Master the Market for CNC Foam Cutting Machines: Essential
Introduction: Navigating the Global Market for cnc foam cutting machine
In the fast-evolving landscape of manufacturing, the CNC foam cutting machine stands out as a vital asset for businesses seeking precision, efficiency, and versatility in their production processes. As industries across Africa, South America, the Middle East, and Europe increasingly demand high-quality foam products—ranging from packaging solutions to automotive components—the importance of investing in advanced cutting technologies cannot be overstated. These machines not only enhance productivity but also significantly reduce material wastage, ultimately driving down operational costs.
This comprehensive guide is designed to equip international B2B buyers with essential insights into the global market for CNC foam cutting machines. We will explore various machine types, the materials they process, and critical aspects of manufacturing and quality control. Additionally, we will highlight reputable suppliers, provide a breakdown of costs, and delve into market trends that are shaping the industry.
By leveraging this information, buyers can make informed sourcing decisions that align with their specific operational needs and budgetary constraints. Whether you are a manufacturer in Australia looking for innovative solutions or a business in Saudi Arabia aiming to streamline production, this guide will empower you with the knowledge necessary to navigate the complexities of the CNC foam cutting machine market effectively. Prepare to enhance your competitive edge in a global economy that increasingly values precision and efficiency.
Understanding cnc foam cutting machine Types and Variations
Type Name | Key Distinguishing Features | Primary B2B Applications | Brief Pros & Cons for Buyers |
---|---|---|---|
Hot Wire Foam Cutter | Utilizes heated wire for precise cutting | Sign-making, model making | Pros: Cost-effective, simple operation; Cons: Limited to specific foam types. |
CNC Router | Versatile, can cut various materials including foam | Furniture, packaging, automotive | Pros: High versatility, precision; Cons: Higher initial investment. |
Water Jet Foam Cutter | Uses high-pressure water jets for cutting | Aerospace, automotive prototypes | Pros: Clean cuts, no heat distortion; Cons: Expensive maintenance, high operating costs. |
Laser Foam Cutter | Employs laser technology for intricate designs | Arts & crafts, custom packaging | Pros: High precision, detailed cuts; Cons: Limited thickness capability. |
Oscillating Knife Cutter | Uses a blade that oscillates for cutting | Textile, upholstery, soft materials | Pros: Effective for soft materials; Cons: Slower cutting speed compared to others. |
Hot Wire Foam Cutter
The Hot Wire Foam Cutter is a popular choice for businesses focused on precision and efficiency. It operates by passing a heated wire through foam, allowing for clean and accurate cuts. This type is particularly suitable for applications such as sign-making and model making, where intricate shapes are required. Buyers should consider the specific foam types they work with, as this cutter is limited to certain materials and may not be suitable for thicker or denser foams.
CNC Router
CNC Routers offer a high level of versatility, capable of cutting various materials, including foam, wood, and plastics. This makes them an ideal choice for industries such as furniture manufacturing and automotive production. While the initial investment can be higher than other types, the ability to handle multiple materials and applications can provide significant long-term value. B2B buyers should assess their production needs and potential material diversity to justify the investment.
Water Jet Foam Cutter
Water Jet Foam Cutters utilize high-pressure water jets to achieve precise cuts without introducing heat, which can distort materials. This technology is particularly beneficial in sectors like aerospace and automotive, where precision is paramount. Although they offer clean cuts and are versatile across different materials, the maintenance and operational costs can be high. Buyers should evaluate their budget and the frequency of use to determine if this technology aligns with their operational goals.
Laser Foam Cutter
Laser Foam Cutters are renowned for their ability to create intricate designs and detailed patterns. This type is widely used in industries such as arts and crafts and custom packaging. While they provide exceptional precision, their capability is often limited to thinner materials. B2B buyers should consider their specific project requirements, particularly the thickness of foam they intend to cut, to ensure compatibility with laser technology.
Oscillating Knife Cutter
The Oscillating Knife Cutter is designed for cutting soft materials, making it an excellent choice for textile and upholstery industries. Its oscillating blade allows for smooth cuts, but it may operate at a slower speed compared to other cutting methods. Buyers should weigh the advantages of cutting soft materials against the potential need for faster production speeds, ensuring that this cutter aligns with their operational efficiency goals.
Related Video: Arduino CNC Foam Cutting Machine (Complete Guide)
Key Industrial Applications of cnc foam cutting machine
Industry/Sector | Specific Application of cnc foam cutting machine | Value/Benefit for the Business | Key Sourcing Considerations for this Application |
---|---|---|---|
Furniture Manufacturing | Custom foam shapes for upholstery and cushioning | Enhanced product quality and customization options | Material compatibility, precision requirements, and delivery timelines |
Automotive Industry | Foam components for soundproofing and safety features | Improved vehicle performance and safety standards | Compliance with industry regulations and material durability |
Packaging Solutions | Protective foam inserts for fragile items | Reduced damage during transport and enhanced customer satisfaction | Foam density options, customization capabilities, and cost-effectiveness |
Construction | Insulation panels and foam forms for concrete structures | Energy efficiency and structural integrity | Insulation properties, fire resistance, and local regulations |
Theatrical Productions | Scenic elements and props made from foam | Lightweight, versatile designs with cost savings | Material sourcing for aesthetics, durability, and ease of handling |
Furniture Manufacturing
In the furniture manufacturing sector, CNC foam cutting machines are utilized to create custom foam shapes for upholstery and cushioning. This technology allows manufacturers to produce high-quality, tailored products that meet specific consumer demands. By offering unique designs, businesses can differentiate themselves in a competitive market. Buyers should consider the compatibility of foam materials with their production processes, the precision of cutting needed for intricate designs, and timely delivery schedules to meet consumer demands.
Automotive Industry
CNC foam cutting machines play a crucial role in the automotive industry, where they are used to manufacture foam components that contribute to soundproofing and enhance safety features. These components are essential for improving overall vehicle performance and ensuring compliance with safety regulations. International buyers should focus on sourcing machines that can handle specific material types, adhere to industry standards, and provide durable products that withstand environmental stresses.
Packaging Solutions
In the packaging industry, CNC foam cutting machines are employed to create protective foam inserts for fragile items. This application significantly reduces the risk of damage during transportation, leading to increased customer satisfaction and lower return rates. For B2B buyers, it is important to evaluate the foam density options available, the machine’s ability to customize shapes for different products, and the overall cost-effectiveness of the solutions provided.
Construction
Within the construction sector, CNC foam cutting machines are used to produce insulation panels and foam forms that support concrete structures. These applications are vital for enhancing energy efficiency and ensuring structural integrity in buildings. Buyers from regions with specific insulation requirements should consider the thermal properties of the foam, fire resistance standards, and compliance with local building regulations when sourcing these machines.
Theatrical Productions
CNC foam cutting technology is widely used in theatrical productions to create lightweight scenic elements and props. The versatility of foam allows for creative designs that are both cost-effective and easy to handle. For international buyers in this sector, it is crucial to source materials that balance aesthetics with durability, ensuring that props can withstand the rigors of performance while remaining visually appealing.
Strategic Material Selection Guide for cnc foam cutting machine
When selecting materials for CNC foam cutting machines, it is crucial to consider the specific properties, advantages, and limitations of each material. This analysis will focus on four common materials used in foam cutting applications: Polyurethane Foam, Polystyrene Foam, EVA Foam, and PET Foam. Each material has unique characteristics that can significantly impact performance and suitability for various applications.
Polyurethane Foam
Key Properties: Polyurethane foam is known for its excellent flexibility and resilience. It has a temperature rating of -40°C to 120°C and offers good pressure resistance, making it suitable for various applications.
Pros & Cons: The durability of polyurethane foam is a significant advantage, as it can withstand repeated compression without losing its shape. However, it tends to be more expensive than other foam types, which may affect budget considerations for buyers. The manufacturing complexity is moderate, as it requires specific machinery for optimal cutting.
Impact on Application: Polyurethane foam is widely used in automotive and furniture industries due to its comfort and cushioning properties. It is also compatible with adhesives and coatings, enhancing its versatility.
Considerations for International Buyers: Buyers in regions like Africa and the Middle East should ensure compliance with local environmental regulations, as some polyurethane foams may contain harmful chemicals. Familiarity with standards such as ASTM D3574 can also be beneficial.
Polystyrene Foam
Key Properties: Polystyrene foam features a low density and excellent thermal insulation properties. It can handle temperatures up to 70°C and is resistant to moisture, making it ideal for various applications.
Pros & Cons: Its low cost and ease of manufacturing make polystyrene foam a popular choice for many businesses. However, it is less durable than polyurethane foam and can be more susceptible to damage from UV exposure and chemicals.
Impact on Application: Polystyrene is commonly used in packaging and insulation applications. Its compatibility with various adhesives makes it suitable for layered constructions.
Considerations for International Buyers: Buyers from South America and Europe should be aware of the recycling regulations surrounding polystyrene foam, as some countries have stringent policies. Compliance with standards such as DIN EN 13163 is essential.
EVA Foam
Key Properties: Ethylene-vinyl acetate (EVA) foam is characterized by its excellent elasticity and impact resistance. It can withstand temperatures between -40°C and 80°C and is resistant to UV radiation and chemicals.
Pros & Cons: EVA foam offers a good balance of durability and cost-effectiveness, making it suitable for various applications, including sports equipment and packaging. However, its manufacturing complexity can be higher due to the need for specialized cutting tools.
Impact on Application: EVA foam is widely used in consumer products, providing cushioning and shock absorption. It is compatible with various printing and lamination processes, enhancing its usability.
Considerations for International Buyers: Buyers in Australia and the Middle East should consider the specific applications of EVA foam and ensure compliance with local standards, such as AS/NZS 1530 for fire safety.
PET Foam
Key Properties: Polyethylene terephthalate (PET) foam is known for its high strength-to-weight ratio and excellent chemical resistance. It can operate in temperatures ranging from -60°C to 100°C.
Pros & Cons: The strength and lightweight nature of PET foam make it ideal for structural applications. However, it is generally more expensive than other foam types, which may limit its use in budget-sensitive projects.
Impact on Application: PET foam is commonly used in aerospace and automotive industries due to its lightweight and strong properties. It can be easily laminated with other materials, enhancing its application range.
Considerations for International Buyers: Buyers from Europe should be aware of the stringent recycling and sustainability standards in place for PET materials, such as the European Union’s Waste Framework Directive.
Summary Table
Material | Typical Use Case for cnc foam cutting machine | Key Advantage | Key Disadvantage/Limitation | Relative Cost (Low/Med/High) |
---|---|---|---|---|
Polyurethane Foam | Automotive and furniture cushioning | Excellent durability and resilience | Higher cost compared to other foams | High |
Polystyrene Foam | Packaging and insulation | Low cost and easy to manufacture | Less durable, UV sensitive | Low |
EVA Foam | Sports equipment and packaging | Good elasticity and impact resistance | Higher manufacturing complexity | Medium |
PET Foam | Aerospace and automotive components | High strength-to-weight ratio | Generally higher cost | High |
This guide provides a comprehensive overview of material selection for CNC foam cutting machines, enabling international B2B buyers to make informed decisions based on their specific application needs and regional compliance requirements.
In-depth Look: Manufacturing Processes and Quality Assurance for cnc foam cutting machine
The manufacturing processes and quality assurance measures for CNC foam cutting machines are critical for ensuring that buyers receive reliable, high-performance equipment. Understanding these processes can help international B2B buyers—especially those from Africa, South America, the Middle East, and Europe—make informed purchasing decisions. Below is a detailed overview of the main stages in manufacturing, key techniques used, and the quality control measures that should be considered.
Manufacturing Processes
1. Material Preparation
The first step in manufacturing CNC foam cutting machines involves the careful selection and preparation of materials. Common materials include aluminum for structural components and high-quality steel for frames. The preparation process typically includes:
- Material Inspection: Ensuring that materials meet specified standards before cutting.
- Cutting and Shaping: Utilizing laser cutting or waterjet cutting technologies to shape the components accurately.
- Deburring: Removing sharp edges and imperfections to enhance safety and precision.
2. Forming
Once materials are prepared, the forming stage involves creating the machine’s core components. Techniques used in this stage include:
- CNC Machining: Precision machining is used to create complex shapes and features that are critical for the machine’s operation.
- Welding: For metal components, welding techniques such as MIG or TIG welding are employed to join parts securely.
- Casting: Some components may be cast to achieve desired shapes and properties.
3. Assembly
In the assembly phase, the individual components are brought together to form the complete CNC foam cutting machine. Key activities include:
- Component Integration: Assembling mechanical, electrical, and software components.
- Alignment and Calibration: Ensuring that all parts are correctly aligned and calibrated to function optimally.
- Wiring and Connectivity: Installing electrical wiring and connectivity for control systems, ensuring compliance with safety standards.
4. Finishing
The final stage involves polishing and finishing the machine to enhance its aesthetic and functional qualities. This includes:
- Surface Treatment: Applying coatings, such as powder coating or anodizing, to protect components from corrosion.
- Quality Checks: Conducting initial quality assessments to identify any defects before testing.
Quality Assurance
Quality assurance is a vital component of the manufacturing process for CNC foam cutting machines. It ensures that products meet international standards and satisfy customer expectations.
International Standards
B2B buyers should be aware of the relevant international standards that govern the manufacturing of CNC foam cutting machines. Key standards include:
- ISO 9001: This standard focuses on quality management systems, ensuring that manufacturers consistently meet customer and regulatory requirements.
- CE Marking: A certification that indicates compliance with European health, safety, and environmental protection standards.
- API Standards: Relevant for machines used in specific industries, particularly in oil and gas.
Quality Control Checkpoints
Quality control checkpoints are critical in maintaining high manufacturing standards. Common checkpoints include:
- Incoming Quality Control (IQC): Inspection of raw materials upon receipt to ensure they meet specified criteria.
- In-Process Quality Control (IPQC): Continuous monitoring during the manufacturing process to catch defects early.
- Final Quality Control (FQC): Comprehensive testing of the finished machine to ensure it meets performance specifications.
Common Testing Methods
To verify the quality of CNC foam cutting machines, various testing methods are employed, including:
- Functional Testing: Assessing the machine’s operational performance under different conditions.
- Load Testing: Evaluating the machine’s ability to handle specified loads without failure.
- Durability Testing: Simulating long-term usage to identify potential points of failure.
Verifying Supplier Quality Control
B2B buyers must take proactive steps to verify the quality control measures of potential suppliers. Here are some actionable strategies:
- Supplier Audits: Conducting on-site audits can provide insights into the supplier’s manufacturing processes and quality assurance practices.
- Requesting Quality Reports: Ask for detailed reports on previous quality inspections and testing outcomes.
- Third-Party Inspections: Engaging an independent third-party inspection service can provide an unbiased evaluation of the supplier’s quality control processes.
Quality Control and Certification Nuances
When dealing with international suppliers, it is essential to understand the nuances related to quality control and certifications:
- Cultural and Regulatory Differences: Quality standards may vary significantly between regions. Buyers should familiarize themselves with local regulations and compliance requirements.
- Language Barriers: Ensure that all documentation and communication are clear and available in a language understood by both parties to avoid misunderstandings.
- Adaptation to Local Markets: Suppliers may need to adapt their products to meet the specific needs and preferences of buyers in different regions, such as Africa or the Middle East.
In conclusion, understanding the manufacturing processes and quality assurance measures for CNC foam cutting machines is essential for international B2B buyers. By focusing on material preparation, forming, assembly, and finishing, alongside robust quality control practices, buyers can ensure they select reliable suppliers that meet their operational needs.
Comprehensive Cost and Pricing Analysis for cnc foam cutting machine Sourcing
When sourcing CNC foam cutting machines, understanding the comprehensive cost structure and pricing dynamics is crucial for international B2B buyers. This analysis will help you navigate the complexities involved in procurement, ensuring you make informed decisions that align with your budget and operational needs.
Cost Components
-
Materials: The cost of raw materials, including the foam itself and the components of the CNC machine, can significantly impact pricing. Common materials used in CNC foam cutting machines include aluminum, steel, and high-quality electronic components. Buyers should assess the quality and source of materials, as these factors influence durability and machine performance.
-
Labor: Labor costs can vary significantly based on the manufacturing location. For instance, countries with lower labor costs may offer competitive pricing but could compromise on quality. Understanding the labor market in the supplier’s region can provide insights into potential cost savings or risks.
-
Manufacturing Overhead: This encompasses indirect costs associated with production, such as utilities, rent, and equipment depreciation. Overhead costs can differ between suppliers, affecting the final price of the CNC foam cutting machine.
-
Tooling: Specialized tooling is often required for manufacturing CNC machines. The cost of these tools can be substantial and may be included in the overall pricing. Custom tooling for specific designs or functionalities will also increase costs.
-
Quality Control (QC): Implementing rigorous QC processes is essential to ensure machine reliability and performance. Suppliers who prioritize QC may charge higher prices, but this can lead to long-term savings by reducing maintenance and replacement costs.
-
Logistics: The cost of transporting the machine to the buyer’s location is a critical factor. Logistics costs can fluctuate based on distance, shipping methods, and local tariffs. It’s advisable to consider logistics when evaluating supplier quotes to avoid unexpected expenses.
-
Margin: Suppliers typically build in a profit margin, which can vary based on market competition and perceived value. Understanding typical margins in the industry can help buyers negotiate better deals.
Price Influencers
Several factors can influence the pricing of CNC foam cutting machines:
-
Volume/MOQ: The minimum order quantity (MOQ) can affect pricing. Bulk orders usually attract discounts, so it’s beneficial to collaborate with other buyers or plan for future needs.
-
Specifications/Customization: Custom features or specifications can lead to higher costs. Buyers should balance the need for customization against budget constraints.
-
Materials and Quality Certifications: Machines built with higher-quality materials and recognized quality certifications (e.g., ISO standards) typically command higher prices. However, these investments can result in lower maintenance costs and longer lifespan.
-
Supplier Factors: The reputation and reliability of the supplier can influence pricing. Established suppliers may charge a premium due to their proven track record.
-
Incoterms: Understanding Incoterms is crucial for managing shipping costs and responsibilities. Choosing the right Incoterm can affect the total landed cost of the machine.
Buyer Tips
-
Negotiation: Effective negotiation can lead to significant cost savings. Be prepared to discuss volume, payment terms, and delivery timelines to leverage better pricing.
-
Cost-Efficiency: Consider the Total Cost of Ownership (TCO), which includes purchase price, maintenance, energy consumption, and resale value. A lower initial price may not always equate to overall savings.
-
Pricing Nuances: International buyers should be aware of currency fluctuations, tariffs, and local economic conditions that may affect machine prices. Engaging with suppliers familiar with your region can provide insights into these factors.
-
Research and Compare: Always compare multiple suppliers and their offerings. This helps ensure you receive a competitive price while meeting your quality and service expectations.
Disclaimer
The prices and analyses provided in this guide are indicative and subject to change based on market conditions, supplier negotiations, and other factors. Always conduct thorough research and obtain multiple quotes to ensure accurate budgeting for your CNC foam cutting machine sourcing needs.
Essential Technical Properties and Trade Terminology for cnc foam cutting machine
Understanding the essential technical properties and trade terminology associated with CNC foam cutting machines is crucial for international B2B buyers. This knowledge not only aids in making informed purchasing decisions but also fosters clearer communication with suppliers and manufacturers. Below are the critical specifications and common trade terms that buyers should be familiar with.
Essential Technical Properties
-
Material Grade
– The material grade refers to the type and quality of foam that the CNC machine can cut. Common materials include polystyrene, polyethylene, and polyurethane. Understanding the material grade is vital because it affects the durability and application of the final product. Buyers must ensure that the machine can handle the specific foam types relevant to their industry, whether for packaging, insulation, or artistic design. -
Cutting Tolerance
– Cutting tolerance indicates the precision with which the machine can cut foam. It is typically measured in millimeters or inches and can range from ±0.5 mm to ±0.1 mm or better. High cutting tolerance is essential for applications requiring intricate designs or tight fitting components, such as in automotive or aerospace industries. Buyers should assess their project requirements to select a machine that meets the necessary precision standards. -
Cutting Speed
– Cutting speed refers to the rate at which the CNC machine can process the foam material, often measured in meters per minute. A higher cutting speed can lead to increased productivity and reduced operational costs. However, it’s important to balance speed with cutting quality. B2B buyers should evaluate their production volume and desired throughput when selecting a machine. -
Power Consumption
– Power consumption is a critical factor, especially for businesses focused on sustainability and operational cost reduction. Machines with lower power requirements can significantly reduce energy bills over time. Buyers should look for machines that offer efficient energy use without compromising performance, particularly in regions where electricity costs are high.
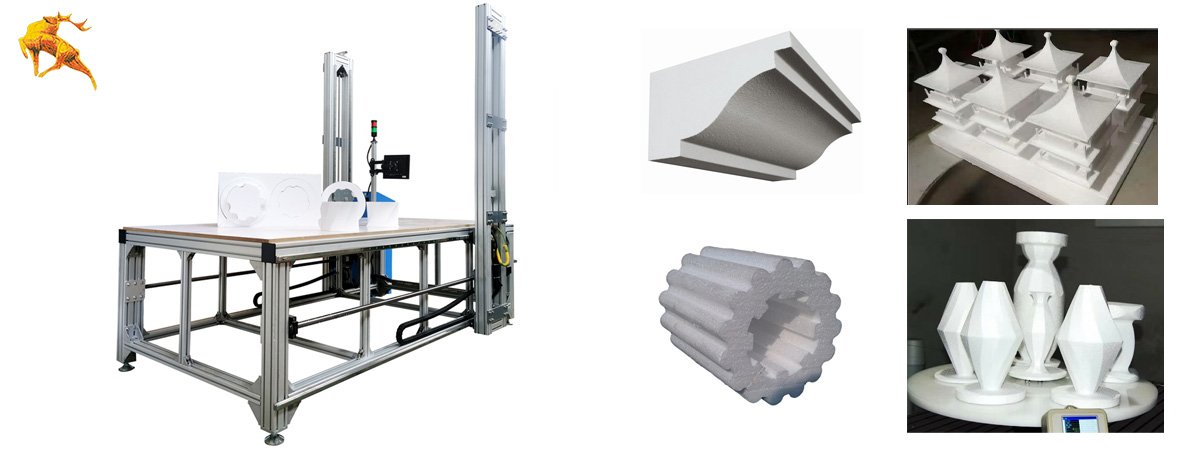
Illustrative Image (Source: Google Search)
- Software Compatibility
– The software used to operate CNC foam cutting machines can vary widely. Compatibility with industry-standard CAD/CAM software is essential for seamless integration into existing workflows. Buyers should ensure that the machine’s software supports the file formats they commonly use to avoid additional costs and time delays.
Common Trade Terminology
-
OEM (Original Equipment Manufacturer)
– OEM refers to companies that produce parts or equipment that may be marketed by another manufacturer. Understanding OEM relationships is crucial for buyers looking for customized solutions or specific machine components. It ensures that buyers are sourcing from reputable manufacturers who meet industry standards. -
MOQ (Minimum Order Quantity)
– MOQ is the smallest number of units a supplier is willing to sell. This term is particularly important for buyers who may only need a small quantity of machines or parts. Knowing the MOQ helps buyers budget effectively and avoid overcommitting to unnecessary inventory. -
RFQ (Request for Quotation)
– An RFQ is a document used to invite suppliers to bid on providing specific goods or services. It is a formal way to gather pricing and terms from multiple suppliers, allowing buyers to compare options efficiently. Properly crafting an RFQ can lead to better pricing and terms. -
Incoterms (International Commercial Terms)
– Incoterms are a series of predefined commercial terms published by the International Chamber of Commerce (ICC) that clarify the responsibilities of buyers and sellers in international transactions. Familiarity with Incoterms helps buyers understand shipping costs, risk transfer, and insurance responsibilities, which is crucial for smooth cross-border transactions. -
Lead Time
– Lead time refers to the amount of time it takes from placing an order until the goods are delivered. Understanding lead times is essential for planning and inventory management. Buyers should factor in lead times when coordinating production schedules to avoid delays.
By familiarizing themselves with these essential technical properties and trade terms, international B2B buyers can make more informed decisions when sourcing CNC foam cutting machines, ultimately improving their operational efficiency and product quality.
Navigating Market Dynamics, Sourcing Trends, and Sustainability in the cnc foam cutting machine Sector
Market Overview & Key Trends
The CNC foam cutting machine sector is witnessing transformative growth driven by several global dynamics. Key drivers include the increasing demand for customized foam products across industries such as automotive, aerospace, and packaging. As these sectors expand in regions like Africa, South America, the Middle East, and Europe, international B2B buyers are presented with a unique opportunity to tap into a growing market.
Emerging technologies, particularly automation and Industry 4.0, are reshaping sourcing trends. CNC machines equipped with advanced software and IoT capabilities enable real-time monitoring and data analytics, enhancing operational efficiency. Buyers should consider suppliers that offer machines with integrated smart technology, as these features can significantly reduce waste and enhance production speed. Additionally, the shift towards online marketplaces for sourcing is becoming prevalent. Platforms that facilitate direct manufacturer-buyer interactions can streamline procurement processes and reduce costs.
Market dynamics are also influenced by geopolitical factors and trade agreements. For instance, trade partnerships between Europe and Africa are fostering cross-border investments in manufacturing technologies. Buyers should remain informed about these agreements, as they can lead to favorable sourcing conditions and potentially lower tariffs.
Sustainability & Ethical Sourcing in B2B
Sustainability is becoming a cornerstone of purchasing decisions in the CNC foam cutting machine sector. As environmental regulations tighten globally, B2B buyers must consider the ecological impact of their sourcing choices. The production of foam materials often involves the use of harmful chemicals; thus, sourcing machines that promote cleaner production processes is essential.
Ethical supply chains are increasingly important. Buyers should prioritize suppliers that demonstrate transparency in their sourcing practices and adhere to environmental regulations. Certifications such as ISO 14001 for environmental management and the Global Organic Textile Standard (GOTS) for organic materials can serve as indicators of a supplier’s commitment to sustainability.
Moreover, the use of recyclable materials in foam production is gaining traction. B2B buyers should seek out CNC foam cutting machines that can efficiently handle eco-friendly materials, thus reducing waste and promoting circular economy practices. Engaging with manufacturers that prioritize sustainability not only aligns with corporate social responsibility goals but also enhances brand reputation in increasingly eco-conscious markets.
Brief Evolution/History
The evolution of CNC foam cutting machines began in the mid-20th century with the advent of computer numerical control technology. Initially, these machines were primarily used in industrial settings for basic foam cutting tasks. However, as industries evolved, so did the technology.
In the late 1990s and early 2000s, advancements in software and hardware enabled the production of more intricate designs, expanding applications into diverse sectors such as architecture, automotive, and consumer goods. Today, CNC foam cutting machines are sophisticated tools that offer precision, speed, and efficiency, allowing B2B buyers to meet the growing demands of customization and sustainability in their respective markets. Understanding this evolution is critical for buyers looking to invest in the latest technologies that align with industry trends and consumer expectations.
Frequently Asked Questions (FAQs) for B2B Buyers of cnc foam cutting machine
-
What should I consider when vetting suppliers for CNC foam cutting machines?
When vetting suppliers, prioritize their experience in manufacturing CNC foam cutting machines and their reputation in international markets. Check for customer reviews and testimonials from businesses similar to yours. Request detailed information on their production capacity, quality control processes, and after-sales support. Certifications such as ISO 9001 can indicate adherence to international quality standards. Additionally, consider their responsiveness and willingness to provide references, which can give insights into their reliability and customer service. -
Can CNC foam cutting machines be customized to meet specific needs?
Yes, many suppliers offer customization options for CNC foam cutting machines. When discussing your requirements, be specific about the types of foam materials you will be cutting, the dimensions needed, and any particular features or software compatibility. Customization may affect the lead time and pricing, so ensure you communicate clearly to align expectations. Inquire about the supplier’s previous customization projects to gauge their capability and creativity in meeting unique specifications. -
What are the typical minimum order quantities (MOQ) and lead times for CNC foam cutting machines?
MOQs for CNC foam cutting machines can vary significantly by supplier, often ranging from one unit for smaller manufacturers to bulk orders for larger firms. Lead times also depend on the complexity of the machine and the supplier’s current production capacity. Generally, expect anywhere from a few weeks to several months. It’s vital to confirm these details before placing an order, as longer lead times can impact your project timelines. Consider negotiating MOQs or exploring suppliers with flexible options that suit your purchasing strategy. -
What payment terms should I expect when purchasing CNC foam cutting machines internationally?
Payment terms can vary widely depending on the supplier and the countries involved. Common practices include upfront deposits (often 30-50%), with the balance due before shipment or upon delivery. Some suppliers may offer financing options or extended payment terms for larger orders. It’s crucial to clarify payment methods accepted, such as wire transfers or letters of credit, as well as any potential fees. Ensure that all payment terms are documented in the contract to avoid disputes later. -
How can I ensure quality assurance and certifications for the machines I purchase?
Request documentation of quality assurance processes and relevant certifications from suppliers. Look for ISO certifications, CE markings, or other industry-specific standards that indicate compliance with international quality norms. Ask about their testing procedures, including performance and safety tests conducted on the machines. Some suppliers may offer a warranty or guarantee period, which can provide additional assurance of the machine’s quality. Consider visiting the factory or requesting a video demonstration to inspect quality firsthand. -
What logistics considerations should I keep in mind when importing CNC foam cutting machines?
Logistics is a critical aspect of international purchases. First, determine the shipping methods available, including air freight for quicker delivery or sea freight for cost-effective options. Understand the incoterms (International Commercial Terms) being offered, which define the responsibilities of both buyer and seller regarding shipping and customs clearance. Be aware of import duties and taxes that may apply in your country. Collaborating with a freight forwarder can help streamline the logistics process and ensure compliance with all regulations. -
How should I handle disputes or issues with suppliers after the purchase?
Establishing a clear communication channel with your supplier is essential for resolving disputes effectively. Document all agreements and communications to provide a reference in case issues arise. If problems occur, address them promptly and professionally, presenting evidence and specific details about the issue. Most reputable suppliers will have a process for handling complaints or warranty claims. If necessary, consider involving a third-party mediator or arbitration to resolve significant disputes, particularly in international contexts where legal systems may differ. -
What are the best practices for maintenance and support for CNC foam cutting machines?
Regular maintenance is crucial to ensure the longevity and efficiency of CNC foam cutting machines. Consult the supplier for recommended maintenance schedules and procedures, including routine inspections and software updates. Ensure you have access to technical support, whether through a local representative or online resources. Training your staff on proper operation and maintenance practices can significantly reduce the risk of breakdowns. Additionally, keeping spare parts on hand can minimize downtime in case of unexpected repairs, ensuring your production remains uninterrupted.
Important Disclaimer & Terms of Use
⚠️ Important Disclaimer
The information provided in this guide, including content regarding manufacturers, technical specifications, and market analysis, is for informational and educational purposes only. It does not constitute professional procurement advice, financial advice, or legal advice.
While we have made every effort to ensure the accuracy and timeliness of the information, we are not responsible for any errors, omissions, or outdated information. Market conditions, company details, and technical standards are subject to change.
B2B buyers must conduct their own independent and thorough due diligence before making any purchasing decisions. This includes contacting suppliers directly, verifying certifications, requesting samples, and seeking professional consultation. The risk of relying on any information in this guide is borne solely by the reader.
Strategic Sourcing Conclusion and Outlook for cnc foam cutting machine
In conclusion, the strategic sourcing of CNC foam cutting machines presents a unique opportunity for international B2B buyers, particularly those in Africa, South America, the Middle East, and Europe. By understanding the nuances of the global market, buyers can leverage competitive pricing, advanced technology, and reliable suppliers to enhance their operational efficiency and product offerings.
Key takeaways include the importance of evaluating suppliers based on their technological capabilities, customer support, and local market knowledge. Engaging in thorough due diligence will not only mitigate risks but also foster long-term partnerships that can drive innovation and cost savings. Additionally, considering local regulations and market trends is crucial for aligning sourcing strategies with regional demands.
As we look to the future, the adoption of sustainable practices and the integration of automation will likely shape the CNC foam cutting landscape. Buyers are encouraged to stay informed about emerging technologies and industry shifts, ensuring they remain competitive.
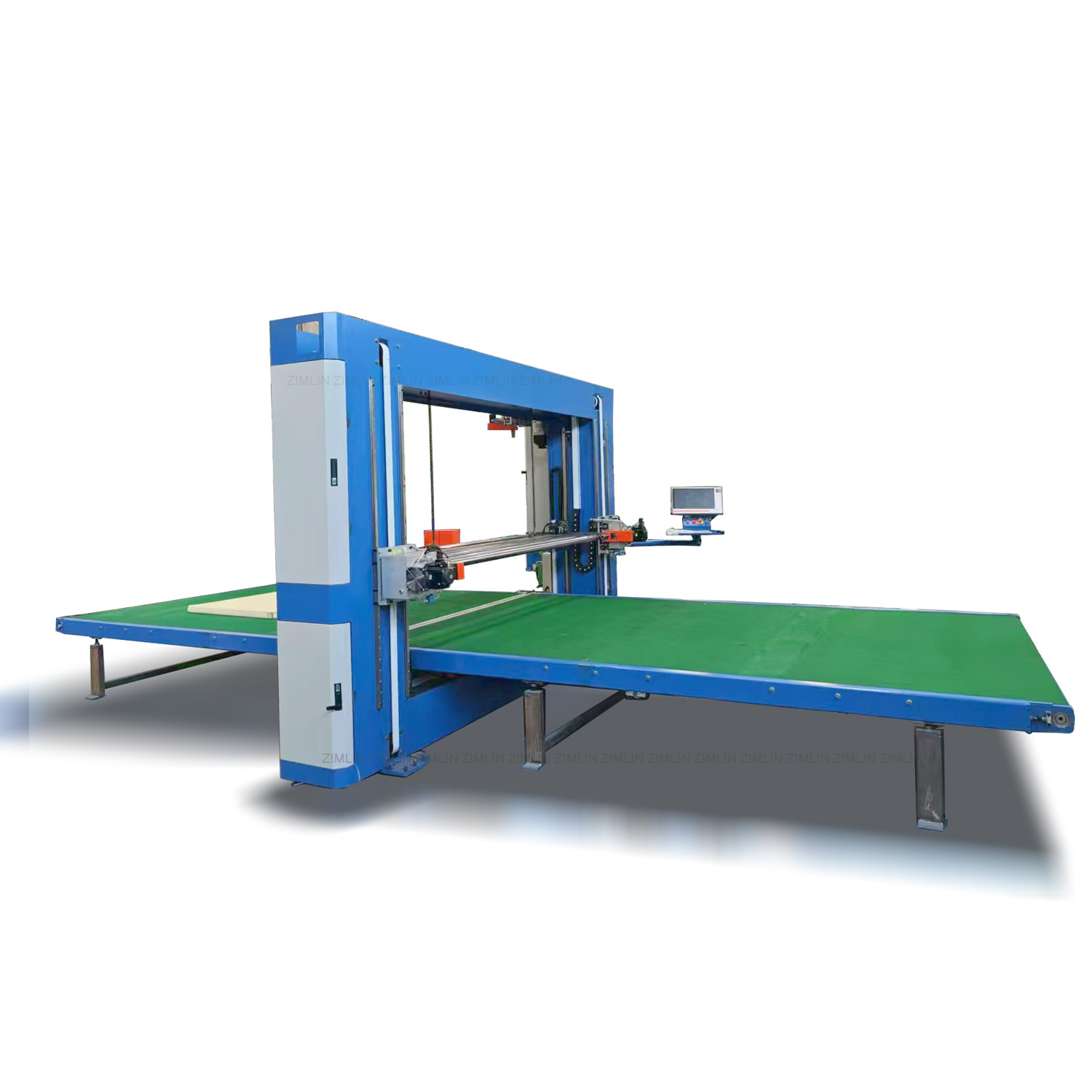
Illustrative Image (Source: Google Search)
Take action now—explore potential suppliers, assess your sourcing strategies, and invest in the right technology to position your business for success in an evolving marketplace. The time to act is now, as opportunities abound for those ready to innovate and adapt.