Master Sourcing CNC Cabinet Machines: Essential Insights
Introduction: Navigating the Global Market for cnc cabinet machine
In an increasingly competitive global marketplace, the CNC cabinet machine has become a pivotal tool for businesses aiming to enhance their production capabilities and meet diverse customer demands. From custom cabinetry in Africa to high-end furniture manufacturing in Europe, these machines offer unparalleled precision, efficiency, and versatility in working with various materials such as wood, composites, and plastics. Their ability to automate complex cutting and shaping processes not only streamlines operations but also significantly reduces waste, making them an essential investment for any forward-thinking enterprise.
This comprehensive guide is crafted specifically for international B2B buyers, providing essential insights into the diverse types of CNC cabinet machines available, including their unique features and applications. Buyers will gain a clear understanding of optimal material selection, manufacturing best practices, and stringent quality control measures necessary for maintaining high standards.
Additionally, the guide delves into supplier evaluation strategies, cost considerations, and prevailing market trends that influence sourcing decisions across different regions, including Africa, South America, the Middle East, and Europe. With dedicated FAQs addressing common challenges faced by buyers, this resource empowers decision-makers to navigate the complexities of sourcing CNC cabinet machines effectively. By leveraging the knowledge contained within this guide, businesses can make informed decisions that align with their strategic goals, ensuring a robust return on investment and a competitive edge in the market.
Understanding cnc cabinet machine Types and Variations
Type Name | Key Distinguishing Features | Primary B2B Applications | Brief Pros & Cons for Buyers |
---|---|---|---|
CNC Router | Utilizes a rotating bit for cutting; supports large workpieces | Cabinet making, furniture, signage | Versatile for various materials; limited detail on small parts |
CNC Laser Cabinet Machine | Employs laser technology for cutting and engraving; high precision | Decorative panels, intricate designs | Clean cuts and minimal waste; higher operational costs |
CNC Vertical Machining Center | Vertical spindle orientation; multi-axis capability | Complex cabinetry, mold making | Excellent for detailed work; requires skilled operators |
CNC Edge Banding Machine | Applies edge banding to plywood or MDF; automated feeding | Furniture assembly, cabinetry finishing | Enhances aesthetics and durability; limited to edge applications |
CNC Panel Saw | Specialized for cutting large panels with precision; saw blade technology | Sheet goods, cabinetry components | High-speed cutting; less versatility for complex shapes |
CNC Router
CNC routers are widely used in cabinetry and furniture manufacturing due to their ability to cut and engrave a variety of materials, including wood, plastics, and composites. They are distinguished by their rotating bits and large work areas, making them suitable for both intricate designs and large-scale production. When considering a CNC router, B2B buyers should evaluate the machine’s spindle power, compatibility with various materials, and the availability of local support and training. This ensures that the investment aligns with production goals while minimizing downtime.
CNC Laser Cabinet Machine
CNC laser cabinet machines utilize laser technology to achieve high precision cutting and engraving on materials like wood, acrylic, and metal. Their ability to create intricate designs with clean edges makes them ideal for decorative panels and custom cabinetry. Buyers should assess the machine’s wattage, cutting speed, and software compatibility, as these factors influence overall efficiency and output quality. While the initial investment may be higher than traditional routers, the reduction in material waste and enhanced design capabilities often justify the cost.
CNC Vertical Machining Center
Vertical machining centers are equipped with a vertical spindle and multi-axis capabilities, allowing for the machining of complex shapes and detailed cabinetry. These machines are particularly suited for high-precision tasks, such as mold making and intricate designs. B2B buyers need to consider factors such as tool change speed, spindle speed, and the machine’s ability to handle various materials. Although they require skilled operators, the investment can lead to significant returns in efficiency and product quality, especially for specialized applications.
CNC Edge Banding Machine
CNC edge banding machines are designed to apply edge banding materials to plywood, MDF, and other substrates, enhancing the aesthetic appeal and durability of cabinetry. These machines automate the feeding and application process, significantly speeding up production times. When sourcing an edge banding machine, buyers should focus on the types of edge materials supported, machine speed, and ease of operation. The primary trade-off is that while these machines improve the final product’s quality, they are limited to edge applications and may require additional equipment for other tasks.
CNC Panel Saw
CNC panel saws are specialized for cutting large panels with precision and speed, making them essential in the cabinetry industry for producing components from sheet goods. They utilize saw blade technology to achieve clean cuts, enhancing productivity in high-volume environments. Buyers should evaluate the saw’s cutting capacity, accuracy, and ease of integration into existing workflows. While panel saws excel in speed and efficiency, they are less versatile for creating complex shapes, so businesses may need to invest in additional machinery for more intricate projects.
Related Video: How To Build Cabinets Using CabinetSense, VCarve Pro And A CNC Machine | Software Tutorial
Key Industrial Applications of cnc cabinet machine
Industry/Sector | Specific Application of CNC Cabinet Machine | Value/Benefit for the Business | Key Sourcing Considerations for this Application |
---|---|---|---|
Furniture Manufacturing | Custom cabinetry production | Enhanced precision and reduced waste in material usage | Machine compatibility with various wood types, local support for maintenance |
Retail Displays | Creation of bespoke retail fixtures and displays | Improved customer engagement through customized designs | Flexibility in design software, lead times for production |
Interior Design | Fabrication of unique, tailored furniture pieces | High-quality finishes and intricate designs | Quality assurance measures, supplier reliability |
Architectural Millwork | Production of architectural details and moldings | Increased project efficiency and reduced labor costs | Sourcing of high-capacity machines, material handling capabilities |
Educational Institutions | Prototyping and teaching tools for design programs | Hands-on learning experiences and skill development | Training support, ease of operation for educational settings |
Furniture Manufacturing
In the furniture manufacturing sector, CNC cabinet machines are pivotal for producing custom cabinetry. They streamline the cutting, shaping, and finishing processes, enabling manufacturers to create intricate designs with high precision. This technology significantly reduces waste, as it optimizes material usage. International buyers should focus on sourcing machines that can handle a variety of wood types and ensure the availability of local technical support for maintenance and training.
Retail Displays
CNC cabinet machines are extensively used to create bespoke retail fixtures and displays, allowing brands to enhance customer engagement through unique designs. These machines enable rapid prototyping and production of customized pieces that align with brand aesthetics. When sourcing, businesses should prioritize flexibility in design software compatibility and consider lead times for production to meet market demands effectively.
Interior Design
In the interior design industry, CNC cabinet machines facilitate the fabrication of tailored furniture pieces that meet specific client needs. The precision offered by CNC technology allows for high-quality finishes and intricate designs that are difficult to achieve manually. Buyers in this sector should emphasize quality assurance measures and supplier reliability to ensure that the final products meet the high standards expected in luxury environments.
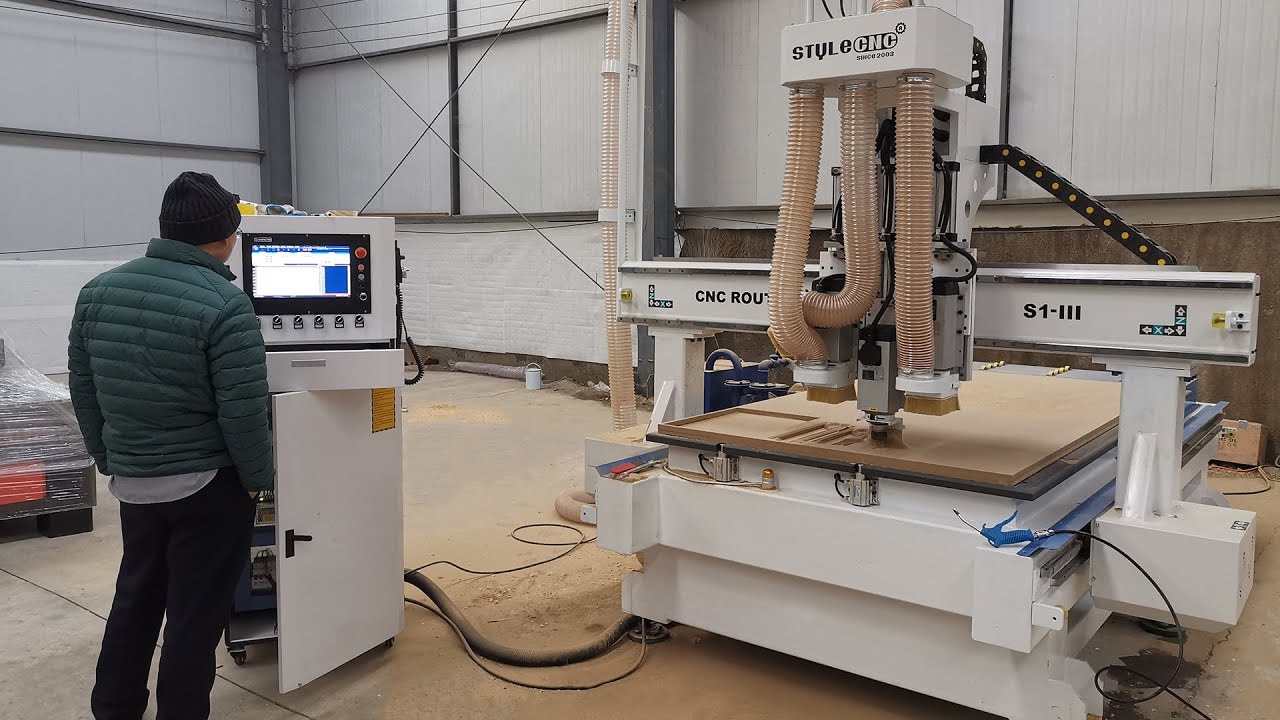
Illustrative Image (Source: Google Search)
Architectural Millwork
CNC cabinet machines play a critical role in producing architectural details and moldings, streamlining the fabrication process and enhancing project efficiency. By automating these tasks, businesses can significantly reduce labor costs and turnaround times. Key considerations for sourcing include the availability of high-capacity machines that can handle larger projects and the ability to manage various materials used in architectural applications.
Educational Institutions
In educational settings, CNC cabinet machines are used for prototyping and teaching tools in design programs. They provide students with hands-on learning experiences, allowing them to develop essential skills in modern manufacturing techniques. When sourcing for educational institutions, it is crucial to ensure that the machines are user-friendly and that suppliers offer adequate training support to facilitate effective learning and operations.
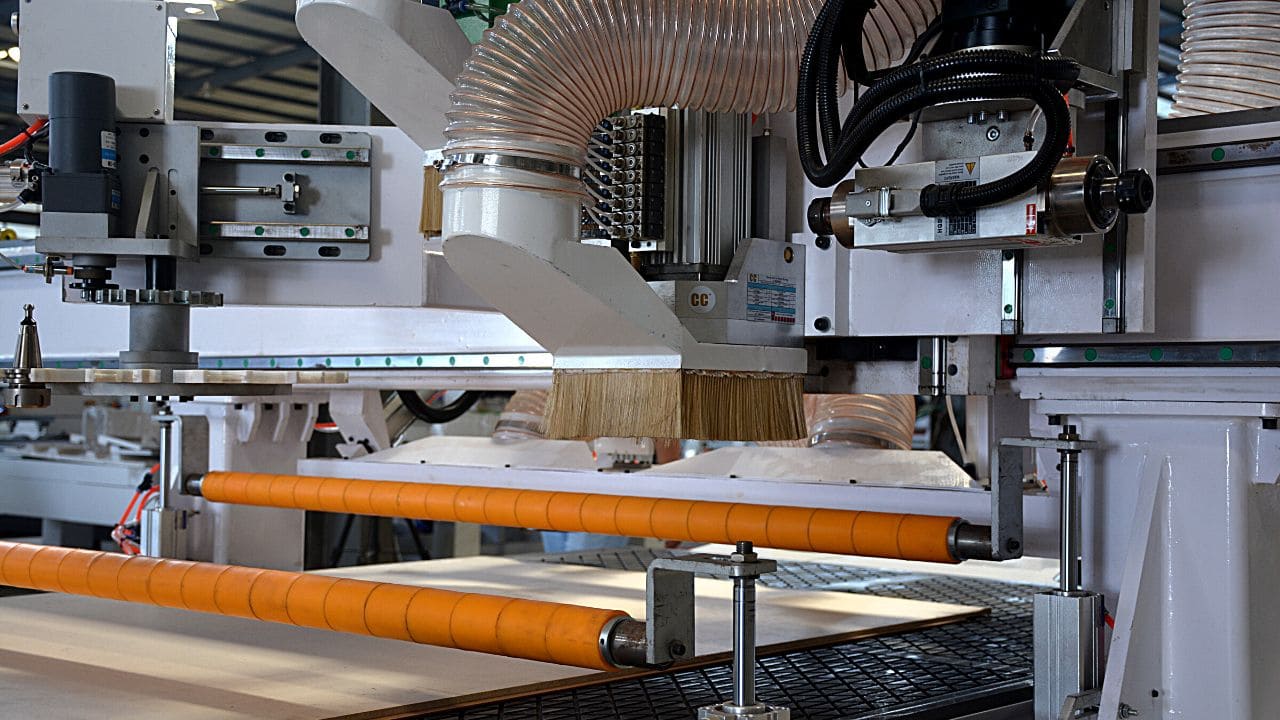
Illustrative Image (Source: Google Search)
Strategic Material Selection Guide for cnc cabinet machine
When selecting materials for CNC cabinet machines, it’s crucial to consider their properties, advantages, disadvantages, and how they align with specific applications. Below is an analysis of four common materials used in the construction and operation of CNC cabinet machines, tailored for international B2B buyers.
Wood
Key Properties: Wood is a versatile material with a natural aesthetic. It typically has a moderate temperature rating and is not prone to corrosion. However, it can be susceptible to moisture and pests.
Pros & Cons: Wood is relatively inexpensive and easy to machine, making it a popular choice for cabinetry. Its lightweight nature allows for easier handling and installation. However, wood can warp or swell in humid conditions, which may compromise structural integrity over time.
Impact on Application: Wood is ideal for applications requiring a warm, natural look, such as residential cabinetry. However, its compatibility with CNC machining is limited to softer woods for intricate designs.
Considerations for Buyers: Buyers in regions like Africa and South America should consider local wood availability and sustainability practices. Compliance with local regulations regarding deforestation and wood treatment is essential. Standards such as ASTM D198 for structural wood should be referenced.
MDF (Medium Density Fiberboard)
Key Properties: MDF is engineered from wood fibers, providing a smooth surface for machining. It has a decent temperature rating but can be affected by moisture if not properly sealed.
Pros & Cons: MDF offers a uniform surface that is easy to paint or veneer, making it suitable for high-quality finishes. It is generally more affordable than solid wood. However, MDF is heavier than solid wood and can emit formaldehyde, which may require compliance with health regulations.
Impact on Application: MDF is widely used in cabinetry and furniture due to its versatility and finish quality. It is particularly compatible with CNC operations, allowing for detailed designs and shapes.
Considerations for Buyers: Buyers from Europe and the Middle East should be aware of compliance with formaldehyde emission standards, such as the European E1 standard. Understanding local sourcing options can also mitigate costs and ensure quality.
Plywood
Key Properties: Plywood is made from layers of wood veneer, providing strength and stability. It has good moisture resistance, particularly when treated, and can withstand moderate temperature variations.
Pros & Cons: Plywood is durable and less prone to warping compared to solid wood. It is also versatile and can be used in various applications. However, the quality can vary significantly based on the grade, and lower-quality plywood may have voids that affect machining.
Impact on Application: Plywood is suitable for cabinetry that requires strength and durability, such as kitchen cabinets. Its layered structure allows for intricate CNC machining while maintaining structural integrity.
Considerations for Buyers: Buyers in regions like the UAE should consider the grade of plywood and its certification, such as BS 5268 for structural use. Local sourcing can also impact cost and availability.
Aluminum
Key Properties: Aluminum is lightweight, corrosion-resistant, and has excellent thermal conductivity. It can withstand high temperatures and is highly durable.
Pros & Cons: Aluminum is ideal for applications requiring strength without added weight. It is easy to machine and can be anodized for additional protection. However, aluminum can be more expensive than wood-based materials and may require specialized tooling for CNC machining.
Impact on Application: Aluminum is suitable for high-end cabinetry and custom applications where durability and aesthetics are paramount. Its compatibility with CNC processes allows for precise cuts and finishes.
Considerations for Buyers: Buyers from Europe and the Middle East should consider compliance with local aluminum standards, such as EN 573 for chemical composition. Understanding the supply chain for aluminum can also help mitigate costs.
Material | Typical Use Case for cnc cabinet machine | Key Advantage | Key Disadvantage/Limitation | Relative Cost (Low/Med/High) |
---|---|---|---|---|
Wood | Residential cabinetry | Natural aesthetic, lightweight | Susceptible to warping and moisture | Low |
MDF | High-quality cabinetry | Smooth surface, easy to finish | Heavier, potential formaldehyde emissions | Medium |
Plywood | Kitchen cabinets | Durable, less prone to warping | Quality can vary significantly | Medium |
Aluminum | High-end cabinetry | Lightweight, corrosion-resistant | Higher cost, requires specialized tooling | High |
This guide provides a comprehensive overview of material selection for CNC cabinet machines, helping international B2B buyers make informed decisions that align with their operational needs and regional standards.
In-depth Look: Manufacturing Processes and Quality Assurance for cnc cabinet machine
Manufacturing Processes for CNC Cabinet Machines
The manufacturing process for CNC cabinet machines is a structured sequence of stages that ensures precision, quality, and efficiency. Understanding these stages is critical for B2B buyers, particularly when evaluating suppliers and ensuring that the machines meet the specific needs of their operations.
1. Material Preparation
The first stage involves selecting and preparing the raw materials, typically wood, MDF (Medium Density Fiberboard), or plywood. Key activities include:
- Material Selection: Buyers must ensure that the chosen materials meet industry standards and are suitable for the intended application. For instance, the density and moisture content of wood can significantly affect machining outcomes.
- Cutting and Sizing: Raw materials are cut into manageable sizes using saws or other cutting equipment. Accurate sizing is crucial to minimize waste and ensure compatibility with CNC machine specifications.
2. Forming
In this stage, the prepared materials undergo shaping and forming processes using CNC technology. Key techniques include:
- CNC Routing: This is the most common technique for shaping cabinet components. CNC routers utilize various bits to carve out intricate designs, grooves, and joints, ensuring high precision and repeatability.
- Edge Banding: For aesthetic and durability purposes, edges of the cut materials are often finished with edge banding. This process can be automated, ensuring uniformity and reducing labor costs.
3. Assembly
Once the components are formed, the next step is assembly. This stage may involve:
- Joining Techniques: Components are joined using various methods such as dowels, screws, or adhesive bonding. CNC machines can also create precise joinery cuts, enhancing the strength and appearance of the final product.
- Quality Checks: Throughout the assembly process, manufacturers conduct intermediate quality checks to ensure that components fit together correctly and meet design specifications.
4. Finishing
The final stage involves surface finishing to enhance the aesthetic appeal and durability of the cabinets. Key activities include:
- Sanding: Automated sanding processes smooth the surfaces of the cabinets, preparing them for finishing.
- Painting or Varnishing: Finishing coats are applied to protect the wood and enhance its visual characteristics. This can be done through spraying or dipping processes, which must be monitored for consistency.
Quality Assurance (QA) in CNC Cabinet Machine Manufacturing
Quality assurance is a critical component of the manufacturing process, ensuring that the CNC cabinet machines meet both international standards and specific customer requirements.
Relevant International Standards
International standards such as ISO 9001 play a vital role in establishing a quality management framework. For specific industries, additional certifications may be necessary, including:
- CE Marking: Indicates compliance with EU safety and environmental requirements, crucial for buyers in Europe.
- API Standards: For machinery intended for specialized applications, adherence to American Petroleum Institute (API) standards may be relevant.
Quality Control Checkpoints
To ensure consistent quality, manufacturers implement several quality control (QC) checkpoints throughout the production process:
- Incoming Quality Control (IQC): Raw materials are inspected upon arrival to verify they meet specified standards. This includes checking for defects and verifying material certifications.
- In-Process Quality Control (IPQC): During manufacturing, operators conduct regular inspections at key stages to identify and rectify issues before they escalate.
- Final Quality Control (FQC): After assembly and finishing, a comprehensive inspection is performed to ensure the final product meets all specifications and quality standards.
Common Testing Methods
Manufacturers utilize various testing methods to verify the quality of CNC cabinet machines, including:
- Dimensional Checks: Using calipers and gauges to ensure that all parts conform to specified dimensions.
- Surface Finish Testing: Evaluating the surface quality using visual inspections and surface roughness testers.
- Functional Testing: Ensuring that all components operate as intended, particularly for moving parts.
Verifying Supplier Quality Control
For B2B buyers, especially those from diverse regions like Africa, South America, the Middle East, and Europe, verifying supplier quality control is essential. Here are practical steps:
- Supplier Audits: Conduct regular audits of suppliers to assess their quality management systems and adherence to international standards. This includes reviewing their processes, documentation, and previous inspection reports.
- Quality Reports: Request detailed quality reports that outline the results of IQC, IPQC, and FQC processes. These reports provide insights into the supplier’s reliability and consistency in quality.
- Third-Party Inspections: Engaging independent third-party inspection services can offer an unbiased evaluation of the manufacturing processes and final products. This is particularly important for buyers unfamiliar with local suppliers or those entering new markets.
QC and Certification Nuances for International Buyers
When sourcing CNC cabinet machines, international buyers must be aware of the following nuances:
- Cultural and Regional Standards: Different regions may have specific standards or regulations that affect the quality and certification of CNC machines. Buyers should familiarize themselves with these standards to ensure compliance.
- Language Barriers: Communication can be a challenge; hence, ensuring that all quality documentation is available in a language understood by the buyer is crucial.
- After-Sales Support: Quality assurance does not end at delivery. Buyers should assess the supplier’s commitment to after-sales support, including warranty policies and availability of spare parts.
By understanding these manufacturing processes and quality assurance practices, B2B buyers can make informed decisions when sourcing CNC cabinet machines, ensuring that they invest in reliable equipment that meets their operational needs and quality expectations.
Related Video: Custom Cabinet Manufacturing Process – European Style Cabinets by Parriott Wood – Made in USA
Comprehensive Cost and Pricing Analysis for cnc cabinet machine Sourcing
Understanding the cost structure and pricing dynamics for sourcing CNC cabinet machines is essential for international B2B buyers. This analysis will break down the key cost components, price influencers, and provide actionable buyer tips to ensure optimal procurement decisions.
Cost Components
-
Materials: The type of materials used in the CNC cabinet machine significantly impacts the overall cost. High-grade steel, aluminum, or specialized alloys can raise the price due to their durability and performance characteristics. Buyers should assess the material quality against their operational needs to avoid overspending.
-
Labor: Labor costs encompass not only the workforce involved in manufacturing but also installation and training. Skilled labor is often required for setup and maintenance, particularly for advanced CNC machines. Understanding local labor markets can help buyers anticipate these costs.
-
Manufacturing Overhead: This includes utilities, rent, and indirect labor costs associated with running the manufacturing facility. Overhead can vary widely based on geographic location and operational efficiency, which can influence the final pricing of the machine.
-
Tooling: The cost of tooling, including cutting tools and fixtures, must be considered as these are essential for the machine’s operation. Tooling costs can be substantial, especially if the machine is designed for specific applications or materials.
-
Quality Control (QC): Ensuring quality through rigorous QC processes can add to the cost. Buyers should inquire about the supplier’s quality certifications (e.g., ISO 9001) and any associated costs for quality assurance to ensure the machine meets industry standards.
-
Logistics: Transportation costs, including shipping, customs duties, and insurance, are crucial for international buyers. These costs can vary significantly based on the supplier’s location and the chosen shipping method.
-
Margin: Supplier profit margins can vary based on market conditions, competition, and the perceived value of the machine. Understanding typical margins in your region can help in negotiating fair prices.
Price Influencers
-
Volume/MOQ: Higher order volumes often lead to discounts due to economies of scale. Establishing a Minimum Order Quantity (MOQ) with suppliers can facilitate better pricing.
-
Specifications/Customization: Custom features or specifications may increase costs. Clearly defining requirements can help avoid unexpected expenses during the procurement process.
-
Materials: As previously mentioned, the choice of materials can significantly affect pricing. Opting for standard materials can reduce costs while still meeting production needs.
-
Quality/Certifications: Machines with higher quality standards and certifications will typically command higher prices. Buyers should balance quality with budget constraints to ensure long-term reliability.
-
Supplier Factors: Reputation, reliability, and service offerings of suppliers can influence pricing. Established suppliers with a track record of quality may charge more but can offer better support.
-
Incoterms: Understanding Incoterms (International Commercial Terms) is essential for managing logistics costs. Terms like FOB (Free On Board) or CIF (Cost, Insurance, and Freight) dictate who bears responsibility for shipping costs and risks.
Buyer Tips
-
Negotiation: Leverage volume and long-term relationship potential when negotiating prices. Suppliers may be willing to offer discounts for repeat orders or bulk purchases.
-
Cost-Efficiency: Focus on the Total Cost of Ownership (TCO) rather than just the upfront price. Consider maintenance, operational efficiency, and potential downtime when evaluating machine costs.
-
International Pricing Nuances: Buyers from Africa, South America, the Middle East, and Europe should be aware of regional market conditions that can affect pricing. Economic stability, currency fluctuations, and local competition can all play a role in final costs.
-
Disclaimer for Indicative Prices: Pricing for CNC cabinet machines can vary widely based on the factors mentioned above. Buyers should conduct thorough market research and obtain multiple quotes to ensure competitive pricing.
By understanding these components and dynamics, B2B buyers can make informed decisions that align with their operational needs and budget constraints, ultimately securing a machine that enhances productivity and profitability.
Spotlight on Potential cnc cabinet machine Manufacturers and Suppliers
This section looks at several manufacturers active in the ‘cnc cabinet machine’ market. This is a representative sample for illustrative purposes; B2B buyers must conduct extensive due diligence before any transaction. Information is synthesized from public sources and general industry knowledge.
Essential Technical Properties and Trade Terminology for cnc cabinet machine
Key Technical Properties of CNC Cabinet Machines
When sourcing CNC cabinet machines, understanding their technical specifications is crucial for making informed purchasing decisions. Here are several critical specifications that B2B buyers should consider:
-
Material Grade
– Definition: Refers to the type and quality of materials the machine can process, such as plywood, MDF, or hardwood.
– Importance: Different materials require specific cutting tools and settings. Choosing a machine compatible with your material grade ensures optimal performance and reduces wear on tools. -
Tolerance
– Definition: The permissible limit of variation in a physical dimension or measured value, usually expressed in millimeters or inches.
– Importance: High tolerance levels are vital for precision work in cabinetry. A machine capable of achieving tight tolerances will produce parts that fit together seamlessly, enhancing overall product quality. -
Spindle Speed
– Definition: The rotational speed of the spindle, typically measured in revolutions per minute (RPM).
– Importance: A higher spindle speed allows for faster cutting and better finishes. B2B buyers should match spindle speed with material type to avoid damage and ensure efficiency. -
Working Area Dimensions
– Definition: The maximum size of the material that the machine can accommodate, usually given in width, depth, and height.
– Importance: Understanding the working area helps buyers select machines that fit their production needs. Larger working areas allow for more extensive and complex projects without the need for multiple setups. -
Control System
– Definition: The software and hardware interface that operators use to command the CNC machine.
– Importance: A user-friendly control system can significantly reduce training time and operational errors. Buyers should prioritize systems that support common file formats and offer robust technical support. -
Power Supply Requirements
– Definition: The electrical specifications required to operate the machine, including voltage and phase.
– Importance: Ensuring compatibility with local power supply systems is essential to avoid operational disruptions. Buyers should verify that their facility can accommodate the machine’s power needs.
Common Trade Terms in CNC Cabinet Manufacturing
Familiarity with industry jargon can streamline communication and negotiations with suppliers. Here are several key terms relevant to CNC cabinet machines:
-
OEM (Original Equipment Manufacturer)
– Definition: A company that produces parts and equipment that may be marketed by another manufacturer.
– Importance: Understanding OEM relationships helps buyers identify the source of machine components and assess quality and reliability. -
MOQ (Minimum Order Quantity)
– Definition: The smallest quantity of a product that a supplier is willing to sell.
– Importance: Knowing the MOQ is crucial for budgeting and inventory management, especially for businesses that may not require large quantities of machinery. -
RFQ (Request for Quotation)
– Definition: A document sent to suppliers requesting pricing and terms for specific products or services.
– Importance: Issuing an RFQ allows buyers to compare offers from multiple suppliers, ensuring competitive pricing and terms. -
Incoterms (International Commercial Terms)
– Definition: A set of predefined commercial terms published by the International Chamber of Commerce (ICC) that clarify the responsibilities of buyers and sellers.
– Importance: Understanding Incoterms is essential for managing shipping logistics, costs, and risks, particularly in international transactions. -
Lead Time
– Definition: The time it takes from placing an order to receiving the product.
– Importance: Knowing the lead time is critical for production planning and ensuring timely delivery, especially for projects with tight deadlines. -
Warranty
– Definition: A promise made by the manufacturer regarding the condition of the machine and the terms of repair or replacement.
– Importance: A solid warranty can protect buyers from unexpected costs and provide peace of mind regarding machine reliability and performance.
By understanding these technical properties and trade terms, international B2B buyers can make more informed decisions when sourcing CNC cabinet machines, ultimately enhancing their operational efficiency and product quality.
Navigating Market Dynamics, Sourcing Trends, and Sustainability in the cnc cabinet machine Sector
Market Overview & Key Trends
The global CNC cabinet machine market is witnessing robust growth, driven by an increasing demand for precision furniture manufacturing and custom cabinetry. As industries in Africa, South America, the Middle East, and Europe expand, the need for efficient and adaptable production methods is paramount. Key trends influencing the market include the rise of automation technologies, integration of IoT for real-time monitoring, and the adoption of advanced materials that enhance durability and aesthetics.
International B2B buyers are increasingly focused on sourcing CNC machines that offer versatility in processing different materials, such as wood, plastics, and composites. Additionally, the trend towards personalized and bespoke furniture solutions is pushing manufacturers to invest in high-capacity CNC machines that can handle complex designs with precision. Buyers should also consider the importance of supplier reliability, as machine downtime can significantly impact production timelines and costs.
Furthermore, geographical factors play a critical role in sourcing strategies. For example, buyers in the Middle East may prioritize suppliers with strong logistics networks to accommodate the region’s vast distances, while European buyers might focus on compliance with stringent EU regulations. Understanding these dynamics is essential for B2B buyers to navigate the complexities of the CNC cabinet machine market effectively.
Sustainability & Ethical Sourcing in B2B
Sustainability is becoming a cornerstone of sourcing strategies in the CNC cabinet machine sector, driven by increasing consumer awareness and regulatory pressures. The environmental impact of manufacturing processes, particularly in terms of waste generation and resource consumption, is prompting buyers to seek machines that minimize their ecological footprint. This includes sourcing from suppliers who utilize sustainable materials and practices, such as reclaimed wood or environmentally friendly adhesives.
Ethical sourcing is equally important, as businesses are increasingly held accountable for their supply chains. Buyers should prioritize suppliers who adhere to ethical labor practices and possess certifications such as FSC (Forest Stewardship Council) or PEFC (Programme for the Endorsement of Forest Certification). These certifications not only demonstrate a commitment to sustainable forestry but also appeal to environmentally conscious consumers.
In addition, the shift towards ‘green’ manufacturing processes is encouraging investments in CNC machines that are energy-efficient and designed to reduce waste. B2B buyers should consider the total lifecycle impact of their machinery, including energy consumption, material waste, and recyclability, to align their sourcing strategies with sustainability goals.
Brief Evolution/History
The evolution of CNC cabinet machines can be traced back to the mid-20th century when numerical control systems were first introduced. Initially, these machines were limited in functionality and primarily used in industrial settings. However, as technology advanced, CNC machines became more sophisticated, incorporating computer technology that allowed for greater precision and versatility in machining processes.
By the late 20th century, the introduction of CAD (Computer-Aided Design) software revolutionized the industry, enabling designers to create complex cabinet designs that could be directly translated into machine instructions. This integration of design and manufacturing processes significantly improved production efficiency and quality. Today, CNC cabinet machines are essential tools in the furniture industry, allowing manufacturers to meet the growing demand for customized solutions while maintaining high standards of craftsmanship. Understanding this evolution provides B2B buyers with valuable context for evaluating current technologies and suppliers in the market.
Related Video: Incoterms for beginners | Global Trade Explained
Frequently Asked Questions (FAQs) for B2B Buyers of cnc cabinet machine
-
What criteria should I consider when vetting suppliers for CNC cabinet machines?
When vetting suppliers, prioritize their experience in manufacturing CNC cabinet machines, including years in business and client testimonials. Assess their production capacity, technology, and adherence to international quality standards (ISO certifications). It’s also crucial to evaluate their after-sales support, including warranty terms and availability of spare parts. Conduct site visits or virtual inspections to verify their operational capabilities and ensure they can meet your specific requirements. -
Can CNC cabinet machines be customized to suit my specific production needs?
Yes, many manufacturers offer customization options for CNC cabinet machines. You can specify dimensions, tooling, software compatibility, and additional features like automated loading systems. When discussing customization, clearly outline your production goals and material types. It’s essential to engage in detailed discussions with potential suppliers to understand their customization capabilities and any associated costs or lead times. -
What are the typical minimum order quantities (MOQs) and lead times for CNC cabinet machines?
MOQs for CNC cabinet machines can vary significantly based on the supplier and the specific machine model. Generally, suppliers may require an MOQ of one machine for standard models, while custom-built machines may have higher MOQs. Lead times can range from a few weeks to several months, depending on the complexity of the machine and the supplier’s production schedule. It’s advisable to discuss these details upfront to align your procurement timeline with production needs. -
What payment terms are commonly offered for international buyers of CNC cabinet machines?
Payment terms can vary, but common practices include a deposit (typically 30-50%) at order confirmation, with the balance due prior to shipping or upon delivery. Some suppliers may offer financing options or letters of credit for larger orders. Always negotiate payment terms that provide you with adequate security and align with your cash flow needs. Be cautious of upfront payments and ensure you have a clear agreement on deliverables. -
How can I ensure quality assurance and certifications for CNC cabinet machines?
To ensure quality, request documentation of the manufacturer’s quality management systems, such as ISO 9001 certifications. Ask for detailed reports of any quality control processes, including material inspections and machine testing. Additionally, consider third-party inspections before shipment to verify that the machine meets specified standards. Establish clear quality benchmarks in your contract to protect your investment and ensure compliance. -
What logistics considerations should I keep in mind when importing CNC cabinet machines?
Logistics are critical in the procurement process. Understand the shipping methods available, including freight options (air vs. sea) and estimated delivery times. Factor in customs duties, taxes, and potential tariffs when calculating total costs. Collaborate with a reliable logistics partner familiar with international shipping regulations to minimize delays and ensure compliance. Clear communication with your supplier regarding shipping documentation is also essential. -
How should I handle disputes that may arise during the procurement process?
Dispute resolution should be outlined in your contract. Common methods include negotiation, mediation, or arbitration, depending on the complexity of the issue. Establish a clear communication channel with your supplier to address concerns promptly. Documentation of all agreements, changes, and communications is crucial in resolving disputes effectively. If necessary, consider legal counsel familiar with international trade laws to guide you through complex situations. -
What ongoing support should I expect after purchasing a CNC cabinet machine?
Post-purchase support can include installation assistance, operator training, and maintenance services. Verify the supplier’s commitment to providing technical support and availability of spare parts. Many suppliers offer service contracts that cover regular maintenance and emergency repairs, which can be beneficial for minimizing downtime. Establish a clear understanding of the support services included in your purchase agreement to ensure seamless operations after acquisition.
Important Disclaimer & Terms of Use
⚠️ Important Disclaimer
The information provided in this guide, including content regarding manufacturers, technical specifications, and market analysis, is for informational and educational purposes only. It does not constitute professional procurement advice, financial advice, or legal advice.
While we have made every effort to ensure the accuracy and timeliness of the information, we are not responsible for any errors, omissions, or outdated information. Market conditions, company details, and technical standards are subject to change.
B2B buyers must conduct their own independent and thorough due diligence before making any purchasing decisions. This includes contacting suppliers directly, verifying certifications, requesting samples, and seeking professional consultation. The risk of relying on any information in this guide is borne solely by the reader.
Strategic Sourcing Conclusion and Outlook for cnc cabinet machine
The strategic sourcing of CNC cabinet machines represents a pivotal opportunity for international B2B buyers aiming to enhance their manufacturing capabilities. By understanding the diverse machine types and their specific applications, businesses can make informed decisions that align with their operational goals. The importance of evaluating supplier reliability, quality control practices, and support services cannot be overstated—these factors are essential for ensuring long-term success and minimizing disruptions.
B2B buyers from Africa, South America, the Middle East, and Europe should prioritize strategic sourcing not just as a procurement function, but as a means to drive competitive advantage. Investing in the right CNC technology can unlock efficiencies, improve product quality, and respond dynamically to market demands.
Looking ahead, the CNC market is poised for continued innovation, driven by advancements in automation and smart manufacturing. As you evaluate your sourcing strategies, consider engaging with suppliers who are aligned with these trends. Take the initiative to explore partnerships that not only meet your immediate needs but also position your business for future growth and success in an increasingly competitive landscape. Your strategic sourcing decisions today will shape the resilience and capability of your operations tomorrow.