Master Kiss Cutting: The Ultimate Cost-Saving Guide (2025)
Introduction: Navigating the Global Market for kiss cutting
In today’s competitive landscape, sourcing kiss cutting services can be a daunting challenge for international B2B buyers, especially when navigating diverse market conditions across regions like Africa, South America, the Middle East, and Europe. Kiss cutting, a specialized die-cutting technique that allows for precise cuts through adhesive materials while preserving the backing, plays a crucial role in creating products such as stickers, labels, and gaskets. Understanding the nuances of this process is essential for companies looking to optimize their production methods and ensure product quality.
This comprehensive guide delves into the various aspects of kiss cutting, covering types of kiss cutting techniques, diverse applications across industries, and essential tips for vetting suppliers. Additionally, we will explore cost considerations and best practices for engaging with manufacturers to ensure that you secure the best value for your investment. By equipping B2B buyers with actionable insights and a clear understanding of the kiss cutting process, this guide aims to empower informed purchasing decisions that can enhance product offerings and improve operational efficiency.
Whether you’re sourcing kiss cutting services from Thailand to Spain, our guide will provide the knowledge necessary to navigate the global market effectively, helping you to make strategic choices that align with your business goals.
Understanding kiss cutting Types and Variations
Type Name | Key Distinguishing Features | Primary B2B Applications | Brief Pros & Cons for Buyers |
---|---|---|---|
Manual Kiss Cutting | Involves manual tools like knives and rulers for precision. | Small series production, prototyping | Pros: Cost-effective, simple setup. Cons: Low accuracy, time-consuming for larger batches. |
Steel Rule Die Cutting | Uses a specialized die to achieve complex shapes. | High-volume sticker production | Pros: High precision, suitable for complex designs. Cons: High initial setup costs, requires specialized equipment. |
Plotter Kiss Cutting | Utilizes a digital plotter for cutting shapes. | Custom sticker and label production | Pros: Flexibility in design, no specialized tooling required. Cons: Slower production speed, limited material thickness. |
Laser Kiss Cutting | Employs a laser for precise, shallow cuts. | High-detail applications, intricate designs | Pros: High accuracy, minimal material waste. Cons: Risk of damaging adhesive properties, higher operational costs. |
Rotary Kiss Cutting | Involves a rotary die press for continuous production. | Mass production of labels and stickers | Pros: Fast production rates, consistent quality. Cons: High initial investment, less flexibility for design changes. |
What is Manual Kiss Cutting and When Should You Use It?
Manual kiss cutting is the simplest form of this technique, utilizing basic tools like knives and rulers. This method is particularly suitable for small batch productions or prototyping where precision isn’t the highest priority. B2B buyers should consider this option when they are testing designs or need a cost-effective solution for limited runs. However, the trade-off is that it can be time-consuming and may lack the accuracy required for larger projects.
Why Choose Steel Rule Die Cutting for Your Business Needs?
Steel rule die cutting is a more advanced method that involves a specialized die to create complex shapes with high precision. This technique is ideal for high-volume sticker production where consistency and detail are crucial. B2B buyers should weigh the benefits of precision against the initial investment in equipment, as the setup costs can be significant. However, once established, this method can yield high-quality products efficiently.
How Does Plotter Kiss Cutting Enhance Customization?
Plotter kiss cutting leverages digital technology to cut shapes without the need for specialized tools. This method is excellent for custom sticker and label production, allowing for intricate designs and quick adjustments. B2B buyers should consider this option for projects requiring flexibility and rapid turnaround times. However, it may come with slower production speeds compared to other methods, which could impact larger orders.
What Are the Benefits and Drawbacks of Laser Kiss Cutting?
Laser kiss cutting utilizes a laser to achieve precise, shallow cuts, making it suitable for high-detail applications. This method is advantageous for intricate designs and minimizes material waste, appealing to B2B buyers focused on sustainability. However, caution is needed as the laser can damage the adhesive properties of certain materials, and operational costs may be higher than traditional methods.
Why Opt for Rotary Kiss Cutting in Mass Production?
Rotary kiss cutting employs a rotary die press, making it suitable for mass production of labels and stickers. This technique offers fast production rates and consistent quality, which is crucial for businesses looking to scale. B2B buyers should consider this method if they have high-volume needs, but they must also be prepared for the high initial investment and reduced flexibility for design changes.
Key Industrial Applications of kiss cutting
Industry/Sector | Specific Application of Kiss Cutting | Value/Benefit for the Business | Key Sourcing Considerations for this Application |
---|---|---|---|
Label Manufacturing | Production of custom adhesive labels | Enables quick production of labels with various shapes, enhancing branding and marketing efforts. | Quality of adhesive, compatibility with printing processes, and ability to handle various materials. |
Automotive Industry | Creating gaskets and seals for automotive parts | Provides precise cuts for efficient sealing, reducing the risk of leaks and improving performance. | Material durability, temperature resistance, and compliance with automotive standards. |
Electronics | Production of foam and rubber pads for devices | Ensures proper cushioning and protection of sensitive components, enhancing product longevity. | Material density, adhesive strength, and compatibility with electronic components. |
Packaging Industry | Kiss cutting of packaging materials for easy opening | Simplifies user experience by providing easy-to-open packaging, reducing frustration and waste. | Material thickness, adhesive quality, and environmental considerations for sustainable packaging. |
Consumer Goods | Custom stickers and decals for branding | Allows for creative branding solutions that can be easily applied and removed, boosting customer engagement. | Design flexibility, adhesive type, and production speed to meet market demands. |
How is Kiss Cutting Used in Label Manufacturing?
In the label manufacturing sector, kiss cutting is employed to create custom adhesive labels that are tailored to specific branding needs. This technique allows for intricate designs while ensuring that the backing paper remains intact, facilitating easy peeling for end-users. For international B2B buyers, especially from regions like Africa and South America, sourcing high-quality adhesive materials that can withstand varying environmental conditions is crucial. Additionally, compatibility with different printing technologies must be considered to ensure optimal production efficiency.
What Role Does Kiss Cutting Play in the Automotive Industry?
In the automotive industry, kiss cutting is vital for producing gaskets and seals that prevent leaks in various engine components. This method allows manufacturers to achieve precise cuts that fit perfectly in the required spaces, enhancing the overall performance and safety of vehicles. For buyers in the Middle East and Europe, it’s essential to evaluate the durability of materials used, particularly under high temperatures and pressures, to ensure compliance with industry regulations and standards.
How is Kiss Cutting Beneficial for Electronics?
Kiss cutting is widely used in the electronics sector to create foam and rubber pads that protect sensitive components within devices. This process ensures that the pads are cut to exact specifications, providing the necessary cushioning to prevent damage during shipping and usage. International buyers, particularly from Europe and Africa, should prioritize sourcing materials that offer high adhesive strength and durability to maintain the integrity of electronic products over time.
How Does Kiss Cutting Enhance Packaging Solutions?
In the packaging industry, kiss cutting is utilized to create packaging materials that are easy to open, enhancing user experience. This method allows for the production of perforated sections that can be easily torn, minimizing frustration for consumers. Buyers from South America and Africa should consider the thickness and quality of materials when sourcing kiss-cut packaging solutions, as these factors can significantly impact the usability and sustainability of the final product.
Why is Kiss Cutting Important for Consumer Goods?
Kiss cutting is essential for producing custom stickers and decals that serve as effective branding tools in the consumer goods sector. This technique allows brands to create unique designs that can be easily applied and removed by consumers, fostering engagement and loyalty. For international buyers, especially in regions like Europe, understanding the flexibility of design options and the types of adhesives used is important to ensure the stickers meet market expectations and consumer preferences.
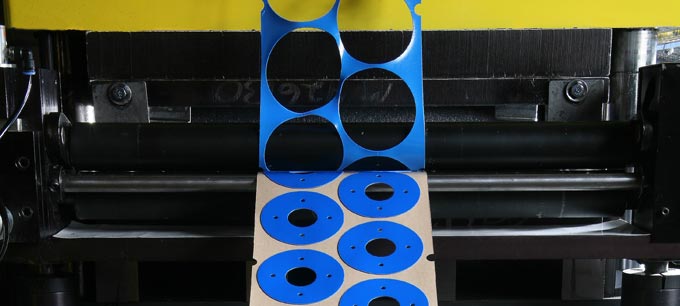
A stock image related to kiss cutting.
3 Common User Pain Points for ‘kiss cutting’ & Their Solutions
Scenario 1: Navigating Inconsistent Cut Depth in Kiss Cutting
The Problem:
B2B buyers often encounter issues with inconsistent cut depths when utilizing kiss cutting techniques. This inconsistency can lead to products that either tear upon peeling or remain stuck to the backing, resulting in waste and increased production costs. Buyers may find themselves frustrated, especially when working with diverse materials or intricate designs, as improper cuts can compromise product quality and brand reputation.
The Solution:
To mitigate issues with cut depth, it’s crucial to invest in high-quality kiss cutting machinery that allows for precise adjustments. Opt for equipment with adjustable pressure settings and depth controls, which enable fine-tuning for various materials. Collaborating with an experienced converter can also provide insights into the best practices for specific substrates. Additionally, conducting regular quality checks and testing prototypes can help ensure that the kiss cutting process meets the desired specifications. By implementing these strategies, buyers can enhance their production efficiency and reduce the incidence of defective products.
Scenario 2: Managing Material Shifts During Production
The Problem:
Material shifts during the kiss cutting process can lead to misalignment and result in imperfect rolls, which complicates downstream applications like labeling or packaging. Buyers may face challenges when their materials do not remain stationary, causing variations in cut precision. This can lead to inconsistent product quality and increased waste, severely affecting operational efficiency.
The Solution:
To address material shifts, it is advisable to use a specialized kiss cutting machine equipped with features that maintain tension and alignment throughout the process. Implementing a robust fixturing system can also prevent movement during production. Moreover, choosing the right backing material that adheres well to the substrate can help keep everything in place. Regularly training staff on handling techniques and machine operation can further reduce the risk of material misalignment, ensuring that the kiss cutting process runs smoothly and efficiently.
Scenario 3: Overcoming Challenges with Adhesive Quality and Compatibility
The Problem:
B2B buyers frequently deal with adhesive quality issues that can arise during kiss cutting, particularly when using pressure-sensitive adhesives. If the adhesive fails to bond properly due to incompatibility with the substrate or environmental factors, it can lead to product failures, increased returns, and dissatisfied customers. This challenge is particularly pronounced when sourcing materials from different regions, where adhesive formulations may vary.
The Solution:
To ensure optimal adhesive performance, it’s essential to conduct compatibility tests between the adhesive and the substrate prior to mass production. Buyers should work closely with suppliers to select adhesives that are specifically formulated for their chosen materials and environmental conditions. Additionally, implementing stringent quality control processes to monitor adhesive application and performance can help detect potential issues early. Educating teams about the importance of adhesive properties and their interaction with various substrates can further enhance product reliability, leading to improved customer satisfaction and reduced costs associated with returns or rework.
By addressing these common pain points with actionable solutions, B2B buyers can enhance their kiss cutting processes, leading to more efficient production and better overall product quality.
Strategic Material Selection Guide for kiss cutting
What Are the Key Materials Used in Kiss Cutting?
Kiss cutting is a versatile die-cutting process that relies on specific materials to achieve optimal results. Understanding the properties, advantages, and limitations of these materials is crucial for international B2B buyers, especially those in diverse markets like Africa, South America, the Middle East, and Europe. Below, we analyze four common materials used in kiss cutting.
Which Adhesive Tapes Are Suitable for Kiss Cutting?
Key Properties: Adhesive tapes typically consist of a backing material coated with a pressure-sensitive adhesive. They are designed for low-stress applications and can withstand moderate temperature variations.
Pros & Cons: Adhesive tapes are relatively inexpensive and easy to apply. They offer good durability for short-term applications. However, they may not perform well under high temperatures or in harsh environmental conditions, limiting their use in demanding applications.
Impact on Application: Adhesive tapes are compatible with various surfaces, making them ideal for temporary bonding or labeling. However, their effectiveness can diminish in high-humidity environments.
Considerations for International Buyers: Buyers should ensure that the adhesive tapes comply with local standards, such as ASTM D-1000 in the U.S. or EN 60454 in Europe. Understanding local preferences for adhesive strength and temperature resistance is also crucial.
How Do Foam Tapes Perform in Kiss Cutting Applications?
Key Properties: Foam tapes are made from various foam materials and can have adhesive on one or both sides. They are designed to compress under pressure, providing excellent cushioning and sealing properties.
Pros & Cons: Foam tapes are highly versatile and can accommodate uneven surfaces. They are durable and provide good insulation. However, they can be more expensive than standard adhesive tapes and may require specialized equipment for kiss cutting.
Impact on Application: Foam tapes are particularly effective in automotive and construction applications where vibration dampening is necessary. Their compressibility allows for a tight seal, but they may not adhere well to oily or contaminated surfaces.
Considerations for International Buyers: Buyers should verify that foam tapes meet relevant standards, such as ISO 9001 for quality management systems. Additionally, understanding the local climate’s impact on foam tape performance is essential.
What Role Do Gaskets Play in Kiss Cutting Processes?
Key Properties: Gaskets are mechanical seals made from various materials, including rubber, PTFE, and cork. They are designed to fill gaps between static surfaces and can withstand varying pressure and temperature conditions.
Pros & Cons: Gaskets provide excellent sealing capabilities and are essential for preventing leaks. However, they can be costly and may require precise cutting techniques to ensure a proper fit.
Impact on Application: Gaskets are critical in industries such as automotive and aerospace, where fluid containment is vital. The choice of gasket material can significantly affect the performance and longevity of the seal.
Considerations for International Buyers: Compliance with industry standards, such as ASTM F104 or DIN 28090, is crucial for gasket materials. Buyers should also consider the specific media compatibility when selecting gasket materials for kiss cutting.
How Are O-Rings Used in Kiss Cutting Applications?
Key Properties: O-rings are circular seals made from elastomeric materials that can withstand pressure and temperature variations. They are available in various materials, including rubber and silicone.
Pros & Cons: O-rings are highly effective for sealing applications and are relatively inexpensive. However, they may not be suitable for extreme temperatures or aggressive chemicals, which can degrade their performance.
Impact on Application: O-rings are widely used in hydraulic and pneumatic systems, where they prevent fluid leakage. The choice of material is critical for ensuring compatibility with the specific media being contained.
Considerations for International Buyers: Buyers should ensure that O-rings meet international standards such as ISO 3601. Understanding the chemical compatibility of O-ring materials is essential, especially in industries with stringent safety regulations.
Summary Table of Strategic Material Selection for Kiss Cutting
Material | Typical Use Case for Kiss Cutting | Key Advantage | Key Disadvantage/Limitation | Relative Cost (Low/Med/High) |
---|---|---|---|---|
Adhesive Tapes | Temporary bonding and labeling | Inexpensive and easy to apply | Limited performance in harsh conditions | Low |
Foam Tapes | Automotive and construction | Excellent cushioning and sealing | Higher cost and specialized equipment needed | Med |
Gaskets | Automotive and aerospace sealing | Effective leak prevention | Can be costly and requires precision | High |
O-Rings | Hydraulic and pneumatic systems | Highly effective for sealing | Not suitable for extreme conditions | Med |
This guide provides valuable insights into the materials used in kiss cutting, helping international B2B buyers make informed decisions that align with their specific applications and regional requirements.
In-depth Look: Manufacturing Processes and Quality Assurance for kiss cutting
What Are the Main Stages of the Kiss Cutting Manufacturing Process?
The kiss cutting process is a specialized type of die cutting that involves several critical stages, from material preparation to finishing. Understanding these stages can help B2B buyers make informed decisions about their manufacturing partners.
Material Preparation: How Is the Right Material Selected for Kiss Cutting?
The first step in kiss cutting involves selecting the appropriate materials, typically adhesive-backed foils or papers. Buyers should consider the following aspects:
- Material Types: Common materials include vinyl, paper, and specialty adhesives. Each material has its unique properties that can affect the kiss cutting process.
- Thickness and Adhesive Properties: The thickness of the material and the type of adhesive used are crucial. The adhesive must be compatible with the intended application, whether for stickers, labels, or other products.
Once the materials are selected, they are prepared for the cutting process, which may involve cleaning and ensuring that they are free from contaminants.
Forming: What Techniques Are Used in the Kiss Cutting Process?
The forming stage is where the actual kiss cutting takes place. Here, several techniques can be utilized:
- Steel Rule Die Cutting: This traditional method uses a die to create specific shapes and is effective for high-volume production. However, it requires significant upfront investment in tooling.
- Laser Kiss Cutting: This technique employs a laser to make shallow cuts in the material. It allows for high precision but can be limited by the types of materials that can withstand the heat.
- Plotter Kiss Cutting: For smaller runs or intricate designs, a digital cutting plotter can be used. This method is more flexible but may not offer the same speed as die cutting.
The choice of technique will depend on factors such as production volume, design complexity, and material compatibility.
Assembly: How Are Kiss Cut Products Prepared for Final Use?
In the assembly stage, kiss cut products are typically left on their backing material, allowing for easy peeling and application. This stage may involve:
- Quality Checks: Ensuring that the kiss cuts are clean and the adhesive properties are intact is essential. Any defects at this stage can compromise the final product’s usability.
- Packaging: Proper packaging is crucial to prevent damage during shipping. Buyers should inquire about the supplier’s packaging practices to ensure product integrity.
Finishing: What Are the Final Steps in Kiss Cutting Production?
The finishing stage includes any additional processes that enhance the product’s functionality or appearance. This may involve:
- Trimming and Cutting: Ensuring that the edges of kiss cut products are clean and free of defects.
- Labeling and Documentation: Providing essential information about the product, such as specifications and usage instructions.
These finishing touches not only improve the product’s appeal but also ensure that it meets the buyer’s standards.
What Quality Assurance Practices Should B2B Buyers Expect for Kiss Cutting?
Quality assurance (QA) is critical in the kiss cutting process to ensure that products meet international standards and buyer specifications. Understanding these practices can help buyers verify the quality of their suppliers.
Which International Standards Are Relevant for Kiss Cutting?
Many suppliers adhere to internationally recognized standards to ensure quality and consistency in their manufacturing processes. Key standards include:
- ISO 9001: This is a widely recognized standard for quality management systems that can help ensure consistent product quality and continuous improvement.
- CE Marking: For products sold in Europe, CE marking indicates compliance with health, safety, and environmental protection standards.
- API Standards: For products used in the oil and gas industry, adhering to American Petroleum Institute (API) standards can be crucial for ensuring quality and safety.
By aligning with these standards, suppliers can provide assurance that their kiss cut products meet stringent quality requirements.
What Are the Key Quality Control Checkpoints During Production?
Implementing effective quality control (QC) checkpoints is essential to catch defects early in the production process. Typical checkpoints include:
- Incoming Quality Control (IQC): This involves inspecting raw materials upon arrival to ensure they meet the required specifications.
- In-Process Quality Control (IPQC): During production, ongoing checks can help identify any issues that may arise from the kiss cutting process.
- Final Quality Control (FQC): At the end of the production line, a comprehensive inspection of finished products ensures they meet all quality standards before shipment.
These checkpoints help maintain product quality throughout the manufacturing process.
How Can B2B Buyers Verify Supplier Quality Control Practices?
To ensure that suppliers adhere to quality control standards, B2B buyers can take several proactive steps:
- Audits: Conducting regular audits of suppliers’ manufacturing facilities can provide insights into their quality control practices.
- Quality Reports: Requesting detailed quality reports from suppliers can help buyers understand their QC processes and any issues encountered during production.
- Third-Party Inspections: Engaging third-party inspection services can offer an unbiased assessment of product quality and adherence to specifications.
These verification steps are particularly important for international buyers who may face challenges related to quality consistency across different regions.
What Are the Quality Control Nuances for International B2B Buyers?
For buyers from Africa, South America, the Middle East, and Europe, there are specific nuances to consider regarding quality control in kiss cutting:
- Regulatory Compliance: Different regions may have unique regulations regarding product safety and quality. It is essential for buyers to understand these requirements to avoid compliance issues.
- Cultural Differences: Communication styles and expectations can vary by region, impacting the effectiveness of quality assurance practices. Establishing clear lines of communication can help bridge these gaps.
- Logistics and Supply Chain Considerations: International shipping can introduce additional risks to product quality. Buyers should work closely with suppliers to ensure that products are adequately protected during transit.
By being aware of these nuances, international buyers can better navigate the complexities of sourcing kiss cut products and ensure they receive high-quality goods that meet their expectations.
Practical Sourcing Guide: A Step-by-Step Checklist for ‘kiss cutting’
In the realm of B2B operations, particularly for international buyers in Africa, South America, the Middle East, and Europe, understanding the nuances of kiss cutting is essential. This guide provides a step-by-step checklist to help you navigate the sourcing process for kiss cutting services or products effectively. By following these actionable insights, you can streamline your procurement process and ensure that you partner with the right suppliers.
Step 1: Define Your Technical Specifications
Before initiating the sourcing process, it’s crucial to outline your technical requirements. This includes the type of materials you need to kiss cut, the dimensions of the products, and the desired adhesive properties. Clearly defined specifications help potential suppliers understand your needs and provide accurate quotes.
- Considerations: Identify whether you require kiss cutting for paper, foam, or other materials. Specify thickness and any special finishing requirements.
Step 2: Research and Identify Suppliers
Conduct thorough research to create a list of potential suppliers specializing in kiss cutting. Use industry directories, trade shows, and online platforms to find reputable companies with a proven track record.
- Where to Look: Focus on suppliers that have experience in your target regions. Look for reviews and case studies that demonstrate their capabilities.
Step 3: Evaluate Supplier Capabilities
Once you have a list of suppliers, assess their capabilities. This includes the technology they use, production capacity, and their experience with kiss cutting.
- Key Questions: Ask about their cutting methods (e.g., manual, steel rule die, or laser kiss cutting) and whether they can handle your specific materials and volumes.
Step 4: Request Samples and Prototypes
Before finalizing a supplier, request samples or prototypes of their kiss cut products. This step allows you to evaluate the quality of their work and ensure it meets your standards.
- What to Assess: Pay attention to the cut precision, ease of peeling, and overall finish. Ensure that the sample adheres well without damaging the backing material.
Step 5: Verify Certifications and Compliance
Ensure that the suppliers you are considering comply with relevant industry standards and certifications. This is especially important for international transactions, where regulations may vary.
- Certification Types: Look for ISO certifications, safety standards, and environmental compliance that align with your company’s values and requirements.
Step 6: Negotiate Terms and Conditions
Once you’ve narrowed down your options, engage in negotiations regarding pricing, lead times, and payment terms. Clear communication at this stage is vital for establishing a mutually beneficial partnership.
- Negotiation Tips: Be upfront about your budget constraints and delivery expectations. This transparency fosters trust and helps avoid future misunderstandings.
Step 7: Establish a Communication Plan
Finally, set up a clear communication plan with your chosen supplier. Regular updates and open lines of communication can help address any issues that arise during production and ensure that your needs are met.
- Best Practices: Use project management tools or regular check-in meetings to maintain a collaborative relationship. This ensures that both parties are aligned on expectations and timelines.
By following this practical sourcing checklist, B2B buyers can effectively procure kiss cutting services tailored to their specific needs, ensuring quality and efficiency in their operations.
Comprehensive Cost and Pricing Analysis for kiss cutting Sourcing
What Are the Key Cost Components in Kiss Cutting Sourcing?
When evaluating the costs associated with kiss cutting, several critical components must be considered. These include materials, labor, manufacturing overhead, tooling, quality control (QC), logistics, and profit margins.
-
Materials: The primary materials in kiss cutting are adhesive-backed foils, paper, and the backing layer. The choice of material significantly affects pricing; high-quality materials with better adhesive properties may incur higher costs.
-
Labor: Labor costs vary based on the complexity of the kiss cutting operation. Manual methods may require less skilled labor, while automated processes necessitate trained personnel for machine operation and maintenance.
-
Manufacturing Overhead: This includes costs related to the production facility, utilities, and equipment depreciation. Efficient operations can help reduce overhead costs, which is vital for competitive pricing.
-
Tooling: The cost of tooling, including dies and cutters, can be substantial. Custom dies for unique shapes can lead to increased costs, particularly if tooling needs to be designed from scratch.
-
Quality Control (QC): Ensuring the kiss cutting process meets quality standards requires investment in QC measures. This may involve both in-process inspections and final product evaluations.
-
Logistics: Shipping costs and logistics play a crucial role, especially for international buyers. Factors such as the shipping method, distances, and handling requirements can significantly impact overall costs.
-
Margin: Finally, suppliers will add a profit margin to cover their operational risks and ensure sustainability. Margins can vary widely based on market demand and competition.
How Do Price Influencers Affect Kiss Cutting Costs?
Several factors influence the pricing structure for kiss cutting services. Understanding these can help buyers make informed purchasing decisions.
-
Volume and Minimum Order Quantities (MOQs): Generally, higher volumes lead to lower per-unit costs due to economies of scale. Suppliers often set MOQs that may affect pricing flexibility.
-
Specifications and Customization: Customized orders can drive up costs, as they may require specialized tooling and additional labor. Buyers should evaluate whether the customization is necessary for their end product.
-
Material Quality and Certifications: Higher-quality materials or those with specific certifications (e.g., ISO) can increase costs but may provide long-term savings through durability and performance.
-
Supplier Factors: The supplier’s location, reputation, and reliability can affect pricing. Established suppliers might charge more due to their track record of quality and service.
-
Incoterms: The chosen Incoterms can influence overall costs. For instance, choosing DDP (Delivered Duty Paid) may result in higher initial prices but lower unexpected costs upon delivery.
What Are the Best Negotiation Tips for International B2B Buyers?
International buyers, particularly from Africa, South America, the Middle East, and Europe, should consider the following strategies to enhance negotiation outcomes in kiss cutting sourcing:
-
Understand Total Cost of Ownership (TCO): Evaluate the TCO rather than just the purchase price. This includes considering logistics, potential rework costs, and product lifespan.
-
Negotiate Based on Volume: Leverage larger order quantities to negotiate better pricing. Suppliers are often willing to provide discounts for bulk orders.
-
Request Samples: Before committing to larger orders, request samples to assess material quality and performance, which can help justify pricing discussions.
-
Be Transparent About Expectations: Clearly communicate your requirements and expectations regarding quality, delivery times, and specifications. This transparency can foster better supplier relationships and lead to more favorable terms.
-
Stay Informed on Market Trends: Knowledge of market trends and pricing can provide leverage in negotiations. Being aware of fluctuations in material costs or changes in demand can help buyers negotiate effectively.
Conclusion
Navigating the cost structure and pricing of kiss cutting requires a thorough understanding of its components and influencers. By leveraging negotiation strategies and focusing on total cost considerations, international B2B buyers can achieve cost-effective sourcing solutions tailored to their needs. As always, indicative prices should be carefully evaluated against the specific context of each transaction to ensure optimal outcomes.
Alternatives Analysis: Comparing kiss cutting With Other Solutions
When evaluating kiss cutting, it’s essential to consider other viable methods that can achieve similar outcomes. Understanding the strengths and weaknesses of these alternatives will empower international B2B buyers to make informed decisions that align with their operational needs and budget constraints.
Comparison Table of Kiss Cutting and Alternative Solutions
Comparison Aspect | Kiss Cutting | Die Cutting | Laser Cutting |
---|---|---|---|
Performance | High precision, ideal for stickers | Versatile for various shapes | Extremely accurate, complex cuts |
Cost | Moderate initial investment | Higher due to tooling costs | High initial costs, ongoing expenses |
Ease of Implementation | Requires specific setups, moderate complexity | Complex setup, requires tooling | Requires skilled operators, specialized equipment |
Maintenance | Low, mostly requires blade checks | Moderate, depends on tooling wear | High, regular calibration needed |
Best Use Case | Sticker production, labels | Bulk production of various shapes | Intricate designs, materials needing fine detail |
What Are the Pros and Cons of Die Cutting?
Die cutting is a well-established method that involves cutting through materials entirely using a die. The advantages of die cutting include its versatility in producing a wide range of shapes and sizes, making it suitable for bulk production runs. However, the initial investment can be substantial due to the need for specialized tooling, which can be a barrier for smaller businesses. Additionally, die cutting may not be as efficient for smaller runs, as the setup time can be significant compared to kiss cutting.
How Does Laser Cutting Compare to Kiss Cutting?
Laser cutting utilizes a focused laser beam to cut through materials with exceptional accuracy. It is particularly beneficial for creating intricate designs and can handle a variety of materials. The primary advantage of laser cutting is its precision, which is unmatched by other methods. However, it involves higher costs both in terms of initial equipment and ongoing operational expenses, as well as the need for skilled operators to manage the technology effectively. Furthermore, laser cutting may not be suitable for all adhesive materials, as heat can affect their integrity.
Conclusion: How Can B2B Buyers Choose the Right Solution?
Choosing the right cutting solution depends on several factors, including the nature of the products, production volume, and budget. For businesses focused on producing stickers or labels with moderate complexity, kiss cutting offers a balance of efficiency and cost-effectiveness. In contrast, die cutting may be more appropriate for companies requiring high-volume production of various shapes, while laser cutting is ideal for those needing intricate designs and high precision. By assessing their specific needs against the strengths and weaknesses of these methods, B2B buyers can make an informed choice that enhances their operational efficiency and product quality.
Essential Technical Properties and Trade Terminology for kiss cutting
What Are the Essential Technical Properties of Kiss Cutting?
Understanding the technical properties of kiss cutting is crucial for B2B buyers looking to optimize their production processes. Here are some key specifications that can impact the efficiency and quality of kiss-cut products:
1. Material Grade
The choice of material grade directly affects the kiss cutting process. Common materials include adhesive-backed films, papers, and foils. Each material has unique properties, such as tensile strength and flexibility, which influence how well it can be cut and how it will perform in its final application. Selecting the right material grade ensures durability and functionality, reducing the risk of product failure in the field.
2. Tolerance Levels
Tolerance refers to the allowable deviation from a specified measurement in the kiss cutting process. Precise tolerances are essential for ensuring that the cut shapes fit perfectly within their intended applications. For instance, a tolerance of ±0.1 mm might be necessary for intricate designs. Adhering to these tolerance levels minimizes waste and ensures that products can be assembled or used as intended, which is critical for maintaining customer satisfaction.
3. Cutting Depth
The optimal cutting depth is a key specification that determines how deeply the die penetrates the material. Ideally, the cutting blade should penetrate just enough to cut through the adhesive layer and part of the silicone layer without damaging the backing material. This ensures that the stickers or components can be easily peeled off without tearing. Understanding cutting depth is vital for maintaining product integrity and usability.
4. Adhesive Properties
The type and quality of adhesive used in kiss cutting products significantly influence their performance. Pressure-sensitive adhesives need to provide sufficient tackiness while allowing for easy removal. The adhesive’s characteristics should align with the intended use, whether it’s for temporary applications or permanent bonding. By selecting the right adhesive properties, buyers can enhance product functionality and customer satisfaction.
5. Die Type and Configuration
The type of die used in kiss cutting—whether it’s steel rule dies or rotary dies—affects the production speed and the complexity of shapes that can be achieved. Different die configurations allow for varied cutting techniques, impacting both efficiency and cost. Understanding the implications of die selection helps buyers make informed decisions that align with their production needs.
What Trade Terminology Should B2B Buyers Know in Kiss Cutting?
Familiarity with industry jargon is essential for effective communication and negotiation in the kiss cutting sector. Here are some common terms that buyers should understand:
1. OEM (Original Equipment Manufacturer)
OEM refers to companies that produce parts or equipment that may be marketed by another manufacturer. In kiss cutting, understanding OEM relationships can be crucial for sourcing quality materials and components that meet specific standards.
2. MOQ (Minimum Order Quantity)
MOQ denotes the smallest quantity of a product that a supplier is willing to sell. For kiss cutting products, knowing the MOQ helps buyers plan their inventory and production schedules effectively, ensuring they don’t overcommit resources.
3. RFQ (Request for Quotation)
An RFQ is a document issued by a buyer to solicit price quotes from suppliers for specific products or services. When engaging in kiss cutting projects, submitting an RFQ can help buyers compare prices and terms from multiple vendors, facilitating informed purchasing decisions.
4. Incoterms (International Commercial Terms)
Incoterms are a set of predefined commercial terms published by the International Chamber of Commerce (ICC). They clarify the responsibilities of buyers and sellers in international transactions, including shipping, insurance, and tariffs. Understanding Incoterms is essential for B2B buyers, especially those sourcing kiss-cut products from different regions.
5. Lead Time
Lead time refers to the period between the initiation of an order and its completion. For kiss cutting projects, shorter lead times can enhance responsiveness to market demands. Buyers should negotiate lead times with suppliers to ensure timely delivery of products.
By grasping these essential properties and trade terms, international B2B buyers can navigate the kiss cutting landscape more effectively, making informed decisions that drive efficiency and profitability.
Navigating Market Dynamics and Sourcing Trends in the kiss cutting Sector
What Are the Key Trends Shaping the Kiss Cutting Market?
The kiss cutting sector is witnessing dynamic growth driven by several global trends, particularly among B2B buyers from Africa, South America, the Middle East, and Europe. One of the primary drivers is the increasing demand for customized products, as businesses seek unique solutions to differentiate themselves in competitive markets. This trend has led to the adoption of advanced technologies, such as laser kiss cutting and automated die cutting machines, which enhance precision and reduce production times.
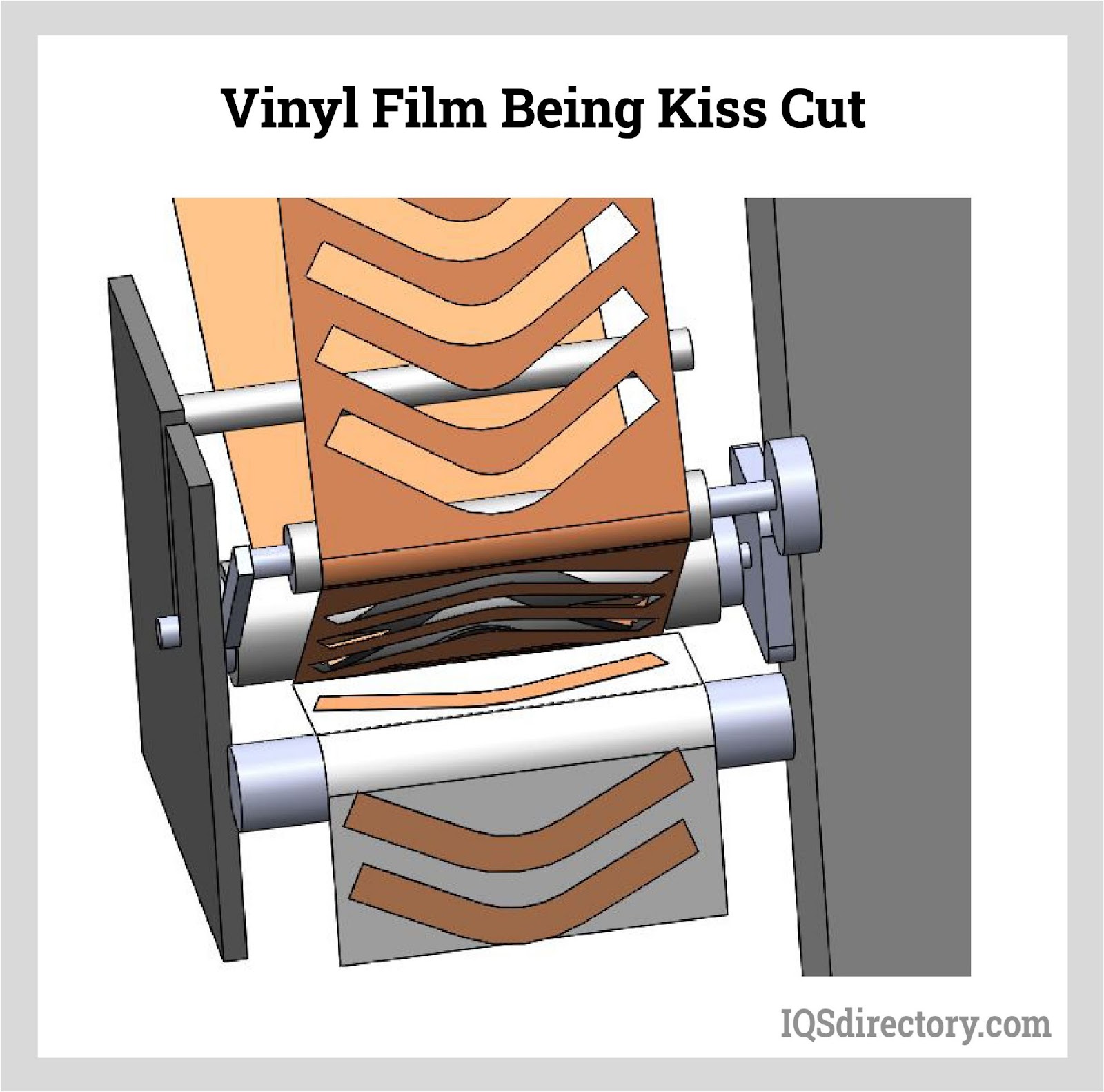
A stock image related to kiss cutting.
Another notable trend is the shift towards digital transformation within the manufacturing sector. Companies are increasingly integrating digital tools and software for design and production processes, allowing for real-time adjustments and improved efficiency. This is particularly relevant for international buyers looking for suppliers that offer cutting-edge capabilities, such as quick-turn prototypes and scalable production runs.
Additionally, the rise of e-commerce has spurred demand for kiss-cut products, especially in packaging and promotional materials. Businesses are looking for solutions that allow for easy handling and application, making kiss cutting an attractive option for sticker manufacturers and packaging companies. Buyers should also be aware of regional trends, such as the growing focus on local sourcing in Africa and South America, which is driven by logistics challenges and a desire to support local economies.
How Is Sustainability Influencing Kiss Cutting Sourcing Decisions?
Sustainability and ethical sourcing are increasingly influencing B2B decisions in the kiss cutting industry. As environmental concerns escalate, buyers are prioritizing suppliers that demonstrate a commitment to sustainable practices. This includes the use of eco-friendly materials, such as biodegradable films and recycled papers, which minimize the environmental impact of kiss-cut products.
Moreover, ethical supply chains are becoming essential for B2B buyers, especially in regions like Europe, where regulatory standards are stringent. Companies are expected to ensure that their sourcing practices do not contribute to environmental degradation or exploit labor. Certifications such as FSC (Forest Stewardship Council) and ISO 14001 for environmental management can provide assurance to buyers regarding the sustainability of their materials.
Investing in suppliers who prioritize sustainability can lead to long-term benefits, including enhanced brand reputation and customer loyalty. As the demand for green products continues to rise, B2B buyers should engage with suppliers who are transparent about their sourcing practices and can provide evidence of compliance with sustainability standards.
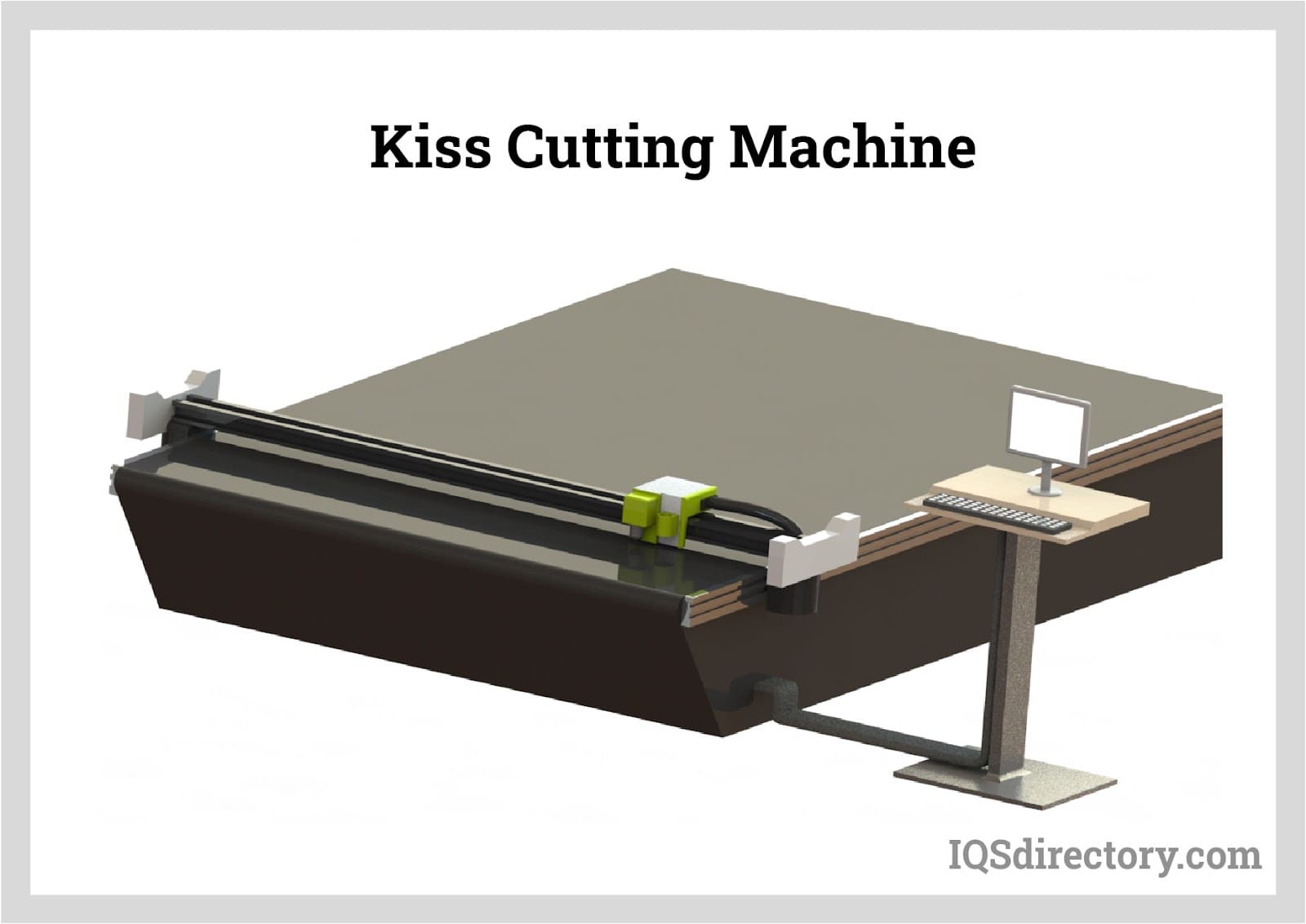
A stock image related to kiss cutting.
What Is the Historical Context of Kiss Cutting in B2B?
Kiss cutting has evolved significantly since its inception, with roots in traditional die cutting techniques. Initially, kiss cutting was a manual process, reliant on skilled artisans who used knives and rulers to create adhesive-backed products. Over the years, technological advancements have transformed the kiss cutting landscape. The introduction of automated machinery and laser cutting technologies has greatly increased production efficiency and precision.
In the early 2000s, the rise of digital printing and design software further revolutionized the kiss cutting process. Manufacturers began to adopt computer-controlled cutting systems, allowing for intricate designs and rapid prototyping. This evolution has not only expanded the capabilities of kiss cutting but has also made it accessible to a broader range of businesses, from small startups to large-scale manufacturers.
As the kiss cutting market continues to grow, international B2B buyers can benefit from understanding these historical developments. This knowledge can inform sourcing decisions and help buyers identify suppliers who are equipped to meet their evolving needs.
Frequently Asked Questions (FAQs) for B2B Buyers of kiss cutting
-
1. How do I solve issues with kiss cutting precision?
Achieving precision in kiss cutting requires careful monitoring of the cutting depth. To solve issues related to imprecise cuts, ensure that the machinery is calibrated correctly, and conduct regular maintenance checks. Using a high-quality steel rule die can also enhance accuracy. Additionally, consider running test cuts on sample materials to confirm that the cut depth is optimal—typically, this involves cutting through the adhesive and a portion of the silicone layer while leaving the backing intact. -
2. What is the best material for kiss cutting applications?
The best materials for kiss cutting depend on the end product. Common choices include adhesive-backed foils, papers, and vinyl. For applications needing durability, consider using thicker adhesive films or specialty materials like PTFE for high-temperature environments. Always assess the specific requirements of your application, such as flexibility, adhesion properties, and environmental resistance, to choose the most suitable material. -
3. How can I customize kiss-cut products for my business needs?
Customization of kiss-cut products can be achieved by working closely with your supplier. Discuss your design specifications, including shapes, sizes, and adhesive types. Many manufacturers offer services like prototype creation, which allows you to test your designs before full production. Ensure you communicate your branding requirements clearly, as this will help in producing cohesive products that align with your marketing goals. -
4. What is the minimum order quantity (MOQ) for kiss cutting services?
Minimum order quantities for kiss cutting services vary by supplier and project scope. Typically, MOQs can range from a few hundred to several thousand units, depending on the complexity of the design and the materials used. When sourcing suppliers, inquire about their flexibility regarding MOQs, especially if you are a small to medium-sized business. Some manufacturers may offer lower MOQs for custom projects to accommodate startups or niche markets. -
5. What payment terms should I expect when sourcing kiss cutting services internationally?
Payment terms can vary significantly across suppliers and regions. Common arrangements include 30% upfront payment with the balance due upon delivery, or net 30/60 terms after invoice. It’s essential to clarify these terms before finalizing contracts. For international transactions, consider using secure payment methods like letters of credit or escrow services to mitigate risks. Always review the supplier’s reputation and payment policies to ensure a smooth transaction. -
6. How do I vet potential suppliers for kiss cutting services?
Vetting suppliers is crucial to ensure quality and reliability. Start by researching their industry reputation, checking online reviews, and requesting references from previous clients. Evaluate their production capabilities, including technology and equipment used for kiss cutting. Finally, ask for samples of their work to assess quality firsthand. Engaging in direct communication can also provide insights into their customer service and responsiveness. -
7. What quality assurance measures should I consider in kiss cutting production?
Quality assurance is vital to ensure that kiss-cut products meet your specifications. Establish clear guidelines for quality control, including material inspections, cut depth checks, and adhesive performance tests. Many manufacturers employ statistical process control methods to monitor production consistency. Additionally, consider requesting third-party inspections or certifications, especially if your products are intended for regulated industries. -
8. How can logistics affect my kiss cutting supply chain?
Logistics plays a significant role in the efficiency of your kiss cutting supply chain. Consider factors such as shipping methods, lead times, and customs clearance processes when planning your orders. Engage with suppliers who have reliable logistics partners and can provide real-time tracking for your shipments. Effective communication regarding delivery schedules and potential delays is essential to maintain production timelines and avoid disruptions in your operations.
Important Disclaimer & Terms of Use
⚠️ Important Disclaimer
The information provided in this guide, including content regarding manufacturers, technical specifications, and market analysis, is for informational and educational purposes only. It does not constitute professional procurement advice, financial advice, or legal advice.
While we have made every effort to ensure the accuracy and timeliness of the information, we are not responsible for any errors, omissions, or outdated information. Market conditions, company details, and technical standards are subject to change.
B2B buyers must conduct their own independent and thorough due diligence before making any purchasing decisions. This includes contacting suppliers directly, verifying certifications, requesting samples, and seeking professional consultation. The risk of relying on any information in this guide is borne solely by the reader.
Strategic Sourcing Conclusion and Outlook for kiss cutting
In today’s competitive landscape, strategic sourcing for kiss cutting presents an invaluable opportunity for international B2B buyers. This technique not only streamlines production but also enhances product design flexibility, making it ideal for various applications, from adhesive tapes to intricate sticker designs. By understanding the nuances of kiss cutting—such as the importance of precise depth control and the choice of materials—businesses can significantly improve their operational efficiency and reduce waste.
Investing in kiss cutting processes can lead to better product quality and customer satisfaction, especially in diverse markets across Africa, South America, the Middle East, and Europe. As buyers seek to optimize their supply chains, collaborating with experienced converters who specialize in kiss cutting will be crucial. This partnership can facilitate tailored solutions that meet specific regional needs and standards.
Looking ahead, the demand for kiss-cut products is expected to grow, driven by innovations in material technology and increasing customization requirements. Now is the time for international B2B buyers to engage with industry experts and explore the potential of kiss cutting to elevate their product offerings. Embrace this opportunity to enhance your strategic sourcing initiatives and position your business for future success.