Master Lead Screw Mechanism: The Complete Buyer’s Guide (2025)
Introduction: Navigating the Global Market for lead screw mechanism
In today’s competitive landscape, international B2B buyers face the challenge of sourcing reliable lead screw mechanisms that ensure precision and efficiency in their operations. Whether you’re in the manufacturing sector in Germany or the agricultural industry in Argentina, understanding the nuances of lead screw technology is essential for enhancing productivity and maintaining quality. This comprehensive guide delves into the intricacies of lead screw mechanisms, exploring various types, applications, and design considerations tailored to meet the diverse needs of buyers from Africa, South America, the Middle East, and Europe.
Our guide provides an in-depth analysis of lead screw mechanisms, including the critical differences between lead screws and alternative solutions like ball screws. We will cover essential topics such as supplier vetting processes, cost considerations, and the latest advancements in material technology. By addressing these key areas, this guide empowers B2B buyers to make informed purchasing decisions that not only optimize operational efficiency but also ensure long-term reliability and performance.
Navigating the global market for lead screw mechanisms can be daunting, but with the right insights and understanding, buyers can confidently select components that align with their specific operational requirements. Prepare to enhance your sourcing strategy and elevate your business capabilities through this essential resource.
Understanding lead screw mechanism Types and Variations
Type Name | Key Distinguishing Features | Primary B2B Applications | Brief Pros & Cons for Buyers |
---|---|---|---|
ACME Lead Screws | Trapezoidal thread profile for high load capacity | Machine tools, jacks, and construction equipment | Pros: High strength, easy to manufacture. Cons: Higher friction compared to ball screws. |
Ball Lead Screws | Incorporates ball bearings for reduced friction | Robotics, CNC machines, and automation systems | Pros: High efficiency, low friction. Cons: Higher cost and complexity in design. |
Square Thread Screws | Square thread profile for better load distribution | Heavy machinery, lifting equipment | Pros: Excellent load handling, self-locking. Cons: Limited speed and efficiency. |
Buttress Lead Screws | Asymmetrical thread profile, ideal for thrust applications | Aerospace, automotive, and heavy machinery | Pros: High axial load capacity. Cons: Not suitable for high-speed applications. |
Trapezoidal Lead Screws | Similar to ACME but with a different thread angle | Linear actuators, automation equipment | Pros: Good balance of load capacity and efficiency. Cons: Moderate wear resistance compared to ball screws. |
What Are ACME Lead Screws and Their Applications?
ACME lead screws feature a trapezoidal thread profile that provides excellent load capacity and strength, making them suitable for applications requiring significant force, such as machine tools and construction equipment. Buyers should consider the ease of manufacturing and cost-effectiveness of ACME screws, but be aware that they may experience higher friction losses compared to alternatives like ball screws. This friction can impact efficiency, particularly in applications with frequent motion.
How Do Ball Lead Screws Enhance Efficiency?
Ball lead screws utilize ball bearings that roll between the screw and nut, dramatically reducing friction and increasing efficiency. This design is ideal for applications in robotics, CNC machines, and automation systems where precision and speed are critical. While they offer high performance and low wear, buyers should factor in the higher initial costs and complexity of installation. The long-term savings in energy and maintenance can offset these initial investments.
What Are the Benefits of Square Thread Screws?
Square thread screws are designed with a thread profile that optimizes load distribution, making them exceptionally effective in heavy machinery and lifting equipment. Their self-locking feature helps maintain position under load, which is beneficial for safety in various industrial applications. However, buyers should note that square thread screws may not perform well at high speeds, limiting their use in some dynamic applications.
Why Choose Buttress Lead Screws for Thrust Applications?
Buttress lead screws are characterized by their asymmetrical thread design, which excels in handling high axial loads, making them suitable for aerospace and automotive applications. They provide robust performance under thrust conditions, but buyers should consider their limitations in speed, as they are not designed for high-velocity operations. The strength of buttress screws can be a significant advantage in demanding environments.
What Makes Trapezoidal Lead Screws a Versatile Option?
Trapezoidal lead screws combine features of both ACME and square thread screws, offering a good balance between load capacity and efficiency. They are commonly used in linear actuators and various automation equipment. Buyers should appreciate the moderate wear resistance and overall versatility of trapezoidal screws, but must also be aware that their performance may not match that of specialized designs like ball screws in high-speed applications.
Key Industrial Applications of lead screw mechanism
Industry/Sector | Specific Application of lead screw mechanism | Value/Benefit for the Business | Key Sourcing Considerations for this Application |
---|---|---|---|
Manufacturing | Precision CNC machines for machining operations | Enhanced accuracy and repeatability in production | Material quality, lead time, and compatibility with existing systems |
Automation | Robotic arms for assembly and material handling | Increased efficiency and reduced labor costs | Customization options, load capacity, and maintenance requirements |
Medical Devices | Surgical tables and positioning systems | Improved patient safety and operational precision | Compliance with medical standards and reliability under load |
Aerospace | Actuation systems in aircraft control surfaces | Reliable performance in critical applications | High strength materials, resistance to environmental factors, and certification |
Textile Industry | Looms and fabric cutting machines | Higher production rates and quality control | Thread compatibility, lubrication needs, and ease of integration |
How Are Lead Screws Used in Manufacturing Applications?
In the manufacturing sector, lead screws are integral to precision CNC machines, where they convert rotational motion into linear motion for accurate machining operations. This application addresses the need for high precision and repeatability, essential for producing intricate parts. International buyers, particularly from regions like Europe and South America, should consider sourcing high-quality materials and ensure compatibility with their existing machinery to avoid operational inefficiencies.
What Role Do Lead Screws Play in Automation?
Lead screws are crucial in robotic arms used for assembly and material handling in automation. They facilitate smooth linear motion, which is vital for tasks requiring precision and speed. By integrating lead screws, companies can enhance operational efficiency and significantly reduce labor costs. Buyers in Africa and the Middle East should focus on customization options to meet specific automation needs and ensure that the lead screws can handle the required load capacities for their applications.
How Are Lead Screws Utilized in Medical Devices?
In the medical field, lead screws are employed in surgical tables and positioning systems to enable precise adjustments during operations. This application enhances patient safety and ensures that medical personnel can operate with accuracy. Buyers from Europe and Africa must consider compliance with stringent medical standards and the reliability of lead screws under load to guarantee optimal performance in critical healthcare settings.
Why Are Lead Screws Important in Aerospace Applications?
Lead screws are used in actuation systems for aircraft control surfaces, where reliability is paramount. They convert motor rotation into linear movement, essential for precise control in flight operations. Aerospace buyers must prioritize sourcing lead screws made from high-strength materials that can withstand environmental factors, ensuring safety and performance. Additionally, certification for aerospace applications is a critical consideration for international B2B buyers.
How Do Lead Screws Improve Production in the Textile Industry?
In the textile industry, lead screws are utilized in looms and fabric cutting machines to facilitate linear movement, which increases production rates and enhances quality control. This mechanism allows for precise positioning, reducing waste and improving the overall efficiency of textile manufacturing processes. Buyers from South America and Africa should assess thread compatibility and lubrication needs to ensure seamless integration into their production lines.
3 Common User Pain Points for ‘lead screw mechanism’ & Their Solutions
Scenario 1: Managing High Friction Losses in Lead Screw Mechanisms
The Problem: One of the most significant challenges faced by B2B buyers of lead screw mechanisms is managing friction losses during operation. In applications requiring precise motion control, such as CNC machines or automated assembly lines, excessive friction can lead to increased wear and tear on components, resulting in reduced efficiency and costly downtime. Buyers often discover that their lead screws are not performing as expected, leading to misalignment issues, inaccurate positioning, and the potential for mechanical failure.
The Solution: To mitigate friction losses, it is crucial to select lead screws with appropriate thread designs and materials. Consider using lead screws with a lower helix angle, which can reduce friction while still allowing for adequate load-bearing capacity. Additionally, opting for nuts made from self-lubricating materials, such as certain plastics or bronze composites, can help maintain smoother operation. Regular maintenance checks to lubricate the lead screw, even with PTFE-based coatings, can also enhance performance. B2B buyers should collaborate with manufacturers to customize lead screw specifications that best suit their application requirements, ensuring longevity and reliability in high-precision environments.
Scenario 2: Overcoming Backlash in Lead Screw Applications
The Problem: Backlash is a common pain point for buyers utilizing lead screw mechanisms, particularly in applications requiring high precision, such as robotics and aerospace. Backlash occurs when there is a gap between the lead screw and nut, leading to a loss of motion control and positioning accuracy. This issue is especially pronounced during rapid directional changes, where the lead screw may not respond immediately to command inputs, resulting in operational delays and inaccuracies that can compromise product quality.
The Solution: To address backlash, B2B buyers should consider implementing preloaded lead screw systems. This involves applying a constant axial load to the nut, which keeps it in firm contact with the screw threads and minimizes play. Buyers can also explore options such as double-nut configurations, where two nuts are used in tandem to cancel out backlash. Additionally, investing in precision lead screws that are designed to minimize backlash through advanced threading techniques can significantly improve positioning accuracy. Engaging with suppliers who offer customizable solutions can help ensure that the chosen lead screws meet specific operational demands while maintaining desired precision levels.
Scenario 3: Sourcing the Right Lead Screw for Diverse Applications
The Problem: International B2B buyers often face difficulties in sourcing the right lead screw mechanism for their specific applications, particularly when dealing with varying load requirements and operational environments. For example, a buyer in South America may require lead screws for agricultural machinery that can withstand harsh environmental conditions, while a buyer in Europe might need precision lead screws for laboratory equipment. The challenge lies in identifying suppliers who can provide high-quality lead screws tailored to specific application needs.
The Solution: To effectively source the right lead screw, buyers should first conduct a thorough needs assessment to determine the required specifications, including load capacity, environmental resistance, and precision levels. Researching suppliers that specialize in customized lead screw solutions can yield better results. For instance, consider manufacturers that offer a variety of materials, such as stainless steel for corrosion resistance or aluminum for lightweight applications. Additionally, establishing relationships with local distributors can facilitate quicker access to tailored solutions. Engaging in conversations with engineering teams from potential suppliers can also provide insights into innovative designs and technologies that enhance lead screw performance, ensuring that the selected components align with operational goals.
Strategic Material Selection Guide for lead screw mechanism
What Are the Key Properties of Common Materials Used in Lead Screw Mechanisms?
When selecting materials for lead screw mechanisms, several factors must be considered, including mechanical properties, environmental resistance, and cost-effectiveness. The most commonly used materials include carbon steel, stainless steel, aluminum, and bronze. Each material has unique properties that affect performance, durability, and suitability for specific applications.
How Does Carbon Steel Perform in Lead Screw Applications?
Key Properties: Carbon steel is known for its high strength and hardness. It can withstand significant loads and is often heat-treated to enhance its mechanical properties. However, it has limited corrosion resistance unless treated with coatings.
Pros & Cons: The primary advantage of carbon steel is its cost-effectiveness and strength, making it suitable for heavy-duty applications. However, its susceptibility to rust can be a significant drawback, especially in humid or corrosive environments, which limits its use in applications exposed to moisture.
Impact on Application: Carbon steel lead screws are ideal for applications requiring high load capacity, such as industrial machinery. However, they may not be suitable for environments with high humidity or corrosive substances.
Considerations for International Buyers: Buyers in regions like Africa and South America should consider local climate conditions when selecting carbon steel. Compliance with international standards such as ASTM A36 can ensure quality and performance.
What Advantages Does Stainless Steel Offer for Lead Screws?
Key Properties: Stainless steel is known for its excellent corrosion resistance, high strength, and durability. It can maintain its mechanical properties at elevated temperatures, making it suitable for a variety of environments.
Pros & Cons: The main advantage of stainless steel is its resistance to rust and corrosion, making it ideal for applications in harsh environments. However, it is generally more expensive than carbon steel, which can impact budget considerations.
Impact on Application: Stainless steel lead screws are often used in food processing, medical devices, and outdoor applications where corrosion resistance is critical. Their longevity can offset the initial cost in many cases.
Considerations for International Buyers: Buyers in Europe, such as Germany, often prefer stainless steel due to stringent regulations on material safety and hygiene. Compliance with standards like DIN EN 10088 can be crucial for market acceptance.
Why Choose Aluminum for Lead Screw Mechanisms?
Key Properties: Aluminum is lightweight and has good corrosion resistance, making it suitable for applications where weight is a concern. It also has decent strength, though not as high as steel.
Pros & Cons: The lightweight nature of aluminum allows for easier handling and reduced energy consumption in applications. However, its lower strength compared to steel can be a limitation in heavy-duty applications.
Impact on Application: Aluminum lead screws are commonly used in robotics and aerospace applications where weight reduction is essential. They are also suitable for lower load applications due to their reduced strength.
Considerations for International Buyers: In regions like the Middle East, where weight is a critical factor in transportation and logistics, aluminum can be a preferred choice. Buyers should ensure compliance with relevant international standards such as ASTM B221.
What Are the Benefits of Using Bronze in Lead Screw Mechanisms?
Key Properties: Bronze is known for its excellent wear resistance and self-lubricating properties, which can reduce friction in lead screw applications. It also has good corrosion resistance.
Pros & Cons: The primary advantage of bronze is its durability and ability to withstand wear, making it suitable for applications with high friction. However, it is typically more expensive than steel and aluminum.
Impact on Application: Bronze lead screws are often used in marine applications and environments where lubrication is challenging. Their resistance to wear makes them ideal for high-precision applications.
Considerations for International Buyers: Buyers in regions with a maritime industry, such as South America, should consider bronze for its corrosion resistance in saltwater environments. Compliance with standards like ASTM B150 can ensure product quality.
Summary Table of Material Selection for Lead Screw Mechanisms
Material | Typical Use Case for Lead Screw Mechanism | Key Advantage | Key Disadvantage/Limitation | Relative Cost (Low/Med/High) |
---|---|---|---|---|
Carbon Steel | Heavy-duty industrial machinery | High strength and cost-effective | Susceptible to corrosion | Low |
Stainless Steel | Food processing, medical devices | Excellent corrosion resistance | Higher cost compared to carbon steel | High |
Aluminum | Robotics, aerospace applications | Lightweight and good corrosion resistance | Lower strength than steel | Medium |
Bronze | Marine applications, high-precision tasks | Excellent wear resistance | Generally more expensive | High |
This guide provides international B2B buyers with a comprehensive overview of material selection for lead screw mechanisms, emphasizing key properties, pros and cons, and specific considerations relevant to different regions.
In-depth Look: Manufacturing Processes and Quality Assurance for lead screw mechanism
What Are the Key Manufacturing Processes for Lead Screw Mechanisms?
The manufacturing of lead screw mechanisms involves several critical stages, each essential for ensuring the final product meets high standards of quality and performance. Understanding these processes is vital for international B2B buyers, particularly those in regions like Africa, South America, the Middle East, and Europe.
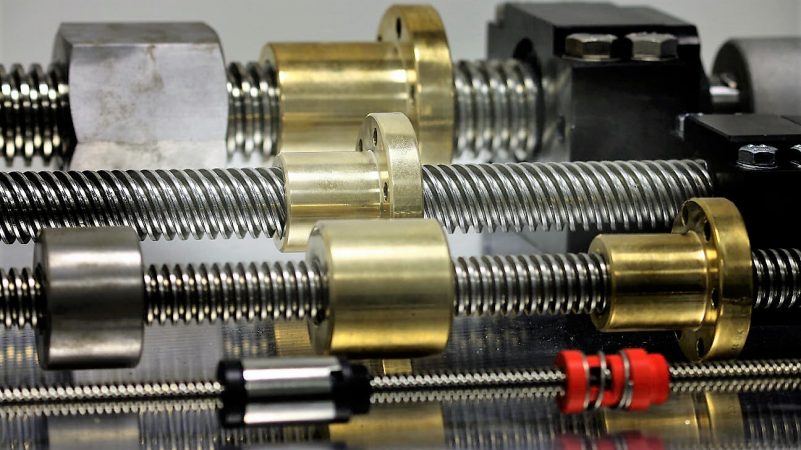
A stock image related to lead screw mechanism.
How Is Material Prepared for Lead Screws?
The first step in the manufacturing process is material preparation. Lead screws are typically made from materials such as carbon steel, stainless steel, or aluminum, chosen for their strength and durability.
-
Material Selection: The choice of material impacts the lead screw’s performance and longevity. For high-load applications, carbon steel is often preferred, while stainless steel is selected for environments requiring corrosion resistance.
-
Material Cutting: Raw materials are cut into appropriate lengths using precision cutting machines. This step ensures that the material is ready for the subsequent forming processes.
-
Heat Treatment: Depending on the application requirements, heat treatment may be applied to enhance the material’s mechanical properties, increasing hardness and tensile strength.
What Forming Techniques Are Used in Lead Screw Manufacturing?
Once materials are prepared, the next stage involves forming the lead screw.
-
Thread Cutting: This is a crucial step where the helical threads are cut onto the screw shaft. Techniques such as CNC machining or rolling are employed to achieve precise thread profiles. The choice between these methods often depends on the required accuracy and production volume.
-
Nut Manufacturing: The lead screw nut is produced concurrently, typically using similar machining techniques to ensure compatibility with the screw threads. The nut’s design may include self-lubricating materials to reduce friction.
-
Assembly of Components: After individual components are formed, they are assembled. This may involve threading the nut onto the screw shaft, ensuring that all parts fit together smoothly for optimal performance.
How Is Finishing Done for Lead Screws?
Finishing processes enhance the lead screw’s performance and appearance.
-
Surface Treatment: Lead screws often undergo surface treatments such as anodizing or plating to improve corrosion resistance and reduce wear. These treatments can significantly extend the lifespan of the components, especially in harsh environments.
-
Precision Grinding: This process is used to achieve the required tolerances and surface finishes. Precision grinding ensures that the lead screw operates smoothly and efficiently, minimizing wear and tear over time.
-
Final Inspection: Before packaging, each lead screw undergoes a final inspection to ensure it meets specified tolerances and quality standards.
What Quality Assurance Measures Are Essential for Lead Screws?
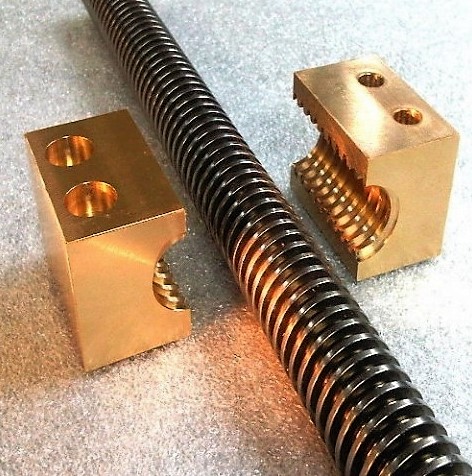
A stock image related to lead screw mechanism.
Quality assurance (QA) is critical in the manufacturing of lead screw mechanisms to ensure reliability and performance. For international B2B buyers, understanding these QA measures is crucial in supplier selection.
Which International Standards Should Buyers Consider?
-
ISO 9001: This widely recognized standard focuses on quality management systems. Suppliers adhering to ISO 9001 demonstrate a commitment to maintaining high quality in their manufacturing processes.
-
CE Marking: For products sold in Europe, CE marking indicates compliance with health, safety, and environmental protection standards. Buyers from Europe should ensure their suppliers have this certification.
-
API Standards: For applications in oil and gas, suppliers may need to comply with American Petroleum Institute (API) standards, which ensure that products can withstand the demanding conditions of these industries.
What Are the Key Quality Control Checkpoints?
To maintain quality throughout the manufacturing process, various checkpoints are implemented:
-
Incoming Quality Control (IQC): This initial checkpoint involves inspecting raw materials upon arrival at the facility. Ensuring that materials meet specified standards is critical to the overall quality of the finished product.
-
In-Process Quality Control (IPQC): During manufacturing, regular inspections are conducted to monitor production processes and ensure they remain within specified tolerances. This helps identify issues early and prevents defects from proceeding to the next stages.
-
Final Quality Control (FQC): After assembly and finishing, the lead screws undergo rigorous testing to ensure they meet all functional and performance criteria. This includes measuring dimensions, checking thread profiles, and testing for smooth operation.
How Can B2B Buyers Verify Supplier Quality Control?
For B2B buyers, particularly those operating in diverse international markets, verifying a supplier’s quality control practices is essential.
-
Supplier Audits: Conducting supplier audits can provide insights into their manufacturing processes and quality assurance measures. Buyers should assess the supplier’s adherence to international standards and their internal QA practices.
-
Quality Reports: Requesting detailed quality reports can help buyers understand a supplier’s performance over time. These reports should include data on defect rates, inspection results, and corrective actions taken.
-
Third-Party Inspections: Engaging third-party inspection services can add an additional layer of assurance. Independent inspectors can verify that products meet specified standards and provide unbiased assessments of the supplier’s quality control processes.
What Are the Unique QC Considerations for International Buyers?
International B2B buyers must be aware of specific nuances when it comes to quality control in the lead screw manufacturing industry.
-
Cultural Differences: Different regions may have varying approaches to quality assurance. Buyers should consider these differences and ensure that their expectations align with those of the supplier.
-
Regulatory Compliance: Understanding local regulations and standards is crucial, especially when sourcing from different continents. Buyers must ensure that products comply with both international and local laws.
-
Communication: Establishing clear communication channels with suppliers can help address quality concerns promptly. Regular updates and feedback loops can enhance collaboration and lead to better outcomes.
By understanding the manufacturing processes and quality assurance measures for lead screw mechanisms, international B2B buyers can make informed decisions and establish reliable partnerships with suppliers in this critical component industry.
Practical Sourcing Guide: A Step-by-Step Checklist for ‘lead screw mechanism’
Introduction
Sourcing lead screw mechanisms for your manufacturing needs involves careful consideration of various factors to ensure optimal performance and reliability. This guide provides a step-by-step checklist to help international B2B buyers, particularly from Africa, South America, the Middle East, and Europe, navigate the procurement process effectively. By following these steps, you can ensure that you select the right lead screw solutions tailored to your specific applications.
Step 1: Define Your Technical Specifications
Establishing clear technical specifications is crucial for identifying the right lead screw mechanism for your application. Consider factors such as load capacity, lead screw type (e.g., ACME, trapezoidal), material, and thread design.
- Load Capacity: Determine the maximum load the lead screw will need to support.
- Precision Requirements: Assess the level of precision needed in your applications, as this will affect your choice of thread design.
Step 2: Research Different Lead Screw Types
Different lead screw types serve distinct purposes and performance needs. Familiarize yourself with options such as single-start and multi-start screws, as well as various thread geometries.
- Single-Start vs. Multi-Start: Multi-start screws can provide higher speeds and loads, which might be necessary for your application.
- Thread Geometry: Understand how different thread shapes can impact friction and efficiency.
Step 3: Evaluate Material Options for Durability
The choice of material can significantly impact the lifespan and performance of the lead screw. Common materials include carbon steel, stainless steel, and aluminum, each offering unique benefits.
- Corrosion Resistance: If your application involves harsh environments, opt for stainless steel or PTFE-coated options.
- Weight Considerations: For lightweight applications, aluminum might be the best choice.
Step 4: Verify Supplier Certifications
Before making a purchase, confirm that your suppliers have relevant industry certifications. This ensures that they meet quality and safety standards necessary for your operations.
- ISO Certification: Look for suppliers certified to ISO 9001 or similar standards, which demonstrate their commitment to quality management.
- Industry-Specific Certifications: Depending on your sector, additional certifications may be required (e.g., aerospace, automotive).
Step 5: Request Samples and Prototypes
Obtaining samples or prototypes is essential to assess the quality and performance of the lead screws. This allows you to test them in your specific applications before making a larger commitment.
- Testing Performance: Evaluate the lead screw under actual working conditions to ensure it meets your specifications.
- Feedback from Technical Teams: Involve your engineering team in the testing process to gather valuable insights.
Step 6: Consider Supplier Support and After-Sales Service
Reliable after-sales support can be a deciding factor in supplier selection. Evaluate the level of support offered by suppliers, including technical assistance and warranty policies.
- Technical Support: Ensure that the supplier provides access to technical experts who can assist with installation or troubleshooting.
- Warranty Terms: Review warranty policies to understand what is covered and for how long.
Step 7: Negotiate Terms and Finalize the Order
Once you have selected a supplier, negotiate the terms of the order, including pricing, delivery schedules, and payment terms. Clear agreements can help prevent misunderstandings later in the process.
- Bulk Discounts: Inquire about discounts for larger orders to optimize your budget.
- Delivery Timelines: Establish clear timelines for delivery to ensure that your project schedules are met.
By following this checklist, B2B buyers can ensure a thorough and informed approach to sourcing lead screw mechanisms, ultimately enhancing operational efficiency and product quality.
Comprehensive Cost and Pricing Analysis for lead screw mechanism Sourcing
What Are the Key Cost Components in Lead Screw Mechanism Sourcing?
Understanding the cost structure of lead screw mechanisms is critical for international B2B buyers, especially those operating in diverse markets such as Africa, South America, the Middle East, and Europe. The total cost of lead screw mechanisms typically encompasses several key components:
-
Materials: The choice of materials significantly influences the cost. Common materials include carbon steel, stainless steel, aluminum, and sometimes specialized coatings for durability. Higher-quality materials may increase the initial cost but can offer longer lifespan and better performance, thus reducing the Total Cost of Ownership (TCO).
-
Labor: Labor costs vary by region and manufacturing complexity. In regions with lower labor costs, such as parts of Africa and South America, manufacturers may be able to offer competitive pricing. However, skilled labor for precision manufacturing in Europe might demand higher wages, impacting overall costs.
-
Manufacturing Overhead: This includes costs related to utilities, maintenance, and facility operations. Efficient manufacturing processes can lower overhead, making it essential for buyers to evaluate suppliers’ operational efficiencies.
-
Tooling: Tooling costs are often significant, especially for custom lead screws. Buyers should inquire about the supplier’s existing tooling capabilities to avoid additional costs associated with creating new molds or dies.
-
Quality Control (QC): Implementing stringent QC measures ensures product reliability but can add to manufacturing costs. Buyers should verify the QC processes of suppliers to ensure they meet international standards, which can mitigate risks of defects.
-
Logistics: Shipping and handling costs can vary widely based on the location of the supplier and the buyer. Incoterms play a crucial role in defining responsibilities and costs associated with transportation and customs duties.
-
Margin: Suppliers will typically include a profit margin in their pricing. Understanding market dynamics and supplier competition can provide leverage during negotiations.
How Do Price Influencers Affect Lead Screw Mechanism Costs?
Several factors can influence pricing for lead screw mechanisms:
-
Volume and Minimum Order Quantity (MOQ): Ordering in bulk can lead to significant discounts. Buyers should assess their needs and potential for future orders to negotiate better pricing terms.
-
Specifications and Customization: Customized lead screws that meet specific application requirements can incur additional costs. Buyers should weigh the benefits of customization against budget constraints.
-
Materials and Quality Certifications: The level of quality and certifications (e.g., ISO standards) can influence pricing. Higher-quality components often command premium prices, but they may reduce maintenance costs over time.
-
Supplier Factors: The supplier’s reputation, reliability, and geographical location can impact pricing. Established suppliers with proven track records may charge more, but their reliability could lead to lower overall costs.
-
Incoterms: Understanding Incoterms is crucial for international transactions. They define the responsibilities of buyers and sellers regarding shipping, insurance, and customs duties, which can significantly affect the final cost.
What Are the Best Buyer Tips for Cost-Efficient Lead Screw Sourcing?
-
Negotiate Effectively: Building a strong relationship with suppliers can facilitate better negotiation outcomes. Be transparent about your needs and expectations, and leverage your purchasing power to secure favorable terms.
-
Focus on Total Cost of Ownership (TCO): Instead of focusing solely on the purchase price, consider the TCO, which includes installation, maintenance, and potential downtime costs. This holistic view can lead to more informed purchasing decisions.
-
Understand Pricing Nuances for International Purchases: Be aware of currency fluctuations, import duties, and taxes that may apply when sourcing from international suppliers. This understanding can help prevent unexpected costs.
-
Research and Compare Suppliers: Conduct thorough market research to identify multiple suppliers. Comparing quotes and service offerings can lead to better pricing and quality options.
-
Stay Informed about Market Trends: Keep abreast of industry trends, material costs, and technological advancements that could impact lead screw pricing. This knowledge can empower you during negotiations and sourcing strategies.
Disclaimer for Indicative Prices
Prices for lead screw mechanisms can vary significantly based on the factors mentioned above. The figures provided in various sources are indicative and should be verified with suppliers for accuracy and relevance to specific purchasing scenarios.
Alternatives Analysis: Comparing lead screw mechanism With Other Solutions
Understanding Alternatives to Lead Screw Mechanisms
When evaluating linear motion solutions, it’s crucial for B2B buyers to consider various alternatives to lead screw mechanisms. Each solution has distinct advantages and disadvantages, impacting performance, cost, and suitability for specific applications. This section explores two viable alternatives: ball screws and electric linear actuators, providing a comprehensive comparison to help international buyers make informed decisions.
Comparison Table of Linear Motion Solutions
Comparison Aspect | Lead Screw Mechanism | Ball Screw | Electric Linear Actuator |
---|---|---|---|
Performance | Moderate efficiency; good for low-speed applications | High efficiency; low friction, suitable for high-speed applications | Varies widely; can achieve high speeds and precision |
Cost | Generally lower cost | Higher initial investment due to precision machining | Varies; often more expensive due to motor integration |
Ease of Implementation | Simple design; easy to integrate | More complex due to precision requirements | Moderate; requires electrical setup and control |
Maintenance | Moderate; requires lubrication and periodic checks | Low; sealed units reduce maintenance needs | Low; usually maintenance-free but may need electrical checks |
Best Use Case | Light to medium-duty applications needing precise motion | High-load, high-speed applications requiring minimal backlash | Versatile applications needing push/pull force; automation tasks |
Detailed Breakdown of Alternatives
What Are the Advantages and Disadvantages of Ball Screws?
Ball screws are designed to reduce friction by using balls that roll between the screw and nut. This design results in higher efficiency and the ability to handle higher speeds and loads compared to lead screws.
Pros:
– High Efficiency: Ball screws can achieve efficiency levels exceeding 90%, making them ideal for applications requiring rapid motion.
– Precision: They offer minimal backlash, providing more accurate positioning, which is essential in CNC machines and robotics.
Cons:
– Higher Cost: The precision manufacturing process involved in producing ball screws results in a higher initial investment.
– Complexity in Installation: Their design and installation require skilled labor to ensure proper alignment and function.
How Do Electric Linear Actuators Compare?
Electric linear actuators convert electrical energy into linear motion and are widely used in automated systems. They can vary significantly in design and function, from simple push-pull units to complex systems with feedback control.
Pros:
– Versatility: They can be used in a wide range of applications, from robotics to medical devices, and offer various configurations.
– Maintenance-Free: Many electric actuators are designed for low maintenance, making them suitable for long-term use.
Cons:
– Initial Cost: The integration of motors and control systems can make electric actuators more expensive than lead screws.
– Power Dependency: Electric actuators require a power source, which can limit their application in remote or off-grid locations.
Conclusion: How Should B2B Buyers Choose the Right Linear Motion Solution?
When selecting a linear motion solution, international B2B buyers should assess their specific application requirements, including load capacity, speed, precision, and budget. Lead screws may be appropriate for cost-sensitive, low to medium-duty applications, while ball screws offer superior performance for high-speed and high-precision needs. Electric linear actuators provide versatility for automated systems but may come at a higher cost. By weighing these factors, buyers from regions like Africa, South America, the Middle East, and Europe can make informed decisions that align with their operational needs and financial constraints.
Essential Technical Properties and Trade Terminology for lead screw mechanism
What Are the Key Technical Properties of Lead Screw Mechanisms?
When evaluating lead screw mechanisms, several technical properties are critical for ensuring optimal performance and compatibility with specific applications. Here are some essential specifications to consider:
1. Material Grade: Why Is It Important for Durability?
Lead screws are commonly made from materials such as carbon steel, stainless steel, and aluminum. The choice of material directly affects the screw’s strength, corrosion resistance, and overall durability. For instance, stainless steel is preferred in environments exposed to moisture or chemicals, while aluminum is lighter and suitable for applications where weight is a concern. Understanding the material grade helps buyers select the right lead screw for their operational environment.
2. Tolerance: How Does It Affect Precision?
Tolerance defines the permissible limit of variation in the lead screw’s dimensions. High precision is crucial in applications requiring accurate linear motion, such as robotics and CNC machinery. Tighter tolerances lead to better alignment and reduced backlash, which is essential for maintaining the integrity of the motion system. Buyers should ensure that the specified tolerance aligns with their application needs to avoid operational inefficiencies.
3. Screw Lead: What Role Does It Play in Motion Control?
The screw lead is the distance the nut moves with one full rotation of the screw. This measurement is pivotal in determining the speed and precision of linear motion. A smaller lead offers finer control, making it suitable for tasks requiring meticulous positioning. Conversely, a larger lead allows for quicker movement, ideal for applications prioritizing speed over precision. Understanding screw lead helps buyers match their performance requirements with the right lead screw design.
4. Pitch: How Does It Influence Load Capacity?
Pitch refers to the distance between adjacent threads on the lead screw. It influences the load capacity and efficiency of the screw mechanism. A finer pitch can handle higher loads but may require more torque to operate. On the other hand, a coarser pitch allows for faster movement but may not support heavy loads effectively. Buyers must consider their application’s load requirements when selecting pitch specifications.
5. Helix Angle: Why Is It Crucial for Friction Management?
The helix angle is the angle formed between the thread and the lead screw shaft. A larger helix angle can reduce friction but may require more torque for operation, affecting the overall efficiency of the mechanism. Understanding the helix angle is vital for buyers who want to optimize their lead screw performance while minimizing energy consumption.
What Are the Common Trade Terminology and Their Importance in Lead Screw Purchases?
Familiarity with trade terminology can enhance communication and negotiation with suppliers. Here are some key terms that international B2B buyers should know:
1. OEM (Original Equipment Manufacturer): What Does It Mean for Sourcing?
OEM refers to companies that produce parts or equipment that may be marketed by another manufacturer. Understanding whether a lead screw is sourced from an OEM can indicate quality assurance and compatibility with existing systems, which is crucial for buyers in sectors like automotive and aerospace.
2. MOQ (Minimum Order Quantity): How Does It Affect Procurement?
MOQ is the minimum number of units that a supplier is willing to sell. Knowing the MOQ helps buyers plan their budgets and inventory effectively. It is especially important for international buyers who may face shipping and storage constraints.
3. RFQ (Request for Quotation): Why Is It Essential in B2B Transactions?
An RFQ is a document sent to suppliers to request pricing information for specific products or services. Issuing an RFQ allows buyers to compare prices and terms, ensuring they receive the best value for their investment in lead screws.
4. Incoterms: How Do They Influence Shipping Agreements?
Incoterms are international commercial terms that define the responsibilities of buyers and sellers in shipping agreements. Understanding these terms helps buyers clarify who is responsible for costs, risks, and insurance during transport, which is critical when sourcing from different regions, including Africa, South America, the Middle East, and Europe.
5. Lead Time: What Should Buyers Expect?
Lead time refers to the time taken from placing an order to delivery. It is crucial for project planning and inventory management. Buyers should discuss lead times with suppliers to ensure timely delivery aligns with their production schedules.
By grasping these technical properties and trade terms, international B2B buyers can make informed decisions, enhance their procurement processes, and optimize the performance of their lead screw mechanisms.
Navigating Market Dynamics and Sourcing Trends in the lead screw mechanism Sector
What Are the Current Market Dynamics and Key Trends in the Lead Screw Mechanism Sector?
The lead screw mechanism sector is experiencing significant growth driven by the increasing demand for automation and precision engineering across various industries, including manufacturing, robotics, and medical devices. As international B2B buyers from regions like Africa, South America, the Middle East, and Europe (e.g., Argentina, Germany) look to enhance operational efficiency, lead screws have become integral in applications requiring accurate linear motion. The global market is witnessing a shift toward smart manufacturing technologies, incorporating Internet of Things (IoT) capabilities that allow for real-time monitoring and control of lead screw systems.
Emerging trends indicate a growing preference for customized lead screw solutions tailored to specific applications, reflecting the unique needs of different sectors. Additionally, advancements in materials science, such as the development of lightweight and high-strength alloys, are enhancing the performance and durability of lead screws. This shift not only improves operational efficiency but also reduces maintenance costs, making lead screws an attractive option for international buyers seeking long-term investments.
Moreover, the rise of e-commerce platforms has simplified sourcing processes, allowing B2B buyers to access a broader range of suppliers and products. This democratization of supply chains enables buyers in emerging markets to compete more effectively on a global scale, leveraging technology to streamline procurement and logistics.
How Can Sustainability and Ethical Sourcing Impact the Lead Screw Mechanism Sector?
In today’s environmentally conscious market, sustainability is paramount for B2B buyers in the lead screw mechanism sector. The environmental impact of manufacturing processes, including lead screw production, necessitates a shift towards sustainable practices. Buyers are increasingly seeking suppliers who prioritize eco-friendly materials, energy-efficient production methods, and waste reduction strategies. This trend aligns with global initiatives aimed at minimizing carbon footprints and promoting responsible consumption.
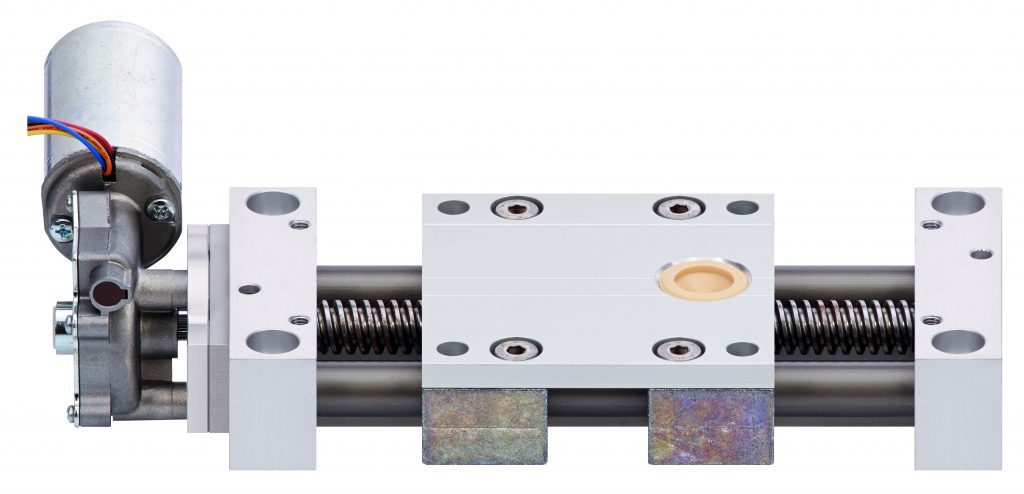
A stock image related to lead screw mechanism.
Ethical sourcing is equally crucial, as buyers demand transparency in their supply chains. Suppliers that can demonstrate adherence to ethical labor practices and sustainable sourcing of raw materials, such as recycled metals or biodegradable lubricants, gain a competitive advantage. Certifications such as ISO 14001 (Environmental Management) or ISO 45001 (Occupational Health and Safety) can bolster supplier credibility, assuring international buyers of their commitment to sustainability.
Furthermore, integrating sustainable practices can enhance brand reputation and customer loyalty. Companies that prioritize sustainability not only attract environmentally conscious consumers but also position themselves favorably in a market increasingly driven by corporate social responsibility (CSR) values. As a result, B2B buyers must evaluate potential suppliers based on their environmental and ethical standards, ensuring alignment with their own corporate values.
What Is the Brief Evolution and History of Lead Screws?
The lead screw mechanism has a rich history, dating back to ancient times when it was first utilized in simple machines such as the screw press. Over the centuries, the design and application of lead screws have evolved significantly. The Industrial Revolution marked a turning point, as advancements in manufacturing processes allowed for more precise and efficient lead screw production.
In the 20th century, the introduction of materials like stainless steel and innovations in thread design further enhanced the performance of lead screws, making them indispensable in various industrial applications. Today, lead screws are a staple in modern machinery, with ongoing research focusing on optimizing their design for higher efficiency and sustainability. The evolution of lead screws reflects broader trends in engineering, emphasizing the importance of precision, reliability, and adaptability in meeting the demands of contemporary industries.
By understanding these historical developments, B2B buyers can appreciate the foundational role lead screws play in current and future technological advancements, positioning them as essential components in the machinery and automation landscape.
Frequently Asked Questions (FAQs) for B2B Buyers of lead screw mechanism
-
How do I select the right lead screw mechanism for my application?
Selecting the right lead screw mechanism involves understanding your specific application requirements, including load capacity, speed, and precision. Consider the type of motion needed (linear or rotary), the environment (temperature, humidity), and the available space. Evaluate the screw’s lead, pitch, and thread design to ensure it aligns with your performance expectations. Consulting with manufacturers or industry experts can provide tailored recommendations based on your operational needs. -
What is the best material for lead screws in harsh environments?
For applications in harsh environments, stainless steel or corrosion-resistant alloys are ideal materials for lead screws. These materials offer excellent durability and resistance to wear, corrosion, and temperature fluctuations. Additionally, consider lead screws with PTFE coatings, which can reduce friction and enhance performance in abrasive conditions. Always assess your specific environmental factors to ensure optimal material selection. -
What are the typical lead screw sizes and their applications?
Lead screws come in various sizes, with common diameters ranging from 4mm to 20mm. Smaller screws are suitable for light-duty applications like 3D printers and CNC machines, while larger screws can handle heavy-duty tasks in industrial machinery and automation equipment. The choice of size should align with the load requirements and space constraints of your application, ensuring both efficiency and effectiveness. -
How do I vet suppliers for lead screw mechanisms?
To vet suppliers for lead screw mechanisms, assess their industry experience, certifications, and product quality. Request samples and inspect their manufacturing processes for precision and reliability. Evaluate customer reviews and case studies to gauge satisfaction levels. Additionally, inquire about their ability to provide customization options and support, as this can be crucial for unique project requirements. -
What are the minimum order quantities (MOQ) for lead screws?
Minimum order quantities (MOQ) for lead screws can vary significantly between suppliers, typically ranging from 10 to 100 units. Factors influencing MOQ include the supplier’s production capabilities, customization options, and material availability. Discussing your specific needs with potential suppliers can often lead to flexible arrangements, especially for bulk orders or long-term partnerships. -
What payment terms should I expect when sourcing lead screws internationally?
Payment terms for international sourcing of lead screws typically involve a deposit (often 30-50%) upfront, with the balance due upon shipment or delivery. Some suppliers may offer credit terms for established relationships. It’s essential to discuss payment methods (like wire transfers or letters of credit) and ensure that terms align with your cash flow capabilities and risk management strategies. -
What quality assurance measures should I look for in lead screw suppliers?
When sourcing lead screws, ensure that suppliers implement rigorous quality assurance measures, including material testing, dimensional inspections, and performance evaluations. Look for certifications such as ISO 9001, which indicate adherence to international quality standards. Additionally, inquire about their warranty policies and after-sales support, as these can be indicative of their commitment to product quality. -
How can I manage logistics and shipping for lead screw procurement?
Effective logistics management for lead screw procurement involves understanding shipping options, customs regulations, and delivery timelines. Collaborate with suppliers to select the most efficient shipping method, considering factors like cost and speed. It’s advisable to work with logistics partners familiar with international trade to navigate customs processes smoothly. Always plan for potential delays and communicate regularly with suppliers to stay updated on shipping statuses.
Important Disclaimer & Terms of Use
⚠️ Important Disclaimer
The information provided in this guide, including content regarding manufacturers, technical specifications, and market analysis, is for informational and educational purposes only. It does not constitute professional procurement advice, financial advice, or legal advice.
While we have made every effort to ensure the accuracy and timeliness of the information, we are not responsible for any errors, omissions, or outdated information. Market conditions, company details, and technical standards are subject to change.
B2B buyers must conduct their own independent and thorough due diligence before making any purchasing decisions. This includes contacting suppliers directly, verifying certifications, requesting samples, and seeking professional consultation. The risk of relying on any information in this guide is borne solely by the reader.
Strategic Sourcing Conclusion and Outlook for lead screw mechanism
As international B2B buyers navigate the complexities of sourcing lead screw mechanisms, understanding their unique benefits and applications is crucial. Lead screws are essential for converting rotational motion into linear motion with high precision, making them ideal for various industries, including manufacturing, robotics, and automation. Their robust design offers significant mechanical advantages, especially in applications requiring high force generation with minimal space.
What Are the Key B2B Takeaways for Sourcing Lead Screws?
Strategic sourcing of lead screw mechanisms involves evaluating material options, thread designs, and load capacities to ensure optimal performance in your specific application. Buyers should consider factors such as friction losses, self-locking capabilities, and the desired speed of operation when making procurement decisions. Additionally, collaborating with reputable suppliers can provide access to custom solutions tailored to unique operational needs.
How Can Buyers Position Themselves for Future Success?
The outlook for lead screw mechanisms remains positive, with advancements in materials and manufacturing techniques promising enhanced efficiency and durability. As industries globally continue to automate and optimize, the demand for high-precision components will only grow. Buyers in Africa, South America, the Middle East, and Europe should actively seek partnerships that prioritize innovation and reliability. Embracing these strategic sourcing practices will position your organization to leverage the full potential of lead screw technology, driving efficiency and competitive advantage in your market.