Master Silicone Molding: The Complete Sourcing Guide (2025)
Introduction: Navigating the Global Market for silicone molding
Silicone molding has become a pivotal technique for international B2B buyers seeking to innovate and streamline their manufacturing processes. As industries across Africa, South America, the Middle East, and Europe grapple with the challenges of sourcing reliable materials and suppliers, understanding the intricacies of silicone molding is essential. This guide serves as a comprehensive resource, detailing the various types of silicone molds, their diverse applications, and critical considerations for supplier vetting.
The versatility of silicone molding is evident in its wide-ranging uses, from prototyping in product design to creating intricate jewelry pieces. Buyers will find insights into cost factors and longevity of molds, enabling them to make informed purchasing decisions. Whether you are a product developer in Poland or a manufacturer in Indonesia, this guide empowers you with actionable strategies to enhance your sourcing efforts.
By navigating the complexities of the silicone molding market, you can leverage this technology to reduce production costs, accelerate time-to-market, and ultimately meet the demands of your customers. With the right knowledge, you can confidently engage with suppliers, ensuring that you select high-quality materials that align with your specific needs and budget. Prepare to embark on a journey through the silicone molding landscape, equipping yourself with the knowledge necessary to thrive in a competitive global market.
Understanding silicone molding Types and Variations
Type Name | Key Distinguishing Features | Primary B2B Applications | Brief Pros & Cons for Buyers |
---|---|---|---|
Room Temperature Vulcanized (RTV) Silicone | Cures at room temperature, flexible, and easy to work with. | Prototyping, jewelry, consumer goods. | Pros: Cost-effective for small runs. Cons: Limited heat resistance. |
Liquid Silicone Rubber (LSR) | High durability, excellent tear resistance, and low shrinkage. | Automotive, medical devices, industrial parts. | Pros: Long-lasting molds. Cons: Higher initial costs. |
Two-Part Silicone Molding | Requires mixing two components, allows for complex shapes. | Custom parts manufacturing, art and crafts. | Pros: Versatile for detailed designs. Cons: Requires precise mixing. |
Translucent Silicone Molds | Allows for visibility of the casting process, ideal for intricate designs. | Arts, crafts, and specialized consumer products. | Pros: Great for visual inspection. Cons: More expensive than opaque options. |
Overmolding | Combines two materials into one part, enhancing functionality. | Electronics, automotive, and consumer products. | Pros: Improved product performance. Cons: Complexity in manufacturing. |
What is Room Temperature Vulcanized (RTV) Silicone and Its Applications?
Room Temperature Vulcanized (RTV) silicone is a popular choice for creating molds that cure at ambient temperatures. This type of silicone is particularly suited for prototyping and jewelry making, as it allows for quick production of custom designs without the need for extensive tooling. B2B buyers should consider the balance between cost and flexibility, as RTV silicone is generally more affordable for small batch runs but may not withstand high temperatures.
How Does Liquid Silicone Rubber (LSR) Differ from Other Types?
Liquid Silicone Rubber (LSR) is characterized by its exceptional durability and low shrinkage, making it ideal for high-volume production. This type of silicone is commonly used in the automotive and medical industries where precision and longevity are paramount. Buyers should evaluate the higher initial costs against the long-term savings due to the durability and efficiency of LSR molds, which can yield thousands of parts.
Why Choose Two-Part Silicone Molding?
Two-Part silicone molding involves mixing two components to create a mold that can accommodate complex geometries and detailed designs. This method is widely used in custom parts manufacturing and arts and crafts. B2B purchasers should be mindful of the need for precise mixing and application techniques, as improper ratios can lead to mold failures or defects in the final product.
What Are the Benefits of Using Translucent Silicone Molds?
Translucent silicone molds allow users to see the casting process, making them ideal for intricate designs and quality control. They are often employed in arts and crafts, as well as in specialized consumer products. While they offer visual advantages, buyers should note that translucent molds typically come at a higher price point than opaque alternatives, so budget considerations are essential.
How Does Overmolding Enhance Product Functionality?
Overmolding is a technique that combines two different materials into a single part, enhancing the functionality and aesthetic appeal of the final product. This method is prevalent in the electronics and automotive sectors, where products benefit from improved grip and reduced vibration. B2B buyers should assess the complexity of their designs and the compatibility of materials, as these factors can significantly influence manufacturing costs and timelines.
Key Industrial Applications of silicone molding
Industry/Sector | Specific Application of Silicone Molding | Value/Benefit for the Business | Key Sourcing Considerations for this Application |
---|---|---|---|
Automotive | Production of complex engine components | Reduces prototyping costs and time, enabling faster market entry. | Ensure high-temperature resistance and durability of silicone. |
Medical Devices | Manufacturing of custom prosthetics | Provides precise replication of anatomical structures for better fit. | Source medical-grade silicone compliant with health regulations. |
Consumer Goods | Creation of custom molds for toys | Enhances product design flexibility and detail for competitive edge. | Look for suppliers with experience in low-volume production. |
Aerospace | Molding parts for aircraft interiors | Lightweight and durable, improving overall aircraft efficiency. | Consider silicone’s thermal stability and weight characteristics. |
Electronics | Encapsulation of sensitive components | Protects against moisture and environmental factors, extending life. | Verify that silicone meets electrical insulation standards. |
How is Silicone Molding Used in the Automotive Industry?
In the automotive sector, silicone molding is crucial for producing complex engine components, gaskets, and seals. The flexibility and durability of silicone allow manufacturers to create prototypes and small batches without the high costs associated with traditional tooling. This approach significantly reduces lead times and enables quicker adjustments based on testing feedback. International buyers should prioritize sourcing silicone that can withstand high temperatures and mechanical stress, ensuring long-lasting performance in demanding environments.
What Role Does Silicone Molding Play in Medical Device Manufacturing?
Silicone molding is essential in the medical device industry, particularly for creating custom prosthetics and surgical tools. The precision offered by silicone molds allows for the accurate replication of anatomical features, ensuring a better fit and improved patient outcomes. Buyers in this sector must seek medical-grade silicone that complies with stringent health regulations and standards, ensuring safety and efficacy in their applications. Additionally, the biocompatibility of silicone is a critical factor for international buyers, particularly in regions with strict medical device regulations.
How is Silicone Molding Beneficial for Consumer Goods?
In the consumer goods industry, silicone molding is widely used for creating custom molds for toys, kitchenware, and decorative items. This method allows for intricate designs and high levels of detail, giving businesses a competitive edge in the market. The versatility of silicone molds also supports low-volume production runs, making it easier for companies to test new designs without significant financial risk. When sourcing silicone for this application, buyers should look for suppliers experienced in producing high-quality molds that can accommodate various materials.
Why is Silicone Molding Important in Aerospace Applications?
Silicone molding plays a vital role in the aerospace sector by enabling the production of lightweight and durable components for aircraft interiors. Silicone’s resistance to extreme temperatures and environmental conditions makes it an ideal choice for parts that must perform reliably under stress. International buyers must consider sourcing silicone that meets aviation industry standards for weight and thermal stability. This ensures that the components contribute to overall aircraft efficiency and safety while maintaining compliance with regulatory requirements.
How Does Silicone Molding Protect Electronic Components?
In the electronics industry, silicone molding is used for encapsulating sensitive components to protect them from moisture, dust, and other environmental factors. This protective layer extends the life of electronic devices and enhances their reliability. When sourcing silicone for encapsulation, buyers should ensure that the material meets electrical insulation standards and is suitable for the specific application. Additionally, the ability to customize silicone formulations for varying levels of flexibility and hardness is a key consideration for international buyers aiming to optimize their products’ performance.
3 Common User Pain Points for ‘silicone molding’ & Their Solutions
Scenario 1: Managing High Production Costs in Silicone Molding
The Problem:
For B2B buyers in industries such as consumer goods or automotive, the costs associated with silicone molding can escalate quickly, especially when transitioning from prototyping to mass production. Buyers often find themselves facing high initial investments for quality silicone materials, which can be a barrier for startups or companies looking to scale. Additionally, the costs may increase due to the need for specialized tools or molds, leading to budget constraints that can hinder product launch timelines.
The Solution:
To mitigate high production costs, buyers should consider a tiered approach to sourcing silicone materials. Start by identifying reputable suppliers who offer a range of silicone grades that cater to different applications. For example, using lower-cost silicone for initial prototypes and switching to higher-grade, durable silicone for final production can balance quality and cost. Additionally, investing in versatile silicone types, like Mold Star™ series, which allow for different applications without needing multiple molds, can further reduce expenses. Always negotiate bulk purchasing agreements with suppliers to lower per-unit costs, and consider leveraging partnerships with local manufacturers to share resources and cut down on transportation costs. By carefully managing material selection and supplier relationships, companies can maintain quality while keeping production expenses in check.
Scenario 2: Ensuring Mold Durability and Performance
The Problem:
A common issue faced by B2B buyers is the premature degradation of silicone molds, which can lead to inconsistent product quality and increased downtime for mold replacements. Industries that rely heavily on silicone molding, such as toy manufacturing or custom crafts, often report that molds wear out faster than expected, resulting in costly production delays and impacting customer satisfaction.
The Solution:
To enhance the longevity and performance of silicone molds, buyers should implement a robust maintenance routine. This includes regular cleaning using mild soap and water to remove any residues that may contribute to mold degradation. Additionally, proper storage is crucial; molds should be stored flat and away from direct sunlight to avoid warping. Buyers can also invest in high-quality silicone options that exhibit low long-term shrinkage and higher tear resistance, such as those from the Mold Star™ series. Furthermore, consider conducting periodic inspections of the molds to assess wear and tear, allowing for proactive replacements before they fail. By prioritizing mold care and investing in durable materials, companies can significantly reduce downtime and maintain consistent production quality.
Scenario 3: Navigating Complex Mold Designs
The Problem:
B2B buyers often encounter challenges when working with complex mold designs, which can result in difficulties during the casting process. Industries like jewelry making or high-precision engineering face specific issues with capturing intricate details, leading to wasted materials and time if the molds do not perform as expected. This can particularly affect companies looking to produce limited runs of customized products.
The Solution:
To tackle the complexities of intricate mold designs, buyers should utilize advanced silicone molding techniques that allow for better detail capture. Start by working with manufacturers that provide specialized silicone products designed for high detail, such as translucent or soft-touch silicones. Employing a two-part mold-making technique can also facilitate complex designs by allowing for the creation of finer details that may not be achievable with single-part molds. Additionally, leveraging technology such as 3D printing to create master patterns can help in producing precise molds more efficiently. Collaborating with experienced mold makers who understand the nuances of silicone molding can provide invaluable insights and techniques that can be applied. By embracing these advanced methods and technologies, companies can improve their product offerings while minimizing material waste and enhancing production efficiency.
Strategic Material Selection Guide for silicone molding
What are the Key Materials for Silicone Molding?
When selecting materials for silicone molding, understanding their properties and applications is crucial for B2B buyers. Here, we analyze four common materials used in silicone molding, focusing on their key properties, advantages, disadvantages, and specific considerations for international buyers.
1. Mold Star™ Silicone Rubber
Key Properties: Mold Star™ silicones are known for their tear resistance and low long-term shrinkage, making them ideal for a variety of applications. They can withstand temperatures up to 450°F (232°C), which is beneficial for casting low-temperature melt metal alloys.
Pros & Cons: One significant advantage is their ease of use, as they require a simple one-to-one mix ratio without the need for vacuum degassing. However, their cost is relatively high compared to latex options, which may deter budget-conscious buyers.
Impact on Application: Mold Star™ silicone is particularly suitable for casting wax, gypsum, and resins, providing excellent detail reproduction. This makes it popular in industries such as jewelry, consumer goods, and prototyping.
Considerations for International Buyers: Buyers from regions like Africa and South America should ensure compliance with local manufacturing standards, as well as ASTM and DIN certifications, to ensure product quality and safety.
2. Room Temperature Vulcanizing (RTV) Silicone
Key Properties: RTV silicone is characterized by its ability to cure at room temperature, providing flexibility and durability. It typically has a temperature resistance ranging from -65°F to 400°F (-54°C to 204°C).
Pros & Cons: The main advantage of RTV silicone is its versatility across various applications, including automotive and consumer products. However, it can be more challenging to work with due to its longer curing times and potential for air bubbles if not mixed properly.
Impact on Application: RTV silicone is often used in applications requiring high detail and precision, such as in the production of intricate molds for collectibles and prototypes.
Considerations for International Buyers: Compliance with international standards such as JIS (Japanese Industrial Standards) is essential for buyers in Europe and the Middle East, particularly in industries with strict quality control measures.
3. High-Performance Silicone
Key Properties: High-performance silicone materials are designed to withstand extreme temperatures and pressures, often rated for use in harsh environments. They exhibit excellent chemical resistance, making them suitable for industrial applications.
Pros & Cons: These silicones offer superior durability and longevity, which can justify their higher cost. However, their manufacturing complexity may require specialized knowledge and equipment, potentially increasing lead times.
Impact on Application: High-performance silicone is ideal for applications in the automotive, aerospace, and medical industries, where reliability and performance are critical.
Considerations for International Buyers: Buyers should verify that high-performance silicones meet specific compliance standards relevant to their industry, such as ISO certifications, to ensure they are sourcing quality materials.
4. Liquid Silicone Rubber (LSR)
Key Properties: Liquid silicone rubber is known for its low viscosity, allowing for intricate designs and fine details. It can withstand temperatures from -60°F to 400°F (-51°C to 204°C) and has excellent elasticity.
Pros & Cons: The primary advantage of LSR is its ability to produce high-quality, repeatable parts with minimal shrinkage. However, the initial investment for LSR processing equipment can be significant, posing a barrier for smaller manufacturers.
Impact on Application: LSR is widely used in consumer electronics, medical devices, and automotive components, where precision and durability are paramount.
Considerations for International Buyers: Buyers from regions like Europe and the Middle East should consider the environmental impact of LSR production and ensure compliance with REACH regulations, which govern the use of chemicals in manufacturing.
Summary Table of Material Selection for Silicone Molding
Material | Typical Use Case for Silicone Molding | Key Advantage | Key Disadvantage/Limitation | Relative Cost (Low/Med/High) |
---|---|---|---|---|
Mold Star™ Silicone Rubber | Jewelry, consumer goods | Easy to use with low shrinkage | Higher cost compared to latex | High |
Room Temperature Vulcanizing | Prototyping, collectibles | Versatile with high detail | Longer curing times, air bubble risk | Medium |
High-Performance Silicone | Automotive, aerospace, medical | Superior durability and chemical resistance | Higher manufacturing complexity | High |
Liquid Silicone Rubber (LSR) | Consumer electronics, medical devices | High-quality, repeatable parts | Significant initial equipment investment | High |
This table provides a quick reference for international B2B buyers to assess the materials suitable for their specific silicone molding needs, taking into account performance characteristics, advantages, limitations, and costs.
In-depth Look: Manufacturing Processes and Quality Assurance for silicone molding
The manufacturing process of silicone molding involves several key stages, each critical for producing high-quality molds that meet diverse applications across industries. Understanding these processes will empower international B2B buyers, particularly from Africa, South America, the Middle East, and Europe, to make informed purchasing decisions.
What Are the Main Stages in the Silicone Molding Manufacturing Process?
Material Preparation: How Is Silicone Prepared for Molding?
The first step in silicone molding is the preparation of silicone materials. This involves selecting the appropriate type of silicone, which can vary based on the application—whether it’s for prototyping, consumer goods, or industrial components.
Typically, silicone is available in two-part systems (a base and a curing agent) that must be mixed in precise ratios, often 1:1 by volume. For specific applications, additives like color pigments or release agents may be incorporated to enhance performance or aesthetics. The mixing must be done thoroughly to avoid air entrapment, which could affect the final product’s quality.
Forming: What Techniques Are Used for Molding Silicone?
Once the material is prepared, it moves to the forming stage. This stage can employ various techniques, including:
- Pouring: The mixed silicone is poured into a mold cavity. This is common for creating intricate designs.
- Injection Molding: For larger production runs, silicone can be injected into a mold under pressure, ensuring uniformity and reducing waste.
- Compression Molding: This technique involves placing a pre-measured amount of silicone into a heated mold, which is then closed to compress the material.
Each technique has its advantages, and the choice often depends on the complexity of the design, production volume, and cost considerations.
Assembly: How Are Silicone Products Assembled?
In many cases, silicone molded parts require assembly, especially when components are produced separately. This can involve bonding, fitting, or mechanical assembly methods. Effective assembly is crucial to maintaining the integrity and functionality of the final product.
For instance, in applications such as automotive or medical devices, precise alignment and secure bonding of silicone components are necessary to ensure performance and safety.
Finishing: What Are the Steps for Finalizing Silicone Products?
The finishing stage involves various processes to enhance the surface quality and functionality of the molded silicone parts. This may include trimming excess material, polishing surfaces, or applying coatings for additional properties such as UV resistance or color.
Finishing is essential for aesthetic appeal and can also contribute to the durability and usability of the final product.
How Is Quality Assurance Implemented in Silicone Molding?
What International Standards Are Relevant for Silicone Molding Quality Control?
Quality assurance in silicone molding is governed by various international standards, with ISO 9001 being one of the most recognized for quality management systems. Compliance with ISO 9001 ensures that manufacturers maintain a consistent quality level in their processes and products.
Additionally, industry-specific certifications such as CE marking for European markets and API standards for the oil and gas industry may apply, depending on the end-use of the silicone products.
What Are the Key Quality Control Checkpoints in Silicone Manufacturing?
Quality control (QC) checkpoints are integral to ensuring that silicone molded products meet specified standards. Common checkpoints include:
-
Incoming Quality Control (IQC): This involves inspecting raw materials before they enter the production process. Ensuring that materials meet specifications is critical to avoiding defects in the final product.
-
In-Process Quality Control (IPQC): During the manufacturing process, regular checks are performed to monitor parameters such as temperature, viscosity, and mixing ratios. This helps identify issues in real-time and allows for immediate corrective actions.
-
Final Quality Control (FQC): Once the silicone products are completed, they undergo final inspections. This may involve dimensional checks, visual inspections for surface defects, and functional testing.
What Testing Methods Are Commonly Used in Silicone Molding Quality Assurance?
Testing methods for silicone products can vary widely based on their intended applications. Common methods include:
- Tensile Testing: To determine the strength and elasticity of the silicone.
- Thermal Stability Testing: To assess how well the silicone performs under extreme temperatures.
- Chemical Resistance Testing: To ensure the silicone can withstand exposure to various chemicals without degrading.
These tests provide valuable insights into the performance and durability of silicone products, helping buyers ensure they meet necessary standards.
How Can B2B Buyers Verify Supplier Quality Control?
What Steps Can Buyers Take to Audit Suppliers?
For international B2B buyers, particularly those from regions like Africa, South America, the Middle East, and Europe, verifying supplier quality control is essential. Here are actionable steps to consider:
-
Supplier Audits: Conducting on-site audits allows buyers to assess the manufacturing processes, quality control measures, and overall operational standards of suppliers.
-
Requesting Quality Reports: Suppliers should provide detailed quality reports, including results from their testing methods and compliance with relevant standards. These documents should be reviewed carefully.
-
Third-Party Inspections: Engaging third-party inspection services can provide an unbiased assessment of the supplier’s capabilities and quality control processes.
What Are the Quality Control Nuances for International Buyers?
When sourcing silicone products internationally, buyers should be aware of specific nuances, including:
-
Regulatory Compliance: Different regions have varying regulations regarding materials, safety, and environmental impact. Ensure that the supplier’s products meet the regulations relevant to your market.
-
Cultural Considerations: Understanding cultural differences in business practices can facilitate better communication and expectations regarding quality and delivery.
-
Language Barriers: Clear communication is vital. Ensure that all quality documentation is available in a language understood by both parties to avoid misunderstandings.
By comprehensively understanding the manufacturing processes and quality assurance methods in silicone molding, international B2B buyers can make informed decisions, ensuring they select suppliers who can deliver high-quality products that meet their specific needs.
Practical Sourcing Guide: A Step-by-Step Checklist for ‘silicone molding’
In the competitive landscape of silicone molding, international B2B buyers must navigate various factors to ensure successful procurement. This practical sourcing guide serves as a checklist to streamline the sourcing process, enabling buyers from regions such as Africa, South America, the Middle East, and Europe to make informed decisions.
1. Step 1: Define Your Technical Specifications
Understanding your product requirements is the first step in sourcing silicone molding. Determine the dimensions, weight, and complexity of the parts you need to produce. Consider the types of silicone that best suit your application, such as heat resistance or flexibility, which can vary based on the intended use.
- Key Considerations:
- Material properties (e.g., hardness, temperature resistance)
- Design complexity and volume of production
2. Step 2: Research Potential Suppliers
Thorough research on potential suppliers is critical. Look for manufacturers with a proven track record in silicone molding and a portfolio that aligns with your industry needs. Utilize online directories and industry forums to gather insights about supplier capabilities and customer feedback.
- Key Considerations:
- Industry certifications (e.g., ISO, CE)
- Customer testimonials and case studies
3. Step 3: Evaluate Supplier Certifications
Before finalizing a supplier, verify their certifications and quality control processes. Suppliers should adhere to international quality standards to ensure that the silicone molds produced are consistent and reliable. This step mitigates risks associated with inferior products and ensures compliance with regulatory requirements in your region.
- Key Considerations:
- Quality assurance protocols
- Compliance with industry-specific regulations
4. Step 4: Request Samples for Testing
Requesting samples is an essential step to assess the quality and suitability of the silicone molds. Evaluate the samples for durability, flexibility, and precision in capturing details. This hands-on approach allows you to identify any potential issues before committing to larger orders.
- Key Considerations:
- Performance under various conditions
- Ease of use in your production process
5. Step 5: Understand Pricing and Terms
Engage in discussions about pricing structures and payment terms with potential suppliers. Understanding the total cost of ownership, including shipping and potential tariffs, is vital for budgeting. Look for transparency in pricing to avoid hidden costs that could impact your bottom line.
- Key Considerations:
- Comparison of quotes from multiple suppliers
- Clarity on payment terms and conditions
6. Step 6: Assess Production Capabilities
Evaluate the supplier’s production capabilities to ensure they can meet your volume requirements. Inquire about their production lead times and capacity to handle both small and large runs. A supplier’s flexibility in scaling production can be a significant advantage.
- Key Considerations:
- Lead times for production and delivery
- Availability of advanced manufacturing technologies
7. Step 7: Establish Communication and Support
Effective communication is crucial for a successful partnership. Ensure the supplier offers robust customer support and is responsive to inquiries. Establishing a clear line of communication helps facilitate problem-solving and enhances collaboration throughout the project lifecycle.
- Key Considerations:
- Responsiveness and availability of support staff
- Clarity in communication regarding project updates
By following this checklist, B2B buyers can effectively navigate the sourcing process for silicone molding, ensuring they select the right suppliers to meet their manufacturing needs.
Comprehensive Cost and Pricing Analysis for silicone molding Sourcing
What Are the Key Cost Components in Silicone Molding Sourcing?
When sourcing silicone molding, understanding the cost structure is essential for international B2B buyers. The main components that influence the total cost include:
-
Materials: Silicone rubber is the primary material, and prices can vary significantly based on the type and quality. High-performance silicones, such as those with specialized properties like low shrinkage or high-temperature resistance, tend to be more expensive. Expect to pay upwards of $100 per gallon for quality silicone.
-
Labor: Skilled labor is required for mold making and production. Labor costs can vary widely by region, with higher costs often found in Europe and North America compared to Africa and South America. Consider the skill level of the workforce and the complexity of the molds being produced.
-
Manufacturing Overhead: This includes costs related to facility maintenance, utilities, and equipment depreciation. Overhead can be significant, especially if specialized equipment is required for high-precision molds.
-
Tooling: Initial tooling costs can be substantial, particularly for custom molds. These costs often include design and engineering services. Buyers should factor in these upfront costs when budgeting for silicone molding projects.
-
Quality Control (QC): Ensuring product quality requires investment in testing and inspection processes. This is crucial, as defects in molds can lead to costly production delays and increased scrap rates.
-
Logistics: Shipping and handling costs can add to the overall price, especially for international transactions. Factors such as distance, shipping method, and customs duties should be considered.
-
Margin: Suppliers typically apply a markup to cover their costs and desired profit margins. Understanding typical margins in the industry can help buyers negotiate better pricing.
How Do Price Influencers Affect Silicone Molding Costs?
Several factors can influence the pricing of silicone molds:
-
Volume/MOQ: Larger orders generally lead to lower per-unit costs. Suppliers may offer discounts for minimum order quantities (MOQs), so it’s beneficial for buyers to consolidate their orders.
-
Specifications and Customization: Custom molds with specific designs or materials can drive up costs. Clearly defining requirements upfront can help avoid unexpected expenses.
-
Materials: The choice of silicone type (e.g., food-grade, high-temperature) impacts pricing. Buyers should assess their specific needs to select the appropriate material without overspending.
-
Quality and Certifications: Molds that meet stringent industry standards or certifications may carry higher costs. While these certifications can assure quality, buyers should weigh them against their own quality requirements.
-
Supplier Factors: The reputation and reliability of the supplier can affect pricing. Established suppliers may charge more due to their experience and quality assurance processes, but they can also reduce risk.
-
Incoterms: Understanding shipping terms is critical, as they dictate who is responsible for various costs and risks during transportation. This can influence the final price significantly.
What Are the Best Buyer Tips for Negotiating Silicone Molding Prices?
For international buyers, particularly those in Africa, South America, the Middle East, and Europe, here are actionable tips to ensure cost efficiency:
-
Negotiate Effectively: Always negotiate pricing, especially for larger orders. Suppliers may have flexibility in pricing, especially if they want to secure a long-term partnership.
-
Consider Total Cost of Ownership (TCO): Evaluate not just the initial purchase price but also ongoing costs associated with maintenance, quality control, and logistics. This holistic approach can lead to better long-term savings.
-
Understand Pricing Nuances: Different regions may have varying pricing structures due to labor costs, material availability, and shipping complexities. Conduct market research to understand these factors in your target sourcing regions.
-
Build Relationships: Establishing a good rapport with suppliers can lead to better pricing and service. Suppliers are often more willing to negotiate with buyers who demonstrate commitment and reliability.
-
Seek Multiple Quotes: Always obtain quotes from several suppliers to compare prices and services. This practice not only provides insight into the market but also strengthens your negotiating position.
By applying these insights, international B2B buyers can effectively navigate the complexities of sourcing silicone molding, ensuring they achieve the best value for their investments.
Alternatives Analysis: Comparing silicone molding With Other Solutions
In today’s competitive manufacturing landscape, B2B buyers need to carefully consider various molding techniques to meet their production needs. Silicone molding is a popular choice, but it’s essential to evaluate alternatives that may better suit specific project requirements, budgets, or production volumes. This analysis provides a comparative overview of silicone molding against two viable alternatives: 3D Printing and Injection Molding.
Comparison Table: Evaluating Silicone Molding Against Alternatives
Comparison Aspect | Silicone Molding | 3D Printing | Injection Molding |
---|---|---|---|
Performance | High flexibility and detail; suitable for low-volume runs. | Excellent for complex designs; ideal for prototypes. | High efficiency for mass production; consistent quality. |
Cost | Higher material costs; lower setup costs. | Equipment and material costs vary; economical for small runs. | High initial tooling costs; economical for large volumes. |
Ease of Implementation | Simple setup; requires minimal training. | User-friendly for designers; requires knowledge of CAD. | Complex setup; requires specialized skills and resources. |
Maintenance | Low; requires basic cleaning and storage. | Low to moderate; depends on printer maintenance. | High; molds need regular upkeep and replacement. |
Best Use Case | Prototyping, small batches, custom designs. | Prototyping, complex geometries, one-off parts. | High-volume production, consistent parts. |
What Are the Advantages and Disadvantages of 3D Printing?
3D Printing has gained traction as a versatile manufacturing method, especially for prototyping and producing intricate designs. The key advantages include the ability to create complex geometries that are often impossible to achieve with traditional methods. Additionally, 3D printing can be more cost-effective for small production runs since it eliminates the need for expensive molds. However, the material properties may not match those produced through silicone or injection molding, which can limit its application in high-stress environments. Furthermore, the speed of production may lag behind that of injection molding for large quantities.
What Are the Benefits and Drawbacks of Injection Molding?
Injection Molding is a well-established technique known for its efficiency in mass production. It allows manufacturers to produce a high volume of parts quickly and with consistent quality. The initial costs for tooling can be quite high, making it less suitable for small runs. However, the per-unit cost decreases significantly as production volumes increase, making it an economical choice for large-scale manufacturing. A downside is the longer lead time for mold creation and the requirement for specialized skills to manage the process. Additionally, design changes can be costly and time-consuming once molds are created.
How Should B2B Buyers Choose the Right Solution?
When considering the right molding solution, B2B buyers should first assess their specific needs regarding volume, complexity, and budget. If the priority is on custom designs and flexibility for small batches, silicone molding may be the best fit. For complex prototypes or one-off parts, 3D printing stands out as a valuable alternative. In contrast, if the project demands high-volume production with tight tolerances, injection molding could be the most efficient choice. Ultimately, a thorough evaluation of these factors will guide buyers in selecting the most effective molding method for their unique requirements.
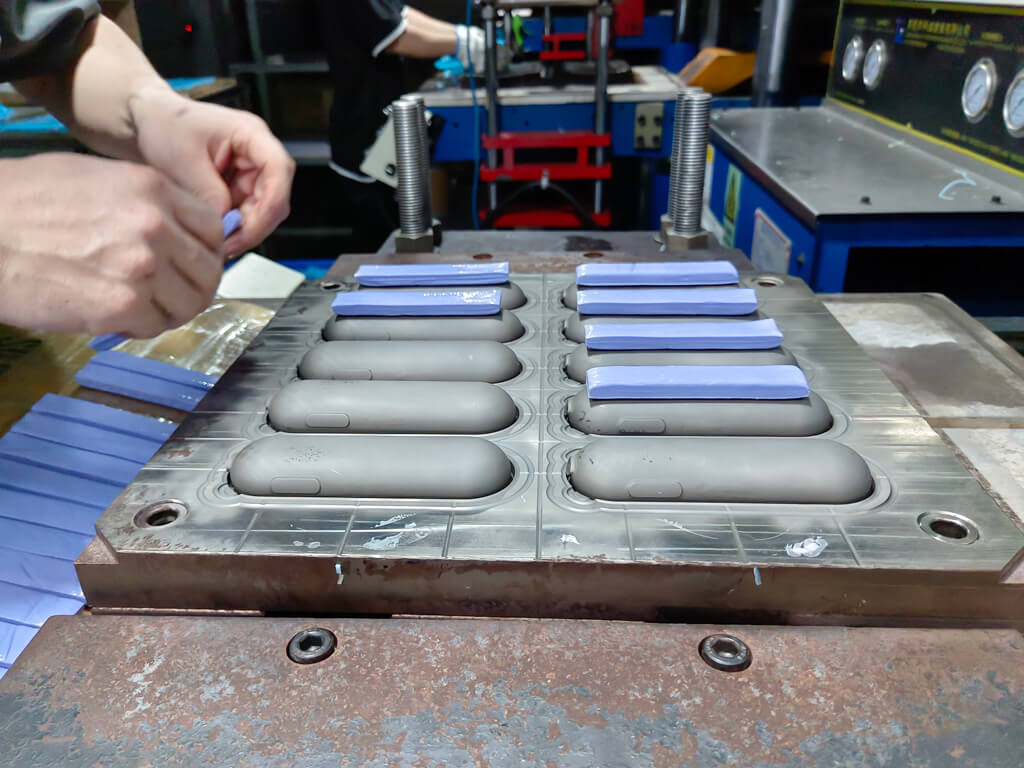
A stock image related to silicone molding.
Essential Technical Properties and Trade Terminology for silicone molding
What Are the Key Technical Properties of Silicone Molding?
When evaluating silicone molding for your B2B needs, understanding its technical properties is crucial. Here are some essential specifications to consider:
1. Material Grade
Material grades in silicone molding determine the performance and suitability of the silicone for specific applications. Higher-grade silicones typically offer enhanced durability, heat resistance, and chemical stability. For B2B buyers, selecting the appropriate material grade can mean the difference between a successful product launch and costly failures.
2. Tensile Strength
Tensile strength measures the maximum stress that silicone can withstand while being stretched. This property is critical for ensuring that the molds will maintain their shape and integrity during the casting process. For manufacturers, understanding tensile strength helps in predicting the lifespan of molds and minimizing production downtime.
3. Temperature Resistance
Silicone molds can typically endure a wide range of temperatures, often from -65°C to 400°C. This versatility allows them to be used in various industries, from food production to automotive. For buyers, knowing the temperature resistance of silicone can guide you in selecting the right product for high-temperature applications, ensuring safety and compliance with industry standards.
4. Cure Time
Cure time refers to the duration required for the silicone to fully harden after mixing. Silicone formulations can vary from fast-curing (around 30 minutes) to slower options (up to several hours). For B2B operations, understanding cure times can optimize production schedules and reduce lead times, thus enhancing overall efficiency.
5. Elongation at Break
This property indicates how much a silicone mold can stretch before breaking. A high elongation percentage (up to 700% in some formulations) allows for easier removal of cast parts without damaging either the mold or the product. For international buyers, this characteristic can be crucial for projects involving complex geometries or intricate designs.
6. Shrinkage Rate
Shrinkage rate refers to the change in dimensions of silicone after curing. Low shrinkage rates are desirable, as they ensure that the final product closely matches the original design specifications. Understanding shrinkage rates helps B2B buyers avoid costly rework and maintain product consistency.
What Are Common Trade Terms Used in Silicone Molding?
Understanding industry jargon can help streamline communication and negotiations in the silicone molding supply chain. Here are some key terms you should know:
1. OEM (Original Equipment Manufacturer)
OEM refers to companies that produce parts or equipment that may be marketed by another manufacturer. In silicone molding, knowing your OEM can help ensure that you’re sourcing high-quality products from reliable suppliers.
2. MOQ (Minimum Order Quantity)
MOQ is the smallest amount of a product that a supplier is willing to sell. For international buyers, understanding MOQs can help in budgeting and inventory management, ensuring you don’t overcommit financially.
3. RFQ (Request for Quotation)
An RFQ is a document sent to suppliers to request pricing and availability for specific products or services. For B2B buyers, submitting a detailed RFQ can lead to better pricing and terms, as it provides suppliers with the necessary information to create competitive offers.
4. Incoterms (International Commercial Terms)
Incoterms are a set of rules that define responsibilities and risks in international shipping. Familiarity with Incoterms helps B2B buyers clarify shipping obligations and costs, minimizing misunderstandings during cross-border transactions.
5. Lead Time
Lead time refers to the total time it takes from placing an order to receiving the goods. Understanding lead times is essential for effective project planning, especially in industries where time-to-market is critical.
6. TPE (Thermoplastic Elastomer)
TPE is a type of polymer that behaves like rubber but can be processed like plastic. In silicone molding discussions, knowing the difference between silicone and TPE can guide product selection based on performance requirements.
By understanding these technical properties and industry terms, international B2B buyers can make informed decisions that align with their manufacturing needs and strategic goals.
Navigating Market Dynamics and Sourcing Trends in the silicone molding Sector
What Are the Key Market Trends in the Silicone Molding Sector?
The silicone molding sector is currently experiencing significant growth driven by advancements in manufacturing technologies and increasing demand across various industries such as automotive, consumer goods, and healthcare. International B2B buyers, particularly from regions like Africa, South America, the Middle East, and Europe, are increasingly recognizing the advantages of silicone molds, including their durability, flexibility, and resistance to extreme temperatures.
Emerging technologies such as 3D printing are being integrated into silicone molding processes, allowing for rapid prototyping and more complex designs. This shift is particularly beneficial for companies looking to reduce lead times and adapt quickly to changing market demands. Furthermore, the trend towards customization is pushing manufacturers to adopt silicone molds, as they can be tailored for specific applications without the high costs associated with traditional tooling methods.
Additionally, the shift towards digital marketplaces and e-commerce platforms is making it easier for international buyers to source silicone molding materials and services. Platforms that aggregate suppliers and provide reviews can help buyers from different regions navigate the complexities of sourcing, enabling them to make informed decisions.
How Can Sustainability and Ethical Sourcing Impact the Silicone Molding Industry?
Sustainability is becoming a critical concern for international B2B buyers, and the silicone molding sector is not immune to these pressures. The environmental impact of silicone production, while generally lower than that of other materials, still raises questions about the sourcing of raw materials and the lifecycle of silicone products. Buyers are increasingly looking for suppliers who demonstrate a commitment to sustainable practices, including the use of recycled materials and processes that minimize waste.
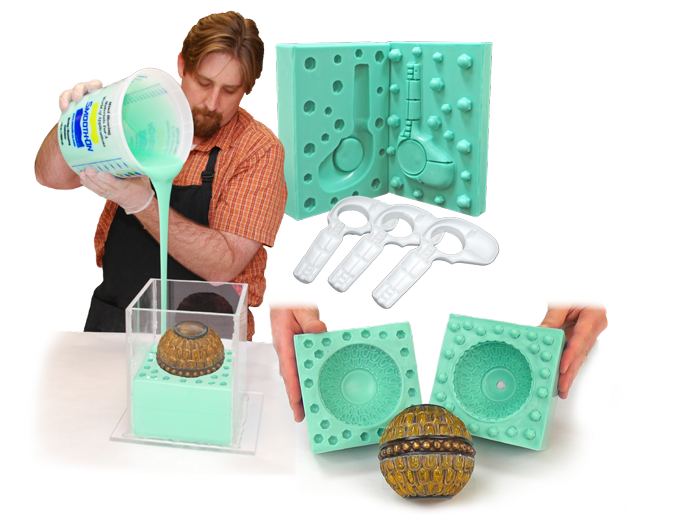
A stock image related to silicone molding.
Ethical supply chains are also gaining importance. Buyers are encouraged to work with manufacturers who provide transparency regarding their sourcing practices and labor conditions. Certifications like ISO 14001 for environmental management and other ‘green’ certifications can help buyers identify suppliers that are committed to sustainable practices.
In addition, innovations in silicone materials, such as bio-based silicones, are emerging as viable alternatives for environmentally conscious buyers. These materials not only reduce the carbon footprint associated with traditional silicone but also cater to the growing demand for sustainable products across various industries.
What Is the Historical Context of Silicone Molding in B2B?
The history of silicone molding can be traced back to the mid-20th century when silicone rubber was first developed. Initially used in specialized applications, its versatility soon led to widespread adoption across multiple sectors. The transition from traditional materials to silicone was largely driven by its superior properties, such as heat resistance and flexibility.
Over the decades, the development of new silicone formulations has expanded its applications significantly, enabling more complex designs and high-volume production. Today, silicone molding is recognized not only for its functional benefits but also for its ability to meet the demands of modern consumers who increasingly value customization and sustainability. As the market continues to evolve, understanding this historical context can help international B2B buyers appreciate the material’s potential and make informed sourcing decisions.
In conclusion, navigating the silicone molding sector involves understanding key market dynamics, the importance of sustainability, and the historical evolution of the material, all of which are critical for making strategic sourcing decisions in today’s competitive landscape.
Frequently Asked Questions (FAQs) for B2B Buyers of silicone molding
-
How do I choose the right silicone molding supplier for my business needs?
Choosing the right silicone molding supplier involves several key steps. First, assess the supplier’s experience and specialization in your specific industry. Look for certifications and quality standards that align with your needs. Request samples to evaluate their product quality and durability. Additionally, check customer reviews and testimonials to gauge their reliability. It’s also crucial to communicate your specific requirements, including customization options and production timelines, to ensure they can meet your expectations. -
What is the best type of silicone for custom mold making?
The best type of silicone for custom mold making often depends on your specific application. For general purposes, Mold Star™ silicones are highly recommended due to their flexibility, durability, and low shrinkage properties. For high-temperature applications, silicone formulations with heat resistance up to 450°F (232°C) are ideal. Always consider the material you will be casting into the mold, as some silicones are better suited for certain materials like wax, resins, or metals. Consulting with your supplier can help determine the best option for your project. -
What are the minimum order quantities (MOQ) for silicone molds?
Minimum order quantities for silicone molds can vary significantly among suppliers and are often influenced by factors such as the complexity of the mold design and production capabilities. Generally, MOQs can range from as low as 10 units for simpler molds to hundreds for more intricate designs. It’s advisable to discuss your specific needs with potential suppliers to negotiate favorable terms and ensure that they can accommodate your production scale. -
What payment terms should I expect when sourcing silicone molds internationally?
Payment terms for international sourcing of silicone molds typically vary by supplier and may include options such as upfront payments, net 30 or 60 days, or even letters of credit for larger orders. It’s essential to establish clear payment conditions before finalizing contracts. Discussing payment security measures, such as escrow services, can help mitigate risks. Ensure that you also understand any additional costs related to international shipping and customs duties that may impact the overall budget. -
How can I ensure quality assurance for silicone molds?
To ensure quality assurance for silicone molds, start by selecting a supplier with a robust quality management system. Request detailed documentation, such as material certifications and test reports, to verify compliance with industry standards. Conduct regular audits and reviews of the manufacturing process, and consider implementing a third-party inspection service for larger orders. Establish clear communication channels for feedback and issue resolution to maintain quality throughout the production process. -
What are the logistics considerations when importing silicone molds?
Logistics considerations for importing silicone molds include understanding shipping options, customs regulations, and potential tariffs. Evaluate the most cost-effective shipping methods, whether by air or sea, based on your delivery timeline. Ensure that your supplier provides all necessary documentation for customs clearance, such as invoices and packing lists. Collaborating with a reliable freight forwarder can streamline the import process and help navigate any challenges related to international shipping. -
What customization options are available for silicone molds?
Customization options for silicone molds are extensive and can include variations in size, shape, and design features. Many suppliers offer the ability to create molds based on your specific product requirements, including details such as texture and surface finish. You may also explore options for colors and additives that enhance the mold’s performance or aesthetic appeal. Discussing your project specifics with the supplier will help identify available customization features that meet your needs. -
How does silicone molding compare to other manufacturing processes?
Silicone molding offers several advantages over traditional manufacturing processes like injection molding. It is often more cost-effective for small production runs, as it requires less upfront investment in tooling. Silicone molds also provide greater flexibility in design, allowing for intricate and complex shapes. Additionally, silicone’s durability and resistance to heat and chemicals make it a superior choice for various applications. However, for large-scale production, injection molding may be more efficient. Evaluating your production volume and design complexity will help determine the best method for your project.
Important Disclaimer & Terms of Use
⚠️ Important Disclaimer
The information provided in this guide, including content regarding manufacturers, technical specifications, and market analysis, is for informational and educational purposes only. It does not constitute professional procurement advice, financial advice, or legal advice.
While we have made every effort to ensure the accuracy and timeliness of the information, we are not responsible for any errors, omissions, or outdated information. Market conditions, company details, and technical standards are subject to change.
B2B buyers must conduct their own independent and thorough due diligence before making any purchasing decisions. This includes contacting suppliers directly, verifying certifications, requesting samples, and seeking professional consultation. The risk of relying on any information in this guide is borne solely by the reader.
Strategic Sourcing Conclusion and Outlook for silicone molding
What Are the Key Takeaways for Strategic Sourcing in Silicone Molding?
In summary, strategic sourcing in silicone molding presents significant advantages for international B2B buyers. By leveraging silicone’s durability, flexibility, and resistance to various conditions, companies can enhance their product development processes while reducing costs associated with traditional manufacturing methods. Whether you are involved in prototyping, consumer goods, or intricate designs in jewelry, understanding the nuances of silicone mold production can lead to superior product outcomes.
How Can International Buyers Optimize Their Sourcing Strategy?
To maximize benefits, buyers from Africa, South America, the Middle East, and Europe should consider establishing partnerships with reputable suppliers who offer high-quality silicone materials and tailored solutions. This approach not only ensures access to innovative molding technologies but also fosters collaboration that can drive efficiency and sustainability in production.
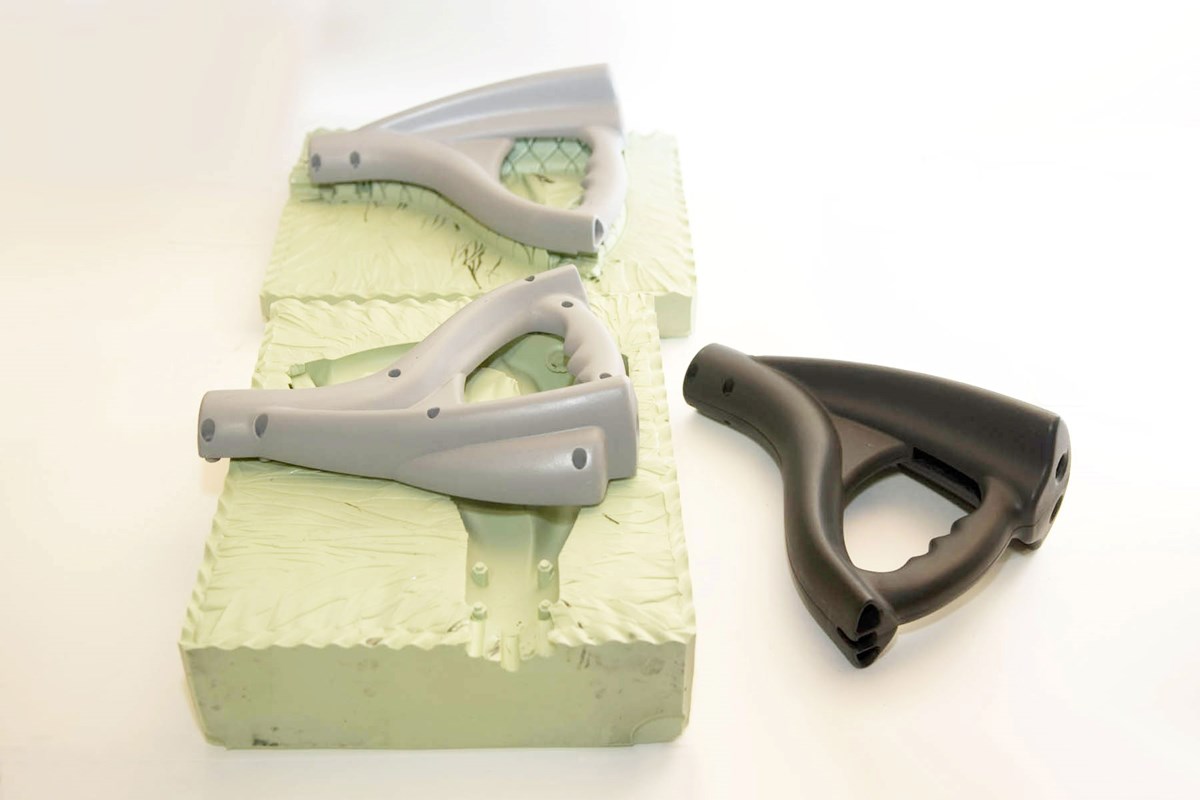
A stock image related to silicone molding.
What’s Next for the Future of Silicone Molding?
As the demand for custom and sustainable products continues to rise, the silicone molding industry is poised for growth. International buyers should stay informed about emerging trends and technologies that can further enhance product quality and reduce lead times. Engaging in continuous learning and networking within the industry will be essential for capitalizing on new opportunities. Embrace the future of silicone molding by taking proactive steps today—connect with trusted suppliers and explore innovative applications that can elevate your business.