better oversight and tracking of quality assurance processes across international suppliers.
Conclusion
Understanding the manufacturing processes and quality assurance protocols associated with CNC programming M codes is essential for B2B buyers. By focusing on material preparation, forming, assembly, and finishing, along with robust quality control measures, buyers can ensure that they source high-quality products that meet their specific needs. Implementing effective verification strategies, including supplier audits and third-party inspections, will further enhance confidence in the suppliers they choose to work with, ultimately leading to successful international partnerships.
Practical Sourcing Guide: A Step-by-Step Checklist for ‘cnc programming m codes list’
Introduction
Navigating the procurement of CNC programming M codes is essential for international B2B buyers seeking to optimize their manufacturing processes. This guide provides a structured checklist to assist you in sourcing the right M codes tailored to your specific CNC machinery and operational needs. The following steps will help you ensure that you select a supplier who can meet your technical requirements while also offering reliable support.
Step 1: Define Your Technical Specifications
Clearly outline the specific M codes you require based on your CNC machines and the operations you intend to perform. Understanding your technical needs will help you communicate effectively with potential suppliers and ensure they can provide the correct codes.
- Consider compatibility: Different CNC machines may use varying M code standards, so identify the brand and model of your equipment.
- List essential functions: Prioritize M codes that control critical functions such as spindle speed, coolant management, and tool changes.
Step 2: Research Potential Suppliers
Conduct thorough research on suppliers who specialize in CNC programming and M codes. This will help you identify credible partners who can provide the support you need.
- Check online reviews: Look for feedback from other B2B buyers in your region to gauge supplier reliability and service quality.
- Evaluate their portfolio: Review case studies or project examples that showcase their expertise in CNC programming.
Step 3: Evaluate Supplier Certifications
Before finalizing a supplier, verify their certifications and compliance with industry standards. This is crucial to ensure that they adhere to quality assurance processes.
- ISO certifications: Look for suppliers with ISO 9001 certification, which indicates a commitment to quality management systems.
- Technical certifications: Suppliers should also have relevant technical certifications specific to CNC operations.
Step 4: Request Sample M Codes
Once you have shortlisted suppliers, request sample M codes to assess their compatibility with your machinery. This step is vital to ensure that the codes work effectively in your production environment.
- Test compatibility: Implement the sample codes in a controlled setting to verify their functionality.
- Evaluate ease of integration: Ensure that the M codes can be easily integrated into your existing programming systems.
Step 5: Understand Support and Training Options
Consider the level of technical support and training that the supplier offers. This can be crucial for your team to effectively utilize the M codes in your operations.
- Training programs: Inquire about available training sessions for your staff to familiarize them with the new M codes.
- Ongoing support: Assess the supplier’s commitment to providing ongoing technical support, especially during the initial implementation phase.
Step 6: Negotiate Terms and Pricing
Engage in discussions to negotiate pricing and terms of service. A clear understanding of costs and conditions will help you make informed decisions.
- Compare quotes: Obtain detailed quotes from multiple suppliers to identify the best value for your investment.
- Review payment terms: Ensure that payment terms align with your financial processes and cash flow.
Step 7: Finalize Your Order
Once you have completed the above steps, finalize your order with the chosen supplier. Ensure that all specifications and agreements are documented to avoid any misunderstandings.
- Confirm delivery timelines: Establish clear timelines for delivery and implementation of the M codes.
- Document everything: Keep a record of all agreements, including pricing, support, and training commitments.
By following this checklist, B2B buyers from Africa, South America, the Middle East, and Europe can make informed decisions when sourcing CNC programming M codes, ultimately enhancing their manufacturing capabilities.
Comprehensive Cost and Pricing Analysis for cnc programming m codes list Sourcing
What Are the Key Cost Components in Sourcing CNC Programming M Codes?
When sourcing CNC programming M codes, understanding the cost structure is crucial for international B2B buyers. Key cost components typically include:
-
Materials: The raw materials used in the production of CNC machines and components can significantly affect costs. Quality materials not only enhance machine performance but also ensure longevity.
-
Labor: Skilled labor is essential for programming, setup, and maintenance. Countries with lower labor costs may offer competitive pricing; however, the quality of labor can vary greatly.
-
Manufacturing Overhead: This includes costs associated with factory operations, such as utilities, rent, and equipment depreciation. Manufacturers with efficient processes can reduce these costs, impacting the final pricing of M codes.
-
Tooling: The cost of tooling is another critical factor. This includes the tools required for producing the parts and can vary based on the complexity and specifications of the components being manufactured.
-
Quality Control (QC): Implementing robust QC processes ensures that the M codes meet industry standards. While this can add to the cost, it mitigates risks associated with defects and non-compliance.
-
Logistics: Transportation and shipping fees are significant, especially for international transactions. Incoterms can influence these costs, determining who is responsible for shipping, insurance, and tariffs.
-
Margin: Suppliers will mark up their costs to achieve a profit margin, which can vary widely based on their market positioning and competition.
How Do Price Influencers Impact CNC M Code Sourcing?
Several factors influence the pricing of CNC programming M codes:
-
Volume/MOQ: Bulk purchases often lead to lower unit costs. Understanding the minimum order quantities (MOQ) can aid in negotiating better pricing.
-
Specifications and Customization: Customized M codes can increase costs due to the additional engineering and programming required. Clearly defining your specifications can help avoid unexpected expenses.
-
Material Quality and Certifications: Higher quality materials and certifications (e.g., ISO standards) can increase costs but often lead to better performance and reliability.
-
Supplier Factors: The supplier’s reputation, experience, and market position can significantly affect pricing. Established suppliers may charge more due to their reliability and service levels.
-
Incoterms: Different Incoterms (e.g., FOB, CIF) will dictate shipping responsibilities and costs, impacting the total price you pay.
What Buyer Tips Can Enhance Cost-Efficiency in CNC M Code Sourcing?
International B2B buyers can adopt several strategies to optimize costs:
-
Negotiation: Engage in open discussions with suppliers regarding pricing, especially if ordering in bulk. Suppliers may offer discounts for larger orders or long-term contracts.
-
Total Cost of Ownership (TCO): Consider not just the upfront costs but also the long-term implications, such as maintenance, operational efficiency, and potential downtime. Investing in higher-quality M codes might save costs in the long run.
-
Research and Compare Suppliers: Evaluate multiple suppliers to understand the market range for M codes. Comparing prices, quality, and service can lead to better purchasing decisions.
-
Understand Regional Pricing Nuances: Pricing can vary by region. For instance, suppliers in Europe may have different pricing structures compared to those in Africa or South America due to labor costs, materials availability, and economic factors.
-
Leverage Technology: Utilize platforms that aggregate supplier information and pricing for easier comparisons. This can streamline the sourcing process and identify the best value options.
Disclaimer on Indicative Prices
While this analysis provides a comprehensive overview of cost structures and pricing influences, actual prices can vary widely based on specific circumstances, supplier negotiations, and market conditions. Always consult with potential suppliers for the most accurate and up-to-date pricing information.
Alternatives Analysis: Comparing cnc programming m codes list With Other Solutions
Introduction: What Are the Alternatives to CNC Programming M Codes?
CNC programming M codes serve as essential commands that control various machine functions, optimizing the machining process. However, as technology evolves, alternative solutions have emerged that can offer similar or enhanced capabilities. This analysis explores these alternatives, allowing international B2B buyers, particularly from regions like Africa, South America, the Middle East, and Europe, to make informed decisions regarding CNC programming options.
Comparison of CNC Programming M Codes List Against Alternative Solutions
Comparison Aspect | CNC Programming M Codes List | Alternative 1: G-Code Programming | Alternative 2: PLC-Based Control Systems |
---|---|---|---|
Performance | High precision and control | Excellent precision; widely adopted | High reliability; less precision in machining tasks |
Cost | Generally low cost | Low to moderate; depends on software | Can be high due to hardware and software integration |
Ease of Implementation | Requires specific knowledge | Moderate; requires understanding of codes | High; often user-friendly interfaces |
Maintenance | Requires regular updates | Regular updates; community support available | Moderate; depends on system complexity |
Best Use Case | Ideal for complex machining | Versatile for various applications | Best for automation and control processes |
Detailed Breakdown of Alternatives
1. G-Code Programming: Is it a Better Option for CNC Machining?
G-code programming is often considered the standard for CNC operations. It allows for high precision and is widely supported across various CNC machines. One of the main advantages of G-code is its versatility, as it can be used for a variety of machining tasks beyond just milling. However, it requires a solid understanding of programming principles, which can pose a challenge for less experienced operators. Additionally, while G-code provides excellent performance, it may necessitate more frequent updates to adapt to new machine capabilities.
2. PLC-Based Control Systems: Can They Replace CNC Programming?
Programmable Logic Controllers (PLCs) have emerged as a viable alternative, particularly for automation and control processes. These systems are known for their reliability and user-friendly interfaces, making them suitable for a broader range of applications. However, PLCs often lack the precision required for intricate machining tasks, limiting their effectiveness in high-precision environments. The costs associated with implementing PLC systems can also be higher due to the need for compatible hardware and software, making them less appealing for businesses focused solely on CNC machining.
Conclusion: How to Choose the Right Solution for Your CNC Needs
When selecting between CNC programming M codes and alternative solutions, B2B buyers should carefully assess their specific requirements. If precision and control in machining tasks are paramount, sticking with M codes or G-code programming may be the best choice. Conversely, if the focus is on automation and broader control applications, PLC-based systems could offer significant benefits. Ultimately, understanding the unique operational needs and available resources will guide buyers in making the most informed decision for their CNC programming requirements.
Essential Technical Properties and Trade Terminology for cnc programming m codes list
What Are the Key Technical Properties of CNC Programming M Codes?
When dealing with CNC programming M codes, understanding their technical specifications is crucial for international B2B buyers. Here are some critical properties to consider:
1. Compatibility with CNC Machines
M codes are often machine-specific, meaning that each manufacturer may implement different codes for similar functions. This compatibility issue can impact your procurement decisions significantly. For buyers in Africa, South America, the Middle East, and Europe, ensuring that the M codes of the CNC machines you are considering align with your operational requirements is essential to avoid costly errors or inefficiencies.
2. Functionality and Control Parameters
Each M code controls specific functions, such as spindle speed, coolant activation, and tool changes. Understanding these functionalities helps buyers select the right machines that meet their production needs. For example, M08 activates flood coolant, which is essential for maintaining optimal temperatures during machining processes. Buyers should prioritize machines that allow for flexible and efficient control of these parameters.
3. Ease of Integration
The ease with which M codes can be integrated into existing CNC systems is another critical property. Compatibility with other software and hardware can streamline operations and reduce downtime. Buyers should evaluate the programming environment and ensure that it supports seamless integration of M codes with their current systems, especially if they are looking to scale operations.
4. Documentation and Support
Comprehensive documentation is vital for understanding the specific M codes associated with each CNC machine. This includes manuals, cheat sheets, and customer support services. Buyers should seek machines that come with robust documentation, especially in multiple languages, to accommodate diverse teams across different regions.
5. Customization and User Macros
Many CNC machines allow for user-defined macros, enabling customization of M codes to suit specific manufacturing processes. This feature can enhance productivity and provide a competitive edge. Buyers should inquire about the extent to which they can customize M codes, particularly if they require specialized operations unique to their industry.
What Are Common Trade Terms Related to CNC Programming?
Navigating the world of CNC programming also involves familiarizing yourself with industry jargon. Here are some essential terms for B2B buyers:
1. OEM (Original Equipment Manufacturer)
An OEM is a company that manufactures products or components that are sold under another company’s brand name. Understanding this term is critical for B2B buyers who may need to source machines or parts from OEMs that meet specific quality and performance standards.
2. MOQ (Minimum Order Quantity)
MOQ refers to the minimum number of units a supplier is willing to sell. This term is particularly relevant for international buyers who may want to negotiate smaller orders initially to test product quality or market demand.
3. RFQ (Request for Quotation)
An RFQ is a formal document requesting a price quote from suppliers. It’s a vital tool for B2B buyers looking to compare pricing and terms across multiple suppliers, especially when sourcing complex machinery like CNC machines.
4. Incoterms (International Commercial Terms)
These are standardized terms that define the responsibilities of buyers and sellers in international trade. Understanding Incoterms is essential for B2B buyers to clarify shipping costs, risks, and delivery responsibilities, which can significantly impact the total cost of ownership.
5. Lead Time
Lead time refers to the duration between placing an order and receiving it. For CNC machinery, longer lead times can affect production schedules. Buyers should consider lead times when making purchasing decisions to ensure timely project execution.
By grasping these technical properties and trade terms, international B2B buyers can make informed decisions in the CNC programming landscape, enhancing operational efficiency and reducing costs.
Navigating Market Dynamics and Sourcing Trends in the cnc programming m codes list Sector
What Are the Current Market Dynamics Affecting CNC Programming M Codes?
The CNC programming sector, particularly concerning M codes, is experiencing significant transformation driven by technological advancements and globalization. The increased automation in manufacturing processes across Africa, South America, the Middle East, and Europe is a primary factor driving demand for precise CNC programming solutions. Countries like Egypt and Saudi Arabia are investing heavily in technology to enhance their manufacturing capabilities, leading to a growing need for skilled programmers who can effectively utilize M codes for machine control.
Emerging trends include the integration of IoT (Internet of Things) and Industry 4.0 principles, which facilitate real-time monitoring and optimization of CNC operations. As international buyers seek suppliers who can provide these advanced capabilities, the demand for comprehensive M code lists tailored to specific machines is rising. Additionally, there is a growing focus on software solutions that simplify programming and enhance machine communication, making it easier for operators to leverage M codes efficiently.
International B2B buyers should also note the shift towards customization in CNC programming. As companies strive to differentiate themselves in competitive markets, the ability to adapt M codes for specific applications will become increasingly important. This trend is particularly relevant in regions with diverse manufacturing needs, such as South America and Europe, where industries range from automotive to aerospace.
How Is Sustainability Influencing B2B Sourcing in CNC Programming?
Sustainability has become a critical consideration for B2B buyers in the CNC programming sector. The environmental impact of manufacturing processes is under scrutiny, prompting companies to seek out suppliers that prioritize eco-friendly practices. This includes sourcing materials and components that are certified as ‘green’ or sustainably produced, thereby reducing the overall carbon footprint of their operations.
Ethical sourcing is also gaining traction, with buyers increasingly interested in the supply chain transparency of their suppliers. Ensuring that suppliers adhere to ethical labor practices and environmental regulations is not only a matter of corporate responsibility but also a competitive advantage in the marketplace. Buyers in regions like the Middle East and Africa are particularly sensitive to these issues, as they seek to align their operations with global sustainability goals.
Moreover, the adoption of ‘green’ certifications can enhance a company’s reputation and appeal to environmentally conscious consumers. For instance, certifications related to energy efficiency or sustainable material use can be valuable assets in marketing campaigns, particularly in Europe, where consumer demand for sustainable products is robust. International B2B buyers should prioritize partnerships with suppliers who demonstrate a commitment to sustainability and ethical practices to align with market expectations and regulatory requirements.
What Is the Historical Context of CNC Programming M Codes?
The evolution of CNC programming and M codes can be traced back to the mid-20th century when numerical control (NC) technology emerged. Initially, NC machines operated using punched tape, which limited their flexibility and functionality. As computer technology advanced, so did the programming methods, leading to the development of G-code and M-code systems. M codes, designated for miscellaneous functions, allowed for more complex operations and control of CNC machines.
Over the years, manufacturers have standardized many M codes, but variations still exist based on machine make and model. This diversity poses challenges for international B2B buyers who must navigate different M code systems when sourcing equipment or programming services. Understanding the historical context of these codes is crucial for buyers looking to implement CNC technology effectively, as it informs their ability to adapt and customize programming to meet specific operational needs.
As CNC technology continues to advance, staying informed about the historical development and current trends in M codes will empower international buyers to make strategic sourcing decisions that enhance their manufacturing capabilities.
Frequently Asked Questions (FAQs) for B2B Buyers of cnc programming m codes list
-
How do I solve compatibility issues with different CNC machines regarding M-Codes?
Compatibility issues can arise because M-Codes vary significantly across different CNC machine manufacturers. To resolve this, start by thoroughly reviewing the user manual of your specific CNC machine, which will contain a detailed list of supported M-Codes. Additionally, consider consulting with the manufacturer or supplier for guidance on how to adapt your code for different machines. When sourcing M-Codes from suppliers, ensure they provide comprehensive documentation to facilitate seamless integration. -
What is the best approach for sourcing a comprehensive M-Code list for my CNC machines?
The most effective way to source a comprehensive M-Code list is to establish a relationship with reputable CNC machine manufacturers or distributors. Look for suppliers that offer detailed documentation, including M-Code lists tailored to specific machine models. Participating in industry trade shows or forums can also connect you with vendors who can provide valuable resources. Always verify that the M-Codes align with your machine’s specifications to ensure compatibility and efficiency. -
How can I ensure the quality of M-Code documentation when sourcing internationally?
To ensure quality M-Code documentation, prioritize suppliers with a strong reputation and positive customer feedback. Request samples of their documentation to assess clarity and completeness. It’s also beneficial to inquire about their quality assurance processes. For international sourcing, consider suppliers who provide localized support or multilingual documentation, which can help mitigate misunderstandings related to M-Codes and machine operations. -
What are the minimum order quantities (MOQ) for M-Code lists from suppliers?
Minimum order quantities for M-Code lists can vary widely depending on the supplier and the specific product. Some suppliers may provide M-Code lists as part of a machine purchase, while others may require a minimum order for documentation alone. When negotiating with suppliers, express your needs and ask about flexibility in MOQs. It’s advisable to consolidate orders with other necessary items to meet MOQ requirements while ensuring you have access to essential documentation. -
What payment terms should I consider when sourcing M-Code lists internationally?
When sourcing M-Code lists internationally, consider payment terms that provide security and flexibility. Common options include letters of credit, advance payments, or net payment terms after delivery. Assess the supplier’s reliability and consider using escrow services for larger transactions to mitigate risk. Always clarify currency exchange rates and transaction fees upfront to avoid unexpected costs. It’s prudent to establish clear terms in writing to protect both parties. -
How do I vet suppliers for M-Code lists effectively?
Effective supplier vetting involves several steps. Start by checking references and reading reviews from other businesses in your industry. Evaluate their experience with CNC machines and the specificity of their M-Code documentation. Request samples of their work and check for certifications that indicate adherence to industry standards. Additionally, consider visiting their facilities or arranging video calls to gauge their operational capabilities and commitment to quality. -
What logistical considerations should I keep in mind when sourcing M-Code lists internationally?
When sourcing M-Code lists internationally, consider shipping times, customs regulations, and potential tariffs that may affect delivery. Work with suppliers who have experience in international shipping to ensure compliance with local laws. Additionally, factor in the time needed for any necessary translations or adaptations of documentation. Establish a clear timeline and maintain open communication with your supplier to address any logistical challenges that may arise during the process. -
How can I customize M-Code lists to fit my specific CNC machines?
Customizing M-Code lists involves a thorough understanding of your CNC machines’ unique capabilities and requirements. Begin by analyzing the existing M-Codes you use and identify any gaps or necessary modifications. Collaborate with your supplier to create tailored documentation that aligns with your machine’s operational needs. It may also be beneficial to involve your CNC operators in the customization process to ensure the M-Codes effectively meet production requirements and enhance workflow efficiency.
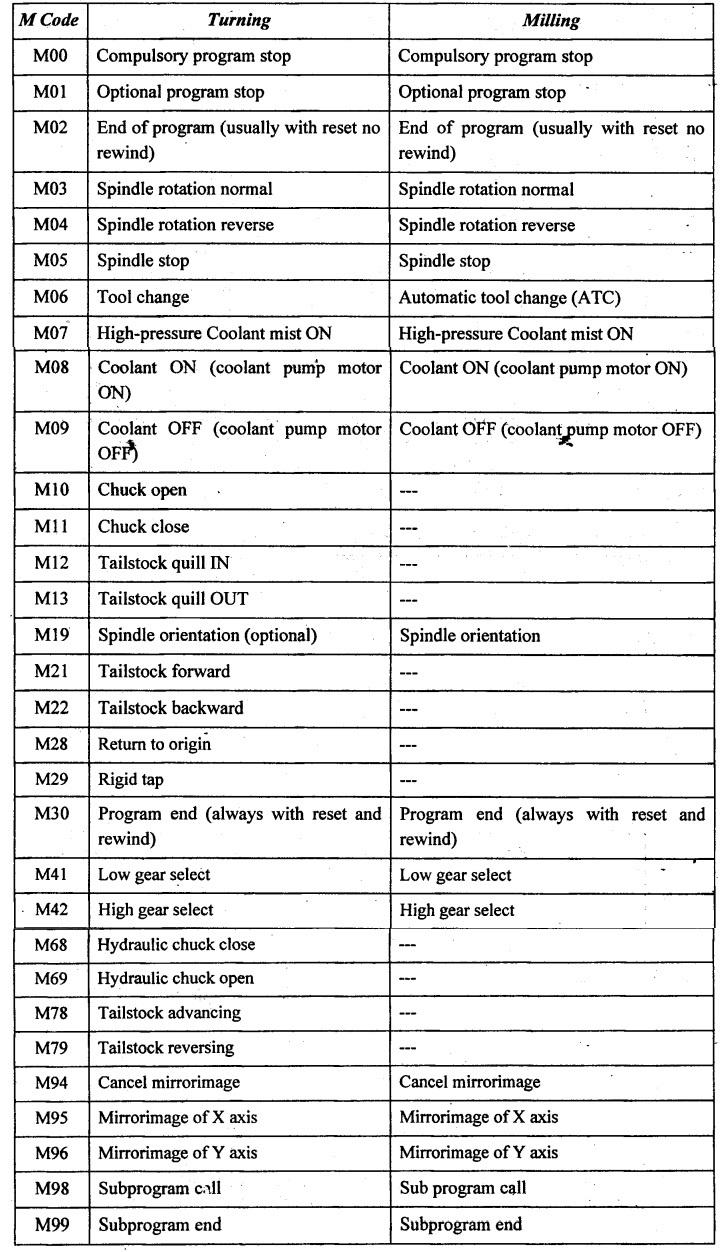
A stock image related to cnc programming m codes list.
Important Disclaimer & Terms of Use
⚠️ Important Disclaimer
The information provided in this guide, including content regarding manufacturers, technical specifications, and market analysis, is for informational and educational purposes only. It does not constitute professional procurement advice, financial advice, or legal advice.
While we have made every effort to ensure the accuracy and timeliness of the information, we are not responsible for any errors, omissions, or outdated information. Market conditions, company details, and technical standards are subject to change.
B2B buyers must conduct their own independent and thorough due diligence before making any purchasing decisions. This includes contacting suppliers directly, verifying certifications, requesting samples, and seeking professional consultation. The risk of relying on any information in this guide is borne solely by the reader.
Strategic Sourcing Conclusion and Outlook for cnc programming m codes list
In summary, the effective utilization of M-Codes in CNC programming is crucial for optimizing machining operations, enhancing productivity, and ensuring precision in manufacturing. For international B2B buyers, particularly those from Africa, South America, the Middle East, and Europe, understanding the diverse functionalities of M-Codes can significantly influence operational efficiency. By strategically sourcing CNC machines and components that align with specific M-Code requirements, businesses can reduce downtime and improve overall output quality.
What are the next steps for international B2B buyers looking to optimize their CNC programming? First, consider investing in training for your team on M-Code applications to leverage the full capabilities of your machinery. Additionally, establish partnerships with reputable suppliers who offer comprehensive support and resources tailored to your operational needs.
Looking ahead, as advancements in CNC technology continue to evolve, staying informed about emerging M-Code functionalities will be vital. By proactively adapting to these changes, businesses can maintain a competitive edge in the global market. Embrace this opportunity to enhance your CNC capabilities and drive your business forward.