Master Dies and Stamping: The Ultimate Guide for B2B Buyers (2025)
Introduction: Navigating the Global Market for dies and stamping
In today’s competitive global market, sourcing high-quality dies and stamping solutions poses a significant challenge for international B2B buyers, particularly those from diverse regions such as Africa, South America, the Middle East, and Europe. As manufacturers increasingly seek to optimize production efficiency and reduce costs, understanding the nuances of the die and stamping industry becomes essential. This guide aims to equip buyers with comprehensive insights into various types of dies and stamping processes, applications across industries, and effective supplier vetting strategies.
By exploring the myriad options—from progressive dies to transfer dies—this resource will help you navigate the complexities of metal stamping, including the critical factors that influence pricing and lead times. Furthermore, we will delve into essential considerations for selecting the right suppliers, ensuring that your sourcing decisions align with quality standards and operational needs.
Whether you’re in Spain assessing local suppliers or in Saudi Arabia looking for global partners, this guide empowers you to make informed purchasing decisions. Ultimately, our goal is to streamline your procurement process, enabling you to leverage dies and stamping technologies that enhance your production capabilities while maintaining a competitive edge in your market.
Understanding dies and stamping Types and Variations
Type Name | Key Distinguishing Features | Primary B2B Applications | Brief Pros & Cons for Buyers |
---|---|---|---|
Progressive Dies | Multiple operations in one setup; automated feeding | Automotive parts, electronics | Pros: High efficiency, reduced cycle time. Cons: Higher initial cost, complex setup. |
Transfer Dies | Moves parts between stations; suitable for larger parts | Aerospace components, heavy machinery | Pros: Flexibility for complex shapes. Cons: More expensive, requires skilled operation. |
Line Dies | Simple, single-operation dies; often manually loaded | Basic metal components, appliances | Pros: Lower cost, easier setup. Cons: Slower production speed, limited complexity. |
Blanking Dies | Cuts out shapes from sheets; retains material for further use | Fabrication, construction | Pros: Material efficiency, versatile applications. Cons: Limited to specific shapes. |
Piercing Dies | Creates holes in materials; focuses on scrap reduction | Electrical enclosures, automotive | Pros: Cost-effective for high-volume production. Cons: Limited to hole-making applications. |
What are Progressive Dies and Their Suitability for B2B Buyers?
Progressive dies are characterized by their ability to perform multiple operations in a single setup, making them highly efficient for high-volume production. These dies are often used in the automotive and electronics industries, where precision and speed are crucial. B2B buyers should consider the initial investment, as progressive dies can be more expensive due to their complexity. However, the long-term savings from reduced cycle times and labor costs can offset this initial expense.
How Do Transfer Dies Enhance Production Capabilities?
Transfer dies are designed to move parts between various stations during the stamping process, making them suitable for larger and more complex parts, such as those used in aerospace and heavy machinery. They offer flexibility in design and can accommodate intricate shapes. Buyers should evaluate their production needs carefully, as transfer dies tend to have higher costs and require skilled operators for effective use. The investment may be justified for businesses that demand versatility and precision in their manufacturing processes.
Why Choose Line Dies for Simplicity and Cost-Effectiveness?
Line dies are known for their simplicity and are often manually loaded, making them a cost-effective option for producing basic metal components used in appliances and other everyday items. While they have a lower initial cost and are easier to set up, their production speed is slower compared to more complex dies. B2B buyers looking for straightforward applications with limited complexity may find line dies to be an ideal choice, balancing affordability and functionality.
What Advantages Do Blanking Dies Offer for Material Efficiency?
Blanking dies are specifically designed to cut shapes out of metal sheets while retaining the remaining material for further processing. They are widely used in fabrication and construction industries. The primary advantage for buyers is the material efficiency they provide, as they maximize the use of raw materials. However, they are limited to specific shapes, which may not suit all production needs. Companies should assess their design requirements to determine if blanking dies align with their production goals.
How Do Piercing Dies Contribute to Cost-Effective Production?
Piercing dies focus on creating holes in materials and are particularly effective in reducing scrap during high-volume production runs. They are commonly used in applications such as electrical enclosures and automotive components. For B2B buyers, the cost-effectiveness of piercing dies makes them an attractive option for companies looking to streamline their manufacturing processes. However, buyers should note that these dies are limited to hole-making tasks, which may not meet all production requirements.
Key Industrial Applications of dies and stamping
Industry/Sector | Specific Application of dies and stamping | Value/Benefit for the Business | Key Sourcing Considerations for this Application |
---|---|---|---|
Automotive | Production of body panels and structural components | High precision and repeatability, reducing waste and rework costs | Material specifications, tooling durability, and supplier reliability |
Electronics | Manufacturing of enclosures and connectors | Enhanced product durability and performance, cost-effective scaling | Compliance with international standards, lead times, and flexibility |
Construction | Creation of metal brackets and fasteners | Improved structural integrity and safety, reduced assembly time | Material grades, custom tooling capabilities, and delivery schedules |
Aerospace | Fabrication of components such as brackets and panels | Lightweight and high-strength parts, critical for performance | Certification requirements, precision tolerances, and traceability |
Consumer Goods | Production of metal housings and decorative components | Aesthetic appeal and functionality, cost-effective mass production | Design adaptability, finish quality, and sourcing of sustainable materials |
How is dies and stamping used in the automotive industry?
In the automotive sector, dies and stamping are essential for producing body panels and structural components. The process allows for high precision in shaping metal sheets, which is critical for safety and performance in vehicles. International buyers must consider material specifications, as different regions may have varying regulations regarding automotive safety standards. Additionally, tooling durability is paramount, as it impacts production efficiency and costs. A reliable supplier can help mitigate risks associated with rework and waste.
What applications exist for dies and stamping in the electronics sector?
In the electronics industry, dies and stamping are used to manufacture enclosures and connectors that require high precision and durability. This method ensures that components can withstand environmental stresses while maintaining performance. For international buyers, compliance with international standards is crucial, particularly for electronic devices. Lead times and supplier flexibility can also affect the production schedule, making it essential to choose a supplier with a proven track record in meeting demand.
How do dies and stamping benefit the construction industry?
The construction industry utilizes dies and stamping to create metal brackets and fasteners, which are critical for structural integrity. These components enhance safety and reduce assembly time, making construction projects more efficient. Buyers in this sector need to focus on material grades to ensure that the products meet local building codes. Custom tooling capabilities are also important, as projects often require unique designs to fit specific architectural needs.
What are the key applications of dies and stamping in aerospace manufacturing?
In aerospace, dies and stamping are employed to fabricate lightweight yet strong components like brackets and panels. The precision achieved through stamping is vital for performance and safety in aircraft. International buyers must navigate certification requirements, which can vary significantly by region. Precision tolerances and traceability are also critical, as they ensure compliance with stringent aerospace regulations and standards.
How are dies and stamping utilized in the consumer goods sector?
The consumer goods industry leverages dies and stamping for producing metal housings and decorative components. This process not only enhances the aesthetic appeal of products but also contributes to their functionality and durability. For international buyers, design adaptability is crucial to accommodate diverse market preferences. Additionally, finish quality and the sourcing of sustainable materials are increasingly important in meeting consumer expectations and regulatory standards.
3 Common User Pain Points for ‘dies and stamping’ & Their Solutions
Scenario 1: Difficulty in Sourcing the Right Die Design for Custom Needs
The Problem:
B2B buyers often face challenges when it comes to sourcing dies that meet their specific requirements. This is particularly true for companies in Africa and South America, where access to advanced die design technology may be limited. A buyer may have a unique product in mind that requires a specialized die, but they find it hard to locate a manufacturer who can create a custom solution. This can lead to delays in production timelines, increased costs, and frustration over potential compromises on product quality.
The Solution:
To effectively tackle this issue, buyers should begin by engaging with manufacturers that specialize in custom die design. It’s essential to clearly communicate your specific requirements, including dimensions, materials, and production volumes. Leverage digital tools such as CAD (Computer-Aided Design) software to create detailed specifications, which can facilitate better communication with potential suppliers. Additionally, consider reaching out to industry-specific forums or trade associations where you can connect with manufacturers who have experience in producing tailored dies. Establishing a close working relationship with a manufacturer can also lead to iterative design processes, ensuring the final product meets your expectations without compromising quality.
Scenario 2: High Production Costs and Material Waste
The Problem:
Many international B2B buyers are concerned about escalating production costs and the resultant material waste during the stamping process. This issue is particularly pronounced in regions like the Middle East, where operational costs can be significant. Buyers often find that their stamping processes are not optimized, leading to excessive scrap metal and increased expenses, which can hinder competitiveness in the market.
The Solution:
To combat high production costs and minimize material waste, companies should invest in high-quality dies designed for efficiency. Selecting dies that require less cutting clearance can improve material utilization and reduce scrap. Additionally, conducting a thorough analysis of the stamping process can reveal inefficiencies. Techniques such as lean manufacturing principles can be applied to streamline operations. Collaborating with suppliers who offer services like die simulation can also help visualize the stamping process, allowing for adjustments before physical production begins. Regularly reviewing and updating your die technology, as well as employee training on best practices, can further enhance operational efficiency.
Scenario 3: Frequent Downtime Due to Die Maintenance Issues
The Problem:
Frequent downtime caused by die maintenance can be a significant pain point for B2B buyers, especially in Europe where production efficiency is critical. A company may experience unexpected failures or breakdowns, leading to costly delays in production schedules. These issues often stem from a lack of proper maintenance protocols or inadequate training for staff on die care, which can result in reduced lifespan of the dies and increased repair costs.
The Solution:
To mitigate downtime due to maintenance issues, it’s crucial to implement a proactive maintenance schedule tailored to your specific dies and stamping operations. Establish a routine inspection protocol to identify wear and tear early, allowing for timely repairs before major breakdowns occur. Additionally, investing in training programs for your maintenance staff on die care and troubleshooting can significantly improve your operational reliability. Utilizing predictive maintenance technologies, such as IoT sensors that monitor die performance in real-time, can also help anticipate issues before they lead to downtime. Lastly, consider working closely with your die supplier to understand the best practices for maintenance and longevity of your dies, ensuring your operations remain efficient and productive.
Strategic Material Selection Guide for dies and stamping
What Are the Key Materials for Dies and Stamping?
When selecting materials for dies and stamping, it is crucial to consider the specific properties and performance characteristics that will influence the manufacturing process and the quality of the final products. Below, we analyze four common materials used in dies and stamping, focusing on their properties, advantages, disadvantages, and considerations for international B2B buyers.
How Does Tool Steel Perform in Dies and Stamping Applications?
Key Properties: Tool steel is renowned for its hardness, wear resistance, and ability to withstand high temperatures. It typically has a high carbon content, which enhances its hardness, making it suitable for high-stress applications.
Pros & Cons: The durability of tool steel makes it ideal for producing intricate dies that require precision. However, it can be expensive and may require complex machining processes. While it performs exceptionally well in high-volume production, its high cost can be a limiting factor for smaller operations.
Impact on Application: Tool steel is compatible with various metals, including aluminum and stainless steel, making it versatile for different stamping applications.
Considerations for International Buyers: Compliance with international standards such as ASTM or DIN is essential. Buyers from regions like Europe or the Middle East should be aware of local regulations regarding material sourcing and environmental compliance.
What Role Does Carbide Play in Die Manufacturing?
Key Properties: Carbide is a composite material made from tungsten and carbon, known for its extreme hardness and resistance to wear. It can withstand higher temperatures than tool steel, making it suitable for demanding applications.
Pros & Cons: The primary advantage of carbide is its longevity and the ability to maintain sharp edges, which reduces downtime for maintenance. However, carbide is brittle, making it susceptible to chipping under shock loads. Additionally, it is significantly more expensive than tool steel.
Impact on Application: Carbide is particularly effective in applications involving abrasive materials, as it minimizes wear and tear on the die.
Considerations for International Buyers: Buyers should consider the availability of carbide in their regions and the associated costs. Compliance with industry standards is also crucial, especially for sectors like automotive manufacturing.
Why Is Aluminum a Viable Option for Stamping Dies?
Key Properties: Aluminum is lightweight, corrosion-resistant, and has excellent thermal conductivity. It is often used for prototypes or low-volume production runs.
Pros & Cons: The main advantage of aluminum is its cost-effectiveness and ease of machining, making it suitable for rapid prototyping. However, it lacks the durability of tool steel or carbide, which can limit its use in high-volume applications.
Impact on Application: Aluminum is compatible with various stamping processes and can be used for parts requiring lightweight materials, such as automotive components.
Considerations for International Buyers: Buyers in Africa and South America may find aluminum more accessible and affordable. However, they should ensure compliance with local material standards and regulations.
How Does Stainless Steel Compare in Die and Stamping Applications?
Key Properties: Stainless steel offers excellent corrosion resistance and strength. It can withstand high temperatures and is suitable for various environments.
Pros & Cons: The durability and corrosion resistance of stainless steel make it ideal for applications in harsh environments. However, it can be more challenging to machine compared to other materials, leading to higher manufacturing costs.
Impact on Application: Stainless steel is suitable for stamping parts that require both strength and resistance to corrosion, such as components in the food and medical industries.
Considerations for International Buyers: Compliance with international standards like JIS or ASTM is crucial, especially for industries with strict regulatory requirements. Buyers should also consider the sourcing of stainless steel in their regions.
Summary Table of Material Selection for Dies and Stamping
Material | Typical Use Case for dies and stamping | Key Advantage | Key Disadvantage/Limitation | Relative Cost (Low/Med/High) |
---|---|---|---|---|
Tool Steel | High-volume production dies | Excellent hardness and wear resistance | High cost and complex machining | High |
Carbide | High-precision stamping applications | Extreme hardness and longevity | Brittle and expensive | High |
Aluminum | Prototyping and low-volume production | Cost-effective and easy to machine | Less durable for high-volume applications | Medium |
Stainless Steel | Corrosive environment applications | Corrosion resistance and strength | Difficult to machine, higher costs | Medium to High |
This guide provides actionable insights for international B2B buyers, helping them make informed decisions regarding material selection in dies and stamping applications. Understanding the properties, advantages, disadvantages, and regional considerations can enhance procurement strategies and optimize production outcomes.
In-depth Look: Manufacturing Processes and Quality Assurance for dies and stamping
What Are the Main Stages of the Manufacturing Process for Dies and Stamping?
Manufacturing dies and stamping components involves a series of well-defined processes that ensure precision and quality. Understanding these stages is crucial for B2B buyers to ensure they partner with suppliers who can meet their specific needs.
Material Preparation: What Materials Are Used and How Are They Prepared?
The first step in the manufacturing process is material preparation. Typically, high-grade tool steels or specialized alloys are selected based on the requirements of the final product. For example, materials may include carbon steels, stainless steels, or aluminum, each chosen for their specific properties such as strength, ductility, and wear resistance.
Before fabrication, materials undergo rigorous inspection to confirm their compliance with international standards. This may involve checking for dimensional accuracy, surface defects, and material properties through techniques such as ultrasonic testing or hardness testing. Proper material preparation is vital, as it directly impacts the die’s performance and the quality of the stamped parts.
Forming Process: What Techniques Are Employed in Die Stamping?
The forming stage is where the actual shaping of materials occurs. This process can be divided into several techniques, including blanking, piercing, and bending.
- Blanking involves cutting out a shape from a sheet of metal, resulting in a ‘blank’ that will be further processed.
- Piercing creates holes in the material, with the scrap material being discarded.
- Bending shapes the metal without cutting, using specialized bending tools and dies.
Each of these processes requires precise control over parameters such as pressure, speed, and die design to ensure that the final products meet stringent specifications. Automation in stamping processes, such as the use of robotic arms, enhances efficiency and consistency, reducing the risk of human error.
Assembly: How Are Dies Assembled for Optimal Performance?
Once individual components are formed, the assembly stage comes into play. This involves fitting together various die parts, which may include upper and lower die sections, guiding pins, and ejector systems.
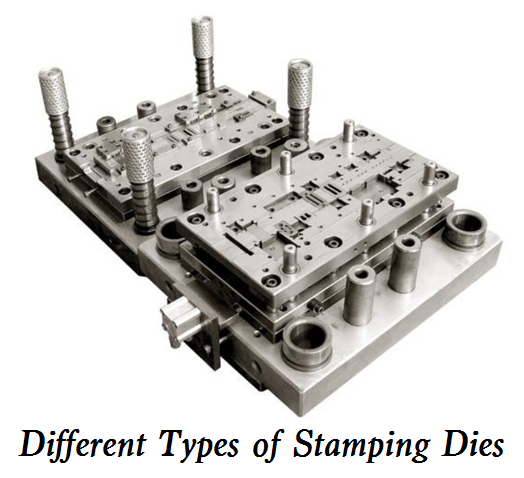
A stock image related to dies and stamping.
Assembly must be conducted with precision to ensure that all components align correctly, which affects the die’s ability to perform consistently. The use of CAD (Computer-Aided Design) software can help in designing the dies and ensuring that all parts fit together seamlessly. Regular maintenance and calibration of dies during assembly are essential for maintaining their longevity and performance.
Finishing: What Finishing Techniques Ensure Quality and Durability?
The final stage, finishing, focuses on enhancing the die’s surface characteristics and ensuring that it meets the required specifications. Techniques such as polishing, coating, and surface hardening may be employed to improve wear resistance and reduce friction during the stamping process.
For B2B buyers, understanding the finishing options available is important for selecting a supplier capable of delivering the desired quality and durability. Surface treatments can also affect the lifespan of both the dies and the stamped components, making this a crucial consideration in the procurement process.
What Quality Assurance Measures Are Commonly Implemented in Dies and Stamping?
Quality assurance (QA) is a critical component of the manufacturing process for dies and stamping, ensuring that products meet international standards and customer expectations.
What International Standards Should B2B Buyers Be Aware Of?
International standards such as ISO 9001 provide a framework for quality management systems. Compliance with these standards signifies that a supplier has implemented effective processes for ensuring product quality, continuous improvement, and customer satisfaction. Additionally, industry-specific standards like CE marking in Europe or API specifications in the oil and gas sector can further define quality benchmarks that suppliers must meet.
B2B buyers should prioritize suppliers who demonstrate adherence to these international standards, as this reduces risks associated with product quality and regulatory compliance.
What Are the Key QC Checkpoints During the Manufacturing Process?
Quality control is typically segmented into several checkpoints:
-
Incoming Quality Control (IQC): This is performed on raw materials before they enter the production process. Materials are inspected to ensure they meet specified requirements.
-
In-Process Quality Control (IPQC): During manufacturing, processes are monitored to catch any deviations from the specified parameters. This can include measuring dimensions, conducting visual inspections, and using advanced techniques like X-ray or magnetic particle testing.
-
Final Quality Control (FQC): Once the products are completed, they undergo a final inspection to ensure they meet all specifications. This may include functional testing, dimensional checks, and aesthetic evaluations.
By implementing these checkpoints, manufacturers can ensure that any defects are identified and rectified before products reach the customer.
How Can B2B Buyers Verify Supplier Quality Control Practices?
To ensure that suppliers maintain high-quality standards, B2B buyers should engage in thorough verification processes. This can include:
-
Supplier Audits: Conducting on-site audits allows buyers to review a supplier’s processes, equipment, and quality control measures firsthand. This transparency fosters trust and ensures that the supplier adheres to required standards.
-
Quality Reports: Requesting regular quality reports can provide insights into a supplier’s performance, including defect rates and corrective actions taken.
-
Third-Party Inspections: Engaging independent inspectors can provide an unbiased evaluation of a supplier’s quality control practices, ensuring compliance with specified standards.
What Are the QC and Certification Nuances for International B2B Buyers?
For international buyers, understanding the nuances of quality control and certification is essential. Regions such as Africa, South America, the Middle East, and Europe may have different regulatory requirements and standards.
-
Documentation: Ensure that suppliers provide all necessary documentation, including compliance certificates, test reports, and inspection records. This documentation is crucial for customs clearance and regulatory compliance.
-
Cultural Considerations: Different regions may have varying approaches to quality assurance. It’s important for buyers to understand these cultural differences to foster effective communication and collaboration.
-
Local Standards: In addition to international standards, be aware of local regulations that may impact product quality. For example, certain countries may require specific certifications for imported goods, which can affect procurement decisions.
By being informed about these aspects, B2B buyers can make more educated decisions when selecting suppliers for dies and stamping components, ensuring both quality and compliance with international standards.
Practical Sourcing Guide: A Step-by-Step Checklist for ‘dies and stamping’
To ensure a successful procurement process for dies and stamping, international B2B buyers must follow a structured approach. This checklist will guide you through the key steps necessary to source high-quality dies and stamping solutions that meet your operational needs.
Step 1: Define Your Technical Specifications
Before initiating the sourcing process, clearly outline your technical requirements. This includes the type of materials you’ll be working with, the dimensions of the parts you need, and the tolerances required for your applications. Understanding these specifications will help you communicate effectively with potential suppliers and ensure they can meet your needs.
- Material Types: Identify whether you will require tool steel, carbide, or other materials.
- Part Complexity: Define the complexity of the parts—will they require single-operation dies or more sophisticated progressive dies?
Step 2: Research and Identify Potential Suppliers
Conduct thorough research to compile a list of potential suppliers that specialize in dies and stamping. Look for companies with a solid reputation in the industry, particularly those with experience in your specific market region.
- Industry References: Seek recommendations from industry peers or consult industry-specific directories.
- Geographical Considerations: Consider suppliers from your target regions—Africa, South America, the Middle East, and Europe—to facilitate easier logistics.
Step 3: Evaluate Supplier Certifications and Capabilities
Before making any commitments, verify that potential suppliers possess the necessary certifications (e.g., ISO 9001). These certifications indicate a commitment to quality management and adherence to industry standards.
- Quality Assurance Processes: Inquire about their quality control measures and testing protocols.
- Production Capabilities: Assess their machinery and technology to ensure they can handle your required production volume and complexity.
Step 4: Request Prototypes and Samples
Ask suppliers for prototypes or samples of their work. This will allow you to evaluate the quality and precision of the dies and stamped parts they produce.
- Functional Testing: Use the samples in real-world applications to test their performance and durability.
- Design Validation: Ensure the samples meet your specifications and design requirements.
Step 5: Negotiate Pricing and Terms
Once you’ve narrowed down your list of suppliers, enter into negotiations regarding pricing, payment terms, and delivery timelines. Transparency in these discussions can lead to a beneficial partnership.
- Volume Discounts: Discuss the possibility of discounts for larger orders or long-term contracts.
- Payment Terms: Clarify payment schedules, especially for international transactions, to avoid misunderstandings.
Step 6: Assess After-Sales Support and Warranty
Inquire about the supplier’s after-sales support and warranty policies. A reliable supplier should offer robust support and service agreements to address any issues post-purchase.
- Technical Support: Confirm availability of technical assistance for installation and maintenance.
- Warranty Coverage: Understand the warranty terms for the dies and stamping equipment to mitigate risks.
Step 7: Finalize Contracts and Place Orders
Once you are satisfied with the supplier’s capabilities, pricing, and support, proceed to finalize contracts. Ensure that all terms are documented clearly to avoid future disputes.
- Contract Clauses: Include clauses for delivery timelines, quality standards, and penalties for non-compliance.
- Order Confirmation: Make sure to receive formal order confirmations to streamline the procurement process.
Following this practical sourcing guide will help international B2B buyers make informed decisions when procuring dies and stamping solutions, ensuring they align with their operational requirements and business goals.
Comprehensive Cost and Pricing Analysis for dies and stamping Sourcing
What Are the Key Cost Components in Dies and Stamping Sourcing?
When sourcing dies and stamping services, international B2B buyers must understand the various cost components that contribute to the overall pricing structure. The primary elements include:
-
Materials: The choice of materials significantly impacts costs. Common materials for dies include tool steel and carbide, with prices fluctuating based on market demand and availability. Specialty materials for high-precision applications may incur additional costs.
-
Labor: Skilled labor is required for both the manufacturing of dies and the stamping process. Labor costs can vary widely by region; for instance, labor in Europe might be costlier than in Africa or South America. Understanding local labor rates is crucial for accurate budgeting.
-
Manufacturing Overhead: This includes expenses related to the factory environment, equipment maintenance, utilities, and administrative costs. Overhead can represent a substantial portion of the total cost, making it essential to assess the supplier’s operational efficiency.
-
Tooling: The cost of tooling can vary depending on the complexity and lifespan of the dies. Custom dies tailored for specific applications will generally be more expensive than standard dies. Buyers should consider whether the tooling costs can be amortized over multiple projects.
-
Quality Control (QC): Ensuring that the stamped parts meet quality standards requires investment in QC processes. This may involve testing, inspection, and certifications that can add to the overall cost but are crucial for compliance and reliability.
-
Logistics: Shipping costs, including customs duties and transportation, should not be overlooked. Incoterms chosen can affect how logistics costs are handled and should align with the buyer’s capabilities.
-
Margin: Suppliers will typically include a profit margin in their pricing. Understanding the competitive landscape can help buyers negotiate better terms.
How Do Price Influencers Affect the Cost of Dies and Stamping?
Several factors can influence the pricing of dies and stamping services:
-
Volume/MOQ (Minimum Order Quantity): Larger orders often lead to lower per-unit costs due to economies of scale. Buyers should negotiate MOQs that align with their production needs to avoid excess inventory or increased costs.
-
Specifications and Customization: Custom designs and specifications can significantly raise costs. Buyers should provide clear and detailed requirements to minimize revisions and additional costs.
-
Materials Quality and Certifications: Higher quality materials and certifications (e.g., ISO standards) can increase costs but may be necessary for certain industries, such as automotive or aerospace. Buyers must weigh the benefits of higher-quality materials against their budget constraints.
-
Supplier Factors: The supplier’s reputation, location, and reliability can influence costs. Suppliers with a strong track record may charge a premium but can offer better service and reliability.
-
Incoterms: The choice of Incoterms can impact the total cost of ownership. Understanding which party bears responsibility for shipping and logistics can help in cost planning.
What Are the Best Negotiation Tips for International B2B Buyers?
When engaging in negotiations for dies and stamping, consider the following strategies:
-
Conduct Thorough Market Research: Understand the pricing landscape and identify multiple suppliers to create competitive tension in negotiations.
-
Focus on Total Cost of Ownership: Evaluate not only the initial price but also ongoing costs such as maintenance, logistics, and potential delays. A lower upfront cost may lead to higher long-term expenses.
-
Leverage Relationships: Building a strong relationship with suppliers can lead to better pricing and terms. Consider long-term partnerships rather than one-off transactions.
-
Be Transparent: Clearly communicate your needs and constraints. Suppliers often appreciate honesty and may be more willing to accommodate specific requests if they understand your business context.
-
Negotiate Terms Beyond Price: Focus on other aspects such as payment terms, lead times, and after-sales support, which can add significant value to the overall agreement.
Conclusion: Why Is Understanding the Cost Structure Critical for International Buyers?
Understanding the comprehensive cost and pricing analysis for dies and stamping sourcing is crucial for international buyers from Africa, South America, the Middle East, and Europe. With the right insights, buyers can make informed decisions, negotiate effectively, and ultimately achieve better value in their sourcing strategies. Always remember to seek indicative prices, as they can fluctuate based on market conditions and specific project requirements.
Alternatives Analysis: Comparing dies and stamping With Other Solutions
Introduction: Exploring Alternatives to Dies and Stamping
In the world of manufacturing, especially for international B2B buyers, choosing the right method for metal forming is crucial. While dies and stamping are widely recognized for their efficiency and precision, various alternative technologies can achieve similar outcomes. Understanding these alternatives allows businesses to make informed decisions based on their specific needs, budget, and operational capabilities.
Comparison Table of Metal Forming Technologies
Comparison Aspect | Dies and Stamping | Laser Cutting | 3D Metal Printing |
---|---|---|---|
Performance | High-speed production, precision cutting and forming | High precision and flexibility for complex shapes | Excellent for prototyping and low-volume production |
Cost | High initial setup cost, but low per-unit cost for large runs | Moderate to high cost, depending on complexity and material | High material and operational costs, suitable for low volume |
Ease of Implementation | Requires significant tooling and setup time | Easier to set up; software-driven | Requires skilled operators and post-processing |
Maintenance | Regular maintenance needed for dies | Lower maintenance; minimal wear on equipment | Maintenance-intensive with potential for material wastage |
Best Use Case | High-volume production of consistent parts | Complex geometries and custom parts | Prototyping and custom one-off parts |
Detailed Breakdown of Alternatives
How Does Laser Cutting Compare to Dies and Stamping?
Laser cutting technology utilizes a focused beam of light to cut materials with high precision. One of its significant advantages is its ability to produce complex shapes without the need for extensive tooling. This method is especially beneficial for projects requiring custom designs or varying geometries. However, while the initial setup may be simpler, the operational costs can increase, especially for high-volume production. For international buyers looking to create unique components or prototypes, laser cutting is a compelling alternative.
What Are the Advantages of 3D Metal Printing Over Traditional Methods?
3D metal printing, or additive manufacturing, is gaining traction for its ability to produce intricate designs that would be difficult or impossible to achieve with traditional methods. This technology allows for rapid prototyping and customization, making it ideal for industries needing unique parts in smaller quantities. However, the material costs and the time required for post-processing can be significant drawbacks. B2B buyers focused on innovation and customization may find 3D printing a suitable alternative, but it is essential to weigh the costs and production timelines against their operational needs.
Conclusion: How to Choose the Right Metal Forming Solution
Selecting the appropriate metal forming method depends on various factors, including production volume, complexity of design, budget, and lead times. For high-volume, consistent parts, dies and stamping remain a robust choice. However, for projects that demand flexibility and customization, alternatives like laser cutting and 3D metal printing offer compelling benefits. International B2B buyers should assess their specific requirements and long-term goals to determine the best solution that aligns with their operational strategies and market demands.
Essential Technical Properties and Trade Terminology for dies and stamping
What Are the Key Technical Properties of Dies and Stamping?
Understanding the technical properties of dies and stamping is crucial for international B2B buyers, especially when evaluating suppliers and ensuring product quality. Here are some essential specifications that buyers should consider:
1. Material Grade
The choice of material for dies is vital as it affects durability and performance. Common materials include tool steel and carbide. Tool steel offers a balance of toughness and wear resistance, while carbide provides superior hardness, making it suitable for high-volume production. Selecting the appropriate material can lead to longer die life and reduced production costs.
2. Tolerance
Tolerance refers to the allowable variation in dimensions of the stamped part. Tight tolerances are critical in applications requiring precision, such as automotive and aerospace components. Buyers should specify tolerances based on their application’s needs, as tighter tolerances can increase manufacturing costs but are essential for ensuring product fit and function.
3. Cutting Clearance
Cutting clearance is the gap between the cutting edges of the die. This specification influences the quality of the cut edge and the amount of force required during stamping. A common practice is to set the cutting clearance to about 10% of the material thickness. Understanding this concept helps buyers optimize production efficiency and minimize scrap.
4. Cycle Time
Cycle time refers to the duration it takes to complete one stamping operation. It can vary based on the complexity of the die and the material being processed. Shorter cycle times lead to increased productivity, making it a key consideration for buyers focused on maximizing output.
5. Die Life
Die life indicates how long a die can be used before it requires maintenance or replacement. It is influenced by factors such as material choice, design, and operating conditions. Buyers should inquire about expected die life when negotiating contracts, as it impacts long-term production costs.
6. Heat Treatment
Heat treatment processes, such as quenching and tempering, are used to enhance the properties of die materials. Proper heat treatment can increase hardness and toughness, which are essential for maintaining die integrity during high-stress operations. Buyers should verify that suppliers adhere to industry standards for heat treatment.
What Are the Common Trade Terms in the Dies and Stamping Industry?
Familiarizing yourself with industry jargon is essential for effective communication and negotiation in the dies and stamping sector. Here are some commonly used terms:
1. OEM (Original Equipment Manufacturer)
OEMs are companies that produce components that are used in another company’s products. Understanding the role of OEMs is crucial for buyers looking to source specific parts or components for their manufacturing processes.
2. MOQ (Minimum Order Quantity)
MOQ refers to the smallest quantity of a product that a supplier is willing to sell. Knowing the MOQ helps buyers manage inventory and production schedules effectively. It is particularly relevant when sourcing dies and stamping services, where production runs can vary significantly.
3. RFQ (Request for Quotation)
An RFQ is a document that buyers send to suppliers to request pricing and terms for a specific product or service. Submitting a well-structured RFQ can lead to better pricing and improved supplier relationships.
4. Incoterms (International Commercial Terms)
Incoterms are a set of international rules that define the responsibilities of buyers and sellers regarding the delivery of goods. Familiarity with Incoterms helps buyers understand shipping costs, risks, and obligations, particularly in cross-border transactions.
5. Lead Time
Lead time is the time it takes from placing an order to receiving the product. In the dies and stamping industry, lead time can be influenced by factors such as material availability and production schedules. Buyers should account for lead time in their planning to avoid production delays.
6. Tolerance Specification
This term refers to the specific limits set for acceptable variations in dimensions. It is essential for ensuring that the final product meets required specifications and functions correctly within its intended application.
By understanding these technical properties and trade terms, international B2B buyers can make informed decisions and foster successful partnerships in the dies and stamping industry.
Navigating Market Dynamics and Sourcing Trends in the dies and stamping Sector
What Are the Current Market Dynamics and Key Trends in the Dies and Stamping Sector?
The dies and stamping sector is experiencing significant transformation driven by globalization, technological advancements, and evolving customer demands. International B2B buyers, particularly from Africa, South America, the Middle East, and Europe, are noticing a shift towards automation and digitalization. Advanced technologies such as Industry 4.0, artificial intelligence, and IoT (Internet of Things) are enhancing the efficiency of stamping processes, reducing production costs, and improving product quality. For instance, predictive maintenance powered by IoT can minimize downtime and extend the lifespan of stamping dies, a critical investment for manufacturers.
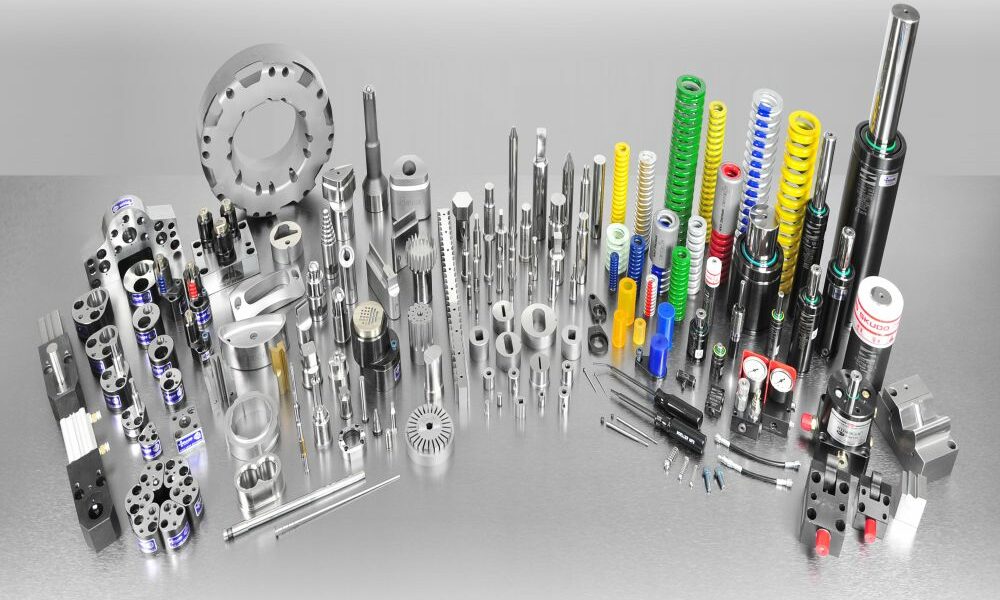
A stock image related to dies and stamping.
Another key trend is the increasing demand for customized solutions. Buyers are seeking suppliers that can offer tailored designs and quick turnaround times, which are essential in today’s fast-paced market. The rise of contract manufacturing is also noteworthy, as it allows companies to leverage specialized expertise while focusing on their core competencies. This model is particularly attractive for firms in emerging markets looking to compete on a global scale without the heavy burden of capital investment.
Moreover, sustainability is becoming an integral part of sourcing strategies. B2B buyers are prioritizing suppliers who demonstrate a commitment to environmental stewardship, which includes minimizing waste and using eco-friendly materials. As such, understanding local regulations and international standards is crucial for navigating the complexities of the global supply chain.
How Does Sustainability and Ethical Sourcing Impact the Dies and Stamping Sector?
Sustainability and ethical sourcing are no longer just buzzwords but essential components of modern business strategy in the dies and stamping sector. The environmental impact of manufacturing processes, including energy consumption and waste generation, is under scrutiny. B2B buyers are increasingly aware that their sourcing choices can either contribute to or mitigate environmental degradation. Suppliers that adopt ‘green’ practices, such as recycling scrap metal and using energy-efficient machinery, can gain a competitive advantage.
Ethical supply chains are equally important, especially in regions where labor practices may be questionable. Buyers are encouraged to partner with manufacturers that uphold fair labor practices and have transparent sourcing policies. Certifications like ISO 14001 for environmental management and ISO 9001 for quality management can serve as indicators of a supplier’s commitment to sustainability and ethical practices.
Furthermore, the use of sustainable materials is gaining traction. For example, sourcing dies and components made from recycled metals not only reduces the carbon footprint but also appeals to environmentally conscious consumers. By prioritizing suppliers who align with these values, B2B buyers can enhance their brand reputation and appeal to a growing demographic that values sustainability.
What Is the Historical Context of the Dies and Stamping Industry and Its Relevance Today?
The dies and stamping industry has evolved significantly since its inception during the industrial revolution. Initially focused on simple tasks, the sector has transformed into a sophisticated field that employs advanced technologies and methodologies. The introduction of cold-forming processes allowed for the mass production of intricate metal components, which has become a staple in various industries, including automotive, aerospace, and electronics.
Over the decades, the focus has shifted from merely fulfilling production quotas to enhancing quality, efficiency, and sustainability. Today’s buyers need to understand this historical context as it informs the current landscape of supplier capabilities and market expectations. The legacy of innovation in dies and stamping serves as a foundation for future advancements, particularly in automation and eco-friendly practices, making it crucial for international B2B buyers to stay informed and adaptable in their sourcing strategies.
Frequently Asked Questions (FAQs) for B2B Buyers of dies and stamping
-
How do I choose the right die for my stamping needs?
Choosing the right die depends on various factors including the type of metal, thickness, and the complexity of the part you want to produce. Start by defining the specifications of your project, such as the required tolerances and production volume. Consult with potential suppliers about their capabilities and experience with similar projects. It’s also beneficial to discuss material options—like tool steel or carbide—and their implications on durability and cost. Always request samples or prototypes to assess the quality before making a final decision. -
What is the best type of stamping die for high-volume production?
For high-volume production, progressive dies are often the best choice. These dies are designed to perform multiple operations in a single cycle, allowing for efficient and consistent output. They can automate processes, reducing labor costs and minimizing errors. However, the initial investment is higher due to the complexity of the tooling. It’s crucial to analyze your production needs and work with suppliers who have experience in high-volume stamping to ensure reliability and quality. -
What are the common payment terms for international die and stamping suppliers?
Payment terms can vary widely among suppliers, but common practices include upfront deposits ranging from 30% to 50% of the total order value, with the balance due upon delivery or after inspection. Some suppliers may offer net 30 or net 60 terms depending on the buyer’s creditworthiness and relationship history. For international transactions, consider using letters of credit to secure the payment process. Always clarify payment terms before finalizing contracts to avoid misunderstandings. -
How can I ensure the quality of dies and stamped parts from international suppliers?
To ensure quality, start by vetting potential suppliers through their certifications (like ISO 9001) and production capabilities. Request samples and conduct thorough inspections upon arrival. Implement quality assurance processes, including dimensional checks and performance testing, to verify compliance with your specifications. Building a solid relationship with your supplier can also facilitate better communication regarding quality standards and expectations. -
What are the minimum order quantities (MOQs) for dies and stamping components?
MOQs can vary significantly depending on the supplier and the complexity of the die. For standard dies, MOQs may be lower, often starting at a few units, while custom dies may require larger orders to justify production costs. Discuss your specific needs with potential suppliers to find flexible options. Some may be willing to accommodate smaller orders, especially if you establish a long-term partnership. -
What logistics considerations should I keep in mind when sourcing dies internationally?
Logistics play a critical role in the timely delivery of dies and stamped parts. Consider factors such as shipping methods, customs clearance, and potential tariffs when calculating the total cost. Work with suppliers who have experience in international shipping and can provide accurate delivery timelines. Additionally, ensure that packaging is robust enough to prevent damage during transit, and consider insurance options for high-value shipments.
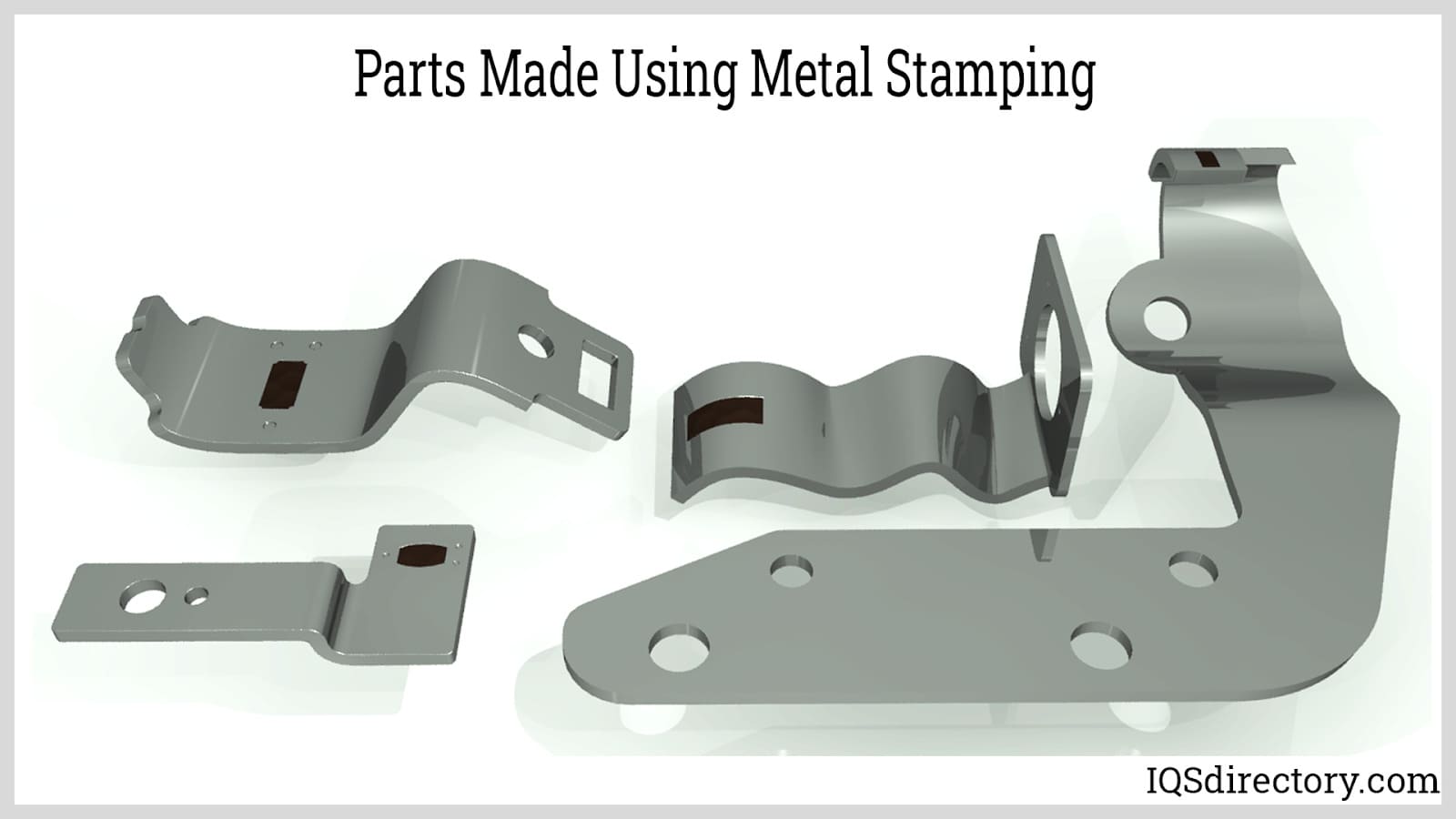
A stock image related to dies and stamping.
-
How do I manage supplier relationships for ongoing die and stamping projects?
Effective supplier relationship management involves regular communication, transparency, and feedback. Schedule regular check-ins to discuss production updates, quality issues, or upcoming projects. Building a collaborative partnership can lead to better pricing, prioritized service, and enhanced innovation. Additionally, consider sharing forecasts and production schedules to help suppliers plan their resources efficiently. -
What are the benefits of customization in die and stamping processes?
Customization in die and stamping processes allows for tailored solutions that meet specific project requirements, enhancing product performance and functionality. Custom dies can optimize material usage and reduce waste, ultimately lowering costs. They can also enable the production of unique parts that differentiate your products in the market. Engaging in early discussions with suppliers about your customization needs can lead to innovative solutions and improved efficiency in production.
Important Disclaimer & Terms of Use
⚠️ Important Disclaimer
The information provided in this guide, including content regarding manufacturers, technical specifications, and market analysis, is for informational and educational purposes only. It does not constitute professional procurement advice, financial advice, or legal advice.
While we have made every effort to ensure the accuracy and timeliness of the information, we are not responsible for any errors, omissions, or outdated information. Market conditions, company details, and technical standards are subject to change.
B2B buyers must conduct their own independent and thorough due diligence before making any purchasing decisions. This includes contacting suppliers directly, verifying certifications, requesting samples, and seeking professional consultation. The risk of relying on any information in this guide is borne solely by the reader.
Strategic Sourcing Conclusion and Outlook for dies and stamping
The strategic sourcing of dies and stamping solutions is essential for international B2B buyers aiming to enhance operational efficiency and cost-effectiveness. As outlined in this guide, understanding the nuances of stamping dies—such as their various types, applications, and the materials used—empowers buyers to make informed decisions. Leveraging these insights can lead to optimized procurement processes and stronger supplier partnerships, ultimately driving innovation within manufacturing sectors.
How Can Strategic Sourcing Enhance Competitive Advantage?
By implementing a strategic sourcing approach, buyers can tap into a global network of suppliers, ensuring access to cutting-edge technologies and high-quality materials. This not only helps in reducing costs but also enhances product quality and accelerates time-to-market. International buyers, especially from Africa, South America, the Middle East, and Europe, should prioritize establishing relationships with reliable suppliers who can provide tailored solutions that meet specific market demands.
What’s Next for International B2B Buyers in Dies and Stamping?
Looking ahead, the demand for precision-engineered components will continue to rise. Buyers are encouraged to stay abreast of emerging trends, such as automation in stamping processes and sustainability in sourcing materials. Engaging with industry experts and participating in relevant forums can provide additional insights. Embrace the opportunity to refine your sourcing strategies today and position your business for future success in the dynamic landscape of dies and stamping.