Master Cutting Die Cut: The Complete Guide for Buyers (2025)
Introduction: Navigating the Global Market for cutting die cut
In today’s fast-paced global market, sourcing cutting dies is a critical challenge for B2B buyers across diverse industries. As businesses seek to enhance their production capabilities, understanding the intricacies of die cutting becomes essential. This comprehensive guide on cutting die cut serves as a vital resource for international B2B buyers, particularly those from Africa, South America, the Middle East, and Europe, including regions like Australia and Vietnam. With a focus on various types of cutting dies, their applications, and the nuances of supplier vetting, this guide aims to empower buyers to make informed decisions.
Navigating the complexities of sourcing cutting dies can be daunting, with factors such as cost, quality, and supplier reliability significantly impacting production efficiency. This guide not only delves into the technical specifications and applications of different die types but also offers actionable insights on evaluating suppliers, understanding pricing structures, and optimizing procurement strategies. By equipping buyers with the knowledge needed to assess their options critically, this guide ensures that they can confidently select the right cutting die solutions tailored to their specific operational needs.
As you explore the sections ahead, you will gain a clearer understanding of how to effectively navigate the global market for cutting dies, enabling your business to achieve greater efficiency and innovation in your production processes.
Understanding cutting die cut Types and Variations
Type Name | Key Distinguishing Features | Primary B2B Applications | Brief Pros & Cons for Buyers |
---|---|---|---|
Steel Rule Dies | Flexible, made from steel rules; can cut various materials | Packaging, labels, custom shapes | Pros: Versatile for multiple materials; Cons: Less durable than rotary dies. |
Rotary Dies | Circular blades that allow continuous cutting | High-volume production for packaging | Pros: High speed and efficiency; Cons: Limited to specific shapes and sizes. |
Flatbed Dies | Rigid dies used with flatbed die cutting machines | Custom designs for signage, graphics | Pros: High precision for intricate designs; Cons: Slower production speed. |
Laser Cutting Dies | Uses laser technology for precision cutting | Prototyping, intricate patterns, textiles | Pros: Extremely precise; Cons: Higher initial investment cost. |
Craft Dies | Designed for smaller-scale operations, often manual | Scrapbooking, card-making | Pros: Affordable and easy to use; Cons: Limited to smaller projects. |
What Are Steel Rule Dies and Their B2B Applications?
Steel rule dies are characterized by their flexibility and ability to cut through a variety of materials, making them a popular choice in the packaging and labeling industries. They are particularly suitable for custom shapes, which is beneficial for businesses looking to differentiate their products. When considering a purchase, B2B buyers should evaluate the specific materials they plan to cut, as the versatility of steel rule dies can significantly impact production efficiency.
How Do Rotary Dies Enhance High-Volume Production?
Rotary dies utilize circular blades that rotate to cut materials continuously, making them ideal for high-volume production environments, such as packaging. They offer significant speed advantages, allowing businesses to meet tight deadlines without compromising quality. However, B2B buyers must be aware that rotary dies are limited to specific shapes and sizes, which may affect their overall utility in diverse applications.
What Advantages Do Flatbed Dies Offer for Custom Designs?
Flatbed dies are rigid and designed for use with flatbed die-cutting machines, providing high precision for intricate designs. These dies are particularly effective for signage and graphic applications where detail is paramount. While they deliver excellent results, B2B buyers should consider the slower production speeds associated with flatbed dies, especially if they require rapid turnaround times.
Why Choose Laser Cutting Dies for Precision Projects?
Laser cutting dies leverage advanced technology to achieve extreme precision, making them suitable for prototyping and intricate patterns, especially in textiles. The accuracy offered by laser cutting can significantly enhance product quality, appealing to businesses that prioritize detail. However, the initial investment for laser cutting technology can be higher, which is a critical consideration for budget-conscious B2B buyers.
How Do Craft Dies Cater to Smaller-Scale Operations?
Craft dies are primarily designed for smaller-scale operations and often used manually, making them an excellent choice for scrapbooking and card-making. They are affordable and user-friendly, which can be advantageous for small businesses or startups. However, the limitation to smaller projects means that B2B buyers must assess whether craft dies align with their production needs, especially if they anticipate scaling up operations in the future.
Key Industrial Applications of cutting die cut
Industry/Sector | Specific Application of Cutting Die Cut | Value/Benefit for the Business | Key Sourcing Considerations for this Application |
---|---|---|---|
Packaging | Custom packaging solutions for e-commerce | Enhances product presentation and protection, reducing returns | Material durability, customization options, lead times |
Automotive | Die-cut components for interior and exterior parts | Improves manufacturing efficiency and reduces waste | Precision requirements, material compatibility, cost-effectiveness |
Textile and Apparel | Die-cutting fabric patterns for garments | Streamlines production and ensures consistency in design | Fabric types, cutting precision, supplier reliability |
Electronics | Die-cutting insulation and protective layers | Increases safety and product longevity | Compliance with safety standards, material specifications |
Printing and Labeling | Die-cut labels and promotional materials | Enhances branding and marketing effectiveness | Design complexity, turnaround time, cost per unit |
How is Cutting Die Cut Used in Packaging Solutions for E-commerce?
In the packaging industry, cutting die cuts are essential for creating custom packaging solutions tailored to specific products. Businesses utilize die-cut designs to craft boxes, inserts, and protective materials that fit their products perfectly, enhancing both presentation and safety during shipping. This method addresses common challenges such as product damage and returns due to inadequate packaging. International buyers should focus on sourcing materials that are durable yet lightweight, ensuring that their packaging solutions meet local regulations while also considering customization options to enhance brand identity.
What Role Does Cutting Die Cut Play in the Automotive Industry?
The automotive sector employs cutting die cuts for manufacturing various components, including interior trim and exterior panels. By using die-cut processes, manufacturers can produce parts with high precision, significantly reducing material waste and production costs. This application is particularly beneficial for international buyers looking to streamline their supply chains while maintaining quality. Buyers must consider the precision requirements and material compatibility to ensure that the die-cut components meet the stringent safety and performance standards of the automotive industry.
How is Die Cutting Applied in Textile and Apparel Manufacturing?
In the textile and apparel industry, die-cutting is utilized to produce fabric patterns efficiently. This technique allows manufacturers to create multiple layers of fabric in a single pass, ensuring uniformity and reducing production time. It solves the problem of inconsistent cuts that can lead to wasted materials and increased labor costs. For international buyers, it’s essential to evaluate the types of fabrics being used, as well as the precision required for intricate designs, to partner with reliable suppliers who can deliver quality cuts consistently.
How Does Die Cutting Enhance Electronics Manufacturing?
Die-cutting in electronics is crucial for producing insulation and protective layers for devices. This application ensures that components are safely housed, preventing damage from heat and environmental factors. By implementing die-cut solutions, manufacturers can enhance the longevity and reliability of their products. Buyers in this sector should prioritize sourcing suppliers who comply with safety standards and can provide materials that meet specific technical specifications, ensuring that the final products are both safe and effective.
What Benefits Does Die Cutting Provide in Printing and Labeling?
In the printing and labeling industry, die-cutting is used to create bespoke labels and promotional materials that stand out. This method enhances branding efforts by allowing for unique shapes and designs that can capture consumer attention. It also addresses common issues such as production delays and inconsistent quality. Buyers should consider the complexity of their designs and the required turnaround times when sourcing die-cut services, as these factors can significantly impact marketing campaigns and overall business success.
3 Common User Pain Points for ‘cutting die cut’ & Their Solutions
Scenario 1: Navigating Material Compatibility Issues in Die Cutting
The Problem:
B2B buyers often face challenges in selecting the right materials for die cutting. Many die cutting machines are designed to work with specific types of materials, and using incompatible materials can lead to poor cuts, jams, or even damage to the machine. For instance, a buyer in South America might purchase a high-quality die cutting machine but struggle to find suitable materials locally. This not only affects production efficiency but can also result in wasted resources and increased costs.
The Solution:
To effectively navigate material compatibility issues, buyers should conduct thorough research on the specifications of their die cutting machines. Manufacturers typically provide guidelines on compatible materials, which can include various types of paper, cardboard, thin craft foam, and even certain fabrics. Buyers should leverage this information to develop a list of preferred suppliers who can provide these materials. Furthermore, engaging with local distributors and manufacturers can facilitate access to bulk purchasing options, reducing costs. Consider establishing partnerships with suppliers who can offer material testing services to ensure optimal compatibility before committing to larger orders. This proactive approach minimizes the risk of production delays and enhances overall workflow efficiency.
Scenario 2: Overcoming Complexity in Die Design and Customization
The Problem:
Another common pain point is the complexity involved in designing custom die cuts. Buyers often require specific shapes or designs tailored to their branding needs, but the process can be daunting, especially for those without in-depth design experience. A buyer from the Middle East may struggle to communicate their vision to manufacturers, leading to misaligned expectations and disappointing results.
The Solution:
To overcome the challenges of die design and customization, buyers should invest in software tools that facilitate the design process. Many die cutting machine manufacturers offer design software that allows users to create and visualize their custom designs before production. Additionally, collaborating with experienced designers or consultants who specialize in die cutting can provide valuable insights and guidance. When communicating with manufacturers, buyers should provide detailed specifications, including dimensions, materials, and desired outcomes. It may also be beneficial to request prototypes or samples before committing to full production runs. This iterative approach allows for adjustments based on feedback, ensuring that the final product aligns with the buyer’s vision.
Scenario 3: Managing Production Efficiency and Downtime
The Problem:
Production efficiency is a critical concern for B2B buyers in the die cutting industry. Unexpected machine downtime due to maintenance issues or technical malfunctions can disrupt workflows, leading to delays in order fulfillment. For instance, a buyer in Europe may experience a sudden breakdown of their die cutting machine during peak production hours, resulting in significant financial losses and damaged client relationships.
The Solution:
To manage production efficiency and minimize downtime, buyers should implement a proactive maintenance schedule for their die cutting machines. This includes regular inspections, cleaning, and timely replacements of worn-out parts. Buyers should also ensure that they are trained on the proper operation of their machines, as improper usage can lead to malfunctions. Developing a relationship with a reliable service provider for machine repairs can provide quick solutions when issues arise. Additionally, buyers should consider investing in backup machinery or alternative production methods to maintain operations during unexpected downtimes. This strategy not only safeguards against potential production halts but also enhances overall business resilience in a competitive market.
Strategic Material Selection Guide for cutting die cut
What Are the Key Materials for Cutting Die Cuts?
When selecting materials for cutting die cuts, it’s essential to understand the properties, advantages, and limitations of each option. This knowledge empowers international B2B buyers to make informed decisions that align with their specific needs and compliance requirements.
What Are the Properties of Steel in Die Cutting?
Key Properties: Steel is renowned for its strength and durability, making it a popular choice for die cutting. It can withstand high temperatures and pressures, ensuring precision cuts. Additionally, steel exhibits excellent corrosion resistance when properly treated.
Pros & Cons: The primary advantage of steel is its longevity and ability to produce clean, precise cuts, which is crucial for high-volume production. However, steel dies can be more expensive compared to alternatives, and the manufacturing process can be complex, requiring specialized equipment and skilled labor.
Impact on Application: Steel is suitable for a wide range of materials, including paper, cardboard, and some plastics. Its robustness makes it ideal for industries such as packaging and textiles.
Considerations for International Buyers: Buyers should ensure compliance with international standards such as ASTM A36 for structural steel. Additionally, understanding local sourcing capabilities and potential tariffs in regions like Africa and South America is vital for cost management.
How Does Aluminum Perform in Die Cutting Applications?
Key Properties: Aluminum is lightweight yet strong, with good thermal and electrical conductivity. It has a lower melting point than steel, which can be advantageous in certain applications.
Pros & Cons: The main advantage of aluminum dies is their cost-effectiveness and ease of machining. They are less durable than steel but can be suitable for short-run production. The downside is that aluminum may not withstand as much wear and tear, leading to a shorter lifespan.
Impact on Application: Aluminum is often used for softer materials, such as thin plastics and paper. It is less effective for tougher materials, where steel would be more appropriate.
Considerations for International Buyers: Compliance with aluminum standards such as ASTM B221 is crucial. Buyers in Europe and the Middle East should also consider the environmental regulations surrounding aluminum production and recycling.
What Are the Benefits of Composite Materials in Die Cutting?
Key Properties: Composite materials, often made from a combination of plastics and metals, offer a unique blend of properties. They can be engineered to provide specific performance characteristics, such as enhanced durability or flexibility.
Pros & Cons: The advantage of composites is their ability to be tailored for specific applications, providing versatility. However, they may not be as strong as steel or aluminum, and their manufacturing process can be more complex and costly.
Impact on Application: Composites are ideal for specialized applications where traditional materials may fall short. They can be used for intricate designs and are often favored in industries like automotive and aerospace.
Considerations for International Buyers: Buyers should be aware of the specific standards for composites, such as ASTM D3039 for tensile properties. Additionally, understanding the supply chain for composite materials in regions like Africa and South America is essential for timely production.
What Role Does Plastic Play in Die Cutting?
Key Properties: Plastic dies are lightweight and can be manufactured in various shapes and sizes. They are resistant to corrosion and can be produced quickly and cost-effectively.
Pros & Cons: The primary advantage of plastic is its affordability and ease of use. However, plastic dies may not be suitable for high-volume production or for cutting tougher materials, as they wear out more quickly than metal dies.
Impact on Application: Plastic is best for low-volume runs and softer materials, making it suitable for craft and hobby applications. It is less effective in industrial settings where precision and durability are critical.
Considerations for International Buyers: Compliance with plastic standards such as ASTM D638 is important. Buyers should also consider the environmental impact of plastic materials and the regulations surrounding their use in various regions.
Summary Table of Material Selection for Cutting Die Cuts
Material | Typical Use Case for Cutting Die Cut | Key Advantage | Key Disadvantage/Limitation | Relative Cost (Low/Med/High) |
---|---|---|---|---|
Steel | High-volume production, packaging | Long-lasting, precise cuts | Higher cost, complex manufacturing | High |
Aluminum | Short-run production, softer materials | Cost-effective, easy to machine | Less durable, shorter lifespan | Medium |
Composite | Specialized applications, intricate designs | Tailored properties, versatile | Higher cost, complex manufacturing | High |
Plastic | Crafting, low-volume runs | Affordable, lightweight | Wears out quickly, less durable | Low |
This guide provides a comprehensive understanding of the materials available for cutting die cuts, enabling international B2B buyers to choose the right option based on their specific needs and compliance requirements.
In-depth Look: Manufacturing Processes and Quality Assurance for cutting die cut
What Are the Main Stages in the Manufacturing Process of Cutting Die Cuts?
The manufacturing process for cutting die cuts involves several critical stages: material preparation, forming, assembly, and finishing. Understanding these stages is vital for B2B buyers, especially those from diverse regions like Africa, South America, the Middle East, and Europe.
Material Preparation: What Are the Key Considerations?
In the initial stage, raw materials such as metal sheets (often steel or aluminum) are selected based on the intended application of the die cuts. The choice of material directly influences the durability and precision of the cutting die. Buyers should consider factors like material thickness and hardness, which can affect performance. For instance, high-carbon steel is often preferred for its longevity, while aluminum may be used for prototypes due to its lighter weight and ease of machining.
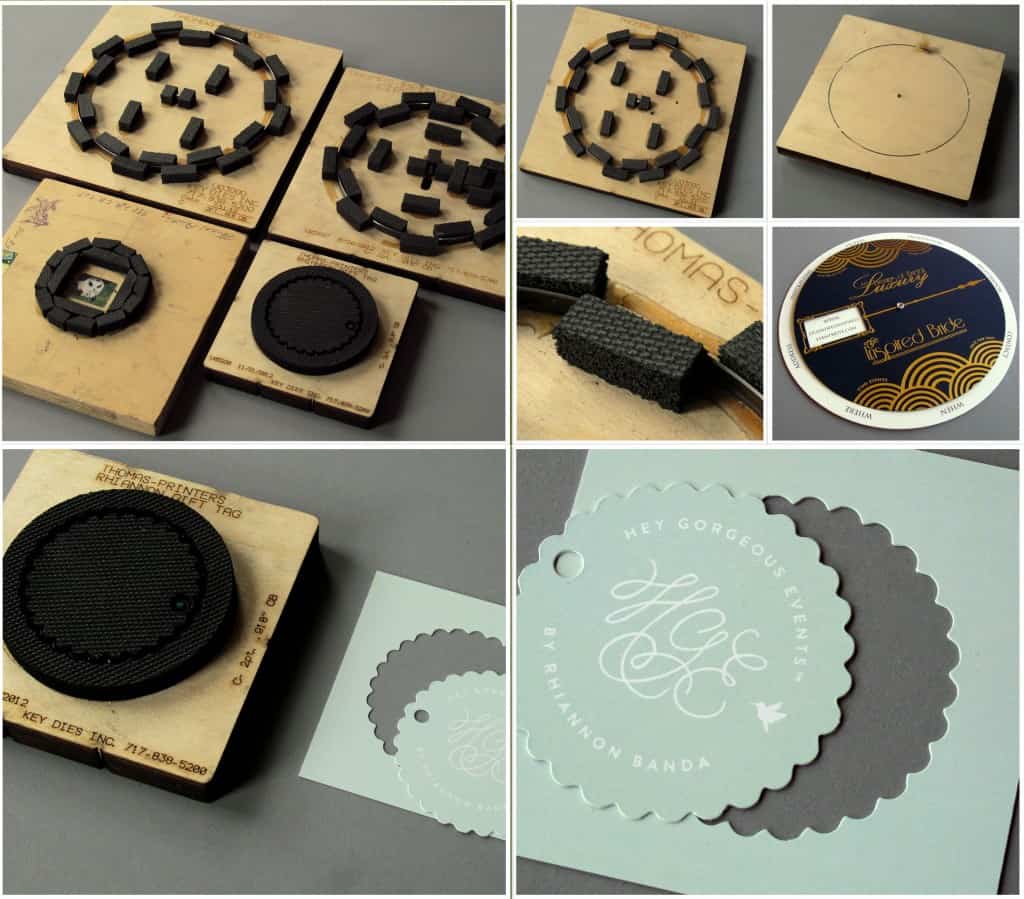
A stock image related to cutting die cut.
Once the materials are chosen, they undergo cutting and shaping to match the required dimensions. This can involve CNC (Computer Numerical Control) machining, which ensures high precision and repeatability. B2B buyers should inquire about the machinery used in this process, as advanced CNC systems can significantly enhance product quality.
Forming: How Is the Cutting Die Shaped?
The forming process involves the actual creation of the die shape. This is typically achieved through a combination of techniques, including laser cutting and die stamping. Laser cutting provides high precision and is suitable for intricate designs, while die stamping is more efficient for bulk production of simpler shapes.
Buyers should be aware of the capabilities of their suppliers in this stage. Inquire about the types of machinery employed and the maximum complexity of shapes they can produce. This information is crucial for aligning supplier capabilities with project requirements.
Assembly: What Does the Assembly Process Involve?
The assembly stage involves putting together various components of the die, including the cutting edges and any additional features such as embossing or perforating elements. This process may also include welding or fastening parts together, depending on the design specifications.
Quality assurance during assembly is paramount. B2B buyers should ask suppliers about their assembly protocols and whether they perform any real-time checks during this stage. This can prevent defects from progressing to the final product.
Finishing: How Is the Die Cut Prepared for Use?
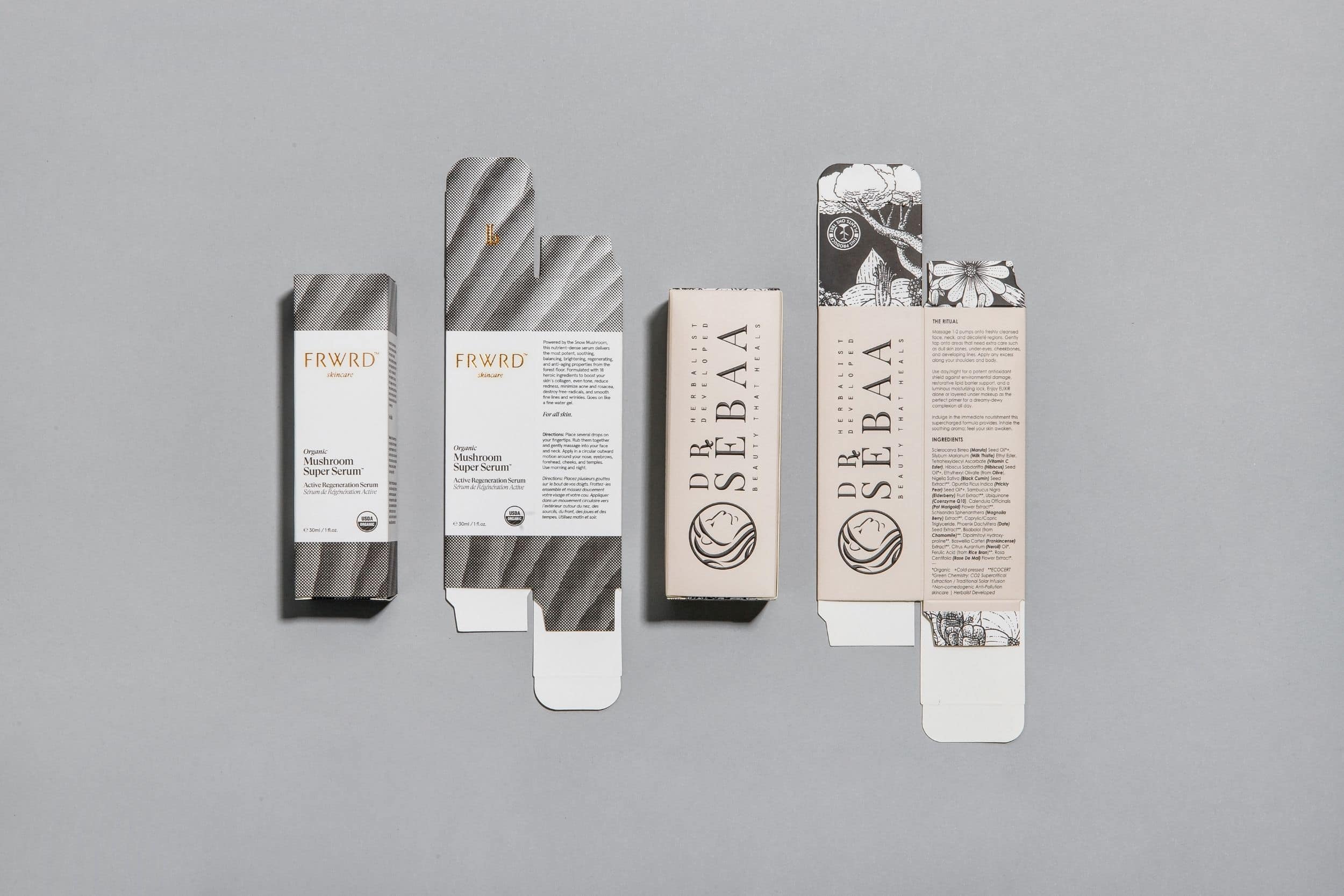
A stock image related to cutting die cut.
The finishing stage typically involves surface treatments to enhance durability and performance. Common techniques include coating, polishing, and heat treatment. Coatings can protect against rust and wear, while polishing can improve the cutting surface, ensuring a clean cut.
It is advisable for buyers to confirm what finishing processes are utilized by their suppliers and to specify any particular requirements they may have. This attention to detail can lead to better performance in the final product.
What Are the Key Quality Assurance Practices in Die Cut Manufacturing?
Quality assurance (QA) is an essential component of the die cut manufacturing process. It ensures that the products meet international and industry-specific standards, providing peace of mind for B2B buyers.
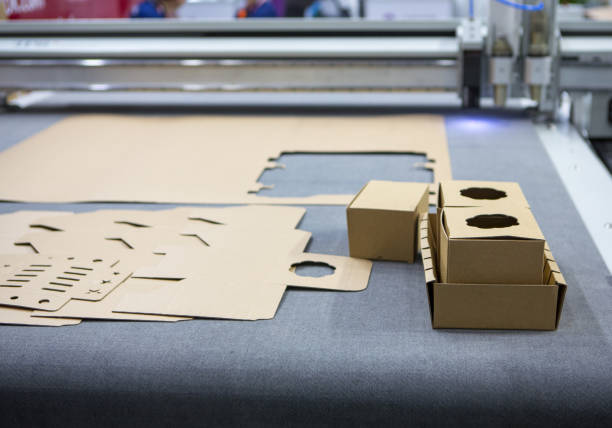
A stock image related to cutting die cut.
What International Standards Should B2B Buyers Consider?
One of the most widely recognized international quality standards is ISO 9001, which focuses on quality management systems. This certification ensures that suppliers have processes in place to consistently deliver high-quality products. B2B buyers should prioritize working with manufacturers that hold ISO 9001 certification.
Additionally, depending on the industry, other certifications such as CE (Conformité Européenne) for products sold in Europe or API (American Petroleum Institute) standards for oil and gas applications may be relevant. Buyers should verify that suppliers comply with these standards, as they often reflect the supplier’s commitment to quality.
What Are the Key Quality Control Checkpoints?
Quality control (QC) checkpoints are critical throughout the manufacturing process. Common checkpoints include:
-
Incoming Quality Control (IQC): This initial inspection checks the quality of raw materials before they enter production. It ensures that only suitable materials are used, reducing the risk of defects.
-
In-Process Quality Control (IPQC): Conducted during the manufacturing process, this involves regular checks to ensure that the die cutting process adheres to specified standards. This may include monitoring machine performance and inspecting the accuracy of cuts.
-
Final Quality Control (FQC): At this stage, the finished products undergo comprehensive testing to ensure they meet quality specifications. This often includes dimensional checks, performance testing, and visual inspections.
B2B buyers should inquire about the specific QC measures implemented by their suppliers and request access to QC reports to evaluate their commitment to quality.
What Common Testing Methods Are Used in Quality Assurance?
Several testing methods are employed to ensure the quality of cutting dies:
-
Dimensional Inspection: This involves measuring the die against specified tolerances using tools like calipers and micrometers.
-
Performance Testing: This assesses how well the die performs under actual cutting conditions, including its ability to cut various materials without wear.
-
Material Testing: Techniques such as hardness testing and metallurgical analysis can confirm that the materials used meet specified standards.
Buyers should confirm that their suppliers utilize these testing methods and are willing to share test results for transparency.
How Can B2B Buyers Verify Supplier Quality Control?
Verifying the quality control processes of suppliers is crucial for B2B buyers. Here are effective strategies to ensure supplier reliability:
-
Conduct Audits: Regular audits can provide insights into the supplier’s manufacturing and QC processes. Buyers should consider scheduling audits to assess compliance with quality standards.
-
Request Quality Reports: Suppliers should be willing to provide documentation of their QC processes, including IQC, IPQC, and FQC reports. These documents can serve as proof of the supplier’s commitment to quality.
-
Utilize Third-Party Inspections: Engaging third-party inspection services can provide an unbiased assessment of the supplier’s quality control measures. This is particularly useful for international buyers who may face challenges in visiting suppliers in person.
-
Understand Certification Nuances: Different regions may have specific certification requirements. Buyers from Africa, South America, the Middle East, and Europe should ensure that suppliers meet local regulations and standards.
By implementing these strategies, B2B buyers can significantly mitigate risks associated with quality and ensure that they are partnering with reliable suppliers in the die cut manufacturing industry.
Practical Sourcing Guide: A Step-by-Step Checklist for ‘cutting die cut’
In the rapidly evolving world of die-cutting, international B2B buyers must navigate a complex landscape to procure the best cutting die cut solutions for their needs. This guide provides a structured checklist designed to streamline the sourcing process, ensuring buyers make informed decisions that align with their operational requirements and budget constraints.
Step 1: Define Your Technical Specifications
Before engaging with suppliers, it’s essential to have a clear understanding of your technical requirements. Consider the types of materials you will be cutting, such as paper, fabric, or metal, and the specific dimensions and shapes needed for your projects.
– Material Compatibility: Ensure that the cutting die can handle the thickness and composition of your materials.
– Precision Needs: Determine the level of precision required for your applications to avoid costly errors.
Step 2: Conduct Market Research
Investigate the current market landscape for cutting die cut solutions. Identify key players, compare product offerings, and gather insights into industry trends.
– Supplier Listings: Use platforms like Alibaba, ThomasNet, or industry-specific directories to compile a list of potential suppliers.
– Customer Reviews: Look for testimonials and case studies to gauge supplier reliability and product quality.
Step 3: Evaluate Potential Suppliers
Before committing, it’s crucial to vet suppliers thoroughly. Request company profiles, case studies, and references from buyers in a similar industry or region.
– Production Capacity: Ensure the supplier can meet your volume requirements without compromising quality.
– Lead Times: Discuss production and shipping timelines to align with your project schedules.
Step 4: Verify Quality Standards and Certifications
Quality assurance is vital in the die-cutting industry. Verify that suppliers adhere to industry standards and have the necessary certifications.
– ISO Certifications: Look for suppliers with ISO 9001 certification, which ensures a commitment to quality management.
– Material Safety: Ensure compliance with relevant safety standards, especially if cutting materials that may affect product safety or environmental impact.
Step 5: Request Samples
Once you’ve narrowed down your options, request samples of the cutting dies. This step allows you to assess the quality and performance firsthand.
– Testing for Compatibility: Use the samples with your materials to verify the cutting efficiency and precision.
– Feedback Loop: Gather input from your production team on the usability and effectiveness of the samples.
Step 6: Negotiate Terms and Pricing
Engage in negotiations with your chosen suppliers to secure favorable terms. Understand the total cost of ownership, including shipping, taxes, and any potential tariffs.
– Volume Discounts: Inquire about bulk order discounts or loyalty programs for repeat business.
– Payment Terms: Discuss flexible payment options that align with your cash flow requirements.
Step 7: Establish a Communication Protocol
Effective communication is key to a successful supplier relationship. Establish clear lines of communication and protocols for updates, feedback, and issue resolution.
– Regular Check-ins: Schedule periodic meetings to review performance and address any concerns.
– Point of Contact: Designate a primary contact person on both sides to streamline communication and decision-making.
By following this practical sourcing checklist, international B2B buyers can navigate the complexities of procuring cutting die cut solutions effectively, ensuring that they select suppliers who align with their operational needs and quality standards.
Comprehensive Cost and Pricing Analysis for cutting die cut Sourcing
What Are the Key Cost Components in Cutting Die Cut Sourcing?
When sourcing cutting die cuts, understanding the cost structure is crucial for international B2B buyers. The cost components typically include:
-
Materials: The choice of materials significantly impacts pricing. Common materials for cutting dies include steel and tungsten carbide, with costs varying based on quality and thickness. Premium materials offer durability but may increase initial costs.
-
Labor: Labor costs encompass the wages of skilled workers involved in die production and assembly. In regions with higher labor costs, such as Europe, you may see elevated pricing compared to countries with lower labor costs, like some parts of Africa or South America.
-
Manufacturing Overhead: This includes expenses related to factory utilities, maintenance, and equipment depreciation. Efficient production processes can lower overhead costs, which can be beneficial for buyers looking for competitive pricing.
-
Tooling: Tooling costs cover the creation of custom dies and molds. Complex designs or specialized dies often require higher tooling investments, which can affect the overall price.
-
Quality Control (QC): Ensuring the precision and quality of die cuts is essential. Implementing rigorous QC processes adds to the cost but is necessary for maintaining standards, especially for industries requiring high precision, such as automotive or aerospace.
-
Logistics: Transportation and shipping costs can vary significantly based on the distance from the supplier and the chosen Incoterms. Buyers should consider these costs as part of their total sourcing expenses.
-
Margin: Suppliers typically add a profit margin to cover their costs and generate profit. This margin can vary widely based on market demand, competition, and supplier reputation.
How Do Price Influencers Affect Cutting Die Cut Costs?
Several factors can influence the pricing of cutting die cuts, including:
-
Volume/MOQ (Minimum Order Quantity): Larger orders often result in lower per-unit costs due to economies of scale. Buyers should assess their needs carefully to negotiate better prices.
-
Specifications and Customization: Custom dies tailored to specific requirements usually incur higher costs. Buyers should balance their need for customization with the associated price increase.
-
Material Quality and Certifications: Higher quality materials and certifications (such as ISO standards) can increase costs but often lead to longer-lasting products. Buyers should evaluate whether the benefits justify the additional expense.
-
Supplier Factors: The reputation and reliability of the supplier can affect pricing. Established suppliers may charge more due to their experience and quality assurance practices.
-
Incoterms: The choice of Incoterms can significantly influence logistics costs and responsibilities. Understanding these terms is crucial for managing shipping expenses effectively.
What Tips Can Help Buyers Optimize Cutting Die Cut Sourcing Costs?
International B2B buyers can leverage several strategies to enhance cost-efficiency in cutting die cut sourcing:
-
Effective Negotiation: Building strong relationships with suppliers can lead to better pricing and terms. Buyers should be prepared to negotiate based on volume and long-term commitments.
-
Total Cost of Ownership (TCO): Beyond the initial price, consider the total cost of ownership, which includes maintenance, replacement, and operational costs. A higher upfront investment in quality may yield lower long-term costs.
-
Understand Pricing Nuances for Different Regions: Pricing can vary by region due to local economic conditions, labor costs, and material availability. Buyers from Africa, South America, the Middle East, and Europe should conduct regional market analyses to identify optimal sourcing strategies.
-
Stay Informed About Market Trends: Being aware of fluctuations in material costs and market demand can help buyers time their purchases effectively, potentially securing better deals.
Disclaimer on Indicative Prices
It is important to note that prices for cutting die cuts can vary widely based on the factors discussed above. The information provided here serves as a guideline, and buyers are encouraged to conduct thorough market research and supplier evaluations to obtain accurate pricing tailored to their specific needs.
Alternatives Analysis: Comparing cutting die cut With Other Solutions
Understanding the Importance of Evaluating Alternatives to Cutting Die Cuts
In the rapidly evolving landscape of manufacturing and crafting, businesses must continually assess various methods and technologies to optimize their production processes. The cutting die cut method is widely recognized for its precision and efficiency in shaping materials. However, it is crucial for B2B buyers to explore alternative solutions that may better suit their specific needs, particularly in diverse markets such as Africa, South America, the Middle East, and Europe.
Comparison Table of Cutting Die Cut and Alternatives
Comparison Aspect | Cutting Die Cut | Laser Cutting | Digital Cutting |
---|---|---|---|
Performance | High precision and repeatability for complex shapes | Extremely high precision; ideal for intricate designs | Good precision; effective for simpler shapes |
Cost | Moderate initial investment; ongoing costs for die maintenance | Higher initial investment; lower material waste | Variable costs based on technology and software |
Ease of Implementation | Requires specific machinery and die sets; setup can be time-consuming | Complex setup; skilled operators needed | User-friendly; software-driven design reduces manual setup |
Maintenance | Requires regular maintenance of dies; can be costly | Minimal maintenance; long lifespan of equipment | Low maintenance; software updates necessary |
Best Use Case | Ideal for high-volume production of consistent shapes | Best for intricate designs and one-off projects | Suitable for prototyping and small batch production |
Detailed Breakdown of Alternatives to Cutting Die Cuts
What Are the Benefits and Drawbacks of Laser Cutting?
Laser cutting is a popular alternative that utilizes high-powered lasers to cut through materials with exceptional precision. One of its primary advantages is the ability to handle intricate designs that would be challenging with traditional die cuts. Additionally, laser cutting generates less waste compared to die cutting, making it a more environmentally friendly option. However, the initial investment for laser cutting machines is considerably higher, and the technology requires skilled operators to ensure optimal results. This method is best suited for businesses focused on custom, low-volume projects where precision is paramount.
How Does Digital Cutting Compare to Traditional Methods?
Digital cutting employs software-driven technology to create shapes and designs directly from digital files. This method is highly adaptable, allowing for quick changes in design without the need for new dies or extensive setup. Digital cutting is particularly advantageous for prototyping and small batch production, as it reduces lead times significantly. However, while it performs well for simpler shapes, it may not match the precision of die cutting or laser cutting for more complex designs. The costs can vary based on the software and machinery used, making it essential for buyers to evaluate their specific production needs.
Making the Right Choice: How Should B2B Buyers Evaluate Their Options?
When selecting the most suitable cutting method, B2B buyers must consider several factors, including production volume, material types, design complexity, and budget constraints. Cutting die cuts excel in high-volume production where consistency and precision are vital, while laser cutting is ideal for detailed work with lower volumes. Digital cutting offers flexibility for rapid prototyping and small runs, making it an excellent choice for businesses that prioritize innovation and adaptability. Ultimately, understanding the strengths and weaknesses of each option will empower buyers to make informed decisions that align with their operational goals.
Essential Technical Properties and Trade Terminology for cutting die cut
What Are the Essential Technical Properties of Cutting Dies?
Understanding the technical properties of cutting dies is crucial for B2B buyers, especially those sourcing from diverse regions such as Africa, South America, the Middle East, and Europe. Here are key specifications to consider:
1. Material Grade: Why Does It Matter?
The material used for cutting dies typically includes high-carbon steel, tool steel, or carbide. Each material offers different hardness and wear resistance, affecting the die’s longevity and performance. For instance, high-carbon steel is suitable for softer materials, while carbide dies are ideal for high-volume production and tougher materials. Selecting the right material grade ensures optimal performance, reducing the frequency of die replacements and maintenance costs.
2. Tolerance Levels: What Should You Expect?
Tolerance refers to the permissible limit of variation in a die’s dimensions. For example, a tolerance of ±0.01mm is standard for precision cutting dies. Inaccurate tolerances can lead to poor fitment in production, resulting in wasted materials and time. Understanding tolerance specifications helps buyers ensure that the dies will meet their production needs without compromising quality.
3. Die Thickness: How Does It Influence Performance?
The thickness of a cutting die can vary significantly, often ranging from 0.5mm to 5mm. Thicker dies are generally more robust and can handle greater pressure, making them suitable for cutting dense materials. Conversely, thinner dies are beneficial for intricate designs and softer materials. Buyers must consider the specific application to choose the appropriate die thickness that balances durability and precision.
4. Cutting Edge Geometry: What Should You Know?
The geometry of the cutting edge, including its angle and profile, directly influences the cutting efficiency and quality. Common geometries include straight, serrated, and beveled edges. Each design serves a specific purpose; for example, beveled edges are better for intricate cuts. Understanding these geometries allows buyers to select dies that enhance production efficiency and reduce scrap rates.
5. Coating: Does It Enhance Durability?
Many cutting dies feature surface coatings such as titanium nitride (TiN) or chromium to enhance durability and reduce friction. These coatings can significantly extend the life of a die, especially in high-volume operations. Buyers should inquire about coating options when sourcing dies, as they can lead to long-term cost savings and improved performance.
What Are Common Trade Terms in the Cutting Die Industry?
In the B2B cutting die sector, familiarity with specific trade terminology is essential for effective communication and negotiation. Here are some common terms:
1. OEM (Original Equipment Manufacturer): What Does It Mean?
OEM refers to companies that produce parts or equipment that may be marketed by another manufacturer. In the context of cutting dies, OEMs are crucial for buyers looking for customized solutions. Understanding OEM relationships can help buyers negotiate better terms and ensure they receive high-quality products tailored to their specifications.
2. MOQ (Minimum Order Quantity): Why Is It Important?
MOQ is the smallest quantity of a product that a supplier is willing to sell. For cutting dies, MOQs can vary widely based on material and complexity. Knowing the MOQ helps buyers plan their purchases effectively, ensuring they meet production needs without overcommitting financially.
3. RFQ (Request for Quotation): How Does It Work?
An RFQ is a standard business process used to invite suppliers to bid on specific products or services. In the cutting die industry, issuing an RFQ allows buyers to obtain pricing and terms from multiple suppliers, facilitating informed decision-making. It is a critical step in sourcing high-quality cutting dies at competitive prices.
4. Incoterms: What Should You Know?
Incoterms are a set of international commercial terms that define the responsibilities of buyers and sellers in shipping goods. Understanding these terms is vital for buyers from different regions, as they outline who is responsible for costs and risks at various stages of the shipping process. Familiarity with Incoterms can prevent misunderstandings and ensure smoother transactions.
By grasping these essential technical properties and trade terms, international B2B buyers can make more informed decisions when sourcing cutting dies, ultimately enhancing their production efficiency and product quality.
Navigating Market Dynamics and Sourcing Trends in the cutting die cut Sector
What Are the Key Market Dynamics and Trends in the Cutting Die Cut Sector?
The cutting die cut sector is experiencing significant transformation driven by global market demands and technological advancements. For international B2B buyers from regions like Africa, South America, the Middle East, and Europe, understanding these dynamics is crucial. The rise of automation and digital technologies, such as die-cutting machines that integrate with design software, has streamlined production processes, reducing lead times and increasing accuracy. This shift towards digitalization allows businesses to adapt quickly to market changes and customer preferences, providing a competitive edge.
Moreover, the demand for customized solutions is on the rise, with buyers increasingly seeking bespoke die-cut designs tailored to specific applications. This trend is particularly evident in packaging, where unique shapes and sizes can enhance product appeal. Additionally, the growing e-commerce sector is driving the need for efficient packaging solutions, further boosting the die-cutting market. As a result, suppliers are now focusing on developing versatile die-cutting technologies that can cater to various materials, including paper, plastic, and textiles, thereby expanding their market reach.
How Can Sustainability and Ethical Sourcing Impact the Cutting Die Cut Sector?
Sustainability has become a pivotal concern in the cutting die cut sector, influencing sourcing decisions among international B2B buyers. The environmental impact of manufacturing processes, including waste generation and resource consumption, is prompting businesses to seek more sustainable options. Ethical sourcing practices are increasingly valued, with buyers prioritizing suppliers who demonstrate a commitment to reducing their carbon footprint and employing eco-friendly materials.
Buyers should consider partnerships with manufacturers that utilize ‘green’ certifications, such as FSC (Forest Stewardship Council) or ISO 14001, which signify responsible environmental practices. Additionally, sourcing from suppliers that offer biodegradable or recyclable materials can enhance brand reputation and appeal to environmentally conscious consumers. As sustainability becomes a focal point for many businesses, integrating these practices into the supply chain not only mitigates environmental impact but also aligns with consumer expectations and regulatory requirements.
What Is the Evolution of the Cutting Die Cut Sector?
The cutting die cut sector has evolved significantly from traditional manual processes to highly automated systems. Initially, die-cutting was a labor-intensive operation, relying on skilled craftsmen to create dies and perform cutting tasks. With the advent of industrialization in the 19th century, mechanical die-cutting machines emerged, revolutionizing the industry by increasing production speed and precision.
In recent decades, technological advancements have further transformed the sector, introducing computer-aided design (CAD) software and digital die-cutting machines. These innovations allow for rapid prototyping and customization, catering to the diverse needs of modern consumers. Today, the cutting die cut sector is characterized by a blend of traditional craftsmanship and advanced technology, providing international B2B buyers with a wide range of options that enhance efficiency and creativity in their production processes.
Frequently Asked Questions (FAQs) for B2B Buyers of cutting die cut
-
How do I choose the right cutting die for my business needs?
Choosing the right cutting die involves assessing the materials you will use, the complexity of the designs you need, and your production volume. For intricate designs, opt for high-quality dies made from durable materials like steel. Additionally, consider the compatibility of the dies with your existing cutting machines. If you plan to scale up production, select dies that can withstand higher usage and are suitable for various materials, including paper, foam, or fabric. -
What is the best die cutting machine for small to medium businesses?
For small to medium businesses, a versatile die cutting machine like the Sizzix Big Shot or similar models is often ideal. These machines accommodate a range of die sizes and types, allowing for flexibility in production. They are user-friendly and require minimal setup, making them suitable for businesses with limited technical expertise. Consider the machine’s compatibility with various die types and ease of maintenance when making your choice. -
How can I ensure the quality of cutting dies from international suppliers?
To ensure quality, conduct thorough supplier vetting by checking their certifications, customer reviews, and previous work samples. Request samples of cutting dies before placing a large order to evaluate their performance and durability. Additionally, establish clear quality assurance protocols, such as inspecting the dies upon arrival and ensuring they meet your specifications. Regular communication with the supplier can also help maintain quality standards throughout your partnership. -
What are the typical minimum order quantities (MOQs) for cutting dies?
Minimum order quantities for cutting dies can vary widely depending on the supplier and the complexity of the designs. Generally, MOQs can range from 50 to 500 units. It’s essential to discuss your needs with suppliers to understand their MOQ policies. If your order volume is lower, some suppliers may offer flexibility or suggest alternatives, such as custom orders, to accommodate your business requirements. -
What payment terms should I expect when sourcing cutting dies internationally?
Payment terms can differ based on the supplier’s policies and your negotiation. Common terms include a deposit (typically 30-50%) upfront, with the balance due before shipment. Some suppliers may offer net payment terms, allowing payment within 30 to 90 days post-delivery. Ensure you clarify payment methods accepted (e.g., wire transfer, credit card) and consider using escrow services for added security when dealing with new suppliers. -
How can I manage shipping and logistics for cutting dies from international suppliers?
Managing shipping and logistics involves selecting reliable freight forwarders who specialize in international shipments. Discuss shipping options, delivery timelines, and costs with your supplier, ensuring you understand any customs duties or taxes that may apply. It’s advisable to use Incoterms (like FOB or CIF) to define responsibilities for shipping and insurance. Regular tracking of your shipments can help mitigate delays and ensure timely delivery. -
What customization options are available for cutting dies?
Many suppliers offer customization options for cutting dies, allowing you to create unique shapes or designs tailored to your brand. Discuss your specific needs with potential suppliers, including size, shape, and material preferences. Some manufacturers may provide design assistance to help you achieve your desired outcome. Be sure to inquire about lead times and any additional costs associated with custom die production. -
How do I handle issues with defective cutting dies from suppliers?
If you encounter defects in cutting dies, promptly contact the supplier to report the issue. Document the defects with photos and detailed descriptions to support your case. Most reputable suppliers will have a return or replacement policy in place. Establish clear communication regarding timelines for resolution and ensure you understand the procedures for returning defective items. Regularly reviewing your supplier’s warranty and return policies can help preemptively address any future issues.
Important Disclaimer & Terms of Use
⚠️ Important Disclaimer
The information provided in this guide, including content regarding manufacturers, technical specifications, and market analysis, is for informational and educational purposes only. It does not constitute professional procurement advice, financial advice, or legal advice.
While we have made every effort to ensure the accuracy and timeliness of the information, we are not responsible for any errors, omissions, or outdated information. Market conditions, company details, and technical standards are subject to change.
B2B buyers must conduct their own independent and thorough due diligence before making any purchasing decisions. This includes contacting suppliers directly, verifying certifications, requesting samples, and seeking professional consultation. The risk of relying on any information in this guide is borne solely by the reader.
Strategic Sourcing Conclusion and Outlook for cutting die cut
What Are the Key Takeaways for International B2B Buyers in Cutting Die Cut?
In summary, strategic sourcing in the die-cutting sector offers significant advantages for international B2B buyers. Understanding the diversity of die-cutting machines and materials is crucial, as it enables buyers to select the right tools tailored to their specific needs. The ability to source quality dies that can cut various materials—including paper, metal, and fabrics—ensures versatility and innovation in product offerings.
Why Is Strategic Sourcing Vital for Cutting Die Cut Success?
Implementing a strategic sourcing approach not only enhances cost efficiency but also builds robust supplier relationships that can lead to improved product quality and reliability. Buyers from Africa, South America, the Middle East, and Europe should prioritize suppliers that demonstrate a commitment to sustainability and innovation, ensuring long-term value and competitive advantage.
What Does the Future Hold for Cutting Die Cut Buyers?
Looking ahead, the die-cutting industry is poised for growth, driven by technological advancements and increasing demand for customized solutions. International buyers should actively seek partnerships with suppliers who are adaptable and can leverage new technologies. By doing so, they will not only meet current market demands but also position themselves for future success. Engage with suppliers today to explore how cutting die cut solutions can elevate your business offerings in this dynamic market.