Master Switch Button Push: The Ultimate Sourcing Guide (2025)
Introduction: Navigating the Global Market for switch button push
In today’s fast-paced global market, sourcing reliable push button switches poses a significant challenge for international B2B buyers. Whether you’re in Africa, South America, the Middle East, or Europe, understanding the nuances of different switch types, applications, and supplier options is essential for making informed purchasing decisions. This comprehensive guide delves into various aspects of push button switches, from momentary and latching types to illuminated options, ensuring that you can navigate the complexities of the market with confidence.
International buyers will benefit from insights on supplier vetting processes, cost considerations, and the critical role of certifications and standards in ensuring product quality and safety. We will also explore the various applications of push button switches across industries such as automotive, electronics, and home automation, highlighting how these components are integral to modern technology solutions.
By equipping yourself with the knowledge provided in this guide, you will be empowered to make strategic choices that enhance your operational efficiency and product reliability. This resource aims to demystify the global landscape for push button switches, providing actionable insights tailored specifically for B2B buyers seeking quality and value.
Understanding switch button push Types and Variations
Type Name | Key Distinguishing Features | Primary B2B Applications | Brief Pros & Cons for Buyers |
---|---|---|---|
Momentary Push Button Switch | Activates only while pressed; returns to default position. | Control panels, machinery operation | Pros: Simple operation; ideal for temporary functions. Cons: Not suitable for continuous use. |
Latching Push Button Switch | Remains in the last position until pressed again. | Lighting control, equipment power | Pros: Convenient for maintaining settings; reduces accidental activation. Cons: May lead to confusion if not labeled properly. |
Illuminated Push Button Switch | Features built-in LED indicators for visibility. | Consumer electronics, machinery | Pros: Enhances user interface; improves usability in low-light conditions. Cons: Higher cost due to additional components. |
Sealed Push Button Switch | Designed for moisture and dust resistance (IP67 rating). | Outdoor equipment, industrial use | Pros: Durable and reliable in harsh environments. Cons: Limited design options and potentially higher prices. |
Subminiature Push Button Switch | Compact design for space-constrained applications. | Medical devices, compact electronics | Pros: Space-saving; suitable for intricate designs. Cons: May not handle high current loads. |
What Are the Characteristics of Momentary Push Button Switches?
Momentary push button switches are designed to be activated only while they are being pressed. Once released, they revert to their original state. This type is commonly used in control panels and machinery operations where temporary activation is required, such as starting a motor or triggering an alarm. When considering a momentary switch, B2B buyers should evaluate the switch’s durability and response time, especially in high-frequency applications.
How Do Latching Push Button Switches Work?
Latching push button switches remain in their last activated position until pressed again, making them ideal for applications like lighting control or powering equipment. These switches can simplify user interactions by eliminating the need for constant pressure. However, buyers should ensure proper labeling to avoid confusion, as users may not always remember the switch’s current state.
Why Choose Illuminated Push Button Switches?
Illuminated push button switches incorporate LED indicators to provide visual feedback, enhancing the user experience, especially in low-light environments. They are widely used in consumer electronics and machinery to improve usability. Buyers should consider the brightness and color of the LEDs, as well as the switch’s compatibility with existing systems, to ensure optimal functionality and aesthetic alignment.
What Are the Benefits of Sealed Push Button Switches?
Sealed push button switches are designed to withstand harsh environmental conditions, with an IP67 rating that protects against moisture and dust. These switches are ideal for outdoor equipment and industrial applications where reliability is crucial. When purchasing sealed switches, B2B buyers should assess the environmental ratings and the expected lifespan of the switch to ensure they meet operational demands.
When to Use Subminiature Push Button Switches?
Subminiature push button switches are compact, making them perfect for space-constrained applications like medical devices and compact electronics. Their small size allows for intricate designs without compromising functionality. However, buyers should be mindful of the current ratings and ensure that the switch can handle the required load, as these switches may not be suitable for high-power applications.
Key Industrial Applications of switch button push
Industry/Sector | Specific Application of switch button push | Value/Benefit for the Business | Key Sourcing Considerations for this Application |
---|---|---|---|
Manufacturing | Control panels for machinery operations | Enhances operational efficiency and safety | Durability, compatibility with existing systems, and ease of installation |
Automotive | Dashboard controls for vehicle functions | Improves user experience and safety in vehicle operation | Compliance with automotive standards, resistance to environmental factors |
Telecommunications | Equipment activation and deactivation | Streamlines service activation and maintenance | Reliability, size, and integration with existing telecom infrastructure |
Consumer Electronics | User interface for electronic devices | Increases product appeal and usability | Aesthetic design, tactile feedback, and LED options for visibility |
Healthcare | Medical equipment control for patient monitoring systems | Ensures quick response times and improves patient safety | Biocompatibility, ease of cleaning, and compliance with health regulations |
How Are Push Button Switches Used in Manufacturing?
In the manufacturing sector, push button switches are integral to control panels that manage machinery operations. These switches allow operators to start, stop, or adjust equipment with a simple push, enhancing operational efficiency and safety. International buyers must consider the durability of these switches, as they need to withstand harsh industrial environments. Compatibility with existing systems is also crucial, ensuring seamless integration into current operations.
What Role Do Push Button Switches Play in Automotive Applications?
In the automotive industry, push button switches serve as essential components for dashboard controls, enabling users to activate various vehicle functions such as ignition, lights, and infotainment systems. This functionality not only improves user experience but also enhances safety by providing a reliable means to control critical systems. Buyers from regions like Europe and the Middle East should ensure that the switches comply with automotive standards and can resist environmental factors such as temperature fluctuations and humidity.
How Are Push Button Switches Utilized in Telecommunications?
Telecommunications companies utilize push button switches to activate and deactivate equipment, thereby streamlining service activation and maintenance processes. These switches enable technicians to manage complex systems efficiently, reducing downtime and enhancing service delivery. When sourcing these components, businesses should prioritize reliability and compatibility with existing telecom infrastructure to avoid disruptions in service.
What Are the Benefits of Push Button Switches in Consumer Electronics?
In consumer electronics, push button switches enhance the user interface of devices, making them more appealing and user-friendly. These switches are often designed to provide tactile feedback and may include LED indicators for visibility in low-light conditions. B2B buyers should focus on the aesthetic design and functionality of these switches, ensuring they meet consumer expectations while also being cost-effective and easy to integrate into existing product lines.
How Are Push Button Switches Applied in Healthcare Equipment?
In the healthcare sector, push button switches are crucial for controlling medical equipment, particularly in patient monitoring systems. These switches facilitate quick response times, which are vital for patient safety during critical situations. Buyers in this field must consider biocompatibility and ease of cleaning to comply with health regulations, ensuring that the switches can be maintained in sterile environments while providing reliable performance.
3 Common User Pain Points for ‘switch button push’ & Their Solutions
Scenario 1: Difficulty in Sourcing Compatible Push Button Switches
The Problem: B2B buyers often encounter challenges when sourcing push button switches that are compatible with their existing systems. This is particularly true for international buyers in regions like Africa and South America, where local vendors may not carry a wide range of options. Incompatibility can lead to project delays, increased costs, and frustrations, especially when the specific requirements of voltage, size, and functionality are not readily available.
The Solution: To overcome sourcing challenges, buyers should conduct thorough research and engage with multiple suppliers. Utilize online platforms that specialize in electrical components to compare specifications and availability. When contacting suppliers, provide detailed information about your existing systems, including technical specifications and certifications required for your region. Additionally, consider working with manufacturers that offer customization options, which can help ensure that the switch meets your specific needs. Leveraging global suppliers who can ship internationally can also broaden your options significantly.
Scenario 2: Poor Quality and Reliability of Push Button Switches
The Problem: Reliability is a significant concern for B2B buyers, particularly in industries where equipment failure can lead to costly downtime. Many buyers report issues with low-quality push button switches that fail to operate as expected after a short period. This is especially pertinent in sectors like manufacturing and automation, where switches endure frequent use and environmental challenges.
The Solution: To mitigate quality concerns, buyers should prioritize sourcing switches from reputable manufacturers known for their reliability and quality assurance processes. Look for switches that meet international standards and have undergone rigorous testing. Request certifications and performance data to understand the switch’s durability under various conditions. Additionally, consider investing in higher-quality switches even if they come at a premium; the long-term savings from reduced failures and maintenance can justify the upfront costs. Establishing a relationship with trusted suppliers who provide warranties can also provide peace of mind.
Scenario 3: Complexity in Installation and Integration
The Problem: Installation and integration of push button switches can be complex, particularly for B2B buyers managing large-scale projects. Buyers often face difficulties in ensuring that the switches integrate seamlessly with existing control systems. Misalignment can lead to functional issues, requiring additional troubleshooting and adjustments that can drain resources and time.
The Solution: To simplify installation and integration, buyers should invest in detailed product documentation and support from manufacturers. When selecting push button switches, consider those that come with comprehensive installation guides and technical support. Moreover, investing in training for your technical team can significantly reduce integration issues. For complex systems, consider collaborating with an experienced electrical engineer or consultant who can assist in the design and installation process. Establishing a clear communication channel with the supplier can also facilitate quicker resolutions for any issues that arise during installation.
Strategic Material Selection Guide for switch button push
What Are the Key Materials Used in Push Button Switches?
When selecting materials for push button switches, it’s essential to consider various factors such as durability, cost, and compatibility with specific applications. Here, we analyze four common materials used in the manufacturing of push button switches: plastic, metal, rubber, and silicone.
How Does Plastic Perform in Push Button Switch Applications?
Key Properties: Plastic is lightweight, resistant to corrosion, and offers good electrical insulation. Common types include polycarbonate and ABS, which can withstand a range of temperatures and pressures.
Pros & Cons: The advantages of plastic include its low cost and ease of manufacturing, making it suitable for high-volume production. However, plastic may not be as durable as metal and can degrade under extreme temperatures or UV exposure.
Impact on Application: Plastic is suitable for indoor applications where moisture and extreme temperatures are not significant concerns. It is often used in consumer electronics and household appliances.
Considerations for International Buyers: Compliance with international standards such as ASTM and IEC is crucial. Buyers from regions like Europe and the Middle East should ensure that the selected plastic meets RoHS regulations to avoid hazardous substances.
What Are the Advantages of Metal in Push Button Switches?
Key Properties: Metals like stainless steel and aluminum offer excellent strength and durability. They are resistant to corrosion and can handle higher temperatures and pressures compared to plastics.
Pros & Cons: The primary advantage of metal is its longevity and robustness, making it ideal for industrial applications. However, metal switches can be more expensive and may require more complex manufacturing processes, which can increase lead times.
Impact on Application: Metal switches are often used in harsh environments, such as manufacturing plants or outdoor settings, where they are exposed to moisture, dust, and extreme temperatures.
Considerations for International Buyers: Buyers should be aware of compliance with standards such as ISO and DIN, especially in Europe. Additionally, understanding the local market’s preferences for metal finishes can influence purchasing decisions.
How Does Rubber Contribute to Push Button Switch Functionality?
Key Properties: Rubber is flexible, provides good tactile feedback, and is resistant to moisture and dust. It can also withstand various temperatures, depending on the type of rubber used.
Pros & Cons: The key advantage of rubber is its ability to create a seal, making it ideal for applications requiring protection against environmental factors. However, rubber may not be suitable for high-temperature applications and can degrade over time if exposed to certain chemicals.
Impact on Application: Rubber is commonly used in automotive and outdoor applications where moisture resistance is critical. It is also prevalent in consumer products that require a soft-touch interface.
Considerations for International Buyers: Buyers should consider the specific rubber compounds used, as different formulations can affect performance. Compliance with automotive industry standards may also be necessary for buyers in that sector.
What Role Does Silicone Play in Push Button Switch Design?
Key Properties: Silicone is highly flexible, resistant to extreme temperatures, and offers excellent durability. It is also non-toxic and provides good electrical insulation.
Pros & Cons: The primary advantage of silicone is its ability to withstand extreme environmental conditions, making it suitable for both indoor and outdoor applications. However, silicone can be more expensive than other materials and may have longer lead times for manufacturing.
Impact on Application: Silicone is often used in applications requiring a high degree of flexibility and durability, such as medical devices and high-performance electronics.
Considerations for International Buyers: Buyers should ensure that silicone materials comply with relevant health and safety regulations, especially in regions like Europe where stringent standards apply.
Summary Table of Material Selection for Push Button Switches
Material | Typical Use Case for switch button push | Key Advantage | Key Disadvantage/Limitation | Relative Cost (Low/Med/High) |
---|---|---|---|---|
Plastic | Indoor consumer electronics | Low cost and lightweight | Less durable, can degrade under UV | Low |
Metal | Industrial and outdoor applications | High durability and strength | Higher cost and complex manufacturing | High |
Rubber | Automotive and moisture-sensitive applications | Good tactile feedback and sealing | Limited high-temperature use | Medium |
Silicone | Medical devices and high-performance electronics | Excellent temperature resistance | Higher cost and longer lead times | High |
This strategic material selection guide provides international B2B buyers with actionable insights for making informed decisions regarding push button switches. Understanding the properties, advantages, and limitations of each material can help in selecting the most suitable option for specific applications.
In-depth Look: Manufacturing Processes and Quality Assurance for switch button push
What Are the Key Stages in the Manufacturing Process of Push Button Switches?
The manufacturing of push button switches involves several critical stages, each designed to ensure efficiency, precision, and adherence to quality standards. Below are the main stages:
1. Material Preparation
The first step in the manufacturing process is selecting and preparing the right materials. Common materials for push button switches include plastic for the button housing, metal for the contacts, and silicone for seals. Material quality is paramount as it directly affects the switch’s durability and functionality. Suppliers should be vetted for material certification, ensuring compliance with international standards such as ISO 9001, which focuses on consistent quality management systems.
2. Forming
Once materials are prepared, they undergo forming processes to create the various components of the push button switch. This includes injection molding for plastic parts and stamping or machining for metal contacts. Advanced techniques such as CNC machining can provide high precision, especially for custom components. Buyers should inquire about the forming methods used and the technology in place to reduce waste and enhance efficiency.
3. Assembly
The assembly phase combines all components into a functional unit. Automated assembly lines are common, utilizing robotics to improve speed and reduce human error. However, manual assembly is also prevalent for more complex designs. B2B buyers should ensure that suppliers have robust assembly processes that include quality checks at each stage to catch defects early.
4. Finishing
Finishing processes enhance the aesthetic appeal and functional properties of the push button switches. This may involve surface treatment such as plating, painting, or applying coatings to improve durability and resistance to environmental factors. Buyers should confirm that suppliers use environmentally friendly finishing techniques and comply with regulations such as RoHS (Restriction of Hazardous Substances).
How Is Quality Assurance Implemented in Push Button Switch Manufacturing?
Quality assurance (QA) is critical in the manufacturing of push button switches to ensure that products meet both regulatory requirements and customer expectations. Here are the components of a robust QA system:
Relevant International Standards for Quality Assurance
Manufacturers often adhere to several international standards, including:
- ISO 9001: This standard ensures that manufacturers have a quality management system in place that focuses on continuous improvement and customer satisfaction.
- CE Marking: For products sold in Europe, CE marking indicates compliance with EU safety, health, and environmental protection standards.
- API Standards: Particularly relevant for switches used in industries like oil and gas, API standards ensure that products meet specific safety and performance criteria.
Key Quality Control Checkpoints
Quality control (QC) processes typically include:
- Incoming Quality Control (IQC): This initial checkpoint involves inspecting raw materials upon arrival to ensure they meet specified standards.
- In-Process Quality Control (IPQC): This ongoing monitoring occurs during the manufacturing process, allowing for real-time adjustments and defect detection.
- Final Quality Control (FQC): This final stage assesses the completed products before shipping, ensuring they meet all specifications and functionality tests.
What Testing Methods Are Commonly Used in Quality Assurance?
Several testing methods are employed to verify the quality and functionality of push button switches:
- Electrical Testing: This includes continuity and resistance tests to ensure proper electrical performance.
- Environmental Testing: Push button switches may be subjected to humidity, temperature, and vibration tests to evaluate their durability in various conditions.
- Mechanical Testing: This assesses the mechanical strength and operational life of the switches, ensuring they can withstand repeated use.
How Can B2B Buyers Verify Supplier Quality Control?
For international B2B buyers, particularly those from Africa, South America, the Middle East, and Europe, verifying a supplier’s quality control is essential. Here are actionable steps:
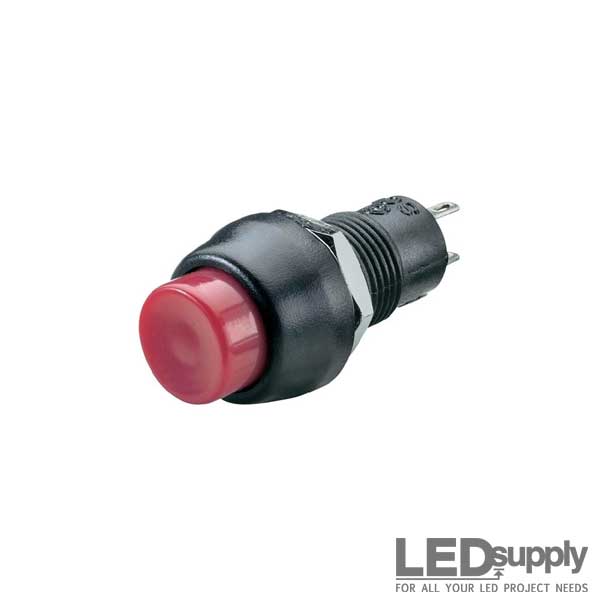
A stock image related to switch button push.
Conduct Supplier Audits
Conducting on-site audits is one of the most effective ways to evaluate a supplier’s manufacturing and QC processes. This allows buyers to observe the production environment, quality checks, and compliance with international standards.
Request Quality Assurance Reports
Suppliers should provide documentation of their QA processes, including IQC, IPQC, and FQC reports. These documents should detail the testing methods used, results obtained, and any corrective actions taken for defects.
Engage Third-Party Inspectors
Utilizing third-party inspection services can provide an unbiased evaluation of the supplier’s processes and product quality. These inspectors can perform random checks and provide reports on compliance with specified standards.
What Are the Quality Control Nuances for International B2B Buyers?
International buyers should be aware of several nuances in quality control:
- Cultural Differences: Different regions may have varying approaches to quality management. Understanding these cultural differences can help facilitate better communication and expectations with suppliers.
- Regulatory Compliance: Buyers must ensure that products comply with the regulations of their own countries. This may require additional testing or certifications that the supplier must fulfill.
- Supply Chain Transparency: It is crucial for buyers to have visibility into the entire supply chain, including sub-suppliers, as quality issues can arise from any part of the production process.
Conclusion
The manufacturing processes and quality assurance systems for push button switches are intricate and require a thorough understanding from B2B buyers. By knowing the key manufacturing stages, quality assurance practices, and verification methods, international buyers can make informed decisions when sourcing push button switches. This diligence not only ensures product quality but also fosters long-term relationships with reliable suppliers across different regions.
Practical Sourcing Guide: A Step-by-Step Checklist for ‘switch button push’
In the competitive landscape of B2B procurement, sourcing push button switches requires a methodical approach to ensure quality, compliance, and suitability for your specific needs. This guide provides a step-by-step checklist designed for international buyers, especially those from Africa, South America, the Middle East, and Europe, to streamline the sourcing process effectively.
Step 1: Define Your Technical Specifications
Before initiating the procurement process, clearly outline the technical specifications of the push button switches you require. This includes details such as voltage, current ratings, type (momentary or latching), and any specific environmental considerations (e.g., IP ratings for moisture and dust resistance). Having precise specifications helps narrow down suppliers who can meet your exact needs.
- Voltage and Current Ratings: Ensure compatibility with your existing systems.
- Type of Switch: Choose between momentary (temporary action) or latching (maintains state).
Step 2: Research Potential Suppliers
Conduct thorough research to identify potential suppliers specializing in push button switches. Look for companies with a strong reputation in the industry and a proven track record of delivering quality products. Utilize online directories, trade shows, and industry forums to gather information.
- Supplier Reviews: Check customer reviews and ratings.
- Industry Experience: Consider suppliers with experience in your specific market or application.
Step 3: Evaluate Supplier Certifications
Verifying supplier certifications is essential to ensure compliance with international quality standards. Look for certifications such as ISO 9001 for quality management, CE marking for European compliance, and RoHS compliance for hazardous substances. These certifications demonstrate that the supplier adheres to strict manufacturing and safety protocols.
- Quality Assurance: Certifications indicate a commitment to quality.
- Regulatory Compliance: Ensures products meet legal requirements in your region.
Step 4: Request Samples for Testing
Before placing a bulk order, request samples of the push button switches. Testing samples allows you to assess the quality, functionality, and suitability of the switches for your application. This step is crucial to avoid costly mistakes later in the procurement process.
- Functionality Testing: Check for responsiveness and durability.
- Compatibility Testing: Ensure the switches integrate seamlessly with your systems.
Step 5: Negotiate Pricing and Terms
Once you have identified a suitable supplier and tested samples, engage in negotiations regarding pricing and terms of sale. Consider factors such as bulk order discounts, payment terms, and delivery schedules. Establishing clear terms can lead to better pricing and service.
- Volume Discounts: Ask about pricing for larger quantities.
- Payment Terms: Clarify payment methods and timelines.
Step 6: Establish Clear Communication Channels
Effective communication with your chosen supplier is key to successful procurement. Establish clear channels for discussing order updates, technical support, and any potential issues that may arise. Regular communication helps build a strong supplier relationship and ensures that any concerns are addressed promptly.
- Contact Points: Identify primary contacts for different issues.
- Response Times: Set expectations for how quickly inquiries will be answered.
Step 7: Plan for Logistics and Delivery
Lastly, ensure that you have a logistics plan in place for the delivery of your push button switches. Consider factors such as shipping methods, customs clearance, and delivery timelines. Proper logistics planning helps avoid delays and ensures that your production schedules remain on track.
- Shipping Options: Evaluate air freight vs. sea freight based on urgency.
- Customs Requirements: Understand documentation needed for smooth importation.
By following this step-by-step checklist, B2B buyers can effectively navigate the sourcing process for push button switches, ensuring they acquire the best products for their needs while minimizing risks associated with procurement.
Comprehensive Cost and Pricing Analysis for switch button push Sourcing
What Are the Key Cost Components in Push Button Switch Sourcing?
When sourcing push button switches for B2B applications, understanding the cost structure is crucial for effective budgeting and negotiation. The primary cost components include:
-
Materials: The type of materials used significantly impacts the overall cost. High-quality plastics, metals, and electronic components often increase production costs but enhance durability and performance.
-
Labor: Labor costs vary by region and production methods. Automated processes may reduce labor costs, while skilled labor for intricate designs may increase them.
-
Manufacturing Overhead: This encompasses utilities, equipment maintenance, and facility costs. Efficient production facilities can minimize overhead, contributing to competitive pricing.
-
Tooling: Initial setup costs for molds and machinery can be substantial, particularly for custom designs. These costs are amortized over the production volume, making them a critical consideration for pricing.
-
Quality Control (QC): Ensuring product quality involves testing and inspections, which add to costs. Rigorous QC can lead to higher upfront expenses but ultimately reduces returns and warranty claims.
-
Logistics: Shipping costs vary based on the shipping method, distance, and weight. Understanding logistics can help buyers negotiate better terms and minimize costs.
-
Margin: Suppliers typically include a margin to cover their costs and profit. This can be influenced by market competition and perceived value.
How Do Price Influencers Affect Push Button Switch Costs?
Several factors influence the pricing of push button switches, making it essential for buyers to be aware of these elements:
-
Volume/MOQ: Bulk orders often result in lower per-unit costs. Understanding the minimum order quantity (MOQ) can help buyers negotiate better pricing.
-
Specifications and Customization: Customized designs or specific technical specifications generally incur higher costs. It’s important to weigh the benefits of customization against the added expense.
-
Materials: The choice of materials directly affects pricing. Premium materials may enhance functionality but can also increase costs significantly.
-
Quality and Certifications: Products that meet international quality standards or certifications often come at a premium. Buyers should assess the necessity of these certifications based on their market requirements.
-
Supplier Factors: Supplier reputation, reliability, and production capabilities can influence pricing. Established suppliers may charge more due to their perceived value and quality assurance.
-
Incoterms: Understanding the delivery terms, including who bears the shipping costs and risks, can affect total costs. Different Incoterms can lead to significant cost variances, especially for international transactions.
What Are Effective Buyer Tips for Sourcing Push Button Switches?
To optimize sourcing strategies, international B2B buyers, particularly from Africa, South America, the Middle East, and Europe, should consider the following tips:
-
Negotiation: Always negotiate terms and prices. Suppliers often have room for adjustments, especially for larger orders or long-term contracts.
-
Cost-Efficiency: Evaluate the Total Cost of Ownership (TCO), which includes not only the purchase price but also shipping, handling, and potential maintenance costs over the product’s lifecycle.
-
Pricing Nuances: Be aware of currency fluctuations and import tariffs that can affect final costs. Understanding these nuances can help in budgeting and financial planning.
-
Supplier Diversification: Avoid relying on a single supplier. By diversifying suppliers, buyers can mitigate risks related to pricing and supply chain disruptions.
-
Market Research: Conduct thorough market research to understand regional price trends and competitor offerings. This information can empower buyers during negotiations.
Disclaimer on Indicative Prices
The prices for push button switches vary widely based on the factors discussed above. The prices mentioned in various sources may serve as a guideline but should not be considered definitive. Always request quotes from multiple suppliers to ensure competitive pricing and better decision-making.
Alternatives Analysis: Comparing switch button push With Other Solutions
In the realm of B2B solutions for control systems and interfaces, the switch button push is a well-known option. However, as technology evolves and industries diversify, it’s crucial to explore alternatives that may better suit specific operational needs. This section examines alternative solutions to the traditional push button switch, providing valuable insights for international B2B buyers from Africa, South America, the Middle East, and Europe.
Comparison Table of Switch Button Push and Alternatives
Comparison Aspect | Switch Button Push | Touchscreen Interface | Voice-Controlled Systems |
---|---|---|---|
Performance | Reliable; tactile feedback | High responsiveness; multi-functional | Varies; dependent on voice recognition accuracy |
Cost | Moderate; generally affordable | Higher initial investment; cost varies by size | High; requires advanced technology and setup |
Ease of Implementation | Simple installation; minimal training | Requires technical setup; user training needed | Complex setup; needs voice recognition software |
Maintenance | Low; occasional cleaning | Moderate; software updates and calibration | High; software maintenance and updates necessary |
Best Use Case | Industrial applications, machinery control | Interactive displays, user interfaces | Smart environments, accessibility applications |
What Are the Benefits and Drawbacks of Touchscreen Interfaces?
Touchscreen interfaces offer a modern alternative to traditional switch button pushes. They provide high responsiveness and the ability to integrate multiple functions into a single interface, making them ideal for complex systems where space is a concern. However, the initial investment can be higher, and the need for user training may complicate implementation. Maintenance also requires regular software updates, which can be a burden for companies looking for low-maintenance solutions.
How Do Voice-Controlled Systems Compare?
Voice-controlled systems represent a cutting-edge solution that enhances user interaction without the need for physical contact. This technology is particularly beneficial in smart environments and accessibility applications, where hands-free operation is essential. While they offer a high level of convenience, the accuracy of voice recognition can vary significantly based on environmental factors and accents, potentially leading to frustrations. Additionally, the setup can be complex and costly, requiring specialized software and ongoing maintenance.
Conclusion: How to Choose the Right Solution for Your Needs
When evaluating alternatives to the switch button push, international B2B buyers must consider several factors, including performance, cost, ease of implementation, maintenance, and the specific use case. While the switch button remains a reliable choice for many industrial applications, alternatives like touchscreen interfaces and voice-controlled systems can provide enhanced functionality and user experience in suitable environments. Ultimately, the right solution will depend on the unique operational requirements and technological readiness of your organization. By weighing these considerations, businesses can make informed decisions that align with their strategic objectives and budgetary constraints.
Essential Technical Properties and Trade Terminology for switch button push
What Are the Key Technical Properties of Push Button Switches?
Understanding the essential technical properties of push button switches is crucial for international B2B buyers. These specifications not only determine the switch’s performance but also its suitability for specific applications. Here are some key properties to consider:
1. Material Grade: Why Does It Matter?
The material grade of push button switches affects their durability, resistance to environmental factors, and overall performance. Common materials include thermoplastic, metal, and silicone. For example, thermoplastic switches are lightweight and cost-effective, while metal switches offer superior durability and aesthetics. Buyers should consider the operating environment—metal options may be more suitable for industrial settings, while plastic may suffice for consumer electronics.
2. Electrical Rating: How Does It Impact Functionality?
The electrical rating indicates the maximum voltage and current the switch can handle, typically expressed in volts (V) and amperes (A). For instance, a switch rated for 12V and 5A is suitable for low-power applications, while higher ratings may be necessary for industrial machinery. Selecting a switch with the correct electrical rating is crucial to avoid failures and ensure safety.
3. Tolerance: What Level of Precision Is Required?
Tolerance refers to the allowable deviation from specified dimensions in the switch’s design. High tolerance levels are essential for applications requiring precise control, such as in automotive or aerospace industries. A tighter tolerance ensures consistent performance, reducing the risk of malfunction. B2B buyers should assess whether their application demands high-precision components.
4. Actuation Force: What Is the Ideal Pressure?
Actuation force is the amount of pressure needed to activate the switch. This property affects user experience and safety. For instance, switches requiring a high actuation force may be more suitable for industrial settings where accidental activation must be minimized, while lower forces may be appropriate for consumer devices. Understanding the required actuation force can enhance product usability.
5. Sealing Rating: How Important Is Protection Against Elements?
The sealing rating, often indicated by the Ingress Protection (IP) code, signifies the switch’s resistance to dust and moisture. An IP67 rating, for example, means the switch is dust-tight and can withstand immersion in water up to a certain depth. For international buyers, especially in regions with harsh environments, selecting a switch with an appropriate sealing rating can prolong product life and reliability.
What Are Common Trade Terms Related to Push Button Switches?
Familiarity with industry terminology helps B2B buyers navigate the procurement process effectively. Here are some common terms:
1. OEM (Original Equipment Manufacturer): What Does It Mean?
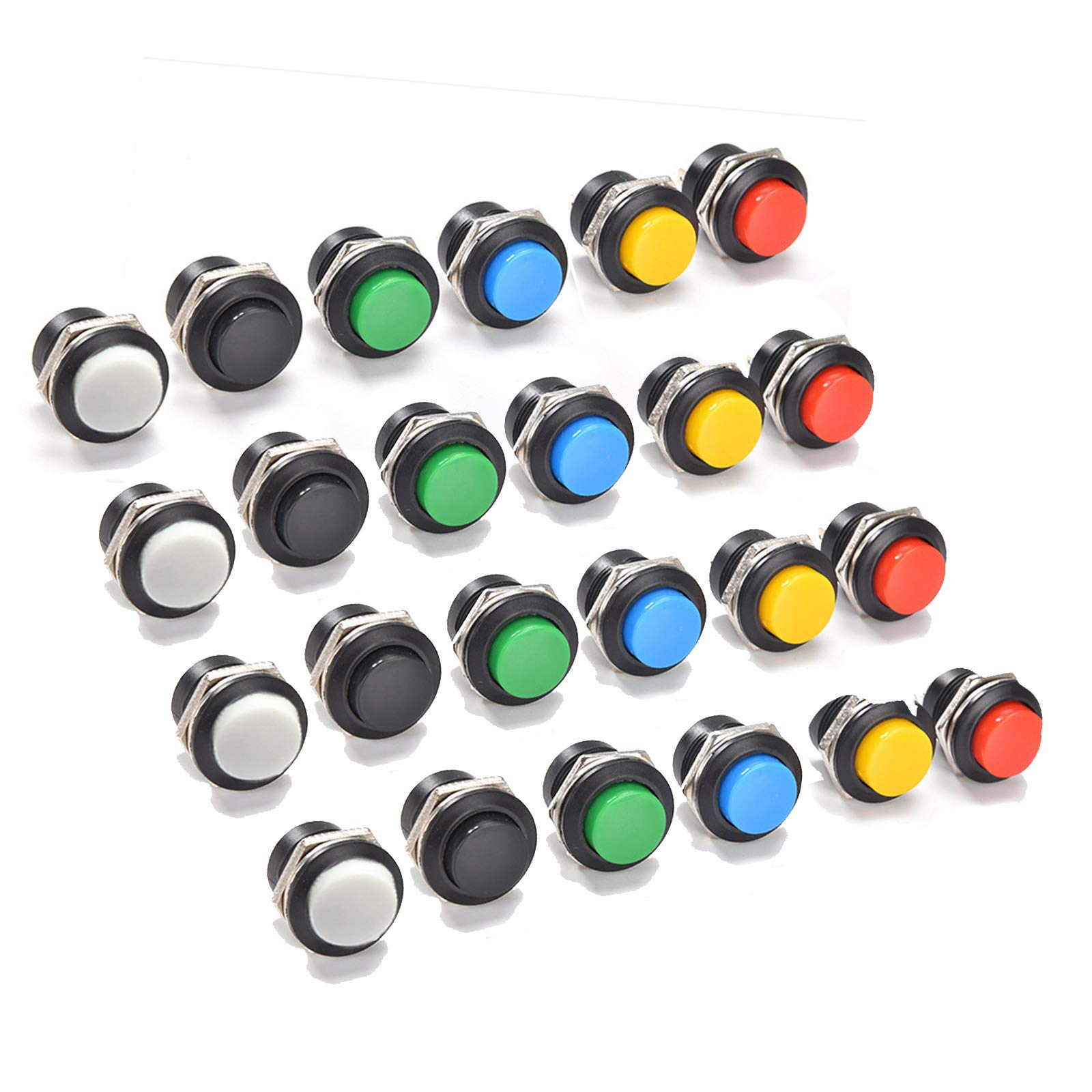
A stock image related to switch button push.
OEM refers to companies that produce parts or equipment that may be marketed by another manufacturer. For B2B buyers, partnering with an OEM can ensure high-quality components tailored to specific needs, often at a lower cost compared to buying from a brand name.
2. MOQ (Minimum Order Quantity): Why Is It Significant?
MOQ is the smallest quantity of a product that a supplier is willing to sell. Understanding MOQ is vital for buyers to manage inventory costs and ensure they are not overstocking. Negotiating lower MOQs can lead to cost savings, especially for smaller businesses.
3. RFQ (Request for Quotation): How Should It Be Used?
An RFQ is a document sent to suppliers requesting a price quote for specific products. B2B buyers should provide detailed specifications to receive accurate quotes. This process helps in comparing offers from different suppliers effectively.
4. Incoterms (International Commercial Terms): What Are They?
Incoterms are international trade terms that define the responsibilities of buyers and sellers in shipping and logistics. They clarify who is responsible for costs, risks, and insurance during transportation. Understanding these terms is crucial for international buyers to avoid unexpected expenses.
5. Lead Time: How Does It Affect Purchasing Decisions?
Lead time is the time taken from placing an order to receiving it. Shorter lead times are preferable for maintaining inventory levels and meeting customer demands. B2B buyers should inquire about lead times when negotiating contracts to align with their operational schedules.
By understanding these technical properties and trade terms, international B2B buyers can make informed purchasing decisions when sourcing push button switches, ensuring they meet the specific needs of their applications.
Navigating Market Dynamics and Sourcing Trends in the switch button push Sector
What Are the Current Market Dynamics and Sourcing Trends in the Switch Button Push Sector?
The global market for switch button push products is experiencing significant growth, driven by the increasing demand for automation in various industries, including manufacturing, automotive, and consumer electronics. In regions like Africa and South America, emerging economies are investing in infrastructure development, which fuels the need for reliable and efficient control systems. Meanwhile, Europe and the Middle East are witnessing a shift towards smart technology integration, where push button switches are pivotal in enhancing user experience and operational efficiency.
A notable trend is the adoption of smart push button switches that integrate with IoT devices. This technology allows for remote control and monitoring, which is particularly appealing to businesses looking to improve operational efficiency and energy management. Furthermore, the rise of e-commerce platforms has simplified sourcing for international buyers, enabling them to access a wider range of products and suppliers. This shift not only enhances competition but also encourages innovation in product design and functionality.
Another emerging trend is the preference for customizable and modular solutions. Buyers are increasingly looking for switch button products that can be tailored to specific applications or environments, particularly in sectors such as healthcare, where specialized controls are crucial. Additionally, the focus on user-friendly designs is reshaping product offerings, as manufacturers aim to cater to a broader audience, including those with accessibility needs.
How Is Sustainability Influencing B2B Sourcing Decisions in the Switch Button Push Sector?
Sustainability is becoming a critical factor in the sourcing decisions of B2B buyers in the switch button push sector. Companies are increasingly aware of the environmental impact associated with the production and disposal of electrical components. This has led to a growing demand for products made from sustainable materials and those that are energy-efficient, thus minimizing their carbon footprint.
Buyers are also prioritizing suppliers who demonstrate a commitment to ethical sourcing practices. This includes ensuring that materials are sourced responsibly, labor conditions are fair, and that there is transparency in the supply chain. Certifications such as ISO 14001 for environmental management and RoHS compliance for hazardous materials are becoming essential for suppliers aiming to appeal to environmentally-conscious buyers.
Moreover, the incorporation of ‘green’ technologies in product design, such as energy-efficient push button switches, is becoming increasingly popular. These products not only meet regulatory standards but also provide long-term cost savings for businesses. As a result, international buyers are encouraged to conduct thorough supplier assessments to ensure that their sourcing aligns with sustainability goals.
What Is the Historical Context of Push Button Switches in B2B Markets?
The push button switch has a rich history that dates back to the late 19th century, initially used in household lighting systems. Over the decades, advancements in technology have transformed these simple mechanical devices into sophisticated electronic controls. The early 20th century saw the introduction of illuminated push button switches, enhancing visibility and usability, which became critical in both residential and commercial applications.
In recent decades, the evolution of push button technology has been marked by the integration of digital features and smart technology, enabling functionalities such as remote control and programmability. This evolution has not only broadened the applications of push button switches but has also set new standards for reliability and performance in various industrial and commercial settings. As international B2B buyers seek innovative solutions, understanding this historical context can provide valuable insights into the development and future direction of push button technologies.
Frequently Asked Questions (FAQs) for B2B Buyers of switch button push
-
How do I choose the right push button switch for my application?
Selecting the appropriate push button switch depends on several factors, including the voltage, current rating, and type of switch action (momentary vs. latching). Consider your specific application environment—will it be exposed to moisture or dust? If so, opt for sealed or IP-rated switches. Additionally, evaluate the aesthetic and functional requirements, such as color and illumination options. Engage with suppliers to understand their product range and request samples for testing before making a bulk purchase. -
What is the best type of push button switch for industrial applications?
For industrial applications, the best push button switches are often those that are robust and designed for heavy-duty use. Sealed push button switches with IP67 ratings are ideal, as they protect against dust and moisture. Look for options with a high operating cycle life and tactile feedback for better usability. Brands that specialize in industrial components often offer customizable options, enabling you to meet specific operational needs. -
What customization options are available for push button switches?
Many manufacturers offer customization options for push button switches, including different colors, sizes, illumination types, and actuator shapes. Some suppliers allow for branding on the switches, such as adding a logo or specific text. Discuss your customization needs with suppliers to understand the available options, lead times, and any associated costs. This is particularly valuable for creating a cohesive product line that aligns with your brand identity. -
What are the minimum order quantities (MOQs) for push button switches?
Minimum order quantities can vary significantly by supplier and product type. While some manufacturers may have an MOQ of 100 units, others may offer lower or higher thresholds depending on the customization level and production costs. It’s advisable to communicate directly with suppliers regarding their MOQs, especially if you are considering sourcing from international markets, as this can affect your overall budgeting and logistics.
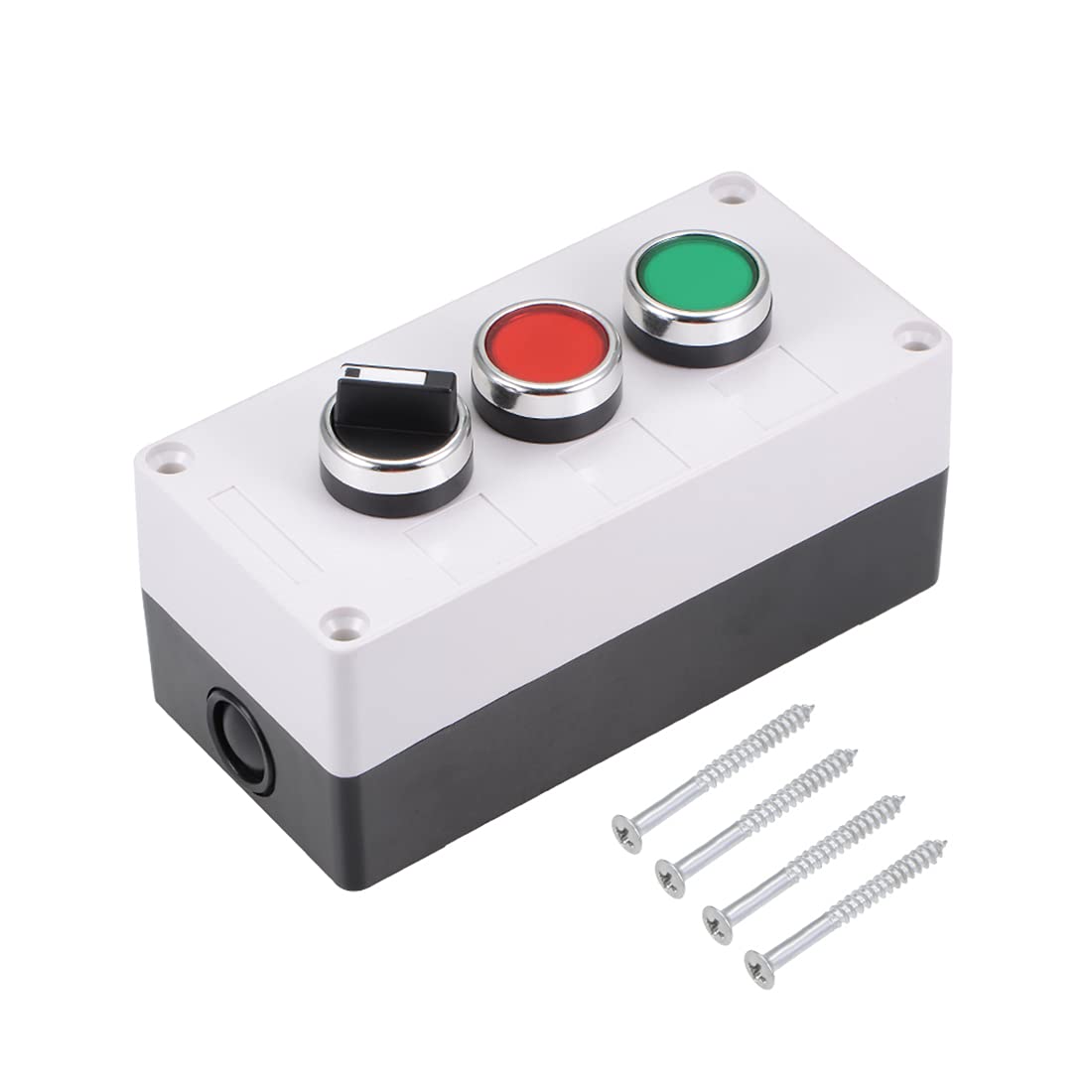
A stock image related to switch button push.
-
How can I vet suppliers for push button switches?
To vet suppliers, start by checking their reputation through online reviews and industry references. Request certifications and compliance documentation to ensure their products meet international quality standards. Conduct video calls or site visits if possible, to assess their manufacturing capabilities and quality control processes. Additionally, consider their experience in exporting to your region, as familiarity with local regulations can ease the import process. -
What payment terms should I expect when sourcing push button switches internationally?
Payment terms can vary widely among suppliers. Common options include payment in advance, letters of credit, or net payment terms (e.g., 30 or 60 days after delivery). It’s essential to negotiate terms that protect your interests while ensuring the supplier feels secure. Be mindful of currency fluctuations and consider using escrow services for large orders to mitigate risks. -
What quality assurance measures should I look for in push button switches?
Quality assurance (QA) measures can include rigorous testing for durability, performance, and safety. Look for suppliers that conduct standard tests such as electrical performance, environmental exposure (temperature, humidity), and lifecycle testing. Request documentation of their QA processes, including any third-party certifications (like ISO 9001) that validate their commitment to quality. This ensures that the switches you receive will meet your operational requirements. -
What logistics considerations should I keep in mind when importing push button switches?
When importing push button switches, consider shipping methods, lead times, and customs regulations in your country. Choose a reliable freight forwarder familiar with electronic components to ensure compliance with international shipping standards. Additionally, factor in potential tariffs or duties that may apply to your order. Planning for these logistics aspects can prevent delays and additional costs, ensuring a smoother supply chain process.
Important Disclaimer & Terms of Use
⚠️ Important Disclaimer
The information provided in this guide, including content regarding manufacturers, technical specifications, and market analysis, is for informational and educational purposes only. It does not constitute professional procurement advice, financial advice, or legal advice.
While we have made every effort to ensure the accuracy and timeliness of the information, we are not responsible for any errors, omissions, or outdated information. Market conditions, company details, and technical standards are subject to change.
B2B buyers must conduct their own independent and thorough due diligence before making any purchasing decisions. This includes contacting suppliers directly, verifying certifications, requesting samples, and seeking professional consultation. The risk of relying on any information in this guide is borne solely by the reader.
Strategic Sourcing Conclusion and Outlook for switch button push
The landscape of strategic sourcing for push button switches presents a myriad of opportunities for international B2B buyers. Understanding the diverse applications—from industrial automation to consumer electronics—allows businesses in Africa, South America, the Middle East, and Europe to tailor their sourcing strategies effectively. By prioritizing quality and reliability, buyers can mitigate risks associated with supply chain disruptions and ensure product longevity.
The value of strategic sourcing lies not just in cost savings, but also in fostering strong relationships with suppliers who can provide innovative solutions and exceptional service. As the demand for customizable and energy-efficient switch solutions grows, companies should focus on suppliers who offer a range of products, including illuminated and sealed push button switches, to meet diverse needs.
Looking ahead, the market for push button switches is poised for growth, driven by advancements in technology and increasing automation across industries. Buyers are encouraged to leverage this momentum by exploring new partnerships and investing in high-quality components that enhance their product offerings. By doing so, they position themselves for success in an increasingly competitive global market.