Master Sourcing CNC Tool Grinding Machines for Optimal
Introduction: Navigating the Global Market for cnc tool grinding machine
The global market for CNC tool grinding machines has become a pivotal arena for manufacturers aiming to enhance precision and efficiency in their operations. As industries across Africa, South America, the Middle East, and Europe increasingly demand high-quality components, the role of CNC tool grinding machines is more critical than ever. These machines not only facilitate the precise shaping and sharpening of cutting tools but also significantly influence production quality and cost-effectiveness.
This guide provides a comprehensive overview tailored specifically for international B2B buyers. It covers the diverse types of CNC tool grinders available, including cylindrical, surface, and internal grinders, and explores their compatibility with various materials. Additionally, it delves into best manufacturing practices, quality control measures, and key considerations for evaluating suppliers. Understanding the total cost of ownership—including initial investment, operational costs, and maintenance—is essential for making informed purchasing decisions.
By equipping buyers with insights into market dynamics, supplier credibility, and lifecycle costs, this guide empowers businesses to navigate the complexities of sourcing CNC tool grinding machines. Whether you’re operating in emerging markets like Nigeria or established economies like France, the knowledge contained within this guide will help you secure the right investment to drive sustainable growth and competitive advantage in your industry.
Understanding cnc tool grinding machine Types and Variations
Type Name | Key Distinguishing Features | Primary B2B Applications | Brief Pros & Cons for Buyers |
---|---|---|---|
CNC Tool & Cutter Grinder | Designed for sharpening and reshaping cutting tools; multi-axis control | Manufacturing of cutting tools, drill bits, end mills | Extends tool life, precise profiles; niche application, requires advanced software |
CNC Universal Grinder | Versatile machine capable of grinding various tool shapes; multiple attachments | General tool manufacturing, custom tooling | High flexibility, suitable for diverse applications; setup complexity can be high |
CNC Roll Grinder | Specialized for grinding cylindrical and tapered rolls; large workpiece capacity | Steel mills, paper industries, rubber processing | Efficient for large parts, high throughput; limited to specific applications |
CNC Surface Grinder | Focused on producing flat surfaces with high precision; programmable axes | Mold making, precision tooling, automotive parts | Excellent surface finish; limited to flat components, higher maintenance costs |
CNC Internal Grinder | Targets internal surfaces with high precision; compact spindle design | Hydraulic components, bearing races, small parts | Tight tolerances for internal diameters; limited to internal grinding tasks |
CNC Tool & Cutter Grinder
CNC Tool & Cutter Grinders are specialized machines that excel in sharpening and reshaping various cutting tools, such as drills and end mills. These grinders utilize multi-axis control to achieve intricate profiles and maintain precise geometries. For B2B buyers, the primary consideration is the software capabilities, as advanced programming can significantly enhance productivity and accuracy. This type of grinder is particularly beneficial for manufacturers who require consistent tool performance and longevity, making it a strategic investment in competitive sectors.
CNC Universal Grinder
The CNC Universal Grinder is a versatile option that can grind a wide range of tool shapes and sizes. Its ability to accommodate multiple attachments allows for extensive customization, making it suitable for general tool manufacturing and custom tooling applications. Buyers should evaluate the machine’s adaptability and the complexity of setup, which can vary based on the specific tools being produced. This flexibility makes it an attractive choice for businesses aiming to diversify their product offerings without investing in multiple machines.
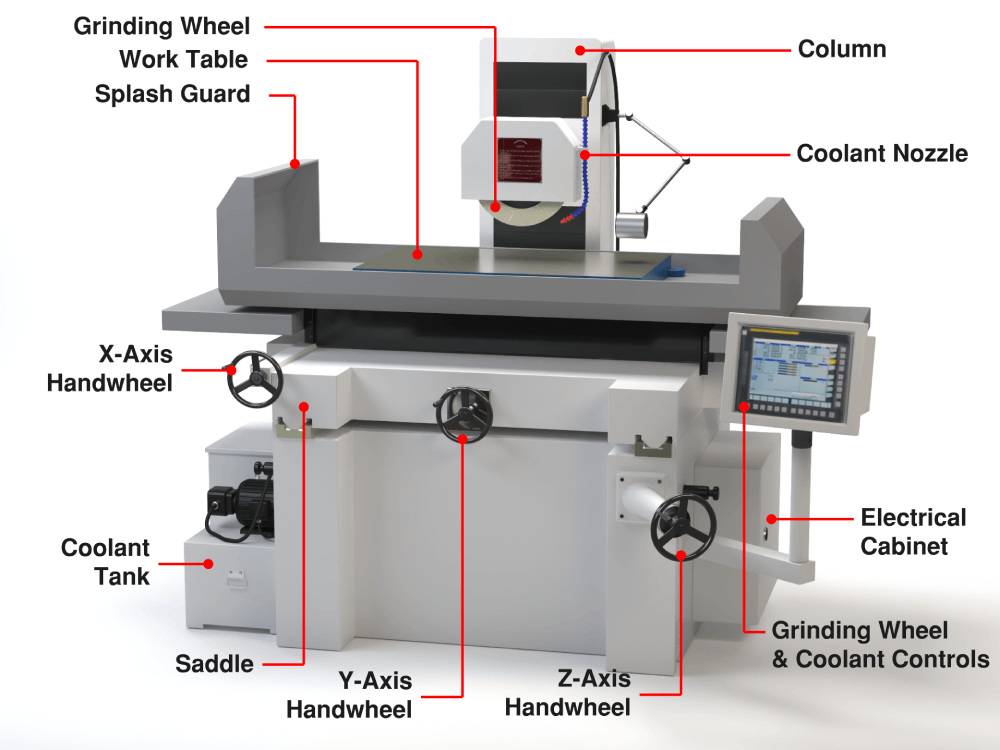
Illustrative Image (Source: Google Search)
CNC Roll Grinder
CNC Roll Grinders are designed specifically for grinding cylindrical and tapered rolls, which are essential in industries such as steel mills, paper production, and rubber processing. These machines can handle large workpieces, offering high throughput and efficiency. B2B buyers should consider the machine’s capacity and the specific requirements of their production processes. While these grinders excel in high-volume environments, their application is somewhat limited to specific industries, necessitating careful evaluation of business needs before purchase.
CNC Surface Grinder
CNC Surface Grinders focus on producing exceptionally flat surfaces with high precision, making them indispensable in applications like mold making and precision tooling. With programmable axes, these machines ensure consistent quality and optimal surface finishes. However, buyers need to be aware of the limitations, as these grinders are restricted to flat components. Additionally, they may incur higher maintenance costs due to wheel wear and the need for frequent calibration, which should be factored into total cost considerations.
CNC Internal Grinder
CNC Internal Grinders specialize in achieving tight tolerances on internal surfaces, making them ideal for producing hydraulic components and bearing races. Their compact spindle design allows for precision in small parts manufacturing. For B2B buyers, the key purchasing considerations include the machine’s spindle range and control software capabilities. Given their specialized nature, these grinders are best suited for businesses focused on high-precision internal grinding tasks, where accuracy is paramount for operational success.
Related Video: S33 CNC Universal cylindrical grinding machine
Key Industrial Applications of cnc tool grinding machine
Industry/Sector | Specific Application of cnc tool grinding machine | Value/Benefit for the Business | Key Sourcing Considerations for this Application |
---|---|---|---|
Automotive | Sharpening cutting tools for engine components | Enhanced tool life and precision in manufacturing | Supplier reliability, local support, and training |
Aerospace | Manufacturing complex cutting tools | High accuracy and compliance with stringent standards | Advanced software capabilities, service agreements |
Medical Devices | Producing surgical tools and instruments | Improved safety and performance in critical applications | Certification compliance, material compatibility |
Energy | Grinding tools for turbine components | Increased efficiency and reduced downtime | Customization options, lead time, and cost of ownership |
Electronics | Fabricating precise cutting tools for circuit boards | Enhanced precision and reduced waste | Supplier’s technological expertise and after-sales service |
Automotive Industry
In the automotive sector, CNC tool grinding machines are essential for sharpening cutting tools used in the production of engine components. This process enhances tool life, ensuring that manufacturers maintain high precision during machining operations. Buyers in this industry should prioritize suppliers that offer reliable maintenance support and training programs, particularly in regions like Africa and South America, where technical expertise may vary. Understanding local service capabilities can significantly impact production efficiency.
Aerospace Industry
CNC tool grinding is pivotal in the aerospace industry for manufacturing complex cutting tools that meet stringent regulatory standards. These machines provide the high accuracy required for components such as turbine blades and landing gear. International B2B buyers must evaluate suppliers based on their advanced software capabilities and willingness to enter into comprehensive service agreements, which are crucial for maintaining operational integrity in high-stakes environments across Europe and the Middle East.
Medical Devices
In the medical devices sector, CNC tool grinding machines are used to produce surgical tools and instruments, where precision is paramount. This application ensures that tools meet safety standards and perform effectively in critical applications. Buyers should focus on sourcing machines that comply with relevant certifications and can handle a variety of materials, especially when operating in diverse markets like Africa and South America, where regulatory requirements may differ.
Energy Sector
The energy sector employs CNC tool grinding machines to grind tools for turbine components, which are critical for maximizing efficiency in energy production. By ensuring tools are finely crafted, businesses can reduce downtime and enhance overall productivity. Buyers should consider customization options and assess the total cost of ownership, including maintenance and operational costs, to ensure a sound investment, particularly in regions with fluctuating energy demands.
Electronics Industry
In electronics, CNC tool grinding is utilized for fabricating precise cutting tools used in circuit board production. This application helps reduce waste and enhances overall manufacturing precision. Buyers should prioritize suppliers with proven technological expertise and robust after-sales service, as these factors can significantly influence production quality and sustainability, especially in competitive markets across Europe and South America.
Related Video: 4 & 5 axis CNC tool grinding machines
Strategic Material Selection Guide for cnc tool grinding machine
When selecting materials for CNC tool grinding machines, international B2B buyers must consider a variety of factors that impact performance, durability, and cost. Below is an analysis of four common materials used in CNC tool grinding applications, focusing on their properties, advantages, disadvantages, and specific considerations for buyers from regions such as Africa, South America, the Middle East, and Europe.
1. High-Speed Steel (HSS)
Key Properties:
High-speed steel is known for its ability to withstand high temperatures without losing hardness, making it ideal for high-performance cutting tools. It also exhibits good wear resistance and toughness.
Pros & Cons:
HSS tools are relatively easy to manufacture and can be sharpened multiple times, extending their lifespan. However, they are less durable than carbide tools and may require more frequent replacements, leading to higher long-term costs.
Impact on Application:
HSS is suitable for machining softer materials and is often used in applications where precision is paramount. However, it may not be the best choice for high-volume production due to its lower wear resistance compared to carbide.
Considerations for International Buyers:
Buyers should ensure compliance with regional standards such as ASTM or DIN. In markets like Argentina and France, the availability of HSS tools and their maintenance support can vary, impacting operational efficiency.
2. Carbide
Key Properties:
Carbide is a composite material known for its exceptional hardness and wear resistance. It maintains its cutting edge at high temperatures and is suitable for machining a wide range of materials.
Pros & Cons:
While carbide tools provide longer tool life and better performance, they are more expensive to produce and can be brittle, making them susceptible to chipping under shock loads.
Impact on Application:
Carbide is ideal for high-speed machining and is commonly used in industries such as aerospace and automotive, where precision and durability are critical.
Considerations for International Buyers:
Buyers must consider the availability of carbide tools and the support for sharpening and maintenance in their region. Compliance with international standards is crucial to ensure product quality and performance.
3. Ceramic
Key Properties:
Ceramic materials offer excellent hardness and thermal resistance, making them suitable for high-speed applications. They are also chemically inert, providing good corrosion resistance.
Pros & Cons:
Ceramics have a long tool life and maintain sharp edges, but they are brittle and can break under heavy loads. The manufacturing process can be complex and costly.
Impact on Application:
Ceramics are typically used for grinding hard materials and can be effective in high-precision applications. However, their brittleness limits their use in more general machining operations.
Considerations for International Buyers:
In regions with stringent quality standards, such as Europe, ensuring compliance with relevant certifications is essential. The availability of ceramic tools and the infrastructure for their maintenance may vary significantly across different markets.
4. Cobalt-Alloyed Steel
Key Properties:
Cobalt-alloyed steel combines the toughness of steel with the wear resistance of cobalt, making it suitable for high-performance applications. It can withstand higher temperatures than standard steel.
Pros & Cons:
This material offers a good balance of cost and performance, making it a versatile choice. However, it is not as hard as carbide, which may limit its application in extremely demanding environments.
Impact on Application:
Cobalt-alloyed steel is often used in environments where a combination of toughness and wear resistance is required, such as in the production of cutting tools for softer materials.
Considerations for International Buyers:
Buyers should assess the local supply chain for cobalt-alloyed tools and ensure that they meet local and international quality standards. The cost-effectiveness of this material can vary based on regional market conditions.
Summary Table
Material | Typical Use Case for cnc tool grinding machine | Key Advantage | Key Disadvantage/Limitation | Relative Cost (Low/Med/High) |
---|---|---|---|---|
High-Speed Steel (HSS) | Precision cutting tools for softer materials | Easy to sharpen and manufacture | Less durable than carbide | Medium |
Carbide | High-speed machining in aerospace and automotive | Exceptional hardness and wear resistance | Brittle and expensive | High |
Ceramic | Grinding hard materials in precision applications | Long tool life and thermal resistance | Brittle and complex manufacturing | High |
Cobalt-Alloyed Steel | Cutting tools for softer materials | Good balance of toughness and wear resistance | Not as hard as carbide | Medium |
This guide provides a comprehensive overview of material selection for CNC tool grinding machines, equipping international B2B buyers with the necessary insights to make informed purchasing decisions.
In-depth Look: Manufacturing Processes and Quality Assurance for cnc tool grinding machine
The manufacturing processes and quality assurance protocols for CNC tool grinding machines are critical components that directly affect the performance and reliability of these machines in various industrial applications. Below is a detailed overview of the typical manufacturing stages, key quality assurance practices, and actionable insights for international B2B buyers.
Manufacturing Processes
The production of CNC tool grinding machines involves several key stages, each crucial for ensuring the final product meets the high standards required in precision engineering.
1. Material Preparation
The manufacturing process begins with selecting high-quality raw materials. Common materials include:
- High-Speed Steel (HSS) and Carbide: Chosen for their durability and ability to maintain sharpness.
- Cast Iron: Often used for machine frames due to its vibration-damping properties.
- Aluminum Alloys: Utilized for specific components to reduce weight without sacrificing strength.
The material undergoes rigorous testing to verify its mechanical properties, ensuring it meets the specifications required for high-precision applications.
2. Forming
The forming stage involves several techniques, including:
- CNC Machining: High-speed machining processes are used to shape the components with precision.
- Laser Cutting: Employed for intricate designs that require tight tolerances.
- Casting: For larger components, casting techniques provide the necessary structural integrity.
Each method is selected based on the specific component requirements and the complexity of the design.
3. Assembly
During assembly, components are meticulously put together. This stage may include:
- Precision Alignment: Ensuring that all moving parts are aligned correctly to minimize wear and improve performance.
- Integration of Control Systems: CNC machines require advanced software and hardware integration, which is tested rigorously during assembly.
Quality control checkpoints are established throughout this stage to ensure that each assembly step adheres to specifications.
4. Finishing
Finishing processes are critical for achieving the desired surface quality and functionality. Techniques include:
- Grinding: Final grinding processes refine the surfaces to achieve the required tolerances and finishes.
- Coating: Protective coatings may be applied to enhance durability and prevent corrosion.
The finishing stage is also where aesthetic considerations are addressed, aligning with branding requirements for B2B buyers.
Quality Assurance
Quality assurance is paramount in the manufacturing of CNC tool grinding machines. Adherence to international standards and rigorous testing methods ensures reliability and performance.
Relevant International Standards
- ISO 9001: This standard outlines requirements for a quality management system (QMS) to ensure consistent quality in manufacturing processes.
- CE Marking: Ensures that products meet EU safety, health, and environmental protection standards, which is particularly relevant for buyers in Europe.
- API Standards: For machines used in the oil and gas sectors, adherence to American Petroleum Institute (API) standards ensures compatibility and safety.
Quality Control Checkpoints
Quality control checkpoints are integrated throughout the manufacturing process:
- Incoming Quality Control (IQC): Raw materials are inspected upon arrival to ensure they meet specifications.
- In-Process Quality Control (IPQC): Ongoing checks during the manufacturing process help identify issues early, reducing waste and rework.
- Final Quality Control (FQC): The final product undergoes comprehensive testing to verify functionality and adherence to specifications before shipping.
Common Testing Methods
Various testing methods are employed to ensure the quality of CNC tool grinding machines:
- Dimensional Inspection: Utilizes precision measuring instruments to verify that components meet specified dimensions.
- Functional Testing: Machines are run through their operational paces to ensure they perform as expected under load.
- Vibration Analysis: Conducted to identify any potential issues with alignment or balance that could affect machine performance.
Verification of Supplier Quality Control
For international B2B buyers, especially from diverse regions such as Africa, South America, the Middle East, and Europe, verifying supplier quality control is essential. Here are actionable steps:
- Supplier Audits: Conducting on-site audits allows buyers to assess the manufacturing processes and quality control measures firsthand.
- Quality Reports: Requesting detailed quality assurance reports can provide insights into the supplier’s adherence to standards and the effectiveness of their QC processes.
- Third-Party Inspections: Engaging third-party inspection services can add an extra layer of verification, ensuring that the products meet the required specifications before delivery.
QC and Certification Nuances for International Buyers
B2B buyers must also be aware of regional nuances in quality certification:
- Regional Standards Compliance: Different markets may have specific regulations that need to be met. For example, buyers in the EU must ensure compliance with CE marking, while those in Africa may encounter varying local standards.
- Cultural Considerations: Understanding the local business practices and quality expectations can aid in building effective supplier relationships.
Conclusion
The manufacturing processes and quality assurance practices for CNC tool grinding machines are intricate and essential for delivering high-quality products. By focusing on material selection, precise manufacturing techniques, and robust quality control measures, buyers can make informed decisions. Implementing thorough verification processes will further ensure that suppliers meet the necessary standards, thereby securing a competitive advantage in the global marketplace.
Related Video: SMART Quality Control for Manufacturing
Comprehensive Cost and Pricing Analysis for cnc tool grinding machine Sourcing
When sourcing CNC tool grinding machines, understanding the comprehensive cost structure and pricing dynamics is crucial for international B2B buyers, especially those operating in Africa, South America, the Middle East, and Europe. The cost components, price influencers, and strategic buyer tips outlined below provide actionable insights for optimizing procurement decisions.
Cost Components
-
Materials: The cost of raw materials is a significant factor in CNC machine pricing. High-quality components, such as hardened steel or advanced ceramics, can increase initial costs but enhance machine durability and performance.
-
Labor: Skilled labor is essential for both manufacturing and maintenance. The availability of qualified technicians can vary significantly by region, impacting the overall labor costs associated with CNC machine production and after-sales support.
-
Manufacturing Overhead: This includes costs related to factory operations, utilities, and administrative expenses. Buyers should consider manufacturers with efficient production processes to ensure competitive pricing.
-
Tooling: Specialized tooling required for different grinding operations can add to the overall cost. Buyers should assess the tooling options available with the machine and whether they can be sourced locally to reduce costs.
-
Quality Control (QC): Investing in robust QC measures ensures that machines meet specified tolerances and performance standards. This can affect the machine’s price but ultimately leads to lower operational costs and enhanced productivity.
-
Logistics: Shipping costs can vary based on the machine’s size and weight, as well as the distance from the manufacturer to the buyer’s location. Understanding Incoterms can help mitigate unexpected logistics expenses.
-
Margin: Suppliers will typically include a profit margin in their pricing. This can fluctuate based on market demand, competition, and the perceived value of the machine.
Price Influencers
-
Volume/MOQ (Minimum Order Quantity): Higher order volumes often lead to lower per-unit costs due to economies of scale. Buyers should negotiate for better pricing based on their purchasing plans.
-
Specifications/Customization: Custom features or specifications can significantly increase costs. Buyers must balance their specific needs with budget constraints, ensuring they do not overpay for unnecessary features.
-
Materials and Quality Certifications: Machines constructed from premium materials and certified for quality (e.g., ISO certifications) will command higher prices. Buyers should verify the certification and performance guarantees offered by suppliers.
-
Supplier Factors: The supplier’s reputation, experience, and service offerings can influence pricing. Established suppliers may charge more but often provide better reliability and support.
-
Incoterms: Understanding the terms of delivery can affect total costs. Options such as FOB (Free on Board) or CIF (Cost, Insurance, Freight) will influence the final price and should be clearly defined in contracts.
Buyer Tips
-
Negotiation: Always negotiate prices, especially when dealing with larger suppliers. Highlighting potential long-term relationships or bulk orders can lead to better terms.
-
Cost-Efficiency: Evaluate the Total Cost of Ownership (TCO), which includes not just the purchase price but also operating costs, maintenance, and potential downtime. A cheaper machine may lead to higher long-term costs if it requires frequent repairs or lacks efficiency.
-
Pricing Nuances for International Buyers: Buyers from Africa, South America, the Middle East, and Europe should be aware of currency fluctuations, import tariffs, and local taxes that can affect the final cost. It’s advisable to consult with a financial expert familiar with international trade.
Disclaimer
Prices for CNC tool grinding machines can vary widely based on specifications, supplier relationships, and market conditions. The insights provided are indicative and should be validated through direct engagement with manufacturers and suppliers to obtain accurate and current pricing information.
Spotlight on Potential cnc tool grinding machine Manufacturers and Suppliers
This section looks at several manufacturers active in the ‘cnc tool grinding machine’ market. This is a representative sample for illustrative purposes; B2B buyers must conduct extensive due diligence before any transaction. Information is synthesized from public sources and general industry knowledge.
Essential Technical Properties and Trade Terminology for cnc tool grinding machine
When sourcing a CNC tool grinding machine, understanding the essential technical properties and relevant trade terminology is crucial for making informed purchasing decisions. This section outlines the critical specifications and industry jargon that will aid international B2B buyers, particularly from Africa, South America, the Middle East, and Europe.
Key Technical Properties
-
Material Grade
– The material grade of the grinding wheel and machine components significantly affects durability and performance. Higher-grade materials can withstand more wear and tear, leading to longer machine life and less frequent replacements. For B2B buyers, investing in machines made from superior materials can reduce downtime and maintenance costs. -
Tolerance
– Tolerance refers to the permissible limit of variation in a physical dimension. For CNC tool grinding machines, tighter tolerances ensure higher precision in tool sharpening. This is vital for industries such as aerospace and automotive, where even minor deviations can lead to performance failures. Buyers should prioritize machines that meet their specific tolerance requirements to ensure product quality. -
Spindle Speed
– The spindle speed, measured in revolutions per minute (RPM), affects the efficiency and quality of the grinding process. Higher spindle speeds allow for faster material removal but can lead to increased heat and wear. Understanding the optimal spindle speed for specific applications is essential for B2B buyers to ensure productivity without compromising tool life.
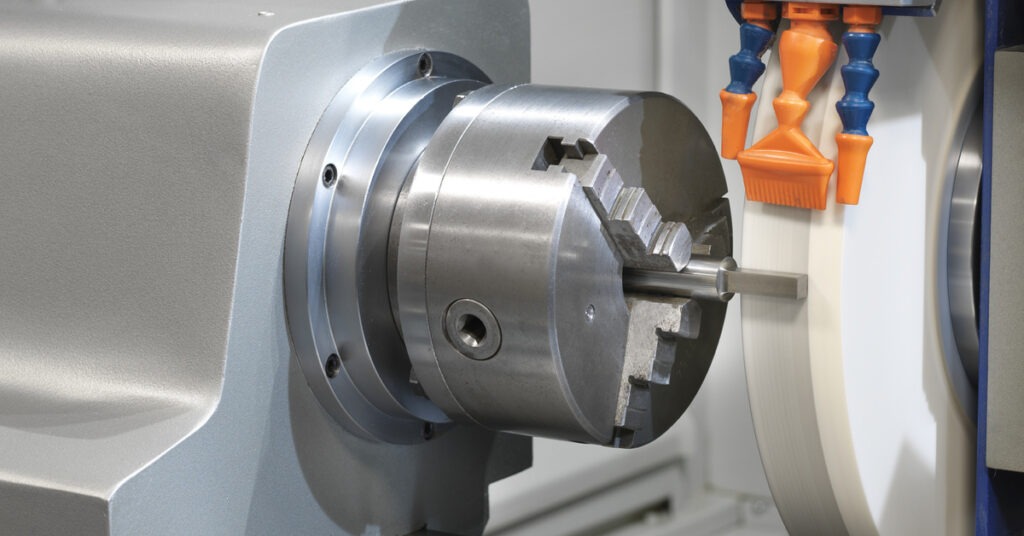
Illustrative Image (Source: Google Search)
-
Power Rating
– The power rating, typically measured in kilowatts (kW), indicates the machine’s capability to handle various workloads. A higher power rating allows for more robust grinding operations, making it suitable for harder materials. Buyers must consider their production needs and select a machine with an appropriate power rating to avoid underperformance or overloading. -
Axis Configuration
– CNC tool grinding machines can have different axis configurations (e.g., 3-axis, 5-axis). More axes provide greater flexibility for complex grinding tasks. For B2B buyers, understanding the axis configuration is critical for ensuring that the machine can meet their specific operational requirements and accommodate a variety of tool shapes.
Common Trade Terminology
-
OEM (Original Equipment Manufacturer)
– An OEM is a company that produces components that are used in another company’s end product. In the context of CNC machines, buyers often engage directly with OEMs for customized solutions or specific machine configurations. Understanding OEM relationships can enhance procurement strategies and ensure quality. -
MOQ (Minimum Order Quantity)
– MOQ refers to the smallest quantity of a product that a supplier is willing to sell. This is a critical consideration for B2B buyers, as it can affect inventory management and cash flow. Knowing the MOQ helps buyers plan their purchases and avoid excess stock or missed opportunities. -
RFQ (Request for Quotation)
– An RFQ is a document that solicits price quotes from suppliers for specific products or services. B2B buyers use RFQs to compare prices and terms from multiple vendors, ensuring they get the best deal. This process is essential for budget management and optimizing procurement costs. -
Incoterms (International Commercial Terms)
– Incoterms are a set of standardized trade terms that define the responsibilities of buyers and sellers in international transactions. They clarify aspects such as shipping costs, risk transfer, and delivery points. Understanding Incoterms is vital for B2B buyers to navigate global trade and mitigate logistical risks. -
Lead Time
– Lead time refers to the time taken from placing an order to receiving the product. In manufacturing, shorter lead times can significantly enhance production efficiency and responsiveness to market demands. Buyers should factor in lead times when planning their operations to maintain smooth workflows.
By familiarizing themselves with these technical properties and trade terms, B2B buyers can make more strategic sourcing decisions, ultimately leading to enhanced operational efficiency and competitive advantage in their respective markets.
Navigating Market Dynamics, Sourcing Trends, and Sustainability in the cnc tool grinding machine Sector
Market Overview & Key Trends
The CNC tool grinding machine sector is experiencing robust growth driven by several global factors. Increasing demand for precision components in industries such as aerospace, automotive, and medical manufacturing is a primary driver. These sectors require high-quality machining capabilities to meet stringent tolerances, pushing manufacturers to invest in advanced CNC grinding technologies. Additionally, the rise of automation and Industry 4.0 initiatives is revolutionizing sourcing strategies, enabling real-time monitoring and predictive maintenance, which enhances operational efficiency.
Emerging markets in Africa and South America are witnessing a surge in manufacturing activities, creating opportunities for B2B buyers to source CNC tool grinding machines tailored to local needs. In Europe and the Middle East, established manufacturers are focusing on upgrading their facilities with cutting-edge technologies to maintain competitiveness. Key trends include the adoption of hybrid machines that combine grinding and additive manufacturing processes, as well as the integration of AI and machine learning for improved machining accuracy and reduced cycle times.
International buyers should also be aware of evolving regional regulations that impact sourcing decisions. Understanding the local compliance requirements, quality standards, and supplier capabilities is crucial for successful procurement. In essence, navigating these market dynamics requires buyers to adopt a strategic approach to sourcing, ensuring alignment with both technological advancements and regional market conditions.
Sustainability & Ethical Sourcing in B2B
Sustainability has become a critical consideration in the CNC tool grinding machine sector. The environmental impact of manufacturing processes is under scrutiny, with an increasing focus on reducing waste, energy consumption, and carbon emissions. For B2B buyers, selecting suppliers who prioritize sustainable practices is essential. This includes assessing the lifecycle of machines, from materials used to energy efficiency during operation.
Ethical sourcing is equally important, as buyers are increasingly expected to ensure that their supply chains adhere to social and environmental standards. This involves evaluating suppliers for their commitment to fair labor practices and responsible material sourcing. Certifications such as ISO 14001 (Environmental Management) and ISO 45001 (Occupational Health and Safety) can serve as indicators of a supplier’s dedication to sustainability.
Moreover, the use of “green” materials and processes—such as eco-friendly coolant systems and recycling initiatives for grinding wheels—can enhance a company’s sustainability profile. By choosing suppliers with robust sustainability credentials, B2B buyers can not only meet regulatory demands but also appeal to environmentally conscious customers and stakeholders.
Brief Evolution/History
The CNC tool grinding machine sector has evolved significantly since its inception in the mid-20th century. Early grinding machines were largely manual, requiring skilled operators to achieve precision. The introduction of CNC technology in the 1970s marked a turning point, enabling automated control and vastly improving accuracy and repeatability.
Over the past few decades, advancements such as multi-axis capabilities, real-time monitoring, and integration with CAD/CAM systems have further refined the grinding process. Today, CNC tool grinding machines are not only pivotal in enhancing productivity but also play a vital role in enabling manufacturers to meet the complex demands of modern production environments. As the industry moves forward, the focus on innovation, sustainability, and ethical sourcing will continue to shape its trajectory.
Related Video: Incoterms for beginners | Global Trade Explained
Frequently Asked Questions (FAQs) for B2B Buyers of cnc tool grinding machine
-
How can I effectively vet suppliers of CNC tool grinding machines?
When vetting suppliers, prioritize their industry experience and reputation. Request references from previous clients, particularly those in your region, to assess reliability and service quality. Verify certifications and compliance with international standards such as ISO 9001. Additionally, consider visiting their facilities or leveraging third-party inspections to evaluate their manufacturing processes and capabilities. This comprehensive approach will help ensure you choose a trustworthy partner that meets your specific needs. -
What customization options should I consider when sourcing CNC tool grinding machines?
Customization can significantly enhance the machine’s performance for specific applications. Discuss options such as software adaptations, spindle configurations, and tooling setups with potential suppliers. Ensure that the machine can accommodate the types of materials you will be grinding and the specific geometries required. It’s also essential to confirm the supplier’s ability to provide ongoing support for any custom features, as this can impact long-term operational efficiency. -
What are the typical minimum order quantities (MOQ) and lead times for CNC tool grinding machines?
MOQs for CNC tool grinding machines can vary widely based on the supplier and machine type. Generally, expect MOQs for specialized machines to be higher, while standard models may have lower thresholds. Lead times often range from a few weeks to several months, depending on the complexity of the machine and current production schedules. Always clarify these details upfront to align your procurement timeline with your operational needs. -
What payment terms are commonly offered for international purchases of CNC grinding machines?
Payment terms can differ significantly by supplier and region. Many suppliers require a deposit (often 30-50%) upon order confirmation, with the balance due before shipment or upon installation. It’s advisable to negotiate terms that suit your cash flow, such as extended payment periods. Additionally, consider using secure payment methods like letters of credit or escrow services to mitigate risks associated with international transactions. -
What quality assurance measures should I look for in CNC tool grinding machines?
Quality assurance is critical in ensuring that the machines meet your operational standards. Ask suppliers about their QA processes, including inspections at various production stages and final testing protocols. Request documentation of quality certifications and compliance with industry standards. It’s also beneficial to inquire about after-sales support and warranty coverage, as these can reflect the supplier’s commitment to quality and customer satisfaction. -
How should I approach logistics for transporting CNC tool grinding machines?
Logistics planning is essential for international shipping of CNC machines. Work with suppliers who have experience in exporting heavy machinery and can provide guidance on packaging, customs clearance, and local regulations. Consider using freight forwarders with expertise in handling industrial equipment to ensure smooth transportation. Additionally, factor in potential delays and costs associated with shipping to avoid disruptions in your production schedule. -
What steps can I take to resolve disputes with suppliers?
To mitigate and resolve disputes effectively, establish clear contractual terms outlining responsibilities, timelines, and quality expectations from the start. Maintain open communication with suppliers to address issues proactively. If disputes arise, attempt to resolve them through negotiation or mediation before escalating to legal avenues. Having a local legal advisor familiar with international trade law can also provide valuable support in navigating complex disputes. -
What certifications should I verify when sourcing CNC tool grinding machines internationally?
Certifications are crucial indicators of a supplier’s adherence to quality and safety standards. Look for ISO certifications, CE marking (for compliance with European standards), and other relevant industry-specific certifications. Additionally, check if the machines comply with local regulations in your country, as this can affect importability and operational legality. Request documentation and verify its authenticity to ensure that the machines meet your operational and regulatory requirements.
Important Disclaimer & Terms of Use
⚠️ Important Disclaimer
The information provided in this guide, including content regarding manufacturers, technical specifications, and market analysis, is for informational and educational purposes only. It does not constitute professional procurement advice, financial advice, or legal advice.
While we have made every effort to ensure the accuracy and timeliness of the information, we are not responsible for any errors, omissions, or outdated information. Market conditions, company details, and technical standards are subject to change.
B2B buyers must conduct their own independent and thorough due diligence before making any purchasing decisions. This includes contacting suppliers directly, verifying certifications, requesting samples, and seeking professional consultation. The risk of relying on any information in this guide is borne solely by the reader.
Strategic Sourcing Conclusion and Outlook for cnc tool grinding machine
The strategic sourcing of CNC tool grinding machines is paramount for international B2B buyers aiming to enhance their manufacturing capabilities and maintain competitive advantage. Key takeaways from this guide emphasize the importance of understanding various machine types—such as cylindrical, surface, centerless, internal, and tool & cutter grinders—each tailored to specific applications and materials. Buyers must consider total cost of ownership, including hidden operational expenses and the necessity for skilled operators and maintenance support, particularly in diverse regions like Africa, South America, the Middle East, and Europe.
Moreover, establishing strong supplier relationships and evaluating their credibility is crucial in ensuring long-term operational efficiency and quality output. As the global market continues to evolve, staying abreast of technological advancements and regional market dynamics will be essential for making informed sourcing decisions.
Looking ahead, international B2B buyers are encouraged to leverage the insights gained from this guide to strategically invest in CNC tool grinding machines that align with their production goals. By prioritizing strategic sourcing, businesses can not only drive growth but also position themselves as leaders in their respective industries. Embrace the opportunity to refine your sourcing strategy today and unlock the full potential of CNC grinding technology.