Master Sourcing Carbon Fiber CNC Machines for Superior
Introduction: Navigating the Global Market for carbon fiber cnc machine
In today’s competitive landscape, the demand for carbon fiber CNC machines is surging as industries seek to leverage the unique properties of carbon fiber composites. These machines offer unparalleled precision and efficiency, enabling manufacturers to produce lighter, stronger components that are crucial in sectors ranging from aerospace to automotive. With the global market for carbon fiber parts projected to grow significantly, understanding the nuances of sourcing and utilizing CNC machines for carbon fiber is essential for international B2B buyers.
This comprehensive guide will serve as your roadmap through the intricacies of the carbon fiber CNC machine market. You will explore various types of machines, the materials utilized in their construction, and the critical manufacturing and quality control processes that ensure high-performance outputs. Additionally, the guide will cover insights on potential suppliers, pricing structures, and market trends, equipping you with the knowledge needed to make informed purchasing decisions.
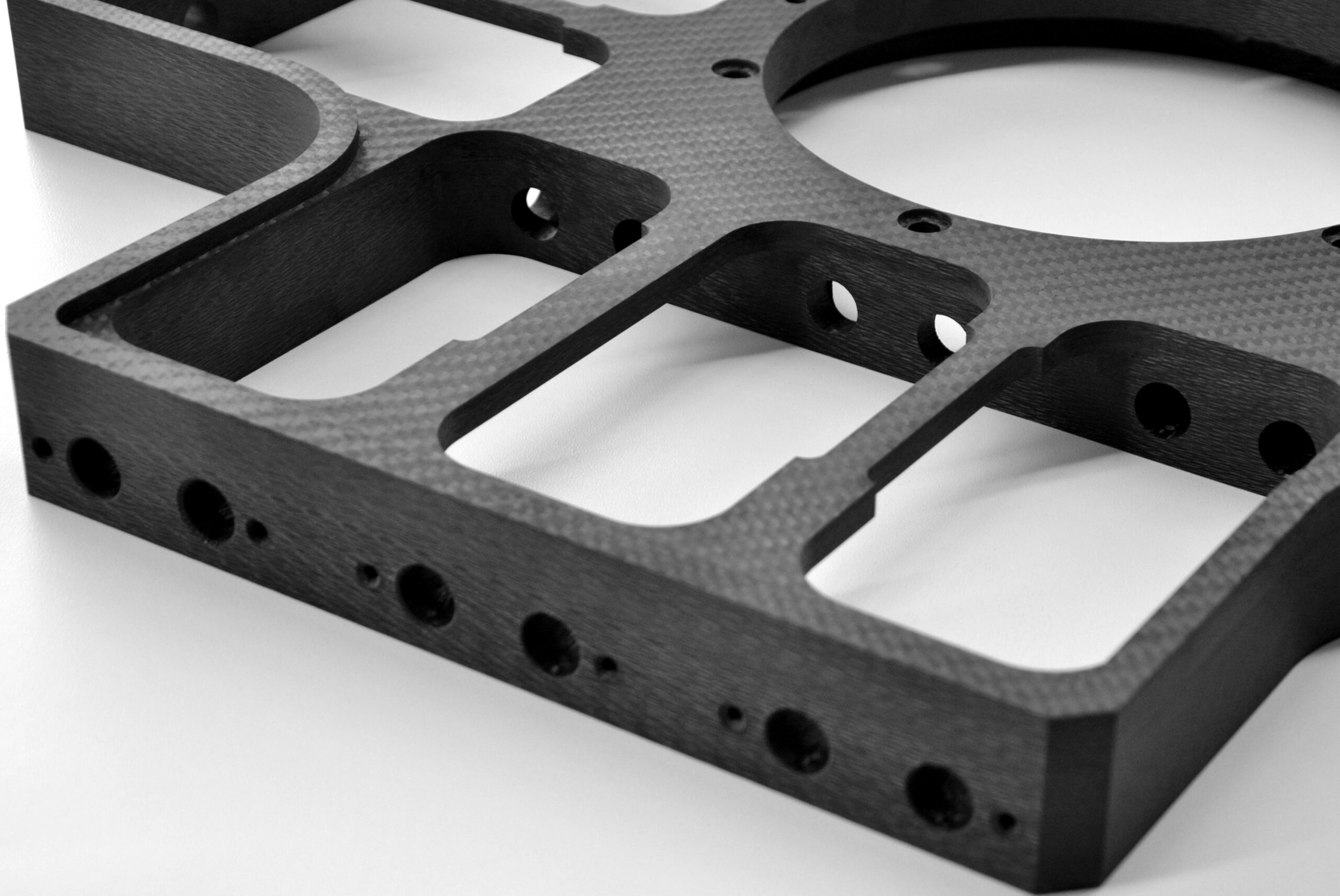
Illustrative Image (Source: Google Search)
Particularly for buyers from Africa, South America, the Middle East, and Europe, this guide empowers you to navigate the complexities of international sourcing. By understanding the key factors influencing the carbon fiber CNC machine market, you can optimize your procurement strategies, enhance product quality, and maintain a competitive edge in your industry. Prepare to unlock valuable insights that will transform your approach to sourcing carbon fiber CNC machines and drive your business forward.
Understanding carbon fiber cnc machine Types and Variations
Type Name | Key Distinguishing Features | Primary B2B Applications | Brief Pros & Cons for Buyers |
---|---|---|---|
3-Axis CNC Machines | Simple design, suitable for basic cutting and shaping | Automotive parts, furniture, signage | Pros: Cost-effective, easy to operate. Cons: Limited in complexity of shapes. |
5-Axis CNC Machines | Ability to work on multiple sides of a part simultaneously | Aerospace components, molds, prototypes | Pros: High precision, complex geometries. Cons: Higher cost, requires skilled operators. |
CNC Routers | Typically larger workspaces, ideal for flat materials | Sign making, cabinetry, artistic designs | Pros: Versatile, can handle large sheets. Cons: Less effective for intricate details compared to milling machines. |
Laser CNC Machines | Uses lasers for cutting, engraving, and marking | Aerospace, automotive, custom signage | Pros: High precision, minimal material waste. Cons: Limited to certain thicknesses and materials. |
Hybrid CNC Machines | Combines additive and subtractive manufacturing techniques | Aerospace, automotive, medical devices | Pros: Versatile, can create complex parts. Cons: More expensive, complex setup. |
3-Axis CNC Machines
3-axis CNC machines are the most basic form of CNC technology, operating along the X, Y, and Z axes. They are ideal for straightforward cutting and shaping tasks, making them suitable for industries like automotive, furniture, and signage. When considering a purchase, buyers should evaluate the machine’s speed and precision, as well as the cost-effectiveness for simpler projects. While they are user-friendly and affordable, their limitations in producing complex shapes should be acknowledged.
5-Axis CNC Machines
5-axis CNC machines provide the capability to manipulate tools on five different axes simultaneously. This allows for intricate designs and multi-sided machining, making them indispensable in aerospace and mold-making industries. Buyers must consider the initial investment and the need for skilled operators to fully utilize the machine’s capabilities. While they offer exceptional precision and versatility, the complexity of operation can be a barrier for some businesses.
CNC Routers
CNC routers are characterized by their larger workspaces and are primarily designed for flat materials. They are widely used in sign-making, cabinetry, and artistic applications. B2B buyers should assess the router’s versatility and ability to handle large sheets of material. While routers are adaptable and efficient for larger projects, they may not be as effective for intricate details compared to milling machines.
Laser CNC Machines
Laser CNC machines utilize high-powered lasers for cutting, engraving, and marking materials. They are especially popular in the aerospace and automotive sectors due to their precision and minimal material waste. Buyers should focus on the machine’s capability to handle various materials and thicknesses. Despite their advantages in accuracy and speed, laser machines have limitations regarding the types of materials they can process effectively.
Hybrid CNC Machines
Hybrid CNC machines integrate both additive and subtractive manufacturing technologies, making them highly versatile. They are suited for complex applications in industries such as aerospace, automotive, and medical device manufacturing. When purchasing, buyers should evaluate the machine’s capabilities in both methods and its overall cost-effectiveness. While hybrids can produce intricate parts with efficiency, their higher price point and complexity can be a drawback for some buyers.
Related Video: CS 198-126: Lecture 12 – Diffusion Models
Key Industrial Applications of carbon fiber cnc machine
Industry/Sector | Specific Application of carbon fiber cnc machine | Value/Benefit for the Business | Key Sourcing Considerations for this Application |
---|---|---|---|
Aerospace | Manufacturing of aircraft components | Reduced weight leading to fuel efficiency | Compliance with aviation standards and certifications |
Automotive | Production of lightweight vehicle parts | Enhanced performance and fuel economy | Material compatibility and CNC machining capabilities |
Medical Devices | Creation of custom prosthetics and implants | Improved patient outcomes and product longevity | Precision machining and biocompatibility requirements |
Sporting Goods | Fabrication of high-performance sports equipment | Superior strength-to-weight ratio | Customization options and rapid prototyping capabilities |
Marine | Building lightweight and durable boat components | Increased speed and fuel efficiency | Resistance to environmental factors and corrosion |
Aerospace
In the aerospace sector, carbon fiber CNC machines are pivotal in the production of lightweight aircraft components, such as fuselage sections, wings, and tail structures. The significant reduction in weight achieved through the use of carbon fiber composites enhances fuel efficiency, which is critical in an industry facing stringent environmental regulations. International buyers must ensure that their suppliers adhere to aviation standards, such as AS9100, and can demonstrate experience in producing parts that meet rigorous safety and performance criteria.
Automotive
The automotive industry increasingly relies on carbon fiber CNC machining for the production of lightweight vehicle parts like body panels, chassis, and drive shafts. This shift not only improves vehicle performance and fuel economy but also meets consumer demand for eco-friendly transportation options. Buyers should consider suppliers with expertise in automotive-grade materials and CNC capabilities that ensure precision and consistency, especially when dealing with high-performance applications in regions like Europe and South America, where regulations are particularly stringent.
Medical Devices
In the medical field, carbon fiber CNC machines are utilized to manufacture custom prosthetics and implants tailored to individual patient needs. The lightweight nature of carbon fiber contributes to improved patient comfort and mobility while ensuring durability and longevity of the devices. Buyers in this sector should prioritize suppliers who can provide biocompatible materials and demonstrate precision machining capabilities, as well as compliance with medical device regulations such as ISO 13485.
Sporting Goods
The sporting goods industry benefits from carbon fiber CNC machining through the production of high-performance equipment, including bicycles, golf clubs, and tennis rackets. The unique strength-to-weight ratio of carbon fiber allows manufacturers to create products that enhance athletic performance. For B2B buyers, it is essential to source from suppliers who offer customization options and rapid prototyping capabilities, enabling quick adjustments to designs based on athlete feedback, particularly in competitive markets across Africa and Europe.
Marine
In marine applications, carbon fiber CNC machines are employed to create lightweight and durable components for boats and yachts, such as hulls and masts. The reduced weight translates to increased speed and better fuel efficiency, essential for competitive sailing and recreational boating. Buyers should focus on sourcing materials that provide resistance to environmental factors, such as UV radiation and corrosion, and seek suppliers with experience in marine-grade carbon fiber composites to ensure longevity and performance in harsh conditions.
Related Video: Carbon Fiber Prepreg Flatbed Digital CNC Cutting Machine
Strategic Material Selection Guide for carbon fiber cnc machine
When selecting materials for carbon fiber CNC machining, it’s crucial to consider various factors that influence performance, cost, and application suitability. Below is an analysis of four common materials used in conjunction with carbon fiber, each evaluated from a B2B perspective.
1. Epoxy Resins
Key Properties:
Epoxy resins are known for their excellent adhesion, chemical resistance, and mechanical properties. They can withstand temperatures up to 150°C and offer good resistance to moisture and various chemicals.
Pros & Cons:
Epoxy resins are durable and provide a strong bond, making them suitable for high-performance applications. However, they can be expensive and may require precise mixing and curing processes, which can complicate manufacturing.
Impact on Application:
Epoxy resins are compatible with a wide range of media, making them ideal for aerospace and automotive applications where exposure to various chemicals is common.
Considerations for International Buyers:
Buyers should ensure compliance with international standards such as ASTM D638 for tensile properties and ASTM D570 for water absorption. Understanding local regulations regarding chemical handling is also essential.
2. Phenolic Resins
Key Properties:
Phenolic resins exhibit excellent thermal stability and flame resistance, withstanding temperatures up to 200°C. They are also resistant to moisture and many chemicals.
Pros & Cons:
The key advantage of phenolic resins is their fire-resistant properties, making them suitable for applications in the aerospace and automotive industries. However, they can be brittle and may not provide the same level of adhesion as epoxy resins.
Impact on Application:
Due to their high-temperature resistance, phenolic resins are often used in environments where heat exposure is a concern, such as in electrical insulation applications.
Considerations for International Buyers:
Compliance with fire safety standards, such as UL 94 for flammability, is critical. Buyers should also consider the availability of phenolic resins in their region, as sourcing may vary significantly.
3. Polyester Resins
Key Properties:
Polyester resins are less expensive than epoxy and phenolic resins and offer good mechanical properties. They typically have a lower temperature resistance, around 120°C.
Pros & Cons:
The primary advantage is their cost-effectiveness, making them suitable for large-scale production. However, they are less durable and have inferior chemical resistance compared to epoxy and phenolic resins.
Impact on Application:
Polyester resins are often used in automotive and consumer goods applications where cost is a significant factor, but they may not be suitable for high-performance environments.
Considerations for International Buyers:
Buyers should be aware of the varying quality standards in different regions and ensure that the polyester resins meet local compliance requirements, such as ISO standards.
4. Bismaleimide (BMI) Resins
Key Properties:
BMI resins are known for their high thermal stability and mechanical strength, withstanding temperatures up to 250°C. They also exhibit excellent chemical resistance.
Pros & Cons:
BMI resins are ideal for high-performance applications, particularly in aerospace. However, they are more challenging to process and can be costly, which may limit their use in some markets.
Impact on Application:
Their superior properties make BMI resins suitable for components that require high strength and thermal resistance, such as in aerospace and advanced automotive applications.
Considerations for International Buyers:
Understanding the specific processing requirements and ensuring compliance with aerospace standards (such as AS9100) is essential for buyers in the aerospace sector.
Summary Table
Material | Typical Use Case for carbon fiber cnc machine | Key Advantage | Key Disadvantage/Limitation | Relative Cost (Low/Med/High) |
---|---|---|---|---|
Epoxy Resins | Aerospace components, automotive parts | Excellent adhesion and durability | High cost and complex processing | High |
Phenolic Resins | Electrical insulation, aerospace applications | Fire resistance and thermal stability | Brittle and lower adhesion | Med |
Polyester Resins | Automotive parts, consumer goods | Cost-effective for large production | Lower durability and chemical resistance | Low |
BMI Resins | Aerospace, advanced automotive components | High thermal stability and strength | Challenging to process and costly | High |
This guide provides international B2B buyers with essential insights into material selection for carbon fiber CNC machining, ensuring informed decisions that align with performance requirements and regional standards.
In-depth Look: Manufacturing Processes and Quality Assurance for carbon fiber cnc machine
Manufacturing carbon fiber CNC machines involves several critical stages, each requiring precision and adherence to quality standards. Understanding these processes is essential for international B2B buyers, particularly those from Africa, South America, the Middle East, and Europe, to ensure they are investing in reliable and high-performance equipment.
Manufacturing Processes
Material Preparation
The first stage in the manufacturing process is material preparation, which involves selecting high-quality carbon fiber and resin systems. The carbon fiber can come in various forms, such as unidirectional sheets or woven fabrics, depending on the application requirements. Resins, primarily epoxy, are chosen for their strong bonding properties and thermal stability.
- Key Techniques:
- Material Sourcing: Ensure suppliers use high-grade carbon fiber from reputable manufacturers to guarantee performance.
- Cutting and Layering: Materials are cut to size and layered according to the specifications of the machine design, considering factors like weight distribution and strength.
Forming
The forming stage is where the carbon fiber is shaped into its final configuration. This process can involve several methods, including:
- Lay-up: Manual or automated placement of carbon fiber layers saturated with resin.
- Prepreg: Use of pre-impregnated carbon fiber that simplifies the lay-up process and ensures consistent resin distribution.
- Molding: Techniques such as vacuum bagging or autoclave curing are employed to consolidate the layers under heat and pressure, enhancing the material’s strength.
Assembly
Once the components are formed, they proceed to the assembly stage. This includes integrating the CNC machine’s mechanical and electronic systems.
- Key Techniques:
- Precision Alignment: Ensuring all parts are aligned to prevent operational issues.
- Fastening: Using specialized adhesives and fasteners that complement the carbon fiber’s properties.
Finishing
The finishing stage involves final touches that enhance the performance and aesthetics of the CNC machine.
- Key Techniques:
- Surface Treatment: Processes like sanding and coating protect against wear and improve appearance.
- Calibration: Precise calibration of CNC systems is crucial for accuracy in machining operations.
Quality Assurance
Quality assurance is vital in the manufacturing of carbon fiber CNC machines to meet international standards and ensure reliability. Understanding the QC process can help buyers verify the quality of their investments.
International Standards
B2B buyers should be aware of relevant international standards that govern manufacturing quality:
- ISO 9001: This standard focuses on quality management systems and is applicable across various industries, ensuring consistent quality and customer satisfaction.
- CE Marking: Indicates conformity with health, safety, and environmental protection standards for products sold within the European Economic Area.
Industry-Specific Standards
Depending on the application, other certifications may be relevant:
- API (American Petroleum Institute): Essential for machines used in oil and gas applications, ensuring they meet specific safety and performance criteria.
QC Checkpoints
The QC process typically involves several checkpoints:
- Incoming Quality Control (IQC): Verification of materials upon receipt to ensure they meet specified standards.
- In-Process Quality Control (IPQC): Continuous monitoring during manufacturing to detect any deviations in real-time.
- Final Quality Control (FQC): Comprehensive inspection of the finished product before shipment, ensuring it meets all quality benchmarks.
Common Testing Methods
To verify the integrity and performance of carbon fiber components, various testing methods can be employed:
- Tensile Testing: Measures the strength of the material under tension.
- Flexural Testing: Assesses the material’s ability to resist bending.
- Thermal Analysis: Evaluates how the material reacts under different temperature conditions.
Verifying Supplier Quality Control
B2B buyers from diverse regions can adopt several strategies to ensure the quality of their suppliers:
- Audits: Conducting regular audits of suppliers can provide insights into their manufacturing processes and adherence to quality standards.
- Reports: Requesting detailed quality reports helps understand the supplier’s QC methodologies and results.
- Third-Party Inspections: Engaging independent inspection services can provide an unbiased assessment of the supplier’s manufacturing quality.
Quality Control Nuances for International Buyers
International buyers should consider several factors when assessing QC:
- Cultural Differences: Understanding regional manufacturing practices can aid in navigating QC expectations.
- Documentation: Ensure that all QC reports, certifications, and compliance documents are available in a language and format that is clear and comprehensible.
- Regulatory Compliance: Familiarize yourself with local regulations that may impact the quality of carbon fiber CNC machines in your market.
By understanding the intricate manufacturing processes and quality assurance protocols associated with carbon fiber CNC machines, B2B buyers can make informed decisions that enhance their operational capabilities and product offerings. Ensuring quality at every stage—from material selection to final inspection—ultimately leads to improved performance, reliability, and customer satisfaction in the competitive landscape of international markets.
Related Video: SMART Quality Control for Manufacturing
Comprehensive Cost and Pricing Analysis for carbon fiber cnc machine Sourcing
Understanding the Cost Structure of Carbon Fiber CNC Machines
When sourcing carbon fiber CNC machines, it is essential to comprehend the various cost components that contribute to the total price. This analysis covers key elements such as materials, labor, manufacturing overhead, tooling, quality control (QC), logistics, and the supplier’s profit margin.
Cost Components
-
Materials: The primary cost driver in carbon fiber CNC machines is the raw materials used, including carbon fiber sheets, resins, and other composite materials. Prices can vary based on the quality and source of the materials.
-
Labor: Skilled labor is crucial for the assembly and operation of CNC machines. Labor costs can fluctuate depending on the region, experience level, and labor market conditions.
-
Manufacturing Overhead: This includes costs associated with utilities, rent, equipment maintenance, and administrative expenses. Efficient manufacturing processes can help minimize these overheads.
-
Tooling: The specific tools required for machining carbon fiber can be expensive. Investing in high-quality tooling can increase efficiency and reduce wear and tear, impacting the overall cost.
-
Quality Control (QC): Ensuring product quality is vital, especially for high-performance applications. QC processes can add to the cost but are necessary to meet industry standards and certifications.
-
Logistics: Shipping and handling costs can vary significantly based on the destination and shipping method. International buyers should consider tariffs, taxes, and potential delays.
-
Margin: Suppliers typically add a profit margin to their costs. This margin can be influenced by competition, demand, and perceived value.
Price Influencers
Several factors can influence the pricing of carbon fiber CNC machines:
-
Volume/MOQ (Minimum Order Quantity): Higher order volumes often result in lower per-unit costs. Buyers should negotiate MOQs to achieve better pricing.
-
Specifications and Customization: Customized machines tailored to specific applications may incur additional costs. Standard models generally offer cost advantages.
-
Materials and Quality Certifications: The choice of materials and the existence of quality certifications (e.g., ISO, ASTM) can significantly affect pricing. Higher quality and certified products may command premium prices.
-
Supplier Factors: The reputation, location, and production capabilities of the supplier can influence pricing. Established suppliers may offer more reliable products but at higher costs.
-
Incoterms: Understanding Incoterms is vital for international transactions. Terms like FOB (Free on Board) or CIF (Cost, Insurance, and Freight) dictate who bears the shipping costs and risks.
Buyer Tips
-
Negotiate Effectively: Always engage in negotiations to secure the best possible price. Highlighting long-term partnerships can be advantageous.
-
Assess Total Cost of Ownership (TCO): Evaluate the TCO, including maintenance, operational costs, and potential downtime. A lower initial price may not always result in overall savings.
-
Consider Local Suppliers: For buyers in Africa, South America, the Middle East, and Europe, sourcing from local suppliers can reduce shipping costs and lead times.
-
Be Aware of Pricing Nuances: Understand the local market dynamics, currency fluctuations, and economic conditions that may affect pricing.
-
Request Detailed Quotations: Always ask for itemized quotes that break down costs. This transparency will help in assessing value and making informed decisions.
In summary, a comprehensive understanding of the cost structure and pricing influences for carbon fiber CNC machines is critical for international B2B buyers. By leveraging this knowledge, buyers can make informed decisions that align with their operational needs and budget constraints. Always remember that pricing can vary widely based on the above factors, and it is advisable to obtain multiple quotes for comparison.
Essential Technical Properties and Trade Terminology for carbon fiber cnc machine
When considering the procurement of carbon fiber CNC machines, understanding the essential technical properties and trade terminology is crucial for making informed purchasing decisions. Here’s a breakdown of the critical specifications and commonly used terms in the industry.
Key Technical Properties
-
Material Grade
Material grade refers to the quality and type of carbon fiber used in the manufacturing process. Common grades include standard modulus and intermediate modulus. Higher grades typically offer superior strength and stiffness, which is vital for high-performance applications such as aerospace and automotive industries. Understanding material grade helps buyers assess the machine’s capability to meet specific project requirements. -
Tolerance
Tolerance defines the allowable variation in dimensions during the machining process. For carbon fiber components, tight tolerances (often within ±0.01 mm) are essential to ensure fit and function in precision applications. In industries like aerospace, where safety is paramount, maintaining strict tolerances can be a significant factor in procurement decisions. -
Cutting Speed
Cutting speed refers to the rate at which the cutting tool moves through the material. For carbon fiber, optimal cutting speeds can vary widely based on the type of fiber and the CNC machine’s capabilities. Buyers should look for machines that can efficiently handle higher cutting speeds without compromising quality, as this can significantly impact production time and costs. -
Feed Rate
The feed rate is the speed at which the material is fed into the cutting tool. A higher feed rate can increase productivity but may also lead to decreased quality if not managed properly. Understanding the ideal feed rates for carbon fiber processing is vital for buyers aiming to balance efficiency and quality. -
Spindle Power
Spindle power indicates the strength and capability of the CNC machine’s spindle motor. A powerful spindle is necessary for machining tough materials like carbon fiber, ensuring that the machine can handle the demands of different applications. Buyers should consider the spindle power to ensure it aligns with their machining needs. -
Dust Collection System
Carbon fiber machining generates fine dust that can be hazardous and harmful to both workers and machinery. A robust dust collection system is essential for maintaining a safe working environment and prolonging the life of the CNC machine. Buyers should prioritize machines equipped with effective dust management solutions.
Common Trade Terminology
-
OEM (Original Equipment Manufacturer)
OEM refers to companies that produce parts and equipment that may be marketed by another manufacturer. In the context of carbon fiber CNC machines, understanding OEM relationships can help buyers identify reliable sources for high-quality components. -
MOQ (Minimum Order Quantity)
MOQ indicates the smallest quantity of a product that a supplier is willing to sell. For international buyers, knowing the MOQ can help in budgeting and inventory planning, especially when sourcing specialized machinery like carbon fiber CNC machines. -
RFQ (Request for Quotation)
An RFQ is a document that solicits pricing and terms from suppliers for specific products or services. When sourcing carbon fiber CNC machines, submitting an RFQ can help buyers compare offers and negotiate better terms, ensuring they secure the best deal. -
Incoterms (International Commercial Terms)
Incoterms are a series of predefined commercial terms used in international transactions. They define the responsibilities of buyers and sellers regarding shipping, insurance, and tariffs. Understanding Incoterms is essential for buyers to manage risks and costs effectively when importing machinery from overseas. -
Lead Time
Lead time refers to the period between placing an order and receiving the product. In the carbon fiber CNC machine market, lead times can vary widely based on supplier capabilities and geographic location. Buyers should factor in lead times to ensure timely project execution. -
Certification
Certification indicates that a product meets specific industry standards and regulations. For carbon fiber CNC machines, certifications such as ISO 9001 can signify quality assurance and reliability, making it a key consideration for buyers.
Understanding these technical properties and trade terms empowers international B2B buyers to make informed decisions when investing in carbon fiber CNC machines, ensuring alignment with their operational needs and compliance with industry standards.
Navigating Market Dynamics, Sourcing Trends, and Sustainability in the carbon fiber cnc machine Sector
Market Overview & Key Trends
The global market for carbon fiber CNC machines is witnessing robust growth, driven by increasing demand across various industries such as aerospace, automotive, and sporting goods. As companies strive to improve efficiency and reduce weight in their products, carbon fiber’s unique properties—strength, lightweight, and corrosion resistance—are becoming more desirable. Notably, the aviation sector, exemplified by manufacturers like Boeing, incorporates extensive use of carbon fiber composites to enhance fuel efficiency, which is a critical factor for international buyers in Europe and the Middle East.
Emerging technologies, including advanced CNC machining techniques and automation, are reshaping sourcing trends. For instance, the adoption of 5-axis CNC machines allows for more complex geometries and precision, appealing to industries that require high-quality components. Additionally, the trend towards digitalization and Industry 4.0 enables real-time monitoring of manufacturing processes, enhancing efficiency and reducing waste, which is particularly beneficial for B2B buyers in Africa and South America looking to streamline their operations.
International buyers should also consider regional dynamics. For instance, Europe has established stringent regulations regarding manufacturing standards and environmental impact, prompting a shift towards eco-friendly materials and processes. Meanwhile, buyers from Africa and South America may find emerging market opportunities as local industries expand their capabilities and seek innovative materials like carbon fiber to improve product offerings.
Sustainability & Ethical Sourcing in B2B
Sustainability is increasingly becoming a focal point in the carbon fiber CNC machine sector, with significant implications for B2B buyers. The production of carbon fiber involves energy-intensive processes, which can contribute to substantial environmental impacts. Therefore, buyers are encouraged to seek suppliers who prioritize sustainable practices, such as utilizing renewable energy sources and implementing waste reduction strategies.
Ethical sourcing is also paramount. Establishing supply chains that prioritize transparency can mitigate risks associated with unethical labor practices and environmental degradation. Buyers should inquire about suppliers’ certifications and adherence to international standards, such as ISO 14001 for environmental management and ISO 26000 for social responsibility.
Moreover, the availability of ‘green’ certifications for materials used in carbon fiber production is gaining traction. Materials that are recyclable or derived from sustainable sources can enhance a company’s reputation and align with consumer expectations for environmental responsibility. As global awareness of sustainability issues continues to rise, integrating these practices into procurement strategies will be crucial for maintaining competitiveness in the international market.
Brief Evolution/History
The evolution of carbon fiber CNC machining can be traced back to the 1960s when carbon fiber was first developed for aerospace applications. Initially, its high cost and complex manufacturing processes limited its use. However, advancements in production techniques and a growing understanding of its properties have led to widespread adoption across various sectors.
In the 1990s, the introduction of Polymer Matrix Composites expanded carbon fiber’s applications, making it accessible for industries such as automotive and sports equipment. Today, carbon fiber CNC machines are essential for manufacturers aiming to produce lightweight, durable components that meet the demands of modern engineering challenges. As technology continues to advance, the future of carbon fiber in manufacturing looks promising, offering new opportunities for innovation and efficiency.
Related Video: How do carbon markets work?
Frequently Asked Questions (FAQs) for B2B Buyers of carbon fiber cnc machine
-
What factors should I consider when vetting suppliers for carbon fiber CNC machines?
When vetting suppliers, prioritize their experience and specialization in carbon fiber machining. Review their certifications and industry standards compliance, such as ISO 9001. Assess their manufacturing capabilities, including technology and equipment used. Request references from previous clients, especially those in your industry or region, to gauge reliability. Additionally, examine their financial stability and after-sales support to ensure they can meet your ongoing needs. -
Can I customize the carbon fiber CNC machine to suit my specific needs?
Most manufacturers offer customization options for carbon fiber CNC machines. Discuss your specific requirements, such as size, capabilities, and any specialized features. Ensure the supplier has experience in customizing machines for your intended applications. Request detailed documentation outlining the customization process, lead times, and associated costs. Always confirm that modifications will not compromise the machine’s performance or warranty. -
What is the typical minimum order quantity (MOQ) and lead time for carbon fiber CNC machines?
The MOQ can vary significantly among suppliers, often ranging from one machine for smaller manufacturers to several units for larger firms. Lead times typically depend on customization requirements and the supplier’s production capacity, ranging from a few weeks to several months. Always clarify these details upfront and consider potential delays in international shipping, especially if sourcing from regions with complex logistics. -
What payment terms should I expect when purchasing a carbon fiber CNC machine?
Payment terms can vary by supplier and region, but common practices include a deposit (usually 30-50%) upon order confirmation, with the balance due before shipping. Some suppliers may offer financing options or payment plans. Ensure that payment methods are secure and consider using escrow services for large transactions to protect both parties. Always review the contract for any penalties related to late payments or cancellations. -
How can I ensure quality assurance and certification of the carbon fiber CNC machine?
Request documentation from suppliers regarding their quality assurance processes and certifications. Look for compliance with international standards such as ISO 9001 for quality management systems. Inquire about the supplier’s testing procedures for the CNC machines, including quality control checks at various production stages. Additionally, request samples of previous work or machine performance metrics to validate their claims. -
What logistics considerations should I keep in mind when importing a carbon fiber CNC machine?
Logistics are critical when importing machinery. Evaluate the supplier’s ability to assist with shipping arrangements and customs clearance. Consider the machine’s dimensions and weight, as this affects shipping costs and methods. Check if the supplier provides packaging that protects the machine during transit. Familiarize yourself with local import regulations and duties to avoid unexpected costs or delays upon arrival. -
How should I handle disputes or issues with a supplier after the purchase?
Establish clear communication channels with your supplier to address any concerns promptly. If a dispute arises, refer to the contract terms, which should outline procedures for conflict resolution. Many suppliers offer warranties or guarantees; understand the terms and conditions associated with these. If necessary, consider mediation or arbitration as alternatives to litigation, which can be costly and time-consuming.
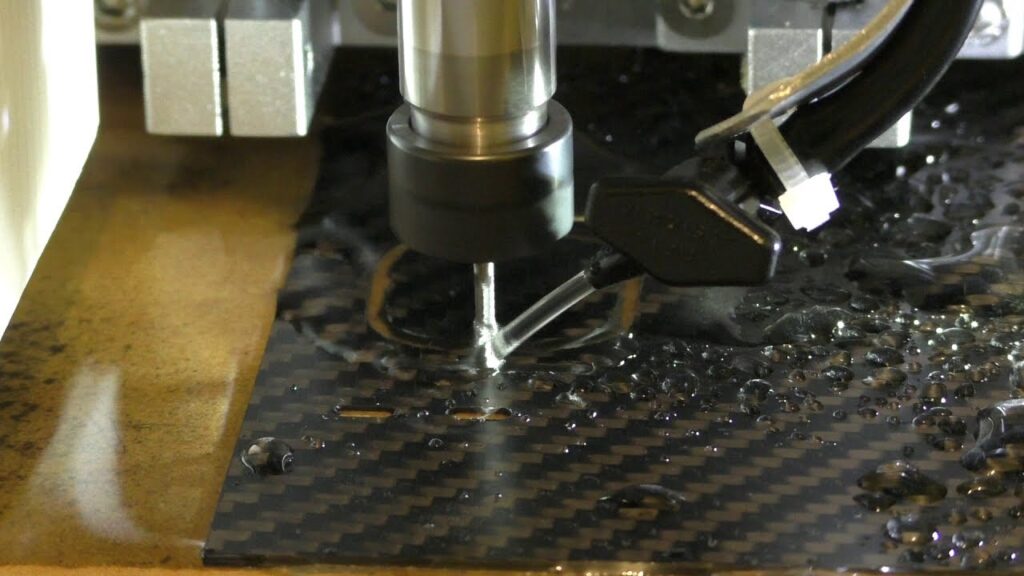
Illustrative Image (Source: Google Search)
- What are the common maintenance requirements for carbon fiber CNC machines?
Regular maintenance is essential for optimal performance and longevity. Schedule routine inspections to check for wear and tear, particularly on cutting tools and components exposed to carbon fiber dust. Lubricate moving parts according to the manufacturer’s guidelines. Keep the machine clean and ensure proper ventilation to minimize dust accumulation. Additionally, consider training for your operators to ensure they follow best practices for maintenance and operation.
Important Disclaimer & Terms of Use
⚠️ Important Disclaimer
The information provided in this guide, including content regarding manufacturers, technical specifications, and market analysis, is for informational and educational purposes only. It does not constitute professional procurement advice, financial advice, or legal advice.
While we have made every effort to ensure the accuracy and timeliness of the information, we are not responsible for any errors, omissions, or outdated information. Market conditions, company details, and technical standards are subject to change.
B2B buyers must conduct their own independent and thorough due diligence before making any purchasing decisions. This includes contacting suppliers directly, verifying certifications, requesting samples, and seeking professional consultation. The risk of relying on any information in this guide is borne solely by the reader.
Strategic Sourcing Conclusion and Outlook for carbon fiber cnc machine
In conclusion, the strategic sourcing of carbon fiber CNC machines represents a pivotal opportunity for international B2B buyers, particularly in Africa, South America, the Middle East, and Europe. As industries increasingly demand lightweight, high-strength materials, the ability to efficiently and effectively source advanced CNC machining solutions will be critical. Key takeaways include understanding the specific requirements for machining carbon fiber, the importance of selecting high-quality tools, and the need for suppliers who can offer both technical support and reliable service.
Investing in carbon fiber CNC technology not only enhances product performance but also positions businesses to compete in rapidly evolving markets. Strategic sourcing allows for cost efficiencies and the ability to innovate, which is vital in sectors ranging from aerospace to automotive and beyond.
Looking forward, B2B buyers should prioritize building partnerships with suppliers who are not only knowledgeable about carbon fiber machining but also committed to sustainability and innovation. As the market continues to evolve, those who embrace these strategies will undoubtedly lead in their respective fields. Engage proactively with suppliers to explore cutting-edge solutions that can transform your manufacturing capabilities.