Master the Costs: How Much Does a CNC Machine Cost for Your
Introduction: Navigating the Global Market for how much does a cnc machine cost
In the rapidly evolving landscape of global manufacturing, understanding the cost of CNC machines is crucial for B2B buyers looking to optimize their production capabilities. Whether you’re a business in Africa, South America, the Middle East, or Europe, making informed decisions about CNC machine investments can significantly impact your operational efficiency and bottom line. This comprehensive guide addresses the essential question: How much does a CNC machine cost?
CNC machines vary widely in price, influenced by factors such as type, size, and advanced features. From entry-level routers to high-end 5-axis machines, the choices available can seem overwhelming. This guide delves into the various types of CNC machines, the materials they can work with, and the nuances of manufacturing and quality control processes. Additionally, we will explore key suppliers, market trends, and frequently asked questions to empower you in making informed sourcing decisions.
By equipping you with a clear understanding of CNC machine costs, operational considerations, and market dynamics, this guide aims to enhance your purchasing strategy. As international buyers navigate the complexities of sourcing, having a reliable resource on CNC machine costs ensures that your investment aligns with your production needs and financial objectives. Prepare to unlock the potential of CNC technology for your business!
Understanding how much does a cnc machine cost Types and Variations
Type Name | Key Distinguishing Features | Primary B2B Applications | Brief Pros & Cons for Buyers |
---|---|---|---|
CNC Mills | Versatile, capable of machining metals, 3 to 5-axis options | Aerospace, automotive, manufacturing | Pros: High precision, versatile materials. Cons: Higher initial cost, requires skilled operators. |
CNC Routers | Designed for softer materials, typically 3-axis | Furniture, signage, cabinetry | Pros: Lower cost, easy to use. Cons: Limited to softer materials, less precision than mills. |
CNC Lathes | Specializes in cylindrical parts, 2 to 4-axis configurations | Automotive parts, medical devices | Pros: Excellent for round parts, high efficiency. Cons: Limited to specific shapes, can be costly. |
5-Axis CNC Machines | Advanced machining flexibility, complex geometries | Aerospace components, intricate designs | Pros: High precision, reduced setup time. Cons: Significant investment, requires skilled operators. |
Metal CNC Machines | Heavy-duty construction, ideal for metalworking | Industrial manufacturing, metal fabrication | Pros: Robust and durable, high precision. Cons: High initial cost, maintenance can be complex. |
CNC Mills
CNC mills are among the most versatile types of CNC machines, capable of machining a variety of materials, including metals and plastics. They typically feature 3 to 5-axis configurations, allowing for complex shapes and high precision. Businesses in sectors such as aerospace and automotive often invest in CNC mills due to their ability to produce intricate parts with tight tolerances. When purchasing, consider the machine’s size, capabilities, and the level of automation required to meet your production needs.
CNC Routers
CNC routers are primarily designed for cutting softer materials like wood, plastic, and composites. They are generally more affordable and easier to operate than mills, making them a popular choice for small to medium-sized enterprises in furniture, signage, and cabinetry industries. While CNC routers offer lower initial costs, they may lack the precision required for more complex projects. Buyers should assess their material requirements and production volume when deciding on a CNC router.
CNC Lathes
CNC lathes excel in creating cylindrical parts and are commonly used in industries such as automotive and medical device manufacturing. With configurations ranging from 2 to 4 axes, they provide high efficiency and precision for round components. When considering a CNC lathe, businesses should evaluate the specific shapes they need to produce and the machine’s capabilities to ensure it aligns with production goals. The investment can be significant, but the efficiency gains can justify the cost.
5-Axis CNC Machines
5-axis CNC machines offer advanced machining capabilities, allowing for the production of complex geometries with high precision. They are particularly beneficial for industries like aerospace, where intricate designs are commonplace. While these machines come with a higher price tag, they can significantly reduce setup times and increase productivity. Companies should consider their production volume and the skill level of their operators, as these machines require specialized training to operate effectively.
Metal CNC Machines
Metal CNC machines are built for heavy-duty applications and are essential in industrial manufacturing and metal fabrication. These machines are designed to handle robust materials and provide exceptional precision. However, they require a substantial investment and ongoing maintenance can be complex. Businesses should weigh the long-term benefits of increased production capabilities against the initial costs and maintenance requirements when considering a metal CNC machine for their operations.
Related Video: The TRUE COST of CNC machining!
Key Industrial Applications of how much does a cnc machine cost
Industry/Sector | Specific Application of how much does a cnc machine cost | Value/Benefit for the Business | Key Sourcing Considerations for this Application |
---|---|---|---|
Aerospace | Precision component manufacturing for aircraft | Enhanced accuracy and reduced waste in production | Evaluate machine precision, size, and supplier support |
Automotive | Custom part production for vehicle assembly | Cost savings through in-house manufacturing | Assess tooling options, machine versatility, and service life |
Electronics | PCB prototyping and small batch production | Faster turnaround and greater design flexibility | Look for software compatibility and training support |
Medical Devices | Manufacturing surgical instruments and implants | High precision and compliance with regulatory standards | Ensure robust quality control and warranty options |
Furniture Design | Custom furniture parts and intricate designs | Unique product offerings and improved production efficiency | Consider material compatibility and machine capabilities |
Aerospace
In the aerospace industry, CNC machines are essential for the precise manufacturing of components that require high accuracy and reliability. The cost of these machines can significantly impact budgeting for projects, especially in sectors where safety is paramount. International buyers should focus on sourcing machines that offer tight tolerances and robust quality assurance processes. Companies must also consider long-term operational costs, such as maintenance and training for specialized staff, to ensure ongoing compliance with industry regulations.
Automotive
The automotive sector benefits from CNC machining through the production of custom parts that streamline assembly processes. By investing in CNC technology, businesses can reduce outsourcing costs and improve turnaround times. Buyers, particularly from emerging markets in Africa and South America, should evaluate the total cost of ownership, including potential savings from in-house production. Key considerations include the machine’s adaptability to various materials and its ability to handle high-volume production runs.
Electronics
CNC machines are pivotal in the electronics industry for prototyping printed circuit boards (PCBs) and producing small batches of components. The ability to quickly iterate designs can significantly enhance a company’s competitive edge. B2B buyers should prioritize machines that offer advanced software integration and ease of use, enabling their teams to adapt quickly to evolving project requirements. Additionally, sourcing from reputable suppliers that provide training and ongoing support can mitigate risks associated with technology adoption.
Medical Devices
In the medical devices sector, CNC machining is used to manufacture surgical instruments and implants that require exceptional precision and adherence to strict regulatory standards. The investment in high-quality CNC machines is justified by the need for reliability and safety in medical applications. International buyers should ensure that the equipment meets relevant certifications and has a solid warranty and support structure. Understanding the costs associated with compliance and quality assurance will be crucial for maintaining market competitiveness.
Furniture Design
CNC technology has revolutionized furniture design, allowing manufacturers to create custom parts and intricate designs with ease. This capability not only enhances creativity but also improves production efficiency. Companies in Europe and the Middle East should consider the specific material requirements and machine capabilities when sourcing CNC machines. Additionally, understanding the potential for automation in furniture production can lead to significant cost savings and improved product offerings in a competitive market.
Related Video: CNC machining – What is it and How Does it Work? (Must Know Basics)
Strategic Material Selection Guide for how much does a cnc machine cost
When selecting materials for CNC machining, understanding the properties, advantages, and limitations of each material is crucial for international B2B buyers. This guide will analyze four common materials used in CNC machining, focusing on their key properties, pros and cons, application impacts, and specific considerations for buyers from Africa, South America, the Middle East, and Europe.
Aluminum
Key Properties: Aluminum is lightweight, corrosion-resistant, and has excellent thermal and electrical conductivity. Its temperature rating typically ranges from -200°C to 600°C, making it suitable for various applications.
Pros & Cons: Aluminum is durable and easy to machine, which reduces manufacturing complexity. However, it can be more expensive than other materials like plastics and may not be suitable for high-stress applications.
Impact on Application: Aluminum is commonly used in aerospace, automotive, and consumer goods due to its lightweight nature and strength. It is compatible with various media, including air and water.
Considerations for International Buyers: Buyers should ensure compliance with standards such as ASTM B221 for aluminum extrusions. Additionally, sourcing aluminum from local suppliers can reduce shipping costs and lead times.
Steel
Key Properties: Steel is known for its high tensile strength and durability, with a temperature rating that can exceed 1,500°C depending on the alloy. It also has good corrosion resistance when treated.
Pros & Cons: Steel’s strength makes it ideal for heavy-duty applications, but it can be more challenging to machine, leading to higher manufacturing costs. It is also heavier than aluminum, which may impact design considerations.
Impact on Application: Steel is widely used in construction, machinery, and automotive industries. Its compatibility with harsh environments makes it suitable for applications exposed to extreme conditions.
Considerations for International Buyers: Buyers must be aware of the various steel grades and their respective standards, such as ASTM A36 or EN 10025. Understanding local regulations regarding steel sourcing and environmental compliance is also essential.
Plastic (e.g., ABS, Nylon)
Key Properties: Plastics like ABS and Nylon are lightweight, resistant to corrosion, and have a lower temperature rating, typically around 80°C to 120°C for ABS and up to 200°C for Nylon.
Pros & Cons: Plastics are generally less expensive and easier to machine than metals, making them suitable for prototypes and low-stress applications. However, they may not be as durable or heat-resistant as metals, limiting their use in high-performance environments.
Impact on Application: Plastics are ideal for consumer products, electronic housings, and automotive components. Their chemical resistance makes them suitable for applications involving various media.
Considerations for International Buyers: Buyers should check for compliance with standards like ISO 9001 for quality management. Understanding the specific properties of different plastics is crucial for selecting the right material for the intended application.
Titanium
Key Properties: Titanium is known for its exceptional strength-to-weight ratio and corrosion resistance. It can withstand temperatures up to 600°C and is biocompatible, making it suitable for medical applications.
Pros & Cons: Titanium is incredibly strong and lightweight, making it ideal for aerospace and medical applications. However, it is more expensive and challenging to machine than other materials, leading to higher production costs.
Impact on Application: Titanium is commonly used in aerospace, medical implants, and high-performance automotive parts. Its compatibility with aggressive media makes it suitable for specialized applications.
Considerations for International Buyers: Buyers should ensure compliance with international standards like ASTM F136 for titanium used in medical applications. Understanding import regulations and sourcing titanium from reliable suppliers is vital for maintaining quality.
Material | Typical Use Case for how much does a cnc machine cost | Key Advantage | Key Disadvantage/Limitation | Relative Cost (Low/Med/High) |
---|---|---|---|---|
Aluminum | Aerospace components, automotive parts | Lightweight and corrosion-resistant | More expensive than plastics | Medium |
Steel | Construction, machinery, automotive | High strength and durability | Challenging to machine, heavier | Medium |
Plastic (e.g., ABS, Nylon) | Consumer products, electronic housings | Cost-effective and easy to machine | Lower durability and heat resistance | Low |
Titanium | Aerospace, medical implants | Exceptional strength-to-weight ratio | High cost and machining difficulty | High |
This analysis provides a comprehensive overview of materials commonly used in CNC machining, enabling B2B buyers to make informed decisions based on their specific application needs and regional considerations.
In-depth Look: Manufacturing Processes and Quality Assurance for how much does a cnc machine cost
Manufacturing Processes for CNC Machines
Understanding the manufacturing processes involved in producing CNC machines is essential for B2B buyers. This knowledge not only aids in evaluating machine quality but also in assessing the overall value proposition of the investment. The main stages of manufacturing CNC machines include material preparation, forming, assembly, and finishing.
Material Preparation
Material preparation is the foundational step in CNC machine manufacturing. It involves selecting high-quality raw materials, which typically include metals like aluminum, steel, and cast iron. The selection process is critical as the material properties directly impact the machine’s durability and precision.
- Material Selection: High-grade materials are chosen based on their machinability, strength, and resistance to wear.
- Cutting and Shaping: Raw materials are cut into manageable sizes using saws or lasers to facilitate further processing.
Forming
Once materials are prepared, the forming stage commences. This involves shaping the material into desired components using various techniques:
- Casting: Molten metal is poured into molds to create complex shapes. This is common for components that require significant mass.
- Machining: This is where CNC technology shines. The prepared materials undergo CNC milling, turning, or drilling to achieve precise dimensions and surface finishes.
- Welding and Joining: For larger assemblies, parts may be welded or mechanically joined. This step is crucial for ensuring structural integrity.
Assembly
After forming, the assembly stage brings together all the components to create the final CNC machine. This process often requires skilled technicians and involves:
- Sub-Assembly Creation: Individual parts are assembled into sub-units (like the spindle assembly, base, and control panel).
- Final Assembly: All sub-units are combined, followed by the installation of electronic systems, software, and safety mechanisms.
Finishing
The finishing stage enhances both the aesthetic and functional properties of the CNC machine. Techniques used include:
- Surface Treatment: This may involve anodizing, powder coating, or painting to protect against corrosion and wear.
- Calibration and Testing: Machines are calibrated to ensure accuracy. This may involve setting up the control systems and testing the machine’s performance under various conditions.
Quality Assurance in CNC Machine Manufacturing
Quality assurance (QA) is paramount in the manufacturing of CNC machines, ensuring that they meet international standards and customer expectations. The QA process typically encompasses several stages, including incoming quality control (IQC), in-process quality control (IPQC), and final quality control (FQC).
International Standards
B2B buyers should be aware of relevant international standards that manufacturers must adhere to:
- ISO 9001: This standard focuses on quality management systems and is crucial for ensuring consistent quality in products and services.
- CE Marking: Required for products sold in the European Economic Area, indicating compliance with safety and environmental protection standards.
- API Standards: For machines used in oil and gas sectors, API standards ensure that equipment is safe and reliable.
Quality Checkpoints
- Incoming Quality Control (IQC): This involves inspecting raw materials upon arrival. Buyers should verify that suppliers maintain rigorous IQC protocols to avoid defects from the start.
- In-Process Quality Control (IPQC): During manufacturing, periodic checks are performed to ensure that the processes remain within specified limits. This is critical for maintaining precision and quality throughout production.
- Final Quality Control (FQC): After assembly, the final product undergoes comprehensive testing to ensure it meets all specifications and standards before shipping.
Common Testing Methods
B2B buyers should inquire about the testing methods used by manufacturers, which may include:
- Dimensional Inspection: Ensuring that all components meet specified measurements.
- Functional Testing: Verifying that the machine operates as intended under various conditions.
- Durability Testing: Assessing the machine’s performance over extended use.
Verifying Supplier Quality Control
To ensure that a CNC machine supplier meets quality standards, international B2B buyers should consider the following verification methods:
- Supplier Audits: Conducting regular audits of suppliers can help assess their adherence to quality standards and operational practices. This includes reviewing their QA processes and certifications.
- Quality Reports: Requesting detailed quality reports from suppliers can provide insights into their manufacturing practices and any issues encountered during production.
- Third-Party Inspections: Engaging third-party inspection services can offer an unbiased evaluation of the supplier’s quality control processes and the final product.
Quality Control Considerations for International Buyers
B2B buyers from Africa, South America, the Middle East, and Europe should be aware of unique QC nuances when dealing with international suppliers:
- Regulatory Compliance: Ensure that the machines comply with local regulations in the buyer’s country, which may differ significantly from the supplier’s country.
- Cultural Differences: Understanding cultural and business practices can aid in navigating potential misunderstandings regarding quality expectations.
- Logistics and Supply Chain: International shipping can introduce risks, including damage during transport. Buyers should consider suppliers that offer robust packaging and logistics solutions.
In summary, understanding the manufacturing processes and quality assurance practices for CNC machines is vital for international B2B buyers. By focusing on these aspects, buyers can make informed decisions that align with their operational needs and quality expectations.
Related Video: Inspection and Quality control in Manufacturing
Comprehensive Cost and Pricing Analysis for how much does a cnc machine cost Sourcing
Analyzing the cost structure and pricing of CNC machines is crucial for international B2B buyers, particularly those from Africa, South America, the Middle East, and Europe. Understanding the various cost components and price influencers can help businesses make informed purchasing decisions.
Cost Components
-
Materials: The type of materials used in CNC machining significantly influences costs. High-quality raw materials, such as metals and composites, often lead to higher production costs. Buyers should assess the material requirements for their specific applications to estimate costs accurately.
-
Labor: Skilled labor is essential for operating CNC machines. Labor costs vary by region and can be a significant part of the overall expense. In some regions, labor may be less expensive, while in others, especially in developed markets, skilled machinists may command higher wages.
-
Manufacturing Overhead: This includes facility costs, utilities, and administrative expenses. Overhead can vary widely based on the supplier’s location and operational efficiency. Understanding a supplier’s overhead can provide insights into their pricing structure.
-
Tooling: CNC machining requires specialized tools that can wear out and need replacement. The costs associated with tooling can add up, especially for projects requiring precision and customization. Buyers should consider these ongoing costs when budgeting.
-
Quality Control (QC): Ensuring product quality incurs additional costs. Implementing QC processes can involve testing equipment and personnel, which contributes to the overall price. Buyers should inquire about the QC practices of potential suppliers to gauge reliability.
-
Logistics: Transporting CNC machines or finished parts can be expensive, especially for international buyers. Shipping costs can vary based on distance, mode of transport, and customs duties. It is crucial to factor these logistics costs into the total purchase price.
-
Margin: Suppliers typically add a profit margin to their costs. This margin can vary based on competition, demand, and the supplier’s positioning in the market. Understanding the typical margins in different regions can aid buyers in negotiations.
Price Influencers
-
Volume/MOQ: The minimum order quantity (MOQ) can significantly affect pricing. Larger orders often lead to lower per-unit costs due to economies of scale. Buyers should assess their needs carefully to optimize order sizes.
-
Specifications/Customization: Custom CNC machines tailored to specific requirements will generally cost more than standard models. Buyers should clearly communicate their needs to suppliers to avoid unexpected costs.
-
Materials: The choice of materials not only affects the initial purchase price but also influences machining complexity and tooling costs. Selecting materials wisely can lead to cost efficiencies.
-
Quality/Certifications: Higher quality and certified machines often come at a premium. Buyers should weigh the benefits of these investments against their operational needs.
-
Supplier Factors: The reputation and reliability of suppliers can impact prices. Established suppliers with proven track records may charge more due to their reliability and service offerings.
-
Incoterms: Understanding international shipping terms is crucial for cost management. Different Incoterms can shift responsibility for shipping costs and risks, affecting the total cost of acquisition.
Buyer Tips
-
Negotiation: Buyers should leverage their purchasing power by negotiating prices, especially for larger orders. Establishing long-term relationships with suppliers can also lead to better terms.
-
Cost-Efficiency: To achieve cost-efficiency, buyers should consider all cost components, not just the purchase price. A comprehensive evaluation of total costs can lead to better decision-making.
-
Total Cost of Ownership (TCO): Beyond the initial purchase price, buyers should evaluate the TCO, which includes maintenance, operational costs, and potential downtime. This assessment can provide a clearer picture of the financial impact of the investment.
-
Pricing Nuances for International Buyers: When sourcing from different regions, consider currency fluctuations, import duties, and varying market conditions. These factors can influence the final cost and should be factored into the decision-making process.
Disclaimer
Prices mentioned throughout this analysis are indicative and can vary significantly based on market conditions, specifications, and supplier negotiations. Always conduct thorough research and obtain quotes from multiple suppliers before making a purchasing decision.
Spotlight on Potential how much does a cnc machine cost Manufacturers and Suppliers
This section looks at several manufacturers active in the ‘how much does a cnc machine cost’ market. This is a representative sample for illustrative purposes; B2B buyers must conduct extensive due diligence before any transaction. Information is synthesized from public sources and general industry knowledge.
Essential Technical Properties and Trade Terminology for how much does a cnc machine cost
Understanding the key technical properties and trade terminology related to CNC machine costs is crucial for international B2B buyers. This knowledge not only aids in making informed purchasing decisions but also enhances negotiation capabilities and operational planning.
Key Technical Properties
-
Material Grade
– Definition: The classification of materials based on their mechanical properties, such as strength, hardness, and ductility.
– B2B Importance: Selecting the appropriate material grade is essential for ensuring the longevity and performance of machined parts. Different CNC machines have varying capabilities for handling specific materials, influencing overall machining costs and project feasibility. -
Tolerance
– Definition: The permissible limit or limits of variation in a physical dimension, often expressed as a range.
– B2B Importance: Precision is critical in CNC machining; tighter tolerances often lead to higher costs due to the need for more advanced machinery and processes. Understanding tolerance requirements helps buyers choose the right machine and avoid costly rework. -
Axis Configuration
– Definition: Refers to the number of axes on which a CNC machine can operate (e.g., 3-axis, 4-axis, 5-axis).
– B2B Importance: The complexity of the part being machined determines the necessary axis configuration. More axes allow for greater flexibility and precision but significantly increase the machine’s cost. Buyers must evaluate their specific needs against the capabilities of available machines. -
Speed and Feed Rate
– Definition: Speed refers to the rate at which the cutting tool moves, while feed rate indicates how quickly the material is fed into the machine.
– B2B Importance: These parameters affect production efficiency and cost. Higher speeds can reduce cycle times but may require more expensive machines. Balancing speed and feed rate is crucial for optimizing machining operations and controlling expenses. -
Power Consumption
– Definition: The amount of electrical power a CNC machine requires to operate effectively.
– B2B Importance: Machines with higher power consumption can lead to increased operational costs. Understanding a machine’s power requirements helps buyers assess long-term energy costs, which can significantly impact total ownership expenses.
Common Trade Terms
-
OEM (Original Equipment Manufacturer)
– Definition: A company that produces parts or equipment that may be marketed by another manufacturer.
– Importance: Understanding OEM relationships is vital when sourcing CNC machines, as it can affect warranty, support, and compatibility with existing equipment. -
MOQ (Minimum Order Quantity)
– Definition: The smallest quantity of a product that a supplier is willing to sell.
– Importance: Knowing the MOQ is essential for budgeting and ensuring that the purchase aligns with production needs. High MOQs can lead to unnecessary inventory costs. -
RFQ (Request for Quotation)
– Definition: A document that solicits bids from suppliers for the supply of goods or services.
– Importance: Issuing an RFQ allows buyers to compare costs and services from multiple suppliers, enabling better negotiation and decision-making. -
Incoterms (International Commercial Terms)
– Definition: A series of predefined commercial terms published by the International Chamber of Commerce (ICC) related to international commercial law.
– Importance: Familiarity with Incoterms helps buyers understand their responsibilities regarding shipping, insurance, and tariffs, which can affect overall costs. -
Lead Time
– Definition: The time taken from placing an order to receiving the product.
– Importance: Recognizing lead times is crucial for project planning and inventory management. Longer lead times may necessitate adjustments in production schedules and cash flow management. -
TCO (Total Cost of Ownership)
– Definition: The comprehensive assessment of all costs associated with acquiring and operating a machine over its lifecycle.
– Importance: TCO provides a holistic view that goes beyond the initial purchase price, helping buyers make informed decisions that factor in maintenance, energy consumption, and potential downtime.
Equipped with knowledge of these technical properties and trade terms, international B2B buyers can navigate the complexities of CNC machine costs more effectively, ensuring that their investments are aligned with operational goals and market demands.
Navigating Market Dynamics, Sourcing Trends, and Sustainability in the how much does a cnc machine cost Sector
Market Overview & Key Trends
The global CNC machine market is experiencing robust growth, driven by advancements in automation and increased demand for precision manufacturing across various sectors, including aerospace, automotive, and electronics. For international B2B buyers, particularly from Africa, South America, the Middle East, and Europe, understanding these market dynamics is crucial for making informed purchasing decisions. Emerging technologies such as IoT and AI are reshaping how CNC machines are utilized, enabling predictive maintenance and enhancing operational efficiency.
Moreover, the trend towards in-house manufacturing is gaining traction, particularly as companies seek to reduce lead times and mitigate supply chain risks. This shift is particularly relevant for regions with burgeoning manufacturing sectors, where local sourcing of CNC machines can provide cost advantages and foster economic growth. Additionally, buyers are increasingly looking for machines that offer scalability and flexibility, allowing them to adapt to changing production demands without incurring significant additional costs.

Illustrative Image (Source: Google Search)
The rise of e-commerce platforms is also transforming the sourcing landscape, providing international buyers with unprecedented access to a wide range of CNC machines from various manufacturers. This increased transparency in pricing and specifications enables buyers to make more strategic decisions. However, it also necessitates a thorough evaluation of suppliers to ensure reliability and quality, particularly when sourcing from different continents.
Sustainability & Ethical Sourcing in B2B
Sustainability is becoming a critical factor in the purchasing decisions of CNC machines. The environmental impact of manufacturing processes, including energy consumption and waste generation, is prompting B2B buyers to seek machines that minimize their ecological footprint. This includes selecting CNC machines that are energy-efficient and designed for easy recycling at the end of their lifecycle.
Furthermore, ethical sourcing practices are gaining importance as businesses strive to ensure that their supply chains are not only efficient but also socially responsible. Buyers are increasingly looking for manufacturers that adhere to international standards for labor rights and environmental protection. Certifications such as ISO 14001 (Environmental Management) and ISO 9001 (Quality Management) can serve as indicators of a supplier’s commitment to sustainability and ethical practices.
Incorporating green materials and processes in CNC machining is also a trend worth noting. For example, the use of biodegradable cutting fluids and recyclable materials can significantly reduce the environmental impact of manufacturing operations. By prioritizing sustainability, B2B buyers can enhance their brand reputation and align with global trends towards responsible consumption.
Brief Evolution/History
The evolution of CNC machining can be traced back to the 1940s, when the first numerical control (NC) machines were developed. These early machines were limited in capability and required manual input, but they laid the foundation for the advanced CNC systems we see today. The 1960s and 1970s marked significant advancements in computer technology, leading to the development of CNC machines that could perform complex tasks with high precision and automation.
As industries evolved, so did the technology behind CNC machines. The introduction of 3-axis machines revolutionized manufacturing processes, allowing for greater flexibility and efficiency. Today, the market includes sophisticated 5-axis machines that enable intricate designs and faster production times. This historical context is essential for international buyers to appreciate the technological advancements that influence current pricing and capabilities in the CNC machine sector.
By understanding these market dynamics, sourcing trends, and the importance of sustainability, B2B buyers can navigate the complexities of the CNC machine market more effectively and make informed purchasing decisions that align with their business objectives.
Related Video: Incoterms for beginners | Global Trade Explained
Frequently Asked Questions (FAQs) for B2B Buyers of how much does a cnc machine cost
-
What factors should I consider when vetting CNC machine suppliers?
When vetting CNC machine suppliers, prioritize their industry experience, reputation, and customer reviews. Look for certifications that indicate compliance with international quality standards, such as ISO 9001. Evaluate their capacity for customization based on your specific needs and check their after-sales support services. Request references from previous clients in your region to gauge their reliability and responsiveness, especially for international transactions. -
Can I customize a CNC machine to fit my specific production needs?
Yes, many suppliers offer customization options for CNC machines to meet unique production requirements. This could include modifications in size, capabilities, or additional features. It is crucial to communicate your specifications clearly and work closely with the supplier to ensure that the machine can accommodate your production processes. Be aware that customization may affect lead times and costs. -
What is the minimum order quantity (MOQ) for CNC machines, and how does it impact pricing?
The MOQ for CNC machines can vary significantly between suppliers and the type of machine being purchased. While some manufacturers may have no MOQ for single units, others may require a minimum order to justify production costs. Higher MOQs can lead to bulk pricing discounts, potentially lowering the unit cost. Always inquire about pricing structures and negotiate terms that align with your budget and production plans. -
What are typical lead times for CNC machine orders, especially for international buyers?
Lead times for CNC machines can range from a few weeks to several months, depending on the complexity of the machine and the supplier’s production capacity. For international buyers, consider potential delays related to shipping and customs clearance. It’s advisable to ask the supplier for a detailed timeline and to factor in additional time for any necessary modifications or customizations to avoid production disruptions. -
How can I ensure quality assurance and certifications for CNC machines?
To ensure quality assurance, request documentation of the machine’s certifications and compliance with international standards, such as CE or ISO certifications. Conduct thorough inspections during production, if possible, or arrange for third-party quality control services. Establish clear quality parameters in your contract and consider including warranty clauses that protect against defects and performance issues.
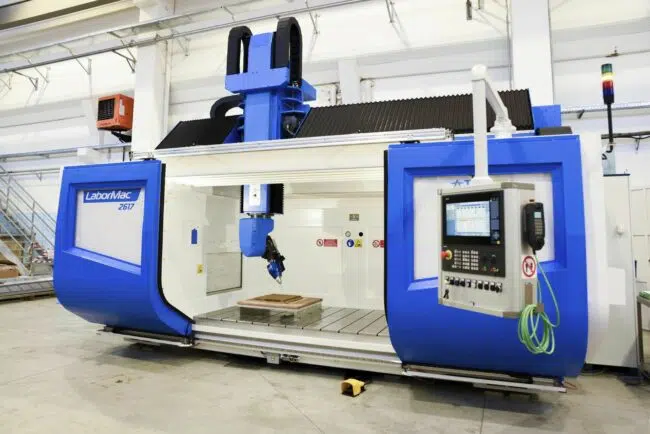
Illustrative Image (Source: Google Search)
-
What logistical considerations should I keep in mind when importing CNC machines?
Logistics for importing CNC machines involve several key considerations, such as shipping methods, customs duties, and local regulations. Choose a reliable freight forwarder experienced in handling heavy machinery to ensure safe transport. Familiarize yourself with import tariffs and taxes in your country to avoid unexpected costs. Additionally, plan for any necessary installation or setup services upon arrival to minimize downtime. -
How do I handle disputes with CNC machine suppliers?
Handling disputes effectively requires a clear communication strategy and an understanding of the terms outlined in your contract. Document all interactions and agreements, and attempt to resolve issues directly with the supplier first. If resolution is not possible, refer to the dispute resolution clause in your contract, which may include mediation or arbitration. Engaging legal counsel familiar with international trade can also provide valuable guidance. -
What payment options are typically available for purchasing CNC machines internationally?
Payment options for international CNC machine purchases may include wire transfers, letters of credit, or payment through escrow services. Each method has its advantages and risks. Letters of credit can provide security for both parties, ensuring that payment is made only when specified conditions are met. Discuss payment terms upfront with the supplier and be wary of upfront payments without guarantees, especially for large investments.
Important Disclaimer & Terms of Use
⚠️ Important Disclaimer
The information provided in this guide, including content regarding manufacturers, technical specifications, and market analysis, is for informational and educational purposes only. It does not constitute professional procurement advice, financial advice, or legal advice.
While we have made every effort to ensure the accuracy and timeliness of the information, we are not responsible for any errors, omissions, or outdated information. Market conditions, company details, and technical standards are subject to change.
B2B buyers must conduct their own independent and thorough due diligence before making any purchasing decisions. This includes contacting suppliers directly, verifying certifications, requesting samples, and seeking professional consultation. The risk of relying on any information in this guide is borne solely by the reader.
Strategic Sourcing Conclusion and Outlook for how much does a cnc machine cost
In summary, understanding the costs associated with CNC machines is crucial for international B2B buyers. The price range can vary significantly, influenced by factors such as machine type, capabilities, brand reputation, and ongoing operational costs. For businesses in Africa, South America, the Middle East, and Europe, strategic sourcing becomes imperative. Prioritize a thorough assessment of your operational needs against the potential return on investment, considering both new and used machines.
Key takeaways include:
– Initial vs. Long-term Costs: Balance upfront costs with long-term operational efficiencies.
– Brand and Model Selection: Invest in reputable brands for reliability and support.
– Training and Maintenance: Factor in the costs of training personnel and maintaining machinery.
As you navigate the CNC machine market, leverage local and international suppliers to negotiate better terms and ensure robust post-purchase support. By making informed decisions today, you can position your business for sustainable growth in an increasingly competitive landscape. Embrace the opportunity to enhance your manufacturing capabilities and drive innovation in your sector.