Master the Art of Sourcing Granite CNC Machines for Maximum
Introduction: Navigating the Global Market for granite cnc machine
In the fast-evolving landscape of the global stone fabrication industry, the granite CNC machine stands out as a vital tool for precision and efficiency. As granite remains a sought-after material for countertops, monuments, and architectural features, understanding the capabilities of CNC technology is essential for businesses aiming to enhance their production quality and operational efficiency. This guide serves as a comprehensive resource for international B2B buyers, particularly those in Africa, South America, the Middle East, and Europe, including key markets such as the UAE and Argentina.
Navigating the complexities of sourcing granite CNC machines involves more than just understanding the technology; it requires insights into various machine types, material specifications, manufacturing processes, and quality control standards. This guide will cover critical topics such as machine types (CNC routers, bridge saws, waterjets), material selection, manufacturing and quality assurance practices, supplier evaluations, and cost considerations.
With a structured approach to frequently asked questions and market trends, this resource empowers buyers to make informed sourcing decisions. By leveraging the insights provided, businesses can enhance their competitiveness, streamline operations, and ultimately achieve greater profitability in the dynamic global market for granite CNC machines.
Understanding granite cnc machine Types and Variations
Type Name | Key Distinguishing Features | Primary B2B Applications | Brief Pros & Cons for Buyers |
---|---|---|---|
CNC Router | Versatile, suitable for softer stones, low cost | Decorative engraving, signage, countertops | Pros: Cost-effective; Cons: Limited to softer stones. |
CNC Bridge Saw | High precision, large cutting capacity | Slab cutting for countertops and tiles | Pros: Excellent for large slabs; Cons: Expensive maintenance. |
5-Axis CNC Machine | Multi-directional cutting, complex shapes | Artistic stone carving, intricate designs | Pros: High versatility; Cons: Requires skilled operators. |
CNC Waterjet | Uses high-pressure water for cutting | Custom shapes, intricate designs | Pros: Minimal heat damage; Cons: Slower cutting speed. |
CNC Stone Carving Machine | Specialized for detailed stone work | Monuments, custom sculptures | Pros: Highly detailed; Cons: Limited to specific tasks. |
CNC Router
CNC routers are popular for their versatility and affordability, making them a great entry-level option for businesses engaging in decorative engraving or countertop fabrication. They are typically designed for softer stones like marble and limestone, which limits their use with harder materials such as granite. Buyers should consider the machine’s spindle power and the software compatibility, as these factors will influence the quality and efficiency of the production process.
CNC Bridge Saw
CNC bridge saws are engineered for precision cutting of large stone slabs, making them essential in the granite fabrication industry. They provide high accuracy and can handle heavy materials, making them ideal for creating countertops and tiles. However, the initial investment and ongoing maintenance can be significant, so businesses should evaluate their production volume and financial capacity before purchasing.
5-Axis CNC Machine
The 5-axis CNC machine offers unparalleled versatility, allowing for complex cuts and intricate designs that are not possible with standard machines. This capability is particularly valuable for businesses focused on artistic stone carving or custom projects that require detailed engravings. While these machines can be more expensive and require skilled operators, the investment can lead to higher-quality products and greater customer satisfaction.
CNC Waterjet
CNC waterjet machines utilize high-pressure water to cut through stone, which is advantageous for creating custom shapes and intricate designs without generating heat that could damage the material. This technology is particularly useful in applications where precision is paramount. However, the cutting speed is generally slower compared to other machines, so buyers need to weigh the benefits of precision against the potential for longer production times.
CNC Stone Carving Machine
These machines are specifically designed for detailed stone carving, making them ideal for creating monuments and custom sculptures. They excel in producing intricate designs and can handle a variety of stone types. However, their specialization means they may not be as versatile as other CNC machines. Buyers should assess their specific needs for stone carving to determine if this machine aligns with their production capabilities and market demands.
Related Video: Work Holding Set-Up for Milling Operations – Basic Tutorial – SMITHY GRANITE 3-in-1
Key Industrial Applications of granite cnc machine
Industry/Sector | Specific Application of granite cnc machine | Value/Benefit for the Business | Key Sourcing Considerations for this Application |
---|---|---|---|
Construction | Precision cutting for architectural stone elements | Enhanced design flexibility and reduced waste | Machine rigidity, spindle power, and compatibility with CAD software |
Monument and Headstone | Custom engraving and shaping for memorial stones | Unique personalization options to meet client demands | Availability of diamond bits, cooling systems, and engraving software |
Interior Design | Fabrication of granite countertops and features | High-quality finishes and increased aesthetic appeal | Sourcing for reliable suppliers of granite and CNC machinery maintenance |
Stone Fabrication | Production of intricate stone carvings and sculptures | Artistic expression with precision and efficiency | Expertise in stone properties and machine calibration requirements |
Landscaping | Creation of decorative stone elements for gardens | Improved visual appeal and durability of outdoor spaces | Weather-resistant features and suitable tooling for outdoor applications |
Detailed Applications
Construction
In the construction industry, granite CNC machines are instrumental for cutting and shaping architectural stone elements such as facades, flooring, and countertops. These machines allow for precise cuts that enhance design flexibility while minimizing waste. Buyers in this sector should prioritize machines with high rigidity and sufficient spindle power to handle the hardness of granite. Additionally, compatibility with CAD software is crucial for seamless design integration, especially for international projects that may involve diverse architectural styles.
Monument and Headstone
Granite CNC machines play a vital role in the monument and headstone sector by enabling custom engraving and shaping. This capability allows businesses to offer personalized memorial stones, catering to specific client preferences. For B2B buyers, it is essential to ensure that the machines are equipped with diamond bits and efficient cooling systems to prevent overheating during the engraving process. Moreover, sourcing reliable engraving software can significantly enhance productivity and artistic output.
Interior Design
In the interior design field, granite CNC machines are used to fabricate high-quality countertops and decorative stone features. The precision offered by these machines results in superior finishes that significantly elevate the aesthetic appeal of residential and commercial spaces. Buyers should consider sourcing machines that provide robust maintenance support and access to reliable granite suppliers to ensure consistent quality in their products.
Stone Fabrication
Granite CNC machines are crucial in stone fabrication for producing intricate carvings and sculptures. These machines allow artisans to achieve artistic expression with remarkable precision and efficiency. International buyers should focus on sourcing machines that are calibrated for various stone properties and ensure that operators are trained in the nuances of CNC technology to maximize output quality and minimize errors.
Landscaping
In landscaping, granite CNC machines are utilized to create decorative stone elements that enhance the visual appeal of gardens and outdoor spaces. These machines can produce weather-resistant features that are not only attractive but also durable. When sourcing for this application, buyers should look for machines with suitable tooling for outdoor conditions and consider the machine’s adaptability to various stone types to meet diverse landscaping needs.
Related Video: CNC machine made out of granite – part1
Strategic Material Selection Guide for granite cnc machine
When selecting materials for granite CNC machines, it is essential to consider their properties, advantages, disadvantages, and the specific needs of international B2B buyers. Here, we analyze four common materials used in the manufacturing and operation of granite CNC machines.
1. Steel
Key Properties: Steel is known for its high tensile strength and durability. It can withstand significant pressure and is resistant to deformation under load. However, it can be prone to corrosion if not properly treated.
Pros & Cons: Steel is relatively cost-effective and can be easily sourced globally. Its high strength makes it suitable for heavy-duty applications. On the downside, untreated steel can rust, necessitating protective coatings, which can increase manufacturing complexity and costs.
Impact on Application: Steel components are often used in the frame and structural elements of CNC machines. The material’s strength ensures stability during operation, which is crucial for precision cutting.
Considerations for International Buyers: Buyers from regions like the Middle East and Africa should ensure compliance with local standards (e.g., ASTM A36 for structural steel) and consider the availability of treated steel to prevent corrosion in humid environments.
2. Aluminum
Key Properties: Aluminum is lightweight and has excellent corrosion resistance. It can withstand moderate temperatures and pressures, making it suitable for various applications in CNC machines.
Pros & Cons: The lightweight nature of aluminum allows for easier handling and installation. Additionally, it is resistant to oxidation, which enhances its durability. However, aluminum is generally less strong than steel, which may limit its use in high-load applications.
Impact on Application: Aluminum is often used in components such as machine housings and support structures. Its lightweight property can improve the machine’s mobility and ease of installation, especially in settings where space is a constraint.
Considerations for International Buyers: Buyers in Europe may prefer aluminum due to its lightweight properties, which can reduce shipping costs. Compliance with European standards (e.g., EN 573 for aluminum alloys) is also crucial.
3. Cast Iron
Key Properties: Cast iron is known for its exceptional vibration dampening properties and high compressive strength. It can withstand high temperatures and is generally resistant to wear.
Pros & Cons: The durability and stability of cast iron make it ideal for precision machining applications. However, it is heavier than other materials, which can complicate transportation and installation. Additionally, cast iron can be brittle, making it susceptible to cracking under extreme stress.
Impact on Application: Cast iron is often used in the base and bed of CNC machines, providing a stable platform for precision cutting. Its ability to absorb vibrations enhances the machine’s accuracy.
Considerations for International Buyers: Buyers from South America should be aware of the availability of cast iron and its compliance with local standards (e.g., ASTM A48). The weight of cast iron may also impact shipping logistics.
4. Composite Materials
Key Properties: Composite materials, such as fiberglass or carbon fiber, offer a combination of lightweight and high strength. They are resistant to corrosion and can withstand varying temperatures.
Pros & Cons: Composites are highly customizable, allowing for specific engineering requirements. They are also resistant to chemical damage, making them suitable for various environments. However, the manufacturing process can be complex and costly.
Impact on Application: Composites are often used in specialized components where weight reduction is critical, such as in moving parts of CNC machines. Their strength-to-weight ratio can enhance machine performance.
Considerations for International Buyers: Buyers from regions with advanced manufacturing capabilities (like Europe) may find composites more accessible. Compliance with industry standards (e.g., ASTM D3039 for composite materials) is essential for quality assurance.
Summary Table
Material | Typical Use Case for granite cnc machine | Key Advantage | Key Disadvantage/Limitation | Relative Cost (Low/Med/High) |
---|---|---|---|---|
Steel | Structural components | High strength and durability | Prone to corrosion | Medium |
Aluminum | Machine housings and support structures | Lightweight and corrosion-resistant | Less strong than steel | Medium |
Cast Iron | Base and bed of CNC machines | Excellent vibration dampening | Heavy and brittle | Medium |
Composite Materials | Specialized components | Lightweight and customizable | Complex and costly manufacturing | High |
This analysis provides international B2B buyers with a comprehensive understanding of material options for granite CNC machines, emphasizing the importance of selecting the right material based on specific operational needs and regional considerations.
In-depth Look: Manufacturing Processes and Quality Assurance for granite cnc machine
Manufacturing Processes for Granite CNC Machines
The manufacturing process for granite CNC machines is intricate and involves several key stages to ensure quality, precision, and durability. Understanding these stages can help international B2B buyers make informed decisions when selecting suppliers.
1. Material Preparation
The first stage of manufacturing granite CNC machines begins with the selection and preparation of materials. High-quality steel and aluminum are typically chosen for the machine’s structural components due to their strength and rigidity.
- Material Selection: Buyers should look for suppliers that utilize high-grade materials to enhance durability and performance.
- Cutting and Shaping: Raw materials are cut and shaped using advanced CNC cutting tools. This ensures that components meet precise specifications necessary for assembly.
2. Forming
Once the materials are prepared, the next step is forming the components of the CNC machine.
- Welding and Joining: For structural components, techniques such as MIG or TIG welding are employed to create a robust framework. This is critical for maintaining the machine’s stability during operation.
- Machining: Parts are machined using CNC lathes and milling machines to achieve the desired dimensions and tolerances. This stage is vital for ensuring that all components fit together seamlessly.
3. Assembly
After the components are formed, they move to the assembly stage.
- Sub-Assembly: Various parts, such as the spindle, axis drives, and cooling systems, are assembled separately before final assembly. This helps in identifying potential issues early in the process.
- Final Assembly: The complete machine is assembled, integrating all sub-assemblies. It is crucial that this stage is performed in a controlled environment to prevent contamination and ensure precision.
4. Finishing
The finishing stage enhances the machine’s functionality and aesthetics.
- Surface Treatment: Components undergo surface treatments such as anodizing or powder coating to improve corrosion resistance and durability.
- Quality Checks: After finishing, each machine goes through rigorous quality checks before it is deemed ready for shipment.
Quality Assurance Standards
Quality assurance (QA) is critical in the manufacturing of granite CNC machines, ensuring that the machines meet international standards and perform reliably.
International Standards
- ISO 9001: This is a globally recognized standard for quality management systems. Suppliers should be certified to ISO 9001, ensuring they have processes in place for consistent quality.
- CE Marking: For European markets, CE marking indicates compliance with health, safety, and environmental protection standards. Buyers should verify that machines are CE certified.
- API Standards: For specific applications in industries like oil and gas, compliance with API standards may be required.
Quality Control Checkpoints
Quality control (QC) checkpoints are integral to the manufacturing process, ensuring that each stage meets specified criteria.
- Incoming Quality Control (IQC): This involves inspecting raw materials upon arrival to confirm they meet the required specifications.
- In-Process Quality Control (IPQC): Regular checks during the manufacturing process help catch defects early. This includes monitoring machining tolerances and assembly alignment.
- Final Quality Control (FQC): Before shipping, machines undergo a comprehensive final inspection, including functional testing, to ensure they operate correctly.
Common Testing Methods
Testing methods play a vital role in verifying the quality of granite CNC machines.
- Functional Testing: Machines are operated under various conditions to ensure they perform as expected. This may include running the machine with actual granite material to test cutting precision.
- Non-Destructive Testing (NDT): Techniques such as ultrasonic testing or dye penetrant inspection can be employed to detect internal flaws without damaging the components.
- Thermal Imaging: This method checks for overheating issues during operation, which can indicate potential mechanical failures.
Verifying Supplier Quality Control
B2B buyers can take several steps to verify the quality control measures of potential suppliers:
- Supplier Audits: Conducting on-site audits allows buyers to assess the supplier’s manufacturing processes and quality control systems directly. This is particularly important for international buyers who may not be familiar with local practices.
- Requesting Quality Reports: Buyers should ask for detailed QC reports that document the results of testing and inspections throughout the manufacturing process.
- Third-Party Inspections: Engaging third-party inspection services can provide an unbiased assessment of the machine’s quality before shipment. This is especially crucial for large investments.
Quality Control Nuances for International Buyers
When sourcing granite CNC machines from suppliers in different regions, international buyers must be aware of specific nuances:
- Cultural Differences: Different regions may have varying standards and practices in manufacturing. Understanding these can help buyers navigate negotiations and expectations.
- Compliance with Local Regulations: Buyers must ensure that machines comply with local regulations in their respective countries, which may differ from the supplier’s country.
- Communication Barriers: Language differences can complicate negotiations and quality verification processes. Clear communication is essential to ensure all specifications are understood and met.
Conclusion
Understanding the manufacturing processes and quality assurance practices for granite CNC machines is crucial for international B2B buyers. By focusing on material preparation, forming, assembly, and finishing, along with robust quality control measures, buyers can ensure they invest in reliable and high-performing machines. Engaging with suppliers who adhere to international standards and demonstrating transparency in their QC processes will further enhance the buyer’s confidence in their purchasing decisions.
Related Video: Epoxy granite cnc mill toolchanger explained
Comprehensive Cost and Pricing Analysis for granite cnc machine Sourcing
When sourcing granite CNC machines, understanding the comprehensive cost structure is crucial for international B2B buyers. This analysis will help identify the key components that contribute to the overall pricing, as well as the factors influencing these costs.
Cost Components
-
Materials: The primary material cost is associated with the components of the CNC machine itself, including high-quality steel for the frame, electronic parts, and specialized cutting tools. Granite CNC machines often utilize diamond-tipped bits for cutting, which can significantly increase the initial material cost.
-
Labor: Labor costs can vary widely based on geographic location and the skill level required for assembly and operation. In regions with higher labor costs, such as parts of Europe, this can lead to a notable increase in the overall price of the machine.
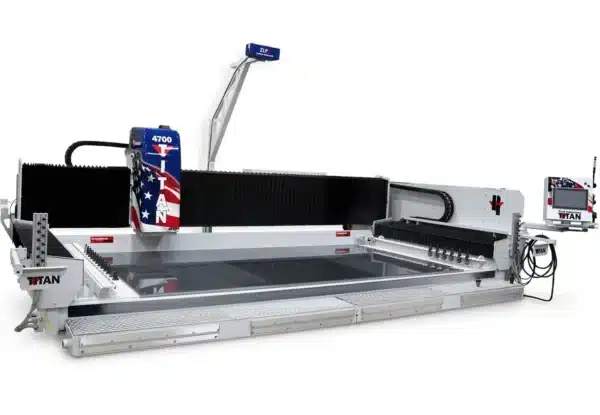
Illustrative Image (Source: Google Search)
-
Manufacturing Overhead: This includes expenses related to factory operations, utilities, and equipment maintenance. Buyers should consider how the supplier’s production efficiencies can impact pricing.
-
Tooling: The cost of tooling, including special fixtures and jigs needed for specific operations, can add to the initial investment. Custom tooling may be necessary for complex designs, which can further escalate costs.
-
Quality Control (QC): Implementing rigorous QC measures ensures that machines meet the required specifications and performance standards. While this may add to the upfront costs, it can prevent more significant expenses due to machine failures or defects later.
-
Logistics: Shipping costs can vary based on the machine’s size, weight, and distance from the supplier. Consideration of import duties, taxes, and insurance is essential for calculating the total logistics cost.
-
Margin: Suppliers typically include a profit margin in their pricing. Understanding the standard margins in different markets can aid in negotiations.
Price Influencers
Several factors can influence the pricing of granite CNC machines:
-
Volume/MOQ: Purchasing in bulk can often lead to discounts. Understanding the minimum order quantities (MOQs) can help buyers negotiate better pricing.
-
Specifications/Customization: Custom machines tailored to specific needs will typically cost more. Buyers should weigh the benefits of customization against the additional costs.
-
Materials: The choice of materials can drastically affect pricing. For example, opting for higher-grade components can ensure better performance but will increase costs.
-
Quality/Certifications: Machines that meet international quality standards (e.g., ISO certifications) may come at a premium. However, these certifications can provide assurance of reliability and performance.
-
Supplier Factors: The reputation and reliability of the supplier can impact pricing. Established suppliers may charge more due to their proven track record.
-
Incoterms: Understanding the terms of shipment (e.g., FOB, CIF) is crucial for pricing. These terms dictate who bears the cost and risk at different points in the shipping process.
Buyer Tips
-
Negotiation: Always be prepared to negotiate pricing. Suppliers may have room to adjust their prices based on volume, payment terms, and long-term partnership potential.
-
Cost-Efficiency: Look for opportunities to optimize costs through supplier relationships or by exploring alternative materials that meet performance requirements at lower prices.
-
Total Cost of Ownership (TCO): Consider not just the purchase price but also the long-term costs associated with maintenance, operation, and potential downtime.
-
Pricing Nuances: International buyers, particularly from regions like Africa, South America, the Middle East, and Europe, should be aware of currency fluctuations and how they can affect pricing. Additionally, differences in local regulations can impact costs.
Disclaimer
Prices can vary widely based on market conditions, supplier terms, and specific machine configurations. This analysis provides a framework for understanding potential costs but does not guarantee pricing accuracy. Always request detailed quotes from multiple suppliers for the most accurate estimates.
Spotlight on Potential granite cnc machine Manufacturers and Suppliers
This section looks at several manufacturers active in the ‘granite cnc machine’ market. This is a representative sample for illustrative purposes; B2B buyers must conduct extensive due diligence before any transaction. Information is synthesized from public sources and general industry knowledge.
Essential Technical Properties and Trade Terminology for granite cnc machine
Key Technical Properties of Granite CNC Machines
When considering a granite CNC machine, it’s essential to understand the critical technical properties that influence performance and suitability for specific applications. Here are several vital specifications to consider:
-
Spindle Power
Spindle power, typically measured in kilowatts (KW), indicates the machine’s ability to cut through hard materials like granite. A spindle power of 2.5 KW or higher is generally recommended for effective granite cutting. This specification is crucial for ensuring the machine can handle the material’s hardness without overheating or stalling. -
Machine Rigidity
Rigidity refers to the machine’s structural stability during operation. A rigid machine minimizes vibrations and maintains precision during cutting and engraving. This property is vital for producing high-quality finishes, particularly in intricate designs. Machines with a robust frame often lead to reduced wear and tear, translating into lower maintenance costs.
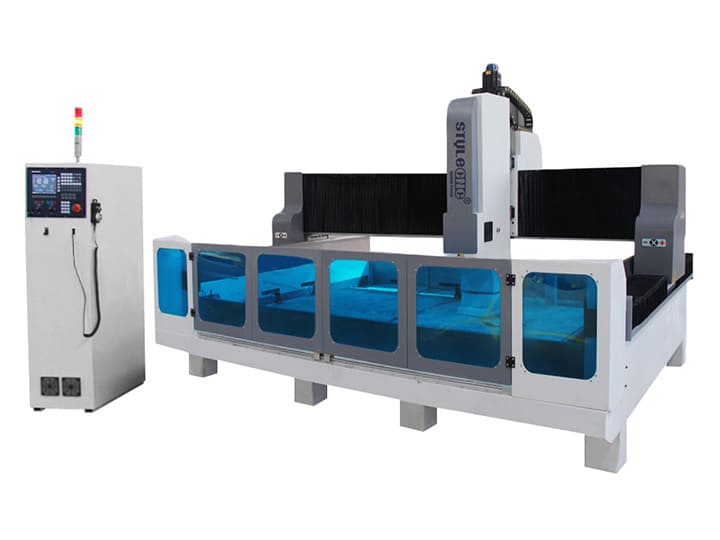
Illustrative Image (Source: Google Search)
-
Cooling System
Given the heat generated during cutting, an efficient cooling system—often water-based—is necessary to prevent the overheating of both the material and the cutting tool. This property not only prolongs the life of the machine and tools but also ensures consistent cutting quality by reducing the risk of thermal damage to the granite. -
Tool Compatibility
The compatibility of the machine with various cutting tools, especially diamond or tungsten carbide bits, is a key factor. Machines that can accommodate a range of tools allow for versatility in operations, from rough cutting to detailed engraving. This property is essential for businesses looking to expand their service offerings without investing in multiple machines. -
Tolerance Levels
Tolerance refers to the permissible limit or limits of variation in a physical dimension. For granite CNC machines, tight tolerances (often within ±0.1 mm) are critical for projects requiring high precision, such as architectural elements or custom countertops. Understanding tolerance levels helps buyers gauge the machine’s capability to meet specific project requirements.
Common Trade Terminology in the Granite CNC Machine Industry
Familiarity with industry terminology is vital for effective communication and negotiation in the B2B space. Here are several common terms that buyers should understand:
-
OEM (Original Equipment Manufacturer)
An OEM refers to a company that produces parts and equipment that may be marketed by another manufacturer. In the context of granite CNC machines, knowing the OEM can help buyers assess the quality and reliability of the machinery and its components. -
MOQ (Minimum Order Quantity)
This term indicates the smallest quantity of a product that a supplier is willing to sell. Understanding MOQs is crucial for buyers, especially when assessing inventory needs and negotiating costs. Lower MOQs can facilitate easier entry into new markets or product lines. -
RFQ (Request for Quotation)
An RFQ is a document that a buyer sends to suppliers to solicit pricing and other details for specific products or services. Buyers should use RFQs to gather comparative pricing and terms, ensuring they receive the best offers from multiple suppliers. -
Incoterms (International Commercial Terms)
These are a set of predefined international trade terms published by the International Chamber of Commerce (ICC) that are widely used in international commercial transactions. Understanding Incoterms helps buyers clarify responsibilities regarding shipping, insurance, and tariffs, which can significantly impact overall project costs. -
Lead Time
Lead time refers to the time taken from placing an order to receiving the product. In the context of CNC machines, understanding lead times is essential for project planning and ensuring timely delivery, especially in industries with tight deadlines. -
Warranty Period
This term refers to the duration during which the manufacturer is responsible for repairs or replacements due to defects. Knowing the warranty period is important for buyers to assess long-term maintenance costs and the reliability of the machine.
Understanding these technical specifications and trade terminologies is essential for B2B buyers in making informed decisions when investing in granite CNC machines. By focusing on these elements, businesses can enhance their operational efficiency and ensure successful project outcomes.
Navigating Market Dynamics, Sourcing Trends, and Sustainability in the granite cnc machine Sector
Market Overview & Key Trends
The global market for granite CNC machines is experiencing robust growth, driven by the increasing demand for precision stone cutting in various applications, including construction, monument fabrication, and interior design. Key drivers include the rising popularity of granite as a high-quality material for countertops and architectural features, which has led to a surge in investments in CNC technology for enhanced efficiency and output quality. International B2B buyers, particularly from regions like Africa, South America, the Middle East, and Europe, are increasingly recognizing the value of advanced CNC machines in meeting the demand for custom stone products.
Emerging trends in this sector include the integration of advanced technologies such as Artificial Intelligence (AI) and the Internet of Things (IoT), which enhance machine capabilities through predictive maintenance and real-time monitoring. These innovations not only improve operational efficiency but also reduce downtime, a critical factor for businesses in competitive markets. Additionally, the rise of e-commerce platforms is facilitating easier access to suppliers, enabling buyers to source machines and parts directly from manufacturers worldwide.
Moreover, sustainability is becoming a pivotal consideration in the purchasing decisions of international buyers. As environmental awareness grows, there is a noticeable shift towards sourcing machines that utilize energy-efficient processes and materials, reflecting a broader commitment to sustainable practices within the industry. This trend is particularly strong in Europe, where regulatory frameworks increasingly emphasize environmental standards.
Sustainability & Ethical Sourcing in B2B
The environmental impact of granite CNC machining is significant, particularly concerning energy consumption and waste generation. As a result, sustainability is a critical factor for B2B buyers who are looking to align their sourcing practices with global environmental standards. Ethical sourcing has emerged as a key priority, with buyers increasingly seeking suppliers who demonstrate a commitment to sustainable practices.
Implementing environmentally friendly processes includes utilizing machines that consume less energy, incorporating water recycling systems during cutting, and reducing waste through optimized cutting patterns. Furthermore, many companies are seeking materials that are certified as ‘green’ or environmentally friendly, ensuring that their supply chains are not only efficient but also responsible.
Certifications such as ISO 14001 for environmental management and adherence to the Global Reporting Initiative (GRI) standards can enhance supplier credibility. Buyers should prioritize partnerships with manufacturers that provide transparency regarding their sourcing practices and offer products made from recycled or sustainably sourced materials. This approach not only helps in meeting regulatory requirements but also enhances brand reputation and customer loyalty in increasingly eco-conscious markets.
Brief Evolution/History
The evolution of CNC machines for granite processing dates back to the late 20th century, coinciding with advancements in computer technology. Initially, stone cutting was a labor-intensive process that relied heavily on manual tools. The introduction of CNC technology revolutionized the industry, allowing for higher precision and efficiency in stone fabrication.
Over the years, the technology has continued to advance, with improvements in machine design, software capabilities, and cutting tools. Today, granite CNC machines feature sophisticated automation, enabling complex designs and reducing production times significantly. As the market continues to grow, the focus is shifting towards integrating sustainable practices and innovative technologies, ensuring that the industry remains competitive and environmentally responsible.
Related Video: International Trade 101 | Economics Explained
Frequently Asked Questions (FAQs) for B2B Buyers of granite cnc machine
-
How can I effectively vet suppliers for granite CNC machines?
Vetting suppliers is crucial to ensure quality and reliability. Start by reviewing their company history and customer feedback, focusing on international trade experience. Request references from other B2B buyers in your region, especially those who have sourced similar machinery. Evaluate their certifications, such as ISO or CE, which indicate compliance with international standards. Additionally, consider conducting an on-site visit if possible, or use third-party inspection services to assess their manufacturing capabilities and quality control processes. -
Can I customize granite CNC machines according to my specific needs?
Many suppliers offer customization options for granite CNC machines to meet specific operational requirements. When discussing customization, clarify your needs regarding size, tooling, software compatibility, and additional features. Ensure that the supplier has the engineering capacity to execute these modifications. Request detailed documentation of the customization process, including timelines and costs, to avoid surprises during production. This will help ensure the final product aligns with your operational goals and enhances efficiency. -
What are the typical minimum order quantities (MOQ) and lead times for granite CNC machines?
Minimum order quantities and lead times can vary significantly between suppliers. Generally, MOQs may range from one machine to several units, depending on the manufacturer’s production capacity and business model. Lead times typically span from 4 to 12 weeks, influenced by factors such as customization, material availability, and shipping logistics. Always confirm these details upfront and factor in potential delays in international shipping, especially in regions with varying customs regulations. -
What payment terms should I expect when purchasing a granite CNC machine?
Payment terms can vary widely among suppliers, but common practices include a deposit (usually 30-50%) at the time of order, with the balance due before shipping. Some suppliers may offer financing options or extended payment terms for larger orders. It is advisable to negotiate terms that align with your cash flow needs while ensuring security. Using letters of credit or escrow services can provide additional protection against potential disputes, especially in international transactions. -
What quality assurance measures and certifications should I look for?
Quality assurance is paramount when sourcing granite CNC machines. Look for suppliers that adhere to recognized quality standards, such as ISO 9001, which ensures consistent quality management practices. Request documentation of quality control processes, including testing and inspection protocols. Additionally, inquire about warranties and after-sales support, as these can be indicators of the supplier’s commitment to product quality and customer satisfaction. -
How should I manage logistics for importing granite CNC machines?
Managing logistics requires careful planning and coordination. Engage with a freight forwarder experienced in handling machinery to navigate customs regulations and shipping logistics effectively. Assess shipping options, such as air freight for speed or sea freight for cost-effectiveness. Ensure that all necessary import permits and documentation are in order to avoid delays. Additionally, consider insurance coverage for the equipment during transit to mitigate risks associated with damage or loss. -
What steps should I take to resolve disputes with suppliers?
Dispute resolution should be addressed proactively in your contract with the supplier. Clearly outline terms regarding quality, delivery, and payment conditions. If issues arise, initiate communication promptly to discuss concerns and seek a resolution. Utilize mediation or arbitration as alternative dispute resolution methods, as they can be less costly and time-consuming than litigation. Having legal counsel familiar with international trade can also be beneficial in navigating complex disputes. -
What are the common challenges faced when sourcing granite CNC machines internationally?
Sourcing granite CNC machines internationally presents several challenges, including language barriers, cultural differences, and varying regulations across countries. Additionally, differences in quality standards can complicate the procurement process. To mitigate these challenges, conduct thorough research on the supplier’s background and ensure clear communication throughout the procurement process. Collaborating with local partners or consultants who understand the regional market can also facilitate smoother transactions and help navigate potential pitfalls.
Important Disclaimer & Terms of Use
⚠️ Important Disclaimer
The information provided in this guide, including content regarding manufacturers, technical specifications, and market analysis, is for informational and educational purposes only. It does not constitute professional procurement advice, financial advice, or legal advice.
While we have made every effort to ensure the accuracy and timeliness of the information, we are not responsible for any errors, omissions, or outdated information. Market conditions, company details, and technical standards are subject to change.
B2B buyers must conduct their own independent and thorough due diligence before making any purchasing decisions. This includes contacting suppliers directly, verifying certifications, requesting samples, and seeking professional consultation. The risk of relying on any information in this guide is borne solely by the reader.
Strategic Sourcing Conclusion and Outlook for granite cnc machine
In conclusion, the strategic sourcing of granite CNC machines presents a valuable opportunity for B2B buyers across Africa, South America, the Middle East, and Europe. As granite remains a sought-after material for construction and design, understanding the capabilities and specifications of CNC technology is crucial. Key takeaways include the importance of selecting machines with robust features such as high spindle power, effective cooling systems, and compatibility with advanced CAD/CAM software.
Investing in the right CNC machinery not only enhances operational efficiency but also ensures precision and quality in granite fabrication, ultimately leading to better customer satisfaction. As the global market continues to evolve, international buyers should remain proactive in sourcing advanced equipment that meets their specific needs while considering local market dynamics.
Looking ahead, it is essential for businesses to forge strong partnerships with reputable suppliers and manufacturers to stay competitive. By prioritizing strategic sourcing practices, companies can leverage technological advancements to propel growth and innovation in their operations. Engage with trusted vendors today to transform your granite processing capabilities and seize emerging opportunities in the marketplace.