Master CNC Machine Coolant Selection for Optimal Efficiency
Introduction: Navigating the Global Market for cnc machine coolant
In the competitive landscape of CNC machining, selecting the right coolant is a pivotal decision that can significantly influence operational efficiency and product quality. CNC machine coolant is not just a lubricant; it is a vital component that ensures optimal temperature control, enhances tool life, and improves surface finishes. As international B2B buyers, particularly those from Africa, South America, the Middle East, and Europe, understanding the nuances of CNC coolants can empower you to make informed sourcing decisions that will impact your bottom line.
This comprehensive guide delves into the various types of CNC coolants available—ranging from water-soluble to synthetic formulations—highlighting their unique applications and benefits. We will explore key considerations for selecting the appropriate coolant based on materials, manufacturing processes, and quality control standards. Additionally, the guide offers insights into suppliers, cost factors, and market trends, equipping you with the knowledge needed to navigate the complexities of the global coolant market.
By the end of this guide, you will possess actionable insights that enhance your sourcing strategy, minimize operational downtime, and ensure the longevity of your CNC machinery. Whether you are looking to optimize your machining processes or simply seeking answers to common FAQs, this resource is designed to support your journey towards making well-informed coolant procurement choices.
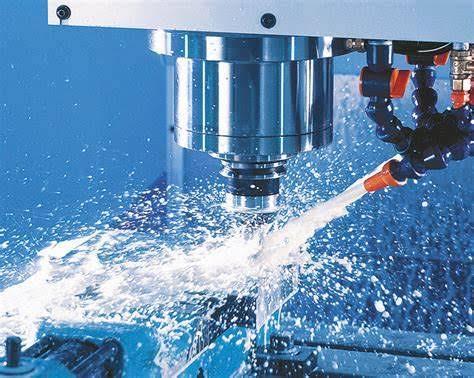
Illustrative Image (Source: Google Search)
Understanding cnc machine coolant Types and Variations
Type Name | Key Distinguishing Features | Primary B2B Applications | Brief Pros & Cons for Buyers |
---|---|---|---|
Water-Soluble Coolants | Mixture of water and additives, good cooling properties | Automotive, Aerospace, Metalworking | Pros: Effective cooling, easy to clean; Cons: Susceptible to bacterial growth, can cause rust. |
Semi-Synthetic Coolants | Blend of oil and water, balanced cooling and lubrication | Industrial Machinery, HVAC | Pros: Good lubrication, reduced foaming; Cons: Higher cost, requires careful concentration monitoring. |
Synthetic Coolants | Fully synthetic, high-performance, excellent lubricating properties | Aerospace, High-Precision Machining | Pros: Superior lubrication, less environmental impact; Cons: More expensive, requires specific handling. |
Oil-Based Coolants | Primarily oil-based, excellent for lubrication | Heavy Machining, Tool & Die Making | Pros: Long tool life, great for low-speed operations; Cons: Poor cooling, can be messy. |
Bio-Based Coolants | Made from renewable resources, environmentally friendly | General Manufacturing, Eco-Conscious Firms | Pros: Biodegradable, reduced health risks; Cons: May be less effective in extreme conditions, can be costlier. |
Water-Soluble Coolants
Water-soluble coolants are a popular choice in CNC machining due to their excellent cooling capabilities. Comprising a blend of water and various additives, they efficiently dissipate heat generated during machining processes. These coolants are particularly suitable for applications in the automotive and aerospace sectors, where precision and surface finish are critical. When purchasing, buyers should consider the potential for bacterial growth and the need for regular maintenance to prevent rust and other corrosion-related issues.
Semi-Synthetic Coolants
Semi-synthetic coolants combine both oil and water to provide a balanced approach to cooling and lubrication. This type of coolant is highly versatile, making it suitable for a variety of applications, including industrial machinery and HVAC systems. Buyers should note that while semi-synthetic coolants offer reduced foaming and good lubrication, they can be more expensive and require careful monitoring of concentration levels to maintain effectiveness.
Synthetic Coolants
Synthetic coolants are fully formulated with synthetic compounds, offering high performance in demanding machining environments. They excel in lubrication and provide excellent heat dissipation, making them ideal for aerospace and high-precision machining applications. However, buyers should be aware that synthetic coolants are often more costly and require specific handling procedures. Their lower environmental impact can be a significant selling point for eco-conscious companies.
Oil-Based Coolants
Oil-based coolants are primarily used in heavy machining and tool and die making. They are renowned for their superior lubrication properties, which significantly extend tool life, especially in low-speed operations. However, buyers should consider that while these coolants provide excellent lubrication, they are not effective at cooling and can create a mess in the machining area. Understanding the specific machining requirements is essential when opting for oil-based solutions.
Bio-Based Coolants
Bio-based coolants are made from renewable resources and are designed to be environmentally friendly. They are gaining traction in general manufacturing and among eco-conscious firms. While these coolants provide reduced health risks and biodegradability, they may be less effective under extreme machining conditions and can come at a higher cost. Buyers should weigh the benefits of sustainability against the performance needs of their specific applications.
Related Video: CNC Coolant Systems & Basics – Flood Coolant, Dry, MQL & More!
Key Industrial Applications of cnc machine coolant
Industry/Sector | Specific Application of CNC Machine Coolant | Value/Benefit for the Business | Key Sourcing Considerations for this Application |
---|---|---|---|
Automotive | Machining engine components and transmission housings | Reduces wear on tools, ensuring high precision and improved surface finish | Compatibility with high-performance materials and temperature resistance |
Aerospace | Machining complex parts from titanium and Inconel | Ensures accurate machining under stringent quality standards | Availability of specialized coolants for exotic materials |
Industrial Machinery | Production of gears, shafts, and hydraulic components | Facilitates tight tolerances and prevents thermal distortion | Consideration for coolant disposal and environmental regulations |
HVAC Systems | Creating intricate parts for heating and cooling applications | Maintains quality in complex cuts and high-precision contours | Need for non-corrosive formulations to protect sensitive components |
Metalworking | High-speed machining of various metal components | Enhances tool life and allows for continuous machining processes | Evaluation of coolant concentration and bacterial growth management |
Automotive Industry
In the automotive sector, CNC machine coolant is crucial for machining engine components and transmission housings. The coolant reduces tool wear, allowing for consistent surface finishes and enhanced dimensional stability. International buyers should prioritize coolants that are compatible with high-performance materials and can withstand elevated temperatures. Moreover, sourcing strategies should consider local regulations regarding coolant disposal, especially in regions like Africa and South America where environmental compliance is increasingly important.
Aerospace Industry
Aerospace applications often involve machining complex parts made from challenging materials such as titanium and Inconel. CNC coolants are essential in these scenarios to ensure precision and adherence to stringent quality standards. Buyers in this sector must focus on sourcing specialized coolants that cater to the unique properties of these materials. Additionally, understanding the coolant’s thermal stability and its impact on machining accuracy is vital, particularly in Europe, where aerospace regulations are stringent.
Industrial Machinery
In the industrial machinery sector, CNC coolants play a vital role in producing gears, shafts, and hydraulic components. The coolants facilitate high-precision machining and help prevent thermal distortion, which is crucial for achieving tight tolerances. B2B buyers should consider sourcing coolants that comply with industry standards and evaluate the environmental regulations surrounding coolant disposal. This is particularly relevant in the Middle East, where industrial growth is significant and compliance with local laws is essential.
HVAC Systems
The HVAC industry relies on CNC machining to create intricate parts for heating, ventilation, and air conditioning systems. The use of CNC machine coolant ensures high-quality finishes in complex cuts and maintains the integrity of high-precision contours. Buyers should prioritize non-corrosive coolant formulations to protect sensitive HVAC components. Sourcing strategies should also include evaluating the coolant’s performance in varying temperatures, which is critical for regions with diverse climatic conditions.
Metalworking
In the metalworking sector, CNC coolants are indispensable for high-speed machining of various metal components. They enhance tool life and support continuous machining processes, reducing downtime and operational costs. International buyers should assess the coolant’s concentration levels and its effectiveness in managing bacterial growth to maintain optimal performance. This is especially important in South America, where manufacturers are increasingly focused on efficiency and sustainability in their operations.
Related Video: CNC Machine Coolant and Water Quality | Clearing Up the Confusion!
Strategic Material Selection Guide for cnc machine coolant
When selecting CNC machine coolants, understanding the properties and implications of various materials is crucial for optimizing performance and ensuring compatibility with specific machining operations. Here, we analyze four common materials used in CNC machine coolants: water-soluble coolants, synthetic coolants, semi-synthetic coolants, and oil-based coolants. Each material has its own set of characteristics that can significantly impact machining efficiency, tool longevity, and overall operational costs.
Water-Soluble Coolants
Key Properties:
Water-soluble coolants are primarily composed of water mixed with additives that enhance lubrication and cooling properties. They typically have a temperature rating suitable for high-speed machining and are effective in dissipating heat due to their high thermal conductivity.
Pros & Cons:
These coolants are generally cost-effective and offer excellent cooling capabilities. However, they can be prone to bacterial growth if not maintained properly, which can lead to contamination issues. Additionally, water-soluble coolants may not provide sufficient lubrication for certain high-load applications.
Impact on Application:
Water-soluble coolants are compatible with a wide range of materials, including aluminum and steel. However, they may not be suitable for machining materials that are sensitive to moisture or require higher lubrication levels.
Considerations for International Buyers:
Buyers should ensure that the chosen water-soluble coolant complies with local regulations regarding environmental impact and safety. Standards such as ASTM and DIN are essential for ensuring quality and compatibility.
Synthetic Coolants
Key Properties:
Synthetic coolants are formulated entirely from chemical compounds without any petroleum or mineral oils. They offer high-temperature resistance and excellent cooling properties, making them suitable for demanding machining operations.
Pros & Cons:
The primary advantage of synthetic coolants is their superior cooling efficiency and reduced risk of bacterial growth. However, they tend to be more expensive than other coolant types and may require specific handling and storage conditions to maintain their effectiveness.
Impact on Application:
Synthetic coolants excel in applications involving difficult-to-machine materials, such as titanium and high-strength alloys. They provide excellent surface finishes and tool life but may not be compatible with all materials.
Considerations for International Buyers:
International buyers should verify compliance with local and international standards, particularly in regions with strict environmental regulations. Understanding the specific formulation and compatibility with existing systems is also crucial.
Semi-Synthetic Coolants
Key Properties:
Semi-synthetic coolants combine both oil and water, providing a balance between lubrication and cooling. They typically have a moderate temperature rating and offer good corrosion resistance.
Pros & Cons:
These coolants provide better lubrication than water-soluble coolants while still offering decent cooling properties. However, they can be more expensive than traditional water-soluble options and may require more frequent maintenance to prevent bacterial growth.
Impact on Application:
Semi-synthetic coolants are versatile and can be used across various machining operations, including milling and turning of ferrous and non-ferrous metals. Their compatibility with a wide range of materials makes them a popular choice.
Considerations for International Buyers:
Buyers should consider the specific machining environment and the materials being processed to ensure compatibility. Additionally, they should check for compliance with local standards to avoid regulatory issues.
Oil-Based Coolants
Key Properties:
Oil-based coolants are derived from petroleum and provide excellent lubrication properties. They are particularly effective in high-load applications and have a high flash point, making them suitable for various machining processes.
Pros & Cons:
The main advantage of oil-based coolants is their superior lubrication, which significantly reduces tool wear. However, they can be costly and may present environmental challenges due to their petroleum base.
Impact on Application:
Oil-based coolants are ideal for heavy machining operations and materials that require high lubrication. However, they may not be suitable for high-speed machining due to their lower cooling efficiency compared to water-based options.
Considerations for International Buyers:
Buyers must be aware of environmental regulations regarding the use of petroleum-based products, especially in regions with stringent laws. Compliance with international standards is also critical to ensure product quality.
Summary Table
Material | Typical Use Case for CNC Machine Coolant | Key Advantage | Key Disadvantage/Limitation | Relative Cost (Low/Med/High) |
---|---|---|---|---|
Water-Soluble Coolants | General machining of aluminum and steel | Cost-effective and excellent cooling | Prone to bacterial growth | Low |
Synthetic Coolants | Machining titanium and high-strength alloys | Superior cooling efficiency | Higher cost and specific handling required | High |
Semi-Synthetic Coolants | Versatile use across various metals | Good balance of lubrication and cooling | More expensive and requires maintenance | Medium |
Oil-Based Coolants | Heavy machining operations | Excellent lubrication and tool life | Environmental concerns and higher cost | High |
This strategic material selection guide provides international B2B buyers with actionable insights into the various types of CNC machine coolants, helping them make informed decisions that align with their operational needs and regulatory requirements.
In-depth Look: Manufacturing Processes and Quality Assurance for cnc machine coolant
Manufacturing CNC coolant involves a series of meticulous processes and stringent quality assurance measures to ensure the product meets the high standards required for effective machining operations. Understanding these stages can greatly aid B2B buyers in making informed decisions when sourcing CNC coolants from suppliers, especially in regions like Africa, South America, the Middle East, and Europe.
Manufacturing Processes for CNC Coolant
Material Preparation
The first step in the manufacturing process involves sourcing high-quality raw materials. The primary components of CNC coolant include water, lubricants (either mineral or synthetic oils), additives for corrosion resistance, and biocides to prevent microbial growth.
- Selection of Ingredients: Suppliers must ensure that all materials meet specific industry standards. For instance, the lubricants should provide adequate cooling and lubrication properties while being compatible with various metals.
- Testing of Raw Materials: Before production, each batch of raw materials should undergo rigorous testing to confirm they meet predefined specifications, including viscosity, pH levels, and thermal stability.
Forming
Once the raw materials are prepared, the formulation process begins. This involves mixing the various components to achieve the desired properties.
- Mixing Techniques: Common methods include high-shear mixing and vacuum blending, which ensure a homogenous mixture. The mixing process must be carefully controlled to achieve the right concentration of each component.
- Temperature Control: Maintaining optimal temperatures during mixing is crucial to prevent degradation of sensitive ingredients, especially synthetic compounds.
Assembly
After forming the coolant, the product may undergo additional processing steps depending on the formulation.
- Emulsification: For water-soluble and semi-synthetic coolants, emulsification techniques are employed to ensure that the oil and water components blend uniformly.
- Packaging: The coolant is then packaged in suitable containers that prevent contamination and degradation during storage and transport. Labels must clearly indicate the product type, concentration, and safety instructions.
Finishing
The final stage of manufacturing involves quality checks and any necessary adjustments.
- Quality Control Sampling: Samples from each batch are taken for further testing to ensure consistency in performance and compliance with specifications.
- Documentation: All manufacturing processes must be documented, including batch numbers and test results, to maintain traceability.
Quality Assurance Standards
To maintain high standards in CNC coolant production, manufacturers must adhere to international and industry-specific quality assurance protocols.
Relevant International Standards
- ISO 9001: This standard focuses on quality management systems and is applicable to any organization, including those manufacturing CNC coolants. Compliance ensures that products consistently meet customer and regulatory requirements.
- CE Marking: For products sold within the European Economic Area (EEA), CE marking signifies that the coolant complies with EU safety, health, and environmental protection standards.
- API Certification: For certain formulations, especially those intended for high-performance applications, certification from the American Petroleum Institute (API) may be required to ensure quality and performance.
Quality Control Checkpoints
Quality control is a continuous process throughout manufacturing and includes several checkpoints:
- Incoming Quality Control (IQC): Raw materials are inspected upon receipt to verify compliance with specifications.
- In-Process Quality Control (IPQC): During the manufacturing process, samples are periodically tested for quality parameters such as viscosity and pH to ensure consistency.
- Final Quality Control (FQC): After production, the final product undergoes comprehensive testing, including thermal stability, lubricity tests, and microbiological evaluations.
Common Testing Methods
To ensure that CNC coolants perform optimally, various testing methods are employed:
- Viscosity Testing: Measures the fluid’s resistance to flow, which is crucial for effective lubrication.
- pH Level Testing: Ensures the coolant is within the optimal range to prevent corrosion and bacterial growth.
- Thermal Conductivity Testing: Assesses the coolant’s ability to dissipate heat.
- Biological Testing: Checks for microbial contamination, which can affect coolant performance and safety.
Verifying Supplier Quality Control
For international B2B buyers, especially those in Africa, South America, the Middle East, and Europe, verifying a supplier’s quality control processes is essential.
- Supplier Audits: Conducting on-site audits can provide insights into the supplier’s manufacturing practices and adherence to quality standards.
- Quality Reports: Requesting detailed quality control reports can help buyers assess the consistency and reliability of the supplier’s products.
- Third-Party Inspections: Engaging third-party organizations to perform inspections can offer an unbiased view of the supplier’s quality assurance practices.
QC and Certification Nuances for International Buyers
When sourcing CNC coolants internationally, buyers must be aware of specific nuances regarding certifications and quality control:
- Regional Standards: Different regions may have varying standards for chemical formulations. For instance, Europe has stringent regulations on chemical safety (REACH), which buyers should consider.
- Documentation Requirements: Buyers should ensure that suppliers provide all necessary documentation, including safety data sheets (SDS) and certificates of conformity, to facilitate compliance with local regulations.
- Cultural Considerations: Understanding the local manufacturing culture can also influence quality. Building strong relationships with suppliers can lead to better communication and improved quality outcomes.
By being informed about the manufacturing processes and quality assurance practices for CNC coolant, B2B buyers can make strategic decisions that enhance their supply chain efficiency and product performance.
Related Video: How It’s Made Air Conditioner In Factories | Air Conditioner Manufacturing Process @Techmachine_
Comprehensive Cost and Pricing Analysis for cnc machine coolant Sourcing
To effectively navigate the sourcing of CNC machine coolant, it is essential for B2B buyers to grasp the underlying cost structure and pricing dynamics. This understanding not only facilitates better purchasing decisions but also enhances negotiation capabilities, particularly for international buyers from regions like Africa, South America, the Middle East, and Europe.
Cost Components of CNC Machine Coolant
-
Materials: The primary component in the cost of CNC coolants is the raw materials used in their formulation. These include water, oil, emulsifiers, and additives for properties such as corrosion resistance and lubrication. The quality and sourcing of these materials significantly influence the final price.
-
Labor: Labor costs encompass the workforce involved in the production process, from chemical formulation to packaging. Skilled labor may command higher wages, particularly in regions with stringent safety and quality standards.
-
Manufacturing Overhead: This includes costs associated with facility maintenance, utilities, and equipment depreciation. Efficient manufacturing processes can help minimize these overhead costs, which are ultimately passed on to the buyer.
-
Tooling: Tooling costs are incurred when specialized equipment is required to produce specific types of coolants. High-precision manufacturing might necessitate more sophisticated tooling, impacting the overall cost.
-
Quality Control (QC): Ensuring that coolants meet industry standards and regulations involves rigorous testing and quality assurance processes. Investing in QC can enhance product reliability, but it also adds to the cost structure.
-
Logistics: Transportation and storage costs play a crucial role, especially for international shipments. Factors such as distance, shipping methods, and customs duties can significantly influence the final price.
-
Margin: Suppliers typically add a profit margin to the total cost, which can vary based on competition, market demand, and supplier positioning.
Price Influencers
-
Volume/MOQ: Pricing often varies based on the volume purchased. Larger orders may qualify for discounts, while smaller orders might incur higher per-unit costs.
-
Specifications/Customization: Custom formulations tailored to specific machining processes or materials can lead to increased costs. Buyers should weigh the benefits of customization against potential price hikes.
-
Materials: The type of coolant (water-soluble, synthetic, semi-synthetic, or oil-based) can vary in price. Higher-quality materials typically command a premium but may offer better performance and longevity.
-
Quality/Certifications: Certifications (such as ISO standards) can add to the cost but may provide assurance of quality and performance, which is especially important in regulated industries.
-
Supplier Factors: The reputation and reliability of the supplier can influence pricing. Established suppliers may charge more due to their proven track record and customer service.
-
Incoterms: Understanding the Incoterms (International Commercial Terms) is crucial for international buyers as they define the responsibilities of buyers and sellers in shipping, which can affect total costs.
Buyer Tips
-
Negotiation: Engage in open discussions with suppliers about pricing. Highlighting long-term relationships or potential bulk purchases can lead to favorable terms.
-
Cost Efficiency: Evaluate the Total Cost of Ownership (TCO) rather than just the upfront cost. Consider factors like tool longevity, machine performance, and maintenance needs.
-
Pricing Nuances: Be aware of regional pricing differences. Economic conditions, currency fluctuations, and local demand can cause price variations between Africa, South America, the Middle East, and Europe.
-
Supplier Relationships: Building strong relationships with suppliers can provide leverage in negotiations and insights into market trends, leading to better pricing over time.
Disclaimer
Prices for CNC machine coolants can fluctuate based on market conditions, supplier availability, and geopolitical factors. Buyers are encouraged to conduct thorough market research and obtain multiple quotes to ensure competitive pricing.
Spotlight on Potential cnc machine coolant Manufacturers and Suppliers
This section looks at several manufacturers active in the ‘cnc machine coolant’ market. This is a representative sample for illustrative purposes; B2B buyers must conduct extensive due diligence before any transaction. Information is synthesized from public sources and general industry knowledge.
Essential Technical Properties and Trade Terminology for cnc machine coolant
CNC machine coolants are crucial for optimizing machining processes across various industries. Understanding the essential technical properties and trade terminology associated with CNC coolants is vital for international B2B buyers to make informed purchasing decisions.
Key Technical Properties of CNC Machine Coolants
-
Type of Coolant
CNC coolants are classified into several categories, including water-soluble, semi-synthetic, synthetic, and oil-based coolants. Each type has specific properties suited for different machining operations. For instance, water-soluble coolants are preferred for high-speed machining due to their superior heat dissipation, while oil-based coolants excel in low-speed, high-precision applications. -
pH Level
The pH level of a coolant typically ranges from 8.5 to 9.5. Maintaining this balance is crucial for preventing corrosion and promoting optimal performance. A coolant with a proper pH level helps reduce the risk of bacterial growth and ensures the longevity of both the coolant and the machinery. Buyers should consider pH stability when selecting coolants for their operations. -
Concentration
For water-soluble coolants, the concentration generally ranges from 4% to 10%. This specification is essential because it affects cooling efficiency, lubrication, and the coolant’s ability to inhibit rust and corrosion. Buyers must assess the recommended concentration for their specific applications to maximize effectiveness and cost efficiency. -
Viscosity
Viscosity measures a fluid’s resistance to flow and is crucial for ensuring proper coolant delivery. Low-viscosity coolants can easily flow through the system and reach the cutting zone, while high-viscosity fluids may hinder performance. Understanding the viscosity requirements for different machining operations can help buyers select the appropriate coolant for their machinery. -
Flash Point
The flash point indicates the temperature at which a coolant can vaporize to form an ignitable mixture in air. This property is particularly relevant for oil-based coolants, where a higher flash point signifies a lower risk of fire hazards. Buyers should prioritize coolants with higher flash points for operations involving high temperatures to ensure safety in the workplace. -
Biostability
Biostability refers to a coolant’s ability to resist microbial growth. Coolants prone to bacterial contamination can lead to system failures and increased maintenance costs. Selecting biostable coolants is essential for reducing downtime and enhancing operational efficiency.
Common Trade Terminology in CNC Coolants
-
OEM (Original Equipment Manufacturer)
This term refers to companies that produce parts or equipment that may be marketed by another manufacturer. In the context of CNC coolants, OEMs often specify the types of coolants compatible with their machines, making it essential for buyers to align their coolant choices with OEM recommendations. -
MOQ (Minimum Order Quantity)
MOQ is the smallest quantity of a product that a supplier is willing to sell. Understanding MOQ is crucial for B2B buyers, as it can impact inventory management and cash flow. Buyers should negotiate MOQs to align with their production needs and storage capabilities. -
RFQ (Request for Quotation)
An RFQ is a document issued by a buyer to solicit price quotes from suppliers for specific products or services. In the CNC coolant market, issuing an RFQ helps buyers gather competitive pricing and understand market conditions, facilitating better purchasing decisions. -
Incoterms
Incoterms (International Commercial Terms) are standardized trade terms that define the responsibilities of buyers and sellers in international transactions. Familiarity with these terms helps B2B buyers navigate shipping, insurance, and delivery responsibilities, reducing potential misunderstandings in cross-border purchases.
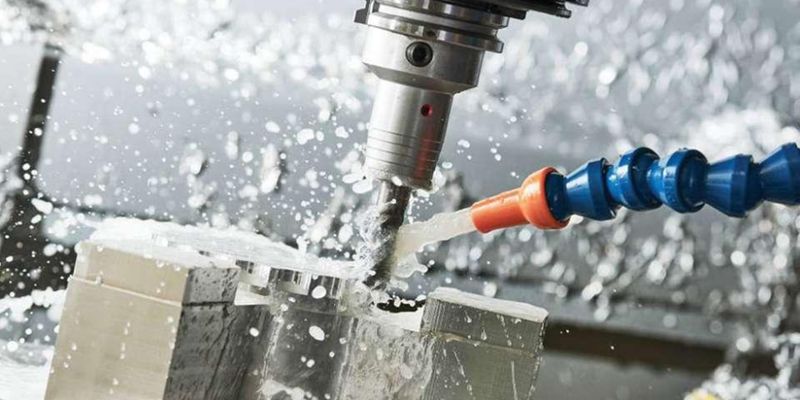
Illustrative Image (Source: Google Search)
-
TDS (Technical Data Sheet)
A TDS provides detailed information about a product’s specifications, including its properties, applications, and handling instructions. For CNC coolants, reviewing the TDS is crucial for understanding compatibility with specific machining operations and ensuring optimal performance. -
Shelf Life
Shelf life refers to the duration a product remains effective and usable under specified storage conditions. Knowing the shelf life of CNC coolants is vital for buyers to manage inventory effectively and avoid using expired products that could compromise machining performance.
Understanding these properties and terms will empower B2B buyers to make informed decisions, ensuring they select the right CNC coolants for their specific applications and operational requirements.
Navigating Market Dynamics, Sourcing Trends, and Sustainability in the cnc machine coolant Sector
Market Overview & Key Trends
The CNC machine coolant market is experiencing significant transformation driven by technological advancements and evolving buyer preferences. The global demand for high-performance machining solutions is propelling the adoption of advanced coolant formulations, such as synthetic and semi-synthetic coolants, which offer superior cooling and lubrication properties. International B2B buyers from regions like Africa, South America, the Middle East, and Europe are increasingly recognizing the value of these products in enhancing tool life and machining efficiency.
Emerging trends include the integration of IoT technology in coolant management systems, allowing for real-time monitoring of coolant conditions, usage, and performance. This data-driven approach helps manufacturers optimize their operations, reduce waste, and lower costs. Additionally, the push towards high-speed machining is leading to a greater emphasis on coolants that can withstand extreme conditions without compromising performance.
Market dynamics are influenced by the growing need for sustainable and environmentally friendly solutions. Buyers are now more inclined to source coolants that not only meet their operational needs but also align with their corporate social responsibility goals. As competition intensifies, suppliers must focus on innovation and responsiveness to regional market demands to maintain their competitive edge.
Sustainability & Ethical Sourcing in B2B
Sustainability is becoming a crucial consideration in the CNC machine coolant sector, as environmental regulations tighten globally. Buyers are increasingly aware of the environmental impact of their sourcing decisions, leading to a demand for eco-friendly coolant solutions. These solutions often include biodegradable and non-toxic formulations that minimize harm to ecosystems and human health.
Ethical sourcing is equally important, with B2B buyers seeking suppliers who adhere to sustainable practices throughout their supply chains. This includes responsible sourcing of raw materials, waste reduction strategies, and transparency in production processes. Certifications such as ISO 14001 (Environmental Management) and Green Seal can help buyers identify suppliers committed to sustainable practices.
Furthermore, buyers are encouraged to evaluate the life cycle of coolants, considering their production, use, and disposal phases. The adoption of circular economy principles—where materials are reused and recycled—can significantly reduce the overall environmental footprint associated with CNC machining operations.
Brief Evolution/History
The evolution of CNC machine coolants has been marked by advancements in chemical formulations and a deeper understanding of machining processes. Initially, traditional oil-based coolants dominated the market; however, as machining techniques evolved, the need for more effective cooling and lubrication solutions became apparent.
The introduction of water-soluble and synthetic coolants in the 20th century revolutionized the industry, providing improved heat dissipation and reduced tool wear. Today, the focus has shifted towards developing high-performance, eco-friendly coolants that meet the demands of modern machining while ensuring compliance with environmental standards. This ongoing evolution highlights the importance of innovation in maintaining competitive advantages in the global CNC machining market.
Related Video: Coolant 101 Series Intro – CNC Machining Tutorials
Frequently Asked Questions (FAQs) for B2B Buyers of cnc machine coolant
-
What criteria should I consider when vetting suppliers for CNC machine coolant?
When vetting suppliers, prioritize their industry experience, product quality, and compliance with international standards. Verify certifications such as ISO 9001 or specific coolant certifications relevant to your region. Request samples to assess product performance, and inquire about their sourcing practices for raw materials. Additionally, evaluate their customer service responsiveness and ability to provide technical support, which can be crucial for troubleshooting and optimizing your operations. -
Can CNC machine coolant be customized to meet specific machining requirements?
Yes, many suppliers offer customization options for CNC machine coolants. You can request formulations tailored to your specific machining processes, such as varying viscosity, lubrication properties, and thermal performance. Discuss your requirements with potential suppliers to understand their capabilities and willingness to develop a solution that aligns with your operational needs. Custom formulations can significantly enhance machining efficiency and tool longevity. -
What are the typical minimum order quantities (MOQ) and lead times for CNC machine coolant?
Minimum order quantities can vary significantly based on the supplier and your specific requirements. Generally, MOQs range from 200 liters to several thousand liters. Lead times typically range from 2 to 6 weeks, depending on the supplier’s production capacity and your location. It’s advisable to negotiate these terms upfront and consider your own inventory management needs to avoid operational disruptions. -
What payment terms are common when sourcing CNC machine coolant internationally?
Payment terms can vary widely among suppliers. Common arrangements include upfront payments, letters of credit, or payment upon delivery. For international transactions, ensure you clarify currency exchange rates and potential transaction fees. Building a solid relationship with your supplier may also lead to more favorable terms, such as extended payment periods or discounts for bulk orders. -
How can I ensure the quality of CNC machine coolant I am sourcing?
To ensure quality, request documentation that includes test results and certifications for the coolant. Reputable suppliers should provide material safety data sheets (MSDS) and reports on performance metrics such as viscosity, pH levels, and thermal stability. Additionally, consider conducting your own testing upon receipt to verify that the coolant meets your operational standards before full-scale usage. -
What logistics considerations should I keep in mind when importing CNC machine coolant?
Logistics for importing CNC machine coolant involve understanding shipping regulations, customs duties, and transportation modes. Ensure that your supplier can provide necessary documentation for customs clearance. Additionally, consider the storage requirements for the coolant upon arrival, as some formulations may have specific handling needs to maintain their efficacy. Collaborate with a logistics partner experienced in chemical imports to streamline the process. -
What steps should I take if I encounter a dispute with my coolant supplier?
In the event of a dispute, start by reviewing the contract and any relevant correspondence with the supplier. Document all communications and issues encountered. Attempt to resolve the matter directly through discussion. If resolution is not achieved, consider mediation or arbitration as outlined in your contract. Additionally, maintaining a professional relationship can often lead to more amicable solutions, so approach the situation with a focus on collaboration. -
Are there specific certifications I should look for when sourcing CNC machine coolant?
Yes, look for certifications relevant to your industry and region, such as ISO 9001 for quality management systems, and specific certifications like NSF or REACH compliance for environmental safety. These certifications indicate that the supplier adheres to established quality standards and regulatory requirements. Additionally, inquire about any industry-specific certifications that may be pertinent to your machining applications, ensuring the coolant is suitable for your operational context.
Important Disclaimer & Terms of Use
⚠️ Important Disclaimer
The information provided in this guide, including content regarding manufacturers, technical specifications, and market analysis, is for informational and educational purposes only. It does not constitute professional procurement advice, financial advice, or legal advice.
While we have made every effort to ensure the accuracy and timeliness of the information, we are not responsible for any errors, omissions, or outdated information. Market conditions, company details, and technical standards are subject to change.
B2B buyers must conduct their own independent and thorough due diligence before making any purchasing decisions. This includes contacting suppliers directly, verifying certifications, requesting samples, and seeking professional consultation. The risk of relying on any information in this guide is borne solely by the reader.
Strategic Sourcing Conclusion and Outlook for cnc machine coolant
In summary, the strategic sourcing of CNC machine coolant is essential for optimizing machining operations across various industries. Buyers must prioritize the selection of appropriate coolant types—water-soluble, semi-synthetic, or synthetic—tailored to specific machining requirements to enhance tool life, improve surface finish, and maintain operational efficiency. Effective coolant management can significantly reduce costs associated with tool replacements and machine downtime, making it a critical component of any manufacturing strategy.
As international B2B buyers from Africa, South America, the Middle East, and Europe evaluate their coolant sourcing options, it is crucial to consider suppliers that not only offer high-quality products but also provide comprehensive support in maintenance and application. Establishing strong partnerships with reliable manufacturers can lead to improved performance and sustainability in machining processes.
Looking ahead, the CNC machining landscape is poised for innovation, driven by advancements in materials and technologies. Buyers should stay informed about emerging trends in coolant formulations and application techniques to remain competitive. Engage with industry experts, attend trade shows, and explore new suppliers to ensure your machining operations are equipped for future challenges.