Master Industrial Air Compressor Service: Key Strategies
Introduction: Navigating the Global Market for industrial air compressor service
In the rapidly evolving landscape of global manufacturing, industrial air compressor service stands as a cornerstone for efficiency and reliability. With compressed air often referred to as the “fourth utility,” its critical role in powering pneumatic tools, machinery, and production processes cannot be overstated. For international B2B buyers, particularly those operating in diverse markets such as Africa, South America, the Middle East, and Europe, understanding the nuances of air compressor services is essential for maintaining operational excellence.
This comprehensive guide delves into the essential aspects of industrial air compressor service, covering a wide array of topics including types of compressors, materials used, manufacturing and quality control standards, supplier selection, cost considerations, and current market trends. Additionally, it addresses frequently asked questions to equip buyers with the knowledge necessary for informed decision-making.
By navigating the complexities of air compressor service, B2B buyers will be empowered to enhance their sourcing strategies, optimize their operational workflows, and ultimately drive profitability. This guide serves not just as a reference tool but as a vital resource that enables businesses to harness the full potential of their compressed air systems. In an era where efficiency is paramount, understanding industrial air compressor service is not merely an option; it is a necessity for sustained competitive advantage in the global market.
Understanding industrial air compressor service Types and Variations
Type Name | Key Distinguishing Features | Primary B2B Applications | Brief Pros & Cons for Buyers |
---|---|---|---|
Rotary Screw Compressors | Continuous operation, high efficiency, low noise | Manufacturing, automotive assembly, food processing | Pros: Durable, low maintenance; Cons: Higher initial cost. |
Reciprocating Compressors | Intermittent operation, versatile, higher pressure | Construction, mining, HVAC systems | Pros: Cost-effective, flexible; Cons: Noisy, requires more maintenance. |
Oil-Free Compressors | No oil contamination, cleaner air output | Pharmaceutical, food and beverage, electronics | Pros: High air quality, compliant with strict regulations; Cons: Typically lower efficiency. |
Variable Speed Drive (VSD) Compressors | Adjusts speed based on demand, energy-efficient | Industrial plants, automotive, textile manufacturing | Pros: Energy savings, reduced wear; Cons: Higher upfront investment. |
Portable Compressors | Lightweight, mobile, easy to transport | Construction sites, outdoor events, emergency services | Pros: Versatile, easy to relocate; Cons: Limited capacity, may not suit all industrial needs. |
Rotary Screw Compressors
Rotary screw compressors are designed for continuous operation, making them ideal for industries that require a constant air supply. They are known for their high efficiency and low noise levels, which contribute to a more pleasant working environment. These compressors are particularly suitable for manufacturing, automotive assembly, and food processing applications where reliability and air quality are paramount. When purchasing, consider the initial investment versus the long-term savings on maintenance and energy costs.
Reciprocating Compressors
Reciprocating compressors are versatile and can handle varying pressure levels, making them suitable for a wide range of applications, including construction, mining, and HVAC systems. They operate intermittently and are generally more cost-effective than rotary screw compressors. However, they can be noisy and require more maintenance, which is a critical consideration for B2B buyers in noise-sensitive environments. Assessing the operational demands and maintenance capabilities is essential when selecting this type.
Oil-Free Compressors
Oil-free compressors are designed to eliminate oil contamination, ensuring a cleaner air output that meets stringent quality standards. They are essential in industries such as pharmaceuticals, food and beverage, and electronics, where air purity is critical. While they provide high air quality and compliance with regulations, they often have lower efficiency compared to oil-lubricated models. B2B buyers should evaluate the operational costs and regulatory requirements specific to their industry when considering oil-free options.
Variable Speed Drive (VSD) Compressors
VSD compressors automatically adjust their speed based on the air demand, leading to significant energy savings and reduced wear on components. They are particularly beneficial in industrial plants, automotive, and textile manufacturing, where air demand fluctuates. Although they come with a higher upfront investment, the long-term energy savings can justify the expense. Buyers should consider their air usage patterns and potential for energy cost reductions when exploring VSD compressor options.
Portable Compressors
Portable compressors are lightweight and easy to transport, making them ideal for construction sites, outdoor events, and emergency services. Their versatility allows for quick deployment in various applications, although they typically have limited capacity compared to stationary models. B2B buyers should assess the specific air requirements of their tasks and the balance between mobility and power when selecting portable compressors for their operations.
Related Video: Kaeser 5C Air Compressor Annual Service
Key Industrial Applications of industrial air compressor service
Industry/Sector | Specific Application of Industrial Air Compressor Service | Value/Benefit for the Business | Key Sourcing Considerations for this Application |
---|---|---|---|
Manufacturing | Powering pneumatic tools for assembly lines | Increased efficiency and reduced labor costs | Reliability, maintenance support, and energy efficiency ratings |
Construction | Operation of construction equipment (e.g., jackhammers) | Enhanced productivity and reduced downtime | Portability, durability, and service availability in remote areas |
Food and Beverage | Cleaning and maintaining hygiene standards | Compliance with health regulations and safety | Oil-free options, ease of cleaning, and low noise levels |
Automotive | Spray painting and surface preparation | Improved finish quality and reduced waste | Precision in air pressure control and compatibility with coatings |
Pharmaceuticals | Providing clean, dry air for processes | Ensured product quality and regulatory compliance | Air purity standards, certifications, and reliability of supply |
Manufacturing
In the manufacturing sector, industrial air compressors are vital for powering pneumatic tools used in assembly lines. These compressors enable consistent operation, which leads to increased efficiency and reduced labor costs. Buyers should consider the reliability and maintenance support of compressors, as unplanned downtime can significantly impact production schedules. Additionally, energy efficiency ratings are crucial for cost management, especially in regions where energy costs are high.
Construction
For the construction industry, air compressors are essential for operating equipment such as jackhammers and nail guns. Their use enhances productivity and minimizes downtime on job sites. When sourcing compressors, buyers should prioritize portability and durability, as construction sites often require equipment that can withstand harsh conditions. Furthermore, service availability in remote areas is critical, ensuring that any potential issues can be addressed swiftly to keep projects on track.
Food and Beverage
In the food and beverage industry, air compressors play a crucial role in maintaining hygiene standards. They are used for cleaning equipment and ensuring that surfaces are free from contaminants. Compliance with health regulations is paramount, and using oil-free air compressors can help meet these requirements. Buyers should focus on the ease of cleaning and low noise levels, as these factors contribute to a safe and efficient working environment.
Automotive
In the automotive sector, air compressors are used extensively for spray painting and surface preparation. The ability to maintain precise air pressure control ensures a smooth finish and reduces waste from overspray. Buyers should consider the compatibility of compressors with various coatings and the precision they offer. This not only enhances the quality of the final product but also streamlines the painting process, leading to higher customer satisfaction.
Pharmaceuticals
The pharmaceutical industry relies on industrial air compressors to provide clean, dry air for various processes, including packaging and product formulation. Ensuring product quality and regulatory compliance is critical in this sector. Buyers must pay attention to air purity standards and the certifications of the compressors they consider. Reliability of supply is also essential, as any interruption in air service can compromise production and compliance with strict industry regulations.
Related Video: Air Compressor (Basics, Parts, Diagram, Working & Applications) Explained with Animation
Strategic Material Selection Guide for industrial air compressor service
When selecting materials for industrial air compressor service, it is essential to consider the specific properties, advantages, and disadvantages of various materials. This analysis focuses on four common materials used in air compressor components: aluminum, stainless steel, carbon steel, and composite materials. Each material has distinct characteristics that can significantly impact performance, durability, and overall operational efficiency.
Aluminum
Key Properties:
Aluminum is lightweight, corrosion-resistant, and has excellent thermal conductivity. It typically has a temperature rating up to 150°C (302°F) and can handle moderate pressures, making it suitable for many compressor applications.
Pros & Cons:
The primary advantage of aluminum is its weight, which facilitates easier installation and maintenance. It is also resistant to rust and corrosion, extending the lifespan of components. However, aluminum can be more expensive than other materials and may not withstand high-pressure applications as effectively as steel.
Impact on Application:
Aluminum is ideal for applications where weight reduction is crucial, such as portable air compressors. However, it may not be suitable for environments with extreme temperatures or pressures.
Considerations for International Buyers:
Buyers should ensure compliance with international standards such as ASTM B221 for aluminum extrusions. In regions like Africa and South America, sourcing aluminum may be more challenging due to availability and cost fluctuations.
Stainless Steel
Key Properties:
Stainless steel boasts high corrosion resistance, excellent strength, and a temperature rating exceeding 300°C (572°F). It is capable of handling high pressures, making it a preferred choice for critical applications.
Pros & Cons:
The durability and resistance to corrosion make stainless steel an excellent long-term investment. However, its higher cost and weight compared to aluminum can be a disadvantage in applications where weight is a concern.
Impact on Application:
Stainless steel is particularly suitable for applications involving humid or corrosive environments, such as food processing or chemical manufacturing. Its robustness ensures reliable performance over time.
Considerations for International Buyers:
Buyers should be aware of the various grades of stainless steel (e.g., 304, 316) and their specific applications. Compliance with standards like ASTM A240 is crucial, especially in Europe where regulations are stringent.
Carbon Steel
Key Properties:
Carbon steel is known for its high strength and durability, with a temperature rating around 200°C (392°F). While it is not as corrosion-resistant as stainless steel, it is often treated to improve its resistance.
Pros & Cons:
The main advantage of carbon steel is its cost-effectiveness and strength. However, it is prone to rust and corrosion if not properly coated or maintained, which can lead to increased maintenance costs over time.
Impact on Application:
Carbon steel is suitable for structural components and applications where weight is not a critical factor. It is commonly used in stationary air compressors.
Considerations for International Buyers:
When sourcing carbon steel, buyers should consider local availability and treatment options to enhance corrosion resistance. Compliance with standards such as ASTM A36 is essential, particularly in regions with strict regulations.
Composite Materials
Key Properties:
Composite materials, often made from a combination of polymers and fillers, offer lightweight and corrosion-resistant properties. They can withstand moderate temperatures and pressures, making them versatile.
Pros & Cons:
The primary advantage of composites is their lightweight nature and resistance to corrosion, which can reduce maintenance needs. However, they may not offer the same strength and durability as metals, especially in high-pressure applications.
Impact on Application:
Composites are ideal for non-structural components and applications where weight savings are critical. They are increasingly used in portable air compressors.
Considerations for International Buyers:
Buyers should verify the specific properties of composite materials, as they can vary widely. Compliance with international standards for composites is still evolving, and buyers should stay informed about regulations in their respective regions.
Summary Table
Material | Typical Use Case for industrial air compressor service | Key Advantage | Key Disadvantage/Limitation | Relative Cost (Low/Med/High) |
---|---|---|---|---|
Aluminum | Portable air compressors | Lightweight and corrosion-resistant | Higher cost, limited high-pressure use | Medium |
Stainless Steel | Food processing, chemical manufacturing | High durability and corrosion resistance | Higher cost and weight | High |
Carbon Steel | Structural components in stationary compressors | Cost-effective and strong | Prone to rust without treatment | Low |
Composite Materials | Non-structural components in portable compressors | Lightweight and corrosion-resistant | Lower strength in high-pressure applications | Medium |
This guide provides a comprehensive overview of the materials used in industrial air compressor service, emphasizing the importance of selecting the right material based on application requirements and regional considerations.
In-depth Look: Manufacturing Processes and Quality Assurance for industrial air compressor service
The manufacturing processes and quality assurance practices for industrial air compressors are critical components that international B2B buyers must understand. This insight is especially valuable for buyers in diverse markets like Africa, South America, the Middle East, and Europe, where the quality and reliability of industrial equipment can vary significantly. Here’s a detailed overview of the typical manufacturing stages, quality control measures, and how buyers can verify supplier compliance with international standards.
Manufacturing Processes
1. Material Preparation
The manufacturing of industrial air compressors begins with the selection and preparation of materials. Common materials include:
- Aluminum and Steel: Used for the compressor housing and components due to their strength and durability.
- Copper: Often used in the construction of electrical components and piping due to its excellent conductivity.
- Plastic and Composites: Utilized in non-structural parts to reduce weight and costs.
Before production, materials undergo rigorous testing to ensure they meet specified standards. This may involve chemical analysis and mechanical testing for stress resistance.
2. Forming
The forming stage involves shaping the prepared materials into the required components. Key techniques used include:
- Casting: Metal components are poured into molds to form complex shapes, such as the compressor housing.
- Machining: Precision tools are used to cut and shape components, ensuring tight tolerances are met. This can include processes like turning, milling, and drilling.
- Welding: Various welding techniques (MIG, TIG, etc.) are employed to join metal parts, ensuring structural integrity.
Each method is selected based on the specific requirements of the compressor model being produced, balancing cost, time, and quality.
3. Assembly
During the assembly phase, the individual components are brought together to form the complete air compressor. This typically involves:
- Sub-assembly: Smaller components are first assembled into modules, such as the motor or the tank.
- Final Assembly: The modules are combined, and additional components like valves, filters, and control systems are installed.
- Alignment and Calibration: Components must be precisely aligned and calibrated to ensure optimal performance. This includes adjusting the pressure settings and ensuring that all moving parts operate smoothly.
Effective assembly practices are crucial for ensuring the reliability and efficiency of the final product.
4. Finishing
The finishing stage focuses on the aesthetic and functional aspects of the compressor. This may include:
- Surface Treatment: Processes like painting, powder coating, or anodizing are used to protect against corrosion and improve appearance.
- Quality Checks: Final inspections are conducted to ensure that the product meets design specifications and quality standards.
Finishing not only enhances the durability of the compressor but also contributes to its marketability.
Quality Assurance
Quality assurance is a vital aspect of the manufacturing process for industrial air compressors, ensuring that products meet both international and industry-specific standards.
International Standards
- ISO 9001: This standard focuses on quality management systems and is applicable to organizations that wish to ensure their products consistently meet customer and regulatory requirements.
- CE Marking: Required for products sold in the European Economic Area, indicating compliance with safety, health, and environmental protection standards.
Industry-Specific Standards
- API Standards: The American Petroleum Institute provides standards for compressors used in the oil and gas industry, emphasizing safety and efficiency.
- ASME Standards: The American Society of Mechanical Engineers establishes guidelines for pressure vessels and piping, ensuring structural integrity.
Quality Control Checkpoints
- Incoming Quality Control (IQC): Verification of raw materials and components before they enter the production process.
- In-Process Quality Control (IPQC): Ongoing inspections during manufacturing to catch defects early and ensure compliance with specifications.
- Final Quality Control (FQC): A comprehensive evaluation of the completed compressor, ensuring it meets all operational and safety standards before shipment.
Common Testing Methods
- Pressure Testing: Compressors are subjected to pressure tests to ensure they can handle operational demands without leaking.
- Performance Testing: Evaluating the compressor’s efficiency, noise levels, and output to ensure it meets specified performance criteria.
- Durability Testing: Simulating long-term use to identify potential failure points and assess the lifespan of components.
Verifying Supplier Quality Control
For international B2B buyers, verifying a supplier’s quality control processes is essential for ensuring product reliability and compliance. Here are several methods to consider:
- Supplier Audits: Conducting on-site audits allows buyers to assess the manufacturing facility, quality control practices, and adherence to international standards firsthand.
- Quality Reports: Request detailed quality assurance reports that outline testing results, compliance certifications, and any corrective actions taken in the past.
- Third-Party Inspections: Engaging independent inspection services can provide unbiased evaluations of the manufacturing process and final products.
QC Considerations for Global Buyers
B2B buyers from Africa, South America, the Middle East, and Europe should be aware of specific nuances related to quality control:
- Cultural and Regulatory Differences: Understanding local regulations and quality expectations is crucial for ensuring compliance and product acceptance in various markets.
- Language Barriers: Clear communication regarding quality standards and expectations is essential. Buyers may need to consider translation services for documentation and audits.
- Supply Chain Reliability: Establishing strong relationships with suppliers who prioritize quality can mitigate risks associated with equipment failure and enhance operational efficiency.
Conclusion
Understanding the manufacturing processes and quality assurance measures for industrial air compressors is vital for B2B buyers. By focusing on key manufacturing stages, adhering to international and industry-specific standards, and verifying supplier quality control, buyers can ensure they procure reliable and efficient equipment tailored to their operational needs. This diligence not only enhances productivity but also fosters long-term partnerships in the global marketplace.
Related Video: SMART Quality Control for Manufacturing
Comprehensive Cost and Pricing Analysis for industrial air compressor service Sourcing
Understanding the cost structure and pricing dynamics associated with industrial air compressor services is crucial for international B2B buyers, especially in regions like Africa, South America, the Middle East, and Europe. This analysis will help buyers make informed decisions and optimize their procurement processes.
Cost Components of Industrial Air Compressor Services
-
Materials: The primary costs stem from the raw materials used in manufacturing air compressors, including metals and polymers. The quality and source of these materials can significantly affect pricing. For instance, high-grade steel or aluminum will increase costs but enhance durability.
-
Labor: Labor costs vary widely depending on the region. In developed markets, skilled labor may demand higher wages, whereas emerging markets might offer competitive labor costs. Understanding local labor rates is essential for cost estimation.
-
Manufacturing Overhead: This includes costs related to factory operations, such as utilities, rent, and equipment maintenance. Overhead can be a substantial part of the overall cost, particularly in regions with higher operational costs.
-
Tooling: The initial costs for molds and dies used in manufacturing can be significant, particularly for custom or specialized compressor designs. Buyers should consider the tooling costs when evaluating suppliers.
-
Quality Control (QC): Ensuring that compressors meet industry standards requires investment in quality assurance processes. This cost is often reflected in the price of the service.
-
Logistics: Shipping and handling costs can vary based on the destination, volume, and weight of the compressors. Buyers should factor in these logistics costs when assessing total expenditures.
-
Margin: Suppliers typically include a profit margin in their pricing. Understanding the market standards for margins in different regions can aid in negotiations.
Price Influencers
Several factors can influence the pricing of industrial air compressor services:
-
Volume/MOQ: Purchasing in larger quantities often leads to discounts. Understanding the minimum order quantities (MOQ) can help buyers negotiate better prices.
-
Specifications/Customization: Custom-built compressors tailored to specific needs will typically incur higher costs due to unique manufacturing processes. Buyers should clearly define their requirements to avoid unexpected expenses.
-
Materials and Quality Certifications: Higher-quality materials and compliance with international quality standards (e.g., ISO certifications) can increase costs but also enhance performance and reliability.
-
Supplier Factors: The reputation and reliability of the supplier play a significant role in pricing. Established suppliers may charge more but can offer superior service and warranty options.
-
Incoterms: The terms of delivery can affect pricing. Understanding Incoterms (International Commercial Terms) is crucial for buyers to estimate total costs accurately, including transportation and insurance.
Buyer Tips for Cost Efficiency
-
Negotiation: Engage suppliers in open discussions about pricing, focusing on long-term partnerships that could lead to better rates. Consider leveraging existing relationships to negotiate favorable terms.
-
Total Cost of Ownership (TCO): Assess the total cost, including purchase price, maintenance, energy consumption, and downtime. A lower initial cost may not always equate to a better deal if the long-term expenses are high.
-
Pricing Nuances: Be aware that pricing structures may vary significantly between regions. For instance, buyers in Europe may face different tariffs and regulations compared to those in Africa or South America.
-
Market Research: Conduct thorough research on market trends and competitor pricing. This knowledge can empower buyers during negotiations and ensure they receive competitive offers.
-
Request for Proposals (RFPs): Utilize RFPs to solicit competitive bids from multiple suppliers. This process not only fosters competition but also provides insights into the market pricing landscape.
Disclaimer
Prices for industrial air compressor services can fluctuate based on various factors, including market conditions and supplier capabilities. This analysis provides indicative pricing guidance but should be supplemented with specific quotes from suppliers to obtain accurate cost estimates.
Spotlight on Potential industrial air compressor service Manufacturers and Suppliers
This section looks at several manufacturers active in the ‘industrial air compressor service’ market. This is a representative sample for illustrative purposes; B2B buyers must conduct extensive due diligence before any transaction. Information is synthesized from public sources and general industry knowledge.
Essential Technical Properties and Trade Terminology for industrial air compressor service
Key Technical Properties of Industrial Air Compressors
When selecting an industrial air compressor, understanding the technical specifications is crucial for making informed purchasing decisions. Here are several key properties that international B2B buyers should consider:
-
Horsepower (HP)
Horsepower measures the power output of the compressor’s motor. It directly affects the compressor’s performance and the amount of air it can produce. Higher horsepower ratings typically indicate greater efficiency and the ability to handle more demanding tasks. Buyers should assess their air usage needs to choose a compressor with an appropriate horsepower rating. -
Cubic Feet per Minute (CFM)
CFM represents the volume of air the compressor can deliver per minute. This metric is essential for determining whether a compressor can meet the air demand of specific applications. For instance, tools with higher CFM requirements will need compressors capable of delivering sufficient airflow consistently. Buyers should calculate the total CFM required for their operations to ensure they select a compressor that can handle peak demands. -
Pounds per Square Inch (PSI)
PSI indicates the pressure level at which the compressor operates. Different applications require different pressure levels; for example, pneumatic tools typically function effectively within a range of 70-90 PSI. Understanding the required PSI for your specific applications will help ensure the selected compressor can maintain optimal performance. -
Tank Size
The size of the storage tank impacts how much compressed air is available on demand. Larger tanks can store more compressed air, which is beneficial for operations that require a continuous supply without frequent cycling of the compressor. Buyers should consider their operational needs and the frequency of air usage when determining the appropriate tank size. -
Noise Level (dB)
Noise levels, measured in decibels (dB), are crucial for workplace safety and comfort. Compressors can be loud, and excessive noise can lead to hearing damage and reduced productivity. Selecting a compressor with a lower noise level can enhance the working environment, especially in settings where employees are in close proximity to the equipment. -
Energy Efficiency Rating
Energy efficiency is an essential consideration for reducing operational costs. Compressors with higher efficiency ratings consume less electricity, resulting in lower utility bills and a reduced carbon footprint. Buyers should look for compressors that meet or exceed industry efficiency standards to optimize long-term savings.
Common Trade Terminology in Industrial Air Compressor Service
Familiarity with industry jargon is vital for effective communication and negotiation in the B2B marketplace. Here are some common terms:
-
OEM (Original Equipment Manufacturer)
Refers to the company that originally manufactures the compressor or its components. Understanding OEM specifications can ensure buyers receive parts and service that meet original design standards, maintaining equipment reliability. -
MOQ (Minimum Order Quantity)
This term indicates the smallest quantity of a product that a supplier is willing to sell. Knowing the MOQ helps buyers plan their purchasing strategies and budget effectively, especially when dealing with bulk orders. -
RFQ (Request for Quotation)
An RFQ is a formal request for suppliers to provide pricing and terms for specific products or services. Utilizing RFQs can facilitate competitive pricing and ensure buyers receive comprehensive proposals that meet their operational needs. -
Incoterms (International Commercial Terms)
These are standardized trade terms that define the responsibilities of buyers and sellers in international transactions. Familiarity with Incoterms helps buyers understand shipping costs, risks, and responsibilities, ensuring smoother logistics and compliance with international trade regulations. -
Aftercooler
An aftercooler is a heat exchanger used to cool the compressed air before it enters the storage tank. Understanding this component is crucial, as it helps reduce moisture in the air and improves system efficiency, prolonging equipment life.
By grasping these essential properties and terms, international B2B buyers can make informed decisions when investing in industrial air compressors, ultimately enhancing operational efficiency and reducing costs.
Navigating Market Dynamics, Sourcing Trends, and Sustainability in the industrial air compressor service Sector
Market Overview & Key Trends
The industrial air compressor service sector is witnessing significant growth driven by various global factors. The increasing demand for energy-efficient and reliable compressed air systems is a primary driver. Industries are now prioritizing operational efficiency and cost reduction, pushing suppliers to innovate and offer advanced technologies such as Variable Speed Drive (VSD) compressors, which optimize energy consumption.
Emerging trends include a rise in smart compressor technologies that incorporate IoT capabilities, enabling real-time monitoring and predictive maintenance. This shift not only enhances operational efficiency but also reduces downtime, which is critical for manufacturers in competitive markets. Additionally, there is a notable increase in the adoption of oil-free compressors, particularly in sectors such as food and beverage, pharmaceuticals, and electronics, where air purity is paramount.
International B2B buyers, particularly from Africa, South America, the Middle East, and Europe, should be aware of regional market dynamics. In Africa and South America, infrastructure development is accelerating, creating new opportunities for compressor services. Meanwhile, the Middle East is focusing on diversifying its economy, leading to investments in manufacturing sectors that rely heavily on compressed air systems. In Europe, stringent environmental regulations are fostering a demand for greener technologies, thus influencing sourcing decisions.
Sustainability & Ethical Sourcing in B2B
Sustainability has become a cornerstone of strategic sourcing in the industrial air compressor service sector. The environmental impact of compressed air systems is significant, with energy consumption accounting for a large portion of operational costs. Buyers are increasingly seeking solutions that reduce energy usage and emissions, emphasizing the importance of sustainable practices.
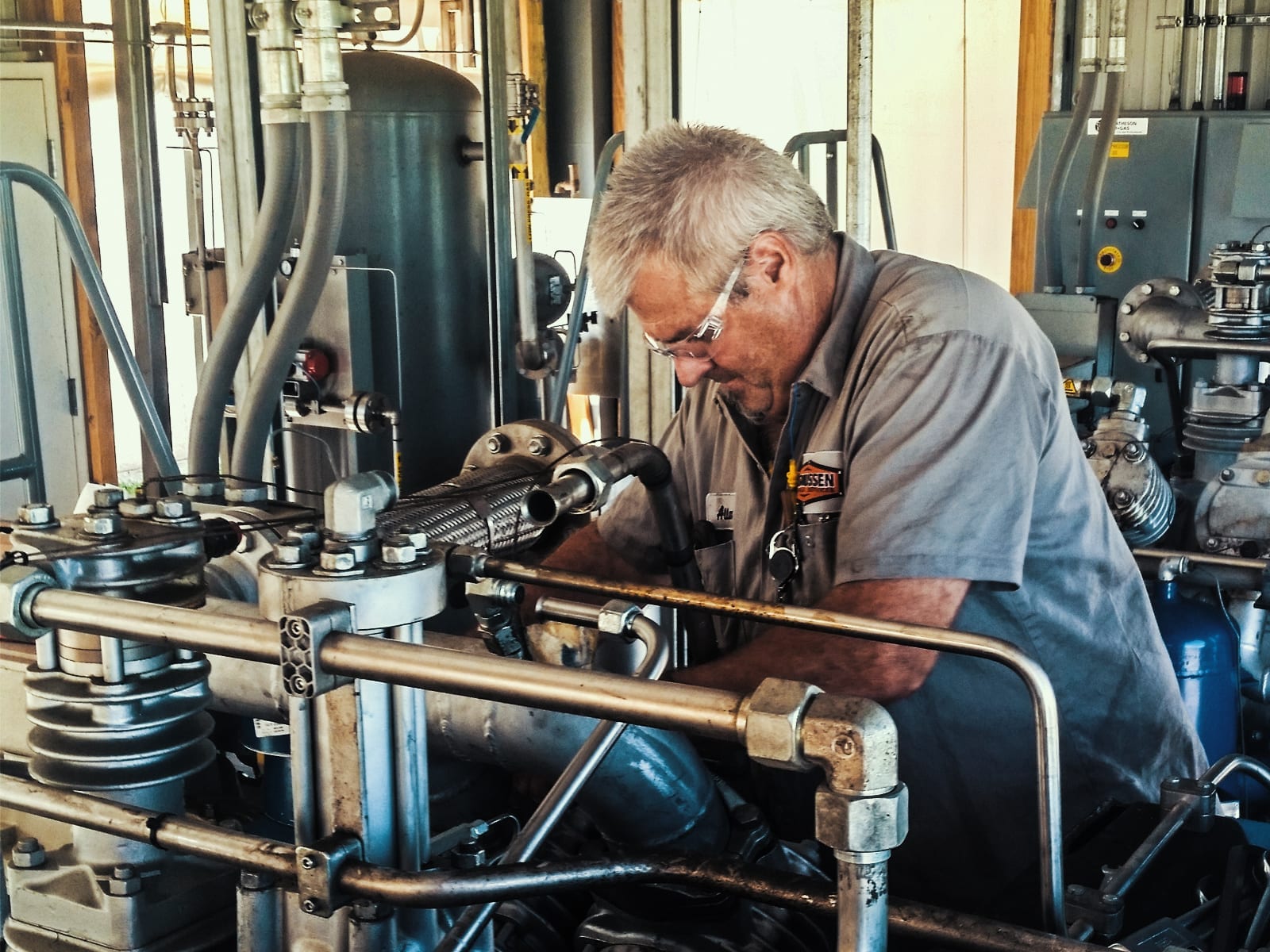
Illustrative Image (Source: Google Search)
Ethical sourcing is also gaining traction, with a focus on supply chain transparency. B2B buyers should consider suppliers that demonstrate a commitment to sustainability through certifications such as ISO 14001 for environmental management and ISO 50001 for energy management. Moreover, sourcing materials and components that are recyclable or derived from sustainable practices is becoming a priority. This not only helps mitigate environmental impact but also aligns with corporate social responsibility goals.
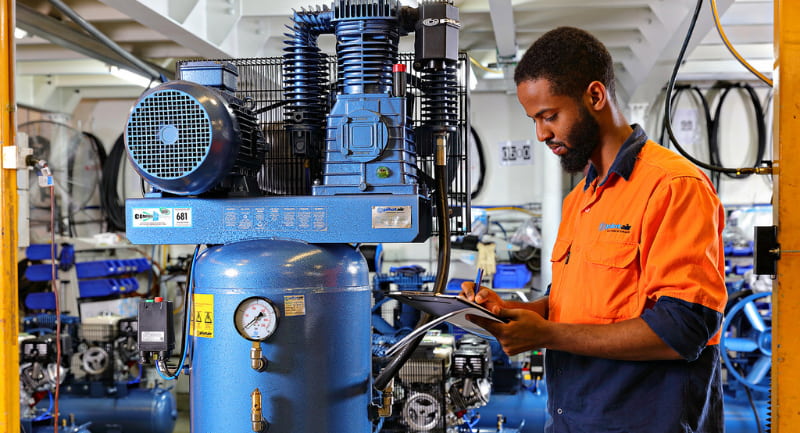
Illustrative Image (Source: Google Search)
Investing in “green” technologies, such as energy-efficient compressors and systems designed for lower emissions, can enhance a company’s market reputation and appeal to environmentally conscious consumers. Buyers should actively seek partnerships with manufacturers and service providers that prioritize sustainability in their operations.
Brief Evolution/History
The evolution of the industrial air compressor service sector traces back to the late 19th century with the advent of the reciprocating compressor, primarily used in mining and construction. Over the decades, advancements led to the introduction of rotary screw compressors in the mid-20th century, which revolutionized the industry by offering higher efficiency and continuous operation.
As industries expanded and diversified, the need for reliable and efficient compressed air systems became paramount. The late 20th and early 21st centuries saw the introduction of automation and digital technologies, transforming how air compressors are monitored and maintained. Today, the focus is not only on performance but also on sustainability and ethical sourcing, reflecting the changing values of global markets and consumers. For international B2B buyers, understanding this evolution is crucial for making informed sourcing decisions and aligning with future market trends.
Related Video: KTU S5 – Industrial Economics and Foreign Trade – Module – 1 (Part A)
Frequently Asked Questions (FAQs) for B2B Buyers of industrial air compressor service
-
How can I effectively vet suppliers for industrial air compressor services?
When vetting suppliers, prioritize their experience in the industry and the specific type of air compressor service you require. Look for suppliers with a proven track record, verified customer testimonials, and relevant certifications. It’s also beneficial to request case studies that demonstrate their capability in handling similar projects. Conducting a background check on their financial stability and operational capacity can further ensure they can meet your demands, especially in international trade where reliability is crucial. -
What customization options should I consider for industrial air compressor services?
Customization options vary widely based on your specific needs, including pressure requirements, size constraints, and intended applications. Discuss with potential suppliers about their ability to tailor compressors to meet your operational needs, such as integrating specific features or enhancing energy efficiency. Additionally, inquire about the flexibility of their designs to accommodate future scalability or modifications, ensuring that your investment remains relevant as your operational demands evolve. -
What are the typical minimum order quantities (MOQ) and lead times for air compressor services?
Minimum order quantities often depend on the supplier’s production capabilities and the complexity of the service required. Generally, MOQs can range from single units to bulk orders for larger projects. Lead times can vary significantly based on customization, availability of components, and shipping logistics. When negotiating with suppliers, clarify these terms upfront to align your project timelines with their production schedules and avoid potential delays. -
What payment terms are standard for international air compressor service transactions?
Payment terms can vary widely among suppliers but often include options like advance payment, payment upon delivery, or a letter of credit for larger orders. It’s essential to discuss and agree upon payment terms that protect both parties. For international transactions, consider the implications of currency exchange rates and transaction fees. Using secure payment methods can mitigate risks associated with fraud, especially when dealing with new suppliers. -
How important are quality assurance (QA) certifications for air compressor services?
Quality assurance certifications are critical as they reflect a supplier’s commitment to maintaining high standards in their products and services. Look for certifications such as ISO 9001, which indicate adherence to international quality management principles. Suppliers with robust QA processes are more likely to deliver reliable, efficient, and safe products. Request documentation of their QA processes and any third-party audits to ensure that they meet your quality expectations. -
What logistics considerations should I keep in mind when sourcing air compressor services?
Logistics play a vital role in the timely delivery of air compressors and associated services. Assess the supplier’s shipping capabilities, including their experience with international shipping regulations and customs procedures. Consider factors such as shipping costs, estimated delivery times, and potential delays due to geopolitical or environmental factors. Establish clear communication with your supplier regarding logistics to avoid misunderstandings and ensure a smooth delivery process. -
How can disputes over air compressor service contracts be effectively managed?
Dispute management should begin with a well-drafted contract that clearly outlines the terms, including service expectations, timelines, and responsibilities. Include a clause for mediation or arbitration to resolve conflicts amicably before escalating to legal action. Open communication is key; maintain a good relationship with your supplier to address issues as they arise. Understanding local laws and regulations related to international trade can also aid in navigating disputes effectively. -
What are the common challenges faced by international B2B buyers in sourcing air compressor services?
International B2B buyers often encounter challenges such as language barriers, differing regulatory standards, and cultural differences in business practices. Additionally, logistical issues, including shipping delays and customs clearance, can complicate the procurement process. To mitigate these challenges, engage with suppliers who have experience in your region and can provide local support. Establishing a clear line of communication and utilizing technology for project management can also help streamline the sourcing process.
Important Disclaimer & Terms of Use
⚠️ Important Disclaimer
The information provided in this guide, including content regarding manufacturers, technical specifications, and market analysis, is for informational and educational purposes only. It does not constitute professional procurement advice, financial advice, or legal advice.
While we have made every effort to ensure the accuracy and timeliness of the information, we are not responsible for any errors, omissions, or outdated information. Market conditions, company details, and technical standards are subject to change.
B2B buyers must conduct their own independent and thorough due diligence before making any purchasing decisions. This includes contacting suppliers directly, verifying certifications, requesting samples, and seeking professional consultation. The risk of relying on any information in this guide is borne solely by the reader.
Strategic Sourcing Conclusion and Outlook for industrial air compressor service
In conclusion, strategic sourcing for industrial air compressor services is crucial for international buyers seeking efficiency, reliability, and cost-effectiveness. By understanding the diverse types of compressors and their applications, businesses can make informed decisions that align with their operational needs. Prioritizing preventative maintenance and optimizing compressor systems not only enhances productivity but also extends equipment life, leading to significant cost savings.
B2B buyers from Africa, South America, the Middle East, and Europe should consider the local market dynamics and supplier capabilities when sourcing compressors. Engaging with reputable suppliers who offer comprehensive support and maintenance services can further mitigate risks associated with downtime and inefficiencies.
Looking ahead, the demand for innovative and sustainable air compressor solutions is set to grow, driven by advancements in technology and an increasing focus on energy efficiency. Buyers are encouraged to stay informed about market trends and consider partnerships that foster long-term value creation. Investing in strategic sourcing today will position businesses for success in an evolving industrial landscape, ensuring they remain competitive and resilient in the face of future challenges.