Master the Market for Portable CNC Plasma Cutting Machines
Introduction: Navigating the Global Market for portable cnc plasma cutting machine
In today’s rapidly evolving industrial landscape, the portable CNC plasma cutting machine has emerged as a critical asset for businesses seeking efficiency, precision, and adaptability. This versatile tool not only enhances productivity but also enables manufacturers to tackle a diverse range of materials, from mild steel to aluminum, with unparalleled accuracy. For international B2B buyers, particularly those in Africa, South America, the Middle East, and Europe, understanding the nuances of this technology is essential for making informed sourcing decisions.
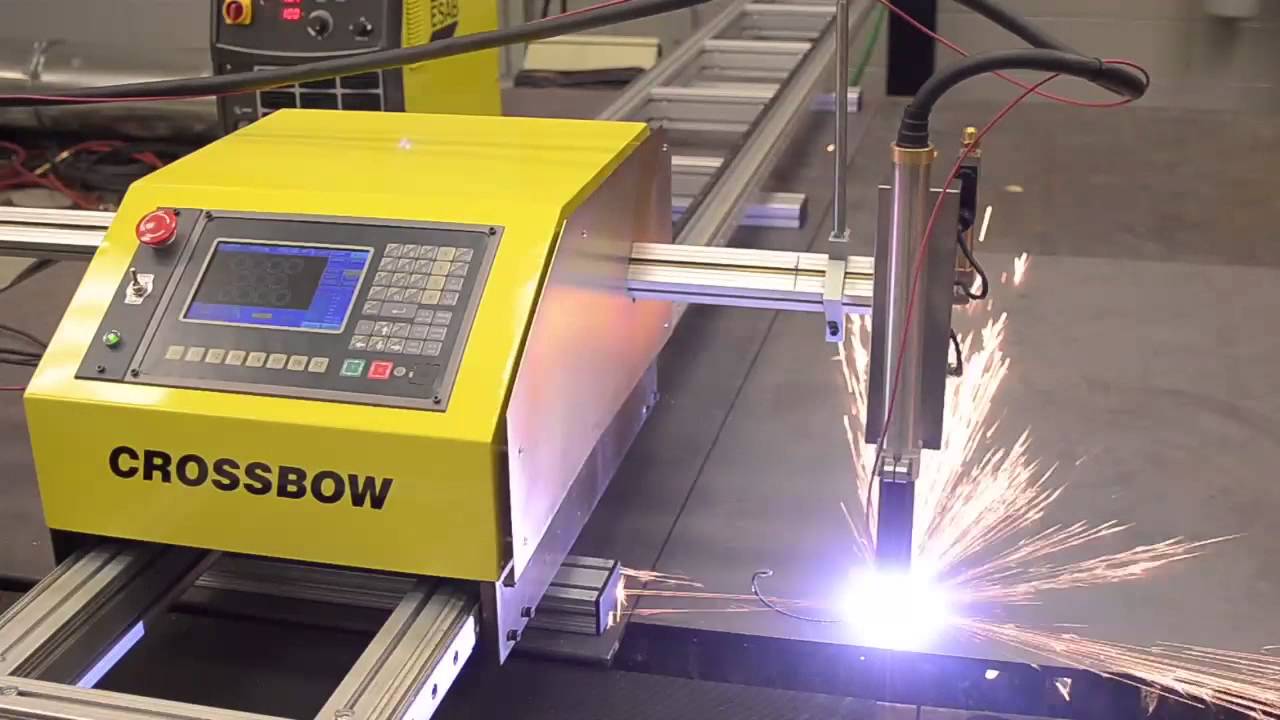
Illustrative Image (Source: Google Search)
This comprehensive guide serves as a roadmap for navigating the global market of portable CNC plasma cutting machines. It covers essential topics including the various types of machines available, the materials they can effectively cut, and the manufacturing and quality control processes that ensure reliability. Additionally, we delve into supplier options, cost considerations, and market trends that can influence purchasing decisions.
By equipping buyers with actionable insights and a deeper understanding of the portable CNC plasma cutting machine landscape, this guide empowers businesses to identify the right solutions tailored to their operational needs. Whether you are a small workshop in Indonesia or a large-scale manufacturer in the UK, this resource aims to enhance your procurement strategy, ensuring you stay competitive in the global marketplace. With the right knowledge, you can confidently invest in technology that drives innovation and efficiency in your operations.
Understanding portable cnc plasma cutting machine Types and Variations
Type Name | Key Distinguishing Features | Primary B2B Applications | Brief Pros & Cons for Buyers |
---|---|---|---|
Handheld CNC Plasma Cutter | Lightweight, portable design; manual operation | Small workshops, on-site repairs | Pros: Affordable, easy to use. Cons: Limited precision compared to larger models. |
Gantry-style Portable Cutter | Fixed gantry structure; larger cutting area | Construction sites, metal fabrication | Pros: High precision, suitable for larger materials. Cons: Less portable, requires setup space. |
Desktop CNC Plasma Cutter | Compact size; designed for small-scale projects | Prototyping, small batch production | Pros: Space-efficient, good for detailed work. Cons: Limited cutting thickness. |
Automated Portable Plasma Cutter | Advanced automation features; remote operation capabilities | Mass production, industrial applications | Pros: High efficiency, reduces labor costs. Cons: Higher initial investment. |
Hybrid Plasma Cutter | Combines plasma and other cutting technologies | Versatile applications across industries | Pros: Multi-functional, adaptable to various materials. Cons: Complexity may require specialized training. |
Handheld CNC Plasma Cutter
The handheld CNC plasma cutter is designed for portability and ease of use, making it ideal for small workshops and on-site repairs. Its lightweight structure allows operators to maneuver the device easily, providing flexibility for various cutting tasks. When considering a purchase, buyers should evaluate the cutter’s cutting speed and thickness capabilities, as these can significantly impact productivity and efficiency in smaller projects.
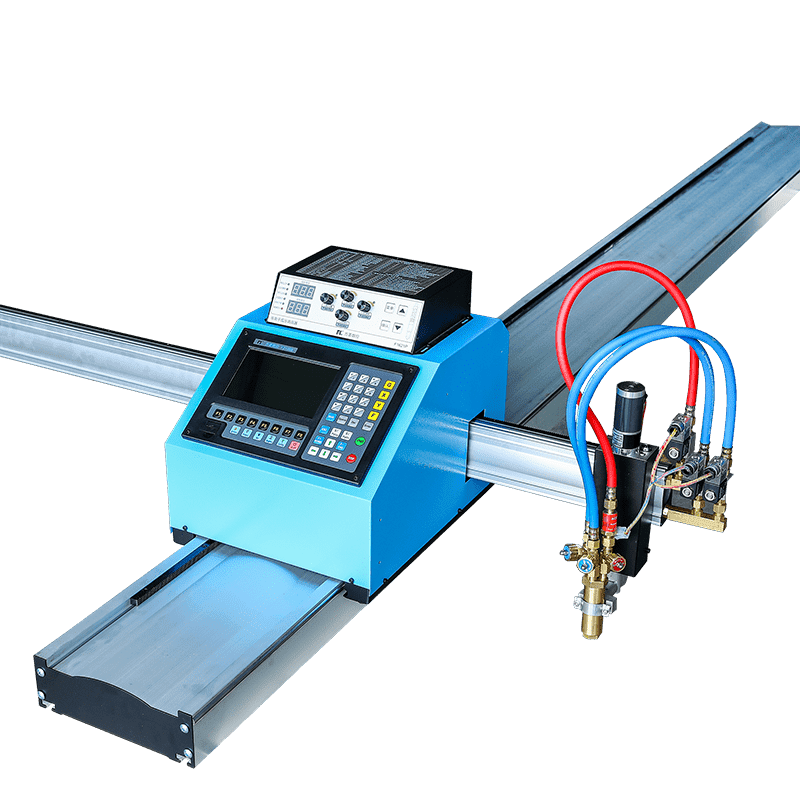
Illustrative Image (Source: Google Search)
Gantry-style Portable Cutter
Gantry-style portable cutters feature a fixed gantry structure that allows for a larger cutting area, making them suitable for construction sites and metal fabrication. These machines excel in precision and are capable of handling substantial materials, which is essential for larger-scale operations. Buyers should consider the machine’s setup requirements and space needs, as these can influence operational efficiency and project timelines.
Desktop CNC Plasma Cutter
The desktop CNC plasma cutter is compact and designed for small-scale projects, making it perfect for prototyping and small batch production. Its space-efficient design allows it to fit into limited workspaces, while still providing the accuracy needed for detailed work. B2B buyers should assess the cutter’s cutting thickness and material compatibility to ensure it meets their specific production needs.
Automated Portable Plasma Cutter
Automated portable plasma cutters incorporate advanced automation features and remote operation capabilities, making them suitable for mass production and industrial applications. These machines enhance efficiency and can significantly reduce labor costs, appealing to businesses aiming for scalability. However, buyers must weigh the higher initial investment against long-term savings and increased output.
Hybrid Plasma Cutter
Hybrid plasma cutters combine plasma technology with other cutting methods, offering versatility across various industries. This adaptability allows them to handle different materials and thicknesses, making them a valuable asset for businesses with diverse cutting needs. Buyers should consider the complexity of operation and the potential requirement for specialized training, which could impact the overall return on investment.
Related Video: HNC-1500W-J-3 portable cnc plasma cutting machine install and operation Video
Key Industrial Applications of portable cnc plasma cutting machine
Industry/Sector | Specific Application of portable cnc plasma cutting machine | Value/Benefit for the Business | Key Sourcing Considerations for this Application |
---|---|---|---|
Metal Fabrication | Cutting complex shapes in sheet metal | Increases precision and reduces material waste | Ensure compatibility with local voltage and power supply |
Construction | Fabricating steel structures on-site | Enhances project timelines and reduces transportation costs | Look for machines with portability and ease of setup |
Automotive | Custom part manufacturing for repairs and modifications | Allows for rapid prototyping and reduced downtime | Assess the machine’s speed and cutting thickness capacity |
Shipbuilding | Cutting hull sections and components | Improves efficiency in large-scale production | Consider corrosion resistance and durability of the machine |
Art and Design | Creating intricate designs for metal art | Expands creative possibilities and product offerings | Evaluate software compatibility for design specifications |
Metal Fabrication
In the metal fabrication industry, portable CNC plasma cutting machines are essential for cutting complex shapes from sheet metal. These machines enable fabricators to achieve high precision while minimizing material waste, which is crucial for maintaining profitability. For B2B buyers, particularly in regions like Africa and South America, sourcing machines that can operate under varying power conditions is vital. Additionally, buyers should consider service and support availability to ensure operational efficiency.
Construction
In construction, portable CNC plasma cutters are used for on-site fabrication of steel structures. This application significantly enhances project timelines by allowing immediate adjustments and customizations without the need to transport materials to a centralized facility. Businesses benefit from reduced transportation costs and improved workflow. Buyers in the Middle East and Europe should prioritize models that are lightweight and easy to set up, as well as those that comply with local safety regulations.
Automotive
The automotive industry employs portable CNC plasma cutting machines for custom part manufacturing, especially for repairs and modifications. These machines facilitate rapid prototyping, enabling automotive businesses to minimize downtime and respond quickly to customer needs. For international buyers, particularly in developing regions, it is important to assess the machine’s cutting speed and thickness capacity to ensure it meets the specific requirements of automotive applications.
Shipbuilding
In shipbuilding, portable CNC plasma cutters are invaluable for cutting hull sections and various components. Their efficiency in large-scale production helps shipbuilders meet tight deadlines and manage costs effectively. Buyers should consider the machine’s resistance to corrosion and durability, as these factors are critical in maritime environments. Additionally, understanding the local supply chain for parts and maintenance services can enhance operational reliability.
Art and Design
In the art and design sector, portable CNC plasma cutting machines are utilized to create intricate metal art and decorative pieces. This application expands creative possibilities for artists and designers, allowing them to produce unique offerings that attract customers. For B2B buyers in Europe and South America, evaluating the machine’s software compatibility is essential to ensure it can handle various design specifications. Furthermore, training and support for artists new to CNC technology can be a valuable consideration in the purchasing process.
Related Video: Crossbow Portable CNC Plasma Cutting Machine (English)
Strategic Material Selection Guide for portable cnc plasma cutting machine
When selecting materials for portable CNC plasma cutting machines, it’s crucial to understand how different materials can affect performance, durability, and overall application suitability. Below is an analysis of three common materials used in the construction of these machines, focusing on their properties, advantages, disadvantages, and considerations for international B2B buyers.
Steel
Key Properties: Steel is known for its high tensile strength and durability. It can withstand high temperatures and pressures, making it suitable for heavy-duty applications. Additionally, it offers good corrosion resistance when treated properly.
Pros & Cons: The primary advantage of steel is its robustness, which translates to longevity and reliability in tough environments. However, it can be heavier than other materials, which may affect portability. Steel’s cost is generally moderate, but manufacturing complexity can increase with custom designs or treatments.
Impact on Application: Steel is ideal for cutting thicker materials and is compatible with a wide range of media, including mild steel, stainless steel, and aluminum. Its durability makes it suitable for industrial applications where precision and strength are paramount.
Considerations for International Buyers: Buyers should ensure compliance with international standards such as ASTM for steel quality. In regions like Africa and South America, sourcing local steel can reduce costs and lead times, while European buyers may prioritize certifications that guarantee material quality.
Aluminum
Key Properties: Aluminum is lightweight and has excellent corrosion resistance. It can operate effectively at lower temperatures, which is beneficial for specific cutting applications.
Pros & Cons: The lightweight nature of aluminum enhances the portability of CNC plasma cutting machines, making them easier to transport and maneuver. However, aluminum is generally less durable than steel, which can limit its use in high-stress applications. The cost of aluminum is typically higher than that of steel, especially for high-grade alloys.
Impact on Application: Aluminum is particularly suited for cutting softer materials and is often used in automotive and aerospace applications. Its compatibility with various alloys can expand the range of projects a machine can handle.
Considerations for International Buyers: Buyers should be aware of regional availability and pricing fluctuations in aluminum. Compliance with standards such as DIN and JIS is essential, particularly in Europe and Asia, where material specifications are strictly regulated.
Composite Materials
Key Properties: Composite materials, such as fiberglass-reinforced plastics, offer a unique combination of lightweight characteristics and high strength. They are resistant to corrosion and can withstand various environmental conditions.
Pros & Cons: The primary advantage of composites is their versatility and customization potential, allowing for tailored solutions for specific applications. However, they can be more expensive to manufacture and may require specialized knowledge for proper handling and maintenance.
Impact on Application: Composites are suitable for specialized applications, such as cutting intricate designs in non-metal materials. They are often used in industries like aerospace and marine, where weight savings are critical.
Considerations for International Buyers: Buyers should ensure that composite materials meet local and international standards for safety and performance. In regions like the Middle East, where environmental conditions can be harsh, selecting high-quality composites is vital for ensuring longevity and performance.
Summary Table
Material | Typical Use Case for portable cnc plasma cutting machine | Key Advantage | Key Disadvantage/Limitation | Relative Cost (Low/Med/High) |
---|---|---|---|---|
Steel | Heavy-duty industrial applications | High durability and strength | Heavier, can affect portability | Medium |
Aluminum | Automotive and aerospace applications | Lightweight, easy to transport | Less durable than steel | High |
Composite Materials | Specialized applications in aerospace and marine | Versatile and customizable | Higher manufacturing costs, specialized care | High |
This guide provides a foundation for international B2B buyers to make informed decisions about material selection for portable CNC plasma cutting machines, considering both performance and regional market dynamics.
In-depth Look: Manufacturing Processes and Quality Assurance for portable cnc plasma cutting machine
The manufacturing of portable CNC plasma cutting machines involves several critical stages, each designed to ensure efficiency, precision, and reliability. Understanding these processes is essential for B2B buyers who wish to source high-quality equipment that meets their operational needs.
Manufacturing Processes
Material Preparation
The first stage in manufacturing involves selecting and preparing raw materials, typically high-grade steel or aluminum. The choice of material is crucial, as it directly affects the machine’s durability and cutting performance. Materials undergo processes such as:
- Cutting: Sheets are cut to size using laser or water jet methods to ensure precision.
- Surface Treatment: Processes like sandblasting or chemical cleaning are employed to remove impurities and enhance adhesion for subsequent coatings.
Forming
In this stage, the prepared materials are shaped into components. Techniques used in forming include:
- CNC Machining: This ensures that parts are accurately shaped according to design specifications. CNC lathes and milling machines are commonly used.
- Bending and Welding: Components are bent into required shapes and welded together to form the frame of the machine. High-quality welding techniques are vital for structural integrity.
Assembly
The assembly phase is where all the individual components come together. Key steps include:
- Sub-Assembly: Smaller groups of parts are assembled first, such as the gantry and cutting head. This allows for easier handling and troubleshooting.
- Integration of Electronics: The CNC control system, including software, is integrated into the machine. This ensures that the machine can execute cutting operations with high precision.
- Final Assembly: The complete machine is assembled, and all components are aligned and secured.
Finishing
Finishing processes enhance the machine’s appearance and protect it from environmental factors. Techniques include:
- Painting and Coating: Powder coating or painting is applied for aesthetic appeal and corrosion resistance.
- Quality Checks: Initial quality checks are conducted to ensure that all parts fit correctly and operate smoothly before the machine is subjected to final testing.
Quality Assurance
Quality assurance is a cornerstone of the manufacturing process, ensuring that the final product meets both international and industry-specific standards.
International Standards
For B2B buyers, understanding the relevant quality standards is critical. Key standards include:
- ISO 9001: This standard focuses on quality management systems and is applicable across various industries. It ensures that manufacturers consistently produce products that meet customer and regulatory requirements.
- CE Marking: Particularly relevant for buyers in Europe, CE marking indicates that the product meets EU safety, health, and environmental protection standards.
- API Standards: For those in the oil and gas sector, adherence to American Petroleum Institute standards is crucial.
Quality Control Checkpoints
Quality control (QC) involves several checkpoints throughout the manufacturing process:
- Incoming Quality Control (IQC): Raw materials are inspected upon arrival to ensure they meet specified standards.
- In-Process Quality Control (IPQC): Ongoing inspections during the manufacturing process help identify any deviations from quality standards in real-time.
- Final Quality Control (FQC): The finished product undergoes thorough testing to ensure it meets all specifications before shipping.
Common Testing Methods
Various testing methods are employed to ensure the quality and reliability of portable CNC plasma cutting machines:
- Functional Testing: This tests the machine’s operational capabilities, ensuring it performs as expected under different conditions.
- Load Testing: Machines are subjected to stress tests to verify their durability and performance under maximum load conditions.
- Electrical Safety Testing: Ensures that all electronic components are safe and comply with relevant electrical standards.
Verifying Supplier Quality Control
For international B2B buyers, verifying a supplier’s quality control processes is essential to mitigate risks associated with sourcing equipment. Here are actionable insights:
- Supplier Audits: Conducting on-site audits allows buyers to observe the manufacturing processes and quality control measures first-hand. This is particularly important for buyers from Africa and South America, where local practices may vary.
- Requesting Quality Reports: Buyers should ask suppliers for detailed QC reports that document compliance with relevant standards and testing results.
- Third-Party Inspections: Engaging third-party inspection services can provide an unbiased assessment of the manufacturer’s QC processes and the quality of the final product.
Quality Control Nuances for International Buyers
Understanding the nuances of quality control can significantly impact sourcing decisions:
- Regulatory Differences: Buyers must be aware of the regulatory requirements specific to their regions. For instance, the CE marking is crucial for European buyers, while API standards may be more relevant to those in the Middle East’s oil and gas sector.
- Cultural Expectations: Quality perceptions can differ by region. Buyers from Europe may have higher expectations regarding precision and aesthetics compared to those in Africa or South America, where functionality may take precedence.
- Communication: Clear communication regarding quality expectations and standards is vital. Buyers should ensure that suppliers understand their specific needs and compliance requirements.
Conclusion
Navigating the manufacturing processes and quality assurance protocols for portable CNC plasma cutting machines is essential for B2B buyers aiming to make informed purchasing decisions. By understanding these intricacies, buyers can enhance their sourcing strategies, ensuring they acquire reliable, high-quality equipment that meets international standards.
Comprehensive Cost and Pricing Analysis for portable cnc plasma cutting machine Sourcing
When sourcing portable CNC plasma cutting machines, understanding the comprehensive cost structure and pricing dynamics is essential for international B2B buyers, especially from Africa, South America, the Middle East, and Europe. This analysis will delve into the various cost components, price influencers, and practical tips for negotiating and ensuring cost efficiency.
Cost Components
-
Materials: The primary materials in a portable CNC plasma cutting machine include steel, aluminum, and electronic components. The quality of these materials directly impacts the machine’s performance and longevity. Buyers should evaluate suppliers based on material certifications to ensure they meet industry standards.
-
Labor: Labor costs vary significantly by region. For instance, labor in Southeast Asia may be less expensive than in Europe, impacting the overall manufacturing cost. Consideration of skilled versus unskilled labor is crucial, particularly in the assembly and quality control processes.
-
Manufacturing Overhead: This includes costs associated with running the manufacturing facility, such as utilities, rent, and administrative expenses. A supplier’s location can influence these costs; for example, factories in regions with lower overhead costs can offer more competitive pricing.
-
Tooling: The initial setup for manufacturing may require specialized tooling, which is a one-time cost but can be substantial. Buyers should inquire about tooling costs and whether they are included in the quoted price or charged separately.
-
Quality Control (QC): Effective QC processes ensure that the machines meet specified standards, impacting both reliability and safety. Investing in quality control can reduce long-term costs related to repairs and warranty claims.
-
Logistics: Shipping costs and import duties can significantly affect the total price, particularly for international buyers. Understanding Incoterms is essential for managing logistics costs effectively.
-
Margin: Suppliers often add a profit margin on top of their costs. This margin can vary based on the supplier’s market position, brand reputation, and the level of customization offered.
Price Influencers
-
Volume/MOQ: Minimum order quantities (MOQs) can influence pricing. Larger orders often qualify for discounts, but buyers should balance the need for inventory with cash flow considerations.
-
Specifications/Customization: Custom features can lead to higher costs. Buyers should clearly define their requirements to avoid unexpected expenses.
-
Materials Quality/Certifications: Higher-quality materials and certifications (like ISO or CE) can increase costs but often lead to better performance and lower maintenance over time.
-
Supplier Factors: Reputation and reliability of the supplier affect pricing. Established suppliers may charge more but offer better warranties and support.
-
Incoterms: Understanding the responsibilities for shipping and handling can help buyers manage costs. Terms like FOB (Free on Board) or CIF (Cost, Insurance, and Freight) dictate who bears the cost and risk at various stages of transport.
Buyer Tips
-
Negotiation: Always negotiate pricing and terms. Be prepared to discuss volumes, payment terms, and delivery schedules to secure the best deal.
-
Cost-Efficiency: Consider the total cost of ownership (TCO), which includes not only purchase price but also operating costs, maintenance, and potential downtime.
-
Pricing Nuances: International buyers should be aware of currency fluctuations and their impact on pricing. It is wise to lock in prices when possible to avoid unexpected increases.
-
Supplier Research: Conduct thorough research on potential suppliers. Online reviews, industry forums, and previous buyer testimonials can provide insights into reliability and service quality.
-
Understanding Local Markets: Each region may have different pricing dynamics influenced by local demand, competition, and economic conditions. Tailoring sourcing strategies to regional characteristics can yield better pricing outcomes.
Disclaimer
Prices for portable CNC plasma cutting machines can vary widely based on the factors outlined above. This analysis provides a general overview and should be used as a guide rather than a definitive pricing framework. Always conduct your own market research and consult with suppliers to get accurate and current pricing information.
Spotlight on Potential portable cnc plasma cutting machine Manufacturers and Suppliers
This section looks at several manufacturers active in the ‘portable cnc plasma cutting machine’ market. This is a representative sample for illustrative purposes; B2B buyers must conduct extensive due diligence before any transaction. Information is synthesized from public sources and general industry knowledge.
Essential Technical Properties and Trade Terminology for portable cnc plasma cutting machine
Key Technical Properties of Portable CNC Plasma Cutting Machines
When considering a portable CNC plasma cutting machine, understanding its technical specifications is crucial for making informed purchasing decisions. Here are some essential properties to consider:
-
Material Grade: This refers to the types of materials the machine can effectively cut, such as mild steel, stainless steel, aluminum, and other alloys. Higher-quality machines can handle a wider range of materials and thicknesses, which is vital for businesses looking to diversify their applications and enhance their service offerings.
-
Cutting Thickness: Measured in millimeters or inches, this specification indicates the maximum thickness of material the machine can cut. Understanding the cutting thickness is essential for buyers to ensure that the machine meets their specific operational requirements, especially in industries like construction or manufacturing where material thickness can vary significantly.
-
Tolerance: Tolerance defines the precision of the cut, typically expressed as a range (e.g., ±0.5 mm). High precision is critical in applications requiring tight fits or intricate designs. B2B buyers should prioritize machines with lower tolerance levels to ensure quality and reduce the need for secondary operations, thereby saving time and costs.
-
Power Output: This is usually measured in amperes and directly affects the cutting speed and efficiency. A higher power output allows for faster cutting of thicker materials, which can lead to increased productivity. Buyers should consider their typical workload and choose a machine that balances power requirements with operational efficiency.
-
Portability Features: This includes weight, dimensions, and ease of transport. Since the target audience is likely to operate in diverse settings—from workshops to job sites—machines that are lightweight and equipped with robust transport options will enhance operational flexibility and reduce logistical challenges.
Common Trade Terminology
Navigating the purchasing landscape for CNC plasma cutting machines also requires familiarity with specific trade terms. Here are key terms that international B2B buyers should understand:
-
OEM (Original Equipment Manufacturer): This term refers to a company that produces parts or equipment that may be marketed by another manufacturer. Understanding OEM relationships is important for buyers seeking reliable parts and support, as it can impact the quality and availability of replacement parts.
-
MOQ (Minimum Order Quantity): This is the smallest quantity of a product that a supplier is willing to sell. Knowing the MOQ helps buyers gauge their purchasing power and plan inventory accordingly, especially in regions where supply chain issues might arise.
-
RFQ (Request for Quotation): An RFQ is a standard business process where a buyer requests price quotes from suppliers for specific quantities of products. Crafting a clear RFQ can lead to competitive pricing and ensures that the buyer receives comprehensive offers that meet their needs.
-
Incoterms: Short for International Commercial Terms, these terms define the responsibilities of buyers and sellers in global trade transactions. Familiarity with Incoterms can help B2B buyers understand shipping responsibilities, risk management, and cost allocation, which is critical for international purchases.
-
Lead Time: This refers to the time taken from placing an order to the delivery of the product. Understanding lead times is essential for project planning and inventory management, especially for businesses operating under tight deadlines.
-
Warranty and Support: A warranty is a guarantee provided by the manufacturer regarding the condition of the machine and the quality of service. Buyers should evaluate warranty terms and after-sales support to ensure they are covered in case of defects or operational issues.
By grasping these technical properties and industry terms, B2B buyers can enhance their decision-making processes, leading to more effective procurement strategies and operational efficiencies in their businesses.
Navigating Market Dynamics, Sourcing Trends, and Sustainability in the portable cnc plasma cutting machine Sector
Market Overview & Key Trends
The portable CNC plasma cutting machine market is experiencing significant growth, driven by advancements in technology and increasing demand for precision in metal fabrication across various industries. Key drivers include the expansion of the automotive, aerospace, and construction sectors, particularly in emerging economies in Africa, South America, and the Middle East. These regions are witnessing a surge in infrastructure development, which in turn boosts the demand for efficient and portable cutting solutions.
Emerging trends include the integration of IoT and AI technologies into portable CNC plasma cutters, enhancing their capabilities for real-time monitoring and data analysis. This allows for improved operational efficiency and reduced downtime, which are crucial for businesses looking to optimize their production processes. Additionally, the rise of e-commerce platforms is changing the dynamics of sourcing, enabling international B2B buyers to access a wider range of suppliers and products with ease.
Buyers should also consider the importance of supplier reliability and technical support when sourcing these machines. As competition intensifies, the ability to provide robust customer service and after-sales support will differentiate suppliers in the market. Buyers from Europe, for instance, may prioritize suppliers who comply with stringent EU regulations, while those from Africa and South America might seek cost-effective solutions that do not compromise on quality.
Sustainability & Ethical Sourcing in B2B
Sustainability has become a pivotal consideration in the portable CNC plasma cutting machine sector. The environmental impact of manufacturing processes, including energy consumption and waste generation, is under scrutiny. Buyers are increasingly looking for suppliers who demonstrate a commitment to reducing their carbon footprint through eco-friendly practices and materials.
Ethical sourcing is equally important, as consumers and businesses alike demand transparency in supply chains. This means that international buyers should prioritize suppliers who have established ethical sourcing policies, ensuring that materials are sourced responsibly and that labor practices adhere to international standards.
Certification plays a critical role in this landscape. Look for suppliers who hold certifications such as ISO 14001 for environmental management systems or other ‘green’ certifications that indicate a commitment to sustainable practices. Additionally, materials like recycled metals or eco-friendly coatings can enhance the sustainability profile of portable CNC plasma cutting machines, making them more appealing to environmentally conscious buyers.
Brief Evolution/History
The evolution of portable CNC plasma cutting machines can be traced back to the early 20th century when plasma cutting technology was first developed. Initially used in industrial settings, advancements in electronics and software have transformed these machines into portable, user-friendly devices suited for various applications.
In recent years, the proliferation of digital technology has made CNC plasma cutters more accessible to small and medium-sized enterprises (SMEs). This democratization of technology has enabled businesses across Africa, South America, the Middle East, and Europe to enhance their manufacturing capabilities without significant capital investment. The trend towards portability reflects a broader shift in the industry towards flexibility and efficiency, allowing businesses to adapt quickly to changing market demands.
As the market continues to evolve, international B2B buyers must stay informed about technological advancements and sustainability practices to make well-informed sourcing decisions.
Frequently Asked Questions (FAQs) for B2B Buyers of portable cnc plasma cutting machine
-
What should I consider when vetting suppliers for portable CNC plasma cutting machines?
When vetting suppliers, prioritize their experience and reputation in the industry. Check their certifications, such as ISO or CE, which indicate compliance with international standards. Request references from previous clients and assess their responsiveness to inquiries. It’s also beneficial to visit their manufacturing facilities, if possible, or utilize third-party inspection services to ensure quality control. Finally, consider their after-sales support and warranty offerings, which are crucial for long-term satisfaction. -
Can I customize a portable CNC plasma cutting machine to meet my specific needs?
Yes, many manufacturers offer customization options. When discussing customization, clearly outline your specific requirements, such as cutting thickness, speed, and software compatibility. Ensure the supplier has experience with custom builds and can provide examples of previous projects. Additionally, inquire about the implications for lead times and costs, as custom features may affect both. A thorough discussion will help align expectations and facilitate a smoother production process. -
What are the typical minimum order quantities (MOQs) and lead times for these machines?
MOQs vary by supplier and can depend on the machine specifications and customization levels. Typically, standard models may have lower MOQs, while customized machines could require higher quantities. Lead times can range from a few weeks to several months, influenced by factors such as production schedules, material availability, and shipping logistics. Always clarify these details upfront to manage your inventory and project timelines effectively. -
What payment terms should I expect when purchasing a portable CNC plasma cutting machine?
Payment terms can vary significantly among suppliers. Common arrangements include a deposit upon order placement (often 30-50%) and the balance upon delivery or installation. Consider negotiating terms that align with your cash flow and project timelines. Additionally, explore payment methods that provide security, such as letters of credit or escrow services, especially for high-value transactions. Understanding these terms upfront can help mitigate financial risks. -
How can I ensure the quality and certification of the machines I am buying?
To ensure quality, request detailed specifications and certifications from the supplier. Look for compliance with international standards such as ISO 9001, which indicates a commitment to quality management. Additionally, ask for test reports or performance evaluations conducted by independent labs. If possible, arrange for a pre-shipment inspection to verify the machinery meets your requirements before dispatch. This diligence can prevent costly errors and ensure reliability. -
What logistics considerations should I keep in mind when sourcing these machines internationally?
Logistics are critical when importing machinery. Consider factors such as shipping methods (air vs. sea), potential customs duties, and local regulations in your country. Ensure your supplier can handle logistics or partner with a reliable freight forwarder experienced in handling heavy machinery. Additionally, confirm the delivery timeline and ensure that you have a plan for receiving and installing the equipment upon arrival, including any necessary local permits or inspections. -
How should I handle disputes with suppliers during the purchasing process?
Establishing clear communication and documentation from the outset can help minimize disputes. If issues arise, attempt to resolve them amicably through direct communication. Refer to your purchase agreement, which should outline terms, conditions, and dispute resolution procedures. If an agreement cannot be reached, consider mediation or arbitration as alternatives to litigation, which can be costly and time-consuming. Having a well-defined contract can significantly aid in resolving conflicts efficiently. -
What additional support should I expect from suppliers after purchasing a portable CNC plasma cutting machine?
Post-purchase support is crucial for ensuring your machine operates effectively. Expect suppliers to offer installation assistance, training for your operators, and ongoing technical support. Inquire about their warranty policies and the availability of spare parts, as these will affect your machine’s longevity and performance. Additionally, some suppliers may provide software updates or maintenance services, enhancing the overall value of your investment. Always clarify these aspects before finalizing your order.
Important Disclaimer & Terms of Use
⚠️ Important Disclaimer
The information provided in this guide, including content regarding manufacturers, technical specifications, and market analysis, is for informational and educational purposes only. It does not constitute professional procurement advice, financial advice, or legal advice.
While we have made every effort to ensure the accuracy and timeliness of the information, we are not responsible for any errors, omissions, or outdated information. Market conditions, company details, and technical standards are subject to change.
B2B buyers must conduct their own independent and thorough due diligence before making any purchasing decisions. This includes contacting suppliers directly, verifying certifications, requesting samples, and seeking professional consultation. The risk of relying on any information in this guide is borne solely by the reader.
Strategic Sourcing Conclusion and Outlook for portable cnc plasma cutting machine
As the demand for portable CNC plasma cutting machines continues to rise across global markets, particularly in Africa, South America, the Middle East, and Europe, strategic sourcing has become a pivotal element for B2B buyers. Key takeaways emphasize the importance of evaluating suppliers not only on price but also on quality, service, and technological capability. Establishing strong relationships with reliable manufacturers can lead to better pricing, improved lead times, and enhanced after-sales support.
Value of Strategic Sourcing lies in its ability to mitigate risks associated with supply chain disruptions and fluctuating market conditions. By diversifying supplier bases and leveraging regional advantages, businesses can secure a competitive edge. Additionally, understanding local regulations and market dynamics is crucial for successful procurement.
Looking ahead, B2B buyers are encouraged to actively engage with suppliers, attend industry trade shows, and participate in forums that foster knowledge exchange. This proactive approach will not only enhance sourcing strategies but also position companies to adapt swiftly to technological advancements and market shifts. Now is the time to invest in robust sourcing strategies that align with future growth, ensuring that your operations remain efficient and competitive in an evolving landscape.