Master Worm and Worm Gear: The Complete Sourcing Guide (2025)
Introduction: Navigating the Global Market for worm and worm gear
Navigating the global market for worm and worm gear can be a daunting challenge for international B2B buyers, especially when seeking reliable solutions that meet specific operational needs. Worm gears are integral components in various applications, ranging from automotive power steering systems to industrial machinery. Understanding the intricacies of sourcing high-quality worm gears, including their types, applications, and the nuances of supplier vetting, is essential for making informed purchasing decisions.
This comprehensive guide delves into the diverse landscape of worm and worm gear, offering insights into the different types available, their respective applications, and the critical factors that influence cost and performance. By addressing common challenges such as lubrication issues and efficiency concerns, this resource equips buyers with the knowledge needed to optimize their procurement strategies.
For international B2B buyers from regions like Africa, South America, the Middle East, and Europe, navigating this market requires a keen understanding of regional supplier dynamics and product specifications. This guide not only enhances your ability to identify reliable suppliers but also empowers you to negotiate better terms, ensuring that your operations benefit from the most suitable worm gear solutions. With actionable insights and expert recommendations, you can confidently approach your sourcing needs, minimizing risks and maximizing value in your supply chain.
Understanding worm and worm gear Types and Variations
Type Name | Key Distinguishing Features | Primary B2B Applications | Brief Pros & Cons for Buyers |
---|---|---|---|
Cylindrical Worm Gear | Features a cylindrical thread that meshes at a 90-degree angle. | Conveyors, speed reducers, elevators | Pros: Compact design, high reduction ratios. Cons: Lower efficiency (30-60%), heat retention. |
Drum-Shaped Worm Gear | Comprised of a drum-shaped worm with a corresponding wheel. | Robotics, medical equipment, automotive | Pros: Suitable for high-tech applications. Cons: Limited torque capacity compared to cylindrical types. |
Dual-Lead Worm Gear | Has different lead angles on the worm’s tooth surfaces. | Precision machinery, adjustable gear systems | Pros: Allows for backlash adjustment. Cons: More complex design may increase costs. |
Self-Locking Worm Gear | Features a small lead angle preventing reverse motion. | Lifts, hoists, and safety mechanisms | Pros: Reduces risk of backdriving. Cons: Not entirely reliable; requires additional safety features. |
High-Viscosity Lubricated Worm Gear | Requires specialized high-viscosity lubricants for operation. | Heavy machinery, industrial applications | Pros: Maintains performance under heavy loads. Cons: High maintenance needs due to lubrication requirements. |
What are the Characteristics of Cylindrical Worm Gears?
Cylindrical worm gears are designed with a spiral thread that meshes seamlessly with a worm wheel at a 90-degree angle. This configuration allows for significant speed reduction and compact design, making it ideal for applications like conveyors and elevators. However, buyers should note that these gears typically exhibit lower efficiency, ranging from 30% to 60%, and may generate excessive heat, necessitating effective cooling solutions.
How Do Drum-Shaped Worm Gears Differ?
Drum-shaped worm gears consist of a drum-shaped worm meshing with a corresponding wheel. This design is particularly advantageous in high-tech applications such as robotics and medical equipment due to its compactness and ability to provide substantial speed reduction. However, it is essential for buyers to consider its limited torque capacity, which may not suit all industrial applications.
What Advantages Do Dual-Lead Worm Gears Offer?
Dual-lead worm gears feature two different lead angles on their tooth surfaces, allowing for axial movement and backlash adjustment. This capability makes them ideal for precision machinery and adjustable gear systems, where fine-tuning is crucial. Although they offer flexibility, buyers should be aware that the complexity of the design can lead to increased manufacturing costs.
Why Choose Self-Locking Worm Gears?
Self-locking worm gears are characterized by a small lead angle that prevents the worm from being turned by the wheel, effectively eliminating the risk of reverse motion. This feature is particularly valuable in applications like lifts and hoists, where safety is paramount. However, it is important to recognize that while they reduce backdriving risks, they are not entirely fail-safe and should be used in conjunction with additional safety mechanisms.
What Should B2B Buyers Know About High-Viscosity Lubricated Worm Gears?
High-viscosity lubricated worm gears are designed to operate under heavy loads, requiring specialized lubricants with high viscosity to maintain performance. These gears are commonly used in heavy machinery and industrial applications. While they can effectively handle significant loads, buyers must consider the high maintenance demands associated with lubrication, including the need for specific pumps and filters, which may increase operational costs.
Key Industrial Applications of worm and worm gear
Industry/Sector | Specific Application of worm and worm gear | Value/Benefit for the Business | Key Sourcing Considerations for this Application |
---|---|---|---|
Manufacturing | Speed reducers in conveyor systems | Enhanced efficiency and control in material handling | Ensure compatibility with existing equipment and load capacity. |
Automotive | Power steering systems | Improved steering precision and vehicle safety | Look for specialized materials to withstand high loads and temperatures. |
Construction | Elevators and hoists | Reliable vertical transportation in buildings and sites | Consider regulatory compliance and safety certifications. |
Robotics | Actuators in robotic arms | Precise movement and control for automation applications | Focus on compact designs and high torque specifications. |
Marine and Fishing | Fishing reels | Increased efficiency and ease of use in catching fish | Evaluate corrosion resistance and durability under marine conditions. |
What Are the Key Industrial Applications of Worm and Worm Gear?
How are Worm and Worm Gears Used in Manufacturing?
In manufacturing, worm gears are commonly used in speed reducers for conveyor systems. These systems require precise control over the speed and torque to ensure materials are moved efficiently. Worm gears provide a high reduction ratio, which allows for smooth operation with fewer moving parts, reducing the likelihood of mechanical failure. International B2B buyers should ensure that the selected worm gear systems are compatible with existing conveyor equipment and can handle the specific load capacities required for their operations.
What Role Do Worm and Worm Gears Play in Automotive Applications?
In the automotive sector, worm gears are integral to power steering systems. They facilitate the conversion of rotational motion from the steering wheel into the linear motion needed to turn the vehicle’s wheels. This application enhances steering precision and safety, especially in larger vehicles. Buyers in this industry should prioritize sourcing high-quality materials that can withstand significant loads and temperature fluctuations, ensuring reliability and durability in performance.
How Are Worm and Worm Gears Utilized in Construction?
In construction, worm gears are essential for elevators and hoists, providing reliable vertical transportation in buildings and construction sites. Their design allows for a compact mechanism capable of lifting heavy loads smoothly. When sourcing these components, it is crucial to consider safety certifications and compliance with local regulations, particularly in regions with stringent safety standards.
What Is the Importance of Worm and Worm Gears in Robotics?
Worm gears are increasingly used in robotics, particularly in actuators that control robotic arms. They offer precise movement and control, which are vital for automation tasks. The compact design of worm gears allows for integration into tight spaces within robotic systems. B2B buyers in this sector should focus on acquiring worm gears that meet high torque specifications and are designed for durability to handle repetitive motions.
How Are Worm and Worm Gears Applied in Marine and Fishing Industries?
In the marine and fishing industries, worm gears are found in fishing reels, enhancing efficiency and ease of use when catching fish. The design allows for smooth operation and high torque, which is essential for reeling in large catches. Buyers should evaluate the corrosion resistance and overall durability of worm gears, as they must withstand harsh marine environments. This ensures longevity and reliability in equipment used in fishing operations.
3 Common User Pain Points for ‘worm and worm gear’ & Their Solutions
Scenario 1: Difficulty in Achieving Optimal Lubrication for Worm Gears
The Problem: One significant challenge faced by B2B buyers is the lubrication of worm gears, which is critical for their performance and longevity. Worm gears operate through sliding friction, necessitating specialized lubricants with high viscosity to maintain a sufficient lubricant film. Many buyers are unaware of the specific lubrication requirements, leading to inadequate lubrication that can cause overheating, increased wear, and ultimately, gear failure. This situation can be particularly troublesome for industries relying on high-performance machinery, such as manufacturing and automotive, where equipment downtime translates to lost revenue.
The Solution: To effectively address lubrication issues, buyers should conduct thorough research on the appropriate lubricants for their worm gear systems. It’s essential to source high-viscosity oils (ISO 320 and above) specifically designed for worm gears. When selecting a lubricant, consider factors such as operating temperature, load conditions, and the specific material composition of the worm and worm wheel. Furthermore, implementing a regular maintenance schedule for monitoring lubricant condition and replenishing supplies can prevent potential failures. Buyers should also invest in proper filtration systems tailored to handle high-viscosity lubricants to ensure optimal performance and prolong gear life.
Scenario 2: Excessive Heat Generation in Worm Gear Systems
The Problem: Excessive heat generation during the operation of worm gears is a common issue that can adversely affect their efficiency and durability. Due to the sliding contact nature of worm gears, frictional heat is generated, which can lead to thermal expansion and potentially damage the gear assembly. B2B buyers in sectors such as mining and heavy machinery may find that high operating temperatures result in reduced efficiency, increased energy costs, and shortened equipment lifespan, causing significant operational setbacks.
The Solution: To mitigate heat generation, buyers should consider implementing cooling solutions, such as heat exchangers or air cooling systems, specifically designed for their equipment. Additionally, selecting materials with better thermal conductivity for worm gears can help dissipate heat more effectively. Regular monitoring of operating temperatures using thermal sensors can provide real-time data, allowing for timely interventions. Buyers should also evaluate their gear design to ensure that it allows for adequate heat dissipation and consider using worm gears with a lower lead angle to reduce frictional forces.
Scenario 3: Difficulty in Sourcing Quality Worm Gears
The Problem: B2B buyers often struggle with sourcing high-quality worm gears that meet specific application requirements. With numerous manufacturers in the market, distinguishing between reliable suppliers and those offering subpar products can be daunting. This challenge is exacerbated for buyers in emerging markets in Africa and South America, where access to quality components can be limited. Poor-quality worm gears can lead to early failure, increased maintenance costs, and operational disruptions.
The Solution: To overcome sourcing difficulties, buyers should establish a clear set of criteria for evaluating suppliers, including certifications, manufacturing processes, and material quality. Engaging with manufacturers who offer detailed technical specifications and testing data can provide assurance of quality. Buyers should also leverage industry networks and online platforms to gather reviews and recommendations from peers. Additionally, consider forming partnerships with local distributors who have established relationships with reputable manufacturers, as they can facilitate access to quality products and offer logistical support. Regularly attending industry trade shows and exhibitions can also provide insights into new suppliers and technologies, helping buyers make informed decisions.
Strategic Material Selection Guide for worm and worm gear
What Are the Key Properties of Common Materials for Worm and Worm Gear?
When selecting materials for worm and worm gears, it’s essential to consider their properties, as these directly affect performance, durability, and suitability for specific applications. Here, we analyze four common materials used in the manufacturing of worm and worm gears: carbon steel, stainless steel, bronze, and plastic.
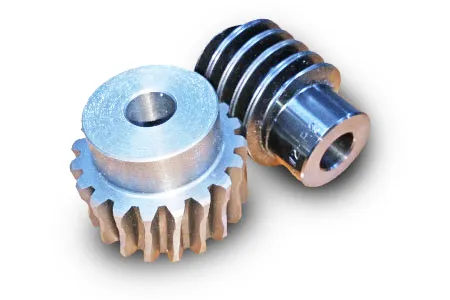
A stock image related to worm and worm gear.
How Does Carbon Steel Perform in Worm Gear Applications?
Key Properties: Carbon steel, particularly grades like S45C and SCM440, offers excellent strength and hardness. It can withstand high temperatures and pressures, making it suitable for heavy-duty applications. However, it is susceptible to corrosion if not properly treated.
Pros & Cons: The main advantages of carbon steel include its high durability and relatively low cost. However, its susceptibility to rust and the need for protective coatings can complicate maintenance. Manufacturing complexity is moderate, requiring specific heat treatment processes to enhance performance.
Impact on Application: Carbon steel is well-suited for applications requiring high strength, such as industrial machinery and automotive systems. However, it may not be ideal for environments with high moisture or corrosive substances.
Considerations for International Buyers: Buyers from regions like Africa and South America should ensure compliance with local standards, such as ASTM or ISO. Carbon steel is widely used and accepted, but buyers should be aware of the need for protective coatings in humid climates.
What Advantages Does Stainless Steel Offer for Worm Gears?
Key Properties: Stainless steel, particularly grades like 304 and 316, is known for its excellent corrosion resistance and ability to withstand high temperatures. It is also non-magnetic, which can be beneficial in specific applications.
Pros & Cons: The primary advantage of stainless steel is its durability and resistance to rust and corrosion, making it suitable for marine and food processing applications. However, it is generally more expensive than carbon steel and can be more challenging to machine, increasing manufacturing complexity.
Impact on Application: Stainless steel is ideal for applications exposed to harsh environments, such as food processing equipment and marine applications. Its corrosion resistance ensures longevity and reliability.
Considerations for International Buyers: Buyers in the Middle East and Europe should consider compliance with standards like DIN and JIS. The higher cost may be justified in applications where corrosion resistance is critical.
Why Choose Bronze for Worm Gear Applications?
Key Properties: Bronze, particularly phosphor bronze, offers excellent wear resistance and low friction properties. It has good corrosion resistance, especially in marine environments, and maintains strength at elevated temperatures.
Pros & Cons: The key advantage of bronze is its ability to reduce wear on mating surfaces, leading to longer life for both the worm and worm gear. However, bronze can be more expensive than steel options and may not handle high loads as effectively.
Impact on Application: Bronze is often used in applications where lubrication is minimal or where corrosion is a concern, such as in marine equipment and low-speed machinery. Its self-lubricating properties can be beneficial in reducing maintenance needs.
Considerations for International Buyers: Buyers should be aware of the higher material costs and ensure compliance with relevant standards. Bronze is often favored in regions with high humidity, such as coastal areas.
How Do Plastics Compare in Worm Gear Applications?
Key Properties: Engineering plastics, such as nylon and acetal, offer lightweight and corrosion-resistant alternatives to metal gears. They can operate effectively at lower loads and have good wear resistance.
Pros & Cons: The main advantage of plastics is their low weight and resistance to corrosion, making them suitable for lightweight applications. However, they may not withstand high temperatures or loads as effectively as metals, limiting their use in heavy-duty applications.
Impact on Application: Plastics are ideal for applications in electronics, robotics, and low-load machinery. Their resistance to corrosion makes them suitable for environments where metal gears would corrode.
Considerations for International Buyers: Buyers in regions with advanced manufacturing capabilities, such as Europe, may find a growing preference for plastic gears in specific applications. Compliance with material safety standards is crucial.
Summary Table of Material Selection for Worm and Worm Gear
Material | Typical Use Case for worm and worm gear | Key Advantage | Key Disadvantage/Limitation | Relative Cost (Low/Med/High) |
---|---|---|---|---|
Carbon Steel | Industrial machinery, automotive systems | High strength and durability | Susceptible to corrosion | Low |
Stainless Steel | Food processing, marine applications | Excellent corrosion resistance | Higher cost and machining complexity | High |
Bronze | Marine equipment, low-speed machinery | Low friction and wear resistance | Higher cost, lower load capacity | Med |
Plastic | Electronics, robotics, low-load machinery | Lightweight and corrosion-resistant | Limited high-temperature performance | Low |
This guide provides a comprehensive overview of material selection for worm and worm gears, enabling international B2B buyers to make informed decisions based on their specific application needs and regional considerations.
In-depth Look: Manufacturing Processes and Quality Assurance for worm and worm gear
What Are the Main Stages of Manufacturing Worm and Worm Gear?
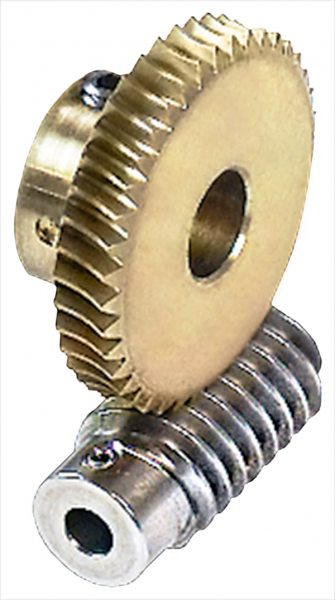
A stock image related to worm and worm gear.
The manufacturing of worm and worm gears involves several critical stages, each designed to ensure high precision and quality. Understanding these stages will help international B2B buyers assess potential suppliers effectively.
1. Material Preparation: What Materials Are Typically Used?
The choice of materials significantly impacts the performance and durability of worm gears. Common materials include:
- Worms: Typically made from high-strength steels such as mechanical structural carbon steel (S45C), alloy steels (SCM440), or stainless steel. These materials provide the necessary hardness and wear resistance.
- Worm Wheels: Often composed of softer materials like cast iron (FC200), phosphor bronze, aluminum bronze, or even engineering plastics like MC nylon. The disparity in hardness between the worm and wheel reduces wear and enhances longevity.
Before manufacturing, materials undergo rigorous inspection to ensure they meet specific mechanical and chemical properties.
2. Forming: How Are Worm Gears Shaped?
The forming process for worm gears involves several techniques:
- Cutting: Worms are produced using processes such as hobbing, shaping, or grinding. Hobbing is the most common method, where a hob cutter shapes the worm’s helical thread.
- Casting: Worm wheels may be cast into shape, allowing for complex geometries and efficient mass production.
- Machining: Precision machining ensures that both the worm and wheel meet dimensional tolerances critical for proper meshing.
Manufacturers often employ CNC (Computer Numerical Control) machines for high precision, allowing for complex designs with minimal human error.
3. Assembly: What Does the Assembly Process Entail?
Once the individual components are manufactured, they undergo assembly. This process typically involves:
- Alignment: Ensuring that the worm and wheel are properly aligned is crucial for efficiency and to minimize wear.
- Backlash Adjustment: Depending on the gear type, adjustments may be necessary to account for wear or to optimize performance.
- Lubrication: Proper lubrication is vital, especially for worm gears due to their sliding contact. Manufacturers must apply the right type of high-viscosity lubricant to ensure smooth operation.
4. Finishing: What Finishing Techniques Are Commonly Used?
Finishing processes enhance the surface quality of worm gears and are essential for performance:
- Grinding: Often used for achieving tighter tolerances and smoother finishes, particularly for the worm.
- Coating: Some manufacturers apply coatings to reduce friction and improve wear resistance.
- Inspection: Each gear undergoes a final inspection to verify dimensions, surface finish, and overall quality before shipping.
What Quality Assurance Standards Should International B2B Buyers Consider?
Quality assurance is critical in the manufacturing of worm gears, especially for international buyers. Familiarity with relevant standards can help assess supplier reliability.
1. What Are the Relevant International Standards?
International standards play a significant role in ensuring product quality:
- ISO 9001: This standard outlines the requirements for a quality management system (QMS) and is fundamental for manufacturers aiming to ensure consistent quality.
- CE Marking: For products intended for the European market, CE marking indicates compliance with EU safety, health, and environmental requirements.
- API Standards: For applications in the oil and gas industry, the American Petroleum Institute (API) sets standards that may be relevant for specific worm gear applications.
2. What Are the Key QC Checkpoints During Manufacturing?
Quality control checkpoints help ensure that products meet specifications:
- Incoming Quality Control (IQC): This involves inspecting raw materials upon receipt to confirm they meet specified standards.
- In-Process Quality Control (IPQC): Throughout the manufacturing process, various checks are performed to ensure components remain within specified tolerances.
- Final Quality Control (FQC): After manufacturing, a comprehensive inspection of the finished product is conducted, including dimensional checks and functional testing.
What Testing Methods Are Commonly Used for Worm Gears?
Testing is crucial for validating the performance and reliability of worm gears. Common methods include:
- Dimensional Inspection: Using tools like calipers and micrometers to ensure adherence to specified dimensions.
- Load Testing: Assessing the gear’s ability to handle specified loads under real-world conditions.
- Noise and Vibration Testing: Evaluating the operational smoothness and identifying potential issues that could lead to premature failure.
How Can B2B Buyers Verify Supplier Quality Control?
Due diligence in verifying a supplier’s quality control is essential for international buyers. Here are practical steps to ensure reliability:
1. What Should Buyers Look for in Supplier Audits?
Conducting or requesting audits can provide valuable insights into a supplier’s manufacturing processes and quality control systems. Consider the following:
- ISO Certification: Ensure the supplier holds relevant certifications, indicating adherence to international quality standards.
- Facility Visits: If possible, visit the manufacturing facility to evaluate equipment, processes, and working conditions firsthand.
2. How Can Buyers Utilize Reports and Third-Party Inspections?
Buyers should request:
- Quality Reports: Suppliers should provide documentation of quality control measures, testing results, and compliance with international standards.
- Third-Party Inspections: Engaging independent inspection agencies can provide an unbiased assessment of product quality before shipment.
What Are the QC and Certification Nuances for International Buyers?
Understanding the nuances of quality control and certification is crucial for international B2B buyers:
- Cultural Differences: Be aware of varying quality standards and practices in different regions, particularly in Africa, South America, and the Middle East.
- Regulatory Compliance: Ensure that products meet local regulations in the destination country, which may differ from the supplier’s country.
- Documentation: Proper documentation and certification can facilitate smoother customs processes and help avoid delays.
By understanding these manufacturing processes and quality assurance practices, international B2B buyers can make informed decisions when selecting suppliers for worm and worm gears, ensuring they receive high-quality products that meet their operational needs.
Practical Sourcing Guide: A Step-by-Step Checklist for ‘worm and worm gear’
To assist international B2B buyers in effectively sourcing worm and worm gear, this practical checklist outlines essential steps to follow. These steps ensure that you procure high-quality components that meet your specific operational needs while minimizing risks associated with vendor reliability and product performance.
Step 1: Define Your Technical Specifications
Before initiating the sourcing process, it is crucial to outline your technical requirements. This includes defining the gear ratio, load capacity, material specifications (e.g., steel for worms, brass for wheels), and operational conditions such as temperature and environment. Clear specifications will help you communicate your needs to potential suppliers and ensure that the products you receive are fit for purpose.
Step 2: Research Suppliers and Manufacturers
Conduct thorough research to identify reputable suppliers and manufacturers of worm and worm gear. Look for companies with a solid track record in your industry and positive customer reviews. Utilize online platforms, trade shows, and industry directories to compile a list of potential partners.
- Check industry certifications: Ensure the suppliers hold relevant certifications (ISO, CE) that validate their manufacturing processes and quality standards.
Step 3: Evaluate Supplier Capabilities
It’s essential to assess the capabilities of your shortlisted suppliers. Request detailed information about their manufacturing processes, equipment, and quality control measures. Understanding their production capacity and technology will help you gauge whether they can meet your volume and customization needs.
- Inquire about design flexibility: Ensure the supplier can accommodate specific design modifications if required.
Step 4: Request Samples for Testing
Before making a bulk purchase, request samples of the worm and worm gear for evaluation. Testing these samples will allow you to assess their performance, durability, and compatibility with your equipment. Pay attention to the quality of the materials used and the precision of the manufacturing.
- Consider running stress tests: Ensure that the samples can handle the expected load and conditions in your application.
Step 5: Assess Pricing and Payment Terms
Gather quotes from multiple suppliers to compare pricing structures. Be cautious of prices that are significantly lower than the market average, as they may indicate inferior quality. Additionally, review payment terms and conditions, including any advance payments or financing options that may be offered.
- Negotiate for better terms: Establish a relationship with suppliers that allows for flexibility in pricing or payment schedules, especially for bulk orders.
Step 6: Verify Supplier Reliability and Support
Ensure that the supplier has a reliable support system in place. This includes their ability to provide after-sales support, warranty terms, and responsiveness to inquiries. Check references and testimonials from other B2B buyers who have worked with the supplier to validate their reliability.
- Evaluate their communication: Good communication is vital for resolving issues quickly and efficiently during the procurement process.
Step 7: Finalize the Contract and Order
Once you have selected a supplier, it is time to finalize the contract. Ensure that all terms, including delivery schedules, quality expectations, and penalties for non-compliance, are clearly outlined. This contract will protect both parties and establish a clear understanding of expectations.
- Include clauses for quality assurance: Specify conditions for quality checks and acceptance criteria to safeguard your investment.
By following this checklist, B2B buyers can effectively navigate the sourcing process for worm and worm gear, ensuring they select reliable suppliers and obtain products that meet their operational needs.
Comprehensive Cost and Pricing Analysis for worm and worm gear Sourcing
What Are the Key Cost Components for Sourcing Worm and Worm Gears?
When sourcing worm and worm gears, understanding the comprehensive cost structure is essential for international B2B buyers. The primary cost components include:
-
Materials: The choice of materials significantly impacts costs. Common materials include mechanical structural carbon steel for worms and cast iron or bronze for worm wheels. Higher-quality materials often result in increased durability but also higher prices.
-
Labor: Labor costs can vary widely depending on the region of manufacturing. Countries with lower labor costs may offer competitive pricing, but this can also affect the quality and consistency of the products.
-
Manufacturing Overhead: This includes costs related to factory operations, such as utilities, maintenance, and equipment depreciation. In regions with higher operational costs, such as parts of Europe, these expenses can contribute significantly to the final price.
-
Tooling: Initial costs for tooling can be substantial, particularly for customized worm gears. Buyers should consider whether the supplier has the necessary equipment to produce the required specifications efficiently.
-
Quality Control (QC): Ensuring that worm gears meet industry standards can add to costs. Rigorous QC processes are essential for maintaining product quality, particularly in applications where reliability is critical.
-
Logistics: Shipping costs can vary based on distance and shipping terms. Incoterms will define responsibilities for shipping costs and risks, which can affect the total cost of ownership.
-
Margin: Suppliers typically build a profit margin into their pricing, which can vary based on market conditions and competition.
How Do Price Influencers Affect Worm and Worm Gear Costs?
Several factors can influence the pricing of worm and worm gears:
-
Volume/MOQ: Minimum Order Quantities (MOQ) can impact pricing significantly. Larger orders typically reduce the unit cost due to economies of scale. Buyers should negotiate for better pricing on bulk orders.
-
Specifications and Customization: Custom-designed worm gears will incur additional costs compared to standard products. Buyers should clearly define their specifications to avoid unexpected price increases.
-
Materials: The choice of materials can greatly influence price. For example, using high-grade alloys may increase the cost but provide better performance and longevity.
-
Quality and Certifications: Products with certifications (e.g., ISO) often come at a premium. However, such certifications can ensure compliance with international standards, which is crucial for many applications.
-
Supplier Factors: The reputation and reliability of the supplier can affect pricing. Established suppliers may charge higher prices due to their track record of quality and service.
-
Incoterms: Understanding Incoterms is crucial for cost management. Different terms (e.g., FOB, CIF) can shift costs between buyer and seller, impacting the overall price.
What Tips Can Help Buyers Optimize Costs When Sourcing Worm and Worm Gears?
International B2B buyers should consider the following strategies to enhance cost efficiency:
-
Negotiation: Always negotiate prices and terms. Suppliers may have flexibility, especially for larger orders or long-term contracts.
-
Total Cost of Ownership (TCO): Look beyond initial pricing. Consider maintenance costs, expected lifespan, and performance to determine the true cost of ownership.
-
Pricing Nuances for International Buyers: Be aware of currency fluctuations, tariffs, and import duties that can affect final costs. Establishing contracts that account for these factors can mitigate risks.
-
Evaluate Local Suppliers: In regions like Africa or South America, local suppliers may offer competitive pricing and reduced shipping costs. However, ensure they meet quality standards.
-
Leverage Technology: Utilize online platforms and B2B marketplaces to compare prices and suppliers efficiently. This can lead to better deals and insights into market pricing trends.
Conclusion
While sourcing worm and worm gears, buyers must be cognizant of the comprehensive cost structure and various pricing influencers. By employing effective negotiation strategies and understanding the Total Cost of Ownership, international B2B buyers can make informed decisions that enhance their sourcing efficiency. Always remember that indicative prices may fluctuate, and continuous market analysis will help maintain competitive advantages.
Alternatives Analysis: Comparing worm and worm gear With Other Solutions
Introduction: What Are the Alternatives to Worm and Worm Gear?
When it comes to mechanical power transmission, worm and worm gear systems are popular for their compact design and high torque reduction capabilities. However, they are not without drawbacks, such as inefficiencies due to sliding friction and lubrication challenges. For international B2B buyers, especially those in Africa, South America, the Middle East, and Europe, understanding alternative solutions can lead to better decisions based on specific operational needs and cost-effectiveness. This section explores viable alternatives to worm and worm gear systems, focusing on performance, cost, ease of implementation, maintenance, and best use cases.
Comparison Table of Worm and Worm Gear vs. Alternatives
Comparison Aspect | Worm And Worm Gear | Helical Gears | Bevel Gears |
---|---|---|---|
Performance | High torque, low speed; self-locking capability | Higher efficiency, smoother operation | Good for changing shaft angles |
Cost | Moderate initial cost; high maintenance costs | Generally lower cost; varied pricing based on application | Higher initial cost; durable materials |
Ease of Implementation | Requires precise alignment; specialized lubrication | Easier to install; more flexible configurations | Requires careful alignment; more complex installation |
Maintenance | High maintenance due to lubrication needs | Lower maintenance; less wear and tear | Moderate maintenance; requires periodic inspection |
Best Use Case | Applications needing compact design and high torque | General-purpose applications, automotive | Power transmission at an angle, machinery |
Detailed Breakdown of Alternatives
What Are the Advantages and Disadvantages of Helical Gears?
Helical gears provide a more efficient alternative to worm gears, primarily due to their rolling contact design, which reduces sliding friction and wear. They operate more smoothly and can handle higher loads, making them ideal for general-purpose applications, including automotive and industrial machinery. The primary downside is that they can be more complex to manufacture and require precise alignment, which can complicate installation. However, their lower maintenance needs and higher efficiency make them a popular choice for many businesses looking to reduce operational costs.
How Do Bevel Gears Compare to Worm and Worm Gear Systems?
Bevel gears are another viable alternative, particularly when a change in the axis of rotation is necessary. They excel in applications where torque must be transmitted at an angle, such as in power tools or machinery. Their design allows for a more efficient transfer of power compared to worm gears, which can be limited by sliding friction. However, bevel gears often come with a higher initial cost and require careful alignment during installation. Regular maintenance is necessary to ensure optimal performance, but overall, they offer a robust solution for businesses needing reliable power transmission.
Conclusion: How Should B2B Buyers Choose the Right Gear Solution?
Selecting the right gear solution depends on a variety of factors, including performance needs, budget constraints, and the specific application requirements. For buyers from regions like Africa, South America, the Middle East, and Europe, understanding the trade-offs between worm gears and their alternatives is crucial. While worm gears may provide a compact design with high torque, alternatives such as helical and bevel gears can offer better efficiency and lower maintenance costs. Ultimately, the best choice will align with operational goals, maintenance capabilities, and long-term cost-effectiveness.
Essential Technical Properties and Trade Terminology for worm and worm gear
What Are the Key Technical Properties of Worm and Worm Gear?
Understanding the essential technical properties of worm and worm gear systems is crucial for international B2B buyers to make informed purchasing decisions. Here are some of the critical specifications to consider:
1. Material Grade: Why Does It Matter?
Worm gears are typically made from various materials, including carbon steel, stainless steel, and bronze. The material choice affects durability, strength, and resistance to wear. For example, a harder material for the worm, such as SCM440 alloy steel, can significantly enhance the lifespan of the gear set. Buyers should assess the application requirements, such as load capacity and environmental conditions, to select the appropriate material grade.
2. Tolerance: What Is Its Role in Performance?
Tolerance refers to the permissible limits of variation in dimensions. High tolerance levels in worm gears are essential for ensuring smooth operation and minimizing backlash. Poor tolerances can lead to increased wear and reduced efficiency. For B2B buyers, specifying the correct tolerance can prevent costly breakdowns and maintenance issues, especially in precision applications like robotics or automotive systems.
3. Reduction Ratio: How Is It Calculated?
The reduction ratio is a critical property that indicates how much the input speed is reduced to achieve the desired output speed. It is determined by the number of threads on the worm and the number of teeth on the worm wheel. For instance, a reduction ratio of 1:120 means that for every 120 turns of the worm, the wheel turns once. This feature is vital for applications requiring high torque and low speed, such as conveyor systems and elevators.
4. Efficiency: What Should You Expect?
Worm gears generally have lower efficiency compared to other gear types, typically ranging from 30% to 60%. This inefficiency arises from the sliding friction during operation. Understanding the efficiency rating is important for buyers to evaluate the energy consumption and heat generation in their systems, which can impact operational costs and equipment longevity.
5. Lead Angle: What Is Its Significance?
The lead angle of the worm is crucial in determining the self-locking capability of the gear set. A smaller lead angle enhances self-locking, preventing reverse motion. This property is particularly valuable in applications like elevators and hoists where safety and control are paramount. Buyers should assess the lead angle to ensure it meets the specific requirements of their application.
What Are Common Trade Terms Related to Worm and Worm Gear?
Familiarity with industry terminology is essential for effective communication and negotiation in the B2B landscape. Here are some common trade terms that buyers should understand:
1. OEM (Original Equipment Manufacturer)
OEM refers to companies that produce components for other manufacturers’ products. In the context of worm gears, knowing the OEM can help buyers ensure compatibility and quality standards, especially when integrating components into larger systems.
2. MOQ (Minimum Order Quantity)
MOQ is the smallest number of units a supplier is willing to sell. Understanding the MOQ is crucial for buyers, particularly in regions where inventory management is essential. It helps in budgeting and planning for future production needs.
3. RFQ (Request for Quotation)
An RFQ is a formal document sent to suppliers to solicit price quotes for specific products or services. For international buyers, issuing an RFQ can streamline procurement processes, ensuring competitive pricing and favorable terms.
4. Incoterms (International Commercial Terms)
Incoterms are a set of rules that define the responsibilities of buyers and sellers in international transactions. Familiarity with these terms is vital for B2B buyers to understand shipping costs, risk transfer, and delivery obligations, particularly when sourcing from different continents like Africa or South America.
5. Backlash: Why Is It Important?
Backlash refers to the degree of play or looseness between the meshing gears. While some backlash is necessary to prevent binding, excessive backlash can lead to inefficiencies and operational issues. Buyers should inquire about acceptable backlash levels to ensure optimal performance in their applications.
By understanding these technical properties and trade terminologies, international B2B buyers can make more informed decisions regarding worm and worm gear systems, enhancing their operational efficiency and long-term success.
Navigating Market Dynamics and Sourcing Trends in the worm and worm gear Sector
What Are the Current Market Dynamics and Key Trends in the Worm and Worm Gear Sector?
The worm and worm gear sector is witnessing significant transformations driven by advancements in technology and changing market demands. One of the primary global drivers is the increasing need for automation across various industries, including manufacturing, automotive, and robotics. International B2B buyers are particularly focused on sourcing components that offer high efficiency and compact designs, which are characteristic of worm gears. With their unique ability to provide high reduction ratios and self-locking features, worm gears are becoming essential for applications requiring precise motion control.
Emerging trends in B2B technology are leaning towards digitalization and data-driven decision-making. Companies are now utilizing IoT (Internet of Things) capabilities to monitor the performance of worm gear systems in real-time, enabling predictive maintenance and reducing downtime. Furthermore, the rise of e-commerce platforms is simplifying the sourcing process for international buyers, allowing them to easily compare products, specifications, and prices across multiple suppliers.
In regions like Africa and South America, the growing industrial base is driving demand for reliable power transmission solutions. Meanwhile, buyers from Europe and the Middle East are increasingly prioritizing quality and sustainability in their sourcing decisions. The market dynamics are thus characterized by a blend of traditional manufacturing practices and modern technological advancements, creating opportunities for B2B buyers to capitalize on innovative solutions.
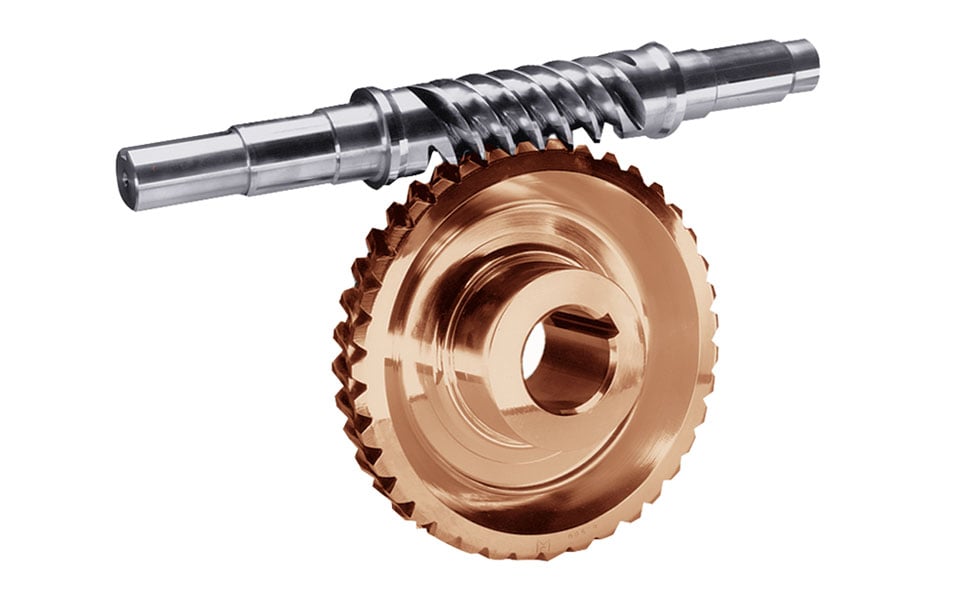
A stock image related to worm and worm gear.
How Can B2B Buyers Embrace Sustainability and Ethical Sourcing in the Worm and Worm Gear Sector?
Sustainability is becoming a critical consideration for B2B buyers in the worm and worm gear sector. The environmental impact of manufacturing processes and materials used in gear production is under scrutiny, prompting companies to adopt more sustainable practices. Buyers should prioritize suppliers who demonstrate a commitment to reducing their carbon footprint and utilizing eco-friendly materials.
Ethical sourcing is equally important, as it ensures that the materials used in worm gears are obtained responsibly. Buyers should look for suppliers with certifications that validate their adherence to environmental and social standards, such as ISO 14001 for environmental management or Fair Trade certifications. Additionally, the use of green lubricants and materials in the manufacturing of worm gears can significantly reduce the environmental impact, making them a more attractive option for buyers focused on sustainability.
Moreover, establishing partnerships with manufacturers who engage in transparent supply chain practices can enhance trust and reliability. International buyers can leverage these relationships to ensure that their procurement processes align with their corporate social responsibility goals, ultimately driving long-term value.
What Is the Brief Evolution and History of Worm Gears Relevant to B2B Buyers?
The evolution of worm gears can be traced back to ancient civilizations, with Archimedes being one of the earliest figures to document their use around 250 BC. Originally designed for lifting water and heavy objects, worm gears have undergone significant advancements, adapting to the needs of modern engineering applications.
Throughout history, the design and materials used in worm gears have evolved. Early versions were made from wood, while contemporary models often utilize high-strength materials like alloy steels and composites to enhance durability and efficiency. This historical context is crucial for B2B buyers, as it highlights the continuous innovation in the sector and underscores the importance of selecting suppliers who stay abreast of technological advancements.
As the demand for automation and precision in various industries grows, understanding the historical significance and technical evolution of worm gears can empower buyers to make informed decisions that align with their operational needs and future growth strategies.
Frequently Asked Questions (FAQs) for B2B Buyers of worm and worm gear
-
How do I solve lubrication issues in worm gears?
Lubrication is critical for the efficient operation of worm gears due to their sliding contact nature. To solve lubrication issues, select a high-viscosity lubricant that can withstand high pressure and temperature. Common options include ISO 460 or ISO 680 gear oils, which provide the necessary film thickness to prevent metal-to-metal contact. Ensure regular monitoring and replenishment of the lubricant, as well as proper filtration systems tailored for high-viscosity oils to maintain optimal performance. -
What is the best material for worm gear applications?
The best materials for worm gears depend on the application and load requirements. Typically, worms are made from harder materials such as carbon steel or stainless steel to resist wear, while worm wheels may be crafted from softer materials like bronze or engineering plastics. For high-tech applications, consider using specialized alloys or composites that offer improved strength and corrosion resistance. Always assess the specific operational environment, including temperature and load, to choose the most suitable materials. -
What customization options are available for worm gears?
Many manufacturers offer customization for worm gears, including variations in size, gear ratio, and material. You can request specific thread profiles or lead angles to optimize performance for your application. Additionally, some suppliers provide options for backlash adjustment through dual-lead worm gears. When discussing customization, clearly communicate your requirements and expected performance outcomes to ensure the final product meets your needs. -
What are the minimum order quantities (MOQ) for worm gears?
Minimum order quantities can vary significantly between suppliers and depend on factors such as the type of worm gear and the complexity of customization. Generally, standard products may have lower MOQs, while custom gears may require larger orders to justify production costs. Always inquire about MOQs upfront during the sourcing process to avoid unexpected costs and delays. -
How should I vet suppliers when sourcing worm gears internationally?
When vetting suppliers for worm gears, consider their industry reputation, certifications, and experience. Request references and check reviews from other B2B buyers to gauge reliability. Additionally, assess their production capabilities, quality assurance processes, and lead times. It’s also beneficial to visit the manufacturing facility, if possible, to evaluate operational standards and workforce competency. -
What are common payment terms for international B2B transactions?
Payment terms in international B2B transactions can vary, but common practices include letters of credit, wire transfers, and payment upon delivery. Negotiate terms that balance risk and liquidity. For larger orders, consider payment in installments based on production milestones. Ensure clarity on currency exchange rates and any potential fees associated with international transactions to avoid surprises. -
How do logistics impact the sourcing of worm gears?
Logistics play a crucial role in the sourcing process for worm gears, affecting delivery times and costs. Assess the supplier’s shipping capabilities, including methods of transport and handling of customs documentation. Consider potential delays due to international shipping regulations, especially if sourcing from regions with complex trade agreements. Establish clear expectations regarding shipping timelines and responsibilities to ensure smooth operations. -
What quality assurance measures should I expect from suppliers of worm gears?
Quality assurance measures for worm gears should include rigorous testing protocols such as dimensional checks, material inspections, and performance evaluations. Reputable suppliers often provide certifications and documentation demonstrating compliance with industry standards. Inquire about their quality control processes, including any third-party audits or testing to ensure consistency and reliability in their products.
Important Disclaimer & Terms of Use
⚠️ Important Disclaimer
The information provided in this guide, including content regarding manufacturers, technical specifications, and market analysis, is for informational and educational purposes only. It does not constitute professional procurement advice, financial advice, or legal advice.
While we have made every effort to ensure the accuracy and timeliness of the information, we are not responsible for any errors, omissions, or outdated information. Market conditions, company details, and technical standards are subject to change.
B2B buyers must conduct their own independent and thorough due diligence before making any purchasing decisions. This includes contacting suppliers directly, verifying certifications, requesting samples, and seeking professional consultation. The risk of relying on any information in this guide is borne solely by the reader.
Strategic Sourcing Conclusion and Outlook for worm and worm gear
As the global market for worm and worm gear continues to evolve, strategic sourcing remains crucial for international B2B buyers, particularly in regions such as Africa, South America, the Middle East, and Europe. By understanding the unique characteristics of worm gears—such as their high reduction ratios and self-locking capabilities—buyers can make informed decisions that enhance operational efficiency. Furthermore, recognizing the importance of specialized lubrication and material selection will mitigate potential maintenance challenges and ensure longevity in gear performance.
Investing in strategic sourcing not only optimizes supply chains but also fosters collaboration with reliable manufacturers who can meet specific industry needs. Given the increasing demand for compact, efficient power transmission solutions, now is the opportune time to align procurement strategies with the latest technological advancements in worm gear design.
As you consider your next sourcing decisions, prioritize partnerships that emphasize innovation and quality. By doing so, you can secure a competitive advantage in your market. Embrace the future of worm gear technology—your next strategic partnership could redefine your operational success.