Master the Cost of a CNC Machine: Your Essential B2B
Introduction: Navigating the Global Market for cost of a cnc machine
In today’s competitive manufacturing landscape, understanding the cost of a CNC machine is paramount for international B2B buyers. As industries across Africa, South America, the Middle East, and Europe strive for efficiency and precision, the investment in CNC technology can significantly influence operational success. This guide delves into the multifaceted world of CNC machines, offering insights that will empower your sourcing decisions and enhance your competitive edge.
The scope of this guide encompasses a variety of essential topics. It will explore the different types of CNC machines, highlighting their specific applications and advantages. We will examine the materials commonly used in CNC machining, ensuring that buyers understand the implications of material selection on cost and performance. Additionally, insights into manufacturing and quality control processes will help buyers assess supplier capabilities and reliability.
Moreover, we will provide an overview of suppliers and market dynamics to facilitate informed vendor selection. The focus on cost factors will enable buyers to evaluate their budgetary constraints against the value provided by various CNC machine options. Finally, a comprehensive FAQ section will address common queries and concerns that arise during the purchasing process.
By equipping you with this knowledge, this guide aims to streamline your procurement process, ensuring that you make well-informed investments that align with your business objectives. Whether you are based in Saudi Arabia, Nigeria, or anywhere in between, understanding the cost of CNC machines is vital for driving efficiency and growth in your operations.
Understanding cost of a cnc machine Types and Variations
Type Name | Key Distinguishing Features | Primary B2B Applications | Brief Pros & Cons for Buyers |
---|---|---|---|
Router CNC Machines | High-speed cutting, versatile materials handling | Woodworking, signage, prototyping | Pros: Affordable, easy to use. Cons: Limited precision compared to others. |
Lathe CNC Machines | Rotational cutting, ideal for cylindrical parts | Aerospace, automotive, metalworking | Pros: High precision, excellent for complex shapes. Cons: Higher cost, requires skilled operators. |
Plasma CNC Machines | Uses plasma cutting for metals | Metal fabrication, construction | Pros: Fast cutting speed, effective for thick materials. Cons: Limited to conductive materials. |
Laser CNC Machines | Uses laser technology for cutting and engraving | Electronics, jewelry, aerospace | Pros: High precision, minimal material waste. Cons: High initial investment, maintenance costs. |
Waterjet CNC Machines | Uses high-pressure water jets for cutting | Aerospace, automotive, stone cutting | Pros: Can cut a wide range of materials, no heat-affected zone. Cons: Slower cutting speed, higher operational costs. |
Router CNC Machines
Router CNC machines are characterized by their ability to cut a variety of materials at high speeds, making them ideal for applications in woodworking, signage, and prototyping. They are particularly suitable for businesses looking for an affordable entry point into CNC machining. Buyers should consider the machine’s ease of use and maintenance, as well as the availability of software and support. While they offer versatility, the trade-off is a lack of precision compared to more advanced CNC types.
Lathe CNC Machines
Lathe CNC machines excel in producing cylindrical parts through rotational cutting. They are widely used in industries such as aerospace, automotive, and metalworking, where precision is paramount. Buyers should evaluate the machine’s capabilities in handling various materials and the cost of skilled operators needed for operation. While the investment may be higher, the precision and ability to create complex shapes often justify the cost for B2B buyers focused on high-quality output.
Plasma CNC Machines
Plasma CNC machines utilize a plasma cutting process, making them particularly effective for metal fabrication and construction. They are known for their fast cutting speeds, which can significantly enhance productivity. However, buyers should note that these machines are limited to conductive materials. When considering a purchase, businesses must weigh the benefits of speed against the potential need for additional equipment for non-conductive materials.
Laser CNC Machines
Laser CNC machines are renowned for their high precision and minimal material waste, making them ideal for applications in electronics, jewelry, and aerospace. The cutting process is clean and efficient, but the initial investment can be substantial. B2B buyers should assess their production needs and the long-term operational costs associated with maintenance and material compatibility. While the upfront costs are higher, the potential for high-quality results can lead to greater profitability.
Waterjet CNC Machines
Waterjet CNC machines use high-pressure water jets to cut a wide range of materials, including metals, stone, and composites. They are particularly advantageous for industries like aerospace and automotive due to their ability to cut without creating a heat-affected zone, preserving material integrity. However, they may operate at slower speeds and incur higher operational costs. Buyers should consider their specific material needs and the potential for slower production times when evaluating this option.
Related Video: Best CNC Router Machine for Beginners in 2024 | Top 5 | Cut/Engraving
Key Industrial Applications of cost of a cnc machine
Industry/Sector | Specific Application of cost of a cnc machine | Value/Benefit for the Business | Key Sourcing Considerations for this Application |
---|---|---|---|
Aerospace | Precision component manufacturing | High accuracy and reduced waste | Certification standards, supplier reliability, and support services |
Automotive | Custom part production | Enhanced efficiency and lower production costs | Material compatibility, lead times, and local regulations |
Electronics | PCB fabrication and assembly | Improved precision and scalability | Technology integration, quality assurance processes, and cost-effectiveness |
Metal Fabrication | Structural component cutting and shaping | Increased production speed and flexibility | Machine durability, maintenance availability, and energy efficiency |
Furniture Manufacturing | Custom furniture design and production | Unique offerings and reduced labor costs | Design software compatibility, supplier location, and logistics |
Aerospace
In the aerospace industry, CNC machines are vital for producing precision components such as turbine blades and fuselage parts. These machines enable manufacturers to maintain tight tolerances, which is crucial for safety and performance. For international buyers, especially in regions like the Middle East and Europe, sourcing CNC machines that meet strict certification standards can be challenging. It’s essential to consider suppliers who can provide robust support services and demonstrate proven reliability in high-stakes environments.
Automotive
CNC machines play a significant role in the automotive sector, particularly for the production of custom parts and prototypes. By leveraging CNC technology, manufacturers can achieve enhanced efficiency and significantly lower production costs through automation. Buyers from Africa and South America should prioritize sourcing machines that are compatible with various materials and can meet local regulations. Additionally, understanding lead times and supplier reliability is crucial for maintaining production schedules.
Electronics
In electronics manufacturing, CNC machines are extensively used for PCB fabrication and assembly. The precision offered by CNC technology allows for the production of complex circuit boards that are essential for modern electronic devices. International buyers must focus on sourcing machines that integrate seamlessly with existing technology and adhere to rigorous quality assurance processes. Cost-effectiveness is also a key consideration, as margins in electronics can be tight.
Metal Fabrication
CNC machines are indispensable in the metal fabrication industry for cutting and shaping structural components. They facilitate increased production speed and flexibility, allowing businesses to respond quickly to market demands. For buyers, especially those in Europe and the Middle East, it’s important to evaluate the durability of machines and the availability of maintenance services. Energy efficiency is another critical factor, as it can significantly impact operational costs.
Furniture Manufacturing
In the furniture sector, CNC machines enable custom design and production, allowing manufacturers to create unique pieces that stand out in a competitive market. This technology not only reduces labor costs but also enhances design capabilities. Buyers from South America and Africa should consider the compatibility of CNC machines with design software, the location of suppliers for logistical efficiency, and the overall cost implications of sourcing these machines.
Related Video: CNC Machine For Large Gear Manufacturing | Most Modern Technology For Large Milling & Turning Center
Strategic Material Selection Guide for cost of a cnc machine
When selecting materials for CNC machines, it is crucial for international B2B buyers to consider the properties, advantages, and limitations of each material. This decision directly impacts the machine’s performance, durability, and overall cost. Below, we analyze four common materials used in CNC machining, focusing on their key properties, pros and cons, application impacts, and specific considerations for buyers from Africa, South America, the Middle East, and Europe.
1. Aluminum Alloys
Key Properties:
Aluminum alloys are lightweight, have excellent corrosion resistance, and can withstand moderate temperatures. They are often rated for pressures up to 300 psi, making them suitable for various applications.
Pros & Cons:
The primary advantage of aluminum alloys is their low weight and ease of machining, which reduces manufacturing complexity and costs. However, they may not be as durable as other materials like steel, particularly under high-stress conditions.
Impact on Application:
Aluminum is compatible with a wide range of media, making it ideal for applications in aerospace, automotive, and consumer products. Its lightweight nature enhances performance in applications where weight is a critical factor.
Considerations for International Buyers:
Buyers should ensure compliance with international standards such as ASTM and DIN. In regions like the Middle East and Africa, sourcing aluminum may be easier due to local suppliers, but it is essential to verify material quality to avoid substandard products.
2. Stainless Steel
Key Properties:
Stainless steel is known for its high strength, excellent corrosion resistance, and ability to withstand high temperatures and pressures. It typically performs well in environments where chemical exposure is a concern.
Pros & Cons:
The key advantage of stainless steel is its durability and resistance to wear and tear, making it suitable for long-term applications. However, it is more expensive than aluminum and can be more challenging to machine, which increases manufacturing complexity.
Impact on Application:
Due to its corrosion resistance, stainless steel is ideal for applications in the food and pharmaceutical industries, where hygiene is paramount. It is also suitable for high-stress environments, such as in oil and gas applications.
Considerations for International Buyers:
Buyers must consider the specific grade of stainless steel required for their applications, as different grades offer varying levels of corrosion resistance. Compliance with standards such as JIS and ASTM is crucial, especially in Europe and South America, where regulations may be stricter.
3. Carbon Steel
Key Properties:
Carbon steel is characterized by its high strength and hardness, making it suitable for high-stress applications. It can withstand significant pressure but is less resistant to corrosion compared to stainless steel.
Pros & Cons:
The main advantage of carbon steel is its cost-effectiveness and high durability in structural applications. However, its susceptibility to rust and corrosion necessitates protective coatings, which can add to the overall cost and complexity.
Impact on Application:
Carbon steel is commonly used in construction and heavy machinery applications. Its strength makes it suitable for components that require high load-bearing capabilities.
Considerations for International Buyers:
Buyers in regions like Africa and the Middle East should be aware of local environmental conditions that may affect carbon steel’s performance, such as humidity and exposure to corrosive elements. Ensuring proper coatings and treatments is essential to maintain durability.
4. Plastics (e.g., Polycarbonate, Nylon)
Key Properties:
Plastics like polycarbonate and nylon are lightweight, resistant to impact, and can handle moderate temperatures. They are not as strong as metals but offer excellent corrosion resistance.
Pros & Cons:
The key advantage of plastics is their versatility and lower cost compared to metals. However, they may not be suitable for high-stress applications and can degrade under extreme temperatures.
Impact on Application:
Plastics are ideal for applications requiring lightweight components, such as in consumer electronics or automotive interiors. Their resistance to chemicals makes them suitable for specific industrial applications.
Considerations for International Buyers:
Buyers should evaluate the specific type of plastic required for their applications, as different plastics have varying properties. Compliance with environmental regulations, particularly in Europe, is essential, as there may be restrictions on certain plastic materials.
Summary Table
Material | Typical Use Case for cost of a cnc machine | Key Advantage | Key Disadvantage/Limitation | Relative Cost (Low/Med/High) |
---|---|---|---|---|
Aluminum Alloys | Aerospace, automotive parts | Lightweight and easy to machine | Less durable under high stress | Low |
Stainless Steel | Food, pharmaceutical equipment | High strength and corrosion resistance | More expensive and harder to machine | High |
Carbon Steel | Construction, heavy machinery | Cost-effective and durable | Susceptible to rust and corrosion | Medium |
Plastics | Consumer electronics, automotive interiors | Versatile and low cost | Not suitable for high-stress applications | Low |
This strategic material selection guide provides essential insights for international B2B buyers, enabling informed decisions that align with their specific operational needs and regional considerations.
In-depth Look: Manufacturing Processes and Quality Assurance for cost of a cnc machine
Understanding the Manufacturing Processes for CNC Machines
When considering the cost of a CNC machine, it is essential for B2B buyers to grasp the intricacies of its manufacturing processes. Each stage significantly impacts the final product’s quality, performance, and price. Here’s a breakdown of the main stages involved in manufacturing CNC machines.
Main Stages of Manufacturing
-
Material Preparation
– Selection of Raw Materials: The foundation of a CNC machine’s performance lies in the choice of materials. Commonly used materials include high-grade steel, aluminum, and composite materials. Buyers should verify the quality of materials as they affect durability and machining capabilities.
– Cutting and Shaping: Raw materials undergo initial cutting using various methods like laser cutting, water jet cutting, or plasma cutting. Precision in this step is crucial for ensuring that subsequent processes are efficient and effective. -
Forming
– Machining Operations: This stage involves various machining processes such as milling, turning, and grinding. Each operation is critical to achieving the desired dimensions and tolerances. Advanced CNC machines may employ multi-axis machining to enhance versatility.
– Welding and Joining: After forming, components are joined through welding or other methods. The integrity of these joints is vital for the machine’s structural stability, impacting long-term performance. -
Assembly
– Component Integration: The assembly stage involves integrating various machine parts, including the spindle, bed, and control systems. Precision alignment during assembly ensures optimal operation and accuracy.
– Electrical and Software Installation: This includes installing the machine’s electrical systems and software, which are integral for its functionality. Buyers should inquire about the compatibility of software with existing systems. -
Finishing
– Surface Treatment: Post-assembly, surface treatments like anodizing or painting may be applied to enhance corrosion resistance and aesthetics. These treatments can also influence the machine’s longevity and maintenance needs.
– Calibration and Testing: Final adjustments and calibrations are performed to ensure the machine meets specified tolerances and operational standards. This is a critical step before the machine is delivered.
Quality Assurance in CNC Machine Manufacturing
Quality assurance (QA) is crucial for ensuring that CNC machines meet international standards and perform reliably in various applications. Buyers should be well-versed in the QA processes that manufacturers implement.
Relevant International Standards
- ISO 9001: This is a globally recognized standard for quality management systems. Compliance indicates that a manufacturer consistently meets customer and regulatory requirements.
- CE Marking: For European buyers, CE marking signifies that the product meets European safety, health, and environmental protection standards.
- API Standards: Particularly relevant for industries like oil and gas, API standards ensure that equipment meets specific safety and reliability criteria.
Quality Control Checkpoints
-
Incoming Quality Control (IQC)
– This involves inspecting raw materials upon arrival to ensure they meet specified quality standards. Buyers can request IQC reports to verify the materials used in their machines. -
In-Process Quality Control (IPQC)
– Continuous monitoring during the manufacturing process helps identify defects early. Techniques such as statistical process control (SPC) are often employed. -
Final Quality Control (FQC)
– Before shipment, the machine undergoes thorough testing, including functional tests and performance evaluations. Buyers should insist on FQC reports that detail the testing processes and outcomes.
Common Testing Methods
- Dimensional Inspection: Ensures that all components meet specified tolerances using tools such as calipers and CMM (Coordinate Measuring Machines).
- Functional Testing: Verifies that the machine operates as intended under various conditions. This may include stress tests and load tests.
- Electrical Testing: Checks all electrical components and systems for safety and functionality.
Verifying Supplier Quality Control
B2B buyers must adopt a proactive approach to ensure that their suppliers maintain high-quality standards. Here are some actionable strategies:
-
Supplier Audits: Conducting regular audits of suppliers allows buyers to evaluate their manufacturing processes and quality control systems directly. This can include reviewing documentation, observing processes, and interviewing staff.
-
Requesting Quality Reports: Suppliers should provide comprehensive quality reports that detail IQC, IPQC, and FQC results. This transparency helps buyers assess the reliability of the products.
-
Third-party Inspections: Engaging third-party inspection agencies can provide an unbiased assessment of the supplier’s quality control processes. This is particularly important for international transactions where trust levels may be lower.
Navigating Quality Control Nuances for International Buyers
For buyers in regions like Africa, South America, the Middle East, and Europe, understanding the nuances of quality control is vital. Here are some considerations:
-
Cultural Differences: Be aware that quality standards and practices may vary significantly between countries. It’s essential to communicate clearly with suppliers about expectations and requirements.
-
Regulatory Compliance: Ensure that suppliers comply with both local and international regulations. This includes understanding import/export regulations and any specific certifications required in your region.
-
Building Relationships: Establishing strong relationships with suppliers can lead to better quality assurance practices. Engaging in regular communication and visits can foster a collaborative environment focused on quality.
By comprehensively understanding the manufacturing processes and quality assurance practices associated with CNC machines, B2B buyers can make informed decisions that align with their operational needs and budget constraints. Prioritizing quality and establishing robust verification processes will not only enhance the procurement experience but also lead to long-term operational success.
Related Video: How to calculate Manufacturing Cost? | Production Planning (PPC) | Explained with example
Comprehensive Cost and Pricing Analysis for cost of a cnc machine Sourcing
When considering the acquisition of CNC machines, understanding the comprehensive cost structure is crucial for international B2B buyers, particularly in regions such as Africa, South America, the Middle East, and Europe. Each component of the cost contributes to the overall price, influencing the total investment and profitability for businesses.
Cost Components
-
Materials: The primary cost driver in CNC machine production is the raw materials. Steel, aluminum, and other alloys used in machine construction fluctuate in price based on global market conditions. Buyers should consider sourcing from local suppliers to mitigate shipping costs and reduce lead times.
-
Labor: Labor costs vary significantly across regions. In countries with lower labor costs, such as some in Africa and South America, the manufacturing overhead may be lower. However, it’s essential to assess the skill level of the workforce, as higher-skilled labor may justify a higher cost due to better quality output.
-
Manufacturing Overhead: This includes utilities, rent, and indirect labor costs associated with the production process. Understanding the local economic conditions can help buyers gauge these expenses. For example, manufacturers in Europe may have higher overheads due to stricter regulations and higher utility costs.
-
Tooling: CNC machines require specific tooling, which can be a significant upfront cost. Custom tooling can drive up expenses, so buyers should evaluate whether standard tooling options are sufficient for their production needs.
-
Quality Control (QC): Investing in QC processes is essential to ensure the reliability and precision of the machines. The cost of QC can vary based on certification requirements and the complexity of the machines. Buyers should consider suppliers with ISO certifications, as this can indicate a commitment to quality.
-
Logistics: Shipping costs can greatly affect the total price. Factors such as distance, shipping method, and import tariffs must be considered. Utilizing Incoterms effectively can help clarify the responsibilities and costs associated with transportation.
-
Margin: Suppliers will typically add a margin to cover their costs and profit. Understanding the market dynamics and typical margins in different regions can help buyers negotiate better terms.
Price Influencers
Several factors can impact the pricing of CNC machines:
-
Volume/MOQ (Minimum Order Quantity): Larger orders often result in lower per-unit costs. Buyers should assess their production needs to negotiate favorable pricing based on volume.
-
Specifications and Customization: Customized machines tailored to specific applications generally cost more. Buyers should clearly define their specifications to avoid unnecessary customizations that can inflate costs.
-
Materials and Quality Certifications: Higher quality materials and certifications often lead to higher prices. Buyers should balance the need for quality with budget constraints, ensuring they don’t compromise on essential performance requirements.
-
Supplier Factors: The reputation, location, and stability of suppliers can influence pricing. Established suppliers may offer reliability but at a premium. Newer suppliers might provide competitive pricing but could pose risks regarding quality and delivery.
-
Incoterms: Understanding Incoterms is vital for international transactions. They define the responsibilities of buyers and sellers, impacting shipping costs and risk management.
Buyer Tips
-
Negotiation: Always approach suppliers with a clear understanding of market prices and be prepared to negotiate. Building relationships with multiple suppliers can provide leverage.
-
Cost-Efficiency: Evaluate the Total Cost of Ownership (TCO), which includes purchase price, maintenance, operation, and potential downtime costs. A lower upfront cost might lead to higher long-term expenses.
-
Pricing Nuances: International buyers should be aware of regional pricing trends and currency fluctuations. Engaging local experts or consultants can provide insights into the best sourcing strategies.
-
Disclaimer for Indicative Prices: Prices for CNC machines can vary widely based on specifications, region, and supplier. Always seek multiple quotes and conduct thorough due diligence to ensure competitive pricing.
By understanding the cost structure and pricing influencers, international B2B buyers can make informed decisions when sourcing CNC machines, ultimately leading to better investment outcomes.
Spotlight on Potential cost of a cnc machine Manufacturers and Suppliers
This section looks at several manufacturers active in the ‘cost of a cnc machine’ market. This is a representative sample for illustrative purposes; B2B buyers must conduct extensive due diligence before any transaction. Information is synthesized from public sources and general industry knowledge.
Essential Technical Properties and Trade Terminology for cost of a cnc machine
Key Technical Properties
When evaluating the cost of a CNC machine, understanding its technical specifications is crucial for making an informed purchasing decision. Here are some essential properties to consider:
1. Material Grade
The material grade of a CNC machine refers to the quality and type of materials used in its construction. Common materials include steel, aluminum, and composite materials. The choice of material affects durability, maintenance costs, and machine precision. B2B buyers must ensure that the machine’s material grade aligns with their production needs and the types of components they will manufacture.
2. Tolerance
Tolerance indicates the permissible limit of variation in a physical dimension. It is critical for determining how closely a CNC machine can produce parts to specified dimensions. High-precision applications may require tighter tolerances, which can increase machine costs. Understanding tolerance requirements helps buyers select a machine that meets their quality standards without incurring unnecessary expenses.
3. Axis Configuration
CNC machines come in various configurations, such as 3-axis, 4-axis, and 5-axis systems. The number of axes directly influences the complexity of parts that can be manufactured. More axes allow for greater flexibility and precision but typically come at a higher cost. Buyers should assess their production capabilities to determine the appropriate axis configuration for their needs.
4. Spindle Speed
Spindle speed refers to the rotation rate of the machine’s spindle, typically measured in revolutions per minute (RPM). Higher spindle speeds enable faster cutting and improved surface finishes, which can significantly impact production efficiency. Buyers should consider their material processing requirements when evaluating spindle speed, as it can also affect tool wear and maintenance costs.
5. Power Rating
The power rating of a CNC machine, usually measured in horsepower (HP) or kilowatts (kW), indicates its capability to handle various materials and cutting tasks. A higher power rating generally allows for more robust machining operations and faster processing times. Buyers should ensure that the machine’s power rating aligns with their intended applications to avoid performance issues.
Common Trade Terms
Familiarity with industry jargon can facilitate smoother negotiations and transactions in the B2B CNC machine market. Here are some key terms to know:
1. OEM (Original Equipment Manufacturer)
An OEM is a company that produces parts or equipment that may be marketed by another manufacturer. In the context of CNC machines, understanding whether a supplier is an OEM can affect warranty, service, and parts availability. Buyers should seek OEMs for reliable quality and support.
2. MOQ (Minimum Order Quantity)
MOQ refers to the minimum number of units a supplier is willing to sell. This term is crucial for buyers, especially those in emerging markets, as it can affect cash flow and inventory management. Understanding MOQs allows buyers to plan their procurement strategies more effectively.
3. RFQ (Request for Quotation)
An RFQ is a document sent to suppliers to solicit price quotes for specific products or services. For CNC machines, issuing an RFQ helps buyers compare prices and specifications from multiple vendors, ensuring they receive the best value. Crafting a clear and detailed RFQ is essential for accurate responses.
4. Incoterms (International Commercial Terms)
Incoterms are a set of predefined international trade terms that clarify the responsibilities of buyers and sellers in shipping. Familiarity with these terms, such as FOB (Free On Board) and CIF (Cost, Insurance, and Freight), helps buyers understand shipping costs and risks associated with international transactions.
5. Lead Time
Lead time refers to the time it takes from placing an order to receiving the product. For CNC machines, longer lead times can impact production schedules. Buyers should inquire about lead times when negotiating contracts to ensure timely delivery of equipment.
Understanding these technical properties and trade terms equips B2B buyers with the knowledge needed to make informed decisions in the CNC machine market. By considering these factors, companies can optimize their purchasing strategies and enhance their operational efficiency.
Navigating Market Dynamics, Sourcing Trends, and Sustainability in the cost of a cnc machine Sector
Market Overview & Key Trends
The global CNC machine market is experiencing significant growth, driven by the increasing demand for automation in manufacturing and the need for precision engineering across various industries. As international B2B buyers from regions such as Africa, South America, the Middle East, and Europe explore sourcing options, they must be aware of the following key trends shaping the market:
- Technological Advancements: The rise of Industry 4.0 is influencing CNC machine capabilities, with smart manufacturing technologies such as IoT and AI integration enhancing machine performance and operational efficiency. Buyers should consider suppliers that offer advanced CNC machines equipped with these technologies to remain competitive.
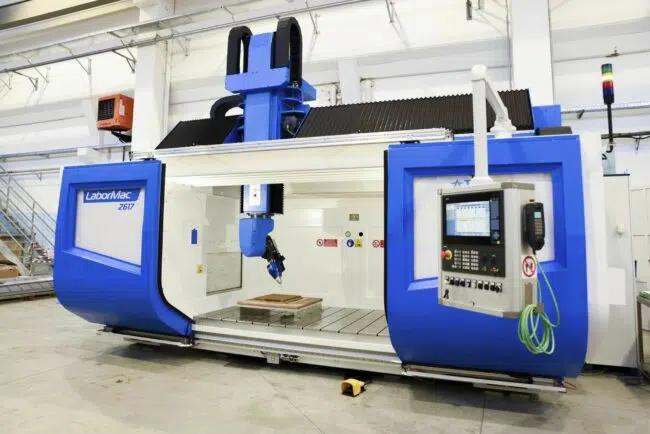
Illustrative Image (Source: Google Search)
-
Customization and Flexibility: There is a growing demand for CNC machines that can handle diverse materials and complex designs. Buyers are encouraged to evaluate suppliers that offer customizable solutions, allowing for greater adaptability to specific project requirements.
-
Regional Demand Variations: While Europe remains a strong market for high-end CNC machines, regions like Africa and South America are witnessing an increase in demand for cost-effective solutions. Buyers should conduct thorough market analysis to identify local suppliers who can meet their budget and quality expectations.
-
Supply Chain Resilience: Disruptions caused by global events have underscored the importance of robust supply chains. International buyers should prioritize suppliers with a proven track record of reliability and risk management strategies, ensuring timely delivery and support.
By understanding these dynamics, B2B buyers can make informed decisions, ensuring that they source CNC machines that align with their operational needs and market conditions.
Sustainability & Ethical Sourcing in B2B
Sustainability is becoming an essential criterion for B2B buyers, particularly in the CNC machine sector. The environmental impact of manufacturing processes and the materials used in CNC machines are under scrutiny, pushing businesses to adopt more sustainable practices.
-
Environmental Impact: The production and operation of CNC machines can contribute to waste and energy consumption. Buyers should seek machines that are designed for energy efficiency and reduced waste generation. This not only meets regulatory requirements but also appeals to environmentally conscious customers.
-
Importance of Ethical Supply Chains: A transparent supply chain enhances a company’s reputation and builds trust with clients. B2B buyers should prioritize suppliers who adhere to ethical sourcing practices, ensuring that materials are procured responsibly and labor standards are upheld.
-
Green Certifications and Materials: Look for suppliers that offer CNC machines made from recyclable materials or those certified by recognized environmental standards (e.g., ISO 14001). These certifications not only indicate a commitment to sustainability but can also enhance the overall value proposition of the machine.
Emphasizing sustainability and ethical sourcing can provide a competitive edge in the market, appealing to a growing segment of environmentally aware customers.
Brief Evolution/History
The CNC (Computer Numerical Control) machine industry has evolved significantly since its inception in the 1950s. Originally developed to automate complex machining tasks, CNC technology has transformed into a cornerstone of modern manufacturing. The introduction of computers allowed for more precise control over machining processes, leading to enhanced accuracy and efficiency.
Over the decades, advancements in technology have led to the integration of CAD/CAM software, enabling seamless design and production workflows. The shift toward automation and smart technologies in recent years has further revolutionized the sector, allowing for real-time data analysis and predictive maintenance. As the market continues to evolve, B2B buyers must stay informed about historical trends and technological advancements to make strategic sourcing decisions that align with their business goals.
Related Video: Chapter 9: International Trade
Frequently Asked Questions (FAQs) for B2B Buyers of cost of a cnc machine
-
What factors influence the cost of a CNC machine?
The cost of a CNC machine can vary significantly based on several factors including the type of machine (e.g., milling, turning, or laser), its size, and the technology used (e.g., 3-axis vs. 5-axis). Additionally, features such as automation, software capabilities, and precision levels can impact pricing. Buyers should also consider the machine’s intended application, as specialized machines for specific industries may command higher prices. -
How do I vet suppliers when sourcing CNC machines internationally?
To effectively vet suppliers, start by checking their credentials and certifications, such as ISO standards. Look for reviews and testimonials from previous clients, and request case studies or examples of their work. Engage in direct communication to assess their responsiveness and willingness to address concerns. Additionally, consider visiting their manufacturing facilities if possible, or utilizing third-party inspection services to ensure quality standards are met. -
Can CNC machines be customized to meet specific needs?
Yes, many manufacturers offer customization options for CNC machines to cater to specific requirements. This can include modifications in size, tooling, software integration, and additional features like enhanced safety systems. When discussing customization, clearly outline your production needs and specifications to the supplier. Be aware that customizations may affect lead times and pricing, so factor these into your budget and timeline. -
What are the typical lead times and minimum order quantities (MOQs) for CNC machines?
Lead times for CNC machines can vary widely depending on the complexity of the machine and the supplier’s current production capacity. Generally, standard machines may have lead times ranging from 4 to 12 weeks, while custom machines can take longer. Regarding MOQs, many suppliers allow for single-unit purchases, but larger orders may yield better pricing. Always confirm these details upfront to avoid surprises later in the procurement process.
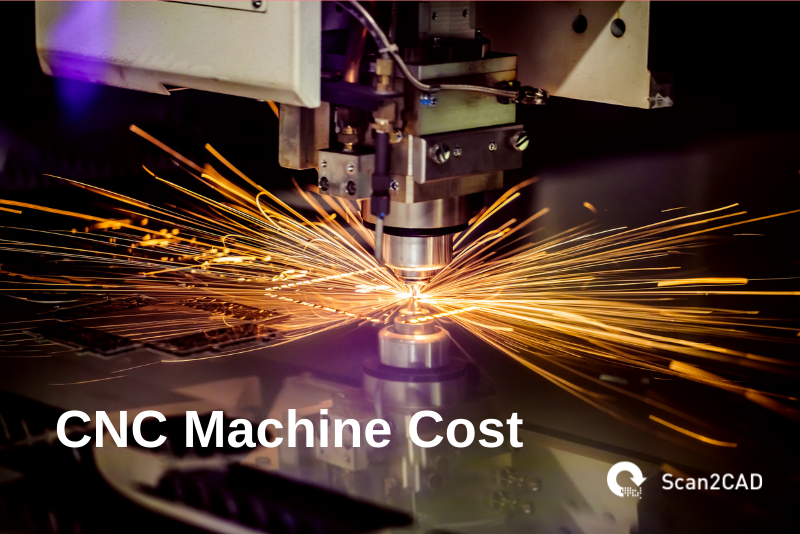
Illustrative Image (Source: Google Search)
-
What payment terms are common when purchasing CNC machines internationally?
Payment terms can differ by supplier and region, but common practices include a deposit (often 30-50%) upfront, with the balance due upon delivery or installation. Some suppliers may offer financing options or letter of credit arrangements. It’s crucial to clarify these terms early in negotiations to ensure alignment with your budget and cash flow requirements, as well as to mitigate risks associated with international transactions. -
How do I ensure quality assurance and certifications for CNC machines?
To ensure quality, request that suppliers provide certificates of compliance with international standards such as ISO 9001 or CE marking, which indicate adherence to quality management systems. Additionally, inquire about their quality control processes, including testing and inspection protocols during manufacturing. Consider requesting samples or trial runs to evaluate machine performance before committing to a larger purchase. -
What logistics considerations should I keep in mind when importing CNC machines?
Logistics play a vital role in the procurement of CNC machines. Key considerations include shipping methods (air vs. sea), customs regulations, and potential tariffs that may apply to your import. Work closely with logistics providers who have experience in international shipping of heavy machinery. Ensure that the supplier can assist with proper packaging to prevent damage during transit and that you have a clear understanding of delivery timelines. -
How can disputes regarding CNC machine purchases be resolved?
Disputes can arise over quality, delivery times, or performance issues. To mitigate risks, establish clear terms and conditions in your purchase agreement, including warranties and return policies. If a dispute occurs, attempt to resolve it through direct communication with the supplier. Should that fail, consider mediation or arbitration, as many international contracts include clauses for alternative dispute resolution. Always document communications and agreements for reference.
Important Disclaimer & Terms of Use
⚠️ Important Disclaimer
The information provided in this guide, including content regarding manufacturers, technical specifications, and market analysis, is for informational and educational purposes only. It does not constitute professional procurement advice, financial advice, or legal advice.
While we have made every effort to ensure the accuracy and timeliness of the information, we are not responsible for any errors, omissions, or outdated information. Market conditions, company details, and technical standards are subject to change.
B2B buyers must conduct their own independent and thorough due diligence before making any purchasing decisions. This includes contacting suppliers directly, verifying certifications, requesting samples, and seeking professional consultation. The risk of relying on any information in this guide is borne solely by the reader.
Strategic Sourcing Conclusion and Outlook for cost of a cnc machine
In navigating the complex landscape of CNC machine procurement, strategic sourcing emerges as a critical factor for international buyers. By leveraging comprehensive market analysis, buyers can identify the most cost-effective suppliers while ensuring quality and reliability. Key takeaways include understanding the total cost of ownership, including maintenance and operational expenses, and the importance of building strong supplier relationships that foster collaboration and innovation.
Value of Strategic Sourcing:
– Cost Efficiency: Engage in competitive bidding to secure the best price.
– Quality Assurance: Prioritize suppliers with proven track records and certifications.
– Local Insights: Utilize regional suppliers to mitigate import tariffs and logistics challenges.
As the global manufacturing landscape evolves, particularly in Africa, South America, the Middle East, and Europe, buyers must remain proactive and adaptable. The demand for CNC machines is projected to grow, driven by advancements in automation and customization. Therefore, it is essential to continuously monitor market trends and supplier performance.
Call to Action:
Invest in strategic sourcing initiatives today to position your organization for future success. By harnessing the power of informed decision-making and collaboration, you can not only reduce costs but also enhance operational efficiencies in your manufacturing processes.