Master Sourcing Strategies for CNC Pipe Bender Machines
Introduction: Navigating the Global Market for cnc pipe bender machine
In today’s global industrial landscape, the precision and efficiency offered by CNC pipe bending machines have become indispensable for manufacturers across various sectors. As companies in Africa, South America, the Middle East, and Europe strive to enhance their production capabilities, investing in advanced pipe bending technology is critical. These machines not only improve the accuracy of bends but also reduce material waste and streamline manufacturing processes, leading to significant cost savings and increased competitiveness.
This guide serves as a comprehensive resource for international B2B buyers, detailing the diverse types of CNC pipe benders available in the market, including electric, hydraulic, and induction models. We will explore essential material considerations that impact bend quality, alongside best practices for manufacturing and quality control to ensure reliable output. Additionally, the guide provides strategic sourcing advice, helping buyers identify reputable global suppliers while navigating the complexities of cost factors, risk mitigation, and return on investment (ROI).
By leveraging the insights and actionable intelligence provided within these pages, you will be empowered to make informed sourcing decisions that align with your operational needs. Whether you are scaling infrastructure projects in Nigeria, enhancing manufacturing processes in Brazil, or modernizing fabrication plants in Italy, this guide will help you unlock the full potential of CNC pipe bending technology, driving efficiency and innovation in your business.
Understanding cnc pipe bender machine Types and Variations
Type Name | Key Distinguishing Features | Primary B2B Applications | Brief Pros & Cons for Buyers |
---|---|---|---|
CNC Electric Pipe Bender | Precision electromechanical actuation, low energy consumption | Automotive, aerospace, lightweight fabrication | High accuracy, low operating costs; limited for thick materials |
CNC Hydraulic Pipe Bender | Hydraulic-powered, strong force for heavy-walled pipes | Construction, oil & gas, power infrastructure | Powerful and versatile; higher maintenance requirements |
CNC Induction Pipe Bender | Induction heating for minimal distortion | Large-diameter pipelines, structural beams | Maintains material integrity; higher initial investment |
CNC Mandrel Bender | Internal mandrel for tight-radius bends | Shipbuilding, HVAC, furniture manufacturing | Produces precise bends; higher setup costs |
CNC Multi-Stack Bender | Multiple tooling stacks for rapid changes | Plumbing, production lines, process industry | Increases productivity; requires skilled setup |
CNC Electric Pipe Bender
CNC Electric Pipe Benders utilize advanced electromechanical systems to achieve high precision and repeatability. These machines are particularly suitable for industries requiring lightweight fabrication, such as automotive and aerospace sectors. Buyers should consider the energy efficiency and lower operational costs associated with electric benders, but they may find limitations in bending thicker materials, which could necessitate a hybrid solution or additional machinery for specific applications.
CNC Hydraulic Pipe Bender
CNC Hydraulic Pipe Benders are favored for their ability to exert significant force, making them ideal for bending heavy-walled pipes found in construction, oil and gas, and power infrastructure projects. They combine robust power with digital controls for accuracy, allowing for complex geometries. However, buyers need to factor in the higher maintenance demands and the need for trained personnel to operate these machines effectively, especially in regions where skilled labor may be scarce.
CNC Induction Pipe Bender
Induction Pipe Benders are designed to heat pipes at the bend point using electromagnetic induction, allowing for large-radius bends with minimal distortion. This technology is particularly valuable for large-diameter pipelines and structural applications, where maintaining material integrity is critical. While the initial investment can be substantial, the long-term benefits include reduced material waste and enhanced production quality. Buyers should assess the availability of technical support and training from suppliers to maximize their investment.
CNC Mandrel Bender
CNC Mandrel Benders incorporate an internal mandrel to support the pipe during bending, which is essential for producing tight-radius bends without collapsing the pipe. This feature makes them indispensable in shipbuilding, HVAC systems, and high-end furniture manufacturing. While they offer high precision and excellent surface finishes, buyers must consider the higher setup costs and the necessity for skilled operators, which could impact overall project timelines and budgets.
CNC Multi-Stack Bender
CNC Multi-Stack Benders are engineered for high-volume production runs, featuring multiple tooling stacks that allow for rapid changes in size and shape. This flexibility makes them ideal for industries like plumbing and large-scale manufacturing. While they significantly boost productivity, buyers should be aware of the complexity in setup and the need for skilled technicians to operate and maintain these machines effectively. Evaluating the total cost of ownership, including maintenance and training, is crucial for making an informed purchase decision.
Related Video: CNC Pipe Bender CH120CNC – Serpentine Tube – OD 38 4×5 CLR37,5 | AMOB
Key Industrial Applications of cnc pipe bender machine
Industry/Sector | Specific Application of CNC Pipe Bender Machine | Value/Benefit for the Business | Key Sourcing Considerations for this Application |
---|---|---|---|
Construction | Bending pipes for HVAC systems and plumbing installations | Ensures precise fittings and reduces waste, leading to cost savings | Compatibility with various pipe materials and wall thicknesses |
Automotive | Fabrication of exhaust systems and chassis components | Enhances design flexibility and improves vehicle performance | Supplier reputation for quality control and compliance with standards |
Energy | Creating complex piping for oil and gas infrastructure | Increases efficiency and safety in energy transport systems | Long-term support and maintenance services, especially in remote areas |
Shipbuilding | Manufacturing curved pipes for ship hulls and systems | Reduces lead time and enhances structural integrity | Availability of specialized tooling for different pipe sizes |
Furniture Manufacturing | Producing custom metal furniture frames and designs | Allows for unique designs and increased market competitiveness | Consideration of design capabilities and material compatibility |
Construction
In the construction sector, CNC pipe bender machines are essential for bending pipes used in HVAC systems and plumbing installations. These machines ensure precise fittings that minimize material waste, which translates into significant cost savings. For international buyers, particularly in regions like Africa and South America, sourcing machines that can handle various pipe materials and wall thicknesses is crucial. Additionally, the ability to quickly adapt to different project requirements can enhance operational efficiency in fast-paced construction environments.
Automotive
CNC pipe bender machines are widely utilized in the automotive industry for fabricating exhaust systems and chassis components. The precision of these machines allows manufacturers to produce complex geometries that enhance vehicle performance and design flexibility. For B2B buyers, especially in Europe, ensuring that suppliers have a strong reputation for quality control and compliance with automotive standards is vital. This focus on quality helps mitigate risks associated with product failures and recalls.
Energy
In the energy sector, CNC pipe bender machines are critical for creating complex piping systems for oil and gas infrastructure. These machines increase efficiency and safety in transporting energy resources by ensuring the integrity of the piping systems. Buyers in the Middle East and Africa should prioritize sourcing machines that offer robust support and maintenance services, particularly in remote areas where downtime can significantly impact operational costs and project timelines.
Shipbuilding
The shipbuilding industry relies on CNC pipe bender machines for manufacturing curved pipes that are integral to ship hulls and various onboard systems. These machines reduce lead times and enhance the structural integrity of vessels, which is crucial for meeting regulatory standards. For international buyers, especially in regions with burgeoning maritime industries, it is essential to consider the availability of specialized tooling that accommodates different pipe sizes and materials, ensuring versatility in production.
Furniture Manufacturing
In the furniture manufacturing sector, CNC pipe bender machines are employed to produce custom metal frames and designs. This capability allows manufacturers to create unique products that stand out in a competitive market, enhancing their appeal to consumers. Buyers should evaluate suppliers based on their design capabilities and the compatibility of their machines with various materials, as this can significantly influence the quality and aesthetics of the final products.
Related Video: CNC Tube Bender – Fast Spiralling Pipe Bending Machine
Strategic Material Selection Guide for cnc pipe bender machine
When selecting materials for CNC pipe bending machines, it is crucial to understand the properties, advantages, and limitations of each material type. This knowledge helps international B2B buyers make informed decisions that align with their operational needs, regulatory requirements, and market conditions. Below, we analyze four common materials used in CNC pipe bending applications.
Carbon Steel
Key Properties: Carbon steel is known for its high strength and durability, making it suitable for high-pressure applications. It typically has a temperature rating of up to 400°C and offers good weldability.
Pros & Cons: Carbon steel is relatively inexpensive compared to other materials, making it a cost-effective choice for many applications. However, it is prone to corrosion, which can limit its lifespan unless properly coated or treated. The manufacturing complexity is moderate, requiring careful handling during bending to avoid deformation.
Impact on Application: Carbon steel is ideal for structural applications, such as in construction and manufacturing. Its compatibility with various media, including water and gas, makes it a versatile choice for many industries.
Considerations for International Buyers: Buyers in regions like Africa and the Middle East should ensure compliance with local standards (e.g., ASTM A106 for seamless carbon steel pipes). Additionally, the availability of corrosion-resistant coatings can enhance the material’s suitability for humid or corrosive environments.
Stainless Steel
Key Properties: Stainless steel is characterized by its excellent corrosion resistance and high-temperature tolerance, often rated up to 800°C. Its composition includes chromium, which provides a protective oxide layer.
Pros & Cons: The durability and aesthetic appeal of stainless steel make it a preferred choice in industries like food processing and pharmaceuticals. However, it is more expensive than carbon steel, and its higher strength can complicate the bending process, requiring specialized equipment.
Impact on Application: Stainless steel is suitable for applications where hygiene and corrosion resistance are critical, such as in piping for food and beverage industries. Its compatibility with a wide range of media, including aggressive chemicals, enhances its usability.
Considerations for International Buyers: Buyers should be aware of compliance with international standards such as ASTM A312 for stainless steel pipes. In Europe, EN 10216-5 is also relevant. The higher initial investment must be justified by the long-term benefits of reduced maintenance and increased lifespan.
Aluminum
Key Properties: Aluminum is lightweight yet strong, with a temperature rating typically around 200°C. It offers excellent corrosion resistance due to its natural oxide layer.
Pros & Cons: The lightweight nature of aluminum makes it easy to handle and transport, reducing overall operational costs. However, it is less durable than steel and can be more expensive, especially in high-strength alloys. The bending process can also be more complex due to its tendency to deform under stress.
Impact on Application: Aluminum is commonly used in automotive and aerospace applications where weight savings are crucial. Its compatibility with various liquids and gases makes it versatile for different sectors.
Considerations for International Buyers: Buyers should consider the availability of specific aluminum grades that meet their application needs, such as 6061 or 6063. Compliance with standards like ASTM B241 is essential, particularly in Europe, where EN 573-3 applies.
Copper
Key Properties: Copper has excellent thermal and electrical conductivity, along with good corrosion resistance. Its temperature rating can reach up to 300°C, making it suitable for various applications.
Pros & Cons: The primary advantage of copper is its conductivity, making it ideal for plumbing and electrical applications. However, it is relatively expensive and can be prone to corrosion in certain environments, particularly in acidic conditions.
Impact on Application: Copper is widely used in plumbing, HVAC systems, and electrical wiring due to its superior conductivity and resistance to corrosion. It is compatible with a variety of fluids, including water and refrigerants.
Considerations for International Buyers: Buyers should be aware of the need for compliance with standards such as ASTM B88 for copper tubing. In regions like South America, local regulations regarding plumbing materials must also be considered.
Material | Typical Use Case for cnc pipe bender machine | Key Advantage | Key Disadvantage/Limitation | Relative Cost (Low/Med/High) |
---|---|---|---|---|
Carbon Steel | Structural applications in construction | Cost-effective and strong | Prone to corrosion | Low |
Stainless Steel | Food processing and pharmaceuticals | Excellent corrosion resistance | Higher cost and complex bending process | High |
Aluminum | Automotive and aerospace | Lightweight and easy to handle | Less durable and more expensive | Medium |
Copper | Plumbing and HVAC systems | Superior conductivity | Relatively expensive and prone to corrosion | High |
In-depth Look: Manufacturing Processes and Quality Assurance for cnc pipe bender machine
In the competitive landscape of CNC pipe bending machine manufacturing, understanding the intricate manufacturing processes and stringent quality assurance protocols is essential for international B2B buyers. This guide provides insights into the typical stages of production and the quality control measures that ensure high-performance machinery.
Manufacturing Processes for CNC Pipe Bender Machines
The manufacturing of CNC pipe bender machines involves several critical stages, each aimed at producing a reliable and efficient product. Below are the main stages of the manufacturing process:
1. Material Preparation
The initial phase involves selecting and preparing the raw materials. Common materials used for CNC pipe bender machines include:
- Carbon Steel: Known for its strength and durability, suitable for heavy-duty applications.
- Stainless Steel: Offers corrosion resistance, making it ideal for industries like automotive and construction.
- Aluminum Alloys: Lightweight and strong, preferred for applications requiring reduced weight.
Once the materials are selected, they undergo cutting, shearing, or machining to achieve the desired dimensions. This preparation ensures that the components fit together seamlessly during the assembly phase.
2. Forming
The forming stage is where the main components of the CNC pipe bender, such as the frame, bending arms, and tooling, are created. Key techniques used in this phase include:
- Laser Cutting: Provides precision in shaping components, reducing material waste.
- CNC Machining: Ensures high accuracy in creating complex parts with tight tolerances.
- Welding: Critical for joining parts, with techniques like MIG or TIG welding ensuring strong, durable connections.
This stage is crucial as it directly impacts the performance and longevity of the final machine.
3. Assembly
During the assembly phase, all individual components come together to form the complete machine. This process often involves:
- Sub-Assembly: Individual components, such as the control panel and hydraulic systems, are assembled separately before being integrated into the main machine.
- Alignment and Calibration: Ensuring that all parts are aligned correctly is vital for the machine’s precision. Calibration of the CNC controls is also performed to guarantee accurate bending operations.
Effective assembly techniques are vital for ensuring that the machine functions as intended, minimizing the risk of operational issues.
4. Finishing
The final stage of manufacturing involves finishing touches that enhance the machine’s aesthetics and functionality. This includes:
- Surface Treatment: Processes like powder coating or anodizing provide corrosion resistance and improve the machine’s appearance.
- Final Inspection: A thorough inspection is conducted to identify any defects or inconsistencies before the machine is shipped to customers.
This stage ensures that the product meets the required standards and is ready for operational deployment.
Quality Assurance Measures
Quality assurance is a fundamental aspect of CNC pipe bender manufacturing, ensuring that each machine meets both international standards and customer expectations. Key elements of the quality assurance process include:
International Standards
Manufacturers often adhere to several international standards, including:
- ISO 9001: Focuses on quality management systems, ensuring consistent quality in products and services.
- CE Marking: Indicates compliance with European health, safety, and environmental protection standards, essential for buyers in Europe.
- API Standards: Relevant for buyers in the oil and gas sector, ensuring that equipment meets industry-specific performance and safety requirements.
These certifications not only enhance the credibility of the manufacturer but also assure buyers of the machine’s quality.
Quality Control Checkpoints
Quality control is typically divided into several checkpoints throughout the manufacturing process:
- Incoming Quality Control (IQC): Inspects raw materials upon arrival to ensure they meet specifications.
- In-Process Quality Control (IPQC): Ongoing inspections during production help identify and rectify issues immediately, reducing waste and rework.
- Final Quality Control (FQC): A comprehensive inspection of the finished product to ensure it meets all specifications and quality standards.
By implementing these checkpoints, manufacturers can maintain high-quality outputs and reduce the likelihood of defects.
Common Testing Methods
To ensure that machines perform as expected, various testing methods are employed, including:
- Functional Testing: Verifies that all components operate correctly under load conditions.
- Performance Testing: Assesses the machine’s bending capabilities across different materials and thicknesses.
- Durability Testing: Simulates long-term usage to identify potential points of failure.
These tests provide critical insights into the machine’s reliability and operational efficiency.
Verifying Supplier Quality Control
For international B2B buyers, particularly from regions such as Africa, South America, the Middle East, and Europe, verifying a supplier’s quality control processes is essential. Here are several methods to ensure supplier credibility:
Supplier Audits
Conducting audits of potential suppliers can provide valuable insights into their manufacturing processes and quality control measures. Buyers should look for:
- Documentation of Quality Control Processes: Comprehensive records of their quality assurance practices.
- Certifications and Accreditations: Validations from recognized bodies that confirm adherence to international standards.
Quality Reports
Requesting quality reports from suppliers can help buyers gauge the consistency of the manufacturer’s output. These reports should include:
- Defect Rates: Historical data on the percentage of defective units produced.
- Compliance Records: Evidence of adherence to industry standards and regulations.
Third-Party Inspections
Engaging third-party inspection services can provide an unbiased evaluation of a supplier’s manufacturing and quality control processes. This can include:
- Pre-shipment Inspections: Ensuring that products meet specifications before they are shipped.
- Random Sampling: Conducting tests on a sample of products to assess overall quality.
Using these methods, B2B buyers can make informed decisions, ensuring that they select reputable suppliers capable of delivering high-quality CNC pipe bender machines.
Conclusion
Understanding the manufacturing processes and quality assurance measures for CNC pipe bender machines is crucial for international B2B buyers. By familiarizing themselves with these processes, buyers can ensure that they source reliable and efficient machinery that meets their operational needs and complies with industry standards. This knowledge not only aids in making informed procurement decisions but also contributes to the long-term success of their projects across diverse markets.
Comprehensive Cost and Pricing Analysis for cnc pipe bender machine Sourcing
In the competitive landscape of CNC pipe bender sourcing, understanding the cost structure and pricing dynamics is crucial for international B2B buyers, especially those in Africa, South America, the Middle East, and Europe. The costs associated with CNC pipe bending machines can be segmented into several key components, each influencing the overall pricing and procurement strategy.
Cost Components
-
Materials: The choice of materials significantly impacts pricing. High-quality steel, aluminum, and specialty alloys typically command higher prices. Additionally, sourcing from different regions can introduce variations in material costs due to local market conditions and tariffs.
-
Labor: Labor costs encompass not just the manufacturing workforce but also skilled technicians required for machine setup and operation. Regions with higher labor costs, such as parts of Europe, may see elevated machine prices, while countries in Africa or South America might benefit from lower labor costs.
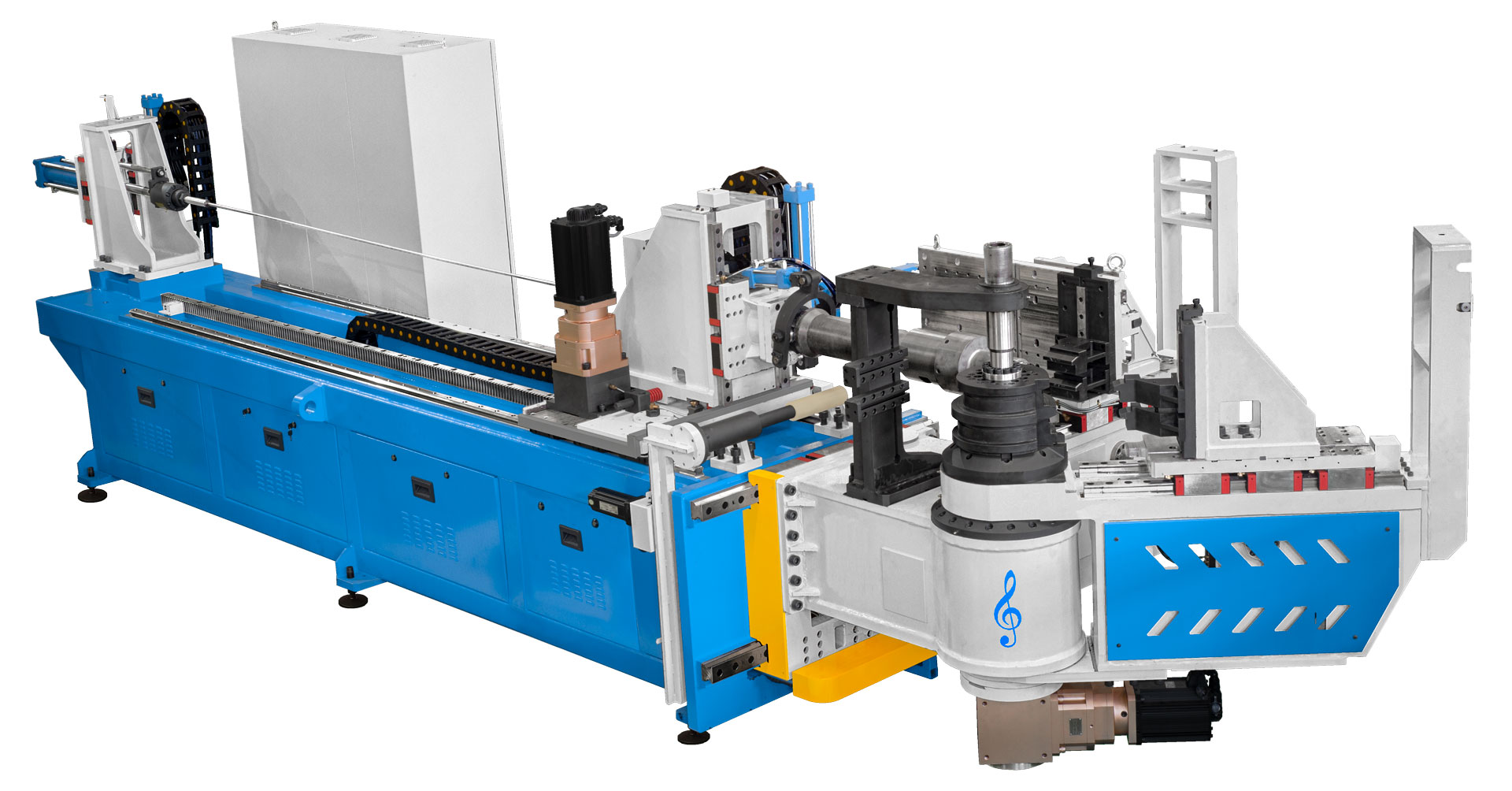
Illustrative Image (Source: Google Search)
-
Manufacturing Overhead: This includes costs related to factory operations, utilities, and administrative expenses. Efficient manufacturing processes can mitigate overhead, but buyers should consider how these factors may influence the final price.
-
Tooling: Custom tooling for specific bending requirements can add significant costs. The complexity of the tooling needed for intricate bends or large diameters will directly affect the machine’s price. Buyers should assess whether standard tooling can meet their needs to avoid additional expenses.
-
Quality Control (QC): Robust QC processes ensure reliability and performance, particularly for high-precision applications. Investment in QC can raise initial costs but is essential for long-term operational efficiency and reducing defect rates.
-
Logistics: Shipping and handling costs vary based on the machine’s size, weight, and destination. Incoterms will also affect who bears these costs, influencing overall pricing and negotiation strategies.
-
Margin: Suppliers typically include a profit margin in their pricing, which can vary significantly based on brand reputation, market demand, and competitive positioning.
Price Influencers
-
Volume/MOQ: Minimum order quantities (MOQs) can heavily influence pricing. Larger orders often lead to discounts, allowing buyers to negotiate better terms based on volume.
-
Specs/Customization: Custom specifications or features can increase costs. Buyers should evaluate whether standard models suffice or if customization is necessary for their applications.
-
Quality/Certifications: Machines with certifications for quality and safety standards, such as ISO or CE, may come at a premium but can provide assurance of performance and compliance.
-
Supplier Factors: The reputation, reliability, and location of suppliers can significantly affect pricing. Established suppliers may charge more but often offer better support and warranty options.
-
Incoterms: Understanding and negotiating Incoterms is crucial for managing logistics costs. Terms like CIF (Cost, Insurance, and Freight) or FOB (Free On Board) can have implications for pricing and risk management.
Buyer Tips
-
Negotiation: Leverage multiple quotes and be prepared to negotiate terms. Highlighting potential volume can encourage suppliers to offer better pricing.
-
Cost-Efficiency: Focus on the Total Cost of Ownership (TCO) rather than just the upfront price. Consider maintenance, operational efficiency, and potential downtime when evaluating costs.
-
Pricing Nuances: International buyers should be aware of currency fluctuations and regional economic conditions that may impact pricing. Building relationships with suppliers can provide insights into market trends that influence costs.
In conclusion, the pricing of CNC pipe bender machines is influenced by a myriad of factors ranging from material choice to supplier relationships. By understanding these components and their implications, international B2B buyers can make informed decisions that align with their operational needs and budget constraints.
Disclaimer: Prices for CNC pipe bending machines are subject to fluctuations based on market conditions, supplier negotiations, and specific project requirements. Always conduct thorough due diligence to obtain accurate quotes tailored to your needs.
Spotlight on Potential cnc pipe bender machine Manufacturers and Suppliers
This section looks at several manufacturers active in the ‘cnc pipe bender machine’ market. This is a representative sample for illustrative purposes; B2B buyers must conduct extensive due diligence before any transaction. Information is synthesized from public sources and general industry knowledge.
Essential Technical Properties and Trade Terminology for cnc pipe bender machine
CNC pipe bending machines are essential tools in various industrial sectors, and understanding their technical properties and trade terminology is crucial for B2B buyers. This knowledge aids in making informed purchasing decisions and ensures that the equipment meets specific operational needs.
Key Technical Properties
-
Material Grade
This refers to the classification of the material used in the pipes, which can include carbon steel, stainless steel, or alloys. Different grades affect the bending process and the final product’s strength and durability. For B2B buyers, selecting the appropriate material grade is vital as it impacts both performance and compliance with industry standards. -
Bend Radius
The bend radius is the minimum radius that a pipe can be bent without causing deformation. It is critical for ensuring that the pipe maintains its integrity and flow characteristics. Buyers need to consider the bend radius specifications to avoid issues in applications requiring precise geometric configurations. -
Tolerance
Tolerance denotes the allowable deviation from a specified dimension. High precision is often required in applications such as automotive and aerospace manufacturing. For B2B buyers, understanding tolerance levels is essential for ensuring that the bent pipes fit seamlessly into larger assemblies and comply with regulatory standards. -
Bending Angle
This specification indicates the degree of bend applied to the pipe. Typical angles include 45°, 90°, and 180°. Buyers must ensure that the CNC machine can achieve the required angles for their specific applications, as this affects both the design and functionality of the finished product. -
Max Wall Thickness
The maximum wall thickness refers to the thickest pipe the machine can bend without compromising its performance. This property is particularly important for sectors such as oil and gas, where thick-walled pipes are common. Buyers should evaluate this specification to ensure that the machine meets their project requirements. -
Cycle Time
Cycle time is the duration it takes for the machine to complete a bending operation. Shorter cycle times can enhance productivity, especially in high-volume production environments. B2B buyers should assess cycle times in relation to their production needs to ensure efficiency and profitability.
Common Trade Terminology
-
OEM (Original Equipment Manufacturer)
This term refers to companies that produce parts and equipment that may be marketed by another manufacturer. Understanding OEM relationships is crucial for buyers seeking quality assurance and compatibility with existing systems. -
MOQ (Minimum Order Quantity)
MOQ is the smallest number of units a supplier is willing to sell. B2B buyers need to be aware of MOQ to manage inventory and cash flow effectively, particularly when sourcing specialized equipment like CNC pipe benders. -
RFQ (Request for Quotation)
An RFQ is a document that solicits price proposals from suppliers. It is a critical step in the procurement process, allowing buyers to compare costs and negotiate terms before making a purchase. -
Incoterms (International Commercial Terms)
Incoterms are a set of predefined commercial terms used in international trade. They define the responsibilities of buyers and sellers regarding shipping, insurance, and tariffs. Familiarity with Incoterms is essential for B2B buyers to avoid misunderstandings and ensure smooth transactions. -
Lead Time
This term refers to the amount of time from the initiation of an order to its completion. Understanding lead times helps buyers plan their production schedules and manage expectations with clients. -
After-Sales Support
After-sales support includes services provided by suppliers after the purchase, such as maintenance, training, and troubleshooting. For B2B buyers, robust after-sales support is crucial for minimizing downtime and ensuring the longevity of their CNC pipe bending machines.
By familiarizing themselves with these technical properties and trade terms, international B2B buyers can make more strategic decisions when investing in CNC pipe bending machines, ultimately enhancing operational efficiency and competitive advantage in their respective markets.
Navigating Market Dynamics, Sourcing Trends, and Sustainability in the cnc pipe bender machine Sector
Market Overview & Key Trends
The CNC pipe bender machine market is currently experiencing significant growth, driven by the increasing demand for high-precision metal forming across various industries such as construction, automotive, and energy. Key global drivers include the rise of automation in manufacturing processes, the need for sustainable practices, and the expansion of infrastructure projects in emerging markets like Africa and South America. As industries aim to enhance efficiency and reduce operational costs, CNC technology offers substantial advantages through automation, allowing for greater production consistency and reduced waste.
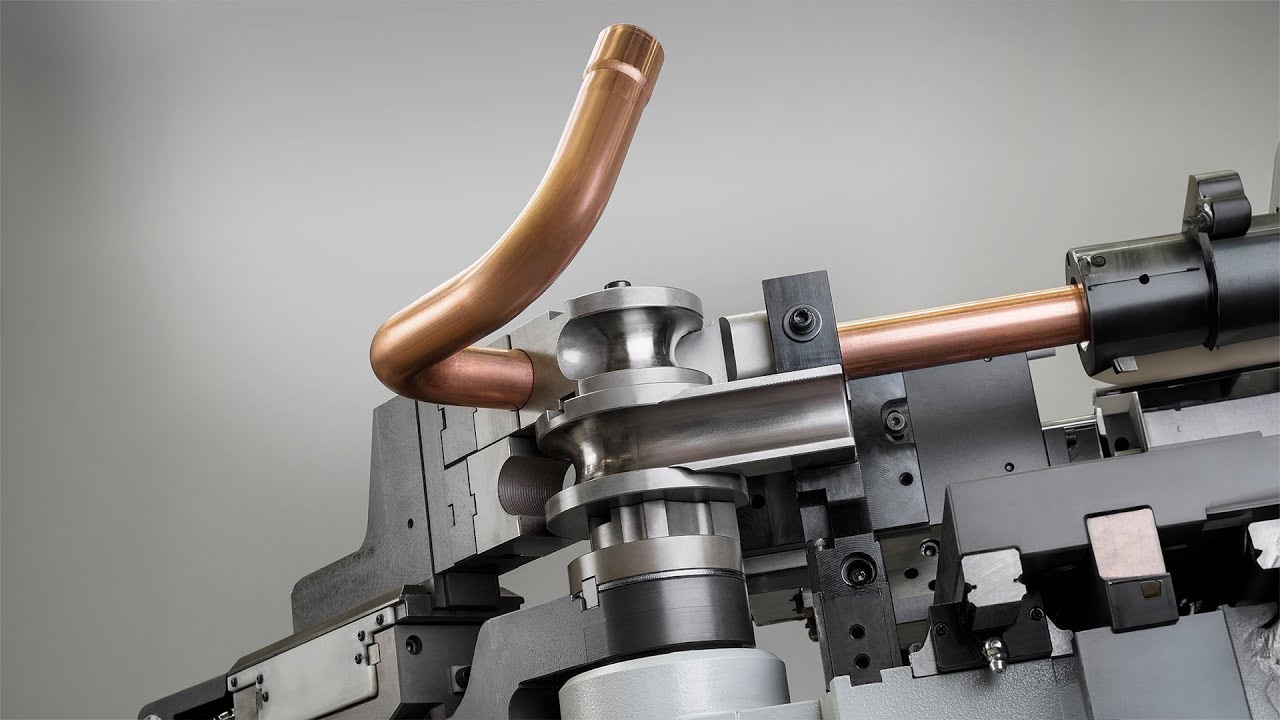
Illustrative Image (Source: Google Search)
Emerging trends indicate a shift towards more advanced CNC machines that incorporate Industry 4.0 technologies, such as IoT connectivity and artificial intelligence. This evolution enables real-time monitoring and predictive maintenance, which can significantly minimize downtime and improve overall productivity. For international B2B buyers, especially those in regions like the Middle East and Europe, leveraging these technological advancements can lead to competitive advantages in terms of quality and speed of production.
Additionally, the market dynamics are influenced by the increasing focus on customization and flexibility in manufacturing processes. Buyers are looking for machines that can handle diverse materials and complex geometries, which is crucial for sectors like aerospace and high-end manufacturing. As a result, understanding the specific capabilities of different CNC pipe bender types—electric, hydraulic, and induction—becomes essential for making informed purchasing decisions.
Sustainability & Ethical Sourcing in B2B
As sustainability becomes a core focus across industries, the CNC pipe bender machine sector is no exception. The environmental impact of manufacturing processes, including energy consumption and waste generation, is under scrutiny. B2B buyers are increasingly prioritizing suppliers who demonstrate commitment to sustainable practices, such as energy-efficient machinery and waste reduction strategies. The adoption of eco-friendly materials and technologies not only helps in minimizing carbon footprints but can also enhance corporate reputation and compliance with international standards.
Moreover, ethical sourcing is gaining traction among international buyers. Establishing supply chains that prioritize fair labor practices and responsible sourcing of materials is critical, especially in regions where regulatory frameworks may be less stringent. Buyers should seek out manufacturers with certifications such as ISO 14001 (Environmental Management) and ISO 45001 (Occupational Health and Safety), as these indicate a commitment to maintaining ethical and sustainable operations.
In terms of materials, opting for recyclable or sustainably sourced inputs can further bolster a company’s sustainability profile. For instance, using stainless steel or aluminum, which are both recyclable, can help reduce environmental impact. By aligning procurement strategies with sustainability goals, businesses can not only meet regulatory requirements but also appeal to increasingly eco-conscious customers.
Brief Evolution/History
The evolution of CNC pipe bending machines has been marked by significant technological advancements that have transformed the manufacturing landscape. Originally, pipe bending was a manual process, relying on simple mechanical tools and skilled labor. The introduction of hydraulic systems in the mid-20th century enabled the bending of larger and thicker pipes, paving the way for more complex applications.
With the advent of computer numerical control (CNC) technology in the late 20th century, the industry saw a revolution in precision and automation. CNC machines allowed for complex geometries and high repeatability, leading to increased efficiency in production. Today, the integration of IoT and AI into CNC pipe bending machines is setting new standards, enabling manufacturers to optimize processes and enhance product quality while minimizing waste. This historical progression underscores the importance of staying updated with technological trends for B2B buyers aiming to enhance their operational capabilities.
Related Video: Incoterms for beginners | Global Trade Explained
Frequently Asked Questions (FAQs) for B2B Buyers of cnc pipe bender machine
-
What should I consider when vetting suppliers of CNC pipe bender machines?
When vetting suppliers, prioritize their experience in the CNC pipe bending industry and check for certifications such as ISO 9001. Review their portfolio for previous projects relevant to your industry. Customer testimonials and case studies can provide insights into their reliability and quality. Additionally, assess their ability to offer post-sale support, including maintenance and technical assistance, as this can significantly impact your operational efficiency. -
Can CNC pipe bender machines be customized for specific projects?
Yes, many manufacturers offer customization options to meet specific project requirements. Customizations can include modifications to the machine’s bending capacity, tooling, or software features to accommodate unique materials or geometries. When discussing customization, ensure that you communicate your exact needs clearly and obtain detailed specifications. Be aware that customized machines may have longer lead times and higher costs, so factor this into your project budget and timeline. -
What are the typical minimum order quantities (MOQs) and lead times for CNC pipe bender machines?
MOQs can vary significantly among suppliers. While some may accept orders for a single machine, others might require bulk orders to justify production costs. Lead times typically range from a few weeks to several months, depending on factors such as machine complexity, customization, and supplier location. Always confirm these details upfront to align with your project schedules, especially in regions with longer shipping times, like Africa or South America. -
What payment terms are generally accepted for international purchases of CNC pipe bender machines?
Payment terms can vary, but common methods include upfront payments, letters of credit, or staggered payments based on production milestones. It’s advisable to negotiate terms that protect your interests, especially when dealing with new suppliers. Consider utilizing escrow services for larger transactions to mitigate risk. Additionally, ensure that the payment terms align with your cash flow and project timelines to avoid financial strain. -
What quality assurance (QA) measures and certifications should I look for?
Look for suppliers that adhere to international quality standards, such as ISO 9001 or CE marking, which indicate compliance with European safety and quality regulations. Ask about their QA processes, including testing protocols and inspections conducted during production. Request documentation of certifications and any relevant compliance records. A robust QA system ensures that the machinery meets your specifications and reduces the risk of defects. -
How can I ensure smooth logistics for the delivery of CNC pipe bender machines?
To ensure smooth logistics, collaborate with your supplier to establish a clear shipping plan that outlines timelines, shipping methods, and responsibilities. Consider engaging a freight forwarder with experience in heavy machinery to navigate customs and regulatory requirements in your country. Additionally, account for potential delays in shipping and customs clearance, particularly in regions with less predictable logistics infrastructure, such as parts of Africa and South America. -
What should I do if I encounter disputes with a supplier?
If a dispute arises, begin by attempting to resolve the issue directly with the supplier through open communication. Document all interactions and agreements for reference. If direct negotiation fails, refer to the contract for dispute resolution clauses, which may include mediation or arbitration. Involving a legal advisor familiar with international trade can provide guidance on the best course of action, especially when dealing with suppliers from different legal jurisdictions. -
How do I assess the total cost of ownership for a CNC pipe bender machine?
The total cost of ownership (TCO) includes not only the initial purchase price but also operational costs, maintenance expenses, and potential downtime. Consider factors such as energy consumption, availability of spare parts, and the frequency of required servicing. Additionally, factor in training costs for operators, as skilled personnel are crucial for maximizing the machine’s capabilities. By calculating TCO, you can make a more informed decision that aligns with your budget and operational goals.
Important Disclaimer & Terms of Use
⚠️ Important Disclaimer
The information provided in this guide, including content regarding manufacturers, technical specifications, and market analysis, is for informational and educational purposes only. It does not constitute professional procurement advice, financial advice, or legal advice.
While we have made every effort to ensure the accuracy and timeliness of the information, we are not responsible for any errors, omissions, or outdated information. Market conditions, company details, and technical standards are subject to change.
B2B buyers must conduct their own independent and thorough due diligence before making any purchasing decisions. This includes contacting suppliers directly, verifying certifications, requesting samples, and seeking professional consultation. The risk of relying on any information in this guide is borne solely by the reader.
Strategic Sourcing Conclusion and Outlook for cnc pipe bender machine
In conclusion, the strategic sourcing of CNC pipe bending machines is a pivotal factor for international B2B buyers looking to enhance operational efficiency and meet the demands of diverse industries. The right machine type—be it electric, hydraulic, induction, mandrel, or multi-stack—can dramatically influence production quality, cost-effectiveness, and project timelines. As buyers navigate the complexities of the global market, understanding the unique features and applications of each machine type is essential for making informed decisions.
Key takeaways include the importance of evaluating supplier reputation, compliance with international standards, and total cost of ownership. Additionally, considering regional factors such as availability of skilled technicians and maintenance support can mitigate risks associated with procurement.
Looking ahead, the evolution of CNC technology promises to introduce even greater efficiencies and capabilities. International buyers, particularly from Africa, South America, the Middle East, and Europe, are encouraged to leverage this knowledge to drive smarter investments in CNC pipe bending systems. By doing so, they can not only enhance their manufacturing capabilities but also position themselves strategically in an increasingly competitive landscape. Now is the time to act—invest wisely, optimize your supply chain, and future-proof your operations.