Master Tube Bending: The Complete Guide for B2B Buyers (2025)
Introduction: Navigating the Global Market for tube bending
Navigating the complexities of the global market for tube bending presents a unique set of challenges for international B2B buyers. Whether you’re sourcing high-quality stainless steel tubing for intricate fluid systems or evaluating the best tube bending techniques for your manufacturing needs, understanding the nuances of this industry is crucial. This guide aims to demystify tube bending by covering various types of bending processes, their specific applications, and best practices for supplier vetting. Additionally, it will provide insights into cost considerations, ensuring that you make informed purchasing decisions tailored to your operational requirements.
As businesses in Africa, South America, the Middle East, and Europe (including key markets like Germany and Poland) seek to streamline operations and enhance product efficiency, the demand for tube bending solutions has surged. This guide empowers you with actionable insights and practical advice, allowing you to identify the right materials, machinery, and techniques that suit your unique project demands. By understanding the fundamental aspects of tube bending—from material properties to the latest technological advancements—you’ll be better positioned to enhance your manufacturing capabilities and foster long-term supplier relationships. Prepare to elevate your procurement strategy and navigate the global market with confidence.
Understanding tube bending Types and Variations
Type Name | Key Distinguishing Features | Primary B2B Applications | Brief Pros & Cons for Buyers |
---|---|---|---|
Ram-Type Bending | Uses a hydraulically driven ram; simple and cost-effective; suitable for larger radii | Automotive exhaust systems | Pros: Cost-effective for simple bends. Cons: Limited precision and radius control. |
Rotary Draw Bending | Offers high precision; uses a mandrel for support; suitable for tight bends | Aerospace, medical devices | Pros: Excellent accuracy; minimal distortion. Cons: Higher setup costs and complexity. |
Roll Bending | Utilizes rollers to shape tubes; ideal for large diameter tubes | Construction, furniture manufacturing | Pros: Efficient for large volumes; versatile. Cons: Limited to specific tube sizes and shapes. |
Compression Bending | Applies pressure to bend; good for thick-walled tubes; requires minimal tooling | Heavy machinery, structural applications | Pros: Strong bends; good for thick materials. Cons: Potential for surface damage if not executed properly. |
Hydroforming | Uses hydraulic pressure to form shapes; allows for complex geometries | Automotive, aerospace, and custom designs | Pros: High flexibility in design; minimal material waste. Cons: More expensive and requires specialized equipment. |
What Are the Characteristics of Ram-Type Bending?
Ram-type bending is one of the oldest methods, characterized by its simplicity and cost-effectiveness. This technique involves a hydraulically driven ram that forces the tube against pivot blocks or rollers, producing bends with a centerline radius typically three to four times the outside diameter of the tube. It is particularly suitable for applications like automotive exhaust systems where large radii are common. Buyers should consider the trade-off between cost and precision, as this method may not achieve the tight tolerances required for more sophisticated applications.
How Does Rotary Draw Bending Offer Precision?
Rotary draw bending stands out for its precision, utilizing a mandrel to support the tube during the bending process. This method is ideal for applications requiring tight bends and high accuracy, such as in aerospace and medical devices. The setup for rotary draw bending can be more complex and costly, but the benefits of minimal distortion and superior quality often justify the investment for B2B buyers needing reliable, high-performance components.
In What Scenarios Is Roll Bending Most Effective?
Roll bending employs rollers to gradually shape the tube, making it an efficient choice for large-diameter tubes used in construction and furniture manufacturing. This technique allows for high-volume production and versatility across various tube sizes and shapes. However, buyers should note that roll bending may be limited to specific dimensions, which can affect design flexibility. Understanding the specifications of their projects is crucial for buyers considering this option.
What Are the Advantages of Compression Bending?
Compression bending is particularly effective for thick-walled tubes, applying pressure to create strong bends with minimal tooling requirements. This method is often used in heavy machinery and structural applications. While compression bending can produce robust components, buyers must be cautious about potential surface damage if the process is not executed correctly. Ensuring that the bending equipment is suited to the material being used is essential for maintaining product integrity.
Why Choose Hydroforming for Complex Designs?
Hydroforming is an advanced method that uses hydraulic pressure to achieve complex geometries and detailed shapes. This technique is favored in industries like automotive and aerospace, where intricate designs are essential. Hydroforming offers significant advantages in terms of material efficiency and design flexibility, making it a preferred choice for custom applications. However, it comes with higher costs and requires specialized equipment, which buyers must factor into their project budgets.
Key Industrial Applications of tube bending
Industry/Sector | Specific Application of Tube Bending | Value/Benefit for the Business | Key Sourcing Considerations for this Application |
---|---|---|---|
Automotive | Exhaust systems and chassis components | Improved performance with reduced weight and fewer joints | Material quality, bend radius, and wall thickness specifications |
Oil & Gas | Pipeline systems for fluid transport | Enhanced flow efficiency with fewer leak points | Corrosion resistance, pressure ratings, and compatibility with fluids |
HVAC | Ductwork and piping for heating and cooling systems | Compact design leading to space-saving installations | Precision in bend angles, material choice, and thermal conductivity |
Aerospace | Fuel and hydraulic lines | Lightweight structures that enhance fuel efficiency | Compliance with industry standards, material certifications, and traceability |
Medical Devices | Tubing for surgical instruments and devices | High precision and reliability, ensuring patient safety | Biocompatibility, sterilization requirements, and tight tolerances |
How is Tube Bending Used in the Automotive Industry?
In the automotive sector, tube bending is crucial for creating exhaust systems and chassis components. This process allows manufacturers to design lightweight structures that enhance vehicle performance while minimizing the number of joints, which can be potential failure points. For international buyers, especially in emerging markets like Africa and South America, sourcing high-quality materials that can withstand temperature variations and corrosion is essential. Additionally, understanding specific bend radii and wall thickness requirements is critical to meet safety and performance standards.
What Role Does Tube Bending Play in Oil & Gas Applications?
In the oil and gas industry, tube bending is employed to create efficient pipeline systems for transporting fluids. By utilizing bent tubes, companies can reduce the number of joints in a pipeline, which minimizes leak risks and enhances overall flow efficiency. Buyers from the Middle East, a region rich in oil resources, should prioritize sourcing materials with high corrosion resistance and appropriate pressure ratings to ensure the longevity and reliability of their systems. Compatibility with various transported fluids is also a key consideration.
How is Tube Bending Applied in HVAC Systems?
Tube bending is essential in the HVAC industry for creating ductwork and piping used in heating and cooling systems. The ability to produce compact and intricate designs allows for better space utilization, which is particularly advantageous in urban environments. Buyers in Europe, such as Germany and Poland, should focus on precision in bend angles and material selection to ensure optimal thermal conductivity and system efficiency. Additionally, understanding local regulations regarding energy efficiency can guide sourcing decisions.
Why is Tube Bending Important in Aerospace Manufacturing?
In aerospace applications, tube bending is used to manufacture fuel and hydraulic lines that require lightweight yet robust structures. The bending process enables the creation of complex shapes that contribute to overall fuel efficiency. International B2B buyers in this sector must ensure compliance with stringent industry standards and material certifications. Traceability of materials used in the manufacturing process is also crucial, as it impacts safety and performance in flight.
How is Tube Bending Utilized in Medical Device Production?
In the medical devices industry, tube bending is vital for producing tubing used in surgical instruments and other medical equipment. The high precision required in this field ensures that each bend meets strict safety and performance standards, ultimately safeguarding patient health. Buyers should prioritize sourcing materials that are biocompatible and can withstand sterilization processes. Additionally, tight tolerances are essential to ensure reliability and effectiveness in medical applications, making it crucial for buyers to establish strong relationships with reputable suppliers.
3 Common User Pain Points for ‘tube bending’ & Their Solutions
Scenario 1: Inconsistent Bends Leading to Product Rework
The Problem:
B2B buyers often face challenges with inconsistent bends when manufacturing components that require precise tube shapes. This inconsistency can result from various factors, including incorrect specifications, poor machine calibration, or substandard tooling. For companies in Africa and South America, where sourcing high-quality bending machines and components can be a challenge, the repercussions can be significant. Rework not only increases production costs but can also lead to delays in project timelines, negatively affecting customer satisfaction and trust.
The Solution:
To mitigate issues related to inconsistent bends, buyers should invest time in selecting high-quality bending machinery that suits their specific needs. Understanding the properties of the materials being bent—such as wall thickness and material type—is crucial. Buyers should ensure that their tube bending machines are properly calibrated and maintained.
Furthermore, investing in quality tooling that matches the specifications of the tubes being bent is essential. For example, if working with stainless steel, sourcing tooling specifically designed for stainless steel can reduce the risk of deformation. Additionally, implementing a regular quality control process, including testing sample bends for precision, can help identify inconsistencies early in the production process, thereby minimizing the need for costly rework.
Scenario 2: Difficulty in Selecting the Right Bending Method
The Problem:
Many international B2B buyers struggle with selecting the most appropriate tube bending method for their applications. With various options available—such as ram-type, roll bending, compression bending, and rotary draw bending—deciding which method to use can be overwhelming. This decision can significantly impact the quality of the final product and the efficiency of the manufacturing process. Buyers in the Middle East and Europe may particularly face issues with local regulations and standards that dictate specific methods for certain applications.
The Solution:
Buyers should conduct a thorough analysis of their specific project requirements before selecting a bending method. Factors to consider include the type of material, desired bend radius, and the complexity of the design. For instance, rotary draw bending is ideal for tight bends and complex shapes, while roll bending is better suited for larger diameter tubes with gentle curves.
Engaging with suppliers who offer consultation services can provide valuable insights tailored to specific projects. Additionally, conducting trials with different methods can yield practical data that informs the final decision. Building partnerships with bending specialists who understand local regulations can also ensure compliance and reduce the risk of costly errors.
Scenario 3: High Costs Associated with Material Waste
The Problem:
A common pain point for B2B buyers involved in tube bending is the high costs associated with material waste. Inefficient bending processes often result in scrap materials, particularly when the bending machine is not optimized or when operators lack sufficient training. This issue is particularly pronounced in industries where margins are tight, such as automotive manufacturing in Europe and oil and gas sectors in Africa.
The Solution:
To reduce material waste, companies should focus on training their operators extensively on the tube bending process and best practices. Offering regular workshops and training sessions can ensure that staff are well-versed in using the machinery and understand the importance of precision in bending.
Investing in advanced bending technology, such as CNC-controlled machines, can also help minimize waste by ensuring accuracy and repeatability. Additionally, implementing a lean manufacturing approach can help identify inefficiencies in the bending process. By continuously analyzing production data and seeking feedback from operators, companies can refine their processes to reduce material waste, leading to significant cost savings over time.
Strategic Material Selection Guide for tube bending
What Are the Key Properties of Common Materials Used in Tube Bending?
When selecting materials for tube bending, it’s essential to understand the properties that will affect product performance, including temperature and pressure ratings, as well as corrosion resistance. Here, we analyze four common materials used in tube bending: stainless steel, aluminum, carbon steel, and copper.
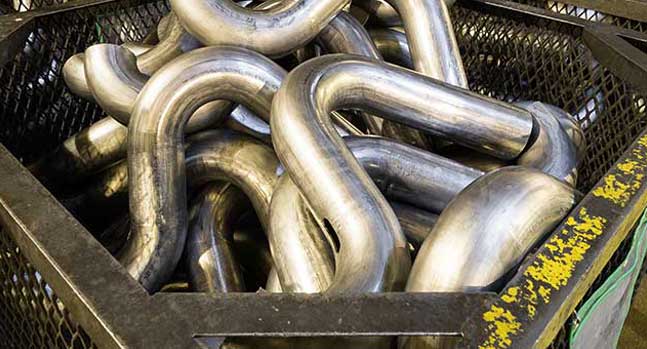
A stock image related to tube bending.
How Does Stainless Steel Perform in Tube Bending Applications?
Key Properties: Stainless steel is known for its excellent corrosion resistance and strength. It can withstand high temperatures and pressures, making it suitable for various applications, including fluid transport systems.
Pros & Cons: The primary advantage of stainless steel is its durability and resistance to rust, which is vital in industries such as food processing and pharmaceuticals. However, it tends to be more expensive than other materials and can be more challenging to bend, requiring specialized tooling.
Impact on Application: Stainless steel’s compatibility with a wide range of media, including corrosive substances, makes it ideal for applications in chemical processing and oil and gas.
Considerations for International Buyers: Buyers in Europe, particularly in Germany and Poland, often prefer stainless steel due to EU regulations on material safety. Compliance with standards like ASTM and DIN is crucial for ensuring quality and safety.
What Are the Advantages of Using Aluminum for Tube Bending?
Key Properties: Aluminum is lightweight and offers good corrosion resistance, although it has a lower strength-to-weight ratio compared to stainless steel.
Pros & Cons: The main advantage of aluminum is its ease of fabrication and lower cost, making it suitable for applications where weight is a concern, such as in automotive or aerospace industries. However, its lower strength may limit its use in high-pressure applications.
Impact on Application: Aluminum is often used in applications where weight savings are critical, such as in transportation and structural components.
Considerations for International Buyers: In South America, where transportation costs can be high, aluminum’s lightweight nature is a significant advantage. Compliance with local standards is essential, as some countries may have specific regulations regarding aluminum use.
Why Choose Carbon Steel for Tube Bending?
Key Properties: Carbon steel offers high strength and is generally more affordable than stainless steel and aluminum. It has moderate corrosion resistance, which can be improved with coatings.
Pros & Cons: The primary advantage of carbon steel is its strength and cost-effectiveness, making it a popular choice for structural applications. However, its susceptibility to rust can be a downside, requiring protective coatings or treatments.
Impact on Application: Carbon steel is often used in construction and automotive applications where strength is paramount.
Considerations for International Buyers: In the Middle East, where environmental conditions can lead to rapid corrosion, buyers should consider protective measures for carbon steel. Familiarity with standards such as JIS and ASTM can help ensure compliance.
What Role Does Copper Play in Tube Bending?
Key Properties: Copper has excellent thermal and electrical conductivity and is naturally resistant to corrosion, making it suitable for plumbing and electrical applications.
Pros & Cons: The key advantage of copper is its conductivity and resistance to corrosion, making it ideal for heat exchangers and electrical wiring. However, it is more expensive than carbon steel and can be less durable under mechanical stress.
Impact on Application: Copper is widely used in HVAC systems and plumbing due to its thermal properties and resistance to corrosion.
Considerations for International Buyers: In Africa, where copper is abundant, local sourcing can reduce costs. Compliance with international standards is essential for ensuring quality in plumbing and electrical applications.
Summary Table of Material Selection for Tube Bending
Material | Typical Use Case for Tube Bending | Key Advantage | Key Disadvantage/Limitation | Relative Cost (Low/Med/High) |
---|---|---|---|---|
Stainless Steel | Chemical processing, food and beverage systems | Excellent corrosion resistance and durability | Higher cost and bending complexity | High |
Aluminum | Automotive, aerospace, lightweight structures | Lightweight and cost-effective | Lower strength compared to steel | Medium |
Carbon Steel | Construction, automotive, structural applications | High strength and affordability | Susceptible to rust without protection | Low |
Copper | HVAC systems, plumbing, electrical applications | Superior conductivity and corrosion resistance | Higher cost and lower mechanical durability | Medium |
This detailed analysis provides international B2B buyers with the necessary insights to make informed decisions regarding material selection for tube bending, taking into account performance, cost, and compliance with relevant standards.
In-depth Look: Manufacturing Processes and Quality Assurance for tube bending
What Are the Main Stages of the Tube Bending Manufacturing Process?
The manufacturing process for tube bending involves several critical stages: material preparation, forming, assembly, and finishing. Each stage plays a vital role in ensuring the final product meets the required specifications and quality standards.
How is Material Prepared for Tube Bending?
Material preparation is the first step in the tube bending process. It typically involves selecting the appropriate tube material, which can range from stainless steel to aluminum, depending on the application requirements. Key considerations during material selection include:
- Material Properties: Understanding the mechanical properties of the material, such as tensile strength and elongation, is crucial. These properties influence the bending process and the final characteristics of the bend.
- Cutting and Deburring: The tube must be cut to the desired length and deburred to remove any sharp edges or imperfections. This step is essential to prevent damage during bending and ensure a smooth finish.
What Techniques Are Used in the Tube Forming Stage?
The forming stage is where the actual bending occurs. Various techniques can be employed based on the specific requirements of the project:
- Rotary Draw Bending: This is the most common method used for precise bends. The tube is clamped and drawn around a die, which allows for tight radius bends with minimal distortion.
- Ram-Type Bending: Often used in simpler applications, this method involves a hydraulic ram that pushes the tube against a bending die. It is suitable for larger radius bends and is typically faster but less precise than rotary draw bending.
- Roll Bending: This technique uses three rollers to gradually bend the tube into the desired shape. It is ideal for creating large-radius curves and can accommodate thicker materials.
How is Quality Assurance Implemented in Tube Bending?
Quality assurance (QA) is crucial in the tube bending manufacturing process to ensure that the final product meets both international standards and customer specifications.
What International Standards Should B2B Buyers Be Aware Of?
International standards like ISO 9001 are essential benchmarks for quality management systems in manufacturing. For tube bending, additional industry-specific certifications may include:
- CE Marking: Required for products sold within the European Economic Area, indicating compliance with safety, health, and environmental protection standards.
- API Standards: The American Petroleum Institute (API) sets standards for the oil and gas industry, which can apply to tube bending in critical applications.
Understanding these standards helps B2B buyers evaluate potential suppliers and ensure compliance with relevant regulations.
What Are the Key Quality Control Checkpoints?
Quality control (QC) checkpoints are vital for maintaining product integrity throughout the manufacturing process. Common QC checkpoints include:
- Incoming Quality Control (IQC): This initial inspection ensures that raw materials meet specified standards before processing begins.
- In-Process Quality Control (IPQC): Throughout the bending process, ongoing inspections help identify any deviations from the expected quality. This may involve monitoring bending angles, checking for ovality, and ensuring wall thickness is within tolerance.
- Final Quality Control (FQC): After the bending process is complete, final inspections are conducted to verify that the product meets all specifications. This may include visual inspections and dimensional checks.
What Testing Methods Are Commonly Used in Tube Bending?
B2B buyers should be aware of the common testing methods employed to ensure quality in tube bending:
- Visual Inspection: A fundamental method where operators check for visible defects, such as surface imperfections or misalignments.
- Dimensional Testing: Measuring the bend radius, angles, and wall thickness using calipers and other precision instruments to ensure compliance with specifications.
- Non-Destructive Testing (NDT): Techniques such as ultrasonic testing or eddy current testing can be used to detect internal flaws without damaging the tube.
How Can B2B Buyers Verify Supplier Quality Control?
Verifying the quality control processes of suppliers is crucial for B2B buyers, especially in international markets. Here are some effective strategies:
- Conduct Supplier Audits: Regular audits of suppliers’ manufacturing facilities can provide insights into their quality management systems and adherence to standards.
- Request Quality Reports: Suppliers should be able to provide documentation of their quality control processes, including inspection reports and compliance certificates.
- Engage Third-Party Inspectors: Utilizing independent inspection services can add an additional layer of assurance regarding the quality of the products before they are shipped.
What Are the QC and Certification Nuances for International B2B Buyers?
When sourcing tube bending products from different regions, international buyers must navigate various QC and certification nuances:
- Understanding Regional Standards: Different countries may have specific standards and certifications that apply to tube bending. For example, European buyers might prioritize CE certification, while buyers in the Middle East might require compliance with local standards.
- Cultural and Communication Differences: Effective communication with suppliers is essential. Misunderstandings regarding quality expectations can arise due to cultural differences, making it important to establish clear specifications and expectations upfront.
- Logistics and Supply Chain Considerations: International shipping can introduce additional risks to product quality. Buyers should consider how products are packaged and transported to minimize potential damage during transit.
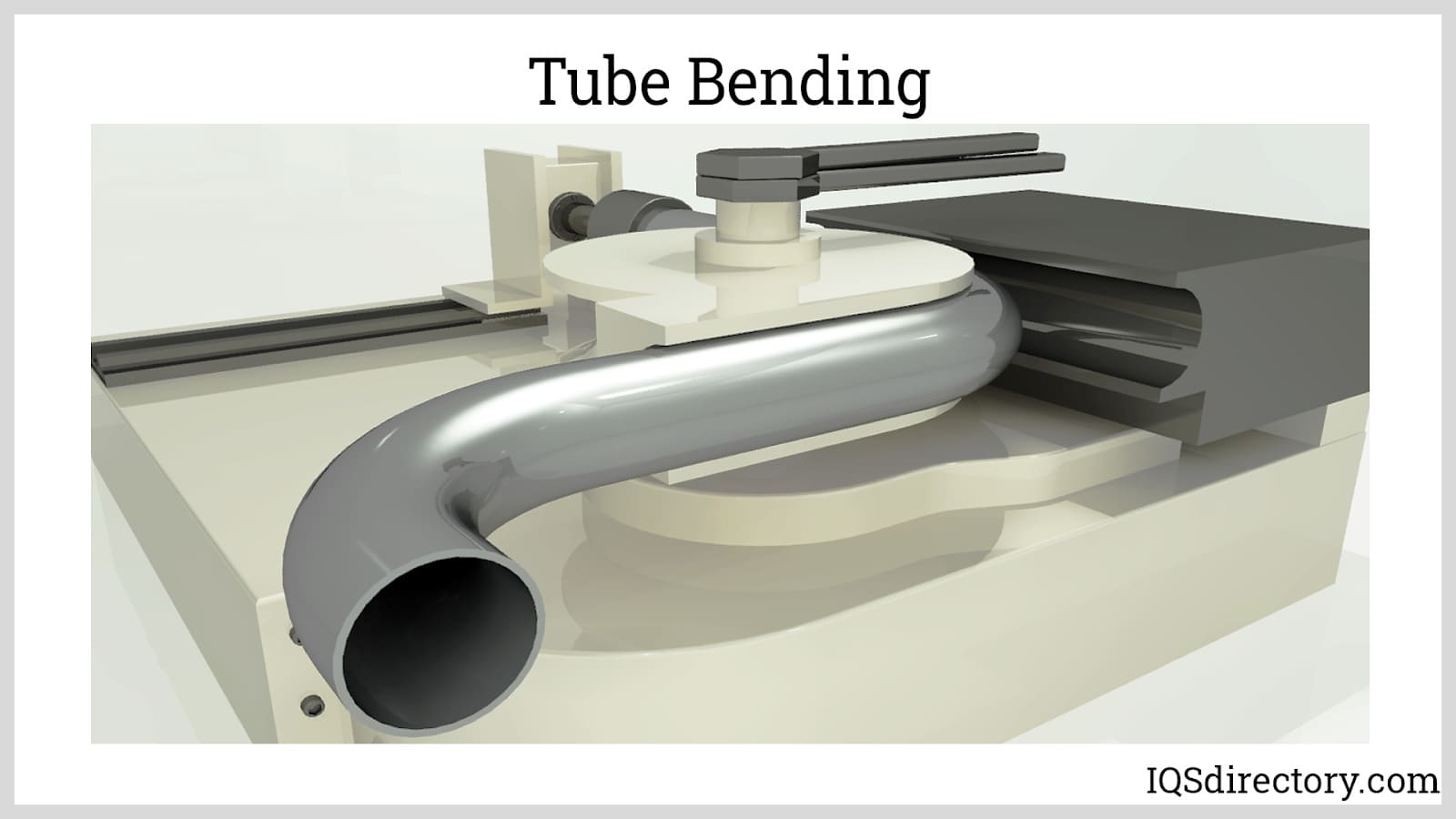
A stock image related to tube bending.
By understanding these aspects of the tube bending manufacturing process and quality assurance, international B2B buyers can make informed decisions, ensuring they source high-quality products that meet their specific needs.
Practical Sourcing Guide: A Step-by-Step Checklist for ‘tube bending’
In the evolving landscape of tube bending, making informed procurement decisions is crucial for B2B buyers. This guide provides a practical checklist to streamline the sourcing process, ensuring you secure the right materials and suppliers for your tube bending needs.
Step 1: Define Your Technical Specifications
Understanding your specific requirements is the foundation of successful tube bending procurement. Clearly outline the type of materials you need (e.g., stainless steel, aluminum) and the technical parameters such as outside diameter, wall thickness, and bend radius. This clarity will help in communicating effectively with suppliers and ensuring they can meet your exact needs.
Step 2: Identify Potential Suppliers
Begin your sourcing journey by compiling a list of potential suppliers specializing in tube bending. Look for manufacturers with a proven track record and positive customer feedback, particularly those who have experience serving international markets. Utilize industry directories, trade shows, and online platforms to discover reliable suppliers.
Step 3: Evaluate Supplier Certifications and Compliance
Before committing, it’s essential to verify that potential suppliers hold relevant certifications, such as ISO 9001 or industry-specific quality standards. These certifications indicate a commitment to quality and compliance with international regulations, which is particularly important for industries like automotive or aerospace that require stringent adherence to standards.
Step 4: Request Samples and Prototypes
Once you have narrowed down your options, request samples or prototypes of the tube bending work. This step allows you to assess the quality of the bends, the consistency of the material, and the precision of the dimensions. Pay attention to factors such as springback and ovality, as these can significantly affect the performance of your final product.
Step 5: Assess Production Capabilities and Lead Times
Understanding a supplier’s production capabilities is vital to ensure they can meet your demand. Inquire about their machinery, technology, and workforce to gauge whether they can handle large orders or custom requirements. Additionally, ask about lead times and their ability to deliver on schedule, as delays can impact your project timelines.
Step 6: Consider Logistics and Shipping Options
Evaluate the logistics involved in sourcing from each supplier. Consider factors such as shipping times, costs, and the supplier’s ability to handle customs for international shipments. Ensure that the supplier has a reliable logistics partner to minimize potential delays and additional expenses.
Step 7: Negotiate Terms and Conditions
Finally, engage in negotiations to finalize pricing, payment terms, and warranties. Ensure that you understand all terms clearly, including what happens in the case of defects or delays. A well-defined agreement protects both parties and fosters a strong business relationship moving forward.
By following these steps, B2B buyers can streamline the sourcing process for tube bending, ensuring they find the right suppliers who meet their technical and logistical needs. This proactive approach not only mitigates risks but also enhances the overall efficiency of your procurement strategy.
Comprehensive Cost and Pricing Analysis for tube bending Sourcing
What Are the Key Cost Components in Tube Bending Sourcing?
When sourcing tube bending services, understanding the cost structure is crucial for international B2B buyers. The primary cost components include:
-
Materials: The type of tubing material significantly influences cost. Stainless steel, aluminum, and carbon steel are common choices, with stainless steel generally being the most expensive due to its corrosion resistance and durability.
-
Labor: Skilled labor is essential for quality tube bending, particularly for intricate designs. Labor costs can vary widely based on regional wage standards, which are notably higher in European countries like Germany compared to some regions in Africa or South America.
-
Manufacturing Overhead: This includes operational costs such as utilities, equipment maintenance, and facility expenses. Efficient manufacturing processes can help lower overhead costs, translating to better pricing for buyers.
-
Tooling: The initial setup for tube bending often requires specialized tooling. The cost can vary based on the complexity of the bends and the need for custom tooling.
-
Quality Control (QC): Ensuring high-quality bends requires investment in QC processes, which may include inspection equipment and procedures. This cost is crucial for industries where precision is vital, such as aerospace and automotive.
-
Logistics: Shipping costs can add significantly to the total price, especially for international buyers. Factors such as distance, shipping method, and customs duties must be accounted for.
-
Margin: Suppliers will add a profit margin to cover their costs and ensure business sustainability. This margin can vary based on market conditions and competition.
How Do Price Influencers Affect Tube Bending Costs?
Several factors can influence the pricing of tube bending services:
-
Volume/MOQ: Higher order volumes often lead to lower per-unit costs due to economies of scale. Negotiating minimum order quantities (MOQs) can be beneficial for buyers looking to manage costs.
-
Specifications and Customization: Custom designs and specific material requirements can increase costs. Buyers should clearly define their specifications to avoid unexpected price increases.
-
Materials: The choice of material not only impacts the base cost but also the bending process. Some materials may require more complex tooling or labor-intensive processes, increasing overall expenses.
-
Quality and Certifications: Suppliers that offer quality certifications (like ISO) may charge higher prices due to the assurance of adherence to industry standards. Buyers should weigh the importance of certifications against their budget constraints.
-
Supplier Factors: The location, reputation, and operational efficiencies of suppliers can influence pricing. Established suppliers with proven track records may charge a premium but offer reliability that can mitigate risks.
-
Incoterms: The terms of shipping can significantly affect costs. Understanding the responsibilities and costs associated with various Incoterms (like FOB, CIF) is crucial for accurate cost assessments.
What Are the Best Buyer Tips for Cost-Efficiency in Tube Bending?
International B2B buyers can adopt several strategies to optimize their sourcing of tube bending services:
-
Negotiate Wisely: Leverage bulk purchasing and long-term contracts to negotiate better pricing. Building a relationship with suppliers can also lead to more favorable terms over time.
-
Consider Total Cost of Ownership (TCO): Look beyond the initial purchase price. Assess the long-term costs associated with maintenance, repairs, and potential downtime. Choosing a slightly more expensive option that offers greater durability may lead to savings in the long run.
-
Understand Pricing Nuances for International Sourcing: Different regions may have varying cost structures. For example, while sourcing from Europe might ensure high quality, it may also come with higher shipping costs. Conversely, suppliers in Africa or South America may offer lower prices but may lack certain certifications.
-
Request Detailed Quotes: Ensure that quotes break down all costs, including materials, labor, and logistics. This transparency helps in making informed comparisons between suppliers.
-
Stay Informed on Market Trends: Keeping abreast of fluctuations in material costs and global supply chain issues can provide leverage in negotiations and help avoid sudden price increases.
Disclaimer for Indicative Prices
Prices for tube bending services can vary widely based on several factors, including the specifics of the project, market conditions, and supplier capabilities. It is advisable for buyers to obtain detailed quotes and conduct thorough research before making purchasing decisions.
Alternatives Analysis: Comparing tube bending With Other Solutions
When considering solutions for creating fluid transport systems, tube bending is one of the most effective methods. However, it is essential for international B2B buyers, particularly from Africa, South America, the Middle East, and Europe, to explore alternatives that may suit their specific needs. This section will delve into viable alternatives to tube bending, providing a comparative analysis to help buyers make informed decisions.
Comparison Aspect | Tube Bending | Welding | Threaded Pipe Systems |
---|---|---|---|
Performance | High precision with fewer connections. | Strong, permanent joints; versatile. | Reliable but more potential leak points. |
Cost | Moderate initial investment; low long-term. | Higher upfront costs; labor-intensive. | Lower initial costs; higher long-term due to leaks. |
Ease of Implementation | Requires specialized equipment; training needed. | Requires skilled labor; complex setups. | Easy to install; minimal training required. |
Maintenance | Low maintenance; fewer fittings to check. | Moderate; requires periodic inspections. | Higher maintenance due to multiple fittings. |
Best Use Case | Ideal for intricate designs and compact systems. | Best for structural applications and high-pressure systems. | Suitable for simple, straight runs; less critical applications. |
What Are the Advantages and Disadvantages of Welding as an Alternative to Tube Bending?
Welding is a widely recognized method for joining metal components. It offers strong, permanent connections, making it ideal for high-pressure applications. One of the main advantages of welding is its versatility; it can be used on various materials and shapes. However, the initial costs can be high due to the need for skilled labor and specialized equipment. Additionally, welded joints can be more challenging to inspect and maintain, requiring periodic checks to ensure integrity.
How Do Threaded Pipe Systems Compare to Tube Bending?
Threaded pipe systems are a traditional method for constructing fluid transport systems. They are generally less expensive upfront and relatively easy to install, which can be appealing for projects with tight budgets. However, threaded systems have a higher potential for leaks due to multiple connection points, which can lead to increased maintenance costs over time. While they are suitable for straightforward applications, they lack the design flexibility and efficiency of tube bending.
Why Choose Tube Bending Over Alternatives?
Tube bending stands out as a preferred method for creating complex fluid systems due to its ability to minimize connection points, thereby reducing the potential for leaks. This not only improves system reliability but also enhances efficiency by allowing for smoother fluid flow. Although the initial investment in tube bending equipment may be moderate, the long-term savings in maintenance and operational efficiency can outweigh these costs.
In conclusion, when selecting between tube bending, welding, and threaded pipe systems, international B2B buyers should carefully assess their specific project requirements, including budget constraints, desired performance, and the complexity of the design. By understanding the unique benefits and limitations of each method, buyers can make informed decisions that align with their operational goals and ensure the longevity and efficiency of their fluid transport systems.
Essential Technical Properties and Trade Terminology for tube bending
What Are the Essential Technical Properties of Tube Bending?
Understanding the critical specifications in tube bending is vital for international B2B buyers. Here are some of the key properties to consider:
1. Material Grade
The grade of the material used for tube bending significantly affects the final product’s strength, flexibility, and durability. Common materials include stainless steel, aluminum, and carbon steel. Stainless steel, for instance, offers corrosion resistance, making it suitable for industries like oil and gas. Selecting the appropriate material grade can enhance performance and longevity, reducing the need for replacements and maintenance.
2. Wall Thickness
Wall thickness is crucial in determining the tube’s strength and ability to withstand pressure. Thicker walls provide greater durability but may limit the degree of bend achievable without compromising structural integrity. In B2B transactions, specifying the correct wall thickness ensures that the products meet the required safety and performance standards, especially in high-pressure applications.
3. Tolerance
Tolerance refers to the allowable deviation from a specified dimension. In tube bending, tighter tolerances are often required for precision applications, such as in aerospace or medical equipment. Understanding tolerance specifications helps buyers ensure that the components will fit seamlessly into their systems, thus avoiding costly rework and delays.
4. Bend Radius
The bend radius is the radius of the curve of the bend. It is a critical factor that influences both the structural integrity and flow characteristics of the tubing. A smaller bend radius can lead to increased stress and potential failure points. For international buyers, knowing the appropriate bend radius helps in selecting the right bending method and tooling, ensuring optimal performance of the final product.
5. Springback
Springback is the tendency of a material to return to its original shape after bending. This property is particularly important in precision applications where exact angles are crucial. Understanding springback helps manufacturers compensate for this effect during the bending process, ensuring that the final product meets the required specifications.
What Are the Common Trade Terms in Tube Bending?
Familiarity with industry jargon is essential for effective communication in B2B transactions. Here are some common terms:
1. OEM (Original Equipment Manufacturer)
An OEM refers to a company that produces parts or equipment that may be marketed by another manufacturer. In tube bending, understanding OEM relationships can help buyers identify reliable suppliers and ensure that they are sourcing high-quality components that meet their specifications.
2. MOQ (Minimum Order Quantity)
MOQ is the smallest quantity of a product that a supplier is willing to sell. Knowing the MOQ is essential for buyers to manage inventory effectively and ensure that they meet production needs without overcommitting resources. This is particularly relevant for businesses in Africa and South America, where supply chain dynamics can vary significantly.
3. RFQ (Request for Quotation)
An RFQ is a document sent to suppliers requesting pricing and terms for specific products or services. This process is crucial for international buyers to compare offers and negotiate better terms. Clarity in the RFQ can lead to more accurate quotes and faster procurement processes.
4. Incoterms (International Commercial Terms)
Incoterms are a set of international rules that define the responsibilities of buyers and sellers in international transactions. Understanding these terms helps buyers from different regions, including Europe and the Middle East, navigate shipping, insurance, and liability issues effectively.
5. Lead Time
Lead time is the amount of time it takes from placing an order to receiving the product. In the context of tube bending, understanding lead times is essential for project planning and maintaining production schedules. Buyers should inquire about lead times when requesting quotes to ensure timely delivery.
By grasping these technical properties and trade terminologies, international B2B buyers can make informed decisions, streamline procurement processes, and enhance operational efficiency in tube bending applications.
Navigating Market Dynamics and Sourcing Trends in the tube bending Sector
What Are the Key Market Dynamics and Trends in Tube Bending for International B2B Buyers?
The tube bending sector is currently experiencing a transformative phase driven by advancements in technology and changing market demands. A significant global driver is the growing emphasis on automation and digitalization within manufacturing processes. For international B2B buyers, particularly from regions such as Africa, South America, the Middle East, and Europe, understanding these technological shifts is crucial for staying competitive. Emerging technologies, including CNC tube bending machines and software that integrates design and manufacturing processes, are streamlining operations and enhancing precision.
Furthermore, the trend towards custom solutions is on the rise. Many industries, including automotive, aerospace, and construction, require specialized tube bending applications that demand flexibility and adaptability in sourcing. Buyers are increasingly looking for suppliers who can offer tailored solutions, rapid prototyping, and shorter lead times. This shift towards customization is complemented by a growing focus on quality assurance, where suppliers are expected to meet stringent international standards, particularly in Europe.
Additionally, the move towards sustainability is reshaping sourcing trends. Buyers are now prioritizing suppliers who demonstrate environmental responsibility through sustainable practices and materials. For instance, the use of recycled metals and eco-friendly lubricants during the bending process is becoming more common. The market dynamics indicate a clear shift towards suppliers who can balance efficiency with environmental stewardship, making it essential for international buyers to align their sourcing strategies accordingly.
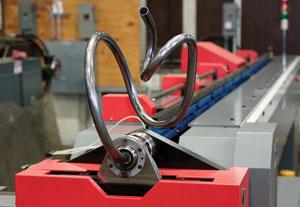
A stock image related to tube bending.
How Are Sustainability and Ethical Sourcing Impacting the Tube Bending Industry?
Sustainability and ethical sourcing have become pivotal considerations in the tube bending industry. The environmental impact of manufacturing processes, including emissions and waste generation, is under increasing scrutiny from consumers and regulatory bodies alike. International B2B buyers must now assess their suppliers’ sustainability practices, focusing on their environmental footprint and commitment to responsible sourcing.
One significant trend is the adoption of ‘green’ certifications and materials. Suppliers who use recyclable materials or are certified by recognized environmental standards, such as ISO 14001, gain a competitive edge. Buyers are encouraged to seek out suppliers who prioritize sustainability in their operations, as this not only reduces environmental impact but also enhances brand reputation.
Additionally, the importance of ethical supply chains cannot be overstated. Many buyers are now demanding transparency from suppliers regarding their sourcing practices, labor conditions, and overall corporate social responsibility (CSR) initiatives. By fostering relationships with ethically responsible suppliers, B2B buyers can ensure compliance with international regulations while contributing to a more sustainable industry.
How Has the Tube Bending Industry Evolved Over Time?
The evolution of the tube bending industry reflects broader technological advancements and changing market needs. Initially, tube bending was largely a manual process reliant on basic tools and techniques. Over the decades, innovations such as hydraulic and CNC bending machines have revolutionized the industry, allowing for greater precision and efficiency.
Today, the focus has shifted towards automation and digital integration, enabling manufacturers to produce complex geometries with minimal waste. The historical reliance on traditional techniques has given way to modern practices that prioritize quality, sustainability, and customization. For B2B buyers, understanding this evolution is vital, as it informs their sourcing decisions and helps identify suppliers who are equipped to meet the demands of contemporary manufacturing environments.
Overall, the tube bending sector is not just adapting to change; it is actively shaping a future that balances efficiency, sustainability, and ethical practices, making it an exciting area for international B2B buyers to explore.
Frequently Asked Questions (FAQs) for B2B Buyers of tube bending
-
How do I solve issues with tube bending quality?
To resolve quality issues in tube bending, start by assessing the four fundamental factors: material, machine, tooling, and lubrication. Ensure that the material specifications align with your application requirements. Use appropriate bending machines and tools designed for the specific tube dimensions. Regularly maintain and lubricate your machines to minimize friction and wear. Additionally, implementing quality control measures during the bending process—such as checking for ovality, wall thinning, and surface finish—can help you identify and rectify problems early. -
What is the best material for tube bending applications?
The best material for tube bending depends on your specific application requirements. Stainless steel is often preferred for its durability, corrosion resistance, and aesthetic appeal, making it ideal for industries like automotive and construction. Aluminum is lightweight and easier to bend, suitable for applications requiring intricate shapes. For high-stress environments, consider carbon steel or specialized alloys. Always evaluate the mechanical properties, such as elongation and yield strength, to ensure they meet the demands of your project. -
How can I determine the right tube bending supplier for my needs?
To find the right tube bending supplier, consider their experience and specialization in your industry. Look for suppliers who demonstrate a strong understanding of your specific requirements, including material specifications and bending techniques. Request samples or case studies to assess their capabilities. Additionally, evaluate their quality assurance processes, certifications, and customer feedback. Engaging in direct communication can also provide insights into their responsiveness and willingness to collaborate on custom solutions. -
What are common minimum order quantities (MOQs) for tube bending services?
Minimum order quantities (MOQs) for tube bending can vary significantly based on the supplier and the complexity of your project. Some suppliers may have MOQs as low as 50 pieces for standard items, while others may require larger orders for custom bends or specialized materials. It’s essential to discuss your needs with potential suppliers to understand their MOQs and negotiate terms that work for both parties. Consider leveraging bulk orders to reduce unit costs while ensuring you meet your project demands. -
What payment terms should I expect when sourcing tube bending services internationally?
When sourcing tube bending services internationally, payment terms can vary widely based on the supplier’s policies and your relationship with them. Common terms include upfront deposits (typically 30-50%) with the balance due upon delivery or after inspection. Some suppliers may offer letters of credit or payment through escrow services for larger orders. Always clarify payment conditions before finalizing contracts to avoid misunderstandings. Consider negotiating terms that provide you with adequate protection while ensuring timely payments for the supplier. -
How can I ensure quality assurance in tube bending processes?
To ensure quality assurance in tube bending, implement a robust quality management system that includes regular inspections throughout the manufacturing process. Establish clear specifications for tolerances, surface finish, and mechanical properties. Conduct tests such as bend tests and dimensional checks to verify compliance. Collaborate with suppliers who possess relevant certifications, such as ISO 9001, which demonstrates their commitment to quality. Additionally, consider third-party inspections for critical projects to further validate the quality of the products received. -
What logistics considerations should I keep in mind when sourcing tube bending services?
When sourcing tube bending services, logistics play a crucial role in ensuring timely delivery and cost efficiency. Assess the supplier’s shipping capabilities, including their experience with international freight and customs regulations specific to your region. Factor in lead times for production and shipping when planning your project timelines. Consider using Incoterms to clarify responsibilities for shipping, insurance, and customs duties. Additionally, evaluate the potential for local suppliers to reduce shipping times and costs, particularly for urgent projects. -
How can I customize tube bending solutions for my specific application?
To customize tube bending solutions effectively, begin by clearly defining your application requirements, including the desired bend angles, radii, and tube dimensions. Collaborate closely with your supplier, providing detailed specifications and, if possible, prototypes or drawings. Discuss the feasibility of your design with their engineering team to ensure that the chosen materials and bending processes can achieve your goals. Many suppliers offer design assistance and prototype services, allowing you to test and refine your custom solutions before full-scale production.
Important Disclaimer & Terms of Use
⚠️ Important Disclaimer
The information provided in this guide, including content regarding manufacturers, technical specifications, and market analysis, is for informational and educational purposes only. It does not constitute professional procurement advice, financial advice, or legal advice.
While we have made every effort to ensure the accuracy and timeliness of the information, we are not responsible for any errors, omissions, or outdated information. Market conditions, company details, and technical standards are subject to change.
B2B buyers must conduct their own independent and thorough due diligence before making any purchasing decisions. This includes contacting suppliers directly, verifying certifications, requesting samples, and seeking professional consultation. The risk of relying on any information in this guide is borne solely by the reader.
Strategic Sourcing Conclusion and Outlook for tube bending
As the global demand for tube bending solutions continues to evolve, B2B buyers must leverage strategic sourcing to enhance operational efficiency and reduce costs. Understanding the fundamental factors that influence tube bending—including material properties, bending techniques, and equipment—enables buyers to make informed decisions that lead to improved product quality and performance. By prioritizing high-quality materials and advanced bending technologies, companies can create more intricate designs with fewer connection points, ultimately minimizing potential leak sources and enhancing system reliability.
For international buyers, particularly those in Africa, South America, the Middle East, and Europe, establishing strong supplier relationships is vital. Engaging with manufacturers that offer comprehensive training and support can further empower teams to adopt best practices in tube bending, ensuring optimal outcomes.
Looking ahead, the focus on sustainability and efficiency will drive innovation in the tube bending sector. Buyers should be proactive in exploring new technologies and processes that align with their business goals. Embrace the opportunity to refine your sourcing strategies, invest in quality suppliers, and stay ahead in a competitive landscape. Your commitment to excellence in tube bending can set the foundation for long-term success and growth.