Master G Codes: The Ultimate Guide to CNC Programming (2025)
Introduction: Navigating the Global Market for g codes
Navigating the intricacies of sourcing G Codes for CNC machines can be a formidable challenge for international B2B buyers, especially in emerging markets across Africa, South America, the Middle East, and Europe. Understanding the diverse applications and types of G Codes is essential for optimizing machining processes, enhancing productivity, and minimizing operational costs. This comprehensive guide delves into the various G Codes, detailing their functions, applications, and the nuances that differentiate them among different CNC machines.
From G00 for rapid positioning to G90 and G91 for absolute and incremental positioning, each code plays a pivotal role in the precision and efficiency of manufacturing processes. Additionally, the guide offers actionable insights on supplier vetting, cost considerations, and best practices for implementation. By equipping B2B buyers with the knowledge needed to make informed purchasing decisions, this resource empowers businesses to enhance their competitive edge in the global market.
Whether you are a buyer looking to streamline your production line in South America or seeking reliable suppliers in Europe, this guide addresses the key challenges faced in sourcing G Codes. By understanding these critical components, businesses can ensure that they leverage the full potential of CNC technology, driving growth and innovation in their respective industries.
Understanding g codes Types and Variations
Type Name | Key Distinguishing Features | Primary B2B Applications | Brief Pros & Cons for Buyers |
---|---|---|---|
G00 – Rapid Positioning | Enables quick movement without cutting; non-contact mode. | Tool changes, setup procedures. | Pros: Increases efficiency; reduces idle time. Cons: Risk of collisions if not careful. |
G01 – Linear Interpolation | Straight-line cutting at a specified feed rate. | Precision machining, contour cutting. | Pros: High accuracy; versatile for various materials. Cons: Slower than rapid positioning. |
G02/G03 – Circular Interpolation | Creates arcs and circular paths; clockwise (G02) and counterclockwise (G03). | Complex shapes, molds, and fixtures. | Pros: Essential for intricate designs; reduces tool wear. Cons: More complex programming required. |
G04 – Dwell | Introduces pauses in the cutting process for specific durations. | Finishing operations, drilling cycles. | Pros: Enhances surface finish; controls heat. Cons: Increases cycle time. |
G20/G21 – Measurement Systems | Defines measurement units (Imperial or Metric). | All CNC operations requiring measurements. | Pros: Flexibility in unit selection; reduces errors. Cons: May require additional programming checks. |
What Are the Characteristics of G00 – Rapid Positioning?
G00 is a fundamental G code that allows CNC machines to move quickly to a specified position without engaging the cutting tool. This rapid positioning is crucial during tool changes or when repositioning the machine for a new operation. B2B buyers should consider the operational speed and safety features of their CNC machines, as rapid movements can lead to collisions if not carefully managed. Investing in machines with advanced sensors and collision detection can mitigate risks associated with this command.
How Does G01 – Linear Interpolation Benefit B2B Operations?
G01 is utilized for linear cutting at a defined feed rate, making it essential for precision machining tasks. This command allows for controlled material removal, which is vital for achieving high-quality finishes and accurate dimensions. When selecting CNC equipment, businesses should evaluate the machine’s ability to handle various feed rates and materials, ensuring flexibility in their production processes. The ability to program and adjust feed rates can significantly enhance efficiency in manufacturing operations.
Why Are G02/G03 – Circular Interpolation Codes Important?
G02 and G03 are critical for creating arcs and circular paths, essential in producing complex shapes and designs. These codes facilitate smoother transitions and reduce tool wear by allowing the cutter to move in a controlled arc. B2B buyers in industries such as mold making or automotive parts manufacturing should prioritize machines that support these commands, as they enhance design capabilities and improve product quality. However, the complexity of programming these codes may require additional training for operators.
What Role Does G04 – Dwell Play in Machining Processes?
The G04 command introduces a dwell time, pausing the cutter for a specified duration. This feature is particularly beneficial in operations where a longer cutting time improves surface finishes, such as drilling or milling. For B2B buyers, understanding the implications of dwell time on cycle times and overall productivity is crucial. While it can enhance finish quality, companies must balance dwell times with production efficiency to maintain competitiveness.
How Do G20/G21 – Measurement Systems Impact CNC Operations?
G20 and G21 define measurement units (Imperial or Metric) in CNC programming, allowing flexibility in operations across different regions and industries. This adaptability is particularly important for international B2B buyers who may deal with various standards. Buyers should ensure that their CNC machines can easily switch between measurement systems to prevent errors during production. Regular checks and programming protocols can help maintain accuracy and efficiency in machining operations.
Key Industrial Applications of g codes
Industry/Sector | Specific Application of g codes | Value/Benefit for the Business | Key Sourcing Considerations for this Application |
---|---|---|---|
Aerospace | Precision machining of aircraft components | High accuracy and reliability in critical parts | Certification standards, supplier reliability, and technical support |
Automotive | CNC milling for engine parts | Enhanced production efficiency and reduced waste | Availability of advanced CNC machines and training for operators |
Medical Devices | Manufacturing surgical instruments | Compliance with stringent health regulations | Quality control measures, material sourcing, and regulatory compliance |
Electronics | PCB manufacturing and assembly | Improved precision and reduced production costs | Supplier certifications, technology updates, and scalability options |
Tool and Die Manufacturing | Custom tool creation using CNC lathes and mills | Customization and flexibility in production | Access to quality materials, machine capabilities, and design support |
How Are G Codes Used in Aerospace Manufacturing?
In the aerospace sector, g codes are vital for the precision machining of aircraft components such as turbine blades and structural elements. The use of G00 for rapid positioning and G01 for linear interpolation ensures that these parts are manufactured with high accuracy and reliability, which is critical for safety. International B2B buyers must ensure that suppliers meet certification standards like AS9100, maintain a robust quality management system, and provide ongoing technical support.
What Role Do G Codes Play in Automotive Production?
In the automotive industry, g codes facilitate CNC milling processes for engine parts and other critical components. By employing G01 for controlled feed rates and G02/G03 for circular interpolation, manufacturers can achieve enhanced production efficiency while minimizing material waste. Buyers should consider the availability of advanced CNC technology and the need for operator training to maximize productivity and maintain quality standards.
How Are G Codes Applied in Medical Device Manufacturing?
For medical device manufacturing, g codes are used in the production of surgical instruments and implants, where compliance with health regulations is paramount. G codes allow for precise machining and repeatability, essential for meeting stringent quality requirements. Buyers in this sector should focus on suppliers with robust quality control measures, reliable material sourcing, and an understanding of regulatory compliance in different regions.
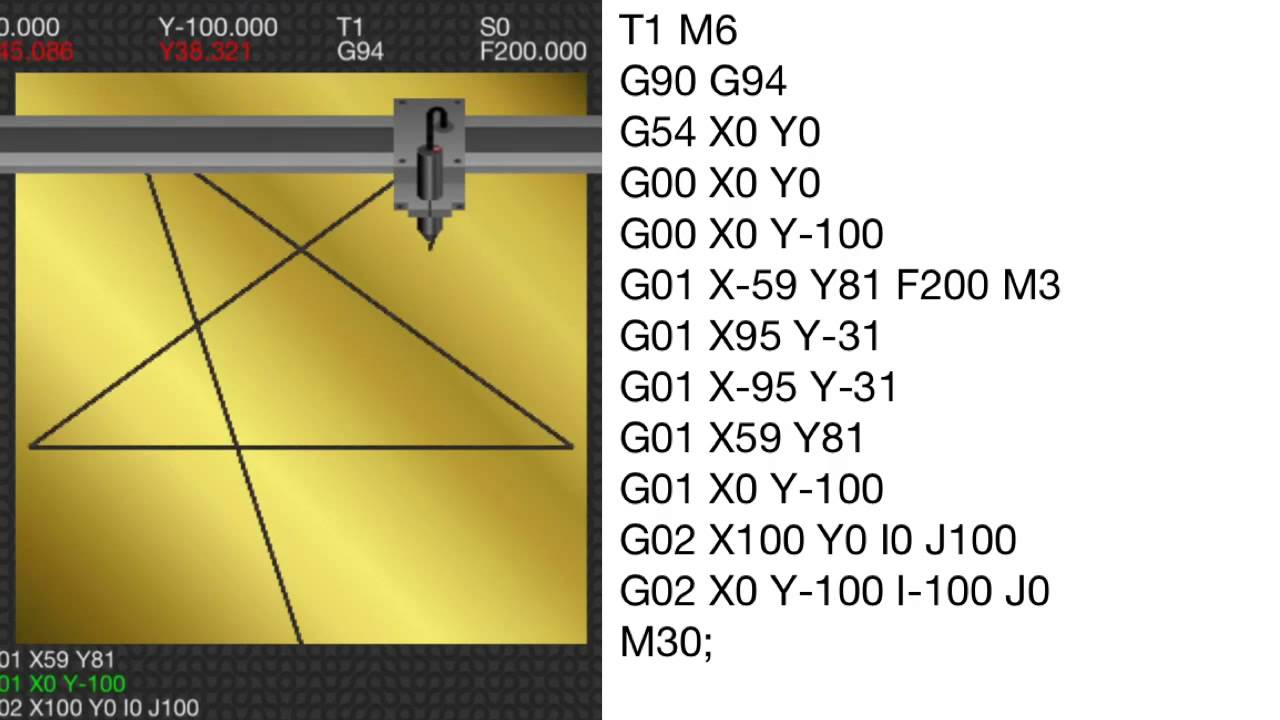
A stock image related to g codes.
How Do G Codes Enhance Electronics Production?
In the electronics sector, g codes are crucial for the manufacturing and assembly of printed circuit boards (PCBs). Utilizing G01 for precise movements and G04 for dwell times during drilling processes allows for improved precision and reduced production costs. B2B buyers should prioritize suppliers that possess the latest technology, maintain certifications, and offer scalability options to meet evolving demands.
Why Are G Codes Important in Tool and Die Manufacturing?
In tool and die manufacturing, g codes enable the custom creation of tools using CNC lathes and mills. This flexibility allows businesses to adapt quickly to market needs and produce highly specialized tools. Buyers should consider access to quality materials, the capabilities of CNC machines, and the availability of design support from suppliers to ensure optimal production outcomes.
3 Common User Pain Points for ‘g codes’ & Their Solutions
Scenario 1: Confusion Over G-Code Variations Across CNC Machines
The Problem:
B2B buyers often face significant challenges when dealing with variations in G-codes across different CNC machine brands. Each manufacturer may implement G-codes differently or even create proprietary codes, leading to confusion during programming and operation. For instance, a buyer in South America may invest in a CNC machine from Europe, only to discover that the standard G-codes they are accustomed to are not compatible. This inconsistency can result in costly errors, increased downtime, and the need for additional training for operators unfamiliar with the new machine’s G-code syntax.
The Solution:
To mitigate this issue, B2B buyers should prioritize thorough research on the specific G-code implementations of the machines they are considering. It’s advisable to consult machine documentation and manufacturers directly to clarify any ambiguities regarding G-code compatibility. Additionally, investing in comprehensive training programs that cover the specific G-codes for the chosen machine is essential. Online courses or workshops that focus on the specific machine’s G-code usage can bridge knowledge gaps. Furthermore, joining industry forums and user groups can provide insights from other users who have navigated similar challenges, allowing buyers to make informed decisions and reduce the learning curve.
Scenario 2: Inadequate Understanding of G-Code Programming Syntax
The Problem:
Many international B2B buyers encounter difficulties due to a lack of understanding of G-code programming syntax. This often leads to errors in programming, such as incorrect commands or misconfigured parameters, which can result in defective parts and machine crashes. Buyers from regions like Africa may find it particularly challenging to source quality training materials or support, which exacerbates the issue. These challenges can lead to wasted materials and increased production costs, impacting overall profitability.
The Solution:
To address this pain point, it is crucial for buyers to invest in high-quality training resources that focus on G-code syntax and programming best practices. This includes accessing online tutorials, webinars, and software simulations that provide hands-on experience with G-code commands. Manufacturers can also assist by offering tailored training sessions for their equipment. Additionally, implementing a mentorship program where experienced operators can guide less experienced staff can enhance understanding. Regularly reviewing and practicing G-code programming in a controlled environment will help solidify the knowledge and skills needed to minimize errors in real-world applications.
Scenario 3: Difficulty in Adapting to Different Measurement Systems
The Problem:
B2B buyers frequently struggle with adapting to different measurement systems (imperial vs. metric) when programming CNC machines using G-codes. For example, a buyer from Europe may purchase equipment from a supplier in the Middle East that predominantly uses imperial measurements. This inconsistency can lead to confusion and mistakes in programming, resulting in parts that are out of specification or unusable. Such errors can delay production schedules and increase costs, particularly if adjustments require reworking or scrapping materials.
The Solution:
To overcome this challenge, B2B buyers should ensure that they clearly define the measurement system at the beginning of any programming task. Implementing G20 or G21 codes at the start of each program can help standardize measurements. Additionally, buyers should familiarize themselves with conversion factors between imperial and metric systems to ensure accurate programming. Creating a reference guide that includes common conversions can be a practical tool for operators. Investing in CNC software that allows for easy switching between measurement systems can also streamline the programming process and reduce the likelihood of errors. Regular training sessions that reinforce the importance of measurement accuracy and provide hands-on experience with both systems will further enhance proficiency and confidence among operators.
Strategic Material Selection Guide for g codes
What Are the Key Properties of Common Materials for G Codes?
When selecting materials for G codes in CNC machining, it is essential to consider their properties that directly affect product performance. The most commonly used materials include aluminum, steel, titanium, and plastics. Each material presents unique advantages and challenges that can influence the machining process and the final application.
How Does Aluminum Perform in CNC Machining with G Codes?
Aluminum is widely recognized for its excellent machinability and lightweight properties. It typically has a temperature rating of around 300°F (150°C) and exhibits good corrosion resistance, making it ideal for outdoor and marine applications.
Pros: Aluminum is relatively inexpensive and easy to machine, allowing for faster production times. Its lightweight nature also makes it suitable for applications requiring reduced weight without sacrificing strength.
Cons: While durable, aluminum can be less robust than other metals like steel, which may limit its use in high-stress applications. Additionally, it can be prone to scratching and denting.
Impact on Application: Aluminum is compatible with various media, including air and water, but may not be suitable for harsh chemicals. International B2B buyers should consider compliance with standards such as ASTM B221 for aluminum extrusions.
What Are the Benefits of Using Steel in G Code Applications?
Steel is a versatile material known for its strength and durability. It can withstand high temperatures and pressures, making it suitable for demanding applications. Steel’s corrosion resistance varies based on the alloy used, with stainless steel offering superior protection.
Pros: Steel’s high tensile strength makes it ideal for structural components. It is also widely available and can be sourced globally, which is advantageous for international buyers.
Cons: Steel can be more challenging to machine compared to aluminum, leading to longer production times and higher tooling costs. It is also heavier, which may not be suitable for all applications.
Impact on Application: Steel is compatible with various media, including oils and gases. Buyers from regions like Africa and South America should ensure compliance with standards such as ASTM A36 for carbon steel.
Why Choose Titanium for G Code Machining?
Titanium is renowned for its high strength-to-weight ratio and exceptional corrosion resistance, making it a preferred choice in aerospace and medical applications. It can withstand temperatures exceeding 1,600°F (870°C) without losing structural integrity.
Pros: Titanium’s strength and lightweight characteristics make it ideal for high-performance applications. Its resistance to corrosion ensures longevity in harsh environments.
Cons: The primary drawback of titanium is its high cost and the complexity involved in machining. It requires specialized tools and processes, which can increase overall production costs.
Impact on Application: Titanium is compatible with various media, including seawater and chemicals, making it suitable for diverse applications. International buyers should be aware of standards like ASTM F136 for titanium alloys.
How Do Plastics Compare in G Code Applications?
Plastics, such as polycarbonate and nylon, are increasingly used in CNC machining due to their lightweight and versatile properties. They can withstand moderate temperatures and provide good chemical resistance.
Pros: Plastics are generally less expensive and easier to machine than metals, allowing for rapid production. They also offer excellent insulation properties and can be used in electrical applications.
Cons: Plastics may not provide the same level of strength and durability as metals, which can limit their application in high-stress environments. They can also be sensitive to temperature changes.
Impact on Application: Plastics are compatible with various media, including water and chemicals, but may not withstand high temperatures. Buyers should consider compliance with standards such as ASTM D638 for tensile properties of plastics.
Summary Table of Material Selection for G Codes
Material | Typical Use Case for g codes | Key Advantage | Key Disadvantage/Limitation | Relative Cost (Low/Med/High) |
---|---|---|---|---|
Aluminum | Aerospace components | Lightweight and easy to machine | Less robust than steel | Low |
Steel | Structural components | High strength and durability | Difficult to machine | Medium |
Titanium | Aerospace and medical parts | Exceptional strength and corrosion resistance | High cost and machining complexity | High |
Plastics | Electrical enclosures | Cost-effective and versatile | Limited strength compared to metals | Low |
This strategic material selection guide provides essential insights for international B2B buyers, helping them make informed decisions when selecting materials for G codes in CNC machining.
In-depth Look: Manufacturing Processes and Quality Assurance for g codes
What Are the Key Stages in Manufacturing G Codes for CNC Machining?
Manufacturing G codes for CNC machines involves several critical stages that ensure precision and quality in the final product. Understanding these stages is essential for B2B buyers, especially in regions like Africa, South America, the Middle East, and Europe, where specific manufacturing standards may vary.
Material Preparation: How Do You Ensure Quality from the Start?
The first stage in the manufacturing process is material preparation. This involves selecting high-quality raw materials that meet industry specifications. For instance, using premium metals such as aluminum or steel can significantly affect the end product’s durability and performance.
Prior to machining, the materials are often cleaned and prepped to eliminate any contaminants that might interfere with the machining process. Buyers should inquire about the supplier’s material sourcing practices and whether they adhere to international standards, such as ASTM or ISO certifications.
Forming: What Techniques Are Used to Achieve Precision?
The forming stage employs various machining techniques to shape the materials into the desired components. Key techniques include:
- CNC Milling and Turning: Utilizing G codes like G00 for rapid positioning and G01 for controlled feed rates allows for precise cuts and shapes.
- Drilling and Tapping: Specific G codes facilitate operations such as drilling holes or threading, essential for assembly.
- 3D Printing: In some instances, G codes are adapted for additive manufacturing, which is gaining traction in producing complex geometries.
During this stage, it is crucial to maintain a controlled environment to prevent material deformation. B2B buyers should ensure that suppliers utilize CNC machines calibrated to industry standards, which can be verified through certification documents.
Assembly: How Do Suppliers Ensure Component Compatibility?
Once the components are formed, the assembly stage begins. This involves bringing together various machined parts to create the final product. It is essential that the components fit together seamlessly, which is where quality assurance measures come into play.
Buyers should inquire about the assembly processes employed by suppliers. Are they using standardized assembly protocols? Are the workers trained in specific assembly techniques that minimize errors? Ensuring that suppliers follow best practices in assembly can greatly enhance the reliability of the final product.
Finishing: What Are the Common Techniques for Surface Treatment?
The finishing stage is critical for enhancing the aesthetics and functionality of the machined parts. Techniques such as anodizing, painting, or polishing may be employed to achieve the desired surface finish.
Buyers should ask suppliers about their finishing processes and whether they meet international quality standards. For instance, does the finishing process comply with ISO 9001 requirements? This can ensure that the final product not only looks good but also performs well under operational stresses.
What Quality Assurance Measures Should B2B Buyers Expect?
Quality assurance (QA) is a pivotal aspect of the manufacturing process for G codes. B2B buyers must understand the quality control measures in place to ensure that products meet their specifications.
Which International Standards Should Be Considered?
International standards, such as ISO 9001, are crucial for maintaining consistent quality in manufacturing processes. Additionally, industry-specific standards, such as CE marking for European markets or API specifications for oil and gas, are essential for compliance.
It is advisable for buyers to verify whether suppliers are certified to these standards, which can often be confirmed through documentation. Understanding the regulatory environment in the supplier’s country can also help buyers navigate compliance issues.
What Are the Key Quality Control Checkpoints?
Quality control checkpoints are vital to catch defects early in the manufacturing process. Common checkpoints include:
- Incoming Quality Control (IQC): Ensures that raw materials meet specified standards before production begins.
- In-Process Quality Control (IPQC): Involves monitoring the manufacturing process to catch any deviations in real-time.
- Final Quality Control (FQC): Conducted on finished products to verify that they meet the required specifications.
Buyers should ask suppliers about their QA processes and how they track and report quality metrics.
How Can Buyers Verify Supplier Quality Control?
To ensure that suppliers maintain high-quality standards, B2B buyers can take several proactive steps:
- Supplier Audits: Conducting regular audits of the supplier’s facilities can provide insights into their manufacturing practices and quality control measures.
- Quality Reports: Requesting detailed quality reports can help buyers understand the frequency of defects and how they are addressed.
- Third-Party Inspections: Engaging independent inspectors can provide an unbiased assessment of the supplier’s quality assurance processes.
These measures can help mitigate risks associated with poor-quality products and ensure that buyers receive components that meet their operational needs.
What Are the Unique Challenges for International Buyers?
International buyers, especially from diverse regions such as Africa, South America, and the Middle East, face unique challenges when sourcing G codes and related components. These challenges can include varying regulatory standards, logistical issues, and the need for clear communication with suppliers.
Understanding the local market dynamics and regulatory requirements can help buyers navigate these challenges effectively. Establishing strong relationships with suppliers and leveraging technology for communication can also enhance collaboration and ensure smoother transactions.
In conclusion, a comprehensive understanding of the manufacturing processes and quality assurance measures for G codes is essential for B2B buyers. By focusing on these aspects, buyers can make informed decisions and ensure the acquisition of high-quality components that meet their operational demands.
Practical Sourcing Guide: A Step-by-Step Checklist for ‘g codes’
In the dynamic world of CNC machining, understanding and sourcing G codes is essential for optimizing production processes. This guide provides a step-by-step checklist for international B2B buyers, particularly those from Africa, South America, the Middle East, and Europe, to effectively procure G codes tailored to their operational needs.
Step 1: Define Your Technical Specifications
Clearly outlining your technical requirements is the first step in the sourcing process. Consider the types of CNC machines you use (e.g., lathes, mills, routers) and the specific operations they perform. This clarity will help suppliers provide the appropriate G codes that align with your machinery and production needs.
- Machine Compatibility: Ensure the G codes you require are compatible with the models you operate.
- Application Needs: Identify the specific tasks (e.g., drilling, milling) that the G codes will facilitate.
Step 2: Research Potential Suppliers
Conduct thorough research to identify suppliers with a strong reputation in G code provision. Utilize online platforms, industry forums, and trade shows to gather a list of potential vendors.
- Industry Experience: Look for suppliers that have experience in your industry to ensure they understand your unique requirements.
- Geographical Focus: Consider suppliers that operate within your region to facilitate smoother communication and logistics.
Step 3: Evaluate Supplier Credentials
Before making a commitment, vet potential suppliers to confirm their reliability and quality. Request documentation such as certifications and quality assurance protocols.
- Certifications: Check for ISO or other relevant certifications that demonstrate compliance with international standards.
- Client References: Ask for case studies or testimonials from other B2B buyers who have sourced G codes from them.
Step 4: Request Samples and Demonstrations
Once you narrow down your supplier options, request samples or demonstrations of the G codes they offer. This step will help you assess the quality and usability of their products.
- Trial Period: If possible, arrange a trial period where you can test the G codes in your CNC machines.
- Feedback Mechanism: Ensure there’s a process for providing feedback to the supplier based on your testing experience.
Step 5: Negotiate Terms and Conditions
Negotiation is a crucial part of the sourcing process. Discuss pricing, delivery timelines, and payment terms to ensure they align with your budget and operational needs.
- Volume Discounts: Inquire about bulk purchasing options or discounts for larger orders.
- Delivery Commitments: Establish clear delivery timelines to avoid production delays.
Step 6: Establish a Quality Control Process
Implement a quality control system to monitor the performance of the G codes you procure. This will help you identify any issues early and maintain production efficiency.
- Performance Tracking: Regularly assess how well the G codes meet your operational requirements.
- Supplier Communication: Maintain open lines of communication with your supplier for ongoing support and troubleshooting.
Step 7: Stay Updated on Industry Trends
The CNC machining industry is continuously evolving. Stay informed about new G codes and technological advancements that could enhance your production processes.
- Continuous Learning: Engage in industry seminars, webinars, and publications to keep abreast of changes.
- Adaptation Strategies: Be prepared to adapt your sourcing strategy based on new developments and innovations in G code technology.
By following these steps, B2B buyers can effectively source G codes that meet their technical requirements while fostering reliable supplier relationships. This proactive approach will contribute to improved operational efficiency and productivity in the competitive landscape of CNC machining.
Comprehensive Cost and Pricing Analysis for g codes Sourcing
What Are the Key Cost Components in G Codes Sourcing?
Understanding the cost structure involved in sourcing G codes is essential for international B2B buyers, particularly in regions like Africa, South America, the Middle East, and Europe. The primary cost components include:
-
Materials: The choice of raw materials significantly impacts the overall cost. High-quality materials can lead to better performance and durability but may also increase initial expenses. For instance, using advanced alloys or plastics can enhance the longevity of components but at a higher upfront cost.
-
Labor: Labor costs vary by region and can affect the pricing of G code programming and machining services. Countries with lower labor costs may offer competitive pricing, but this can sometimes come at the expense of quality. Assessing local labor markets is crucial for making cost-effective decisions.
-
Manufacturing Overhead: This includes the indirect costs associated with running a manufacturing facility, such as utilities, rent, and administrative expenses. Understanding these overheads can provide insights into the pricing strategies of potential suppliers.
-
Tooling: The costs associated with tooling—like molds, dies, and fixtures—can be significant. Custom tooling may be necessary for specific G code applications, which can lead to higher costs. Consider suppliers that have the capability to leverage existing tooling to minimize expenses.
-
Quality Control (QC): Implementing stringent QC measures ensures that the G codes produced meet the required specifications and standards. While this may add to the cost, it can prevent costly rework and returns down the line.
-
Logistics: Shipping and handling costs can vary widely based on the location of the supplier and the delivery destination. Incoterms chosen can influence these costs, making it essential to negotiate terms that provide the best value.
-
Margin: Suppliers will build their profit margins into pricing. Understanding the typical margin in the industry can help buyers gauge whether a price is reasonable or inflated.
How Do Price Influencers Affect G Codes Sourcing?
Several factors influence the pricing of G codes, which buyers should consider:
-
Volume/MOQ: Minimum order quantities (MOQs) can significantly affect pricing. Higher volumes often lead to lower per-unit costs, so negotiating bulk orders can yield cost savings.
-
Specifications and Customization: The complexity and specificity of the G codes required can drive up costs. Custom solutions tailored to unique applications may incur additional charges, so clarity on project specifications is critical.
-
Materials and Quality Certifications: The choice of materials and the necessity for specific quality certifications (like ISO) can affect pricing. Suppliers with certifications may charge a premium, reflecting their commitment to quality.
-
Supplier Factors: The reputation, reliability, and location of suppliers can also impact pricing. Established suppliers may charge more due to their experience and track record, but they may also offer better quality and support.
-
Incoterms: The terms of trade, such as FOB (Free on Board) or CIF (Cost, Insurance, and Freight), dictate who bears shipping costs and risks. Understanding these terms is essential for accurate cost assessments.
What Are Effective Buyer Tips for Cost-Efficiency in G Codes Sourcing?
To optimize costs when sourcing G codes, consider the following tips:
-
Negotiate Effectively: Engage suppliers in discussions about pricing and terms. Leverage volume purchases or long-term contracts to negotiate better prices.
-
Assess Total Cost of Ownership (TCO): Look beyond initial purchase prices and consider the TCO, which includes maintenance, operational efficiency, and potential downtime costs.
-
Understand Pricing Nuances for International Markets: Different regions may have varying pricing structures based on local economic conditions, tariffs, and taxes. Buyers from Africa, South America, the Middle East, and Europe should conduct regional market research to identify trends and potential cost savings.
-
Be Aware of Indicative Prices: Pricing in the G codes market can fluctuate based on demand and supply dynamics. Always request detailed quotes and understand that prices can change based on market conditions.
By carefully considering these cost components, influencers, and actionable strategies, international B2B buyers can navigate the complexities of G code sourcing more effectively, ensuring they achieve the best value for their investments.
Alternatives Analysis: Comparing g codes With Other Solutions
Exploring Alternatives to G Codes for CNC Machining
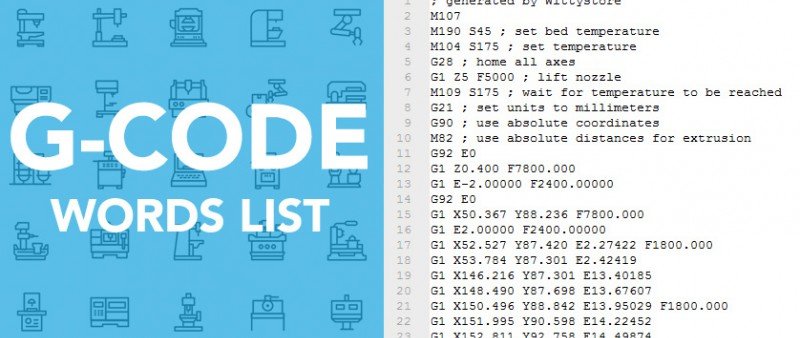
A stock image related to g codes.
In the landscape of CNC machining, G codes have become a staple for controlling machine tools. However, as technology evolves, alternative solutions have emerged that may offer enhanced capabilities or different functionalities. This section provides a comparative analysis of G codes against two viable alternatives: Parametric Programming and PLC (Programmable Logic Controller) Programming. Understanding these alternatives can help international B2B buyers, particularly from Africa, South America, the Middle East, and Europe, make informed decisions tailored to their specific operational needs.
Comparison Aspect | G Codes | Parametric Programming | PLC Programming |
---|---|---|---|
Performance | High precision in machining; optimized for various tasks. | Can adapt quickly to design changes, allowing for flexibility. | Suitable for complex automation and control tasks; can handle multiple machine operations simultaneously. |
Cost | Generally low initial cost; software and training may incur additional expenses. | Potentially higher initial setup costs due to complexity; can save costs in the long run through adaptability. | Higher upfront investment in hardware and software; offers long-term savings through efficiency. |
Ease of Implementation | Straightforward for those familiar with CNC; requires training for optimal use. | Requires specialized knowledge and training, which can increase implementation time. | Steeper learning curve; requires understanding of both programming and electrical systems. |
Maintenance | Regular updates needed for software; minimal hardware maintenance. | Maintenance is mainly software-based; adaptability can complicate maintenance processes. | Requires regular hardware checks and updates; complex systems may require specialized technicians. |
Best Use Case | Ideal for standard machining tasks with set parameters. | Best for projects requiring frequent design changes or customization. | Optimal for integrated systems needing coordination between various machinery and processes. |
What Are the Pros and Cons of Parametric Programming?
Pros: Parametric programming allows for dynamic adjustments in the machining process. This adaptability is particularly beneficial for businesses that frequently modify designs or need to produce customized products. The ability to change parameters without rewriting the entire program can significantly enhance efficiency.
Cons: The initial setup of parametric programming can be complex and may require a higher investment in training and software. Additionally, it may be less intuitive for operators accustomed to traditional G code systems, leading to potential operational delays during the transition.
How Does PLC Programming Compare to G Codes?
Pros: PLC programming excels in environments where automation and control of multiple machines are necessary. It allows for sophisticated control sequences, making it suitable for complex manufacturing processes. With PLCs, manufacturers can streamline operations and improve production efficiency.
Cons: The complexity of PLC systems can lead to higher upfront costs and a steep learning curve. Maintenance can also be more demanding, as it involves both software and hardware components, which may require specialized knowledge and skilled technicians.
How Can B2B Buyers Choose the Right Solution?
When selecting between G codes and alternative solutions such as parametric programming or PLC programming, international B2B buyers should consider their specific operational requirements, including the complexity of their machining tasks, budget constraints, and the necessary level of flexibility. For businesses focused on high-volume, standardized production, G codes may be the most efficient choice. Conversely, companies seeking to innovate with customizable designs or integrate complex automated systems might find parametric or PLC programming more advantageous. Ultimately, understanding the unique needs of your operations will guide you in choosing the most effective solution for your CNC machining challenges.
Essential Technical Properties and Trade Terminology for g codes
What Are the Essential Technical Properties of G Codes?
Understanding the key technical properties of G Codes is crucial for international B2B buyers involved in CNC machining. Here are some critical specifications that you should consider:
1. Precision and Tolerance
Precision refers to how close a manufactured part is to its specified dimensions, while tolerance is the allowable deviation from those dimensions. In CNC machining, achieving high precision and tight tolerance is essential for ensuring part compatibility and functionality. B2B buyers must prioritize suppliers that can consistently meet specified tolerances, as this directly impacts product quality and operational efficiency.
2. Feed Rate
The feed rate is the speed at which the tool moves through the material, typically measured in millimeters per minute (mm/min). Selecting an appropriate feed rate is vital as it affects both the surface finish of the machined part and the tool’s lifespan. Buyers should inquire about the feed rates that suppliers can accommodate to ensure that they align with their production requirements.
3. Material Compatibility
Different G Codes are optimized for various materials, including metals, plastics, and composites. Knowing the material compatibility of G Codes helps buyers select the right machining processes and ensures that the tools can effectively handle the specified materials. It is advisable for buyers to communicate their material needs clearly to avoid costly mistakes.
4. Axis Configuration
CNC machines can operate across multiple axes, typically 3-axis, 4-axis, or 5-axis configurations. The choice of axis configuration affects the complexity and variety of parts that can be manufactured. Buyers should assess their production needs and choose suppliers who have the capability to work with the necessary axis configurations, ensuring versatility in their manufacturing processes.
5. Cycle Time
Cycle time refers to the total time required to complete a machining operation. Reducing cycle time is crucial for improving productivity and cost-efficiency. Buyers should evaluate suppliers based on their ability to optimize cycle times while maintaining quality, as this can lead to significant savings in both time and resources.
What Are Common Trade Terms Related to G Codes?
Familiarity with industry jargon can greatly enhance communication and negotiations with suppliers. Here are some essential terms to know:
1. OEM (Original Equipment Manufacturer)
An OEM is a company that produces parts or equipment that may be marketed by another manufacturer. Understanding the role of OEMs is important for buyers, as it can influence pricing, quality, and support services. B2B buyers should ensure that they are sourcing from reputable OEMs to guarantee the reliability of their components.
2. MOQ (Minimum Order Quantity)
MOQ is the smallest quantity of a product that a supplier is willing to sell. This term is significant for B2B buyers as it impacts inventory management and cash flow. Buyers should negotiate MOQs that align with their production schedules to avoid overstocking or delays.
3. RFQ (Request for Quotation)
An RFQ is a document sent to suppliers to solicit price quotes for specific products or services. For B2B buyers, issuing RFQs can lead to competitive pricing and better supplier relationships. Including detailed specifications in RFQs ensures accurate and comparable quotes from suppliers.
4. Incoterms (International Commercial Terms)
Incoterms are a set of international rules that define the responsibilities of buyers and sellers regarding the delivery of goods. Understanding Incoterms is essential for international B2B transactions, as they clarify shipping costs, risks, and responsibilities, helping to prevent disputes.
5. CNC (Computer Numerical Control)
CNC refers to the automated control of machining tools and 3D printers by a computer. This technology is vital in modern manufacturing, allowing for high precision and efficiency. B2B buyers should look for suppliers with advanced CNC capabilities to meet their production needs effectively.
By grasping these technical properties and trade terms, international B2B buyers can make more informed decisions, ensuring that they partner with suppliers that meet their specific requirements and enhance their operational efficiency.
Navigating Market Dynamics and Sourcing Trends in the g codes Sector
What Are the Key Market Trends Influencing the G Codes Sector?
The global landscape for G codes is evolving rapidly, driven by advancements in CNC technology and the increasing automation of manufacturing processes. As international B2B buyers, especially from regions like Africa, South America, the Middle East, and Europe, it’s essential to recognize the key trends shaping the market. One significant driver is the push towards Industry 4.0, which emphasizes smart manufacturing and connectivity. This has led to a rise in demand for sophisticated G code programming capabilities that enable seamless integration with IoT devices and advanced analytics.
Moreover, the increasing focus on precision and efficiency in manufacturing processes is prompting companies to adopt more advanced G code practices. The rise of additive manufacturing technologies, particularly in countries like Spain and Vietnam, is also influencing sourcing trends. Buyers are seeking suppliers that offer comprehensive solutions, including training on G code programming, CNC machine operation, and ongoing technical support.
Additionally, sustainability is becoming a critical factor. Companies are increasingly looking for suppliers who can provide eco-friendly materials and processes, reinforcing the importance of sourcing from manufacturers committed to sustainable practices. This trend is particularly relevant for buyers in Africa and South America, where local regulations are tightening around environmental impacts.
How Can B2B Buyers Ensure Sustainability and Ethical Sourcing in the G Codes Sector?
Sustainability and ethical sourcing are paramount in today’s manufacturing landscape, especially for B2B buyers. The environmental impact of manufacturing processes, including energy consumption and waste generation, is under scrutiny. Therefore, it is crucial for buyers to partner with suppliers who prioritize sustainable practices, such as using energy-efficient machinery and minimizing waste through optimized G code programming.
One effective way to ensure sustainable sourcing is by looking for suppliers with recognized certifications, such as ISO 14001 for environmental management systems. These certifications demonstrate a commitment to reducing environmental footprints and promoting responsible sourcing of materials. Additionally, buyers should inquire about the use of ‘green’ materials in the production of CNC components and G code applications, such as biodegradable lubricants or recycled materials.
Furthermore, engaging with suppliers who adopt a circular economy approach can significantly enhance sustainability efforts. This involves not only sourcing materials responsibly but also ensuring that products can be reused or recycled, thus reducing the overall environmental impact.
What Is the Evolution of G Codes and Their Relevance to Today’s B2B Buyers?
The concept of G codes has evolved significantly since its inception in the 1950s, transitioning from simple machine commands to complex programming languages that control modern CNC machines. Initially designed to facilitate basic movements, G codes have expanded to encompass a wide range of functionalities, including advanced machining techniques and multi-axis operations.
Today, G codes are integral to various industries, from aerospace to automotive manufacturing. This evolution reflects a broader shift towards automation and precision in manufacturing, making G codes more relevant than ever for B2B buyers. Understanding the history and advancements in G code technology can provide valuable insights into selecting the right suppliers and technologies that align with their operational needs.
By recognizing these market dynamics and trends, international B2B buyers can make informed decisions, ensuring they not only meet current demands but also anticipate future challenges and opportunities in the G codes sector.
Frequently Asked Questions (FAQs) for B2B Buyers of g codes
-
How do I solve issues with G-Code compatibility across different CNC machines?
To address compatibility issues with G-Code across various CNC machines, first, ensure you are familiar with the specific G-Codes used by each machine manufacturer. Different machines may implement G-Codes differently, so consult the machine’s manual or technical support for clarification. It’s advisable to standardize your G-Code programming by using common codes (like G00, G01, G02, etc.) and avoiding manufacturer-specific commands when possible. Testing programs on a simulator before executing them on the actual machine can also help identify potential issues. -
What is the best approach to source G-Codes for my CNC machining needs?
The best approach to source G-Codes is to engage with reputable suppliers who specialize in CNC programming and tooling. Start by defining your specific requirements, such as the type of machining, material, and complexity of parts. Research suppliers through online platforms, industry forums, and trade shows, and seek recommendations from industry peers. Request samples or demo programs to evaluate the quality of their G-Codes and ensure they align with your CNC machines. Additionally, verify their expertise in your specific region, whether it be Africa, South America, the Middle East, or Europe. -
How can I ensure the quality of G-Code programming services?
To ensure quality in G-Code programming services, conduct thorough supplier vetting. Look for suppliers with a proven track record and positive customer reviews. Ask for references from previous clients and evaluate their experience with similar projects. Request samples of their G-Code programs to assess accuracy and efficiency. Additionally, inquire about their quality assurance processes, including how they handle errors and machine compatibility issues. Consider suppliers who offer post-programming support and training to ensure your team can effectively use the G-Codes provided. -
What are the typical minimum order quantities (MOQs) for G-Code programming services?
Minimum order quantities (MOQs) for G-Code programming services can vary significantly based on the supplier and the complexity of the programming required. Some suppliers may have low MOQs, especially for simple or standard G-Code programs, while others may require higher quantities for custom programming. When negotiating with suppliers, clearly communicate your needs and explore options for batch programming or bundled services to meet MOQ requirements. If you are a smaller operation, consider partnering with other businesses to meet MOQ thresholds collectively. -
What payment terms should I expect when sourcing G-Codes internationally?
Payment terms for international sourcing of G-Codes can vary widely depending on the supplier’s policies and the nature of your agreement. Common payment methods include wire transfers, credit terms (30, 60, or 90 days), and letter of credit arrangements for larger orders. It’s crucial to negotiate payment terms that suit both parties and to establish clear milestones for payment linked to project deliverables. Ensure that all terms are documented in a contract to avoid misunderstandings. Additionally, be aware of currency exchange rates and any transaction fees that may apply. -
How can I customize G-Codes to fit my specific machining processes?
Customizing G-Codes to fit your machining processes involves understanding your specific operational needs and the capabilities of your CNC machines. Work closely with your programming team or supplier to define the parameters that need adjustment, such as feed rates, tool paths, and dwell times. Utilize simulation software to visualize how changes in G-Codes affect machining outcomes before implementation. Additionally, consider training for your operators to ensure they can effectively adapt G-Codes to new projects as required. -
What logistics considerations should I keep in mind when sourcing G-Codes?
When sourcing G-Codes, logistics considerations include shipping times, customs regulations, and potential delays associated with international trade. Ensure that your supplier can provide timely delivery of programming files, especially if you are working on a tight production schedule. Familiarize yourself with customs requirements in your country to prevent any interruptions in receiving your G-Code files. It may also be beneficial to explore digital delivery options to expedite the process and reduce shipping costs. -
How can I troubleshoot common G-Code errors during CNC machining?
Troubleshooting common G-Code errors involves a systematic approach. Start by reviewing the error messages displayed by your CNC machine, as they can provide clues to the issue. Check for syntax errors or unsupported commands in the G-Code. Use a G-Code simulator to run the program virtually and identify potential problems before actual machining. Additionally, ensure that the machine settings match the parameters defined in the G-Code. If issues persist, consult with your supplier or a CNC programming expert for assistance.
Important Disclaimer & Terms of Use
⚠️ Important Disclaimer
The information provided in this guide, including content regarding manufacturers, technical specifications, and market analysis, is for informational and educational purposes only. It does not constitute professional procurement advice, financial advice, or legal advice.
While we have made every effort to ensure the accuracy and timeliness of the information, we are not responsible for any errors, omissions, or outdated information. Market conditions, company details, and technical standards are subject to change.
B2B buyers must conduct their own independent and thorough due diligence before making any purchasing decisions. This includes contacting suppliers directly, verifying certifications, requesting samples, and seeking professional consultation. The risk of relying on any information in this guide is borne solely by the reader.
Strategic Sourcing Conclusion and Outlook for g codes
The strategic sourcing of G codes is pivotal for international B2B buyers seeking to enhance their manufacturing efficiencies. By understanding the fundamental G codes, such as G00 for rapid travel and G01 for linear interpolation, companies can optimize their CNC machining processes. This knowledge not only streamlines production but also reduces operational costs and minimizes errors.
How Can Strategic Sourcing of G Codes Drive Competitive Advantage?
In regions such as Africa, South America, the Middle East, and Europe, leveraging advanced CNC capabilities through effective G code programming can significantly differentiate businesses in competitive markets. As you engage with suppliers and manufacturers, consider the importance of selecting machines that support a comprehensive range of G codes, ensuring flexibility and adaptability in your production lines.
What Should International Buyers Focus on Moving Forward?
Looking ahead, it is essential for international buyers to prioritize the integration of cutting-edge CNC technologies and training in G code programming. Collaborating with suppliers that offer robust support and resources will empower your workforce, leading to improved product quality and innovation.
In conclusion, as global markets evolve, strategic sourcing of G codes should be at the forefront of your operational strategy. Embrace this opportunity to enhance your manufacturing capabilities and drive your business towards sustained growth and success.