Master Sourcing Strategies for CNC Stone Cutting Machines
Introduction: Navigating the Global Market for cnc stone cutting machine
In today’s competitive landscape, the CNC stone cutting machine stands as a pivotal asset for businesses engaged in stone fabrication and construction. As global demand for high-quality stone products escalates, investing in advanced CNC technology is not just an option but a necessity. These machines enhance precision, minimize waste, and optimize labor costs, making them indispensable for companies aiming to thrive in the international market.
This comprehensive guide delves into the essential facets of sourcing CNC stone cutting machines, tailored for B2B buyers from Africa, South America, the Middle East, and Europe. It covers a wide array of topics, including the various types of CNC machines available, the materials they can process—such as granite, marble, and sandstone—and critical manufacturing and quality control standards. Additionally, it evaluates the landscape of suppliers, providing insights into their reputations and service offerings, which are crucial for long-term partnerships.
Understanding the pricing structures and financing options available is also a focal point, empowering buyers to make informed financial decisions. The guide addresses common questions and concerns, ensuring that buyers are equipped with the knowledge needed to navigate this complex market confidently. By leveraging this resource, international B2B buyers can streamline their sourcing process, ultimately enhancing operational efficiency and driving business growth in the stone industry.
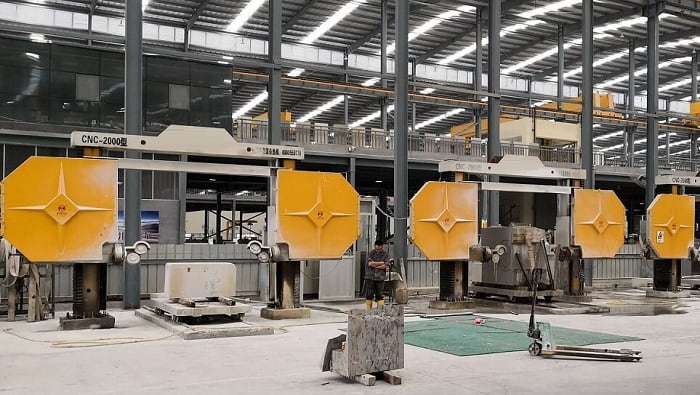
Illustrative Image (Source: Google Search)
Understanding cnc stone cutting machine Types and Variations
Type Name | Key Distinguishing Features | Primary B2B Applications | Brief Pros & Cons for Buyers |
---|---|---|---|
CNC Router | Versatile, can handle various materials, high-speed cutting | Signage, cabinetry, furniture manufacturing | Pros: High speed, flexibility. Cons: May require additional tooling for stone. |
Water Jet Cutter | Uses high-pressure water jets, minimal material waste | Architectural elements, custom designs | Pros: No heat distortion, intricate cuts. Cons: Higher operating costs, slower than routers. |
Bridge Saw | Fixed blade setup, ideal for large stone slabs | Slab cutting, countertops | Pros: Precision cuts, excellent for thick materials. Cons: Limited to straight cuts. |
5-Axis CNC Machine | Multi-directional cutting capabilities | Complex shapes, sculptures | Pros: Exceptional detail, versatile. Cons: Higher investment and maintenance costs. |
Laser Cutter | High precision, uses focused light to cut | Decorative stonework, intricate designs | Pros: Clean edges, minimal waste. Cons: Limited thickness capability, higher energy consumption. |
CNC Router
CNC routers are known for their versatility and speed, making them suitable for a variety of materials beyond stone, such as wood and plastics. They excel in applications like signage and cabinetry, where quick turnaround times are essential. When considering a CNC router, buyers should evaluate their shop’s production needs, as they may require additional tooling specifically designed for stone to achieve optimal results.
Water Jet Cutter
Water jet cutters utilize high-pressure jets of water, sometimes mixed with abrasives, to cut through materials with precision. This technology is particularly advantageous in applications requiring intricate designs or where heat distortion must be avoided. B2B buyers should consider the operational costs and the slower cutting speeds compared to other machines, as these factors can impact overall productivity and project timelines.
Bridge Saw
The bridge saw is a staple in stone fabrication, designed for cutting large slabs with precision. Its fixed blade setup allows for consistent, straight cuts, making it ideal for countertop production and other large-scale applications. Buyers should assess the types of stone they will be working with and the volume of production, as this will influence the overall efficiency and ROI of the investment.
5-Axis CNC Machine
5-axis CNC machines offer advanced capabilities by allowing multi-directional cutting, which is essential for creating complex shapes and detailed sculptures. This type of machine is well-suited for high-end projects that demand exceptional detail. However, potential buyers should be prepared for a higher initial investment and ongoing maintenance costs, which are critical factors in the decision-making process.
Laser Cutter
Laser cutters provide high precision by using focused light to cut through materials, resulting in clean edges and minimal waste. They are particularly effective for decorative stonework and intricate designs, appealing to businesses that focus on aesthetic applications. B2B buyers should be aware of the limitations regarding material thickness and the higher energy consumption associated with laser cutting, as these can affect operational efficiency.
Related Video: FUSION CNC – Large 3D Stone Cutting & Engraving CNC Router Machine ( 4 Axis)
Key Industrial Applications of cnc stone cutting machine
Industry/Sector | Specific Application of CNC Stone Cutting Machine | Value/Benefit for the Business | Key Sourcing Considerations for this Application |
---|---|---|---|
Construction | Precision cutting of stone slabs for facades and flooring | Enhances aesthetic appeal, reduces waste, and improves installation efficiency | Machine size and capabilities, support and training availability |
Monument and Memorial Fabrication | Custom engraving and shaping of memorial stones | Provides personalized products, increases customer satisfaction | Material compatibility, customization options, and service support |
Interior Design and Architecture | Creation of intricate designs and countertops | Elevates design quality, allows for complex shapes and finishes | Software compatibility, precision specifications, and training |
Landscaping | Cutting and shaping stone for outdoor features | Improves project aesthetics and functionality | Durability of the machine, maintenance services, and parts availability |
Art and Sculpture | Crafting artistic stone sculptures and installations | Expands creative possibilities and market offerings | Flexibility of machine settings, precision, and material handling capabilities |
Detailed Applications
Construction
In the construction industry, CNC stone cutting machines are indispensable for precision cutting of stone slabs used in facades, flooring, and other structural elements. These machines solve the problem of inconsistent cuts that can lead to wastage and increased labor costs. International buyers, particularly from regions like Africa and South America, should consider sourcing machines that offer robust support and training, as this will ensure efficient operation and maintenance. The ability to handle various stone types is also crucial to meet diverse project specifications.
Monument and Memorial Fabrication
CNC stone cutting machines are widely used in the fabrication of custom memorial stones, allowing for intricate engraving and precise shaping. This application not only enhances the aesthetic value of memorials but also caters to the growing demand for personalized products, thereby increasing customer satisfaction. Buyers should focus on machines that offer high customization options and compatibility with different stone materials. Reliable service support is essential to ensure operational continuity, especially in markets where technical assistance may be limited.
Interior Design and Architecture
In the realm of interior design and architecture, CNC stone cutting machines facilitate the creation of unique countertops and intricate stone designs. The ability to produce complex shapes and high-quality finishes significantly elevates the overall design quality. Buyers from Europe and the Middle East should prioritize machines that integrate seamlessly with design software, ensuring that their creative visions can be realized without technical hindrances. Precision specifications are critical to maintaining the high standards expected in luxury markets.
Landscaping
For landscaping applications, CNC stone cutting machines are employed to shape and cut stone for outdoor features such as patios, walkways, and decorative elements. The use of these machines enhances project aesthetics while improving functionality and durability of the stone installations. When sourcing, buyers should evaluate the machine’s durability and maintenance services, as well as the availability of replacement parts. This is especially important in regions where harsh weather conditions can affect outdoor installations.
Art and Sculpture
In the art and sculpture sector, CNC stone cutting machines provide artists with the tools to craft detailed stone sculptures and installations. This application expands the creative possibilities and market offerings for artists, allowing them to explore new designs and techniques. Buyers should look for machines that offer flexibility in settings and precision, as these factors are crucial in achieving the desired artistic outcomes. Additionally, understanding the machine’s material handling capabilities can help artists work with various stone types effectively.
Related Video: Hualong Stone Machinery HSNC-500 CNC Granite Marble Cutting Machine
Strategic Material Selection Guide for cnc stone cutting machine
When selecting materials for CNC stone cutting machines, international B2B buyers must consider several factors that influence performance, cost, and suitability for specific applications. Below is an analysis of four common materials used in CNC stone cutting machines, focusing on their properties, advantages and disadvantages, application impacts, and considerations for buyers from diverse regions.
1. Steel
Key Properties:
Steel is known for its high tensile strength and durability. It can withstand high temperatures and pressures, making it suitable for heavy-duty applications. Corrosion resistance can be enhanced through various treatments.
Pros & Cons:
Steel offers excellent durability and strength, ensuring longevity in demanding environments. However, it can be heavy, which may complicate machine mobility. The cost of high-quality steel can be significant, impacting overall machine pricing.
Impact on Application:
Steel is compatible with a variety of stone materials, including granite and marble. Its robustness allows for precise cutting and shaping, essential for high-quality finishes.
Considerations for Buyers:
Buyers from regions like Europe and the Middle East should ensure compliance with standards such as ASTM and DIN. Additionally, understanding local sourcing options can help mitigate costs.
2. Aluminum
Key Properties:
Aluminum is lightweight yet strong, with good corrosion resistance. It has a lower melting point compared to steel, which can be advantageous in certain applications.
Pros & Cons:
The primary advantage of aluminum is its weight, which facilitates easier handling and installation. However, it may not be as durable as steel under heavy loads, and its cost can be moderate to high depending on the alloy.
Impact on Application:
Aluminum is often used in parts of the machine that require precision and less weight, such as frames and supports. Its compatibility with softer stones makes it a preferred choice for intricate designs.
Considerations for Buyers:
International buyers should consider the availability of specific aluminum grades that meet their operational needs. Compliance with local standards is also crucial to ensure quality and safety.
3. Composite Materials
Key Properties:
Composite materials, often made from a combination of resins and fibers, offer unique properties such as lightweight construction and resistance to corrosion and wear.
Pros & Cons:
Composites provide excellent durability and can be tailored for specific applications. However, they may have higher manufacturing complexity and costs, which can deter some buyers.
Impact on Application:
These materials are particularly effective in reducing vibration during cutting, leading to enhanced precision. They are suitable for cutting softer stones and intricate designs.
Considerations for Buyers:
Buyers in emerging markets like Africa and South America should assess the availability of composite materials and their suppliers. Understanding the manufacturing capabilities in their region can also influence the decision.
4. Carbide
Key Properties:
Carbide is a hard material known for its wear resistance and ability to maintain sharp edges at high temperatures. It is often used for cutting tools in CNC machines.
Pros & Cons:
The key advantage of carbide is its longevity and performance in cutting applications, reducing the frequency of tool changes. However, it can be brittle and more expensive than other materials.
Impact on Application:
Carbide tools are ideal for cutting hard stones like granite and quartz. Their precision ensures clean cuts and reduces the risk of chipping.
Considerations for Buyers:
Buyers should evaluate the lifecycle costs of carbide tools, including replacement frequency. Compliance with international standards for cutting tools is essential for ensuring quality.
Summary Table
Material | Typical Use Case for cnc stone cutting machine | Key Advantage | Key Disadvantage/Limitation | Relative Cost (Low/Med/High) |
---|---|---|---|---|
Steel | Structural components and frames | High durability and strength | Heavy, complicates mobility | High |
Aluminum | Lightweight frames and supports | Lightweight, easy to handle | Less durable under heavy loads | Medium |
Composite | Vibration-dampening components | Tailored properties, corrosion-resistant | Higher manufacturing complexity | High |
Carbide | Cutting tools for hard stones | Excellent wear resistance | Brittle, higher initial cost | High |
This guide serves as a strategic resource for international B2B buyers, providing insights into material selection that can influence the performance and cost-effectiveness of CNC stone cutting machines. Understanding these factors will enable buyers to make informed decisions that align with their operational needs and market standards.
In-depth Look: Manufacturing Processes and Quality Assurance for cnc stone cutting machine
Manufacturing a CNC stone cutting machine involves several critical stages, each designed to ensure the final product meets the high standards required for precision and durability. For international B2B buyers, especially from regions like Africa, South America, the Middle East, and Europe, understanding these processes is essential not only for making informed purchasing decisions but also for ensuring that the machines will perform reliably in various operational contexts.
Manufacturing Processes
1. Material Preparation
The first step in the manufacturing process is the careful selection and preparation of raw materials. This typically involves:
- Material Selection: High-quality metals, such as steel and aluminum, are chosen for their durability and strength. Some manufacturers may also use composite materials for specific components.
- Cutting and Shaping: Raw materials are cut and shaped using various methods, including laser cutting, water jet cutting, or traditional machining. This ensures that the components fit together precisely during assembly.
2. Forming
Once the materials are prepared, the next stage is forming the individual components of the CNC machine. Key techniques include:
- CNC Machining: This is a critical stage where computer numerical control (CNC) technology is utilized to create precise dimensions and tolerances. Components like the frame, table, and motor mounts are machined to exact specifications.
- Welding and Joining: High-strength welding techniques are employed to assemble larger components, ensuring structural integrity and stability. This is particularly important for the machine’s base, which must withstand significant operational forces.
3. Assembly
The assembly stage involves bringing together all the machined and formed components. This includes:
- Component Integration: Motors, control systems, and the cutting head are integrated into the machine. Proper alignment is crucial to ensure accurate cutting and operational efficiency.
- Electrical Wiring: During assembly, the electrical systems are installed and tested. This includes wiring for power supply, control panels, and safety features.
4. Finishing
Finishing processes enhance both the aesthetic and functional qualities of the CNC stone cutting machine. These processes may involve:
- Surface Treatment: Components may undergo surface treatments such as painting, anodizing, or powder coating to improve corrosion resistance and appearance.
- Final Assembly: The last step involves a comprehensive assembly of all components, ensuring that all mechanical and electrical systems are operational and that safety standards are met.
Quality Assurance
Quality assurance (QA) is a vital aspect of the manufacturing process, ensuring that the CNC machines meet both international standards and industry-specific requirements. Here are the key components of QA for CNC stone cutting machines:
International Standards
- ISO 9001: This internationally recognized standard outlines criteria for a quality management system (QMS). Compliance indicates that a manufacturer is committed to quality control and continuous improvement.
- CE Marking: For machines sold in Europe, CE marking is essential. It shows that the product meets EU safety, health, and environmental protection standards.
Industry-Specific Standards
- API Standards: For machines used in specific applications, such as oil and gas, adherence to API standards may be required. This ensures that machines can operate safely in demanding environments.
Quality Control Checkpoints
Quality control is implemented at various checkpoints throughout the manufacturing process:
- Incoming Quality Control (IQC): This initial checkpoint verifies that raw materials meet specified standards before they are used in production.
- In-Process Quality Control (IPQC): During assembly, periodic checks are conducted to ensure that components are being manufactured according to specifications.
- Final Quality Control (FQC): Once assembly is complete, the entire machine undergoes testing to verify functionality and safety before it leaves the factory.
Common Testing Methods
Several testing methods are employed to ensure the reliability of CNC stone cutting machines:
- Functional Testing: Machines are run through their operational cycles to ensure they perform as expected.
- Calibration Checks: Precision instruments are used to calibrate the machine, ensuring that it can make accurate cuts.
- Safety Tests: Safety features, such as emergency stops and protective shields, are tested to ensure compliance with safety standards.
Verifying Supplier Quality Control
For international B2B buyers, verifying the quality control processes of potential suppliers is crucial. Here are several actionable strategies:
- Conduct Supplier Audits: Regular audits can provide insights into the manufacturer’s quality control systems, adherence to standards, and overall production capabilities.
- Request Quality Reports: Ask suppliers for documentation of their quality control processes, including any certifications and testing results. This can provide reassurance about the reliability of the machines.
- Engage Third-Party Inspectors: Utilizing third-party inspection services can provide an unbiased assessment of the manufacturing processes and quality assurance measures in place.
Quality Control and Certification Nuances for International Buyers
International buyers should be aware of the following nuances when it comes to quality control and certification:
- Regional Compliance: Different regions may have varying requirements for machine certification. For instance, machines imported into the EU must have CE marking, while other regions may have their own certifications.
- Understanding Local Standards: Buyers should familiarize themselves with local standards that may impact the operation and maintenance of CNC machines in their respective markets.
- Support and Service: Consider the availability of after-sales support and service, as this can significantly affect long-term operational success and adherence to quality standards.
In summary, understanding the manufacturing processes and quality assurance measures associated with CNC stone cutting machines is essential for B2B buyers. By focusing on quality standards, supplier verification, and compliance with regional regulations, buyers can make informed decisions that lead to successful procurement and operational efficiency.
Related Video: Amazing factories | Manufacturing method and top 4 processes | Mass production process
Comprehensive Cost and Pricing Analysis for cnc stone cutting machine Sourcing
When considering the sourcing of CNC stone cutting machines, understanding the comprehensive cost structure and pricing dynamics is essential for international B2B buyers. This analysis will delve into the key cost components, price influencers, and provide actionable insights tailored for buyers from Africa, South America, the Middle East, and Europe.
Cost Components
-
Materials: The primary materials used in CNC stone cutting machines include high-grade steel, aluminum, and specialized components like motors and controllers. The quality and sourcing of these materials significantly impact the overall cost. Buyers should evaluate suppliers based on their material certifications and sourcing practices to ensure durability and performance.
-
Labor: Labor costs encompass both direct labor for assembly and indirect labor for design and engineering. Regions with lower labor costs may offer more competitive pricing, but it is crucial to assess the skill level of the workforce to ensure quality standards are met.
-
Manufacturing Overhead: This includes utilities, facility costs, and administrative expenses associated with production. Manufacturers in regions with higher operational costs may reflect these expenses in their pricing. Understanding these overheads can help buyers anticipate cost variations across different suppliers.
-
Tooling: Specialized tooling for CNC machines can be a significant expense. This includes cutting tools, fixtures, and other accessories necessary for machine operation. Buyers should consider the longevity and efficiency of tooling when evaluating total costs.
-
Quality Control (QC): Quality assurance processes add to the manufacturing costs but are crucial for ensuring machine reliability and performance. Buyers should inquire about the QC measures employed by manufacturers to avoid future operational issues.
-
Logistics: Shipping costs can vary dramatically based on the machine’s size, weight, and the distance from the manufacturer to the buyer’s location. International buyers must factor in potential tariffs and customs fees, which can significantly affect total expenditures.
-
Margin: The manufacturer’s profit margin is another component of the pricing structure. Understanding typical margins in the industry can help buyers gauge whether they are receiving a fair price.
Price Influencers
-
Volume/MOQ: Purchasing in larger quantities often leads to discounts. Buyers should consider their current and future needs to negotiate better pricing based on minimum order quantities.
-
Specifications/Customization: Customization options can drive up costs. Buyers should clearly define their requirements to avoid unnecessary expenses while ensuring the machine meets their operational needs.
-
Materials and Quality Certifications: Machines built with higher-quality materials and recognized certifications (like ISO) may come at a premium but often result in lower maintenance costs and longer lifespans.
-
Supplier Factors: The reputation and reliability of the supplier can influence pricing. Established manufacturers may charge more for their expertise and support but can offer better long-term value.
-
Incoterms: The chosen Incoterms (International Commercial Terms) can affect logistics costs and risks. Buyers should understand the implications of different Incoterms to negotiate better shipping arrangements.
Buyer Tips
-
Negotiation: Always negotiate pricing and terms. Establishing a relationship with suppliers can lead to better deals and terms over time.
-
Cost-Efficiency: Evaluate the total cost of ownership, not just the initial purchase price. This includes operational costs, maintenance, and potential downtime.
-
Pricing Nuances: Be aware of regional pricing variations. For instance, machines sourced from Europe may carry higher prices due to stricter regulations and quality controls compared to those from other regions.
-
Research and Due Diligence: Conduct thorough research on potential suppliers. Look for customer reviews, case studies, and testimonials to validate their claims.
-
Stay Informed: Keep abreast of market trends and fluctuations in material costs, as these can influence machine pricing. Understanding these dynamics allows for more informed purchasing decisions.
In conclusion, a strategic approach to sourcing CNC stone cutting machines, characterized by an understanding of cost components and pricing influencers, will enhance the decision-making process for international B2B buyers. Always consider the long-term implications of your investment to ensure maximum value.
Spotlight on Potential cnc stone cutting machine Manufacturers and Suppliers
This section looks at several manufacturers active in the ‘cnc stone cutting machine’ market. This is a representative sample for illustrative purposes; B2B buyers must conduct extensive due diligence before any transaction. Information is synthesized from public sources and general industry knowledge.
Essential Technical Properties and Trade Terminology for cnc stone cutting machine
When considering the acquisition of a CNC stone cutting machine, understanding its technical specifications and trade terminology is essential for making informed purchasing decisions. This section outlines critical properties and common terms that international B2B buyers should be familiar with.
Key Technical Properties
-
Material Grade
– Definition: The classification of materials used in the construction of the CNC machine, typically ranging from mild steel to high-grade stainless steel.
– Importance: Higher material grades ensure durability and longevity, which translates to lower maintenance costs and increased reliability in operations. Buyers should assess the material grade to ensure it meets the demands of their specific applications. -
Tolerance
– Definition: The permissible limit or limits of variation in a physical dimension of the machine’s parts or the finished product.
– Importance: Precision is crucial in stone cutting. Tolerances determine how closely the machine can cut to the specified dimensions. A tighter tolerance often indicates higher quality and enables more complex designs, making it a vital consideration for manufacturers aiming for superior craftsmanship. -
Power Consumption
– Definition: The amount of electrical energy consumed by the CNC machine during operation, usually measured in kilowatts (kW).
– Importance: Understanding power consumption is critical for budgeting and operational efficiency. Machines with lower power requirements can significantly reduce overhead costs, especially in regions with high electricity prices. -
Spindle Speed
– Definition: The rotational speed of the spindle, typically measured in revolutions per minute (RPM).
– Importance: Spindle speed affects the cutting efficiency and the quality of the finish. Higher speeds can enhance productivity but may also require more robust tooling and materials. Buyers should match spindle speeds with the types of stone they plan to cut. -
Cutting Area
– Definition: The maximum dimensions of the material that can be processed by the machine, usually specified in length, width, and height.
– Importance: The cutting area determines the size of projects the machine can handle. Buyers should evaluate their production needs to ensure the machine can accommodate their largest materials.
Common Trade Terminology
-
OEM (Original Equipment Manufacturer)
– Definition: A company that produces parts and equipment that may be marketed by another manufacturer.
– Relevance: Understanding OEM relationships is essential for buyers looking for quality assurance and support. Machines sourced directly from OEMs often come with better warranties and after-sales service. -
MOQ (Minimum Order Quantity)
– Definition: The smallest quantity of a product that a supplier is willing to sell.
– Relevance: Knowing the MOQ is crucial for budgeting and inventory management. Buyers should negotiate terms that allow flexibility based on their production cycles. -
RFQ (Request for Quotation)
– Definition: A document issued by a buyer to invite suppliers to submit price proposals for specific products or services.
– Relevance: Using RFQs helps buyers compare offers from different suppliers effectively. A well-structured RFQ can lead to better pricing and terms. -
Incoterms (International Commercial Terms)
– Definition: A series of predefined international sales terms published by the International Chamber of Commerce (ICC) that clarify the responsibilities of buyers and sellers.
– Relevance: Familiarity with Incoterms is crucial for international transactions, as they define who is responsible for shipping, insurance, and tariffs. This knowledge aids in avoiding unexpected costs and delays. -
Lead Time
– Definition: The amount of time from the initiation of a process until its completion, particularly in the context of order fulfillment.
– Relevance: Understanding lead times helps buyers plan their production schedules. Longer lead times may necessitate adjustments in inventory management to avoid production delays.
By grasping these technical properties and trade terms, B2B buyers can navigate the complexities of purchasing CNC stone cutting machines more effectively, ensuring they make choices that align with their operational needs and business goals.
Navigating Market Dynamics, Sourcing Trends, and Sustainability in the cnc stone cutting machine Sector
The CNC stone cutting machine market is experiencing significant growth driven by several global factors. Increasing demand for precision in stone fabrication across various sectors, such as construction, architecture, and art, is propelling the market forward. Additionally, the rise of automation in manufacturing processes is enhancing productivity and reducing labor costs, which is particularly attractive to international B2B buyers. Countries in Africa, South America, the Middle East, and Europe are witnessing a growing trend toward advanced machining technologies that offer better efficiency and lower material waste.
Emerging technologies, such as artificial intelligence and the Internet of Things (IoT), are also shaping the sourcing landscape. These innovations enable real-time monitoring and predictive maintenance, which can significantly reduce downtime and maintenance costs. Furthermore, buyers are increasingly prioritizing suppliers who offer comprehensive support, including training and service packages, which enhances the overall value proposition of CNC machines. In regions like Poland and South Africa, local economic conditions and regulatory frameworks are influencing procurement strategies, with a focus on sourcing from manufacturers who understand the unique challenges of these markets.
Sustainability & Ethical Sourcing in B2B
The environmental impact of stone cutting and fabrication is a growing concern among international buyers. Sustainable practices in sourcing and manufacturing are becoming essential to comply with regulations and meet consumer expectations. Ethical sourcing involves selecting suppliers who utilize environmentally friendly materials and processes, thereby minimizing the ecological footprint of operations.
Buyers should look for manufacturers that hold certifications such as ISO 14001, which demonstrates a commitment to effective environmental management systems. Additionally, the use of recycled materials and the implementation of energy-efficient technologies in CNC stone cutting machines can contribute to a greener supply chain. As sustainability becomes a key differentiator in procurement decisions, B2B buyers are encouraged to engage with suppliers who not only provide high-quality machinery but also demonstrate a commitment to ethical practices and sustainability.
Brief Evolution/History
The evolution of CNC stone cutting machines dates back to the late 20th century when computer numerical control technology began to revolutionize manufacturing processes. Initially, these machines were primarily used for large-scale industrial applications. However, advancements in technology have led to greater accessibility and versatility, allowing smaller fabricators to adopt CNC systems for various applications, from intricate carvings to large slab processing. Today, the market is characterized by a diverse range of machine types and capabilities, catering to the specific needs of different regions and sectors, making them indispensable tools for modern stone fabrication businesses.
Related Video: What Is International Trade?
Frequently Asked Questions (FAQs) for B2B Buyers of cnc stone cutting machine
-
How do I vet suppliers for CNC stone cutting machines?
When sourcing CNC stone cutting machines, it’s crucial to conduct thorough supplier vetting. Start by researching the supplier’s reputation in the industry through online reviews and testimonials. Verify their certifications, such as ISO and CE, to ensure compliance with international quality standards. Additionally, request references from previous clients, particularly those in your region, to gauge their experience. Finally, consider visiting the supplier’s facility, if possible, to assess their production capabilities and quality control processes firsthand. -
Can I customize the CNC stone cutting machine to suit my specific needs?
Many manufacturers offer customization options for CNC stone cutting machines to meet unique operational requirements. Discuss your specific needs, such as size, material compatibility, and functionality, with potential suppliers. This may include adjustments to software, hardware, or additional features like automatic tool changers. Ensure that the supplier provides a clear outline of customization capabilities and any associated costs. Document these specifications in your contract to avoid misunderstandings later. -
What are the minimum order quantities (MOQ) and lead times for CNC machines?
Minimum order quantities (MOQs) for CNC stone cutting machines can vary significantly among suppliers. Some may have MOQs as low as one unit, while others may require larger orders. Lead times also depend on the machine model and the complexity of any customizations. Typically, lead times can range from a few weeks to several months. Always confirm these details before placing an order, and consider discussing expedited options if your project timeline is tight. -
What payment terms should I expect when purchasing internationally?
Payment terms for CNC stone cutting machines can vary widely based on the supplier’s policies and your negotiation. Common practices include a deposit upon order confirmation (often 30-50% of the total) and the balance before shipment. For international transactions, consider using secure payment methods like letters of credit or escrow services to mitigate risks. Always clarify the currency used for the transaction and any potential additional fees, such as bank transfer charges or currency conversion costs.
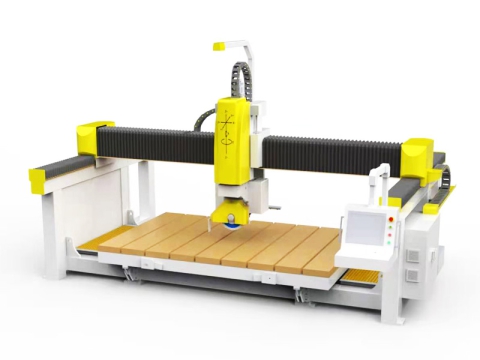
Illustrative Image (Source: Google Search)
-
What quality assurance measures and certifications should I look for?
Quality assurance is vital in the CNC stone cutting machine procurement process. Look for suppliers who adhere to recognized quality standards, such as ISO 9001, which indicates a commitment to quality management. Request detailed information about their quality control processes, including testing procedures for machines before shipment. Additionally, inquire about warranties and post-purchase support, as these can provide added assurance of the machine’s reliability and performance. -
How will logistics and shipping be handled for my CNC machine?
Logistics for shipping CNC stone cutting machines can be complex, especially for international buyers. Discuss with your supplier how they handle shipping, including freight options, insurance, and customs clearance. Make sure to understand the Incoterms (e.g., FOB, CIF) that dictate responsibilities for shipping costs and risks. It’s often beneficial to partner with a freight forwarder experienced in handling machinery shipments to navigate potential challenges and ensure timely delivery. -
What should I do if there is a dispute with the supplier?
In the event of a dispute with your supplier, it’s essential to address the issue promptly and professionally. Start by reviewing the contract to understand your rights and obligations. Communicate your concerns clearly, providing any supporting documentation. If direct negotiation fails, consider mediation or arbitration as alternatives to litigation, which can be costly and time-consuming. Having a clear dispute resolution clause in your contract can also streamline this process. -
How can I ensure proper installation and training for my CNC machine?
Proper installation and training are crucial for maximizing the performance of your CNC stone cutting machine. Confirm with your supplier that they offer installation services, either onsite or remotely, to ensure the machine is set up correctly. Additionally, inquire about training programs for your staff, which should cover both operation and maintenance. A well-structured training program will help your team become proficient and reduce the likelihood of operational errors, ultimately enhancing productivity.
Important Disclaimer & Terms of Use
⚠️ Important Disclaimer
The information provided in this guide, including content regarding manufacturers, technical specifications, and market analysis, is for informational and educational purposes only. It does not constitute professional procurement advice, financial advice, or legal advice.
While we have made every effort to ensure the accuracy and timeliness of the information, we are not responsible for any errors, omissions, or outdated information. Market conditions, company details, and technical standards are subject to change.
B2B buyers must conduct their own independent and thorough due diligence before making any purchasing decisions. This includes contacting suppliers directly, verifying certifications, requesting samples, and seeking professional consultation. The risk of relying on any information in this guide is borne solely by the reader.
Strategic Sourcing Conclusion and Outlook for cnc stone cutting machine
In the rapidly evolving landscape of CNC stone cutting machines, strategic sourcing emerges as a critical factor for international B2B buyers. Understanding the nuances of machine specifications, financing options, and long-term value can significantly impact operational efficiency and profitability. By focusing on reliable suppliers with a strong service and support framework, businesses can mitigate risks associated with equipment downtime and maintenance costs.
Key Takeaways:
– Evaluate Total Cost of Ownership: Consider not just the initial purchase price but also the costs associated with maintenance, training, and potential downtime.
– Seek Expert Guidance: Leverage the expertise of seasoned consultants who can tailor recommendations based on your specific production needs and shop layout.
– Leverage Financing Solutions: Explore various financing options to optimize cash flow while investing in essential machinery.
As you look to enhance your operations, prioritize strategic sourcing to ensure you acquire the right CNC stone cutting machine that aligns with your business goals. The future holds immense potential for growth in regions such as Africa, South America, the Middle East, and Europe. Embrace this opportunity by making informed decisions that will position your business for sustained success in the competitive stone fabrication market.