Master Industrial Air Compressor Repair Near Me for Optimal
Introduction: Navigating the Global Market for industrial air compressor repair near me
In today’s interconnected global economy, the efficiency of industrial air compressors is paramount to maintaining operational productivity across various sectors. For businesses in Africa, South America, the Middle East, and Europe, the ability to access reliable and timely air compressor repair services is crucial. The phrase “industrial air compressor repair near me” transcends mere convenience; it signifies the importance of having expert technicians who can quickly diagnose and resolve issues, minimizing downtime and ensuring that production processes remain uninterrupted.
This guide provides a comprehensive overview of industrial air compressor repair, addressing key aspects such as types of compressors, materials used in manufacturing, quality control measures, and a detailed look at suppliers and cost considerations. By delving into the nuances of the market, we empower B2B buyers with actionable insights that facilitate informed sourcing decisions.
From understanding the intricacies of preventative maintenance to exploring emergency repair options, this resource equips decision-makers with the knowledge necessary to enhance their operational efficiency. Additionally, it tackles frequently asked questions to clarify common concerns and challenges faced by industries relying on compressed air solutions. Whether you’re in Vietnam, France, or beyond, this guide aims to streamline your approach to sourcing industrial air compressor repair services, ultimately driving your business’s success in a competitive landscape.
Understanding industrial air compressor repair near me Types and Variations
Type Name | Key Distinguishing Features | Primary B2B Applications | Brief Pros & Cons for Buyers |
---|---|---|---|
Preventative Maintenance | Scheduled inspections, routine servicing | Manufacturing, Automotive | Pros: Reduces unexpected breakdowns, extends lifespan. Cons: Requires ongoing investment. |
Emergency Repairs | On-call service for urgent issues | All sectors | Pros: Quick response, minimizes downtime. Cons: Higher costs due to urgency, potential for rushed repairs. |
Parts Replacement Services | Focus on component upgrades and replacements | Food & Beverage, Pharma | Pros: Improves efficiency, ensures compliance. Cons: May require additional downtime for installation. |
System Audits | Comprehensive evaluations of compressor efficiency | Energy, Manufacturing | Pros: Identifies inefficiencies, potential cost savings. Cons: Initial investment in auditing services. |
Training and Development | On-site training for staff on compressor operation | All sectors | Pros: Enhances operational knowledge, reduces errors. Cons: Time-consuming, potential disruption to operations. |
Preventative Maintenance
Preventative maintenance involves scheduled inspections and routine servicing of industrial air compressors to ensure optimal performance. This type of service is particularly vital for industries such as manufacturing and automotive, where equipment reliability is crucial. B2B buyers should consider the long-term cost savings associated with reduced unexpected breakdowns and extended equipment lifespan. However, it requires a consistent investment and commitment from management to adhere to maintenance schedules.
Emergency Repairs
Emergency repairs are critical for businesses that experience unexpected compressor failures. These services provide on-call assistance to resolve urgent issues, significantly minimizing downtime. All sectors, particularly those reliant on continuous operations, can benefit from this type of service. While the quick response is advantageous, buyers should be aware that emergency repairs often come at a premium and may lead to rushed solutions if not managed properly.
Parts Replacement Services
Parts replacement services focus on upgrading or replacing worn-out components of air compressors. This is essential in sectors like food and beverage or pharmaceuticals, where compliance with health standards is paramount. By improving system efficiency and ensuring compliance, these services can lead to better operational performance. However, buyers should consider the potential downtime required for installation, which could impact production schedules.
System Audits
Conducting system audits is a comprehensive approach to evaluating the efficiency of air compressor operations. This service is particularly beneficial for energy-intensive industries, as it identifies inefficiencies and areas for potential cost savings. B2B buyers should view audits as an investment that can lead to significant operational improvements. However, the initial cost of auditing services can be a barrier for some companies, necessitating careful budget considerations.
Training and Development
Training and development services provide on-site education for staff on the proper operation and maintenance of air compressors. This is crucial across all sectors, as it enhances operational knowledge and reduces the likelihood of errors. Investing in training can lead to improved safety and efficiency within the workplace. However, it can be time-consuming and may temporarily disrupt regular operations, requiring strategic planning to implement effectively.
Related Video: DeWALT Air Compressor Repair – How to Replace the Regulator Repair Kit
Key Industrial Applications of industrial air compressor repair near me
Industry/Sector | Specific Application of industrial air compressor repair near me | Value/Benefit for the Business | Key Sourcing Considerations for this Application |
---|---|---|---|
Manufacturing | Regular maintenance and emergency repairs for assembly lines. | Minimizes downtime and ensures continuous production flow. | Availability of skilled technicians and parts supply. |
Food & Beverage | Compliance testing and maintenance of food-grade compressors. | Ensures product safety and adherence to health regulations. | Certifications for food safety and reliability of service. |
Pharmaceuticals | Air quality testing and repair of sterile air systems. | Guarantees product integrity and compliance with industry standards. | Expertise in regulatory requirements and specialized equipment. |
Energy Sector | Maintenance of compressors in power generation facilities. | Enhances operational efficiency and reduces energy costs. | Ability to perform energy audits and system optimizations. |
Construction | On-site repairs for portable air compressors used in construction. | Reduces project delays and maintains workflow efficiency. | Proximity to service locations and quick response times. |
Detailed Applications
Manufacturing
In the manufacturing sector, industrial air compressors are critical for powering assembly lines and pneumatic tools. Regular maintenance and emergency repairs are essential to minimize downtime, as even minor disruptions can lead to significant financial losses. Buyers should consider service providers with a robust parts supply and skilled technicians capable of servicing various compressor brands. This ensures that any issues can be resolved quickly, maintaining production efficiency and reducing operational costs.
Food & Beverage
The food and beverage industry relies heavily on air compressors that meet stringent health and safety standards. Regular compliance testing and maintenance of food-grade compressors are crucial to ensure product safety and adherence to health regulations. B2B buyers must prioritize service providers with the necessary certifications and experience in food safety. This ensures that all maintenance and repairs meet industry standards, protecting both product integrity and consumer health.
Pharmaceuticals
In the pharmaceutical sector, air quality is paramount, particularly in sterile environments. Industrial air compressor repair services must include air quality testing and the maintenance of sterile air systems to guarantee compliance with stringent industry regulations. Buyers should seek service providers with expertise in regulatory requirements and specialized equipment to ensure that their air systems meet the necessary standards, thereby safeguarding product integrity and public health.
Energy Sector
For the energy sector, particularly in power generation, the efficiency of industrial air compressors can significantly impact operational costs. Regular maintenance not only enhances performance but also helps in identifying potential energy savings. B2B buyers should look for service providers who offer energy audits and system optimizations, as these can lead to substantial reductions in energy consumption and operational costs over time.
Construction
In the construction industry, portable air compressors are often used for various tools and equipment. On-site repairs are essential to avoid project delays caused by equipment failure. Buyers should consider the proximity of service locations and the quick response times of repair services to ensure minimal disruption to workflow. A reliable repair service can significantly enhance project efficiency and maintain timelines, which is crucial in the competitive construction market.
Related Video: How to repair fix air compressor not building pressure easy fix
Strategic Material Selection Guide for industrial air compressor repair near me
When selecting materials for industrial air compressor repair, it is crucial to consider the specific properties, advantages, and limitations of each material. This analysis focuses on four common materials used in air compressor components: Aluminum, Stainless Steel, Bronze, and Composite Materials. Each material presents unique characteristics that can significantly impact performance, durability, and cost.
Aluminum
Key Properties: Aluminum is lightweight and has excellent corrosion resistance, making it suitable for various components in air compressors. It typically withstands moderate temperature and pressure ranges, up to about 150°C and 5 bar.
Pros & Cons: The primary advantages of aluminum include its low weight, ease of machining, and good thermal conductivity. However, it is less durable than other metals under high-stress conditions and can be more expensive than some alternatives.
Impact on Application: Aluminum is particularly effective in applications requiring lightweight components, such as compressor housings and covers. Its corrosion resistance makes it ideal for environments with moisture or chemicals.
Considerations for International Buyers: Buyers from regions like Africa and South America should consider the availability of aluminum and the associated costs. Compliance with international standards, such as ASTM and DIN, is essential for ensuring quality and performance.
Stainless Steel
Key Properties: Stainless steel is known for its high strength, excellent corrosion resistance, and ability to withstand high temperatures (up to 300°C) and pressures (up to 10 bar).
Pros & Cons: The key advantage of stainless steel is its durability and resistance to corrosion, making it suitable for harsh environments. However, it is heavier than aluminum and can be more challenging to machine, increasing manufacturing complexity and costs.
Impact on Application: Stainless steel is often used in critical components such as valves, fittings, and piping systems where strength and reliability are paramount. Its compatibility with various media, including corrosive substances, makes it versatile.
Considerations for International Buyers: Buyers in Europe and the Middle East should ensure that the stainless steel grades comply with local standards (e.g., EN 10088) and consider the implications of import tariffs on costs.
Bronze
Key Properties: Bronze, an alloy of copper, is known for its excellent wear resistance and good corrosion resistance, particularly in marine environments. It can handle moderate temperatures and pressures.
Pros & Cons: The advantages of bronze include its durability and low friction characteristics, making it suitable for bearings and bushings. However, it can be more expensive than aluminum and stainless steel, and its availability may vary by region.
Impact on Application: Bronze is particularly useful in applications where low friction and wear resistance are critical, such as in compressor rotors and bearings. Its compatibility with lubricants enhances its performance in moving parts.
Considerations for International Buyers: Buyers should be aware of the varying standards for bronze alloys in different regions. Compliance with ASTM B505 or similar standards is crucial for ensuring material quality.
Composite Materials
Key Properties: Composite materials, often made from a combination of polymers and fibers, offer excellent corrosion resistance and can be engineered for specific performance characteristics.
Pros & Cons: The primary advantage of composites is their lightweight nature and resistance to corrosion and chemicals. However, they may not withstand high temperatures or pressures as effectively as metals, limiting their application scope.
Impact on Application: Composites are increasingly used in non-structural components such as air filters and sound insulation panels. Their flexibility allows for tailored solutions in specific applications.
Considerations for International Buyers: Buyers should evaluate the certifications of composite materials, particularly in sectors like food and pharmaceuticals, where compliance with standards such as FDA or EU regulations is necessary.
Summary Table
Material | Typical Use Case for industrial air compressor repair near me | Key Advantage | Key Disadvantage/Limitation | Relative Cost (Low/Med/High) |
---|---|---|---|---|
Aluminum | Compressor housings and covers | Lightweight and corrosion-resistant | Less durable under high stress | Medium |
Stainless Steel | Valves, fittings, and piping systems | High strength and corrosion-resistant | Heavier and more complex to machine | High |
Bronze | Bearings and bushings | Excellent wear resistance | More expensive and variable availability | High |
Composite Materials | Non-structural components like filters | Lightweight and customizable | Limited high-temperature performance | Medium |
This strategic material selection guide provides international B2B buyers with essential insights into the materials commonly used in industrial air compressor repair, enabling informed decision-making that aligns with operational needs and compliance standards.
In-depth Look: Manufacturing Processes and Quality Assurance for industrial air compressor repair near me
Industrial air compressor repair is a critical service for various sectors, ranging from manufacturing to healthcare. Understanding the manufacturing processes and quality assurance measures involved in this industry is essential for international B2B buyers, particularly those from Africa, South America, the Middle East, and Europe. Here, we delve into the typical stages of manufacturing and the quality control standards that govern air compressor repair services.
Manufacturing Processes
The manufacturing process for industrial air compressor repair involves several key stages, each crucial for ensuring the reliability and efficiency of the equipment. Below are the main stages of the manufacturing process:
1. Material Preparation
The first step involves sourcing high-quality materials that meet industry specifications. Common materials include:
– Aluminum and Steel: Used for compressor bodies and components due to their strength and lightweight properties.
– Seals and Gaskets: Made from rubber or silicone to ensure airtight connections.
– Lubricants: Essential for minimizing friction within moving parts.
B2B buyers should ensure that suppliers have stringent material selection processes to guarantee durability and performance.
2. Forming
This stage involves shaping materials into the required components. Techniques include:
– Casting: Used for complex shapes, allowing for better structural integrity.
– Machining: Involves cutting, drilling, and finishing components to precise specifications.
– Welding: Essential for assembling parts, particularly in the compressor casing.
Buyers should look for suppliers that utilize advanced technologies like CNC machining for precision.
3. Assembly
Once the individual components are ready, they are assembled into a complete air compressor. This process typically involves:
– Sub-Assembly: Pre-assembling certain parts before final assembly to streamline the process.
– Integration of Electronics: Installing control systems and sensors for monitoring performance.
Effective assembly processes ensure that the compressors are built to last, which is vital for maintaining operational efficiency.
4. Finishing
The final stage includes surface treatments and coatings to enhance durability and prevent corrosion. Techniques may involve:
– Powder Coating: Provides a protective layer that is resistant to chemicals and wear.
– Anodizing: Commonly used for aluminum parts to increase corrosion resistance.
Finishing processes are vital for extending the lifespan of compressors, particularly in harsh environments.
Quality Assurance
Quality assurance (QA) is critical in the manufacturing and repair of industrial air compressors. It ensures that all products meet international standards and function effectively in their intended applications.
Relevant International Standards
Several standards govern the quality of air compressor manufacturing and repair, including:
– ISO 9001: Focuses on quality management systems, ensuring consistent quality in products and services.
– CE Marking: Indicates conformity with health, safety, and environmental protection standards for products sold within the European Economic Area.
– API Standards: Relevant for compressors used in the oil and gas industry, emphasizing safety and reliability.
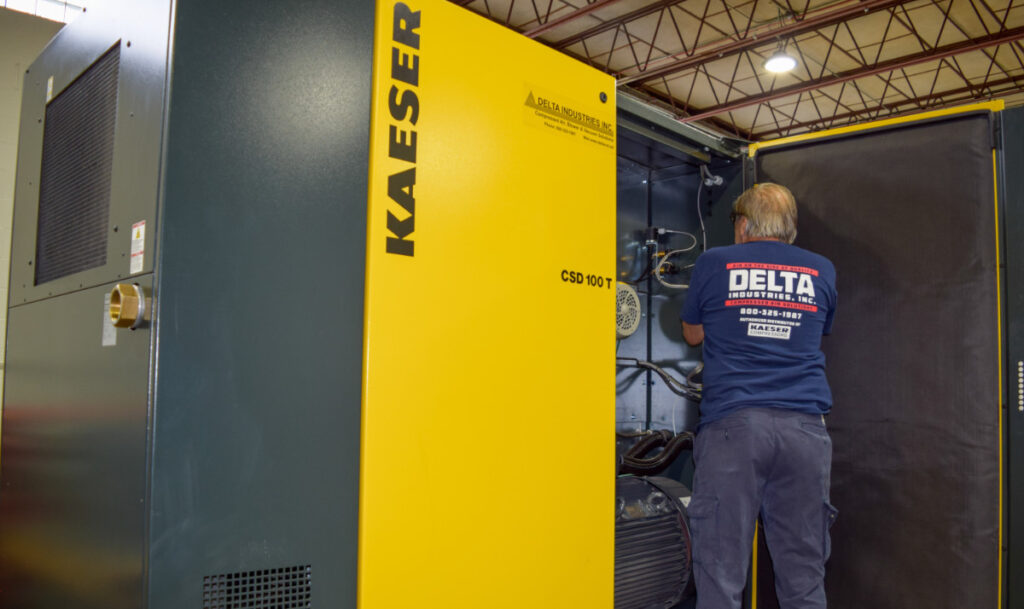
Illustrative Image (Source: Google Search)
B2B buyers should prioritize suppliers that adhere to these standards, as they reflect a commitment to quality.
Quality Control Checkpoints
Quality control (QC) involves several checkpoints throughout the manufacturing process:
– Incoming Quality Control (IQC): Inspects raw materials upon arrival to ensure they meet specifications.
– In-Process Quality Control (IPQC): Monitors processes during manufacturing to detect defects early.
– Final Quality Control (FQC): Conducts thorough testing on the finished product to verify performance and safety.
These checkpoints are essential for identifying and rectifying issues that could affect compressor performance.
Common Testing Methods
Various testing methods are employed to ensure the quality and performance of air compressors:
– Pressure Testing: Assesses the integrity of the compressor under operational conditions.
– Ultrasonic Leak Detection: Identifies air leaks, which can significantly impact efficiency.
– Performance Testing: Evaluates the compressor’s output and efficiency against specified benchmarks.
International buyers should request documentation of these tests to verify compliance with quality standards.
Verifying Supplier Quality Control
For international B2B buyers, verifying a supplier’s quality control measures is paramount. Here are actionable steps to assess supplier QC:
- Conduct Audits: Regular audits of suppliers can provide insights into their QC processes and adherence to standards.
- Request Quality Reports: Ask for documentation of past QC tests and certifications to understand their compliance history.
- Utilize Third-Party Inspections: Engage third-party agencies to conduct independent inspections, ensuring unbiased assessments of quality.
QC and Certification Nuances for International Buyers
When sourcing air compressor repair services from different regions, buyers must be aware of the nuances in quality control and certification processes. For instance:
– Regional Standards: Different regions may have unique compliance requirements. Buyers should familiarize themselves with local regulations in their target markets.
– Cultural Considerations: Understanding cultural differences in business practices can facilitate better communication regarding quality expectations.
By prioritizing suppliers that demonstrate robust quality assurance processes and compliance with international standards, B2B buyers can secure reliable and efficient air compressor repair services that meet their operational needs.
Related Video: Largest Screw Compressor Manufacturing, Assembly & Repair Process. Incredible Efficient Compressor
Comprehensive Cost and Pricing Analysis for industrial air compressor repair near me Sourcing
When sourcing industrial air compressor repair services, understanding the comprehensive cost structure is crucial for international B2B buyers. The costs associated with these services can be categorized into several key components, each influencing the final pricing.
Cost Components
-
Materials: The cost of replacement parts is a significant aspect of the overall expense. Common materials include filters, gaskets, and lubricants. The price can vary based on the brand and quality of components used.
-
Labor: Skilled technicians are essential for effective repair and maintenance. Labor costs depend on the complexity of the repair and the local wage standards. For instance, labor rates may be higher in Europe compared to parts of Africa or South America.
-
Manufacturing Overhead: This includes the indirect costs related to running repair operations, such as utilities and facility maintenance. These costs are typically factored into service pricing.
-
Tooling: Specialized tools may be required for certain repairs, contributing to the overall cost. The need for advanced diagnostics or specific equipment can increase repair costs.
-
Quality Control (QC): Ensuring that repairs meet industry standards often involves additional testing and certification processes, which can add to the overall expense.
-
Logistics: If parts need to be sourced from different locations, shipping costs can significantly impact the total price. This is especially relevant for international buyers, where customs and tariffs may also apply.
-
Margin: Service providers typically mark up their costs to ensure profitability. Understanding the typical margins in your region can aid in negotiating better pricing.
Price Influencers
Several factors can influence the pricing of industrial air compressor repair services:
-
Volume/MOQ: Larger orders often lead to reduced unit costs. Negotiating for bulk repair services or scheduled maintenance can yield savings.
-
Specifications/Customization: Custom solutions may carry additional costs. Buyers should clarify their needs to avoid unexpected charges.
-
Materials Quality/Certifications: Higher quality parts or those with certifications (like ISO) may come at a premium. However, investing in quality can reduce long-term operational costs.
-
Supplier Factors: The reputation and reliability of the supplier can influence pricing. Established companies may charge more due to their track record and service guarantees.
-
Incoterms: Understanding the terms of shipment (e.g., FOB, CIF) is essential for calculating total costs, especially for international purchases.
Buyer Tips
-
Negotiation: Engage in discussions with multiple service providers to compare pricing and services. Leverage quotes to negotiate better terms or discounts.
-
Cost Efficiency: Look for service providers that offer preventative maintenance plans. These can help mitigate unforeseen repair costs and extend the lifespan of your equipment.
-
Total Cost of Ownership (TCO): Consider not just the initial repair costs but the long-term savings from energy efficiency and reduced downtime. Conduct energy audits to identify potential savings.
-
Pricing Nuances for International Buyers: Be aware of regional pricing differences. In some markets, you may find lower labor costs, while in others, high-quality parts may justify higher prices. Always factor in shipping and customs costs for imported parts.
-
Disclaimer for Indicative Prices: Pricing for industrial air compressor repair can vary widely based on numerous factors, including the specific services required and regional market conditions. Always seek detailed quotes tailored to your specific needs.
By understanding these cost structures and price influencers, international B2B buyers can make informed decisions when sourcing industrial air compressor repair services, ultimately ensuring better value and efficiency for their operations.
Essential Technical Properties and Trade Terminology for industrial air compressor repair near me
Key Technical Properties of Industrial Air Compressors
Understanding the technical properties of industrial air compressors is vital for international B2B buyers to make informed decisions. Here are several critical specifications:
-
Material Grade
– Definition: The quality of materials used in compressor components, such as aluminum, cast iron, or stainless steel.
– Importance: Higher-grade materials improve durability and resistance to wear, which is crucial for maintaining compressor efficiency and longevity, especially in harsh operational environments typical in industries across Africa and the Middle East. -
Tolerance
– Definition: The permissible limit of variation in a physical dimension. For compressors, this often refers to the spacing and alignment of moving parts.
– Importance: Tight tolerances ensure better performance and reliability, reducing the risk of mechanical failure. This is particularly significant for B2B buyers in high-precision sectors like aerospace or pharmaceuticals. -
Flow Rate
– Definition: The volume of air the compressor can deliver, usually measured in cubic feet per minute (CFM).
– Importance: A higher flow rate is essential for applications requiring substantial compressed air supply. Buyers need to match the compressor’s flow rate with their operational demands to avoid inefficiencies. -
Pressure Rating
– Definition: The maximum pressure the compressor can achieve, often indicated in pounds per square inch (PSI).
– Importance: Understanding pressure ratings is critical for selecting compressors that can meet specific application needs. Different industries, from manufacturing to food processing, have varying pressure requirements. -
Energy Efficiency Rating
– Definition: A measure of the compressor’s energy consumption relative to its output, often expressed in kilowatts per CFM.
– Importance: Energy-efficient compressors reduce operational costs and environmental impact. For international buyers, especially in regions with high energy costs, this is a key consideration.
Common Trade Terminology in Industrial Air Compressor Repair
Familiarizing oneself with industry jargon is crucial for effective communication and negotiation in B2B transactions. Here are some common terms:
-
OEM (Original Equipment Manufacturer)
– Definition: A company that produces parts and equipment that may be marketed by another manufacturer.
– Importance: Knowing whether parts are OEM or aftermarket can affect quality and compatibility. Buyers often prefer OEM parts for reliability. -
MOQ (Minimum Order Quantity)
– Definition: The smallest quantity of a product that a supplier is willing to sell.
– Importance: Understanding MOQ is essential for budgeting and inventory management, particularly for businesses operating in regions with fluctuating demand. -
RFQ (Request for Quotation)
– Definition: A document issued by a buyer to solicit price offers from suppliers for specific products or services.
– Importance: An RFQ helps buyers compare prices and terms across multiple suppliers, ensuring they receive the best deal. -
Incoterms (International Commercial Terms)
– Definition: A set of predefined international rules that clarify the responsibilities of buyers and sellers in international transactions.
– Importance: Understanding Incoterms is critical for international shipping and logistics, as they dictate who is responsible for shipping costs, insurance, and tariffs. -
Preventive Maintenance
– Definition: Regularly scheduled maintenance activities aimed at preventing equipment failures.
– Importance: Implementing preventive maintenance strategies can significantly reduce downtime and repair costs, making it essential for operational efficiency. -
Ultrasonic Leak Detection
– Definition: A method used to identify leaks in compressed air systems through ultrasonic sound waves.
– Importance: This technology is vital for minimizing energy losses associated with leaks, which can be significant in industrial settings. Buyers should consider suppliers that offer this service as part of their maintenance programs.
By understanding these technical properties and trade terms, international B2B buyers can enhance their procurement strategies, ensuring they select the right equipment and services for their specific industrial needs.
Navigating Market Dynamics, Sourcing Trends, and Sustainability in the industrial air compressor repair near me Sector
Market Overview & Key Trends
The industrial air compressor repair sector is experiencing significant transformation driven by several global factors. Increased manufacturing demands in regions such as Africa, South America, and the Middle East are propelling the need for reliable air compressor systems. Technological advancements in predictive maintenance, such as IoT-enabled monitoring systems, are emerging as critical tools for enhancing operational efficiency and minimizing downtime. B2B buyers are increasingly focused on data analytics to optimize compressor performance and energy consumption, thus leading to cost reductions.
Moreover, the shift towards automation in manufacturing processes is creating a demand for sophisticated air compressor solutions that can integrate seamlessly with existing systems. Buyers should note the trend of remote servicing capabilities offered by suppliers, allowing for rapid diagnostics and repairs without the need for on-site visits, which is especially valuable in regions with limited access to skilled technicians.
As businesses navigate these dynamics, understanding regional market conditions, including local regulations and supply chain logistics, becomes essential for sourcing the right services and parts. The demand for customized service plans is on the rise, with buyers seeking tailored solutions that align with their specific operational needs and sustainability goals.
Sustainability & Ethical Sourcing in B2B
Sustainability is becoming a cornerstone of the industrial air compressor repair sector, influencing both purchasing decisions and supplier selection. The environmental impact of compressed air systems is substantial, often accounting for up to 40% of a facility’s total energy consumption. Thus, B2B buyers are increasingly prioritizing energy-efficient solutions that reduce carbon footprints and operational costs.
Moreover, the importance of ethical supply chains cannot be overstated. Buyers are encouraged to partner with suppliers who demonstrate a commitment to sustainable practices, including the use of recycled materials and eco-friendly lubricants in their repair processes. Certifications such as ISO 14001 for environmental management systems can serve as a benchmark for assessing a supplier’s sustainability credentials.
Investing in green technologies not only enhances a company’s reputation but also positions it favorably in a market that is progressively leaning towards environmentally responsible practices. By prioritizing sustainability in procurement, companies can achieve long-term cost savings while contributing to global environmental goals.
Brief Evolution/History
The industrial air compressor repair sector has evolved significantly over the last few decades. Initially, repair services were largely reactive, focusing on fixing breakdowns as they occurred. However, advancements in technology have shifted this paradigm towards a more proactive approach. The introduction of preventative and predictive maintenance strategies has enabled companies to anticipate failures before they occur, significantly reducing downtime and repair costs.
As industries have become more automated, the demand for sophisticated compressor systems has surged, driving innovation in repair techniques and service offerings. This evolution reflects a broader trend towards operational efficiency and sustainability, making it imperative for international B2B buyers to stay informed about the latest developments in this critical sector.
Related Video: Global Trade & Logistics – What is Global Trade?
Frequently Asked Questions (FAQs) for B2B Buyers of industrial air compressor repair near me
-
What criteria should I use to vet suppliers for industrial air compressor repair?
When vetting suppliers for industrial air compressor repair, consider their industry reputation, experience, and certifications. Look for companies with a proven track record, ideally in your specific industry. Check for certifications such as ISO 9001, which indicates quality management systems. Additionally, read customer reviews and request case studies to evaluate their service capabilities. Ensure they have skilled technicians who are familiar with your equipment brands and models. -
Can suppliers customize their repair services based on our specific needs?
Yes, many suppliers offer customization options for repair services. It’s essential to communicate your specific requirements, such as equipment type, operational conditions, and industry standards. Some suppliers may provide tailored maintenance plans, preventative measures, or specific certifications for industries like food and pharmaceuticals. Discussing your needs upfront can lead to more effective service solutions and improved equipment performance. -
What are the typical minimum order quantities (MOQ) and lead times for parts and services?
MOQs can vary significantly based on the supplier and the specific parts required. Generally, larger suppliers may have lower MOQs due to their inventory levels. Lead times also depend on the complexity of the repairs and availability of parts; it could range from a few days to several weeks. Always clarify these details with your supplier before placing an order to avoid unexpected delays in your operations. -
What payment terms should I expect when engaging with international suppliers?
Payment terms can vary widely among international suppliers. Common arrangements include upfront payment, partial payments, or net terms (30, 60, or 90 days). It’s advisable to establish clear payment terms in your contract. Additionally, consider using secure payment methods such as letters of credit or escrow services to protect your investment, especially when dealing with new suppliers. -
How do I ensure quality assurance and certifications for the repair services?
To ensure quality assurance, inquire about the supplier’s quality control processes and relevant certifications. Request documentation of their quality management systems and any industry-specific certifications. Suppliers should provide guarantees for their work, including warranties on repairs and replaced parts. Regular audits of their processes and customer feedback can also help maintain high-quality standards. -
What logistics considerations should I keep in mind when sourcing repair services?
Logistics play a crucial role in the efficiency of repair services. Consider the supplier’s location relative to your facility to minimize transportation delays. Understand their shipping methods, costs, and timelines for parts delivery. Additionally, ensure that the supplier has a clear process for handling emergencies and can provide on-site service if necessary, especially in regions where equipment downtime can significantly impact production. -
How can I handle disputes with suppliers regarding repair services?
To handle disputes effectively, establish clear terms and conditions in your contract, including service level agreements (SLAs). In the event of a dispute, maintain open communication with the supplier to discuss the issue. If necessary, escalate the matter to higher management or utilize mediation services. Having a well-defined resolution process in place can help mitigate issues and maintain a positive working relationship. -
What should I do if I encounter recurring issues with my air compressor after repairs?
If recurring issues arise, document the problems and communicate them promptly to your supplier. Request a thorough analysis of the repairs conducted and any follow-up services that may be required. It’s important to understand whether the issues are due to inadequate repairs, poor-quality parts, or operational misuse. If the supplier is unable to resolve the issue satisfactorily, consider exploring alternative suppliers with better service guarantees.
Important Disclaimer & Terms of Use
⚠️ Important Disclaimer
The information provided in this guide, including content regarding manufacturers, technical specifications, and market analysis, is for informational and educational purposes only. It does not constitute professional procurement advice, financial advice, or legal advice.
While we have made every effort to ensure the accuracy and timeliness of the information, we are not responsible for any errors, omissions, or outdated information. Market conditions, company details, and technical standards are subject to change.
B2B buyers must conduct their own independent and thorough due diligence before making any purchasing decisions. This includes contacting suppliers directly, verifying certifications, requesting samples, and seeking professional consultation. The risk of relying on any information in this guide is borne solely by the reader.
Strategic Sourcing Conclusion and Outlook for industrial air compressor repair near me
In conclusion, effective strategic sourcing for industrial air compressor repair is critical for international B2B buyers aiming to enhance operational efficiency and reduce costs. By focusing on preventative maintenance and predictive analysis, companies can significantly minimize downtime, which is essential for maintaining productivity in various sectors, from manufacturing to healthcare.
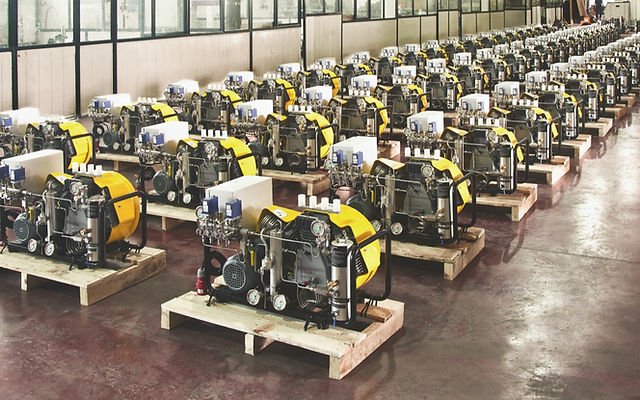
Illustrative Image (Source: Google Search)
Moreover, leveraging local service providers can yield faster response times and tailored solutions that meet specific operational needs. Buyers should prioritize partnerships with suppliers who offer comprehensive service programs, including energy audits and system optimizations, to ensure sustainable practices and cost-effectiveness.
As the global market evolves, the demand for advanced air compressor solutions will only grow. Buyers from Africa, South America, the Middle East, and Europe should actively engage with suppliers who demonstrate a commitment to innovation and customer-centric service. By doing so, they can secure reliable repair services that not only extend equipment lifespan but also contribute to overall business resilience.
Take action now: Evaluate your current air compressor service providers and explore new strategic partnerships to stay ahead in an increasingly competitive landscape.